High-Precision Instrument Mounting via Metal 3D Printing
목차
In the intricate world of advanced technology, where measurements push the boundaries of physics and devices operate under demanding conditions, the humble mount plays a surprisingly critical role. Precision instruments – whether they are aligning lasers, stabilizing sensors in satellites, holding delicate samples in medical scanners, or ensuring accuracy in metrology labs – rely entirely on their mounting systems for stability, alignment, and operational integrity. The slightest vibration, thermal expansion, or misalignment can compromise data, lead to system failure, or invalidate results. Traditionally, manufacturing these high-precision instrument mounts involved complex multi-axis CNC machining, often from solid billets of specialized materials. While effective, this approach faces limitations in geometric complexity, material waste, lead times, and the ability to integrate advanced features like internal cooling channels or optimized lightweight structures. Enter metal additive manufacturing (AM), commonly known as metal 3D 프린팅. This transformative technology offers a powerful alternative, enabling the creation of instrument mounts with unprecedented design freedom, optimized performance characteristics, and the potential for significant cost and lead time efficiencies, particularly for complex or low-volume production runs. This post delves into the world of high-precision instrument mounts, exploring why metal AM is rapidly becoming the go-to solution for engineers and procurement managers across aerospace, automotive, medical, and industrial sectors, with a specific focus on materials like 316L stainless steel and the remarkable low-expansion alloy, Invar.
Introduction: The Critical Role of Precision Instrument Mounts in High-Tech Industries
Precision instrument mounts are far more than simple brackets or fixtures; they are engineered components integral to the function and reliability of sophisticated systems. Their primary purpose is to securely hold, position, and maintain the alignment of sensitive instruments relative to a reference frame or other components, often under challenging environmental conditions. Think of the laser system in a semiconductor manufacturing tool, the optical components in a satellite telescope, the sensors in an autonomous vehicle’s LiDAR system, or the probes in a coordinate measuring machine (CMM). In each case, the mount must provide a stable, predictable, and often isolated platform.
Why Stability and Precision Matter:
- Maintaining Alignment: Optical systems require components to be aligned within microns or even nanometers. Any drift or misalignment in the mounts due to vibration, shock, or thermal changes can render the system useless. Laser paths, sensor orientations, and sample positions must remain exact.
- 진동 감쇠: Many instruments are sensitive to external vibrations (from machinery, acoustics, or transport). Mounts often need to incorporate damping features or be made from materials that inherently reduce the transmission of vibrations to the instrument. Undamped vibrations can introduce noise into measurements or cause fatigue failures.
- 열 안정성: Temperature fluctuations can cause materials to expand or contract. In precision applications, even minute thermal expansion can lead to significant misalignment or stress. Mounts, especially those used in optics, metrology, or space applications, must often exhibit minimal dimensional change across a wide operating temperature range. This necessitates the use of specialized low coefficient of thermal expansion (CTE) materials.
- Structural Integrity: Mounts must be strong and stiff enough to support the instrument’s weight and withstand any operational loads (like acceleration in aerospace or automotive applications) without deforming. Deflection under load can cause misalignment.
- Environmental Resistance: Depending on the application, mounts may need to resist corrosion (e.g., in medical or marine environments), outgassing (in vacuum or space applications), or extreme temperatures.
The Limitations of Traditional Manufacturing:
For decades, CNC machining has been the standard for producing high-quality mounts. However, it presents certain challenges, especially as instrument designs become more complex and performance demands increase:
- Geometric Constraints: Machining complex internal features, organic shapes optimized for stiffness-to-weight ratio (topology optimization), or integrated functionalities like conformal cooling channels can be extremely difficult, time-consuming, or impossible. This often leads to designs that are compromises rather than optimal solutions.
- 재료 낭비: Subtractive manufacturing starts with a larger block of material and removes what isn’t needed. For expensive or specialized materials like Invar, this can result in significant and costly waste.
- Assembly Complexity: Achieving complex geometries often requires machining multiple individual parts and then assembling them. Each interface in an assembly introduces potential tolerance stack-up, alignment errors, and points of failure. Part consolidation, where multiple functions are integrated into a single component, is highly desirable but often difficult with machining.
- 리드 타임: Tooling setup, programming, machining time, and assembly can lead to long lead times, particularly for intricate designs or small production volumes. Prototyping iterations can be slow and expensive.
The demand for higher performance, greater design complexity, reduced weight, and faster development cycles in industries utilizing sensitive instrumentation has created a significant opportunity for alternative manufacturing processes. Metal additive manufacturing directly addresses many of the limitations inherent in traditional methods, offering a compelling pathway to creating the next generation of stable mounting solutions for critical, high-tech applications. Companies seeking a competitive edge in producing or utilizing high-precision equipment are increasingly turning to metal AM service providers who possess the expertise and advanced capabilities, like those found at Met3dp, to realize these advanced designs.
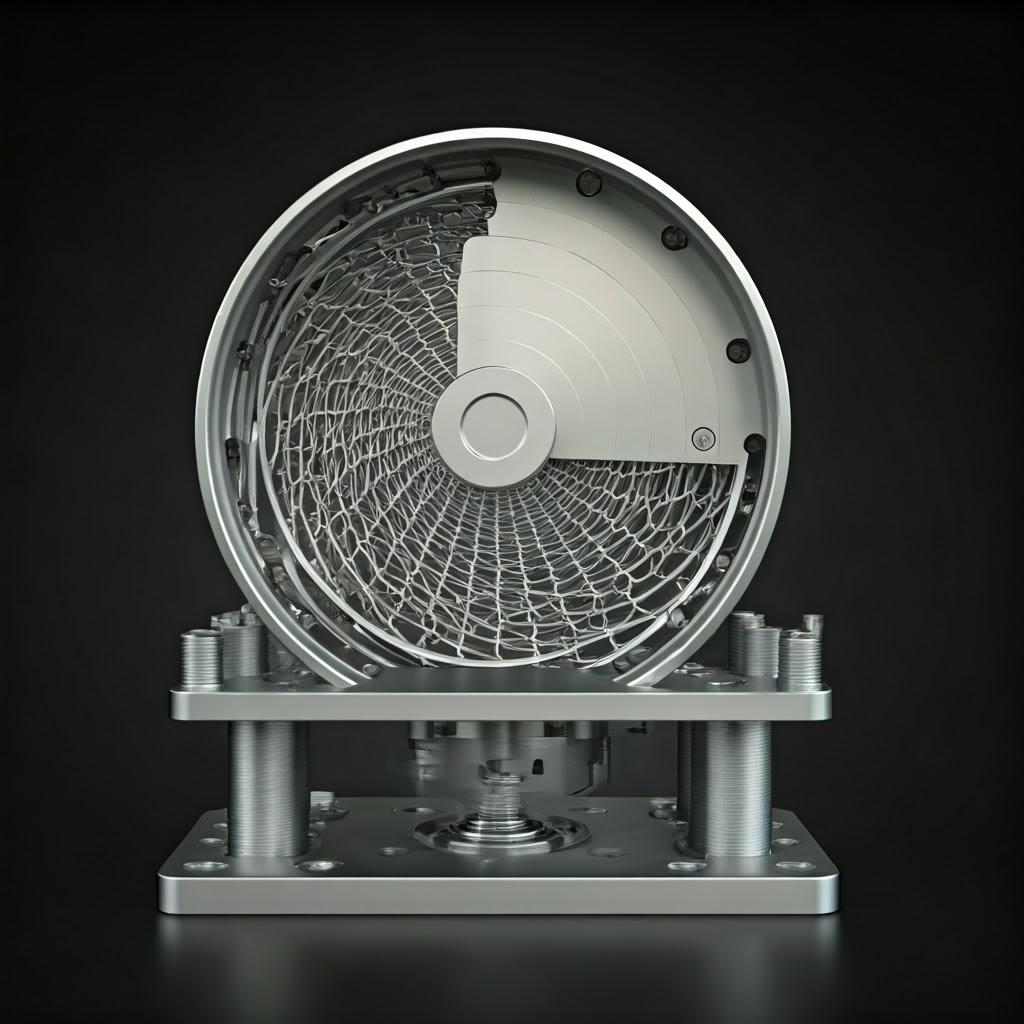
Applications & Use Cases: Where Precision Mounting Excels
The need for high-precision, stable mounting solutions permeates virtually every advanced technology sector. The ability to hold components steady, aligned, and isolated from environmental disturbances is fundamental. Metal additive manufacturing is making significant inroads into these applications by enabling designs and material combinations previously unattainable. Here’s a look at key industries and specific use cases where 3D printed precision instrument mounts are delivering value:
1. Aerospace and Defense:
- Satellite Instrumentation: Mounts for optical payloads (telescopes, cameras), sensors, antennas, and electronics must withstand launch vibrations, thermal cycling in space (-150°C to +150°C or wider), and maintain extreme pointing accuracy over years. Low CTE materials like Invar, often combined with topology optimization for minimum weight (critical for launch costs), are ideal candidates for AM.
- Aircraft Sensors and Avionics: Mounts for gyroscopes, accelerometers, navigation systems, and targeting pods require high stiffness, vibration damping, and reliability under high G-forces and varying temperatures. AM allows for complex, lightweight brackets integrated directly into the aircraft structure.
- Optical Benches and Targeting Systems: Ground-based or airborne optical systems need exceptionally stable mounts for lasers, mirrors, and detectors. AM enables the creation of monolithic optical benches with integrated mounts, reducing assembly complexity and improving stability.
2. Medical Devices:
- Diagnostic Imaging Equipment (MRI, CT, PET): Sensitive detectors and patient positioning systems require mounts that are non-magnetic (often requiring specific alloys), vibration-resistant, and dimensionally stable. AM can create custom mounts tailored to specific machine geometries and patient interfaces. Materials like 316L stainless steel or titanium alloys are commonly used.
- Surgical Robotics and Tooling: Mounts for robotic arms, cameras, and surgical instruments demand high precision, rigidity, and the ability to be sterilized. AM allows for complex, ergonomic designs, often incorporating internal channels for cooling or fluid delivery, using biocompatible materials like 316L or Ti6Al4V.
- Laboratory Automation and Analysis: High-throughput screening systems, microscopes, and sample handlers rely on precise, repeatable positioning. Custom 3D printed mounts can optimize workflow, reduce footprint, and improve the integration of various components.
3. Metrology and Scientific Instrumentation:
- Coordinate Measuring Machines (CMMs): Probe heads, sensor mounts, and structural components require extreme dimensional stability and stiffness to ensure measurement accuracy down to the sub-micron level. Low-CTE materials like Invar are essential, and AM allows for optimized frame designs and probe mountings.
- Microscopy (Electron, Atomic Force): Mounts must provide exceptional vibration isolation and thermal stability to achieve atomic-scale resolution. AM enables the creation of intricate, damped mounting structures tailored to specific microscope stages and environmental chambers.
- Synchrotrons and Particle Accelerators: Beamline instrumentation, detector mounts, and sample manipulators operate in demanding environments (vacuum, radiation) and require precise alignment. AM allows for the creation of complex mounts from specialized materials resistant to these conditions.
- Optical Testing and Interferometry: Mounts for lasers, mirrors, beam splitters, and detectors used in optical testing setups require high stability and fine adjustment capabilities. AM can produce mounts with integrated flexures or adjustment mechanisms, often using low-CTE Invar.
4. Industrial Automation and Manufacturing:
- Robotic End-Effectors: Mounts for grippers, sensors, and tools on industrial robots need to be lightweight (to maximize payload and speed) yet rigid. AM enables topology-optimized designs tailored to specific tasks.
- Machine Vision Systems: Camera and lighting mounts require stable positioning for reliable inspection and guidance. Custom AM mounts can fit into tight spaces on production lines and integrate cooling or protective features.
- Semiconductor Manufacturing Equipment: Wafer handling systems, lithography tools, and inspection stations demand ultra-high precision and stability, often in cleanroom or vacuum environments. Low-outgassing materials and low-CTE alloys like Invar are critical, and AM provides design flexibility for complex equipment geometries. Wholesale precision components suppliers are increasingly looking to AM to meet the custom needs of this sector.
5. Automotive:
- Sensor Mounting (LiDAR, Radar, Cameras): Autonomous driving and ADAS systems rely on precise sensor alignment. Mounts must withstand road vibrations, temperature swings, and impacts while maintaining sensor calibration. AM allows for integrated, durable mounting solutions specific to vehicle platforms.
- Engine Test Cells: Mounting sensors for temperature, pressure, and vibration measurement in engine dynamometers requires robustness and thermal stability. Custom AM mounts can position sensors optimally in harsh testing environments.
- Manufacturing Jigs and Fixtures: While not directly instrument mounts, the fixtures used to hold parts during manufacturing or inspection require high precision and stability. AM is widely used to create custom, lightweight, and ergonomic fixtures quickly.
Across these diverse fields, the core requirements often converge: precision, stability (mechanical and thermal), reliability, and often, customization or complex geometry. Metal additive manufacturing, particularly using advanced powder bed fusion techniques like Selective Electron Beam Melting (SEBM) or Selective Laser Melting (SLM), provides the tools to meet these demanding requirements. Service providers specializing in 금속 3D 프린팅 are crucial partners for companies needing these high-performance components, offering expertise in material selection, design optimization, and process control to ensure the final mount meets or exceeds specifications. The ability to source custom instrument mount manufacturers who leverage AM technology is becoming a key competitive advantage.
Why Metal Additive Manufacturing for Instrument Mounts? Unlocking Performance & Design Freedom
The decision to adopt metal additive manufacturing (AM) for producing high-precision instrument mounts stems from its inherent advantages over traditional subtractive methods like CNC machining, particularly when dealing with complex designs, specialized materials, or the need for optimized performance. While machining remains suitable for simpler geometries or high-volume production of standardized parts, AM unlocks possibilities previously considered unfeasible or cost-prohibitive. Engineers and procurement managers are increasingly recognizing these benefits:
1. 독보적인 디자인 자유도 및 복잡성:
- 복잡한 지오메트리: AM builds parts layer by layer, allowing for intricate internal channels (for cooling, fluid flow, or cable routing), complex external shapes, negative draft angles, and hollow structures without the constraints imposed by cutting tools or mold requirements. This freedom enables designs that are truly optimized for function, not just manufacturability via traditional means.
- 토폴로지 최적화: Engineers can use software tools to define load paths, constraints, and performance goals (e.g., maximize stiffness, minimize weight), and the software generates an organic, often lattice-like structure that meets these requirements using the minimum amount of material. Machining such complex shapes is often impossible or economically unviable. For instrument mounts, this means creating structures that are exceptionally stiff and stable exactly where needed, while drastically reducing overall mass – crucial for aerospace, robotics, and portable devices.
- 파트 통합: Multiple components that would traditionally be manufactured separately and then assembled (e.g., a bracket, a heat sink, a vibration damper) can often be redesigned and printed as a single, monolithic part. This eliminates assembly time and costs, removes potential points of failure or misalignment at interfaces, improves overall structural integrity, and reduces tolerance stack-up issues.
2. Lightweighting:
- Reduced Mass: Through topology optimization and the ability to create internal lattice structures or hollow sections, AM can significantly reduce the weight of instrument mounts compared to solid machined components, while maintaining or even increasing stiffness and strength.
- 혜택: Lightweighting is critical in applications like:
- 항공우주: Lower launch costs, improved fuel efficiency, increased payload capacity.
- 자동차: Better vehicle dynamics, fuel economy.
- 로봇 공학: Faster movements, lower inertia, higher payload capacity for the robot arm.
- 의료 기기: Improved portability, easier handling for portable or wearable devices.
3. Enhanced Performance Characteristics:
- Integrated Functionality: Design freedom allows for the direct integration of performance-enhancing features. Examples include:
- 컨포멀 냉각 채널: Internal channels that precisely follow the contour of heat-generating components or critical areas of the mount, providing far more efficient thermal management than drilled channels or attached heat sinks.
- Vibration Damping Structures: Incorporating specific lattice geometries or designing flexures directly into the mount can help isolate the instrument from external vibrations.
- Optimized Flow Paths: For mounts that also serve as manifolds or conduits for fluids or gases.
- 머티리얼 속성: AM processes often result in fine-grained microstructures, which can lead to excellent mechanical properties (strength, fatigue resistance) that meet or exceed those of cast or wrought materials, especially after appropriate post-processing like Hot Isostatic Pressing (HIP).
4. Material Possibilities:
- Specialized Alloys: AM excels at processing materials that are difficult or expensive to machine, such as high-temperature superalloys, certain titanium alloys, and low-expansion alloys like Invar (FeNi36). Machining Invar, for instance, is notoriously challenging due to its gummy nature and work hardening. AM provides a more efficient route to producing complex Invar components essential for thermally stable mounts.
- Novel Materials: The layer-by-layer nature of AM opens doors to functionally graded materials (varying composition across the part) or metal matrix composites, although these are still emerging areas.
- 재료 낭비 감소: As an additive process, AM uses only the material needed to build the part and its supports, resulting in significantly less waste compared to subtractive machining, especially for complex parts or expensive materials like Invar or aerospace-grade titanium. This “buy-to-fly” ratio is much more favorable.
5. Rapid Prototyping and Iteration:
- 속도: AM allows for the rapid production of prototypes directly from CAD data, often within days, without the need for tooling. This accelerates design cycles, enabling engineers to test multiple iterations quickly and converge on an optimal design much faster than with traditional methods.
- Cost-Effective Iteration: The cost of producing a single prototype or a small batch via AM is often significantly lower than setting up for machining, making design exploration more accessible.
6. Customization and Low-Volume Production:
- 온디맨드 제조: AM is ideal for producing custom, one-off parts or small batches without the high setup costs associated with traditional manufacturing. This is perfect for specialized scientific instruments, custom medical device fixtures, or replacement parts for legacy systems.
- Tailored Solutions: Instrument mounts can be perfectly tailored to the specific geometry, weight, and performance requirements of the instrument and its operating environment.
Why Choose AM Over CNC Machining for Mounts? A Comparative Glance:
기능 | 금속 적층 제조(AM) | CNC 가공 | Advantage for Precision Mounts |
---|---|---|---|
디자인 복잡성 | High (Internal channels, lattices, organic shapes) | Moderate to High (Limited by tool access, setup) | AM enables optimized, lightweight, and consolidated designs impossible with machining. |
부품 통합 | 우수 | 제한적 | AM reduces assembly errors, weight, and potential failure points. |
경량화 | Excellent (Topology optimization, internal voids) | Limited (Material removal constraints) | AM significantly reduces mass while maintaining stiffness, crucial for dynamic/mobile applications. |
재료 낭비 | Low (Additive process) | High (Subtractive process, especially complex parts) | AM is more cost-effective and sustainable for expensive materials like Invar. |
리드 타임(프로토) | Fast (Days) | Moderate to Slow (Weeks, depending on complexity) | AM accelerates design iteration and validation. |
리드 타임(제작) | Moderate (Process time + Post-processing) | Potentially Faster for high volumes (if simple) | AM can be faster for complex, low-volume parts. |
재료 선택 | Wide range, excels with difficult-to-machine alloys | Wide range, standard materials readily available | AM efficiently processes critical materials like Invar needed for thermal stability. |
설정 비용 | Low (No tooling) | High (Tooling, programming, fixtures) | AM is cost-effective for custom parts and low volumes. |
표면 마감 | Moderate (Requires post-processing for smooth finish) | Excellent (Directly achievable) | Machining preferred for critical surfaces needing high finish without post-processing. |
허용 오차 | Good (Requires post-machining for highest precision) | Excellent (Directly achievable) | Machining preferred for features needing sub-100-micron accuracy without post-processing. |
시트로 내보내기
In summary, metal additive manufacturing offers a compelling suite of advantages for producing high-precision instrument mounts, especially when complexity, weight, performance optimization, or the use of specialized materials like Invar are key drivers. It empowers engineers to break free from traditional manufacturing constraints and design truly innovative mounting solutions. Partnering with an experienced AM provider like Met3dp, which combines expertise in advanced 인쇄 방법 with high-quality material production, ensures that the potential of AM is fully realized for your critical applications.
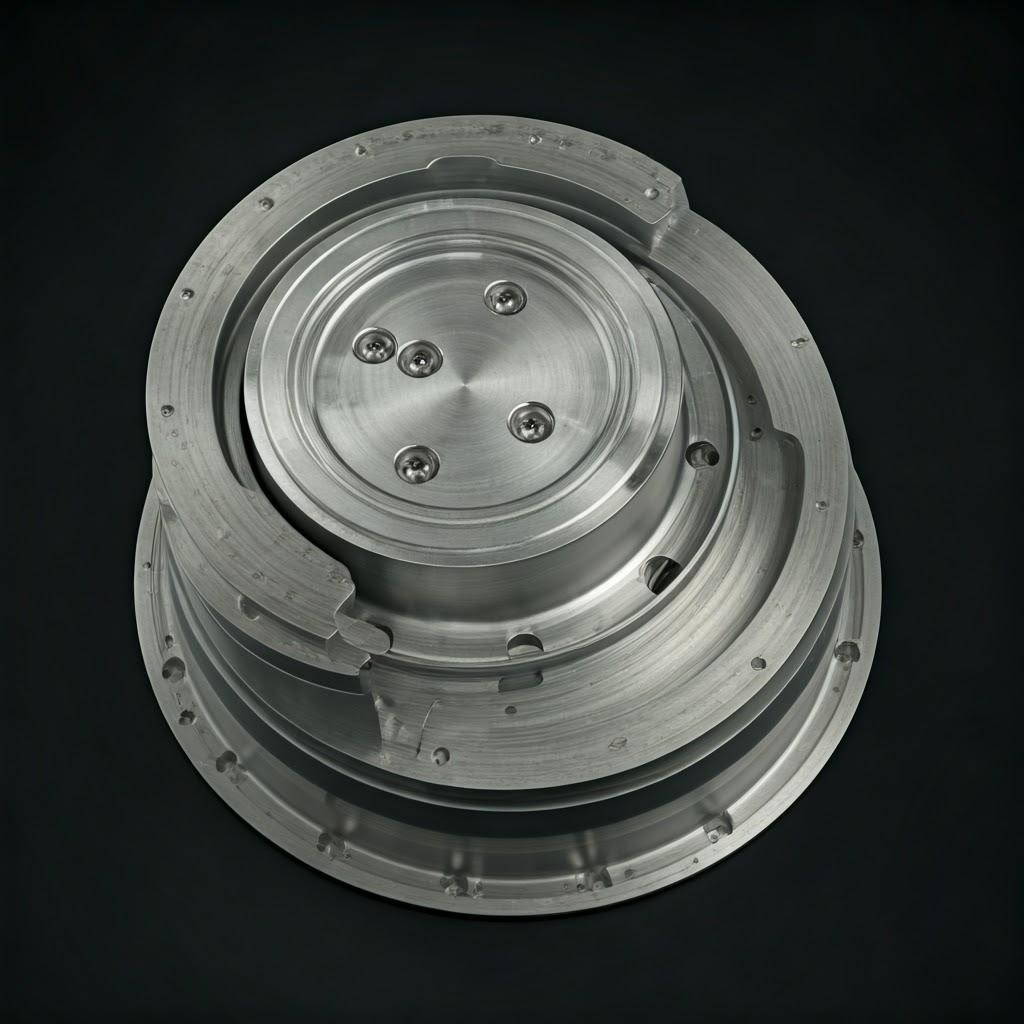
Material Focus: 316L Stainless Steel & Invar for Optimal Performance
The performance of a precision instrument mount is fundamentally tied to the material from which it is made. While metal additive manufacturing can process a wide array of alloys, two materials stand out for their frequent use in high-precision mounting applications due to their specific and often complementary properties: 316L 스테인리스 스틸 및 Invar (FeNi36). Understanding their characteristics is crucial for selecting the right material for your specific needs.
1. 316L Stainless Steel (Austenitic Stainless Steel)
316L is one of the most widely used stainless steel alloys in additive manufacturing, known for its excellent combination of corrosion resistance, mechanical properties, biocompatibility, and processability.
- Key Properties & Benefits for Mounts:
- 뛰어난 내식성: The high chromium and molybdenum content gives 316L exceptional resistance to corrosion in a wide range of environments, including chlorides, acids, and bodily fluids. This makes it ideal for mounts used in medical devices, marine applications, chemical processing, and food industries.
- Good Mechanical Strength and Ductility: 316L offers a good balance of tensile strength, yield strength, and elongation, ensuring mounts are robust and resistant to fracture. Its properties are generally comparable to wrought 316L.
- 생체 적합성: 316L is widely accepted for medical implants and devices (ISO 10993), making it suitable for surgical tool mounts or internal device fixtures.
- Weldability and Polishability: Parts made from 316L can be easily welded (if assembly is needed, though AM aims to consolidate) and polished to a high surface finish, important for cleanroom or optical applications.
- Cost-Effectiveness and Availability: Compared to more exotic alloys like Invar or titanium, 316L powder is relatively cost-effective and readily available from quality suppliers.
- Good AM Processability: 316L is well-characterized and reliably processed using Laser Powder Bed Fusion (LPBF/SLM) and other AM techniques, leading to dense, high-quality parts.
- 제한사항:
- Moderate Thermal Expansion: 316L has a coefficient of thermal expansion (CTE) typical of austenitic stainless steels (around 16−17×10−6/K). While acceptable for many applications, this level of expansion can cause significant dimensional changes and misalignment in systems highly sensitive to temperature fluctuations, such as precision optics or metrology equipment.
- 밀도: It is denser than aluminum or titanium alloys, which can be a disadvantage in weight-critical applications (though AM’s lightweighting capabilities can mitigate this).
- Typical Applications for 316L Mounts:
- Medical device components (surgical robots, diagnostic equipment)
- Marine hardware and sensor mounts
- Chemical processing equipment fixtures
- Food-grade machinery components
- General industrial sensor and equipment mounts where extreme thermal stability is not the primary concern.
2. Invar (FeNi36 / Alloy 36)
Invar is an iron-nickel alloy specifically engineered for its remarkably low coefficient of thermal expansion (CTE) at room temperature and moderately elevated temperatures. Its name comes from the word “invariable,” referring to its lack of thermal expansion.
- Key Properties & Benefits for Mounts:
- Extremely Low CTE: This is Invar’s defining characteristic. Its CTE is typically around 1.2×10−6/K near room temperature, roughly 10-15 times lower than stainless steel or aluminum, and significantly lower than titanium. This exceptional dimensional stability makes it the material of choice for applications where even minute thermal expansion or contraction cannot be tolerated.
- Good Strength and Toughness: Invar provides adequate strength and toughness for mounting applications, particularly when dimensional stability is the overriding requirement.
- AM Processability: While challenging to machine traditionally, Invar powder can be successfully processed using LPBF/SLM, enabling the creation of complex geometries that leverage its low CTE. Careful parameter control and post-process heat treatment are critical.
- 제한사항:
- 더 높은 비용: Invar powder is significantly more expensive than 316L stainless steel due to its high nickel content and specialized manufacturing process.
- 낮은 내식성: Invar does not possess the inherent corrosion resistance of stainless steels. It can be susceptible to rusting in humid environments unless protected by coatings (e.g., nickel plating).
- Machining Difficulty: Although AM bypasses much of the difficulty, post-process machining of critical features can still be challenging compared to steel.
- Heat Treatment Sensitivity: Achieving the optimal low CTE state in Invar requires specific heat treatment protocols after printing to relieve stress and stabilize the microstructure. Improper heat treatment can compromise its low-expansion properties.
- 밀도: Similar to steel, it is relatively dense.
- Typical Applications for Invar Mounts:
- Optical mounts (mirrors, lenses, lasers) in telescopes, interferometers, and precision alignment systems.
- Metrology equipment frames and fixtures (CMMs, gauges).
- Aerospace structures requiring dimensional stability (satellite optical benches, composite tooling molds).
- Semiconductor manufacturing equipment components (lithography stages, wafer handling).
- Scientific instrumentation requiring high stability (physics experiments, measurement devices).
Material Properties Comparison:
속성 | 316L 스테인리스 스틸 | Invar (FeNi36 / Alloy 36) | Significance for Mounts |
---|---|---|---|
주요 혜택 | Corrosion Resistance, Cost, Availability | Extremely Low Thermal Expansion (CTE) | Choose based on environmental exposure vs. need for ultimate dimensional stability. |
CTE (approx. @ 20°C) | ~16−17×10−6/K | ~1.2×10−6/K | Invar is vastly superior for temperature-sensitive applications. |
Density (approx.) | ~8.0g/cm3 | ~8.1g/cm3 | Similar densities; lightweighting via AM design is key for both. |
Yield Strength (Typical AM) | ~450-550 MPa | ~250-350 MPa (Annealed) | 316L generally stronger, but Invar adequate for most static mounting loads. |
내식성 | 우수 | Poor (Requires coating for protection) | 316L suitable for harsh environments; Invar needs controlled environments or plating. |
상대적 비용 | Lower | Significantly Higher | Budget constraints often favor 316L unless Invar’s low CTE is non-negotiable. |
AM Processability | Well-established, reliable | Requires careful control & heat treatment | Both feasible, but Invar demands more process expertise. |
가공성 | 양호 | 어려운 | AM reduces reliance on machining, benefiting Invar part creation. |
시트로 내보내기
Choosing the Right Material & Supplier:
The selection between 316L and Invar (or potentially other alloys like Titanium for high strength-to-weight) depends critically on the specific performance requirements, operating environment, and budget constraints of the application.
- If 내식성 또는 비용 are primary drivers, and moderate thermal expansion is acceptable: 316L is often the best choice.
- If ultimate dimensional stability across temperature changes is paramount (e.g., optics, metrology, space): Invar is typically required, despite its higher cost and need for environmental protection.
Crucially, the quality of the final part depends not only on the material choice but also on the quality of the metal powder and the expertise of the additive manufacturing service provider. Companies like Met3dp specialize in producing high-quality, spherical metal powders optimized for AM processes like SEBM and LPBF. Their use of advanced gas atomization and PREP technologies ensures powders with high sphericity and good flowability, leading to denser, more reliable printed parts. Met3dp manufactures a wide range of powders, including stainless steels and potentially specialized alloys required for demanding applications, providing customers with both the materials and the 전문성 needed to successfully implement metal AM for high-precision instrument mounts. When sourcing an Invar 3D printing supplier or a 316L stainless steel 3D printing service, verifying their powder quality control processes and experience with these specific materials is essential.
Design for Additive Manufacturing (DfAM): Optimizing Mounts for Printability & Functionality
Design for Additive Manufacturing (DfAM) represents a fundamental shift in mindset compared to traditional Design for Manufacturing (DFM) principles tailored for subtractive processes like CNC machining. Instead of primarily considering tool access, draft angles, and material removal strategies, DfAM focuses on leveraging the unique capabilities and accommodating the specific constraints of layer-by-layer fabrication. Applying DfAM principles is not merely recommended for precision instrument mounts; it is essential for unlocking the full potential of AM in terms of performance, cost-effectiveness, and reliability. Failing to design with the AM process in mind can lead to print failures, suboptimal performance, excessive post-processing requirements, and increased costs.
Core DfAM Principles for Precision Instrument Mounts:
- Leverage Geometric Freedom for Functional Gain:
- 토폴로지 최적화: This is perhaps the most impactful DfAM technique for mounts. By defining load cases (instrument weight, vibration inputs, operational forces), boundary conditions (attachment points), and objectives (minimize mass, maximize stiffness, specific natural frequency), software algorithms can generate highly efficient, often organic-looking structures. The result is a mount that is stiff and stable precisely where needed, using the minimum material, leading to significant weight savings without compromising performance. This is invaluable for aerospace, robotics, and portable systems.
- 격자 구조: Incorporating internal lattice structures (e.g., gyroids, octet truss) allows for further lightweighting while maintaining structural integrity. Lattices can also be designed to provide specific vibration damping characteristics or facilitate heat dissipation – highly relevant for instrument mounts.
- 파트 통합: Actively look for opportunities to combine multiple components of a mounting assembly into a single printed part. Can a bracket, heat sink, and vibration damper be integrated? Can alignment features be built directly into the mount? This simplifies assembly, reduces tolerance stack-up, enhances rigidity, and lowers overall system cost.
- Conformal Channels: Design internal channels that precisely follow the contours of heat sources or areas needing thermal management. For instruments generating heat or operating in varying temperatures, conformal cooling/heating channels integrated into the mount offer superior thermal control compared to traditional methods. Cable routing channels can also be integrated to neaten assemblies.
- Optimize Build Orientation:
- Impact: The orientation in which the mount is printed on the build plate significantly affects support structure requirements, surface finish on different faces, residual stress distribution, build time, and potentially mechanical properties (anisotropy).
- 고려 사항:
- Minimize Supports: Orient the part to reduce the volume and complexity of required support structures, especially on critical functional surfaces or hard-to-reach internal areas. Self-supporting angles (typically >45 degrees from horizontal) should be utilized where possible.
- 표면 마감: Surfaces facing downwards or requiring extensive support will generally have a rougher finish. Orient the part so that critical surfaces (e.g., mating interfaces, optical alignment datums) are upward-facing or vertical if possible, or are easily accessible for post-machining.
- 기계적 속성: Properties can vary slightly depending on the build direction relative to the loading direction in the final application. Orient the part to align the strongest build axis with the primary load path if critical.
- 열 관리: Orientation affects heat dissipation during the build, influencing residual stress.
- Collaboration: Choosing the optimal orientation often involves trade-offs. Collaborating with an experienced AM service provider like Met3dp during the design phase is crucial, as they can simulate different orientations and advise on the best strategy based on their specific product capabilities and process knowledge.
- Design Effective Support Structures:
- Necessity: Supports are required to anchor the part to the build plate, prevent warping due to thermal stress, and support overhanging features and down-facing surfaces during the layer-by-layer build process.
- Optimization: While necessary, supports consume material, add build time, require removal effort, and can mar the part surface. DfAM aims to minimize reliance on supports through smart design choices (e.g., using chamfers instead of sharp overhangs, orienting features to be self-supporting) and designing supports that are effective yet easy to remove.
- 유형: Different support types (e.g., solid, lattice, conical) can be used depending on the location and function. Consider ease of access for removal tools (pliers, EDM wires, CNC tools).
- Integration: Sometimes, functional features of the part itself can be designed to also act as supports during the build, potentially reducing the need for dedicated sacrificial structures.
- Account for Process Constraints:
- Minimum Wall Thickness/Feature Size: AM processes have limits on the minimum thickness of walls and the smallest features (pins, holes) they can reliably produce. These depend on the specific machine, laser/electron beam spot size, and powder characteristics. Design walls and features above these minimums (e.g., typically >0.4-0.5 mm for fine features in LPBF).
- Hole Orientation and Shape: Small holes are often printed more accurately when oriented vertically. Horizontally oriented small holes may print slightly elliptical and might require support; designing them as teardrop shapes can make them self-supporting.
- Powder Removal: For hollow sections or internal channels, ensure there are adequate escape holes (at least 2-3 mm diameter, preferably larger, and strategically located) to allow for the removal of unfused powder after the build. Trapped powder adds weight and can be a contamination concern.
- Fillets and Radii: Incorporate fillets at sharp internal corners to reduce stress concentrations, which can be points of weakness or crack initiation, especially under vibration or load. Smooth transitions generally improve printability and part strength.
- Design for Post-Processing:
- Machining Allowances: If certain surfaces require tight tolerances or a very smooth finish that cannot be achieved directly by AM, add extra material (machining stock, e.g., 0.5-1.0 mm) to these specific areas in the CAD model to allow for post-machining.
- 접근성: Ensure that areas requiring support removal, machining, polishing, or inspection are accessible after the part is printed. Deep, narrow internal channels requiring surface finishing can be problematic.
- Fixturing: Consider how the part will be held for various post-processing steps like machining or measurement. Integrating simple fixturing features into the design can save significant setup time later.
The Iterative Nature of DfAM:
DfAM is not always a linear process. It often involves collaboration between the part designer and the AM service provider. Tools like build simulation software can predict potential issues like deformation or overheating, allowing designers to modify the geometry or build setup proactively. Prototyping and testing remain crucial steps to validate design choices and ensure the final instrument mount meets all functional requirements. Embracing DfAM principles from the outset is key to maximizing the benefits of metal AM for creating lighter, stronger, more functional, and often more cost-effective precision instrument mounts compared to those constrained by traditional manufacturing paradigms.
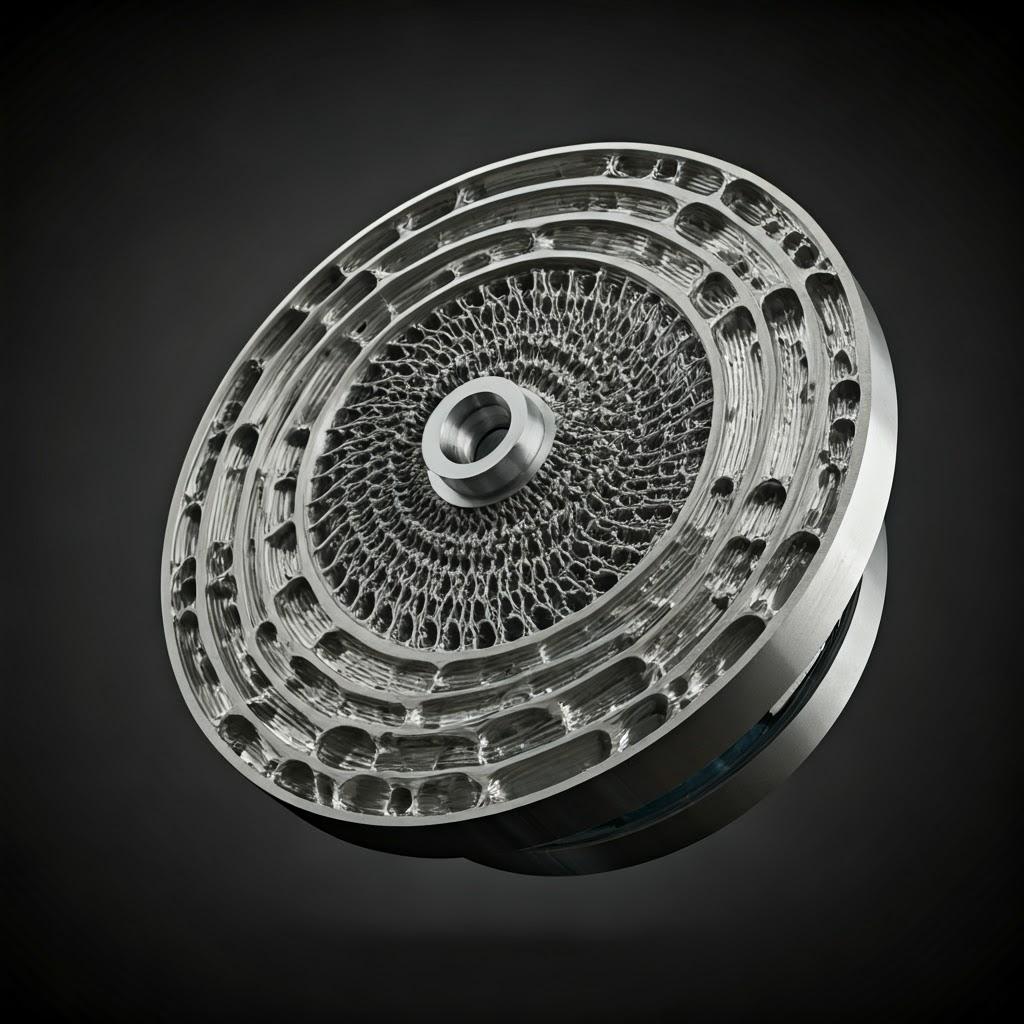
Achieving Precision: Tolerance, Surface Finish, and Dimensional Accuracy in 3D Printed Mounts
For components designed to hold sensitive instruments, precision is paramount. Understanding the levels of tolerance, surface finish, and dimensional accuracy achievable with metal additive manufacturing is critical for engineers designing mounts and for procurement managers setting specifications and evaluating suppliers. While metal AM offers incredible design freedom, it has inherent characteristics regarding precision that differ from conventional machining. Often, a combination of AM and post-processing is required to meet the tightest requirements.
As-Printed Capabilities:
Metal AM processes like Laser Powder Bed Fusion (LPBF/SLM) and Selective Electron Beam Melting (SEBM) build parts layer by layer, typically 20-100 micrometers (mum) thick. This process inherently influences the achievable precision:
- 치수 정확도:
- General Tolerances: As a general guideline, for well-controlled processes and properly calibrated machines, typical dimensional tolerances for as-printed metal AM parts are often in the range of pm0.1 mm to pm0.2 mm for smaller features (up to ~50-100 mm), or pm0.1 to pm0.2 of the overall dimension for larger parts. For example, a 200 mm long feature might have a tolerance of pm0.2 mm to pm0.4 mm.
- Influencing Factors: Actual achievable accuracy depends heavily on the part geometry (complexity, size, bulk), material (thermal properties), build orientation, support strategy, machine calibration, powder quality (particle size distribution, flowability), and thermal management during the build. Residual stresses built up during printing can cause warping or distortion, affecting final dimensions, especially after removal from the build plate.
- Met3dp’s Approach: Achieving consistent accuracy requires robust process control. Companies like Met3dp emphasize the reliability and accuracy of their printing systems and the quality of their metal powders, which are produced using advanced atomization techniques to ensure consistent spherical morphology and flowability – factors crucial for predictable melting and solidification, and thus better dimensional control.
- 표면 마감(거칠기):
- As-Printed Ra: The surface finish of as-printed metal parts is inherently rougher than machined surfaces due to the partially melted powder particles adhering to the surface and the layer-wise construction. Typical surface roughness (Ra – Arithmetic Average Roughness) values depend on orientation and process:
- Vertical Walls: Often achieve the best finish, potentially Ra 8−15mum.
- Upward-Facing Surfaces: Slightly rougher, Ra 10−20mum.
- Downward-Facing Surfaces (Supported): Significantly rougher where supports attach, potentially Ra 20−50mum or more, requiring significant finishing.
- Stepped Surfaces: The layer steps on angled surfaces also contribute to roughness.
- SEBM vs. LPBF: SEBM typically operates at higher temperatures and uses larger powder particles, often resulting in a rougher surface finish (e.g., Ra 25−45mum) compared to LPBF, but potentially lower residual stress.
- Implications for Mounts: For general structural parts, as-printed finish might suffice. However, for precision instrument mounts, mating surfaces, sealing faces, optical component interfaces, or kinematic locating features, this roughness is usually unacceptable and requires improvement via post-processing.
- As-Printed Ra: The surface finish of as-printed metal parts is inherently rougher than machined surfaces due to the partially melted powder particles adhering to the surface and the layer-wise construction. Typical surface roughness (Ra – Arithmetic Average Roughness) values depend on orientation and process:
Achieving Higher Precision with Post-Processing:
For most high-precision instrument mounts, critical features will require post-processing, primarily CNC machining, grinding, or lapping, to achieve the necessary tolerances and surface finishes.
- Tolerances: Post-machining operations can easily achieve tolerances in the range of pm0.01 mm to pm0.05 mm (10−50mum), and even tighter tolerances down to single microns (mum) with specialized grinding or lapping processes on critical datums or interfaces. This allows designers to leverage the geometric freedom of AM for the overall shape while ensuring precision only where it’s functionally required.
- 표면 마감: Machining can dramatically improve surface finish, typically achieving Ra 0.8−3.2mum. Grinding and lapping can achieve optical-grade finishes with Ra well below 0.1mum. Polishing techniques can also significantly smooth surfaces for aesthetic or functional reasons (e.g., cleanability).
Comparison: As-Printed vs. Post-Processed Precision:
기능 | As-Printed Metal AM (Typical LPBF) | Post-Processed (Machining/Grinding) | Significance for Precision Mounts |
---|---|---|---|
허용 오차 | pm0.1−0.2 mm or pm0.1−0.2 | pm0.01−0.05 mm (Machining)<br> pm0.001−0.01 mm (Grinding) | AM suitable for general form; post-processing essential for critical interfaces & alignments. |
Surface Finish (Ra) | 8−25mum (Varies by orientation) | 0.8−3.2mum (Machining)<br> $\< 0.1 \\mu m$ (Lapping/Polishing) | Post-processing required for smooth mating surfaces, sealing, or optical interfaces. |
기능 | Complex overall geometry | High precision on specific features | Combine AM’s complexity with machining’s precision for optimal results. |
시트로 내보내기
Quality Control and Verification:
Ensuring that the final mount meets the specified precision requirements involves rigorous quality control:
- 진행 중인 모니터링: Advanced AM systems incorporate sensors to monitor the melt pool, temperature gradients, and layer consistency during the build, helping to ensure process stability.
- Post-Build Metrology: Coordinate Measuring Machines (CMMs), 3D laser scanners, and optical profilometers are used to verify dimensional accuracy and surface finish after printing and after any post-machining steps.
- 비파괴 검사(NDT): Techniques like CT scanning can be used to inspect internal features, check for porosity, and verify complex geometries that are otherwise inaccessible.
핵심 요점:
Metal additive manufacturing provides good baseline dimensional accuracy and a characteristic surface finish directly from the machine. However, for the demanding requirements of high-precision instrument mounts, designers must anticipate the need for targeted post-processing, primarily machining or grinding, on critical features and surfaces. By strategically combining the design freedom of AM with the precision of subtractive finishing techniques, and by partnering with a quality-focused AM provider, engineers can create mounting solutions that offer both geometric complexity and exacting accuracy. Procurement managers should clearly define tolerance and finish requirements on drawings, specifying which features require post-processing, to ensure accurate quoting and successful part realization.
Essential Post-Processing Steps for Functional Instrument Mounts
A metal 3D printed part, upon removal from the printer, is rarely ready for its final application, especially in the context of high-precision instrument mounts. A series of post-processing steps are typically required to transform the raw printed component into a functional, reliable, and finished product. These steps are crucial for relieving internal stresses, removing temporary structures, achieving desired material properties, ensuring dimensional accuracy, obtaining the required surface finish, and sometimes adding protective layers. Understanding this workflow is vital for planning production timelines and costs.
Typical Post-Processing Workflow for Metal AM Mounts:
- 스트레스 완화 열처리:
- 목적: The rapid heating and cooling cycles inherent in powder bed fusion processes create significant internal stresses within the printed part. These stresses can cause distortion or cracking, especially after the part is removed from the build plate’s anchoring effect. Stress relief is a critical first step for most metal AM parts, particularly larger components or those made from materials prone to stress buildup like titanium alloys or Invar.
- 프로세스: The part, often while still attached to the build plate, is heated in a furnace to a specific temperature (below the material’s transformation temperature), held for a duration, and then slowly cooled. This allows the microstructure to relax, significantly reducing residual stresses. Specific cycles depend heavily on the material (e.g., Invar requires carefully controlled cycles to maintain its low CTE properties) and part geometry.
- Importance for Mounts: Ensures dimensional stability over time and prevents unexpected warping that could compromise instrument alignment.
- Removal from Build Plate:
- 프로세스: Once stress-relieved (if performed on the plate), the part needs to be separated from the build plate it was printed on. This is typically done using wire Electrical Discharge Machining (EDM), sawing, or sometimes CNC machining.
- 고려 사항: Care must be taken not to damage the part during removal. The interface layer between the part/supports and the plate is often designed to facilitate easier removal.
- 가루 제거(파우더 제거):
- 목적: Unfused metal powder remains within internal channels, hollow sections, and clings to the part surface after printing. This loose powder must be thoroughly removed.
- 프로세스: Typically involves manual brushing, tapping, and using compressed air or inert gas jets in a controlled environment (depowdering station) to recover the unused powder (which can often be sieved and reused). Ultrasonic cleaning baths or specialized vibration systems may also be employed.
- 도전 과제: Removing powder from complex internal geometries or lattice structures can be difficult. DfAM principles (e.g., adequate escape holes) are crucial here. Trapped powder is unacceptable as it adds weight and can be a source of contamination or interfere with function.
- 지원 구조 제거:
- 목적: Sacrificial support structures, used during the build to anchor the part and support overhangs, must be removed.
- 프로세스: This can range from simple manual breaking (for lightly sintered supports) to more involved methods like cutting with hand tools, wire EDM (especially for complex internal supports), or CNC machining. The method depends on the support design, material, and accessibility.
- 고려 사항: Support removal can leave witness marks or rough areas on the part surface (“scars”) that may require further finishing. Care must be taken not to damage the actual part during removal. Designing supports for easy removal is a key DfAM aspect.
- Hot Isostatic Pressing (HIP) – Optional but Often Recommended:
- 목적: HIP is a process that combines high temperature and high inert gas pressure (typically Argon) to eliminate internal microporosity that can sometimes remain after the AM process. This densifies the material, significantly improving fatigue life, fracture toughness, and overall mechanical integrity.
- 프로세스: Parts are heated in a specialized HIP vessel under high isostatic pressure for a set duration.
- When Used: Often required for critical components in aerospace, medical implants, and highly loaded industrial parts where material integrity is paramount. For precision mounts subject to vibration or fatigue loading, HIP can provide an extra margin of safety and ensure long-term reliability. It can also improve the consistency of material properties.
- Machining / Finishing of Critical Features:
- 목적: As discussed previously, to achieve tight tolerances (pm0.01−0.05 mm or better) and smooth surface finishes (Ra $\< 3.2 \\mu m$) on specific functional surfaces (mating faces, alignment datums, bearing bores, optical interfaces).
- 프로세스: Utilizes standard CNC milling, turning, grinding, or lapping operations. Requires careful fixture design to hold the often complex AM part accurately. Machining allowances must have been included in the DfAM stage.
- Necessity: Almost always required for high-precision instrument mounts to guarantee accurate positioning and assembly.
- Surface Treatment and Finishing:
- 목적: To improve the overall surface finish, clean the part, enhance aesthetics, or prepare for coating.
- Processes:
- Bead Blasting/Shot Peening: Creates a uniform matte finish, removes loose particles, and can induce compressive residual stresses (shot peening) to improve fatigue life.
- 텀블링/진동 마감: Smoothens surfaces and edges using abrasive media in a tumbling barrel or vibratory bowl. Good for batch processing of smaller parts.
- 전기 연마: Electrochemical process that removes a thin layer of material, resulting in a very smooth, clean, and bright surface. Often used for medical (316L) or vacuum applications.
- Manual Polishing/Linishing: For achieving specific high-gloss finishes or smoothing localized areas.
- Coating or Plating:
- 목적: To provide corrosion protection (essential for materials like Invar in humid environments), enhance wear resistance, alter surface electrical or thermal properties, or improve aesthetics.
- Processes: Nickel plating (common for Invar), powder coating, painting, anodizing (for titanium), physical vapor deposition (PVD) coatings, etc.
- 고려 사항: Coating thickness needs to be accounted for if applied to dimensionally critical surfaces. Surface preparation is key for good adhesion.
- Cleaning and Inspection:
- 목적: Final cleaning to remove any residual machining fluids, polishing compounds, or contaminants. Final inspection verifies dimensions, surface finish, and checks for any defects before shipping.
- Processes: Ultrasonic cleaning, visual inspection, CMM measurements, surface profilometry, NDT if required.
The specific sequence and necessity of these steps depend heavily on the material (e.g., Invar’s need for specific heat treatment and coating), the complexity of the part, and the stringent requirements of the final application. Planning for post-processing is not an afterthought; it’s an integral part of the manufacturing workflow for metal AM parts, impacting lead times and overall costs. Engaging with a full-service provider who offers comprehensive post-processing capabilities or has established partnerships for these services is crucial for receiving functional, application-ready precision instrument mounts.
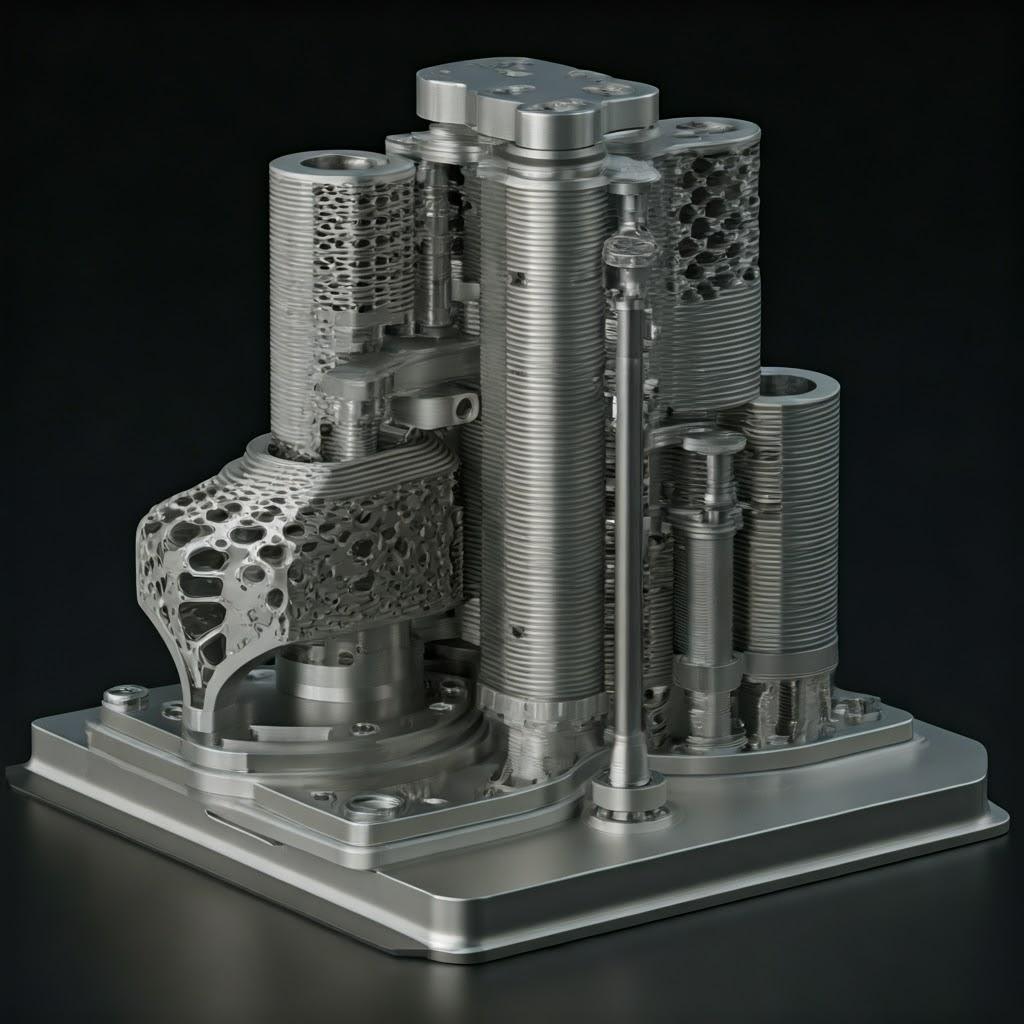
Overcoming Challenges in Metal 3D Printing Precision Mounts
While metal additive manufacturing offers significant advantages for producing complex and high-performance instrument mounts, the technology is not without its challenges. Achieving the required precision, material integrity, and reliability demands careful process control, material science understanding, and often, iterative refinement. Awareness of these potential hurdles allows engineers and manufacturers to proactively implement mitigation strategies.
Common Challenges and Mitigation Strategies:
- Residual Stress, Warpage, and Distortion:
- 도전: The intense, localized heating from the laser or electron beam and subsequent rapid cooling creates steep thermal gradients, leading to internal stresses within the part as it’s built layer by layer. These stresses can cause the part to warp, distort, or even crack, especially after removal from the build plate or during post-processing. This is a major concern for maintaining the dimensional accuracy required for precision mounts.
- Mitigation:
- Process Simulation: Software tools can simulate the build process to predict areas of high stress and potential distortion, allowing for adjustments to orientation or support strategies before printing.
- Optimized Build Parameters: Fine-tuning laser/beam power, scan speed, layer thickness, and scan strategy helps manage heat input and reduce thermal gradients.
- Build Plate Heating: Pre-heating the build plate (common in LPBF, inherent in SEBM operating in vacuum) reduces the temperature difference between the solidified material and the surrounding powder bed, lowering stress buildup.
- Smart Support Strategies: Robust support structures anchor the part firmly during the build, resisting warpage forces. Supports also act as heat sinks.
- 스트레스 완화 열처리: As discussed, this is a critical post-processing step to relax internal stresses before support removal or extensive machining. Specific protocols are essential, especially for sensitive materials like Invar.
- 지원 구조 제거:
- 도전: Supports are necessary but need to be removed cleanly without damaging the part. Accessing supports within complex internal geometries or delicate lattice structures can be extremely difficult. Incomplete removal leaves undesirable material, while aggressive removal can damage functional surfaces.
- Mitigation:
- DfAM for Support Minimization: Orienting the part and using self-supporting angles (>45°) drastically reduces the need for supports. Designing features like chamfers instead of sharp overhangs helps.
- Optimized Support Design: Using easily removable support types (e.g., thin interfaces, perforated structures), ensuring adequate spacing for tools, and considering the removal method (manual, EDM, machining) during the design phase.
- Advanced Removal Techniques: Employing wire EDM for intricate or hard-to-reach supports provides precise removal with minimal force on the part.
- 재료 선택: Some materials are easier to remove supports from than others.
- Porosity (Gas and Lack-of-Fusion):
- 도전: Small voids or pores can sometimes form within the printed material. Gas porosity arises from gas trapped within the powder or dissolved in the melt pool. Lack-of-fusion porosity occurs when the laser/beam energy isn’t sufficient to fully melt and fuse adjacent melt tracks or layers. Porosity degrades mechanical properties (especially fatigue strength) and can be detrimental to the integrity of a precision mount.
- Mitigation:
- High-Quality Powder: Using high-quality, gas-atomized spherical powders with low internal porosity and controlled particle size distribution is fundamental. Met3dp’s focus on advanced powder production using gas atomization and PREP technologies directly addresses this, aiming for powders with high sphericity, good flowability, and low satellite content, which promotes dense packing and consistent melting.
- Optimized Process Parameters: Developing and strictly controlling parameters (power, speed, hatch spacing, layer thickness) specific to the material and machine ensures complete melting and fusion.
- Controlled Atmosphere: Maintaining a high-purity inert gas atmosphere (Argon or Nitrogen) in the build chamber minimizes oxidation and gas pickup during printing.
- 열간 등방성 프레싱(HIP): The most effective way to eliminate any remaining internal porosity, densifying the part to near 100% theoretical density. Often mandatory for critical applications.
- Surface Finish Limitations:
- 도전: As discussed, the as-printed surface finish is inherently rougher than machined surfaces. While acceptable for some applications, it’s often insufficient for mating surfaces, sealing interfaces, or optical component mounts requiring smoothness for alignment or low friction.
- Mitigation:
- Orientation Strategy: Positioning critical surfaces optimally during build planning (upward-facing, vertical).
- 매개변수 최적화: Finer powders and thinner layers can sometimes yield slightly better finishes, often at the cost of build speed. Contour scanning strategies can also improve sidewall finishes.
- Targeted Post-Processing: Accepting the as-printed finish where possible and planning for specific finishing operations (machining, polishing, bead blasting, electropolishing) only on the surfaces where improved finish is functionally required.
- Anisotropy (Direction-Dependent Properties):
- 도전: Due to the layer-wise build process and columnar grain growth often observed along the build direction (Z-axis), the mechanical properties (e.g., strength, ductility) of AM parts can sometimes differ depending on whether they are measured parallel or perpendicular to the build direction. This anisotropy needs to be considered, especially for mounts subjected to specific load directions.
- Mitigation:
- Build Orientation Consideration: Aligning the critical load path in the application with the most favorable build orientation (often XY plane or 45 degrees) if anisotropy is significant for the chosen material/process.
- 열처리: Certain heat treatments can help homogenize the microstructure and reduce the degree of anisotropy.
- Process Selection: Some processes (like SEBM with its high build temperature) might result in less pronounced anisotropy compared to others.
- Material Characterization: Relying on supplier data or conducting tests to understand the anisotropic behavior of the specific material as processed by the chosen AM method.
- Powder Management and Handling:
- 도전: Metal powders can be reactive, hazardous (inhalation risk), and require careful handling, storage, and traceability, especially in regulated industries like aerospace and medical. Ensuring powder quality and preventing cross-contamination between different materials is critical.
- Mitigation:
- Strict Protocols: Implementing rigorous procedures for powder handling, sieving, blending, storage (e.g., controlled atmosphere), and traceability (batch tracking).
- Dedicated Equipment: Using separate equipment (e.g., sieves, build modules) for different material types to prevent cross-contamination.
- Supplier Quality Control: Partnering with reputable powder suppliers like Met3dp who provide certified materials with documented quality control ensures a reliable starting point.
Successfully navigating these challenges requires a combination of robust DfAM practices, deep understanding of material science, meticulous process control during printing, appropriate post-processing techniques, and rigorous quality assurance. Partnering with an experienced metal AM service provider who has demonstrated expertise in producing high-precision components, possesses advanced equipment, and maintains stringent quality management systems is often the most effective way to mitigate risks and ensure the successful production of reliable, high-performance instrument mounts.
Selecting Your Metal AM Partner: Choosing the Right Precision Instrument Mount Supplier
The success of your precision instrument mount project heavily relies on the capabilities, expertise, and quality standards of your chosen metal additive manufacturing service provider. Not all AM bureaus are created equal, especially when dealing with the stringent requirements of high-precision components and specialized materials like Invar. Making an informed decision requires evaluating potential partners across several key criteria. Procurement managers and engineering teams should collaborate closely during this B2B supplier selection process.
Key Criteria for Evaluating Metal AM Service Providers:
- Technical Expertise and Consultation:
- Application Understanding: Does the provider understand the specific challenges and requirements of precision instrument mounts (e.g., stability, alignment, thermal management, vibration)?
- DfAM Support: Do they offer design consultation services to help optimize your mount design for additive manufacturing? Can they provide expert advice on topology optimization, support strategies, feature resolution, and powder removal for complex geometries?
- Materials Science Knowledge: Do they possess deep knowledge of the materials required, particularly specialized alloys like Invar (FeNi36)? Do they understand the nuances of processing these materials and the necessary heat treatments to achieve desired properties (like low CTE)?
- 문제 해결: Do they have a track record of solving complex manufacturing challenges related to precision AM parts?
- Technology, Equipment, and Capabilities:
- Relevant AM Processes: Do they operate the appropriate metal AM technology for your needs? Laser Powder Bed Fusion (LPBF/SLM) is common for high resolution, while Selective Electron Beam Melting (SEBM) offers advantages like lower residual stress and suitability for certain reactive materials, often favored for medical and aerospace applications. Met3dp, for instance, specializes in SEBM printers alongside advanced powder production.
- Machine Park: What is the size, age, and maintenance status of their machine park? Do they have sufficient capacity? Are their machines properly calibrated and maintained for consistent results?
- Powder Quality Control: How do they manage and qualify their metal powders? Do they use high-quality powders from reputable sources or produce their own with rigorous QC? Ask about powder sourcing, testing (e.g., chemistry, particle size distribution, morphology, flowability), handling, storage, and traceability. Met3dp’s emphasis on in-house powder production using advanced gas atomization and PREP technologies is a significant advantage here, ensuring control over this critical input material.
- In-House Post-Processing: What post-processing capabilities do they have in-house (e.g., heat treatment furnaces, CNC machining centers, surface finishing equipment, metrology labs)? Relying on third-party subcontractors for critical steps can sometimes introduce delays or quality control challenges. A provider with integrated capabilities often offers better control and potentially faster turnaround.
- Material Portfolio and Expertise:
- Required Materials: Do they routinely process the specific materials needed for your mount (e.g., 316L Stainless Steel, Invar)?
- 경험: How many successful projects have they completed using these specific materials? Can they provide material datasheets based on their actual process parameters and testing?
- New Material Development: Are they capable of working with or developing parameters for less common or custom alloys if required?
- Quality Management System (QMS) and Certifications:
- ISO 9001: This is the baseline certification for a quality management system, indicating documented processes and commitment to quality.
- Industry-Specific Certifications: Depending on your application, look for relevant certifications:
- AS9100: Aerospace quality management standard.
- ISO 13485: Medical device quality management standard.
- Process Control & Monitoring: What measures do they take to monitor and control the printing process in real-time? How do they ensure consistency from build to build and machine to machine?
- Inspection and Testing: What metrology equipment (CMM, scanners) and non-destructive testing (NDT) methods (e.g., CT scanning, dye penetrant) do they employ? Do their inspection capabilities match the precision requirements of your mount?
- Traceability: Can they provide full traceability for materials, process parameters, and quality checks throughout the manufacturing workflow?
- Track Record, Case Studies, and References:
- Proven Experience: Ask for examples of past projects involving similar precision, complexity, or materials. Case studies demonstrating successful outcomes are valuable indicators.
- Customer References: Speaking with existing customers, particularly those in similar industries or with comparable applications, can provide candid insights into the provider’s performance, reliability, and communication.
- Capacity, Lead Time, and Scalability:
- Project Volume: Can they handle your required production volume, whether it’s prototypes, small batches, or potentially larger series production?
- Quoted Lead Times: Are their quoted lead times realistic and competitive? How do they manage production scheduling and potential bottlenecks (especially in post-processing)?
- 확장성: If your needs grow, can they scale production accordingly?
- Communication, Collaboration, and Support:
- 응답성: How quickly and effectively do they respond to inquiries and requests for quotes?
- 투명성: 프로세스, 역량, 잠재적 과제에 대해 개방적인가요?
- Collaboration: Do they foster a collaborative approach, working with your engineering team to achieve the best possible outcome?
- Customer Support: What level of technical support do they offer before, during, and after the project?
Supplier Selection Checklist Summary:
기준 | 주요 질문 |
---|---|
기술 전문성 | Do they understand precision mounts? Offer DfAM support? Know Invar/316L nuances? |
기술 및 장비 | Appropriate AM process (LPBF/SEBM)? Machine quality/capacity? Robust powder QC (like Met3dp’s)? In-house post-processing? |
재료 능력 | Offer required alloys? Proven experience with them? Provide reliable material data? |
Quality System & Certs | ISO 9001 certified? AS9100/ISO 13485 if needed? Strong process control? Advanced inspection/NDT capabilities? Full traceability? |
Track Record & References | Relevant case studies available? Positive customer references? |
Capacity, Lead Time, Scale | Can handle required volume? Realistic lead times? Ability to scale? |
커뮤니케이션 및 지원 | Responsive? Transparent? Collaborative? Good technical support? |
시트로 내보내기
Choosing the right metal AM partner is a strategic decision. Thoroughly vetting potential suppliers against these criteria will significantly increase the likelihood of receiving high-quality, reliable precision instrument mounts that meet your specifications, delivered on time and within budget. Look for partners like Met3dp who demonstrate a holistic approach, combining advanced printing technology, superior material quality, and deep application expertise.
Cost Considerations & Lead Times for 3D Printed Instrument Mounts
Understanding the factors that drive the cost and lead time of metal additive manufacturing is crucial for project planning, budgeting, and comparing AM against traditional manufacturing methods. While AM offers unique advantages, its cost structure and production timelines differ significantly from CNC machining or casting.
Factors Influencing Metal AM Cost:
The final price of a 3D printed precision instrument mount is influenced by a complex interplay of factors:
- Material Type and Cost:
- The raw material powder cost is a primary driver. Specialized alloys like Invar are significantly more expensive per kilogram than common materials like 316L stainless steel. Titanium alloys and superalloys also command premium prices.
- Powder quality (sphericity, purity, particle size distribution) also impacts cost, but higher quality often leads to better print results and potentially less waste or fewer failures.
- Part Volume and Mass:
- Directly dictates the amount of expensive metal powder consumed. Larger, denser parts naturally cost more.
- DfAM techniques like topology optimization and lattice structures are key to minimizing volume while meeting performance requirements, thus directly reducing material cost.
- Part Complexity and Geometry:
- While AM handles complexity well, highly intricate designs might require more sophisticated support structures or longer print times due to intricate scan paths.
- Ease of powder removal from internal channels also plays a role; designs requiring extensive manual depowdering increase labor costs.
- Part Bounding Box Size and Orientation:
- The overall dimensions (length x width x height) determine how much space the part occupies within the build chamber. Larger parts utilize more machine capacity and potentially require longer build times, increasing the cost allocated per part.
- Build height (Z-dimension) is often the most significant driver of print time, as the machine must process each layer sequentially. Optimizing orientation to minimize height can sometimes reduce cost.
- Support Structure Volume and Complexity:
- Supports consume material (adding to cost) and require time and labor for removal (adding post-processing cost). Designs minimizing support needs are more cost-effective.
- 머신 시간(빌드 시간):
- Calculated based on the number of layers, the area to be scanned per layer, the chosen scan strategy, and the machine’s operational parameters. Longer build times equate to higher machine utilization costs.
- Factors like layer thickness (thinner layers = better resolution but longer time), laser/beam power, and scan speed influence this.
- 사후 처리 요구 사항:
- This can be a very significant portion of the total cost, sometimes exceeding the printing cost itself. Each step adds labor, machine time, and potentially specialized tooling costs:
- Stress Relief / Heat Treatment (furnace time, energy, specialized cycles for Invar).
- Support Removal (labor, tools, potentially wire EDM time).
- HIP (expensive specialized equipment and long cycle times).
- CNC Machining (programming, setup, machine time, tooling – especially for hard materials or tight tolerances).
- Surface Finishing (blasting, tumbling, polishing labor/media/equipment).
- Coating/Plating (materials, processing time).
- This can be a very significant portion of the total cost, sometimes exceeding the printing cost itself. Each step adds labor, machine time, and potentially specialized tooling costs:
- Quantity (Batch Size):
- AM has relatively low setup costs compared to tooling for casting or injection molding. However, there are still setup tasks (build preparation, machine setup). Costs per part generally decrease with larger batch sizes as setup costs are amortized, and build chambers can potentially be nested with multiple parts. However, the economies of scale are typically less dramatic than in mass production methods.
- Quality Assurance and Inspection:
- Basic dimensional checks are standard. However, requirements for extensive CMM reports, NDT (like CT scanning), material certification testing, or detailed documentation add labor and equipment costs.
Lead Time Considerations:
Lead time is the total time from order placement to part delivery. For metal AM, it comprises several stages:
- Pre-Processing (1-3 days):
- Order review, CAD file preparation, build simulation (optional), build file generation, production scheduling.
- Printing (Build Time) (1-7+ days):
- Highly variable depending on part size (especially height), complexity, quantity (nesting), and chosen parameters. A small mount might print overnight; a large, complex one or a full build plate could take several days to a week.
- Post-Processing (3 days – 2+ weeks):
- This often constitutes the longest and most variable portion of the lead time. Each step adds time:
- Cooling and Depowdering: ~0.5-1 day.
- Stress Relief: ~1-2 days (including furnace time and controlled cooling).
- Build Plate/Support Removal: ~0.5-2 days (depending on complexity, method).
- HIP: ~2-4 days (including shipping to/from HIP facility if not in-house).
- Machining: ~2-10+ days (depending on complexity, number of features, shop loading).
- Finishing/Coating: ~1-5 days.
- Inspection: ~0.5-1 day.
- This often constitutes the longest and most variable portion of the lead time. Each step adds time:
- Shipping (1-5 days):
- Depends on location and shipping method.
Total Estimated Lead Times:
- Prototypes (Simple, minimal post-processing): ~5-10 working days.
- Prototypes/Low Volume (Complex, requiring machining/heat treat): ~2-4 weeks.
- Production Batches: ~3-6+ weeks (depending heavily on quantity and post-processing complexity).
AM vs. Machining Lead Time Comparison:
- Complex, Low Volume: AM is often significantly faster than machining from billet, as it avoids complex programming, multiple setups, and potentially custom tooling.
- Simple, High Volume: CNC machining can be faster once set up, especially if multiple parts can be run concurrently on efficient machines.
- Key Factor: The extent of post-machining required for the AM part significantly impacts its total lead time comparison. If an AM part requires extensive machining, the lead time advantage may diminish.
Key Takeaway for Procurement and Engineering:
Obtaining accurate quotes requires providing detailed CAD models, clear specifications (material, tolerances, surface finishes, required certifications), and desired quantities. Engage with potential suppliers early to discuss DfAM possibilities that can reduce both cost and lead time. Be aware that post-processing is often a major driver for both cost and delivery time in high-precision metal AM components.
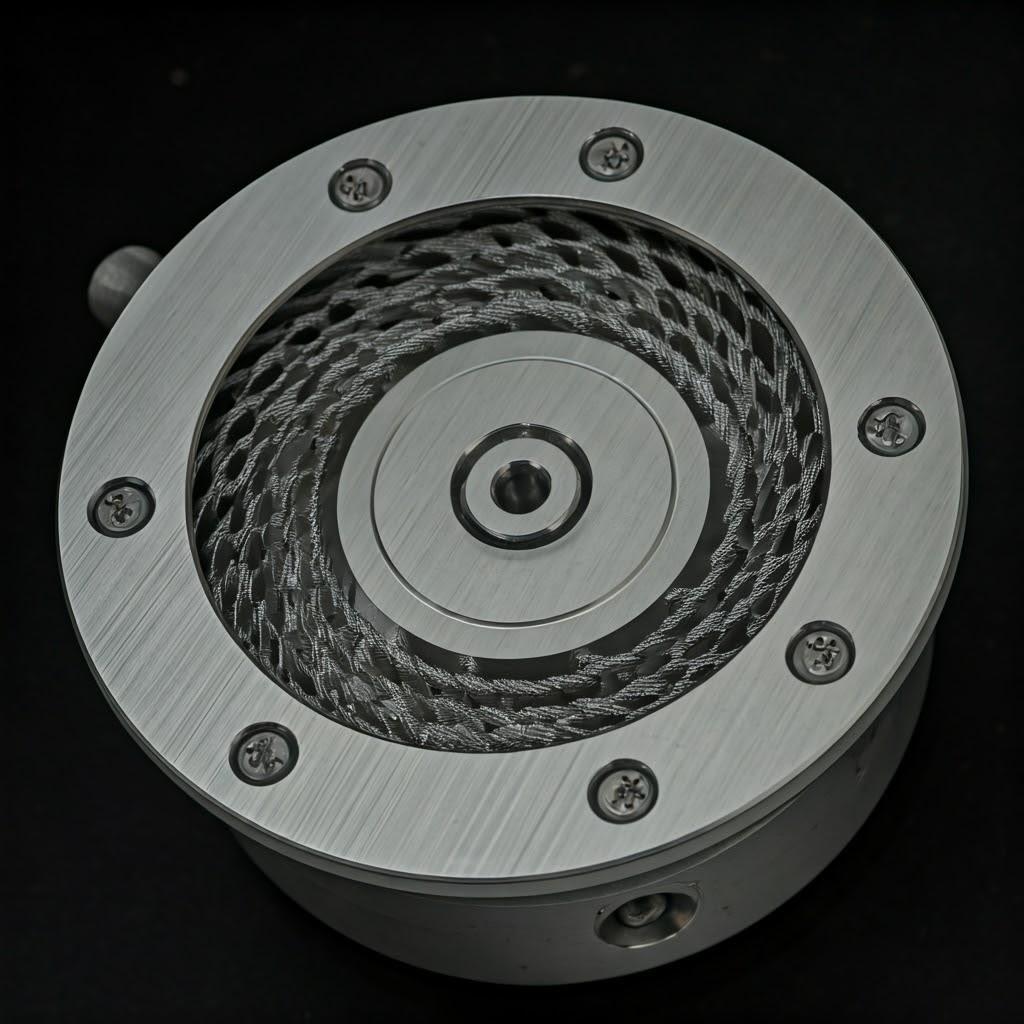
Frequently Asked Questions (FAQ) about 3D Printed Instrument Mounts
Here are answers to some common questions engineers and procurement managers have when considering metal additive manufacturing for precision instrument mounts:
Q1: How does the cost of a metal 3D printed instrument mount compare to a CNC machined one?
A: There’s no single answer, as it depends heavily on several factors:
- 복잡성: For highly complex geometries (internal channels, topology optimization, lattice structures) that are difficult or impossible to machine, AM is often more cost-effective, even at low volumes. Machining such parts might require multiple complex setups or fabricating and assembling multiple pieces, increasing cost.
- 볼륨: For simple geometries produced in high volumes, CNC machining typically becomes more cost-effective due to established automation and faster cycle times once set up. AM has lower setup costs, making it competitive for prototypes and low-volume production runs (typically 1-100s of parts).
- Material: For expensive materials like Invar that are difficult to machine (leading to high tool wear and slow speeds) and generate significant waste in subtractive processes, AM can be more competitive due to better material utilization (lower buy-to-fly ratio), even if the raw powder cost is high.
- 파트 통합: If AM allows you to consolidate multiple machined parts into a single printed component, the AM part might be cheaper when considering the total cost (part cost + assembly labor + reduced risk of assembly error).
- 후처리: If the AM part requires extensive post-machining to meet tolerances, this adds significantly to the cost, potentially making CNC machining from the start more viable if the geometry allows.
- Recommendation: Get quotes for both methods based on your specific design, material, quantity, and tolerance requirements to make an informed decision. Consider the total lifecycle cost, including design flexibility and potential performance gains from AM.
Q2: What level of precision and thermal stability can I realistically expect from a 3D printed Invar mount?
A:
- 정확성: As-printed dimensional tolerances for Invar are typically in the range of ±0.1 mm to ±0.2 mm or ±0.1−0.2%. Surface finish (Ra) might be around 10−25μm (LPBF). To achieve the micron-level tolerances ($ \pm 0.01 – 0.05$ mm or better) and smooth finishes (Ra <1.6μm) usually required for critical alignment features on precision optical or metrology mounts, post-machining of those specific features is essential.
- 열 안정성: This is Invar’s key benefit. When correctly processed (including appropriate stress relief and stabilization heat treatments after printing), 3D printed Invar retains its extremely low coefficient of thermal expansion (CTE), typically around 1.2×10−6/K near room temperature. This ensures minimal dimensional change with temperature fluctuations, critical for maintaining alignment in sensitive systems. It’s crucial to work with a provider experienced in Invar processing and heat treatment to guarantee this property.
Q3: Are 3D printed metal parts as strong and reliable as components made from traditional wrought or cast materials?
A: Yes, potentially. With mature process control and appropriate post-processing, metal AM parts can exhibit excellent mechanical properties:
- 밀도: Techniques like LPBF and SEBM, when optimized, can achieve part densities >99.5%, sometimes reaching >99.9% relative density, comparable to cast or wrought materials.
- Strength & Ductility: As-printed properties can sometimes match or exceed those of cast equivalents. With post-processing like Hot Isostatic Pressing (HIP) – which eliminates internal porosity – and appropriate heat treatments, the mechanical properties (yield strength, ultimate tensile strength, elongation, fatigue strength) of AM parts can often meet or even exceed standard specifications for wrought materials, especially in certain alloys like titanium.
- Reliability: The key is consistency. Partnering with a reputable AM provider who utilizes high-quality powder, maintains strict process control, performs necessary NDT, and can provide material certifications and test data is crucial for ensuring the reliability required for critical applications like instrument mounts. For demanding applications, properties should always be verified through testing that reflects service conditions.
Q4: How do I ensure the quality and consistency of 3D printed mounts, especially for critical applications requiring certification?
A: Ensuring quality requires a multi-faceted approach throughout the supply chain:
- Supplier Selection: Choose a provider with a robust Quality Management System (QMS), ideally certified to ISO 9001 and, if applicable, AS9100 (aerospace) or ISO 13485 (medical). Verify their experience with your specific material and application type.
- Material Control: Insist on using powder from reputable sources with batch traceability and material certifications conforming to relevant standards (ASTM, ISO, AMS). Understand the supplier’s powder handling and recycling procedures.
- 프로세스 제어: Ensure the provider utilizes machines with in-process monitoring capabilities and maintains strict control over critical process parameters, documented for each build.
- Clear Specifications: Provide detailed drawings with unambiguous tolerances, surface finish requirements (specifying which surfaces need finishing), required post-processing (heat treatments, HIP), and any NDT requirements.
- Post-Processing Verification: Ensure all required post-processing steps are performed correctly (e.g., verify heat treatment cycles).
- Inspection and Testing: Define the required level of inspection (e.g., CMM reports for critical dimensions, surface roughness measurements) and NDT (e.g., CT scanning for internal integrity, dye penetrant for surface defects). Request final inspection reports.
- Documentation: Require a comprehensive documentation package, including material certifications, build logs (if available/agreed), heat treatment records, inspection reports, and certificates of conformance.
Conclusion: Elevate Your Instrumentation with Advanced Metal Additive Manufacturing
In the demanding realms of aerospace, medical technology, metrology, and advanced industrial automation, the quest for higher precision, enhanced performance, and greater design flexibility is relentless. Precision instrument mounts, though often overlooked, are fundamental enablers of progress in these fields. As we’ve explored, metal additive manufacturing offers a paradigm shift in how these critical components can be designed and produced.
By moving beyond the constraints of traditional machining, metal AM empowers engineers to create instrument mounts that are:
- Geometrically Optimized: Leveraging topology optimization and generative design for unparalleled stiffness-to-weight ratios.
- Functionally Integrated: Incorporating features like conformal cooling, vibration damping structures, and consolidated assemblies directly into the mount.
- 가벼움: Drastically reducing mass for applications where weight is critical, without sacrificing stability.
- Materially Advanced: Enabling the efficient use of specialized alloys like low-expansion Invar for ultimate thermal stability, or corrosion-resistant 316L for harsh environments.
- Rapidly Prototyped and Customized: Accelerating development cycles and enabling tailored solutions for specific instrumentation needs.
Successfully harnessing these benefits requires a holistic approach, encompassing rigorous Design for Additive Manufacturing (DfAM) principles, a clear understanding of achievable precision and necessary post-processing steps, and meticulous attention to potential challenges like residual stress and porosity. Critically, it demands partnership with a knowledgeable and capable metal AM service provider.
Choosing a supplier like Met3dp, which combines decades of collective expertise with cutting-edge technology – from advanced SEBM printing systems known for accuracy and reliability to in-house production of high-quality, spherical metal powders – ensures a foundation of quality and capability. Met3dp provides comprehensive metal 3d printing solutions, spanning equipment, materials, and application development services, partnering with organizations to accelerate their adoption of additive manufacturing.
By embracing metal AM, companies can not only improve the performance and reliability of their current instrumentation but also unlock entirely new possibilities in device design and capability. Whether you need the exceptional thermal stability of Invar for optical systems, the biocompatibility and corrosion resistance of 316L for medical devices, or topology-optimized lightweight structures for aerospace sensors, metal additive manufacturing provides the tools to elevate your instrumentation to the next level.
Ready to explore how metal additive manufacturing can revolutionize your precision instrument mounting solutions? Contact Met3dp today to discuss your application requirements with our team of experts and discover how our advanced capabilities can power your organization’s innovation.
공유
중국 칭다오에 본사를 둔 선도적인 적층 제조 솔루션 제공업체인 MET3DP Technology Co. 당사는 산업용 3D 프린팅 장비와 고성능 금속 분말을 전문으로 합니다.
관련 기사
Met3DP 소개
최근 업데이트
제품
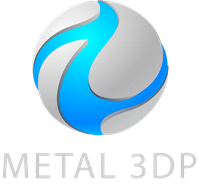
3D 프린팅 및 적층 제조용 금속 분말
문의 정보
- 칭다오시, 산둥성, 중국
- [email protected]
- [email protected]
- +86 19116340731