3D Printed Sensor Holders for High-Performance Vehicles
목차
Introduction: The Critical Role of Sensor Holders in High-Performance Automotive Applications
In the intricate ecosystem of modern high-performance vehicles, every component plays a crucial role. From the roaring engine delivering immense power to the sophisticated electronic systems managing performance, safety, and driver assistance, precision and reliability are paramount. Often overlooked, yet fundamentally critical, are the mounting solutions used to secure the vast array of sensors distributed throughout the vehicle. Automotive sensor holders, or sensor brackets, are unsung heroes, ensuring that delicate and vital electronic eyes and ears are perfectly positioned, securely fastened, and protected from the harsh operating environments encountered in performance driving, motorsport, and advanced automotive applications. These components are not mere pieces of hardware; they are precision-engineered interfaces that guarantee the accuracy and dependability of data feeding into critical systems like engine control units (ECUs), transmission control units (TCUs), anti-lock braking systems (ABS), traction control systems (TCS), and increasingly complex Advanced Driver-Assistance Systems (ADAS).
The demands placed on sensor holders in high-performance vehicles significantly exceed those in standard passenger cars. Consider the environment: extreme temperatures radiating from engines and exhausts, constant high-frequency vibrations from stiff suspension and powerful drivetrains, potential impacts, and the relentless pursuit of weight reduction to enhance dynamics and fuel efficiency. Furthermore, the packaging constraints in performance vehicles, often featuring tightly packed engine bays, complex aerodynamic elements, and custom configurations, necessitate mounting solutions with intricate geometries and optimized forms that traditional manufacturing methods struggle to produce efficiently or effectively. A poorly designed or manufactured sensor holder can lead to sensor misalignment, signal noise due to vibration, premature sensor failure, or inaccurate data transmission, potentially compromising vehicle performance, safety, and reliability. Imagine a wheel speed sensor bracket flexing under cornering loads, feeding erroneous data to the ABS and traction control, or a MAP (Manifold Absolute Pressure) sensor holder vibrating excessively, leading to incorrect fuel mixture calculations. The consequences range from suboptimal performance to critical system malfunctions.
This is where the transformative power of 금속 3D 프린팅, also known as additive manufacturing (AM), enters the picture. For engineers, designers, and procurement managers in the high-performance automotive sector, including OEMs, Tier 1/2 suppliers, motorsport teams, and aftermarket tuning specialists, metal AM offers an unprecedented solution to the challenges of creating robust, lightweight, and geometrically complex sensor holders. Traditional methods like CNC machining, while precise, can be wasteful in terms of material (subtractive process) and limited in geometric freedom, especially for producing organically shaped, topology-optimized designs. Casting might be suitable for high volumes but lacks the precision and material properties required for many critical applications and involves expensive tooling. Sheet metal fabrication often struggles with complex 3D geometries and stiffness requirements. Metal 3D 프린팅, however, builds parts layer by layer directly from CAD data, enabling the creation of highly optimized, lightweight structures with intricate internal features and complex external shapes, perfectly tailored to the specific sensor and its mounting location. This technology allows for rapid design iteration, consolidation of multiple parts into a single component, and the use of advanced materials like high-strength aluminum alloys, ideal for demanding automotive environments. Companies like Met3dp are at forefront, leveraging advanced powder bed fusion technologies and high-quality metal powders to deliver industrial-grade components that meet the stringent requirements of the automotive industry. This introductory section sets the stage, highlighting the indispensable nature of sensor holders and introducing metal additive manufacturing as a key enabling technology for achieving superior performance, reliability, and design flexibility in the demanding world of high-performance vehicles.
What Are Automotive Sensor Holders Used For? Diverse Applications in Modern Vehicles
The modern automobile is a marvel of electromechanical engineering, teeming with sensors that monitor virtually every aspect of its operation and environment. These sensors are the vehicle’s sensory organs, providing real-time data crucial for performance optimization, safety systems, emissions control, diagnostics, and driver assistance features. Automotive sensor holders are the vital mechanical interfaces responsible for precisely positioning and securely mounting this diverse array of sensors in their designated locations. Their applications span the entire vehicle architecture, from the powertrain and chassis to the cabin and exterior. Understanding the breadth of these applications underscores the need for versatile, reliable, and often custom-designed mounting solutions – a need increasingly met by metal additive manufacturing.
Powertrain Sensor Mounting: The engine and transmission are sensor-rich environments, operating under high temperatures and vibrations. Holders are needed for:
- MAP (Manifold Absolute Pressure) Sensors: Mounted on the intake manifold, requiring stability to ensure accurate air pressure readings for fuel injection calculations. Holders must withstand engine vibrations and heat.
- MAF (Mass Air Flow) Sensors: Located in the air intake tract, needing precise positioning for correct airflow measurement. Holders must ensure an airtight seal and resist intake pulsations.
- Throttle Position Sensors (TPS): Attached to the throttle body, requiring accurate alignment to report throttle angle to the ECU.
- Camshaft and Crankshaft Position Sensors: Critical for engine timing, these sensors require extremely stable and precise mounting near rotating components, often in tight spaces. Holders must resist thermal expansion and vibration to maintain accurate gaps.
- Oxygen (O2) Sensors: Mounted in the exhaust system, holders (often integrated into exhaust bungs) must withstand extreme temperatures and corrosive gases.
- Knock Sensors: Attached directly to the engine block, requiring rigid mounting to accurately detect detonation frequencies.
- Temperature Sensors (Coolant, Oil, Air): Require holders that ensure good thermal contact (if applicable) and secure positioning within fluid passages or air streams.
Chassis and Suspension Sensor Mounting: Vehicle dynamics rely heavily on chassis-mounted sensors. Holders are required for:
- Wheel Speed Sensors: Crucial for ABS, TCS, and ESC (Electronic Stability Control), these sensors need precise alignment relative to the tone ring on the wheel hub. Holders must withstand high G-forces, impacts from road debris, and environmental exposure (water, salt, dirt). Metal AM allows for optimized designs that protect the sensor while maintaining rigidity.
- Suspension Position/Travel Sensors: Used in active suspension systems and data logging, requiring robust mounting to suspension arms or links, accurately tracking movement despite constant articulation and impacts.
- Steering Angle Sensors: Typically mounted on the steering column, requiring stable brackets to ensure accurate measurement of driver input.
- Accelerometers and Gyroscopic Sensors (IMU – Inertial Measurement Unit): Often centrally mounted, these sensors require extremely rigid holders to accurately measure vehicle body motion (acceleration, yaw, pitch, roll) for stability control and ADAS. Vibration isolation may sometimes be integrated into the holder design.
ADAS and Autonomous Driving Sensor Mounting: The proliferation of ADAS features and the move towards autonomous driving have dramatically increased the number and complexity of sensors, demanding highly specialized holders:
- LiDAR (Light Detection and Ranging) Sensors: Require very stable, precisely aligned mounts, often on the roof, grille, or bumpers. Holders must maintain alignment under vibration and thermal changes and often require complex shapes to integrate smoothly with vehicle styling. Metal AM is ideal for creating custom, low-profile, high-stiffness LiDAR brackets.
- RADAR (Radio Detection and Ranging) Sensors: Typically mounted behind the grille or bumper fascia. Holders must be rigid, maintain precise aiming angles, and be made of materials that do not interfere with radar signals (though metal holders are often feasible if positioned correctly relative to the active face).
- Camera Systems (Forward-facing, Surround-view): Require stable mounts, often integrated into windshield assemblies, mirror housings, or bumpers. Holders must prevent vibration to ensure clear image quality and accurate perception for features like lane-keeping assist and collision avoidance.
- Ultrasonic Sensors: Used for parking assist, requiring small, discreet holders integrated into bumper fascias.
기타 애플리케이션:
- Fuel Level Sensors: Brackets within the fuel tank.
- Tire Pressure Monitoring System (TPMS) Sensors: While often integrated into the valve stem, some systems use wheel-well mounted receivers requiring brackets.
- Occupant Detection Sensors: Mounting brackets within seats or cabin trim.
- Environmental Sensors (Ambient Temperature, Rain/Light Sensors): Brackets for mounting behind grilles or on windshields.
Meeting B2B Needs: 대상 automotive Tier 1 suppliers 및 OEM procurement managers, sourcing reliable, cost-effective, and high-performance sensor holders is critical. They often require 모조리 volumes for production lines. Metal 3D printing offers a compelling pathway for producing complex, lightweight, and durable holders, particularly for low-to-mid volume performance vehicles or for rapid prototyping and validation cycles. Aftermarket parts distributors also benefit, as metal AM enables the production of custom sensor brackets for modified vehicles, engine swaps, or performance upgrades where standard mounting solutions are inadequate. The ability to create bespoke designs tailored to specific sensor types and unique mounting locations, often consolidating multiple bracket pieces into one, is a significant advantage offered by additive manufacturing providers like Met3dp, who can act as a key 공급업체 for these specialized components.
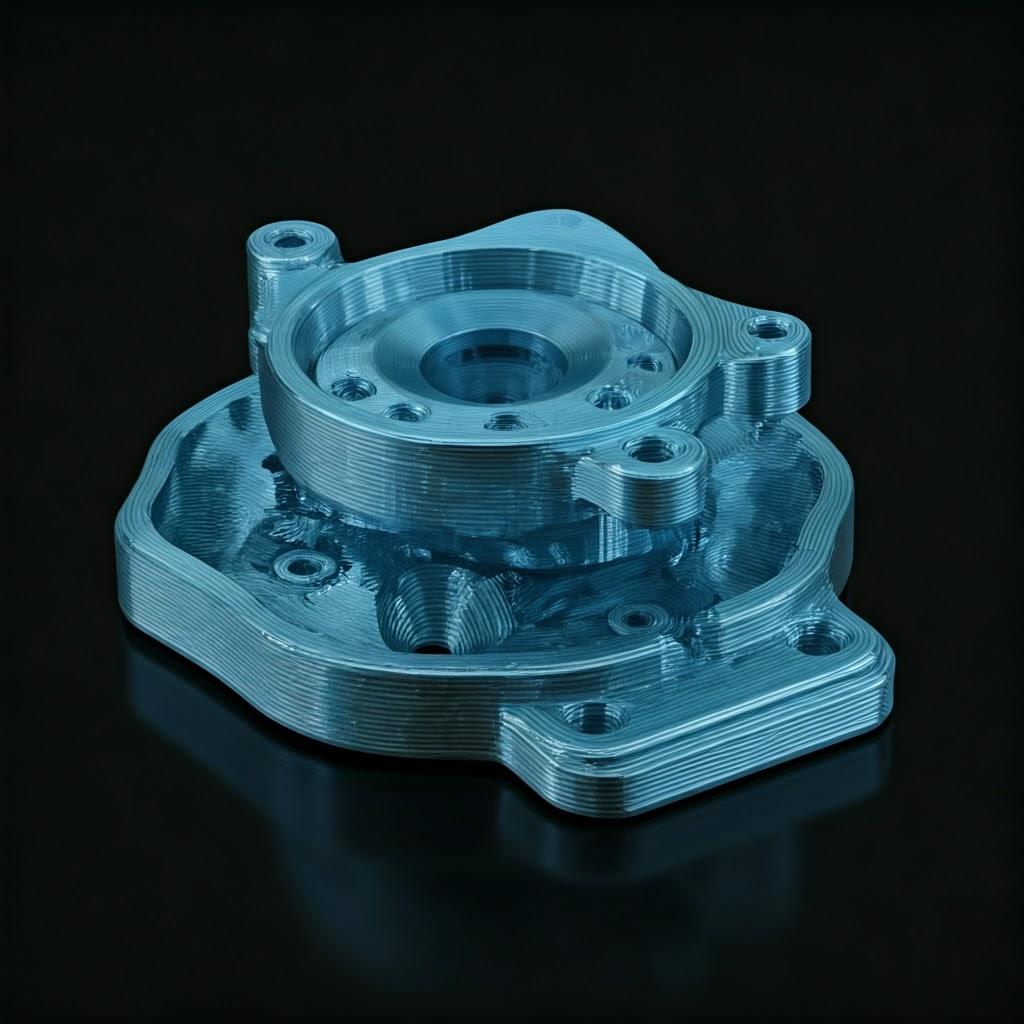
Why Choose Metal 3D Printing for Automotive Sensor Holders? Unlocking Performance Advantages
While traditional manufacturing methods like CNC machining, casting, and sheet metal fabrication have long served the automotive industry, metal additive manufacturing (AM) presents a paradigm shift, offering distinct advantages, particularly for components like sensor holders in high-performance and specialized vehicle applications. The decision to utilize metal 3D printing isn’t merely about adopting a novel technology; it’s about unlocking tangible performance benefits, design freedoms, and production efficiencies that directly address the demanding requirements of the modern automotive landscape. For engineers striving for optimal packaging and weight reduction, and for procurement specialists seeking agile and capable automotive component suppliers, understanding these advantages is key.
1. 독보적인 디자인 자유도 및 복잡성:
- 토폴로지 최적화: Metal AM allows designers to utilize topology optimization software to create holders with organic, load-path-optimized shapes. Material is placed only where structurally necessary, resulting in components that are significantly lighter (often 30-60%) than traditionally designed counterparts while maintaining or even increasing stiffness and strength. This is crucial for reducing unsprung mass (for chassis sensors) and overall vehicle weight in performance applications.
- 파트 통합: Complex assemblies consisting of multiple brackets, fasteners, and mounting elements can often be redesigned and printed as a single, integrated component. This reduces part count, simplifies assembly, minimizes potential failure points (like bolted joints loosening under vibration), and lowers overall system weight. Imagine consolidating a sensor bracket, a heat shield element, and wiring harness clip features into one printed part.
- Internal Features & Conformal Cooling: AM can create intricate internal channels or cavities within the holder structure. This could potentially be used for conformal cooling channels (using air or even liquid) to protect sensitive electronics from excessive heat soak radiating from nearby engine or exhaust components, or for integrating vibration damping structures.
- 복잡한 지오메트리: Tight packaging constraints in performance vehicles often necessitate holders with highly complex, non-orthogonal shapes that are difficult or impossible to machine or cast efficiently. Metal AM excels at producing these intricate geometries directly from CAD data without the need for complex tooling or multiple machining setups.
2. Rapid Prototyping and Iteration:
- Speed to First Part: Producing functional metal prototypes of sensor holders can be done in days rather than the weeks or months often required for traditional tooling (casting) or complex CNC programming and setups. This drastically accelerates the design validation and iteration cycle.
- Testing Multiple Designs: Engineers can quickly print and test several design variations (e.g., different mounting points, stiffness levels, sensor orientations) to find the optimal solution without incurring significant tooling costs for each iteration. This agility is invaluable in the fast-paced development cycles of motorsport and performance vehicles.
3. Low-Volume Production Viability & Customization:
- Tooling-Free Manufacturing: Metal AM eliminates the need for expensive molds, dies, or fixtures associated with casting or forming. This makes it economically viable to produce sensor holders in low-to-medium volumes, typical for niche performance vehicles, motorsport applications, classic car restorations, or aftermarket upgrades.
- 대량 사용자 지정: Need a slightly different mounting angle for a sensor on a modified vehicle? Or a bespoke bracket for a unique sensor integration project? Metal AM allows for easy customization of designs with minimal extra cost compared to modifying traditional tooling or machining setups. This is highly attractive for aftermarket parts distributors and tuning shops requiring unique solutions.
- 주문형 생산: Parts can be produced on demand, reducing the need for large inventory holdings, especially for slow-moving or highly specialized holder designs. This aligns well with lean manufacturing principles and just-in-time supply chains sought by automotive procurement teams.
4. Material Performance & Selection:
- 고급 합금: Metal AM allows for the use of high-performance alloys, such as the recommended AlSi10Mg and A7075 aluminum alloys, which offer excellent strength-to-weight ratios ideal for automotive applications. Other materials like Titanium alloys (for extreme strength and heat resistance) or Stainless Steels (for corrosion resistance) can also be utilized depending on the specific requirement.
- Optimized Microstructures: The rapid solidification inherent in powder bed fusion processes can lead to fine-grained microstructures, potentially offering enhanced mechanical properties compared to cast equivalents. Partners like Met3dp, with expertise in powder metallurgy and process control using techniques like gas atomization (GA) and Plasma Rotating Electrode Process (PREP), ensure high-quality, dense parts with reliable material properties.
5. Comparison with Traditional Methods:
기능 | Metal 3D Printing (L-PBF/SEBM) | CNC 가공 | 캐스팅 | Sheet Metal Fab. |
---|---|---|---|---|
자유로운 디자인 | Very High (Complex shapes, internal channels) | Moderate (Limited by tool access) | Moderate (Requires draft angles) | Low (Primarily 2D/2.5D) |
복잡성 | Handles high complexity well | Difficulty increases with complexity | Mold complexity drives cost | 제한된 복잡성 |
무게 감소 | Excellent (Topology optimization, lattices) | Good (Pocketing) | Fair (Wall thickness limits) | Fair (Material choice) |
부품 통합 | 우수 | 제한적 | 제한적 | Poor |
재료 낭비 | Low (Recyclable powder) | High (Subtractive) | Moderate (Gates, runners) | Moderate (Offcuts) |
툴링 비용 | 없음 | Low (Fixturing) | High (Molds/Dies) | Moderate (Dies/Forms) |
리드 타임(프로토) | Fast (Days) | Moderate (Days/Weeks) | Slow (Weeks/Months) | Moderate (Days/Weeks) |
리드 타임(제작) | Moderate (Scalable) | 빠른 | Fast (High volume) | 빠른 |
Cost (Low Vol.) | 경쟁력 있는 | 보통-높음 | 매우 높음 | 보통 |
Cost (High Vol.) | 더 높음 | Lower | 최저 | 낮음 |
재료 선택 | Growing range (Al, Ti, Steel, Ni alloys) | Very Wide | Wide (Castable alloys) | Wide (Formable sheets) |
Typical Precision | Good ($ \pm 0.1$ to $ \pm 0.2$ mm typical, post-machinable) | Excellent ($ \pm 0.01$ mm possible) | Fair ($ \pm 0.5$ mm typical) | Fair ($ \pm 0.2$ mm typical) |
시트로 내보내기
While CNC machining offers superior precision out-of-the-machine and casting excels at high-volume cost-effectiveness, metal 3D printing uniquely combines design freedom, rapid iteration, customization, and efficient low-volume production, making it an ideal solution for optimizing automotive sensor holders in performance-critical applications. It empowers engineers to create solutions previously unattainable, pushing the boundaries of vehicle performance and efficiency.
Recommended Materials: AlSi10Mg and A7075 Aluminum Alloys for Optimal Performance
Selecting the right material is fundamental to the success of any engineering component, and 3D printed automotive sensor holders are no exception. The material must provide the necessary mechanical strength, stiffness, durability, and environmental resistance while ideally contributing to weight reduction goals. For many automotive applications, particularly those balancing performance, weight, and cost, aluminum alloys are prime candidates. Among the powder options available for Laser Powder Bed Fusion (L-PBF) – a common metal AM process – AlSi10Mg 및 A7075 stand out as excellent choices for sensor holders, albeit with different strengths and considerations. Understanding their properties helps engineers and automotive material specifiers 정보에 입각한 결정을 내리세요.
AlSi10Mg: AM을 위한 주력 알루미늄 합금
AlSi10Mg is arguably the most widely used aluminum alloy in metal additive manufacturing. It’s essentially a casting alloy adapted for AM processes, known for its excellent processability, good strength-to-weight ratio, and favorable thermal properties.
- 구성: Primarily aluminum, with significant additions of Silicon (~9-11%) and Magnesium (~0.2-0.45%). Silicon improves fluidity during the melting/solidification process inherent in AM and enhances casting characteristics (though used here in a non-casting context), while Magnesium allows for strengthening through heat treatment (precipitation hardening).
- Key Properties & Benefits for Sensor Holders:
- Good Processability: AlSi10Mg melts and solidifies reliably under laser exposure, leading to relatively stable printing processes and the ability to produce dense parts (typically >99.5% density) with fine microstructures. This reliability is crucial for wholesale suppliers needing consistent production.
- 뛰어난 무게 대비 강도 비율: While not the strongest aluminum alloy, its low density combined with good mechanical properties after heat treatment makes it ideal for lightweighting sensor brackets without compromising structural integrity.
- Good Thermal Conductivity: Aluminum alloys generally offer good thermal conductivity, which can be beneficial for dissipating heat away from the sensor itself or the holder if mounted near hot components.
- 내식성: Offers adequate corrosion resistance for many automotive environments, though surface treatments like anodizing or painting are often recommended for long-term durability, especially against road salt.
- 용접성: Can be welded if necessary for post-processing or integration, although AM often aims to eliminate such needs through part consolidation.
- 비용 효율성: Generally, AlSi10Mg powder is one of the more economical metal AM powders, contributing to a lower overall part cost compared to titanium or high-performance nickel alloys.
- Typical Mechanical Properties (Heat Treated, L-PBF):
- Ultimate Tensile Strength (UTS): $ 380 – 450 $ MPa
- Yield Strength (YS): $ 240 – 300 $ MPa
- Elongation at Break: $ 6 – 12 $%
- Hardness: $ 100 – 120 $ HBW
- Density: $ \approx 2.67 $ g/cm³
- 고려 사항: Its properties are good but may not be sufficient for the most demanding high-strength applications where A7075 might be considered. Ductility is moderate.
A7075: High-Strength Performance Aluminum
A7075 is a well-known high-performance aluminum alloy from the 7xxx series, typically used in aerospace and high-stress structural applications due to its exceptional strength, rivaling some steels but at a fraction of the weight. Traditionally a wrought alloy (used in plates, extrusions), adapting it for additive manufacturing has been challenging but is now increasingly feasible, offering significant performance gains.
- 구성: Primarily aluminum, with Zinc (~5.1-6.1%) as the main alloying element, plus Magnesium (~2.1-2.9%) and Copper (~1.2-2.0%). These elements enable significant strengthening through precipitation hardening heat treatments (e.g., T6 condition).
- Key Properties & Benefits for Sensor Holders:
- 탁월한 무게 대비 강도 비율: This is the primary advantage of A7075. Its high yield and tensile strength make it suitable for sensor holders subjected to extreme loads, high vibrations, or where maximum stiffness is required in a minimal package size. This is particularly relevant in motorsport or aerospace-grade automotive applications.
- 높은 경도: Offers better wear resistance compared to AlSi10Mg.
- Challenges & Considerations in AM:
- 처리 가능성: A7075 is notoriously more challenging to process via L-PBF than AlSi10Mg. It is prone to solidification cracking (hot tearing) due to its wide freezing range and susceptibility to hydrogen porosity. Achieving high-density, crack-free parts requires carefully controlled process parameters, specialized machine capabilities, and potentially modified alloy compositions optimized for AM. This often translates to higher part costs and requires working with experienced AM service providers like Met3dp, who possess deep materials science knowledge.
- 내식성: Generally has lower corrosion resistance compared to AlSi10Mg or 6xxx series alloys, particularly susceptibility to stress corrosion cracking (SCC) in certain tempers. Appropriate surface protection (e.g., anodizing, specific paint systems) is usually essential.
- 비용: A7075 powder is typically more expensive than AlSi10Mg, and the more demanding printing process further increases the cost per part.
- Typical Mechanical Properties (Heat Treated, L-PBF – Note: Properties can vary significantly based on process optimization):
- Ultimate Tensile Strength (UTS): $ 500 – 570 $ MPa
- Yield Strength (YS): $ 450 – 520 $ MPa
- Elongation at Break: $ 2 – 8 $% (Generally lower ductility than AlSi10Mg)
- Hardness: $ \approx 150 $ HBW
- Density: $ \approx 2.81 $ g/cm³ (Slightly denser than AlSi10Mg)
Met3dp’s Material Expertise:
Choosing between AlSi10Mg and A7075 depends heavily on the specific application requirements:
- Use AlSi10Mg for: General-purpose sensor holders, applications where moderate strength, good processability, and cost-effectiveness are key drivers. Ideal for rapid prototyping and many standard performance vehicle applications.
- Use A7075 for: Highly loaded brackets, components requiring maximum stiffness and strength with minimal weight, applications where cost is secondary to performance (e.g., competitive motorsport, aerospace-derived automotive tech). Requires careful design and collaboration with an expert AM provider.
Met3dp, leveraging its advanced powder manufacturing capabilities including 업계를 선도하는 가스 분무 및 PREP 기술, produces high-quality spherical metal powders optimized for AM processes like L-PBF and SEBM. Our unique nozzle and gas flow designs ensure metallic spheres with high sphericity and good flowability – critical factors for achieving consistent powder bed density and ultimately, high-quality, reliable printed parts. While specializing in materials like TiNi, TiTa, TiAl, TiNbZr, CoCrMo, stainless steels, and superalloys, Met3dp possesses the metallurgical expertise to work with demanding alloys like aluminum, ensuring that the powders used meet the stringent quality controls necessary for producing sensor holders that perform reliably in critical automotive systems. Our comprehensive solutions, spanning printers, powders, and application development, make us a valuable partner for companies seeking to implement metal AM for demanding components.
Material Comparison Table:
속성 | AlSi10Mg (Heat Treated) | A7075 (Heat Treated, AM) | Importance for Sensor Holders |
---|---|---|---|
주요 혜택 | Good balance of properties, processability | Very High Strength | Depends on load case and optimization potential |
수율 강도 | $ 240 – 300 $ MPa | $ 450 – 520 $ MPa | Resistance to permanent deformation under load |
Ultimate Tensile Str. | $ 380 – 450 $ MPa | $ 500 – 570 $ MPa | Maximum stress before fracture |
밀도 | $ \approx 2.67 $ g/cm³ | $ \approx 2.81 $ g/cm³ | Lower is better for weight reduction |
Stiffness (E Modulus) | $ \approx 70 $ GPa | $ \approx 72 $ GPa | Resistance to deflection under load (important for alignment) |
Ductility (% Elong.) | $ 6 – 12 $% | $ 2 – 8 $% | Ability to deform before fracture (toughness indicator) |
Processability (L-PBF) | 우수 | Challenging (requires expertise) | Affects cost, reliability, achievable quality |
내식성 | 양호 | Fair (requires protection) | Durability in automotive environments |
비용 | 보통 | 높음 | Overall component budget |
시트로 내보내기
By carefully considering the operating conditions, load requirements, weight targets, and budget, automotive engineers can select the most appropriate aluminum alloy, leveraging the capabilities of metal additive manufacturing and expert partners like Met3dp to produce superior sensor holders for high-performance vehicles.
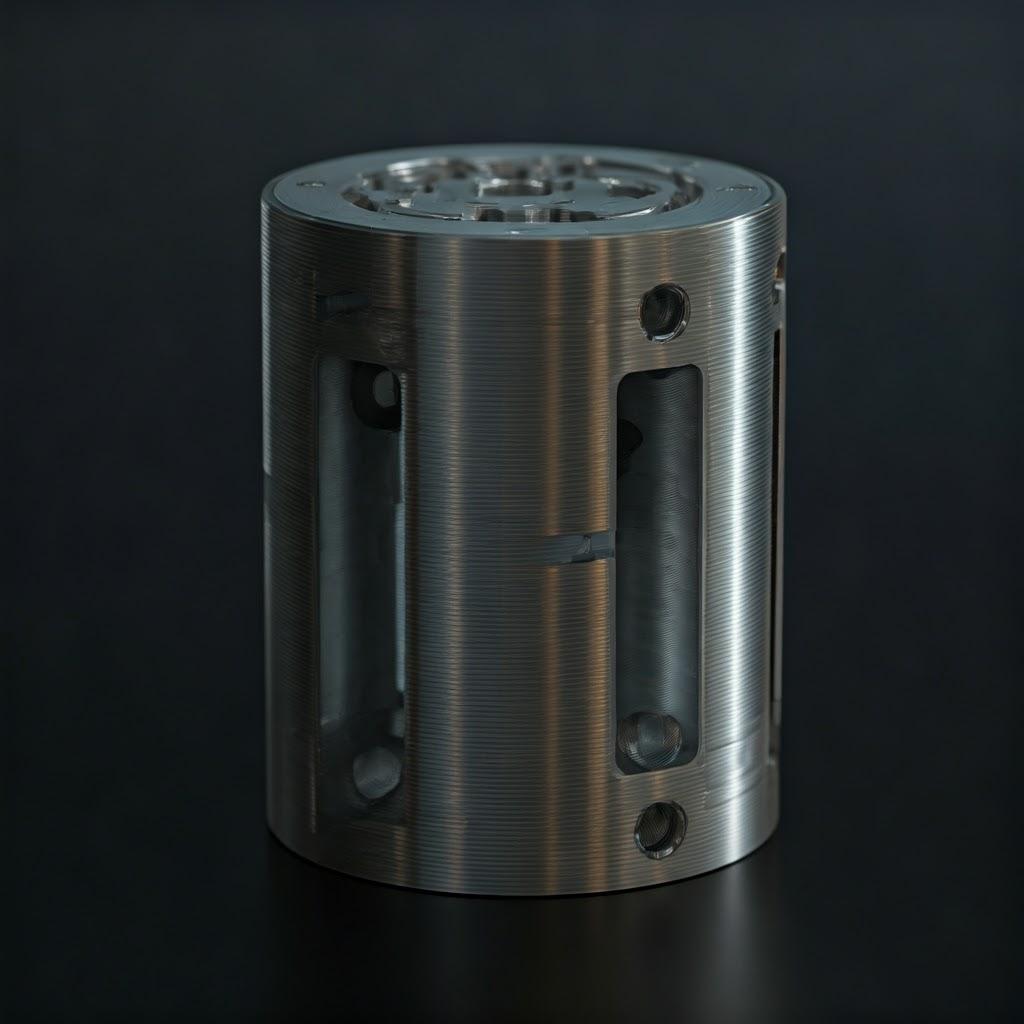
Design for Additive Manufacturing (DfAM): Optimizing Sensor Holders for 3D Printing Success
Simply replicating a design intended for CNC machining or casting and sending it to a metal 3D printer rarely yields optimal results. To truly harness the power of additive manufacturing for automotive sensor holders, engineers must embrace 적층 제조를 위한 설계(DfAM) principles. DfAM is a design philosophy that considers the unique capabilities and constraints of AM processes right from the conceptual stage. It moves beyond merely making a part printable; it focuses on leveraging AM’s strengths – like complex geometries, topology optimization, and part consolidation – to create components that are lighter, stronger, more functional, and potentially cheaper to produce in the context of AM. For engineers designing critical components like sensor brackets, and for procurement managers seeking efficient manufacturing solutions from their AM suppliers, understanding and implementing DfAM is crucial for success.
Key DfAM Principles for Sensor Holders:
- 토폴로지 최적화:
- 개념: This computational method optimizes material layout within a defined design space based on load conditions, constraints, and performance goals (e.g., minimize weight, maximize stiffness).
- Application for Sensor Holders: Define the sensor mounting points, vehicle attachment points, and any stay-out zones (e.g., for wiring, nearby components). Apply expected loads (static weight, vibration G-forces, potential impacts). The software then generates an organic, load-path-driven geometry, removing material from non-critical areas. This often results in intricate, lattice-like, or bone-like structures that are incredibly efficient structurally.
- 혜택: Significant weight reduction (often 30-60% or more) while maintaining or increasing stiffness, which is critical for accurate sensor positioning and reducing overall vehicle mass. It creates forms difficult or impossible to achieve traditionally.
- 파트 통합:
- 개념: Redesigning assemblies of multiple parts to be printed as a single, monolithic component.
- Application for Sensor Holders: A sensor mounting assembly might traditionally involve a main bracket, shims for alignment, separate clips for wiring harnesses, and multiple fasteners. DfAM encourages integrating these elements into one printable part. Imagine a holder with integrated cable routing channels, built-in standoffs, or snap-fit features.
- 혜택: Reduced part count, simplified assembly (lower labor costs), elimination of potential failure points (fasteners loosening), improved structural integrity, and often further weight reduction.
- Lattice Structures and Infill:
- 개념: Replacing solid volumes with internal lattice structures (e.g., cubic, gyroid, honeycomb).
- Application for Sensor Holders: For bulkier sections of a holder design, internal lattices can significantly reduce weight and material consumption while maintaining good compressive strength and stiffness. Different lattice types can also be chosen to influence vibration damping characteristics – potentially beneficial for isolating sensitive sensors.
- 혜택: Weight reduction, material savings (lower cost), potential for tailoring mechanical properties like vibration damping.
- Designing for Support Minimization:
- 개념: Orienting the part and designing features to minimize the need for temporary support structures during the build process. Powder bed fusion processes require supports for overhanging features (typically below 45 degrees from the horizontal) and to anchor the part to the build plate.
- Application for Sensor Holders:
- 자립 각도: Design overhangs to be greater than 45 degrees where possible.
- Chamfers and Fillets: Use chamfers instead of sharp overhangs at downward-facing edges. Large fillets can also help transition angles.
- Orientation: Consider the build orientation carefully during the design phase. Orienting critical surfaces vertically often yields better surface finish. Orienting for minimal overhangs reduces support needs. This is often a trade-off analysis.
- 내부 채널: Design internal channels with diamond or teardrop shapes to make them self-supporting, avoiding the need for difficult-to-remove internal supports.
- 혜택: Reduced material usage (supports are waste), significantly faster and easier post-processing (support removal is often labor-intensive), potentially lower part cost, and reduced risk of damaging the part during support removal.
- Feature Design Rules:
- Minimum Wall Thickness: Metal AM processes have limits on the minimum thickness of walls and features they can reliably produce (often around 0.4−0.8 mm, depending on the material, machine, and feature height). Designs must respect these limits.
- Hole Orientation and Shape: Horizontal holes often print slightly elliptical due to layer effects and may require supports. Vertical holes generally print more accurately. Small holes may need to be designed slightly undersized and then drilled or reamed post-print for high precision.
- Embossed/Engraved Features: Design text or logos with appropriate depth and width to ensure legibility after printing and potential surface finishing.
- 열 발산: Consider how the part’s geometry will affect heat buildup during printing. Large solid sections can accumulate stress. Thin, uniform walls are often preferable.
- Designing for Post-Processing:
- Machining Allowances: If certain surfaces require very high precision or specific finishes (e.g., mounting faces, bearing bores), add extra stock material (e.g., 0.5−1.0 mm) in the design specifically for post-machining.
- Support Access: Ensure support structures are designed in locations where they can be physically accessed and removed without damaging delicate features.
- Inspection Features: Consider adding small features or datums specifically for aiding dimensional inspection (e.g., with CMM probes).
Collaboration is Key: Effective DfAM often involves close collaboration between the design engineers and the additive manufacturing service provider, like Met3dp. Met3dp’s engineers possess deep knowledge of the capabilities and limitations of their specific 인쇄 방법 (including L-PBF and potentially SEBM depending on the material and application) and materials (like AlSi10Mg and A7075). They can provide crucial feedback on design printability, suggest optimizations for cost and performance, advise on optimal build orientation, and help develop effective support strategies. This collaborative approach ensures that the final sensor holder design is not only functional but also manufacturable efficiently and reliably, meeting the stringent demands of the high-performance automotive sector. Utilizing DfAM transforms metal 3D printing from just a manufacturing method into a powerful design tool.
Achievable Tolerances, Surface Finish, and Dimensional Accuracy in Metal AM
When engineers and procurement specialists evaluate manufacturing processes for critical components like automotive sensor holders, questions about precision are paramount. Can metal additive manufacturing deliver the required dimensional accuracy? What kind of surface finish can be expected? Understanding the achievable tolerances and surface characteristics of metal AM processes, such as Laser Powder Bed Fusion (L-PBF), is essential for setting realistic expectations, designing appropriately, and determining necessary post-processing steps. While metal AM may not match the inherent micro-precision of high-end CNC machining straight off the build plate, it offers remarkable accuracy for complex geometries and can readily achieve very tight tolerances with secondary finishing operations.
Dimensional Accuracy and Tolerances:
- General Achievable Tolerances: For typical L-PBF processes using aluminum alloys like AlSi10Mg or A7075, general achievable tolerances for as-built parts (after stress relief but before machining) are often in the range of:
- $ \pm 0.1 $ mm to $ \pm 0.2 $ mm for smaller features (e.g., up to 50 mm)
- $ \pm 0.2 $% to $ \pm 0.5 $% of the nominal dimension for larger features.
- 정확도에 영향을 미치는 요인: Achieving these tolerances consistently depends on several factors:
- 머신 보정: Precise calibration of the laser scanning system, powder recoating mechanism, and build environment is critical. Reputable AM service bureaus invest heavily in machine maintenance and calibration.
- 프로세스 매개변수: Laser power, scan speed, layer thickness, hatch spacing, and gas flow significantly impact melt pool stability, shrinkage, and final part dimensions. Optimized parameters, developed through rigorous testing by providers like Met3dp, are key.
- 머티리얼 속성: Different materials exhibit varying shrinkage rates and thermal behavior during processing. Powder quality (particle size distribution, sphericity, flowability), such as the high-quality powders produced by Met3dp’s advanced atomization techniques, contributes to process stability and dimensional consistency.
- Part Geometry and Size: Larger parts and complex geometries with varying cross-sections are more prone to thermal distortion and deviation.
- 빌드 오리엔테이션: The orientation of the part on the build plate affects accuracy. Features built vertically tend to be more dimensionally accurate in the X-Y plane than those built horizontally or at an angle.
- Support Strategy: Supports help anchor the part and manage thermal stress, influencing final geometry. Poor support strategy can lead to warping or deviation.
- Thermal Stress: Residual stress built up during the layer-by-layer heating and cooling cycles can cause distortion, especially after the part is removed from the build plate. Post-print heat treatment (stress relief) is crucial for dimensional stability.
- 더 엄격한 허용 오차 달성: For critical features like mounting holes, mating surfaces, or precise sensor interfaces requiring tolerances tighter than $ \pm 0.1 $ mm, post-machining (CNC milling, drilling, reaming, grinding) is typically employed. DfAM principles dictate adding machining stock to these specific features in the original CAD model.
표면 마감(거칠기):
- As-Built Surface Roughness (Ra): The surface finish of as-built metal AM parts is inherently rougher than machined surfaces due to the layer-wise construction and partially melted powder particles adhering to the surface. Typical Ra values depend heavily on orientation and process parameters:
- 상위 표면: Generally the smoothest, potentially Ra $ 6 – 10 $ $ \mu m $.
- Vertical Walls (X-Y Plane): Moderate roughness, often Ra $ 8 – 15 $ $ \mu m $.
- Upward-Facing Sloped Surfaces: Roughness increases as the angle approaches horizontal.
- Downward-Facing (Supported) Surfaces: Typically the roughest surfaces (Ra $ 15 – 25 $ $ \mu m $ or more) due to the contact points with support structures. Removing supports also affects the local finish.
- 표면 마감 개선: For applications requiring smoother finishes (for aesthetics, sealing surfaces, fatigue performance, or precise fluid flow), various post-processing methods are used:
- 연마제 블라스팅(비드, 모래): Common for achieving a uniform matte finish and removing loose powder. Can achieve Ra $ 3 – 6 $ $ \mu m $.
- 텀블링/진동 마감: Uses media to smooth surfaces and edges, effective for batches of smaller parts.
- Micro-Machining/Polishing: Can achieve very smooth, mirror-like finishes ($R_a < 0.8 $ $ \mu m $) on specific surfaces but is often manual or requires specialized equipment.
- 전기 연마: An electrochemical process that removes material to smooth surfaces, effective for complex shapes but alloy-dependent.
- CNC 가공: Provides precisely controlled surface finishes on specific features.
Dimensional Inspection and Quality Control:
Ensuring sensor holders meet specifications requires robust quality control procedures.
- 방법: Common inspection methods include:
- Coordinate Measuring Machines (CMM): For high-accuracy point measurements of critical dimensions and geometric dimensioning and tolerancing (GD&T).
- 3D Laser Scanning / Structured Light Scanning: Captures the full geometry of the part, allowing comparison to the original CAD model and assessment of overall form deviation (heat maps). Ideal for complex, topology-optimized shapes.
- Traditional Metrology: Calipers, micrometers, height gauges for basic dimensional checks.
- Importance of Technical Drawings: Even for AM parts, clear technical drawings specifying critical dimensions, tolerances (including GD&T), required surface finishes, and inspection datums are essential for effective communication between designers and the manufacturing supplier.
Summary Table: Tolerances & Surface Finish
기능 | As-Built (Typical L-PBF Aluminum) | After Post-Processing | 고려 사항 |
---|---|---|---|
General Tolerance | $ \pm 0.1 – 0.2 $ mm / $ \pm 0.2 – 0.5 $% | < $ \pm 0.05 $ mm (Machined) | Design intent, cost, critical features |
Surface Roughness (Ra) | $ 8 – 25 $ $ \mu m $ (Varies by surface) | $ 3 – 6 $ $ \mu m $ (Bead Blast) | Aesthetics, fatigue, sealing, flow |
< $ 0.8 $ $ \mu m $ (Polished/Machined) | |||
Achievable Precision | 양호 | Excellent (with machining) | Define critical dimensions clearly |
시트로 내보내기
By understanding these characteristics and working with experienced providers like Met3dp, who employ rigorous process control and offer comprehensive post-processing and inspection capabilities, engineers can confidently utilize metal AM to produce automotive sensor holders that meet demanding dimensional and surface requirements.
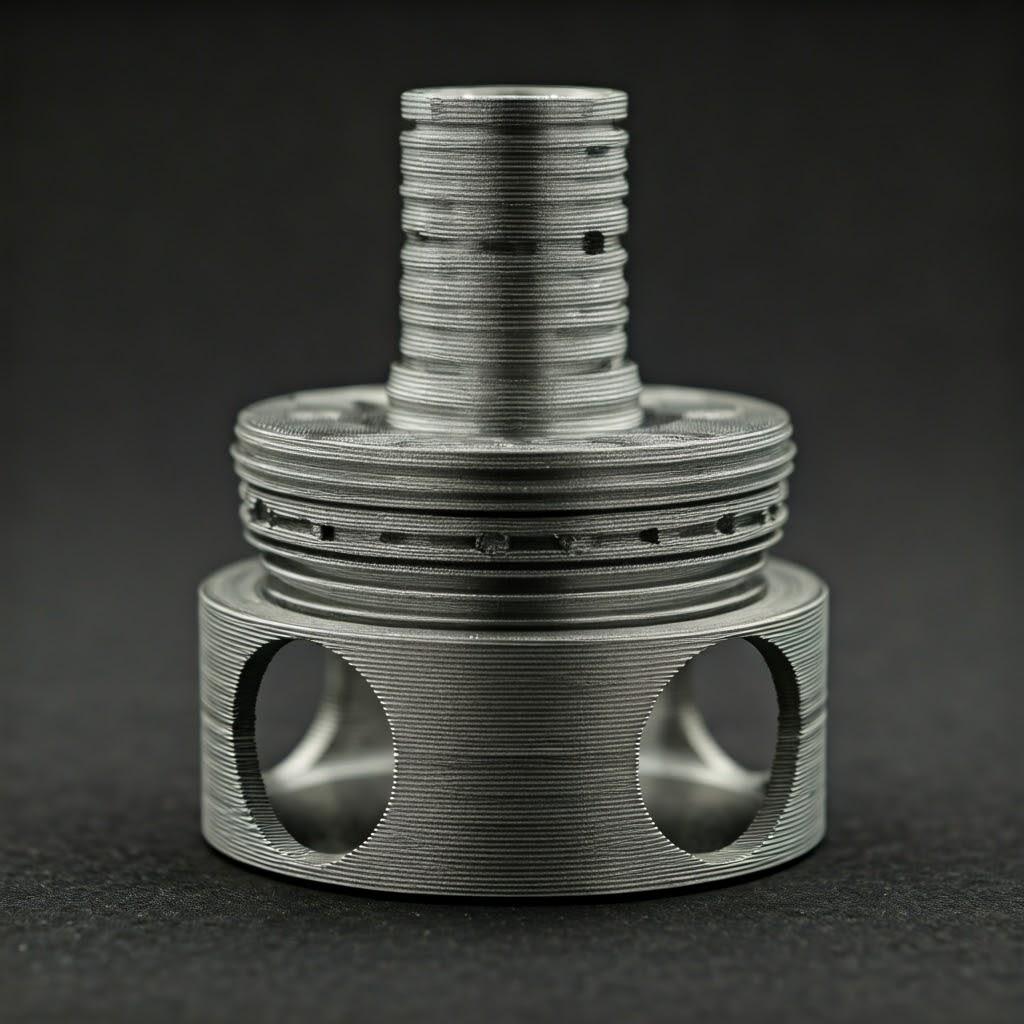
Essential Post-Processing Steps for 3D Printed Automotive Sensor Holders
Producing a part on a metal 3D printer is often just the midpoint of the manufacturing journey. For components like automotive sensor holders, especially those made from reactive materials like aluminum alloys and destined for demanding environments, post-processing is not merely optional; it’s a critical sequence of steps required to achieve the desired material properties, dimensional accuracy, surface finish, and overall component integrity. These steps transform the raw printed part into a functional, finished product ready for assembly. Understanding these processes is vital for designers specifying requirements and for procurement teams evaluating quotes from AM service providers, as post-processing contributes significantly to the final cost and lead time.
1. Stress Relief Heat Treatment:
- Why it’s needed: The rapid heating and cooling cycles inherent in L-PBF create significant internal stresses within the printed part as it’s built layer by layer, anchored to the build plate. These residual stresses can cause distortion or cracking when the part is removed from the plate and can negatively impact mechanical properties and long-term dimensional stability.
- 프로세스: Before removing the part from the build plate, the entire plate with the attached part(s) is typically placed in a furnace and subjected to a controlled heating and cooling cycle. For AlSi10Mg and A7075, this usually involves heating to a moderate temperature (e.g., $ 300^\circ C $ for AlSi10Mg) for a specific duration (e.g., 2 hours) followed by slow cooling. This allows the material’s microstructure to relax, significantly reducing internal stresses.
- Importance: This is arguably the most critical post-processing step for ensuring dimensional stability and preventing unexpected failures later. Reputable providers consider this a standard, non-negotiable step.
2. Part Removal from Build Plate:
- 프로세스: Once stress-relieved and cooled, the sensor holder needs to be separated from the metal build plate it was printed on. This is typically done using:
- 와이어 EDM(방전 가공): Precise method using an electrically charged wire to cut through the base of the part and its supports. Offers a clean cut with minimal force.
- Band Saw: A faster but less precise method, suitable for parts where the base surface finish is not critical or will be machined later. Requires careful handling.
- 고려 사항: The chosen method depends on part geometry, required precision at the base, and production volume.
3. Support Structure Removal:
- Why it’s needed: The support structures used to anchor overhangs and dissipate heat during printing must be removed.
- 프로세스: This is often the most labor-intensive step and can involve:
- 수동 제거: Using pliers, chisels, grinders, or specialized hand tools to break or cut away accessible supports. Requires skill to avoid damaging the part surface. DfAM plays a huge role here – well-designed supports in accessible locations are easier to remove.
- CNC 가공: Supports in easily accessible areas can sometimes be milled away.
- Wire EDM: Can be used for intricate or hard-to-reach supports, but is slower and more expensive.
- 도전 과제: Poorly designed or overly dense supports can be extremely difficult and time-consuming to remove, increasing costs and the risk of part damage. Marks or “witness lines” are often left on the surfaces where supports were attached, usually requiring further finishing.
4. Solution Treatment and Aging (Hardening Heat Treatment – e.g., T6 Temper):
- Why it’s needed: For alloys like AlSi10Mg and particularly A7075, a specific heat treatment cycle is required after printing and stress relief to achieve the desired final mechanical properties (strength, hardness). As-built parts often have suboptimal strength.
- Process (Example for Al Alloys – T6):
- 솔루션 처리: Heating the part to a high temperature (e.g., $ \approx 530^\circ C $ for AlSi10Mg, $ \approx 470^\circ C $ for A7075) to dissolve alloying elements into the aluminum matrix (solid solution).
- 담금질: Rapidly cooling the part (e.g., in water or polymer) to trap the alloying elements in solution.
- Artificial Aging: Reheating the part to a lower temperature (e.g., $ 160 – 180^\circ C $) for an extended period (hours). This causes the alloying elements to precipitate out as fine, dispersed particles within the aluminum matrix, which obstruct dislocation movement and significantly increase strength and hardness.
- Importance: Absolutely essential for achieving the published high-strength properties of alloys like A7075 and optimizing AlSi10Mg performance. Without proper T6 treatment, the parts will be significantly weaker. Met3dp’s metallurgical expertise ensures these critical heat treatments are performed correctly according to material specifications.
5. Machining (Optional but Common):
- Why it’s needed: To achieve tolerances tighter than standard AM capabilities, create specific high-quality surface finishes on mating faces, or precisely finish features like mounting holes or bearing interfaces.
- 프로세스: Using standard CNC milling, drilling, reaming, or turning operations on specific features of the 3D printed part. Requires careful fixture design to hold the often complex AM part geometry securely.
- 고려 사항: Requires DfAM planning (adding machining stock). Adds cost and lead time but guarantees precision where needed.
6. Surface Finishing:
- Why it’s needed: To improve aesthetics, remove support witness marks, enhance corrosion resistance, improve wear resistance, or prepare the surface for painting or coating.
- Common Processes for Aluminum Sensor Holders:
- Bead Blasting: Provides a uniform, non-directional matte finish, cleans the surface, and can slightly improve fatigue life through compressive stress introduction. Various media (glass bead, ceramic) can be used for different effects.
- 텀블링/진동 마감: Smooths surfaces and edges, good for deburring.
- Anodizing: An electrochemical process that creates a hard, corrosion-resistant aluminum oxide layer on the surface. Can be dyed in various colors. Improves wear resistance and provides excellent corrosion protection, highly recommended for automotive exterior or underhood components.
- Powder Coating/Painting: Provides color and an additional protective layer against corrosion and chemicals. Requires proper surface preparation.
- 연마: For achieving mirror-like finishes on specific areas, usually a manual process.
Sequence Example: A typical sequence for a high-performance A7075 sensor holder might be: Print -> Stress Relief -> Wire EDM Removal -> Manual Support Removal -> Solution Treatment & Aging (T6) -> CNC Machining (Critical Faces/Holes) -> Bead Blasting -> Anodizing -> Final Inspection.
Engaging with a full-service provider like Met3dp, which offers or manages these essential post-processing steps alongside printing and material supply, simplifies the supply chain for 자동차 제조업체 and ensures that the final sensor holders meet all performance and quality requirements.
Common Challenges in 3D Printing Sensor Holders and Mitigation Strategies
While metal additive manufacturing offers tremendous advantages for producing complex automotive sensor holders, it’s not without its challenges. Like any advanced manufacturing process, potential issues can arise during printing or post-processing. However, understanding these potential pitfalls and implementing appropriate mitigation strategies – often involving a combination of smart design (DfAM), optimized process parameters, high-quality materials, and robust quality control – allows manufacturers to reliably produce high-quality components. Working with an experienced AM supplier like Met3dp, who possesses deep process knowledge and control, is key to navigating these challenges successfully.
1. Warping and Distortion:
- 도전: Significant temperature gradients between the freshly melted layer and previously solidified material can cause internal stresses to build up. If these stresses exceed the material’s yield strength or the anchoring force of the supports, the part can warp during the build or distort after being removed from the build plate. This is particularly prevalent in large, flat parts or parts with abrupt changes in cross-section.
- 완화 전략:
- Optimized Support Structures: Well-designed supports anchor the part securely and help conduct heat away, reducing thermal gradients. Strategic placement and density are crucial.
- Build Plate Heating: Maintaining an elevated temperature on the build plate reduces the temperature difference between the part and its surroundings, lowering stress accumulation.
- 프로세스 매개변수 최적화: Fine-tuning laser power, scan speed, and scan strategy (e.g., island scanning patterns) can minimize localized heat buildup and residual stress.
- 파트 오리엔테이션: Orienting the part to minimize large flat surfaces parallel to the build plate or reduce thermal mass concentration can help.
- 스트레스 완화 열처리: Performing this step 전에 removing the part from the build plate is essential to relax internal stresses and ensure dimensional stability.
- Simulation: Thermal simulation software can predict areas prone to high stress and distortion, allowing for design or support modifications proactively.
2. Difficulty in Support Structure Removal:
- 도전: Supports are necessary but removing them can be time-consuming, labor-intensive, and risk damaging the part, especially if they are dense or located in hard-to-reach internal channels or delicate features. Support contact points also leave witness marks on the surface.
- 완화 전략:
- DfAM for Supports: Design parts with self-supporting angles (>45°) where possible. Use fillets and chamfers to ease transitions. Design internal channels with self-supporting shapes (teardrop, diamond).
- Optimized Support Generation: Using advanced AM preparation software to generate supports that are strong enough to function but minimal in volume and contact area. Utilizing perforation patterns or specific structures (e.g., tree supports) can make them easier to remove.
- Accessibility Planning: Ensure during the design and orientation phase that support structures will be physically accessible for removal tools.
- Appropriate Removal Techniques: Using the right tools (specialized pliers, EDM, careful machining) based on the support type and location.
- 표면 마감: Plan for downstream finishing steps (blasting, tumbling, machining) to remove support witness marks from critical surfaces.
3. Porosity (Lack of Fusion or Gas Porosity):
- 도전: Small voids or pores within the printed material can compromise its mechanical properties (especially fatigue strength) and density. Porosity can arise from gas trapped within the powder or melt pool (gas porosity) or from incomplete melting and fusion between layers or scan tracks (lack of fusion).
- 완화 전략:
- High-Quality Powder: Using powders with controlled particle size distribution, high sphericity, good flowability, and low internal gas content is paramount. Met3dp’s use of advanced 가스 분무 및 PREP 기술 focuses on producing such high-quality powders. Proper powder handling and storage (e.g., avoiding moisture contamination) are also critical.
- Optimized Process Parameters: Ensuring sufficient energy density (laser power, speed) to fully melt the material and allow layers to fuse properly. Scan strategy optimization also plays a role.
- Controlled Build Atmosphere: Maintaining a high-purity inert gas atmosphere (Argon or Nitrogen) in the build chamber minimizes oxidation and reduces the potential for gas pickup by the melt pool.
- 열간 등방성 프레싱(HIP): For absolutely critical applications requiring maximum density and elimination of internal voids, HIP can be performed as a post-processing step. It involves subjecting the part to high temperature and high isostatic pressure, which collapses internal pores. However, it adds significant cost and lead time.
- 품질 관리: Using non-destructive testing (NDT) methods like CT scanning (Computed Tomography) or micrography on test coupons to detect and quantify porosity levels.
4. Residual Stress and Cracking:
- 도전: Even if significant warping is avoided, high residual stresses can remain within the part, potentially leading to premature failure under load or cracking during post-processing (like machining). Certain alloys, like high-strength A7075, are more susceptible to solidification cracking during the printing process itself if parameters are not carefully controlled.
- 완화 전략:
- 프로세스 제어: As mentioned for warping, optimized parameters, build plate heating, and scan strategies are key. For crack-susceptible alloys like A7075, specialized parameter sets developed through rigorous material science are necessary.
- 스트레스 완화 열처리: Essential for reducing residual stress after printing.
- 디자인 고려 사항: Avoiding sharp internal corners, which act as stress concentrators. Using generous fillets and smooth transitions.
- Material Selection/Development: Sometimes, slightly modified alloy compositions optimized for AM can improve crack resistance.
- Careful Post-Processing: Understanding the stressed state of the part before aggressive machining is important.
5. Surface Finish Imperfections:
- 도전: Beyond general roughness, issues like “stair-stepping” on curved surfaces, partially sintered powder adherence, or dross formation can occur. Support removal marks are also a common imperfection.
- 완화 전략:
- Orientation and Layer Thickness: Using smaller layer thicknesses can reduce the stair-stepping effect on shallow angles, but increases build time. Optimal orientation helps place critical surfaces favorably.
- 프로세스 매개변수: Proper energy input and gas flow help achieve cleaner surfaces.
- 후처리: Bead blasting, tumbling, or machining are effective ways to remove adhered powder and improve overall surface uniformity and finish quality as required by the application.
By anticipating these challenges and leveraging DfAM, advanced process controls, high-quality materials, appropriate post-processing, and rigorous quality assurance protocols, manufacturers like Met3dp can consistently deliver high-performance, reliable 3D printed automotive sensor holders that meet the demanding specifications of their clients in the performance vehicle sector. Addressing these challenges proactively is key to successfully integrating metal AM into the automotive supply chain.
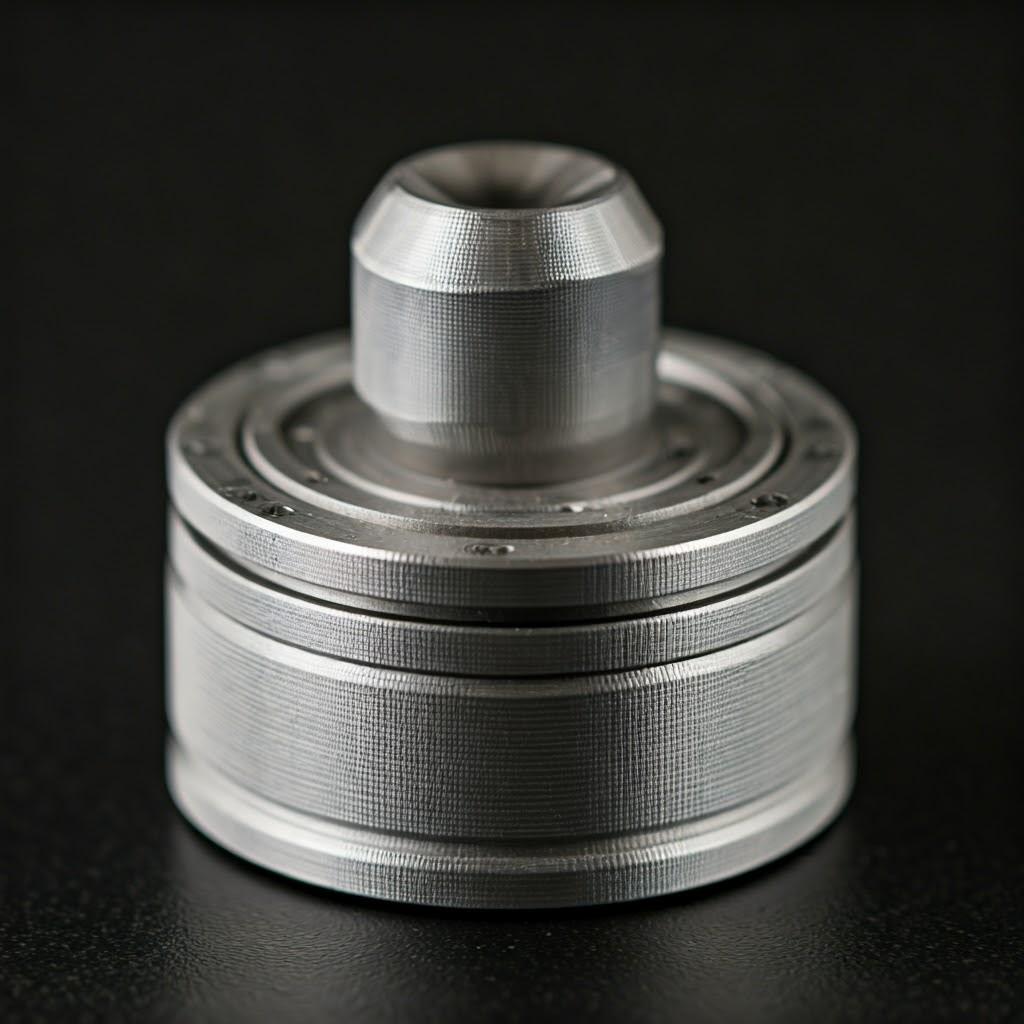
Selecting the Right Metal 3D Printing Service Provider: A Buyer’s Guide for Automotive Needs
Choosing a manufacturing partner is a critical decision, especially when dealing with advanced technologies like metal additive manufacturing for demanding automotive applications. The quality, reliability, and performance of your 3D printed sensor holders depend heavily on the capabilities and expertise of your chosen AM service provider 또는 공급업체. For automotive engineers and procurement managers, navigating the landscape of AM bureaus requires a structured evaluation process focusing on technical competence, quality assurance, material expertise, and overall service. Simply choosing based on the lowest quoted price can lead to substandard parts, project delays, and ultimately higher costs. Here’s a buyer’s guide to help you select the right partner for your automotive sensor holder needs, highlighting criteria where experienced providers like Met3dp excel.
Key Evaluation Criteria for AM Suppliers:
- Technical Expertise and Application Experience:
- DfAM Support: Does the provider offer expert Design for Additive Manufacturing support? Can they collaborate with your engineering team to optimize designs for printability, weight reduction (topology optimization), part consolidation, and cost-effectiveness? Look for providers who proactively suggest improvements rather than just printing the submitted file.
- Materials Science Knowledge: Do they possess deep expertise in the specific materials you require (e.g., AlSi10Mg, A7075)? Do they understand the nuances of processing these materials via AM, including optimal parameter sets and required heat treatments to achieve desired properties? Met3dp, with its roots in advanced powder manufacturing and metallurgy, brings this fundamental expertise.
- Automotive Experience: Have they successfully completed projects for the automotive industry, particularly for performance or specialized vehicles? Can they provide relevant case studies or references demonstrating their ability to meet automotive standards and requirements? Understanding the context (vibration, temperature, packaging constraints) is crucial.
- Equipment, Technology, and Capacity:
- Machine Park: What specific metal AM technologies do they operate (e.g., L-PBF, SEBM)? What is the make, model, and age of their machines? Do they have machines with appropriate build volumes for your sensor holder sizes? Well-maintained, industrial-grade equipment (like the systems Met3dp utilizes) is essential for consistent results.
- 프로세스 제어: What measures do they take to monitor and control the printing process in real-time (e.g., melt pool monitoring, environmental controls)? Consistency is key for part quality.
- Capacity and Scalability: Can they handle your required volumes, from single prototypes to low-volume production runs or potentially larger 도매 주문? What are their typical lead times, and do they have surge capacity or relationships with trusted partners to manage fluctuations in demand?
- Material Quality, Handling, and Traceability:
- Powder Sourcing/Manufacturing: Where do they source their metal powders? Do they manufacture their own, like Met3dp leveraging its 가스 분무 및 PREP 기술, or use qualified third-party suppliers? High-quality, spherical powder with controlled particle size distribution is fundamental to part quality.
- Powder Management: What are their procedures for powder handling, storage (preventing moisture/contamination), testing, and recycling/rejuvenation? Proper management ensures consistent material properties from batch to batch.
- Traceability: Can they provide full traceability for the powder batch used for your specific parts, linking it back to material certifications? This is often a requirement for critical automotive components.
- Quality Management System (QMS) and Certifications:
- ISO 9001: This certification is a baseline requirement, indicating a documented and implemented QMS for ensuring consistent quality and customer satisfaction.
- IATF 16949 (Automotive Specific): While not always held by all AM bureaus (especially smaller ones), certification to this automotive quality standard (or demonstrating compliance with its principles) is a significant advantage when supplying parts directly or indirectly to major automotive OEMs. It signifies robust processes for production part approval (PPAP), risk management (FMEA), traceability, and continuous improvement. Inquire about their QMS and any relevant industry certifications. Met3dp is committed to industry-leading quality standards appropriate for aerospace, medical, and automotive sectors.
- 검사 기능: What metrology equipment do they have in-house (CMM, 3D scanners, surface profilometers)? What NDT capabilities (e.g., CT scanning for porosity checks) can they offer or manage?
- Post-Processing Capabilities:
- Integrated Services: Does the provider offer a comprehensive range of in-house or tightly managed post-processing services, including stress relief, support removal, heat treatment (specifically the required cycles for your alloy, like T6), CNC machining, and various surface finishing options (blasting, anodizing, etc.)? A single point of contact simplifies project management and accountability.
- 전문성: Do they have proven expertise in performing these post-processing steps correctly, particularly critical heat treatments that define the final material properties?
- Customer Service and Communication:
- Quoting Process (RFQ): Is their quoting process clear, detailed, and timely? Does the quote break down costs (printing, material, post-processing)?
- 응답성: Are they responsive to inquiries and technical questions?
- 프로젝트 관리: Do they provide clear communication throughout the project lifecycle, including updates on progress and potential challenges?
- 기술 지원: Is knowledgeable engineering support available to discuss design feasibility, material selection, and application requirements?
Supplier Evaluation Checklist:
기준 | 주요 질문 | Ideal Response / What to Look For |
---|---|---|
Expertise & Experience | DfAM support? Material knowledge (AlSi10Mg/A7075)? Automotive project examples? | Collaborative design advice, deep material understanding, relevant case studies/references |
Equipment & Technology | Machine type/age/volume? Process monitoring? | Industrial-grade L-PBF/SEBM, evidence of control, suitable build size |
Capacity & Scalability | Prototype/Production volume? Lead times? Scalability for 모조리? | Clear capacity statements, realistic lead times, plan for scaling |
Material Quality & Handling | Powder source/quality control? Handling/storage procedures? Traceability? | High-quality powder (e.g., Met3dp’s atomized powders), documented procedures, batch traceability |
Quality Management & Certs | ISO 9001? IATF 16949 compliance/awareness? Inspection capabilities (CMM, 3D scan)? NDT options? | ISO 9001 minimum, automotive standard awareness/compliance, appropriate metrology & NDT |
포스트 프로세싱 | In-house/managed services (Heat Treat, Machining, Finishing)? Expertise in required steps (e.g., T6)? | Comprehensive, controlled services; proven heat treatment capabilities |
Customer Service & Communication | Clear quotes? Responsiveness? Project updates? Technical support availability? | Detailed RFQ response, prompt communication, proactive updates, accessible engineering support |
시트로 내보내기
By thoroughly evaluating potential suppliers against these criteria, automotive companies can build strong partnerships with capable metal AM providers like Met3dp, ensuring they receive high-quality, reliable sensor holders that meet the demanding performance and quality standards of the industry. This diligence upfront mitigates risks and maximizes the benefits of adopting additive manufacturing.
Cost Factors and Lead Time Considerations for Wholesale and Custom Orders
Integrating 3D printed metal sensor holders into automotive projects, whether for prototypes, custom builds, or 모조리 production volumes, requires a clear understanding of the associated costs and lead times. Unlike traditional high-volume methods where tooling amortization dominates, additive manufacturing costs are driven by different factors, primarily related to machine time, material consumption, and labor-intensive post-processing. Lead times are also influenced by a unique set of variables. Understanding these dynamics helps engineers optimize designs for cost-effectiveness and allows procurement specialists to budget accurately and manage project timelines.
Key Cost Drivers for Metal 3D Printed Sensor Holders:
- Part Design Complexity and Volume:
- Bounding Box Volume: Larger parts simply take up more space in the machine and consume more material, directly increasing cost.
- True Part Volume: The actual volume of material used in the part influences material cost and, to some extent, print time. Topology optimization and lattice structures (DfAM) can significantly reduce this.
- 복잡성: While AM handles complexity well, highly intricate designs might require more extensive support structures or more careful orientation, slightly impacting build time and post-processing effort. However, complexity is less of a cost driver than in traditional machining.
- Material Type and Consumption:
- 파우더 비용: Different metal powders have vastly different costs per kilogram. High-performance alloys like A7075 or Titanium are significantly more expensive than standard AlSi10Mg or stainless steels.
- Amount Used: The volume of the part itself plus the volume of required support structures determines the total material consumed. Efficient DfAM minimizes both.
- 파우더 재활용: Efficient powder recycling and reuse practices by the AM supplier can help mitigate material costs, though there’s always some loss and need for rejuvenation. Met3dp’s focus on high-quality powder production also implies efficient usage protocols.
- Machine Time (Printing Time):
- Build Height: This is often the primary driver of print time. The machine deposits material layer by layer, so taller parts take longer, regardless of how many parts are nested on the build plate.
- Number of Layers: Determined by build height and chosen layer thickness (thinner layers = longer print time but potentially better surface finish).
- Volume to Scan: The total area the laser needs to scan per layer influences time. Dense, solid parts take longer per layer than those with thin walls or lattice structures.
- Machine Occupancy: The cost includes amortization of the expensive AM machine, operational costs (power, gas), and operator time. Efficient nesting of multiple parts onto a single build plate can significantly reduce the per-part machine time cost.
- 사후 처리 요구 사항:
- Labor Intensity: Support removal is often manual and can be a major cost component, especially for complex parts with hard-to-reach supports.
- 열처리: Stress relief and hardening cycles require furnace time and energy, adding cost. Complex or specialized cycles cost more.
- 가공: If CNC machining is required for tight tolerances or specific finishes, this adds significant cost based on setup time, machine time, and complexity.
- 표면 마감: Steps like bead blasting, anodizing, or painting add cost based on the process, required masking, and labor involved. Anodizing A7075 might require specific protocols compared to AlSi10Mg.
- Quality Assurance and Inspection:
- Level of Inspection: Basic dimensional checks are standard, but requirements for full CMM reports, 3D scanning comparisons, GD&T analysis, or NDT (like CT scanning for porosity) add cost based on equipment time and operator expertise.
- Documentation: Requirements for extensive documentation (material certs, inspection reports, PPAP elements) add administrative overhead cost.
- Order Quantity (Economies of Scale):
- Setup Costs: While AM avoids tooling costs, there are still setup costs associated with preparing the build file, loading the machine, and initial process verification. These costs are amortized over the number of parts in an order.
- Nesting Efficiency: Larger orders allow for more efficient nesting of parts on the build plate, maximizing machine utilization and reducing per-part print time.
- Post-Processing Batches: Handling parts in larger batches for heat treatment, finishing, and inspection can be more efficient than processing single pieces.
- Wholesale Pricing: For significant volumes, 공급업체 can often offer discounted 도매 가격 reflecting these efficiencies. However, the cost reduction curve in AM is generally flatter than in casting or injection molding.
Lead Time Considerations:
Lead time is the total time from order placement to part delivery. It’s influenced by:
- Quoting and Order Processing: Initial communication, file preparation, and scheduling (can be hours to days).
- Machine Queue: The availability of the appropriate machine; popular machines may have backlogs (can be days to weeks).
- 인쇄 시간: Highly variable based on build height and volume (can range from hours for small parts to several days for large/tall builds).
- Cooling and Stress Relief: Required time for the build to cool and undergo heat treatment (typically 1-2 days).
- Part Removal and Support Removal: Labor-dependent (hours to days, depending on complexity and quantity).
- Hardening Heat Treatment (if required): Furnace time for solutionizing and aging (typically 1-2 days, including ramp/soak times).
- 가공 및 마무리: Depends on the complexity and number of steps (can range from hours to several days).
- 품질 검사: Time required for specified measurements and documentation (hours to days).
- 해운: Transit time to the customer.
Typical Lead Time Ranges (Estimates):
- Prototypes (1-5 parts): Often 5-15 business days, depending on complexity and post-processing. Expedited options may be available at higher cost.
- Low-Volume Production (10-100 parts): Typically 2-6 weeks, heavily dependent on nesting efficiency and post-processing batching.
- Wholesale Orders (100+ parts): May require dedicated machine time or multiple machines; lead times need careful planning and discussion with the supplier, potentially involving staged deliveries over several weeks or months.
Engaging with a provider like Met3dp, which integrates various 제품 and services from powder to finished part, can potentially streamline the workflow and offer more predictable lead times compared to managing multiple vendors for printing, heat treatment, and machining. Clear communication about requirements and realistic timelines is crucial for successful project execution.
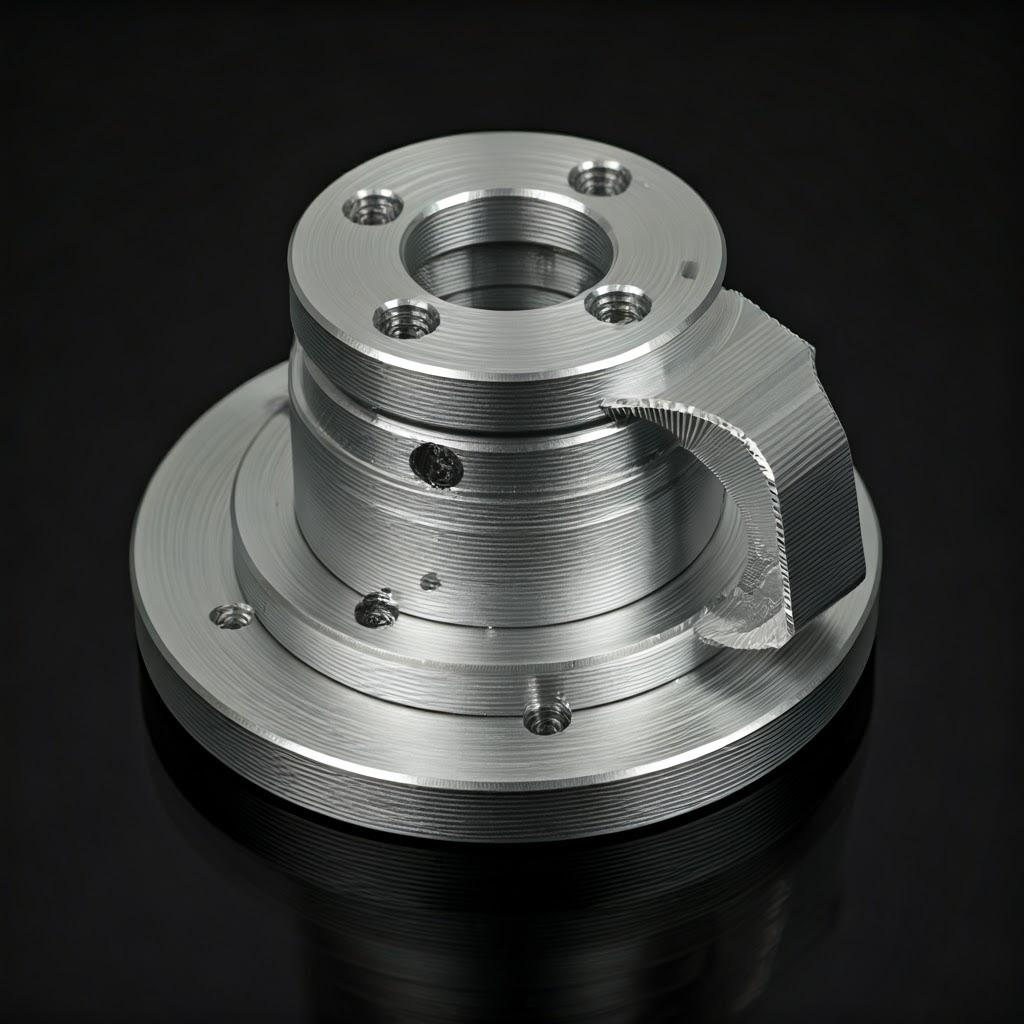
Frequently Asked Questions (FAQ) about 3D Printed Automotive Sensor Holders
As metal additive manufacturing becomes increasingly adopted in the automotive sector, engineers, designers, and procurement professionals often have questions about its application for components like sensor holders. Here are answers to some frequently asked questions:
1. How does the strength and performance of 3D printed aluminum (AlSi10Mg, A7075) sensor holders compare to traditionally manufactured ones (CNC machined from billet, cast)?
This is a nuanced question.
- 머티리얼 속성: Metal AM parts, particularly after appropriate heat treatment (like T6 for AlSi10Mg and A7075), can achieve mechanical properties (yield strength, ultimate tensile strength) that are comparable, and sometimes even superior, to cast equivalents due to the fine-grained microstructure formed during the rapid solidification process. Compared to wrought materials (like billet used for CNC machining), AM parts may exhibit slightly lower ductility or fatigue strength in some orientations due to the layer-wise build process and potential for microscopic imperfections if not printed under optimal conditions. However, for alloys like A7075, optimized AM processes can achieve strengths very close to traditional wrought tempers.
- 디자인 최적화: The key advantage of AM often lies not in matching bulk material properties but in enabling superior designs. Topology optimization allows AM sensor holders to be significantly lighter for the same stiffness or strength compared to a traditionally designed part. This means the AM part can meet or exceed performance requirements (like maintaining sensor position under vibration) at a lower weight.
- 결론: When designed using DfAM principles and manufactured by an expert provider using quality materials and processes (including heat treatment), 3D printed sensor holders can offer equivalent or superior 기능적 성능 compared to traditional methods, often with significant weight savings. Collaboration with the AM supplier is key to ensure properties meet specifications.
2. Is metal 3D printing a cost-competitive alternative to CNC machining for producing automotive sensor holders?
It depends heavily on several factors:
- 부품 복잡성: For simple bracket geometries that are easily machined from standard stock, CNC machining is almost always more cost-effective, especially as volume increases. For highly complex, topology-optimized, or consolidated designs that would require intricate multi-axis machining, multiple setups, or significant material waste via CNC, metal AM becomes much more competitive, even at lower volumes.
- 생산량: Metal AM has minimal setup cost (no tooling) making it economical for prototypes and low volumes (e.g., 1-100 parts). CNC machining has moderate setup costs but lower per-part costs at higher volumes. Traditional casting has very high tooling costs but the lowest per-part cost at very high volumes (thousands). There is a crossover point where CNC becomes cheaper than AM, and another where casting becomes cheapest. For sensor holders, AM often wins for complexity and low-to-mid volumes, while CNC is better for simpler shapes or moderate volumes.
- Lead Time Requirements: For rapid prototyping or urgent low-volume needs, AM’s speed can provide value that outweighs a potentially higher per-part cost.
- 가치 제안: If AM enables significant weight reduction or performance improvement (e.g., through topology optimization) that provides downstream value (better vehicle performance, fuel economy), the higher initial cost might be justified.
- Recommendation: Evaluate both AM and CNC (if feasible for the design) based on quotes reflecting the specific geometry, material, quantity, and tolerance requirements.
3. What quality assurance (QA) and inspection processes are typically used for critical 3D printed automotive components like sensor holders?
Given the critical function of sensors, rigorous QA is essential. Common practices include:
- Material Certification: Ensuring the metal powder used conforms to required specifications (chemistry, particle size distribution) and providing batch traceability.
- 프로세스 모니터링: Utilizing in-situ monitoring capabilities on the AM machine (e.g., melt pool monitoring, thermal imaging) where available, and tightly controlling process parameters (laser power, speed, gas atmosphere).
- Post-Process Verification: Confirming that required heat treatments were performed correctly (e.g., hardness testing).
- 치수 검사: Using CMM or 3D scanning to verify critical dimensions and GD&T specifications against the technical drawing or CAD model. Full part scanning can confirm complex geometries.
- 비파괴 검사(NDT): For highly critical applications, CT scanning can be used to inspect internal integrity and detect porosity or inclusions. Dye penetrant testing or magnetic particle inspection might be used to check for surface-breaking defects, although less common for typical sensor brackets unless specific features warrant it.
- Documentation: Providing certificates of conformity, material certifications, dimensional inspection reports, and potentially elements of Production Part Approval Process (PPAP) documentation if required by the automotive customer. Reputable 공급업체 like Met3dp have robust QMS procedures incorporating many of these elements.
4. Can metal AM realistically scale to handle large volume or wholesale orders (e.g., hundreds or thousands) for sensor holders needed for a production vehicle line?
Scalability in AM is different from traditional mass production.
- Current State: Metal AM is generally best suited for low-to-medium volume production (tens to hundreds, potentially low thousands depending on size/complexity). Producing tens or hundreds of thousands of parts via AM for a mass-market vehicle is typically not cost-effective compared to casting or injection molding (for polymer alternatives).
- Scaling Mechanisms: Scaling AM production involves:
- Multiple Machines: Utilizing a fleet of printers running in parallel.
- 중첩: Maximizing the number of parts per build plate.
- 자동화: Implementing automated systems for powder handling, build plate exchange, and potentially some post-processing steps (though support removal often remains manual).
- Feasibility: For niche performance vehicles, motorsport, or specialized automotive applications with lower annual volumes, using AM for production sensor holders is entirely feasible and increasingly common. For 모조리 orders supplying these markets, AM suppliers with sufficient machine capacity and streamlined workflows can meet demand.
- Future Trends: As AM technology matures, print speeds increase, and automation improves, the economics will continue to shift, potentially making AM viable for larger volumes in the future. Discuss specific volume requirements and timelines directly with potential suppliers to assess their capacity.
5. What information does an AM service provider need to provide an accurate quote (RFQ) for a 3D printed sensor holder?
To get a timely and accurate quote, provide the following:
- CAD Model: A 3D model in a standard format (e.g., STEP, IGES, STL – though STEP is preferred for detailed analysis).
- Technical Drawing (if available): A 2D drawing specifying critical dimensions, tolerances (including GD&T), required surface finishes for specific features, and material callouts.
- Material Specification: Clearly state the desired alloy (e.g., AlSi10Mg, A7075) and any required temper/heat treatment condition (e.g., T6).
- 주문 수량: Specify the number of parts needed (for prototypes, initial batch, or estimated annual volume).
- 사후 처리 요구 사항: Detail any necessary machining, specific surface finishes (e.g., bead blast, anodize type/color), or testing/inspection requirements.
- Application Context (Optional but helpful): Briefly explaining the part’s function and operating environment can help the supplier offer better DfAM advice or material suggestions.
Providing comprehensive information upfront allows the AM supplier to accurately assess manufacturability, estimate costs, and propose realistic lead times.
Conclusion: Driving Automotive Innovation with Advanced Metal 3D Printed Sensor Holders
The relentless pursuit of performance, efficiency, and advanced functionality in the automotive industry demands continuous innovation in every component, right down to the essential sensor holders. As we’ve explored, metal additive manufacturing offers a powerful toolkit for engineers and designers striving to meet these demands. By leveraging the unique capabilities of processes like Laser Powder Bed Fusion, manufacturers can create automotive sensor holders that are not just functional, but truly optimized.
The ability to produce complex, lightweight structures through topology optimization, consolidate multiple components into a single integrated part, and utilize high-performance aluminum alloys like AlSi10Mg and A7075 translates directly into tangible benefits: reduced vehicle mass, improved packaging solutions in constrained spaces, enhanced component stiffness for reliable sensor readings, and accelerated development cycles through rapid prototyping. DfAM principles empower engineers to think beyond traditional manufacturing constraints, unlocking new levels of design efficiency.
However, realizing these benefits requires more than just access to a 3D printer. It demands a holistic approach encompassing smart design, careful material selection, meticulous process control during printing, critical post-processing steps like heat treatment and finishing, and rigorous quality assurance. Most importantly, it requires partnership with a knowledgeable and capable 첨가 제조 공급업체.
Met3dp stands as a leader in this field, offering comprehensive solutions that span the entire AM value chain. From our industry-leading metal powder production using advanced atomization techniques ensuring material quality, to our state-of-the-art printing equipment and deep expertise in materials science and process optimization, we provide the foundation for producing high-integrity components. Our commitment extends through essential post-processing and quality validation, ensuring that the final sensor holders delivered to our automotive clients meet the most stringent performance and reliability standards.
For automotive OEMs, Tier 1/2 suppliers, motorsport teams, and aftermarket specialists seeking a reliable partner to leverage metal AM for sensor holders and other critical components, Met3dp offers the technology, expertise, and collaborative approach needed to drive innovation forward. We invite you to engage with our team to explore how our capabilities can help you achieve your specific project goals, whether it’s optimizing an existing design, developing a novel solution, or scaling production for your next high-performance vehicle.
Contact Met3dp today to discuss your automotive additive manufacturing needs and discover how we can help you engineer the future.
공유
중국 칭다오에 본사를 둔 선도적인 적층 제조 솔루션 제공업체인 MET3DP Technology Co. 당사는 산업용 3D 프린팅 장비와 고성능 금속 분말을 전문으로 합니다.
관련 기사
Met3DP 소개
최근 업데이트
제품
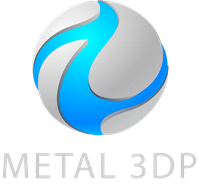
3D 프린팅 및 적층 제조용 금속 분말