3D Printing Satellite Panels with Lightweight Aluminum Alloys
목차
Introduction: The Orbital Shift – How 3D Printed Satellite Panels are Revolutionizing Aerospace Engineering
The aerospace industry stands at the precipice of unprecedented transformation, driven by relentless demands for lighter, faster, and more cost-effective spacecraft. Satellites, the workhorses of modern communication, navigation, Earth observation, and scientific discovery, are central to this evolution. Traditionally, manufacturing satellite components, particularly structural panels, has been a complex, costly, and time-consuming process involving subtractive machining, intricate assembly of multiple parts, and significant material waste. However, a powerful technological wave – 금속 적층 제조(AM)로 더 잘 알려져 있습니다. 금속 3D 프린팅 – is fundamentally reshaping how satellite panels and other critical 우주선 구성 요소 are designed, developed, and produced. This orbital shift promises not just incremental improvements but a paradigm change, enabling performance levels and mission capabilities previously considered unattainable.
Satellite panels are far more than simple coverings; they are multifunctional elements critical to mission success. They provide structural integrity, house sensitive electronics, manage thermal loads, and serve as mounting platforms for vital instruments and subsystems. The relentless pressure to reduce launch costs – often calculated in tens of thousands of dollars per kilogram sent into orbit – places an enormous premium on 경량 구성 요소. Every gram saved translates directly into significant financial savings or increased payload capacity. This is where the synergy between advanced lightweight alloys 및 금속 3D 프린팅 진정으로 빛납니다.
Traditional manufacturing methods often struggle to achieve optimal lightweighting without compromising structural integrity or incurring prohibitive costs. Machining large billets of metal into complex panel geometries inherently leads to substantial material waste (a poor buy-to-fly ratio), and assembling multiple smaller pieces introduces potential points of failure (joints, fasteners) while adding weight and complexity. 금속 적층 제조, conversely, builds parts layer by meticulous layer directly from digital designs using high-performance metal powders. This process unlocks unparalleled design freedom, enabling engineers to create highly optimized, complex geometries, including internal lattice structures and topologically optimized forms that mimic natural structures like bone – strong where needed, minimal elsewhere. This capability allows for the creation of satellite panels that are significantly lighter than their traditionally manufactured counterparts, yet possess equivalent or even superior strength and stiffness.
The advantages extend beyond mere weight reduction. AM facilitates rapid prototyping and design iteration, drastically shortening development cycles for new satellite platforms or components. Part consolidation, where multiple components are redesigned and printed as a single, monolithic piece, reduces assembly time, minimizes potential failure points, simplifies supply chains, and further decreases overall weight. Furthermore, AM enables the use of advanced materials specifically engineered for the harsh environment of space, offering tailored properties like high strength-to-weight ratios, specific thermal conductivity, and resistance to radiation and extreme temperature fluctuations.
Leading this charge requires not only innovative design approaches but also robust manufacturing capabilities and superior materials science. Companies like Met3dp, headquartered in Qingdao, China, are pivotal B2B aerospace suppliers in this domain. Specializing in industrial-grade 금속 3D 프린팅 equipment and the production of high-performance 금속 분말, Met3dp provides the foundational technologies necessary for aerospace engineers and procurement managers to leverage the full potential of AM. Our printers boast industry-leading build volumes, precision, and reliability – essential qualities when producing mission-critical space technology. Combined with our expertise in advanced 금속 분말다음을 포함합니다. lightweight aluminum alloys like AlSi10Mg and Scalmalloy®, as well as space-proven Titanium alloys like Ti-6Al-4V, Met3dp empowers organizations to manufacture next-generation satellite panels that meet the stringent demands of modern space exploration and commercialization. This technological leap is not just changing how satellites are built; it’s expanding what they can achieve.
Key Takeaways for Aerospace Professionals:
- Weight is Paramount: Metal AM offers unprecedented opportunities for lightweighting satellite panels, directly impacting launch costs and payload capacity.
- Complexity is an Asset: AM enables intricate designs (topology optimization, lattice structures) impossible with traditional methods, improving performance and functionality.
- Consolidation Simplifies: Printing multiple parts as one reduces assembly needs, potential failures, weight, and logistical complexity.
- Speed Accelerates Innovation: Rapid prototyping and shorter production lead times allow for faster development and deployment of satellite systems.
- Material Choice Matters: Advanced alloys tailored for AM and space environments are key enablers for optimal panel performance.
- Supplier Expertise is Crucial: Partnering with experienced AM providers like Met3dp ensures access to reliable equipment, high-quality materials, and application support.
This introduction sets the stage for a deeper exploration into the specific applications, benefits, materials, and considerations involved in utilizing 금속 3D 프린팅 for the production of advanced satellite panels, targeting the needs and interests of 항공우주 공학 teams and B2B procurement specialists seeking cutting-edge manufacturing solutions.
Core Functions: What Roles Do Satellite Panels Play in Modern Spacecraft Architecture?
To fully appreciate the impact of metal additive manufacturing on satellite design, it’s essential to understand the diverse and critical functions performed by various panels within a spacecraft architecture. These are not mere passive surfaces; they are highly engineered components integral to the satellite’s survival, operation, and overall mission success. The demands placed upon these panels – structural resilience during launch, operational stability in the harsh space environment, and specific functional performance – drive the need for advanced materials and manufacturing techniques like 금속 3D 프린팅.
Satellite panels can be broadly categorized based on their primary function, although many often serve multiple purposes simultaneously. Understanding these roles highlights why properties like stiffness, strength-to-weight ratio, thermal management, and dimensional accuracy are non-negotiable requirements for 항공우주 공학 and procurement teams sourcing 임무 수행에 중요한 부분.
1. Structural Panels (Primary and Secondary Structures): These form the backbone and skeleton of the satellite, providing the essential framework upon which all other components are mounted.
- Load Bearing: Must withstand extreme mechanical loads during launch, including intense vibrations, acoustic pressures, and high G-forces, without deformation or failure.
- Stiffness & Stability: Provide a rigid platform to maintain the precise alignment of sensitive instruments (like telescopes, antennas, sensors) throughout the mission lifetime, resisting micro-vibrations and thermal distortions in orbit.
- Interface Points: Incorporate precise mounting interfaces (brackets, inserts, bosses) for attaching subsystems, payloads, and mechanisms.
- 공통 양식: Often designed as isogrid or orthogrid structures (traditionally machined) or increasingly incorporating topology optimization and lattice structures (ideal for AM) to maximize stiffness while minimizing mass. Honeycomb sandwich panels are also common, where AM might be used for the face sheets or complex core geometries.
2. Equipment & Payload Mounting Panels: These panels serve as dedicated platforms for attaching specific satellite subsystems and the primary mission payload.
- Secure Attachment: Provide robust and reliable mounting points for delicate and often heavy equipment, including communication transponders, propulsion tanks, reaction wheels, batteries, onboard computers, and scientific instruments.
- Thermal Conduction Paths: Often designed to help conduct heat away from mounted electronics towards dedicated radiator panels.
- 진동 감쇠: May incorporate features or materials to isolate sensitive equipment from spacecraft bus vibrations.
- Precision Requirements: Demand high dimensional accuracy and tight tolerances for interface points to ensure proper alignment and function of attached hardware.
3. Thermal Management Panels (Radiators & Heat Shields): Controlling temperature is critical for satellite longevity and performance. Panels play a key role in radiating waste heat into space and shielding components from extreme temperatures.
- Radiator Panels: Designed with specific surface finishes (high emissivity coatings) and often internal structures (integrated heat pipes or fluid loops – potentially enhanced by AM) to efficiently reject waste heat generated by electronics and payloads. They need good thermal conductivity through the panel thickness.
- 열 차폐: Protect sensitive components from direct solar radiation or heat generated by other parts of the satellite (e.g., propulsion systems). Often utilize multi-layer insulation (MLI), but the underlying structural panel must withstand the temperature gradients.
- 머티리얼 속성: Require materials with appropriate thermal conductivity, stability across wide temperature ranges (-150°C to +150°C or more), and low thermal expansion.
4. Electronics Housings & Enclosures: These panels form boxes or enclosures to protect sensitive electronic components from the hazards of the space environment.
- Environmental Protection: Shield electronics from radiation (galactic cosmic rays, solar particles), micrometeoroids, atomic oxygen (in LEO), and electrostatic discharge.
- EMI/EMC Shielding: Often designed to prevent electromagnetic interference between different electronic systems. AM allows for complex internal shielding geometries.
- 구조적 지원: Provide mechanical support and mounting points for circuit boards and electronic assemblies.
- Thermal Management Integration: May incorporate features like heat sinks or conduction paths to manage heat generated by the enclosed electronics.
5. Solar Array Substrate Panels: These provide the structural backing for the photovoltaic cells that generate power for the satellite.
- Lightweight Structure: Must be extremely lightweight yet stiff enough to support the fragile solar cells during deployment and operation.
- Deployment Mechanisms: Often part of complex, deployable wing structures requiring intricate hinge mechanisms and reliable deployment kinematics. AM can potentially integrate some mechanism features.
- 열 안정성: Need to maintain flatness and dimensional stability across varying temperatures to ensure optimal solar cell performance and prevent cell cracking.
6. RF (Radio Frequency) Component Panels: Some panels integrate or support elements of the satellite’s communication or sensing systems.
- Antenna Reflectors/Structures: Panels shaped precisely to reflect or focus radio waves. Surface accuracy and stability are paramount.
- Waveguide Integration: AM allows for the possibility of integrating complex waveguide structures directly into structural panels, reducing connections and potential signal loss.
Summary Table: Satellite Panel Functions & Requirements
Panel Type | Primary Function(s) | Key Requirements | Relevance of Metal AM |
---|---|---|---|
Structural Panels | Load bearing, Stiffness, Component mounting | High Strength-to-Weight, High Stiffness, Fatigue Resistance, Precise Interfaces | Topology Optimization, Lattice Structures, Part Consolidation, Lightweighting |
Equipment Mounting | Secure attachment, Thermal path, Vibration damping | High Strength, Dimensional Accuracy, Good Thermal Conductivity, Stiffness | Complex Interface Geometries, Integrated Brackets, Optimized Conduction Paths |
열 관리 | Heat radiation (Radiators), Heat shielding | Specific Thermal Conductivity, High Emissivity (Surface), Thermal Stability | Integrated Cooling Channels, Complex Geometries for Heat Pipes, Optimized Radiator Shapes, Lightweight Structures |
Electronics Housings | Environmental protection, EMI shielding, Structure | Radiation Shielding, Strength, Thermal Management, EMI Gasketing Compatibility | Complex Internal Features, Conformal Shapes, Integrated Shielding, Part Consolidation |
Solar Array Substrates | Solar cell support, Deployment structure | Extreme Lightweighting, High Stiffness, Thermal Stability, Deployability | Ultra-lightweight Lattice Cores, Optimized Stiffeners, Integration of Mechanism Interfaces |
RF Component Panels | Antenna support/shaping, Waveguide integration | High Dimensional Accuracy, Surface Smoothness, RF Performance, Stability | Precise Complex Shapes (Reflectors), Integrated Waveguides, Lightweight Support Structures |
시트로 내보내기
Understanding these diverse and demanding roles underscores why the aerospace industry is keenly interested in 금속 적층 제조. The ability to create 경량, complex, highly integrated satellite panels using space-grade materials like AlSi10Mg, 스칼말로이®및 Ti-6Al-4V directly addresses the core challenges faced by 항공우주 공학 teams. For B2B procurement managers, sourcing panels produced via AM from capable suppliers like Met3dp offers a pathway to enhanced performance, reduced costs, and streamlined spacecraft component acquisition.
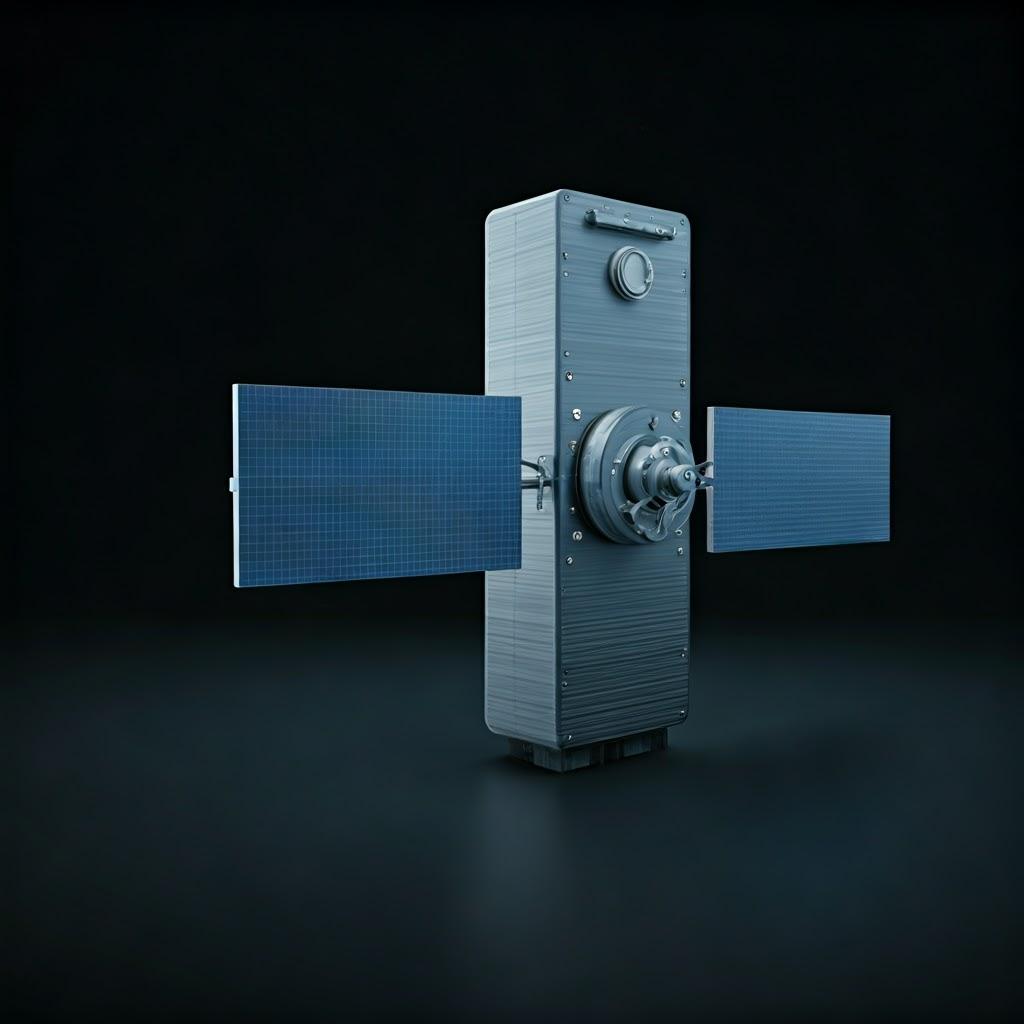
The Additive Advantage: Why Choose Metal 3D Printing for Satellite Panel Production?
While traditional manufacturing methods like CNC machining, sheet metal forming, casting, and complex assembly have served the aerospace industry for decades, they face inherent limitations when pushed to meet the escalating demands for lighter, more complex, and rapidly developed satellite components. Metal additive manufacturing (AM)또는 금속 3D 프린팅, offers a compelling suite of advantages that directly address these limitations, making it an increasingly preferred method for producing next-generation satellite panels. 대상 항공우주 엔지니어 focused on performance and procurement managers focused on value and supply chain efficiency, the benefits of AM are transformative.
Let’s dissect the key advantages of using 금속 3D 프린팅 에 비해 전통적인 제조 specifically in the context of satellite panel production:
1. Unparalleled Lightweighting Capabilities:
- AM 이점: Metal AM excels at creating complex internal geometries like 격자 구조 and enables 토폴로지 최적화 algorithms. These tools remove material from low-stress areas while reinforcing critical load paths, resulting in components that are significantly lighter (often 20-60% weight reduction) than traditionally machined or fabricated parts, without compromising strength or stiffness. This is paramount for reducing satellite launch costs.
- Traditional Limitation: Machining complex internal voids or lattices is often impossible or prohibitively expensive. Sheet metal structures have limitations in achieving truly optimized 3D load paths. Casting may require thick sections for flow, adding weight.
- Example: A structural bracket panel traditionally made from multiple machined pieces and fasteners can be redesigned using topology optimization and printed as a single, lighter AM component using 스칼말로이® 또는 Ti-6Al-4V.
2. Radical Part Consolidation:
- AM 이점: Complex assemblies comprising numerous individual parts (brackets, fasteners, plates, mounts) can often be redesigned and printed as a single, monolithic component. This drastically reduces part count, eliminates assembly labor and time, removes potential failure points associated with joints (welds, fasteners), simplifies inventory management, and inherently reduces overall weight.
- Traditional Limitation: Manufacturing complexity often dictates breaking down structures into simpler sub-components that must then be joined, adding complexity, weight, and inspection requirements.
- Example: An electronics housing panel requiring multiple internal mounting points, shielding walls, and external interfaces can be printed as one integrated piece, eliminating dozens of fasteners and several assembly steps.
3. Extreme Design Freedom and Complexity:
- AM 이점: AM builds parts layer-by-layer, freeing designers from many constraints imposed by traditional methods (e.g., tool access for machining, draft angles for casting, bend radii for sheet metal). This allows for the creation of highly intricate features, conformal shapes that follow complex curves, integrated cooling channels, internal voids, and functionally graded materials (though the latter is still emerging).
- Traditional Limitation: Designs are often dictated by the manufacturing process. Complex internal features are difficult or impossible. Tooling costs can make complex shapes uneconomical, especially for low-volume satellite production.
- Example: A thermal management panel can be printed with integrated, conformally shaped internal channels for fluid cooling loops, optimized precisely for the heat load distribution – a design impossible to machine.
4. Accelerated Prototyping and Development Cycles:
- AM 이점: Moving from a digital design file (CAD) to a physical metal part can be significantly faster with AM, especially for complex geometries, as it often bypasses the need for extensive tooling (molds, dies, fixtures). This enables rapid iteration – engineers can design, print, test, and refine components much more quickly, accelerating the overall satellite development timeline.
- Traditional Limitation: Creating tooling for casting or complex fixtures for machining can take weeks or months, making design iterations slow and costly.
- Example: Different design variations for a critical payload mounting panel can be printed and structurally tested within days or weeks using AM, compared to months using traditional methods involving casting pattern creation or complex multi-axis machining setups.
5. Improved Material Efficiency (Buy-to-Fly Ratio):
- AM 이점: Additive manufacturing is a near-net-shape process, meaning it uses primarily only the material needed for the final part, plus support structures (which are often recyclable). This significantly reduces material waste compared to subtractive processes like CNC machining, where a large percentage of an expensive raw material billet can be machined away. This is particularly important for costly aerospace alloys 같은 Ti-6Al-4V 및 스칼말로이®.
- Traditional Limitation: Subtractive machining inherently generates significant waste (chips). The ratio of raw material purchased to the final weight of the part (buy-to-fly ratio) can be very high (e.g., 10:1 or even 20:1 for complex machined parts).
- Example: Printing a complex Ti-6Al-4V satellite panel might achieve a buy-to-fly ratio closer to 2:1 or 3:1 (including supports), compared to potentially much higher ratios for machining it from a solid block.
6. Reduced Lead Times for Complex & Low-Volume Parts:
- AM 이점: For highly complex components or parts needed in low volumes (typical for many satellite programs), AM can often deliver finished parts faster than traditional methods burdened by tooling lead times or extensive machining/assembly sequences. This improves aerospace supply chain responsiveness.
- Traditional Limitation: Tooling, setup times, and multi-step processing can lead to long lead times, especially for custom or non-standard components.
- Example: Producing a set of 5 unique, highly complex structural panels for a specific satellite mission might be completed faster via AM than commissioning casting patterns or programming intricate 5-axis machining paths.
7. Enhanced Customization and On-Demand Manufacturing:
- AM 이점: Since AM works directly from digital files, modifying a design for specific mission requirements or creating unique variations is relatively straightforward, requiring only changes to the CAD model rather than physical tooling. This supports on-demand production and spares strategies.
- Traditional Limitation: Customization often requires significant retooling or reprogramming, making it costly and time-consuming.
Comparison Table: Metal AM vs. Traditional Manufacturing for Satellite Panels
기능 | 금속 적층 제조(AM) | Traditional Manufacturing (Machining, Assembly, Casting) | Advantage for Satellite Panels? |
---|---|---|---|
경량화 | Excellent (Topology Opt., Lattices) | Limited by process constraints | 높음 |
부품 통합 | High potential | Difficult / Adds complexity | 높음 |
디자인 복잡성 | High (Internal features, Conformal) | Restricted by tooling, access, process physics | 높음 |
Prototyping Speed | Fast (Tool-less for complex parts) | Slow (Tooling/Setup dependent) | 높음 |
재료 낭비 | Low (Near-net-shape) | High (Subtractive) / Moderate (Casting) | 중간-높음 |
Lead Time (Complex) | Potentially Shorter | Potentially Longer (Tooling, Multi-step) | 중간-높음 |
사용자 지정 | Easy (Digital file modification) | Costly / Time-consuming (Retooling) | Medium |
표면 마감 | Rougher (as-built), requires post-processing | Smoother (Machined), but limitations on complex surfaces | Depends on Requirements |
치수 정확도 | Good, improving, requires process control & post-machining | Very High (Machining), Moderate (Casting) | Depends on Requirements |
Cost (per part) | Can be higher for simple parts, competitive for complex/consolidated | Lower for simple/high-volume, higher for complex/low-volume tooling | Depends on Complexity/Volume |
시트로 내보내기
Leveraging these advantages requires expertise in both design for additive manufacturing (DfAM) and the printing process itself. Partnering with a knowledgeable 금속 AM 서비스 제공업체 like Met3dp, which offers not only state-of-the-art 인쇄 방법 like Selective Electron Beam Melting (SEBM) but also deep material science knowledge, is crucial. Met3dp’s capabilities enable aerospace manufacturers 그리고 그들의 B2B 공급업체 to fully exploit the benefits of additive manufacturing, pushing the boundaries of satellite panel design and performance while optimizing the aerospace supply chain.
Material Matters: Selecting Optimal Lightweight Alloys for 3D Printed Satellite Panels
The choice of material is absolutely fundamental to the success of any aerospace component, and 3D printed satellite panels are no exception. The demanding space environment – encompassing vacuum, extreme temperature cycles, radiation, and the violent forces of launch – dictates a stringent set of material requirements. Furthermore, the overarching goal of 경량화 to reduce launch costs heavily influences material selection. Fortunately, 금속 적층 제조 is compatible with a range of advanced aerospace alloys perfectly suited for these challenges. The three recommended powders – AlSi10Mg, 스칼말로이®및 Ti-6Al-4V – represent a spectrum of properties catering to different panel applications and performance needs.
Understanding the characteristics of each alloy is crucial for 항공우주 엔지니어 making design decisions and for procurement managers sourcing materials or 금속 3D 프린팅 서비스. Key properties to consider include:
- Density (ρ): Directly impacts weight (Lower is better for lightweighting).
- Specific Strength (Ultimate Tensile Strength / Density): Strength per unit weight – a critical metric for aerospace.
- Specific Stiffness (Young’s Modulus / Density): Stiffness per unit weight – important for structural stability.
- Thermal Conductivity (k): Ability to conduct heat – vital for thermal management panels.
- 열팽창 계수(CTE): How much the material expands/contracts with temperature changes – low CTE is preferred for dimensional stability.
- 피로 강도: Resistance to failure under cyclic loading (e.g., vibrations).
- Environmental Resistance: Compatibility with vacuum (low outgassing), radiation, temperature extremes, and potential corrosive elements (e.g., residual propellants).
- Printability & Processability: Ease of printing high-quality, dense parts using AM processes (like Laser Powder Bed Fusion – L-PBF or Electron Beam Melting – EBM) and ease of post-processing (heat treatment, machining).
Let’s examine the recommended materials in detail:
1. Aluminum-Silicon-Magnesium Alloy (AlSi10Mg): The Workhorse Aluminum
- 구성: Primarily Aluminum, with ~10% Silicon and <0.5% Magnesium.
- 속성:
- 장점: Relatively low density (~2.67 g/cm³), good printability via L-PBF, excellent thermal conductivity (~120-150 W/m·K), good corrosion resistance, readily available, relatively cost-effective compared to other aerospace alloys. Offers moderate strength after appropriate heat treatment.
- 단점: Lower strength and temperature resistance compared to Scalmalloy® or Ti-6Al-4V (loses significant strength above ~150-200°C). Lower fatigue strength.
- Typical Satellite Panel Applications:
- Structural panels with moderate loading requirements.
- Electronics housings where good thermal dissipation is needed.
- Heat exchangers and radiator panel components (especially internal structures).
- Mounting brackets for less critical components.
- Prototypes where cost and speed are primary drivers.
- Why it Matters: AlSi10Mg provides a reliable and well-understood baseline for many AM applications. Its balance of low density, good thermal properties, and printability makes it suitable for a wide range of panels where extreme mechanical performance isn’t the sole driver.
2. Scalmalloy®: The High-Performance Aluminum
- 구성: An Aluminum-Magnesium-Scandium alloy (proprietary composition by APWorks/Airbus). Specifically designed for additive manufacturing.
- 속성:
- 장점: Very high specific strength, approaching that of Ti-6Al-4V but at a lower density (~2.66 g/cm³). Excellent ductility and toughness compared to other high-strength AM aluminums. Good fatigue properties and weldability (useful for potential post-processing or assembly). Retains strength better at slightly elevated temperatures than AlSi10Mg. Exceptional printability via L-PBF.
- 단점: Higher material cost compared to AlSi10Mg. Scandium is an expensive alloying element. Requires precise process control during printing and heat treatment to achieve optimal properties. Less thermal conductivity than AlSi10Mg (~100 W/m·K).
- Typical Satellite Panel Applications:
- Primary structural panels requiring maximum lightweighting under significant loads.
- Highly loaded brackets and interface components.
- Direct replacement for heavier traditional aluminum or even some titanium components.
- Components subjected to significant vibration or fatigue loading.
- Performance-critical applications where weight savings justify the higher material cost.
- Why it Matters: Scalmalloy® pushes the boundaries of what’s possible with aluminum alloys in AM. It allows engineers to design extremely lightweight yet strong and durable satellite panels, directly competing with titanium in many structural applications while offering lower density and often easier processing.
3. Titanium Alloy (Ti-6Al-4V, Grade 5 & Grade 23 ELI): The Space-Proven Standard
- 구성: Titanium alloyed with ~6% Aluminum and ~4% Vanadium. Grade 23 (ELI – Extra Low Interstitial) has lower oxygen, nitrogen, and carbon content for improved ductility and fracture toughness.
- 속성:
- 장점: Excellent specific strength, especially at elevated temperatures (maintains strength well up to ~300-400°C). High stiffness. Exceptional corrosion resistance (inert in most environments). Biocompatible (though less relevant for panels). Good fatigue life. Grade 23 offers enhanced damage tolerance. Extensive flight heritage in aerospace.
- 단점: Higher density compared to aluminum alloys (~4.43 g/cm³). Significantly higher material cost. More challenging to print (reactive with oxygen/nitrogen, requires inert atmosphere or vacuum – EBM is well-suited) and post-process (difficult to machine, specific heat treatments needed like HIP). Lower thermal conductivity (~6.7 W/m·K).
- Typical Satellite Panel Applications:
- Critical structural panels operating under high loads or at elevated temperatures (e.g., near engines or high-power electronics).
- Mounting brackets for heavy components or those requiring maximum stiffness.
- Components requiring extreme durability, fatigue resistance, or fracture toughness (often Grade 23 ELI).
- Panels potentially exposed to corrosive substances (e.g., propellant interfaces).
- Applications where the higher density is acceptable due to superior mechanical or thermal performance requirements.
- Why it Matters: Ti-6Al-4V remains the benchmark for high-performance aerospace applications. Its proven track record, excellent mechanical properties across a range of temperatures, and superb corrosion resistance make it the material of choice for the most demanding satellite panel applications, despite its higher weight and cost compared to advanced aluminums.
Material Properties Comparison Table (Typical Values for AM)
속성 | 단위 | AlSi10Mg (Heat Treated) | Scalmalloy® (Heat Treated) | Ti-6Al-4V (Grade 5, Annealed/HIP) | Ti-6Al-4V (Grade 23, Annealed/HIP) |
---|---|---|---|---|---|
Density (ρ) | g/cm³ | ~2.67 | ~2.66 | ~4.43 | ~4.42 |
최대 인장 강도(UTS) | MPa | ~350 – 450 | ~500 – 540 | ~900 – 1000 | ~830 – 950 |
항복 강도(0.2% 오프셋) | MPa | ~250 – 350 | ~450 – 500 | ~830 – 930 | ~760 – 880 |
파단 연신율 (%) | % | ~6 – 12 | ~10 – 16 | ~10 – 18 | ~12 – 20 |
Young’s Modulus (E) | 평점 | ~70 – 75 | ~75 – 80 | ~110 – 115 | ~105 – 110 |
Specific Strength (UTS/ρ) | kNm/kg (approx.) | ~131 – 169 | ~188 – 203 | ~203 – 226 | ~188 – 215 |
Specific Stiffness (E/ρ) | MNm/kg (approx.) | ~26 – 28 | ~28 – 30 | ~25 – 26 | ~24 – 25 |
Thermal Conductivity (k) | W/m·K | ~120 – 150 | ~100 – 120 | ~6.7 | ~7.0 |
Max Operating Temp (approx.) | °C | ~150 | ~200 | ~350 | ~350 |
시트로 내보내기
Note: Properties can vary significantly based on AM process parameters, build orientation, heat treatment, and testing conditions. These are representative values.
Met3dp’s Role in Material Excellence: Selecting the right alloy is only part of the equation. The quality and consistency of the 금속 분말 itself are critical for achieving the desired material properties in the final printed part. This is where Met3dp’s expertise as a 금속 분말 공급업체 becomes invaluable. Utilizing industry-leading powder manufacturing technologies like Vacuum Induction Melting Gas Atomization (VIGA) and Plasma Rotating Electrode Process (PREP), Met3dp produces 고품질 금속 분말 characterized by:
- 높은 구형성: Ensures good powder flowability and high packing density in the powder bed, leading to denser, more uniform parts.
- Low Satellite Content: Minimizes fine particles attached to larger ones, improving flow and reducing potential defects.
- Controlled Particle Size Distribution (PSD): Tailored PSDs optimized for specific AM processes (L-PBF, EBM) ensure consistent melting and layer formation.
- High Purity & Controlled Chemistry: Strict control over alloy composition and minimization of impurities (like oxygen, nitrogen) are crucial for achieving target mechanical and physical properties, especially for reactive alloys like Titanium.
Met3dp offers a comprehensive product portfolio that includes not only standard alloys like AlSi10Mg 및 Ti-6Al-4V (including Grade 23 ELI) but also extends to more specialized materials relevant to aerospace, such as superalloys (Inconel 718, 625), other titanium alloys (TiAl, TiNbZr), and stainless steels, ensuring that B2B procurement teams and engineers have access to the right materials for their demanding satellite panel applications. Our commitment to powder quality directly translates to more reliable and performant 3D printed components for the 항공우주 산업.
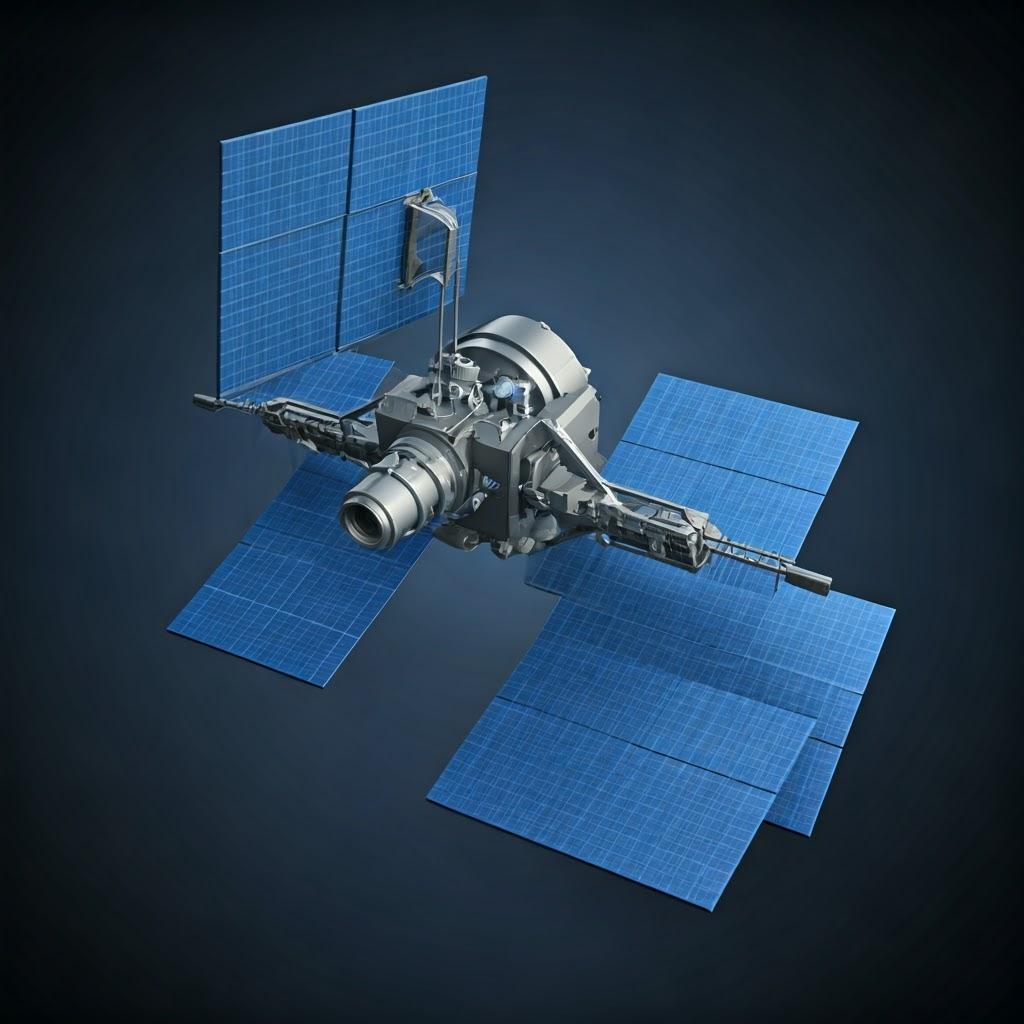
Designing for the Stars: Key Considerations for Additively Manufactured Satellite Panels
Successfully leveraging 금속 적층 제조(AM) 에 대한 satellite panels requires more than simply converting an existing design file and hitting “print.” It demands a fundamental shift in design philosophy, embracing the principles of 적층 제조를 위한 설계(DfAM). DfAM isn’t just about accommodating the printing process; it’s about actively exploiting its unique capabilities – like creating complex geometries and consolidating parts – to achieve superior performance, lighter weight, and faster development, goals paramount in 항공우주 공학. For B2B design services and in-house engineering teams, mastering DfAM is key to unlocking the full potential of 금속 3D 프린팅 에 대한 우주선 구성 요소.
Here are crucial DfAM considerations when designing satellite panels for metal AM production:
1. Embrace Topology Optimization:
- What it is: A computational design technique where software algorithms, given a design space, load conditions, constraints, and material properties, determine the most efficient material layout to meet performance targets (e.g., stiffness, strength). It essentially carves away unnecessary material, leaving behind an optimized, often organic-looking structure.
- Why it Matters for Panels: This is arguably the most powerful tool for achieving drastic 경량화 in structural and mounting panels. It ensures material is placed only where it’s structurally necessary to handle launch loads and operational stresses, leading to significant mass reduction compared to traditional designs based on standard profiles or pocketing.
- How to Apply:
- Define the design space (maximum allowable volume).
- Accurately define all load cases (static, dynamic, thermal).
- Specify constraints (fixed points, keep-out zones for interfaces or components).
- Select manufacturing constraints suitable for AM (e.g., minimum member size).
- Utilize robust simulation software (FEA integrated with topology optimization tools like Altair OptiStruct, Dassault Systèmes TOSCA, Ansys Discovery, etc.).
- Interpret and refine the often complex output into a manufacturable AM design.
- 고려 사항: Requires accurate load definition and simulation expertise. The resulting geometries can be complex and may require careful orientation and support planning for printing.
2. Leverage Lattice Structures Strategically:
- What they are: Engineered porous structures composed of repeating unit cells (e.g., strut-based like cubic or octet-truss, or surface-based like TPMS – Triply Periodic Minimal Surfaces such as gyroids or Schwarzites). AM is uniquely capable of producing these intricate internal structures.
- Why they Matter for Panels:
- 경량화: Used as core structures in sandwich panels or as infill for thicker sections, significantly reducing weight while maintaining good stiffness and buckling resistance.
- 에너지 흡수: Can be designed to crush predictably, potentially enhancing resilience to vibration or impact loads.
- 열 관리: High surface area within lattices can enhance heat transfer, useful for integrated cooling or radiator panel cores. TPMS structures offer smooth, continuous surfaces beneficial for fluid flow.
- 맞춤형 속성: Stiffness and strength can be tuned by varying cell type, size, and strut/wall thickness.
- How to Apply:
- Select appropriate lattice type based on primary function (stiffness, heat transfer, etc.).
- Integrate lattice generation tools within CAD or specialized software.
- Ensure strut/wall thickness is well above the minimum printable feature size for the chosen AM process and material.
- Consider powder removal from complex internal lattices – design for accessibility or use TPMS structures which are inherently self-draining.
- 고려 사항: Designing, simulating, and inspecting complex lattices can be challenging. Ensuring complete powder removal is critical.
3. Pursue Aggressive Part Consolidation:
- What it is: Rethinking assemblies made of multiple traditionally manufactured parts (plates, brackets, fasteners, tubes) and redesigning them to be printed as a single, monolithic component.
- Why it Matters for Panels: Reduces assembly time and labor, eliminates potential failure points at joints/fasteners, simplifies supply chain and inventory management, often reduces overall weight by eliminating flanges and fastener mass, and can improve structural efficiency.
- How to Apply:
- Analyze existing panel assemblies: Identify adjacent parts with simple interfaces, numerous fasteners, or components performing related functions.
- Redesign interfaces for seamless integration within a single AM part.
- Incorporate mounting features, fluid channels, or brackets directly into the main panel structure.
- Perform thorough functional and structural analysis (FEA) of the consolidated design to ensure it meets all original requirements.
- 고려 사항: Increases the complexity of the single AM part. Failure of a consolidated part might be more critical than failure of a single component in an assembly (requires rigorous validation). May complicate repairs (replacement instead of fixing a sub-component).
4. Design for Support Minimization and Removal:
- Why Supports are Needed: Metal AM processes like L-PBF require support structures for overhang features (typically below 45° from horizontal) to anchor them to the build plate or lower layers, prevent warping, and conduct heat away. EBM often requires fewer supports due to the powder cake providing some support.
- Why Minimize Them: Supports consume extra material, add printing time, require significant post-processing effort for removal, and can leave witness marks affecting surface finish.
- How to Design:
- Orientation: Orient the panel in the build chamber to make critical surfaces vertical or upward-facing, and minimize downward-facing overhangs.
- 자립 각도: Design overhangs to be above the critical angle (e.g., >45°) where possible. Use chamfers instead of sharp overhangs.
- Self-Supporting Features: Use diamond or teardrop shapes for horizontal holes instead of perfect circles.
- 접근성: Ensure support structures are physically accessible for removal tools (manual or automated). Avoid trapping supports in enclosed cavities unless dissolvable supports or specific strategies are used.
- Support Design: Work with the AM provider to optimize support type (e.g., cone, block, line) and density (using easily breakable contact points) for easier removal while still providing necessary function.
- 고려 사항: Optimal orientation often involves trade-offs between support needs, surface finish, build time, and potential distortion.
5. Adhere to Process-Specific Feature Limitations:
- 벽 두께: Design walls thicker than the minimum printable limit for the chosen process/material (e.g., typically 0.3-0.5 mm for L-PBF, potentially thicker for EBM). Very thin walls are prone to warping and damage during handling/post-processing. Consider buckling behavior.
- Feature Size: Small holes, pins, slots, and fine details have minimum producible sizes. Horizontal holes are often less accurate than vertical ones.
- Aspect Ratio: Very tall, thin features can be prone to vibration or distortion during the build.
- Channels: Internal channels need minimum diameters for effective powder removal (typically >1-2 mm, depending on length and complexity).
6. Manage Residual Stress Through Design:
- The Problem: Rapid heating and cooling during AM builds significant internal stresses, which can cause warping, cracking, or dimensional inaccuracies.
- Design Solutions:
- Avoid large, flat, unsupported areas parallel to the build plate.
- Use generous fillets and radii instead of sharp internal corners where stress concentrates.
- Incorporate stress-relieving features or topology where appropriate.
- Consider build orientation’s impact on thermal gradients.
- Gradual transitions in thickness are preferred over abrupt changes.
7. Design with Post-Processing in Mind:
- Machining Allowances: If tight tolerances or specific surface finishes are required on certain features (e.g., mounting interfaces, mating surfaces), add extra stock material (e.g., 0.5-2 mm) in those areas in the CAD model to be removed by CNC machining later.
- Datum Features: Include clear, easily accessible datum features in the design to facilitate setup for post-machining and inspection (CMM).
- Access: Ensure tools and probes have access for support removal, surface finishing (e.g., blasting, polishing), and NDT inspection (e.g., line-of-sight for certain methods).
Partnering for DfAM Success: Mastering DfAM, especially for mission-critical 위성 구성 요소, requires experience. Collaborating with a knowledgeable AM partner is invaluable. Met3dp, with its deep expertise in both 금속 3D 프린팅 equipment (including high-performance SEBM systems) and advanced 금속 분말, offers comprehensive application development services. Our team can assist 항공우주 엔지니어 및 B2B 공급업체 in optimizing panel designs specifically for additive manufacturing, considering material properties, process capabilities, support strategies, and post-processing requirements to ensure a successful outcome from concept to flight-ready part. This collaborative approach helps mitigate risks and maximizes the benefits AM offers.
Precision in Orbit: Achieving Tight Tolerances, Surface Finish, and Dimensional Accuracy
While metal additive manufacturing unlocks incredible design freedom, components destined for orbit must meet stringent requirements for precision. Satellite panels often incorporate critical interfaces for mounting sensitive payloads, aligning structural elements, or ensuring thermal contact. Therefore, understanding and managing 치수 정확도, 허용 오차및 표면 마감 is paramount for 항공우주 엔지니어 및 품질 보증 teams. While AM may not match the as-built precision of high-end CNC machining across the entire part, strategic design and post-processing allow it to meet the demanding 항공우주 표준 에 대한 임무 수행에 중요한 부분.
As-Built vs. Finished Precision: It’s crucial to distinguish between the precision achievable directly from the AM process (“as-built”) and the final precision after post-processing steps like machining.
- As-Built Accuracy: Typically ranges from ±0.1 mm to ±0.2 mm for smaller features, or ±0.5% to ±1% of the overall dimension for larger parts. This variability is influenced by numerous factors (see below). It’s generally sufficient for non-critical features or parts where overall form is more important than exact dimensions.
- As-Built Surface Finish (Roughness, Ra): Highly dependent on the AM process (L-PBF generally smoother than EBM), material, parameters, build orientation, and location on the part.
- Vertical Walls: Often the smoothest, potentially 5-15 µm Ra.
- Upward-Facing Surfaces: Slightly rougher due to powder partially adhering, perhaps 10-20 µm Ra.
- Downward-Facing (Overhang) Surfaces: Typically the roughest due to support structure contact points or direct exposure to the energy source, potentially >20-25 µm Ra.
- Finished Accuracy & Surface Finish: By incorporating post-machining steps (CNC milling, turning, grinding) for critical features, tolerances comparable to traditional manufacturing (e.g., ±0.01 mm to ±0.05 mm or tighter) and very smooth surface finishes (Ra < 1 µm) can be achieved where necessary.
Factors Influencing As-Built Precision:
- AM Machine Calibration & Condition: Regular calibration of scanners/electron gun, beam focus, and motion systems is vital.
- 프로세스 매개변수: Laser/beam power, scan speed, layer thickness, hatch spacing, scan strategy all impact melt pool stability and solidification, affecting accuracy and finish.
- 파우더 품질: Consistent particle size distribution (PSD), morphology (sphericity), and flowability of the 금속 분말 (a core strength of Met3dp’s offerings) contribute to uniform layers and stable melting.
- 열 효과: Residual stresses built up during heating/cooling cycles can cause warping and distortion, affecting final dimensions. Support strategy and stress relief are key controls.
- 파트 오리엔테이션: Affects support needs, surface roughness on different faces, and susceptibility to thermal distortion.
- Support Strategy: Density and location of supports influence heat dissipation and potential distortion during the build and removal stages.
- 열처리: Post-build heat treatments (stress relief, HIP, annealing) can cause minor dimensional changes that need to be accounted for.
Managing Tolerances and Surface Finish for Satellite Panels:
- Geometric Dimensioning and Tolerancing (GD&T): Apply GD&T rigorously but strategically. Define tight tolerances 오직 on critical interfaces (e.g., mounting holes/pads, mating surfaces, alignment features). Use looser profile tolerances for less critical surfaces where AM’s as-built accuracy is sufficient. This avoids unnecessary and costly post-machining.
- Designate Critical Surfaces: Clearly indicate on drawings which surfaces require post-machining and specify the final tolerance and surface finish requirements (e.g., Ra value).
- Near-Net-Shape Strategy: Design the AM part as a “near-net-shape” blank, adding sufficient machining stock (e.g., 0.5-2 mm) specifically on critical surfaces.
- Datum Features: Incorporate robust, easily accessible datum features into the design. These are essential reference points for accurately setting up the part on CNC machines for post-processing and on CMMs for inspection.
- Surface Finish Improvement:
- Overall Smoothing: Techniques like bead blasting, sand blasting, or tumbling can improve general surface finish and remove loose powder, often sufficient for non-critical areas.
- Targeted Finishing: For specific requirements like improved fatigue life, sealing, or RF performance, more advanced techniques like abrasive flow machining (AFM), electrochemical polishing (ECP), or manual polishing might be employed after initial smoothing or machining.
Typical Surface Roughness (Ra) Comparison:
Surface Condition / Process | Typical Ra Range (µm) | 참고 |
---|---|---|
As-Built Metal AM (L-PBF) | ||
– Vertical Wall | 5 – 15 | Generally smoothest as-built surface |
– Upward-Facing Surface | 10 – 20 | Slight roughness from partially sintered powder |
– Downward-Facing (Supported) | 15 – 30+ | Rougher due to support contact points / melt dynamics |
As-Built Metal AM (EBM) | 20 – 40+ | Generally rougher than L-PBF due to larger layer thickness/particles |
Post-Processing Finishes | ||
– Bead / Sand Blasting | 2 – 10 | Provides a uniform matte finish, removes loose particles |
– Tumbling / Vibratory Finishing | 1 – 5 | Good for bulk finishing, edge rounding |
– CNC Machining (Milling/Turning) | 0.4 – 6.3 | Standard machining range, controllable |
– CNC Machining (Grinding) | 0.1 – 1.6 | For very high precision and smooth finishes |
– Polishing / Lapping | < 0.1 – 0.8 | For mirror finishes, optical or sealing surfaces |
시트로 내보내기
Inspection and Metrology – Ensuring Compliance: Verifying that the final satellite panel meets all dimensional and surface specifications is critical. A multi-stage inspection approach is often used:
- 진행 중인 모니터링: Some advanced AM machines offer real-time monitoring of melt pool characteristics or layer topography, providing early indications of potential issues.
- 비파괴 검사(NDT): CT scanning is invaluable for checking internal geometry, detecting voids/inclusions, and verifying powder removal from internal channels. Other NDT methods (DPI, UT, RT) check for surface and subsurface flaws (covered more in Post-Processing).
- 3D Scanning: Laser or structured light scanning captures the overall geometry of the as-built or finished part, allowing comparison to the original CAD model and assessment of overall form and warp.
- Coordinate Measuring Machine (CMM): Touch probe or optical CMMs provide high-accuracy measurements of specific features, dimensions, and GD&T callouts, typically performed after final machining on critical features.
Met3dp’s Commitment to Precision: Achieving consistent precision starts with reliable equipment and high-quality materials. Met3dp provides industrial 금속 3D 프린터 engineered for accuracy and repeatability, essential for producing 임무 수행에 중요한 부분. Our rigorous quality control in 금속 분말 production ensures consistent feedstock, which is fundamental to achieving predictable results build after build. While post-processing is often required for the tightest tolerances, starting with a high-quality, dimensionally accurate as-built part from a reliable system significantly streamlines the path to a flight-ready satellite panel, reinforcing our role as a trusted B2B supplier for demanding 항공우주 제조 애플리케이션.
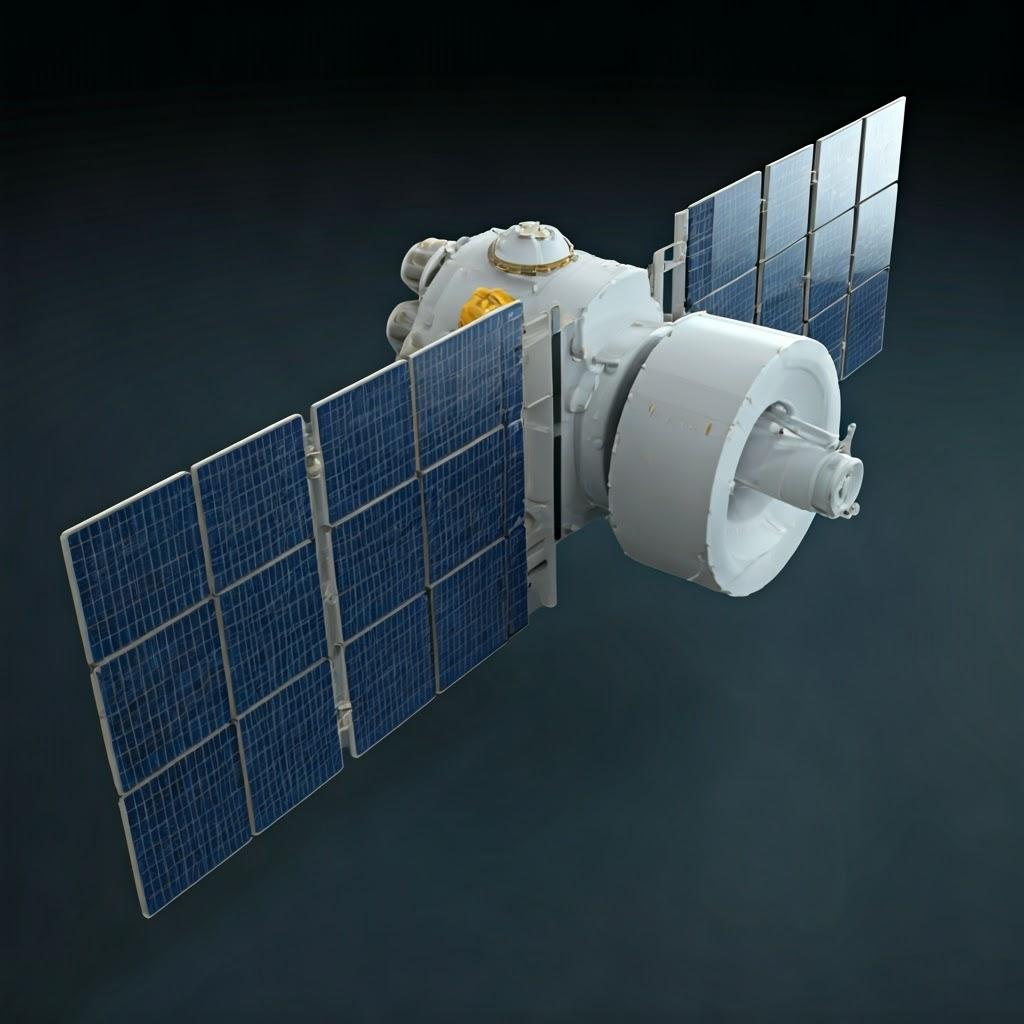
Beyond the Build: Essential Post-Processing Steps for 3D Printed Satellite Panels
A common misconception about 금속 적층 제조 is that parts come off the printer ready for immediate use. While AM creates the near-net shape, a series of crucial 후처리 steps are almost always required to transform an as-built component into a flight-ready satellite panel that meets stringent 항공우주 requirements for mechanical properties, dimensional accuracy, surface finish, and overall integrity. Understanding this workflow is vital for accurate project planning, costing, and lead time estimation by 엔지니어링 및 procurement teams.
The specific steps and their sequence can vary depending on the material (e.g., AlSi10Mg, 스칼말로이®, Ti-6Al-4V), the AM process used (L-PBF, EBM), design complexity, and the application’s specific requirements. However, a typical workflow includes:
1. Thermal Treatments (Often First Steps):
- 스트레스 해소: This is typically the very first step after the build finishes, often performed while the part is still attached to the build plate inside a furnace with an inert atmosphere (e.g., Argon). The rapid heating and cooling cycles inherent in AM (especially L-PBF) induce significant internal residual stresses. Stress relief involves heating the part to a specific temperature (below transformation points), holding it, and slowly cooling it down. This reduces internal stresses, preventing distortion or cracking during subsequent steps like part removal or machining.
- Heat Treatment (for Properties): Performed after part removal and sometimes after rough machining. This aims to optimize the material’s microstructure and mechanical properties.
- 열간 등방성 프레싱(HIP): Considered essential for most critical 항공우주 부품, especially those made from Ti-6Al-4V. Parts are subjected to high temperature (just below melting point) and high isostatic pressure (using an inert gas like Argon, ~100-200 MPa) for several hours. This process effectively closes internal pores and voids that might have formed during printing, significantly improving density (to near 100%), ductility, fatigue life, and fracture toughness.
- Solution Annealing & Aging (Hardening): Specific heat treatment cycles tailored to the alloy (e.g., T6 heat treatment for AlSi10Mg 및 스칼말로이®) to dissolve alloying elements into the matrix and then precipitate them in a controlled manner to achieve desired strength, hardness, and ductility levels. Parameters (temperature, time) are critical and alloy-specific.
2. Physical Separation and Support Removal:
- 빌드 플레이트에서 파트 제거: After stress relief (if needed on the plate), the printed panel is carefully detached from the build plate. This is often done using wire EDM (Electrical Discharge Machining) for a clean cut, or sometimes a bandsaw.
- 지원 구조 제거: This can be one of the most time-consuming and labor-intensive steps. Supports are typically removed manually using hand tools (pliers, cutters, grinders) or sometimes via CNC machining or specialized methods like electrochemical machining for difficult-to-reach areas. Care must be taken to avoid damaging the part surface. Witness marks where supports were attached are common and often require further finishing. DfAM strategies that minimize supports and ensure accessibility are highly beneficial here.
3. Surface Refinement and Finishing:
- Bulk Powder Removal & Cleaning: Thoroughly removing any residual, unfused 금속 분말, especially from internal channels or complex lattice structures, is critical. This typically involves compressed air blow-off, bead blasting, or ultrasonic cleaning. Trapped powder can be a contamination issue or add unwanted mass.
- General Surface Smoothing: As-built AM surfaces are relatively rough. Various methods can provide a more uniform and smoother finish:
- Bead Blasting / Sand Blasting: Propels fine media (glass beads, ceramic, aluminum oxide) at the surface. Creates a uniform matte finish, improves cosmetic appearance, and can impart compressive stress beneficial for fatigue life.
- Tumbling / Vibratory Finishing: Places parts in a tub with abrasive media, which vibrates or tumbles. Good for smoothing surfaces and deburring edges on multiple parts simultaneously, though less precise for specific features.
- Abrasive Flow Machining (AFM): Pushes an abrasive putty through internal channels or over surfaces to smooth them. Effective for internal passages.
- Electrochemical Polishing (ECP): Uses an electrochemical process to remove material, resulting in a very smooth, bright finish. Particularly effective on certain alloys like stainless steels and some titanium alloys.
- Targeted Surface Finishing: Specific areas requiring very low roughness (e.g., Ra < 0.8 µm) for sealing, optical mounting, or RF performance usually require manual polishing or precision machining/grinding.
4. Machining for Precision:
- CNC 가공: As discussed previously, critical interfaces, mounting holes, mating surfaces, and any features requiring tolerances tighter than AM’s as-built capability are typically finished using CNC milling, turning, or grinding. This requires careful fixture design to hold the often complex AM part securely and accurately referencing datum features.
5. Inspection and Quality Assurance (NDT):
- 비파괴 검사(NDT): Essential for verifying the integrity of flight hardware. NDT is often performed at multiple stages (e.g., after HIP, after final machining).
- Computed Tomography (CT) Scanning: Provides detailed 3D visualization of the part’s interior, detecting porosity, inclusions, cracks, and verifying internal geometries without damaging the part.
- Dye Penetrant Inspection (DPI) or Fluorescent Penetrant Inspection (FPI): Detects surface-breaking cracks.
- Ultrasonic Testing (UT): Detects subsurface flaws using sound waves.
- Radiographic Testing (RT): X-ray based method to find internal defects.
- Final Dimensional Inspection: Using CMM or 3D scanning to confirm all dimensions and GD&T requirements are met.
6. Final Cleaning and Coating:
- Final Cleaning: Rigorous cleaning procedures to remove any residues from machining fluids, NDT chemicals, or handling, ensuring the part is ready for integration into the satellite assembly (often performed in a cleanroom environment).
- Coating / Surface Treatment: Applying specialized coatings if required by the design, such as:
- Thermal Control Coatings: Paints or deposited layers with specific emissivity and absorptivity for radiator panels or thermal management.
- 부식 방지: Anodizing (for aluminum alloys like AlSi10Mg, 스칼말로이®) or conversion coatings.
- Wear Resistance Coatings: For specific interface points.
Process Flow Considerations: The exact sequence matters. For example, HIP is usually done before final machining, as the process can cause slight dimensional changes. NDT might occur after heat treatments and again after final machining. Effective planning and integration of these 후처리 steps are crucial for managing cost and lead time. B2B finishing services specializing in AM parts often play a key role in this ecosystem.
동안 Met3dp primarily focuses on providing industry-leading 금속 3D 프린터 및 고품질 금속 분말, we understand that these are just the initial stages of producing a flight-ready component. Our team possesses the knowledge of the entire AM workflow and can provide valuable insights and guidance to customers navigating the complexities of post-processing, ensuring that the parts produced using our systems and materials ultimately meet the demanding specifications of aerospace component finishing 에 대한 satellite panels.
Navigating Challenges: Common Issues in 3D Printing Satellite Panels and Expert Solutions
While the advantages of 금속 적층 제조 에 대한 satellite panels are compelling, like any advanced manufacturing process, it’s not without its potential challenges. Proactively understanding these common issues and implementing effective mitigation strategies is key to achieving consistent, high-quality results suitable for mission-critical aerospace applications. Partnering with an experienced and knowledgeable AM supplier can significantly help navigate these complexities.
Here are some common challenges encountered in 3D printing satellite panels and expert solutions:
1. Warping and Distortion:
- 문제입니다: Deviation from the intended geometry caused by the build-up and release of internal residual stresses during the printing process. Large, flat panels or parts with abrupt thickness changes are particularly susceptible.
- Causes: High thermal gradients during rapid heating/cooling cycles, insufficient support allowing the part to lift from the build plate, improper stress relief.
- Solutions:
- Optimized Orientation: Orienting the panel to minimize large flat areas parallel to the build plate and reduce thermal stresses.
- Effective Support Strategy: Using robust supports, particularly near edges and overhangs, to anchor the part firmly and conduct heat away efficiently. Simulation tools can help optimize support placement.
- 프로세스 매개변수 최적화: Fine-tuning scan strategies (e.g., island scanning, varying parameters across sections) to manage heat input.
- Prompt & Proper Stress Relief: Performing stress relief heat treatment immediately after the build, often before removing the part from the build plate, is critical.
- Design Modifications: Incorporating ribs or other stiffening features, using gradual thickness transitions.
2. Residual Stress Management:
- 문제입니다: Even if warping is controlled, high internal stresses can remain, potentially leading to premature cracking during post-processing (e.g., machining) or reduced fatigue life in service.
- Causes: Inherent to layer-wise melting and solidification. Influenced by material properties, part geometry, and process parameters.
- Solutions:
- Effective Thermal Post-Processing: Stress relief and HIP are primary methods for reducing residual stress to acceptable levels.
- Optimized Process Parameters: As with warping, careful control over energy input and scan strategy helps manage stress accumulation.
- 디자인 고려 사항: Avoiding sharp internal corners (use fillets), minimizing large variations in cross-section.
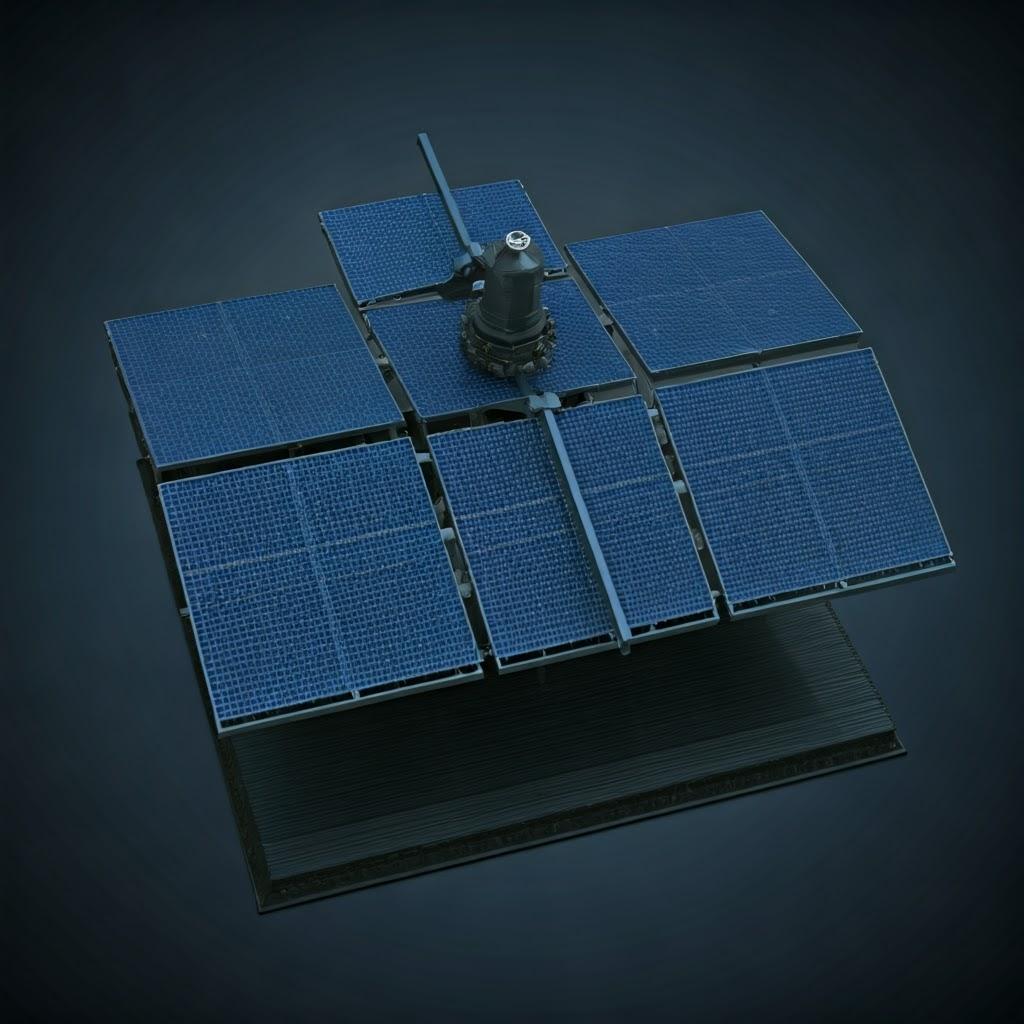
3. Porosity:
- 문제입니다: Small internal voids or pores within the printed material. Porosity degrades mechanical properties, particularly ductility, fatigue strength, and fracture toughness – critical for reliable aerospace components.
- Causes:
- 가스 다공성: Trapped shielding gas (e.g., Argon in L-PBF) within the melt pool due to instability or contamination.
- 키홀 다공성: Caused by excessive energy density creating unstable, deep melt pools that collapse and trap gas.
- 융합 부족 다공성: Insufficient energy density leading to incomplete melting between layers or scan tracks.
- Powder Quality Issues: Entrained gas within powder particles, poor powder packing due to irregular morphology or incorrect particle size distribution.
- Solutions:
- Rigorous Process Parameter Optimization: Developing stable parameter sets (power, speed, layer thickness, hatch spacing) validated through extensive testing (e.g., creating and analyzing density cubes).
- High-Quality Powder: 사용 중 금속 분말 with high sphericity, low internal gas content, controlled PSD, and minimal satellites (like those produced by Met3dp) ensures good flowability, packing density, and consistent melting. Proper powder handling and storage to prevent moisture/gas pickup is essential.
- Effective Shielding Gas Flow: Ensuring proper laminar flow of inert gas in L-PBF systems to remove fumes without disturbing the melt pool.
- 열간 등방성 프레싱(HIP): Very effective at closing gas and lack-of-fusion porosity, significantly improving material integrity. Often mandatory for critical Class A aerospace parts.
4. Support Removal Difficulties & Surface Imperfections:
- 문제입니다: Supports that are difficult or impossible to remove without damaging the part surface, or leaving significant witness marks that require extensive finishing. Internal supports in complex channels pose particular challenges.
- Causes: Overly dense supports, poor accessibility designed into the part, fragile part features near supports.
- Solutions:
- DfAM for Supports: Designing parts to be self-supporting where possible, orienting to minimize support needs, ensuring physical access for removal tools.
- Optimized Support Design: Using specialized support generation software to create structures that are strong enough during the build but easier to remove (e.g., smaller contact points, perforated structures, material-specific support strategies).
- Advanced Removal Techniques: Exploring wire EDM, electrochemical machining, or specialized tooling for challenging supports.
- Surface Finish Planning: Accepting that support contact points will be rougher and planning for necessary finishing steps (grinding, blending, machining).
5. Powder Management and Safety:
- 문제입니다: Risk of cross-contamination between different alloys, powder degradation over time (oxidation, moisture absorption), and safety hazards associated with handling fine, potentially reactive metal powders (especially Aluminum and Titanium).
- Causes: Inadequate procedures, poor storage conditions, lack of specialized equipment.
- Solutions:
- Strict Procedures: Implementing rigorous protocols for machine cleaning between builds with different alloys, dedicated powder handling equipment (sieves, hoppers, storage containers) per material family.
- Controlled Environment: Storing powders in sealed containers with desiccants or under inert gas. Managing humidity in the production environment. Regular powder testing (chemistry, PSD, flowability).
- Safety Measures: Proper grounding of equipment to prevent static discharge, use of appropriate PPE (respirators, conductive clothing), inert atmosphere handling for reactive powders, ATEX-rated vacuum cleaners, operator training on safe handling procedures and emergency response (e.g., Class D fire extinguishers for metal fires).
- Reliable Powder Supply: Sourcing consistently high-quality powders from reputable suppliers like Met3dp minimizes variability and potential degradation issues.
6. Achieving Consistent Material Properties:
- 문제입니다: Ensuring that mechanical properties (strength, ductility, fatigue life) are consistent across a single build, between different builds, and between different machines. Critical for certification and reliability.
- Causes: Variations in process parameters, machine calibration drift, inconsistent powder feedstock, slight differences in thermal history within a build.
- Solutions:
- Robust Process Development & Validation: Thoroughly developing and locking down process parameters for each material/machine combination.
- Machine Calibration & Maintenance: Strict adherence to scheduled calibration and preventative maintenance routines.
- Consistent Powder Quality: Using powder from qualified suppliers with tight quality controls and managing batches effectively.
- Witness Coupons: Including standardized test specimens (witness coupons) within each build platform for mechanical testing (tensile, fatigue) and microstructural analysis to verify properties for each production run.
- Statistical Process Control (SPC): Monitoring key process variables and output characteristics to ensure stability and detect drift over time.
Partnering to Overcome Challenges: Navigating these potential hurdles requires expertise, robust equipment, high-quality materials, and established processes. This is where partnering with a company like Met3dp provides significant value. Our commitment extends beyond just selling printers and powders; we aim to be a reliable AM supplier and partner. Our industry-leading printers are designed for stability and consistency. Our advanced 금속 분말 are manufactured under stringent quality controls to minimize material-related issues. Furthermore, our technical expertise allows us to support customers in process development, DfAM, and troubleshooting, helping them successfully implement 금속 3D 프린팅 for demanding 항공우주 제조 다음과 같은 애플리케이션 satellite panels and ensuring they achieve the required quality and reliability for their B2B manufacturing solutions.
Choosing Your Partner: Selecting the Right Metal AM Service Provider for Aerospace Components
The decision to leverage 금속 적층 제조 for critical components like satellite panels is significant. Equally important is the selection of the right partner to bring these designs to life. Whether you are seeking a metal 3D printing service bureau to produce parts or considering bringing the technology in-house by purchasing equipment and materials, choosing a supplier is a strategic decision that goes far beyond just comparing price quotes. For demanding 항공우주 제조, where reliability, precision, and traceability are non-negotiable, partnering with a capable, experienced, and trustworthy organization is paramount. Evaluating potential AM suppliers requires a thorough assessment of their capabilities, experience, and quality systems.
Here are key criteria for procurement managers 및 engineering teams to consider when selecting a 금속 AM partner for 항공우주 부품:
1. Aerospace Experience and Certifications:
- Proven Track Record: Has the supplier successfully produced components for other aerospace clients? Can they provide case studies or references (within NDA constraints)? Experience with similar applications (structural parts, thermal components, etc.) is highly valuable.
- Relevant Certifications: Is the supplier certified to aerospace quality standards, primarily AS9100? While not all AM providers hold this yet, having it (or demonstrating a clear path towards it) indicates a mature Quality Management System suitable for aerospace requirements. ISO 9001 is a minimum baseline. Understanding of specific customer or agency requirements (e.g., NASA, ESA standards) is also beneficial.
- Documentation & Traceability: Are they familiar with the rigorous documentation package typically required for flight hardware, including material certifications, build logs, process parameters, NDT reports, and certificates of conformance?
2. Material Expertise and Qualification:
- 특정 합금 경험: Do they have deep expertise in processing the specific lightweight alloys you require (AlSi10Mg, 스칼말로이®, Ti-6Al-4V다음을 포함합니다. 23등급 ELI)? Can they demonstrate consistent, optimized material properties for these alloys printed on their machines?
- Powder Quality Control: How do they source, test, handle, and store their 금속 분말? What measures do they take to prevent cross-contamination and degradation? Do they have traceability for powder batches? (This aligns with Met3dp’s core strength in producing high-quality, traceable powders).
- Material Qualification Process: Do they have established processes for qualifying materials and parameters on their machines to ensure repeatable results that meet aerospace specifications?
3. Equipment Capabilities, Condition, and Capacity:
- Appropriate Technology: Do they operate the right type of AM technology (e.g., L-PBF, EBM) best suited for your material and application?
- Machine Specifications: Are their machines well-maintained and regularly calibrated? Do they have appropriate build volumes to accommodate the size of your satellite panels? Do they utilize machines known for reliability and precision (like those offered by Met3dp)?
- Capacity and Redundancy: Do they have sufficient machine capacity to meet your required lead times, even considering potential maintenance or other projects? Do they have multiple machines capable of running your part to provide redundancy?
4. Technical and DfAM Support:
- Design for Additive Manufacturing (DfAM) Expertise: Can their engineering team provide valuable input on optimizing your panel design for AM? This includes topology optimization, lattice structures, support strategy, orientation planning, and feature design for manufacturability and post-processing.
- Application Engineering: Do they have skilled application engineers who understand both the AM process and the demands of aerospace applications? Can they collaborate effectively with your design team? (Met3dp offers comprehensive application development services).
- 문제 해결: Do they have a track record of effectively troubleshooting and resolving potential build issues?
5. Comprehensive Post-Processing Capabilities:
- Integrated Workflow: Does the supplier offer critical 후처리 steps in-house (e.g., stress relief, heat treatment, basic finishing), or do they manage a network of qualified partners for services like HIP, precision CNC machining, specialized NDT, and coating?
- 프로세스 제어: How do they manage and control the quality of these external post-processing steps if applicable? Understanding the entire process chain is vital.
- 전문성: Do they understand the specific requirements for post-processing aerospace-grade AM parts (e.g., specific heat treatment cycles for Ti-6Al-4V, NDT standards)?
6. Robust Quality Management System (QMS):
- 프로세스 제어: Does their QMS encompass rigorous controls over all stages – design review, build preparation, machine operation, material handling, post-processing, inspection, and documentation?
- Traceability: Can they provide end-to-end traceability, linking the final part back to the specific machine, build parameters, operator, powder batch, and all post-processing and inspection records? This is non-negotiable for flight hardware.
- 검사 기능: Do they have calibrated inspection equipment (CMM, 3D scanners, NDT equipment or access) and trained personnel to verify parts meet all specifications?
7. Confidentiality and Intellectual Property (IP) Protection:
- Security Measures: What procedures and systems do they have in place to protect your sensitive design data and intellectual property? Ensure robust Non-Disclosure Agreements (NDAs) are executed.
8. Communication, Responsiveness, and Location:
- Collaboration: Are they easy to communicate with and responsive to technical questions and project updates? A collaborative relationship is key.
- Logistics: Consider the implications of their location on shipping times, costs, and the feasibility of site visits or audits.
Checklist: Key Questions for Potential AM Suppliers
범주 | Questions to Ask |
---|---|
Aerospace Credentials | What is your experience with aerospace projects? Are you AS9100 certified? How do you handle flight hardware documentation & traceability? |
재료 전문성 | Which specific alloys (AlSi10Mg, Scalmalloy®, Ti-6Al-4V Gr 5/23) do you process regularly? How do you qualify/control powder quality & properties? |
장비 및 용량 | What types/models of AM machines do you operate? What are their build volumes? How is maintenance/calibration handled? What is your capacity? |
기술 지원 | Do you offer DfAM consultation? Who provides technical support? Can you share examples of collaborative design optimization? |
포스트 프로세싱 | Which post-processing steps do you perform in-house vs. outsource? How do you qualify/manage external suppliers? |
Quality & Traceability | Can you describe your QMS? How do you ensure full part traceability? What inspection/NDT methods do you utilize? |
Confidentiality | What measures are in place to protect customer IP and design data? |
Communication/Logistics | Who is the primary point of contact? What are typical communication protocols? What are standard lead times (subject to project details)? |
시트로 내보내기
Bringing AM In-House with Met3dp: For organizations considering establishing or expanding their own 금속 AM capabilities for strategic reasons (e.g., high volume, rapid iteration needs, maximum control), selecting the right equipment and material supplier is crucial. Met3dp stands out as an ideal partner in this scenario. We provide not just industry-leading metal 3D printers known for their reliability, accuracy, and large build volumes, but also the 고품질 금속 분말 essential for producing consistent, aerospace-grade components. Crucially, we back our technology with comprehensive training, application development support, and responsive service, empowering our customers to successfully implement and scale 금속 적층 제조 다음과 같은 까다로운 애플리케이션을 위한 satellite panels. Choosing Met3dp is an investment in a complete, reliable AM ecosystem.
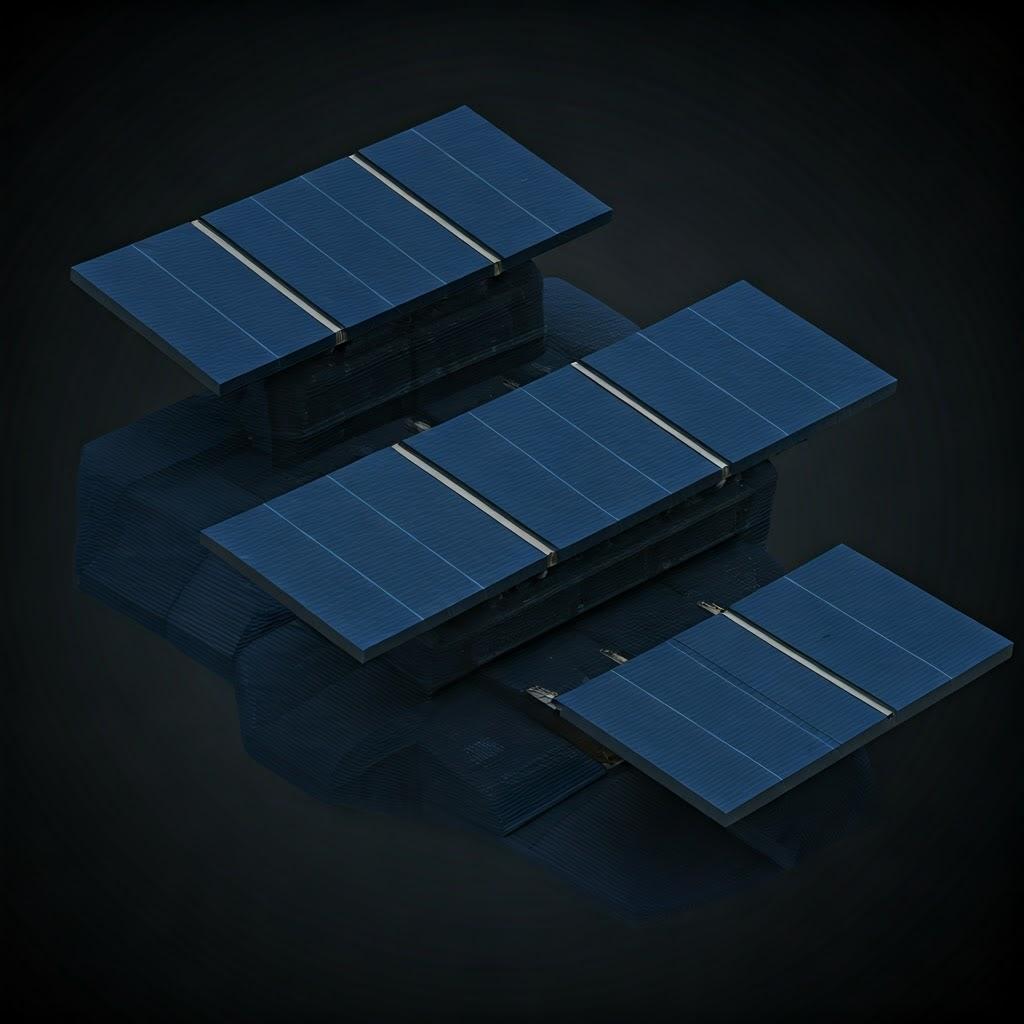
Budgeting for Innovation: Understanding Cost Factors and Lead Times for 3D Printed Panels
Additive manufacturing offers transformative potential, but adopting it for components like satellite panels requires a clear understanding of the associated costs and timelines. While AM can lead to significant savings in areas like launch cost (due to lightweighting) and assembly labor (due to part consolidation), the production cost of the AM part itself is driven by a complex interplay of factors throughout the entire workflow. B2B procurement specialists and engineers need to look beyond just the price per part and consider the total cost of ownership and value proposition.
Deconstructing the Cost of Metal AM Satellite Panels:
The final price tag on a 3D printed satellite panel is influenced by far more than just the raw material consumed. Key cost drivers include:
- 재료비:
- 파우더 가격: 고성능 aerospace alloys vary significantly in price (€/kg), with Ti-6Al-4V generally being the most expensive, followed by 스칼말로이®, and then AlSi10Mg.
- Material Consumption: This includes the volume of the final part 플러스 the volume of support structures required during the build. Efficient DfAM and support strategies minimize this.
- Powder Recycling/Loss: While unfused powder can often be sieved and reused, there are limits to refresh cycles, and some material is inevitably lost during handling and processing. This efficiency factor impacts overall material cost.
- AM Machine Operations:
- Machine Depreciation: Industrial metal AM systems represent a significant capital investment, and their cost needs to be amortized over the parts produced.
- 구축 시간: A major driver. Calculated based on the number of layers (part height) multiplied by the time per layer (determined by scanning area and parameters). Larger, taller, or more complex parts take longer. Efficient nesting of multiple parts on a build plate can improve throughput but might increase build height.
- Consumables & Utilities: Cost of inert gas (Argon, Nitrogen), electricity (machines and auxiliary equipment like chillers), filters, recoater blades, etc.
- Preparation and Setup Labor:
- 사전 처리: Engineering time for DfAM review, build simulation (thermal, stress), orientation optimization, support structure generation, and slicing the CAD file into machine instructions.
- Machine Setup: Operator time for loading the build file, preparing the build plate, loading powder, and initiating the build process.
- Post-Processing Costs (Often >50% of Total Cost):
- Thermal Treatments: Cost of furnace time, energy, and inert gas for stress relief, HIP, and/or solution annealing/aging cycles. HIP is particularly energy and time-intensive.
- Part/Support Removal: Labor time for cutting parts from the build plate and manually or mechanically removing support structures. Can be significant for complex parts with extensive supports.
- CNC 가공: Costs associated with fixture design/fabrication, programming CNC toolpaths, machine setup time, machining time, tooling wear, and skilled machinist labor for achieving tight tolerances on critical features.
- 표면 마감: Labor, equipment time, and consumables for bead blasting, tumbling, polishing, or other finishing methods required to meet surface specifications.
- Inspection & NDT: Significant cost contributor involving expensive equipment (CT scanners, CMMs) and certified personnel time for performing tests and generating detailed reports (required for aerospace).
- Labor (Skilled Personnel):
- Costs associated with trained AM machine operators, application engineers, post-processing technicians, quality inspectors, and project managers involved throughout the workflow.
- Quality Assurance & Documentation:
- Overhead costs associated with maintaining a robust QMS (e.g., AS9100), performing calibrations, managing documentation, and ensuring full traceability.
리드 타임에 영향을 미치는 요인:
The time it takes from design finalization to receiving a flight-ready satellite panel is similarly complex:
- Design Iteration & Preparation: Time spent on DfAM, simulation, and build file setup (can range from hours to days).
- Machine Queue Time: Availability of suitable AM machines at a service bureau or in-house (can range from days to weeks, depending on demand).
- AM Build Time: Pure printing time (can range from hours for small parts to many days for large, complex panels or full build plates).
- Post-Processing Pipeline: This is often the longest and most variable part of the lead time.
- Thermal treatments (Stress relief, HIP, Heat Treat): Each step can take 1-3 days including heating/cooling cycles.
- Logistics: Time required to move parts between different processing steps (e.g., from printer to heat treater to machine shop to NDT lab), especially if involving external suppliers.
- Support Removal & Machining: Depends heavily on complexity (can range from hours to days per part).
- Finishing & Inspection: Can add several more days.
- Qualification & Documentation: Time for final review, documentation compilation, and sign-off.
Typical Lead Times: For a moderately complex aerospace part requiring multiple post-processing steps, total lead times of 4 to 10 weeks are common, though this can vary significantly.
Obtaining Accurate Estimates: To get reliable cost and lead time estimates when submitting a Request for Quote (RFQ), provide potential suppliers with:
- 3D CAD model (STEP format preferred).
- 2D drawings with clear GD&T, critical dimensions, and surface finish requirements.
- Specified material (including grade, e.g., Ti-6Al-4V Grade 23).
- Required heat treatments (Stress Relief, HIP, Annealing, etc.).
- NDT requirements (e.g., CT scanning class/resolution, FPI standard).
- Required quantity and delivery date.
- Any applicable specifications or standards (e.g., AS9100 compliance).
Engaging with experienced AM suppliers 같은 Met3dp (for equipment/materials/support) or qualified service bureaus early in the design process allows for DfAM input that can optimize not only performance and weight but also potentially reduce build time and post-processing complexity, leading to better control over additive manufacturing pricing and timelines. Our reliable equipment and consistent powders also contribute to more predictable build cycles and quality outcomes, reducing costly rework or delays in the demanding aerospace manufacturing economics landscape.
Frequently Asked Questions (FAQ) about 3D Printing Satellite Panels
Here are answers to some common questions engineers and procurement managers have about using metal additive manufacturing for satellite panels:
Q1: How does the strength of 3D printed satellite panels compare to traditionally manufactured ones? A: When produced correctly, metal AM satellite panels can exhibit mechanical properties that meet or even exceed those of traditional cast or wrought counterparts, especially when considering specific strength (strength-to-weight ratio). Key factors include:
- Alloy Choice: Using high-performance alloys like 스칼말로이® 또는 Ti-6Al-4V.
- 프로세스 최적화: Ensuring dense, defect-free parts through optimized print parameters.
- 후처리: Implementing appropriate heat treatments (like stress relief, solution annealing/aging) and HIP(열간 등방성 프레싱), which is crucial for closing internal porosity and maximizing fatigue life and ductility, often making AM parts comparable to wrought materials.
- 디자인: Leveraging 토폴로지 최적화 및 격자 구조 allows AM parts to be significantly lighter while providing equivalent stiffness and strength for specific load cases. It’s important to note that AM parts can exhibit some anisotropy (properties varying slightly with build direction), which must be accounted for during design and testing phases.
Q2: Are 3D printed metal parts like satellite panels readily certifiable for space flight? A: 예, 3D printed metal components are increasingly being certified and flown on satellites and launch vehicles, but it requires a rigorous and well-documented qualification process. Certification isn’t automatic; it involves:
- Process Stability: Demonstrating a stable, repeatable, and statistically controlled manufacturing process (printing parameters, powder handling, post-processing).
- Material Characterization: Extensive testing of material properties (tensile, fatigue, fracture toughness, etc.) using witness coupons from multiple builds to establish reliable design allowables.
- 비파괴 검사(NDT): Thorough inspection (often including CT scanning for internal quality) to verify part integrity and absence of critical defects.
- Traceability & Documentation: Maintaining meticulous records linking the final part to all process steps, material batches, and inspection results.
- Adherence to Standards: Following established aerospace guidelines (e.g., NASA-STD-6016, ESA’s ECSS standards, or specific customer requirements). Partnering with suppliers experienced in aerospace qualification protocols significantly streamlines this process.
Q3: What are the main advantages of using Scalmalloy® over Ti-6Al-4V for satellite panels, or vice versa? A: The choice between these two excellent aerospace alloys depends heavily on the specific requirements of the satellite panel:
- Choose Scalmalloy® When:
- Maximum Lightweighting is Priority: Its density is ~40% lower than Ti-6Al-4V, offering significant weight savings.
- Operating Temperatures are Moderate: Performs well up to ~150-200°C.
- High Specific Strength is Needed: Its strength-to-weight ratio rivals Titanium alloys in many cases.
- Machinability/Print Speed is a Factor: Generally easier and faster to print and machine than Titanium.
- Choose Ti-6Al-4V When:
- Elevated Temperatures are Expected: Maintains excellent strength up to ~350°C or higher.
- Exceptional Corrosion Resistance is Required: Titanium is highly inert.
- Maximum Absolute Strength, Stiffness, or Damage Tolerance is Critical: Especially Grade 23 ELI offers superior fracture toughness.
- Proven Flight Heritage is Desired: Titanium alloys have a longer history in space applications.
- Higher Density is Acceptable due to performance needs outweighing weight considerations.
- Summary: 스칼말로이® excels for lightweight structural applications at moderate temperatures, while Ti-6Al-4V is the choice for higher temperatures, maximum durability, and extreme environments.
Q4: Can complex internal features like cooling channels be reliably printed and cleaned? A: Yes, creating complex internal channels is a key strength of 금속 적층 제조. However, reliability hinges on proper design and process control:
- Design for Manufacturability: Channels need sufficient diameter (typically >1-2 mm, depending on length/complexity) to allow unfused powder to be removed. Smooth, sweeping bends are better than sharp corners. Incorporating access ports for cleaning and inspection can be beneficial. Using self-draining geometries like TPMS lattices can also help.
- Powder Removal: Thorough cleaning protocols involving vibration, compressed air, and potentially solvent flushing are essential after printing.
- Verification: CT scanning is often used as an NDT method to confirm that channels are fully cleared of powder and meet dimensional specifications before the panel is put into service. With careful DfAM and post-processing, highly efficient and conformally cooled satellite panels can be reliably produced using AM.
Conclusion: Launching the Future – The Enduring Value of Metal AM for Satellite Manufacturing
The journey through the intricacies of 3D printing satellite panels reveals a technology that is far more than just a novelty; 금속 적층 제조 represents a fundamental enabler for the next generation of aerospace innovation. By offering unprecedented capabilities in 경량화, 부품 통합및 디자인의 자유, AM directly addresses the core drivers of modern satellite development: reducing launch costs, increasing payload capacity and functionality, and accelerating deployment timelines.
The ability to utilize advanced lightweight alloys 같은 AlSi10Mg, the high-performance 스칼말로이®, and the space-proven Ti-6Al-4V, combined with optimized designs born from DfAM principles like 토폴로지 최적화 및 격자 구조, allows engineers to create satellite panels that are lighter, stronger, and more functionally integrated than ever before. While the path involves careful consideration of process parameters, rigorous 후처리 including heat treatments like HIP, and thorough 품질 보증 및 NDT, the results are increasingly proving essential for competitive satellite platforms.
Successfully navigating this advanced manufacturing landscape requires more than just technology; it requires expertise and reliable partnerships. Choosing the right AM supplier – one with proven 항공우주 experience, deep material expertise, robust equipment, comprehensive support, and a commitment to quality and traceability – is critical.
Met3dp stands at the forefront of this technological wave, providing the foundational elements required for success. Our industry-leading metal 3D printers, engineered for precision and reliability, combined with our meticulously produced 고품질 금속 분말, form the bedrock of consistent and performant additive manufacturing. Beyond the technology, our commitment to application development support ensures our partners can fully leverage the potential of AM for their most demanding applications.
As the space industry continues its rapid expansion, driven by constellations, exploration missions, and commercial ventures, the role of 금속 적층 제조 will only grow. It offers the agility, performance enhancements, and potential for supply chain resilience needed to build the future in orbit.
Ready to explore how metal AM can revolutionize your satellite manufacturing? 연락처 Met3dp today to learn more about our comprehensive solutions – from advanced SEBM printers and high-performance powders to expert application support – and discover how we can help launch your organization’s additive manufacturing goals. Visit us at https://met3dp.com/ to begin the conversation.
공유
중국 칭다오에 본사를 둔 선도적인 적층 제조 솔루션 제공업체인 MET3DP Technology Co. 당사는 산업용 3D 프린팅 장비와 고성능 금속 분말을 전문으로 합니다.
관련 기사
Met3DP 소개
최근 업데이트
제품
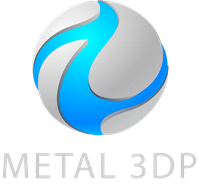
3D 프린팅 및 적층 제조용 금속 분말