custom aerospace vents using metal 3D printing
목차
소개
In the high-stakes world of aerospace engineering, every component plays a critical role in ensuring safety, performance, and efficiency. Among these essential elements are ventilation systems, often underestimated yet vital for maintaining operational integrity and passenger comfort. Unlike their standardized counterparts in other industries, aerospace vents frequently demand custom designs to meet the specific and rigorous requirements of aircraft and spacecraft. These tailored solutions address unique airflow management needs, accommodate complex structural integrations, and adhere to stringent weight and material specifications. The increasing demand for optimized aerospace systems has paved the way for innovative manufacturing technologies, with metal 3D 프린팅 emerging as a powerful tool for producing high-performance, custom aerospace vents. This advanced manufacturing approach offers unprecedented design freedom, the ability to utilize lightweight yet robust materials, and the potential for rapid iteration and production of intricate geometries that were once considered unachievable with traditional methods. As the aerospace industry continues to push the boundaries of innovation, the role of metal 3D printing in delivering bespoke ventilation solutions is becoming increasingly significant, offering engineers and procurement managers a pathway to achieve superior performance and efficiency in their designs. At Metal3DP, we understand the critical nature of aerospace components and are dedicated to providing cutting-edge metal additive manufacturing solutions that meet the exacting standards of this demanding industry.
What are Custom Aerospace Vents Used For?
Custom-designed vents in aerospace applications serve a multitude of critical functions, each tailored to the specific needs of the aircraft or spacecraft system. Their applications are far-reaching, impacting everything from the comfort of passengers to the operational reliability of sensitive electronic equipment. One primary use is cabin pressure regulation. Aircraft cabins require carefully controlled air pressure to ensure passenger comfort and safety at high altitudes. Custom vents are integral to these systems, allowing for the precise inflow and outflow of air to maintain the desired pressure levels throughout the flight. The design of these vents must consider factors such as airflow volume, noise reduction, and integration with the aircraft’s environmental control system.
Another crucial application lies in avionics cooling. Modern aircraft are equipped with a vast array of sophisticated electronic systems, which generate heat during operation. Overheating can lead to malfunctions and system failures, posing significant safety risks. Custom vents are strategically placed to facilitate efficient airflow and heat dissipation, ensuring that critical avionics components remain within their optimal operating temperature range. These vents often feature complex internal geometries designed to maximize heat transfer while minimizing weight and space requirements.
Furthermore, custom vents play a vital role in fluid management systems. This can include the venting of fuel tanks to regulate pressure changes due to temperature variations and altitude, as well as the management of hydraulic and other fluid systems. Proper venting is essential for the safe and efficient operation of these systems, preventing pressure build-up or vacuum conditions that could lead to damage or failure. The materials used for these vents must be compatible with the fluids they come into contact with and capable of withstanding the operational pressures and temperatures.
In addition to these core functions, custom aerospace vents are also used for:
- Air distribution: Ensuring even airflow throughout the cabin or specific compartments.
- 연기 추출: Removing potentially harmful gases or particles from the air.
- De-icing and anti-icing systems: Directing airflow to prevent ice formation on critical surfaces.
- Noise reduction: Designing vents to minimize aerodynamic noise entering the cabin.
The specific design and requirements for each of these applications necessitate a tailored approach, highlighting the limitations of off-the-shelf solutions. By leveraging the capabilities of metal 3D printing, companies like Metal3DP can produce vents with intricate internal channels, optimized airflow pathways, and seamless integration with surrounding structures, ultimately contributing to enhanced performance, safety, and efficiency in aerospace systems.
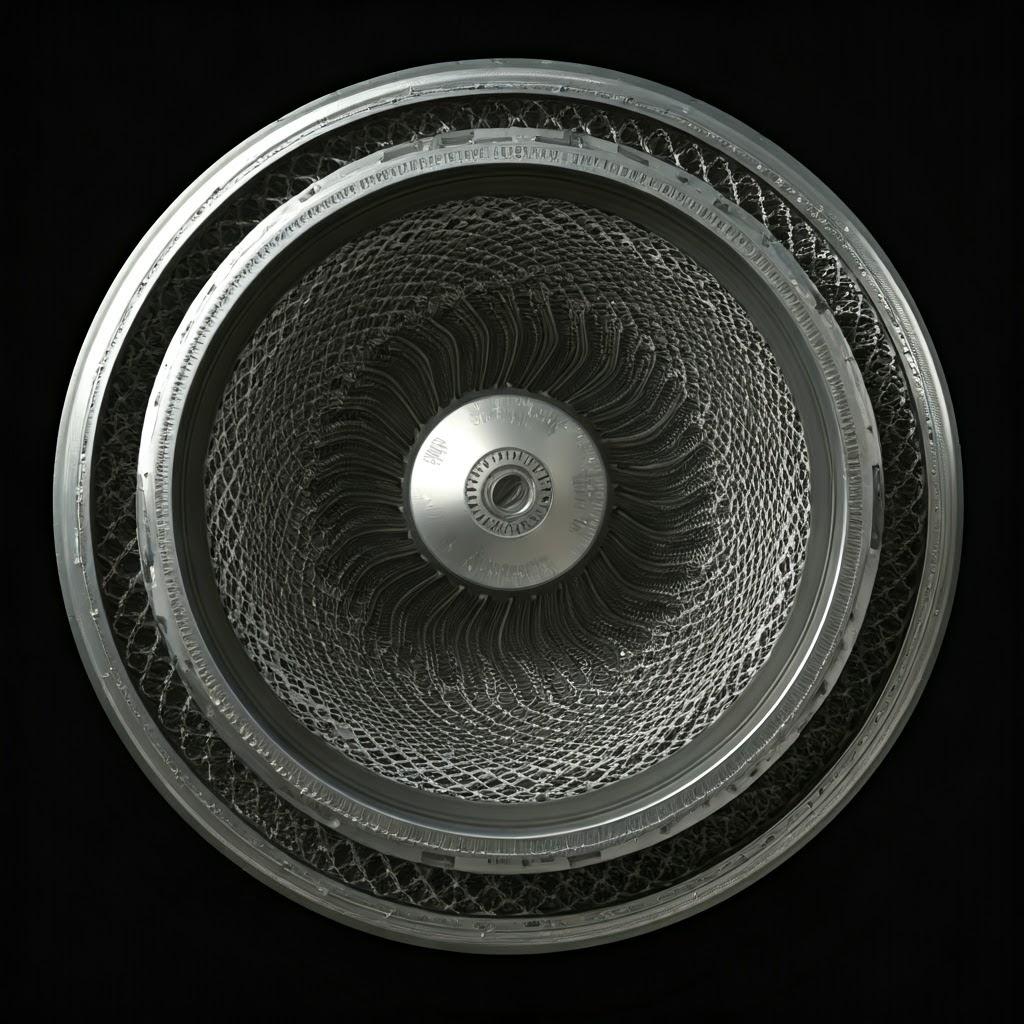
Why Use Metal 3D Printing for Custom Aerospace Vents?
The adoption of metal 3D printing for the production of custom aerospace vents offers a compelling array of advantages over traditional manufacturing methods, making it an increasingly attractive solution for the aerospace industry. One of the most significant benefits is 디자인의 자유. Additive manufacturing processes allow for the creation of complex geometries that would be difficult, if not impossible, to achieve with conventional techniques such as machining or casting. This enables engineers to design vents with optimized airflow characteristics, intricate internal structures for enhanced cooling or fluid management, and seamless integration features, leading to improved performance and reduced assembly requirements. For example, complex internal lattice structures can be incorporated to maximize strength while minimizing weight – a critical factor in aerospace applications.
재료 효율성 is another key advantage. Traditional subtractive manufacturing methods often involve removing a significant amount of material to achieve the final part shape, resulting in substantial waste. In contrast, metal 3D printing builds parts layer by layer, using only the material needed for the component. This not only reduces material costs but also conserves valuable resources, which is particularly important when working with expensive aerospace-grade alloys.
신속한 프로토 타입 capabilities offered by metal 3D printing are invaluable in the aerospace industry’s fast-paced development cycles. The ability to quickly iterate on designs and produce functional prototypes allows engineers to test and refine their concepts efficiently, significantly reducing lead times compared to traditional tooling-dependent methods. This agility accelerates the design process and enables faster time-to-market for new aerospace technologies.
Furthermore, metal 3D printing facilitates functional integration. Complex assemblies can often be consolidated into a single 3D-printed part, eliminating the need for multiple components and fasteners. This reduces weight, simplifies assembly processes, and enhances the reliability of the final product by minimizing potential failure points. For custom aerospace vents, this could mean integrating mounting features, flow guides, and structural elements directly into the vent design.
생산할 수 있는 능력 on-demand and low-volume production runs is also a significant advantage. Aerospace often requires highly specialized parts in limited quantities. Metal 3D printing eliminates the need for expensive tooling, making it economically viable to produce small batches or even individual custom vents tailored to specific aircraft or mission requirements.
에서 Metal3DP, we utilize advanced metal 3D printing technologies that empower our clients in the aerospace sector to leverage these benefits fully. Our state-of-the-art equipment and expertise in materials like AlSi10Mg and Scalmalloy® enable the creation of high-performance, custom aerospace vents that meet the stringent demands of the industry.
Recommended Materials and Why They Matter
The selection of the appropriate material is paramount when 3D printing custom aerospace vents, as the material properties directly impact the performance, durability, and safety of the component in demanding aerospace environments. Metal3DP recommends AlSi10Mg 및 스칼말로이® as excellent choices for these applications due to their exceptional characteristics.
AlSi10Mg is a widely used aluminum alloy in metal 3D printing, renowned for its lightweight nature combined with good strength and thermal conductivity. In the context of aerospace vents, its low density is crucial for minimizing overall aircraft weight, which directly translates to improved fuel efficiency and performance. The good thermal conductivity of AlSi10Mg makes it suitable for vents involved in cooling systems, effectively dissipating heat from sensitive electronics. Furthermore, this alloy exhibits good corrosion resistance, an essential property for aerospace components that may be exposed to various environmental conditions. Its mechanical properties, including high tensile strength and hardness, ensure the vent can withstand the operational stresses encountered during flight.
스칼말로이®, on the other hand, is a high-performance aluminum-magnesium-scandium alloy specifically developed for additive manufacturing applications requiring exceptional strength-to-weight ratio. This material offers significantly higher strength compared to conventional aluminum alloys while maintaining a low density. For aerospace vents, particularly those in critical structural or high-stress areas, Scalmalloy® provides a superior solution for weight reduction without compromising on structural integrity. Its excellent fatigue resistance is also a significant advantage for components subjected to cyclic loading during flight. While potentially more expensive than AlSi10Mg, the enhanced performance characteristics of Scalmalloy® can justify its use in demanding applications where weight savings and high strength are paramount.
The table below summarizes the key properties of these recommended powders:
속성 | AlSi10Mg | 스칼말로이® | Relevance to Aerospace Vents |
---|---|---|---|
밀도 | ~2.7g/cm³ | ~2.67 g/cm³ | Lightweighting is crucial for fuel efficiency and performance. Both alloys offer low density. |
Tensile Strength (UTS) | ~450 MPa (as-built) | ~520 MPa (as-built) – Can be higher with HT | Ensures the vent can withstand operational stresses. Scalmalloy® offers superior strength. |
수율 강도 | ~240 MPa (as-built) | ~455 MPa (as-built) – Can be higher with HT | Indicates the material’s resistance to permanent deformation under load. Scalmalloy® shows a significant advantage. |
휴식 시 신장 | ~4-10% (as-built) | ~11-13% (as-built) – Can be higher with HT | Measures the ductility of the material, important for impact resistance. |
열 전도성 | ~130-160 W/m·K | ~140W/m-K | Important for vents involved in cooling applications. AlSi10Mg offers good thermal conductivity. |
내식성 | 양호 | 양호 | Essential for aerospace components exposed to various environmental conditions. |
무게 대비 강도 비율 | 높음 | 매우 높음 | A critical factor in aerospace. Scalmalloy® excels in this aspect. |
일반적인 애플리케이션 | General structural parts, housings, manifolds | High-performance structural components, lightweight applications | Versatile for various vent applications; Scalmalloy® ideal for highly stressed, weight-sensitive components. |
시트로 내보내기
By offering these high-quality metal powders and leveraging our expertise in metal 3D printing, Metal3DP empowers aerospace engineers to design and manufacture custom vents with optimized performance characteristics tailored to their specific needs.
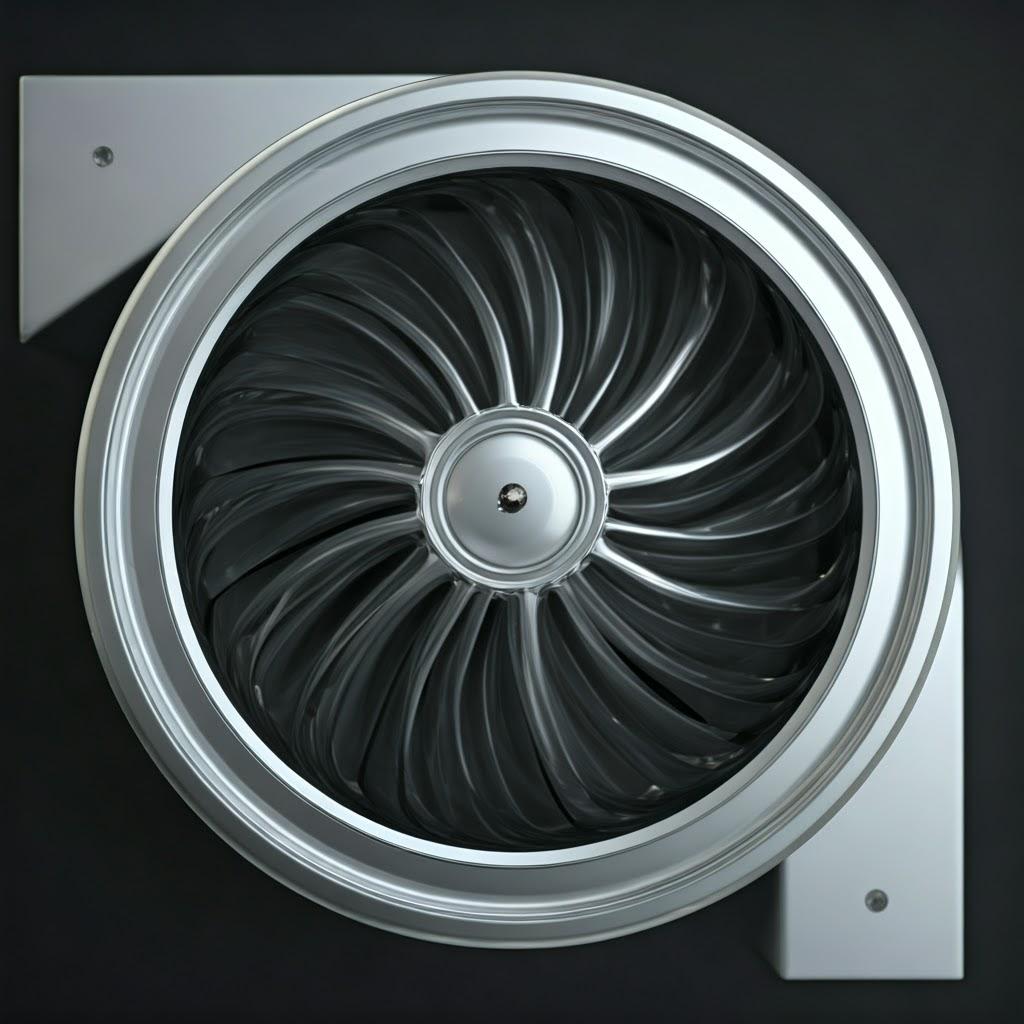
Design Considerations for Additive Manufacturing
Designing custom aerospace vents for metal 3D printing requires a shift in mindset compared to traditional manufacturing approaches. The layer-by-layer build process offers unique opportunities and imposes specific constraints that engineers must consider to optimize the final part for performance, cost-effectiveness, and manufacturability.
One of the primary design considerations is airflow optimization. The complex geometries achievable with metal 3D printing allow for the creation of internal channels and intricate flow paths that can significantly improve the efficiency and effectiveness of ventilation. Engineers can design vents with smooth, curved internal surfaces to minimize turbulence and pressure drop, or incorporate features like guide vanes to direct airflow precisely where it’s needed. Computational Fluid Dynamics (CFD) analysis plays a crucial role in simulating and optimizing these internal flow geometries before physical production.
Weight minimization is paramount in aerospace applications. Additive manufacturing enables the creation of lightweight designs through techniques like 토폴로지 최적화 and the incorporation of 격자 구조. Topology optimization uses algorithms to identify and remove material from low-stress areas of a part, resulting in a design that meets performance requirements with the minimum possible weight. Lattice structures, which are intricate, repeating geometric patterns, can fill the interior of a part, providing high stiffness and strength while significantly reducing mass. These techniques are particularly valuable for designing aerospace vents where every gram saved contributes to better fuel efficiency and overall aircraft performance.
Self-supporting structures should be a key consideration in the design process to minimize the need for support material during printing. Support structures are often required to prevent overhangs and unsupported areas from collapsing during the build process. While they are necessary in many cases, they add to material usage, increase build time, and require post-processing for removal, which can impact surface finish and dimensional accuracy. Designing parts with shallower overhang angles, incorporating self-supporting geometries, and strategically orienting the part on the build platform can reduce or eliminate the need for supports.
Feature integration is another significant advantage of metal 3D printing. Designers can integrate multiple functionalities into a single part, such as mounting features, fluid connectors, or sensors directly into the vent design. This reduces the number of individual components, simplifies assembly, and can improve the overall reliability of the system.
벽 두께 및 ribbing are important structural considerations. While thin walls can save weight, they must be sufficiently robust to withstand operational loads and pressures. Incorporating ribs or other stiffening features can provide the necessary structural integrity without significantly increasing weight.
Finally, 재료 선택 and its implications for the design must be considered from the outset. Different metal powders have varying mechanical properties, thermal characteristics, and processing requirements, which can influence the design choices. For instance, the minimum feature size and achievable tolerances can vary depending on the material and the printing process. Consulting with experts at Metal3DP early in the design phase can help optimize the vent design for the chosen material and the specific requirements of the aerospace application.
Tolerance, Surface Finish, and Dimensional Accuracy
In the aerospace industry, precision is non-negotiable. Custom aerospace vents must adhere to strict tolerance requirements to ensure proper fit, functionality, and integration with other critical systems. Metal 3D printing technologies have advanced significantly in their ability to achieve tight tolerances, but the actual achievable precision depends on several factors, including the printing process (e.g., Selective Laser Melting (SLM), Direct Metal Laser Sintering (DMLS)), the material used, the part geometry, and the post-processing steps.
Generally, metal 3D printed parts can achieve dimensional accuracies in the range of ±0.1 to ±0.5 mm, and sometimes even tighter tolerances with optimized parameters and post-machining. Features with critical interfaces may require post-processing, such as CNC machining, to achieve the exact specifications demanded by aerospace standards. When designing aerospace vents for metal 3D printing, it’s crucial to identify critical dimensions and tolerances early in the design phase and to communicate these requirements clearly to the 3D printing service provider, such as Metal3DP.
표면 마감 is another important consideration for aerospace vents. The as-built surface finish of metal 3D printed parts is typically rougher compared to parts produced by traditional machining. The surface roughness is influenced by the metal powder particle size, laser power, layer thickness, and build orientation. Typical surface roughness (Ra) values for SLM/DMLS parts can range from 5 to 20 $\mu$m. For many aerospace applications, this surface finish may need to be improved through post-processing techniques such as media blasting, polishing, or chemical etching to meet aerodynamic requirements, reduce friction, or enhance corrosion resistance. The specific surface finish requirements will depend on the vent’s application and its interaction with airflow or other fluids.
치수 정확도 refers to the degree to which the printed part matches the intended design dimensions. While metal 3D printing offers good overall accuracy, factors like material shrinkage during solidification and thermal stresses during the build process can lead to deviations. Careful process control, optimized build parameters, and accurate compensation for material shrinkage in the design phase are essential to achieving the desired dimensional accuracy. For complex geometries, it’s often beneficial to incorporate pilot holes or machining allowances in the design to allow for precise finishing of critical features after printing.
에서 Metal3DP, we employ rigorous quality control measures and utilize advanced 3D printing equipment to ensure that our custom aerospace vents meet the specified tolerance and dimensional accuracy requirements. We also offer a range of post-processing services to achieve the desired surface finish and final dimensions, ensuring that the parts are ready for integration into demanding aerospace systems.
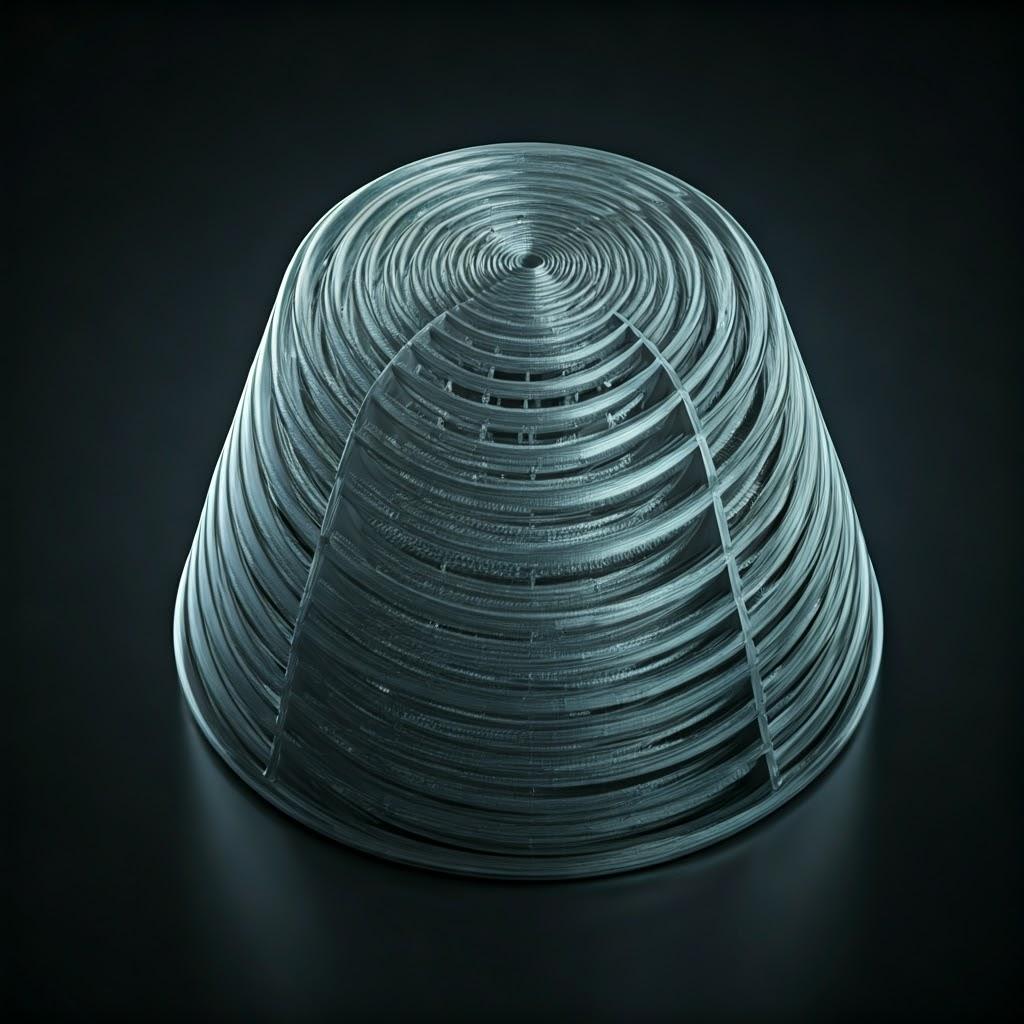
후처리 요구 사항
Metal 3D printed custom aerospace vents often require several post-processing steps to achieve the final desired properties, surface finish, and dimensional accuracy needed for aerospace applications. These steps are crucial for ensuring the parts meet the stringent requirements of the industry.
One of the initial post-processing steps is powder removal. After the printing process, loose metal powder remains within the internal channels and on the surface of the part. This powder needs to be carefully removed, especially from intricate internal geometries of vents. Techniques such as air blasting, ultrasonic cleaning, and vacuuming are commonly used for this purpose.
Stress relief heat treatment is often necessary to reduce residual stresses that build up during the rapid heating and cooling cycles of the 3D printing process. These residual stresses can lead to warping or cracking if not relieved. A controlled heat treatment cycle, tailored to the specific metal alloy, helps to improve the mechanical properties and dimensional stability of the printed vent.
Support structure removal is another essential step if the design required supports during printing. Supports are typically removed mechanically using tools like pliers or cutters, or through machining processes. The removal process must be carefully executed to avoid damaging the delicate features of the vent. In some cases, dissolvable support materials can be used to simplify removal.
표면 마감 is often required to achieve the desired surface roughness. Techniques include:
- Media blasting: Using abrasive particles propelled by air to create a uniform matte finish and remove partially sintered powder.
- 연마: Employing mechanical or chemical methods to achieve a smoother surface, which may be necessary for aerodynamic performance or aesthetic reasons.
- Chemical etching: Using chemical solutions to remove a thin layer of material from the surface, resulting in a smoother finish.
CNC 가공 may be necessary for achieving very tight tolerances on critical features, such as mounting interfaces or fluid connections. While 3D printing can produce complex shapes, machining can provide the precision required for specific functional surfaces. Often, a hybrid approach is used where the basic shape is 3D printed, and critical features are then machined to final dimensions.
코팅 can be applied to enhance the performance and durability of the aerospace vents. These may include:
- Anodizing: For aluminum alloys, to improve corrosion resistance and wear properties.
- Painting: For aesthetic purposes or additional environmental protection.
- Specialized coatings: To provide thermal barrier properties, wear resistance, or other specific functionalities.
Inspection and quality control are the final critical post-processing steps. This includes dimensional checks, non-destructive testing (NDT) such as dye penetrant inspection or X-ray inspection to identify any internal defects, and material analysis to ensure the printed part meets the required specifications. For aerospace applications, rigorous quality assurance processes are paramount.
에서 Metal3DP, we offer comprehensive post-processing services to ensure that our 3D printed metal aerospace vents meet the highest standards of quality and performance required by the aerospace industry. Our expertise in heat treatment, surface finishing, machining, and coatings allows us to deliver готовые к использованию components that are ready for integration into critical aerospace systems.
Common Challenges and How to Avoid Them
While metal 3D printing offers numerous advantages for producing custom aerospace vents, several common challenges can arise during the process. Understanding these challenges and implementing appropriate strategies to avoid them is crucial for achieving high-quality, reliable parts.
One common challenge is warping and distortion. These issues can occur due to the high thermal gradients and residual stresses generated during the layer-by-layer build process. Thin walls and large flat areas are particularly susceptible to warping.
- How to avoid it: Optimize part orientation on the build platform to minimize unsupported areas and reduce the build height. Employ strategic placement of support structures to anchor the part and prevent deformation. Utilize optimized build parameters, such as laser power and scan strategies, to reduce thermal stresses. Stress relief heat treatment after printing is also essential to mitigate residual stresses.
Another challenge is inconsistent material properties. Variations in density, porosity, and microstructure can occur if the printing parameters are not properly controlled, leading to parts that do not meet the required mechanical properties.
- How to avoid it: Use well-calibrated 3D printers and establish optimized and consistent build parameters for the chosen metal powder. Ensure a stable printing environment with controlled temperature and humidity. Employ in-process monitoring techniques to detect and correct any deviations during the build. Partner with reputable material suppliers like those providing powders for Metal3DP to ensure consistent powder quality.
지원 제거 can be challenging, especially for complex internal geometries. Improper support removal can damage the part’s surface or delicate features.
- How to avoid it: Design parts with self-supporting geometries whenever possible. Optimize the design and placement of support structures for easy removal. Consider using dissolvable support materials for intricate internal channels. Employ skilled technicians for support removal and use appropriate tools to minimize the risk of damage.
Achieving tight tolerances and desired surface finish can be difficult with the as-built parts. Aerospace applications often demand high precision and smooth surfaces.
- How to avoid it: Design parts with machining allowances for critical features that require tight tolerances. Utilize appropriate post-processing techniques such as CNC machining, grinding, polishing, or chemical etching to achieve the desired surface finish and dimensional accuracy. Work with a 3D printing service provider that has expertise in post-processing, like Metal3DP.
다공성 within the printed part can compromise its strength and fatigue resistance, which are critical for aerospace components.
- How to avoid it: Optimize build parameters, including laser power, scan speed, and layer thickness, to ensure full melting and fusion of the metal powder. Use high-quality metal powders with good flowability and sphericity. Employ inert build atmospheres to prevent oxidation and contamination. Hot Isostatic Pressing (HIP) can be used as a post-processing step to reduce porosity and further enhance mechanical properties.
By understanding these common challenges and implementing the recommended avoidance strategies, aerospace engineers and procurement managers can effectively leverage metal 3D printing to produce high-quality, custom aerospace vents that meet the demanding requirements of the industry.
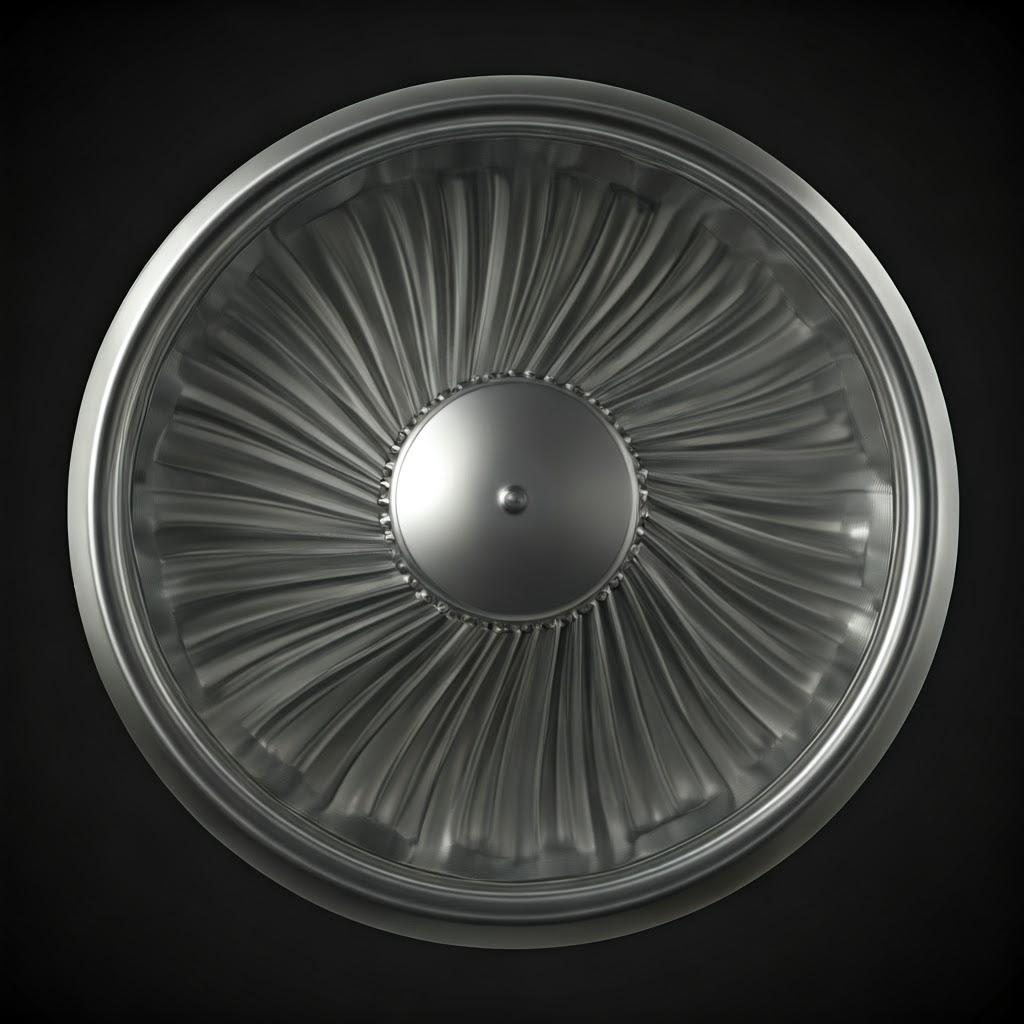
How to Choose the Right Metal 3D Printing Service Provider
Selecting the right metal 3D printing service provider is a critical decision for aerospace companies looking to produce custom vents. The quality, reliability, and performance of these components directly impact the safety and efficiency of aircraft and spacecraft. Therefore, a thorough evaluation of potential providers is essential. Here are key criteria to consider:
Certifications and Standards: Ensure the service provider holds relevant industry certifications, such as AS9100 for aerospace quality management systems. This certification indicates a commitment to stringent quality standards and processes required for aerospace components. Inquire about their adherence to other relevant aerospace standards and regulatory requirements.
소재 전문성: The provider should have extensive experience working with the specific metal alloys required for your application, such as AlSi10Mg and Scalmalloy®. They should possess a deep understanding of the material properties, processing parameters, and post-processing requirements for these materials to ensure optimal performance of the printed vents. Metal3DP boasts comprehensive expertise in a wide range of high-performance metal powders tailored for aerospace applications.
Technology and Equipment: Evaluate the type and capabilities of the metal 3D printing equipment the provider uses. Advanced machines with precise control over build parameters and robust monitoring systems are crucial for achieving high accuracy and repeatability. Consider the build volume capacity if your vent designs are large.
Quality Control Processes: A reliable service provider will have robust quality control procedures in place, including in-process monitoring, post-build inspection, and material testing. They should be able to provide detailed inspection reports and material certifications to ensure the printed vents meet the required specifications.
Post-Processing Capabilities: As discussed earlier, post-processing is often essential for aerospace vents. Ensure the provider offers a comprehensive range of services, including stress relief heat treatment, support removal, surface finishing (e.g., polishing, media blasting), CNC machining for tight tolerances, and specialized coatings. An in-house capability for these services can streamline the production process and ensure better quality control.
Experience and Portfolio: Review the provider’s track record and experience in serving the aerospace industry. Ask for case studies or examples of similar projects they have undertaken. A provider with a proven history of producing high-quality aerospace components is a more reliable choice.
Design Optimization Support: A valuable service provider will offer expertise in designing for additive manufacturing (DfAM). They should be able to provide guidance on optimizing your vent designs for metal 3D printing to improve performance, reduce weight, and enhance manufacturability. Collaboration with their engineering team can be highly beneficial.
Communication and Customer Support: Effective communication and responsive customer support are crucial for a smooth and successful project. The provider should be readily available to answer your questions, provide updates, and address any concerns promptly.
Lead Times and Production Capacity: Discuss the typical lead times for similar projects and assess their production capacity to ensure they can meet your project timelines and potential future volume requirements.
By carefully considering these factors, you can select a metal 3D printing service provider that aligns with your specific needs and ensures the production of high-quality, custom aerospace vents. Metal3DP is committed to providing industry-leading metal additive manufacturing solutions with a focus on quality, accuracy, and reliability for mission-critical aerospace parts. Our expertise in advanced metal powders and state-of-the-art printing technology makes us a trusted partner for the aerospace industry.
Cost Factors and Lead Time
Understanding the cost factors and lead time associated with metal 3D printing custom aerospace vents is essential for effective project planning and budgeting. Several elements influence the overall cost and the time required to produce these components.
비용 요소:
- 재료비: The cost of the metal powder is a significant factor. Aerospace-grade alloys like AlSi10Mg and Scalmalloy® can vary in price. The quantity of material used, which is influenced by the part’s volume and the amount of support material required, will directly impact the material cost. Optimized designs utilizing topology optimization and lattice structures can help minimize material usage.
- 구축 시간: The time it takes to print a part depends on its size, complexity, and the chosen layer thickness. Longer build times translate to higher machine operating costs. Optimizing part orientation and minimizing the build height can help reduce build time.
- 후처리 비용: The extent of post-processing required will affect the final cost. Simple steps like powder removal will have a minimal impact, while more complex processes like extensive machining, multiple surface finishing steps, and specialized coatings will add to the overall expense.
- 인건비: The cost of labor involved in design optimization, print setup, machine operation, post-processing, and quality control will be factored into the total price.
- Equipment and Overhead Costs: The service provider’s investment in equipment, maintenance, and operational overhead will also be reflected in their pricing.
- Quantity and Volume: While metal 3D printing is often cost-effective for low to medium volumes and complex geometries, higher production volumes may benefit from economies of scale. Discussing potential future needs with your provider is advisable.
리드 타임:
- Design and Optimization: The initial design phase, including any necessary optimization for additive manufacturing, will contribute to the overall lead time.
- Print Preparation and Scheduling: Once the design is finalized, there is time required for print preparation, including build plate setup and machine scheduling.
- 구축 시간: As mentioned earlier, the actual printing duration depends on the part’s characteristics.
- 후처리 시간: The time needed for post-processing steps can vary significantly depending on the complexity and number of operations required. Heat treatment, support removal, surface finishing, and machining can all add to the lead time.
- 품질 검사: Thorough quality inspection and testing are crucial for aerospace components and will add to the overall lead time.
- Shipping and Delivery: The final step is the shipping and delivery of the completed parts.
While traditional manufacturing methods for complex aerospace components can sometimes involve long lead times due to tooling and setup, metal 3D printing can offer faster turnaround times, especially for intricate, custom designs and low to medium production volumes. At Metal3DP, we strive to provide transparent cost estimates and realistic lead times, working closely with our clients to meet their project requirements efficiently. Factors such as design complexity, material availability, and the extent of post-processing will influence the final cost and delivery schedule.
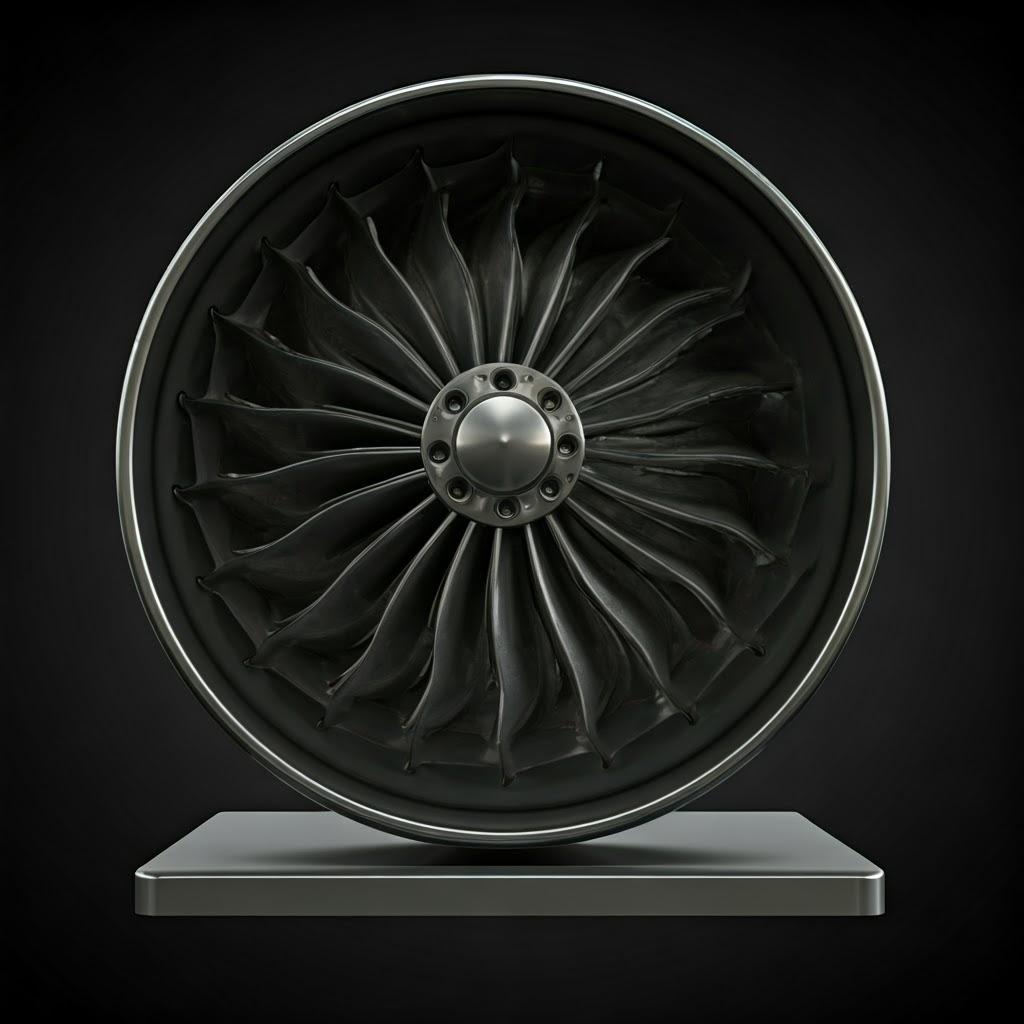
자주 묻는 질문(FAQ)
Q: What types of aerospace vents are best suited for metal 3D printing? A: Metal 3D printing is particularly well-suited for producing custom aerospace vents with complex internal geometries for optimized airflow or cooling, lightweight vents with intricate lattice structures, and integrated vents that combine multiple functionalities into a single part. It’s also ideal for low to medium volume production and rapid prototyping of new vent designs.
Q: Can metal 3D printed aerospace vents meet stringent aerospace material specifications and testing requirements? A: Yes, when the appropriate metal powders are used and the printing process is carefully controlled, metal 3D printed parts can meet or exceed many aerospace material specifications. Reputable service providers like Metal3DP provide material certifications and conduct rigorous testing to ensure compliance with industry standards. Post-processing techniques like Hot Isostatic Pressing (HIP) can further enhance material properties.
Q: How does the cost of metal 3D printed aerospace vents compare to traditionally manufactured vents? A: The cost comparison depends on several factors, including the complexity of the design, production volume, and material used. For highly complex geometries and low to medium volumes, metal 3D printing can often be more cost-effective than traditional methods that require expensive tooling. For very high production volumes of simpler designs, traditional methods might be more economical. However, the benefits of design freedom, rapid prototyping, and functional integration offered by 3D printing can provide significant overall value.
Q: What are the typical tolerances achievable with metal 3D printing for aerospace vents? A: Metal 3D printing can typically achieve tolerances in the range of ±0.1 to ±0.5 mm in the as-built condition. Tighter tolerances can be achieved through post-processing techniques like CNC machining. The achievable tolerance depends on the printing technology, material, and part geometry. Critical dimensions should be identified early in the design process.
Q: Is surface finishing required for metal 3D printed aerospace vents? A: Often, yes. The as-built surface finish of metal 3D printed parts is typically rougher than that achieved by machining. Depending on the application, surface finishing techniques like media blasting, polishing, or chemical etching may be required to meet aerodynamic requirements, reduce friction, or improve aesthetics.
Q: Can metal 3D printing be used for end-use production of aerospace vents, or is it limited to prototyping? A: Metal 3D printing is increasingly being used for end-use production of aerospace components, including vents. Advancements in material properties, process control, and post-processing techniques have made it a viable option for functional parts in commercial and military aircraft.
결론
The integration of metal 3D printing into the manufacturing of custom aerospace vents represents a significant leap forward for the aerospace industry. This transformative technology offers unparalleled design freedom, enabling the creation of complex geometries optimized for airflow, weight reduction, and functional integration. Materials like AlSi10Mg and Scalmalloy® provide the necessary strength-to-weight ratio and durability required for demanding aerospace applications.
While challenges such as achieving tight tolerances and desired surface finishes need careful consideration, advancements in printing processes and post-processing techniques are continuously expanding the capabilities of metal 3D printing. By partnering with experienced and certified service providers like Metal3DP, aerospace engineers and procurement managers can leverage the benefits of additive manufacturing to produce high-performance, custom vents that meet the stringent standards of the industry.
The ability to rapidly prototype, produce complex geometries, and optimize designs for specific applications makes metal 3D printing an invaluable tool for innovation in the aerospace sector. As the industry continues to push the boundaries of performance and efficiency, metal additive manufacturing will undoubtedly play an increasingly crucial role in shaping the future of aerospace component design and production. Contact Metal3DP today to explore how our cutting-edge metal 3D printing solutions can power your organization’s additive manufacturing goals in the aerospace industry.
공유
중국 칭다오에 본사를 둔 선도적인 적층 제조 솔루션 제공업체인 MET3DP Technology Co. 당사는 산업용 3D 프린팅 장비와 고성능 금속 분말을 전문으로 합니다.