Custom Connector Housings for Aerospace Systems
목차
Introduction: Defining Aerospace Connector Housings and Their Function
In the complex and demanding world of aerospace engineering, every component, no matter how small, plays a critical role in ensuring safety, reliability, and performance. Among these essential elements are aerospace connector housings. These components might not always capture the spotlight like engines or wings, but they are fundamental to the intricate network of electrical and data systems that enable modern aircraft, spacecraft, and defense platforms to function flawlessly.
At its core, an aerospace connector housing serves as a protective enclosure for electrical or optical connectors. Its primary functions include:
- Physical Protection: Shielding the delicate connector interfaces (pins, sockets, fiber optic termini) from physical damage due to impact, vibration, shock, and abrasion. This is paramount in environments where mechanical stresses are constant and intense.
- Environmental Sealing: Preventing the ingress of contaminants such as dust, moisture, de-icing fluids, jet fuel, hydraulic fluids, and other potentially corrosive substances that can compromise electrical connections and lead to system failures. Effective sealing is crucial for maintaining signal integrity and preventing short circuits.
- Electrical Shielding (EMI/RFI): In many aerospace applications, particularly those involving sensitive avionics or communication systems, connector housings provide electromagnetic interference (EMI) and radio frequency interference (RFI) shielding. This prevents external electromagnetic fields from disrupting signal transmission and protects other nearby systems from noise generated by the connector itself.
- Strain Relief: Providing mechanical support for the cables entering the connector, preventing stress from being transferred directly to the termination points. This enhances the durability and lifespan of the entire cable assembly.
- Alignment and Mating: Ensuring the correct orientation and secure locking of mating connectors, guaranteeing a reliable connection is established and maintained, even under challenging operational conditions.
These housings are more than simple boxes; they are precisely engineered components designed to maintain the integrity of vital data and power links within an aircraft or spacecraft. The failure of a single connector, often traceable to inadequate housing protection, can have cascading effects, potentially leading to mission-critical system failures. Therefore, the design, material selection, and manufacturing method for these housings are subjects of intense scrutiny within the aerospace industry. As systems become more complex and integrated, the demands placed on these seemingly simple components continue to escalate, driving the need for innovative solutions.
The Unforgiving Aerospace Environment: Why Robust Housings are Non-Negotiable
The operational environment for aerospace components is arguably one of the most challenging encountered in any engineering field. Connector housings must withstand a relentless barrage of extreme conditions, making robustness and reliability non-negotiable requirements. Consider the spectrum of challenges:
- 극한의 온도: Components experience vast temperature fluctuations, from the sub-zero temperatures at high altitudes or in space (-55°C or lower) to the high temperatures near engines or in equipment bays (+125°C, +175°C, or even higher in specific zones). Materials must maintain their structural integrity, sealing properties, and dimensional stability across these ranges without cracking, warping, or degrading.
- Vibration and Shock: Aircraft and launch vehicles generate significant vibration during takeoff, flight, and landing. Connector housings must endure these constant vibrational loads, as well as sudden high-G shocks, without loosening, fatiguing, or causing intermittent electrical contact issues (fretting). Secure locking mechanisms and robust construction are essential.
- Pressure Differentials: Components must function reliably from sea level pressures to the low pressures of high altitudes or the vacuum of space. Sealing integrity is critical to prevent pressure loss in pressurized cabins or modules and to protect internal components from the external environment.
- Corrosion and Contamination: Exposure to humidity, salt spray (in marine environments or coastal airfields), hydraulic fluids, fuels, cleaning solvents, and de-icing agents necessitates materials with excellent corrosion resistance. Contamination by dust, sand, and other particulates also poses a threat to connector interfaces.
- Radiation: Space applications introduce the challenge of ionizing radiation, which can degrade certain materials over time, potentially compromising the long-term reliability of connector housings in satellites and deep-space probes.
- Outgassing (Space): In the vacuum of space, materials can release trapped gasses (outgassing), which can contaminate sensitive optical surfaces or electronics. Low-outgassing materials are often required for space-grade components.
- 무게 제약: Every gram counts in aerospace. Housings must provide maximum protection and performance while contributing minimally to the overall weight of the system. This constant drive for lightweighting fuels the search for advanced materials and manufacturing processes.
Failure to meet these stringent environmental demands can lead to catastrophic system failures. Consequently, aerospace engineers and procurement managers prioritize connector housings manufactured from high-performance materials using processes that guarantee consistency, reliability, and adherence to rigorous industry standards (like AS9100).
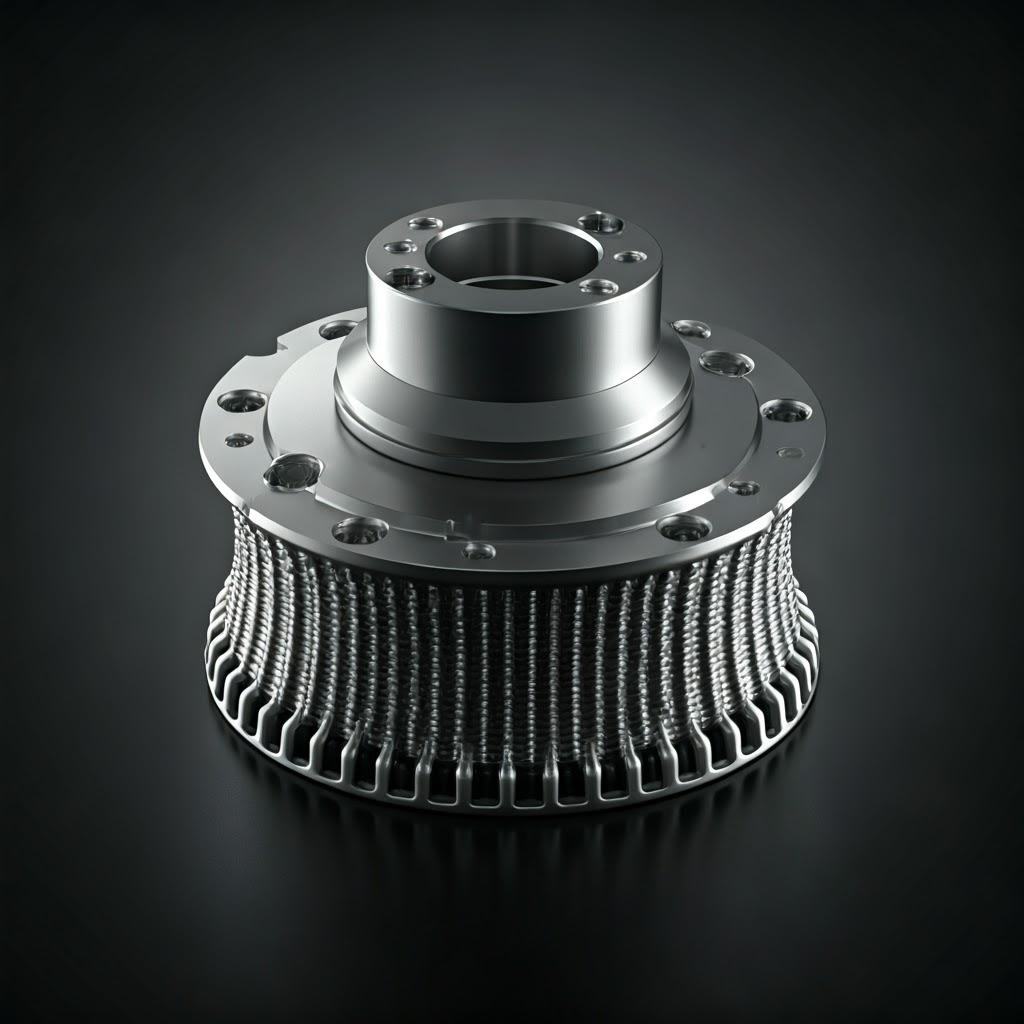
The Imperative for Customization in Modern Aerospace Design
While standard off-the-shelf connectors and housings exist, the increasing complexity, miniaturization, and specific functional requirements of modern aerospace systems frequently necessitate custom connector housings. Several factors drive this need:
- Space Constraints: As aircraft and spacecraft pack more electronics into tighter spaces (e.g., avionics bays, wing roots, UAV payloads), connector housings often need unique shapes, profiles, or mounting features to fit precisely within allocated envelopes. Standard rectangular or circular housings may not be feasible.
- Specific Mating Requirements: Custom designs might be needed to interface with unique or non-standard equipment, accommodate specific cable exit angles, or integrate multiple connector types into a single, consolidated housing.
- Integrated Functionality: There’s a growing trend towards integrating features directly into the housing, such as integrated shielding partitions, cooling channels, mounting brackets, or sensor mounts. This reduces part count, assembly time, and potential points of failure.
- Weight Optimization: Customization allows engineers to tailor the housing’s geometry specifically to the load requirements, removing unnecessary material through topology optimization and achieving maximum weight savings beyond what standard components offer.
- Unique Environmental Needs: Specific applications might demand specialized sealing configurations, unique EMI/RFI shielding solutions, or compatibility with non-standard fluids or temperatures, driving the need for custom designs and material selections.
- Legacy System Integration: Retrofitting new systems into older aircraft often requires custom connector solutions to interface modern electronics with existing wiring harnesses and mounting points.
Traditional manufacturing methods like CNC machining from billet or injection molding/casting (for high volumes) can struggle to meet these customization demands efficiently or cost-effectively, especially for the low-to-medium volumes often required in aerospace projects. Machining complex, organically shaped, or internally channeled custom housings can be incredibly time-consuming and generate significant material waste. Creating molds or tooling for casting or injection molding is often prohibitively expensive for small production runs or prototypes. This is where the unique capabilities of metal additive manufacturing become transformative.
Metal Additive Manufacturing: A Paradigm Shift for Connector Housing Production
Metal Additive Manufacturing (AM), commonly known as metal 3D 프린팅, offers a powerful alternative for producing high-performance, custom aerospace connector housings. Technologies like Powder Bed Fusion (PBF) – which includes Selective Laser Melting (SLM), Direct Metal Laser Sintering (DMLS), and Electron Beam Melting (EBM) – build parts layer by layer directly from a digital model using fine metal powders. This approach fundamentally changes the production landscape for components like connector housings:
- 전례 없는 디자인 자유: AM removes many traditional manufacturing constraints. Engineers can design highly complex geometries, internal lattice structures for weight reduction, conformal cooling channels, and organically shaped housings optimized for specific space envelopes – features often impossible or impractical to machine or cast.
- 신속한 프로토타이핑 및 반복: Custom housing designs can be printed, tested, and refined in a matter of days, drastically accelerating the development cycle compared to the weeks or months required for traditional tooling and machining setups. This agility is crucial in fast-paced aerospace programs.
- Cost-Effective Customization: Since AM is a tool-less process, the cost difference between printing one custom design or ten slightly different variations is minimal compared to the high tooling costs associated with traditional methods. This makes AM ideal for low-to-medium volume production runs of specialized housings.
- 파트 통합: Multiple components of a connector assembly (e.g., housing, bracket, strain relief) can potentially be integrated into a single, complex 3D printed part. This reduces assembly time, eliminates potential leak paths or failure points at joints, and can further reduce weight.
- 재료 효율성: AM processes typically use only the material needed to build the part and its supports, resulting in significantly less material waste compared to subtractive methods like CNC machining, which can machine away up to 80-90% of the initial material block for complex parts. This is particularly beneficial when using expensive aerospace-grade alloys like titanium.
- 온디맨드 제조: Digital designs can be stored and printed as needed, enabling distributed manufacturing models and reducing the need for large physical inventories. Spare parts or updated designs can be produced quickly without requiring existing tooling.
For aerospace engineers and procurement managers seeking aerospace component suppliers capable of delivering highly customized, high-performance connector housings efficiently, metal AM presents a compelling value proposition. It enables innovation, accelerates timelines, and offers a cost-effective route for complex, low-volume parts that are increasingly common in the industry.
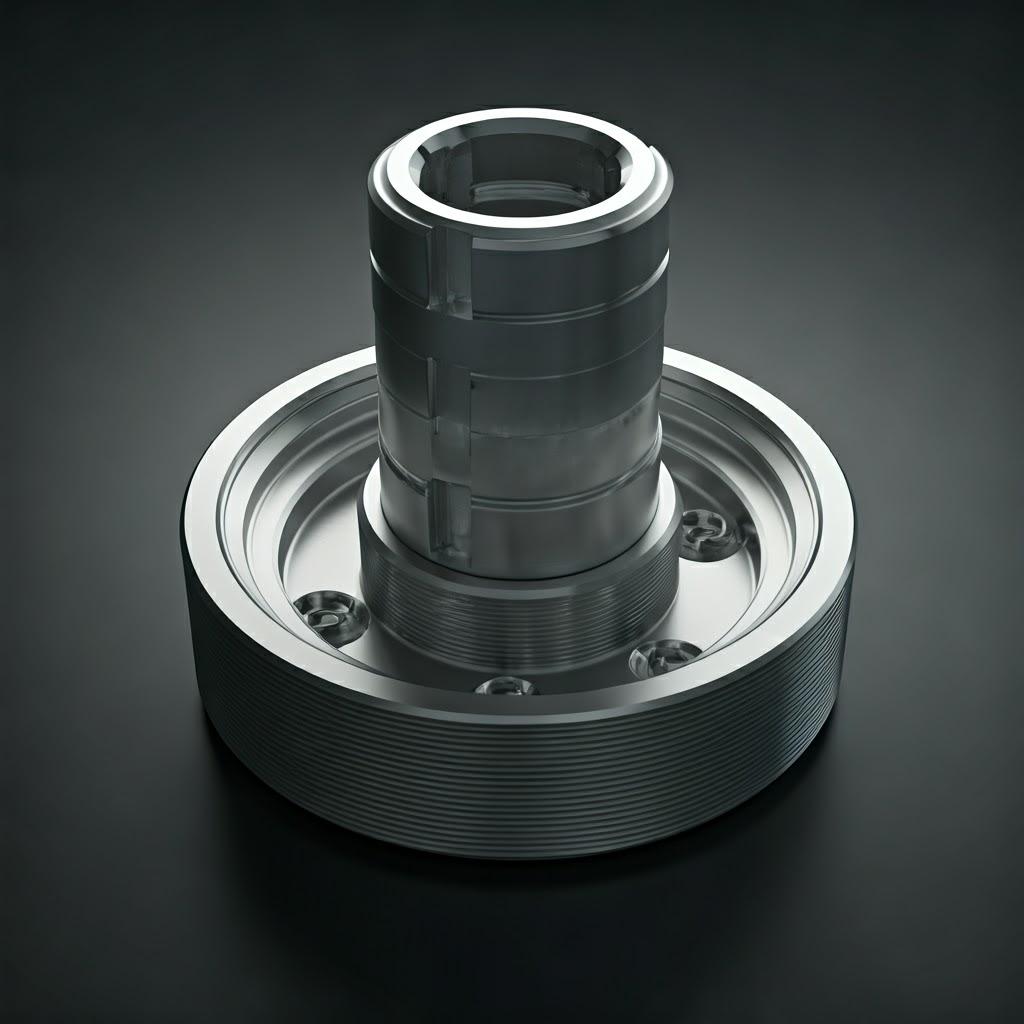
Partnering with Expert Metal AM Suppliers like Met3dp
Successfully leveraging metal AM for critical components like aerospace connector housings requires partnering with a knowledgeable and capable metal 3D printing service provider. The intricacies of process parameter optimization, material science, quality control, and post-processing demand specialized expertise.
Met3dp, headquartered in Qingdao, China, stands as a leading provider of comprehensive additive manufacturing solutions tailored for demanding industrial applications, including aerospace. Our expertise spans the entire AM ecosystem:
- Advanced Metal Powders: Met3dp manufactures a wide range of high-quality spherical metal powders specifically optimized for PBF processes. Utilizing cutting-edge gas atomization and Plasma Rotating Electrode Process (PREP) technologies, we ensure our powders, including aerospace-grades like Ti-6Al-4V and stainless steels like 316L, exhibit high sphericity, excellent flowability, controlled particle size distribution, and high purity – critical factors for achieving dense, reliable, high-performance printed parts.
- State-of-the-Art Printing Equipment: Our portfolio includes Selective Electron Beam Melting (SEBM) printers, known for their ability to process high-temperature, crack-prone materials efficiently and produce parts with low residual stress, often reducing the need for extensive heat treatment. Our systems deliver industry-leading build volume, accuracy, and reliability suitable for mission-critical aerospace components.
- Decades of Collective Expertise: Our team possesses deep knowledge in metal AM, materials science, and application engineering. We collaborate closely with clients, offering design for additive manufacturing (DfAM) support, process optimization, and comprehensive solutions to help organizations successfully implement 3D printing and accelerate their digital manufacturing transformations.
Choosing a supplier like Met3dp ensures access not only to advanced technology but also to the crucial expertise needed to navigate the complexities of producing flight-worthy aerospace components. We understand the rigorous quality and performance demands of the industry and are equipped to deliver custom connector housings that meet the highest standards.
Mapping the Skies: Where are Custom Aerospace Connector Housings Predominantly Used?
The need for robust, reliable, and often customized connector housings permeates virtually every segment of the aerospace industry. These components are ubiquitous, forming the unseen backbone of electrical and data networks in a vast array of applications. Understanding where they are most critically employed highlights the diverse challenges they must overcome. Procurement managers sourcing from wholesale aerospace component distributors or directly from custom connector manufacturers need to appreciate these varied application environments.
Commercial Aviation: Enhancing Safety and Efficiency in Flight Systems
In commercial airliners, millions of passengers and countless tons of cargo rely on the flawless operation of complex electronic systems every day. Custom connector housings are essential in numerous areas:
- Avionics Bays: These densely packed areas house the aircraft’s “brain” – flight control computers, navigation systems (GPS, INS), communication radios (VHF, HF, SATCOM), weather radar, and cockpit displays. Connector housings must provide exceptional EMI/RFI shielding to prevent interference between systems, withstand vibration, and fit within extremely tight space constraints. Custom shapes and integrated mounting features are common.
- Engine Nacelles and Pylons: The environment near engines is particularly harsh, characterized by high temperatures (requiring materials like Ti-6Al-4V or high-temperature nickel alloys), intense vibration, and potential exposure to fuel and hydraulic fluids. Connectors for engine sensors (temperature, pressure, vibration), FADEC (Full Authority Digital Engine Control) systems, and actuators require exceptionally robust and heat-resistant housings.
- Fly-by-Wire (FBW) Systems: Modern aircraft rely heavily on FBW systems, where pilot inputs are transmitted electronically to flight control surfaces. The integrity of these data links is paramount. Connector housings within the FBW network must ensure absolute connection reliability under all flight conditions, demanding high resistance to vibration, shock, and environmental factors.
- In-Flight Entertainment (IFE) and Cabin Systems: While perhaps less critical for flight safety, the extensive network of connectors for IFE screens, cabin lighting, passenger service units, and galley equipment requires reliable housings, often needing to meet specific flammability and smoke toxicity regulations (e.g., FAR 25.853). Customization might be needed for aesthetic integration or unique mounting scenarios.
- Landing Gear Systems: Connectors associated with landing gear position sensors, braking systems (brake-by-wire), and steering controls face severe shock, vibration, and exposure to runway debris, water, and de-icing fluids. Housings here need exceptional sealing (IP rating) and mechanical durability.
Defense and Military Aerospace: Ensuring Reliability in Mission-Critical Applications
Military aircraft, helicopters, and missile systems operate under even more extreme conditions and demand the highest levels of reliability and survivability. Custom connector housings are critical for:
- Electronic Warfare (EW) Systems: Pods and internal systems for radar jamming, signals intelligence (SIGINT), and countermeasures contain sensitive high-frequency electronics. Connector housings must provide superior EMI/RFI shielding effectiveness (>80dB or higher) and often require specialized finishes or materials.
- Secure Communications: Encrypted data links and secure voice communication systems rely on connectors protected by tamper-resistant or specially keyed housings to maintain signal security.
- Weapon Systems Integration: Connectors linking aircraft pylons to missiles, bombs, or targeting pods require rugged, quick-disconnect housings capable of withstanding extreme G-forces during maneuvers and weapon release. Reliability is absolutely critical.
- Radar and Sensor Systems: Advanced Active Electronically Scanned Array (AESA) radars and various optical/infrared sensors employ numerous connectors. Housings need to withstand vibration, manage heat dissipation (sometimes requiring integrated cooling features), and maintain performance across wide temperature ranges. Custom form factors are often required for conformal installations.
- Rugged Computing and Vetronics: Military ground vehicles and aircraft employ ruggedized computers and displays designed to survive harsh battlefield conditions. The external connectors are key vulnerability points, necessitating extremely robust, environmentally sealed, and often custom-designed housings.
B2B aerospace parts suppliers serving the defense sector must adhere to stringent military specifications (MIL-STD, DEF STAN) regarding materials, performance, and testing for all components, including connector housings.
Space Exploration: Meeting Extreme Demands Beyond Earth’s Atmosphere
Spacecraft, satellites, and launch vehicles represent the pinnacle of environmental challenges, pushing the limits of material science and engineering. Connector housings for space applications face unique hurdles:
- 진공 환경: Materials must exhibit low outgassing properties to prevent contamination of sensitive optics or electronics. Sealing must prevent leakage in the vacuum.
- Extreme Temperature Cycles: Satellites orbiting Earth experience rapid and extreme temperature swings as they pass between direct sunlight and shadow. Housings must endure thermal cycling without degradation or inducing stress on the connectors.
- Radiation Hardening: Exposure to cosmic rays and charged particles in space requires materials and designs that resist radiation damage over long mission durations (years or decades). Certain materials can become brittle or change electrical properties when irradiated.
- Launch Stresses: Housings must survive the intense vibration, acoustic noise, and high G-forces experienced during rocket launch.
- Weight Minimization: Launch costs are directly proportional to mass. Every gram saved is critical. Lightweight materials like Ti-6Al-4V, combined with topology optimization enabled by AM, are highly advantageous for space connector housings. Applications include satellite bus electronics, payload instruments, communication antennas, and propulsion system sensors.
소싱 항공우주 등급 소재 and components for space requires suppliers with specific expertise and adherence to space agency standards (e.g., NASA, ESA).
Unmanned Aerial Vehicles (UAVs): Enabling Compact and Lightweight Designs
The rapidly growing field of UAVs (drones), from small reconnaissance aircraft to large High-Altitude Long-Endurance (HALE) platforms, places a premium on size, weight, and power (SWaP). Custom connector housings are key enablers:
- Miniaturization: UAVs have extremely limited space for electronics. Custom housings allow connectors to be integrated into very tight spaces, often with non-standard shapes and mounting.
- 무게 감소: Using lightweight materials like Ti-6Al-4V and topology-optimized designs achieved through AM is critical for maximizing flight endurance and payload capacity.
- Payload Integration: Housings for connectors linking interchangeable payloads (cameras, sensors, communication relays) need to be robust, reliable, and often feature quick- Mating/demating mechanisms.
- Environmental Exposure: Depending on the mission profile, UAVs can face significant vibration, varying temperatures, and exposure to rain or dust, requiring appropriately sealed and durable housings.
Locating Wholesale Aerospace Component Distributors and Manufacturers
Engineers and procurement professionals seeking suppliers for these critical components often search for “wholesale aerospace connector suppliers,” “custom aerospace housing manufacturers,” or “B2B aerospace parts distributors.” Finding the right partner involves assessing not just their product offerings but also their manufacturing capabilities, quality certifications (AS9100), material expertise, and understanding of the specific application environment. Additive manufacturing specialists like Met3dp, who control both the high-quality powder production and the advanced printing processes, offer a vertically integrated solution that is increasingly attractive for producing custom, high-performance aerospace connector housings tailored to these diverse and demanding applications.
The Additive Advantage: Why Metal 3D Printing is Revolutionizing Aerospace Connector Housing Production
For decades, the production of aerospace connector housings primarily relied on traditional manufacturing techniques like CNC machining from billet (for metals) or injection molding (for high-volume polymers). While effective, these methods present limitations, particularly when dealing with the increasing demands for customization, complexity, and rapid development cycles in modern aerospace. Metal Additive Manufacturing (AM) offers a suite of compelling advantages that are fundamentally changing how these critical components are designed and produced. Aerospace engineers and procurement managers 점점 더 ~로 바뀌고 있습니다 metal AM service providers to leverage these benefits.
Design Freedom Unleashed: Complex Geometries and Integrated Features
Perhaps the most significant advantage of metal AM, particularly Powder Bed Fusion (PBF) processes like SLM and SEBM, is the liberation from traditional Design for Manufacturability (DfM) constraints.
- Complex External Shapes: AM allows the creation of highly organic and complex external housing geometries tailored to fit perfectly within restricted spaces or to improve aerodynamic profiles, without the setup complexity or toolpath limitations of CNC machining.
- Intricate Internal Features: Internal channels for conformal cooling (to dissipate heat from high-power connectors), integrated EMI/RFI shielding partitions, or complex pathways for fiber optics can be designed directly into the housing structure. Machining such internal features is often impossible or requires assembling multiple pieces.
- 격자 구조: Internal lattice or gyroid structures can be incorporated to significantly reduce weight while maintaining structural integrity, a capability unique to AM.
- Feature Integration: Mounting flanges, alignment keys, cable management features, and even spring elements can potentially be integrated directly into the single printed part, reducing the need for downstream assembly.
This design freedom allows engineers to create connector housings that are truly optimized for function and application environment, rather than being constrained by the limitations of how they can be machined or molded.
Lightweighting Strategies: Topology Optimization and Material Efficiency
Weight is a perpetual concern in aerospace design. Metal AM provides powerful tools for creating lightweight yet strong connector housings:
- 토폴로지 최적화: Software tools can analyze the stress distributions within a housing under expected loads and automatically remove material from non-critical areas, resulting in highly optimized, often organic-looking shapes that use the minimum amount of material necessary. AM is uniquely capable of producing these complex, optimized geometries directly.
- 재료 선택: AM enables the use of high strength-to-weight ratio materials like Ti-6Al-4V more efficiently. While titanium ~할 수 있다 be machined, it is difficult and generates substantial expensive scrap. AM uses only the necessary powder, making titanium a more economically viable option for complex, weight-critical housings.
- Hollow Structures and Lattices: As mentioned, the ability to create hollow sections or incorporate internal lattice structures drastically reduces part weight compared to solid machined components, while maintaining required stiffness and strength.
These strategies can lead to weight savings of 30-50% or even more for connector housings compared to traditionally manufactured equivalents, directly translating to improved fuel efficiency, increased payload capacity, or enhanced performance.
Part Consolidation: Reducing Assembly Complexity and Potential Failure Points
Traditional connector assemblies often involve multiple components: the main housing body, backshells, strain reliefs, mounting brackets, EMI gaskets, etc. Each part requires separate manufacturing, inventory management, and assembly steps. Each interface between parts represents a potential failure point (e.g., loosening under vibration, compromised environmental sealing).
Metal AM enables 부품 통합, where multiple functions are integrated into a single, monolithic printed component. 예를 들어
- A housing and its mounting bracket can be printed as one piece.
- Strain relief features can be designed directly into the back of the housing.
- Internal shielding walls can eliminate the need for separate EMI gaskets or inserts in some designs.
Consolidating parts offers significant benefits:
- Reduced Assembly Time and Labor Costs: Fewer parts mean simpler and faster assembly.
- Improved Reliability: Eliminating joints and interfaces reduces potential points of failure.
- Lower Part Count and Inventory: Simplifies logistics and supply chain management.
- Enhanced Structural Integrity: Monolithic parts can be inherently stronger and stiffer.
Accelerated Timelines: Rapid Prototyping and Reduced Lead Times for Production
The aerospace industry demands agility. Metal AM dramatically shortens the timeline from design concept to functional part:
- 신속한 프로토타이핑: Design iterations for custom housings can be printed and physically tested in days, compared to weeks or months for traditional prototypes requiring tooling or complex machining setups. This allows for faster design validation and optimization.
- Tool-Less Production: AM eliminates the need for expensive and time-consuming mold or die creation (for casting/molding) or complex fixture design (for CNC). Production can begin almost immediately after the final design is approved.
- 리드 타임 단축: For low-to-medium volume production runs typical of many custom aerospace components, the overall lead time for AM (including printing and post-processing) is often significantly shorter than traditional methods, especially for complex geometries. This is crucial for meeting tight program schedules.
- 온디맨드 제조: Digital part files enable manufacturing closer to the point of need or producing spare parts quickly without reliance on legacy tooling.
Material Versatility and Performance Enhancement via Metal AM
Metal AM processes can work with a wide range of aerospace-relevant alloys, including stainless steels (like 316L), titanium alloys (like Ti-6Al-4V), aluminum alloys, nickel superalloys (like Inconel 625 or 718), and copper alloys. This allows engineers to select the optimal material for the specific performance requirements of the connector housing (e.g., temperature resistance, corrosion resistance, strength-to-weight ratio).
Furthermore, the layer-by-layer process can sometimes result in fine-grained microstructures with excellent mechanical properties. Companies like Met3dp focus heavily on optimizing the link between their high-quality 금속 분말 and their printing processes (like SEBM) to ensure the resulting parts meet or exceed the properties of wrought or cast materials, delivering consistent, high-performance components suitable for demanding aerospace applications.
Comparing Metal AM (PBF) with Traditional Manufacturing (CNC, Casting)
To fully appreciate the additive advantage, it’s helpful to compare PBF metal AM with traditional methods for producing custom connector housings:
기능 | Metal AM (PBF: SLM/SEBM) | CNC 가공 | 투자 주조 |
---|---|---|---|
디자인 복잡성 | Very High (Internal channels, lattices) | Moderate to High (Limited by tool access) | Moderate (Limited by mold complexity) |
사용자 지정 비용 | Low (Tool-less) | High (Programming, setup, fixtures) | Very High (Tooling/Mold Cost) |
리드 타임(프로토) | Fast (Days) | Moderate (Days to Weeks) | Slow (Weeks to Months) |
Lead Time (Low Vol) | 보통 | 보통에서 높음 | Slow (Requires tooling) |
재료 낭비 | Low (Powder recycling) | High (Subtractive process) | Moderate (Gates, runners) |
무게 감소 | Excellent (Topology opt., lattices) | Limited (Primarily material choice) | Moderate (Near-net shape) |
부품 통합 | 우수 | 제한적 | 제한적 |
Surface Finish (As-Built) | Moderate to Rough | Good to Excellent | 양호 |
Achievable Tolerance | Good (Post-machining often needed) | 우수 | 양호 |
이상적인 볼륨 | Prototypes, Low-to-Medium | Prototypes, Low-to-High | Medium-to-High |
시트로 내보내기
This table highlights that while CNC offers superior tolerance and surface finish directly, and casting is economical at high volumes, metal AM excels in design freedom, customization, speed for complex prototypes, and weight reduction potential, making it uniquely suited for the challenges of modern custom aerospace connector housing production.
The Role of Advanced Metal 3D Printing Technologies
The effectiveness of metal AM relies heavily on the sophistication of the printing technology and the quality of the materials used. Met3dp utilizes advanced processes like 선택적 전자빔 용융(SEBM). SEBM uses an electron beam instead of a laser, typically operating in a vacuum and at higher build chamber temperatures. This offers specific advantages for certain aerospace applications:
- Reduced Residual Stress: The higher processing temperatures inherently stress-relieve the parts during the build, often reducing or eliminating the need for extensive post-build heat treatments, saving time and cost.
- Processing Crack-Prone Materials: SEBM is particularly adept at processing materials like Ti-6Al-4V and other high-temperature alloys that can be susceptible to cracking in laser-based systems.
- High Productivity: Electron beams can often scan faster than lasers, potentially leading to higher build rates for certain geometries.
Coupling advanced printing systems like SEBM with meticulously produced, highly spherical metal powders derived from processes like gas atomization or PREP, as Met3dp does, ensures the highest quality and consistency for demanding aerospace components like connector housings.
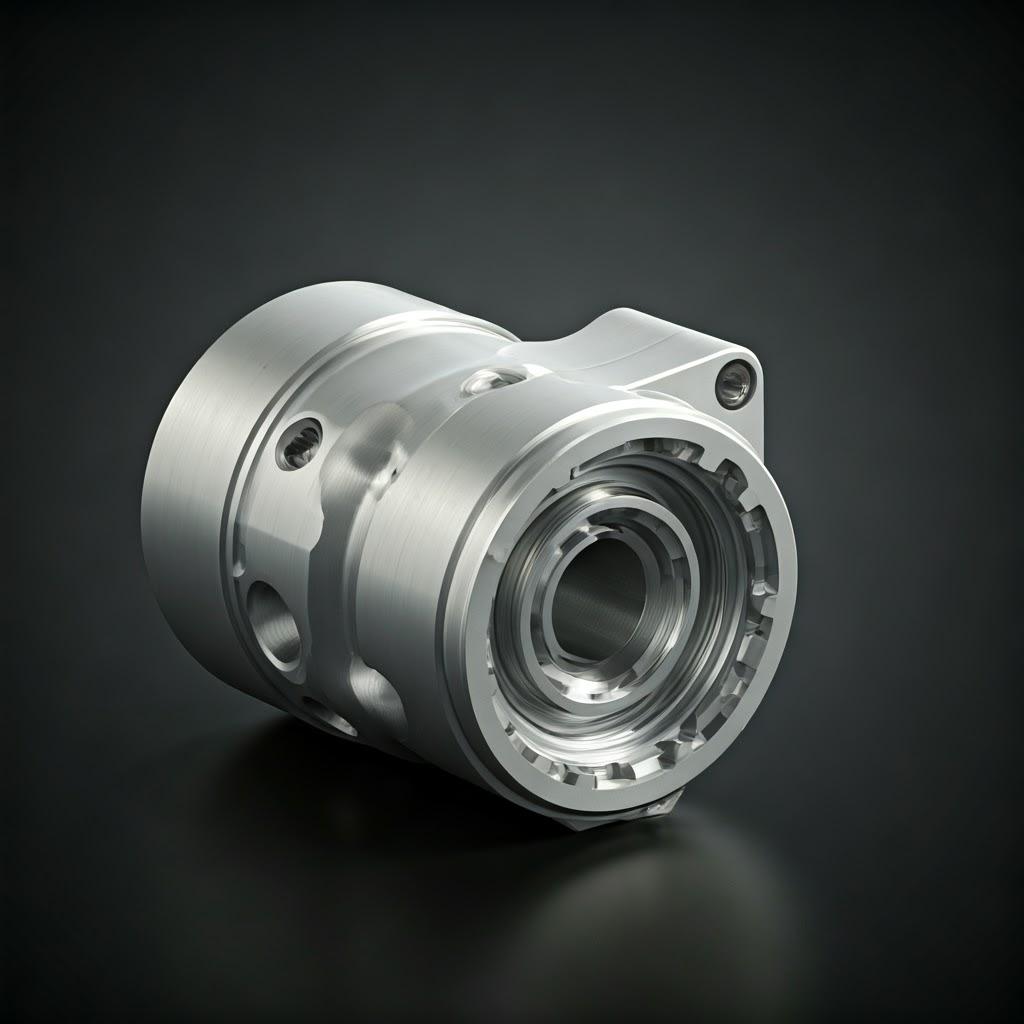
Material Matters: Selecting the Optimal Metal Powders (316L & Ti-6Al-4V) for Aerospace Connectors
Choosing the right material is fundamental to the performance and reliability of any aerospace component, and connector housings are no exception. The material dictates the housing’s ability to withstand harsh environments, protect the delicate connector interfaces, meet weight targets, and satisfy electromagnetic compatibility (EMC) requirements. While metal AM opens the door to using various alloys, two materials stand out as particularly well-suited and commonly used for 3D printed aerospace connector housings: 316L 스테인리스 스틸 및 Ti-6Al-4V 티타늄 합금. Understanding their properties and the importance of powder quality from reliable 금속 분말 공급업체 is crucial for success.
Understanding the Demands: Key Material Properties for Connector Housings
Before diving into specific materials, let’s outline the key properties engineers evaluate when selecting a material for an aerospace connector housing:
- 내식성: Essential for resisting degradation from humidity, salt spray, fuels, hydraulic fluids, and cleaning agents prevalent in aerospace operations.
- 강도와 내구성: The ability to withstand mechanical loads, impacts, vibration, and shock without deformation or fracture. Yield strength, ultimate tensile strength, and fatigue strength are critical parameters.
- Temperature Stability: Maintaining mechanical properties and dimensional stability across the wide operating temperature range (-55°C to +175°C or higher).
- Weight (Density): High strength-to-weight ratio is highly desirable to minimize overall aircraft or spacecraft mass.
- EMI/RFI Shielding Effectiveness: The material’s inherent ability (often enhanced by geometry and coatings) to block electromagnetic interference. Good electrical conductivity generally correlates with better shielding.
- Manufacturability (Printability): How readily and reliably the material can be processed using the chosen metal AM technology (e.g., SLM, SEBM) to achieve dense, defect-free parts.
- 비용: The raw material cost and the cost associated with printing and post-processing it.
- Environmental Compatibility: Factors like outgassing (for space), flammability, and toxicity might be relevant depending on the specific application.
316L Stainless Steel: The Robust and Reliable Workhorse
316L is an austenitic stainless steel alloy containing chromium, nickel, and molybdenum. It is widely used across many industries, including aerospace, for its excellent combination of properties and processability via AM.
- Key Properties of 316L:
- 뛰어난 내식성: The addition of molybdenum provides superior resistance to general corrosion, pitting, and crevice corrosion, particularly in chloride-containing environments (like coastal areas or exposure to de-icing salts). It also resists attack from many industrial chemicals and aerospace fluids.
- Good Strength and Ductility: 316L offers a good balance of tensile strength (typically >500 MPa after printing and stress relief) and ductility (elongation >40%), making it tough and resistant to fracture.
- Good High-Temperature Performance: While not a high-temperature superalloy, 316L maintains useful strength up to moderate temperatures encountered in many aerospace applications (well above 200°C).
- 비자기: In the annealed condition, 316L is typically non-magnetic, which can be important for applications sensitive to magnetic fields.
- Weldability/Joinability: Can be readily welded if needed for assembly or modification (though part consolidation via AM aims to minimize this).
- 뛰어난 인쇄성: 316L is one of the easier and more established metal alloys to process reliably using Laser Powder Bed Fusion (L-PBF/SLM) techniques, achieving high densities (>99.5%).
- 비용 효율성: Compared to titanium alloys or nickel superalloys, 316L powder is significantly less expensive, making it an attractive option when the absolute highest strength-to-weight ratio or extreme temperature resistance is not required.
- Aerospace Applications for 316L Housings:
- General avionics and cabin system connectors where robust environmental protection and good strength are needed, but weight is not the absolute primary driver.
- Ground support equipment (GSE) connectors.
- Applications requiring excellent corrosion resistance in harsh atmospheric conditions.
- Prototypes where cost-effectiveness is important during initial design phases.
- Connectors in less temperature-critical zones of the aircraft.
Procurement managers 찾고있다 stainless steel wholesale suppliers for AM powders should verify the powder quality meets aerospace requirements for purity and consistency.
Ti-6Al-4V (Grade 5) Titanium Alloy: The High-Performance Lightweight Champion
Ti-6Al-4V (often abbreviated as Ti64) is the most widely used titanium alloy, accounting for more than 50% of all titanium tonnage globally. It’s an alpha-beta alloy renowned for its exceptional combination of high strength, low density, and excellent corrosion resistance, making it a go-to material for demanding aerospace applications.
- Key Properties of Ti-6Al-4V:
- Very High Strength-to-Weight Ratio: This is Ti64’s defining characteristic. It offers strength comparable to many steels but at roughly 40-45% lower density. This makes it ideal for weight-critical aerospace components. Typical tensile strength after printing and heat treatment can exceed 1000 MPa.
- 뛰어난 내식성: Ti64 forms a stable, protective oxide layer that provides outstanding resistance to corrosion in most natural environments, including seawater, and many industrial chemicals and aerospace fluids.
- High-Temperature Capability: It retains good strength at elevated temperatures, suitable for applications up to around 350-400°C, making it viable for hotter zones near engines or in high-speed aircraft.
- 낮은 열 팽창: Compared to steels and aluminum alloys, titanium has a lower coefficient of thermal expansion, reducing thermal stress in assemblies experiencing temperature fluctuations.
- 생체 적합성: While less relevant for connector housings, its excellent biocompatibility makes it suitable for medical implants (demonstrating its inertness).
- Good Printability (especially with SEBM): While Ti64 can be processed using L-PBF, it is somewhat reactive and benefits from the vacuum environment and higher build temperatures of SEBM technology (like that used by Met3dp), which helps manage residual stresses and ensures optimal material properties. High densities (>99.7%) are achievable.
- Aerospace Applications for Ti-6Al-4V Housings:
- Weight-critical applications: anywhere minimizing mass is paramount (satellites, UAVs, performance aircraft).
- Applications requiring high strength and durability in demanding mechanical environments (e.g., landing gear, flight control systems).
- Housings located in high-temperature zones (engine nacelles, pylons, environmental control systems).
- Space applications where low outgassing and strength-to-weight are critical.
- Components requiring exceptional corrosion resistance combined with high strength.
신뢰할 수 있는 titanium alloy distributors specializing in high-quality powders certified for aerospace AM processes is essential when specifying Ti-6Al-4V.
Comparing 316L vs. Ti-6Al-4V for Connector Housings (Table Format)
속성 | 316L 스테인리스 스틸 | Ti-6Al-4V (Grade 5) Titanium Alloy | Considerations for Connector Housings |
---|---|---|---|
밀도 | ~7.9-8.0 g/cm³ | ~4.43g/cm³ | Significant weight savings with Ti-6Al-4V (approx. 45% lighter). |
Typical Tensile Strength (AM) | ~500-600 MPa | ~950-1100 MPa (Heat Treated) | Ti-6Al-4V는 much higher strength. |
무게 대비 강도 비율 | 보통 | 우수 | Key advantage for Ti-6Al-4V in aerospace. |
내식성 | Excellent (general, pitting) | Excellent (esp. oxidizing environments) | Both are excellent; Ti-6Al-4V may have an edge in some specific media. |
최대 서비스 온도 | Moderate (~300°C continuous use limit) | Higher (~350-400°C) | Ti-6Al-4V is preferred for higher temperature applications. |
열 전도성 | Lower (~16 W/m·K) | Very Low (~7 W/m·K) | Can impact heat dissipation from connectors; may require design features. |
전기 전도성 | Lower (compared to Al, Cu) | 매우 낮음 | Impacts EMI shielding effectiveness (geometry/coatings often compensate). |
Printability (AM) | Excellent (esp. L-PBF) | Good (esp. SEBM); more reactive | Both are well-established AM materials. |
Powder Cost | Lower | Significantly Higher | Major factor in overall part cost. |
포스트 프로세싱 | Standard (stress relief, finishing) | Often requires specific heat treatments | Ti-6Al-4V processing requires more care. |
시트로 내보내기
결론: 선택 316L when cost is a major driver, weight is less critical, and operating temperatures are moderate, but good corrosion resistance and durability are still required. Choose Ti-6Al-4V when maximum weight savings, high strength, and/or higher temperature resistance are primary requirements, and the higher cost is justified by performance gains.
The Importance of High-Quality Metal Powders from Trusted Suppliers
The final performance of a 3D printed metal connector housing is inextricably linked to the quality of the metal powder used. Simply specifying “316L” or “Ti-6Al-4V” is not enough. For demanding aerospace applications, partnering with a metal AM powder supplier that guarantees consistent, high-quality material is paramount. Key powder characteristics influencing part quality include:
- 구형성: Highly spherical powder particles flow evenly and pack densely in the powder bed, leading to more uniform melting and higher final part density (fewer voids).
- 입자 크기 분포(PSD): A controlled PSD ensures good flowability and resolution, impacting surface finish and feature definition. Aerospace standards often specify acceptable PSD ranges.
- 흐름성: Measured by Hall flow rate, good flowability ensures uniform powder deposition across the build plate layer after layer, preventing defects.
- Chemical Purity: Contaminants (like oxygen, nitrogen, carbon in titanium; inclusions in steel) can drastically degrade mechanical properties (especially fatigue life and ductility). Strict control over the powder manufacturing process is needed to minimize impurities.
- Absence of Satellites: Small, irregular particles attached to larger spherical ones (“satellites”) can hinder flowability and packing density.
- Batch-to-Batch Consistency: Reliable suppliers implement rigorous quality control to ensure that powder properties remain consistent from one batch to the next, guaranteeing repeatable part performance.
Inferior powder quality can lead to porosity, poor mechanical properties, dimensional inaccuracies, and inconsistent results – all unacceptable for flight-critical components.
Met3dp’s Commitment to Premium Powder Production (Gas Atomization, PREP)
Recognizing the critical link between powder quality and part performance, Met3dp has invested heavily in state-of-the-art powder production technologies. Our commitment ensures that the 316L, Ti-6Al-4V, and other advanced alloy powders we supply meet the stringent requirements of the aerospace industry.
- Advanced Atomization Technologies: We employ industry-leading 가스 분무(GA) 및 플라즈마 회전 전극 공정(PREP) 기법.
- 가스 분무: Uses high-pressure inert gas jets to break up a stream of molten metal into fine droplets, which solidify into spherical powder. Our proprietary nozzle and gas flow designs optimize this process for high sphericity and controlled particle sizes.
- PREP: Rotates a consumable electrode rod at high speed while melting its tip with a plasma torch. Centrifugal force throws off molten droplets that solidify in an inert atmosphere, resulting in exceptionally clean and spherical powders with minimal satellites, ideal for the most demanding applications like aerospace and medical.
- 엄격한 품질 관리: Every batch of Met3dp powder undergoes extensive testing for chemical composition, particle size distribution, morphology (sphericity), flowability, and density, ensuring it meets or exceeds industry standards.
- Optimized for AM Processes: Our powders are specifically developed and characterized for optimal performance in Powder Bed Fusion systems, including our own SEBM printers, ensuring compatibility and predictable results.
By controlling the powder production process using advanced techniques and stringent QC, Met3dp provides aerospace manufacturers and B2B 구매자 with the confidence that the foundational material for their 3D printed connector housings is of the highest possible quality, enabling the production of dense, reliable, and high-performance components. Explore more about our comprehensive 금속 3D 프린팅 솔루션을 제공합니다.
Design for Additive Manufacturing (DfAM): Optimizing Connector Housing Geometry for Metal 3D Printing Success
Successfully leveraging the power of metal additive manufacturing for components like aerospace connector housings requires more than simply sending an existing CAD file to the printer. It demands a fundamental shift in design thinking, moving away from the constraints of traditional subtractive or formative processes towards embracing the possibilities and respecting the nuances of layer-by-layer fabrication. This approach is known as 적층 제조를 위한 설계(DfAM). Implementing DfAM principles from the outset is crucial for maximizing the benefits of AM – achieving lightweighting, part consolidation, optimal performance, and cost-effectiveness. Collaborating with experienced DfAM service providers 또는 metal AM suppliers like Met3dp, who possess deep DfAM expertise, can significantly streamline this process and unlock the full potential of the technology.
Thinking Additively: Key Principles of DfAM for Housings
DfAM isn’t just a set of rules; it’s a methodology that integrates manufacturing process capabilities into the design phase. For metal aerospace connector housings produced via Powder Bed Fusion (PBF), key DfAM principles include:
- Embracing Complexity (Where Beneficial): Unlike machining, where complexity adds cost and time, AM handles intricate geometries with relative ease. DfAM encourages engineers to leverage this by designing features like internal channels, conformal shapes, and integrated functionalities that were previously impractical.
- Designing for Orientation: How a part is oriented on the build plate significantly impacts print time, support structure requirements, surface finish on different faces, and even mechanical properties (due to anisotropic behavior in some AM processes/materials). DfAM involves considering the optimal orientation early in the design process.
- Minimizing Support Structures: Support structures are often necessary in PBF to anchor the part to the build plate and support overhanging features. However, they consume extra material, add print time, and require removal in post-processing, which adds labor cost and can affect surface finish. A core DfAM goal is to design parts that minimize the need for supports, often by utilizing self-supporting angles.
- Considering Powder Removal: For housings with internal cavities or channels, DfAM necessitates designing escape holes or pathways to allow unfused powder to be removed after printing. Trapped powder adds weight and can pose risks if it comes loose later.
- Optimizing for Post-Processing: DfAM anticipates downstream processes. Designing features to be easily accessible for support removal, machining critical interfaces, or surface finishing can significantly reduce post-processing time and cost.
- Leveraging Part Consolidation: DfAM actively looks for opportunities to combine multiple components of an assembly (e.g., housing, bracket, backshell) into a single, integrated AM part, reducing assembly complexity and improving reliability.
- Understanding Material & Process Limitations: DfAM considers the specific capabilities and limitations of the chosen AM process (e.g., SLM, SEBM) and material (e.g., 316L, Ti-6Al-4V), such as minimum feature size, achievable tolerances, and thermal behavior.
Adopting a DfAM mindset ensures that the final design is not only functional but also efficiently manufacturable via metal 3D printing, maximizing the technology’s advantages for aerospace component design.
Wall Thickness Considerations and Minimum Feature Sizes
Metal AM processes have limitations on the minimum size of features and walls they can reliably produce. Designing below these thresholds can lead to incomplete formation, poor resolution, or structural weakness.
- Minimum Wall Thickness: This depends on the specific AM machine (beam spot size, layer thickness), the material being printed, and the orientation of the wall.
- For PBF processes like SLM and SEBM, a general guideline for robust walls is often in the range of 0.4mm to 1.0mm. Thinner walls might be possible but require careful validation and may be more prone to distortion or damage during handling and post-processing.
- Vertical walls generally print more reliably at minimum thickness than horizontal or low-angle walls (which essentially become overhangs).
- 최소 피처 크기: This refers to small details like pins, bosses, or embossed text.
- Positive features (protrusions) are generally easier to print small than negative features (holes, slots).
- Minimum reliably printable feature sizes are often slightly larger than minimum wall thickness, typically starting around 0.5mm to 1.0mm. Very fine details may lose definition due to melt pool dynamics and powder particle size.
- Aspect Ratio: Tall, thin walls can be prone to warping or instability during the build. DfAM considers limiting excessive aspect ratios where possible or adding reinforcing features (ribs).
Engineers designing connector housings must ensure that all critical structural elements, sealing surfaces, and functional features adhere to these minimums. Trying to replicate designs intended for micromachining without considering AM limitations will likely lead to printing failures or non-functional parts.
Support Structure Strategy: Minimizing Waste and Post-Processing
Support structures are a critical but often undesirable necessity in PBF metal printing. They serve several functions:
- Anchoring: Secure the part to the build plate, preventing warping or shifting during the build.
- Supporting Overhangs: Provide a foundation for features angled below a certain threshold relative to the build plate (typically < 45 degrees). Without supports, these overhangs would deform or collapse into the powder bed.
- Heat Conduction: Help dissipate heat away from the molten zone, reducing thermal stress and preventing overheating of delicate features.
However, supports present challenges:
- 재료 낭비: Supports are sacrificial and represent wasted expensive metal powder.
- Increased Build Time: Printing supports adds to the overall machine time.
- Difficult Removal: Removing metal supports can be labor-intensive (manual breaking, cutting, machining) and potentially damage the part surface.
- Surface Finish Impact: The areas where supports attach to the part typically have a rougher surface finish that requires refinement.
Effective DfAM strategies for support structures include:
- Designing Self-Supporting Angles: Where possible, design overhangs and features to be above the critical self-supporting angle (often ~45 degrees, but machine/material dependent). Using chamfers instead of sharp horizontal overhangs is a common technique.
- Optimizing Part Orientation: Choose a build orientation that minimizes the total area requiring support. This is often a trade-off with other factors like surface finish requirements or build time.
- Using Optimized Support Types: Modern AM software allows for various support structures (e.g., block, line, cone, tree, lattice supports). Selecting the type that provides adequate support with minimal material usage and easier removal is key. Lattice supports, for instance, can be strong yet use less material and be easier to remove than solid blocks.
- Designing for Accessibility: Ensure support structures are located where they can be easily reached for removal tools. Avoid placing supports in deep internal cavities unless absolutely necessary and accessible.
- Minimizing Contact Points: Design supports to connect to the part at minimal contact points or on non-critical surfaces where possible, making removal scars less impactful.
Incorporating Internal Channels for Cooling or Shielding
One of the powerful capabilities of AM is the ability to create complex internal channels within a part – something extremely difficult or impossible with traditional methods. For aerospace connector housings, this can be leveraged for:
- Conformal Cooling: High-power connectors generate heat. Internal channels conforming closely to the heat source can be designed to allow airflow or even liquid coolant circulation, improving thermal management and preventing overheating.
- Integrated Shielding: Internal walls or compartments can be designed within the housing to provide EMI/RFI shielding between different connector sections or cable bundles within the same housing, improving signal integrity.
- Wire Routing: Complex internal pathways can potentially guide wires or fiber optics within the housing structure itself.
However, designing effective internal channels requires careful DfAM:
- Powder Removal: This is the biggest challenge. Channels must have sufficient diameter (typically >1-2mm, depending on length and complexity) and accessible openings (escape holes) to allow for complete removal of unfused powder after the build. Trapped powder is unacceptable. Multiple access points might be needed for complex networks.
- Self-Supporting Design: Internal channels often have “roofs” that act as horizontal overhangs. Designing channel cross-sections with self-supporting shapes (e.g., diamond, teardrop) can eliminate the need for internal supports, which are extremely difficult or impossible to remove.
- 표면 마감: The internal surface finish of AM channels will be relatively rough (as-built condition). If a smooth internal surface is required (e.g., for fluid flow), it may necessitate secondary processing steps like abrasive flow machining or chemical polishing, adding complexity and cost.
Designing for Orientation and Build Plate Placement
As mentioned, the orientation of the connector housing on the build plate is a critical DfAM decision with multiple implications:
- 지원 구조: Orienting the part to minimize steep overhangs reduces the need for supports.
- 표면 마감: Surfaces facing upwards or vertical generally have better surface finish than surfaces facing downwards (which are affected by support contact points) or low-angle surfaces (which exhibit stair-stepping effects). Critical surfaces should ideally be oriented for optimal finish or positioned for easy post-process machining.
- 구축 시간: Taller builds generally take longer. Orienting the part to minimize its height (Z-dimension) can sometimes reduce print time, though this often conflicts with minimizing supports.
- 기계적 속성: Due to the layer-wise construction, AM parts can exhibit anisotropic mechanical properties (strength may vary depending on the direction of load relative to the build layers). Critical stress directions should be considered when choosing orientation, although this effect is often less pronounced with optimized parameters and materials like Ti-6Al-4V processed via SEBM.
- 열 관리: Orientation can influence heat buildup and dissipation during the build, potentially affecting residual stress and warping.
- Build Plate Packing: When printing multiple housings, their orientation and placement affect how many parts can fit onto a single build plate, impacting overall throughput and cost per part.
DfAM involves using simulation tools and process expertise to find the optimal orientation that balances these competing factors for the specific housing design and application requirements.
Leveraging Simulation Tools for Design Validation
Modern engineering workflows increasingly incorporate simulation tools early in the design process, and this is particularly valuable for DfAM:
- 토폴로지 최적화: As discussed previously, these tools automatically generate lightweight, load-optimized geometries ideally suited for AM production.
- Process Simulation: Specialized AM simulation software can predict potential issues 전에 printing, such as:
- Thermal Distortion and Warping: Simulating the heat buildup and cooling during the layer-by-layer process helps identify areas prone to warping. This allows designers to adjust the orientation, add or strengthen supports, or modify the design to mitigate these risks.
- 잔여 스트레스: Predicting the buildup of internal stresses helps optimize heat treatment strategies.
- Support Structure Effectiveness: Simulating whether the planned supports will be sufficient to prevent build failure.
- Performance Simulation: Standard FEA (Finite Element Analysis) tools can be used to verify the structural integrity, thermal performance (e.g., effectiveness of cooling channels), and vibration response of the AM housing design under operational loads.
Using simulation proactively allows designers to iterate and refine the housing design digitally, significantly reducing the risk of costly build failures and ensuring the final part meets performance requirements. Companies like Met3dp often utilize such tools as part of their engineering support services to help clients optimize designs for successful additive manufacturing.
Precision Perfected: Achieving Tight Tolerances, Superior Surface Finish, and Dimensional Accuracy in 3D Printed Housings
While metal AM excels in creating complex geometries, achieving the high levels of precision often required for aerospace components, particularly mating interfaces and sealing surfaces on connector housings, demands careful process control and often involves secondary finishing operations. Understanding the achievable limits of metal 3D printing tolerances, the nature of surface finish in metal AM, and the factors influencing overall 치수 정확도 is crucial for engineers and procurement managers evaluating precision manufacturing suppliers.
Understanding Achievable Tolerances with Metal Powder Bed Fusion
Tolerance refers to the permissible range of variation in a dimension of a part. In metal AM, achievable tolerances are influenced by numerous factors, including the machine, material, part size and geometry, and post-processing.
- General Tolerances (As-Built): For typical PBF processes (SLM, SEBM), general achievable tolerances for well-controlled processes are often cited in the range of:
- ± 0.1 mm to ± 0.2 mm for smaller dimensions (e.g., up to 50-100 mm).
- ± 0.1% to ± 0.2% of the nominal dimension for larger features.
- Machine Specificity: Higher-end machines with better calibration, thermal control, and finer beam spots can often achieve tighter tolerances within this range. Met3dp’s focus on industry-leading equipment contributes to achieving high precision.
- Geometry Dependence: Complex geometries, thin walls, and large flat surfaces can be more prone to slight variations or warping compared to simpler, chunkier parts.
- Need for Post-Machining: Crucially, for features requiring very tight tolerances – such as connector mating interfaces, O-ring grooves, threaded holes, or precision mounting surfaces – the as-built AM tolerances are often insufficient. These critical features are typically designed with extra stock material (“machining allowance”) and are finished using CNC 가공 after the printing and stress relief stages. This hybrid approach leverages AM’s geometric freedom and CNC’s precision where needed. Tolerances achievable with post-machining are typically ± 0.01 mm to ± 0.05 mm or even tighter, meeting standard aerospace requirements.
It is essential to clearly define critical dimensions and tolerances on engineering drawings, indicating which surfaces require post-machining to achieve final specifications.
Factors Influencing Dimensional Accuracy
Achieving consistent dimensional accuracy in metal AM depends on meticulous control over numerous factors:
- Printer Calibration: Regular calibration of the scanner system, beam focus, and build platform leveling is essential.
- 프로세스 매개변수: Laser/electron beam power, scan speed, layer thickness, hatch spacing, and scan strategy all influence the melt pool size and stability, affecting dimensional accuracy. Optimized parameter sets developed by experienced providers like Met3dp are key.
- 머티리얼 속성: Variations in powder characteristics (PSD, flowability, morphology) can affect packing density and melting behavior. Using consistent, high-quality powder is crucial. The thermal expansion coefficient of the material also plays a role.
- 열 효과: Uneven heating and cooling during the build process lead to thermal stresses, which can cause warping and distortion, impacting final dimensions. Factors like part orientation, support strategy, and machine thermal management (e.g., heated build plate/chamber, as in SEBM) influence this.
- Part Size and Geometry: Larger parts experience more cumulative thermal stress. Complex geometries can create localized heat traps or stress concentrations.
- 빌드 오리엔테이션: As discussed under DfAM, orientation affects thermal behavior and support needs, both influencing accuracy.
- 후처리: Stress relief heat treatments are vital for dimensional stability but can cause slight, predictable dimensional changes that must be accounted for. Improper support removal can also distort parts.
Achieving high accuracy requires a holistic approach, combining robust machine technology, quality materials, optimized process parameters, sound DfAM principles, and controlled post-processing.
Surface Finish Characteristics: As-Built vs. Post-Processed
Surface finish, typically quantified by average roughness (Ra), is another critical characteristic for connector housings, affecting sealing, aesthetics, and sometimes electrical contact or friction.
- As-Built Surface Finish: The surface finish of parts directly after PBF printing is inherently rougher than machined surfaces. Typical Ra values range from 5 µm to 20 µm, 다음에 따라 다름:
- Orientation: Top-facing surfaces are generally smoothest. Vertical walls show layer lines. Downward-facing surfaces supported by structures are typically the roughest due to support contact points. Angled surfaces exhibit “stair-stepping” inherent to the layer-wise process, with lower angles resulting in rougher finishes.
- 프로세스 매개변수: Layer thickness (thinner layers = smoother), beam energy input, and scan strategy influence melt pool stability and resulting surface texture.
- 파우더 입자 크기: Finer powders can contribute to smoother finishes but may have flowability trade-offs.
- Machine Type: Different machine optics and control systems can yield slightly different surface characteristics.
- Post-Processed Surface Finish: For many connector housing applications, the as-built surface finish is acceptable for non-critical external surfaces. However, sealing surfaces, mating faces, or aesthetically important areas often require improvement through post-processing. Common methods include:
- Bead Blasting / Sand Blasting: Provides a uniform matte finish, removing some loose particles and reducing Ra slightly (e.g., down to 5-10 µm Ra).
- Tumbling / Vibratory Finishing: Uses abrasive media in a tumbling barrel or vibratory bowl to smooth surfaces and round edges. Can achieve smoother finishes (e.g., 1-5 µm Ra) but is generally limited to external surfaces and less precise feature control.
- CNC 가공: Used for critical surfaces requiring smooth finishes (Ra < 1 µm often achievable) and tight tolerances.
- 연마: Manual or automated polishing can achieve very smooth, mirror-like finishes (Ra << 1 µm) for specific requirements.
- 전기 연마: An electrochemical process that removes a microscopic layer of material, smoothing surfaces and improving corrosion resistance, particularly effective for stainless steels like 316L.
Techniques for Improving Surface Roughness (Ra)
Beyond secondary processing, some strategies during printing can help optimize the as-built finish:
- Orientation: Prioritize orienting critical surfaces vertically or upwards if possible.
- 매개변수 최적화: Fine-tuning parameters like contour scans (laser passes around the edge of each layer) can improve sidewall finish.
- Thinner Layers: Using smaller layer thicknesses results in finer stair-stepping on angled surfaces, improving perceived smoothness, but increases build time.
- Beam Offset Compensation: Software can adjust the beam path slightly to compensate for melt pool characteristics and improve dimensional accuracy, which indirectly relates to effective surface smoothness on features.
However, achieving finishes comparable to machining typically requires dedicated post-processing steps. Explore Met3dp’s 인쇄 방법 and capabilities for achieving desired part characteristics.
Metrology and Quality Control for Aerospace Components
Verifying that the final 3D printed and post-processed connector housing meets the specified dimensional and surface finish requirements is critical, especially for aerospace. Common metrology techniques include:
- Coordinate Measuring Machines (CMMs): High-precision touch probes measure discrete points to verify critical dimensions and geometric tolerances (GD&T). Essential for final acceptance of machined features.
- 3D Laser Scanning / Structured Light Scanning: Non-contact methods that capture millions of points to create a 3D model of the printed part. This can be compared to the original CAD model to visualize deviations across the entire surface, useful for complex geometries and verifying overall form.
- Surface Roughness Testers (Profilometers): Stylus-based instruments measure the surface profile to quantify Ra and other roughness parameters.
- Visual Inspection: Magnified visual checks for surface defects, incomplete features, or residual support material.
- Computed Tomography (CT) Scanning: Industrial X-ray technique used for non-destructive inspection of internal features, checking for trapped powder, internal voids, or defects within the part’s volume. Increasingly important for qualifying critical AM aerospace parts.
A robust Quality Management System (QMS), ideally certified to aerospace standards like AS9100, ensures these checks are performed consistently and documented thoroughly. Aerospace manufacturers demand this level of quality assurance from their component suppliers.
The Role of High-Resolution Printing Systems
The precision capabilities of the metal AM system itself form the foundation for achieving accurate parts. High-resolution systems, characterized by:
- Fine Beam Spot Size: Allows for the creation of smaller features and sharper details.
- Precise Scanner Control: Accurate and fast positioning of the laser or electron beam ensures geometric fidelity.
- Advanced Software Algorithms: Sophisticated control over parameters and scan strategies optimizes melting and minimizes deviations.
- Stable Thermal Management: Consistent temperatures within the build chamber reduce warping and improve predictability.
Met3dp’s investment in industry-leading printing equipment provides a strong basis for producing connector housings with high as-built accuracy and fine feature resolution, minimizing the amount of compensatory post-processing required.
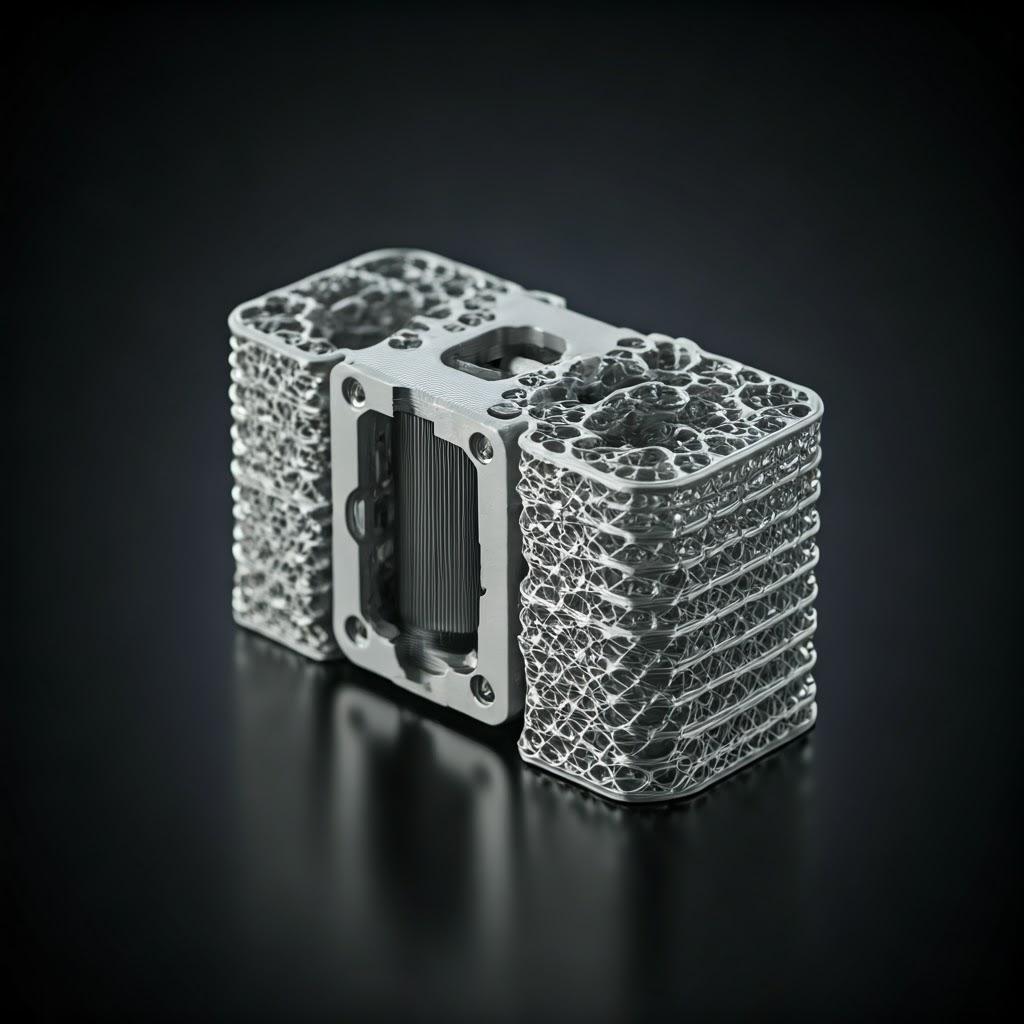
Beyond the Build: Essential Post-Processing Steps for Aerospace Connector Housings
A common misconception about metal 3D printing is that parts come out of the machine ready to use. In reality, particularly for demanding applications like aerospace connector housings, the printing process is just the first step. A series of crucial metal 3D printing post-processing steps are nearly always required to transform the as-built part into a functional, reliable component meeting stringent aerospace specifications. These steps address residual stress, powder removal, support structures, surface finish, dimensional tolerances, and material properties. Understanding these requirements is vital when evaluating metal AM service providers and calculating total part cost and lead time.
Stress Relief and Heat Treatment: Ensuring Material Stability and Performance
The rapid heating and cooling cycles inherent in PBF processes create significant internal stresses within the as-built part. These stresses can lead to distortion (especially after removal from the build plate), reduced mechanical performance, and potential cracking over time.
- 스트레스 해소: This is typically the very first step after the build finishes and excess powder is removed. The part, often while still attached to the build plate, is heated in a furnace to a specific temperature below its transformation point, held for a period, and then slowly cooled. This allows the material’s crystal lattice to relax, significantly reducing internal stresses.
- Necessity: Absolutely critical for parts made with L-PBF (SLM/DMLS) due to higher thermal gradients. For SEBM, which operates at elevated temperatures, the need for extensive stress relief can sometimes be reduced or eliminated, which is an advantage of Met3dp’s SEBM technology.
- Typical Cycles: For 316L, stress relief might involve heating to 600-800°C. For Ti-6Al-4V, it’s often done around 650-800°C in a vacuum or inert atmosphere furnace to prevent oxidation.
- Further Heat Treatments (Solution Annealing, Aging): Beyond stress relief, additional heat treatments may be required to achieve the desired final microstructure and mechanical properties (e.g., optimizing strength, ductility, hardness, fatigue life).
- Ti-6Al-4V: Often undergoes solution treatment followed by aging (STA) or annealing cycles to achieve specific strength and ductility combinations required by aerospace standards (e.g., AMS specifications for Ti-6Al-4V). These typically involve higher temperatures (e.g., 900-950°C for solution treatment) in a vacuum furnace.
- 316L: May be annealed (e.g., ~1050°C) to maximize ductility and corrosion resistance if required.
적절한 heat treatment for aerospace alloys is critical and must be performed using calibrated furnaces and precisely controlled cycles, followed by appropriate testing (e.g., hardness, tensile tests) to verify results.
Support Structure Removal: Techniques and Considerations
Once stress-relieved, the part needs to be separated from its support structures. This can be one of the most labor-intensive and potentially damaging post-processing steps if not planned carefully during DfAM.
- 빌드 플레이트에서 파트 제거: Typically done using wire EDM (Electrical Discharge Machining), band sawing, or sometimes manual breaking for smaller parts/supports. Wire EDM provides a clean cut with minimal force exerted on the part.
- Support Removal Techniques:
- Manual Breaking/Cutting: Supports are often designed with weakened interfaces or perforation points allowing them to be broken off manually using pliers or hand tools. This is quick but leaves rough witness marks.
- Machining (Milling/Grinding): CNC machining or manual grinding can be used to remove support structures, especially bulky ones or those on critical surfaces. This offers more control over the final surface but adds time and cost.
- Wire EDM / Plunge EDM: Can be used to precisely cut away supports in difficult-to-reach areas, but is slower.
- 고려 사항:
- 접근성: Supports hidden in deep pockets or internal channels are extremely challenging to remove. DfAM is key to avoid this.
- Material: Titanium alloys like Ti-6Al-4V are tougher to cut or machine than stainless steel, making support removal more laborious.
- Damage Risk: Applying excessive force during manual removal can distort or break delicate features.
Efficient and careful support removal is crucial for achieving the final part geometry without compromising its integrity.
Surface Finishing Operations: Machining, Polishing, Blasting
As discussed previously, the as-built surface finish of AM parts often needs refinement. Connector housings may require various finishing operations depending on functional and aesthetic requirements:
- 연마제 블라스팅(비드/모래 블라스팅): Common for achieving a uniform matte finish, cleaning surfaces, and removing semi-sintered particles. Different media (glass beads, aluminum oxide) produce different finishes.
- 텀블링/진동 마감: Effective for smoothing external surfaces and deburring edges on batches of parts, reducing Ra values significantly.
- CNC 가공: Essential for achieving tight tolerances and smooth finishes on critical interfaces (mating faces, sealing grooves, mounting holes).
- Grinding/Polishing: For achieving very smooth surfaces (low Ra) where required, often done manually or with robotic assistance for complex shapes.
- 전기 연마: Particularly effective for 316L, providing a very smooth, clean, and corrosion-resistant surface by electrochemically removing material.
The specific combination of finishing steps depends entirely on the requirements defined in the part specification and drawing.
Coatings and Platings for Enhanced Performance
While base materials like 316L and Ti-6Al-4V offer good intrinsic properties, coatings or platings are sometimes applied to 3D printed connector housings to further enhance specific characteristics:
- EMI/RFI Shielding: While the metal housing itself provides shielding, plating with highly conductive metals like copper, nickel, or silver can significantly improve shielding effectiveness, especially at higher frequencies. Electroless nickel plating is a common choice.
- 부식 방지: Although 316L and Ti64 are highly corrosion-resistant, specialized coatings (e.g., chemical conversion coatings like chromate or phosphate, paint, PVD coatings) might be applied for extreme environments or specific fluid compatibility.
- 내마모성: Hard coatings (e.g., TiN, CrN applied via PVD) could be used if the housing experiences significant abrasive wear, though this is less common for standard connectors.
- 전기 전도도: Plating can enhance surface conductivity for grounding or contact purposes.
- Cosmetic Finishes: Anodizing (for Titanium), painting, or powder coating can provide specific colors or aesthetic finishes.
Applying coatings requires proper surface preparation of the AM part to ensure good adhesion. Working with qualified aerospace component finishing suppliers experienced with AM parts is recommended.
Cleaning and Final Inspection Protocols
Throughout the post-processing chain, cleaning steps are necessary to remove residues from machining coolants, blasting media, polishing compounds, or plating chemicals.
- Final Cleaning: A final, thorough cleaning process (often involving ultrasonic cleaning in specific solvents or detergents) is performed to ensure the connector housing is free from any contaminants before final inspection and packaging.
- Final Inspection: Includes dimensional verification (CMM, scanning), surface finish checks, visual inspection for defects, and potentially NDT (like CT scanning for critical parts) to ensure the finished housing meets all specifications outlined in the drawing and quality plan. Material certifications and process documentation traceability are key deliverables for aerospace components.
Working with Qualified Post-Processing Partners
The range of required post-processing steps often necessitates specialized equipment and expertise that may not all reside within a single AM service bureau. Many 금속 3D 프린팅 서비스 제공업체 have established relationships with qualified partners for services like heat treatment, precision machining, plating, and NDT. When selecting a supplier, it’s important to understand their in-house capabilities versus their network of subcontractors and ensure the entire supply chain meets aerospace quality standards (e.g., AS9100 certification, Nadcap accreditation for special processes). Met3dp, with its focus on comprehensive solutions, assists clients in navigating these post-processing requirements to ensure end-to-end quality.
Navigating Challenges: Overcoming Potential Hurdles in Metal 3D Printing Aerospace Connectors
While metal additive manufacturing offers transformative potential for producing custom aerospace connector housings, it’s not without its technical challenges. Achieving the required quality, reliability, and consistency demands a deep understanding of the process physics, materials science, and potential failure modes. Acknowledging these metal 3D printing problems and implementing robust mitigation strategies is key to successfully deploying AM for critical aerospace components. Partnering with an experienced and technologically advanced reliable AM supplier like Met3dp, who proactively addresses these challenges, is crucial for mitigating risks.
Mitigating Warping and Residual Stress
Perhaps the most pervasive challenge in metal PBF is managing the thermal stresses generated during the rapid heating and cooling cycles. These stresses can cause:
- 워핑: Distortion of the part during the build, potentially causing the part to lift from the supports or collide with the powder recoater blade, leading to build failure.
- 잔여 스트레스: Internal stresses remaining in the part after cooling, which can compromise dimensional stability, reduce fatigue life, and potentially lead to cracking.
완화 전략:
- Optimized Support Structures: Robust supports are essential to anchor the part firmly to the build plate and resist warping forces. DfAM plays a key role here.
- 빌드 오리엔테이션: Orienting the part to minimize large flat surfaces parallel to the build plate and reduce overall thermal mass gradients can help.
- Scan Strategy Optimization: Using specific patterns (e.g., island scanning, checkerboard patterns) breaks up long, continuous melt tracks, distributing heat more evenly and reducing stress buildup. Parameters like beam power and speed are also critical.
- Process Simulation: Predicting stress accumulation during the design phase allows for proactive adjustments to geometry or supports.
- 스트레스 완화 열처리: Essential post-processing step to relax internal stresses (as detailed previously).
- Elevated Temperature Processing (SEBM): Technologies like Electron Beam Melting (SEBM), utilized by Met3dp, operate with significantly higher build chamber temperatures. This keeps the part hot throughout the build, acting like an in-situ stress relief process and resulting in parts with much lower residual stress compared to typical L-PBF, significantly reducing warping risk.
Ensuring Part Density and Avoiding Porosity
Achieving near-full density (typically >99.5% or higher for aerospace) is critical for mechanical integrity. Porosity (internal voids) can act as stress concentrators, drastically reducing fatigue life and overall strength.
Causes of Porosity:
- Lack of Fusion: Insufficient energy input (low power, high speed) fails to completely melt the powder particles, leaving gaps between layers or scan tracks.
- Keyholing: Excessive energy input creates deep, unstable melt pools that can collapse, trapping gas and forming pores.
- 가스 다공성: Gasses dissolved in the molten metal or trapped within hollow powder particles can form pores upon solidification.
- Poor Powder Quality: Irregularly shaped powder or powder with internal voids packs less efficiently and can trap gas.
완화 전략:
- Optimized Process Parameters: Extensive process development is required to find the optimal window for laser/beam power, scan speed, layer thickness, and hatch spacing for each material to achieve consistent, complete melting without keyholing. Met3dp invests heavily in developing robust parameters for its materials and SEBM systems.
- High-Quality Powder: Using highly spherical powder with low internal gas content and controlled PSD, like those produced by Met3dp using GA and PREP, is fundamental. Good powder flowability ensures uniform layer deposition.
- Inert Atmosphere Control: Maintaining a high-purity inert gas atmosphere (Argon or Nitrogen for L-PBF) or vacuum (SEBM) minimizes contamination and reactions that could introduce porosity.
- 열간 등방성 프레싱(HIP): A post-processing step involving high temperature and high pressure in an inert atmosphere. HIP can effectively close internal pores (except those open to the surface), achieving near 100% density. However, it adds significant cost and lead time and can affect dimensions, so it’s typically reserved for the most critical applications where internal porosity tolerance is near zero. Often, well-controlled AM processes can achieve sufficient density without HIP.
Challenges in Removing Internal Supports from Complex Geometries
As highlighted in the DfAM and post-processing sections, removing support structures from intricate internal channels or cavities within a connector housing is a major challenge.
완화 전략:
- DfAM is Paramount: The best solution is to design the need for internal supports out wherever possible, using self-supporting channel geometries (e.g., teardrop, diamond shapes).
- Provide Access: If internal supports are unavoidable, design adequate access ports for tools or flushing.
- Specialized Support Structures: Using easily crushable or soluble support materials (less common in direct metal printing but researched) or optimized lattice supports can help.
- Advanced Removal Techniques: Abrasive flow machining or chemical etching might be considered in specific cases, but these are complex, costly, and require careful validation to ensure they don’t damage the part or alter critical dimensions. Often, designs requiring extensive, inaccessible internal supports are deemed unsuitable for current AM technology.
Material Contamination and Powder Handling Protocols
Metal powders, especially reactive ones like Ti-6Al-4V, are sensitive to contamination from oxygen, nitrogen, moisture, and cross-contamination from other metal powders. Contamination severely degrades mechanical properties.
완화 전략:
- Strict Powder Handling: Using controlled environments (glove boxes, sealed containers), inert gas purging, and dedicated equipment (sieves, hoppers, build modules) for each material type prevents cross-contamination and exposure to atmosphere.
- 파우더 수명 주기 관리: Tracking powder usage, recycling (sieving to remove oversized particles or spatters), and regular testing of recycled powder chemistry are essential to maintain material integrity. Met3dp adheres to rigorous powder handling and quality control protocols.
- Inert Gas Quality: Ensuring the purity of the argon or nitrogen used in the build chamber (for L-PBF) is critical.
Ensuring Consistency Across Production Batches
Achieving the same high quality for every part, whether printing one or one hundred connector housings, is essential for aerospace. Aerospace manufacturing challenges often revolve around repeatability.
완화 전략:
- Robust Quality Management System (QMS): Implementing a certified QMS (like AS9100) provides the framework for process control, documentation, traceability, and continuous improvement.
- Machine Calibration and Maintenance: Regular preventative maintenance and calibration ensure the AM system performs consistently.
- 프로세스 모니터링: In-situ monitoring tools (e.g., melt pool monitoring, thermal imaging) can provide real-time data on build stability, potentially detecting defects as they form (though this technology is still evolving for definitive quality assessment).
- Consistent Feedstock: Using powder from a trusted supplier like Met3dp, with certified batch-to-batch consistency, is fundamental.
- Standardized Procedures: Documented and strictly followed procedures for build setup, operation, powder handling, and post-processing minimize human error and variability.
- Statistical Process Control (SPC): Analyzing process data and part measurements over time helps identify trends and maintain process stability.
By understanding these potential challenges and partnering with a knowledgeable supplier like Met3dp that employs advanced technology (SEBM), high-quality materials, rigorous process controls, and comprehensive DfAM support, aerospace engineers and procurement managers can confidently leverage metal AM to produce reliable, high-performance custom connector housings.
Supplier Selection: How to Choose the Right Metal 3D Printing Service Provider for Aerospace Components
The decision to adopt metal additive manufacturing for critical components like aerospace connector housings is significant. However, realizing the full potential of this technology – achieving flight-worthy parts that meet stringent performance, quality, and reliability standards – hinges critically on selecting the right manufacturing partner. Not all 금속 3D 프린팅 서비스 제공업체 are created equal, especially when catering to the demanding aerospace sector. Engineers and procurement managers must conduct thorough due diligence, evaluating potential suppliers against a rigorous set of criteria to ensure they possess the necessary expertise, technology, and quality controls. Partnering with a capable and certified supplier is paramount for mitigating risks and ensuring project success.
Assessing Technical Capabilities: Equipment, Materials, Expertise
The foundation of any capable AM supplier lies in their technical prowess. Key areas to evaluate include:
- Equipment Portfolio:
- Technology Match: Do they operate the appropriate PBF technology (SLM, DMLS, SEBM) best suited for your housing’s material (316L, Ti-6Al-4V) and complexity? For instance, SEBM technology, offered by Met3dp, excels with Ti-6Al-4V due to its lower residual stress and ability to handle reactive materials in vacuum.
- Machine Quality & Features: Are their machines industrial-grade, well-maintained, and equipped with necessary process monitoring or control features?
- 볼륨을 구축합니다: Can their machines accommodate the size of your connector housing design?
- Resolution & Accuracy: What are the stated accuracy and minimum feature size capabilities of their systems?
- 재료 전문성:
- Qualified Materials: Do they have proven experience and validated process parameters specifically for aerospace-grade 316L and Ti-6Al-4V? Can they provide material datasheets based on printed properties?
- Broader Portfolio: Do they offer other relevant aerospace alloys (e.g., aluminum alloys, Inconel) should your needs evolve?
- Powder Sourcing & Quality: Where do they source their powders? Do they have stringent incoming quality checks? A supplier like Met3dp, which manufactures its own high-quality powders using advanced GA and PREP methods, offers a significant advantage in controlling this critical input variable.
- 프로세스 전문성:
- Parameter Development: Do they possess the expertise to optimize printing parameters for specific geometries and performance requirements, or do they rely solely on standard machine manufacturer settings?
- Metallurgical Understanding: Does their team include materials scientists or metallurgists who understand the nuances of alloy behavior during AM and subsequent heat treatment?
Quality Management Systems and Certifications (e.g., AS9100)
For the aerospace industry, quality isn’t just desirable; it’s mandatory. A supplier’s commitment to quality is best demonstrated through its QMS and relevant certifications:
- AS9100 Certification: This is the internationally recognized QMS standard specifically for the Aviation, Space, and Defense industries. It incorporates ISO 9001 requirements but adds stringent controls for safety, reliability, airworthiness, traceability, configuration management, and risk management. AS9100 certified additive manufacturing providers demonstrate a commitment to meeting the highest industry standards. This should be considered a primary requirement when selecting a supplier for flight components.
- ISO 9001 Certification: A foundational QMS standard, indicating documented processes for quality control, consistency, and continuous improvement. It’s a good baseline but often insufficient on its own for aerospace prime contractors.
- Nadcap Accreditation: While AS9100 covers the overall system, Nadcap provides specific accreditation for “special processes” like heat treatment, non-destructive testing (NDT), welding, and coatings. If your supplier performs these critical steps in-house or outsources them, verifying their or their partner’s Nadcap accreditation adds another layer of assurance.
Demand evidence of these certifications and understand the scope of their QMS implementation.
Material Traceability and Process Control Standards
Aerospace components require meticulous traceability – the ability to track a part’s history from raw material batch through every manufacturing and inspection step.
- Powder Batch Traceability: The supplier must demonstrate clear tracking of which specific powder batch (with its associated chemistry and PSD certifications) was used for each build job. This is vital for investigation should any issues arise later. Suppliers like Met3dp, controlling powder production, inherently offer robust traceability.
- Process Parameter Logging: Industrial AM systems log critical process parameters during the build (e.g., beam power, chamber oxygen levels, temperature). The supplier should maintain these records as part of the build documentation.
- Configuration Management: Strict controls must be in place to ensure the correct design revision (CAD file, drawing) is used for manufacturing.
- Documentation: Comprehensive documentation packages, including material certs, build logs, post-processing records (heat treat charts), inspection reports (CMM, NDT), and certificates of conformance, are standard deliverables for aerospace parts.
Verify the supplier’s procedures for maintaining this level of traceability and control.
Evaluating Engineering Support and DfAM Expertise
As detailed earlier, DfAM is critical for optimizing connector housings for additive manufacturing. A valuable supplier acts as a partner, offering engineering support:
- DfAM Consultation: Can their engineers review your design and provide constructive feedback on optimizing geometry, minimizing supports, ensuring powder removal, and selecting the best orientation?
- Simulation Capabilities: Do they offer process simulation to predict warping or stress, or topology optimization services to help achieve lightweighting goals?
- 문제 해결: Do they have the expertise to troubleshoot potential build issues related to complex geometries or specific performance requirements?
This collaborative approach ensures the design is manufacturable efficiently and effectively.
Capacity, Lead Times, and Scalability for Production Volumes
Consider both your immediate prototyping needs and potential future production requirements:
- Machine Capacity: Do they have sufficient machine availability to meet your required lead times for prototypes and potential follow-on orders? What is their typical backlog?
- 확장성: If your project moves from prototype to low- or mid-volume production, does the supplier have the capacity (multiple machines, efficient workflow, robust post-processing) to scale up production accordingly?
- Lead Time Transparency: Do they provide realistic and reliable lead time estimates based on current capacity and the complexity of your part and its post-processing requirements?
Understanding the Value Proposition: Why Partner with Met3dp?
Choosing a supplier isn’t just about ticking boxes; it’s about finding a partner committed to your success. Met3dp offers a compelling value proposition for aerospace clients seeking custom connector housings:
- Integrated Solution: As both a manufacturer of high-quality, aerospace-grade metal powders (316L, Ti-6Al-4V, custom alloys) using advanced GA and PREP technologies, and a provider of advanced SEBM printing services, Met3dp offers unparalleled control over the entire AM process chain, ensuring material quality and process synergy.
- Technology Advantage: Our expertise in SEBM provides distinct advantages for materials like Ti-6Al-4V, delivering parts with low residual stress and excellent material properties, often reducing post-processing needs.
- 전문성: Our team comprises specialists with decades of collective experience in metal AM, materials science, and aerospace applications, providing expert DfAM and application development support.
- Quality Focus: We operate under rigorous quality control protocols, ensuring material traceability and consistent part quality suitable for demanding industries. (Learn more 회사 소개).
- Customer Collaboration: We partner closely with clients to understand their unique challenges and deliver tailored solutions that leverage the full potential of additive manufacturing.
Finding Reliable B2B Metal AM Suppliers and Manufacturers
Beyond direct search, consider industry directories, trade shows (like Formnext), and recommendations from trusted sources. When engaging potential B2B metal printing partners, prepare a detailed Request for Quote (RFQ) package including CAD models, drawings specifying critical dimensions and tolerances, material specifications, required certifications, quantities, and desired lead times. This allows for accurate quotes and meaningful comparisons between potential suppliers.
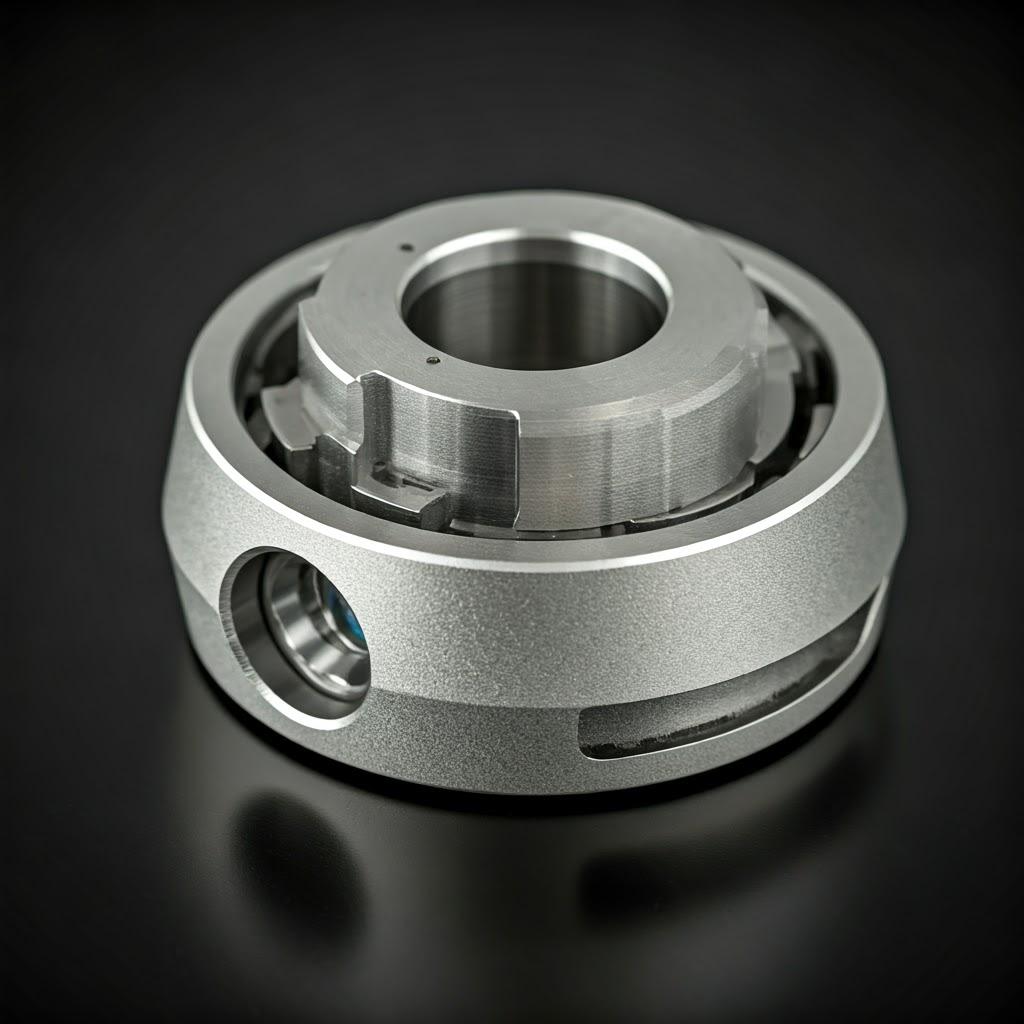
Understanding the Investment: Key Cost Factors and Lead Time Expectations for 3D Printed Connector Housings
One of the primary considerations for adopting any manufacturing technology is its cost-effectiveness and the time required to receive parts. While metal AM offers compelling advantages for custom aerospace connector housings, it’s essential to understand the factors that drive metal 3D printing cost and influence aerospace component lead times. This knowledge helps engineers justify the technology choice and allows procurement managers to budget and plan effectively. Obtaining detailed quotes from potential metal 3D printing distributors or service bureaus is crucial, but understanding the underlying cost structure provides valuable context.
Material Costs: Powder Price and Consumption
Material is a significant cost component, especially for expensive aerospace alloys:
- 파우더 가격: There’s a substantial difference in cost per kilogram between common alloys.
- 316L 스테인리스 스틸: Relatively economical.
- Ti-6Al-4V Titanium Alloy: Significantly more expensive (often 5-10 times the price of 316L or more) due to raw material costs and complex powder production processes.
- Other Alloys: Nickel superalloys (Inconel) are also premium-priced. Aluminum alloys are generally less expensive than stainless steel.
- Material Consumed: The cost isn’t just the powder in the final part; it includes:
- Part Volume: The actual volume of the connector housing.
- 지원 구조: The volume of powder used for sacrificial supports. Efficient DfAM minimizes this.
- Process Losses: Some powder is inevitably lost during handling, sieving, and printing (though efficient suppliers minimize waste through recycling).
- Build Density: Densely packed builds (multiple parts printed simultaneously) utilize powder more efficiently than printing single parts in a large build volume.
Takeaway: Material choice (especially Ti-6Al-4V vs. 316L) is a major cost driver. Designs optimized for minimum volume and support structures (DfAM) directly reduce material costs.
Build Time: Machine Hours and Complexity
The time the AM machine spends printing the part is another major cost factor, typically billed at an hourly rate that covers machine depreciation, maintenance, energy, inert gas/vacuum, and facility overheads.
- 파트 볼륨 및 높이: Larger volume parts naturally take longer to print. Build time is often strongly correlated with the part’s height (Z-dimension) as each layer takes a certain amount of time to deposit and fuse.
- Number of Parts per Build: Printing multiple parts simultaneously (nesting) distributes the machine setup and cooldown time across more items, reducing the cost per part.
- Complexity & Scan Strategy: Very intricate geometries or requirements for specific scan strategies (e.g., for fine features or stress reduction) can influence the overall time per layer.
- 기계 기술: Different AM technologies and specific machine models have varying build rates. SEBM can sometimes offer faster volume build rates than L-PBF for certain materials/geometries due to faster beam scanning capabilities.
Takeaway: Optimize designs for minimum height where possible (balancing against support needs) and leverage build plate nesting for multiple parts to reduce machine time cost per part.
Labor Costs: Design Optimization, Setup, Post-Processing
Human effort is involved throughout the AM workflow:
- Engineering/DfAM Support: Time spent by engineers optimizing the design, simulating the process, and preparing the build file.
- Machine Setup & Operation: Labor for loading powder, setting up the build job, monitoring the print, and unloading the finished build.
- 파우더 처리 및 재활용: Time spent sieving, handling, and managing powder inventory safely and efficiently.
- Part & Support Removal: Significant labor can be involved in carefully removing parts from the build plate and meticulously removing support structures, especially complex or internal ones. This is often a major bottleneck and cost driver in post-processing.
- Finishing & Inspection: Manual labor for surface finishing (polishing, deburring), cleaning, visual inspection, and metrology.
Takeaway: Designs that minimize support structures and manual finishing requirements directly reduce labor costs. Automation in post-processing (where applicable) can help, but many steps remain labor-intensive.
Post-Processing Requirements and Complexity
As detailed previously, post-processing steps add significant cost and time:
- 열처리: Furnace time, energy consumption, inert gas/vacuum costs. Complex cycles (like STA for Ti-6Al-4V) take longer and cost more than simple stress relief.
- 가공: CNC machine time (milling, turning, EDM), tooling costs, programming time. The number and complexity of machined features directly impact cost.
- 표면 마감: Costs associated with blasting media, tumbling equipment operation, polishing consumables and labor, or specialized processes like electropolishing.
- Coatings/Platings: Costs charged by specialized plating shops, dependent on the coating material, thickness, and masking requirements.
Takeaway: Clearly specify only necessary post-processing. Over-tolerancing or requesting unnecessarily fine finishes dramatically increases cost. DfAM should aim to minimize reliance on extensive post-processing where possible.
Quality Control and Inspection Costs
The level of required inspection significantly impacts cost:
- Standard Inspection: Visual checks, basic dimensional measurements.
- Advanced Metrology: CMM programming and measurement time, 3D scanning and analysis time.
- 비파괴 검사(NDT): Costs for CT scanning, radiographic testing, or penetrant testing if required for internal defect detection or crack checking – CT scanning, in particular, can be expensive.
- Documentation: Time spent compiling comprehensive quality documentation packages.
Takeaway: Define the appropriate level of inspection based on criticality. Requiring extensive NDT for non-critical components adds unnecessary cost.
Factors Influencing Lead Times
Lead time – the total time from order placement to receiving finished parts – is influenced by many of the same factors as cost:
- Design & Preparation: Time for DfAM review, simulation (if needed), and build file preparation (typically 1-3 days).
- 인쇄 시간: Highly variable based on part size, complexity, and quantity (can range from hours for small parts to many days for large, complex builds or large batches).
- Machine Queue: Supplier’s current workload and machine availability significantly impact when a build can start. Booking capacity in advance for production runs is advisable.
- 후처리 시간: This often constitutes a large portion of the total lead time.
- Heat treatment: Typically 1-3 days (including furnace cycles and cooling).
- Support/Part Removal: Can range from hours to days depending on complexity.
- Machining: Highly variable based on features (can be days or weeks for complex parts).
- Finishing/Coating: Adds days or weeks, depending on the process and supplier lead times.
- Inspection & Shipping: Final QC checks and transit time.
Realistic Expectations:
- 프로토타입: For relatively simple connector housings requiring standard post-processing, lead times of 1 to 3 weeks are often achievable.
- Production Runs: For larger quantities or parts needing extensive post-processing and rigorous QA, lead times can extend from several weeks to several months.
Takeaway: Engage with suppliers early, provide complete RFQ information, and discuss lead time expectations upfront. Well-planned DfAM and clearly defined requirements can help streamline the process. Contact Met3dp to discuss your specific project timelines and get a detailed quote.
Elevating Aerospace Systems: The Enduring Value of Custom Metal 3D Printed Connector Housings
Throughout this exploration, we’ve delved into the critical role of connector housings in aerospace, the unique challenges they face, and how metal additive manufacturing, particularly using robust materials like 316L stainless steel and high-performance Ti-6Al-4V titanium alloy, offers a transformative approach to their production. The advantages offered by metal AM are not merely incremental improvements; they represent a fundamental shift towards greater design freedom, optimized performance, and increased manufacturing agility, ultimately contributing to safer, more efficient, and more capable aerospace systems.
Recap: Key Advantages for Aerospace Applications
Metal 3D printing brings a powerful combination of benefits directly applicable to the demands of aerospace connector housings:
- 독보적인 디자인 자유도: Enabling complex geometries, internal features (cooling, shielding), and topology optimization for lightweighting that are impossible or impractical with traditional methods.
- Rapid Customization & Prototyping: Accelerating development cycles by allowing swift iteration and production of bespoke housing designs tailored to specific space, weight, or functional constraints.
- 무게 감소: Significantly reducing component weight through topology optimization and the efficient use of high strength-to-weight materials like Ti-6Al-4V, contributing to fuel savings and increased payload capacity.
- 파트 통합: Reducing assembly complexity, potential failure points, and logistical overhead by integrating multiple functions into a single printed part.
- 성능 향상: Allowing the use of optimal materials like Ti-6Al-4V for high-strength, high-temperature, or corrosive environments, and enabling designs with integrated thermal management or enhanced EMI shielding.
- Efficient Low-Volume Production: Providing a cost-effective method for producing the customized, low-to-medium volume batches often required in aerospace projects, avoiding high tooling costs.
Future Trends: Advancements in Materials and Processes
The field of metal additive manufacturing is continuously evolving, promising even greater capabilities for aerospace components in the future:
- 새로운 재료: Development of novel alloys specifically designed for AM, offering enhanced properties (higher temperature resistance, greater strength, improved printability). Research into printing ceramics or metal matrix composites for specialized housing applications.
- Faster Printing Processes: Innovations aimed at increasing build speeds without compromising quality, further improving economic viability for larger production volumes.
- Improved In-Situ Monitoring & Control: More sophisticated real-time monitoring of the melt pool and build process, coupled with AI-driven feedback loops to automatically adjust parameters, leading to enhanced quality assurance and reduced post-build inspection needs.
- 자동화 향상: Greater automation in post-processing steps like powder removal and support removal to reduce labor costs and lead times.
- 하이브리드 제조: Tighter integration of additive and subtractive processes within single machine platforms for increased efficiency.
The Role of Metal AM in Sustainable Aerospace Manufacturing
Additive manufacturing also aligns well with the growing emphasis on sustainability in the aerospace industry:
- 재료 낭비 감소: Compared to subtractive machining, AM generates significantly less material scrap, particularly beneficial when using expensive alloys like titanium. Powder recycling further improves material utilization.
- 경량화: Reduced component weight directly translates to lower fuel consumption during aircraft operation, reducing emissions.
- On-Demand Production & Distributed Manufacturing: Printing parts when and where they are needed reduces inventory holding and transportation emissions associated with complex global supply chains.
Final Thoughts: Embracing Additive Manufacturing for Competitive Advantage
Custom metal 3D printed connector housings are more than just components; they are enablers of innovation. By freeing designers from traditional constraints and allowing for optimized, integrated, and lightweight solutions, metal AM empowers aerospace companies to build next-generation aircraft, spacecraft, and defense systems. While challenges exist, partnering with knowledgeable and technologically advanced suppliers like Met3dp, who offer end-to-end solutions from high-quality powder production to advanced printing and engineering support, allows organizations to confidently harness the power of additive manufacturing. Embracing this technology is increasingly becoming not just an option, but a necessity for maintaining a competitive edge in the dynamic aerospace industry. Explore how Met3dp’s comprehensive 금속 3D 프린팅 솔루션 can elevate your next project.
Frequently Asked Questions (FAQ): Your Top Queries About 3D Printed Aerospace Connector Housings Answered
Q1: What are the typical tolerances achievable for 3D printed metal connector housings?
A1: As-built tolerances using Powder Bed Fusion (SLM, SEBM) are typically in the range of ±0.1mm to ±0.2mm for smaller features, or ±0.1% to ±0.2% for larger dimensions. However, critical interfaces, mating surfaces, or sealing grooves requiring tighter tolerances (e.g., ±0.01mm to ±0.05mm) usually need post-process CNC machining. DfAM involves designing these features with machining allowance.
Q2: How does the cost of 3D printing compare to CNC machining for custom connector housings?
A2: The cost comparison depends heavily on part complexity and volume.
- For highly complex geometries or low volumes (prototypes, 1-100 parts): Metal 3D printing is often more cost-effective because it avoids high tooling/fixture costs and extensive programming/setup time associated with machining complex shapes from billet.
- For simpler geometries or higher volumes: CNC machining may become more economical as the setup costs are amortized over more parts, and machining cycle times for simple shapes can be faster than AM build times. Material choice also plays a huge role; AM reduces waste for expensive materials like Ti-6Al-4V, potentially making it more competitive even if machining appears faster. A detailed quote comparison is always recommended.
Q3: What certifications should I look for in a metal AM supplier for aerospace parts?
A3: The most critical certification is AS9100, the Quality Management System standard specific to the Aviation, Space, and Defense industries. This demonstrates the supplier’s commitment to the rigorous quality, traceability, and risk management processes required for flight components. ISO 9001 is a good baseline but generally insufficient alone. Depending on the required post-processing, Nadcap accreditation for special processes like heat treatment or NDT is also highly valuable.
Q4: Can internal features like shielding or cooling channels be effectively printed?
A4: Yes, one of the key advantages of metal AM is the ability to create complex internal features. However, successful implementation requires careful Design for Additive Manufacturing (DfAM). Key considerations include:
- Powder Removal: Channels must be designed with sufficient diameter and accessible escape holes for complete removal of unfused powder.
- Self-Supporting Geometries: Internal channel roofs should ideally be designed with self-supporting angles (e.g., teardrop or diamond shapes) to avoid the need for internal supports, which are very difficult to remove.
- 표면 마감: Internal surfaces will have an as-built roughness unless specific secondary processes (like abrasive flow machining) are employed.
Q5: What is the typical lead time for receiving prototype or production aerospace connector housings?
A5: Lead times are highly variable. Factors include part complexity, size, quantity, material, machine availability, and the extent of required post-processing (heat treatment, machining, finishing, inspection).
- 프로토타입: Often range from 1 to 3 weeks.
- Production Runs: Can range from several weeks to several months, depending heavily on volume and complexity. Engaging with suppliers early and providing clear requirements allows for more accurate lead time estimates.
공유
중국 칭다오에 본사를 둔 선도적인 적층 제조 솔루션 제공업체인 MET3DP Technology Co. 당사는 산업용 3D 프린팅 장비와 고성능 금속 분말을 전문으로 합니다.
관련 기사
Met3DP 소개
최근 업데이트
제품
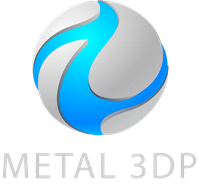
3D 프린팅 및 적층 제조용 금속 분말