Custom Fixtures for Aerospace Testing via 3D Printing
목차
Introduction: The Critical Role of Custom Test Fixtures in Aerospace Validation
In the demanding world of aerospace engineering, failure is not an option. Every component, from the smallest fastener to the largest structural assembly, undergoes rigorous testing to ensure it meets stringent safety, performance, and reliability standards. Central to this critical validation process are test fixtures – bespoke devices meticulously designed and manufactured to hold, position, support, or interface with a component or assembly during testing procedures. These aren’t generic, off-the-shelf items; they are custom-engineered solutions tailored precisely to the unique geometry, load requirements, and testing protocols of the specific aerospace part under evaluation.
The integrity of aerospace testing hinges directly on the quality, accuracy, and suitability of these fixtures. They must accurately replicate the operational environment, apply loads precisely, withstand demanding test conditions (like vibration, thermal cycling, or fatigue loading), and allow for accurate measurement and data acquisition without influencing the test results. Whether validating a new turbine blade design, performing structural tests on fuselage panels, verifying the function of landing gear mechanisms, or conducting environmental checks on sensitive avionics, the test fixture is an indispensable, albeit often unseen, hero of aerospace development and certification.
Traditionally, manufacturing these custom fixtures involved subtractive methods, primarily CNC machining from billet materials like aluminum or steel. While effective, this approach often entails significant lead times, high costs (especially for complex geometries or low-volume requirements), and limitations in design complexity. The iterative nature of aerospace design, where components frequently undergo modifications, further exacerbates these challenges, as new or modified fixtures are often required quickly to keep development timelines on track.
This is where metal additive manufacturing (AM), commonly known as metal 3D 프린팅, emerges as a transformative technology. It offers a paradigm shift in how custom aerospace test fixtures are designed, produced, and utilized. By building fixtures layer-by-layer directly from digital models using high-performance metal powders, AM enables unprecedented design freedom, rapid production cycles, and the creation of highly optimized, lightweight, and complex tooling solutions that were previously impossible or prohibitively expensive to manufacture. For engineers and procurement managers in aerospace, understanding the potential of metal 3D printing for creating custom test fixtures is no longer just an advantage – it’s becoming a necessity for staying competitive and accelerating innovation. Companies seeking reliable, high-performance 금속 3D 프린팅 solutions find partners like Met3dp invaluable, leveraging advanced technologies to meet the rigorous demands of the aerospace industry.
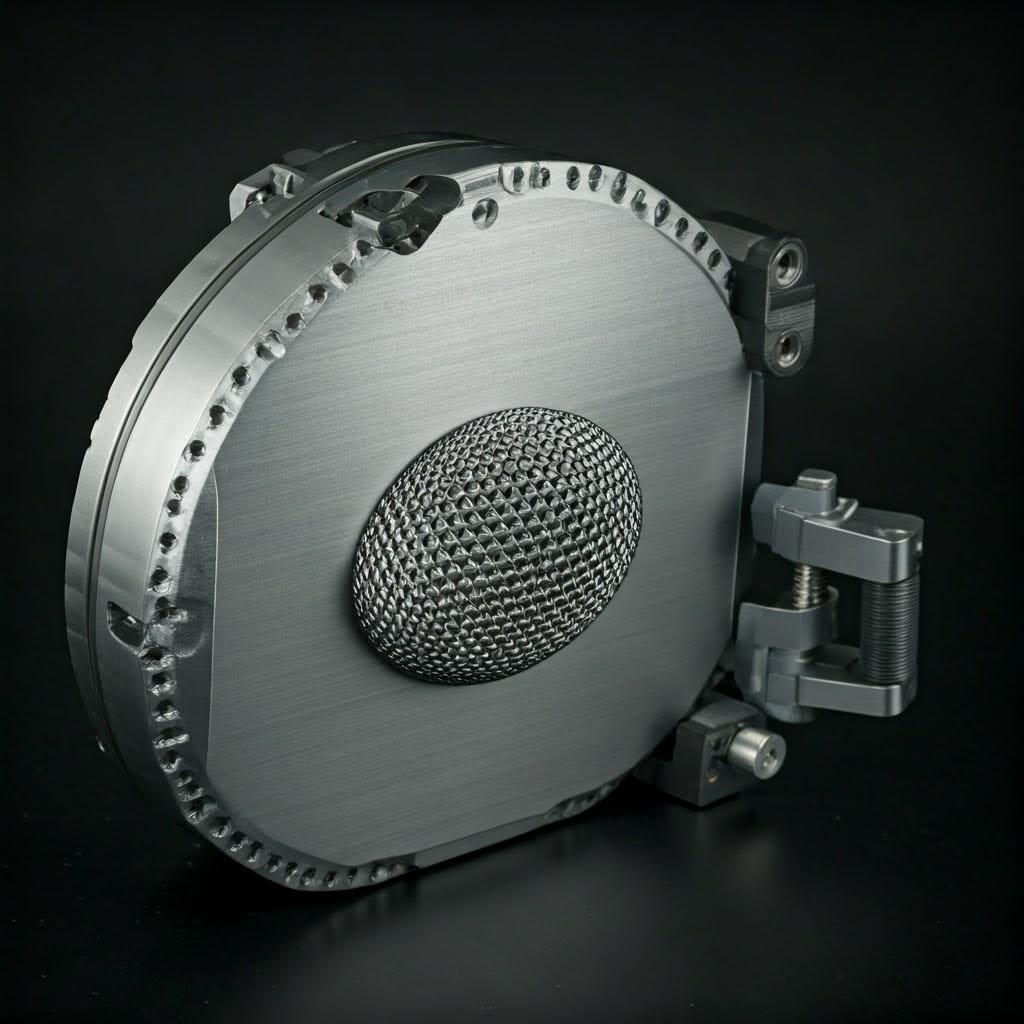
What are Custom Aerospace Test Fixtures Used For? Applications and Industries
Custom aerospace test fixtures are the unsung workhorses supporting a vast array of validation activities across the entire lifecycle of aircraft, spacecraft, missiles, and related systems. Their applications span research and development (R&D), manufacturing quality control, maintenance, repair, and overhaul (MRO). The need for precise, reliable, and often highly specialized fixtures makes them critical assets for aerospace manufacturers, tier suppliers, testing laboratories, and MRO facilities.
Key Application Areas:
- Structural Testing:
- Static Load Tests: Fixtures designed to hold components (e.g., wing sections, fuselage panels, control surfaces) while specific static loads are applied to verify strength and stiffness. These fixtures must rigidly support the test article without interfering with load paths or measurement points.
- Fatigue Testing: Specialized fixtures are required to securely mount components subjected to cyclic loading over extended periods to simulate operational lifetimes and identify potential failure modes. These fixtures must endure millions of cycles without degradation.
- Vibration and Acoustic Testing: Fixtures used to mount components or entire assemblies onto shaker tables or within acoustic chambers. These fixtures need to be dynamically stiff to transmit the required vibration or acoustic energy accurately without introducing unwanted resonances. Low-mass designs are often preferred.
- Functional Testing:
- Mechanism Testing: Fixtures for testing the operation of moving parts like landing gear retraction/extension, flap/slat actuation, door mechanisms, or thrust reversers. They replicate mounting points and allow for simulated operational forces and movements.
- Fluid System Testing: Holding components like valves, pumps, or tubing assemblies during pressure testing, leak testing, or flow rate verification. Fixtures must provide secure sealing and connection points compatible with test fluids and pressures.
- Avionics and Electrical System Testing: Fixtures designed to hold electronic boxes, wiring harnesses, or sensors in specific orientations for functional checks, environmental screening (e.g., thermal cycling, humidity), or electromagnetic compatibility (EMC) testing. These often require non-conductive elements or specific grounding provisions.
- Environmental Testing:
- Thermal Testing: Fixtures capable of holding components within thermal chambers during extreme temperature cycling or thermal shock tests. Materials with low thermal expansion (like Invar) or thermal stability are often crucial.
- Altitude and Vacuum Testing: Fixtures designed for use within vacuum chambers to simulate high-altitude or space environments, requiring materials with low outgassing properties.
- Humidity and Corrosion Testing: Fixtures used in environmental chambers must withstand corrosive atmospheres or high humidity without degrading or contaminating the test article. Materials like 316L stainless steel are often suitable.
- Manufacturing and Assembly Support:
- Assembly Jigs: While not strictly ‘test’ fixtures, similar custom jigs and fixtures are used to hold components in precise alignment during assembly operations. Metal 3D printing offers rapid production of these critical manufacturing aids.
- Metrology and Inspection Fixtures: Custom fixtures designed to hold parts securely and repeatably for dimensional inspection using Coordinate Measuring Machines (CMM), laser scanners, or optical systems. Accuracy and stability are paramount.
- Ground Support Equipment (GSE) and MRO:
- Specialized fixtures and tools are required for maintenance tasks, such as engine handling fixtures, component removal/installation tools, or repair jigs. Metal AM allows for on-demand production of replacement or specialized MRO tooling, reducing aircraft downtime.
서비스 제공 산업:
- Commercial Aviation (Aircraft OEMs, Tier Suppliers, Airlines)
- Military and Defense (Fighter Jets, Transport Aircraft, UAVs, Missile Systems)
- Space Exploration (Satellites, Launch Vehicles, Spacecraft Components)
- Urban Air Mobility (eVTOL Aircraft)
- Aerospace Research Institutions
The versatility required means that fixtures can range from simple brackets to highly complex, multi-part assemblies incorporating pneumatic or hydraulic actuation. Metal 3D printing provides the flexibility to address this wide spectrum of needs efficiently.
Why Metal 3D Printing Excels for Aerospace Fixture Manufacturing
The advantages of employing metal additive manufacturing for producing custom aerospace test fixtures, compared to traditional subtractive manufacturing, are compelling and address many of the pain points faced by aerospace engineers and procurement teams. Metal AM isn’t just a different way to make the same part; it enables the creation of 더 나은 fixtures, faster and often more cost-effectively, especially for complex or low-volume requirements.
주요 이점:
- Rapid Prototyping and Production (Lead Time Reduction):
- 속도: Metal AM can produce complex fixtures directly from a CAD file in days, compared to weeks or even months for traditional machining, which involves CAM programming, material procurement, setup, machining time, and potentially multiple operations.
- 응답성: This speed is crucial in R&D environments where designs iterate quickly. A new or modified fixture can be printed and delivered rapidly, keeping testing schedules on track and accelerating development cycles. Delays waiting for tooling are significantly minimized.
- 온디맨드 제조: Fixtures can be produced as needed, reducing the need for large inventories of potentially obsolete tooling. Digital inventories (CAD files) replace physical ones.
- 디자인의 자유와 복잡성:
- Geometric Complexity: AM builds parts layer-by-layer, easily handling intricate shapes, internal channels (e.g., for cooling or sensor integration), thin walls, and complex curvatures that are difficult, time-consuming, or impossible to achieve with CNC machining.
- 토폴로지 최적화: Engineers can use software tools to optimize the fixture’s design for maximum stiffness and strength while minimizing weight and material usage. This results in highly efficient, lightweight fixtures that are easier to handle and may perform better dynamically (e.g., in vibration testing).
- 파트 통합: Multiple components of a fixture assembly can potentially be consolidated into a single, monolithic printed part, reducing assembly time, potential failure points, and overall complexity.
- Material Variety and Performance:
- AM processes can utilize a range of high-performance aerospace-grade metals, including stainless steels (like 316L), tool steels, superalloys (like Inconel), and specialized alloys (like Invar for low thermal expansion).
- Material properties often meet or exceed those of wrought or cast equivalents, especially when combined with appropriate post-processing like heat treatment. Companies like Met3dp utilize advanced powder manufacturing techniques like gas atomization and PREP to ensure high-quality, spherical metal powders, leading to dense, reliable printed parts with superior mechanical properties.
- Cost-Effectiveness (Especially for Low Volumes & High Complexity):
- Reduced Machining Costs: For highly complex fixtures, the cost of multi-axis CNC machining, specialized tooling, and skilled labor can be substantial. AM often becomes more cost-effective as complexity increases.
- 재료 낭비 최소화: AM is an additive process, using only the material needed to build the part and its supports. Subtractive machining starts with a larger block of material and removes the excess, generating significant waste (swarf).
- 툴링이 필요 없는 제작: AM does not require dedicated molds or dies, making it ideal for one-off custom fixtures or very small production runs where the cost of traditional tooling would be prohibitive.
- 경량화:
- Through topology optimization and the ability to create internal lattice structures, AM allows for significant weight reduction in fixtures compared to solid machined counterparts. Lighter fixtures are easier to handle, potentially reduce setup time, and can improve the dynamic performance of test setups (e.g., lower inertia in vibration testing).
Comparison Table: Metal AM vs. Traditional Machining for Aerospace Fixtures
기능 | 금속 적층 제조(AM) | 전통적인 CNC 가공 |
---|---|---|
리드 타임 | Days (Rapid Prototyping & Production) | 몇 주에서 몇 달까지 |
디자인 복잡성 | High (Handles complex geometries, internal channels) | Moderate to High (Limited by tool access) |
부품 통합 | High potential | Low potential |
토폴로지 최적화 | Easily integrated for lightweighting & performance | Difficult / Less common |
재료 낭비 | Low (Additive process) | High (Subtractive process) |
Cost (Low Volume) | Often Lower (especially for complex parts) | High (Setup & programming costs dominate) |
Cost (High Volume) | Can be higher per part | Potentially Lower per part (amortized setup) |
필요한 도구 | None (Digital file) | Cutting tools, potentially workholding jigs |
재료 선택 | Growing range of aerospace alloys | Wide range of established materials |
최소 피처 크기 | Limited by process resolution (~0.1-0.5 mm typical) | High precision possible |
표면 마감 | Typically rougher (as-built), requires post-processing | Generally smoother |
시트로 내보내기
By leveraging these advantages, aerospace companies can significantly enhance their testing capabilities, reduce operational costs, and accelerate their innovation pipelines.
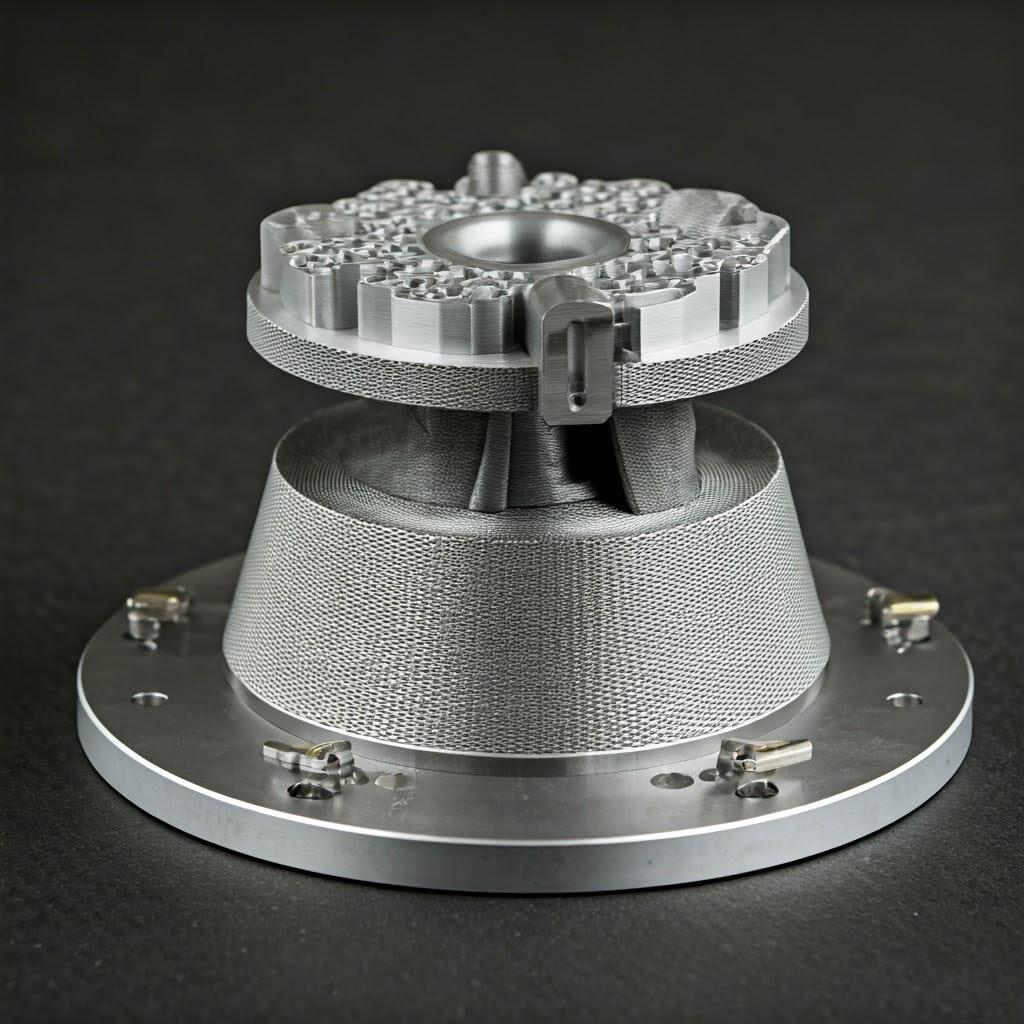
Recommended Materials (316L & Invar) for 3D Printed Aerospace Fixtures: Properties and Advantages
Choosing the right material is fundamental to the success of any 3D printed aerospace test fixture. The material must possess the necessary mechanical strength, stiffness, thermal properties, corrosion resistance, and dimensional stability to withstand the specific test conditions and accurately interface with the component under test. While various metals can be 3D printed, 316L 스테인리스 스틸 및 Invar (FeNi36) are two particularly well-suited and commonly recommended options for aerospace fixtures, each offering distinct advantages.
Met3dp, leveraging its expertise in advanced powder manufacturing systems including industry-leading gas atomization and Plasma Rotating Electrode Process (PREP) technologies, produces high-quality spherical powders crucial for achieving optimal results with these materials in processes like Selective Laser Melting (SLM) or Electron Beam Melting (EBM).
1. 316L 스테인리스 스틸:
316L is an austenitic chromium-nickel stainless steel containing molybdenum, known for its excellent corrosion resistance, good formability, and respectable strength. It’s a workhorse material in many industries, including aerospace, medical, and marine.
- Key Properties & Advantages for Fixtures:
- 뛰어난 내식성: Highly resistant to atmospheric corrosion, various chemicals, and saline environments. Crucial for fixtures used in environmental testing (humidity, salt spray) or those exposed to aerospace fluids.
- Good Strength and Ductility: Offers a good balance of tensile strength, yield strength, and elongation, ensuring fixtures are robust and resistant to brittle fracture. Suitable for static load, functional, and moderate fatigue applications.
- Weldability & Machinability: Easily weldable if needed for complex assemblies (though AM allows part consolidation) and readily machinable for critical features requiring very tight tolerances or specific surface finishes after printing.
- Biocompatibility (for certain applications): While less common for general fixtures, its biocompatibility is an advantage if fixtures interact with sensitive components or require specific cleaning protocols.
- Cost-Effectiveness & Availability: 316L powder is one of the more common and cost-effective metal powders available for AM, making it a practical choice for a wide range of fixture applications where extreme temperature stability isn’t the primary driver.
- 인쇄 가능성: Generally considered one of the easier metal alloys to process reliably using Powder Bed Fusion (PBF) techniques like SLM, resulting in dense, high-quality parts.
- Typical Aerospace Fixture Applications:
- Structural test fixtures (static loads)
- Assembly jigs and check gauges
- Fixtures for functional testing of mechanisms
- Tooling for MRO operations
- Brackets and supports for environmental chambers (where extreme temperature stability is not required)
2. Invar (FeNi36):
Invar is an iron-nickel alloy specifically engineered for its uniquely low coefficient of thermal expansion (CTE) near room temperature. Its name comes from the word “invariable,” referring to its lack of expansion or contraction with temperature fluctuations.
- Key Properties & Advantages for Fixtures:
- Extremely Low CTE: This is Invar’s defining characteristic. It maintains exceptional dimensional stability even when subjected to significant temperature changes. This is critical for fixtures used in metrology, optical alignment, or thermal cycling tests where maintaining precise dimensions is paramount.
- Good Strength and Toughness: While not as strong as some high-strength steels, Invar provides adequate mechanical properties for many fixture applications.
- 기계 가공성: Can be machined, although it requires specific techniques due to its gummy nature. Post-print machining allows for achieving very high precision on critical surfaces.
- Enabling High-Precision Applications: Invar allows the creation of metrology fixtures, optical benches, or tooling for composite layup molds where thermal expansion differences between the tool and the part must be minimized.
- Typical Aerospace Fixture Applications:
- Metrology and CMM fixtures requiring high stability
- Optical alignment fixtures for sensors or lasers
- Tooling for manufacturing or testing composite components (matching CTE)
- Fixtures used within wide-ranging thermal test chambers
- Supports for sensitive instrumentation during environmental testing
Material Properties Comparison:
속성 | 316L 스테인리스 스틸 | Invar (FeNi36) | 단위 | 참고 |
---|---|---|---|---|
밀도 | ~7.9 – 8.0 | ~8.1 | g/cm³ | Relatively similar density. |
영의 계수 | ~190 – 200 | ~140 – 150 | 평점 | 316L is significantly stiffer. |
Yield Strength (Annealed) | ~200 – 250 | ~240 – 280 | MPa | Similar yield strengths in typical conditions. |
궁극의 인장 강도 | ~500 – 600 | ~450 – 500 | MPa | 316L generally has higher ultimate strength. |
휴식 시 신장 | High (~40-60%) | Moderate (~30-40%) | % | 316L is more ductile. |
경도(어닐링) | ~70-80 HRB / ~150 HV | ~70-80 HRB / ~150 HV | HRB / HV | Similar hardness. |
CTE (20-100°C) | ~16 – 17 | ~1.2 – 1.6 | µm/(m·°C) | Invar’s key advantage: extremely low thermal expansion. |
열 전도성 | ~16 | ~10 | W/(m-K) | Both are relatively poor thermal conductors compared to aluminum. |
내식성 | 우수 | Moderate (Requires plating in harsh env.) | – | 316L excels here. |
Relative Cost (Powder) | Lower | 더 높음 | – | Invar powder is typically more expensive than 316L. |
Printability (PBF) | Generally Good | Moderate (Requires careful parameter ctrl) | – | Both are printable, Invar may require more process optimization. |
시트로 내보내기
Choosing Between 316L and Invar:
- Choose 316L if:
- Excellent corrosion resistance is required.
- The fixture operates primarily near room temperature or thermal stability is not the most critical factor.
- Higher stiffness or ductility is needed.
- Cost is a major consideration.
- Choose Invar if:
- Exceptional dimensional stability across temperature changes is the primary requirement (metrology, thermal cycling, optical alignment).
- The fixture interfaces with materials with low CTE (like composites).
- Cost is secondary to achieving thermal stability.
By understanding the properties of these materials and partnering with an experienced additive manufacturing provider like Met3dp, aerospace companies can leverage the power of 3D printing to create highly effective, custom test fixtures optimized for their specific validation needs. Met3dp’s portfolio includes not only common alloys like 316L but also expertise in processing specialized materials, ensuring customers can access the optimal powder for their demanding applications. Sources and related content
Design for Additive Manufacturing (DfAM) Principles for Optimized Test Fixtures
Simply replicating a design intended for CNC machining using metal additive manufacturing rarely unlocks the full potential of 3D printing. To truly leverage the benefits of AM for aerospace test fixtures – achieving lightweight designs, complex geometries, reduced lead times, and optimal performance – engineers must embrace Design for Additive Manufacturing (DfAM). DfAM involves rethinking the design process from the ground up, considering the unique opportunities and constraints of layer-by-layer fabrication. Implementing DfAM principles is crucial for creating successful, cost-effective, and highly functional 3D printed fixtures.
Key DfAM Principles for Aerospace Fixtures:
- Build Orientation Strategy:
- 영향: The orientation of the fixture on the build plate significantly affects support requirements, surface finish on different faces, residual stress accumulation, and ultimately, print time and cost.
- 고려 사항: Orient the part to minimize the volume of support structures needed, especially on critical surfaces or hard-to-reach areas. Prioritize critical dimensions or features to be built in orientations known to yield higher accuracy (often XY plane vs. Z-axis). Consider how thermal stresses might accumulate and potentially cause warping based on the orientation.
- Support Structure Optimization:
- Necessity: Metal Powder Bed Fusion (PBF) processes require support structures for overhanging features (typically angles below 45 degrees from horizontal) and to anchor the part to the build plate, preventing warping.
- DfAM Approach: Design features to be self-supporting where possible (e.g., using chamfers or fillets instead of sharp horizontal overhangs). If supports are unavoidable, design them for easy removal (e.g., using specific interface types, ensuring accessibility for tools). Consider the surface finish requirements of supported surfaces, as they will typically be rougher after support removal. Advanced support strategies might involve optimized lattice supports that are strong yet use less material and are easier to remove.
- Feature Design & Sizing:
- Minimum Wall Thickness: AM processes have limitations on the minimum thickness of walls and features they can reliably produce. Design walls to be above this threshold (often 0.4-1.0 mm, depending on the process and material) to ensure structural integrity.
- Hole Design: Small horizontal holes can be challenging to print accurately without supports. Consider designing holes vertically if possible. For horizontal holes, teardrop shapes can often make them self-supporting. Minimum printable hole diameters depend on the machine resolution.
- Threads and Fine Features: While AM can produce some threads directly, for critical or high-precision threads, it’s often better to design the hole slightly undersized and plan for post-print tapping or thread milling. Similarly, very fine features might require post-machining for accuracy.
- Lightweighting Strategies:
- 토폴로지 최적화: Use specialized software to remove material from non-critical areas while maintaining structural integrity and stiffness requirements. This is ideal for fixtures where weight is a concern (e.g., dynamic testing, ease of handling). The organic, complex shapes resulting from topology optimization are often perfectly suited for AM production.
- 격자 구조: Incorporate internal lattice structures (e.g., gyroids, honeycombs) to reduce mass significantly while maintaining good compressive strength and stiffness. This can create lightweight yet robust fixture bodies.
- Hollowing: For bulky sections, consider hollowing the part with escape holes for trapped powder removal, significantly reducing material consumption and weight. Ensure internal supports are added if needed within the hollow cavity.
- Designing for Post-Processing:
- Machining Allowances: If specific surfaces require high precision or a very smooth finish, add extra stock material (machining allowance) to those areas in the CAD model, anticipating post-print CNC machining.
- 접근성: Ensure that areas requiring support removal, machining, or inspection are physically accessible after the part is printed. Avoid deep, enclosed cavities where supports cannot be removed or powder cannot be evacuated.
- Workholding: Consider how the fixture itself will be held for any necessary post-processing steps like machining. Incorporate datum features or clamping surfaces into the AM design if needed.
- 파트 통합:
- Opportunity: Assess if multiple components of a traditionally fabricated fixture assembly can be redesigned and consolidated into a single, monolithic printed part.
- 혜택: Reduces assembly time and labor, eliminates potential failure points at joints or fasteners, and can create lighter, stiffer structures.
- Caveats: Ensure the consolidated design is still manufacturable via AM (e.g., powder removal from internal channels) and consider if different materials were previously used for different components.
By applying these DfAM aerospace principles, engineers can move beyond simple substitution and create truly optimized rapid tooling solutions. Thinking additively from the start ensures that the final 3D printed fixture meets performance requirements while maximizing the inherent advantages of the manufacturing process.
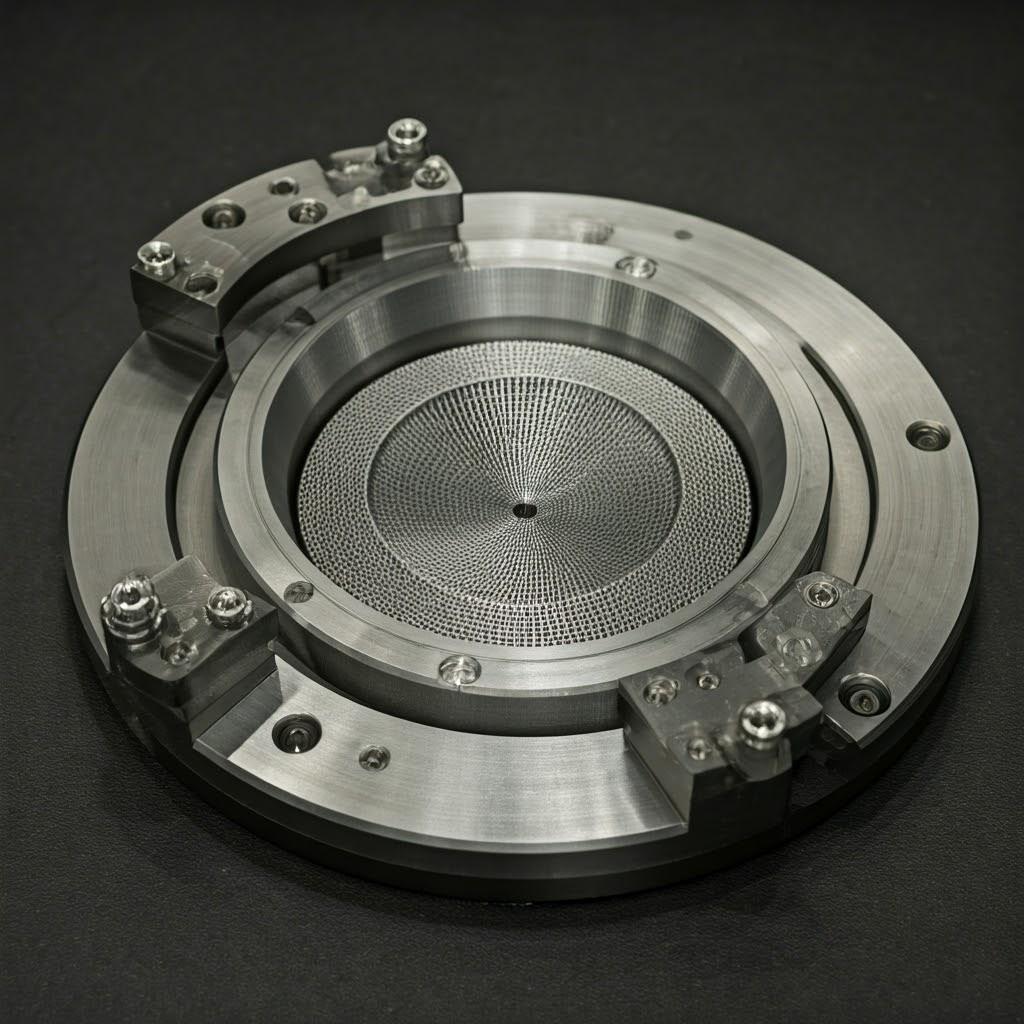
Achieving Precision: Tolerance, Surface Finish, and Dimensional Accuracy in Metal AM Fixtures
For aerospace test fixtures, precision is often paramount. The fixture must hold the test article securely, repeatably, and in the correct orientation without influencing the test outcome. Understanding the levels of tolerance, surface finish, and dimensional accuracy achievable with metal additive manufacturing is crucial for engineers specifying and designing these components. While AM offers remarkable capabilities, it’s essential to have realistic expectations and plan for post-processing when exceptionally high precision is required.
Factors Influencing Precision:
- AM 프로세스: Different metal AM technologies (e.g., Laser Powder Bed Fusion – LPBF/SLM, Electron Beam Melting – EBM) have inherent differences in resolution, layer thickness, and energy input, affecting achievable tolerances and surface finish. Met3dp specializes in advanced SEBM (Selective Electron Beam Melting) printers, known for producing parts with low residual stress, particularly beneficial for complex geometries. You can explore various 인쇄 방법 and their characteristics to understand these nuances better.
- 머신 보정: The accuracy and calibration of the 3D printer itself are fundamental. Well-maintained, high-quality machines like those developed by Met3dp, designed for industry-leading accuracy and reliability, are essential for consistent results.
- Material: Different metal powders behave differently during melting and solidification, influencing shrinkage, potential distortion, and achievable detail resolution.
- Part Size and Geometry: Larger parts and complex geometries are more susceptible to thermal stresses and potential distortion during the build, which can affect final dimensional accuracy.
- Build Parameters: Process parameters like laser/electron beam power, scan speed, layer thickness, and hatching strategy directly impact the melt pool characteristics, density, surface finish, and accuracy.
- 후처리: Stress relief heat treatments are often necessary and can cause minor dimensional changes. Machining is typically required for achieving tolerances tighter than the inherent AM process capability.
Typical Tolerances:
- As-Built Tolerances: For typical metal PBF processes (LPBF/EBM), achievable “as-built” tolerances (i.e., directly off the printer after support removal but before machining) are often in the range of:
- ±0.1 mm to ±0.3 mm for smaller features (e.g., < 25 mm)
- ±0.5% to ±1.0% of the nominal dimension for larger features.
- Note: These are general guidelines; specific capabilities depend heavily on the factors mentioned above.
- Machined Tolerances: For critical features like mating surfaces, datum points, or interfaces requiring high precision, post-print CNC machining is employed. Machining can achieve much tighter tolerances, typically ±0.01 mm to ±0.05 mm, or even tighter depending on the specific machining process and setup. Tight tolerance 3D printing usually implies leveraging post-machining for critical dimensions.
표면 마감(거칠기):
- As-Built Surface Finish (Ra): The surface finish of as-built metal AM parts is inherently rougher than machined surfaces due to the layer-by-layer process and partially melted powder particles adhering to the surface.
- 상위 표면: Generally smoother.
- Vertical Walls: Typically have a roughness (Ra) ranging from 6 µm to 20 µm, depending on the process and parameters. EBM often produces rougher surfaces than LPBF.
- Supported Surfaces: Surfaces where support structures were attached are usually the roughest and show witness marks after removal, often requiring subsequent finishing.
- 내부 채널: Can be difficult to finish and will typically retain the as-built roughness.
- Post-Processed Surface Finish: Various post-processing techniques can significantly improve the surface finish:
- Bead Blasting/Shot Peening: Provides a uniform matte finish, typically Ra 3 µm to 10 µm. Can also improve fatigue life.
- 텀블링/진동 마감: Smoothens surfaces and edges, effective for batches of smaller parts.
- 가공: Can achieve very smooth finishes (Ra < 1 µm) on specific surfaces.
- 연마: Manual or automated polishing can achieve mirror-like finishes (Ra < 0.1 µm) if required, though this is labor-intensive.
- Achieving the desired surface finish metal AM often involves selecting the appropriate secondary operations.
Dimensional Accuracy and Verification:
- Importance: Ensuring the final fixture meets the required dimensional specifications is critical for its function.
- Metrology: Post-production inspection using calibrated measurement tools is essential.
- CMM (Coordinate Measuring Machine): The gold standard for verifying complex geometries and tight tolerances. Fixtures should be designed with clear datum features for repeatable CMM setup.
- Laser Scanning/Structured Light Scanning: Useful for capturing the overall geometry of complex shapes and comparing it to the original CAD model.
- Calipers/Micrometers: Suitable for simpler dimensional checks.
- 품질 보증: Partnering with an AM provider with robust quality management systems (e.g., ISO 9001, AS9100 for aerospace) ensures processes are in place for dimensional verification and reporting.
Engineers must specify required tolerances and surface finishes clearly on drawings, indicating which features are critical and may require post-machining versus those where as-built conditions are acceptable. This allows the AM service provider to plan the manufacturing process effectively, including necessary machining allowances and post-processing steps.
Essential Post-Processing Steps for 3D Printed Aerospace Test Fixtures
Metal 3D printing rarely yields a finished part straight off the build plate. For demanding applications like aerospace test fixtures, post-processing is a critical stage that transforms the as-built part into a functional, reliable component meeting all specifications. Understanding these steps is essential for planning production timelines, estimating costs, and ensuring the final fixture performs as intended.
Common Post-Processing Stages:
- Stress Relief / Heat Treatment:
- Why: The rapid heating and cooling inherent in PBF processes create significant residual stresses within the printed part. These stresses can cause distortion (especially after removal from the build plate), reduce mechanical performance, and potentially lead to premature failure.
- 프로세스: Parts are typically heat-treated while still attached to the build plate (or immediately after removal) in a controlled atmosphere furnace. The specific temperature, soak time, and cooling rate depend on the material (e.g., 316L, Invar) and the desired outcome (stress relief, annealing, solution treatment, aging).
- 혜택: Relieves internal stresses, improves dimensional stability, homogenizes the microstructure, and can optimize mechanical properties (e.g., increase ductility, toughness, or hardness depending on the treatment). Heat treatment aerospace parts is a standard requirement for ensuring component integrity.
- 참고: Heat treatment can cause slight dimensional changes, which must be accounted for if tight tolerances are required.
- 빌드 플레이트에서 파트 제거:
- 프로세스: Once heat treatment (if performed on the plate) is complete, the part needs to be separated from the build plate. This is typically done using:
- 와이어 EDM(방전 가공): Precise method, often used for parts requiring a clean separation surface or minimal force application.
- Bandsaw: A common, faster method for less critical separations.
- 고려 사항: The removal method should avoid damaging the part itself.
- 프로세스: Once heat treatment (if performed on the plate) is complete, the part needs to be separated from the build plate. This is typically done using:
- 지원 구조 제거:
- 도전: Removing support structures without damaging the part surface requires care and often manual labor. Supports are typically made of the same material as the part.
- 방법:
- 수동 제거: Using pliers, cutters, grinders, or specialized tools to break or cut away supports.
- 가공: Milling or grinding away support structures, especially larger ones or those on critical surfaces.
- Design Impact: As discussed in DfAM, designing supports for easier removal (e.g., with smaller contact points or specific geometries) significantly simplifies this step. Surfaces where supports were attached will typically require further finishing.
- CNC 가공:
- 목적: To achieve tolerances, surface finishes, or features beyond the capability of the as-built AM process. This is common for:
- Critical mating interfaces
- Datum surfaces for measurement or assembly
- High-precision bores or mounting holes
- Threaded holes (tapping/milling)
- Achieving very smooth surface finishes on specific areas.
- 프로세스: The 3D printed fixture is mounted onto a CNC milling machine or lathe, and material is precisely removed from designated areas based on the design specifications (requiring machining allowances in the DfAM phase). CNC machining fixtures themselves are often made using AM, highlighting the synergy between the technologies.
- 목적: To achieve tolerances, surface finishes, or features beyond the capability of the as-built AM process. This is common for:
- 표면 마감:
- Goal: To improve the as-built surface roughness, remove support witness marks, enhance aesthetics, or prepare the surface for coatings.
- Techniques:
- Bead Blasting / Sand Blasting: Creates a uniform, non-directional matte finish. Different media (glass beads, aluminum oxide) yield different results.
- Tumbling / Vibratory Finishing: Uses abrasive media in a rotating or vibrating drum to deburr edges and smooth surfaces, suitable for batches of parts.
- Grinding / Polishing: Manual or automated processes to achieve progressively smoother finishes, potentially down to mirror quality for specific applications (e.g., optical interfaces).
- 전기 연마: An electrochemical process that removes a microscopic layer of material, resulting in a very smooth, clean, and corrosion-resistant surface, particularly effective for stainless steels like 316L.
- Cleaning and Inspection:
- Cleaning: Thoroughly cleaning the fixture to remove any residual powder (especially from internal channels), machining fluids, or contaminants.
- Inspection: Performing final dimensional checks (CMM, scanning), visual inspection, and potentially non-destructive testing (NDT) like CT scanning if internal integrity is critical.
Choosing a provider like Met3dp, which offers comprehensive solutions potentially spanning printers, high-quality powders (viewable on their 제품 페이지), and application support, ensures that these critical post-processing steps are considered early in the project lifecycle. Proper planning and execution of post-processing are key to realizing the full benefits of metal AM for aerospace test fixtures.
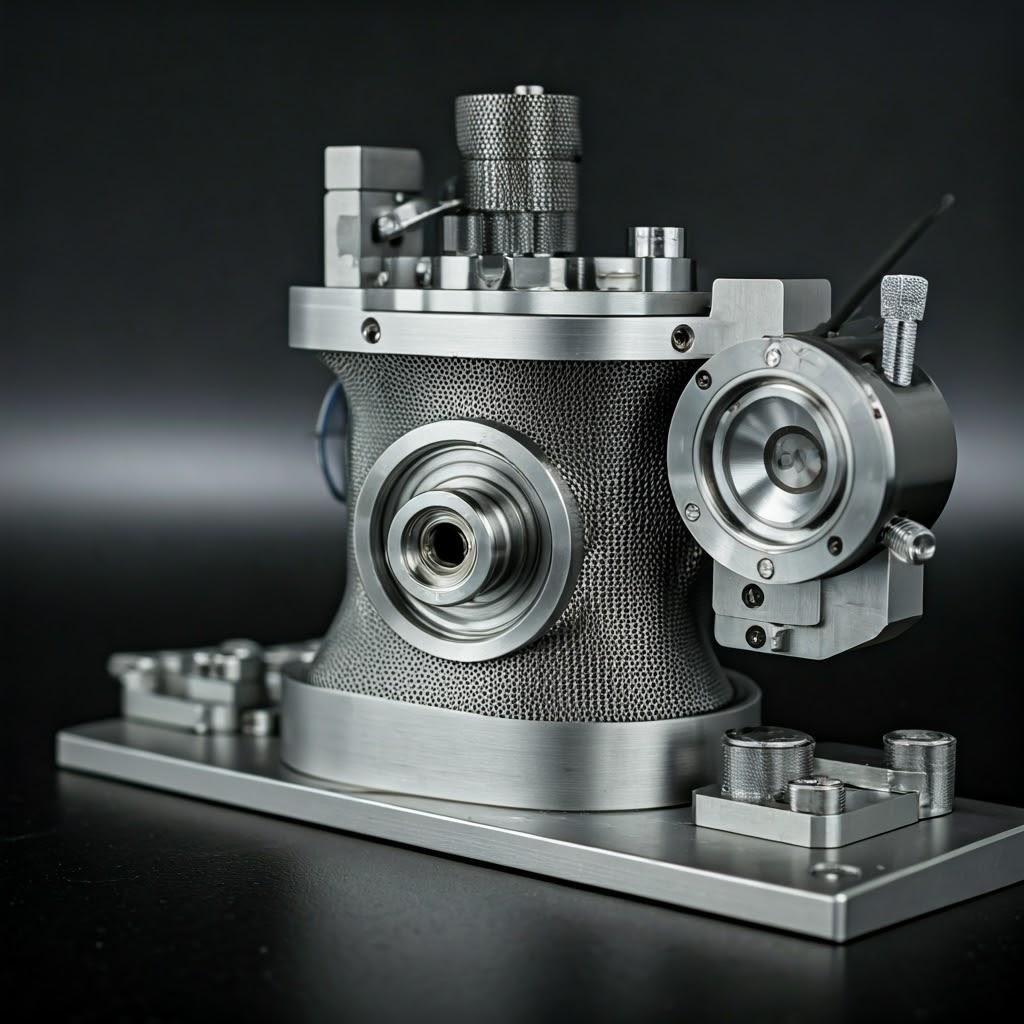
Overcoming Common Challenges in Metal 3D Printing for Aerospace Tooling
While metal additive manufacturing offers significant advantages for producing aerospace test fixtures, it’s not without its challenges. Understanding potential issues and how to mitigate them through careful design, process control, and collaboration with an experienced AM provider is crucial for success. Forewarned is forearmed, enabling engineers and procurement managers to anticipate and address these hurdles effectively.
Common Challenges and Mitigation Strategies:
- Warping and Distortion:
- Cause: Uneven heating and cooling during the layer-by-layer printing process generate internal stresses (residual stress). If these stresses exceed the material’s yield strength or the anchoring force of supports, the part can warp or distort, especially after removal from the build plate. This is a major concern for warping distortion metal AM.
- Mitigation:
- DfAM: Orient the part to minimize thermal gradients; use topology optimization to reduce bulk material; add sacrificial features or ribs to increase stiffness during the build.
- Support Strategy: Robust support structures are essential to anchor the part firmly to the build plate and conduct heat away. Optimize support placement and density.
- 프로세스 매개변수: Fine-tuning laser/beam power, scan strategy (e.g., island scanning), and preheating (especially in EBM) can minimize stress buildup.
- 스트레스 해소: Performing a stress relief heat treatment cycle before removing the part from the build plate is often standard practice.
- Support Removal Difficulty:
- Cause: Supports are made of the same dense metal as the part and can be strongly bonded, especially in inaccessible areas or when dense supports are required. Removal can be time-consuming, labor-intensive, and risks damaging the part surface.
- Mitigation:
- DfAM: Design parts to be self-supporting where possible; minimize overhang angles; design supports with optimized geometries (e.g., tapered, perforated, smaller contact points) for easier breaking or machining; ensure physical access for removal tools.
- 프로세스 제어: Use optimized support parameters offered by build preparation software.
- 후처리: Budget adequate time and resources for careful manual or machined support removal and subsequent surface finishing of witness marks.
- Residual Stress Effects:
- Cause: Beyond macroscopic warping, residual stresses remain even in seemingly stable parts. These internal stresses can negatively impact fatigue life, dimensional stability over time, and susceptibility to stress corrosion cracking.
- Mitigation:
- 열처리: Proper stress relief cycles are the primary method for significantly reducing residual stress to acceptable levels.
- 프로세스 최적화: Techniques like EBM (which uses higher build chamber temperatures) naturally result in lower residual stress compared to LPBF. Scan strategies can also influence stress patterns.
- 디자인: Avoid sharp internal corners or abrupt changes in thickness, which act as stress concentrators.
- 다공성:
- Cause: Small voids or pores within the printed material can arise from trapped gas (e.g., argon shielding gas, dissolved gases in powder), incomplete fusion between layers or scan tracks (Lack-of-Fusion porosity), or keyholing effects (instability in the melt pool at high energy densities). Porosity can degrade mechanical properties like fatigue strength and ductility.
- Mitigation:
- High-Quality Powder: Using high-purity, spherical powders with consistent particle size distribution and low internal porosity is critical. Met3dp’s focus on advanced powder production (Gas Atomization, PREP) directly addresses this, ensuring optimal powder characteristics.
- Optimized Process Parameters: Developing and using validated parameter sets (power, speed, layer thickness, hatching) specific to the material and machine ensures consistent melting and fusion, minimizing lack-of-fusion and keyholing.
- Process Atmosphere Control: Maintaining a high-purity inert gas atmosphere (Argon or Nitrogen) in the build chamber prevents oxidation and gas entrapment.
- 열간 등방성 프레싱(HIP): A post-processing step involving high temperature and high pressure, which can effectively close internal pores and significantly improve density and mechanical properties. Often required for critical aerospace components.
- Surface Finish Limitations:
- Cause: The inherent layer-wise nature and adherence of partially melted powder result in rougher surfaces compared to machining. Supported surfaces are particularly affected.
- Mitigation:
- Orientation: Orient critical surfaces vertically or as top surfaces for better as-built finish.
- Parameter Tuning: Finer layer thicknesses and specific contour scan parameters can improve sidewall finish, albeit potentially increasing build time.
- 후처리: Plan for necessary surface finishing steps (blasting, machining, polishing) based on the requirements for specific surfaces. Clearly define surface finish requirements on drawings.
- Quality Assurance and Consistency:
- 도전: Ensuring every printed fixture meets the required specifications, especially regarding material properties, internal integrity, and dimensional accuracy, requires robust quality assurance aerospace protocols.
- Mitigation:
- Powder Control: Strict quality control of incoming metal powders (chemistry, particle size, flowability, morphology).
- 프로세스 모니터링: In-situ monitoring capabilities (melt pool monitoring, thermal imaging) can provide real-time insights into build quality.
- 빌드 후 검사: Implementing rigorous inspection protocols, including dimensional verification (CMM), material testing (tensile tests on witness coupons), density checks, and potentially NDT (CT scanning) for critical fixtures.
- Supplier Certification: Partnering with suppliers holding relevant certifications (ISO 9001, AS9100) demonstrates a commitment to quality management.
By anticipating these challenges and working with knowledgeable partners who possess both advanced equipment and deep process expertise, aerospace companies can reliably leverage metal 3D printing to produce high-performance custom test fixtures.
Selecting the Right Metal 3D Printing Service Provider for Aerospace Applications
Choosing the right manufacturing partner is as critical as the design and material selection when implementing metal additive manufacturing for aerospace test fixtures. The unique demands of the aerospace industry – stringent quality requirements, complex components, and the need for reliable performance – necessitate partnering with a service provider that possesses the right expertise, equipment, and certifications. Evaluating AM vendors requires careful consideration of several key factors to ensure your custom fixtures are produced correctly, on time, and to the required standards.
Key Criteria for Evaluating Suppliers:
- Aerospace Experience and Certifications:
- AS9100 Certification: This is the standard Quality Management System (QMS) requirement for the aviation, space, and defense industries. Partnering with an AS9100 certified 3D printing provider demonstrates a commitment to rigorous quality control, process documentation, traceability, and continuous improvement aligned with aerospace expectations.
- Proven Track Record: Look for suppliers with documented experience in producing parts (including tooling and fixtures) for aerospace clients. Case studies, references, and examples of previous work can indicate their understanding of the industry’s specific needs and challenges.
- Material Expertise and Portfolio:
- Relevant Materials: Ensure the provider has proven experience and validated processes for the specific metals you require, such as 316L, Invar, or potentially other aerospace alloys (e.g., Inconel, Titanium alloys) if needed for different applications.
- Powder Quality Control: Inquire about their powder sourcing and quality control procedures. High-quality, aerospace-grade powders are fundamental to achieving dense, reliable parts with consistent mechanical properties. Providers like Met3dp, who manufacture their own high-performance metal powders using advanced techniques like PREP and gas atomization, offer significant advantages in material quality assurance. Learn more 우리에 대하여 and our commitment to material excellence.
- 재료 개발: Some providers also engage in material research and may offer specialized or customized alloys.
- Technological Capabilities (Equipment):
- Appropriate AM Technology: Understand the different metal AM processes (LPBF, EBM, DED) and choose a supplier whose equipment matches your requirements for precision, surface finish, material compatibility, and part size. Met3dp’s expertise in Selective Electron Beam Melting (SEBM), for example, offers benefits like reduced residual stress for complex parts.
- Machine Fleet: Consider the number and type of machines they operate. A larger, diverse fleet can offer greater capacity, potentially shorter lead times, and redundancy. Ensure machines are well-maintained and calibrated.
- 볼륨을 구축합니다: Verify their printers can accommodate the size of the fixtures you need to produce.
- In-House Post-Processing Capabilities:
- Integrated Services: Suppliers offering a wide range of in-house post-processing services (stress relief/heat treatment, CNC machining, surface finishing, NDT inspection) can provide a more streamlined, efficient, and accountable workflow.
- Managed Services: If certain processes are outsourced, ensure the provider has a robust system for managing and qualifying their subcontractors.
- 전문성: Verify they have the necessary expertise and equipment for the specific post-processing steps your fixture requires (e.g., furnaces with controlled atmospheres, multi-axis CNC machines, metrology labs).
- Engineering and DfAM Support:
- Collaboration: Look for a partner willing to collaborate on design optimization (DfAM). Their expertise can help you leverage AM’s benefits fully, improve manufacturability, reduce costs, and enhance fixture performance.
- Technical Consultation: Can they provide guidance on material selection, orientation strategies, support design, and tolerance expectations?
- Quality Management Systems (QMS) and Inspection:
- Traceability: Robust systems for tracking materials, process parameters, and production steps are crucial for aerospace.
- 검사 기능: Availability of CMM, laser scanning, NDT methods (like CT scanning if required for critical internal structures), and material testing capabilities (e.g., tensile testing of witness coupons).
- Reporting: Ability to provide comprehensive quality documentation, including material certifications, dimensional inspection reports, and certificates of conformance.
- Lead Time, Responsiveness, and Communication:
- Quoting Speed: How quickly can they provide accurate quotes?
- Stated Lead Times: What are their typical lead times for the required materials and post-processing?
- Communication: Clear, proactive communication throughout the production process is essential.
Supplier Evaluation Checklist Table:
기준 | Key Questions to Ask | Importance (Aerospace) |
---|---|---|
AS9100 인증 | Are you AS9100 certified? Can you provide the certificate? | 매우 높음 |
Aerospace Experience | Can you share examples or case studies of similar aerospace fixtures/tooling you’ve produced? | 매우 높음 |
Material Expertise (e.g., Invar) | Do you have validated parameters and experience with [Specific Material]? What are your powder QC procedures? | 매우 높음 |
AM Technology & Equipment | What specific AM machines do you operate? What is their build volume and typical accuracy? | 높음 |
후처리 기능 | What post-processing (heat treatment, machining, finishing, NDT) do you perform in-house? How do you manage outsourced processes? | 매우 높음 |
DfAM / Engineering Support | Do you offer DfAM consultation? Can you assist with design optimization for AM? | 높음 |
Quality Systems & Inspection | Describe your QMS. What inspection methods (CMM, NDT) are available? What documentation is provided? | 매우 높음 |
Lead Time & Responsiveness | What is your typical quoting time? What is the estimated lead time for this project? How will you communicate progress? | 높음 |
비용 경쟁력 | Provide a detailed cost breakdown. Are there options to reduce cost (e.g., design changes)? | 중간에서 높음 |
시트로 내보내기
오른쪽 선택 certified aerospace supplier is an investment in quality, reliability, and successful project execution. Thorough vetting ensures your custom aerospace test fixtures meet the rigorous standards demanded by the industry.
Understanding Cost Factors and Lead Times for Custom 3D Printed Fixtures
One of the primary drivers for adopting metal additive manufacturing is the potential for accelerated timelines and cost savings, particularly for complex or low-volume parts like custom aerospace test fixtures. However, understanding the specific factors influencing metal 3D printing cost aerospace and production timelines is essential for accurate budgeting, planning, and managing expectations in B2B procurement AM.
Key Cost Drivers:
- Part Volume and Bounding Box:
- Material Consumption: The sheer volume of the part directly impacts the amount of expensive metal powder required. Larger parts consume more material.
- 구축 시간: Larger parts, or parts occupying a larger footprint (bounding box) on the build plate, generally take longer to print, increasing machine time costs. Hollowing and lattice structures can mitigate this.
- 머티리얼 유형:
- 파우더 비용: The base cost of metal powders varies significantly. Common materials like 316L stainless steel are generally less expensive than specialized alloys like Invar, titanium alloys, or high-temperature superalloys.
- 인쇄 가능성: Some materials are more challenging to print reliably, potentially requiring longer print times, more support, or more intensive process monitoring, which can influence cost.
- Part Complexity and Design:
- 지원 구조: Highly complex geometries with numerous overhangs require extensive support structures. This increases material consumption, build time, and significantly adds to the labor required for post-print support removal and surface finishing. DfAM plays a crucial role here – optimizing designs to be self-supporting reduces cost.
- Wall Thickness/Features: Very thin walls or extremely fine features can slow down the printing process (requiring different parameters) and may increase the risk of build failure, potentially impacting cost.
- 사후 처리 요구 사항:
- 열처리: Standard stress relief is often included, but specialized cycles (annealing, aging) add cost.
- 가공: The extent of CNC machining required is a major cost factor. Machining tight tolerances on multiple surfaces significantly increases cost compared to parts needing minimal or no machining.
- 표면 마감: Basic finishes like bead blasting are relatively inexpensive. More advanced finishing like tumbling, electropolishing, or manual polishing add progressively more cost due to labor and specialized equipment.
- Inspection: Basic dimensional checks are standard. Advanced inspection like CMM reports on many features or NDT (CT scanning) adds significant cost.
- Quality and Certification Requirements:
- 테스트: Requirements for destructive testing (e.g., tensile testing of witness coupons) add material and labor costs.
- Documentation: Extensive documentation packages (detailed inspection reports, material traceability, certificates of conformance) required for aerospace increase administrative overhead and cost. AS9100 compliance inherently involves higher operational costs reflected in pricing.
- 주문 수량:
- Setup Costs: AM has setup costs associated with preparing the build file, loading the machine, and post-processing setup. These costs are amortized over the number of parts in a build.
- 볼륨 할인: Printing multiple copies of a fixture in a single build, or ordering larger quantities, typically reduces the cost per part compared to a single one-off unit.
Factors Influencing Lead Times:
- Quoting and Engineering Review: Initial phase for assessing feasibility, providing a quote, and potentially discussing DfAM adjustments. (Typically 1-5 days)
- Queue Time: Time waiting for machine availability. This depends on the service provider’s current workload and machine capacity. (Can range from days to weeks)
- 빌드 준비: Preparing the final build file, including orientation and support generation. (Typically <1 day)
- 인쇄 시간: Actual time the part spends printing in the machine. This depends on part height, volume, and process parameters. (Can range from hours for small parts to many days for large/complex builds)
- Cool Down and Part Removal: Allowing the build chamber and part to cool before removal. (Typically hours to <1 day)
- 후처리: This is often the longest and most variable part of the lead time.
- Heat Treatment: 1-3 days (including furnace time and cooling)
- Support Removal: Hours to days, depending on complexity.
- Machining: Days to weeks, depending on complexity and machine availability.
- Finishing/Inspection: Days, depending on requirements.
- 해운: Transit time to your facility.
Typical Lead Time Range: For a moderately complex aerospace fixture requiring standard post-processing (stress relief, bead blast, minor machining), typical lead times might range from 2~6주. Fixtures requiring extensive machining, complex finishing, or advanced NDT could take significantly longer. Rapid prototyping services might offer expedited options at a higher cost.
Understanding these cost and time factors allows for better additive manufacturing pricing comparisons and realistic project scheduling when sourcing custom 3D printed aerospace fixtures.
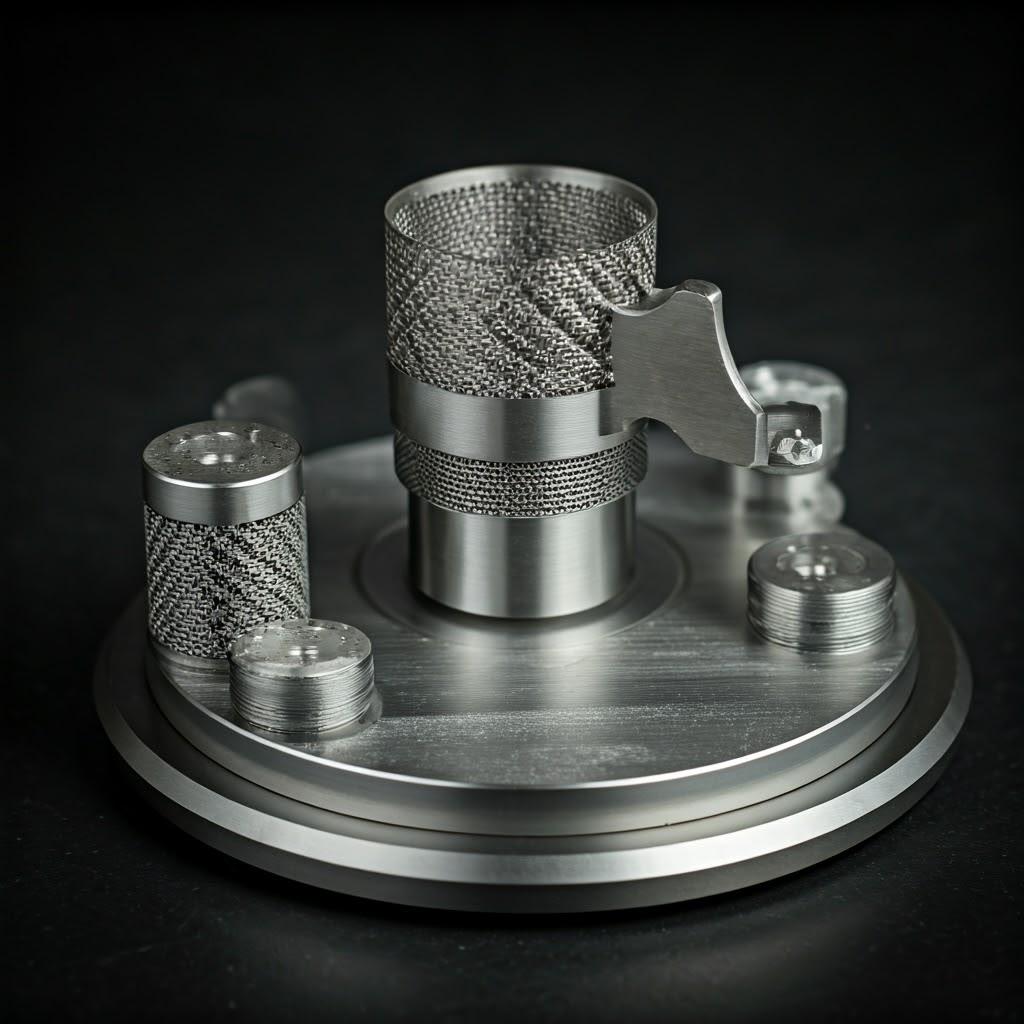
Frequently Asked Questions (FAQ) about 3D Printed Aerospace Test Fixtures
Here are answers to some common questions engineers and procurement managers have about using metal 3D printing for aerospace test fixtures:
- Are 3D printed metal fixtures as strong and durable as machined fixtures?
- Yes, when designed and processed correctly. Metal AM processes like LPBF and EBM can produce fully dense parts (typically >99.5% density) with mechanical properties (yield strength, tensile strength, fatigue life) that are often comparable or even superior to equivalent cast materials, and potentially approaching wrought properties, especially after appropriate post-processing like heat treatment and HIP (if needed). The key is selecting the right alloy (e.g., 316L, Invar), optimizing the design for AM (DfAM), ensuring proper printing parameters, and performing necessary post-processing (like stress relief). For critical applications, properties can be verified using witness coupons printed alongside the fixture.
- What types of aerospace test fixtures are best suited for metal 3D printing?
- Metal AM excels for fixtures that benefit from:
- 복잡한 지오메트리: Tooling with internal channels, conformal shapes, or organic structures derived from topology optimization.
- Low-Volume / Custom Needs: One-off or small batches where traditional tooling costs (molds, dies, complex machining setup) are prohibitive.
- Rapid Turnaround: Situations where lead time is critical, such as rapid prototyping or replacing damaged tooling quickly to minimize downtime.
- Lightweight Requirements: Fixtures for dynamic testing (vibration) or those that need to be handled frequently benefit from AM’s lightweighting capabilities (topology optimization, lattice structures).
- 파트 통합: Redesigning multi-part assemblies into a single printed component to reduce complexity and assembly time.
- Metal AM excels for fixtures that benefit from:
- Can we get material certifications for 3D printed fixtures?
- Yes. Reputable AM service providers specializing in aerospace applications can typically provide comprehensive material documentation. This usually includes:
- Powder Certification: Certificate from the powder manufacturer detailing the chemical composition and specifications of the powder batch used.
- Certificate of Conformance (CoC): A document from the AM provider stating that the part was manufactured according to the specified requirements (drawing, process specifications).
- Witness Coupon Testing (Optional): Mechanical properties (e.g., tensile strength, yield strength, elongation) can be verified by testing witness specimens printed alongside the fixture on the same build plate, with results provided in a test report. Ensure these requirements are discussed and agreed upon with the provider beforehand.
- Yes. Reputable AM service providers specializing in aerospace applications can typically provide comprehensive material documentation. This usually includes:
- Is 3D printing always cheaper than CNC machining for fixtures?
- Not always. The cost-effectiveness depends heavily on complexity, volume, and material.
- AM is often more cost-effective for: Very complex geometries that require extensive multi-axis machining or multiple setups; low volume (e.g., 1-10 units); designs optimized using topology optimization which are difficult to machine.
- CNC Machining is often more cost-effective for: Simpler geometries; larger production volumes; parts where the primary cost driver is raw material bulk rather than machining time.
- A thorough cost analysis comparing AM and traditional methods is recommended for each specific application.
- Not always. The cost-effectiveness depends heavily on complexity, volume, and material.
- What information do I need to provide to get a quote for a 3D printed fixture?
- To get an accurate quote, you should typically provide:
- 3D CAD 모델: In a standard format (e.g., STEP, IGES, STL).
- Technical Drawing (Optional but Recommended): Specifying critical dimensions, tolerances, surface finish requirements, material callout, and any post-processing needs (heat treatment, specific machining areas).
- Material Specification: (e.g., 316L, Invar).
- Quantity Required.
- Required Certifications or Documentation.
- Desired Lead Time.
- To get an accurate quote, you should typically provide:
이 aerospace AM FAQ covers some key considerations, but always feel free to discuss specific project requirements in detail with your chosen AM service provider.
Conclusion: Revolutionizing Aerospace Testing with On-Demand Metal Additive Manufacturing
The aerospace industry’s relentless pursuit of safety, performance, and innovation places immense pressure on testing and validation processes. Custom test fixtures are the bedrock of reliable validation, ensuring that components meet the demanding standards required for flight. Traditionally, the long lead times, design constraints, and high costs associated with machining these bespoke tools have presented significant bottlenecks.
Metal additive manufacturing has emerged as a powerful, transformative solution, fundamentally changing how aerospace test fixtures are conceived, designed, and produced. By enabling the rapid, on-demand production of complex, lightweight, and highly optimized fixtures from high-performance alloys like 316L and Invar, metal 3D printing offers compelling advantages: drastically reduced lead times, unprecedented design freedom through DfAM and topology optimization, potential for part consolidation, and cost-effectiveness, particularly for intricate or low-volume requirements.
From structural and functional testing to environmental validation and MRO tooling, the applications are vast. Leveraging metal AM allows aerospace engineers to iterate faster, procurement managers to source tooling more efficiently, and organizations to accelerate their development cycles while maintaining the highest standards of quality and reliability. While challenges related to design, precision, post-processing, and quality assurance exist, they can be effectively managed by embracing DfAM principles and partnering with experienced, certified suppliers equipped with advanced technologies and robust processes.
Companies like Met3dp are at the forefront of this revolution, providing not only industry-leading AM equipment like advanced SEBM printers but also high-quality, specialized metal powders manufactured using state-of-the-art atomization techniques. By offering comprehensive solutions and deep expertise, Met3dp empowers aerospace organizations to harness the full potential of additive manufacturing.
As the aerospace industry continues to push boundaries, metal 3D printing will undoubtedly play an increasingly vital role in developing and validating the next generation of aircraft and spacecraft. Adopting this technology for custom test fixtures is no longer just an option; it’s a strategic imperative for maintaining competitiveness and enabling innovation in the skies and beyond. Explore how Met3dp’s capabilities can power your organization’s additive manufacturing goals by visiting our website: https://met3dp.com/
.
공유
중국 칭다오에 본사를 둔 선도적인 적층 제조 솔루션 제공업체인 MET3DP Technology Co. 당사는 산업용 3D 프린팅 장비와 고성능 금속 분말을 전문으로 합니다.
관련 기사
Met3DP 소개
최근 업데이트
제품
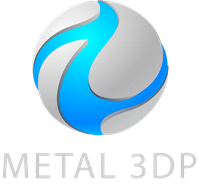
3D 프린팅 및 적층 제조용 금속 분말