AM 프로세스 종합 가이드
목차
매혹적인 세계로 오신 것을 환영합니다. AM 프로세스를 통해 기존 제조업의 경계를 끊임없이 허물고 있습니다. 이 가이드에서는 금속 분말 모델부터 응용 분야, 장단점 등 다양한 측면을 조명하며 적층 제조의 복잡성에 대해 자세히 살펴봅니다. 현대의 경이로운 제조 기술을 통해 흥미롭고 유익한 여행을 떠나보세요!
적층 제조 개요
3D 프린팅이라고도 불리는 적층 제조는 재료를 한 층씩 추가하여 3차원 물체를 만드는 프로세스입니다. 큰 블록에서 재료를 빼는 기존 제조 방식과 달리 적층 제조는 처음부터 물체를 제작하기 때문에 복잡한 디자인이 가능하고 낭비를 줄일 수 있습니다.
AM 프로세스의 주요 세부 사항
- 기술: 레이어별 재료 추가
- 사용된 재료: 금속, 폴리머, 세라믹 및 복합재
- 애플리케이션: 항공우주, 자동차, 헬스케어, 소비재 등
- 장점: 복잡한 형상, 낭비 감소, 사용자 지정 및 신속한 프로토타이핑
- 도전 과제: 재료의 한계, 표면 마감, 높은 초기 비용
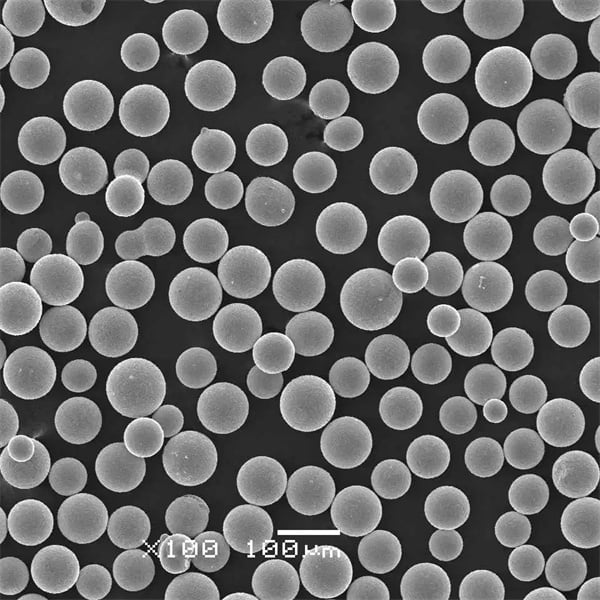
적층 제조에 사용되는 금속 분말의 종류
적층 가공 분야에서 금속 분말은 매우 중요한 구성 요소입니다. 가장 일반적으로 사용되는 금속 분말과 그 구성 및 고유한 특성을 살펴보겠습니다.
AM용 일반 금속 분말
금속분말 | 구성 | 속성 | 애플리케이션 |
---|---|---|---|
티타늄(Ti-6Al-4V) | 90% 티타늄, 6% 알루미늄, 4% 바나듐 | 고강도, 경량, 내식성 | 항공우주, 의료용 임플란트 |
스테인리스 스틸(316L) | 16-18% 크롬, 10-14% 니켈, 2-3% 몰리브덴 | 부식 방지, 내구성, 우수한 용접성 | 의료 기기, 식품 가공 |
알루미늄(AlSi10Mg) | 89-91% 알루미늄, 9-11% 실리콘, 0.2-0.4% 마그네슘 | 가볍고, 열전도율이 좋고, 강하고 | 자동차, 항공우주 |
인코넬(IN718) | 50-55% 니켈, 17-21% 크롬, 4.75-5.5% 니오븀 | 내열성, 고온에서의 높은 강도 | 터빈, 항공우주 부품 |
코발트-크롬(CoCr) | 55-65% 코발트, 27-30% 크롬, 5-7% 몰리브덴 | 내마모성, 생체 적합성, 높은 경도 | 치과 임플란트, 정형외과용 장치 |
구리(Cu) | 99.9% 구리 | 뛰어난 열 및 전기 전도성 | 전기 부품, 열교환기 |
공구강(H13) | 0.35-0.45% 탄소, 5-5.5% 크롬, 1-1.2% 몰리브덴 | 높은 경도, 내마모성, 우수한 가공성 | 금형, 금형, 절삭 공구 |
니켈 합금(하스텔로이 X) | 47-52% 니켈, 20.5-23% 크롬, 17-20% 철 | 산화 방지, 고온에서의 높은 강도 | 화학 처리, 항공 우주 |
마그네슘(AZ91D) | 8.5-9.5% 알루미늄, 0.6-1.4% 아연, 0.15% 망간 | 가볍고 우수한 중량 대비 강도 비율 | 자동차, 전자 |
텅스텐(W) | 99.95% 텅스텐 | 매우 높은 융점, 밀도, 강함 | 항공우주, 방위 애플리케이션 |
상세 금속 파우더 모델
- 티타늄(Ti-6Al-4V): 뛰어난 중량 대비 강도와 생체 적합성으로 잘 알려진 이 합금은 항공우주 및 의료 산업에서 필수적인 소재입니다. 피로와 부식에 대한 저항성이 뛰어나 중요한 부품에 이상적입니다.
- 스테인리스 스틸(316L): 다용도 합금인 316L 스테인리스 스틸은 내구성과 부식에 대한 저항성이 뛰어나다는 평가를 받고 있습니다. 의료 기기 및 식품 가공 장비와 같이 위생과 수명이 가장 중요한 환경에서 널리 사용됩니다.
- 알루미늄(AlSi10Mg): 이 합금은 가볍고 열전도율이 뛰어난 것으로 알려져 있습니다. 강도는 유지하면서 무게를 줄이는 것이 중요한 자동차 및 항공우주 분야에서 많이 사용됩니다.
- 인코넬(IN718): 극한의 온도와 기계적 응력을 견딜 수 있는 것으로 유명한 인코넬 718은 항공우주 산업에서 터빈 엔진 및 기타 고온 응용 분야에 광범위하게 사용됩니다.
- 코발트-크롬(CoCr): 이 생체 적합성 합금은 높은 경도와 내마모성으로 인해 의료용 임플란트에 적합합니다. 정형외과 및 치과 분야에서 수명과 신뢰성을 보장합니다.
- 구리(Cu): 구리는 열 및 전기 전도성이 뛰어나 효율적인 열 전달이 중요한 전기 엔지니어링 및 열교환기 애플리케이션에 필수적입니다.
- 공구강(H13): 금형 및 절삭 공구 제작에 이상적인 H13 공구강은 높은 경도와 내마모성을 제공하여 제조 공정에서 내구성과 정밀성을 보장합니다.
- 니켈 합금(하스텔로이 X): 이 합금은 고온 환경에서 탁월하며 산화에 강하고 강도를 유지합니다. 극한 조건에서의 신뢰성이 필수적인 화학 공정 및 항공 우주 분야에 사용됩니다.
- 마그네슘(AZ91D): 가장 가벼운 구조용 금속 중 하나인 마그네슘 AZ91D는 자동차 및 전자 산업과 같이 경량화가 중요한 곳에 사용되어 강도와 가벼움의 균형을 잘 맞추고 있습니다.
- 텅스텐(W): 놀랍도록 높은 융점과 밀도로 잘 알려진 텅스텐은 특히 극한 환경에 노출될 것으로 예상되는 항공우주 및 방위 산업 분야에서 없어서는 안 될 소재입니다.
적층 제조 공정의 응용
적층 가공의 다재다능함은 광범위한 응용 분야에 반영되어 있습니다. 여기에서는 AM을 활용하여 혁신의 한계를 뛰어넘는 다양한 산업 분야를 살펴봅니다.
AM 활용 산업
산업 | 애플리케이션 | 혜택 |
---|---|---|
항공우주 | 엔진 부품, 구조 부품, 툴링 | 경량 부품, 리드 타임 단축, 복잡한 형상 |
자동차 | 프로토타입, 맞춤형 부품, 경량 부품 | 설계 유연성, 신속한 프로토타입 제작, 무게 감소 |
헬스케어 | 임플란트, 보철물, 수술 기구 | 사용자 지정, 생체 적합성, 정밀한 형상 |
소비재 | 맞춤형 제품, 웨어러블 기술, 가전 제품 | 개인화, 온디맨드 생산, 재고 감소 |
아키텍처 | 스케일 모델, 맞춤형 구성 요소, 건설 도구 | 맞춤형 디자인, 신속한 생산, 재료 낭비 감소 |
교육 | 교구, 프로토타입 개발, 연구 | 실습 학습, 혁신적인 디자인, 비용 효율적인 프로토타이핑 |
방어 | 경량 갑옷, 무기 부품, 현장 수리 도구 | 내구성, 맞춤화, 신속한 제조 |
에너지 | 터빈 부품, 열교환기, 파이프라인 | 고성능, 재료 효율성, 복잡한 디자인 |
AM 공정의 장점
- 설계 유연성: AM을 사용하면 기존 방식으로는 불가능하거나 비용이 많이 드는 복잡하고 정교한 디자인을 제작할 수 있습니다.
- 사용자 지정: 개인의 필요에 따라 제품을 맞춤 제작할 수 있어 의료용 임플란트 및 맞춤형 부품에 이상적입니다.
- 폐기물 감소: 재료가 한 층씩 추가되어 감산 제조 공정에 비해 낭비를 최소화합니다.
- 신속한 프로토타이핑: AM을 사용하면 설계를 빠르게 반복하고 테스트하여 개발 주기를 단축할 수 있습니다.
- 경량 구조: 적층 가공은 항공우주 및 자동차 산업에서 매우 중요한 경량 부품을 생산할 수 있습니다.
적층 제조 공정의 단점
- 재료 제한: 모든 재료가 3D 프린팅에 적합한 것은 아니므로 적용 가능한 범위가 제한됩니다.
- 표면 마감: 적층 가공으로 생산된 부품은 원하는 표면 품질을 얻기 위해 후처리가 필요한 경우가 많습니다.
- 초기 비용: 적층 제조 기술과 재료에 대한 초기 투자 비용이 높기 때문에 소규모 운영에서는 접근성이 떨어질 수 있습니다.
- 생산 속도: 적층 가공은 복잡성과 맞춤화 측면에서 탁월하지만 대량 생산 시 기존 대량 생산 방식에 비해 속도가 느릴 수 있습니다.
AM 금속 분말 비교
다양한 매개 변수에 걸쳐 이러한 금속 분말이 서로 어떻게 쌓이는지 자세히 살펴보겠습니다.
금속분말 | 힘 | 무게 | 내식성 | 내열성 | 비용 |
---|---|---|---|---|---|
티타늄(Ti-6Al-4V) | 높음 | 빛 | 우수 | 양호 | 높음 |
스테인리스 스틸(316L) | 보통 | 무거운 | 우수 | 보통 | 보통 |
알루미늄(AlSi10Mg) | 보통 | 매우 가벼움 | 양호 | 보통 | 낮음 |
인코넬(IN718) | 매우 높음 | 무거운 | 양호 | 우수 | 매우 높음 |
코발트-크롬(CoCr) | 높음 | 무거운 | 우수 | 양호 | 높음 |
구리(Cu) | 낮음 | 무거운 | Poor | Poor | 낮음 |
공구강(H13) | 높음 | 무거운 | 보통 | 보통 | 보통 |
니켈 합금(하스텔로이 X) | 높음 | 무거운 | 양호 | 우수 | 매우 높음 |
마그네슘(AZ91D) | 낮음 | 매우 가벼움 | Poor | Poor | 낮음 |
텅스텐(W) | 매우 높음 | 매우 무겁다 | 우수 | 우수 | 매우 높음 |
공급업체 및 가격 세부 정보
적층 제조용 금속 분말을 소싱할 때는 주요 공급업체와 가격을 파악하는 것이 중요합니다. 자세한 내용은 다음과 같습니다:
공급업체 | 금속분말 | 가격(kg당) | 연락처 세부 정보 |
---|---|---|---|
회가나스 AB | 티타늄(Ti-6Al-4V) | $300 | www.hoganas.com |
샌드빅 | 스테인리스 스틸(316L) | $150 | www.materials.sandvik |
EOS GmbH | 알루미늄(AlSi10Mg) | $100 | www.eos.info |
카펜터 기술 | 인코넬(IN718) | $400 | www.carpentertechnology.com |
Arcam AB | 코발트-크롬(CoCr) | $350 | www.arcam.com |
GKN 회가나에 | 구리(Cu) | $50 | www.gknpm.com |
뵐러 우드데홀름 | 공구강(H13) | $120 | www.bohler-uddeholm.com |
헤인즈 인터내셔널 | 니켈 합금(하스텔로이 X) | $450 | www.haynesintl.com |
고급 분말 및 코팅(AP&C) | 마그네슘(AZ91D) | $80 | www.advancedpowders.com |
버팔로 텅스텐 Inc. | 텅스텐(W) | $500 | www.buffalotungsten.com |
AM 프로세스의 장단점
모든 기술에는 장단점이 있습니다. 다음은 적층 제조 공정의 장단점을 자세히 비교한 것입니다:
측면 | 장점 | 제한 사항 |
---|---|---|
디자인 | 복잡한 지오메트리, 사용자 정의 허용 | 재료 특성에 따른 제한 |
자료 사용량 | 낭비 감소, 효율적인 사용 | 사용 가능한 재료의 범위 제한 |
프로덕션 | 신속한 프로토타이핑, 온디맨드 생산 | 대용량일 경우 느림 |
비용 | 툴링 비용 절감, 자재 낭비 감소 | 높은 초기 투자 비용 |
유연성 | 손쉬운 디자인 수정, 다양한 애플리케이션 | 후처리가 필요한 경우가 많습니다. |
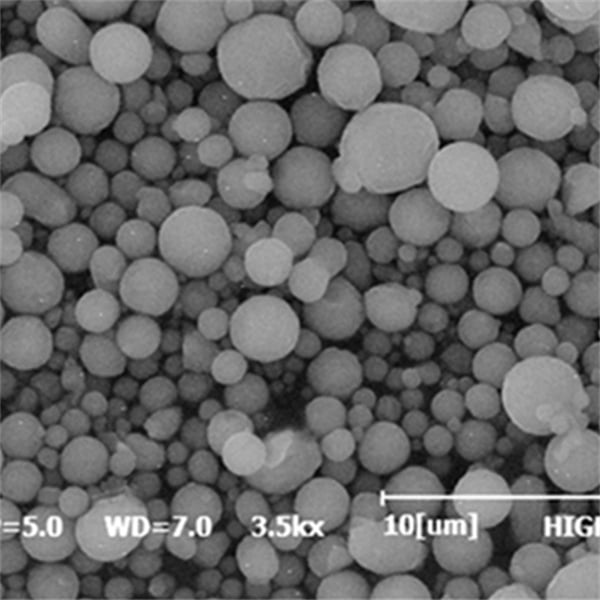
자주 묻는 질문
AM 프로세스에 대한 몇 가지 일반적인 질문을 통해 의구심을 해소해 보겠습니다.
질문 | 답변 |
---|---|
적층 제조(AM)란 무엇인가요? | 3D 프린팅은 재료를 층층이 쌓아 올려 물체를 만드는 방식으로, 복잡한 디자인이 가능하고 폐기물을 줄일 수 있습니다. |
AM에 사용할 수 있는 재료는 무엇인가요? | 금속, 폴리머, 세라믹, 복합재 등 다양한 소재를 사용할 수 있습니다. |
AM의 주요 장점은 무엇인가요? | AM은 설계 유연성, 맞춤화, 낭비 감소, 신속한 프로토타이핑, 경량 구조물 제작 기능을 제공합니다. |
AM에 제한이 있나요? | 예, 재료 제한, 표면 마감 문제, 높은 초기 비용, 대량 생산 시 느린 생산 속도 등의 한계가 있습니다. |
AM의 혜택을 가장 많이 받는 산업은 무엇인가요? | 항공우주, 자동차, 의료, 소비재, 건축, 교육, 국방, 에너지 산업은 AM의 혜택을 크게 누리고 있습니다. |
AM은 기존 제조업과 어떻게 다른가요? | 적층 가공은 낭비가 적은 복잡한 맞춤형 부품을 제작하는 데 탁월하지만 기존 대량 생산 방식에 비해 초기에는 속도가 느리고 비용이 많이 들 수 있습니다. |
적층 가공에 사용되는 일반적인 금속 분말에는 어떤 것이 있나요? | 일반적인 금속 분말에는 티타늄(Ti-6Al-4V), 스테인리스 스틸(316L), 알루미늄(AlSi10Mg), 인코넬(IN718), 코발트-크롬(CoCr) 등이 있습니다. |
AM을 대량 생산에 사용할 수 있나요? | 적층 가공은 프로토타이핑 및 맞춤형 부품 제작에 이상적이지만, 일반적으로 기존 방식에 비해 대량 생산에는 속도가 느리고 비용 효율성이 떨어집니다. |
AM 부품에는 어떤 후처리가 필요합니까? | 후처리에는 원하는 품질과 특성을 얻기 위한 표면 마감, 열처리, 기계 가공, 코팅 등이 포함될 수 있습니다. |
AM 재료의 비용은 기존 재료와 어떻게 비교되나요? | 3D 프린팅 재료는 특수한 특성으로 인해 더 비쌀 수 있지만, 폐기물 및 툴링 비용 절감을 통해 비용 절감을 실현할 수 있습니다. |
결론
적층 제조는 설계와 생산에 접근하는 방식을 혁신적으로 변화시키며 탁월한 유연성과 효율성을 제공합니다. 항공우주부터 의료 분야에 이르기까지 적층 제조의 적용 분야는 매우 광범위하고 다양합니다. 극복해야 할 과제도 있지만 이 혁신적인 기술의 장점은 분명합니다. 이 분야가 계속 발전함에 따라 더욱 흥미로운 발전과 산업 전반에 걸친 광범위한 채택을 기대할 수 있습니다.
공유
중국 칭다오에 본사를 둔 선도적인 적층 제조 솔루션 제공업체인 MET3DP Technology Co. 당사는 산업용 3D 프린팅 장비와 고성능 금속 분말을 전문으로 합니다.
관련 기사
Met3DP 소개
최근 업데이트
제품
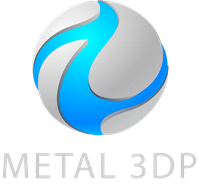
3D 프린팅 및 적층 제조용 금속 분말