Conformal Cooling Plates
목차
Introduction to Aerospace Conformal Cooling Plates
In the demanding realm of aerospace engineering, thermal management stands as a critical factor influencing the performance, efficiency, and longevity of various components. Among the sophisticated solutions employed for heat dissipation, conformal cooling plates have emerged as a highly effective technology. These intricately designed structures are engineered to match the complex geometries of heat-generating components, ensuring efficient heat transfer and maintaining optimal operating temperatures. By precisely following the contours of the device they are cooling, conformal cooling plates offer significant advantages over traditional cooling methods, particularly in applications where space and weight are at a premium. This blog post delves into the world of aerospace conformal cooling plates, exploring their importance, the transformative role of metal 3D 프린팅 in their manufacturing, and the key material considerations for achieving peak performance. At Metal3DP, we understand the critical nature of thermal management in aerospace and offer advanced metal additive manufacturing solutions to produce high-quality, custom conformal cooling plates.
The Critical Role of Conformal Cooling Plates in Aerospace Applications
Aerospace applications subject components to extreme operational conditions, characterized by high power densities and stringent reliability requirements. Effective thermal management is paramount to prevent overheating, which can lead to performance degradation, material failure, and ultimately, mission compromise. Conformal cooling plates play a vital role in a multitude of aerospace systems, including:
- Avionics and Electronics Cooling: Dissipating heat generated by sophisticated electronic systems, ensuring their continuous and reliable operation during flight.
- Engine Component Cooling: Managing the intense heat produced by engine parts, such as combustion chambers and turbine blades, to enhance efficiency and extend lifespan.
- Actuator and Hydraulic System Cooling: Maintaining optimal temperatures for hydraulic actuators and systems, crucial for flight control and other critical functions.
- 열교환기: Facilitating efficient heat transfer in various onboard systems, contributing to overall energy efficiency.
- Satellite and Spacecraft Thermal Management: Regulating the temperature of sensitive instruments and systems in the harsh thermal environment of space.
The ability of conformal cooling plates to closely integrate with the shape of the heat source allows for maximized contact area and minimized thermal resistance. This leads to more efficient heat extraction compared to conventional flat or geometrically limited cooling solutions. The intricate channels within these plates can be designed to optimize fluid flow and heat transfer rates, contributing to lighter and more compact overall system designs – a significant advantage in aerospace, where weight savings directly translate to fuel efficiency and payload capacity. Aerospace engineers and procurement managers recognize the value of these advanced cooling solutions in pushing the boundaries of performance and reliability. Companies like Metal3DP are at the forefront of providing the manufacturing expertise to realize these complex designs.
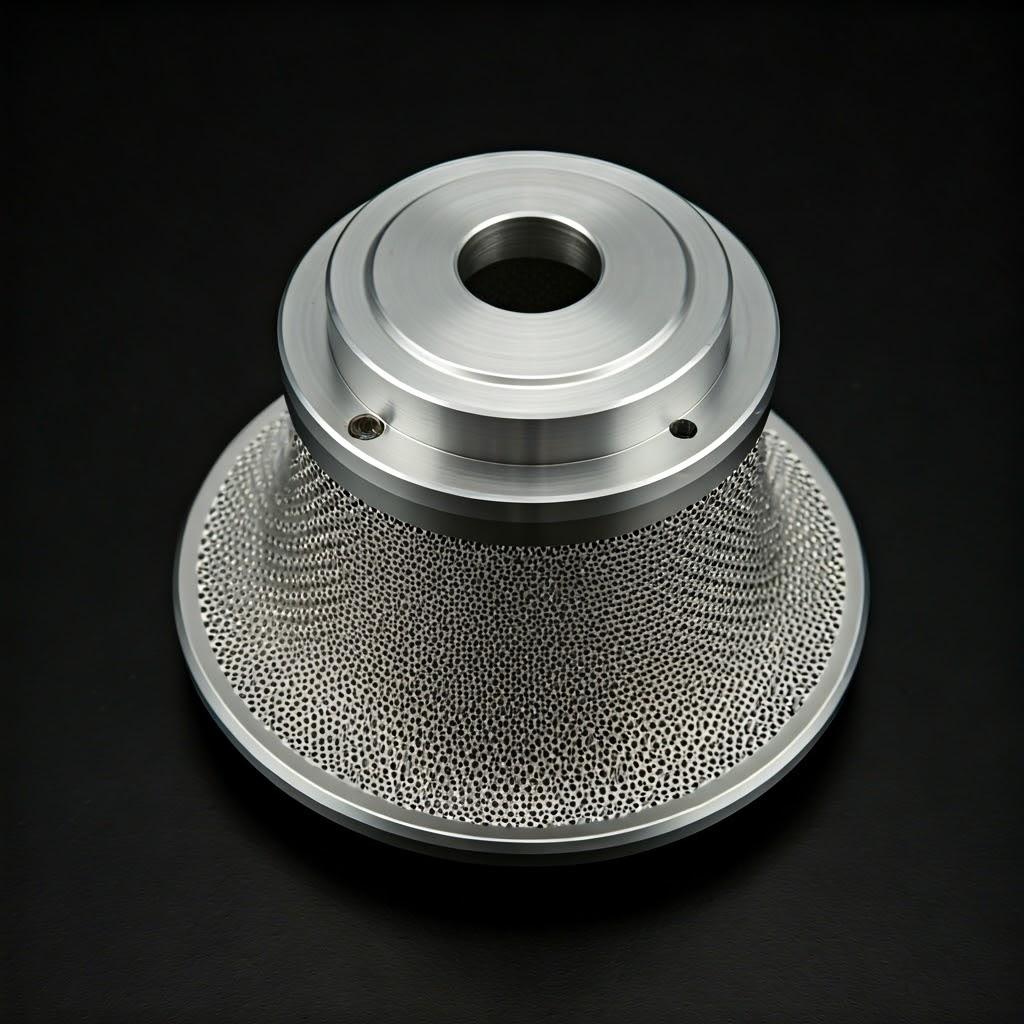
Why Metal 3D Printing is Revolutionizing Aerospace Cooling Plate Manufacturing
Traditional manufacturing methods often struggle to produce the complex internal channels and intricate geometries required for effective conformal cooling plates. These limitations can result in designs that are less efficient, heavier, or require multiple assembled components, increasing the risk of failure points. Metal 3D printing, also known as metal additive manufacturing, offers a paradigm shift in the fabrication of these critical components by enabling the creation of highly complex shapes directly from digital designs. The advantages of using metal 3D printing for aerospace conformal cooling plates are numerous:
- 자유로운 디자인: Additive manufacturing processes, such as Selective Laser Melting (SLM) and Direct Metal Laser Sintering (DMLS), allow for the creation of intricate internal cooling channels that precisely follow the contours of the component being cooled. This level of design freedom is virtually impossible to achieve with traditional methods like machining or casting.
- 토폴로지 최적화: 3D printing facilitates the implementation of topology optimization, a design approach that removes material from non-critical areas while maintaining structural integrity and thermal performance. This results in lighter cooling plates with enhanced efficiency.
- 조립 감소: Complex cooling channel networks can be integrated into a single part, eliminating the need for brazing or welding multiple components. This reduces weight, potential leak points, and manufacturing complexity.
- 신속한 프로토타이핑 및 반복: Metal 3D printing enables rapid prototyping, allowing engineers to quickly test and refine cooling plate designs, significantly accelerating the development cycle. This agility is crucial in the fast-paced aerospace industry.
- Customization and Low-Volume Production: Additive manufacturing is well-suited for producing customized cooling solutions and low-volume production runs, which are often required for specific aerospace applications or niche markets.
Metal3DP leverages advanced metal 3D printing technologies and our expertise in materials science to manufacture high-performance conformal cooling plates tailored to the unique demands of the aerospace sector. Our industry-leading print volume and accuracy ensure the production of reliable and efficient cooling solutions. You can learn more about our metal 3D printing capabilities on our 금속 3D 프린팅 페이지.
Material Selection: Understanding AlSi10Mg and IN625 for Optimal Performance
The choice of material is paramount in determining the performance and reliability of aerospace conformal cooling plates. The material must possess a combination of high thermal conductivity, strength-to-weight ratio, corrosion resistance, and compatibility with the operating environment. Metal3DP recommends AlSi10Mg and IN625 as excellent powder options for manufacturing these critical components due to their specific properties:
AlSi10Mg (Aluminum Silicon Magnesium):
- 높은 열전도율: Aluminum alloys, including AlSi10Mg, exhibit excellent thermal conductivity, facilitating efficient heat transfer away from the heat source.
- 가벼움: Aluminum’s low density contributes to significant weight savings, a crucial factor in aerospace applications where every gram counts.
- 우수한 중량 대비 강도 비율: AlSi10Mg offers a good balance of strength and weight, making it suitable for structural cooling components.
- 뛰어난 인쇄성: This alloy is well-established in laser powder bed fusion processes, offering good surface finish and dimensional accuracy.
IN625 (Nickel-Chromium Alloy):
- 고온 강도: IN625 retains its mechanical properties at elevated temperatures, making it suitable for cooling components near engine parts or in high-temperature environments.
- 뛰어난 내식성: This nickel-based superalloy exhibits exceptional resistance to corrosion and oxidation, crucial for long-term reliability in harsh aerospace environments.
- Good Weldability and Fabricability: While typically more challenging to print than AlSi10Mg, advancements in metal 3D printing processes at Metal3DP allow for the production of complex IN625 cooling plates with high integrity.
- 높은 강도와 연성: IN625 offers a high level of strength and ductility, ensuring the structural integrity of the cooling plate under demanding operational loads.
The selection between AlSi10Mg and IN625 depends on the specific application requirements, including operating temperature, weight constraints, and corrosion environment. Our team at Metal3DP can provide expert guidance on material selection to ensure optimal performance for your aerospace cooling plate needs. We utilize advanced powder making systems to ensure the high quality of our metal powders, as detailed on our 제품 페이지.
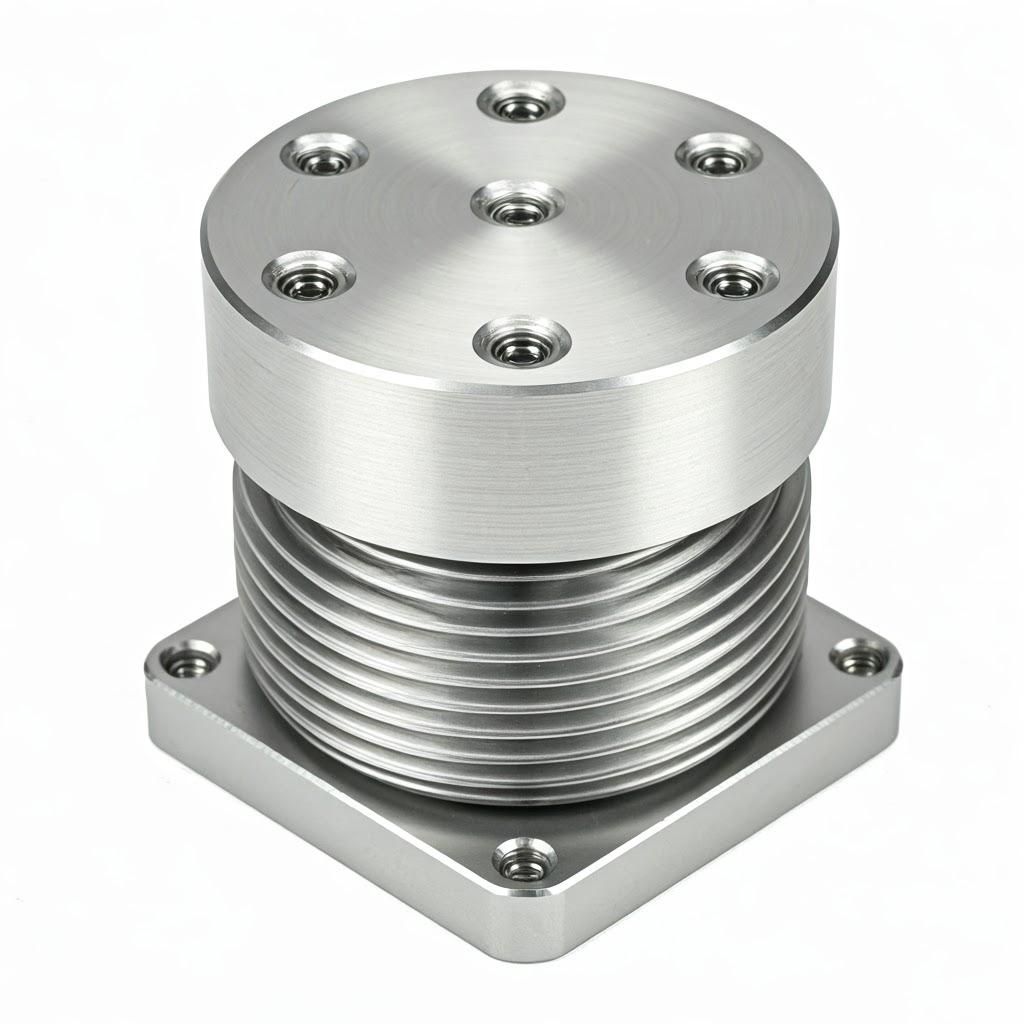
Design Optimization for Additively Manufactured Cooling Plates
The inherent design freedom offered by metal 3D printing opens up unprecedented opportunities for optimizing the performance of aerospace conformal cooling plates. Unlike traditional manufacturing constraints, additive manufacturing allows for the creation of complex internal geometries that maximize heat transfer efficiency and minimize pressure drop. Key design considerations for additively manufactured cooling plates include:
- Conformal Channels: Designing cooling channels that closely follow the contours of the heat-generating component ensures maximum contact area and efficient heat extraction. This can involve intricate curves, varying cross-sections, and complex branching networks tailored to the specific thermal load distribution.
- 격자 구조: Incorporating lightweight lattice structures within the cooling plate design can enhance structural rigidity while minimizing weight. These structures can also contribute to increased surface area for heat dissipation.
- Surface Area Enhancement: Features like fins, pin fins, and microchannels can be integrated into the internal cooling channels to significantly increase the surface area available for heat transfer, leading to improved cooling performance.
- Flow Optimization: Computational Fluid Dynamics (CFD) analysis plays a crucial role in optimizing the design of internal channels to ensure uniform flow distribution and minimize pressure drop across the cooling plate. This is essential for efficient coolant circulation.
- Integration of Features: Metal 3D printing allows for the integration of mounting features, fluid inlet/outlet ports, and even sensors directly into the cooling plate design, reducing the need for additional components and assembly steps.
- Wall Thickness and Support Structures: Careful consideration of wall thickness is essential to balance structural integrity and thermal conductivity. Support structures, necessary during the printing process for overhanging features, must be strategically designed for easy removal without compromising the final part’s geometry or surface finish.
에서 Metal3DP, our design engineers possess extensive experience in optimizing conformal cooling plate designs for additive manufacturing. We leverage advanced CAD software and simulation tools to ensure that the final product meets the most demanding aerospace requirements. Our expertise helps customers unlock the full potential of metal 3D printing for their thermal management solutions. To understand more about the additive manufacturing process, you can visit our page on 인쇄 방법.
Achieving Precision: Tolerance, Surface Finish, and Dimensional Accuracy in 3D Printed Cooling Plates
In the critical applications of aerospace, dimensional accuracy and surface finish are paramount for the proper fit, function, and reliability of components like conformal cooling plates. Metal 3D printing technologies have made significant strides in achieving tight tolerances and acceptable surface finishes. However, it’s important for engineers and procurement managers to understand the capabilities and limitations of these processes:
- Dimensional Tolerance: The achievable dimensional tolerance in metal 3D printing depends on factors such as the printing technology (e.g., SLM, DMLS), material, part geometry, and build parameters. Typically, tolerances in the range of ±0.1 mm or even finer can be achieved for critical features. Metal3DP의 advanced equipment and optimized processes are geared towards maximizing dimensional accuracy for aerospace components.
- 표면 마감: The as-printed surface finish in metal 3D printing is generally rougher compared to machined surfaces. The surface roughness is influenced by the powder particle size, laser parameters, and layer thickness. Post-processing techniques, as discussed in the next section, are often employed to achieve smoother surface finishes required for specific applications, such as ensuring proper sealing or reducing fluid flow resistance.
- 정확도에 영향을 미치는 요인: Several factors can influence the dimensional accuracy and surface finish of 3D printed metal parts, including:
- 파우더 특성: Particle size distribution and sphericity of the metal powder significantly impact the final part quality. Metal3DP utilizes high-quality metal spherical powders produced with advanced gas atomization and PREP technologies to ensure optimal results.
- Printer Calibration and Maintenance: Properly calibrated and maintained 3D printing equipment is crucial for consistent and accurate results.
- Build Orientation and Support Structures: The orientation of the part during printing and the design of support structures can affect dimensional accuracy and surface finish, particularly for complex geometries.
- Sintering/Melting Process Control: Precise control of laser power, scan speed, and other process parameters is essential for achieving the desired density and dimensional accuracy.
While metal 3D printing offers significant advantages in creating complex geometries, achieving specific tolerance and surface finish requirements often necessitates careful process control and post-processing. At Metal3DP, we have the expertise and capabilities to meet the stringent quality standards of the aerospace industry.
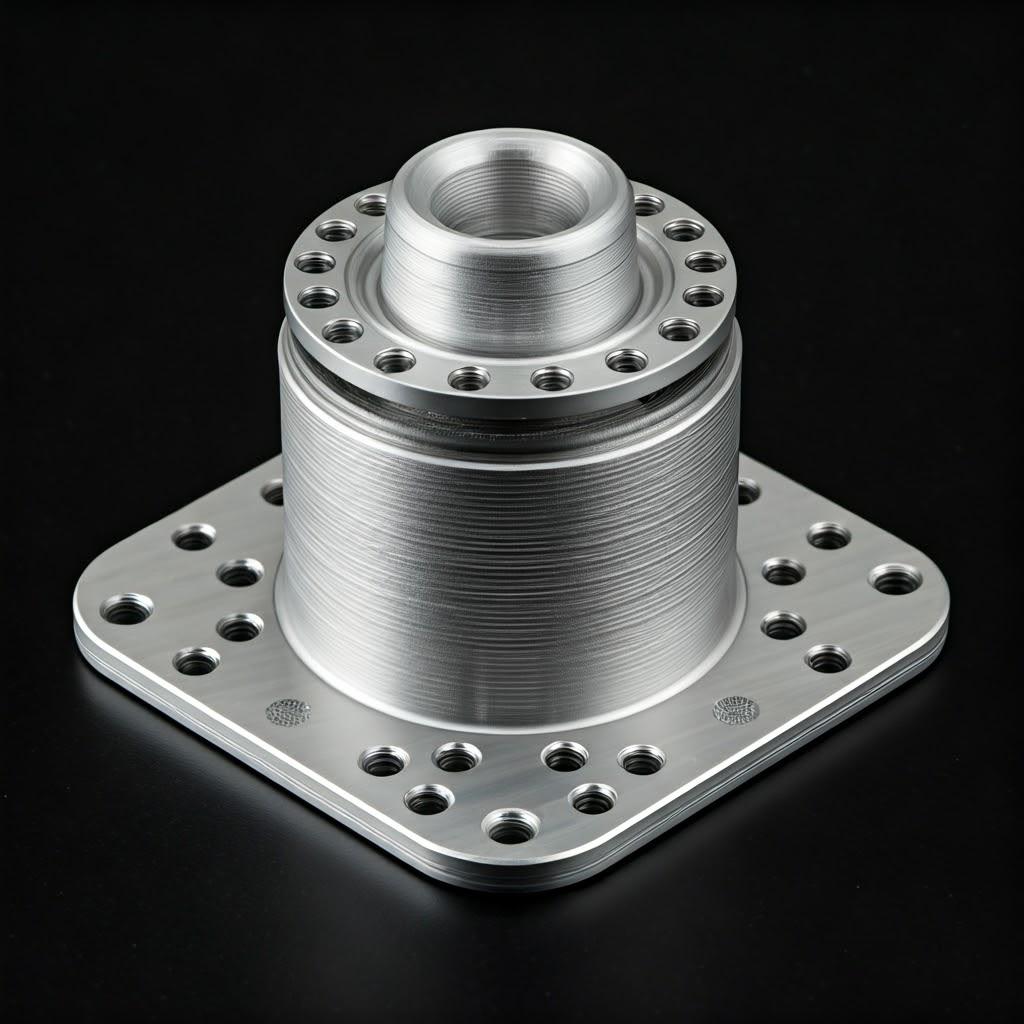
Post-Processing Techniques for Aerospace-Grade Cooling Plates
While metal 3D printing produces near-net-shape parts, post-processing steps are often required to achieve the final desired properties, surface finish, and dimensional accuracy for aerospace conformal cooling plates. Common post-processing techniques include:
- 지원 제거: Support structures, essential during the printing process, need to be carefully removed without damaging the delicate features of the cooling plate. Techniques include manual removal, machining, and chemical dissolution, depending on the material and support geometry.
- 열처리: Thermal post-processing, such as stress relieving, annealing, or hot isostatic pressing (HIP), can be employed to improve the mechanical properties, reduce residual stresses, and increase the density of the 3D printed parts.
- CNC 가공: For critical surfaces or tight tolerances that cannot be achieved directly through 3D printing, precision CNC machining can be used as a secondary operation. This is particularly relevant for interfaces and mounting surfaces.
- 표면 마감: To achieve smoother surface finishes for improved fluid flow or sealing, various surface treatment methods can be employed, including:
- Media Blasting: Using abrasive media to remove surface oxides and reduce roughness.
- 연마: Mechanical or chemical polishing techniques to achieve very smooth surfaces.
- 전기 연마: Using an electrochemical process to smooth and deburr metal surfaces.
- Coating and Surface Treatment: Depending on the application environment, coatings such as anodizing (for aluminum alloys) or passivation (for stainless steels) can be applied to enhance corrosion resistance and wear properties.
Metal3DP offers comprehensive post-processing services to ensure that our 3D printed aerospace conformal cooling plates meet the most stringent industry standards. Our understanding of material properties and aerospace requirements allows us to select and execute the appropriate post-processing steps for optimal performance and reliability. We are committed to providing end-to-end manufacturing solutions for our clients.
Overcoming Challenges in Metal 3D Printing of Cooling Plates
While metal 3D printing offers significant advantages, there are also potential challenges that need to be addressed to ensure the successful fabrication of high-quality aerospace conformal cooling plates:
- Warping and Distortion: Thermal stresses during the printing process can lead to warping or distortion of complex geometries, particularly for large parts or thin-walled structures. Optimized build orientation, support structure design, and process parameter control are crucial to minimize these issues.
- 다공성: Insufficient melting or sintering of the metal powder can result in porosity within the printed part, which can negatively impact its mechanical strength and thermal conductivity. Careful selection of process parameters and high-quality metal powders, like those produced by Metal3DP, are essential to minimize porosity.
- Support Removal Damage: Improperly designed or removed support structures can leave surface defects or even damage delicate features of the cooling plate. Experienced technicians and appropriate removal techniques are necessary.
- Residual Stresses: The rapid heating and cooling cycles during metal 3D printing can induce residual stresses in the part, which can lead to cracking or dimensional instability. Post-processing heat treatments are often required to relieve these stresses.
- Material Property Variability: Achieving consistent and predictable material properties in 3D printed parts requires careful control of the entire process chain, from powder production to printing and post-processing. Metal3DP의 rigorous quality control measures ensure the consistency and reliability of our materials and processes.
- Cost and Scalability: While metal 3D printing is ideal for complex geometries and low-to-medium volume production, the cost per part can be higher than traditional methods for very large production runs. Understanding the cost drivers and optimizing designs for efficient printing are important considerations.
By understanding these potential challenges and implementing best practices in design, material selection, printing, and post-processing, it is possible to consistently produce high-performance aerospace conformal cooling plates using metal 3D printing. Metal3DP의 expertise and comprehensive capabilities help our customers navigate these challenges and realize the full potential of additive manufacturing. You can learn more about our company and our commitment to quality on our 회사 소개 페이지.

Selecting a Trusted Metal 3D Printing Service Provider for Aerospace Components
Choosing the right metal 3D printing service provider is a critical decision for aerospace engineers and procurement managers. The quality, reliability, and performance of additively manufactured conformal cooling plates directly impact the success of aerospace applications. Here are key factors to consider when evaluating potential suppliers:
- Industry Experience and Expertise: Look for a provider with a proven track record in serving the aerospace industry. Experience with aerospace materials, quality standards (e.g., AS9100 certification), and demanding application requirements is essential. Metal3DP has extensive experience in providing additive manufacturing solutions for aerospace, medical, automotive, and industrial manufacturing sectors.
- Material Capabilities: Ensure the service provider offers the specific metal powders required for your application, such as AlSi10Mg and IN625, and has expertise in processing these materials to achieve optimal properties. Metal3DP manufactures a wide range of high-quality metal powders optimized for laser and electron beam powder bed fusion.
- Printing Technology and Equipment: Evaluate the types of metal 3D printing technologies and the sophistication of the equipment used by the provider. Advanced machines with high accuracy and repeatability are crucial for producing reliable aerospace components. Metal3DP의 printers deliver industry-leading print volume, accuracy, and reliability.
- Quality Assurance and Certifications: Verify that the provider has robust quality management systems in place, including material traceability, process controls, and inspection procedures. Relevant certifications, such as AS9100, demonstrate a commitment to quality standards.
- Design and Engineering Support: A strong service provider should offer design optimization expertise for additive manufacturing, helping you to leverage the full potential of the technology and ensure the manufacturability and performance of your cooling plates. Metal3DP provides comprehensive solutions spanning SEBM printers, advanced metal powders, and application development services. 1 1. met3dp.sg met3dp.sg
- Post-Processing Capabilities: Determine if the provider offers the necessary post-processing services to meet your requirements, including support removal, heat treatment, surface finishing, and inspection. An end-to-end solution can streamline the manufacturing process.
- Communication and Customer Support: Effective communication, responsiveness, and a collaborative approach are vital for a successful partnership. Choose a provider that is willing to work closely with your team to understand your specific needs and provide timely support.
- Lead Times and Production Capacity: Assess the provider’s lead times and production capacity to ensure they can meet your project timelines and volume requirements.
By carefully evaluating these factors, you can select a metal 3D printing service provider like Metal3DP that can deliver high-quality, reliable conformal cooling plates for your critical aerospace applications.
Cost Analysis and Lead Time for 3D Printed Aerospace Cooling Plates
Understanding the cost factors and lead times associated with metal 3D printing is crucial for budgeting and project planning. Several elements influence the overall cost and turnaround time for additively manufactured aerospace conformal cooling plates:
- 재료비: The cost of metal powders, such as AlSi10Mg and IN625, is a significant factor. Specialty alloys and smaller batch orders can result in higher material costs. Metal3DP의 in-house powder production capabilities provide a competitive advantage in material sourcing.
- 인쇄 시간: The build time on the 3D printer is a key cost driver. Factors influencing print time include the part’s volume, complexity, layer height, and the number of parts being printed simultaneously.
- Machine Costs and Overhead: The cost of operating and maintaining the metal 3D printing equipment, as well as general overhead expenses, are factored into the final price.
- Design and Engineering Fees: If design optimization or engineering support is required from the service provider, these services will contribute to the overall cost. Metal3DP offers application development services to assist with design and optimization.
- 후처리 비용: The cost of post-processing steps, such as support removal, heat treatment, machining, and surface finishing, will add to the total manufacturing cost. The complexity and number of post-processing steps will influence these costs.
- Quality Assurance and Inspection: Rigorous quality control procedures and inspections, essential for aerospace components, contribute to the overall cost.
리드 타임: The lead time for 3D printed aerospace cooling plates depends on several factors:
- Design Complexity and Optimization: Intricate designs that require significant optimization may have longer lead times.
- 자료 가용성: The availability of the specific metal powder can impact the start of the printing process. Metal3DP maintains a stock of high-quality metal powders.
- 인쇄 시간: As mentioned earlier, the build time on the 3D printer directly affects the lead time.
- Post-Processing Duration: The time required for post-processing steps can vary depending on the complexity and number of operations.
- Quality Inspection and Documentation: Thorough quality checks and documentation processes add to the overall lead time.
While metal 3D printing can offer faster turnaround times for prototypes and low-volume production compared to traditional methods, it’s important to discuss lead time expectations with your service provider early in the project. Metal3DP is committed to providing transparent and realistic lead times for our additive manufacturing services.
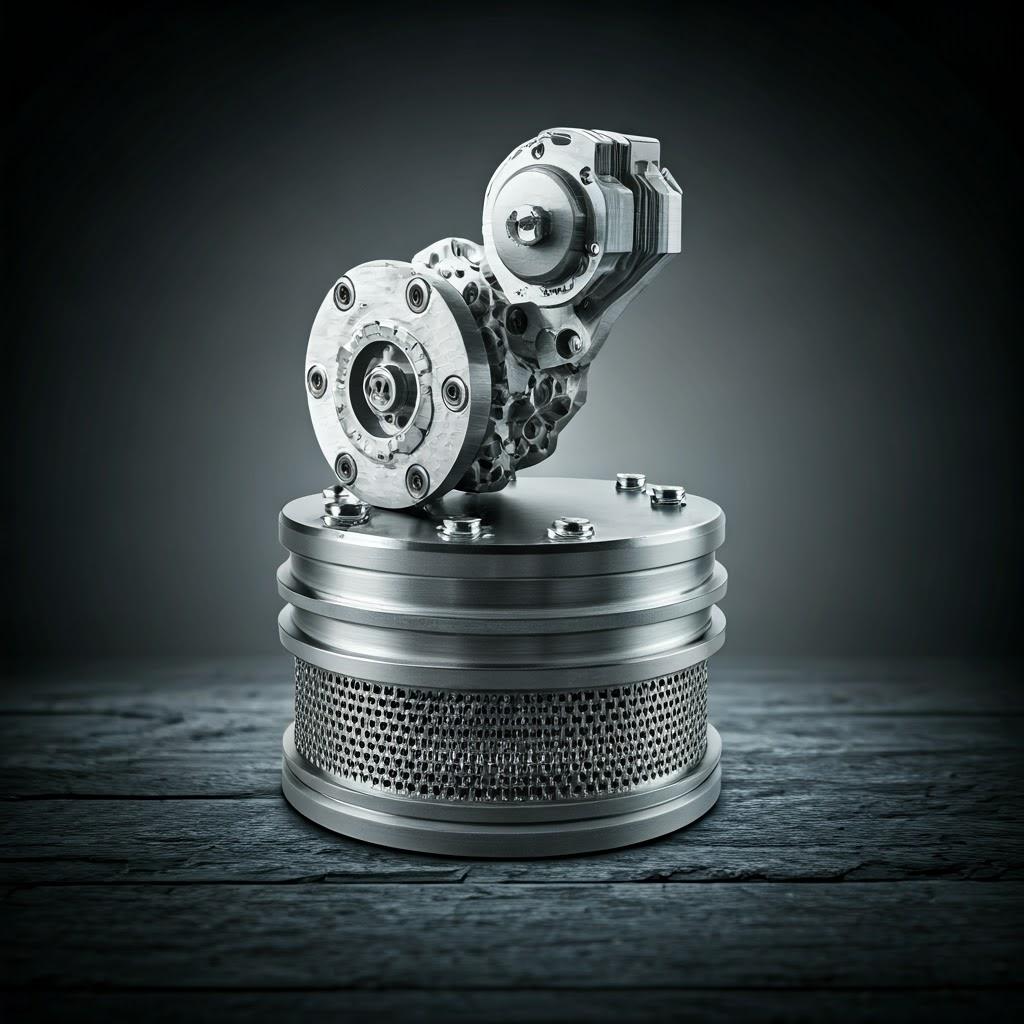
자주 묻는 질문(FAQ)
- What are the typical applications of conformal cooling plates in aerospace? Conformal cooling plates are used in aerospace for cooling avionics, engine components, actuators, hydraulic systems, heat exchangers, and thermal management systems in satellites and spacecraft. They are essential for maintaining optimal operating temperatures and ensuring the reliability of critical systems.
- Why is metal 3D printing preferred over traditional methods for manufacturing these cooling plates? Metal 3D printing offers significant advantages in terms of design freedom, allowing for complex internal cooling channels and optimized geometries that are difficult or impossible to achieve with traditional methods. It also enables rapid prototyping, reduced assembly, and customization.
- What are the key considerations when designing a conformal cooling plate for metal 3D printing? Key considerations include optimizing the design for conformal channels, incorporating lattice structures for weight reduction, enhancing surface area for heat transfer, optimizing fluid flow, integrating functional features, and carefully planning for support structures.
- What post-processing steps are typically required for 3D printed aerospace cooling plates? Common post-processing steps include support removal, heat treatment (e.g., stress relieving, HIP), CNC machining for critical surfaces, surface finishing (e.g., polishing), and application of protective coatings.
- How do I choose the right metal powder for my aerospace cooling plate application? The choice of metal powder depends on the specific performance requirements, including thermal conductivity, strength-to-weight ratio, operating temperature, and corrosion resistance. Alloys like AlSi10Mg and IN625 are often preferred for their specific properties. Consulting with a material expert at a company like Metal3DP can help in making the optimal selection.
Conclusion: The Future of Aerospace Cooling with Metal 3D Printing
Metal 3D printing is revolutionizing the design and manufacturing of aerospace conformal cooling plates, offering unprecedented opportunities for enhanced thermal management, weight reduction, and improved performance. The ability to create complex, application-specific cooling solutions with advanced materials like AlSi10Mg and IN625 is empowering aerospace engineers to push the boundaries of innovation.
As the aerospace industry continues to demand lighter, more efficient, and highly reliable components, metal additive manufacturing will play an increasingly vital role. Companies like Metal3DP, with our expertise in metal powders, advanced printing technologies, and comprehensive post-processing capabilities, are poised to be key enablers of this transformation. By partnering with a trusted and experienced metal 3D printing service provider, aerospace organizations can unlock the full potential of additive manufacturing to create next-generation thermal management solutions that drive efficiency, reliability, and performance. Contact Metal3DP today to explore how our capabilities can power your organization’s additive manufacturing goals.
공유
중국 칭다오에 본사를 둔 선도적인 적층 제조 솔루션 제공업체인 MET3DP Technology Co. 당사는 산업용 3D 프린팅 장비와 고성능 금속 분말을 전문으로 합니다.
관련 기사
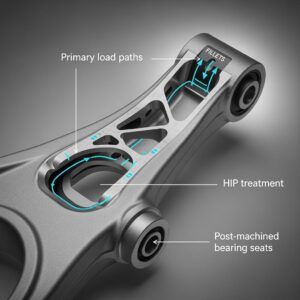