3D Printed Thermal Interface Hardware
목차
Introduction – Ensuring Peak Performance in Orbit: The Critical Role of Custom Satellite Thermal Interfaces
In the unforgiving environment of space, maintaining optimal operating temperatures for sensitive electronic components within satellites is paramount. Fluctuations in temperature can lead to performance degradation, system failures, and ultimately, mission compromise. This is where custom satellite thermal interfaces play a vital role. These meticulously engineered components facilitate efficient heat transfer away from critical electronics, ensuring they remain within their specified temperature ranges despite the extreme thermal conditions encountered in orbit. The demand for increasingly sophisticated and compact satellites with complex geometries necessitates innovative manufacturing approaches. Metal 3D 프린팅, also known as metal additive manufacturing, has emerged as a powerful technology to produce highly customized thermal interface hardware that meets the stringent performance and design requirements of the aerospace industry. By leveraging the capabilities of metal 3D printing, engineers and procurement managers can achieve unprecedented design freedom, optimize thermal performance, and potentially reduce lead times and costs compared to traditional manufacturing methods. At Metal3DP, we understand the critical nature of satellite components and offer advanced metal 3D printing solutions tailored to the unique demands of the aerospace sector. Our industry-leading print volume, accuracy, and reliability ensure that mission-critical parts meet the highest standards.
What are 3D Printed Thermal Interface Hardware for Satellites Used For? – Diverse Applications in Spacecraft Thermal Management
3D printed thermal interface hardware for satellites serves a multitude of critical functions within spacecraft thermal management systems. These custom-designed components act as conduits for heat transfer between various elements, ensuring the reliable operation of sensitive electronics and instruments. Some key applications include:
- 방열판: Dissipating heat generated by electronic components such as microprocessors, power amplifiers, and communication modules. Custom 3D printed heat sinks can be designed with complex internal geometries and optimized surface areas to maximize heat dissipation into the spacecraft’s thermal control system.
- Thermal Straps: Providing flexible thermal pathways between components that experience relative motion or are located on different structural elements. 3D printing allows for the creation of intricate strap designs that accommodate movement while maintaining efficient thermal conductivity.
- Conductive Fillers and Spacers: Ensuring efficient heat transfer across interfaces between components and mounting surfaces. Custom-shaped 3D printed fillers and spacers can precisely fit complex geometries, eliminating air gaps that impede thermal performance.
- Cold Plates: Providing a thermally controlled surface for mounting multiple heat-generating components. 3D printing enables the creation of lightweight cold plates with integrated cooling channels optimized for specific thermal loads and spatial constraints.
- Thermal Management Structures: Integrating thermal pathways and features directly into structural components, reducing the need for separate thermal interface hardware. This can lead to weight savings and simplified assembly.
The ability to create complex and highly customized geometries through metal 3D printing opens up new possibilities for optimizing thermal management in satellites. Metal3DP‘s expertise in metal additive manufacturing allows us to produce intricate thermal interface hardware tailored to the specific needs of various satellite subsystems. Our high-quality metal powders, manufactured using advanced powder making systems, ensure the thermal conductivity and structural integrity required for demanding space applications.
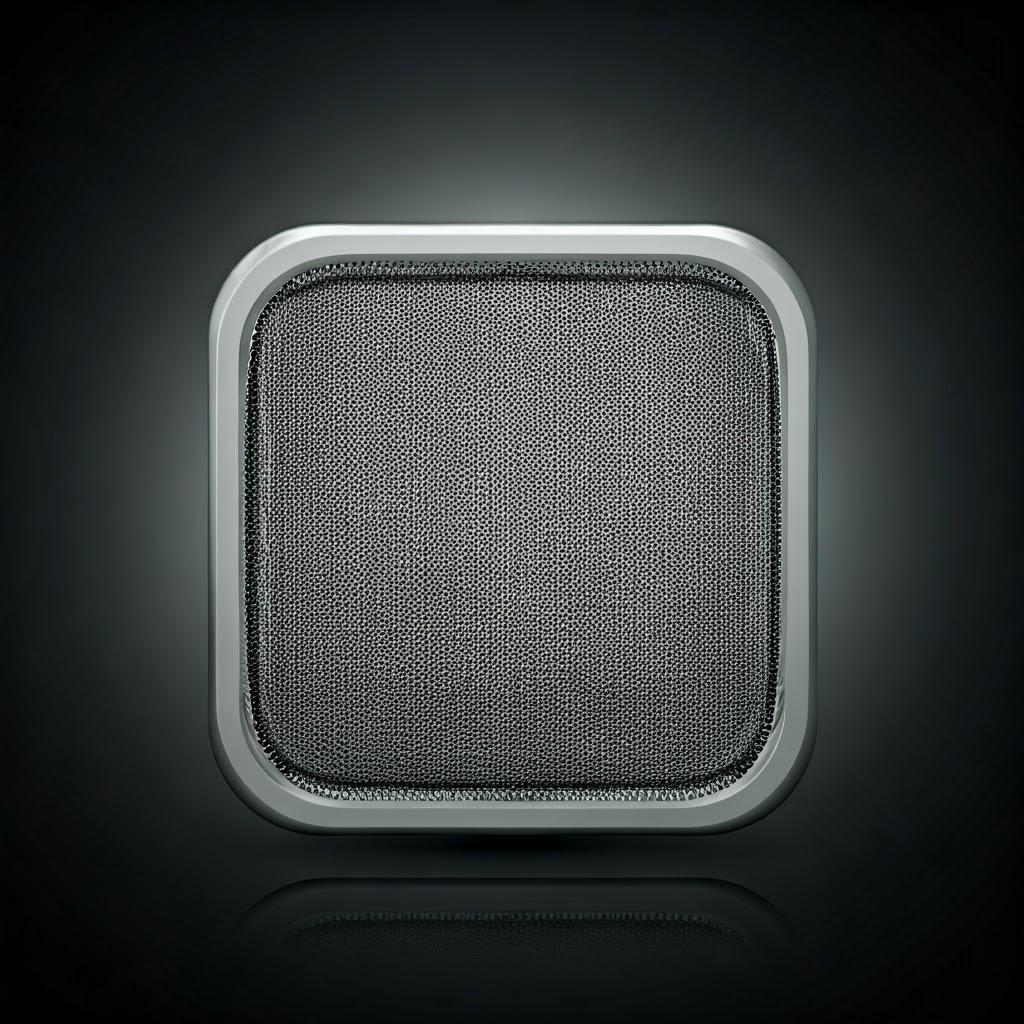
Why Use Metal 3D Printing for Satellite Thermal Interface Hardware? – Unlocking Design Freedom and Performance Advantages
Adopting metal 3D printing for the fabrication of satellite thermal interface hardware offers a compelling array of advantages over traditional manufacturing methods:
- 디자인의 자유와 복잡성: Metal 3D printing allows for the creation of intricate geometries, including complex internal channels, thin walls, and optimized surface features, that are often impossible or cost-prohibitive to achieve with conventional techniques like machining or casting. This design flexibility enables engineers to tailor thermal interfaces precisely to the specific thermal requirements and spatial constraints of satellite components.
- 머티리얼 최적화: Metal 3D printing facilitates the use of advanced materials like AlSi10Mg and CuCrZr, which offer excellent thermal conductivity and lightweight properties crucial for aerospace applications. Furthermore, the ability to precisely control material deposition can lead to optimized material usage and reduced waste.
- 경량화: In the aerospace industry, every gram counts. Metal 3D printing enables the creation of lightweight yet structurally sound thermal interface hardware through topology optimization and the design of intricate lattice structures. This can lead to significant fuel savings and increased payload capacity for satellites.
- 신속한 프로토타이핑 및 반복: Metal 3D printing significantly accelerates the prototyping process, allowing engineers to quickly iterate on designs and test different thermal management solutions. This rapid feedback loop reduces development time and costs.
- Customization and Small Batch Production: Satellites often require highly customized components, and production volumes can be relatively low. Metal 3D printing is ideally suited for producing small batches of complex, custom-designed thermal interface hardware without the need for expensive tooling.
- Integration of Features: 3D printing allows for the integration of multiple functionalities into a single component, such as combining heat dissipation features with structural support. This can simplify assembly, reduce part count, and improve overall system reliability.
Metal3DP is at the forefront of leveraging these advantages to provide cutting-edge metal 3D printing services for the aerospace industry. Our state-of-the-art Selective Electron Beam Melting (SEBM) printers and high-quality metal powders enable the production of complex, high-performance satellite thermal interface hardware with exceptional accuracy and reliability. Explore our range of metal 3D printing services to see how we can support your aerospace manufacturing needs.
Recommended Materials and Why They Matter for Satellite Thermal Interfaces – Exploring AlSi10Mg and CuCrZr
The choice of material is critical for the performance of satellite thermal interface hardware. Factors such as thermal conductivity, density, strength, and compatibility with the space environment must be carefully considered. Metal3DP recommends AlSi10Mg and CuCrZr as excellent material choices for 3D printed satellite thermal interfaces due to their specific properties:
AlSi10Mg (Aluminum Silicon Magnesium):
속성 | 가치 | Significance for Thermal Interfaces |
---|---|---|
열 전도성 | ~120-160 W/m·K | Excellent ability to conduct heat away from electronic components, crucial for maintaining optimal operating temperatures. |
밀도 | ~2.67 g/cm³ | Low density is highly desirable in aerospace applications to minimize weight and improve fuel efficiency. |
힘 | Tensile Strength (UTS): ~350-420 MPa | Provides sufficient structural integrity to withstand launch loads and operational stresses. |
내식성 | 양호 | Offers resistance to the harsh space environment, ensuring long-term reliability. |
인쇄 가능성 | Excellent with Laser Powder Bed Fusion | Well-established material for L-PBF, allowing for the creation of complex geometries with good surface finish. Metal3DP utilizes advanced L-PBF technology to process AlSi10Mg with high precision. |
시트로 내보내기
CuCrZr (Copper Chromium Zirconium):
속성 | 가치 | Significance for Thermal Interfaces |
---|---|---|
열 전도성 | ~300-380 W/m·K | Superior thermal conductivity compared to aluminum alloys, making it ideal for applications requiring very efficient heat dissipation. |
밀도 | ~ Higher density than aluminum alloys, which may be a consideration for extremely weight-sensitive applications. However, its superior thermal performance can outweigh this in many cases. Higher density can also offer better vibration dampening. | |
힘 | Tensile Strength (UTS): ~350-500 MPa | Provides excellent structural strength and resistance to thermal fatigue. |
내식성 | 양호 | Suitable for the space environment, offering good resistance to oxidation. |
인쇄 가능성 | Good with Laser Powder Bed Fusion | Can be effectively processed using L-PBF to create complex geometries. Metal3DP has developed expertise in processing CuCrZr to achieve optimal thermal and mechanical properties. |
시트로 내보내기
The selection between AlSi10Mg and CuCrZr depends on the specific thermal management requirements of the satellite component. For applications prioritizing lightweighting with good thermal conductivity, AlSi10Mg is an excellent choice. When maximum heat dissipation is paramount, and slightly higher weight is acceptable, CuCrZr offers superior thermal performance. Metal3DP offers both AlSi10Mg and CuCrZr powders, manufactured with our industry-leading gas atomization and PREP technologies, ensuring high sphericity and flowability for optimal 3D printing. Contact Metal3DP to discuss your specific material requirements and how our high-quality metal powders can enable the creation of advanced satellite thermal interface hardware.
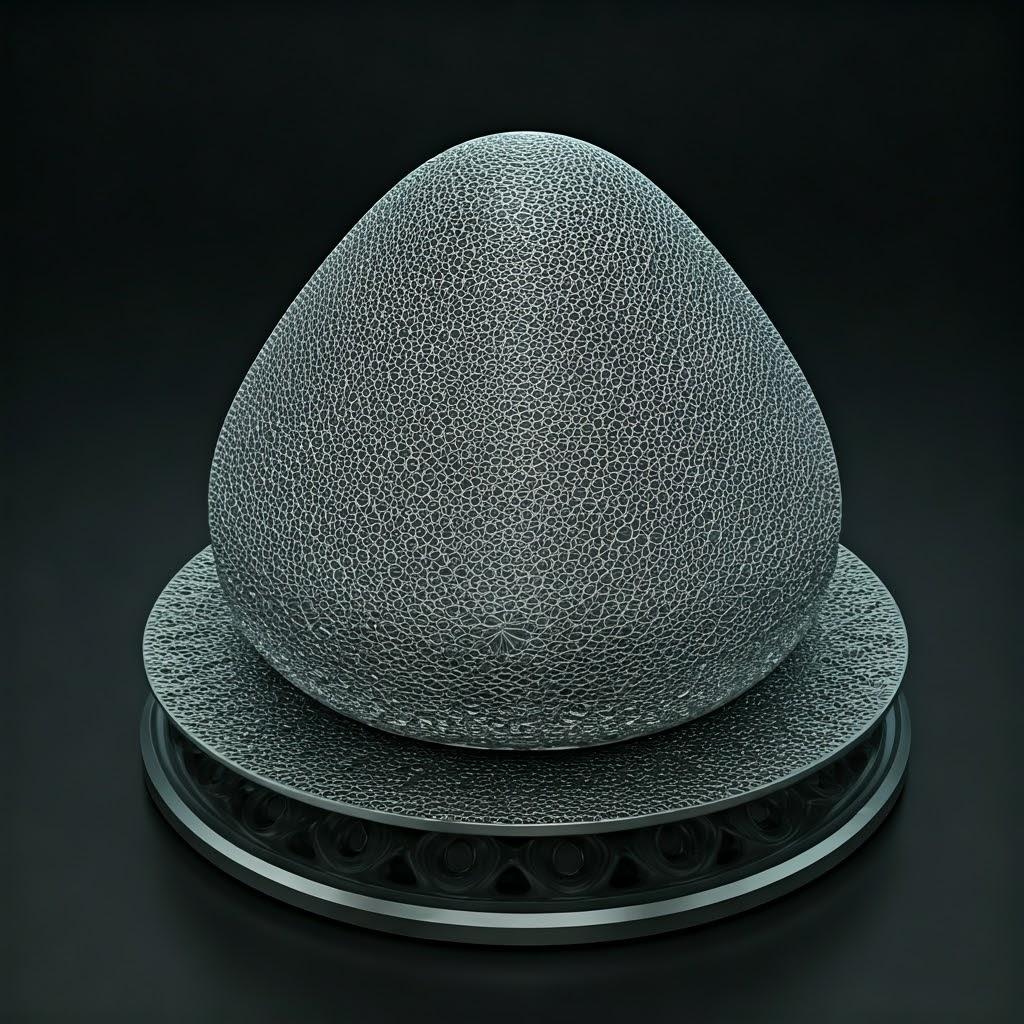
Design Considerations for Additive Manufacturing of Satellite Thermal Interfaces – Optimizing for Thermal Efficiency and Structural Integrity
Designing satellite thermal interfaces for additive manufacturing requires a different mindset compared to traditional methods. To fully leverage the capabilities of metal 3D printing and achieve optimal thermal efficiency and structural integrity, several key design considerations must be taken into account:
- 토폴로지 최적화: Utilize topology optimization software to generate designs that maximize thermal performance while minimizing material usage and weight. This involves defining the design space, applying thermal and structural loads, and allowing the software to iteratively remove material from low-stress or low-heat-flux areas. The complex, organic shapes generated by topology optimization are ideally suited for metal 3D printing.
- 컨포멀 냉각 채널: For heat sink and cold plate applications, design conformal cooling channels that closely follow the contours of the heat-generating components. This maximizes the contact area for heat transfer and improves cooling efficiency compared to traditional straight channels. Metal 3D printing’s design freedom makes creating these intricate internal geometries possible.
- Surface Area Enhancement: Incorporate features that increase the surface area for heat dissipation, such as fins, pin fins, or microchannels. The fine feature resolution of metal 3D printing allows for the creation of complex and densely packed surface structures that significantly enhance convective heat transfer.
- Material Distribution: Strategically distribute material to optimize both thermal conductivity and structural strength. For example, thicker sections can be used in high-stress areas, while thinner, more intricate features can be employed in areas requiring high surface area for heat transfer.
- Interface Design: Carefully consider the design of mating surfaces to ensure good thermal contact. Design features like textured surfaces or integrated mounting features can improve thermal conductance across interfaces and simplify assembly.
- Self-Supporting Structures: Design parts with self-supporting geometries whenever possible to minimize the need for support structures during printing. This reduces material waste, post-processing time, and the risk of surface damage during support removal.
- Orientation Optimization: Optimize the part orientation on the build platform to balance thermal performance, structural integrity, and printability. Consider the direction of heat flow, stress loads, and the potential for anisotropic material properties resulting from the layer-by-layer printing process.
- 벽 두께 및 피처 크기: Adhere to the minimum feature size and wall thickness capabilities of the chosen metal 3D printing process and material. Metal3DP provides detailed design guidelines for our SEBM and L-PBF processes to ensure manufacturability and performance.
By carefully considering these design principles, engineers can harness the full potential of metal 3D printing to create highly efficient and reliable thermal interface hardware for demanding satellite applications. Metal3DP‘s application development services can provide expert guidance on optimizing designs for metal additive manufacturing.
Tolerance, Surface Finish, and Dimensional Accuracy of 3D Printed Satellite Thermal Interfaces – Meeting Stringent Aerospace Requirements
In the aerospace industry, precision is paramount. Satellite components, including thermal interfaces, often have tight tolerance requirements to ensure proper fit, functionality, and performance under extreme conditions. Metal 3D printing technologies have made significant strides in achieving the dimensional accuracy and surface finish necessary for many aerospace applications.
- 치수 정확도: The dimensional accuracy achievable with metal 3D printing depends on several factors, including the chosen printing technology (e.g., L-PBF, SEBM), the material, part geometry, and build parameters. Metal3DP‘s advanced SEBM printers are known for their high accuracy and repeatability, typically achieving tolerances of ±0.1-0.2 mm or better for critical dimensions. Laser Powder Bed Fusion (L-PBF) also offers excellent accuracy, often within a similar range. Careful process control and optimized build parameters are essential to consistently achieve tight tolerances.
- 표면 마감: The as-printed surface finish of metal 3D printed parts is typically rougher than that achieved by machining. The surface roughness is influenced by the powder particle size, layer thickness, and the presence of partially sintered powder particles. For thermal interfaces, a smooth surface finish is often desirable to maximize contact area and improve thermal conductance. Post-processing techniques such as shot peening, polishing, and CNC machining can be employed to achieve the required surface finish. Metal3DP offers a range of post-processing services to meet specific surface finish requirements.
- Factors Affecting Accuracy and Finish:
- 머신 보정: Regular calibration of the 3D printer is crucial for maintaining dimensional accuracy.
- 머티리얼 속성: Different metal powders exhibit varying levels of shrinkage and distortion during the printing process.
- 빌드 오리엔테이션: The orientation of the part on the build platform can affect both accuracy and surface finish.
- 지원 구조: The placement and removal of support structures can impact surface quality.
- 후처리: Heat treatment can relieve internal stresses and improve dimensional stability, while machining can achieve very tight tolerances and smooth surfaces.
Metal3DP employs rigorous quality control measures and utilizes advanced 3D printing equipment to ensure that our metal additive manufactured parts meet the stringent dimensional accuracy and surface finish requirements of the aerospace industry. We work closely with our clients to understand their specific needs and implement appropriate manufacturing and post-processing strategies to deliver high-precision thermal interface hardware.
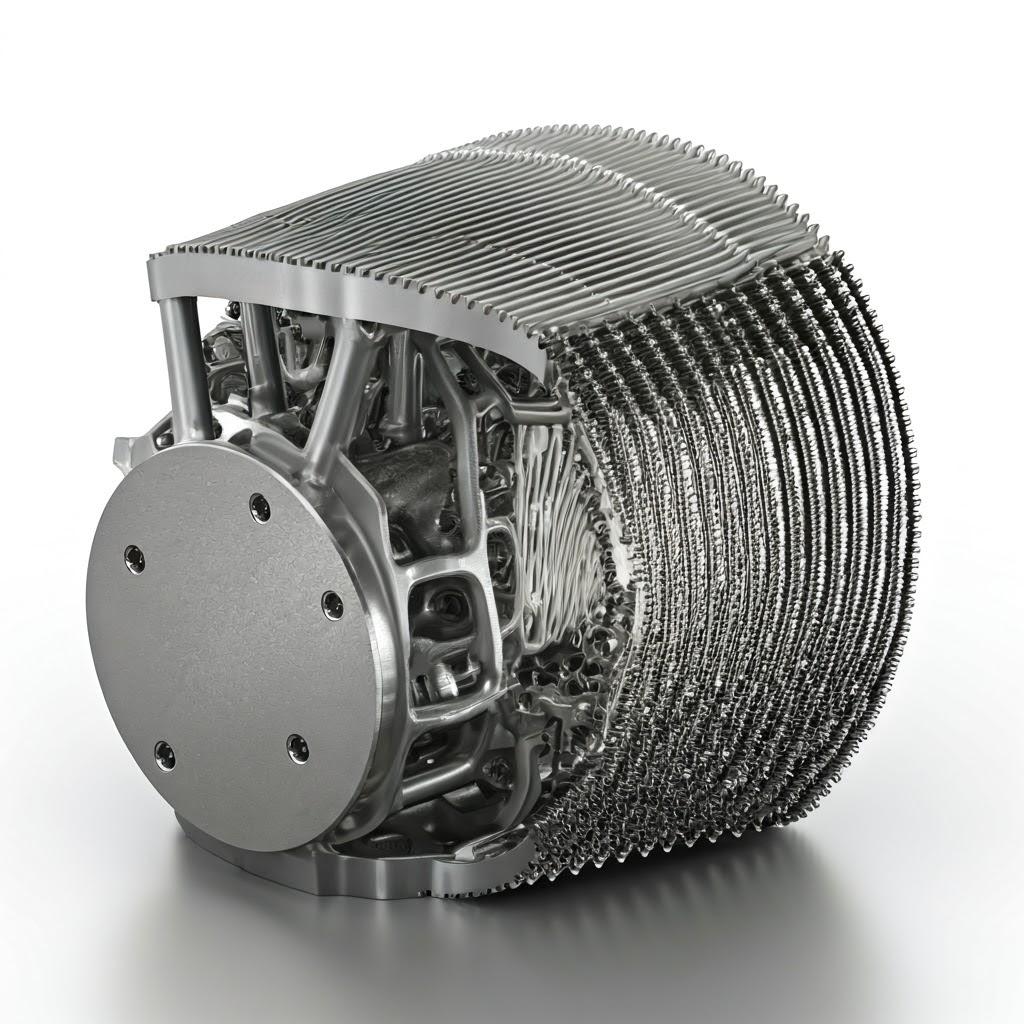
Post-Processing Requirements for Satellite Thermal Interface Hardware – Enhancing Performance and Reliability
While metal 3D printing offers significant advantages in creating complex geometries, post-processing steps are often necessary to achieve the final desired properties, performance, and surface finish for satellite thermal interface hardware. Common post-processing requirements include:
- 스트레스 완화 열처리: Metal 3D printed parts can contain residual stresses due to the rapid heating and cooling cycles during the printing process. Heat treatment is often performed to relieve these stresses, improve dimensional stability, and enhance mechanical properties. The specific heat treatment cycle depends on the material and application requirements.
- 지원 구조 제거: Support structures are often required to prevent part deformation during printing. These structures need to be carefully removed after the build is complete. The removal process can involve manual breaking, cutting, or machining, depending on the support material and geometry.
- 표면 마감: As mentioned earlier, the as-printed surface finish may not be suitable for all applications. Techniques like shot peening, abrasive blasting, polishing, and electrochemical polishing can be used to improve surface smoothness, reduce roughness, and enhance contact for better thermal transfer.
- CNC 가공: For critical dimensions and tight tolerances that cannot be achieved directly through 3D printing, CNC machining can be used as a secondary process to refine specific features and ensure precise mating with other components.
- Cleaning and Inspection: Thorough cleaning is essential to remove any residual powder particles or contaminants from the printed parts. Non-destructive testing (NDT) methods, such as visual inspection, dye penetrant inspection, or X-ray inspection, may be employed to ensure the internal integrity and quality of the parts, especially for critical aerospace applications.
- Coating and Surface Treatment: Depending on the application and environmental conditions, surface coatings or treatments may be required to enhance corrosion resistance, improve thermal emissivity, or modify other surface properties. Examples include anodizing for aluminum alloys or specialized thermal control coatings.
Metal3DP offers a comprehensive suite of post-processing services to ensure that our 3D printed metal parts meet the demanding requirements of satellite applications. Our experienced team can advise on the most appropriate post-processing steps to achieve the desired performance, reliability, and surface finish for your custom thermal interface hardware.
Common Challenges and How to Avoid Them in 3D Printing Satellite Thermal Interfaces – Ensuring Successful Manufacturing
While metal 3D printing offers numerous benefits, there are also potential challenges that need to be addressed to ensure the successful manufacturing of high-quality satellite thermal interface hardware:
- Warping and Distortion: Residual stresses during the printing process can lead to warping or distortion of the parts, especially for complex geometries or thin-walled structures.
- 솔루션: Optimize part orientation, use appropriate support structures, and implement stress relief heat treatment. Consider design modifications to minimize large unsupported areas.
- 다공성: Internal porosity can compromise the mechanical strength and thermal conductivity of the printed parts.
- 솔루션: Optimize printing parameters such as laser power, scan speed, and layer thickness. Ensure the use of high-quality, spherical metal powders with good flowability, such as those produced by Metal3DP‘s advanced powder making system.
- Support Structure Removal Damage: Removing support structures can sometimes leave surface blemishes or damage the part, especially for delicate features.
- 솔루션: Design self-supporting geometries where possible. Optimize support placement and use dissolvable support materials if compatible with the chosen metal and printing process. Employ skilled technicians for support removal and utilize appropriate tools.
- Achieving Tight Tolerances: Meeting the stringent dimensional accuracy requirements of aerospace applications can be challenging.
- 솔루션: Utilize high-precision 3D printing equipment like Metal3DP‘s SEBM printers. Optimize build parameters and consider post-processing steps such as CNC machining for critical dimensions.
- 표면 거칠기: The as-printed surface finish may not meet the requirements for optimal thermal contact.
- 솔루션: Employ appropriate surface finishing techniques such as polishing, shot peening, or electrochemical polishing.
- Material Property Consistency: Ensuring consistent material properties throughout the printed part and between different builds is crucial for reliability.
- 솔루션: Work with a reputable metal 3D printing service provider like Metal3DP that has strict quality control procedures and expertise in processing aerospace-grade materials. Our high-quality metal powders and optimized printing processes ensure consistent and reliable material properties.
- Powder Management: Proper handling and storage of metal powders are essential to prevent contamination and ensure optimal print quality.
- 솔루션: Follow strict powder handling protocols and use appropriate storage containers in controlled environments. Metal3DP adheres to rigorous powder management standards.
By understanding these potential challenges and implementing appropriate mitigation strategies, engineers and procurement managers can successfully leverage metal 3D printing to produce high-performance satellite thermal interface hardware. Partnering with an experienced provider like Metal3DP, which offers comprehensive solutions spanning equipment, materials, and application development, can significantly reduce these risks.
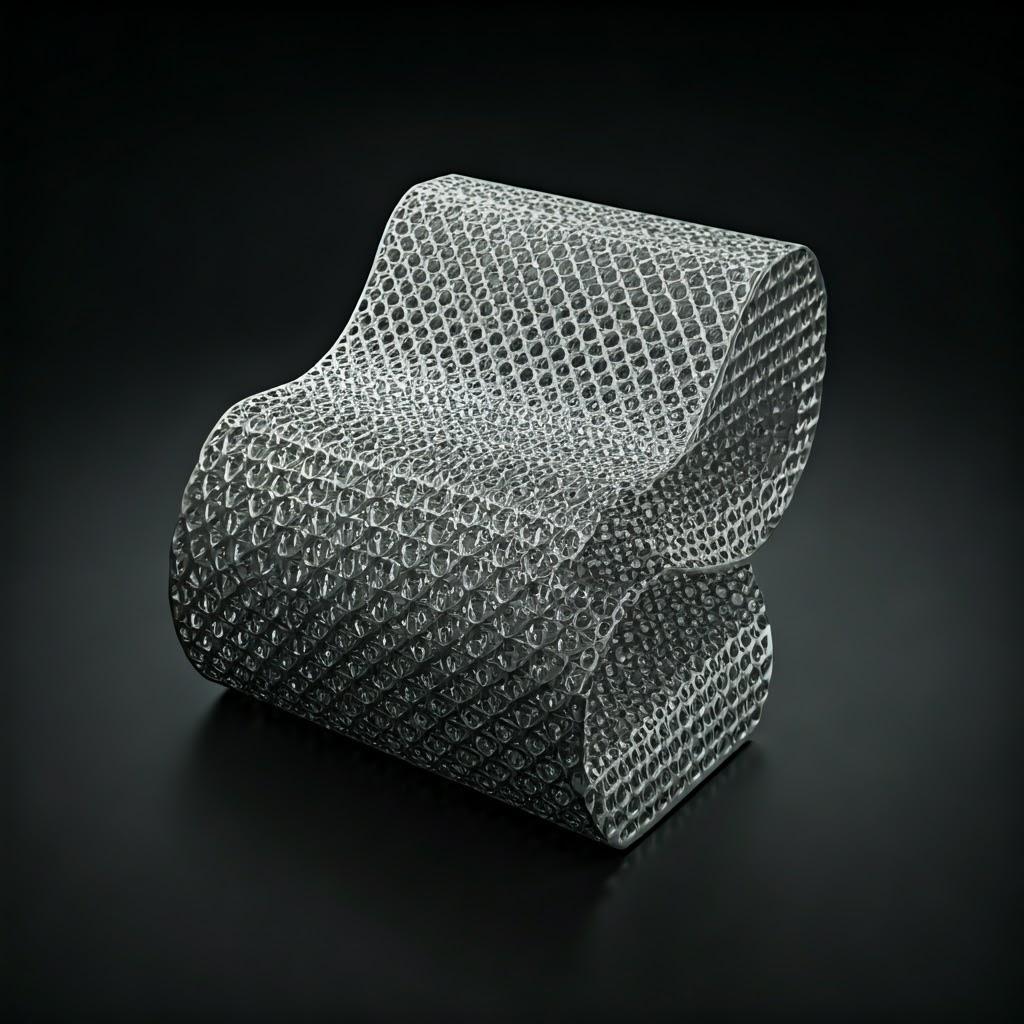
How to Choose the Right Metal 3D Printing Service Provider for Satellite Components – Key Considerations for Aerospace Applications
Selecting the right metal 3D printing service provider is a critical decision for aerospace companies seeking to manufacture high-performance satellite components like thermal interfaces. Given the stringent requirements of the space industry, several key factors should be carefully evaluated:
- Aerospace Certifications and Standards: Ensure the service provider holds relevant aerospace certifications such as AS9100 or Nadcap. These certifications demonstrate a commitment to quality management systems and process control necessary for producing reliable aerospace-grade parts. Metal3DP is committed to adhering to the highest quality standards relevant to the industries we serve.
- Material Capabilities: Verify that the provider has experience processing the specific metal alloys required for your application (e.g., AlSi10Mg, CuCrZr). They should also have a robust understanding of the material properties and how they are affected by the 3D printing process. Metal3DP offers a wide range of high-quality metal powders optimized for laser and electron beam powder bed fusion.
- Printing Technology and Equipment: Understand the types of metal 3D printing technologies the provider utilizes (e.g., L-PBF, SEBM). Different technologies offer varying levels of accuracy, surface finish, and build volume. Metal3DP leverages industry-leading SEBM printers known for their accuracy and reliability. You can learn more about our printing methods here: https://met3dp.com/printing-methods/
- Design and Engineering Support: A strong service provider should offer design and engineering support to optimize your parts for additive manufacturing. This includes guidance on topology optimization, material selection, and design for manufacturability. Metal3DP provides comprehensive solutions spanning equipment, advanced metal powders, and application development services.
- Post-Processing Capabilities: Inquire about the in-house post-processing services offered, such as heat treatment, surface finishing, CNC machining, and inspection. A provider with comprehensive post-processing capabilities can streamline the manufacturing process and ensure the final parts meet your specifications. Metal3DP offers a range of post-processing services to enhance the performance and reliability of 3D printed parts.
- Quality Control and Inspection: Understand the provider’s quality control procedures and inspection methods. They should have robust processes in place to ensure dimensional accuracy, material integrity, and overall part quality.
- Lead Times and Production Capacity: Discuss lead times and production capacity to ensure the provider can meet your project timelines and volume requirements.
- Experience and Expertise: Look for a provider with a proven track record of successfully manufacturing metal 3D printed parts for the aerospace industry or other demanding sectors. Their experience and expertise can be invaluable in navigating the complexities of metal additive manufacturing. Metal3DP has decades of collective expertise in metal additive manufacturing. You can learn more about our company here: https://met3dp.com/about-us/
By carefully considering these factors, you can select a metal 3D printing service provider that can reliably produce high-quality satellite thermal interface hardware that meets the stringent demands of aerospace applications.
Cost Factors and Lead Time for 3D Printed Satellite Thermal Interfaces – Understanding the Economics of Space-Grade Manufacturing
The cost and lead time for 3D printed satellite thermal interfaces are influenced by several factors that need to be considered for effective project planning and budgeting:
- 재료비: The cost of the metal powder (e.g., AlSi10Mg, CuCrZr) is a significant factor. Specialty alloys and smaller batch orders of powder can result in higher material costs. Metal3DP manufactures a wide range of high-quality metal powders. You can explore our product offerings here: https://met3dp.com/product/
- 구축 시간: The time it takes to print a part depends on its size, complexity, and the chosen printing technology. Longer build times translate to higher machine operation costs.
- 후처리 비용: The extent of post-processing required (e.g., heat treatment, support removal, surface finishing, machining) will impact the overall cost. Complex post-processing steps will increase the final price.
- 인건비: Engineering design optimization for 3D printing, machine setup, operation, post-processing, and quality control all contribute to labor costs.
- Quantity and Batch Size: While 3D printing is advantageous for low to medium volume production, larger quantities can sometimes benefit from economies of scale in material procurement and build setup.
- 지오메트리의 복잡성: Highly complex parts with intricate internal features or thin walls may require more design optimization, specialized support structures, and longer build times, thus increasing costs.
- Quality Assurance and Inspection: Stringent quality control procedures and non-destructive testing, often required for aerospace applications, will add to the overall cost.
리드 타임:
- Design and Optimization: The initial design and optimization phase for additive manufacturing can take time, depending on the complexity of the part and the need for simulations (e.g., thermal analysis, structural analysis).
- 인쇄 시간: The actual printing duration is determined by the part’s volume and the printer’s build rate.
- 후처리 시간: The time required for post-processing steps can vary significantly depending on the complexity and the number of processes involved.
- Quality Control and Inspection: Thorough inspection processes can add to the overall lead time, especially for critical aerospace components.
- Shipping and Logistics: The time for final part shipment also needs to be factored into the overall lead time.
While the initial cost per part for 3D printing might be higher than traditional manufacturing methods for very high volumes, it often offers cost advantages for complex geometries, low to medium production runs, and rapid prototyping due to reduced tooling costs and faster turnaround times. Metal3DP works closely with clients to provide transparent cost breakdowns and realistic lead times based on their specific project requirements. Contact us to discuss your project and receive a detailed quotation.
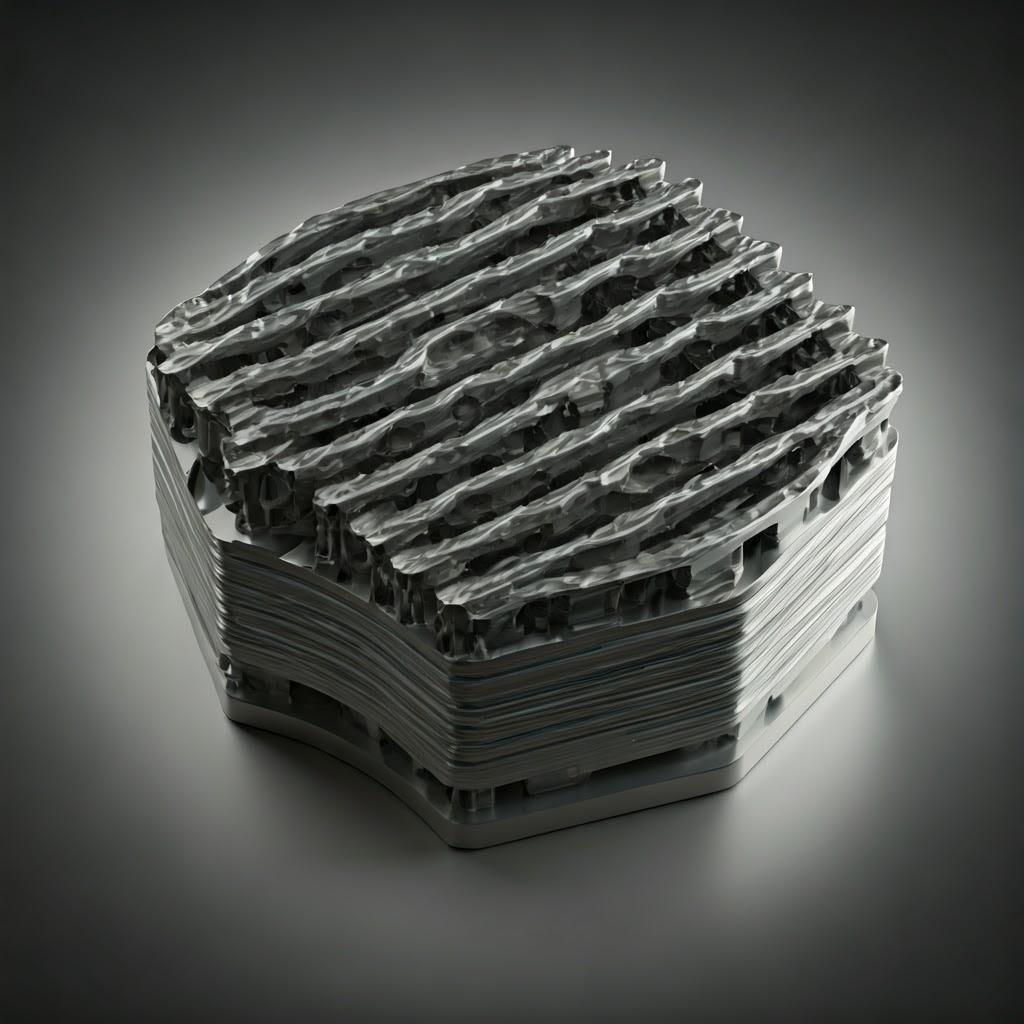
Frequently Asked Questions (FAQ) – Addressing Common Inquiries About 3D Printed Satellite Thermal Interfaces
- Can metal 3D printed thermal interfaces meet the thermal conductivity requirements for satellite applications? Yes, with the appropriate material selection and optimized design, metal 3D printed thermal interfaces can achieve excellent thermal conductivity. Materials like CuCrZr offer superior thermal performance, while AlSi10Mg provides a good balance of thermal conductivity and lightweighting. Metal3DP offers both materials with well-defined thermal properties suitable for space applications.
- What level of dimensional accuracy can be achieved with 3D printed satellite thermal interfaces? The dimensional accuracy depends on the printing technology and post-processing. Metal3DP‘s SEBM technology can achieve tolerances of ±0.1-0.2 mm or better. For tighter tolerances, post-processing such as CNC machining can be employed.
- Are 3D printed metal parts strong enough for the harsh environment of space? Yes, when the appropriate materials and printing parameters are used, metal 3D printed parts can exhibit excellent mechanical properties suitable for the space environment. Materials like AlSi10Mg and CuCrZr offer high strength-to-weight ratios. Post-processing, such as heat treatment, can further enhance mechanical properties.
Conclusion – Embracing the Future of Spacecraft Thermal Management with Metal 3D Printing
Metal 3D printing is revolutionizing the design and manufacturing of custom satellite thermal interface hardware. Its ability to create complex geometries, optimize material usage, reduce weight, and accelerate prototyping offers significant advantages for the aerospace industry. By leveraging advanced materials like AlSi10Mg and CuCrZr and partnering with experienced service providers like Metal3DP, engineers and procurement managers can unlock new possibilities for enhancing spacecraft thermal management systems. The design freedom, performance advantages, and potential for cost and lead time reductions make metal 3D printing an increasingly compelling solution for the demanding requirements of space-bound applications. Contact Metal3DP today to explore how our cutting-edge systems and high-quality metal powders can power your organization’s additive manufacturing goals for satellite technology.
공유
중국 칭다오에 본사를 둔 선도적인 적층 제조 솔루션 제공업체인 MET3DP Technology Co. 당사는 산업용 3D 프린팅 장비와 고성능 금속 분말을 전문으로 합니다.
관련 기사
Met3DP 소개
최근 업데이트
제품
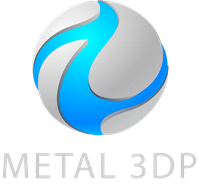
3D 프린팅 및 적층 제조용 금속 분말