Vibration Damper Housings via 3D Printed Titanium
목차
Introduction: Revolutionizing Aerospace Components with 3D Printed Titanium Damper Housings
The aerospace industry stands at the vanguard of technological adoption, relentlessly pursuing innovations that enhance performance, safety, and efficiency. In this quest, materials and manufacturing processes play pivotal roles. Traditional methods, while reliable, often impose limitations on design complexity, material utilization, and production speed, especially for intricate components like vibration damper housings. These critical parts, essential for mitigating potentially damaging vibrations in aircraft, satellites, and other high-performance systems, demand exceptional material properties, precise manufacturing, and increasingly, optimized designs for weight reduction. Enter metal additive manufacturing (AM), specifically leveraging the remarkable properties of titanium alloys like Ti-6Al-4V. The advent of robust 금속 3D 프린팅 technologies, such as Selective Electron Beam Melting (SEBM) and Laser Powder Bed Fusion (LPBF), is not merely an alternative; it’s a revolution, fundamentally reshaping how aerospace components are conceived, designed, and produced.
Vibration damper housings, often intricate structures designed to encapsulate damping mechanisms, protect sensitive equipment, and maintain structural integrity under extreme conditions, present unique manufacturing challenges. They require materials with high strength-to-weight ratios, excellent fatigue resistance, and stability across wide temperature ranges – characteristics inherent to titanium alloys. Furthermore, the need to minimize weight without compromising structural performance is paramount in aerospace, where every gram saved translates into fuel efficiency gains or increased payload capacity. Metal 3D 프린팅 offers an unprecedented solution, enabling the creation of complex, topologically optimized geometries that were previously impossible or prohibitively expensive to manufacture using subtractive methods like CNC machining. By strategically adding material layer by layer directly from CAD data, AM allows engineers to consolidate multiple parts into a single, intricate component, integrate internal channels or lattice structures for enhanced damping or cooling, and tailor designs specifically to the unique vibrational profile of an application.
The shift towards 3D printed titanium for vibration damper housings signifies more than just a manufacturing upgrade; it represents a paradigm shift in aerospace engineering. It empowers designers to achieve levels of optimization and functional integration previously unattainable. Companies specializing in advanced metal powders and printing systems, such as Met3dp, are crucial enablers in this transition. Met3dp, headquartered in Qingdao, China, leverages decades of collective expertise and industry-leading technologies like gas atomization and Plasma Rotating Electrode Process (PREP) to produce high-sphericity, high-flowability titanium powders (including Ti-6Al-4V and its ELI variant) specifically optimized for AM processes. Our advanced SEBM printers deliver the industry-leading print volume, accuracy, and reliability required for mission-critical aerospace parts. This convergence of advanced materials science, sophisticated design tools, and precise manufacturing technology is paving the way for next-generation aerospace systems that are lighter, more robust, and capable of operating under more demanding conditions. For procurement managers and engineers in aerospace, automotive, medical, and industrial manufacturing, understanding the capabilities and implications of 3D printed titanium damper housings is no longer optional—it’s essential for maintaining a competitive edge and driving future innovation. This technology offers a pathway to shorter development cycles, reduced tooling costs, on-demand production, and the creation of superior-performing components that redefine the boundaries of engineering possibility.
What Are Aerospace Vibration Damper Housings Used For?
Vibration is an inherent and often detrimental phenomenon in virtually all aerospace platforms, from commercial airliners and high-performance military jets to helicopters, unmanned aerial vehicles (UAVs), and orbiting satellites. Generated by engines, rotors, aerodynamic forces, and mechanical systems, these vibrations can range from low-frequency structural oscillations to high-frequency noise, impacting passenger comfort, equipment reliability, structural fatigue life, and overall mission success. Aerospace vibration damper housings are specialized enclosures meticulously engineered to house, protect, and integrate various damping mechanisms, playing a critical role in controlling and mitigating these unwanted vibrations across a wide spectrum of applications. Their primary function is to contain the damping element (which could be elastomeric, hydraulic, friction-based, or employ advanced piezoelectric or magnetorheological principles) while providing a secure structural interface with the vibrating system and the platform’s airframe or chassis.
Key Functions and Applications:
- Protecting Sensitive Equipment: Avionics, sensors, optical systems, and other delicate electronic components are highly susceptible to vibrational damage or performance degradation. Damper housings isolate these systems, ensuring their accuracy, longevity, and reliable operation in harsh vibrational environments. Examples include housings for inertial navigation units (INUs), flight control computers, and reconnaissance camera gimbals.
- Enhancing Structural Integrity: Uncontrolled vibrations can lead to fatigue failure in critical structural members. Damper housings, often integrated with tuned mass dampers or other damping systems, help dissipate vibrational energy, reducing stress concentrations and extending the fatigue life of airframes, engine mounts, landing gear components, and rotor systems.
- Improving Passenger and Crew Comfort: In commercial and business aircraft, minimizing cabin noise and vibration is crucial for passenger experience and crew well-being. Damper housings contribute to solutions that isolate engine noise, reduce airframe buzzing, and smooth out turbulence-induced vibrations.
- Stabilizing Payloads: In satellites and spacecraft, micro-vibrations from reaction wheels, cryocoolers, or thruster firings can disrupt sensitive instruments or pointing accuracy. Specialized damper housings are used to isolate scientific instruments, communication antennas, and telescope assemblies, ensuring mission objectives are met.
- Controlling Rotorcraft Vibrations: Helicopters are particularly prone to significant vibrations from main and tail rotors. Damper housings are integral parts of complex vibration control systems designed to counteract these forces, improving handling, reducing pilot fatigue, and minimizing airframe stress.
- Engine Vibration Management: Gas turbine engines generate substantial vibrations. Damper housings are used within engine assemblies and mounting systems to manage these forces, preventing damage to the engine itself and isolating the airframe from excessive vibration transmission.
- Landing Gear Systems: Landing gear experiences significant impact and vibration during takeoff and landing. Damper housings protect shock absorbers and related mechanisms, ensuring smooth operation and structural durability.
Industry-Specific Use Cases:
- Commercial Aviation: Focus on cabin comfort, structural fatigue life extension, and avionics protection. Housings often need to meet stringent regulatory requirements (e.g., FAA, EASA).
- Military Aviation: Emphasis on ruggedness, performance under extreme G-forces and temperatures, protection of mission-critical systems (radar, targeting pods, EW systems), and stealth considerations (vibration reduction contributing to lower acoustic signature).
- Space Applications: High reliability, extreme temperature variations, radiation resistance, outgassing prevention, and precision isolation for scientific instruments or communication payloads are key concerns. Weight is often the most critical factor.
- UAVs/Drones: Weight optimization is paramount for endurance and payload capacity. Housings protect sensitive sensor payloads (cameras, LiDAR) and flight control systems from motor and aerodynamic vibrations.
- Helicopters: Managing intense, complex vibrations from rotor systems is the primary challenge. Housings are key components in active and passive vibration control systems.
The design of these housings is therefore highly application-specific, requiring careful consideration of the vibrational frequencies to be damped, the environmental conditions (temperature, pressure, potential contaminants), the load requirements, the interface points, and, critically, weight and space constraints. Traditionally, manufacturing these often complex shapes from high-strength materials like titanium or specialty steels involved extensive machining from billet, casting followed by machining, or assembling multiple fabricated pieces. These methods often result in significant material waste, limitations on geometric complexity, and longer lead times, making them prime candidates for the disruptive potential of metal additive manufacturing. Procurement specialists seeking aerospace component suppliers need to recognize that partners leveraging AM can offer significant advantages in producing these vital parts.
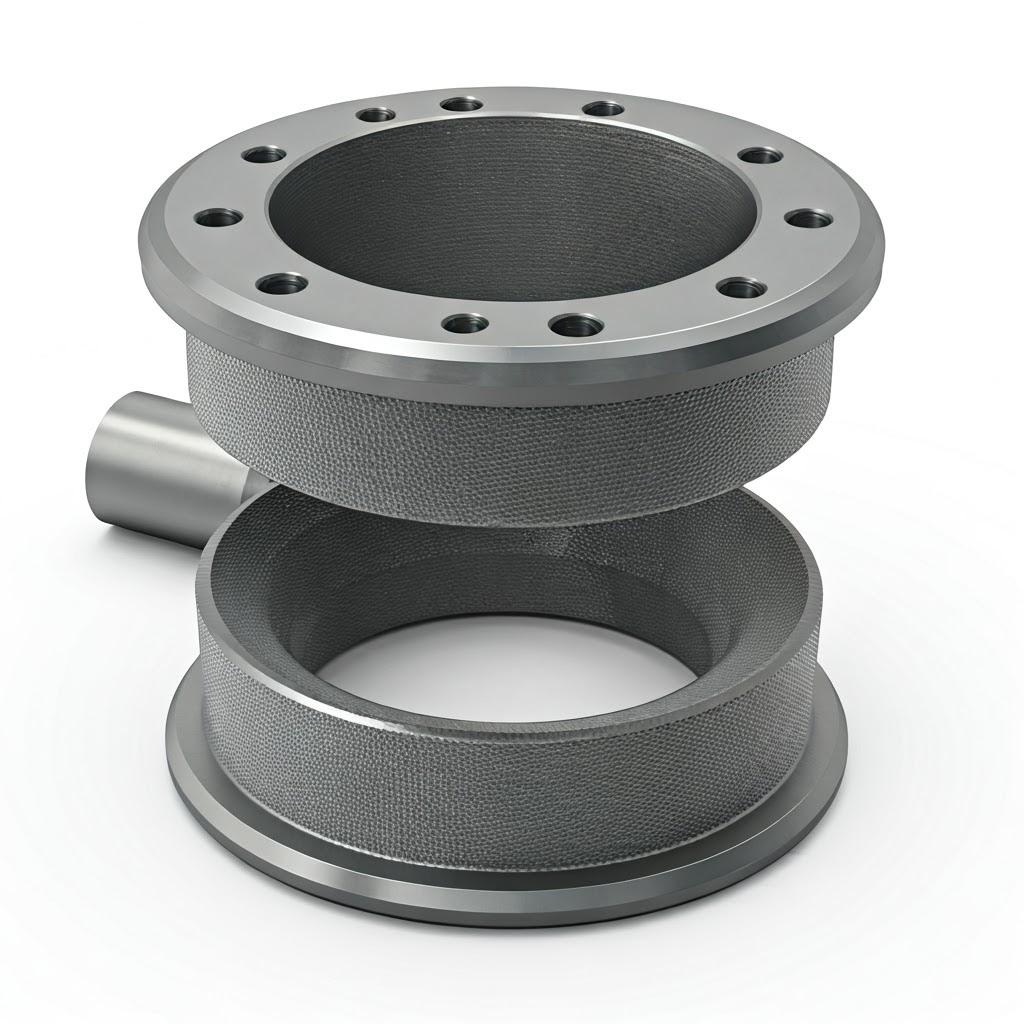
Why Use Metal 3D Printing for Vibration Damper Housings?
The decision to employ metal additive manufacturing (AM) for producing aerospace vibration damper housings stems from a compelling convergence of advantages that directly address the limitations of traditional manufacturing methods while unlocking new possibilities in design and performance. While CNC machining, casting, and fabrication have served the industry well, metal 3D printing, particularly using processes like SEBM or LPBF with materials like Ti-6Al-4V, offers a unique value proposition for these critical components.
Key Advantages of AM for Damper Housings:
- Unprecedented Design Freedom & Complexity:
- 토폴로지 최적화: AM allows engineers to use sophisticated software tools to determine the most efficient material distribution for a given set of load paths and constraints. This results in highly organic, lightweight structures that maintain or even exceed the stiffness and strength of traditionally designed parts, but with significantly less mass. For a damper housing, this means achieving the required structural integrity and vibration isolation with minimal weight penalty – a critical factor in aerospace.
- 파트 통합: Complex assemblies that previously required multiple individual components to be manufactured and then joined (via welding, brazing, or fasteners) can often be redesigned and printed as a single, monolithic piece. This eliminates joints, which can be potential failure points or sources of unwanted vibration, reduces assembly time and cost, simplifies inventory management, and often improves overall structural performance. A multi-part damper housing assembly can potentially become a single, highly optimized 3D printed unit.
- Internal Features & Lattice Structures: AM enables the creation of complex internal channels, voids, and intricate lattice structures within the housing walls. These features can be engineered for specific functions:
- Enhanced Damping: Lattices can be designed to absorb specific vibrational frequencies.
- Integrated Cooling: Internal channels can allow for fluid or air cooling if the damping mechanism generates heat.
- Further Weight Reduction: Lattices provide structural support with minimal material usage.
- 사용자 지정: Each damper housing can be easily customized for specific vibrational profiles or mounting configurations without the need for expensive tooling changes, making AM ideal for low-to-mid volume production runs or specialized applications.
- Significant Weight Reduction:
- As mentioned, topology optimization and lattice structures enabled by AM are primary drivers of weight savings. For aerospace applications, reducing weight directly translates to lower fuel consumption, increased payload capacity, or improved maneuverability. Titanium alloys like Ti-6Al-4V already boast an excellent strength-to-weight ratio, and AM maximizes this benefit by placing material only where it is structurally necessary. Reductions of 20-50% or more compared to traditionally manufactured counterparts are often achievable for complex components like damper housings.
- Accelerated Development & Prototyping:
- AM allows for rapid iteration cycles. Design modifications can be implemented in CAD and a new prototype printed within days or weeks, compared to the months potentially required for tooling adjustments in traditional manufacturing. This speed is invaluable during the development and testing phases of new aerospace platforms or systems, allowing engineers to quickly validate different damping strategies or housing designs.
- Material Efficiency & Reduced Waste:
- Subtractive manufacturing, like CNC machining, starts with a solid block of material and removes large portions, often resulting in significant material waste (buy-to-fly ratio). This is particularly costly with expensive materials like aerospace-grade titanium. Additive manufacturing, being an additive process, uses material much more efficiently, typically only consuming the material needed for the part and the necessary support structures. While some powder recycling and support removal are involved, the overall material waste is considerably lower.
- Supply Chain Advantages:
- 주문형 생산: Parts can be printed as needed, reducing the need for large inventories and warehousing costs.
- Reduced Tooling: AM often eliminates the need for expensive molds, dies, or fixtures associated with casting or complex machining setups.
- Decentralized Manufacturing: Digital part files can be sent electronically to certified AM facilities closer to the point of need, potentially shortening supply chains and lead times.
Comparison with Traditional Methods:
기능 | Metal 3D Printing (e.g., SEBM/LPBF) | CNC 가공 | 투자 주조 | Fabrication/Assembly |
---|---|---|---|---|
자유로운 디자인 | Very High (complex geometries, internal features) | Moderate (limited by tool access, fixtures) | High (complex shapes possible) | Low (limited by joining methods) |
부품 복잡성 | High (ideal for intricate, consolidated parts) | Moderate to High (increases cost/time) | 높음 | 낮음에서 보통 |
Weight Opt. | Excellent (topology opt., lattices) | Good (pocketing, thinning walls) | Moderate (requires uniform wall thickness) | Fair (depends on component design) |
재료 낭비 | 낮음(첨가 공정) | High (subtractive process) | Moderate (runners, gates) | Low (efficient use of sheet/stock) |
리드 타임(프로토) | 빠름(일/주) | Moderate to Fast (depends on complexity) | Slow (tooling required) | Moderate (depends on complexity) |
Lead Time (Prod) | Moderate (scalable, but slower per part than mass prod) | Fast (for established processes) | Moderate to Fast (once tooling exists) | Moderate (assembly time) |
툴링 비용 | None to Low (supports) | Low to Moderate (fixtures) | High (molds) | Low (jigs, fixtures) |
재료 선택 | Growing (Ti alloys, Ni superalloys, Al, Steel) | Very Wide | 와이드 | Very Wide |
부품 통합 | 우수 | 제한적 | 제한적 | Not Applicable (focuses on joining parts) |
이상적인 볼륨 | Low to Mid, Custom | Low to High | Mid to High | Low to High |
시트로 내보내기
While traditional methods remain viable and cost-effective for simpler designs or very high-volume production, metal AM provides a distinct advantage for complex, performance-critical, weight-sensitive components like aerospace vibration damper housings, especially when customization or rapid development is required. Companies like Met3dp, with their expertise in both advanced printing technologies and high-quality powder production, are key partners in realizing these benefits for aerospace manufacturers and suppliers.
Recommended Materials: Ti-6Al-4V & Ti-6Al-4V ELI Deep Dive
The selection of the right material is paramount for aerospace components, and for vibration damper housings subjected to demanding operational conditions, titanium alloys stand out as prime candidates. Specifically, Ti-6Al-4V and its higher purity variant, Ti-6Al-4V ELI (Extra Low Interstitials), are widely adopted in aerospace additive manufacturing due to their exceptional combination of properties perfectly suited for this application. Understanding why these specific alloys matter is crucial for engineers designing these components and for procurement managers sourcing AM services and materials.
Ti-6Al-4V (Grade 5 Titanium): The Workhorse Alloy
Ti-6Al-4V is the most common titanium alloy, accounting for more than 50% of total titanium usage globally. It’s an alpha-beta alloy, meaning its microstructure contains both alpha and beta phases, offering a balance of properties that make it incredibly versatile.
- Key Properties & Benefits for Damper Housings:
- 높은 중량 대비 강도 비율: This is arguably the most significant advantage for aerospace. Ti-6Al-4V offers strength comparable to many steels but at roughly 56% of the density. This allows for significantly lighter damper housings without compromising structural integrity, contributing directly to fuel efficiency and payload capacity.
- 뛰어난 내식성: Titanium naturally forms a stable, protective oxide layer, making it highly resistant to corrosion from atmospheric conditions, saltwater, and many industrial chemicals. This ensures the longevity and reliability of the damper housing, even in harsh operating environments.
- 피로 강도가 좋습니다: Aerospace components, especially those dealing with vibration, are subjected to cyclic loading. Ti-6Al-4V exhibits excellent resistance to fatigue crack initiation and propagation, crucial for the durability of a damper housing.
- High Operating Temperature: It retains good strength at elevated temperatures, typically up to around 315°C (600°F), and performs well at cryogenic temperatures, making it suitable for a wide range of aerospace applications from engine components to spacecraft structures.
- Weldability & Fabricability (Traditional): While AM is the focus, it’s worth noting the alloy is generally weldable and fabricable using conventional techniques, though AM offers unique advantages.
- 생체 적합성: While less critical for damper housings than medical implants, its biocompatibility indicates its non-reactive nature.
Ti-6Al-4V ELI (Grade 23 Titanium): Enhanced Performance
Ti-6Al-4V ELI (Extra Low Interstitials) is a higher-purity version of Grade 5. The primary difference lies in the reduced content of interstitial elements, particularly oxygen and iron. This subtle chemical modification leads to significant improvements in specific properties.
- Key Properties & Benefits (Compared to Grade 5):
- Superior Fracture Toughness: The reduction in interstitial elements significantly enhances the material’s resistance to crack propagation, especially at cryogenic temperatures. This makes Ti-6Al-4V ELI the preferred choice for critical components where fracture is a primary concern, or for applications involving very low temperatures (e.g., spacecraft propellant tanks or structures).
- 향상된 연성: ELI grade exhibits better elongation and reduction of area, meaning it’s more deformable before fracturing.
- 피로 강도 강화: The higher purity generally leads to improved fatigue life compared to standard Grade 5, making it even more suitable for components under high cyclic stress, like vibration damper housings in demanding applications.
- 생체 적합성: Its enhanced properties also make it a primary choice for medical implants.
Why These Titanium Alloys Matter for AM Damper Housings:
The combination of high strength, low density, excellent fatigue resistance, and corrosion resistance makes both Ti-6Al-4V and Ti-6Al-4V ELI ideal for manufacturing lightweight, durable, and reliable vibration damper housings via AM. The choice between Grade 5 and Grade 23 often depends on the specific requirements of the application:
- Choose Ti-6Al-4V (Grade 5) when: General high performance is needed, cost is a significant factor (it’s generally less expensive than ELI), and extreme fracture toughness or cryogenic performance is not the absolute primary driver.
- Choose Ti-6Al-4V ELI (Grade 23) when: Maximum fracture toughness, enhanced fatigue life, superior performance at cryogenic temperatures, or meeting specific stringent aerospace or medical specifications are required. The slightly higher cost is justified by the enhanced properties.
The Role of Powder Quality in AM Performance:
The success of 3D printing these titanium housings heavily relies on the quality of the metal powder used. Key powder characteristics influencing the final part properties include:
- 입자 크기 분포(PSD): Affects powder bed density, flowability, and the resolution of the final part. A controlled PSD is crucial for consistent melting and layer formation.
- 구형성: Highly spherical particles flow better, leading to more uniform powder layers and denser, stronger final parts with fewer voids.
- 흐름성: Essential for uniformly spreading thin layers of powder across the build platform in powder bed fusion processes (LPBF/SEBM). Poor flowability can lead to defects.
- Purity & Chemistry: Must precisely match the alloy specification (e.g., Ti-6Al-4V or ELI). Contaminants like oxygen, nitrogen, or carbon can significantly degrade mechanical properties. Low oxygen content is particularly crucial for titanium alloys.
- Absence of Satellites: Small, irregular particles attached to larger spherical ones (satellites) can hinder flowability and packing density.
Met3dp’s Commitment to Powder Excellence:
This is where a specialized provider like Met3dp becomes critical. Met3dp utilizes advanced production technologies like Vacuum Induction Melting Gas Atomization (VIGA) 및 플라즈마 회전 전극 공정(PREP).
- Gas Atomization (VIGA): Produces fine, spherical powders suitable for processes like LPBF. Met3dp’s equipment employs unique nozzle and gas flow designs to achieve high sphericity and good flowability, crucial for high-resolution parts.
- 플라즈마 회전 전극 공정(PREP): Known for producing exceptionally clean and spherical powders with minimal internal porosity and satellites. This method is particularly advantageous for demanding aerospace and medical applications requiring the highest material integrity, often yielding powders ideal for SEBM processes.
By controlling the entire powder production process, from raw material selection to final powder characterization, Met3dp ensures its Ti-6Al-4V and Ti-6Al-4V ELI powders meet the stringent requirements for aerospace additive manufacturing. Our powders enable customers to 3D print dense, high-quality titanium vibration damper housings with superior mechanical properties, consistency, and reliability, forming the foundation for leveraging the full benefits of AM technology. Partnering with a supplier that understands both the materials science and the printing process is essential for achieving optimal results in demanding applications like aerospace vibration control.
Material Property Comparison (Typical Values for Wrought, AM properties are process-dependent):
속성 | 단위 | Ti-6Al-4V (Grade 5) – Annealed | Ti-6Al-4V ELI (Grade 23) – Annealed | Significance for Damper Housings |
---|---|---|---|---|
밀도 | g/cm³ (lb/in³) | 4.43 (0.160) | 4.43 (0.160) | Low density enables significant weight savings. |
궁극의 인장 강도 | MPa (ksi) | 950 (138) | 860 (125) | High strength ensures structural integrity under load. |
항복 강도(0.2% 오프셋) | MPa (ksi) | 880 (128) | 790 (115) | Resistance to permanent deformation. |
휴식 시 신장 | % | 14 | 18 | Higher ductility (ELI) indicates better formability/toughness. |
Fracture Toughness (K<sub>IC</sub>) | MPa√m (ksi√in) | 55-115 (50-105) | >70 (>64), often higher | ELI grade offers superior resistance to crack propagation. Crucial. |
Fatigue Strength (Rotating Beam, 10<sup>7</sup> cycles) | MPa (ksi) | ~510 (~74) | Often higher than Grade 5 | Critical for components subjected to vibration and cyclic loading. |
탄성 계수 | GPa (Msi) | 114 (16.5) | 114 (16.5) | Stiffness of the material. |
Max Operating Temp. | °C (°F) | ~315 (~600) | ~315 (~600) | Suitability for various aerospace operating environments. |
내식성 | 우수 | 우수 | Ensures longevity and reliability in diverse conditions. |
시트로 내보내기
Note: Properties of AM parts are highly dependent on the specific printing process (LPBF, SEBM), parameters, build orientation, and post-processing (e.g., heat treatment, HIP). The table provides typical values for comparison.
Choosing between Ti-6Al-4V and Ti-6Al-4V ELI, sourced from a reputable powder supplier like Met3dp, ensures that the foundational material properties required for high-performance, 3D printed aerospace vibration damper housings are met, enabling engineers to fully exploit the design and manufacturing advantages of additive manufacturing.
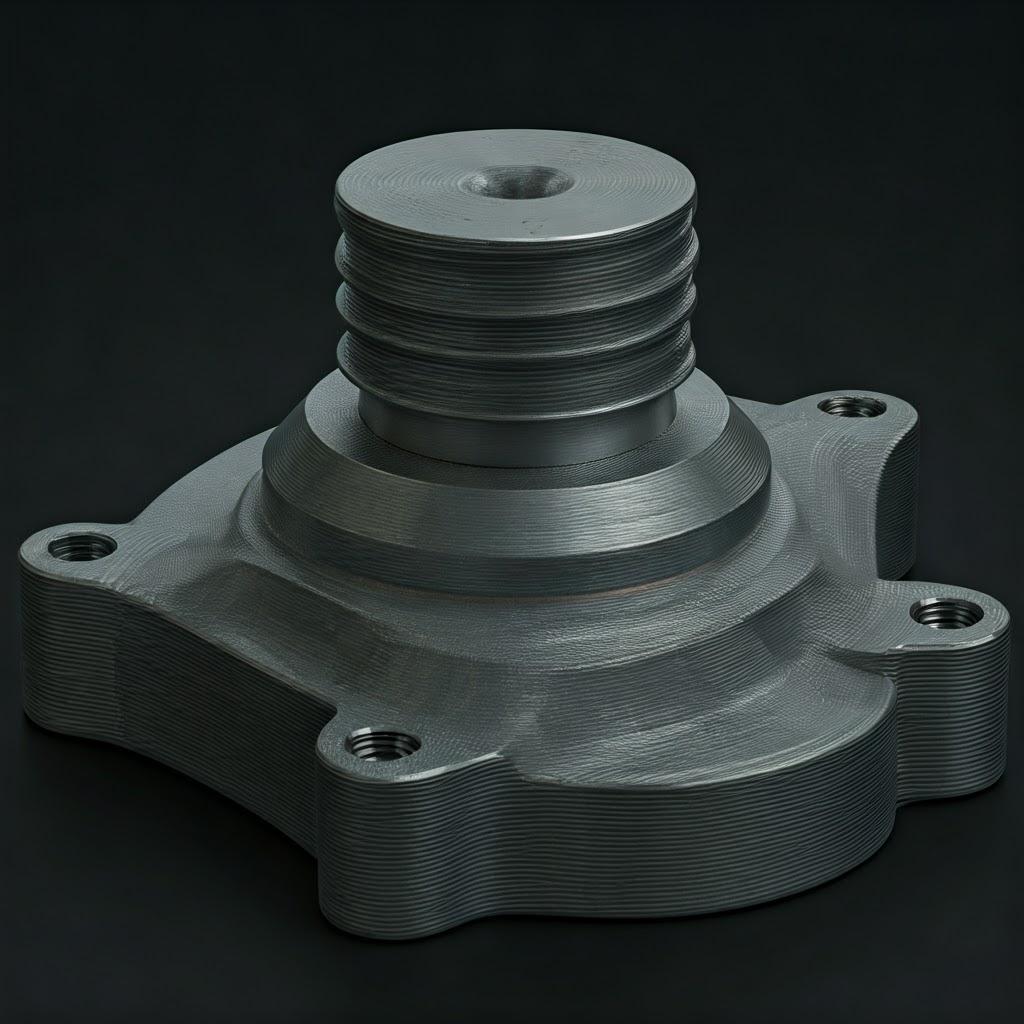
Design Considerations for Additively Manufactured Damper Housings
Transitioning the production of aerospace vibration damper housings from traditional methods to additive manufacturing isn’t just about replicating existing designs with a new technology. To fully harness the power of AM and achieve optimal performance, weight reduction, and cost-effectiveness, engineers must embrace Design for Additive Manufacturing (DfAM) principles. DfAM involves rethinking the design process from the ground up, considering the unique capabilities and constraints of the chosen AM process (like SEBM or LPBF) and material (Ti-6Al-4V / ELI). For damper housings, this means focusing on functional optimization, manufacturability, and lifecycle performance.
Key DfAM Principles for Titanium Damper Housings:
- 토폴로지 최적화:
- 개념: This computational method optimizes material layout within a defined spatial volume for a given set of loads, boundary conditions, and constraints (like stiffness or stress limits). It essentially “carves away” unnecessary material, leaving behind an organic, load-bearing structure.
- Application for Housings: Ideal for reducing the mass of the housing structure while ensuring it can withstand operational loads and effectively transfer vibrational energy to the damping mechanism. This leads to highly efficient, lightweight designs often impossible to machine conventionally. Software tools (e.g., Altair OptiStruct, Ansys Mechanical, nTopology) are used to generate these optimized forms based on FEA (Finite Element Analysis) results.
- 고려 사항: Optimized designs often feature complex, freeform surfaces that are well-suited to AM. However, manufacturability constraints (e.g., minimum feature size, overhang angles) must be incorporated into the optimization process.
- Lattice Structures and Cellular Materials:
- 개념: AM enables the creation of intricate, repeating unit cell structures (lattices) within a part’s volume or skin. These structures can be stochastic (foam-like) or periodic (trusses, gyroids, honeycombs).
- Application for Housings:
- 무게 감소: Replacing solid sections with low-density lattices significantly reduces mass while retaining tailored structural support.
- 진동 감쇠: Specific lattice geometries can be designed to absorb or dissipate vibrational energy at target frequencies, potentially enhancing the housing’s damping contribution.
- 열 관리: Open-cell lattices can improve heat dissipation if the damping mechanism generates significant heat.
- Increased Stiffness-to-Weight Ratio: Certain lattice types offer exceptional stiffness for their density.
- 고려 사항: Lattice design requires specialized software. Ensuring powder removal from intricate internal lattices post-printing is critical. The fatigue performance of lattice structures under aerospace loading conditions needs careful evaluation and validation.
- 파트 통합:
- 개념: Redesigning assemblies of multiple components into a single, integrated part printable in one go.
- Application for Housings: A damper housing assembly might traditionally consist of a main body, cover plates, mounting brackets, and fasteners. DfAM encourages engineers to integrate these elements into a monolithic design. This eliminates fasteners (potential failure points), reduces assembly labor, simplifies inventory, and can improve overall stiffness and sealing.
- 고려 사항: Consolidated designs can become highly complex, potentially increasing print time or requiring more complex support structures. Functional requirements (e.g., access for maintenance) must be maintained.
- Designing for Manufacturability (AM Process Specifics):
- 지원 구조: Most powder bed fusion processes require support structures for overhanging features (typically angles below 45 degrees from the horizontal) and to anchor the part to the build plate, mitigating warping due to thermal stresses.
- Minimizing Supports: Orient the part during build preparation to reduce the need for supports. Design features to be self-supporting where possible (e.g., using chamfers instead of sharp horizontal overhangs).
- Optimizing Supports: Use easily removable support structures (e.g., conical or tree-like supports) and ensure access for removal tools. Consider the impact of support contact points on surface finish. Met3dp’s application engineers can provide guidance on optimal orientation and support strategies for our SEBM systems.
- Overhang Angles and Self-Supporting Features: Understand the critical overhang angle limit for the specific machine/material combination. Design features like internal channels with diamond or teardrop cross-sections to make them self-supporting.
- Minimum Wall Thickness & Feature Size: Adhere to the process limitations regarding the smallest reliable features and thinnest stable walls that can be printed. This varies between LPBF and SEBM and depends on parameters.
- Thermal Management & Residual Stress: Large, bulky features or rapid changes in cross-section can exacerbate thermal gradients during printing, leading to residual stress and potential warping or cracking. DfAM involves designing for more uniform thermal distribution where possible (e.g., smooth transitions, avoiding large solid blocks).
- Powder Removal: Ensure internal channels or complex voids have escape holes for trapped powder removal after printing. This is crucial for lattices and consolidated designs.
- 지원 구조: Most powder bed fusion processes require support structures for overhanging features (typically angles below 45 degrees from the horizontal) and to anchor the part to the build plate, mitigating warping due to thermal stresses.
- Hole Orientation and Quality:
- Vertical holes generally print with better circularity than horizontal holes, which can be slightly distorted (elliptical) due to the layered manufacturing process, especially smaller diameter holes.
- Consider designing critical holes slightly undersized for subsequent reaming or machining to achieve tight tolerances and optimal surface finish.
- Surface Finish Considerations:
- As-printed surfaces have inherent roughness depending on the process (SEBM generally rougher than LPBF initially), layer thickness, and orientation (upward-facing surfaces are typically smoother than downward-facing or side walls).
- Designate critical surfaces that require smoother finishes or tighter tolerances for post-processing (machining, polishing). Factor access for these post-processing steps into the design.
Integrating DfAM with Simulation:
- Process Simulation: Simulating the AM build process can predict thermal behavior, residual stress accumulation, and potential distortion. This allows for design modifications or build strategy adjustments (e.g., optimizing orientation or support structures) before committing to a physical print, saving time and material.
- Performance Simulation: Using FEA to simulate the performance of the AM-designed housing under expected vibrational loads, static loads, and thermal conditions is crucial for validation before physical testing.
By thoughtfully applying these DfAM principles, engineers can leverage metal 3D printing not just as a replacement manufacturing method but as a tool to create superior aerospace vibration damper housings – lighter, stronger, more functionally integrated, and produced more efficiently. Partnering with an experienced AM provider like Met3dp, who understands the nuances of DfAM for titanium alloys and possesses advanced printing capabilities through various 인쇄 방법, is key to successfully navigating the design and manufacturing process.
Achieving Precision: Tolerance, Surface Finish, and Dimensional Accuracy
While metal additive manufacturing offers unparalleled design freedom, a common question from engineers and procurement managers, particularly in the precision-driven aerospace sector, concerns the achievable levels of tolerance, surface finish, and overall dimensional accuracy for components like vibration damper housings. Understanding the capabilities and limitations of AM processes like Selective Electron Beam Melting (SEBM) and Laser Powder Bed Fusion (LPBF) in these areas is crucial for setting realistic expectations and planning necessary post-processing steps.
Understanding the Terminology:
- Tolerance: The permissible limit or limits of variation in a physical dimension of a part. It defines the acceptable range for a feature’s size, form, orientation, or location. Aerospace components often have tight tolerances on critical interfaces and features.
- Surface Finish (Surface Roughness): A measure of the texture of a surface, typically quantified by parameters like Ra (average roughness). It describes the fine-scale irregularities inherent from the manufacturing process. Smooth surfaces are often required for sealing, fatigue performance, or mating interfaces.
- 치수 정확도: How closely the final printed part conforms to the nominal dimensions specified in the original CAD model.
Factors Influencing Precision in Metal AM:
Several factors inherent to the layer-by-layer process influence the final precision of a 3D printed titanium damper housing:
- AM Process Type:
- LPBF(레이저 파우더 베드 퓨전): Generally capable of finer features, thinner layers (typically 20-60 µm), and achieving better as-printed surface finishes (Ra 6-15 µm often cited, but variable). It uses a laser beam with a smaller spot size.
- SEBM(선택적 전자빔 용융): Typically uses thicker layers (50-100 µm) and a higher energy electron beam, resulting in faster build rates but generally rougher as-printed surfaces (Ra 20-40 µm often cited). However, SEBM operates in a vacuum at elevated temperatures, which significantly reduces residual stresses compared to LPBF, potentially leading to better dimensional stability for larger or complex parts, reducing the need for extensive stress relief post-processing. Met3dp specializes in SEBM technology, recognizing its advantages for producing dense, low-stress parts from reactive materials like titanium, ideal for critical applications.
- Machine Calibration & Condition: Regular maintenance and precise calibration of the AM system are essential for consistent accuracy.
- 머티리얼 속성: The specific titanium alloy (Ti-6Al-4V vs. ELI) and, critically, the powder quality (PSD, sphericity, flowability) influence melt pool stability and final part characteristics. Met3dp’s high-quality powders contribute significantly to process stability and part consistency.
- Part Geometry & Size: Larger parts or those with complex geometries are more susceptible to thermal distortion and deviation from the nominal CAD dimensions.
- 빌드 오리엔테이션: The orientation of the part on the build platform significantly impacts surface finish (up-facing vs. down-facing vs. side walls) and dimensional accuracy due to the anisotropic nature of layer-wise building and support structure influence.
- 레이어 두께: Thinner layers generally allow for finer detail and smoother surfaces on curved or angled features but increase build time.
- Scan Strategy: The pattern used by the laser or electron beam to melt the powder affects the microstructure, surface finish, and residual stress.
- Thermal Stresses & Distortion: Temperature gradients during melting and solidification cause internal stresses. If not managed (through build strategy, preheating as in SEBM, or supports), these stresses can lead to warping and dimensional inaccuracies. SEBM’s high build chamber temperature minimizes this significantly.
- 후처리: Stress relief heat treatments can cause minor dimensional changes. Support removal can affect surface finish at contact points. Machining is often used to achieve final tolerances and finishes on critical features.
Typical Achievable Precision (As-Printed):
It’s crucial to note that achievable precision is highly dependent on the specific combination of machine, material, parameters, and part geometry. However, general guidelines are:
- 치수 정확도:
- General tolerances often fall within ±0.1 mm to ±0.3 mm (or ±0.1% to ±0.2% of the dimension) for well-controlled processes. Smaller features might achieve tighter tolerances.
- ISO/ASTM 52900 standards provide frameworks for specifying tolerances for AM parts.
- Surface Roughness (Ra):
- LPBF: As-printed Ra typically ranges from 6 µm to 15 µm, depending on orientation and parameters.
- SEBM: As-printed Ra typically ranges from 20 µm to 40 µm.
- These values are significantly rougher than machined or polished surfaces (which can be < 1 µm Ra).
Strategies for Achieving High Precision:
- Process Selection: Choose the AM process (LPBF or SEBM) that best balances resolution, surface finish requirements, build speed, and material properties for the specific damper housing design.
- DfAM for Precision: Design critical features with precision in mind. Orient the part optimally during build setup. Consider adding machining allowances (extra material) to surfaces that require tight tolerances or smooth finishes achieved through post-machining.
- Optimized Parameters & Build Strategy: Work with an experienced AM provider like Met3dp to utilize optimized, validated parameters and scan strategies for Ti-6Al-4V/ELI that minimize defects and maximize accuracy.
- Post-Processing Machining: For critical dimensions, mating surfaces, sealing faces, or bearing bores requiring tolerances tighter than ±0.1 mm or surface finishes smoother than Ra 5-6 µm, post-print CNC machining is typically necessary. The high accuracy of modern CNC machining can easily achieve sub-micron surface finishes and micron-level tolerances.
- Surface Finishing Techniques: Various techniques can improve the as-printed surface finish without full machining:
- Abrasive Blasting (Sandblasting, Bead Blasting): Provides a uniform matte finish, improving aesthetics and removing loose particles. Can slightly improve Ra.
- 텀블링/진동 마감: Uses abrasive media in a tumbling barrel or vibratory bowl to smooth surfaces and edge-break features. Effective for batches of smaller parts.
- Chemical Polishing/Etching: Can smooth surfaces but requires careful control and handling of chemicals.
- 전기 연마: An electrochemical process that preferentially removes material from peaks, resulting in a very smooth, clean surface. Effective for titanium.
- Micro-Machining / Laser Polishing: Advanced techniques for achieving very smooth surfaces on specific areas.
- Quality Control & Metrology: Implement rigorous quality control procedures using high-precision measurement tools like Coordinate Measuring Machines (CMMs), 3D scanners, and surface profilometers to verify dimensional accuracy and surface finish against specifications.
Conclusion on Precision:
While as-printed metal AM parts may not match the ultra-high precision of CNC machining across all features directly off the printer, they offer a high degree of accuracy suitable for many applications. For aerospace vibration damper housings, a hybrid approach is often optimal: leverage AM’s design freedom and weight reduction capabilities for the overall structure, and incorporate targeted post-machining and finishing steps for critical interfaces and features requiring the highest levels of tolerance and surface quality. Understanding the inherent capabilities of the chosen AM process, utilizing DfAM principles, and planning for necessary post-processing allows engineers to confidently specify and procure high-precision, high-performance damper housings manufactured using titanium AM. Met3dp’s focus on process control, from powder quality to printing parameters on our advanced SEBM systems, provides a solid foundation for achieving excellent dimensional accuracy and material integrity, which can then be refined through appropriate post-processing to meet the most stringent aerospace requirements.
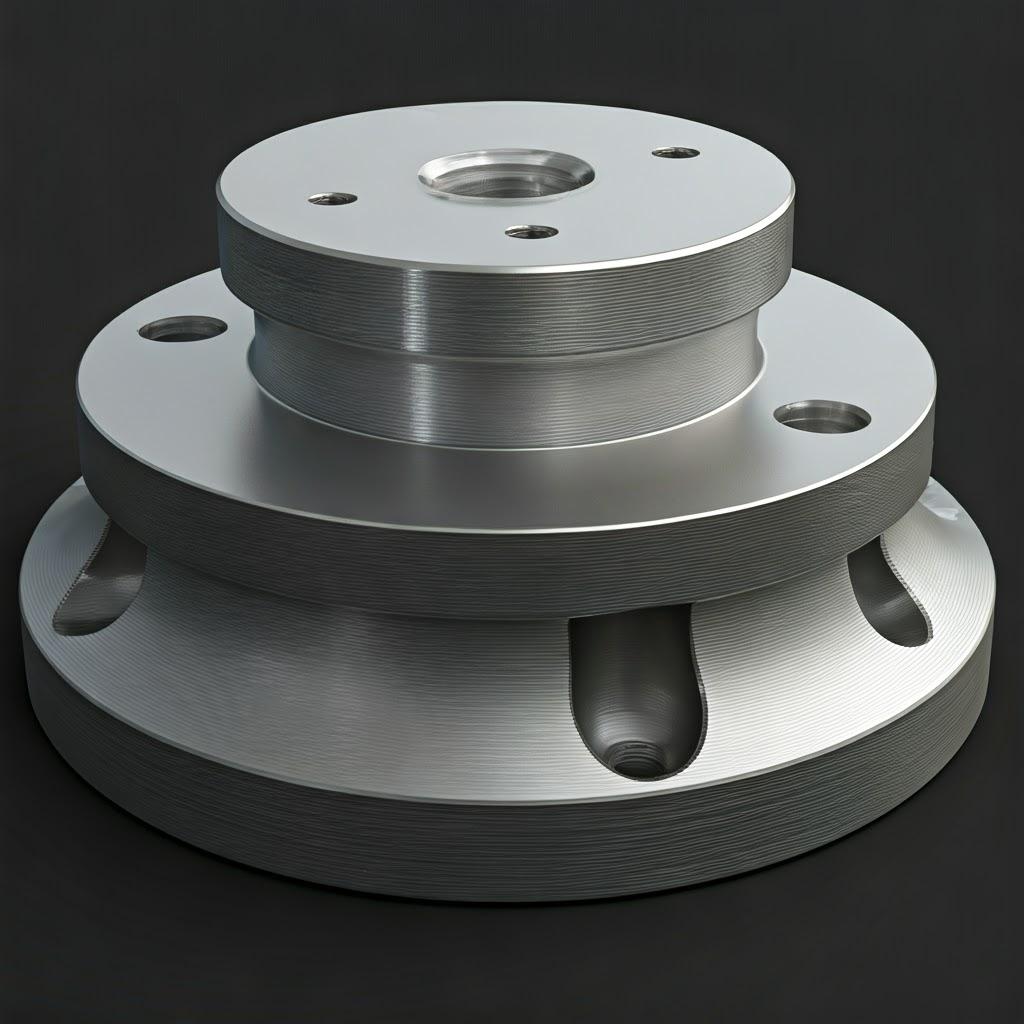
Essential Post-Processing for Titanium Damper Housings
Producing a titanium vibration damper housing using metal additive manufacturing doesn’t end when the part comes out of the printer. A series of essential post-processing steps are typically required to transform the as-printed component into a flight-ready, fully functional aerospace part. These steps are crucial for achieving the desired material properties, dimensional accuracy, surface finish, and overall reliability demanded by the aerospace industry. Engineers and procurement managers must factor these processes into their project planning, timelines, and cost estimations.
Common Post-Processing Steps for AM Titanium Housings:
- Powder Removal / Depowdering:
- 목적: To remove any unfused metal powder trapped within internal channels, lattice structures, or adhering to the part’s surface.
- 방법: Typically involves manual brushing, compressed air blow-off, ultrasonic cleaning baths, or specialized depowdering stations. For complex internal geometries, careful planning (including escape holes in the design phase) and thorough execution are vital. Incomplete powder removal can add weight, potentially compromise performance, and become loose contamination later.
- 고려 사항: Titanium powder is reactive and requires careful handling, often under inert gas conditions, especially for fine powder recovery and recycling, to prevent contamination (particularly oxygen pickup).
- 스트레스 완화 열처리:
- 목적: To reduce the internal residual stresses generated during the rapid heating and cooling cycles inherent in the AM process (especially significant in LPBF). High residual stresses can cause distortion during or after printing, cracking, and reduced fatigue life.
- 방법: The part is heated in a vacuum or inert atmosphere furnace to a specific temperature (typically below the beta transus temperature for Ti-6Al-4V, e.g., 595°C – 840°C / 1100°F – 1550°F, depending on the goal), held for a period, and then slowly cooled.
- 고려 사항: This is almost always required for LPBF titanium parts 전에 removal from the build plate to prevent distortion. SEBM parts, built at elevated temperatures, have significantly lower residual stress, often requiring less intensive or no stress relief before plate removal, which is a key advantage of the SEBM process employed by Met3dp. However, a post-build heat treatment might still be performed to optimize microstructure and mechanical properties. Precise control of temperature and atmosphere is critical to avoid detrimental phase changes or contamination (like alpha case formation).
- 빌드 플레이트에서 파트 제거:
- 목적: To separate the printed housing(s) and their support structures from the metal build plate they were fused to during printing.
- 방법: Typically done using wire Electrical Discharge Machining (EDM) or a band saw. Wire EDM provides a cleaner cut with minimal mechanical stress on the part.
- 고려 사항: Care must be taken not to damage the part during removal. The build plate can often be resurfaced and reused.
- 지원 구조 제거:
- 목적: To remove the temporary support structures required during the build.
- 방법: Can involve manual breaking (for easily snappable designs), cutting with hand tools, CNC machining, or sometimes wire EDM for difficult-to-access supports.
- 고려 사항: This step can be labor-intensive and time-consuming, especially for complex parts with intricate supports. It can leave witness marks or rough areas on the part surface where supports were attached, often requiring further finishing. Designing for minimal and easily removable supports (DfAM) is crucial.
- 열간 등방성 프레싱(HIP):
- 목적: To eliminate internal porosity (voids) within the printed material and further improve density, fatigue life, ductility, and fracture toughness. HIP subjects the part to high temperature (below the melting point but often near stress relief temperatures) and high inert gas pressure (e.g., Argon) simultaneously. The pressure collapses internal voids, diffusion bonding the material across the void interfaces.
- 방법: Performed in specialized HIP vessels. Parts are heated under high isostatic pressure (typically 100-200 MPa / 15-30 ksi) for several hours.
- 고려 사항: HIPing is common, often mandatory, for critical aerospace components, including fatigue-critical parts like damper housings, to achieve maximum material integrity and properties comparable or superior to wrought or cast materials. It adds cost and time but significantly enhances reliability. It can cause minor dimensional changes that need to be accounted for.
- Solution Treatment & Aging (STA) Heat Treatment (Optional/Specific):
- 목적: To further optimize the microstructure and mechanical properties (primarily strength) of Ti-6Al-4V beyond what stress relief or HIP provides. Involves heating above the beta transus, quenching, and then aging at a lower temperature.
- 방법: Requires precise control over heating temperatures, soak times, cooling rates (quenching), and aging parameters.
- 고려 사항: STA generally increases strength but can potentially reduce ductility or fracture toughness compared to an annealed or HIPed condition. The necessity depends entirely on the specific performance requirements of the damper housing. Often, the properties achieved through optimized printing, stress relief, and HIP are sufficient.
- 가공:
- 목적: To achieve final dimensional tolerances on critical features (e.g., mounting interfaces, bearing bores, sealing surfaces) and improve surface finish where required.
- 방법: Utilizes conventional CNC milling, turning, grinding, or drilling operations.
- 고려 사항: Requires careful fixture design to hold the potentially complex AM part without distortion. Machining allowances must be included in the AM design phase for surfaces requiring machining. Titanium can be challenging to machine, requiring appropriate tooling, speeds, and feeds.
- 표면 마감:
- 목적: To achieve the desired surface texture for aesthetic, functional (e.g., sealing, fatigue, flow), or coating preparation purposes.
- 방법: As detailed previously – abrasive blasting, tumbling, chemical polishing, electropolishing, manual grinding/polishing.
- 고려 사항: The choice of method depends on the required finish level, part geometry, cost, and batch size.
- Cleaning & Inspection:
- 목적: Final cleaning to remove any machining fluids, polishing compounds, or debris. Rigorous inspection ensures the part meets all dimensional, surface finish, and material integrity specifications.
- 방법: Aqueous or solvent cleaning, ultrasonic cleaning. Inspection methods include CMM, 3D scanning, surface profilometry, visual inspection, Non-Destructive Testing (NDT) like X-ray or CT scanning (to verify internal integrity and check for residual powder or defects), and potentially penetrant testing for surface crack detection.
- 고려 사항: NDT is particularly important for verifying the internal soundness of critical aerospace parts, especially after HIP.
Workflow Integration:
The sequence of these steps is important. For example, stress relief (especially for LPBF) must happen before build plate removal. HIP is typically performed after support removal but before final machining, as HIP can cause slight shrinkage. Final machining and surface finishing are usually among the last steps before final cleaning and inspection.
Understanding this comprehensive post-processing workflow is vital for accurately assessing the total lead time and cost associated with producing aerospace-grade titanium vibration damper housings via AM. While the printing itself might be relatively fast, these downstream steps add significant time and value. Partnering with a vertically integrated provider or a network of trusted suppliers capable of managing these steps efficiently is crucial. Met3dp, with its deep understanding of the entire 금속 3D 프린팅 ecosystem, from powder to finished part, assists clients in navigating these post-processing requirements to ensure components meet the exacting standards of the aerospace industry.
Common Challenges in 3D Printing Damper Housings & Mitigation Strategies
While metal additive manufacturing offers transformative potential for producing components like titanium vibration damper housings, the technology is not without its challenges. Recognizing these potential hurdles early in the design and manufacturing planning stages, and implementing effective mitigation strategies, is key to successfully producing high-quality, reliable aerospace parts. Many of these challenges are interconnected, often stemming from the complex thermal dynamics inherent in melting and solidifying metal powder layer by layer.
Common Challenges & How to Avoid Them:
- Residual Stress and Warping/Distortion:
- 도전: Rapid heating and cooling cycles during printing create temperature gradients, leading to internal stresses within the part. These stresses can cause the part to warp or distort during the build, after removal from the build plate, or during post-processing (like support removal). This is generally more pronounced in LPBF than SEBM due to the lower process temperature and faster cooling rates in LPBF.
- 완화 전략:
- Process Selection: SEBM, operating at elevated temperatures (e.g., 600-700°C for Ti-6Al-4V), inherently minimizes residual stress compared to LPBF. Met3dp’s expertise in SEBM is a significant advantage here.
- Optimized Build Orientation & Supports: Careful orientation can balance thermal gradients. Robust support structures anchor the part and help dissipate heat, resisting warping forces.
- Optimized Scan Strategy: Using techniques like island scanning or checkerboard patterns can distribute heat input more evenly.
- 스트레스 완화 열처리: Performing a controlled heat treatment cycle (often mandatory for LPBF before plate removal) relaxes internal stresses.
- Process Simulation: Simulating the build can predict stress accumulation and distortion, allowing for pre-compensation in the design or adjustments to the build strategy.
- DfAM: Avoiding large, solid cross-sections and incorporating smooth transitions can reduce stress concentrations.
- Porosity (Gas Porosity & Lack-of-Fusion Voids):
- 도전: Small voids or pores can become trapped within the printed material. Gas porosity arises from dissolved gases in the melt pool coming out of solution during solidification. Lack-of-fusion porosity occurs when the energy input is insufficient to completely melt and fuse powder particles or successive layers. Porosity degrades mechanical properties, particularly fatigue life, and is unacceptable in critical aerospace components.
- 완화 전략:
- High-Quality Powder: Using powder with low trapped gas content and controlled PSD, like those produced by Met3dp using PREP or advanced VIGA, is crucial. Proper powder handling to avoid moisture or atmospheric contamination is also vital.
- Optimized Process Parameters: Precise control over energy density (beam power, scan speed, hatch spacing, layer thickness) is key to achieving full melting and fusion without overheating (which can increase gas porosity). Extensive parameter development and validation are necessary.
- Vacuum Environment (SEBM): SEBM’s high vacuum environment minimizes the pickup of atmospheric gases during printing.
- 열간 등방성 프레싱(HIP): HIP is highly effective at closing internal porosity (both gas and lack-of-fusion), significantly improving material integrity and fatigue performance. It is often considered standard practice for critical AM aerospace parts.
- 비파괴 검사(NDT): X-ray radiography or Computed Tomography (CT) scanning can detect internal porosity in finished parts.
- Support Structure Removal Difficulties & Surface Quality:
- 도전: Supports, while necessary, can be difficult and time-consuming to remove, especially from complex internal geometries or delicate features. Removal processes can potentially damage the part or leave undesirable witness marks on the surface, requiring further finishing.
- 완화 전략:
- DfAM for Supports: Design the part to be self-supporting as much as possible. Optimize orientation to minimize the volume and complexity of supports needed.
- Optimized Support Design: Use support structures specifically designed for easier removal (e.g., smaller contact points, perforations, lower density supports where possible). Software tools offer various strategies.
- Process Selection: SEBM often requires fewer, less dense supports than LPBF due to the powder sintering providing some self-support and lower thermal gradients.
- Appropriate Removal Techniques: Use the right tools and methods (manual breaking, cutting, machining, EDM) based on the support type and location.
- Post-Finishing: Plan for necessary grinding, blending, or machining to clean up support interface points on critical surfaces.
- 표면 거칠기:
- 도전: As-printed surfaces, particularly with SEBM or on downward-facing/side surfaces in LPBF, can be rougher than required for certain applications (e.g., sealing, fatigue-critical areas, aerodynamic surfaces). The “stair-stepping” effect on angled surfaces is also inherent.
- 완화 전략:
- Orientation: Orient critical surfaces upwards or optimize the angle to minimize roughness where possible.
- 매개변수 최적화: Finer layer thicknesses (in LPBF) and optimized contour scans can improve finish, though potentially at the cost of build time.
- 후처리: Implement appropriate surface finishing techniques (blasting, tumbling, polishing, machining) as required by the design specifications. See previous section.
- Machining Allowance: Include extra material in the design for surfaces that need to be machined to achieve a specific smooth finish.
- 치수 정확도 및 반복성:
- 도전: Achieving and consistently repeating tight dimensional tolerances across multiple builds or machines can be challenging due to the many variables influencing the process (thermal effects, machine calibration, powder variations, etc.).
- 완화 전략:
- Robust Quality Management System (QMS): Implement stringent process controls, regular machine calibration and maintenance, and thorough powder management protocols (tracking, testing, recycling procedures). AS9100 certification is often required for aerospace suppliers.
- 프로세스 모니터링: In-situ monitoring tools (thermal cameras, melt pool monitoring) can provide real-time data to help ensure process stability.
- Process Validation: Thoroughly validate the entire process (machine, material, parameters, post-processing) for the specific part before starting production.
- Post-Machining: Rely on post-machining for features requiring the highest level of accuracy and repeatability.
- Experienced Provider: Partnering with an established AM provider like Met3dp, with deep process knowledge and robust quality systems, is crucial.
- Powder Handling and Contamination:
- 도전: Titanium powders are sensitive to contamination, particularly by oxygen and nitrogen, which can embrittle the material. Handling fine metal powders also poses safety considerations (flammability, inhalation). Cross-contamination between different alloy types must be avoided.
- 완화 전략:
- 제어 환경: Handle and store powder under inert gas (Argon) or vacuum conditions.
- Proper PPE: Use appropriate personal protective equipment when handling powders.
- 파우더 수명 주기 관리: Implement strict procedures for powder loading, unloading, sieving, recycling (testing reused powder chemistry and morphology), and traceability.
- Dedicated Equipment: Use dedicated equipment (sieves, containers, potentially even printers) for specific materials where possible to avoid cross-contamination.
Addressing these challenges requires a holistic approach, combining intelligent design (DfAM), careful process selection, rigorous process control, appropriate post-processing, and robust quality assurance. Success in 3D printing critical components like aerospace vibration damper housings relies heavily on the expertise and capabilities of the manufacturing partner. Met3dp’s focus on high-quality powder production, advanced SEBM printing technology, and comprehensive application support helps clients navigate these challenges effectively, delivering reliable, high-performance titanium components.
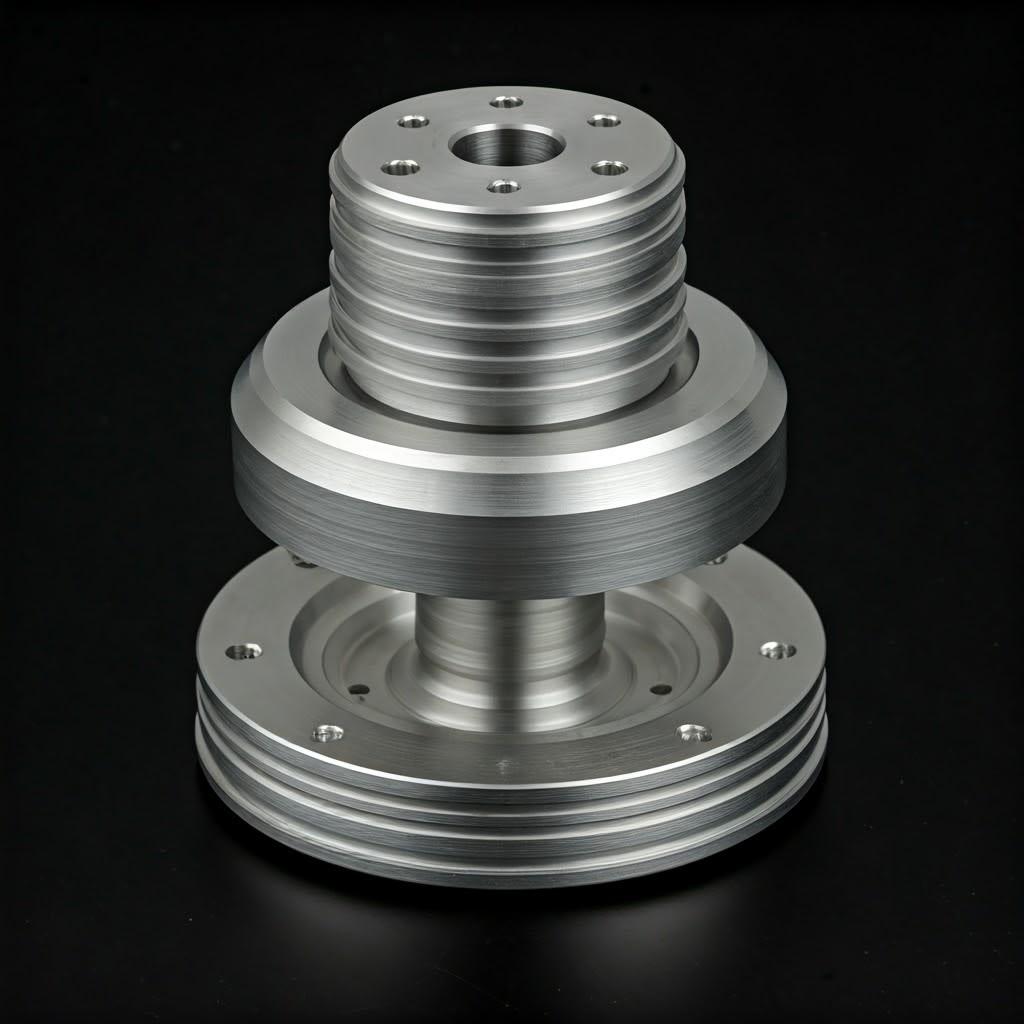
How to Choose the Right Metal 3D Printing Service Provider for Aerospace Housings
Selecting the right additive manufacturing partner is as critical as the design and material selection when producing high-stakes components like aerospace vibration damper housings. The quality, reliability, and airworthiness of the final part depend heavily on the capabilities, expertise, and quality systems of your chosen service provider. For engineers and procurement managers navigating the complex landscape of metal AM suppliers, a structured evaluation process focusing on key criteria is essential. Not all providers offering “metal 3D printing” possess the specific expertise and certifications required for demanding aerospace applications, particularly with reactive materials like titanium.
Key Criteria for Evaluating Aerospace AM Suppliers:
- Aerospace Certifications & Quality Management System (QMS):
- AS9100 Certification: This is the internationally recognized QMS standard for the aerospace industry. Certification to AS9100 (or equivalent, e.g., EN 9100) demonstrates that the provider has implemented rigorous processes for traceability, configuration management, risk management, process control, and continuous improvement, specifically tailored to aerospace requirements. It is often a non-negotiable requirement for flight-critical or structural components.
- ISO 9001 Certification: While foundational, ISO 9001 alone is generally insufficient for primary aerospace manufacturing. However, it indicates a baseline commitment to quality management.
- Nadcap Accreditation: While AS9100 covers the overall QMS, Nadcap (National Aerospace and Defense Contractors Accreditation Program) provides specific accreditation for special processes like heat treating, materials testing, welding, and increasingly, additive manufacturing. Nadcap AM accreditation signifies a high level of process control and technical competence specific to AM.
- Robust QMS: Beyond certifications, evaluate the provider’s internal quality manual, procedures for process validation, non-conformance handling, corrective actions, and metrology capabilities. Ask for evidence of process stability and repeatability.
- Material Expertise & Handling:
- Titanium Specialization: Does the provider have specific, demonstrable experience printing Ti-6Al-4V and Ti-6Al-4V ELI? Working with titanium requires specialized knowledge due to its reactivity and specific processing needs.
- Powder Sourcing & Management: Where do they source their powder? Do they have stringent incoming inspection procedures? What are their protocols for powder handling, storage (inert atmosphere), sieving, blending, and recycling to prevent contamination and ensure consistency? Traceability of powder batches back to the raw material source is critical. Companies like Met3dp, which manufacture their own 고품질 금속 분말, offer a distinct advantage in controlling this crucial input variable.
- Material Property Validation: Can they provide material test data (tensile, fatigue, chemistry) from witness coupons printed alongside actual parts, demonstrating that the final material properties meet aerospace specifications (e.g., AMS standards)?
- Technology & Equipment Capability:
- Appropriate AM Technology: Do they operate the right type of AM technology (e.g., SEBM, LPBF) for your specific housing design and requirements? Do they have experience with the specific challenges and benefits of that technology for titanium? Met3dp’s specialization in SEBM offers advantages in reduced residual stress and suitability for reactive materials like titanium.
- Machine Park & Condition: What specific machine models do they operate? Are the machines well-maintained and calibrated? What is their build volume capacity? Do they have sufficient machine capacity to handle your production volume requirements (from prototypes to serial production)? Redundancy (multiple machines) is important for mitigating downtime risks.
- Process Monitoring & Control: What level of in-situ process monitoring (e.g., melt pool monitoring, thermal imaging) do they employ? How do they ensure consistent parameter control build after build?
- Post-Processing Capabilities:
- 인하우스 대 아웃소싱: Does the provider offer essential post-processing steps like stress relief, HIP, support removal, machining, and surface finishing in-house, or do they rely on qualified subcontractors? In-house capabilities can streamline the workflow, reduce lead times, and simplify quality management.
- Expertise in Post-Processing: Do they have proven expertise in the specific post-processing required for titanium AM parts (e.g., vacuum heat treatment, HIP parameters for AM titanium, titanium machining)? If outsourcing, how do they manage the quality and traceability of these external processes? Nadcap accreditation for these processes (whether in-house or at the subcontractor) is highly desirable.
- Technical Expertise & Application Support:
- Engineering Team: Does the provider have experienced materials scientists, process engineers, and design engineers who understand DfAM principles and can provide technical support? Can they assist with design optimization, build orientation strategy, support structure design, and troubleshooting?
- Aerospace Experience: Do they have a proven track record of successfully producing parts for the aerospace industry? Can they provide case studies or references (within confidentiality limits)? Understanding the specific documentation and validation requirements of aerospace projects is crucial. Met3dp brings decades of collective expertise in metal AM, partnering with organizations to accelerate their adoption of the technology for demanding applications. Learn more 우리에 대하여.
- Metrology & Inspection Capabilities:
- 장비: Do they possess the necessary metrology equipment (CMMs, 3D scanners, surface profilometers) to accurately measure and verify part dimensions and surface finish against specifications?
- NDT Capabilities: Do they offer or have certified partners for Non-Destructive Testing (NDT) methods like X-ray or CT scanning, essential for verifying internal integrity and detecting defects like porosity in critical aerospace parts?
- Lead Time & Responsiveness:
- Quoting Process: Is their quoting process clear, detailed, and timely?
- Production Lead Times: Can they provide realistic lead time estimates for prototypes and production runs, factoring in all necessary printing and post-processing steps?
- Communication: Are they responsive to inquiries and proactive in communicating project status?
- Cost & Value:
- While cost is always a factor, it should be evaluated in the context of quality, reliability, and overall value. The cheapest option may not provide the necessary quality assurance or technical expertise for aerospace components.
- Request detailed quotes that break down costs associated with printing, materials, support removal, heat treatment, HIP, machining, finishing, and inspection.
Supplier Evaluation Checklist:
기준 | 주요 질문 | Ideal Response / Evidence |
---|---|---|
Certifications & QMS | AS9100 certified? Nadcap AM/Heat Treat/NDT accredited? Robust internal QMS documentation? Traceability procedures? | AS9100 cert visible, Nadcap scope covers needed processes, clear QM, demonstrated traceability |
Material Expertise (Ti) | Experience with Ti-6Al-4V / ELI? Powder source & control? Handling procedures? Material testing capability & data? | Specific Ti project examples, controlled powder management, test reports meeting AMS specs |
기술 및 장비 | Appropriate AM tech (SEBM/LPBF)? Machine models & condition? Build volume? Capacity/Redundancy? Process monitoring? | Relevant tech (e.g., Met3dp SEBM), well-maintained modern machines, sufficient capacity |
포스트 프로세싱 | In-house capabilities (Heat Treat, HIP, Machining)? Expertise in Ti post-processing? Qualified subcontractors (if used)? | In-house preferred, demonstrated expertise/Nadcap for processes, strong supplier management |
Technical Support & Experience | Engineering team expertise (DfAM, Materials)? Aerospace project track record? Application support availability? | Experienced engineers, relevant case studies, collaborative approach (e.g., Met3dp team) |
Metrology & Inspection | CMM, 3D scanning, profilometry available? NDT capabilities (X-ray/CT)? Calibration program? | Comprehensive calibrated equipment, certified NDT capabilities |
Lead Time & Responsiveness | Clear quotes? Realistic lead times quoted? Proactive communication? | Transparent pricing, reliable timelines, responsive points of contact |
비용 및 가치 | Detailed cost breakdown? Competitive pricing relative to quality/service? | Clear value proposition, cost justified by quality and reliability |
Location & Logistics (Optional) | Geographic location impact on shipping/communication? Export control compliance (if applicable)? | Suitable logistics, ITAR/EAR compliance if needed |
Company Stability & Reputation | How long in business? Financial stability? Customer references/testimonials? | Established provider, positive industry reputation (e.g., Met3dp’s leadership position) |
시트로 내보내기
Choosing the right supplier involves careful due diligence, including facility audits, technical discussions, and potentially sample part evaluations. For critical aerospace components like vibration damper housings, prioritizing quality, expertise, and robust process control over solely cost considerations is paramount to ensuring mission success and safety.
Understanding Cost Factors and Lead Times for Production
While the performance benefits of 3D printed titanium vibration damper housings are compelling, understanding the associated cost drivers and typical lead times is crucial for project budgeting, planning, and procurement decisions. Metal additive manufacturing involves a different cost structure compared to traditional methods, and accurately estimating project timelines requires considering the entire workflow, from design finalization to final inspection.
Key Cost Factors in Metal AM:
- 재료비:
- 파우더 가격: Aerospace-grade titanium powders (Ti-6Al-4V, Ti-6Al-4V ELI) are inherently expensive due to the energy-intensive processes required for extraction, alloying, and atomization (like PREP or VIGA used by Met3dp). ELI grades are typically more expensive than standard Grade 5 due to the higher purity requirements.
- 파우더 소비량: The primary cost is the amount of powder consumed to print the part itself. However, costs also include powder used for support structures and potential losses during handling and recycling. Efficient nesting of multiple parts within a single build can help optimize powder usage relative to machine time.
- 파우더 재활용: While powder recycling is standard practice to reduce costs, there are associated costs for sieving, testing, and managing recycled powder batches to ensure quality. There’s also a limit to how many times powder can be effectively recycled before its properties (like morphology or oxygen content) degrade.
- AM Machine Time:
- Hourly Rate: AM service providers typically charge based on the time the machine is occupied printing the parts. This rate incorporates machine depreciation, energy consumption, maintenance, software licenses, and facility overheads. SEBM machines, while potentially having faster volume build rates, are complex systems, impacting the hourly rate.
- 구축 시간: This is determined by:
- Part Volume: Larger or more solid parts naturally take longer to print.
- Part Height: Build time is directly related to the number of layers required. Taller parts take longer.
- 레이어 두께: Thinner layers increase resolution but significantly increase the number of layers and thus build time.
- Scan Strategy & Parameters: Optimized parameters balance speed and quality.
- Nesting Efficiency: How many parts can be efficiently packed onto the build plate per run influences the machine time allocated per part.
- 인건비:
- 사전 처리: CAD file preparation, build setup (orientation, support generation), and machine loading require skilled technician/engineer time.
- 후처리: This is often the most labor-intensive part. Powder removal, stress relief, part removal, support removal, machining, surface finishing, cleaning, and inspection all require significant hands-on effort by skilled personnel. The complexity of the part and its support structures directly impacts this cost.
- 후처리 비용:
- Heat Treatment (Stress Relief / HIP / STA): Requires specialized furnaces (vacuum/inert atmosphere) and HIP vessels, consuming energy and time. HIPing, in particular, is a significant cost addition but often necessary for aerospace quality.
- 가공: Costs depend on the complexity of the required machining operations, the amount of material to be removed, the required tolerances, and CNC machine time/programming.
- 표면 마감: Costs vary widely depending on the chosen method (blasting, tumbling, polishing) and the required final finish specification.
- Consumables: Costs associated with cutting tools, abrasive media, cleaning agents, etc.
- Quality Assurance & Inspection:
- Costs associated with metrology (CMM, scanning), NDT (X-ray/CT), material testing (witness coupons), documentation, and quality personnel time. The level of inspection required by aerospace standards adds to the overall cost.
- Design & Engineering:
- While potentially an internal cost, complex DfAM, topology optimization, and process simulation require specialized software and engineering expertise, which contributes to the overall project cost, especially during development phases.
- Quantity & Scale:
- 프로토타이핑: One-off prototypes are typically expensive due to setup costs not being amortized.
- Serial Production: As production volume increases, per-part costs tend to decrease due to efficiencies in build nesting, optimization of post-processing workflows, and amortization of setup/programming costs. However, AM typically remains more expensive per part than traditional mass production methods like casting for very high volumes of simple parts. Its strength lies in complex, low-to-mid volume, or customized components.
Factors Influencing Lead Times:
Lead time encompasses the entire duration from order placement (or finalized design) to delivery of the finished, inspected part.
- Quoting & Order Processing: Initial communication, technical review, quote generation, and order confirmation take time. (Typically days)
- 빌드 준비: Final CAD checks, support generation, build file creation, and scheduling machine time. (Typically days)
- 인쇄 시간: Varies significantly based on part size, complexity, nesting, and chosen AM process/parameters. (Can range from hours for very small parts to many days or even weeks for large/complex builds).
- Cooling & Depowdering: Machine cool-down time post-build, followed by careful powder removal. (Typically hours to a day)
- 스트레스 해소: Furnace cycle time, including heating, soaking, and controlled cooling. (Typically 1-2 days, including setup)
- Build Plate Removal & Support Removal: Time required for cutting parts off the plate and subsequent manual or automated support removal. Highly variable based on complexity. (Hours to days)
- 열간 등방성 프레싱(HIP): HIP cycle times are long (often 8-12 hours or more, plus heat-up/cool-down). Scheduling access to HIP units (which are often shared resources or external services) can also add significant time. (Typically adds several days to a week or more, including logistics if outsourced).
- 가공: Depends on the extent and complexity of machining required. CNC programming and setup also take time. (Days to weeks)
- 표면 마감: Varies based on the method and required finish. (Hours to days)
- 검사 및 품질 보증: Time for CMM, NDT, material testing, and final documentation review. (Days)
- Shipping & Logistics: Transit time to the customer.
Typical Overall Lead Times:
- 프로토타입: For a moderately complex titanium aerospace housing requiring standard post-processing (stress relief, support removal, basic finishing, inspection), lead times might range from 2~6주.
- Production Parts (with HIP & Machining): For parts requiring the full suite of post-processing including HIP and final machining, lead times are typically longer, potentially ranging from 6 to 12 weeks or more, depending heavily on scheduling external services like HIP and the complexity of machining.
Managing Costs & Lead Times:
- DfAM: Optimize the design not only for performance but also for manufacturability – minimize volume, reduce complexity where possible without sacrificing function, and design for easier support removal and powder evacuation.
- Clear Specifications: Provide clear, unambiguous drawings and specifications, including critical tolerances, surface finishes, and required certifications/testing, to avoid delays and quoting errors.
- Supplier Collaboration: Work closely with your chosen AM provider (like Met3dp) early in the design process. Their expertise can help optimize the design for their specific processes, potentially reducing costs and lead times. Visit our general site 여기.
- Volume Planning: Discuss potential future production volumes with the supplier, as this can influence pricing and allow them to plan capacity.
- Realistic Expectations: Understand that producing high-quality, certified aerospace components via AM involves a complex, multi-step process that inherently takes time and investment.
By understanding these cost and lead time drivers, engineers and procurement managers can better plan projects, set realistic budgets, and effectively communicate expectations when leveraging the powerful capabilities of metal additive manufacturing for components like titanium vibration damper housings.
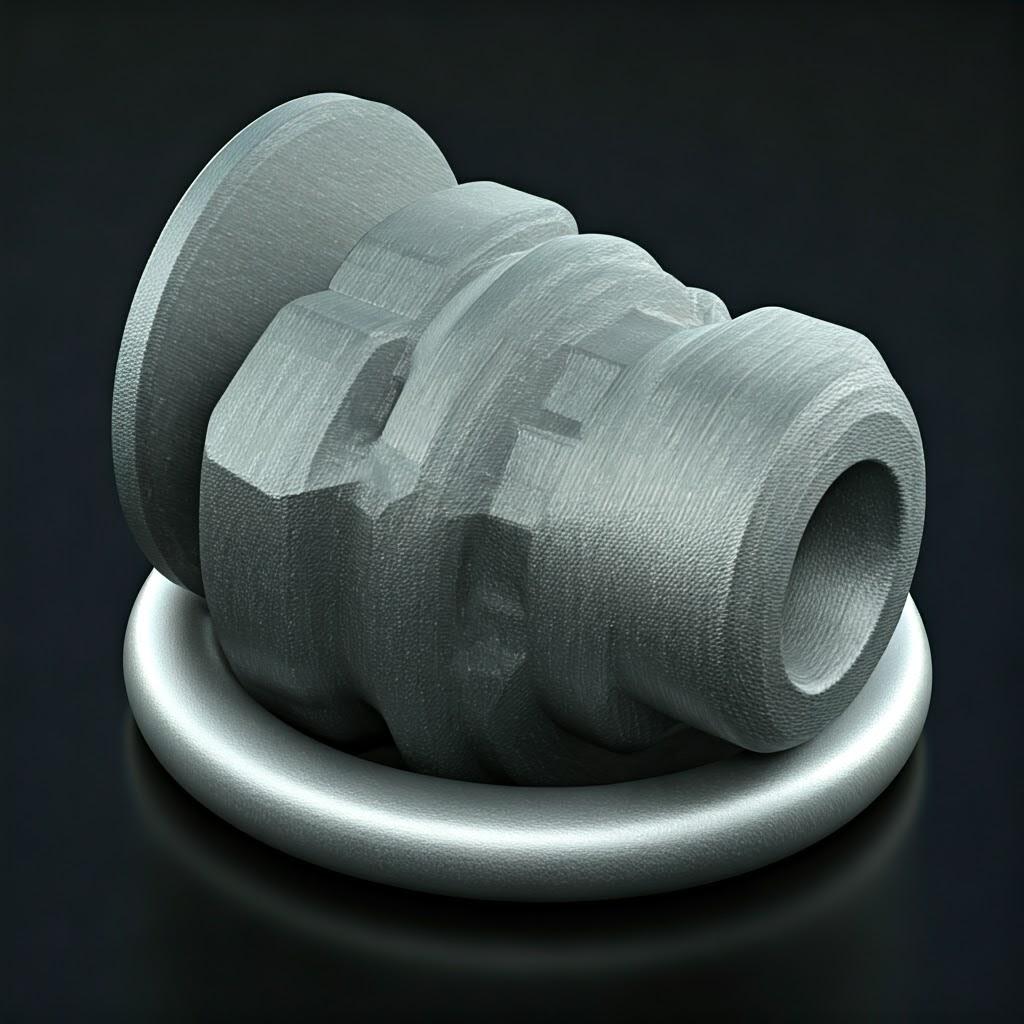
Frequently Asked Questions (FAQ) about 3D Printed Titanium Damper Housings
Here are some common questions engineers and procurement managers have regarding the use of additive manufacturing for titanium vibration damper housings:
1. Are 3D printed titanium parts as strong and reliable as traditionally manufactured (e.g., machined from billet or forged) parts?
- Yes, when produced using optimized processes and appropriate post-processing, 3D printed Ti-6Al-4V and Ti-6Al-4V ELI components can exhibit mechanical properties (like tensile strength, yield strength, fatigue life) that are comparable, and sometimes even superior, to their wrought or cast counterparts. Key factors include:
- 프로세스 제어: Using well-characterized powders (like those from Met3dp) and validated printing parameters on well-maintained machines (like Met3dp’s SEBM systems) to achieve high density (>99.7%).
- 후처리: Implementing crucial steps like stress relief and, particularly for aerospace, Hot Isostatic Pressing (HIP) is vital. HIP closes internal porosity, significantly improving fatigue life, ductility, and overall material integrity, often resulting in properties that meet or exceed aerospace standards for wrought materials.
- 마이크로 구조: AM processes can create unique microstructures that can be tailored through heat treatment to achieve desired property balances.
- Validation: Rigorous testing (tensile tests, fatigue tests on witness coupons printed with the parts) and NDT are essential to verify properties and ensure reliability, just as they are for traditionally manufactured critical parts. Partnering with an AS9100 certified provider ensures these validation steps are integral to the process.
2. How does the cost of a 3D printed titanium damper housing compare to CNC machining the same part from a solid block?
- The cost comparison is highly dependent on the 복잡성 of the part and the production volume.
- For highly complex geometries: AM is often more cost-effective. Designs involving intricate internal features, topology optimization, or significant part consolidation are extremely difficult, time-consuming, and generate massive material waste if machined from billet. AM produces these complex shapes directly with much lower material waste (better buy-to-fly ratio).
- For relatively simple geometries: CNC machining from billet might be cheaper, especially as volume increases, due to faster machining times per part once set up.
- 재료 낭비: AM’s additive nature significantly reduces waste of expensive titanium compared to subtractive machining, which is a major cost factor.
- 압형: AM avoids the high cost of specialized tooling or fixtures that might be needed for complex machining setups or casting.
- 리드 타임: For prototypes or low volumes, AM’s speed can offer significant cost savings in terms of development time, even if the per-part price is higher.
- Overall: For the complex, lightweight, often customized designs typical of optimized aerospace damper housings, AM frequently offers a better total value proposition when considering design freedom, weight savings, reduced assembly, and material efficiency, even if the direct print cost seems high.
3. What kind of surface finish can be expected on a 3D printed titanium housing, and is it suitable for sealing surfaces?
- As-printed surface finish varies by process (SEBM generally rougher than LPBF) and orientation, typically ranging from Ra 6 µm to 40 µm. This is generally not smooth enough for direct use as a dynamic sealing surface or high-precision mating interface.
- Achieving smooth finishes:
- 가공: Post-print CNC machining is the most common and reliable method to achieve smooth (Ra < 1 µm), tightly toleranced surfaces required for seals or critical fits. Machining allowances must be included in the AM design.
- Polishing/Finishing: Techniques like tumbling, electropolishing, or manual polishing can improve the general surface finish significantly but might struggle to achieve the flatness and specific Ra values required for demanding seals across large areas compared to machining.
- Design Consideration: Engineers must identify critical surfaces requiring smooth finishes early in the design phase and incorporate necessary machining allowances and post-processing steps into the manufacturing plan and cost estimation. Assume that critical interfaces on an AM part will likely require post-machining for optimal performance.
Conclusion: The Future of Aerospace Manufacturing with Titanium AM Damper Housings
The adoption of metal additive manufacturing, specifically using high-performance titanium alloys like Ti-6Al-4V and Ti-6Al-4V ELI, represents a significant leap forward in the production of critical aerospace components such as vibration damper housings. This technology transcends being merely a novel manufacturing method; it is a powerful enabler of innovation, offering engineers unprecedented design freedom to create lighter, stronger, and more functionally integrated parts that were previously unattainable. The ability to topologically optimize structures, consolidate assemblies, incorporate complex internal features like lattice structures, and rapidly iterate on designs provides a distinct competitive advantage in the demanding aerospace sector.
For vibration damper housings, the benefits are clear: significant weight reduction directly impacting fuel efficiency or payload capacity, improved structural integrity through part consolidation and optimized load paths, enhanced damping characteristics via tailored geometries, and the potential for faster development cycles. While challenges related to process control, post-processing complexity, and cost exist, they are being effectively addressed through advancements in technology, materials science, simulation tools, and the growing expertise of specialized AM providers. The implementation of rigorous quality management systems, exemplified by AS9100 certification, and crucial post-processing steps like Hot Isostatic Pressing ensure that AM titanium components meet and often exceed the stringent reliability and performance standards required for flight.
Choosing the right manufacturing partner is paramount to harnessing these advantages. Companies like Met3dp, with vertically integrated capabilities spanning advanced powder production (utilizing PREP and VIGA for superior Ti-6Al-4V / ELI powders) and state-of-the-art printing solutions (specializing in SEBM technology ideal for low-stress titanium parts), are at the forefront of this manufacturing revolution. Our deep expertise in materials science, additive manufacturing processes, and the specific demands of the aerospace industry allows us to collaborate effectively with clients, transforming complex engineering challenges into tangible, high-performance components.
As the aerospace industry continues to push the boundaries of performance and efficiency, metal additive manufacturing will undoubtedly play an increasingly vital role. For vibration damper housings and countless other complex metal components, AM offers a pathway to enhanced capabilities, reduced lead times for complex parts, and a more agile, adaptable approach to manufacturing. Embracing this digital manufacturing transformation is key for aerospace companies seeking to innovate and maintain leadership in a rapidly evolving global market.
Contact Met3dp today to explore how our comprehensive metal additive manufacturing solutions, from industry-leading powders to advanced printing systems and expert application support, can power your organization’s goals and help you realize the full potential of 3D printed titanium for your next aerospace project.
공유
중국 칭다오에 본사를 둔 선도적인 적층 제조 솔루션 제공업체인 MET3DP Technology Co. 당사는 산업용 3D 프린팅 장비와 고성능 금속 분말을 전문으로 합니다.
관련 기사
Met3DP 소개
최근 업데이트
제품
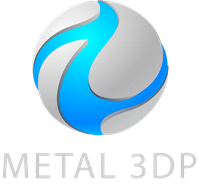
3D 프린팅 및 적층 제조용 금속 분말