Custom Fixtures for Aerospace Assembly
목차
Introduction to Custom Aerospace Assembly Fixtures via Metal 3D Printing
In the high-stakes world of aerospace manufacturing, precision and efficiency are not just goals; they are absolute necessities. Every component, every assembly, must adhere to stringent standards to ensure the safety and performance of aircraft. Traditional manufacturing methods for creating assembly fixtures often involve lengthy lead times, complex tooling, and limitations in design complexity. However, a transformative technology has emerged, offering a paradigm shift in how these critical tools are developed: metal 3D 프린팅, also known as metal additive manufacturing.
Custom aerospace assembly fixtures, fabricated using cutting-edge metal 3D printing techniques, are revolutionizing how aerospace engineers and procurement managers approach their manufacturing challenges. These fixtures are specifically designed to hold, support, and align aerospace components during various stages of assembly, ensuring accuracy and repeatability. By leveraging the power of additive manufacturing, it becomes possible to create intricate geometries tailored precisely to the unique contours of aircraft parts, optimizing the assembly process like never before.
에서 Metal3DP Technology Co., LTD, headquartered in Qingdao, China, we are at the forefront of this revolution. We specialize in providing advanced additive manufacturing solutions, including state-of-the-art 3D printing equipment and a comprehensive range of high-performance metal powders. Our commitment to industry-leading print volume, accuracy, and reliability makes us a trusted partner for mission-critical parts in aerospace, medical, automotive, and other demanding fields. Explore our metal 3D printing services to discover how we can support your aerospace manufacturing needs.
The Critical Role of Custom Fixtures in Aerospace Assembly Processes
The assembly of aerospace components is an intricate dance of precision and coordination. From the fuselage to the wings, from engine components to interior fittings, each step requires meticulous alignment and secure holding of parts. This is where custom assembly fixtures play an indispensable role. These purpose-built tools are the backbone of efficient and accurate aerospace manufacturing, ensuring that components are positioned correctly for fastening, welding, bonding, or other assembly operations.
Without custom fixtures, aerospace assembly would be plagued by inconsistencies, increased error rates, and significant delays. Imagine trying to align complex curved panels or hold intricate brackets in place without a precisely engineered tool designed for that specific task. The consequences could range from minor misalignments requiring rework to critical errors compromising the structural integrity of the aircraft.
Custom fixtures provide several key benefits in aerospace assembly:
- Enhanced Accuracy: They ensure that parts are located and oriented with the highest degree of precision, minimizing dimensional variations in the final assembly.
- Improved Repeatability: Once a fixture is designed and manufactured, it allows for consistent assembly of identical components, crucial for maintaining quality standards across production runs.
- Increased Efficiency: Fixtures streamline the assembly process by simplifying part handling and alignment, reducing the time and labor required for each operation.
- Reduced Errors and Rework: By providing stable and accurate positioning, fixtures minimize the chances of assembly errors, leading to less rework and lower manufacturing costs.
- Support for Complex Geometries: Aerospace components often feature intricate and unconventional shapes. Custom fixtures can be designed to accommodate these complexities, providing the necessary support and access for assembly.
Given these critical functions, the quality and design of assembly fixtures directly impact the overall efficiency, cost-effectiveness, and ultimately, the safety of aerospace manufacturing. Choosing the right manufacturing method for these fixtures is therefore a decision of paramount importance.
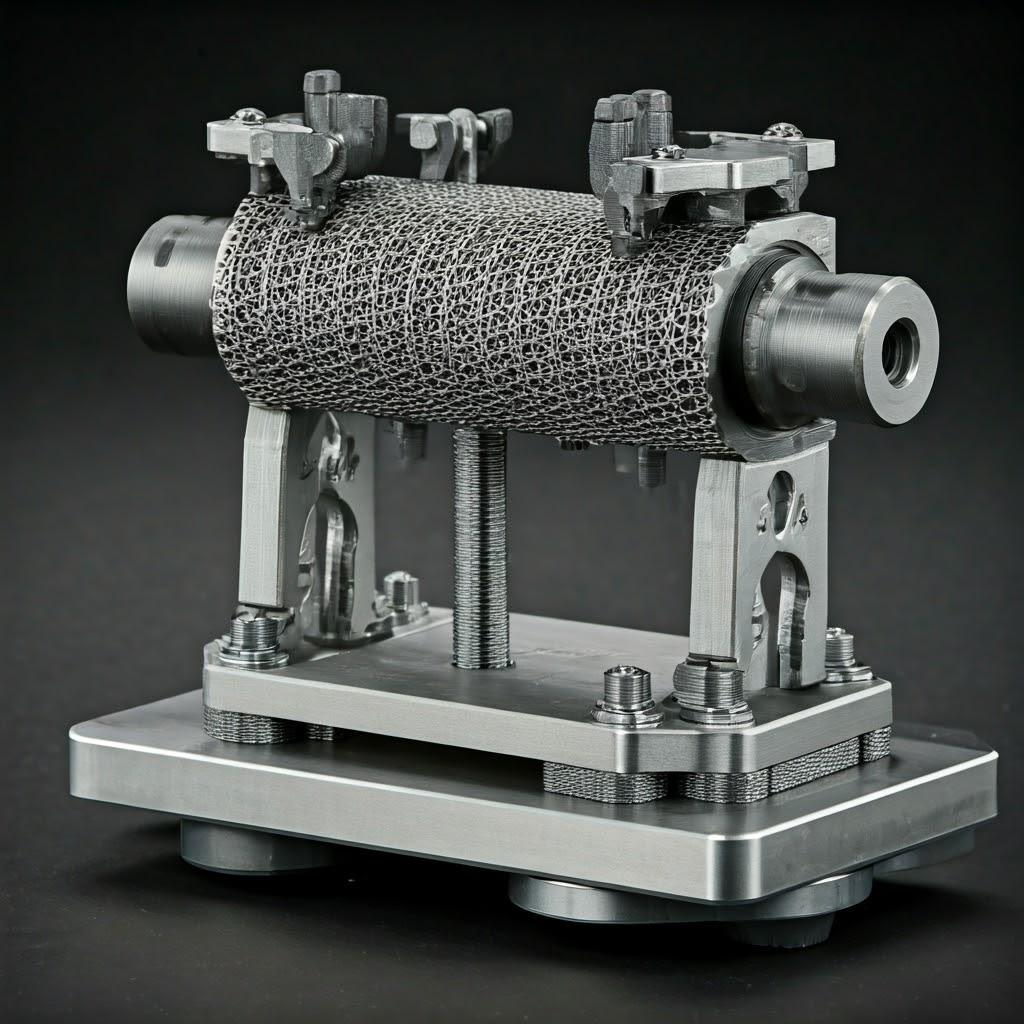
Advantages of Utilizing Metal 3D Printing for Aerospace Assembly Fixtures
While traditional manufacturing methods like CNC machining have long been the standard for producing assembly fixtures, metal 3D printing offers a compelling array of advantages that are particularly well-suited to the demanding requirements of the aerospace industry.
- 디자인의 자유와 복잡성: Metal 3D printing allows for the creation of highly complex geometries that would be difficult or impossible to achieve with traditional subtractive methods. This enables the design of fixtures that precisely match the contours of intricate aerospace parts, providing optimal support and alignment. Engineers can incorporate features like conformal cooling channels or integrated vacuum channels directly into the fixture design, enhancing functionality and efficiency.
- Rapid Prototyping and Reduced Lead Times: The aerospace industry often involves rapid design iterations and the need for quick turnaround on tooling. Metal 3D printing significantly reduces lead times for fixture production compared to traditional methods that may involve extensive machining and tooling processes. This agility allows for faster design validation and quicker implementation of new assembly processes.
- Material Efficiency and Waste Reduction: In subtractive manufacturing, a significant portion of the raw material is removed to create the final part. Metal 3D printing, on the other hand, builds parts layer by layer, using only the material needed for the design. This results in significantly less material waste, which is particularly important when working with expensive metals commonly used in aerospace.
- 사용자 지정 및 온디맨드 제조: Each aerospace assembly task may require unique fixturing solutions. Metal 3D printing excels at producing highly customized fixtures tailored to specific part geometries and assembly requirements. This on-demand manufacturing capability eliminates the need for large inventories of standard fixtures and allows for the creation of specialized tools as needed.
- 경량화 잠재력: Metal 3D printing allows for the creation of optimized internal lattice structures and thin-walled designs, reducing the overall weight of the fixture without compromising its strength and rigidity. This is particularly beneficial in aerospace manufacturing, where weight reduction is a critical factor in fuel efficiency and performance.
- Integration of Multiple Components: Complex assembly fixtures that would traditionally require multiple machined parts to be assembled can often be consolidated into a single 3D-printed component. This reduces assembly time, minimizes the number of fasteners required, and enhances the overall structural integrity of the fixture.
에서 Metal3DP, our industry-leading selective electron beam melting (SEBM) printers are ideally suited for producing complex and high-performance metal parts for aerospace applications. Coupled with our advanced powder making system, which ensures high sphericity and flowability of our metal powders, we empower our customers to achieve exceptional results in their additive manufacturing endeavors. Learn more about our printing methods and how they can benefit your aerospace fixture production.
Material Selection: Why 316L and Invar are Ideal for Aerospace Fixtures
The choice of material is paramount when designing and manufacturing assembly fixtures, especially in the demanding environment of aerospace manufacturing. The material must possess the necessary strength, stiffness, wear resistance, and dimensional stability to ensure accurate and reliable performance over extended use. Metal3DP offers a comprehensive portfolio of high-quality metal powders optimized for laser and electron beam powder bed fusion, including two materials particularly well-suited for custom aerospace assembly fixtures: 316L stainless steel and Invar.
316L 스테인리스 스틸:
- 뛰어난 내식성: Aerospace environments can be harsh, with exposure to various fluids and atmospheric conditions. 316L stainless steel exhibits exceptional resistance to corrosion and oxidation, ensuring the longevity and reliability of the fixture.
- 높은 강도와 연성: This austenitic stainless steel offers a good balance of high tensile strength and ductility, making it capable of withstanding the stresses encountered during assembly operations without fracturing.
- Good Weldability and Machinability: While 3D printing eliminates the need for extensive welding, the inherent weldability of 316L is a testament to its robust metallurgical properties. Its good machinability also allows for post-processing if required to achieve very tight tolerances or specific surface finishes.
- 비용 효율적: Compared to some other high-performance alloys, 316L offers a cost-effective solution for many aerospace fixturing applications without sacrificing essential performance characteristics.
Invar (FeNi36):
- Ultra-Low Coefficient of Thermal Expansion (CTE): This nickel-iron alloy is renowned for its extremely low coefficient of thermal expansion over a wide temperature range. This is a critical property for aerospace assembly fixtures, as temperature fluctuations during manufacturing or operational environments can cause dimensional changes in the fixture, leading to inaccuracies. Invar’s stability ensures consistent and precise part positioning regardless of temperature variations.
- Good Strength and Toughness: While its strength may not be as high as some stainless steels, Invar still offers sufficient strength and toughness for many fixturing applications, particularly where dimensional stability is the primary concern.
- Suitability for Precision Applications: The exceptional dimensional stability of Invar makes it ideal for critical aerospace assembly fixtures where even minute thermal expansion could lead to unacceptable variations in the final product.
Metal3DP utilizes industry-leading gas atomization and plasma rotating electrode process (PREP) technologies to manufacture our high-quality metal powders. This ensures that powders like 316L and Invar possess high sphericity and excellent flowability, which are crucial for achieving dense, high-quality 3D-printed parts with superior mechanical properties. Our advanced powder making system allows us to tailor the powder characteristics to the specific requirements of additive manufacturing processes, ensuring optimal results for your custom aerospace assembly fixtures. You can explore our range of high-quality metal powders to find the perfect material for your application. Sources and related content
Design Optimization for 3D Printed Aerospace Assembly Fixtures
The transition from traditional manufacturing to metal 3D printing opens up exciting possibilities for optimizing the design of aerospace assembly fixtures. Unlike subtractive methods, additive manufacturing imposes fewer constraints on geometry, allowing engineers to create innovative and highly functional fixture designs. However, to fully leverage the benefits of 3D printing, it’s crucial to consider specific design principles tailored to this technology.
- 토폴로지 최적화: This computational technique can be used to identify and remove material in areas of the fixture that are not structurally critical, resulting in lightweight yet strong designs. For aerospace, where weight reduction is paramount, topology optimization can lead to significant benefits.
- 격자 구조: Instead of solid infill, 3D printing allows for the creation of intricate internal lattice structures. These structures can provide excellent strength-to-weight ratios and can be customized to meet specific stiffness requirements in different areas of the fixture.
- Conformal Features: Metal 3D printing enables the integration of conformal features such as cooling channels or vacuum pathways directly into the fixture design. For example, conformal cooling channels can help dissipate heat generated during assembly processes, while integrated vacuum channels can provide secure part holding without the need for additional clamping mechanisms.
- 파트 통합: Complex assembly fixtures that traditionally require multiple components can often be designed as a single 3D-printed part. This reduces assembly time, minimizes the number of fasteners, and improves overall structural integrity.
- Ergonomics and Accessibility: When designing fixtures, it’s essential to consider the human factor. 3D printing allows for the creation of fixtures with improved ergonomics, making them easier and safer for assembly technicians to use. Features like integrated handles or clear access points can be incorporated directly into the design.
- Modularity and Reconfigurability: For aerospace applications with evolving product designs, 3D printing can facilitate the creation of modular or reconfigurable fixtures. This can involve designing fixtures with interchangeable components or features that can be easily adapted to accommodate design changes, reducing the need for entirely new fixtures.
By embracing these design considerations, aerospace manufacturers can create 3D-printed assembly fixtures that are not only precisely tailored to their specific needs but also lighter, more functional, and more efficient than those produced using traditional methods. Metal3DP‘s expertise in application development services can help your organization explore these design possibilities and optimize your fixtures for metal additive manufacturing.
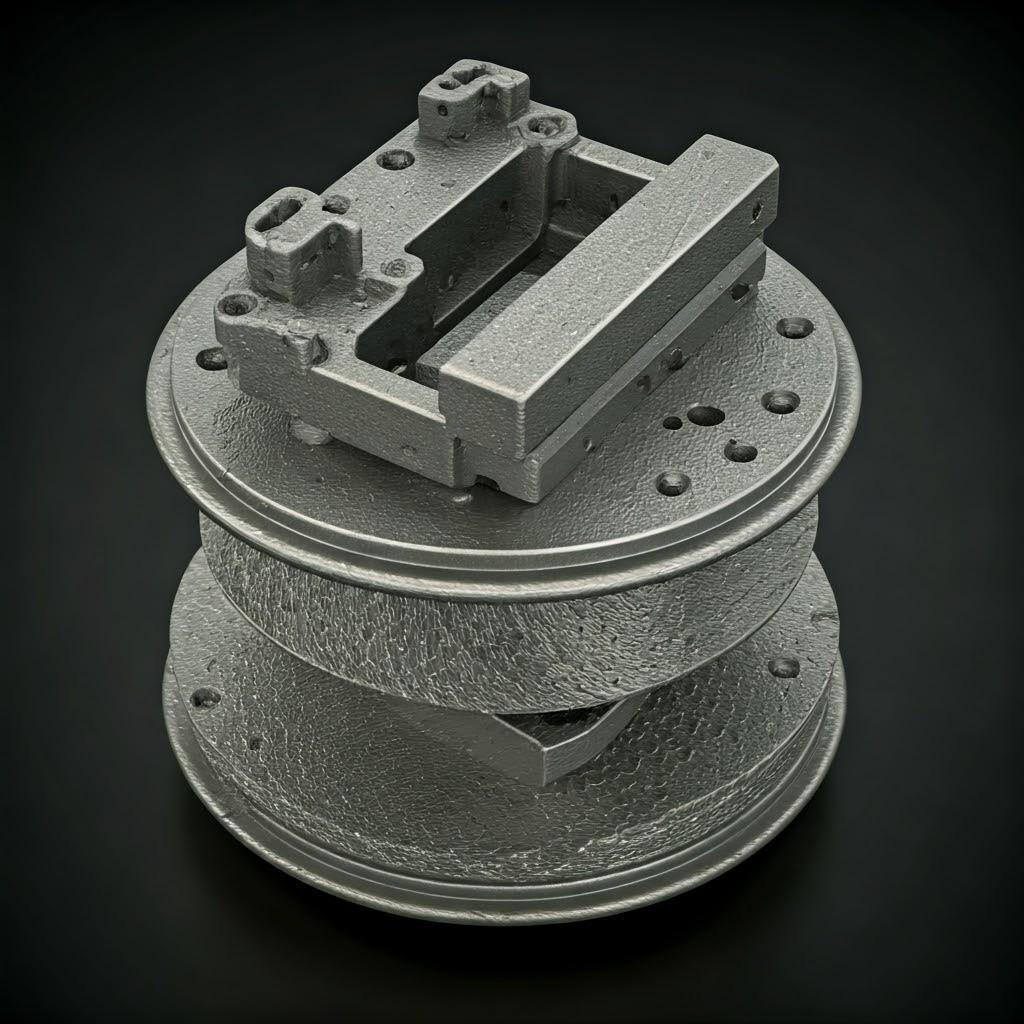
Achieving Precision: Tolerance, Surface Finish, and Dimensional Accuracy in 3D Printed Fixtures
In the aerospace industry, even the slightest deviation from specified dimensions can have significant consequences. Therefore, the tolerance, surface finish, and dimensional accuracy of assembly fixtures are critical factors. Metal 3D printing technologies, particularly Selective Electron Beam Melting (SEBM) as offered by Metal3DP, are capable of achieving impressive levels of precision.
- Tolerance Capabilities: The achievable tolerance in metal 3D printing depends on several factors, including the printing technology, material, part geometry, and post-processing. With optimized design and careful process control, SEBM can achieve tolerances in the range of ±0.1 to ±0.2 mm for critical dimensions. For tighter tolerances, post-machining operations can be employed.
- 표면 마감: The as-printed surface finish in metal 3D printing is typically rougher than that achieved by machining. However, for many assembly fixturing applications, a smooth surface finish may not be a primary requirement. If necessary, various post-processing techniques such as polishing, sanding, or media blasting can be used to improve the surface finish.
- 치수 정확도: Dimensional accuracy refers to the ability of the 3D-printed part to match the intended design dimensions. SEBM technology, known for its high energy input and stable build environment, contributes to excellent dimensional accuracy in the final parts. Factors influencing accuracy include material shrinkage during solidification and potential thermal distortion. Careful process parameter optimization and support structure design are crucial for minimizing these effects.
Metal3DP‘s SEBM printers are engineered to deliver industry-leading accuracy and reliability. Our comprehensive understanding of material behavior and process parameters allows us to produce metal 3D-printed parts, including assembly fixtures, with consistent and high dimensional accuracy. We work closely with our customers to understand their specific precision requirements and tailor our processes to meet those needs.
Streamlining Post-Processing for Aerospace Assembly Fixtures
While metal 3D printing offers significant advantages in terms of design freedom and reduced lead times, post-processing is often a necessary step to achieve the final desired properties and finish for aerospace assembly fixtures. Streamlining these post-processing steps is crucial for maximizing efficiency and minimizing overall production time.
- 지원 구조 제거: Metal 3D printing typically requires the use of support structures to anchor the part to the build plate and prevent distortion during the printing process. Removing these supports is usually the first post-processing step. For SEBM, the partially sintered powder surrounding the supports often allows for relatively easy removal.
- 열처리: Depending on the material and application requirements, heat treatment may be necessary to relieve internal stresses, improve mechanical properties (such as hardness and strength), or achieve the desired microstructure. For aerospace-grade materials like 316L and Invar, specific heat treatment cycles are often required.
- 표면 마감: As mentioned earlier, if a smoother surface finish is required, various techniques can be employed. These include abrasive methods like grinding and polishing, as well as non-abrasive methods like chemical etching or electropolishing. The choice of method depends on the desired surface roughness and the complexity of the fixture geometry.
- CNC 가공: For applications requiring very tight tolerances on specific features, CNC machining can be used as a secondary process after 3D printing. This allows for the creation of highly precise mating surfaces or critical dimensions.
- Inspection and Quality Control: Thorough inspection is essential to ensure that the 3D-printed fixture meets the required dimensional accuracy and quality standards. Techniques such as coordinate measuring machines (CMMs) and non-destructive testing (NDT) methods may be used.
Metal3DP understands the importance of efficient post-processing. We can provide guidance and support in selecting the appropriate post-processing techniques for your specific aerospace assembly fixture requirements. Our expertise in material science and additive manufacturing processes ensures that the chosen post-processing steps are optimized to achieve the desired outcome without compromising the integrity or performance of the fixture.
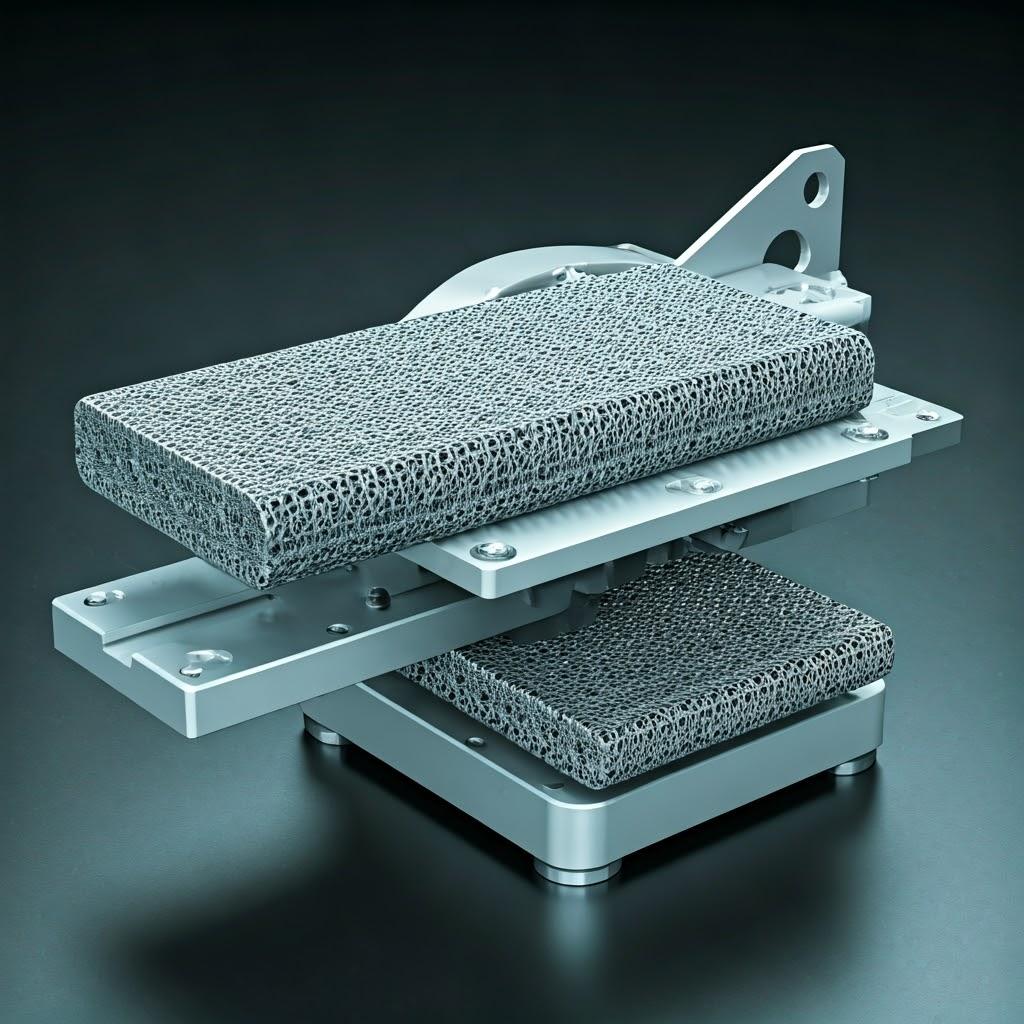
Overcoming Common Challenges in 3D Printing Aerospace Fixtures
While metal 3D printing offers numerous benefits, there are also potential challenges that need to be addressed to ensure successful production of aerospace assembly fixtures.
- Warping and Distortion: Thermal stresses during the printing process can sometimes lead to warping or distortion of the part, especially for large or complex geometries. Careful design optimization, including the orientation of the part on the build plate and the design of support structures, can help mitigate these issues. Metal3DP‘s expertise in process parameter optimization is crucial in minimizing warping and ensuring dimensional accuracy.
- 다공성: The presence of internal voids or porosity can compromise the mechanical properties of the 3D-printed part. Optimizing printing parameters, such as laser power or electron beam current, scan speed, and powder bed density, is essential to minimize porosity and achieve dense, high-quality parts. Our advanced powder making system, producing high-sphericity and flowability powders, also contributes to reduced porosity.
- Support Removal Difficulties: In some cases, removing support structures can be challenging, especially for intricate geometries or delicate features. Designing self-supporting geometries where possible and optimizing support structure design for ease of removal are important considerations.
- Material Property Consistency: Ensuring consistent material properties throughout the 3D-printed part is crucial for aerospace applications. Factors such as uniform powder bed packing, consistent energy input, and controlled cooling rates play a significant role. Metal3DP‘s rigorous quality control measures and advanced printing technology help ensure the consistency and reliability of the material properties in our 3D-printed parts.
- Scalability and Cost: For high-volume production, the scalability and cost-effectiveness of metal 3D printing need to be carefully evaluated. While 3D printing excels at producing complex, customized parts in lower volumes, optimizing the design for manufacturability and leveraging efficient printing strategies can improve scalability and reduce costs.
By understanding these potential challenges and implementing appropriate design and process optimization strategies, aerospace manufacturers can effectively leverage metal 3D printing to create high-performance assembly fixtures. Metal3DP is committed to providing our customers with the expertise and support needed to overcome these challenges and achieve successful outcomes in their metal additive manufacturing endeavors. We encourage you to contact us to explore how our capabilities can power your organization’s additive manufacturing goals.
Selecting a Reliable Metal 3D Printing Service Provider for Aerospace Applications
Choosing the right metal 3D printing service provider is a critical decision for aerospace companies looking to leverage this advanced technology for their assembly fixtures. The quality, reliability, and expertise of the service provider will directly impact the success of your project. Here are key factors to consider when evaluating potential partners:
- Industry Experience and Certifications: Look for a provider with a proven track record in serving the aerospace industry. Do they have experience working with aerospace-grade materials and adhering to stringent quality standards? Relevant certifications, such as AS9100 for aerospace quality management systems, are strong indicators of their commitment to quality and reliability. Metal3DP is dedicated to providing high-quality solutions for mission-critical parts in aerospace and other demanding fields.
- Material Capabilities: Ensure the provider offers the specific metal powders required for your application, such as 316L and Invar. They should have expertise in processing these materials to achieve the desired mechanical properties and dimensional accuracy. Metal3DP manufactures a wide range of high-quality metal powders optimized for laser and electron beam powder bed fusion, including innovative alloys relevant to aerospace.
- Printing Technology and Equipment: Understand the types of metal 3D printing technologies the provider utilizes. Selective Electron Beam Melting (SEBM), as employed by Metal3DP, offers unique advantages for certain aerospace applications, such as high density and minimal residual stress. The provider should have well-maintained and calibrated equipment to ensure consistent and accurate results. Our printers deliver industry-leading print volume, accuracy, and reliability.
- Design and Engineering Support: A reliable provider should offer comprehensive design and engineering support to help optimize your fixtures for 3D printing. This includes guidance on material selection, design for additive manufacturing (DfAM) principles, and potential design improvements to enhance functionality and manufacturability. Metal3DP provides comprehensive solutions spanning SEBM printers, advanced metal powders, and application development services. 1 1. met3dp.sg met3dp.sg
- Post-Processing Capabilities: Inquire about the provider’s in-house or partnered post-processing capabilities, such as heat treatment, surface finishing, and CNC machining. These services are often necessary to achieve the final desired properties and tolerances for aerospace fixtures.
- Quality Control and Inspection Processes: A robust quality management system and thorough inspection processes are essential to ensure that the 3D-printed fixtures meet the required specifications. Ask about their inspection methods, including dimensional measurement and material testing.
- Lead Times and Scalability: Discuss the provider’s typical lead times for similar projects and their capacity for handling your production volumes, both for prototypes and potential future scaling.
- Communication and Customer Support: Effective communication and responsive customer support are crucial for a smooth and successful partnership. Choose a provider that is proactive, transparent, and readily available to address your questions and concerns.
By carefully evaluating these factors, you can select a metal 3D printing service provider that aligns with your aerospace manufacturing needs and helps you realize the full potential of this transformative technology. We encourage you to learn more about Metal3DP and how our expertise can support your organization’s additive manufacturing goals.
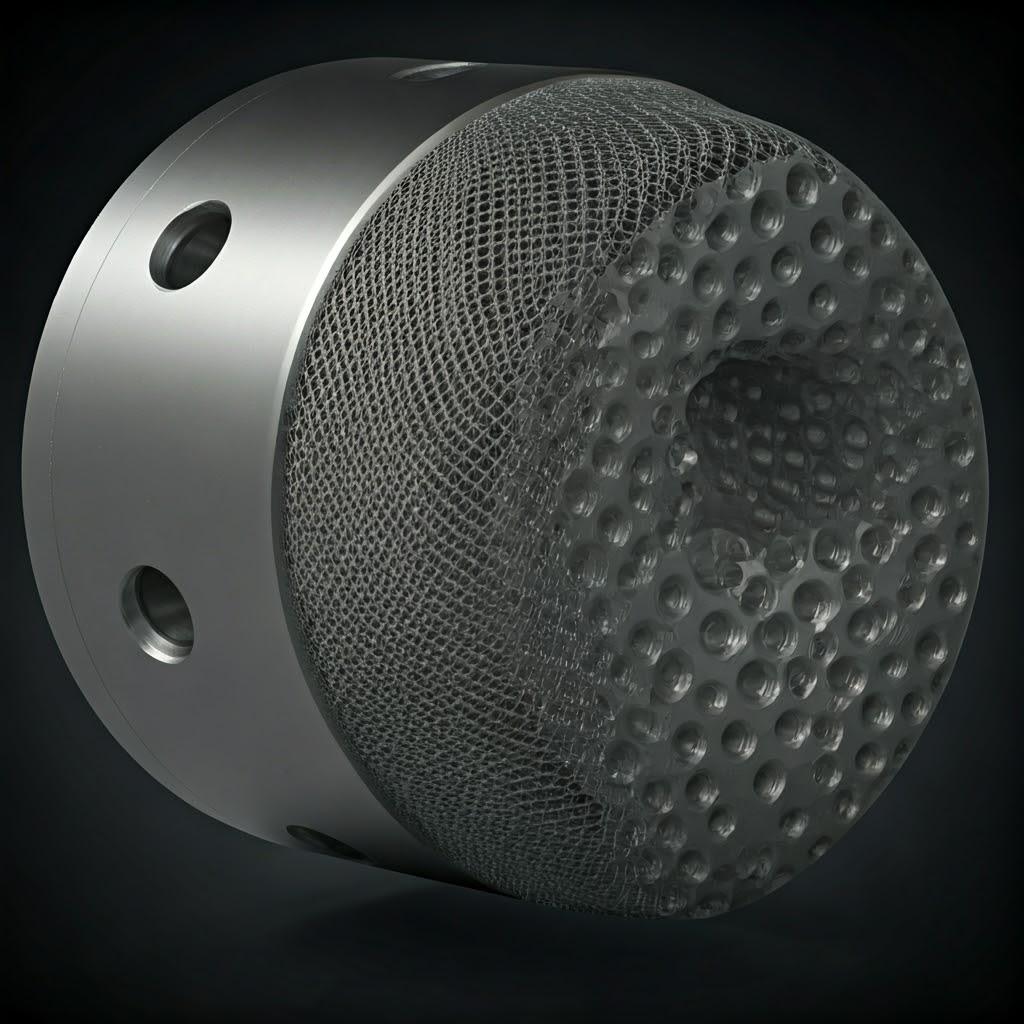
Understanding Cost Drivers and Lead Times for Custom Aerospace Fixtures
When considering metal 3D printing for custom aerospace assembly fixtures, understanding the key cost drivers and typical lead times is essential for effective planning and budgeting.
비용 요소:
- 재료비: The cost of the metal powder is a significant factor. Aerospace-grade materials like 316L and Invar can vary in price depending on market conditions and supplier. The quantity of material used for each fixture, which is influenced by the design and the need for support structures, also impacts the overall material cost. Metal3DP manufactures high-quality metal powders, potentially offering cost advantages compared to sourcing materials separately.
- 인쇄 시간: The duration of the 3D printing process depends on factors such as the size and complexity of the fixture, the layer height used, and the printing technology. Longer print times translate to higher machine operating costs.
- Pre-Processing Costs: This can include design optimization for 3D printing, preparation of the 3D model, and build setup. While these are often one-time costs, they are important to consider. Metal3DP‘s application development services can help optimize designs to minimize printing time and material usage.
- 후처리 비용: As discussed earlier, post-processing steps like support removal, heat treatment, surface finishing, and machining add to the overall cost. The complexity and number of post-processing steps required will influence these costs.
- 인건비: This includes the labor involved in operating the 3D printer, performing post-processing, and conducting quality control.
- Equipment and Overhead Costs: Metal 3D printing service providers have significant investments in equipment and facilities, which are factored into their pricing.
리드 타임:
- Design and Engineering: The initial design and optimization phase can take varying amounts of time depending on the complexity of the fixture and the need for iterations.
- 인쇄 시간: As mentioned earlier, the build time on the 3D printer is a key component of the lead time.
- 후처리: The time required for post-processing steps can range from a few hours to several days, depending on the complexity and the specific processes involved.
- Quality Control and Inspection: Thorough inspection can add to the overall lead time, especially for critical aerospace applications where stringent quality checks are necessary.
- Shipping and Delivery: The time taken for the finished fixtures to be shipped to your facility also needs to be factored in.
Metal 3D printing generally offers shorter lead times for complex, custom parts compared to traditional manufacturing methods that may involve extensive tooling. However, it’s crucial to discuss lead times and cost factors in detail with your chosen service provider, such as Metal3DP, to get an accurate estimate for your specific project. Factors like part geometry, material selection, and required post-processing will all play a role in the final cost and delivery timeline.
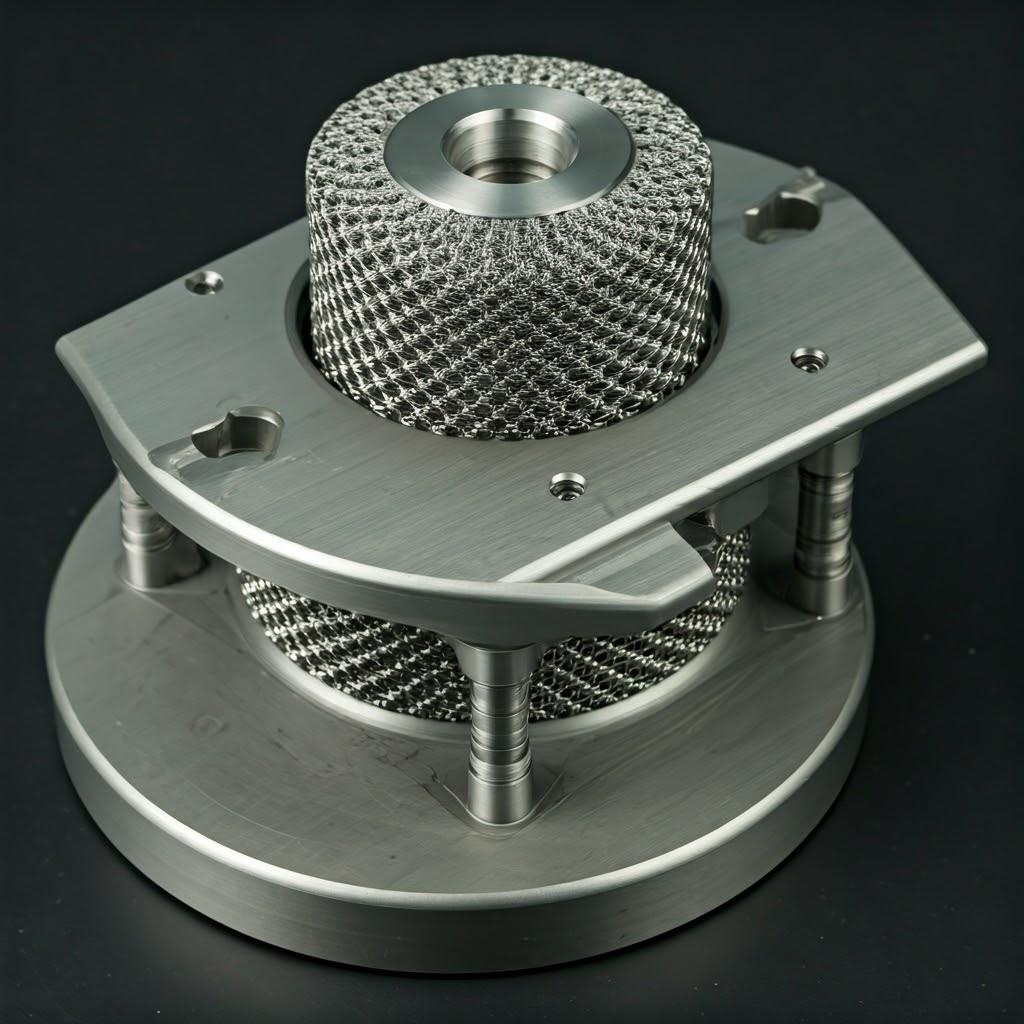
자주 묻는 질문(FAQ)
- Q: Can metal 3D printed aerospace fixtures meet the same strength and durability requirements as traditionally manufactured fixtures?
- A: Yes, when the design, material selection, and printing process are optimized, metal 3D printed fixtures can achieve comparable or even superior strength and durability to those manufactured using traditional methods. Technologies like Selective Electron Beam Melting (SEBM) from Metal3DP produce dense parts with excellent mechanical properties. Post-processing treatments like heat treatment further enhance these properties.
- Q: What are the typical tolerances achievable with metal 3D printing for aerospace assembly fixtures?
- A: Depending on the printing technology and material, tolerances of ±0.1 to ±0.2 mm are achievable for critical dimensions with metal 3D printing. For applications requiring tighter tolerances, post-machining can be employed. Metal3DP‘s advanced printing technology is engineered for high accuracy and reliability.
- Q: Is metal 3D printing cost-effective for producing aerospace assembly fixtures?
- A: The cost-effectiveness of metal 3D printing depends on factors such as the complexity of the fixture, the quantity needed, and the material used. For complex geometries and low to medium volumes, metal 3D printing often offers a more cost-effective solution than traditional methods due to reduced tooling costs and material waste. Discuss your specific requirements with Metal3DP for a detailed cost analysis.
Conclusion: Embracing Metal 3D Printing for Advanced Aerospace Assembly Fixtures
The aerospace industry demands the highest levels of precision, efficiency, and reliability in its manufacturing processes. Custom assembly fixtures are integral to achieving these standards. Metal 3D printing has emerged as a transformative technology, offering unparalleled design freedom, reduced lead times, and the ability to create highly optimized fixtures tailored to the unique challenges of aerospace assembly.
By leveraging materials like 316L stainless steel and Invar, and partnering with experienced providers like Metal3DP Technology Co., LTD, aerospace manufacturers can unlock new levels of innovation and efficiency in their assembly operations. From intricate geometries and lightweight designs to enhanced accuracy and streamlined post-processing, metal 3D printing offers a compelling pathway to the future of aerospace manufacturing.
Metal3DP is committed to providing cutting-edge systems and high-quality metal powders to empower the next generation of manufacturing. We invite you to explore our website to learn more about our SEBM printers, advanced metal powders, and application development services. Contact us today to discover how Metal3DP can partner with your organization to achieve your additive manufacturing goals and drive innovation in your aerospace assembly processes.
공유
중국 칭다오에 본사를 둔 선도적인 적층 제조 솔루션 제공업체인 MET3DP Technology Co. 당사는 산업용 3D 프린팅 장비와 고성능 금속 분말을 전문으로 합니다.
관련 기사
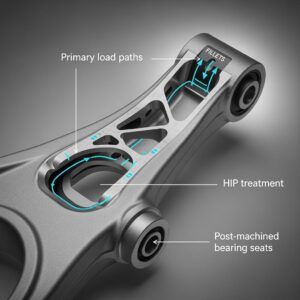