Custom Enclosures for Thermal Batteries via 3D Printing
목차
Introduction: Revolutionizing Thermal Battery Enclosures with Metal 3D Printing
Thermal batteries stand as unique, high-power density energy sources, critical for applications demanding immediate, reliable power after long periods of storage. Unlike conventional batteries, they remain inert until activated, typically by a pyrotechnic charge, making them ideal for single-use, mission-critical scenarios often found in the 항공우주 및 방어 sectors. The enclosure housing these vital components is far more than just a container; it’s a precisely engineered shield responsible for structural integrity, environmental protection, and operational safety. Traditionally, manufacturing these custom metal enclosures involved subtractive methods like CNC machining from billet or complex fabrication processes. However, the advent of 금속 적층 제조(AM)일반적으로 ~로 알려짐 금속 3D 프린팅, is fundamentally reshaping how these critical components are designed and produced.
Metal 3D printing technologies, such as Laser Powder Bed Fusion (LPBF) and Electron Beam Melting (EBM), build parts layer by layer directly from digital models using high-performance metal powders. This approach unlocks unprecedented design freedom, enabling the creation of highly complex, optimized, and lightweight thermal battery enclosures that were previously impossible or prohibitively expensive to manufacture. For engineers and procurement managers in demanding industries, understanding the potential of AM is crucial for developing next-generation thermal batteries with enhanced performance, reduced weight, and potentially faster development cycles. This shift towards additive manufacturing represents a significant leap forward, offering tailored solutions for the unique challenges posed by 항공우주 부품, 국방 애플리케이션, and other specialized industrial systems requiring robust, reliable power sources. Companies like Met3dp are at the forefront, providing both the advanced equipment and high-quality materials needed to realize the full potential of AM for these demanding applications.
What Are Thermal Battery Enclosures Used For?
The enclosure of a thermal battery performs several critical functions essential for the battery’s reliable operation, particularly under the extreme conditions often encountered in its typical deployment environments. Understanding these functions highlights the stringent requirements placed upon the enclosure’s design and material properties.
- Structural Support and Integrity: The enclosure provides the primary structure, holding the internal battery stack (cells, separators, electrolytes, heat sources) securely in place. It must withstand significant mechanical stresses, including launch accelerations, high G-forces during maneuvers, and potential impacts. The integrity of the enclosure ensures the precise alignment and contact of internal components, which is vital for proper activation and performance.
- Environmental Protection: Thermal batteries are often deployed in harsh environments. The enclosure acts as a barrier, protecting the sensitive internal components from:
- Shock and Vibration: Intense vibrations during missile flight, spacecraft launch, or vehicle operation necessitate robust enclosure designs.
- Temperature Extremes: While designed to operate at high internal temperatures post-activation, the enclosure must protect the inert battery during storage across a wide range of ambient temperatures.
- Humidity and Contaminants: For long-term storage and reliability, the enclosure often needs to provide a hermetic or near-hermetic seal to prevent moisture ingress or contamination that could degrade components or affect activation.
- 격리: Upon activation, thermal batteries generate significant heat very rapidly, melting the electrolyte and initiating the electrochemical reaction. The enclosure must safely contain these high temperatures (often exceeding 500°C) and internal pressures that might develop, preventing leaks or rupture. This containment is crucial for the safety of the overall system, whether it’s a missile power source, spacecraft component또는 emergency power unit.
- Thermal Management (Pre-Activation): In some designs, the enclosure might play a role in passively managing the temperature of the battery before activation, ensuring it remains within the specified storage range.
Key Applications & Operating Conditions:
The demanding functions of the enclosure are driven by its applications:
- Missiles and Munitions: Providing primary power for guidance, control, and telemetry during flight, often experiencing extreme acceleration and vibration.
- Spacecraft: Powering deployment mechanisms, emergency systems, or specific mission phases, requiring high reliability and low weight in the vacuum and thermal extremes of space.
- Torpedoes and Underwater Vehicles: Supplying power in high-pressure, corrosive marine environments.
- Aircraft Emergency Power: Powering essential systems like emergency lighting or flight controls if primary power is lost.
- Downhole Tools (Oil & Gas): Providing power for sensors and actuators in high-temperature, high-pressure subterranean environments.
Given these thermal battery applications, the enclosure must be designed and manufactured to meet stringent performance criteria, often governed by rigorous military or aerospace standards. The need for a high-reliability power source in these defense system enclosures or critical industrial parts makes the enclosure’s quality paramount.
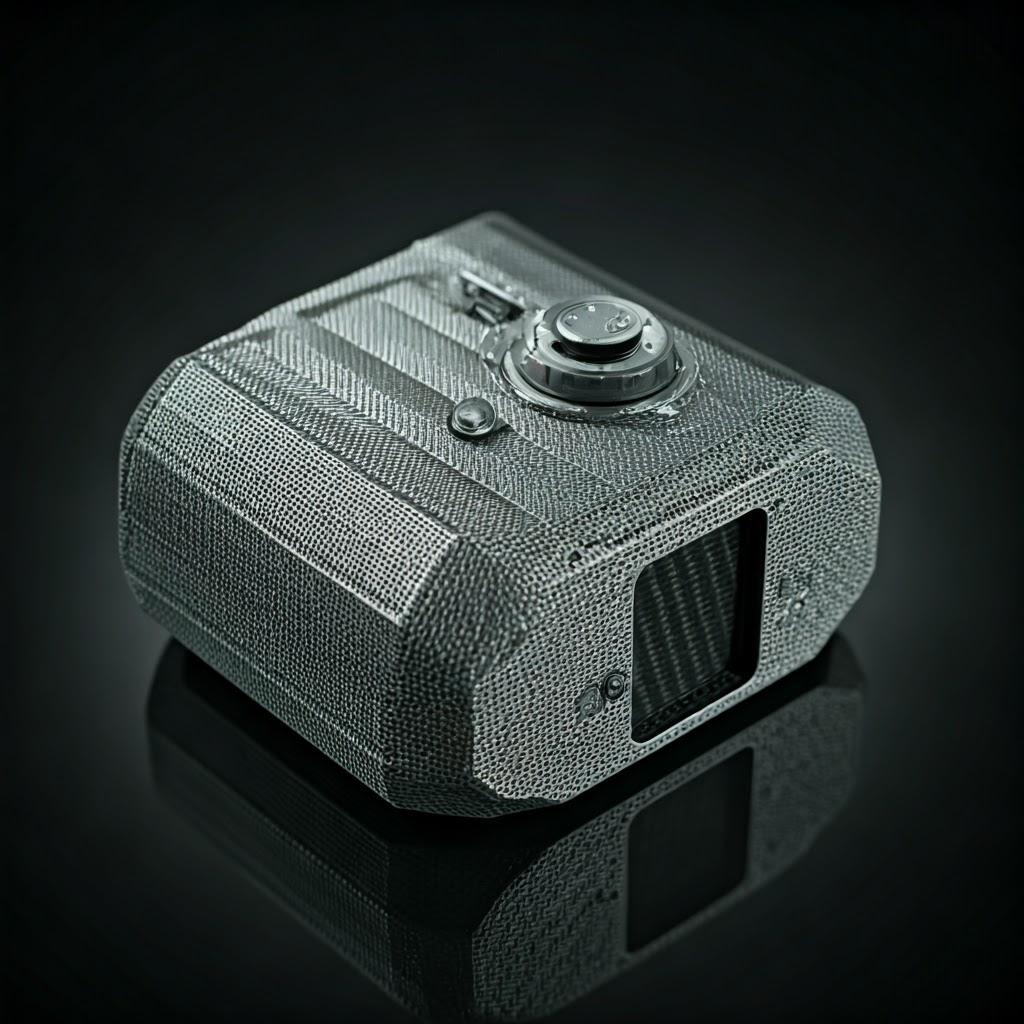
Why Use Metal 3D Printing for Thermal Battery Enclosures?
While traditional manufacturing methods like CNC machining, casting, and sheet metal fabrication have long been used for thermal battery enclosures, 금속 적층 제조(AM) offers compelling advantages that directly address the evolving demands for higher performance, lower weight, and increased design complexity in these critical components. Comparing 3D printing vs CNC machining or other conventional techniques reveals why AM is becoming an increasingly attractive option for manufacturing complex metal parts.
Key Advantages of Metal AM for Enclosures:
- 독보적인 디자인 자유도: AM builds parts layer-by-layer, liberating designers from many constraints imposed by subtractive or formative processes. This allows for:
- 복잡한 내부 기능: Integration of intricate cooling channels, internal baffles, or optimized pathways for activation gases without complex assembly or machining setups.
- Conformal Designs: Enclosures can be shaped to fit precisely within tight space envelopes in missiles or satellites, maximizing energy density.
- Organic Shapes: Creation of smooth, curved surfaces that are difficult or impossible to machine efficiently.
- Significant Weight Reduction: Mass is a critical factor in aerospace and defense applications. AM enables:
- 토폴로지 최적화: Software algorithms can remove material from non-critical areas while maintaining structural integrity, resulting in significantly lighter parts.
- 격자 구조: Internal lattice or gyroid structures can replace solid material, drastically reducing weight while providing tailored stiffness and strength. This lightweight enclosure design capability is a major driver for AM adoption.
- 파트 통합: Multiple components that would traditionally be manufactured separately and then assembled (e.g., enclosure body, brackets, connector housings) can often be printed as a single, monolithic part. This reduces:
- Assembly time and labor costs.
- Potential points of failure (joints, fasteners).
- Overall part count and supply chain complexity.
- 신속한 프로토타이핑 및 반복: Creating prototypes of complex enclosure designs using traditional methods can be slow and costly. AM allows for the production of functional metal prototypes in days rather than weeks or months. This facilitates:
- Faster design validation and testing cycles.
- Quicker implementation of design improvements based on test results.
- Reduced time-to-market for new thermal battery systems. This capability for rapid prototyping thermal battery components is invaluable.
- Suitability for Low-to-Mid Volume Production: Thermal batteries are often produced in relatively low volumes compared to consumer goods. Setting up tooling for casting or complex machining jigs can be uneconomical. AM is tool-less, making it cost-effective for producing highly customized or complex enclosures in smaller batch sizes. Leading metal AM suppliers can efficiently manage these production runs.
- 소재의 다양성: AM processes can work with a growing range of high-performance metals and alloys perfectly suited for demanding applications, including the recommended AlSi10Mg and IN625.
By leveraging these 적층 제조의 이점, designers can create thermal battery enclosures that are lighter, fit into more constrained spaces, potentially offer better thermal management, and are produced more efficiently, especially for complex geometries. It addresses inherent challenges in thermal battery packaging, pushing the boundaries of performance and integration.
Recommended Materials (AlSi10Mg & IN625) and Why They Matter
The choice of material is fundamental to the performance and reliability of a thermal battery enclosure. It must meet specific structural, thermal, and environmental requirements dictated by the application. Metal 3D printing offers excellent compatibility with advanced alloys suitable for these demanding roles. Two commonly recommended materials, AlSi10Mg and IN625, offer distinct advantages depending on the specific needs. Understanding their properties is key to effective thermal battery material selection.
1. AlSi10Mg (Aluminum Alloy)
AlSi10Mg is a widely used aluminum alloy in additive manufacturing, known for its excellent combination of properties that make it suitable for a variety of applications, including certain types of thermal battery enclosures.
- 속성:
- 가벼움: Aluminum alloys offer significant weight savings compared to steels or nickel-based superalloys, a critical factor in aerospace and portable applications. Density is approximately 2.67 g/cm³.
- 우수한 중량 대비 강도 비율: While not as strong as steel or Inconel, AlSi10Mg provides good mechanical strength relative to its low density, particularly after appropriate heat treatment.
- 뛰어난 열 전도성: Aluminum’s high thermal conductivity can be advantageous for dissipating heat away from sensitive areas or, conversely, ensuring rapid and uniform heat distribution if needed, although thermal management in thermal batteries is complex post-activation.
- 우수한 내식성: Exhibits good resistance to atmospheric corrosion.
- Weldability & Processability: It is generally readily processable using Laser Powder Bed Fusion (LPBF) systems.
- Suitability for Thermal Battery Enclosures: AlSi10Mg is often considered for enclosures where:
- Weight reduction is a primary driver.
- Operating temperatures and structural loads are moderate.
- Extreme corrosion resistance or very high-temperature strength is not the main requirement.
- Cost-effectiveness is a significant factor.
- Met3dp’s Offering: Leveraging advanced gas atomization techniques, Met3dp produces high-quality, spherical AlSi10Mg powder optimized for LPBF processes. This ensures good flowability, high packing density, and consistent melting behavior, leading to dense, reliable printed parts with predictable AlSi10Mg properties. Explore Met3dp’s advanced 금속 3D 프린팅 솔루션을 제공합니다.
Table: AlSi10Mg Key Properties (Typical Values for LPBF)
속성 | Typical Value (After Heat Treatment) | 단위 | Significance for Enclosures |
---|---|---|---|
밀도 | ~2.67 | g/cm³ | Lightweight design potential |
궁극의 인장 강도 | 330 – 430 | MPa | Structural integrity under moderate loads |
수율 강도 | 230 – 300 | MPa | Resistance to permanent deformation |
휴식 시 신장 | 6 – 10 | % | Ductility, resistance to fracture |
경도 | 100 – 120 | HV | Wear and scratch resistance |
열 전도성 | 120 – 140 | W/(m-K) | Heat dissipation capability |
최대 서비스 온도 | ~150 – 200 | °C | Suitable for moderate temperature environments pre-activation |
시트로 내보내기
2. IN625 (Inconel 625 – Nickel Superalloy)
Inconel 625 is a nickel-chromium superalloy renowned for its exceptional performance in harsh environments, making it a prime candidate for high-performance thermal battery enclosures.
- 속성:
- Excellent High-Temperature Strength: Maintains high strength and structural integrity at elevated temperatures, crucial for containing the heat generated during battery activation.
- 뛰어난 내식성: Highly resistant to a wide range of corrosive media, including acids, seawater, and oxidation at high temperatures. Essential for long-term storage and operation in harsh conditions (e.g., marine environments).
- High Toughness and Fatigue Strength: Resists cracking and failure under cyclic loading and mechanical stress.
- Good Weldability & Fabricability: Although requiring careful parameter control, IN625 is well-suited for processing via metal AM techniques like LPBF.
- Suitability for Thermal Battery Enclosures: IN625 is the preferred choice when:
- The enclosure must withstand very high temperatures post-activation (potentially > 500°C).
- Exceptional corrosion resistance is required due to the operating environment or internal chemistry.
- High structural loads or fatigue resistance are critical performance factors.
- Performance outweighs cost and weight considerations (IN625 is denser and more expensive than AlSi10Mg).
- Met3dp’s Offering: Met3dp provides premium IN625 powder, manufactured using advanced atomization processes to ensure the high sphericity and purity needed for demanding applications. This focus on powder quality translates directly to superior mechanical IN625 properties and reliability in 3D printed high-temperature alloy printing 컴포넌트입니다.
Table: IN625 Key Properties (Typical Values for LPBF)
속성 | Typical Value (After Stress Relief/Annealing) | 단위 | Significance for Enclosures |
---|---|---|---|
밀도 | ~8.44 | g/cm³ | Higher density than aluminum, factor in weight calculations |
궁극의 인장 강도 | 830 – 1000 | MPa | Excellent structural integrity, especially at high temperatures |
수율 강도 | 500 – 650 | MPa | High resistance to deformation under significant loads |
휴식 시 신장 | 30 – 50 | % | High ductility and toughness, resistant to brittle fracture |
경도 | ~220 – 280 | HV | 우수한 내마모성 |
열 전도성 | ~9.8 | W/(m-K) | Lower thermal conductivity (acts more as an insulator) |
최대 서비스 온도 | Up to ~650 – 800 (for strength) | °C | Suitable for high-temperature containment post-activation |
시트로 내보내기
Material Selection Criteria Summary:
- 온도: IN625 for high-temp containment; AlSi10Mg for moderate temps.
- 무게: AlSi10Mg offers significant advantages.
- 힘: IN625 provides superior strength, especially at high temperatures.
- 부식: IN625 offers superior resistance, particularly in aggressive environments.
- 비용: AlSi10Mg is generally more cost-effective.
Partnering with an experienced AM provider like Met3dp, who possesses deep knowledge of both material science and 금속 3D 프린팅 processes, is crucial for selecting the optimal material and achieving the desired enclosure performance. Their expertise in producing high-quality Met3dp metal powders ensures a reliable foundation for manufacturing mission-critical components like thermal battery enclosures.
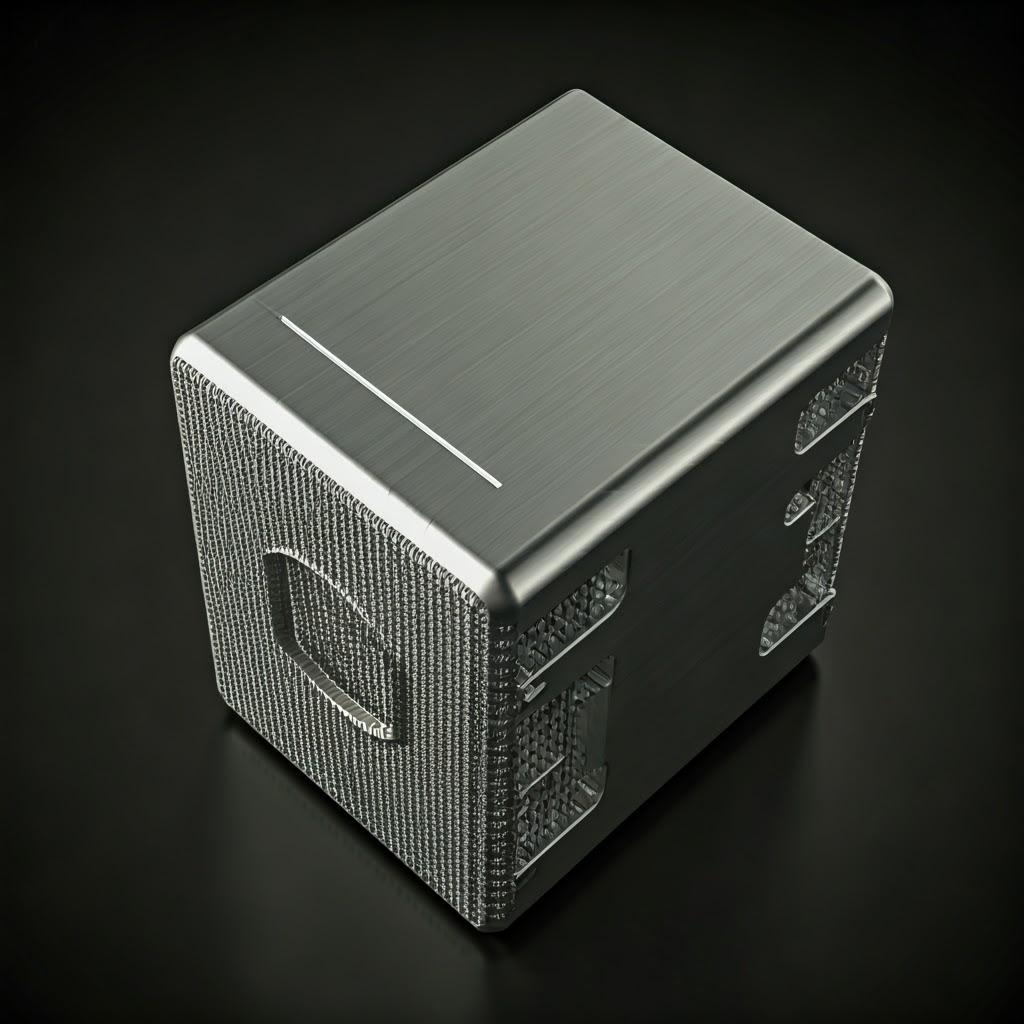
Design Considerations for Additive Manufacturing of Enclosures
Transitioning from traditional manufacturing methods to additive manufacturing (AM) for thermal battery enclosures isn’t just about changing the production technique; it requires a shift in design philosophy. Embracing 적층 제조를 위한 설계(DfAM) principles is crucial to fully leverage the benefits of metal 3D printing and create truly optimized components. Applying DfAM ensures manufacturability, enhances performance, reduces weight, and can minimize post-processing efforts. For engineers designing custom thermal battery enclosures, understanding these considerations is paramount.
Key DfAM Principles for Thermal Battery Enclosures:
- Embrace Geometric Complexity:
- Internal Channels & Cavities: AM excels at creating complex internal structures. Consider integrating conformal cooling channels for thermal management (if applicable pre-activation), internal baffles for structural support or electrolyte flow control, or complex pathways for activation mechanisms – features often impossible or extremely costly with subtractive methods.
- Organic Shapes & Conformal Design: Design the enclosure to fit precisely within available space constraints, maximizing volume utilization in tightly packed systems like missiles or satellites. Smooth, organic shapes can also improve stress distribution.
- Weight Reduction Strategies:
- 토폴로지 최적화: Utilize specialized software to analyze load paths and remove material from areas not critical to structural integrity. This data-driven approach generates highly efficient, often organic-looking structures that significantly reduce weight while meeting performance requirements. This is a cornerstone of lightweight enclosure design using AM.
- 격자 구조: Replace solid sections with internal lattice or gyroid structures. These mathematically generated structures offer excellent strength-to-weight ratios and can be tailored for specific stiffness, vibration damping, or even thermal properties. Selecting the right unit cell type and density is critical.
- 파트 통합:
- Integrated Features: Look for opportunities to combine multiple parts into a single printed component. Can mounting brackets, connector interfaces, or fastening points be directly integrated into the enclosure body? This reducing part count AM strategy simplifies assembly, reduces inventory, eliminates potential leak paths or failure points at joints, and lowers overall system complexity.
- Designing for Manufacturability (LPBF/EBM Specifics):
- Minimize Support Structures: Support structures are often necessary in Powder Bed Fusion (PBF) processes to anchor overhangs and dissipate heat. However, they consume extra material, add print time, and require removal in post-processing (which can be challenging for internal features). Design considerations include:
- 자립 각도: Orient features so that overhangs are typically below 45 degrees from the horizontal, minimizing the need for supports.
- 기능 오리엔테이션: Choose the build orientation strategically to reduce the volume of support needed, especially for critical surfaces or hard-to-reach internal areas.
- Accessible Supports: If supports are unavoidable, design them for easier access and removal without damaging the part surface.
- 벽 두께: Maintain appropriate minimum wall thicknesses suitable for the chosen material and process (often around 0.4-1.0 mm, but depends on specifics). Very thin walls can be difficult to print reliably or may warp. Conversely, overly thick sections can accumulate residual stress.
- Hole Orientation: Horizontal holes often print with better circularity than vertical ones due to the layer-wise process, although small vertical holes can sometimes be printed without support. Consider orientation based on tolerance requirements.
- Powder Removal: Ensure internal cavities or channels have escape holes designed in to allow for complete removal of unfused powder after printing. Trapped powder can add weight and potentially compromise performance or safety.
- Minimize Support Structures: Support structures are often necessary in Powder Bed Fusion (PBF) processes to anchor overhangs and dissipate heat. However, they consume extra material, add print time, and require removal in post-processing (which can be challenging for internal features). Design considerations include:
- Thermal Considerations:
- 열 발산: While IN625 has low thermal conductivity, the design can still influence heat management. Thin walls or integrated fins (if externally feasible) might be considered, though the primary containment function post-activation is key. For AlSi10Mg, the higher conductivity allows for more active thermal management design possibilities if needed.
- Residual Stress Management: Large, bulky designs or sharp transitions in thickness can increase residual stress build-up during printing. Smooth transitions and careful design can help mitigate this (discussed further under Challenges).
Software Tools for DfAM:
Advanced CAD and simulation software plays a vital role in DfAM. Tools like nTopology, Altair Inspire, Siemens NX, Dassault Systèmes CATIA, and specialized modules within standard CAD packages enable topology optimization, lattice generation, build simulation, and support structure design.
By thoughtfully applying these metal 3D printing design rules, engineers can move beyond simply replicating traditionally designed enclosures and instead create superior components optimized for additive manufacturing. Collaborating with an experienced AM service provider like Met3dp early in the design phase can provide invaluable insights into process-specific constraints and opportunities, ensuring the final design is both high-performing and manufacturable. Understanding the nuances of different 인쇄 방법 like LPBF or SEBM is crucial for effective DfAM.
Achievable Tolerance, Surface Finish, and Dimensional Accuracy
A common question from engineers and procurement managers evaluating metal AM pertains to the achievable precision: what level of dimensional accuracy additive manufacturing can deliver, what are the typical metal 3D printing tolerances, and what kind of surface finish metal AM parts possess? Understanding these aspects is crucial for managing expectations and determining the need for post-processing steps, especially for components like thermal battery enclosures where precise fits and sealing surfaces can be critical.
Factors Influencing Accuracy and Tolerances:
The final accuracy of a 3D printed metal part is influenced by a complex interplay of factors:
- AM System: The specific machine used, its calibration status, laser/electron beam spot size, and control systems significantly impact precision. High-end industrial systems, like those utilized by Met3dp, offer greater control and repeatability.
- 머티리얼 속성: Each metal powder behaves differently during melting and solidification (e.g., shrinkage rates, thermal conductivity), affecting final dimensions.
- Part Geometry & Size: Larger parts and complex geometries are more susceptible to thermal distortion and deviation. The location and orientation of features within the build chamber also play a role.
- Build Parameters: Layer thickness, laser/beam power, scan speed, and scan strategy are meticulously controlled but influence the melt pool dynamics and resulting part characteristics.
- 지원 구조: How the part is supported can affect stress build-up and potential distortion upon removal.
- 후처리: Stress relief heat treatments can cause minor dimensional changes. Machining is often used to achieve tighter tolerances on critical features.
Typical Tolerances:
While specific capabilities vary, general tolerance expectations for metal PBF processes (like LPBF) are often in the range of:
- General Tolerances: ±0.1 mm to ±0.2 mm for smaller dimensions (e.g., up to 25 mm).
- Larger Dimensions: ±0.1% to ±0.2% of the nominal dimension for larger features.
Important Considerations:
- Critical Dimensions: It’s essential to clearly identify critical dimensions and their required tolerances on engineering drawings. These features may require specific orientation strategies during the build or dedicated post-processing steps (like CNC machining).
- 업계 표준: Standards like ISO/ASTM 52902 provide frameworks for specifying tolerances for AM parts.
- Supplier Capability: Discuss tolerance capabilities directly with your AM service provider. Experienced providers like Met3dp can advise on achievable tolerances for specific geometries and materials based on their equipment and process controls.
표면 마감(거칠기):
The as-built surface finish of metal AM parts is inherently rougher than machined surfaces due to the layer-by-layer fusion of powder particles.
- Typical Ra Values: As-built surface roughness (Ra) often ranges from 6 µm to 20 µm (micrometers), depending on the material, parameters, and surface orientation (upward-facing, downward-facing, vertical walls). Downward-facing surfaces impacted by support structures tend to be rougher.
- 표면 마감 개선: Post-processing is essential for achieving smoother finishes. Common methods include:
- Bead Blasting/Sand Blasting: Creates a uniform matte finish, typically improving Ra slightly.
- 텀블링/진동 마감: Can smooth surfaces and break sharp edges, particularly effective for batches of smaller parts.
- 연마: Manual or automated polishing can achieve very smooth, mirror-like finishes (Ra < 1 µm) but is labor-intensive.
- 전기 연마: An electrochemical process that can smooth surfaces, especially effective on complex geometries.
- CNC 가공: Used on specific surfaces requiring high smoothness and tight tolerances (e.g., sealing faces, mating features).
Achieving Precision:
For thermal battery enclosures, achieving the required precision metal components specifications often involves a combination of careful DfAM, precise printing process control, and targeted post-processing. While AM might not match the sub-micron tolerances of high-precision machining across the entire part in its as-built state, it provides the complex geometry, and subsequent machining ensures critical features meet exact requirements. Defining the necessary Ra value 3D printing surfaces should meet, and specifying critical tolerances upfront, allows providers like Met3dp to plan the entire workflow, from printing to final finishing, ensuring the enclosure meets all functional requirements.
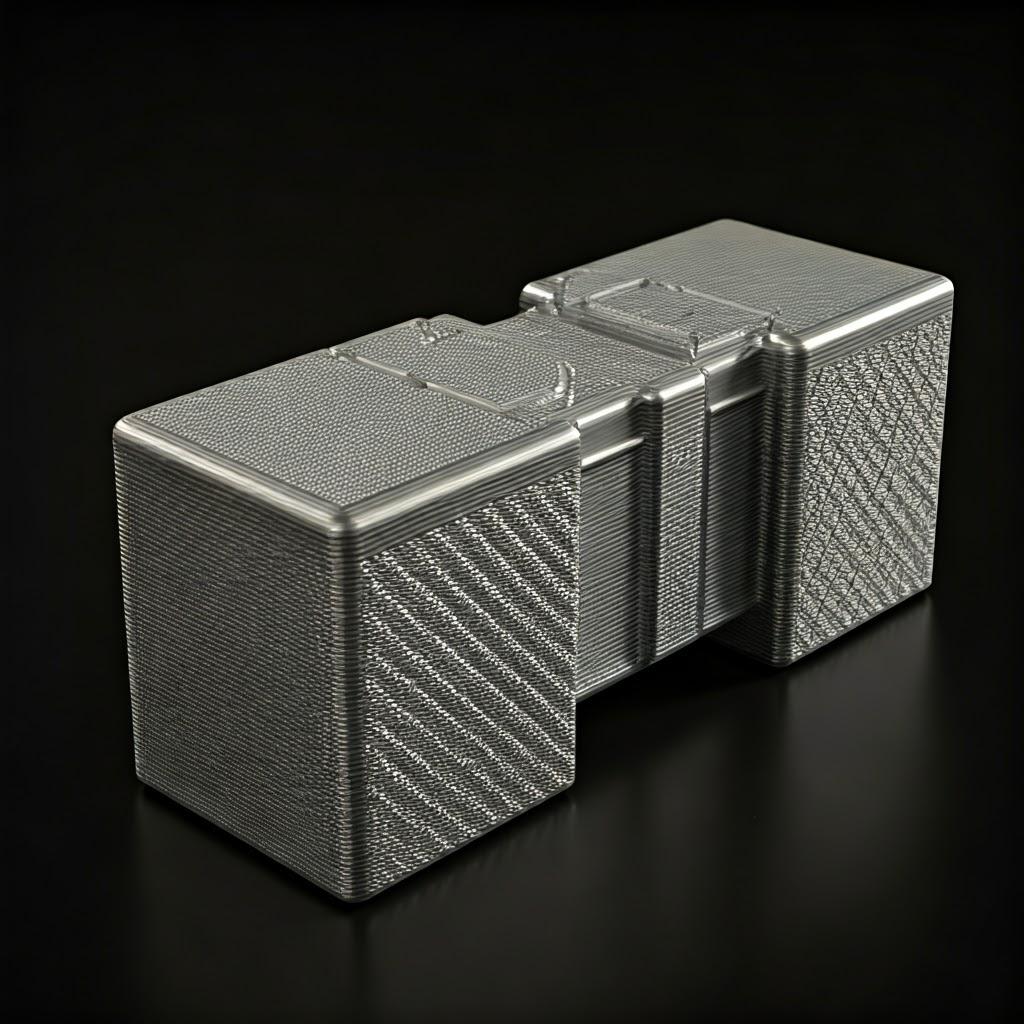
Post-Processing Requirements for Optimal Performance
Obtaining a finished, functional thermal battery enclosure rarely stops when the part comes out of the 3D printer. Metal 3D printing post-processing is a critical stage that transforms the as-built component into a final product meeting stringent performance, safety, and quality standards. These steps are essential for removing supports, relieving internal stresses, achieving required tolerances and surface finishes, and ensuring material properties meet specifications. Planning for post-processing should be integral to the overall manufacturing strategy.
Common Post-Processing Steps for 3D Printed Enclosures:
- Stress Relief / Heat Treatment:
- 목적: The rapid heating and cooling cycles inherent in metal PBF processes create internal stresses within the printed part. Heat treatment (stress relief, annealing, or solution treatment followed by aging, depending on the alloy and requirements) is crucial to relax these stresses, prevent distortion, improve dimensional stability, and optimize mechanical properties (e.g., ductility, strength).
- Material Specifics: This step is particularly critical for alloys like IN625, which often require specific heat treatment IN625 cycles (e.g., annealing) to achieve desired high-temperature strength and corrosion resistance. AlSi10Mg also typically undergoes heat treatment (e.g., T6) to enhance its strength.
- 프로세스: Parts are heated in a controlled atmosphere furnace following specific temperature profiles (heating rate, soak time, cooling rate).
- 빌드 플레이트에서 파트 제거:
- Parts are typically printed on a thick metal build plate. Removal usually involves wire EDM (Electrical Discharge Machining) or sawing to detach the component(s).
- 지원 구조 제거:
- 목적: Removing the temporary structures used to anchor the part during printing.
- 방법: This is often done manually using hand tools, pliers, or grinders. For complex internal supports, specialized tools or electrochemical methods might be necessary. Careful removal is needed to avoid damaging the part surface. Support removal metal AM difficulty is a key DfAM consideration.
- 가루 제거(파우더 제거):
- 목적: Ensuring all unfused metal powder is removed from the part, especially from internal channels, cavities, and complex lattice structures. Trapped powder can add unintended weight, become sintered during heat treatment, or pose a contamination risk.
- 방법: Compressed air blasting, vibration, ultrasonic cleaning, and manual brushing are used. Designing adequate escape holes is critical for effective depowdering.
- CNC 가공:
- 목적: To achieve tight tolerances on critical features, create specific mating surfaces, produce very smooth surface finishes (e.g., for sealing), or add features not easily formed during printing (e.g., threaded holes).
- 애플리케이션: CNC machining 3D printed parts is common for flatness requirements on sealing flanges, precise bore diameters for connectors, or critical interface dimensions.
- 표면 마감:
- 목적: To improve surface roughness, aesthetics, or prepare the surface for subsequent coatings.
- 방법: As discussed previously, techniques include bead blasting (common for a uniform matte finish), tumbling, polishing, electropolishing. The choice depends on the required surface finishing additive manufacturing level.
- Cleaning & Inspection:
- 목적: Final cleaning to remove any machining fluids, blasting media, or contaminants. Followed by rigorous quality inspection (dimensional checks, surface inspection, potentially NDT like CT scanning) to verify compliance with specifications.
Integration with Design:
The required post-processing steps significantly impact lead time and cost. Therefore, it’s crucial to consider these needs during the DfAM phase. For instance, designing for easier support removal or minimizing the number of surfaces requiring tight-tolerance machining can streamline the workflow. Partnering with a full-service provider like Met3dp, who offers integrated printing and post-processing capabilities, ensures a seamless transition from digital file to finished thermal enclosure finishing, guaranteeing quality and performance. Their experience across various 제품 demonstrates a comprehensive understanding of these critical finishing steps.
Common Challenges in 3D Printing Thermal Battery Enclosures and How to Mitigate Them
While metal 3D printing offers numerous advantages for producing thermal battery enclosures, like any advanced manufacturing process, it comes with potential challenges. Understanding these potential issues and implementing effective mitigation strategies is key to ensuring the production of high-quality, reliable components. Experienced AM providers employ rigorous process controls and quality checks to overcome these hurdles.
Potential Challenges & Mitigation Strategies:
- Warping and Residual Stress:
- 도전: The high thermal gradients during printing can cause internal stresses to build up. If not managed, these stresses can lead to warping (distortion) of the part during or after the build, or even cracking. Residual stress additive manufacturing is a primary concern, especially in larger parts or complex geometries.
- Mitigation:
- Build Simulation: Software simulation can predict stress accumulation and potential distortion, allowing for adjustments to orientation or support strategy before printing.
- Optimized Build Parameters: Careful control of laser power, scan speed, and layer thickness helps manage thermal input.
- Appropriate Support Strategy: Well-designed supports anchor the part and help dissipate heat, reducing stress.
- Platform Heating: Maintaining an elevated temperature in the build chamber (common in EBM, sometimes used in LPBF) reduces thermal gradients.
- Post-Build Stress Relief: A critical heat treatment step performed before removing the part from the build plate significantly reduces internal stress.
- 다공성:
- 도전: Small voids or pores can form within the printed material due to trapped gas, incomplete fusion between layers, or powder inconsistencies. Excessive porosity control metal AM is critical as pores can act as stress concentrators, reducing fatigue life and potentially compromising hermeticity.
- Mitigation:
- High-Quality Powder: Using powder with controlled particle size distribution, high sphericity, and low internal porosity (like those produced by Met3dp using advanced atomization).
- Optimized Print Parameters: Fine-tuning parameters (power, speed, hatch spacing) to ensure complete melting and fusion.
- Controlled Atmosphere: Maintaining a high-purity inert gas atmosphere (Argon or Nitrogen) in the build chamber minimizes oxidation and gas entrapment.
- 열간 등방성 프레싱(HIP): A post-processing step involving high temperature and high pressure. HIP processing metal AM effectively closes internal pores, achieving near-full theoretical density and significantly improving mechanical properties. This is often specified for critical aerospace and defense components.
- Cracking:
- 도전: Certain alloys, particularly those susceptible to solidification cracking or strain-age cracking (some nickel superalloys or specialized aluminum alloys if not processed correctly), can develop cracks during printing or post-processing.
- Mitigation:
- Material-Specific Parameters: Developing and using validated build parameters specific to the alloy being printed.
- 열 관리: Controlling heating and cooling rates via build parameters and platform heating.
- Appropriate Heat Treatment: Carefully designed stress relief and annealing cycles.
- Alloy Selection: Choosing alloys known for good processability via AM where possible.
- Support Removal Difficulties:
- 도전: Supports in hard-to-reach internal areas or complex geometries can be difficult or impossible to remove completely without damaging the part. Support structure challenges 가 일반적입니다.
- Mitigation:
- DfAM: Designing parts to minimize the need for internal supports (self-supporting angles, optimized orientation).
- Optimized Support Design: Using support types (e.g., tree supports, block supports with specific patterns) designed for easier detachment.
- Accessibility Planning: Ensuring tools or processes can reach support structures.
- Powder Removal from Internal Cavities:
- 도전: Ensuring all unfused powder is removed from intricate internal channels or lattice structures, which is crucial for weight, safety, and performance.
- Mitigation:
- DfAM: Designing adequate powder escape holes (size and location).
- Thorough Cleaning Procedures: Utilizing optimized combinations of compressed air, vibration, and potentially ultrasonic cleaning.
- Inspection: Using methods like borescopes or CT scanning to verify complete powder removal in critical applications.
- Quality Control and Consistency:
- 도전: Ensuring consistent part quality (dimensional accuracy, material properties, defect levels) across different builds and machines requires robust process control.
- Mitigation:
- Rigorous QMS: Implementing a strong Quality Management System (e.g., ISO 9001, AS9100).
- 프로세스 모니터링: In-situ monitoring of the melt pool and build process where available.
- Powder Management: Strict control over powder sourcing, handling, storage, and recycling to maintain quality.
- Regular Calibration & Maintenance: Ensuring AM equipment is performing optimally.
- Comprehensive Testing: Performing necessary mechanical testing, NDT (Non-Destructive Testing), and dimensional analysis as required by specifications. Quality control 3D printing is non-negotiable for critical parts.
By proactively addressing these common metal 3D printing defects and challenges through careful design, meticulous process control, appropriate post-processing, and rigorous quality assurance, manufacturers can confidently produce high-integrity thermal battery enclosures that meet the demanding requirements of aerospace, defense, and specialized industrial applications.
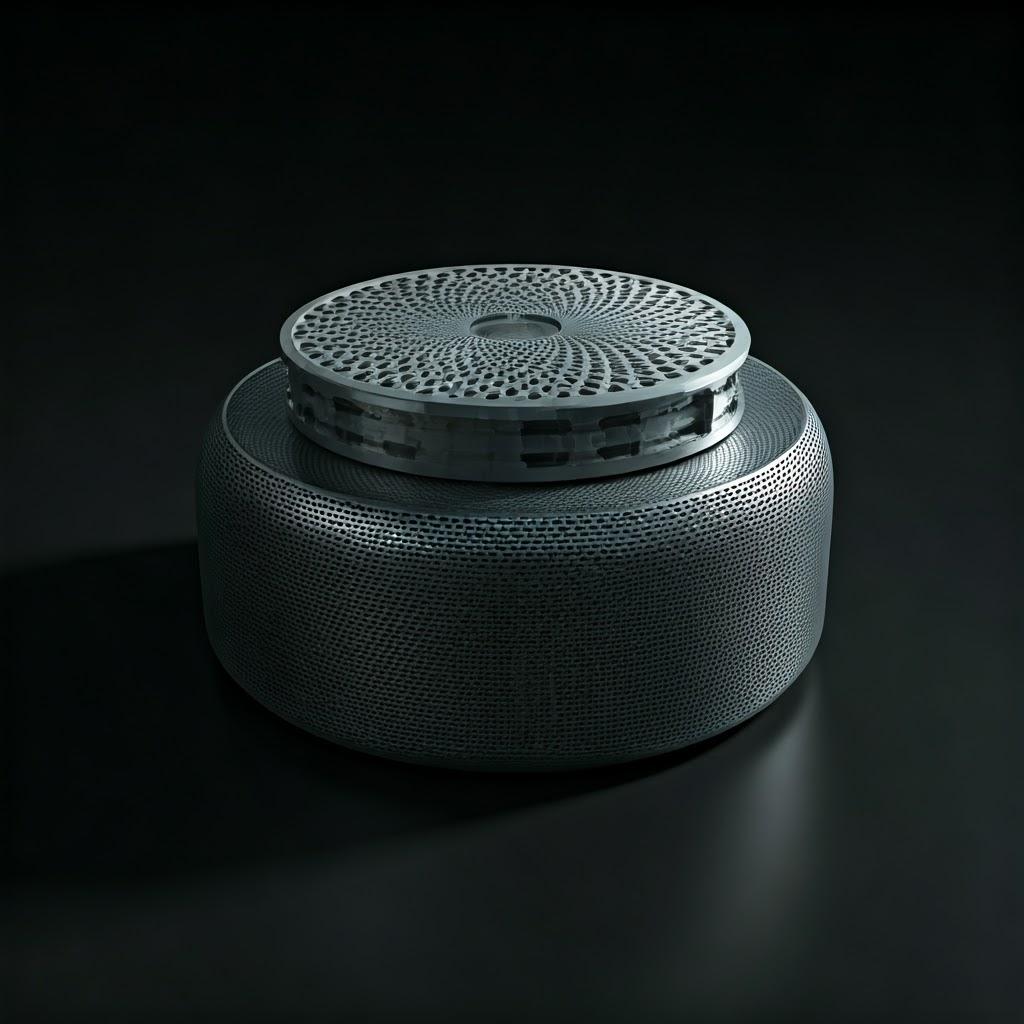
How to Choose the Right Metal 3D Printing Service Provider
Selecting the right manufacturing partner is as critical as the design and material choices when producing high-stakes components like thermal battery enclosures via metal additive manufacturing. The quality, reliability, and performance of the final part heavily depend on the capabilities, expertise, and process controls of your chosen metal 3D printing service provider. For procurement managers and engineers sourcing these components, evaluating additive manufacturing companies requires careful consideration of several key factors.
Key Criteria for Evaluating AM Suppliers:
- Materials Expertise & Availability:
- Relevant Materials: Does the provider have proven experience printing the specific alloys required (e.g., AlSi10Mg, IN625)? Ask for case studies or data on parts printed with these materials.
- Powder Quality Control: Inquire about their powder sourcing, testing, handling, and traceability procedures. Consistent, high-quality powder is fundamental to part quality. Companies like Met3dp, which manufacture their own high-performance powders using advanced methods like gas atomization and PREP, often have superior control over this crucial input.
- Industry Experience & Certifications:
- Application Knowledge: Do they understand the specific requirements and challenges of your industry (e.g., aerospace, defense)? Experience with similar components (e.g., demanding enclosures, high-temperature parts) is invaluable.
- 인증: For aerospace and defense applications, certifications like AS9100 are often mandatory. ISO 9001 certification demonstrates a commitment to a robust Quality Management System (QMS). Verify the provider holds relevant and current certifications.
- Equipment Capabilities & Technology:
- Machine Park: What types of metal AM systems do they operate (e.g., LPBF, EBM)? Do they have machines suitable for the required materials and part size?
- 볼륨을 구축합니다: Ensure their printers can accommodate the dimensions of your enclosure design. Met3dp prides itself on printers delivering industry-leading print volume, accuracy, and reliability.
- Process Control & Monitoring: Do they employ advanced process monitoring or control systems to ensure build consistency and detect potential issues in real-time?
- Post-Processing Capabilities:
- Integrated Services: Can the provider handle all necessary post-processing steps in-house (heat treatment, support removal, machining, finishing, inspection)? A single-source provider simplifies logistics and ensures accountability throughout the entire workflow.
- Specialized Equipment: Do they have the necessary furnaces for specific heat treatment cycles (e.g., vacuum furnaces for reactive materials or high-temp alloys), CNC machines for precision finishing, and NDT equipment (e.g., CT scanners)?
- Engineering & DfAM Support:
- 전문성: Does the provider offer Design for Additive Manufacturing (DfAM) support? Can their engineers collaborate with your team to optimize the enclosure design for printability, performance, and cost-effectiveness? Early collaboration with an experienced certified metal AM partner can prevent costly redesigns later.
- Quality Management System (QMS):
- Documentation & Traceability: A strong QMS ensures documented procedures, process control, material traceability, and thorough inspection protocols. Request information about their quality control processes and inspection capabilities.
- Track Record: Look for evidence of consistent quality and reliability through customer testimonials, case studies, or performance data.
- Lead Time & Capacity:
- Realistic Timelines: Can the provider offer realistic lead times that meet your project schedule? Understand their current capacity and typical turnaround times for similar projects.
- Communication: Clear and proactive communication regarding project status is essential.
Choosing a partner like Met3dp provides access to decades of collective expertise in metal AM. As a company specializing in both advanced SEBM printers and high-quality metal powders, Met3dp offers comprehensive solutions spanning the entire additive manufacturing value chain. Their focus on industry-leading accuracy and reliability makes them a strong candidate for mission-critical components like thermal battery enclosures. To learn more about their background and commitment to quality, visit the 회사 소개 section of their website. Partnering with a knowledgeable and capable AM supplier is fundamental to successfully implementing additive manufacturing for demanding applications.
Cost Factors and Lead Time for 3D Printed Enclosures
Understanding the financial and time investments required for producing custom thermal battery enclosures via metal AM is crucial for project planning and budgeting. Both metal 3D printing cost and lead time are influenced by a multitude of factors, and obtaining an accurate B2B additive manufacturing quote requires providing detailed information to the service provider.
Key Cost Drivers:
- Material Type & Consumption:
- 재료비: High-performance alloys like IN625 are significantly more expensive per kilogram than AlSi10Mg or stainless steels.
- Part Volume: The sheer amount of material required directly impacts cost. This includes the part itself and any necessary support structures. DfAM techniques like topology optimization can reduce material usage and cost.
- Powder Reuse/Recycling: The provider’s ability to safely recycle unfused powder can influence overall material costs, though strict quality control is essential.
- 머신 시간(빌드 시간):
- Part Complexity & Size: Larger and more complex parts require longer print times, occupying expensive AM machinery.
- 레이어 두께 및 매개변수: Finer layer thicknesses improve resolution but increase build time. Optimized build parameters balance speed and quality.
- 중첩 및 빌드 밀도: Printing multiple parts simultaneously in a single build (nesting) can improve machine utilization and reduce per-part cost, but depends on part geometry and orientation requirements.
- Labor & Setup:
- File Preparation: Preparing the build file, designing support structures, and setting up the print job requires skilled labor.
- Machine Operation: Monitoring the build process.
- 후처리: This can be a significant labor component, including support removal, machining, finishing, and inspection. Complex finishing requirements add considerably to the cost.
- 사후 처리 요구 사항:
- 열처리: Furnace time and energy consumption.
- 가공: CNC machining time, tooling, and programming add costs, especially for tight tolerances or complex features.
- 표면 마감: Polishing, blasting, or coating steps add material and labor costs.
- Inspection: The level of required inspection (visual, dimensional, NDT like CT scanning) impacts cost.
- 주문 수량:
- 규모의 경제: While AM is suitable for low volumes, setup costs are amortized over larger quantities. Per-part costs generally decrease with increasing batch sizes, although the effect might be less pronounced than in traditional mass production methods.
Optimizing AM Cost:
- Apply DfAM principles to reduce material usage and minimize complex post-processing.
- Consolidate parts where feasible.
- Clearly define only necessary critical tolerances and surface finishes.
- Discuss material choices and potential alternatives with the supplier.
리드 타임에 영향을 미치는 요인:
- Print Time: Directly related to part size, complexity, and build parameters (can range from hours to many days).
- Machine Availability: Queue times for available printers at the service provider.
- Post-Processing Complexity: Each step (heat treatment, machining, finishing, inspection) adds time to the overall workflow. Heat treatment cycles alone can take hours or days. Machining setups and operations can also be time-consuming.
- Engineering & File Prep: Initial design review, DfAM adjustments, and build preparation time.
- 해운: Logistics time for delivery.
Typical Lead Time Ranges:
Lead time metal 3D printing can vary significantly, but typical ranges for complex components like thermal battery enclosures might be:
- 프로토타입: 1-3주
- Low Volume Production: 3-8 weeks (highly dependent on complexity, post-processing, and quantity)
It is essential to discuss specific project requirements with the service provider to get accurate cost estimates and realistic lead time projections. Transparent communication and detailed specifications are key to managing expectations for both additive manufacturing pricing and delivery schedules.
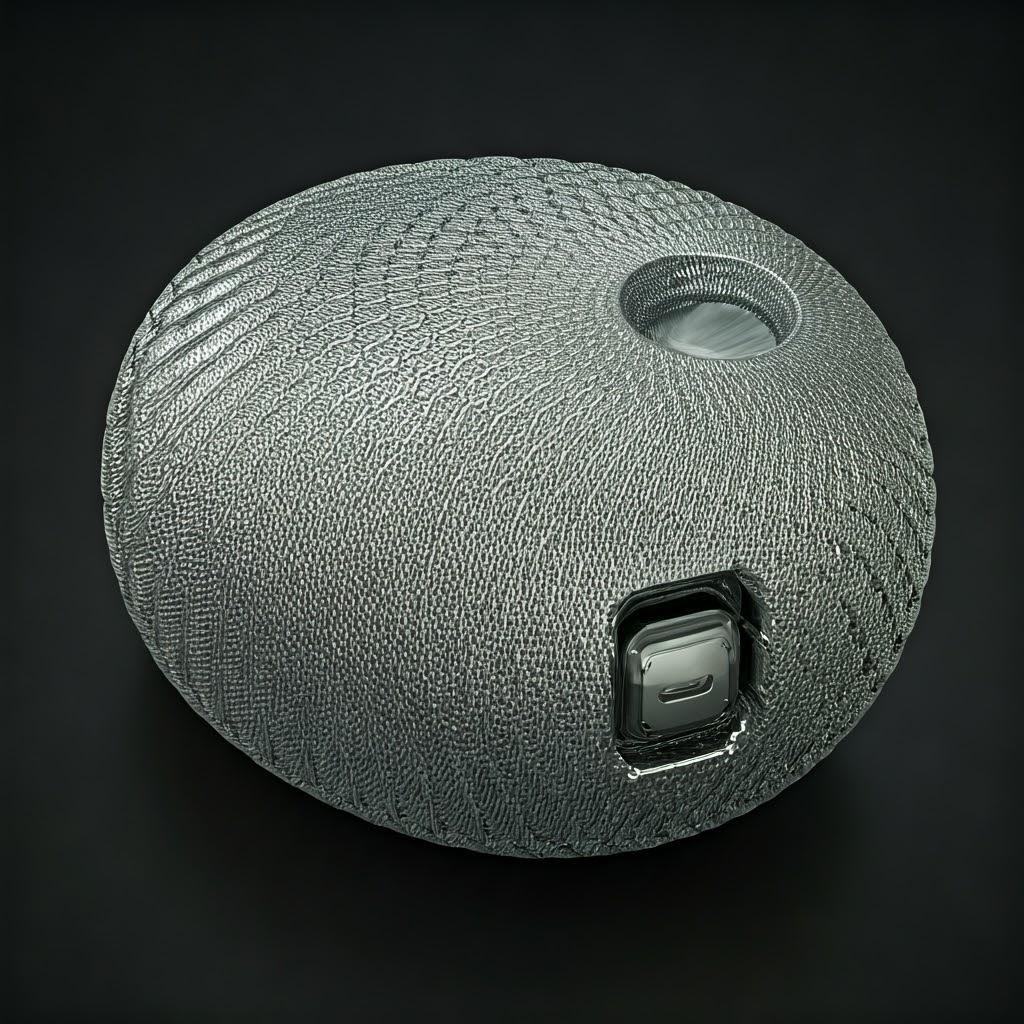
자주 묻는 질문(FAQ)
Here are answers to some common questions regarding the use of metal 3D printing for thermal battery enclosures:
- Q1: What is the typical minimum wall thickness achievable for 3D printed thermal battery enclosures?
- A: While process and material dependent, minimum achievable wall thicknesses in metal AM (specifically LPBF) are typically around 0.4 mm to 1.0 mm. However, for structural integrity, thermal considerations, and ease of handling/post-processing, designers often specify wall thicknesses greater than this minimum, commonly 1.0 mm or more, unless significant weight optimization justifies thinner sections validated by simulation. It’s best to consult with the AM provider regarding specific capabilities for the chosen material and geometry.
- Q2: Can metal 3D printing produce hermetically sealed enclosures?
- A: Yes, metal AM processes like LPBF, when properly controlled and often combined with post-processing like HIP, can produce fully dense parts (typically >99.5% density) capable of achieving hermetic seals. Achieving hermeticity requires careful design (e.g., appropriate sealing surfaces), high-quality printing to avoid porosity or defects, and often specific post-processing like precision machining of sealing faces and rigorous leak testing (e.g., helium leak testing) for verification. Partnering with a provider experienced in producing pressure vessels or sealed components is recommended.
- Q3: How does the strength of a 3D printed enclosure compare to a machined one?
- A: The mechanical properties (yield strength, ultimate tensile strength, elongation) of parts produced by metal AM can be comparable to, and sometimes even exceed, those of wrought or cast materials, especially after appropriate heat treatment and potentially HIP processing. For alloys like AlSi10Mg and IN625, well-controlled AM processes can achieve properties meeting or exceeding typical specifications for machined counterparts made from billet of a similar alloy composition. However, properties can be anisotropic (directionally dependent) in AM parts, which needs consideration during design and validation testing.
- Q4: What quality certifications are important when sourcing 3D printed enclosures for aerospace/defense?
- A: For critical aerospace and defense applications, AS9100 certification is paramount. This standard incorporates ISO 9001 requirements but adds specific quality and safety criteria for the Aviation, Space, and Defense (ASD) industry. Other relevant aspects might include Nadcap accreditation for specific processes (like heat treatment or NDT), ITAR compliance (for defense projects in the US), and robust material traceability documentation (e.g., conforming to AMS specifications for powders). Verifying a supplier’s adherence to these standards ensures rigorous quality control throughout the manufacturing process.
Conclusion: The Future of Thermal Battery Enclosures is Additive
The demanding requirements of thermal batteries—reliability under extreme conditions, high power density, and often stringent space and weight constraints—necessitate advanced solutions for their enclosures. Metal additive manufacturing has emerged as a transformative technology, offering unparalleled advantages over traditional methods for creating these critical components.
By leveraging the 디자인의 자유 of AM, engineers can craft custom thermal battery enclosures with complex internal features, optimized topologies, and integrated functionalities, leading to significant 체중 감소 and enhanced performance. The ability to use high-performance materials like lightweight AlSi10Mg for moderate conditions or robust, high-temperature resistant IN625 for extreme environments allows for tailored material selection based on specific application needs. Furthermore, AM facilitates 신속한 프로토타이핑 and is economically viable for the low-to-mid volume production runs often associated with specialized defense and aerospace systems.
While challenges like managing residual stress, ensuring powder removal, and meeting tight tolerances exist, they are effectively addressed through careful DfAM, meticulous process control, appropriate post-processing techniques like heat treatment and HIP, and rigorous quality assurance protocols.
Choosing the right manufacturing partner is crucial to realizing the full potential of this technology. An experienced provider like Met3dp, with deep expertise in metal powders, advanced AM systems (including SEBM), comprehensive post-processing capabilities, and a commitment to quality demonstrated through industry knowledge and robust processes, can be instrumental in successfully developing and producing next-generation thermal battery enclosures.
The future of high-performance thermal battery systems is intrinsically linked to advancements in manufacturing. Metal AM provides the tools to build lighter, more complex, and better-performing enclosures, paving the way for innovation in critical power sources across demanding industries.
Ready to explore how metal 3D printing can revolutionize your thermal battery enclosure design? Contact the experts at Met3dp today to discuss your specific requirements and discover how our cutting-edge additive manufacturing solutions can power your next project.
공유
중국 칭다오에 본사를 둔 선도적인 적층 제조 솔루션 제공업체인 MET3DP Technology Co. 당사는 산업용 3D 프린팅 장비와 고성능 금속 분말을 전문으로 합니다.
관련 기사
Met3DP 소개
최근 업데이트
제품
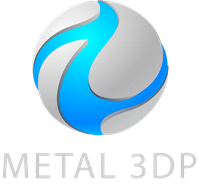
3D 프린팅 및 적층 제조용 금속 분말