유체 시스템을 위한 금속 3D 프린팅의 복잡한 매니폴드
목차
Introduction: Revolutionizing Fluid Control with Metal 3D Printed Industrial Manifolds
The landscape of industrial fluid control is undergoing a significant transformation, driven by the disruptive capabilities of 금속 적층 제조(AM), commonly known as metal 3D 프린팅. At the heart of this revolution lies the potential to reimagine components like industrial manifolds – the central hubs directing flow in hydraulic, pneumatic, and other fluid systems. Traditionally manufactured through subtractive methods like CNC machining or casting, manifolds often face limitations in terms of geometric complexity, weight, potential leak paths, and production lead times, especially for custom manifold designs or low-to-medium volume requirements sought by B2B manufacturing clients.
Metal 3D printing fundamentally changes the paradigm. By building parts layer by layer directly from metal powder, AM unlocks unprecedented 디자인의 자유, enabling the creation of manifolds with highly complex internal geometries, optimized flow paths, and integrated functionalities previously impossible or prohibitively expensive to achieve. This capability is not just an incremental improvement; it’s a step-change allowing engineers in aerospace, automotive, medical, and industrial sectors to design more efficient, compact, and reliable fluid control systems.
Imagine consolidating multiple components into a single, 3D printed manifold, eliminating numerous connection points – common sources of leaks and assembly complexity. Picture internal channels curved and blended perfectly to minimize pressure drop and turbulence, enhancing overall system performance. Consider the rapid prototyping and production of custom manifold blocks tailored precisely to specific application needs, drastically reducing development cycles. These are no longer futuristic concepts but tangible benefits being realized today through metal AM solutions.
For procurement managers and engineers seeking wholesale manifold suppliers 또는 B2B manufacturing partners, understanding the potential of metal 3D printing is crucial. It offers a pathway to enhanced performance, reduced system complexity, lighter components (critical in aerospace and automotive), and potentially faster time-to-market. Companies like Met3dp, specializing in both advanced metal 3D printing equipment and high-performance 금속 분말, are at the forefront, providing the technology and expertise needed to leverage additive manufacturing for demanding fluid power applications. This article serves as a comprehensive guide for technical and procurement professionals exploring the application of metal 3D printing for producing complex, high-performance industrial manifolds. We will delve into the uses, advantages, material considerations, design principles, quality aspects, and supplier selection criteria pertinent to adopting this transformative technology for your fluid system components.
What are Industrial Manifolds and Their Critical Functions?
Before exploring the advantages of additive manufacturing, it’s essential to understand the fundamental role of industrial manifolds. In essence, an industrial manifold is a engineered block, typically made of metal or sometimes polymer, designed to consolidate and direct the flow of fluids (liquids or gases) within a system. Think of it as the central “junction box” or “control center” for fluid power. Instead of connecting various valves, regulators, gauges, and actuators with a complex web of individual pipes, tubes, and fittings, these components are mounted directly onto or integrated within the manifold block. Internal passages within the manifold then route the fluid between these components and to the various output ports connected to the wider system.
Key Functions and Roles:
- Fluid Distribution and Regulation: The primary function is to distribute fluid from a single source (like a pump or compressor) to multiple circuits or actuators, and potentially collect return flow. Valves mounted on the manifold control the direction, pressure, and flow rate to each circuit.
- System Consolidation and Simplification: By housing multiple fluid control components and their interconnections within a single block, manifolds drastically reduce the number of external connections. This minimizes potential leak points, simplifies system assembly, reduces installation time, and saves valuable space.
- Centralized Control Point: Manifolds provide a convenient and organized location for mounting control valves, sensors, and test points, making system operation, monitoring, and maintenance easier.
- Integration of Logic: ~ 안에 hydraulic manifolds 및 pneumatic manifolds, the internal passages and valve arrangements create specific fluid logic circuits (e.g., sequencing operations, safety interlocks).
Common Types and Applications:
Manifolds are ubiquitous across numerous industries, tailored to specific needs:
- Hydraulic Manifolds:
- Function: Control high-pressure hydraulic fluid (typically oil) to power actuators like cylinders and motors.
- 산업: Industrial machinery (presses, injection molding machines), mobile equipment (construction, agriculture), aerospace fluid systems (landing gear, flight controls), automotive (power steering, transmission control).
- 특성: Robust construction to handle high pressures (often thousands of PSI), complex internal pathways, mounting interfaces for standard hydraulic valves (e.g., CETOP, ISO standards). Many OEM manifold applications demand custom designs.
- Pneumatic Manifolds:
- Function: Distribute compressed air to control pneumatic actuators (cylinders, grippers), valves, and tools.
- 산업: Industrial automation components (factory assembly lines, robotics, packaging machinery), medical devices, process control.
- 특성: Typically operate at lower pressures than hydraulics, often made from aluminum or engineered plastics, focus on fast response times and compact design.
- Fluid Distribution Blocks:
- Function: Simpler designs primarily focused on splitting or combining fluid flows with minimal control elements integrated directly. Used for coolant distribution, lubrication systems, chemical processing.
- 산업: Automotive (coolant systems), manufacturing (machine tool cooling), chemical processing, oil & gas fluid control.
- Instrumentation Manifolds:
- Function: Used to isolate, bleed, and calibrate pressure instruments (gauges, transmitters) connected to a process line, often featuring 2-valve, 3-valve, or 5-valve configurations.
- 산업: Process industries (oil & gas, chemical, power generation), laboratory equipment.
Traditional Manufacturing Constraints:
Conventionally, manifolds are produced using subtractive techniques:
- 가공: Drilling and milling ports and passages into a solid block of metal (steel, aluminum, ductile iron) or sometimes plastic. This often involves drilling from multiple faces, requiring plugs to seal off cross-drilled access holes – potential leak points. Complex internal curves are impossible; passages are typically straight lines with sharp intersections, which can cause turbulence and pressure drops.
- 캐스팅: Creating a near-net shape through casting, followed by machining critical surfaces and ports. While potentially reducing machining time for complex external shapes, internal passage complexity remains limited.
These traditional methods impose limitations, particularly when engineers require:
- Highly intricate internal flow paths for optimal performance.
- Significant weight reduction without compromising strength.
- Consolidation of numerous functions into a very compact space.
- Rapid prototyping or low-volume production of custom designs.
It is precisely these limitations that metal additive manufacturing effectively overcomes, positioning it as a compelling alternative for wholesale manifold production 및 custom fluid circuit requirements, especially for demanding OEM manifold applications where performance and integration are paramount. Understanding these core functions and traditional constraints highlights the opportunities presented by adopting 금속 3D 프린팅 서비스.
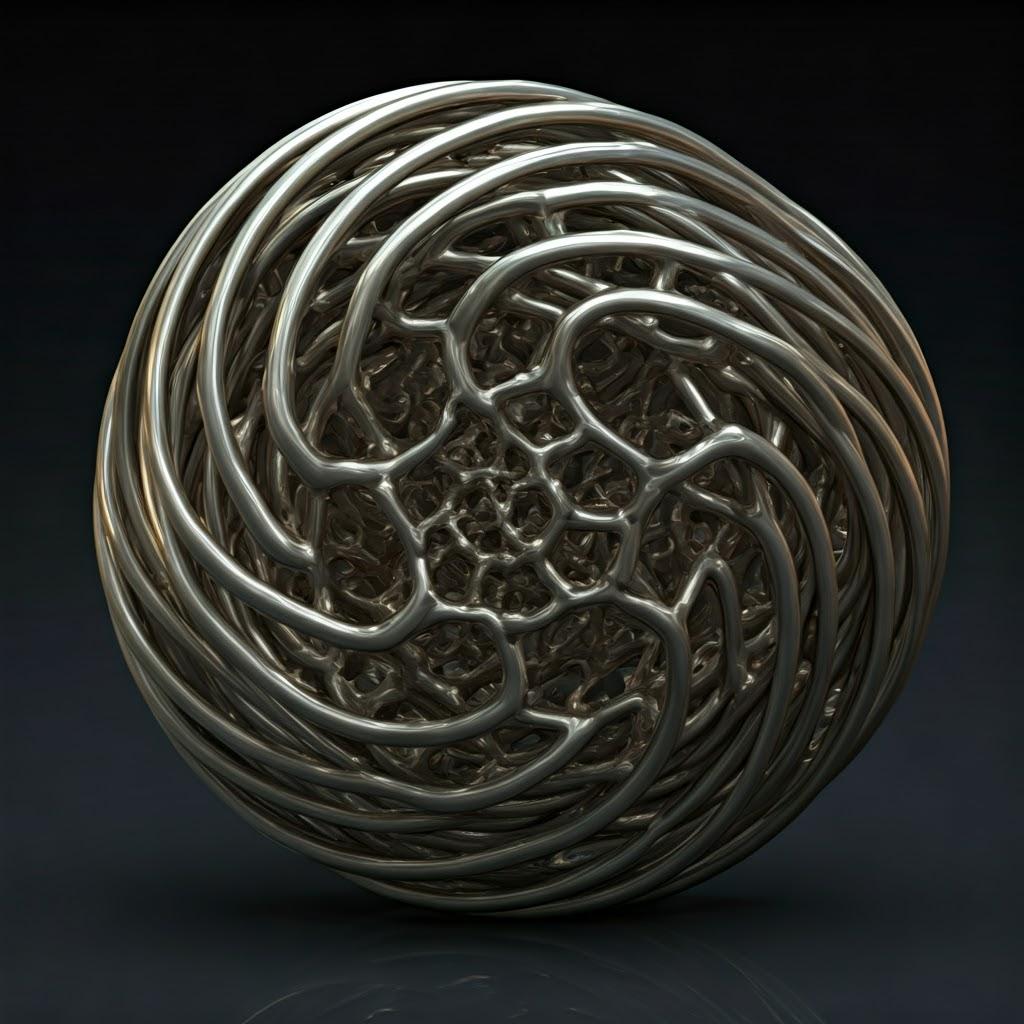
Why Choose Metal Additive Manufacturing for Complex Manifolds?
The decision for engineers and procurement managers to adopt metal additive manufacturing (AM) for industrial manifolds stems from a compelling set of advantages over traditional subtractive methods, particularly when dealing with complex designs, demanding performance requirements, or specific logistical needs. For B2B manufacturing clients 및 wholesale manifold suppliers, metal AM offers transformative potential across the entire product lifecycle.
1. Unprecedented Design Freedom and Geometric Complexity:
- Organic and Optimized Flow Paths: Unlike machined manifolds limited to straight drilled holes and sharp angles, AM allows for smooth, curved, and variable-diameter internal channels. This minimizes turbulence, reduces pressure drop, and significantly improves fluid dynamic efficiency, leading to better system performance and potentially lower energy consumption. Think of internal passages designed using computational fluid dynamics (CFD) for perfect flow, printed directly.
- 토폴로지 최적화: Algorithms can be used to remove material from low-stress areas while maintaining structural integrity, resulting in significantly lighter manifolds without sacrificing strength or pressure rating. This is crucial for weight-sensitive applications like aerospace, automotive, and robotics.
- Internal Features: Complex internal features like integrated filters, baffles, venturis, or heat exchangers can be designed and built directly into the manifold structure, something unachievable with drilling alone.
2. Part Consolidation and System Simplification:
- Reducing Component Count: Multiple individual components (e.g., fittings, connectors, brackets, separate valve blocks) can often be integrated into a single, monolithic 3D printed manifold.
- Eliminating Leak Paths: Every joint, fitting, or plug in a traditional manifold system is a potential leak point. Consolidation drastically reduces the number of seals and connections, significantly improving system reliability and reducing maintenance needs. This is a major selling point for OEM manifold solutions.
- Simplified Assembly: Fewer parts mean faster and simpler system assembly, reducing labor costs and potential assembly errors.
3. Lightweighting:
- 재료 효율성: Additive manufacturing uses material only where needed. Combined with topology optimization, weight reductions of 50% or more compared to traditionally machined blocks are achievable, while maintaining or even improving performance.
- Impact: Reduced weight translates to fuel savings in mobile applications (aerospace, automotive), lower inertia in moving parts (robotics), and easier handling and installation.
4. Accelerated Prototyping and Reduced Lead Times (Especially for Custom/Low Volume):
- 신속한 반복: Design modifications can be implemented and new prototypes printed in days rather than weeks or months, accelerating the development cycle for custom manifold designs.
- Tooling Elimination: AM requires no specific tooling (molds, jigs, fixtures) like casting or complex machining setups. This makes it highly cost-effective for producing prototypes, low-volume batches, or highly customized parts requested by industrial component distributors.
- 주문형 생산: Facilitates digital inventory and on-demand manufacturing, reducing the need for large physical inventories, particularly relevant for spare parts or specialized fluid power component suppliers.
5. Enhanced Performance:
- Improved Flow Efficiency: As mentioned, optimized internal channels lead to lower pressure drops and more efficient fluid transfer.
- 열 관리: AM allows for the integration of conformal cooling channels or heat-dissipating structures directly within the manifold body, improving thermal management for demanding applications.
6. Material Options:
- High-Performance Alloys: Metal AM processes can utilize a wide range of high-performance alloys (like Stainless Steels, Nickel Superalloys, Aluminum alloys, Titanium alloys) tailored to specific requirements such as corrosion resistance, high temperature strength, or chemical compatibility. Companies like Met3dp offer specialized powders optimized for these demanding applications.
Comparison Table: Traditional vs. Metal AM for Manifolds
기능 | Traditional Manufacturing (Machining/Casting) | Metal Additive Manufacturing (e.g., LPBF/SLM) | Key Benefit of AM |
---|---|---|---|
Internal Geometry | Limited to straight lines, sharp angles | Complex curves, organic shapes, variable dia. | Optimized flow, reduced pressure drop |
부품 통합 | Difficult, requires multiple components | High potential to integrate multiple parts | Fewer leak points, simpler assembly, reduced weight |
무게 | Often bulky, optimization limited | Significant lightweighting via topology opt. | Fuel efficiency, lower inertia, easier handling |
자유로운 디자인 | Constrained by tooling & process | Near-limitless geometric freedom | Innovation, enhanced functionality |
Lead Time (Custom) | Weeks/Months (tooling, setup) | Days/Weeks (no tooling) | Faster prototyping, quicker time-to-market |
툴링 비용 | Can be high, especially for low volumes | 없음 | Cost-effective for custom/low volume |
Potential Leak Points | Numerous (plugs, fittings, seals) | Minimal (due to consolidation) | Improved reliability, reduced maintenance |
재료 낭비 | High (subtractive process) | 낮음(첨가 공정) | More sustainable, lower raw material input per part |
이상적인 볼륨 | High volume production | Prototypes, low-to-medium volume, custom | Flexibility in production scale |
시트로 내보내기
While traditional methods remain suitable for very high-volume production of simple manifold designs, 금속 적층 제조 provides unparalleled advantages for complex, high-performance, customized, or weight-critical manifolds. For businesses seeking advanced fluid control solutions and reliable manifold manufacturers, partnering with an experienced metal 3D printing service provider like Met3dp opens doors to innovation and competitive advantage in demanding markets like aerospace, automotive, and industrial automation.
Material Selection for 3D Printed Manifolds: 316L, IN625, AlSi10Mg Explored
Choosing the right material is paramount to the success of any 3D printed industrial manifold. The material dictates the component’s mechanical properties, corrosion resistance, weight, temperature tolerance, and ultimately, its suitability for the specific fluid system application. While metal additive manufacturing supports a growing range of alloys, three commonly recommended powders stand out for many manifold applications: 스테인리스 스틸 316L, Nickel Alloy IN625 (Inconel 625)및 알루미늄 합금 AlSi10Mg. Understanding their properties helps engineers and procurement managers make informed decisions when specifying requirements for metal AM service bureaus.
1. 스테인리스 스틸 316L:
- 설명: 316L is an austenitic chromium-nickel stainless steel containing molybdenum. The “L” denotes low carbon content, which improves weldability and reduces sensitization (chromium carbide precipitation) during processes like 3D printing, enhancing corrosion resistance, particularly in chloride environments.
- 주요 속성:
- 뛰어난 내식성: Highly resistant to general corrosion, pitting, and crevice corrosion in various industrial environments, including moderate chloride exposure, chemicals, and marine atmospheres. Ideal for water, many chemicals, and food-grade applications.
- Good Strength and Ductility: Offers a good balance of tensile strength, yield strength, and elongation, making it tough and durable.
- Good Weldability & Printability: Generally prints well using Laser Powder Bed Fusion (LPBF/SLM) techniques, resulting in dense parts.
- 생체 적합성: Can be used in certain medical applications (though specific certifications are required).
- 적당한 비용: Relatively cost-effective compared to nickel superalloys or titanium.
- Typical Manifold Applications: Hydraulic systems using standard hydraulic fluids, pneumatic systems (especially in corrosive environments), chemical processing manifolds, food and beverage processing, water treatment systems, marine applications.
- 고려 사항: Lower strength-to-weight ratio compared to aluminum or titanium. Maximum operating temperature is generally lower than IN625.
2. Nickel Alloy IN625 (Inconel® 625):
- 설명: IN625 is a nickel-chromium-molybdenum-niobium superalloy known for its exceptional strength, corrosion resistance, and performance at extreme temperatures.
- 주요 속성:
- 뛰어난 내식성: Superior resistance to a wide range of severely corrosive environments, including high chloride media (seawater), acids (sulfuric, phosphoric, nitric), and alkaline solutions. Excellent resistance to pitting, crevice corrosion, and intergranular attack.
- High Strength at Elevated Temperatures: Maintains significant strength and toughness from cryogenic temperatures up to ~815°C (1500°F) and beyond for certain applications. Excellent fatigue and creep resistance.
- Excellent Fabricability & Printability: Prints well with LPBF, achieving high density and good mechanical properties in the as-built and heat-treated states.
- Typical Manifold Applications: High-pressure hydraulic systems operating in harsh chemical or high-temperature environments, aerospace fluid systems (fuel lines, hydraulics near engines), oil & gas fluid control (downhole tools, subsea equipment), chemical processing involving aggressive media, marine applications requiring superior saltwater resistance, heat exchanger manifolds.
- 고려 사항: Higher material cost compared to 316L or AlSi10Mg. Higher density than aluminum or titanium. Requires specific post-processing (heat treatments) to achieve optimal properties.
3. Aluminum Alloy AlSi10Mg:
- 설명: AlSi10Mg is a widely used aluminum casting alloy known for its good strength-to-weight ratio, excellent thermal conductivity, and good printability in AM processes. The silicon content improves fluidity during melting, while magnesium allows for strengthening via heat treatment (precipitation hardening).
- 주요 속성:
- 뛰어난 무게 대비 강도 비율: Significantly lighter than steel or nickel alloys, making it ideal for lightweighting manifolds in weight-sensitive applications.
- Good Thermal Conductivity: Useful for applications where heat dissipation from the manifold or the fluid is important.
- Good Corrosion Resistance (in specific environments): Performs well in atmospheric conditions and with certain fluids, but less resistant than 316L or IN625 in aggressive chemical or marine environments.
- 우수한 인쇄성: One of the most common and well-understood aluminum alloys for LPBF.
- 비용 절감: Generally less expensive than stainless steel or nickel alloys.
- Typical Manifold Applications: Automotive hydraulics and thermal management systems (coolant manifolds), aerospace components where weight saving is critical (but environmental conditions are less severe), robotics, industrial automation (especially pneumatic systems), heat sinks or thermally active manifolds.
- 고려 사항: Lower absolute strength and temperature resistance compared to 316L and IN625. Requires appropriate surface treatment (e.g., anodizing) if enhanced corrosion or wear resistance is needed. Susceptible to galvanic corrosion if paired with dissimilar metals.
Material Selection Summary Table:
속성 | 스테인리스 스틸 316L | Nickel Alloy IN625 | 알루미늄 AlSi10Mg | Primary Driver |
---|---|---|---|---|
내식성 | Excellent (General) | Outstanding (Severe) | Good (Specific Env.) | Environment, Fluid Type |
Strength @ Room Temp | 양호 | 매우 좋음 | 양호 | Pressure Rating, Mechanical Loads |
Strength @ High Temp | 보통 | 우수 | Poor | 작동 온도 |
Density / Weight | 높음 | 매우 높음 | 낮음 | Weight Sensitivity (Aerospace, Auto, Robotics) |
열 전도성 | 낮음 | 보통 | 높음 | Heat Dissipation Needs |
상대적 비용 | Medium | 높음 | 낮음-중간 | 예산 제약 |
Primary Advantage | Balanced Properties | Extreme Environments | 경량 | Key Performance Indicator |
시트로 내보내기
The Role of the Metal Powder Supplier:
The quality of the final printed manifold is heavily dependent on the quality of the metal powder used. Characteristics like particle size distribution (PSD), sphericity, flowability, and chemical purity directly impact the printing process stability and the final part’s density, microstructure, and mechanical properties. Partnering with a reputable 금속 분말 공급업체 같은 Met3dp is crucial. Met3dp utilizes industry-leading gas atomization and PREP technologies to produce 고품질 금속 분말, including alloys like 316L, IN625, and AlSi10Mg, specifically optimized for laser powder bed fusion processes. Their expertise ensures consistent powder quality, batch-to-batch traceability, and powders tailored for achieving dense, high-performance metal parts, giving confidence to 도매 구매자 및 OEMs relying on AM for critical components like industrial manifolds. Explore Met3dp’s metal powder offerings to understand the range available for your specific application needs.
Ultimately, the optimal material choice involves a trade-off analysis based on the specific operating conditions (pressure, temperature, fluid type, external environment), performance requirements (strength, weight), and budget constraints. Consulting with experienced application engineers at a knowledgeable metal 3D printing service provider is highly recommended to select the most suitable powder for your complex manifold application.
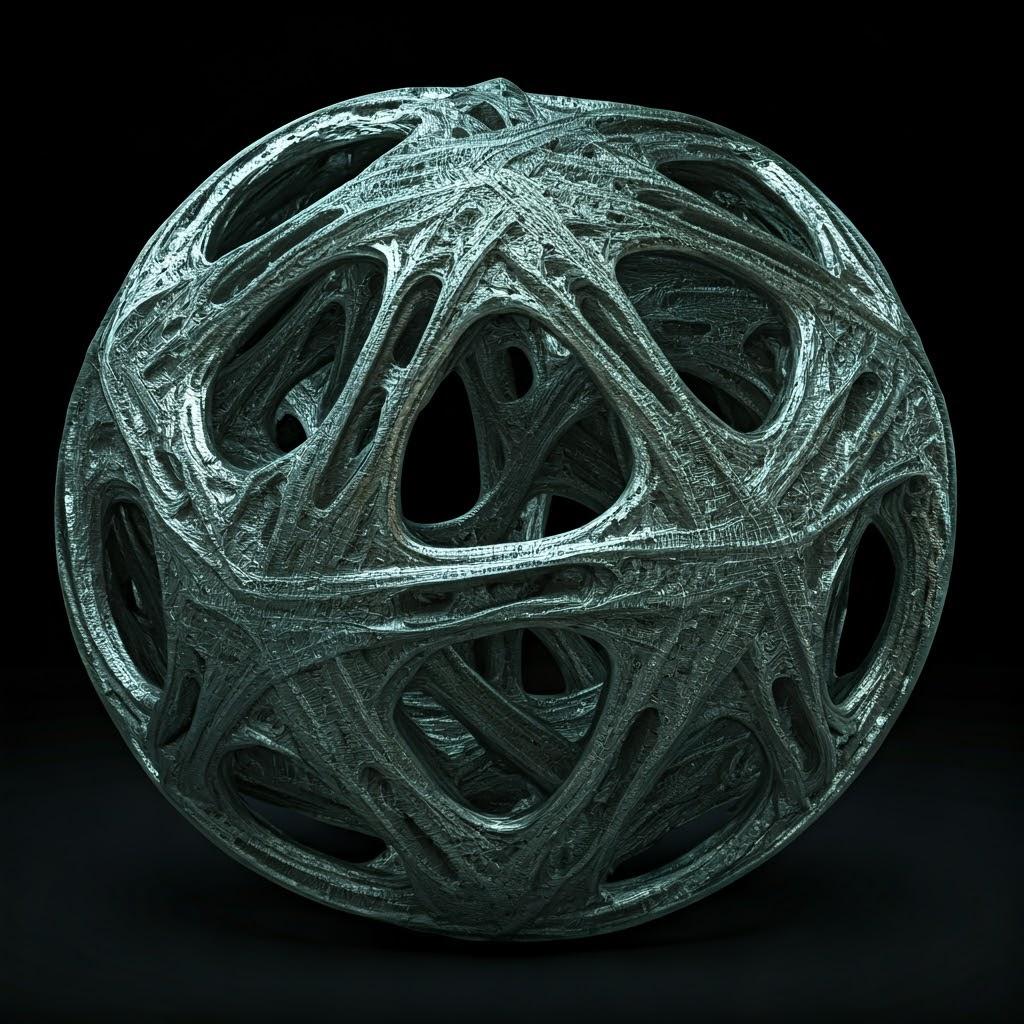
Design for Additive Manufacturing (DfAM) Principles for Optimal Manifold Performance
Simply replicating a manifold design originally intended for machining or casting often fails to leverage the true potential of metal additive manufacturing. To unlock the significant benefits in performance, weight, and consolidation, engineers must embrace 적층 제조를 위한 설계(DfAM) principles. DfAM involves rethinking the component’s architecture from the ground up, considering the unique capabilities and constraints of the layer-by-layer building process. For custom manifold design and achieving superior fluid dynamics, DfAM is not just recommended; it’s essential. Applying these principles is key for OEM manifold solutions aiming for peak performance and efficiency.
Key DfAM Principles for Metal AM Manifolds:
- Optimize Internal Flow Paths:
- Smooth Curves and Blends: Eliminate the sharp 90-degree turns inherent in drilled passages. Replace them with smooth, sweeping bends and blended intersections designed using Computational Fluid Dynamics (CFD) analysis. This drastically reduces turbulence, minimizes pressure drop across the manifold, and improves overall fluid flow efficiency.
- Variable Cross-Sections: Channel diameters can be varied smoothly along their length to precisely control flow velocity or pressure according to system requirements.
- Teardrop/Diamond Shapes for Horizontal Channels: Avoid large, unsupported flat internal “ceilings” which require extensive internal supports that are difficult or impossible to remove. Designing horizontal channels with self-supporting geometries like teardrops or diamonds minimizes the need for internal supports.
- Minimize and Optimize Support Structures:
- 자립 각도: Design features to adhere to the “45-degree rule” (or the specific angle limit for the chosen material/machine combination) wherever possible. Surfaces angled above this threshold relative to the build plate typically do not require support structures.
- 파트 오리엔테이션: Carefully consider the part’s orientation on the build plate during the design phase. Orienting the manifold strategically can minimize the volume of support needed, reduce print time, improve surface finish on critical faces, and make support removal easier. This often involves trade-offs between support volume, surface quality, and potential distortion.
- Accessible Supports: When supports are unavoidable (e.g., for overhangs below the self-supporting angle, large holes parallel to the build plate), design them to be accessible for easy removal during post-processing. Avoid trapping supports in enclosed internal cavities unless they are designed to remain (e.g., as lattice structures) or soluble support materials are used (less common in metal AM).
- Integration of Sacrificial Features: Sometimes, small features can be added specifically to support a critical area during the build, which are then easily machined away later.
- Part Consolidation Strategy:
- Identify Integration Opportunities: Analyze the existing fluid system assembly. Can brackets, sensor mounts, adjacent valve blocks, or sections of tubing be integrated directly into the manifold body?
- Redesign Interfaces: Ensure that integrating parts doesn’t compromise accessibility for assembly, maintenance, or connection of external components. Design integrated features with appropriate tolerances and access points.
- Wall Thickness Considerations:
- Minimum Wall Thickness: Adhere to minimum printable wall thickness guidelines for the specific material and AM process (often around 0.4-1.0 mm, but varies). Thin walls may warp, fail to print reliably, or lack sufficient strength.
- Uniformity (Where Possible): While variable thickness is a benefit, large, abrupt changes can sometimes lead to thermal stresses. Aim for smoother transitions where feasible. Ensure walls are thick enough to withstand operating pressures and mechanical loads, considering safety factors.
- Topology Optimization for Lightweighting:
- Load Path Analysis: Use Finite Element Analysis (FEA) to understand the stress distribution within the manifold under operating conditions (pressure, mounting forces, vibration).
- Material Removal: Employ topology optimization software to iteratively remove material from low-stress regions, creating organic, load-bearing structures that significantly reduce weight while meeting performance requirements. The resulting complex geometries are often only manufacturable via AM.
- Feature Resolution and Accuracy:
- Small Features: Understand the minimum feature size (holes, pins, slots) that can be reliably produced by the chosen AM process and material. Very small or intricate details may require post-machining for accuracy.
- Threads and Sealing Surfaces: While threads can sometimes be printed directly, they often lack the required precision and surface finish. It’s generally recommended to design holes to be tapped or critical sealing surfaces (like O-ring grooves or flange faces) to be finish-machined after printing for optimal performance and reliability.
- Embrace Complex Geometries:
- Internal Structures: Design internal baffles, mixers, flow straighteners, or even integrated heat exchange channels (like conformal cooling) directly into the manifold body to enhance functionality beyond simple fluid routing.
- External Features: Integrate mounting points, identification tags, or unique external shapes optimized for packaging within tight system constraints.
Benefits of Applying DfAM:
DfAM Principle Applied | Resulting Benefit for Manifold | Impact on B2B Value Chain |
---|---|---|
Optimized Flow Paths | Lower pressure drop, higher efficiency, reduced energy consumption | Enhanced system performance for OEM products |
Minimized Support Structures | Reduced post-processing time/cost, potentially better surfaces | Faster lead times, lower cost per part for wholesale buyers |
부품 통합 | Fewer parts, fewer leak points, simpler assembly, lower weight | Improved reliability, reduced assembly cost, better logistics |
토폴로지 최적화 | Significant weight reduction | Competitive advantage in weight-sensitive markets (Aero/Auto) |
Wall Thickness Control | Structural integrity, printability | Reliable components meeting specifications |
Machining Allowances | Achieves critical tolerances/finishes | Functionally reliable parts, reduced quality escapes |
Integrated Features | Enhanced functionality, reduced system complexity | Innovative product offerings, higher value components |
시트로 내보내기
Implementing DfAM effectively requires close collaboration between design engineers and the 금속 AM 서비스 제공업체. Leveraging the expertise of companies like Met3dp, who understand the nuances of various 금속 3D 프린팅 방법 like Selective Electron Beam Melting (SEBM) and Laser Powder Bed Fusion (LPBF), is crucial. Their experience with different materials, machine capabilities, and post-processing techniques informs the design process, ensuring the final manifold is not only innovative but also manufacturable, functional, and cost-effective. By adopting a DfAM mindset, businesses can truly harness the transformative power of additive manufacturing for creating next-generation industrial manifolds.
Achievable Tolerances, Surface Finish, and Dimensional Accuracy in Metal AM Manifolds
A critical consideration for engineers and procurement managers evaluating metal 3D printing for industrial manifolds is understanding the achievable levels of precision. While AM offers incredible geometric freedom, it’s important to have realistic expectations regarding dimensional tolerances, surface finish (roughness), and overall accuracy, both in the “as-built” state and after potential post-processing steps. These factors directly impact the manifold’s ability to seal properly, interface correctly with other components, and function reliably. Supplier quality standards and process control are key to achieving consistent results.
Dimensional Tolerances:
- As-Built Tolerances: For typical Laser Powder Bed Fusion (LPBF/SLM) processes used for materials like 316L, IN625, and AlSi10Mg, general dimensional tolerances are often in the range of ±0.1 mm to ±0.2 mm (±0.004″ to ±0.008″) for smaller features (e.g., up to 100 mm), potentially increasing slightly for larger dimensions due to thermal effects across the build. Some providers might claim tighter general tolerances (e.g., ±0.05 mm) with highly calibrated machines and optimized processes, but this should be confirmed for specific geometries and features.
- Factors Influencing Tolerance:
- 머신 보정: Accuracy of the laser/electron beam positioning system, scanner calibration.
- 프로세스 매개변수: Laser power, scan speed, layer thickness, hatch spacing.
- 머티리얼 속성: Thermal expansion coefficient, shrinkage during cooling.
- Thermal Stresses: Internal stresses built up during the layer-wise melting and solidification can cause warping or distortion, affecting final dimensions. Build strategy and support structures play a role here.
- Part Geometry and Size: Larger parts and complex geometries are generally more prone to deviation.
- Critical Dimensions: For features requiring tighter tolerances than the general process capability (e.g., valve mounting interfaces, port locations, sealing surfaces), post-machining is almost always necessary. It’s crucial to identify these critical dimensions on drawings and incorporate machining allowances (extra stock material, typically 0.5 mm to 1.0 mm or more) in the AM design.
표면 마감(거칠기):
- As-Built Surface Roughness (Ra): The surface finish of metal AM parts is inherently rougher than machined surfaces due to the layer-wise construction and partially melted powder particles adhering to the surface. The roughness varies significantly depending on the surface orientation relative to the build direction:
- Upward-Facing Surfaces (Up-skins): Generally smoother, often in the range of Ra 6-15 µm (240-600 µin).
- Vertical Walls: Moderate roughness, typically Ra 8-20 µm (320-800 µin).
- Downward-Facing Surfaces (Down-skins) & Supported Areas: Significantly rougher due to the necessary support structures or the nature of printing overhangs. Can range from Ra 15 µm to over 30 µm (600-1200+ µin). Supports leave witness marks upon removal.
- 내부 채널: Roughness depends on orientation and whether supports were needed. Can be challenging to improve significantly without specialized post-processing.
- Factors Influencing Roughness:
- 레이어 두께: Thinner layers generally produce smoother surfaces but increase print time.
- 파우더 입자 크기: Finer powders can lead to smoother finishes but may pose challenges in flowability and handling.
- 프로세스 매개변수: Scan strategy, beam offset.
- 파트 오리엔테이션: As described above, orientation is a major factor.
- Achieving Smoother Finishes: If the as-built roughness is insufficient for the application (e.g., for sealing surfaces, reducing friction in flow paths, aesthetics), post-processing methods are required. Options include:
- CNC 가공: Provides the best control for achieving smooth, precise surfaces on specific features (Ra < 1 µm possible).
- Bead Blasting/Shot Peening: Provides a uniform matte finish, cleans the surface, and can impart compressive stress but only moderately improves Ra (e.g., Ra 5-10 µm).
- 텀블링/진동 마감: Can smooth external surfaces and edges, especially for smaller parts (Ra 2-6 µm achievable).
- Polishing/Lapping: Manual or automated polishing for achieving very smooth, mirror-like finishes on accessible surfaces (Ra < 0.1 µm possible).
- 전기 연마: Electrochemical process that removes a thin layer of material, smoothing peaks and valleys, improving corrosion resistance, and providing a bright finish (can reach Ra < 1 µm). Effective but requires handling chemicals.
치수 정확도:
- 정의: Refers to how closely the printed part conforms to the nominal dimensions specified in the CAD model. It encompasses both tolerance (deviation from nominal) and geometric form (flatness, circularity, parallelism).
- Achieving Accuracy: Requires a combination of:
- Well-Maintained Equipment: Regularly calibrated printers.
- Optimized Process Parameters: Developed specifically for the material and machine.
- Effective Thermal Management: Strategies during the build (e.g., preheating, scan strategy) and post-build (stress relief heat treatment) to minimize distortion.
- Careful Support Strategy: Properly designed supports help anchor the part and prevent warping.
- Quality Control & Inspection: Using tools like CMM (Coordinate Measuring Machines), 3D scanners, or CT scanning (for internal features) to verify dimensional accuracy against the design intent.
Summary Table: Precision Expectations
매개변수 | As-Built (Typical LPBF) | Post-Processed (Method Dependent) | 주요 고려 사항 |
---|---|---|---|
허용 오차 | ±0.1 to ±0.2 mm (General) | < ±0.025 mm (Machining) | Identify critical dimensions, design for machining |
Surface Finish (Ra) | 6-30+ µm (Orientation Dep.) | < 1 µm to 10 µm | Application needs (sealing, flow), post-process cost |
Internal Channels | Ra 10-30+ µm, may need support | Difficult to improve significantly | DfAM for smooth flow, consider flow friction |
Small Features | Limited by beam spot/layer | Machining for high precision | Define minimum feature size requirements |
Overall Accuracy | Good, but affected by thermal | High (with machining) | Process control, heat treatment, inspection vital |
시트로 내보내기
When engaging with a metal 3D printing service provider, it’s crucial to clearly define the required tolerances, surface finishes, and critical features for your industrial manifold. Discussing these requirements early allows the provider to select the appropriate process parameters, plan necessary post-processing steps, and establish suitable quality control measures. Reputable providers focused on 정밀 엔지니어링 will work with you to ensure the final manifold meets the necessary 치수 안정성 and functional requirements for demanding applications in aerospace, medical, or industrial automation.
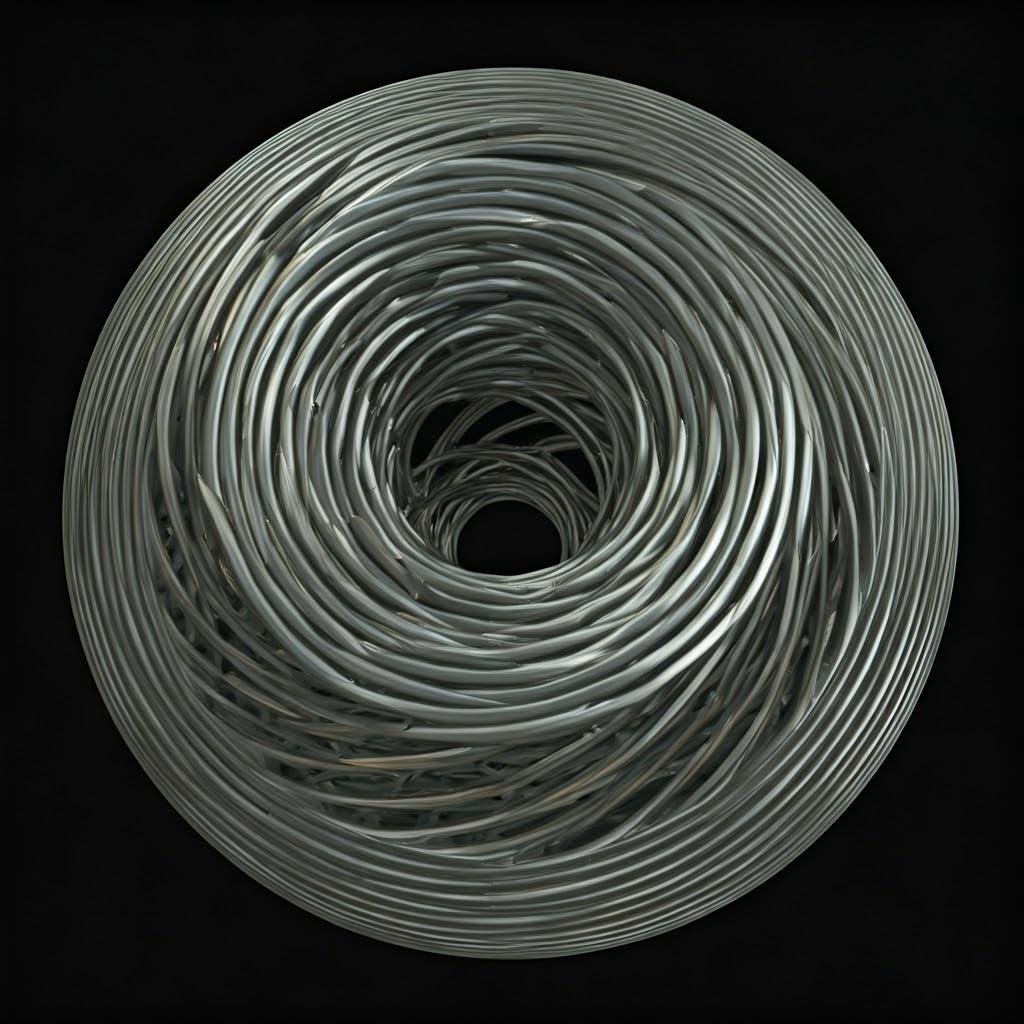
Essential Post-Processing Steps for Functional Metal 3D Printed Manifolds
Producing a complex industrial manifold using metal additive manufacturing doesn’t end when the printer stops. The “green” part emerging from the machine requires a series of crucial post-processing steps to transform it into a functional, reliable component ready for integration into a fluid system. Understanding these steps is vital for engineers designing the part and for procurement managers factoring in total cost and lead time when working with AM service bureaus. The specific sequence and necessity of these steps depend on the material, application requirements, and chosen AM technology.
Common Post-Processing Workflow for Metal AM Manifolds:
- De-Powdering:
- Objective: Remove the bulk of the loose, unfused metal powder surrounding the part(s) within the build chamber.
- 방법: Typically involves manual brushing, vacuuming, or using compressed air/inert gas blow-off within a controlled environment (powder handling station) to recover unused powder for potential recycling. Automated de-powdering systems are also emerging.
- Importance: Thorough powder removal is critical, especially from internal channels, to prevent contamination and ensure proper function. Complex internal geometries can make this challenging.
- 스트레스 완화 열처리:
- Objective: Relieve internal stresses built up during the rapid heating and cooling cycles inherent in the layer-by-layer AM process. These stresses can cause distortion or cracking, especially after the part is removed from the build plate.
- 방법: Heating the part (often while still attached to the build plate) in a furnace with a controlled atmosphere (vacuum or inert gas like Argon) to a specific temperature (below the material’s aging or solution annealing temperature), holding it for a set duration, and then cooling slowly. Parameters vary significantly based on the alloy (e.g., ~650°C for IN625, ~300°C for AlSi10Mg, ~500-800°C range for 316L depending on goals).
- Importance: Essential for dimensional stability during subsequent steps (like removal from build plate and machining) and for long-term component reliability. Required for nearly all metal AM parts, especially those with complex geometries or demanding applications.
- Removal from Build Plate:
- Objective: Separate the printed manifold(s) from the metal base plate they were built upon.
- 방법: Commonly done using wire EDM (Electrical Discharge Machining) or band sawing. Machining can also be used.
- Importance: Requires careful handling to avoid damaging the parts. The separation method choice can depend on part geometry and required precision at the base.
- 지원 구조 제거:
- Objective: Remove the temporary support structures required during the build process for overhangs and angled features.
- 방법: Can range from manual breaking/clipping (for easily accessible, light supports) to more involved methods like CNC machining, grinding, or EDM, especially for dense or hard-to-reach supports. DfAM plays a huge role here – well-designed supports are easier to remove.
- Importance: Supports must be removed cleanly without damaging the part surface. Witness marks where supports were attached are common and may require further finishing. Support removal strategies must be considered during the design phase.
- Further Heat Treatment (Optional but Common):
- Objective: Optimize the material’s microstructure and mechanical properties (e.g., strength, ductility, hardness, fatigue life) beyond just stress relief.
- 방법: Depends on the alloy and desired properties. Examples include:
- 열간 등방성 프레싱(HIP): Combines high temperature and high pressure (using an inert gas like Argon) to close internal porosity (gas voids, lack-of-fusion defects), significantly improving fatigue life and impact strength. Often specified for critical aerospace or medical parts.
- Solution Annealing & Aging: Used for precipitation-hardenable alloys (like AlSi10Mg, some nickel alloys) to achieve maximum strength. Involves heating to dissolve precipitates, quenching, then aging at a lower temperature to form fine, strengthening precipitates.
- Annealing: Can be used to soften the material, improve ductility, or refine grain structure.
- Importance: Tailors the material properties to meet the specific demands of the manifold’s operating environment. Heat treatment for metal AM parts is a specialized field requiring precise control.
- CNC 가공:
- Objective: Achieve tight tolerances, critical surface finishes, and precise features that cannot be reliably produced by the AM process alone.
- 방법: Using standard CNC milling, drilling, tapping, boring, or turning operations.
- Importance: Essential for:
- Sealing Surfaces: O-ring grooves, flange faces, port connections.
- Critical Tolerances: Valve mounting interfaces, precise port locations, bore diameters.
- Threaded Holes: Tapping holes for standard fittings.
- 표면 마감 개선: On specific functional areas.
- 참고: Requires designing the AM part with sufficient stock material (machining allowance) on the relevant features. Requires careful fixturing of often complex AM shapes.
- Surface Finishing & Cleaning:
- Objective: Improve surface roughness, clean the part, remove contaminants, or prepare for coating.
- 방법: As discussed previously: bead blasting, tumbling, polishing, electropolishing. Followed by thorough cleaning cycles (e.g., ultrasonic cleaning) to remove any machining fluids, blasting media, or residues, especially from internal channels.
- Importance: Ensures cleanliness required for fluid systems, improves aesthetics, and can enhance performance (e.g., smoother flow, better sealing).
- Inspection and Testing:
- Objective: Verify that the finished manifold meets all design specifications and quality requirements.
- 방법:
- 치수 검사: CMM, 3D scanning.
- Visual Inspection: Checking for surface defects.
- Internal Inspection: CT scanning (X-ray computed tomography) is invaluable for non-destructively verifying internal channel integrity, detecting porosity, and measuring internal features.
- Material Certification: Verifying material composition and properties (often via testing coupons printed alongside the parts).
- Manifold Leak Testing: Pressure testing (hydrostatic or pneumatic) to ensure all seals and the manifold body are leak-tight under operating conditions. This is a critical final step for any fluid component.
- Importance: Guarantees the quality, safety, and reliability of the final product delivered to the OEM or end-user.
Post-Processing Considerations Summary:
단계 | 목적 | Typical Necessity | Key Factor |
---|---|---|---|
De-Powdering | Remove loose powder | Always | Thoroughness, internal channels |
스트레스 풀기 | Prevent distortion, stabilize dimensions | Almost Always | Alloy type, thermal cycles |
Build Plate Removal | Separate part from plate | Always | Method (EDM, saw), handling |
지지대 제거 | Remove temporary build supports | Always (if supports used) | Accessibility, DfAM, required finish |
Further Heat Treatment | Optimize mechanical properties, reduce porosity | Often (HIP, Age, Anneal) | Application criticality, material |
CNC 가공 | Achieve tight tolerances & critical finishes | Very Common (Critical Areas) | Tolerances, sealing, threads |
Surface Finish/Cleaning | Improve Ra, clean, prepare for coating/assembly | 공통 | Application needs, internal channels |
Inspection & Testing | Verify quality, dimensions, integrity, function | Always (esp. Leak Testing) | Quality standards, safety, reliability |
시트로 내보내기
Partnering with a vertically integrated service provider or managing a network of qualified suppliers for these diverse post-processing steps is crucial for successfully implementing metal AM for industrial manifolds. The complexity and cost associated with post-processing must be factored into the overall project scope when evaluating metal 3D printing cost estimations.
Addressing Common Challenges in 3D Printing Industrial Manifolds
While metal additive manufacturing offers tremendous advantages for producing complex industrial manifolds, the technology is not without its challenges. Awareness of these potential issues allows engineers, manufacturing partners및 quality assurance teams to implement mitigation strategies proactively, ensuring successful outcomes and reliable components. Overcoming these hurdles often requires deep process expertise and rigorous quality control.
Common Challenges and Mitigation Strategies:
- Warping and Distortion:
- Cause: Uneven heating and cooling during the layer-by-layer process induce internal stresses (residual stress). When the part cools or is removed from the build plate, these stresses can cause it to warp or deviate from the intended geometry. Complex geometries and large parts are more susceptible.
- Mitigation:
- Optimized Build Orientation: Positioning the part to minimize large flat areas parallel to the recoater and distribute thermal mass effectively.
- Robust Support Structures: Designing sufficient supports to anchor the part securely to the build plate and resist deformation forces.
- 프로세스 매개변수 최적화: Fine-tuning laser/beam power, scan speed, and scan strategy (e.g., island scanning) to manage heat input.
- Platform Pre-heating: Used in some processes (like SEBM and some LPBF systems) to reduce thermal gradients.
- 스트레스 완화 열처리: Performing this critical step 전에 removing the part from the build plate helps relax stresses and maintain dimensional stability.
- 다공성:
- Cause: Small voids or pores within the printed material. Can be caused by gas trapped during melting (gas porosity) or incomplete fusion between layers/scan lines (lack-of-fusion porosity). Porosity can degrade mechanical properties (especially fatigue strength) and potentially create leak paths.
- Mitigation:
- Optimized Process Parameters: Ensuring sufficient energy density to fully melt the powder without overheating (which can trap gas). Parameter sets are typically developed per material/machine combination.
- High-Quality Metal Powder: Using powder with consistent spherical morphology, optimized particle size distribution, and low internal gas content. Sourcing from reputable 금속 분말 공급업체 like Met3dp, known for their advanced atomization techniques, is key.
- Controlled Build Atmosphere: Maintaining a high-purity inert gas environment (Argon or Nitrogen) in the build chamber to minimize oxidation and gas pickup.
- 열간 등방성 프레싱(HIP): An effective post-processing step to close internal pores and achieve near-full theoretical density, often required for critical applications.
- Support Structure Removal Difficulties:
- Cause: Supports are necessary but can be difficult, time-consuming, and costly to remove, especially if they are dense, located in internal channels, or made from tough materials like IN625. Improper removal can damage the part surface.
- Mitigation:
- DfAM: Designing for minimal support needs (self-supporting angles, optimal orientation). Designing supports intelligently (e.g., tapered, perforated, strategically placed) for easier access and detachment.
- Specialized Removal Tools/Techniques: Using appropriate tools (hand tools, CNC machining, EDM) based on support design and location.
- Planning Access: Ensuring removal tools can physically reach the support structures. Avoid designing “trapped” supports unless absolutely necessary and accounted for.
- Residual Stress Management:
- Cause: As mentioned, residual stresses are inherent to the process. Even if they don’t cause immediate warping, high residual stresses can negatively impact fatigue life, corrosion resistance, and dimensional stability over time or during machining.
- Mitigation:
- 스트레스 완화 열처리: The primary method for reducing residual stresses to acceptable levels. Timing (before/after build plate removal) and parameters are critical.
- Build Strategy Optimization: Scan strategies and part orientation can influence the magnitude and distribution of stress.
- Process Simulation: Advanced simulation tools can predict stress accumulation, helping optimize build setups.
- Surface Finish Limitations:
- Cause: The layer-wise nature and adherence of partially melted powder inherently limit the as-built surface smoothness, especially on down-skins and supported surfaces. Internal channels are particularly challenging.
- Mitigation:
- Orientation and Parameter Tuning: Optimizing build setup for the best possible as-built finish on critical surfaces.
- 후처리: Utilizing appropriate techniques (machining, blasting, polishing, electropolishing) to achieve the required finish on functional surfaces. Acknowledge that achieving very smooth finishes on complex internal channels can be difficult or impossible.
- DfAM: Design internal channels to minimize the need for supports and promote smoother flow paths (e.g., teardrop shapes).
- Powder Handling and Contamination:
- Cause: Metal powders can be reactive (especially Aluminum, Titanium), pose health hazards if inhaled, and are susceptible to contamination (e.g., moisture, cross-contamination between different alloys). Contamination can severely degrade material properties.
- Mitigation:
- 제어 환경: Using dedicated powder handling stations with appropriate ventilation and grounding.
- Strict Procedures: Implementing rigorous protocols for powder loading, unloading, sieving, storage, and traceability.
- Dedicated Equipment: Using separate equipment (sieves, containers, vacuums) for different material types to prevent cross-contamination.
- Atmospheric Control: Storing reactive powders under inert gas or vacuum.
- Quality Assurance and Consistency:
- Cause: Ensuring consistent part quality (dimensional accuracy, material properties, defect levels) across different builds, machines, and batches requires robust process control and validation.
- Mitigation:
- 프로세스 모니터링: In-situ monitoring of key process parameters (melt pool temperature, layer uniformity) where available.
- Rigorous Qualification: Qualifying machines, materials, and processes according to industry standards (e.g., SAE AMS standards for aerospace).
- 재료 테스트: Testing powder batches and producing witness coupons alongside parts for mechanical property verification.
- 비파괴 검사(NDT): Utilizing CT scanning, radiography, or ultrasonic testing to inspect internal integrity.
- Comprehensive Quality Management System (QMS): Implementing systems like ISO 9001 or AS9100 (for aerospace) ensures procedures are documented, followed, and audited.
Addressing these challenges requires a combination of smart design (DfAM), meticulous process control, appropriate post-processing, and rigorous quality assurance. Partnering with an experienced and well-equipped metal 3D printing service provider is essential. Companies like Met3dp, with decades of collective expertise in metal AM, possess the knowledge and capabilities to navigate these complexities. Their focus on advanced powder manufacturing 및 industry-leading printing technology provides a foundation for producing high-quality, reliable metal AM manifolds, helping clients troubleshoot potential issues and successfully adopt additive manufacturing for demanding fluid system applications.
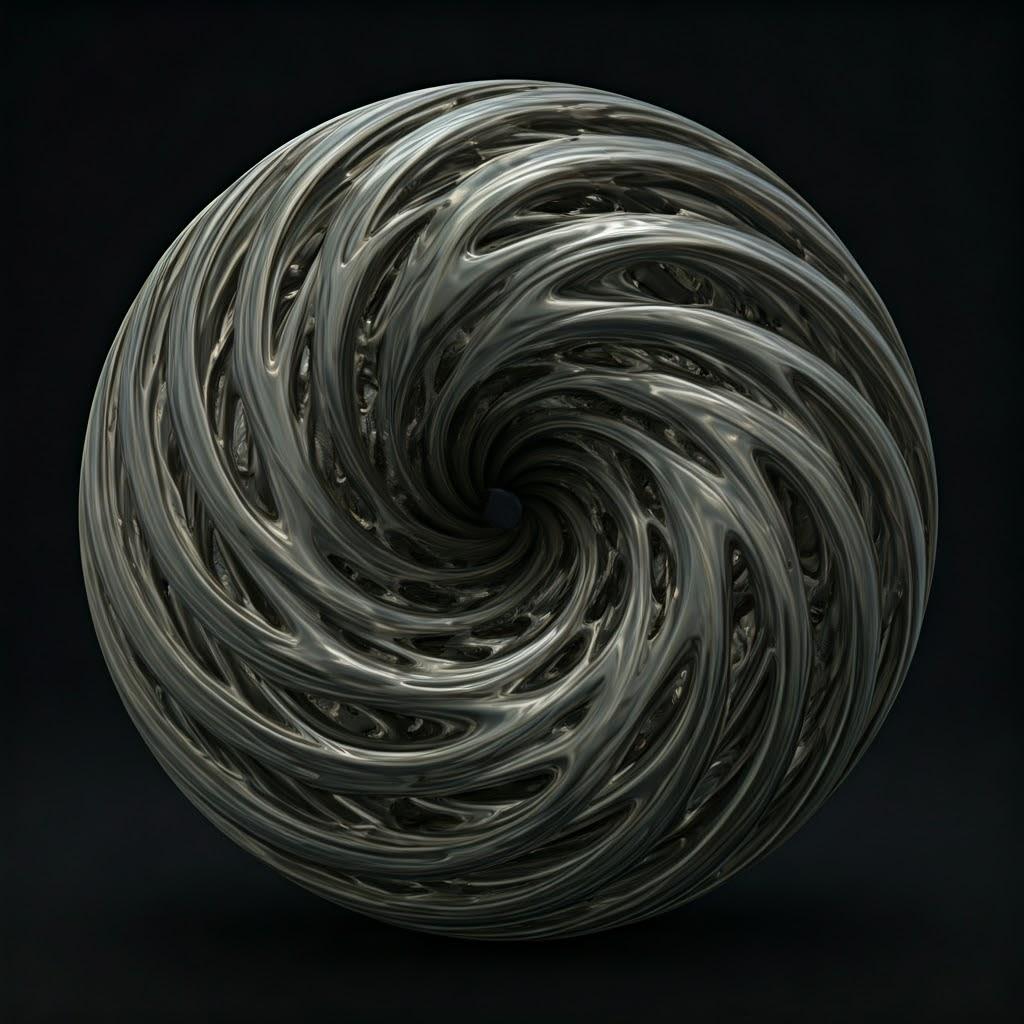
Selecting the Ideal Metal 3D Printing Service Provider for Manifolds
Choosing the right manufacturing partner is as critical as the design itself when implementing metal additive manufacturing for industrial manifolds. The capabilities, expertise, and quality systems of your chosen AM service bureau will directly impact the success of your project, the quality of the final component, and the reliability of your supply chain. For OEMs, industrial component distributors, and engineers seeking wholesale manifold production, evaluating potential suppliers requires looking beyond just price. A true B2B additive manufacturing partner offers comprehensive support and proven capabilities.
Key Criteria for Evaluating Metal AM Service Providers:
- Technical Expertise and Experience:
- Material Knowledge: Do they have deep expertise in processing the specific metal alloys required for your manifold (e.g., 316L, IN625, AlSi10Mg, or others)? Can they advise on material selection trade-offs?
- Process Understanding: Are they proficient in the relevant AM processes (LPBF, SEBM, etc.) and understand the nuances of parameter optimization for density, accuracy, and surface finish?
- DfAM Support: Can they provide constructive feedback on your design to optimize it for additive manufacturing? Do they have application engineers experienced with fluid dynamics, support strategy, and post-processing considerations specifically for manifolds?
- 업계 경험: Have they successfully produced similar components (manifolds, hydraulic blocks, fluid system parts) for your industry (aerospace, automotive, medical, industrial)? Can they provide case studies or references?
- Equipment Capabilities and Capacity:
- Machine Fleet: What types of metal AM machines do they operate? Do they have machines suitable for your required material and part size? Consider the build volume constraints.
- Redundancy and Scalability: Do they have multiple machines capable of running your part? This provides redundancy and capacity for scaling production from prototypes to low or medium series volumes.
- Technology Relevance: Are they using up-to-date, well-maintained industrial-grade equipment?
- Quality Management System and Certifications:
- QMS: Do they operate under a robust Quality Management System? ISO 9001 certification is a fundamental requirement, demonstrating commitment to quality processes and continuous improvement.
- Industry-Specific Certifications: Depending on your application, certifications like AS9100 (Aerospace), ISO 13485 (Medical Devices), or IATF 16949 (Automotive) may be required. These indicate adherence to stringent industry-specific quality standards and traceability requirements.
- 재료 추적성: Can they provide full traceability for metal powders, from the original batch to the final part?
- 프로세스 제어: What measures do they have in place for monitoring and controlling the printing process?
- 검사 기능: Do they have in-house capabilities for dimensional inspection (CMM, 3D scanning), NDT (like CT scanning for internal checks), material testing, and leak testing?
- Post-Processing Capabilities:
- 인하우스 대 아웃소싱: Do they perform critical post-processing steps like heat treatment, support removal, CNC machining, and surface finishing in-house, or do they rely on external suppliers? In-house capabilities generally offer better control over quality, lead time, and communication.
- Range of Services: Can they manage the entire workflow from raw powder to finished, tested manifold? This simplifies the supply chain for the customer.
- Communication and Project Management:
- 응답성: Are they responsive to inquiries and provide clear communication throughout the project?
- 기술 지원: Is there a dedicated point of contact (e.g., project manager or application engineer) for technical discussions?
- Quoting Process: Is their quoting clear, detailed, and timely? Does it outline all included steps and potential variables?
- Cost and Lead Time:
- 경쟁력 있는 가격: While cost shouldn’t be the 오직 factor, pricing should be competitive and transparent. Understand what is included in the quote.
- Reliable Lead Times: Can they provide realistic and reliable lead time estimates for prototypes and production orders? What is their track record for on-time delivery?
- Location and Logistics:
- 해운: Consider shipping costs and transit times, especially for international suppliers.
- Facility Audits: Is it possible to audit their facility to assess their capabilities and quality systems firsthand?
Evaluation Checklist Summary:
Evaluation Area | Key Questions to Ask | Importance Level |
---|---|---|
기술 전문성 | Material knowledge? DfAM support? Industry experience? Process understanding? | 매우 높음 |
Equipment/Capacity | Suitable machines? Build volume? Redundancy? Scalability? Technology age? | 높음 |
Quality & Certs | ISO 9001? Industry-specific certs (AS9100/ISO 13485)? Traceability? Inspection capabilities? QMS robustness? | Very High (Critical) |
포스트 프로세싱 | In-house capabilities (Heat Treat, Machining, Finishing)? Full workflow management? | 높음 |
Communication | Responsiveness? Technical contact? Clear quoting? Project updates? | Medium |
비용 및 리드타임 | Competitive pricing? Transparent quotes? Realistic & reliable lead times? | 높음 |
Location/Logistics | Shipping implications? Audit possibility? | Medium (Depends on needs) |
시트로 내보내기
Selecting a partner like Met3dp can streamline this process significantly. As a company headquartered in Qingdao, China, Met3dp not only provides industry-leading metal 3D printing equipment (like their SEBM systems known for accuracy and reliability) but also possesses deep expertise in 고성능 금속 분말 manufactured using advanced gas atomization and PREP technologies. Their integrated approach, combining machine manufacturing, material science, and application development services, positions them as a comprehensive solution provider. Understanding their specific capabilities, quality commitment, and decades of collective expertise, which you can explore further by learning about Met3dp, gives confidence when sourcing critical components like complex industrial manifolds. Choosing a provider with proven expertise across the entire AM ecosystem minimizes risks and maximizes the potential for success.
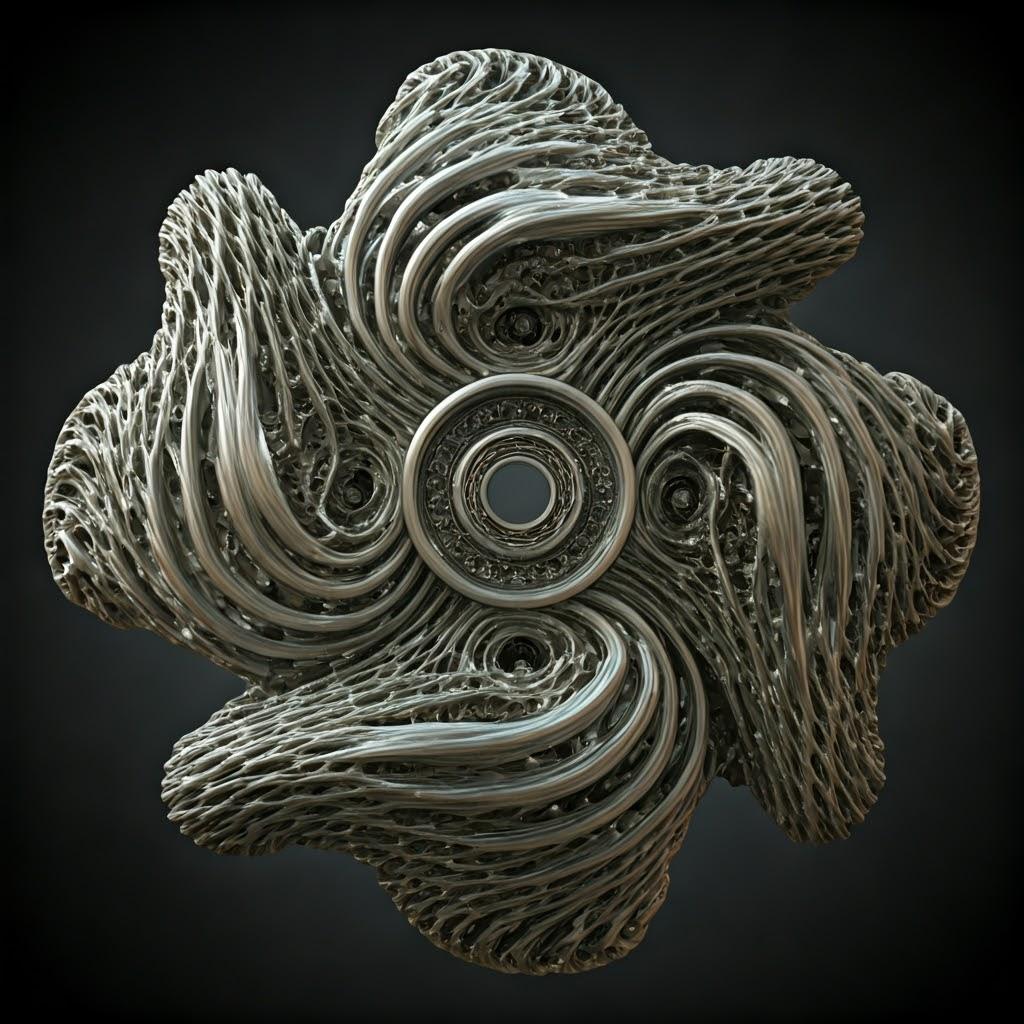
Understanding Cost Drivers and Lead Times for Metal AM Manifolds
For procurement managers and engineers budgeting for projects involving metal 3D printed manifolds, understanding the factors that influence cost and lead time is crucial. Unlike traditional high-volume manufacturing where tooling amortization dominates, metal 3D printing cost estimation is more heavily influenced by material consumption, machine time, and post-processing requirements. Requesting detailed quotes from potential AM service bureaus is always necessary for accurate figures, but knowing the key drivers helps in preliminary planning and design optimization.
Major Cost Drivers for Metal AM Manifolds:
- Material Type and Consumption:
- 파우더 비용: The raw material cost varies significantly between alloys. Common materials like 316L and AlSi10Mg are generally less expensive than high-performance alloys like IN625 or Titanium grades. Powder quality and specifications also impact price.
- Part Volume: The actual volume of the printed part directly correlates to the amount of expensive metal powder consumed. Larger parts cost more.
- 지원 구조 볼륨: Supports also consume material and must be factored in. Designs requiring extensive supports will be more expensive. DfAM principles aimed at minimizing supports directly reduce cost.
- Powder Recycling/Waste: While unused powder can often be sieved and reused, there are limits and handling costs associated with this.
- 머신 시간:
- Build Height (Z-Height): This is often the primary driver of print time. Taller parts take longer to build, regardless of how many parts are on the build plate (within limits).
- Part Complexity & Density: Very intricate features or fully dense sections require more scanning time per layer compared to simpler geometries or parts with internal voids/lattices.
- 레이어 두께: Thinner layers produce better surface finish and resolution but significantly increase the number of layers and thus the total print time.
- 머신 시간당 요금: Service providers factor in the depreciation, maintenance, operation, and overhead costs of expensive industrial metal AM systems into their hourly rates. Rates vary based on machine type and capabilities.
- Post-Processing Intensity:
- 열처리: Costs depend on the type (stress relief vs. HIP vs. full annealing/aging), cycle duration, furnace capacity, and required atmosphere (vacuum, inert gas). HIP is a significant cost addition but may be necessary for critical parts.
- 지원 제거: Labor-intensive manual removal or time on specialized equipment (EDM, CNC) adds cost, particularly for complex or internal supports.
- CNC 가공: Costs depend heavily on the number of features requiring machining, the required tolerances, surface finish specifications, and the complexity of setting up and fixturing the AM part.
- 표면 마감: Costs vary based on the method (blasting is relatively inexpensive, multi-stage polishing or electropolishing is more costly) and the surface area treated.
- Inspection and Testing: Basic dimensional checks are standard, but extensive NDT (like CT scanning) or rigorous leak testing protocols add significant cost.
- Labor and Setup:
- File Preparation: Preparing the CAD file for printing, generating support structures, and creating the build layout requires skilled labor.
- Machine Setup/Teardown: Loading powder, setting up the build, and post-build machine cleaning take time. These costs are often amortized over the parts in a build.
- Manual Post-Processing: Labor for de-powdering, manual support removal, finishing, and handling.
- 주문 수량:
- 규모의 경제: While AM avoids tooling costs, some economies of scale still apply. Setup costs can be amortized over more parts in a larger batch. Fully utilizing a build platform with multiple parts is more cost-effective than printing a single small part.
- Wholesale Pricing Models: Suppliers may offer tiered pricing for larger volume orders or ongoing production agreements.
Typical Lead Time Factors:
Lead time is the duration from order placement to part delivery. For metal AM manifolds, it typically ranges from a few days (for very simple, rapid prototypes) to several weeks or even months for complex parts requiring extensive post-processing and rigorous testing, especially for production quantities.
- Current Machine Backlog: The provider’s current workload and machine availability is often the biggest factor.
- Print Time: Determined by build height, complexity, and layer thickness (can range from hours to many days).
- Post-Processing Duration:
- Heat treatment cycles can take 1-3 days (including ramp-up, soak, cool-down).
- Support removal and machining can take hours to days depending on complexity.
- Finishing processes add further time.
- HIP processing requires scheduling with specialized facilities and adds significant time (often 1-2 weeks).
- Quality Control/Inspection: Time required for dimensional checks, NDT, leak testing.
- 해운: 고객 위치까지의 운송 시간.
Cost & Lead Time Estimation Table:
팩터 | 비용에 미치는 영향 | Impact on Lead Time | Mitigation / Optimization Strategy |
---|---|---|---|
재료 선택 | High (e.g., IN625 > 316L > Al) | Minor | Select material based on actual need, not over-spec |
Part Size/Volume | High (Directly proportional) | Moderate (Taller parts take longer) | DfAM (Topology opt.), minimize bulk |
Support Volume | 보통 | Minor | DfAM (Self-supporting angles, orientation) |
복잡성 | Moderate (Longer scan time) | Moderate (Longer print time) | Simplify non-functional features if possible |
레이어 두께 | Moderate (Thinner = longer time) | High (Thinner = more layers) | Use optimal thickness for required finish/detail |
후처리 요구 사항 | Very High (Machining, HIP, Polish) | Very High (Multiple sequential steps) | DfAM (Minimize supports, design for machining) |
Quality Requirements | High (CT Scan, Extensive Tests) | Moderate (Testing duration) | Specify only necessary inspection levels |
주문 수량 | Moderate (Setup amortization) | High (Larger orders take longer) | Optimize batch sizes, discuss blanket orders |
Supplier Backlog | Indirect (May affect pricing) | High (Queue time) | Plan ahead, communicate needs early |
시트로 내보내기
To get reliable metal 3D printing cost estimations and lead times for your specific manifold design, provide potential suppliers with a detailed 3D CAD model, clear drawings specifying materials, critical tolerances, surface finishes, and required testing/certifications. Engage in technical discussions to ensure all requirements are understood and explore opportunities for optimization.
FAQ: Metal 3D Printed Industrial Manifolds
Here are answers to some 자주 묻는 질문 regarding the use of metal additive manufacturing for industrial manifolds:
1. What pressure ratings can metal 3D printed manifolds typically handle?
Metal AM manifolds can be designed to handle very high pressures, often equivalent to or exceeding those of conventionally machined counterparts made from the same material. The pressure rating depends primarily on:
- 재료 선택: High-strength alloys like IN625 or specific steels naturally handle higher pressures than aluminum alloys.
- Design (Wall Thickness & Geometry): Proper DfAM, including sufficient wall thickness calculated using FEA based on operating pressures and safety factors, is crucial.
- Part Quality (Density): Achieving a dense, defect-free part through optimized printing parameters and potentially HIP is essential for high-pressure integrity.
- 후처리: Proper heat treatment optimizes material strength.
Manifolds for hydraulic systems operating at several hundred bar (thousands of PSI) are commonly produced using metal AM. It’s essential to perform rigorous pressure testing (proof and burst testing, if required) on the final design to validate its performance according to application standards.
2. Are material certifications and traceability available for metal AM manifolds?
Yes, reputable 금속 3D 프린팅 서비스 제공업체 operating under robust quality systems (like ISO 9001, AS9100) can typically provide comprehensive 재료 인증 and traceability. This usually includes:
- Powder Certification: Certificate of Conformance (CoC) from the metal powder supplier detailing the specific batch number, chemical composition, particle size distribution, and other relevant properties.
- Process Traceability: Documentation linking the specific powder batch(es) used to the specific build job and part serial numbers.
- Mechanical Property Testing: Results from tensile tests, hardness tests, or other required tests performed on witness coupons printed alongside the actual parts in the same build job.
- Post-Processing Records: Documentation of heat treatment cycles, machining operations, and inspection results.
Clearly specify your certification and traceability requirements when requesting quotes, especially for regulated industries like aerospace or medical.
3. How does metal AM compare to traditional casting or machining for manifolds in terms of cost and lead time?
The comparison depends heavily on the specific manifold design (complexity) and the required quantity:
- 복잡성:
- AM Excels: For highly complex internal geometries, integrated features, topology-optimized lightweight designs, AM is often the 오직 feasible manufacturing method, or significantly more efficient than extremely complex multi-axis machining and fabrication.
- Traditional Favored: For simple block manifolds with straight drilled holes, traditional machining is typically faster and cheaper, especially at volume.
- 수량:
- AM Favored (Low Volume/Prototypes): AM avoids high upfront tooling costs (casting molds, complex machining fixtures), making it very cost-effective for prototypes, custom parts, and low-volume production (typically < 100-500 units, depending on complexity). Lead times for prototypes are significantly shorter.
- Traditional Favored (High Volume): Once tooling costs are amortized over thousands of units, the per-part cost for casting or high-speed machining of simpler designs becomes lower than AM. Lead times for established high-volume processes can also be very fast.
- Lead Time (First Article): AM is almost always faster for delivering the first functional prototype due to the absence of tooling lead times.
- Overall Value: Consider the total value proposition: AM might enable performance gains (better flow, lighter weight, fewer leaks) that justify a higher per-part cost in certain applications, even at moderate volumes.
비교 요약:
팩터 | 메탈 AM | 캐스팅 | Machining (from Block) |
---|---|---|---|
복잡성 | Very High (Internal & External) | Moderate (External), Low (Internal) | Moderate (External), Low (Internal – Drilled) |
툴링 비용 | 없음 | High (Mold) | Low/Moderate (Fixtures) |
Per-Part Cost (Low Vol) | 보통-높음 | Very High (due to tooling) | High (Machining time) |
Per-Part Cost (High Vol) | 보통-높음 | 낮음 | Low-Moderate |
리드 타임(프로토) | 빠른 | Very Slow (Tooling) | Slow-Moderate |
Lead Time (Prod) | 보통 | Fast (Once tooling exists) | Fast (Optimized setups) |
자유로운 디자인 | 최고 | 보통 | 낮음 |
부품 통합 | 우수 | 제한적 | 제한적 |
경량화 | Excellent (Topology Opt.) | Fair (Near Net Shape) | Poor (Subtractive) |
시트로 내보내기
4. What is the typical Minimum Order Quantity (MOQ) for metal AM manifolds?
의 주요 장점 중 하나는 금속 3D 프린팅 is its suitability for producing single units or very small batches cost-effectively, as there are no tooling costs to amortize. Therefore, the technical MOQ is often just one piece. This makes AM ideal for:
- Prototyping and design validation.
- Custom, one-off manifold solutions.
- Spare parts or legacy component replacement.
- Low-volume production runs.
However, pricing per part will generally decrease with larger batch sizes due to the amortization of setup costs and better utilization of build platform space. Discuss volume pricing with your chosen supplier.
5. Can valves or sensors be integrated directly during the printing process?
Currently, directly printing functional electromechanical components like valve actuators or electronic sensors as an integral part of the metal manifold during the primary AM build is generally not feasible with standard metal AM processes. However, AM enables:
- Optimized Interfaces: Designing highly precise and optimized mounting ports, cavities, and channels specifically for seamlessly integrating standard or custom valves and sensors after printing.
- Consolidated Housings: Printing complex housings that previously required multiple parts to hold sensors or valve cartridges.
- Embedded (but separate) Components: Research is ongoing into multi-material printing or embedding simple components during pauses in the build, but this is not yet common practice for industrial metal parts like manifolds.
The primary value lies in using AM’s design freedom to create superior interfaces 및 housings for these components, leading to more compact and efficient assemblies.
Conclusion: The Future of Fluid Systems Manufacturing with Metal AM Manifolds
Metal additive manufacturing represents a paradigm shift in the design and production of industrial manifolds. As we’ve explored, the ability to create highly 복잡한 지오메트리, achieve significant 부품 통합, enable substantial 경량화, and optimize fluid flow paths offers tangible benefits that traditional manufacturing methods often cannot match. For engineers and procurement managers in demanding sectors like aerospace, automotive, medical technology, and advanced industrial automation, metal AM provides a powerful tool for innovation and competitive advantage.
The journey to successfully implementing metal 3D printed manifolds involves embracing 적층 제조를 위한 설계(DfAM) principles, carefully selecting appropriate high-performance materials like 316L, IN625, or AlSi10Mg, understanding the achievable tolerances and necessary post-processing steps, and proactively addressing potential manufacturing challenges. Perhaps most importantly, success hinges on choosing the right B2B additive manufacturing partner – one with proven expertise, robust quality systems, and the right technological capabilities.
The advantages are clear: reduced leak points leading to higher reliability, simplified assembly processes, enhanced system performance through optimized flow, weight savings critical for mobile applications, and accelerated development cycles for custom solutions. While cost and lead time considerations require careful analysis, particularly regarding post-processing intensity, the overall value proposition of AM for complex or critical manifolds is increasingly compelling.
As the technology continues to mature with advancements in printing speed, new material development, enhanced process monitoring, and increasing automation, the adoption of metal AM for fluid system components will undoubtedly grow. We are moving towards a future where digital manufacturing transformation allows for on-demand production of highly optimized, customized fluid control solutions.
Partnering with a forward-thinking leader in this space is key to unlocking this potential. Met3dp, with its comprehensive portfolio spanning 업계를 선도하는 SEBM 프린터, advanced 금속 분말 제조, and extensive application development expertise, stands ready to support your organization’s journey into additive manufacturing. We empower businesses to leverage the full benefits of metal 3D printing, enabling the creation of next-generation industrial manifolds and accelerating innovation in fluid systems.
Ready to revolutionize your fluid control systems? Explore the possibilities of metal additive manufacturing. Visit Met3dp.com or contact our team today to discuss your specific manifold application and discover how our cutting-edge systems and materials can power your manufacturing goals.
공유
중국 칭다오에 본사를 둔 선도적인 적층 제조 솔루션 제공업체인 MET3DP Technology Co. 당사는 산업용 3D 프린팅 장비와 고성능 금속 분말을 전문으로 합니다.
관련 기사
Met3DP 소개
최근 업데이트
제품
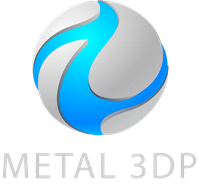
3D 프린팅 및 적층 제조용 금속 분말
문의 정보
- 칭다오시, 산둥성, 중국
- [email protected]
- [email protected]
- +86 19116340731