Electric Motor Rotor Supports via Metal AM
목차
Introduction: Revolutionizing Electric Motor Design with AM Rotor Supports
The relentless drive for efficiency, power density, and performance in electric motors across aerospace, automotive, medical, and industrial sectors is pushing the boundaries of traditional manufacturing. Components like the electric motor rotor support, a critical element ensuring the stability, alignment, and longevity of the rotating assembly, are prime candidates for innovation. Enter metal additive manufacturing (AM), more commonly known as metal 3D 프린팅. This transformative technology is moving beyond prototyping and into serial production, offering unprecedented design freedom and performance capabilities for complex parts like rotor supports. By enabling intricate geometries, lightweight structures, and the use of advanced materials, metal AM facilitates the creation of rotor supports that are not only lighter and stronger but can also integrate additional functionalities, fundamentally changing how engineers approach electric motor design and assembly.
Traditionally, manufacturing rotor supports involves subtractive methods like CNC machining from billet or casting processes. While effective, these methods often face limitations regarding geometric complexity, material waste, and lead times for intricate designs. Machining complex internal channels for cooling or creating highly optimized, topology-driven shapes can be difficult, time-consuming, and costly. Casting might require expensive tooling and can have limitations in achievable tolerances and material properties without significant post-processing. Metal AM, particularly Powder Bed Fusion (PBF) techniques like Selective Laser Melting (SLM) and Electron Beam Melting (EBM), overcomes many of these hurdles. It builds parts layer by layer directly from 3D CAD data, using high-energy sources (lasers or electron beams) to fuse fine metal powders. This allows for:
- 독보적인 디자인 자유도: Creation of complex internal features, topology-optimized structures, and organic shapes previously impossible or impractical to manufacture.
- 경량화 잠재력: Significant weight reduction through optimized geometries and lattice structures without compromising structural integrity, crucial for applications where weight is a penalty (e.g., aerospace, electric vehicles).
- 파트 통합: Combining multiple components of a rotor support assembly into a single printed part, reducing assembly time, potential failure points, and overall system complexity.
- 소재 혁신: Utilizing advanced metal alloys specifically chosen for demanding operating conditions like high temperatures or corrosive environments.
- Accelerated Development Cycles: Rapid iteration from design to functional prototype to production part, speeding up innovation and time-to-market.
For procurement managers and engineers seeking 첨단 제조 solutions for high-performance electric motor components, understanding the potential of metal AM for producing rotor supports is crucial. It represents a shift towards more agile, efficient, and capable production methods. Companies like Met3dp, headquartered in Qingdao, China, are at the forefront of this revolution, providing comprehensive solutions that include industry-leading 금속 3D 프린팅 equipment and high-performance metal powders tailored for demanding industrial applications. Their expertise spans the entire AM ecosystem, empowering businesses to leverage this technology for critical components like rotor supports, thereby gaining a significant competitive edge through enhanced performance enhancement and manufacturing agility. As we delve deeper, we will explore the specific applications, benefits, materials, and considerations involved in utilizing metal AM for these vital motor parts.
Critical Functions: What Are Electric Motor Rotor Supports Used For?
The electric motor rotor support, while perhaps not as widely recognized as the stator or windings, plays an indispensable role in the reliable and efficient operation of an electric motor. Its primary function is to securely locate and support the rotor assembly – the rotating part of the motor, typically containing magnets or conductive bars – within the motor housing, ensuring precise alignment with the stator (the stationary part). This alignment is critical for maintaining the correct air gap between the rotor and stator, which is essential for generating torque efficiently and minimizing electrical losses, vibration, and noise.
The specific functions and design requirements of a rotor support can vary significantly depending on the type, size, and application of the electric motor. Key responsibilities typically include:
- Maintaining Rotor Alignment: Ensuring the rotor spins accurately on its axis, concentric to the stator bore, throughout the motor’s operating speed range and under varying loads. Misalignment can lead to reduced efficiency, increased wear on bearings, excessive vibration, and potential contact between rotor and stator, leading to catastrophic failure.
- Bearing Housing: Often integrating housings or mounting points for the bearings that facilitate the rotor’s rotation. The support must provide a rigid and dimensionally accurate interface for these bearings to function correctly and achieve their expected lifespan.
- Load Bearing: Supporting the weight of the rotor assembly and reacting to the dynamic loads generated during operation, including rotational forces, torque reactions, and potential imbalances.
- 진동 감쇠: In some designs, the support may contribute to damping vibrations originating from the rotor or bearings, contributing to quieter and smoother operation.
- 열 관리: In high-performance motors, the rotor support might incorporate features to aid in heat dissipation, potentially including integrated cooling channels or fins, helping to manage temperatures within the rotor and bearings.
- Structural Integrity: Providing overall structural rigidity to the motor assembly, ensuring that components maintain their relative positions under operational stresses and environmental conditions.
These critical functions highlight why the design and manufacture of rotor supports demand high precision and robust materials. They are integral components in a wide array of applications:
- Automotive Powertrains: Essential in electric vehicle (EV) traction motors, where high speeds, significant torque, vibration, and the need for lightweighting place extreme demands on components. Rotor supports ensure the powertrain’s reliability and efficiency.
- Aerospace Actuators and Generators: Used in flight control surface actuators, landing gear systems, auxiliary power units (APUs), and environmental control systems. Reliability, minimal weight, and performance under extreme temperatures and vibrations are paramount.
- Industrial Machinery: Found in high-speed spindles for machine tools, pumps, compressors, robotics, and factory automation equipment. Durability, precision alignment, and long service life are key requirements.
- 의료 기기: Utilized in surgical drills, pumps, centrifuges, and diagnostic imaging equipment (like MRI gradient coils). Biocompatibility (depending on the specific device), low vibration, and high reliability are often critical.
- 소비자 가전: Smaller versions might be found in high-performance drones, appliances, and power tools where efficiency and compact design are important.
Given the diverse and demanding nature of these rotor support applications, manufacturers are increasingly looking towards advanced materials and production methods. Metal AM offers a pathway to create electric motor components that meet the stringent requirements of high-speed motors and other challenging environments, enabling designs previously unattainable through conventional means. Understanding these core functions underscores the importance of careful material selection and precise manufacturing, areas where specialized AM providers like Met3dp excel, offering solutions tailored to the unique demands of 자동차 파워트레인, aerospace actuators, and critical 산업 기계.
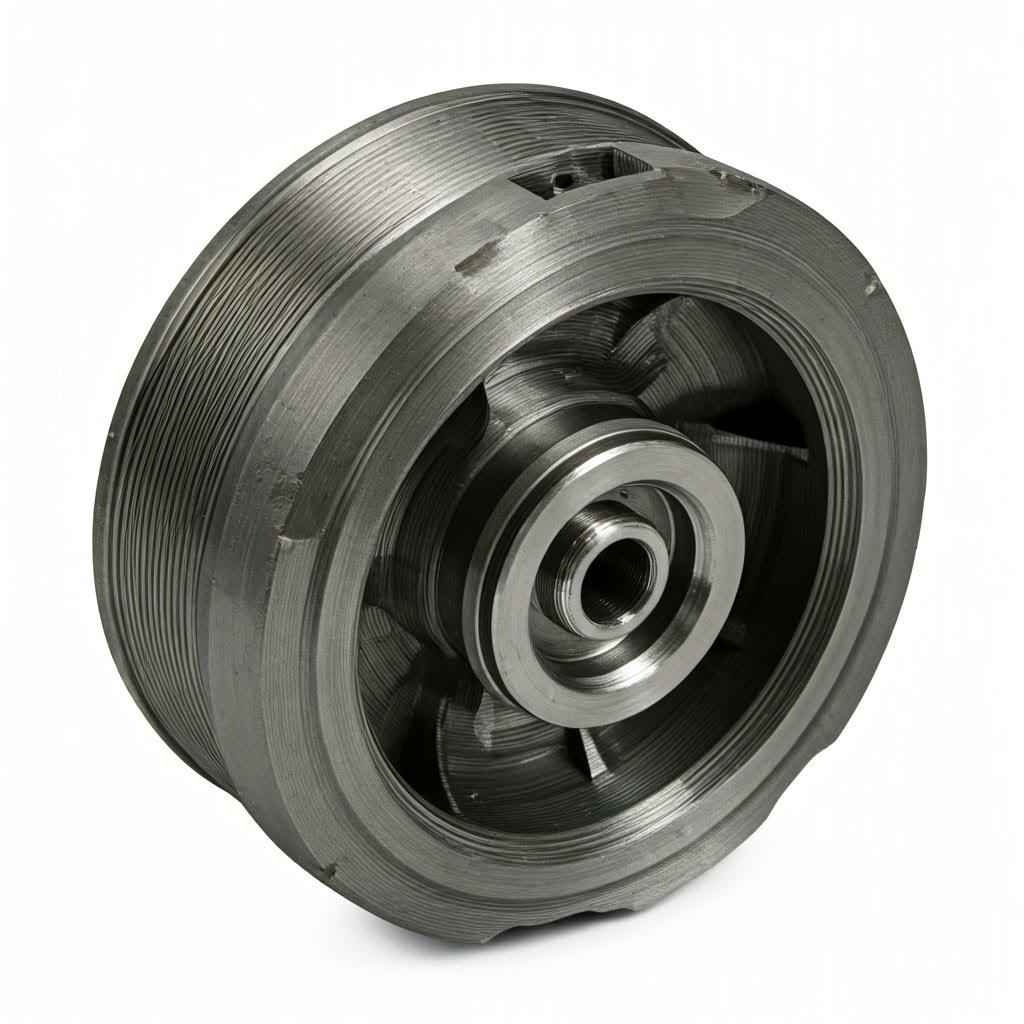
The Additive Advantage: Why Use Metal 3D Printing for Rotor Supports?
While traditional manufacturing methods like CNC machining and casting have long served the industry, metal additive manufacturing presents a compelling suite of advantages specifically beneficial for producing electric motor rotor supports, particularly complex or high-performance variants. Opting for 금속 3D 프린팅 isn’t just about adopting a new technology; it’s about unlocking tangible engineering and business benefits that directly address the limitations of conventional approaches. Procurement managers and engineers evaluating production methods for rotor supports should consider the following key advantages offered by AM:
1. Unmatched Design Freedom & Complexity:
- 토폴로지 최적화: AM allows for the practical realization of topology-optimized designs, where material is placed only where structurally necessary. This results in organic, highly efficient shapes that minimize weight while maintaining or even increasing stiffness and strength – ideal for rotor supports where rotational inertia and overall motor weight are critical.
- Internal Features: Complex internal channels for cooling fluid or air can be directly integrated into the support structure during the printing process. This enhanced thermal management capability is invaluable for high-power density motors, improving performance and lifespan.
- 격자 구조: Internal lattice or gyroid structures can be incorporated to further reduce weight while providing tailored structural support and vibration damping characteristics. These intricate geometries are virtually impossible to achieve subtractively.
2. Significant Lightweighting:
- Directly linked to design freedom, AM enables substantial weight reduction compared to solid components designed for traditional manufacturing constraints.
- Reduced rotor support weight lowers the overall mass and rotational inertia of the motor assembly. This translates to faster acceleration/deceleration, lower energy consumption, and reduced loading on bearings, particularly crucial in automotive (EVs) and aerospace applications.
3. Part Consolidation:
- Multiple individual components that might traditionally make up a rotor support assembly (e.g., brackets, bearing housings, mounting plates) can often be redesigned and consolidated into a single, monolithic part printed via AM.
- 이점은 다음과 같습니다.
- Reduced part count and Bill of Materials (BOM) complexity.
- Elimination of assembly steps (labor, time, potential errors).
- Removal of joints and fasteners, which can be potential failure points or sources of vibration.
- Improved overall structural integrity.
4. Accelerated Prototyping and Development:
- Metal AM facilitates 신속한 프로토타이핑 of functional rotor supports directly from CAD data, drastically reducing the time required for design iteration compared to waiting for tooling (casting) or complex machining setups.
- Engineers can quickly test different design variations, materials, and optimization strategies, leading to faster innovation and a shorter time-to-market for new motor designs.
5. Material Flexibility and Performance:
- AM processes can work with a wide range of high-performance metal powders, including aluminum alloys (like AlSi10Mg for lightweighting) and nickel superalloys (like IN625 for high-temperature strength and corrosion resistance) – the focus of this article.
- This allows engineers to select the optimal material based on the specific operating conditions (temperature, load, corrosive environment) of the rotor support, rather than being constrained by the limitations of traditional processes (e.g., castability). Met3dp, for instance, specializes in producing high-quality, gas-atomized powders like AlSi10Mg and IN625, ensuring optimal material properties for demanding AM applications.
6. Supply Chain Optimization and On-Demand Production:
- AM enables localized, on-demand production, reducing reliance on complex global supply chains and long lead times associated with traditional methods, especially for specialized or low-volume parts.
- Digital inventory (storing CAD files instead of physical parts) allows for parts to be printed only when needed, minimizing warehousing costs and waste. This is particularly advantageous for spare parts or customized motor configurations. For B2B clients needing wholesale AM services or reliable 공급업체 partnerships, this agility is a significant benefit.
Comparison: Traditional vs. Additive Manufacturing for Rotor Supports
기능 | Traditional Manufacturing (CNC Machining/Casting) | Metal Additive Manufacturing (PBF) | Advantage for Rotor Supports |
---|---|---|---|
기하학적 복잡성 | Limited by tool access, draft angles, tooling | High, enables complex internal features, lattices | Optimized designs, integrated cooling, lightweighting |
경량화 | Moderate (via pocketing, material choice) | Significant (via topology optimization, lattices) | Reduced inertia, improved motor efficiency/responsiveness |
부품 통합 | Difficult, requires assembly | Feasible, can print monolithic multi-functional parts | Reduced assembly time/cost, fewer failure points |
재료 낭비 | High (subtractive CNC), Moderate (casting) | Low (additive process, powder recycling) | Cost savings, more sustainable |
툴링 비용 | High (casting molds), None (CNC) | None (direct digital manufacturing) | Lower cost for low-to-mid volumes, faster setup |
Lead Time (New Design) | Weeks to Months (tooling, setup) | Days to Weeks (direct printing) | Faster iteration, quicker time-to-market |
머티리얼 옵션 | Broad, but process-limited (e.g., castability) | Growing range of weldable alloys, including advanced | Optimal material selection for performance (e.g., IN625) |
최소 주문 수량 | Often high (casting) | Low (economical for single parts or small batches) | Ideal for customization, prototypes, spare parts |
시트로 내보내기
동안 traditional vs additive methods each have their place, the specific demands placed on modern electric motor rotor supports – complexity, lightweighting, performance – often align perfectly with the strengths of 금속 3D 프린팅. Embracing AM provides a distinct additive advantage, enabling engineers and manufacturers to push the performance envelope and optimize their 공급망 for these critical components.
Material Matters: Recommended Metal Powders (AlSi10Mg & IN625) for Rotor Supports
Selecting the right material is fundamental to the success of any engineering component, and electric motor rotor supports are no exception. The operating environment – temperature, loads, rotational speed, potential exposure to corrosive agents – dictates the necessary material properties. Metal additive manufacturing offers the flexibility to utilize advanced alloys tailored to these demands. For rotor supports, two materials frequently stand out due to their complementary properties: AlSi10Mg (an aluminum alloy) and IN625 (a nickel-chromium superalloy). Understanding their characteristics is key to leveraging them effectively.
1. AlSi10Mg: The Lightweight Standard
AlSi10Mg is an aluminum alloy containing silicon and magnesium, widely used in casting and increasingly popular in metal AM, particularly Selective Laser Melting (SLM). It’s often the go-to choice when lightweighting is a primary design driver.
- 주요 속성:
- 낮은 밀도: Approximately 2.67 g/cm³, significantly lighter than steels or nickel alloys, directly contributing to lower motor weight and inertia.
- 우수한 중량 대비 강도 비율: Offers respectable mechanical strength and stiffness, suitable for many moderate load-bearing applications.
- 뛰어난 열 전도성: Helps dissipate heat generated in the rotor or bearings, beneficial for thermal management within the motor.
- 우수한 내식성: Generally performs well in typical operating environments.
- Weldability/Printability: Exhibits good processability in SLM systems, allowing for the creation of fine features and complex geometries.
- Benefits for Rotor Supports:
- Maximum Lightweighting: Ideal for applications where minimizing mass is critical (aerospace, EVs, robotics, drones).
- Reduced Rotational Inertia: Enables faster motor dynamics (acceleration/deceleration).
- 열 관리: Aids in keeping bearing and rotor temperatures under control.
- 비용 효율성: Generally more economical than nickel superalloys in terms of raw material cost.
- 고려 사항:
- Lower High-Temperature Strength: Mechanical properties degrade significantly at elevated temperatures (typically above 150-200°C), limiting its use in very high-temperature motors.
- Moderate Fatigue Strength: May require careful design considerations in high-cycle fatigue applications compared to steels or titanium.
Met3dp AlSi10Mg Powder: Leveraging advanced gas atomization technology, Met3dp produces 고강도 알루미늄 합금 powders like AlSi10Mg with high sphericity and excellent flowability. This ensures consistent powder layering and melting during the PBF process, resulting in dense, high-quality printed parts with reliable mechanical properties, perfectly suited for lightweight rotor supports.
2. IN625 (Inconel 625): The High-Performance Champion
IN625 is a nickel-chromium-molybdenum-niobium superalloy, renowned for its exceptional combination of high strength, toughness, and outstanding corrosion resistance across a broad temperature range. It’s a workhorse material in demanding industries like aerospace, chemical processing, and marine applications.
- 주요 속성:
- Excellent High-Temperature Strength: Retains significant strength and creep resistance at elevated temperatures (up to 650°C and beyond, depending on the application).
- Superb Corrosion Resistance: Highly resistant to oxidation, acids, alkalis, and seawater, making it suitable for harsh operating environments.
- High Fatigue Strength: Offers excellent resistance to cyclic loading.
- Good Weldability/Printability: Can be successfully processed using both SLM and EBM, although parameter optimization is crucial.
- Benefits for Rotor Supports:
- High-Temperature Operation: Suitable for motors operating in hot environments or those with very high power density leading to significant heat generation.
- Harsh Environments: Ideal where exposure to corrosive fluids or atmospheres is a concern.
- High Reliability & Durability: Excellent fatigue and creep properties contribute to long service life under demanding load conditions.
- Structural Integrity: High strength allows for robust designs even with complex geometries.
- 고려 사항:
- Higher Density: Significantly denser (approx. 8.44 g/cm³) than aluminum alloys, resulting in heavier components if not aggressively topology-optimized.
- 더 높은 재료비: Nickel superalloys are considerably more expensive than aluminum alloys.
- Lower Thermal Conductivity: Less effective at passive heat dissipation compared to aluminum.
- Print Challenges: Can be more prone to residual stress and cracking during printing if parameters are not carefully controlled; requires robust support strategies.
Met3dp IN625 Powder: Met3dp employs industry-leading gas atomization and Plasma Rotating Electrode Process (PREP) technologies to manufacture superior 니켈 초합금 powders like IN625. PREP, in particular, is known for producing highly spherical powders with very few satellites and low internal porosity, ideal for achieving the high-density, defect-free microstructures required for mission-critical IN625 applications, such as high-performance rotor supports demanding exceptional 온도 저항 및 내식성.
Material Selection Summary Table:
속성 | AlSi10Mg | IN625 (Inconel 625) | Selection Driver for Rotor Support |
---|---|---|---|
주요 혜택 | 경량 | High Temperature Strength, Corrosion Resist. | Application’s main priority (weight vs. environment) |
밀도 | 낮음(~2.67g/cm³) | High (~8.44 g/cm³) | Minimize weight (Al) vs. Accept higher weight (IN) |
Operating Temp. | Moderate (up to ~150-200°C) | High (up to ~650°C+) | Motor operating temperature dictates choice |
힘 | Good (Excellent Strength-to-Weight) | 매우 높음 | Load requirements, potential for thinner walls (IN) |
내식성 | 양호 | 우수 | Necessary for harsh chemical or marine environments (IN) |
열 전도성 | 우수 | 보통 | Passive cooling needs favor Al |
비용 | Lower | 더 높음 | 예산 제약 |
인쇄 가능성 | Generally Easier | More Challenging (Stress/Cracking Risk) | Manufacturing feasibility and parameter control |
시트로 내보내기
Ultimately, the choice between AlSi10Mg properties 및 IN625 applications for an electric motor rotor support depends on a thorough analysis of the performance requirements, operating environment, and cost constraints. Metal AM providers like Met3dp, with their deep materials science expertise and production of high-quality Met3dp powders, are invaluable partners in making this critical selection and ensuring the final printed part meets or exceeds expectations.
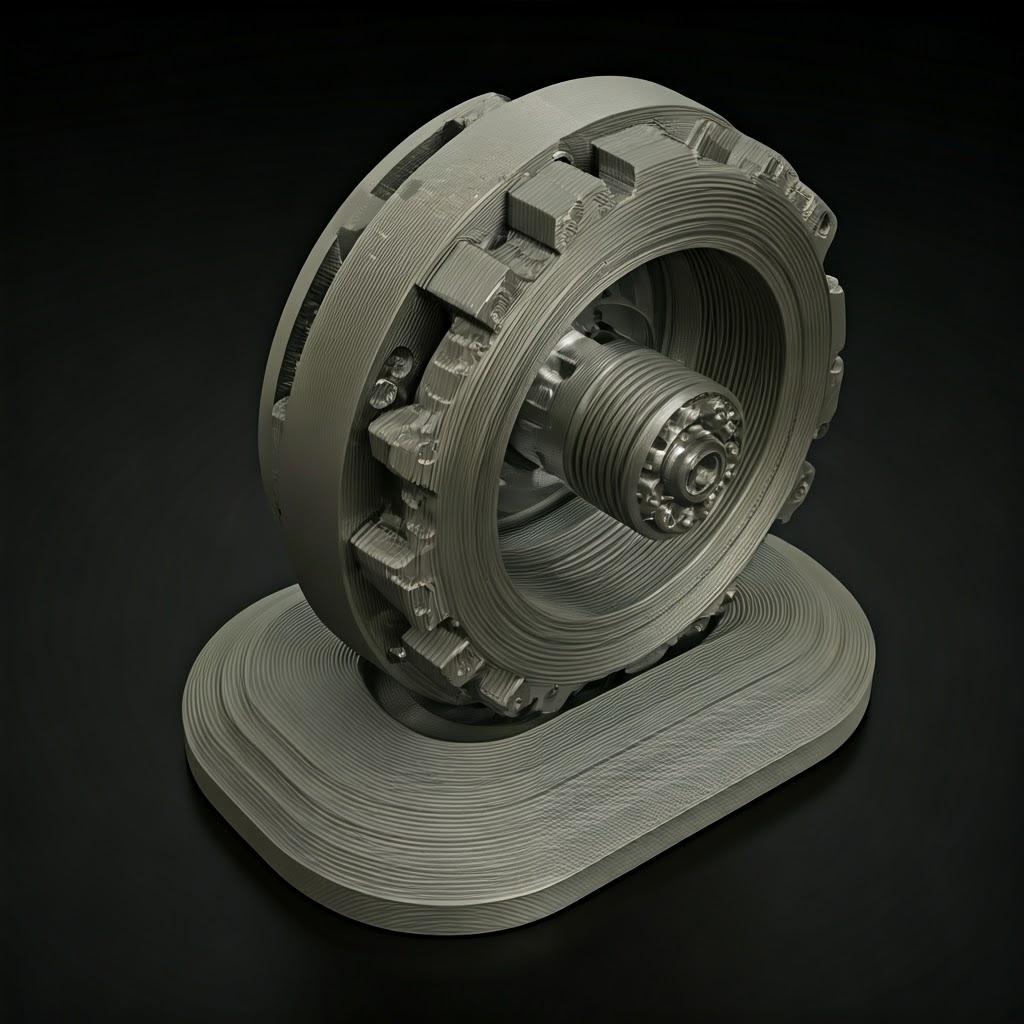
Design for Additive Manufacture (DfAM): Optimizing Rotor Supports for 3D Printing
Simply taking a design intended for CNC machining or casting and sending it to a metal 3D printer rarely yields optimal results. To truly harness the power of additive manufacturing for electric motor rotor supports, engineers must embrace Design for Additive Manufacture (DfAM) principles. DfAM is not just about ensuring a part ~할 수 있다 be printed; it’s about strategically designing the part to leverage AM’s unique capabilities – maximizing performance, minimizing weight, reducing print time and cost, and ensuring manufacturability. For a component as critical as a rotor support, applying DfAM is essential for success.
Key DfAM considerations for metal AM rotor supports include:
1. Leveraging Geometric Freedom:
- 토폴로지 최적화: This is arguably AM’s superpower. Software tools can analyze load paths and functional requirements (stiffness, vibration modes) and generate highly organic, load-bearing structures that use material only where needed. Applying topology optimization to a rotor support can lead to significant weight savings while maintaining or even improving structural performance compared to bulky, traditionally designed counterparts. The resulting shapes are often impossible to machine conventionally.
- 격자 구조: Incorporating internal lattice or gyroid structures can further reduce mass while providing tailored mechanical properties (e.g., stiffness, energy absorption). They can also improve “printability” by reducing large solid cross-sections prone to thermal stress. For rotor supports, lattices might be used strategically in lower-stress areas or to dampen vibrations.
- Integrated Features: Think beyond just structural support. Can cooling channels be directly integrated into the support arms? Can sensor mounts, cable routing paths, or bearing preload features be built directly into the part? DfAM encourages consolidating functionality into a single printed component.
2. Process-Specific Design Rules:
- 다른 금속 3D 프린팅 방법, primarily Powder Bed Fusion (PBF) techniques like SLM and EBM used for AlSi10Mg and IN625, have specific design constraints:
- Overhangs and Support Structures: Steep overhangs and horizontal surfaces cannot be printed directly onto loose powder; they require support structures. DfAM involves designing parts to minimize the need for supports (e.g., using self-supporting angles, typically >45° from the horizontal) or designing supports that are easy and non-damaging to remove. Critical surfaces requiring high accuracy should ideally be oriented upwards or designed to avoid supports.
- 벽 두께: There are minimum printable wall thicknesses (dependent on material, machine, parameters), typically around 0.4-1.0 mm. Walls that are too thin may warp or fail to resolve properly. Conversely, very thick sections can accumulate thermal stress and increase print time/cost.
- Hole Orientation and Size: Small horizontal holes can be challenging to print accurately without supports. Vertical holes are generally easier. Minimum hole diameters depend on the process resolution.
- Residual Stress Management: Large flat areas or sharp transitions in thickness can lead to warping due to residual stresses built up during the rapid heating and cooling cycles. DfAM involves using fillets, ribs, and potentially stress-relieving geometries to mitigate these effects. Build plate orientation also plays a crucial role here.
3. Designing for Post-Processing:
- Consider how the part will be handled after printing. Will surfaces require machining for tight tolerances (e.g., bearing fits, mating interfaces)? If so, DfAM involves adding sufficient extra material (machining allowance or “stock”) to these specific areas.
- How will support structures be removed? Ensure there is adequate access for tools (manual or CNC) to remove supports without damaging the part, especially internal supports within complex channels.
- Plan for heat treatment (stress relief, homogenization, aging) which is often required. Ensure the design can withstand the thermal cycles without excessive distortion.
4. Material Considerations:
- The chosen material (e.g., lightweight AlSi10Mg vs. high-temp IN625) influences design choices. IN625’s higher density necessitates more aggressive lightweighting via topology optimization or lattices if mass is a concern. Its propensity for higher residual stress might require more careful thermal management design features or support strategies compared to AlSi10Mg.
- Material anisotropy (properties varying with build direction) can occur in AM parts. DfAM considers the primary load directions relative to the build orientation to optimize mechanical performance.
DfAM Workflow Elements for Rotor Supports:
- Functional Decomposition: Clearly define all structural, thermal, and interfacing requirements.
- Initial Concept Generation: Explore designs leveraging AM (topology optimization, lattices, consolidation).
- Process Simulation: Use simulation tools to predict thermal stresses, distortion, and potential print failures 전에 committing to a build. This helps refine the design and optimize orientation/supports.
- Support Strategy Planning: Intelligently design support structures that are effective yet minimized and removable.
- Post-Processing Integration: Designate surfaces needing machining, ensure access for support removal, and account for heat treatment effects.
- Collaboration: Work closely with AM service providers like Met3dp. Their engineers possess deep expertise in DfAM 원칙 and can provide invaluable feedback on design manufacturability, material selection, and process optimization, ensuring the generative design concepts translate into successful, high-performance 토폴로지 최적화-driven rotor supports.
By thoughtfully applying DfAM 원칙, engineers can move beyond simply replicating existing designs and truly unlock the transformative potential of metal AM for creating next-generation electric motor rotor supports optimized for weight, performance, and manufacturability.
Precision Defined: Tolerance, Surface Finish, and Dimensional Accuracy in AM Rotor Supports
While metal AM excels at producing complex geometries, achieving the tight tolerances, specific surface finishes, and high dimensional accuracy required for components like electric motor rotor supports often necessitates a combination of precise printing and targeted post-processing. Engineers and procurement managers must understand the typical capabilities and limitations of AM processes regarding precision to set realistic expectations and plan necessary finishing steps.
치수 정확도:
- This refers to how closely the final part dimensions match the nominal dimensions specified in the CAD model.
- Typical “as-built” accuracy for metal Powder Bed Fusion (PBF) processes like SLM and EBM is often in the range of ±0.1 mm to ±0.2 mm, or ±0.1% to ±0.2% of the dimension, whichever is greater. However, this can be influenced by:
- Part Size and Geometry: Larger parts or complex shapes are more susceptible to thermal distortion, potentially impacting overall accuracy.
- 빌드 오리엔테이션: Orientation affects heat buildup, support needs, and potential warping.
- Material: Different materials exhibit varying degrees of shrinkage and stress accumulation (e.g., IN625 can be more challenging than AlSi10Mg).
- 머신 보정: The accuracy and calibration of the AM machine itself are critical. Met3dp utilizes industry-leading printers known for their accuracy and reliability, crucial for mission-critical parts.
- 열 효과: Residual stress and post-build shrinkage must be anticipated and potentially compensated for in the design or build setup.
- For features requiring higher accuracy (e.g., bearing bores, mating surfaces with tolerances tighter than ±0.1 mm), post-print CNC machining is typically required.
표면 마감(거칠기):
- The as-built surface finish of metal AM parts is inherently rougher than machined surfaces. This is due to the layer-by-layer process and the partially melted powder particles adhering to the surface.
- Surface roughness (often measured as Ra – arithmetic average roughness) depends heavily on:
- 빌드 오리엔테이션: Upward-facing surfaces and vertical walls tend to be smoother than downward-facing surfaces (supported) or steeply angled surfaces. Top surfaces are often the smoothest.
- 레이어 두께: Thinner layers generally produce finer finishes but increase build time.
- 파우더 특성: Powder particle size distribution and morphology influence the finish. High-quality powders, like those produced by Met3dp using advanced atomization, contribute to better surface quality.
- 프로세스 매개변수: Laser/beam power, scan speed, etc., affect the melt pool characteristics and resulting surface.
- Typical as-built Ra values for SLM/EBM can range from 6 µm to 25 µm (or roughly 250 to 1000 µin).
- Implications for Rotor Supports:
- Bearing seats and critical mating surfaces almost always require post-machining or other finishing operations (polishing, grinding) to achieve the necessary smoothness (often Ra < 1.6 µm or even < 0.8 µm).
- Aerodynamic or hydrodynamic surfaces (if applicable, e.g., integrated cooling fins) might benefit from smoothing processes to improve flow efficiency.
- Surfaces where supports were attached will typically be rougher and require finishing.
Achieving Tight Tolerances:
- The most reliable way to achieve tolerances tighter than the inherent capability of the AM process is through subtractive finishing.
- 하이브리드 제조: Some advanced systems combine additive and subtractive processes within the same machine, allowing for critical features to be machined during the build process or immediately after.
- Post-Print Machining: The standard approach involves printing the rotor support slightly oversized (adding machining stock, typically 0.5 mm to 2 mm) on critical features and then using CNC machining (milling, turning, grinding) to bring those features into final tolerance and achieve the desired surface finish. Careful fixture design is needed to hold the often-complex AM part accurately during machining.
- Inspection and Quality Control: Rigorous inspection using tools like Coordinate Measuring Machines (CMM), 3D scanners, and surface profilometers is essential to verify that the final 치수 안정성 및 surface roughness (Ra) meet specifications. Comprehensive 품질 관리 procedures are non-negotiable for critical components.
Summary Table: Precision in Metal AM Rotor Supports
매개변수 | As-Built AM Capability (Typical PBF) | Factors Influencing | Achieving Higher Precision | Requirement for Rotor Supports |
---|---|---|---|---|
치수 정확도 | ±0.1 to ±0.2 mm or ±0.1-0.2% | Size, Geometry, Orientation, Material, Machine, Thermal | Post-print CNC Machining, Process Control | High (especially bearing fits, mating faces) |
Surface Finish (Ra) | 6 µm – 25 µm | Orientation, Layer Thickness, Powder, Parameters | Machining, Polishing, Blasting, Tumbling | High on specific features (bearing seats <1.6 µm) |
반복성 | Good (with process control) | Process Stability, Machine Calibration, Powder Quality | Strict Process Control, QA/QC | High (for series production) |
시트로 내보내기
In summary, while metal AM provides the geometric freedom, achieving the final required metal AM tolerances 및 표면 마감 for demanding applications like rotor supports usually involves a strategic combination of optimized printing and precise post-processing. Partnering with an experienced AM provider like Met3dp, who understands these nuances and possesses both advanced printing capabilities (leveraging their high-quality powders and equipment) and established post-processing workflows, is key to ensuring the final component meets all 정밀 제조 specifications.
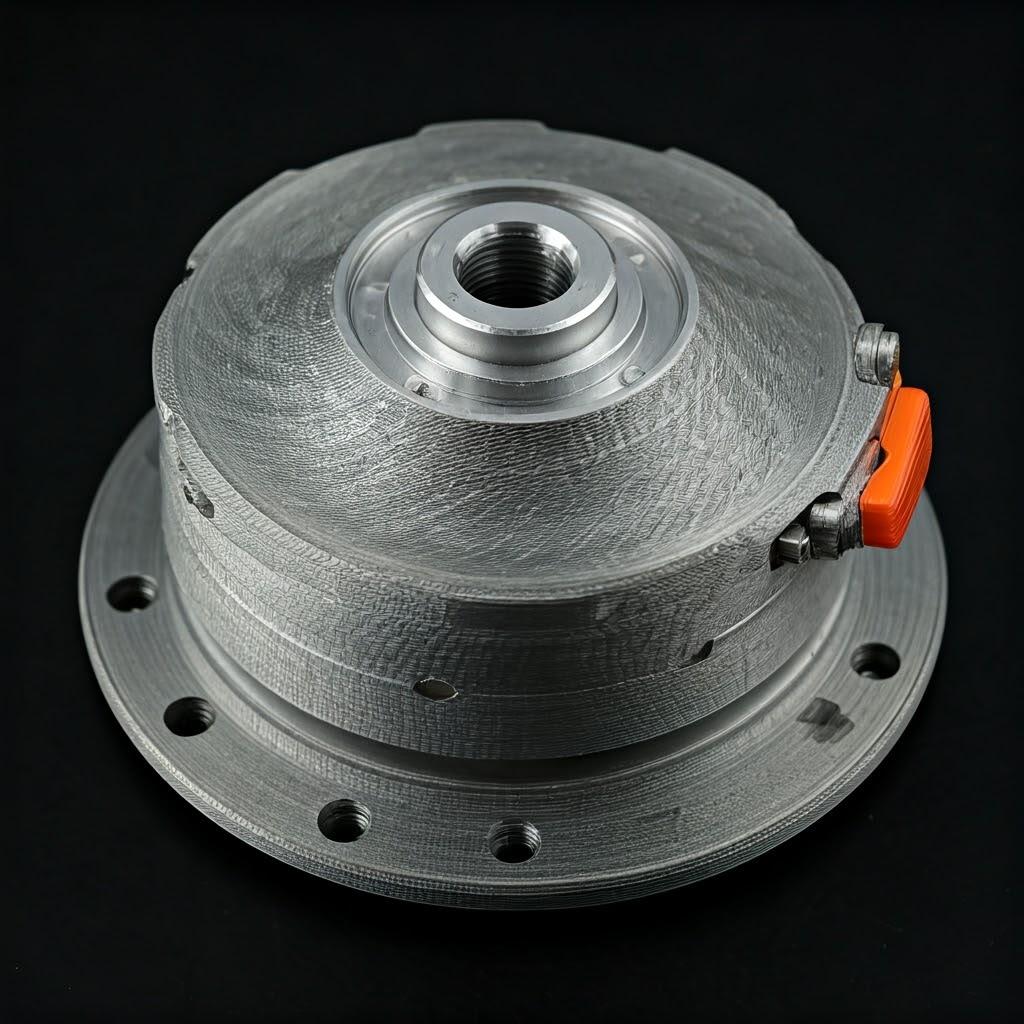
Beyond the Build: Essential Post-Processing for Metal AM Rotor Supports
Once the metal 3D printer completes its work, the journey of the electric motor rotor support is far from over. The “green” part, fresh off the build plate, requires several crucial 후처리 steps to transform it into a functional, reliable component ready for assembly. These steps are essential to relieve internal stresses, remove support structures, achieve final dimensional accuracy and surface finish, and ensure the desired material properties. Understanding these requirements is vital for planning production timelines and costs.
Common post-processing steps for metal AM rotor supports include:
1. Stress Relief / Heat Treatment:
- Why: The rapid heating and cooling cycles inherent in PBF processes create significant internal stresses within the printed part. If not relieved, these stresses can cause distortion during subsequent steps (like removal from the build plate or machining) or even lead to premature failure in service.
- 프로세스: The entire build plate with the part(s) still attached is typically placed in a furnace and subjected to a specific heat treatment cycle. This involves heating to a defined temperature (below the melting point but high enough to allow atomic movement), holding for a period, and then cooling at a controlled rate.
- For AlSi10Mg: Typically involves stress relief at around 250-300°C. Solution treatment and aging (T6 condition) might also be applied to maximize strength, involving higher temperatures followed by quenching and artificial aging.
- For IN625: Stress relief usually occurs at higher temperatures (e.g., 870-980°C). Solution annealing or aging treatments might also be performed depending on the desired final properties (strength vs. ductility/corrosion resistance).
- Atmosphere: Heat treatments are often performed in a vacuum or inert atmosphere (like Argon) to prevent oxidation, especially for reactive materials or high-temperature treatments.
2. Part Removal from Build Plate:
- 방법: After stress relief (if performed on the plate), the rotor support needs to be separated from the metal build plate it was printed on. This is typically done using:
- Wire EDM (Electrical Discharge Machining): Precise, minimal force, good for complex interfaces.
- Band Sawing: Faster, more common for simpler geometries or where the interface isn’t critical.
- Consideration: The separation method should minimize stress induction and avoid damaging the part.
3. Support Structure Removal:
- Why: Supports are necessary during the build but must be removed afterward. This can be one of the most labor-intensive and challenging post-processing steps, especially for complex internal supports.
- 방법:
- Manual Removal: Using pliers, cutters, grinders, and chisels (requires skill and care).
- CNC Machining: Milling or grinding away support structures, often more precise and repeatable for accessible supports.
- Electrochemical Machining (ECM) or Chemical Etching: Can sometimes be used for specific materials and geometries, particularly internal channels, but requires careful control.
- Impact: Support removal locations often leave witness marks or rougher surfaces (“support scars”) that typically require further finishing. DfAM plays a crucial role in designing supports for easier support removal methods.
4. Hot Isostatic Pressing (HIP):
- Why: Although PBF aims for fully dense parts, microscopic internal voids or pores can sometimes remain. HIP closes these internal pores, improving fatigue life, ductility, and impact strength. It’s often specified for critical applications (aerospace, medical).
- 프로세스: Involves subjecting the part to high temperature (below melting point) and high isostatic pressure (using an inert gas like Argon) simultaneously in a specialized vessel.
- 혜택: Results in near 100% theoretical density, enhancing mechanical properties and ensuring consistency. Especially beneficial for fatigue-critical rotor supports.
5. Machining for Tolerances and Finish:
- Why: As discussed previously, to achieve tight CNC machining allowances for bearing fits, mating surfaces, and specific surface finish requirements (Ra).
- 프로세스: Using CNC mills, lathes, or grinders to machine designated features to final specifications. Requires careful fixturing of the potentially complex AM part.
6. Surface Finishing:
- Why: To improve the overall surface quality beyond the as-built or support-removed state, reduce friction, improve aesthetics, or prepare for coatings.
- 방법:
- Abrasive Blasting (Sand/Bead Blasting): Provides a uniform matte finish, removes loose powder, can slightly improve fatigue life via compressive stress.
- 텀블링/진동 마감: Uses abrasive media in a rotating or vibrating bowl to smooth surfaces and deburr edges (good for batches of smaller parts).
- Polishing/Lapping: Manual or automated processes for achieving very smooth, mirror-like finishes on specific surfaces.
- 전기 연마: An electrochemical process that removes a thin layer of material, smoothing surfaces and improving corrosion resistance (common for stainless steels, applicable to IN625).
7. Coating (Optional):
- Why: To add specific surface properties not inherent to the base material, such as wear resistance, corrosion protection (beyond base material capability), thermal barrier, or specific electrical properties.
- 방법: PVD (Physical Vapor Deposition), CVD (Chemical Vapor Deposition), thermal spray coatings, plating, painting.
Post-Processing Workflow Summary:
The exact sequence and necessity of these steps depend on the material, design complexity, and application requirements. A typical workflow might look like this:
Build -> Stress Relief (on plate) -> Part Removal -> Support Removal -> (Optional HIP) -> CNC Machining -> Surface Finishing (Blasting/Tumbling/Polishing) -> (Optional Coating) -> Final Inspection
Understanding the necessity and implications of these 후처리 요구 사항 is critical for accurately estimating costs and lead times. Experienced AM partners like Met3dp incorporate these steps into their production planning, offering a complete manufacturing solution from powder to finished surface finishing techniques and validated component, ensuring the final rotor support meets all engineering specifications.
Navigating Challenges: Common Issues in Printing Rotor Supports and Solutions
While metal AM offers significant advantages, it’s not without its challenges, especially when producing complex, high-precision components like electric motor rotor supports. Awareness of potential issues allows engineers and manufacturers to proactively implement mitigation strategies during design, simulation, build preparation, and post-processing phases. Partnering with experienced service providers who understand how to navigate these hurdles is crucial.
Here are some common challenges encountered when 3D printing metal rotor supports and how to address them:
1. Warping and Distortion:
- Cause: Uneven heating and cooling during the PBF process leads to the buildup of internal residual stresses. When these stresses exceed the material’s yield strength or the part’s structural stiffness, they can cause the component to warp, lift from the build plate, or distort after removal. This is particularly prevalent in large flat sections, thin walls, or asymmetric designs. IN625, with its higher melting point and thermal gradients, can be more susceptible than AlSi10Mg.
- 완화 전략:
- Design Optimization (DfAM): Use fillets instead of sharp corners, incorporate ribs for stiffness, minimize large solid cross-sections, potentially use lattice structures.
- 빌드 오리엔테이션: Orient the part strategically on the build plate to minimize thermal gradients and the cross-sectional area parallel to the recoater blade.
- 지원 구조: Use robust support structures designed not just to hold overhangs but also to anchor the part firmly to the build plate and act as heat sinks.
- Process Simulation: Employ simulation software to predict stress accumulation and distortion, allowing for pre-compensation in the CAD model or optimization of orientation/supports.
- Optimized Parameters: Use validated process parameters (laser/beam power, scan speed, hatching strategy) known to minimize stress for the specific material and geometry.
- 스트레스 해소: Perform appropriate heat treatment cycles immediately after the build, often while the part is still on the build plate.
2. Residual Stress Management:
- Issue: Even if warping doesn’t occur, high residual stresses can remain locked within the part, potentially impacting fatigue life, dimensional stability during machining, or leading to cracking.
- 완화 전략:
- All strategies listed for warping mitigation also help manage residual stress.
- Post-Build Heat Treatment: Essential for reducing residual stress to acceptable levels. The specific cycle (temperature, time, cooling rate) is critical and material-dependent.
- HIP: Can help relieve stress and improve properties, although primarily targeted at closing porosity.
3. Porosity:
- Cause: Microscopic voids within the printed material can arise from several factors:
- 가스 다공성: Trapped gas (e.g., Argon shielding gas, dissolved gases in powder) within the melt pool.
- 융합 부족 다공성: Insufficient energy input leading to incomplete melting and bonding between layers or scan tracks.
- 키홀 다공성: Excessive energy density causing melt pool instability and vaporization, trapping gas.
- 파우더 품질: Internal porosity within powder particles or poor powder packing.
- Impact: Porosity degrades mechanical properties, particularly fatigue strength and ductility. Critical for rotating components like rotor supports.
- 완화 전략:
- Optimized Process Parameters: Precise control over laser/beam power, scan speed, layer thickness, and hatch spacing is crucial to ensure stable melting and full fusion.
- High-Quality Powder: Use powders with low internal gas content, controlled particle size distribution, and good flowability (like those from Met3dp produced via advanced atomization/PREP). Prevent powder contamination prevention through proper handling and storage.
- Shielding Gas Control: Ensure proper flow and purity of the inert shielding gas in the build chamber.
- HIP: Effective at closing internal porosity after printing.
- 비파괴 검사(NDT): Use X-ray or CT scanning to detect internal porosity in critical parts.
4. Support Removal Challenges:
- Issue: Supports in intricate internal channels or on delicate features can be extremely difficult or impossible to remove without damaging the part. Incomplete removal can impede fluid flow (if used for cooling) or act as crack initiation sites.
- 완화 전략:
- DfAM: Design the part to minimize the need for internal or critical surface supports. Orient the part optimally.
- Support Design: Use support types designed for easier removal (e.g., perforated supports, tapered supports, materials designed to break away easily if using multi-material systems, though less common in PBF).
- Access Planning: Ensure clear line-of-sight and tool access for manual or CNC removal during the design phase.
- Specialized Removal Techniques: Consider dissolvable supports (less common for metals) or advanced methods like electrochemical machining for specific cases.
5. Cracking:
- Cause: Primarily driven by high residual stresses, especially in materials prone to solidification cracking or those with low ductility at high temperatures (some nickel alloys or specialized aluminum alloys can be susceptible if parameters are not optimized). Can occur during the build or subsequent heat treatment.
- 완화 전략:
- 재료 선택: Choose alloys known for good weldability/printability.
- 매개변수 최적화: Careful control of thermal gradients via scan strategies and energy input.
- Preheating: Using elevated build plate temperatures (common in EBM, sometimes used in SLM for crack-prone alloys).
- Stress Relief Design: Incorporating stress-relieving features in the geometry.
- Controlled Heating/Cooling: Particularly during post-build heat treatment.
6. Surface Finish Deviations:
- Issue: Achieving consistent and specified surface finish across complex geometries can be difficult due to orientation effects and support interactions.
- 완화 전략:
- Orientation Optimization: Prioritize critical surfaces for optimal orientation (up-facing, vertical).
- Targeted Post-Processing: Plan for specific finishing operations (machining, polishing, blasting) on surfaces requiring controlled roughness.
- Parameter Tuning: Fine-tuning process parameters can influence as-built surface quality.
Successfully producing reliable metal AM rotor supports requires anticipating these common challenges and implementing robust solutions throughout the workflow. A proactive approach, combining smart design (DfAM), process simulation, meticulous build failure analysis when necessary, high-quality materials and equipment, and controlled post-processing, is essential. This is where the expertise of a dedicated AM partner like Met3dp becomes invaluable, providing the process knowledge and quality control necessary to overcome these hurdles and deliver components meeting the demanding requirements of the electric motor industry.
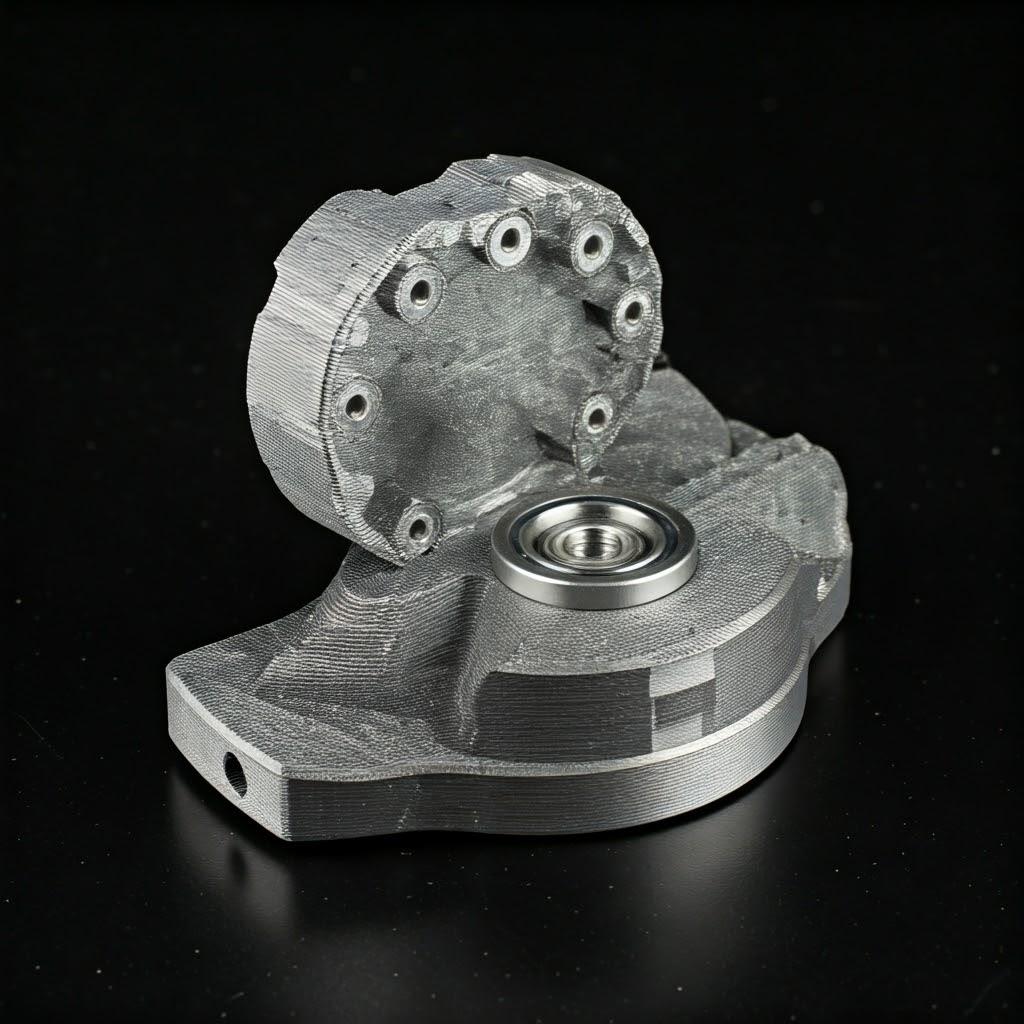
Supplier Selection: How to Choose the Right Metal 3D Printing Service Provider for Rotor Supports
Selecting the right manufacturing partner is as crucial as perfecting the design and material choice, especially for critical components like electric motor rotor supports produced via metal AM. The quality, reliability, and performance of the final part heavily depend on the expertise, equipment, processes, and quality systems of your chosen metal AM service bureau. For engineers and procurement managers navigating this landscape, particularly those seeking wholesale AM services or long-term 공급업체 relationships, a structured evaluation process is key.
Here are critical factors to consider when evaluating potential metal 3D printing service providers for rotor supports:
1. Technical Expertise and Experience:
- Application Knowledge: Does the provider have demonstrable experience printing parts for similar applications (e.g., automotive, aerospace, industrial machinery) or similar component types (e.g., rotating machinery parts, complex housings)? Can they discuss relevant case studies or examples?
- 재료 전문성: Do they specialize in the required materials (AlSi10Mg, IN625)? Do they understand the nuances of printing these specific alloys, including parameter optimization, heat treatment protocols, and potential challenges? Do they manufacture their own high-quality powders or have stringent quality control for sourced powders? Companies like Met3dp, which manufacture their own 고품질 금속 분말 using advanced Gas Atomization and PREP technologies, often have deeper material science understanding.
- DfAM Support: Can their engineering team provide expert DfAM consultation to help optimize your rotor support design for printability, performance, and cost-effectiveness?
2. Equipment and Technology:
- 머신 기능: Do they operate industrial-grade PBF machines (SLM/EBM) suitable for AlSi10Mg and IN625? What is the build volume, accuracy, and monitoring capability of their equipment? Do they have a sufficient number of machines to handle your potential volume and provide redundancy? Met3dp emphasizes its industry-leading print volume, accuracy, and reliability tailored for mission-critical parts.
- 프로세스 제어: What measures are in place for process monitoring and control during the build (e.g., melt pool monitoring, oxygen level control, thermal imaging)? Consistent process control is vital for part quality and repeatability.
- 파우더 처리: Do they have robust procedures for powder handling, storage, sieving, and recycling to prevent contamination and ensure powder quality throughout its lifecycle?
3. Quality Management Systems and Certifications:
- QMS: Is the provider certified to relevant quality standards?
- ISO 9001: Essential baseline for quality management.
- AS9100: Crucial for aerospace applications, indicating stricter process control and traceability.
- IATF 16949: Important for automotive suppliers.
- ISO 13485: Required for medical device components.
- Traceability: Can they provide full material and process traceability, from raw powder batch to final inspection report? This is non-negotiable for critical parts.
- 검사 기능: Do they have in-house CMM, 3D scanning, NDT (X-ray/CT), surface analysis, and material testing capabilities to validate part quality?
4. Post-Processing Capabilities:
- Integrated Services: Does the provider offer a comprehensive suite of in-house or tightly managed external post-processing services, including stress relief, heat treatment (with appropriate atmosphere control), support removal, HIP, precision CNC machining, and various surface finishing options? A single-source provider simplifies the supply chain.
- Machining Expertise: If post-print machining is required for tolerances, do they have experience machining complex AM parts, including appropriate fixture design and understanding of potential distortions?
5. Capacity, Lead Time, and Cost:
- Capacity: Can they meet your volume requirements, both for prototypes and potential series production?
- 리드 타임: What are their typical typical lead times for parts similar to your rotor support, considering material, complexity, and post-processing? Do they offer expedited services if needed?
- Cost Structure: Is their pricing transparent? Do they provide detailed quotes outlining costs for printing, material, supports, post-processing, and quality assurance? Understand their B2B pricing models if seeking wholesale or ongoing supply.
6. Communication and Support:
- 응답성: Are they responsive to inquiries and requests for technical support?
- 프로젝트 관리: Do they assign a dedicated point of contact for your project?
- Collaboration: Are they willing to work collaboratively to solve challenges and optimize results?
7. Company Stability and Reputation:
- Track Record: How long have they been providing metal AM services? What is their reputation in the industry? Can they provide references?
- 전문성: Look into the background of their technical team. Companies like Met3dp, with decades of collective expertise in metal additive manufacturing, offer a strong foundation of knowledge and reliability. Headquartered in Qingdao, China, they provide comprehensive solutions spanning printers, powders, and application development.
Evaluation Checklist Summary:
기준 | 주요 질문 | Why it Matters for Rotor Supports |
---|---|---|
Technical/Materials Expertise | Experience with AlSi10Mg/IN625? Application knowledge? DfAM support? Powder quality control? | Ensures understanding of material behavior & design optimization. |
Equipment/Technology | Industrial PBF machines? Build volume? Accuracy? Process monitoring? Powder handling? | Determines part quality, consistency, and achievable complexity. |
Quality/Certifications | ISO 9001? AS9100/IATF? Traceability? Inspection capabilities (CMM, NDT)? | Guarantees process control, part validation, and reliability. |
포스트 프로세싱 | In-house heat treatment, machining, finishing? HIP? Support removal skill? | Ensures parts meet final tolerance, finish, & property requirements. |
Capacity/Lead Time/Cost | Volume capability? Quoted lead times? Pricing transparency? B2B models? | Determines production feasibility, scheduling, and budget alignment. |
Support/Communication | Responsiveness? Technical support quality? Project management? Collaboration willingness? | Facilitates smooth project execution and problem-solving. |
Company Reputation | Years in business? Industry standing? References? Team expertise (e.g., Met3dp’s collective experience)? | Indicates reliability, stability, and trustworthiness as a partner. |
시트로 내보내기
올바른 선택 metal AM service provider evaluation process is an investment in the success of your project. Thorough due diligence, focusing on these key areas, will help you identify a partner like Met3dp capable of delivering high-quality, reliable electric motor rotor supports that meet demanding specifications.
Understanding Investment: Cost Factors and Lead Times for AM Rotor Supports
While metal additive manufacturing unlocks significant performance and design benefits for electric motor rotor supports, understanding the associated costs and production timelines is crucial for project planning and budgeting. Both cost and lead time are influenced by a complex interplay of factors specific to AM. Procurement managers and engineers need insight into these metal 3D printing cost drivers to make informed decisions and manage expectations effectively.
Key Cost Factors:
- 재료비:
- 파우더 가격: The raw material powder is a significant cost component. Nickel superalloys like IN625 are substantially more expensive per kilogram than aluminum alloys like AlSi10Mg. The price can also vary based on powder quality, sphericity, particle size distribution, and supplier. Met3dp, manufacturing its own high-performance powders, aims to provide competitive value.
- Material Consumption: The total volume of the part, including any necessary support structures, directly impacts the amount of powder consumed. While unused powder can often be recycled, there are costs associated with sieving, testing, and rejuvenating it.
- 머신 시간(빌드 시간):
- 파트 볼륨 및 높이: Larger parts and taller builds (requiring more layers) take longer to print, occupying expensive machine time. Industrial metal AM machines represent significant capital investment, and their hourly operating rates are a major cost factor.
- 복잡성: While AM handles complexity well, very intricate features or dense support structures can sometimes slow down the printing process (e.g., shorter scan vectors, more recoater movements).
- Nesting/Build Density: Printing multiple parts simultaneously in one build (nesting) can significantly reduce the per-part machine time cost, making AM more economical for small to medium batch production. Skilled service providers optimize build layouts for efficiency.
- Labor and Setup:
- 빌드 준비: Time required for engineers to prepare the build file, including orientation optimization, support generation, and slicing.
- Machine Setup/Teardown: Loading powder, setting up the build plate, preheating, and then removing the build, cleaning the machine.
- Manual Intervention: Some level of operator oversight is typically required during the build.
- 후처리 비용:
- 지원 제거: Can be highly labor-intensive, especially for complex parts or difficult-to-access supports. The amount and complexity of supports directly impact this cost.
- Heat Treatment/HIP: Furnace time, energy consumption, and controlled atmosphere costs add up. HIP requires specialized, expensive equipment.
- CNC 가공: Required for tight tolerances and specific finishes. Costs depend on the number of features to be machined, the complexity of setups/fixturing, and machining time.
- 표면 마감: Costs vary widely depending on the method (blasting is relatively inexpensive, multi-stage polishing is costly) and the surface area treated.
- Inspection/QA: Time and resources for dimensional inspection (CMM), surface analysis, NDT, and documentation.
- Design and Engineering:
- DfAM Services: If the service provider assists with design optimization, topology analysis, or simulation, these engineering services will be factored into the cost.
Typical Lead Times:
Lead time refers to the total time from order placement to shipment of the finished part. For metal AM rotor supports, this can vary significantly based on similar factors to cost:
- 인쇄 시간: Can range from hours for small, simple parts to several days or even weeks for very large, complex builds or high-volume nested builds.
- 후처리: This often takes as long or longer than the printing itself.
- Heat Treatment: Cycles can take 8-24 hours or more, plus furnace loading/unloading/cooling.
- Machining: Depends heavily on complexity, feature count, and machine shop scheduling (can range from days to weeks).
- Support Removal/Finishing: Varies greatly with part complexity (hours to days).
- HIP: Requires scheduling on specialized equipment, can add several days to a week or more.
- Queue Time: The service provider’s current backlog for machines, post-processing equipment, and personnel significantly impacts start time.
- Inspection and Shipping: Final QA checks and shipping logistics add to the overall time.
Estimated Lead Time Breakdown (Illustrative):
스테이지 | Typical Duration (Simple Part) | Typical Duration (Complex Part w/ Machining & HIP) | 참고 |
---|---|---|---|
Order Review/Setup | 1-2 Days | 2-4 Days | Includes DfAM checks, build prep, scheduling |
인쇄 | 1-3 Days | 3-10+ Days | Highly dependent on size, height, nesting |
열처리 | 1-2 Days | 1-3 Days | Includes furnace cycle, cooling, handling |
Part/Support Removal | 0.5-1 Day | 1-3 Days | Depends on complexity, access |
HIP (if required) | N/A | 3-7 Days | Includes shipping to/from HIP facility if not in-house, cycle time |
CNC 가공 | N/A | 3-10 Days | Depends on features, tolerances, shop scheduling |
표면 마감 | 0.5-1 Day | 1-3 Days | Blasting vs. polishing etc. |
Inspection/QA | 0.5 Days | 1-2 Days | CMM, NDT etc. |
Total Estimated | ~5 – 10 Business Days | ~15 – 35+ Business Days | Highly variable, always request specific quote |
시트로 내보내기
Key Takeaways for Procurement & Engineering:
- Complexity Drives Cost & Time: More complex geometries, tighter tolerances, and extensive post-processing significantly increase both cost and lead time.
- Material Choice Matters: IN625 parts will be more expensive than AlSi10Mg parts of the same design due to powder cost and potentially more rigorous processing.
- Volume Impacts Per-Part Cost: While setup costs are amortized over larger batches, increasing volume also ties up machine capacity for longer. Evaluate B2B pricing models for potential discounts at higher quantities.
- DfAM is Crucial: Optimizing the design for AM can significantly reduce material usage, print time, support needs, and post-processing effort, directly lowering cost and lead time.
- Get Detailed Quotes: Always obtain comprehensive quotes from potential suppliers detailing all cost components and estimated lead times based on your specific design and requirements.
Understanding these 비용 요인 및 리드타임 dynamics allows for better project planning, budgeting, and realistic scheduling when adopting metal AM for producing high-performance electric motor rotor supports.
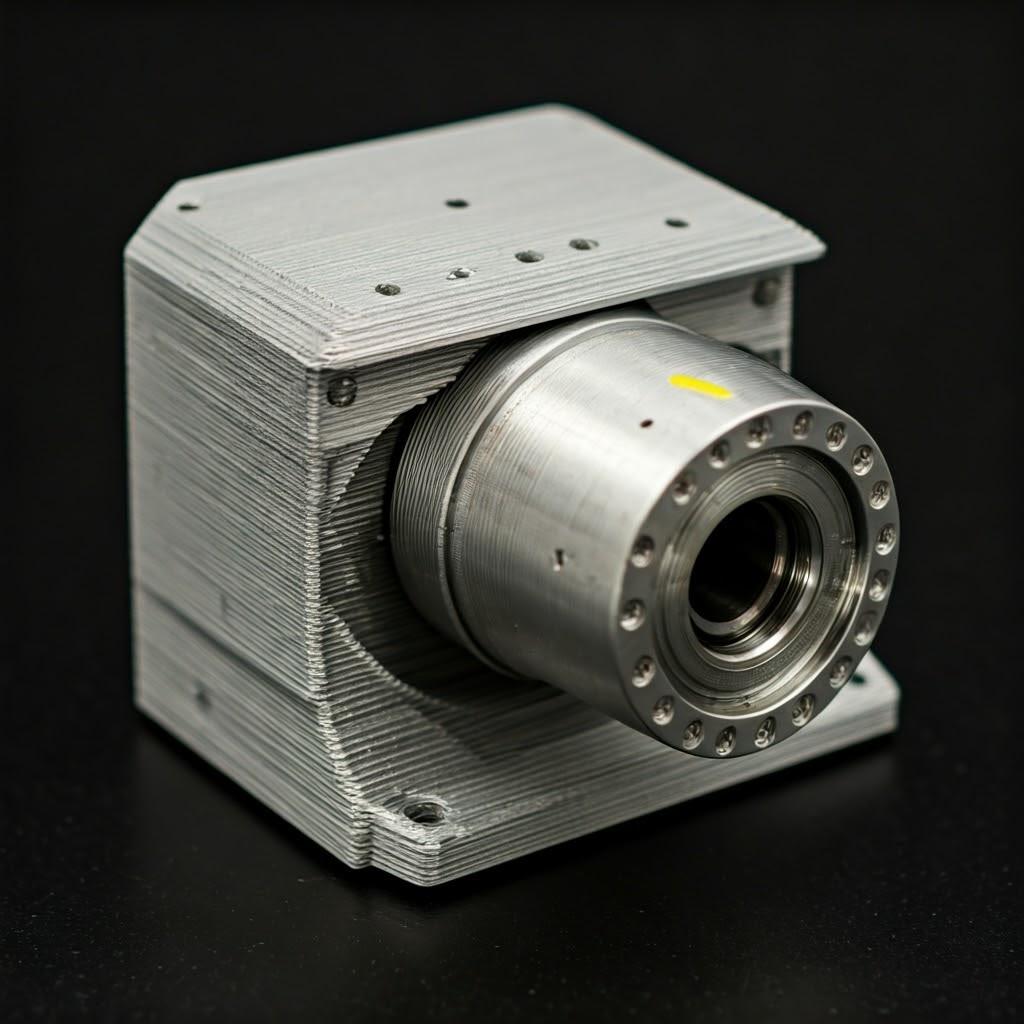
Frequently Asked Questions (FAQ) about Metal AM Rotor Supports
Here are answers to some common questions engineers and procurement managers have when considering metal additive manufacturing for electric motor rotor supports:
1. How does the strength of a 3D printed metal rotor support compare to one made traditionally (e.g., machined from billet or cast)?
The mechanical properties (like yield strength, ultimate tensile strength, fatigue strength) of metal AM parts, when produced using optimized parameters and appropriate post-processing (like heat treatment and HIP), can be comparable or even superior to cast components and potentially rival wrought materials (machined from billet), especially in the build direction.
- AlSi10Mg: Typically achieves properties similar to or better than A356/A360 cast aluminum alloys after proper heat treatment (T6).
- IN625: Can achieve properties meeting or exceeding wrought annealed specifications, particularly after HIP which eliminates internal porosity. However, properties can exhibit some anisotropy (variation depending on build direction vs. transverse direction). It’s crucial to design and test based on validated material data from the AM process used, rather than relying solely on standard wrought or cast material datasheets. Working with experienced providers like Met3dp ensures processes are optimized to achieve target mechanical properties reliably.
2. Is metal 3D printing cost-competitive with CNC machining or casting for rotor supports?
The cost comparison (AM vs. CNC vs. Casting) depends heavily on several factors:
- 복잡성: For highly complex geometries (internal channels, lattices, topology-optimized shapes) that are difficult or impossible to machine or cast, AM can be more cost-effective, even at low volumes, by eliminating tooling costs and complex machining setups.
- 볼륨:
- Prototypes & Low Volume (1-100s): AM is often highly competitive due to the lack of tooling costs (vs. casting) and potentially complex setup/programming (vs. CNC).
- Medium Volume (100s-1000s): The comparison becomes closer. Efficient nesting and optimized post-processing in AM compete against amortized tooling costs (casting) or efficient multi-axis CNC production. Part consolidation enabled by AM can shift the balance in its favor.
- High Volume (10,000s+): Traditional methods like casting or high-speed CNC machining are typically more cost-effective for simpler designs due to economies of scale.
- Material: AM might allow the use of expensive materials (like IN625) more efficiently (less waste) than subtractive machining, potentially offsetting higher process costs for certain designs.
- Total Cost of Ownership: Consider factors beyond just part price, such as reduced assembly costs (due to part consolidation), improved performance (lighter weight, better cooling), and faster time-to-market enabled by AM.
3. What are the typical lead times for obtaining prototype or production batches of metal AM rotor supports?
As detailed in the previous section, lead time estimates vary significantly.
- 프로토타입: For a single, moderately complex rotor support without extensive post-processing, lead times might range from 1 to 3 weeks, depending on supplier backlog and material availability.
- Production Batches: For small-to-medium batches requiring full post-processing (heat treat, machining, inspection), lead times are more likely in the range of 4 to 8 weeks, potentially longer for very complex parts, large batches, or if specialized processing like HIP is required. It’s essential to get specific lead time quotes from your chosen supplier based on your final part design, material, quantity, and finishing requirements. Factors like machine availability and existing queue heavily influence actual delivery times.
Conclusion: The Future of Electric Motors is Additive – Embracing AM Rotor Supports
The journey through the intricacies of producing electric motor rotor supports via metal additive manufacturing reveals a powerful synergy between advanced design possibilities and cutting-edge production technology. From leveraging the lightweighting potential of AlSi10Mg to harnessing the high-temperature resilience of IN625, metal AM offers engineers unprecedented tools to optimize these critical components. By enabling complex geometries through 토폴로지 최적화, integrating cooling channels, consolidating parts, and accelerating development cycles, AM directly addresses the relentless push for higher performance, power density, and efficiency in electric motors across diverse industries.
While challenges related to precision, post-processing, and cost exist, they are navigable through careful Design for Additive Manufacture (DfAM), robust process control, and strategic supplier selection. Understanding metal AM tolerances, surface finish capabilities, and the necessity of steps like heat treatment and machining allows for realistic planning and successful implementation. The ability to achieve mechanical properties comparable or superior to traditional methods, coupled with the design freedoms offered, makes a compelling case for adopting AM, particularly for demanding applications in aerospace, automotive, medical, and high-performance industrial machinery.
The investment in metal AM for rotor supports extends beyond the component itself; it represents an investment in manufacturing innovation, supply chain agility, and a potential 경쟁 우위. As the technology matures, costs decrease, and material options expand, metal 3D printing is set to become an increasingly integral part of advanced motor technology.
For companies looking to explore or scale their use of metal AM for rotor supports or other critical components, partnering with a knowledgeable and capable provider is paramount. Organizations like Met3dp, with their comprehensive ecosystem of industry-leading printers, high-quality proprietary metal powders, and deep application expertise, stand ready to assist. They provide the necessary support from design consultation through to fully validated production parts, empowering businesses to transition confidently towards next-generation manufacturing.
To learn more about how Metal3DP’s additive manufacturing solutions can revolutionize your electric motor designs and power your organization’s journey into digital manufacturing, visit their website at https://met3dp.com/. The future of high-performance electric motors is inextricably linked with the capabilities of additive manufacturing – embracing it today means building the competitive edge for tomorrow.
공유
중국 칭다오에 본사를 둔 선도적인 적층 제조 솔루션 제공업체인 MET3DP Technology Co. 당사는 산업용 3D 프린팅 장비와 고성능 금속 분말을 전문으로 합니다.
관련 기사
Met3DP 소개
최근 업데이트
제품
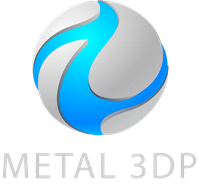
3D 프린팅 및 적층 제조용 금속 분말