3D Printed Gimbal Frames for Aerospace Optical Systems
목차
Introduction: Revolutionizing Aerospace Optics with 3D Printed Gimbal Frames
The aerospace industry operates at the pinnacle of engineering, demanding components that meet stringent requirements for performance, reliability, and weight. Within this demanding sector, optical systems used for imaging, targeting, communication, and surveillance rely heavily on the stability and precision provided by gimbal frames. Traditionally, manufacturing these intricate structures involved complex machining processes, often leading to long lead times, material waste, and limitations in design complexity. However, the advent of 금속 적층 제조(AM)또는 3D 프린팅, is fundamentally changing how aerospace gimbal frames are designed and produced.
Metal 3D printing offers unprecedented design freedom, enabling the creation of highly optimized, lightweight structures that were previously impossible to manufacture. This technology allows engineers to consolidate multiple parts into a single, complex component, reducing assembly time, potential points of failure, and overall system weight – a critical factor in aerospace applications where every gram counts. For procurement managers and engineers focused on 정밀 엔지니어링 and enhancing optical system stability, additive manufacturing presents a compelling value proposition. It accelerates development cycles through rapid prototyping and facilitates the production of highly customized or low-volume components without the prohibitive costs associated with traditional tooling.
Companies like Met3dp are at the forefront of this revolution, providing advanced 금속 3D 프린팅 solutions tailored for demanding industries like aerospace. By leveraging cutting-edge powder bed fusion technologies, including Selective Electron Beam Melting (SEBM), and high-performance metal powders, Met3dp empowers aerospace manufacturers to push the boundaries of gimbal frame design, achieving superior performance and reliability for mission-critical optical systems. This shift towards additive manufacturing aerospace components signifies a move towards more agile, efficient, and innovative production paradigms. The ability to produce intricate internal channels for cooling, integrate mounting features directly into the frame, and utilize topology optimization for maximum stiffness-to-weight ratios are just a few examples of how AM is transforming gimbal frame manufacturing, ultimately leading to more capable and efficient aerospace platforms.
What Are Aerospace Gimbal Frames Used For? Applications and Industries
Aerospace gimbal frames are sophisticated mechanical structures designed to support and stabilize sensitive payloads, primarily optical or sensor systems, allowing them to be accurately pointed regardless of the motion or vibrations of the host platform (aircraft, spacecraft, satellite, or UAV). The core gimbal function is to provide rotational freedom along multiple axes (typically two or three – pitch, roll, yaw) using a system of nested rings and precision bearings. This ensures the payload, such as a camera, telescope, antenna, or laser designator, remains fixed on a target or oriented in a specific direction, compensating for the platform’s movements.
The applications for aerospace gimbal frames are diverse and critical across several sectors:
- Satellite Imaging and Earth Observation: High-resolution cameras and sensors mounted on satellites require exceptionally stable gimbal systems to capture clear imagery and data from orbit. These gimbals must operate reliably in the harsh environment of space, enduring extreme temperatures and radiation while maintaining pointing accuracy over long operational lifetimes. Aerospace procurement for satellite components often prioritizes suppliers with proven space heritage and stringent quality control.
- 무인 항공기(UAV): Drones used for surveillance, reconnaissance, mapping, and inspection rely heavily on gimbaled UAV payloads, typically cameras (EO/IR – Electro-Optical/Infra-Red). The gimbal isolates the camera from the drone’s vibrations and maneuvers, providing smooth, stable footage crucial for mission success. Lightweighting is paramount for maximizing UAV flight endurance and payload capacity.
- Manned Aircraft: Military aircraft use gimbal systems for targeting pods, reconnaissance sensors, and communication antennas. Commercial aircraft might use smaller gimbals for weather radar or external cameras. These systems must withstand high G-forces, aerodynamic loads, and significant vibration.
- 우주 탐험: Telescopes (like Hubble or James Webb), interplanetary probes, and landers utilize complex gimbal mechanisms for precise instrument pointing, antenna orientation for communication with Earth, and maneuvering solar arrays.
- 국방 및 보안: EO/IR systems on gimbal frames are standard for airborne, ground-based, and naval surveillance and targeting applications. They provide critical situational awareness and targeting capabilities in all weather conditions, day or night. B2B suppliers in this sector must often meet stringent military specifications (MIL-STD).
Key Industries Relying on High-Performance Gimbals:
산업 | Primary Application Areas | Key Requirements | Procurement Focus |
---|---|---|---|
항공우주 | Satellites, Aircraft (Manned & Unmanned), Space Probes | Lightweight, High Stiffness, Thermal Stability, Reliability, Vibration Damping | AS9100 Certification, Proven Heritage |
방어 | Surveillance, Targeting Pods, Reconnaissance, Missile Seekers | Ruggedness, Precision, Environmental Sealing, MIL-STD Compliance, ITAR Control | Secure Supply Chain, Long-Term Contracts |
Remote Sensing | Aerial Mapping, Environmental Monitoring, Lidar Systems | Accuracy, Stability, Integration with GPS/INS | System Integrators, Specialized Suppliers |
Communications | Satellite Communication Antennas, Tracking Systems | Pointing Accuracy, Reliability, Environmental Resistance | High-Volume Manufacturers, Telecom Sector |
시트로 내보내기
The complexity, precision, and environmental demands placed on aerospace gimbal frames make them ideal candidates for the advanced manufacturing capabilities offered by metal 3D printing, enabling designs optimized for specific mission requirements.
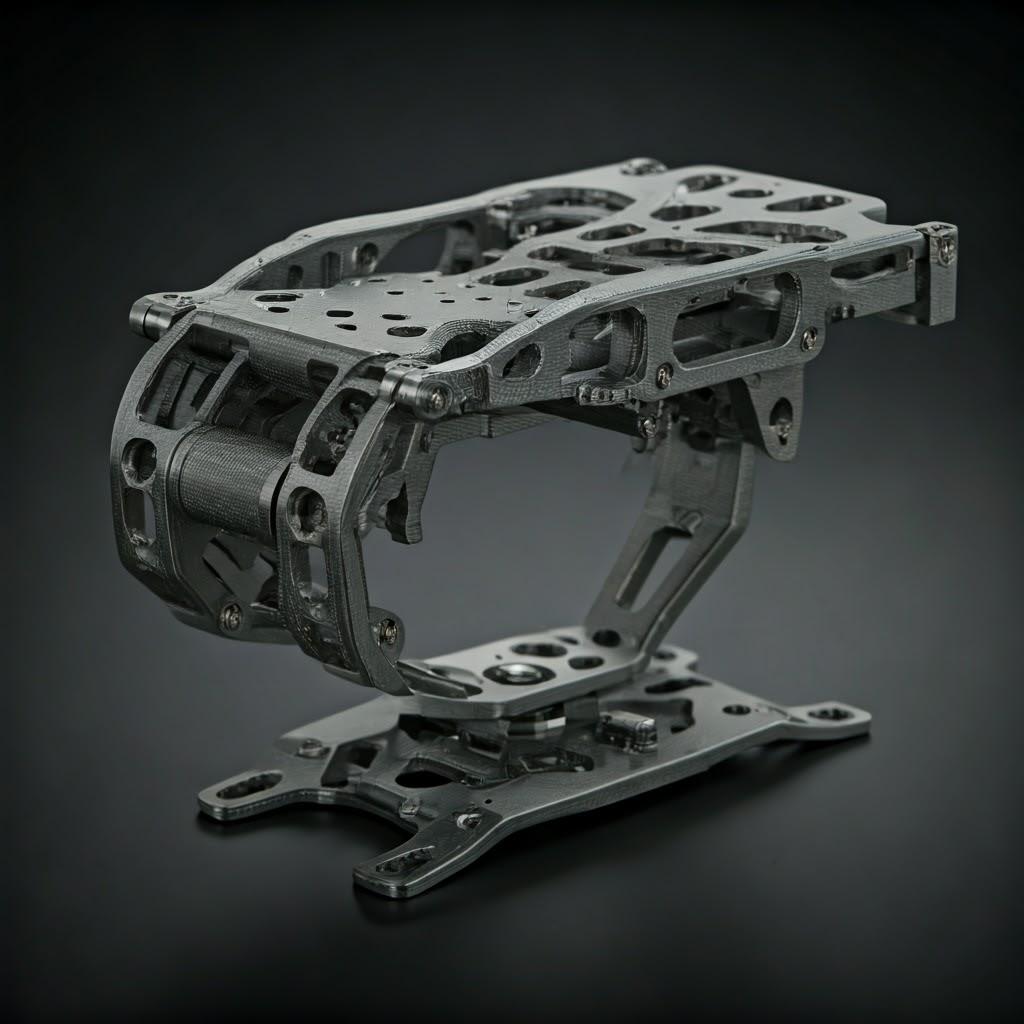
Why Use Metal 3D Printing for Aerospace Gimbal Frames? Key Advantages
While traditional manufacturing methods like CNC machining have long been used to produce gimbal frames, metal additive manufacturing (AM) offers distinct advantages that are particularly beneficial for aerospace applications. These advantages address key industry drivers such as weight reduction, performance enhancement, and accelerated development cycles. Comparing Metal AM vs CNC machining reveals why AM is increasingly becoming the preferred method for complex aerospace components like gimbals.
Key Advantages of Metal AM for Gimbal Frames:
- 대폭적인 경량화:
- 토폴로지 최적화: AM allows engineers to use sophisticated software tools to optimize the gimbal’s structure, placing material only where it’s structurally necessary. This results in organic-looking, highly efficient designs that minimize mass while maintaining or even increasing stiffness compared to traditionally manufactured parts. Lightweighting aerospace components directly translates to fuel savings, increased payload capacity, or extended mission duration.
- 격자 구조: Internal lattice or honeycomb structures can be easily integrated into the design using AM. These structures provide excellent stiffness-to-weight ratios and can also aid in vibration damping – a critical factor for optical system stability.
- 재료 효율성: AM typically uses only the material needed for the part and its supports, reducing the significant material waste often associated with subtractive machining, especially when starting with large billets of expensive aerospace alloys like Titanium.
- Unprecedented Design Freedom & Complexity:
- 복잡한 지오메트리: AM removes many of the constraints imposed by traditional manufacturing. Engineers can design highly intricate shapes, internal channels (e.g., for thermal management or wiring), and conformal features that would be difficult or impossible to machine. This enables 복잡한 형상 제조 tailored for optimal performance.
- 파트 통합: Multiple components that would traditionally be manufactured separately and then assembled (using fasteners or bonding) can often be consolidated into a single, monolithic part using AM. This reduces part count, eliminates potential failure points at joints, simplifies assembly, shortens the supply chain, and often improves overall structural integrity. Exploring part consolidation benefits is a key driver for AM adoption in aerospace procurement.
- Accelerated Development and Production:
- 신속한 프로토타이핑: Producing functional metal prototypes of gimbal designs is significantly faster with AM than waiting for tooling or complex machining setups. This allows for quicker design iteration, testing, and validation, shortening the overall development timeline. Rapid prototyping aerospace components enables faster innovation cycles.
- Tooling Elimination: AM does not require expensive molds, dies, or fixtures associated with casting or forging. This drastically reduces upfront costs and lead times, particularly for low-to-medium volume production runs or highly customized designs.
- 온디맨드 제조: Digital AM files allow for parts to be produced closer to the point of need, potentially enabling distributed manufacturing networks and reducing reliance on long, complex global supply chains.
- 소재의 다양성:
- AM processes can work with a wide range of high-performance aerospace alloys, including Titanium alloys (like Ti-6Al-4V), Nickel superalloys, Aluminum alloys, and specialty materials like Invar, known for its low coefficient of thermal expansion (CTE). Companies like Met3dp specialize in producing and qualifying these advanced powders for AM.
Comparison Table: Metal AM vs. Traditional Machining for Gimbals
기능 | 금속 적층 제조(AM) | 전통적인 CNC 가공 | Key Benefit for Gimbals via AM |
---|---|---|---|
자유로운 디자인 | High (Complex geometries, internal features) | Moderate (Limited by tool access & process) | Optimized structures, integrated features |
경량화 | Excellent (Topology optimization, lattices) | Limited (Primarily through pocketing) | Reduced mass, improved stiffness-to-weight ratio |
부품 통합 | High potential | Low potential | Fewer parts, reduced assembly, higher reliability |
재료 낭비 | Low (Additive process) | High (Subtractive process, especially complex parts) | Cost savings, sustainability |
Prototyping Speed | 빠른 | Slower (Requires setup, potentially tooling) | Faster design iteration & validation |
툴링 비용 | 없음 | High (for complex or high-volume parts) | Lower cost for custom/low-volume production |
Lead Time (New Design) | 짧은 | Long (Programming, setup, potential tooling) | Faster time-to-market / mission deployment |
Surface Finish (as built) | Generally Rougher | Generally Smoother | Requires post-processing for critical surfaces |
치수 정확도 | Good, continually improving | 매우 높음 | Often requires post-machining for tight tolerances |
시트로 내보내기
By leveraging these advantages, metal 3D printing empowers engineers and manufacturers to create next-generation aerospace gimbal frames that offer superior performance, reduced weight, and faster development timelines compared to traditional methods. Partnering with an experienced 금속 AM 서비스 제공업체 like Met3dp ensures access to the necessary expertise and technology to realize these benefits fully.
Recommended Materials: Ti-6Al-4V and Invar for Optimal Performance
Selecting the right material is paramount for designing aerospace gimbal frames that meet demanding performance criteria, including low weight, high stiffness, and thermal stability, especially for optical systems where minute expansions or contractions can affect pointing accuracy. Metal additive manufacturing processes, particularly Powder Bed Fusion (PBF) techniques like Selective Laser Melting (SLM) and Selective Electron Beam Melting (SEBM), can process a variety of aerospace-grade alloys. For gimbal applications, two materials stand out due to their exceptional properties: Titanium alloy Ti-6Al-4V and Iron-Nickel alloy Invar (FeNi36).
1. Titanium Alloy Ti-6Al-4V (Grade 5): The Aerospace Workhorse
Ti-6Al-4V is arguably the most widely used titanium alloy in aerospace due to its excellent combination of properties, which are retained well in parts produced via AM.
- 주요 속성:
- 높은 중량 대비 강도 비율: This is the primary reason for its prevalence in aerospace. It allows for strong, stiff structures that are significantly lighter than steel counterparts.
- 뛰어난 내식성: Titanium naturally forms a stable, protective oxide layer, making it highly resistant to corrosion in various environments, including oxidizing acids and chloride solutions.
- 피로 강도가 좋습니다: Crucial for components subjected to cyclic loading and vibrations, common in aircraft and launch vehicles.
- 생체 적합성: While less relevant for gimbals, its biocompatibility makes it suitable for medical implants as well.
- Good Performance at Moderate Temperatures: Maintains good strength up to around 300-400°C (570-750°F).
- Why Use Ti-6Al-4V for Gimbals?
- 경량화: Enables significant mass reduction compared to steel or even some aluminum alloys, critical for satellite and UAV applications.
- 강성: Provides the necessary rigidity to maintain pointing accuracy under load.
- Manufacturability via AM: Ti-6Al-4V is well-characterized and widely available for various metal AM processes, including SLM and SEBM. Companies like Met3dp offer high-quality, gas atomized Titanium powder specifically optimized for AM, ensuring good flowability and high packing density, leading to superior part quality.
- 고려 사항:
- Moderate CTE: While better than aluminum, its Coefficient of Thermal Expansion (CTE) might still be too high for ultra-precise optical systems requiring extreme thermal stability across temperature fluctuations seen in space.
- 비용: Titanium alloys are generally more expensive than steels or aluminum alloys, both in terms of raw material and processing.
2. Invar (FeNi36): The Champion of Thermal Stability
Invar is an iron-nickel alloy notable for its uniquely low Coefficient of Thermal Expansion (CTE) around room temperature. Its name comes from the word “invariable,” referring to its relative lack of expansion or contraction with temperature changes.
- 주요 속성:
- Extremely Low CTE: Invar exhibits one of the lowest CTE values among metals and alloys near room temperature (typically around 1.2×10−6/°C). This is crucial for applications where dimensional stability during temperature fluctuations is critical.
- Good Strength and Ductility: While not as strong as Ti-6Al-4V, it possesses adequate mechanical properties for many structural components.
- 자기 속성: It is ferromagnetic.
- Why Use Invar for Gimbals?
- 뛰어난 열 안정성: Essential for high-precision optical benches, telescopes, and gimbal systems, particularly in space environments where temperature swings can be significant. Minimizing thermal expansion/contraction prevents defocusing or misalignment of optical elements.
- Precision Instrumentation: Often the material of choice when dimensional stability is the overriding design requirement.
- 고려 사항:
- Higher Density: Invar is significantly denser than Titanium (approx. 8.1 g/cm³ vs 4.4 g/cm³ for Ti-6Al-4V), making it less suitable where weight is the absolute primary constraint.
- AM Processing Challenges: Processing Invar via AM can be more challenging than Titanium. It requires careful parameter optimization to control residual stress and achieve desired low CTE properties in the final part. However, specialized powder production techniques, like the Plasma Rotating Electrode Process (PREP) offered by Met3dp for certain alloys, can yield highly spherical powders ideal for AM. Procurement teams looking for PREP Invar Powder B2B suppliers need partners with expertise in handling this specialty alloy.
- 비용: Invar powders suitable for AM can be expensive and less commonly available than Ti-6Al-4V.
Material Selection Summary for Aerospace Gimbals:
재질 | 주요 장점 | Primary Use Case for Gimbals | Main Drawback | Met3dp Powder Capability |
---|---|---|---|---|
Ti-6Al-4V | 높은 중량 대비 강도 비율 | Lightweight, stiff gimbals for UAVs, aircraft, general satellites | Moderate CTE | High-Quality Gas Atomized Powder |
Invar (FeNi36) | Extremely Low CTE | Ultra-stable gimbals for high-precision optical systems (space telescopes) | High Density, AM Challenges | Specialized Powders (e.g., PREP) |
시트로 내보내기
Met3dp’s Role as a Material and Service Provider:
Choosing the right material is only part of the equation. The quality of the metal powder and the expertise of the AM service provider are crucial for achieving the desired material properties and part performance. Met3dp, as a leading 금속 분말 공급업체 and AM solutions provider, leverages industry-leading powder manufacturing techniques like Vacuum Induction Melting Gas Atomization (VIGA) and PREP to produce high-sphericity, high-purity metal powders, including Ti-6Al-4V and potentially specialized alloys like Invar. Their expertise extends to optimizing printing processes, such as SEBM, which is known for producing parts with low residual stress, particularly beneficial for complex geometries like gimbal frames. Partnering with Met3dp ensures access to both high-quality materials and the process knowledge needed to successfully manufacture demanding aerospace components. Their portfolio includes not just standard alloys but also innovative materials like TiNi, TiTa, TiAl, and TiNbZr, demonstrating a commitment to advancing material options for 적층 제조.
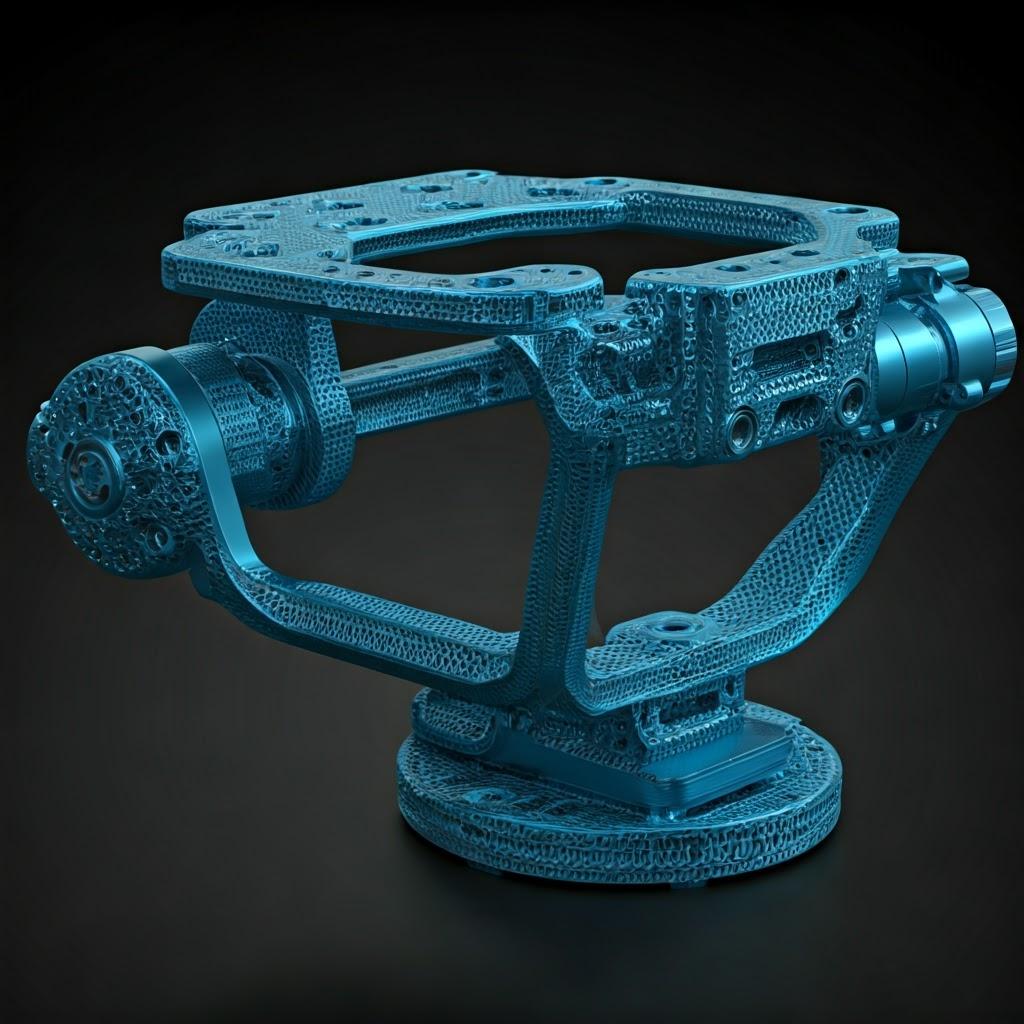
Design for Additive Manufacturing (DfAM) Principles for Gimbal Frames
Successfully leveraging metal additive manufacturing (AM) for aerospace gimbal frames requires more than simply converting an existing conventionally manufactured design file to an AM-compatible format. To truly unlock the benefits of lightweighting, part consolidation, and performance optimization, engineers must embrace 적층 제조를 위한 설계(DfAM) principles. DfAM involves designing components specifically with the capabilities and constraints of the chosen AM process in mind. For complex parts like gimbals, applying DfAM is crucial for achieving functional requirements while ensuring manufacturability and cost-effectiveness. Partnering with an experienced AM provider like Met3dp, who understands the nuances of processes like Selective Electron Beam Melting (SEBM), can significantly enhance the DfAM process.
Key DfAM Principles for Aerospace Gimbals:
- 토폴로지 최적화:
- 개념: This computational technique optimizes material layout within a defined design space based on specific load cases, boundary conditions, and performance goals (e.g., maximize stiffness, minimize mass).
- Application for Gimbals: Topology Optimization Aerospace tools generate highly organic and efficient load-bearing structures, removing material from low-stress areas. This is ideal for creating lightweight yet stiff gimbal arms and frames, directly contributing to reduced system inertia and power consumption. The resulting complex shapes are often only manufacturable via AM.
- 고려 사항: Optimized designs often require smoothing and interpretation to ensure manufacturability (e.g., avoiding features too thin to print reliably).
- Lattice Structures and Infill:
- 개념: Replacing solid volumes with internal lattice structures (e.g., honeycomb, gyroid, stochastic foams) can significantly reduce weight while maintaining structural integrity and increasing surface area (beneficial for heat dissipation).
- Application for Gimbals: Lattice Structures Design can be applied to bulkier sections of the gimbal frame to reduce mass without compromising stiffness. They can also be designed to provide specific vibration damping characteristics, enhancing optical stability.
- 고려 사항: Lattice complexity can increase design and simulation time. Minimum strut thickness and cell size are limited by the AM process resolution. Ensuring powder removal from intricate internal lattices is crucial.
- 파트 통합:
- 개념: Redesigning assemblies to combine multiple separate components into a single, monolithic printed part.
- Application for Gimbals: Brackets, mounts, cable routing features, and even elements of the bearing housings can potentially be integrated directly into the main gimbal frame structure. This reduces part count, eliminates fasteners (potential failure points), simplifies assembly, and improves overall structural efficiency.
- 고려 사항: Consolidated designs can be more complex to print and post-process. Repairability might be reduced if a single integrated feature is damaged.
- Feature Design for AM:
- 벽 두께: Adhering to minimum printable Wall Thickness AM guidelines for the chosen material and process (e.g., SEBM) is essential to prevent print failures or warping. Thin walls should generally be oriented vertically if possible.
- Holes and Channels: The orientation and diameter of holes impact printability. Horizontal holes may require internal supports or be designed as self-supporting diamond or teardrop shapes. Complex internal channels for cooling or wiring are feasible but require careful design for powder removal.
- Overhangs and Support Structures: Steep overhangs beyond a certain angle (typically 45 degrees for many metal PBF processes, though SEBM can sometimes handle lower angles due to powder sintering) require support structures. DfAM aims to minimize the need for supports by using self-supporting angles or orienting the part strategically on the build plate. Support Structure Strategy is critical as supports consume material, add print time, and require post-processing for removal, potentially affecting surface finish.
- Orientation and Anisotropy:
- 개념: The orientation of the part on the build platform affects surface finish, the need for supports, print time, and potentially the mechanical properties (anisotropy) due to the layer-by-layer build process.
- Application for Gimbals: Critical functional surfaces or features requiring the highest accuracy/smoothest finish should ideally be oriented upwards or vertically. Orienting the part to minimize large, flat overhangs reduces support requirements. Understanding potential anisotropy in mechanical properties (strength, ductility may vary slightly in Z vs. XY directions) is important for critical load paths, although processes like SEBM often result in more isotropic properties compared to SLM due to higher processing temperatures.
DfAM Guidelines Summary Table:
DfAM Principle | Goal | Key Benefit for Gimbals | 고려 사항 |
---|---|---|---|
토폴로지 최적화 | Maximize stiffness-to-weight ratio | Significant lightweighting, high performance | Manufacturability constraints, simulation complexity |
격자 구조 | Reduce mass in solid sections, add functionality | Lightweighting, vibration damping | Design complexity, powder removal |
부품 통합 | Reduce part count and assembly steps | Higher reliability, simplified logistics | Print complexity, repairability |
Feature Design | Ensure manufacturability, optimize performance | Reliable printing, functional integration | Process limitations (wall thickness, overhangs) |
Orientation Strategy | Minimize supports, optimize properties & finish | Reduced post-processing, predictable performance | Trade-offs between finish, supports, properties |
시트로 내보내기
Applying these DfAM Guidelines Metal Printing effectively often requires collaboration between design engineers and AM process experts. Companies like Met3dp provide this crucial link, offering guidance on designing parts optimized for their advanced 인쇄 방법, ensuring that the final gimbal frame meets both performance specifications and manufacturing realities.
Achieving Precision: Tolerance, Surface Finish, and Dimensional Accuracy in AM Gimbals
Aerospace gimbal frames, particularly those supporting optical systems, demand high levels of precision. While metal additive manufacturing offers numerous advantages in terms of design freedom and lightweighting, understanding and managing tolerances, surface finish, and overall dimensional accuracy is critical for ensuring the final component meets functional requirements. The achievable precision depends on the specific AM process, the material used, part geometry, build orientation, and post-processing steps employed.
Tolerances in Metal AM:
- General Tolerances: As-built metal AM parts typically achieve tolerances in the range of ±0.1 mm to ±0.2 mm (±0.004″ to ±0.008″) for smaller features, with tolerance ranges potentially widening over larger dimensions (e.g., ±0.1% to ±0.2% of the total length). Processes like Selective Electron Beam Melting (SEBM), known for operating at higher temperatures which reduces internal stresses, can sometimes offer better dimensional stability for large or complex parts compared to SLM. Met3dp’s industry-leading printers are engineered for high SEBM Accuracy.
- Factors Influencing Tolerance: Key factors include thermal stresses during printing (leading to minor warping or distortion), powder characteristics, laser/electron beam calibration, layer thickness, and part geometry complexity.
- 더 엄격한 허용 오차 달성: For critical features like bearing interfaces, mounting surfaces, or alignment datums requiring tolerances tighter than the standard as-built capability, secondary CNC machining operations are typically required during post-processing. DfAM should account for adding machining stock (e.g., 0.5mm – 1.0mm) to these specific surfaces.
표면 마감(거칠기):
- As-Built Surface Finish: The surface finish of as-built metal AM parts is generally rougher than machined surfaces. Surface roughness (Ra) values typically range from 5 µm to 25 µm (200 µin to 1000 µin), depending on the process, material, layer thickness, and surface orientation (upward-facing, downward-facing, vertical walls). Downward-facing surfaces impacted by support structures tend to be rougher after support removal.
- 표면 마감 개선: Various post-processing techniques can significantly improve the Surface Roughness AM Parts:
- 연마제 블라스팅(비드/모래 블라스팅): Provides a uniform matte finish, removes loose powder, but only marginally improves Ra values.
- 텀블링/진동 마감: Uses media to smooth surfaces and edges, effective for batches of smaller parts.
- 전기 연마: An electrochemical process that removes a thin layer of material, resulting in a very smooth, bright, and clean surface. Excellent for complex geometries and internal channels.
- CNC 가공: Used on specific surfaces requiring high smoothness and tight tolerances.
- 수동 연마: Labor-intensive but can achieve mirror finishes on accessible surfaces.
Dimensional Accuracy and Stability:
- 정의: Dimensional accuracy refers to how closely the final part conforms to the intended dimensions specified in the CAD model. Dimensional stability refers to the part’s ability to maintain its shape and size under operational conditions, particularly thermal fluctuations (Dimensional Stability Aerospace).
- Achieving Accuracy: This requires careful process control during printing, appropriate stress relief heat treatments after printing, and precise metrology for verification. Quality Control AM 가 가장 중요합니다.
- Metrology and Inspection: Verifying the dimensional accuracy of complex AM gimbal frames often requires advanced metrology tools:
- Coordinate Measuring Machines (CMM): Provide high-accuracy point measurements for critical dimensions and geometric dimensioning and tolerancing (GD&T) verification.
- 3D Laser Scanning / Structured Light Scanning: Capture dense point cloud data of the entire part surface, allowing comparison to the original CAD model (geometry verification) and assessment of overall form and deviation.
- 열 안정성: For applications requiring extreme stability (e.g., using Invar), not only must the AM process produce a dense part, but appropriate heat treatments may be needed to achieve the desired low-CTE microstructure. The inherent stability of the material itself is the primary factor here.
Precision Considerations Summary:
매개변수 | As-Built Capability (Typical Metal PBF) | Methods for Improvement | Importance for Gimbals |
---|---|---|---|
허용 오차 | ±0.1 to ±0.2 mm | CNC Machining (Critical Features) | Essential for interfaces, bearings, alignment |
Surface Finish (Ra) | 5 µm to 25 µm | Machining, Polishing, Electropolishing, Blasting | Affects friction (bearings), sealing, aesthetics |
치수 정확도 | Good, process-dependent | Process Control, Heat Treatment, Metrology | Ensures correct assembly and function |
열 안정성 | Material & Microstructure Dependent | Material Selection (e.g., Invar), Heat Treatment | Critical for optical pointing accuracy in varying temps |
시트로 내보내기
Achieving the necessary Metal 3D Printing Tolerances and finish for aerospace gimbals often involves a hybrid approach, leveraging AM for complex geometry creation and lightweighting, followed by targeted post-processing (especially machining) for critical interface features. Collaborating with a provider like Met3dp ensures that these considerations are integrated early in the design and manufacturing planning stages.
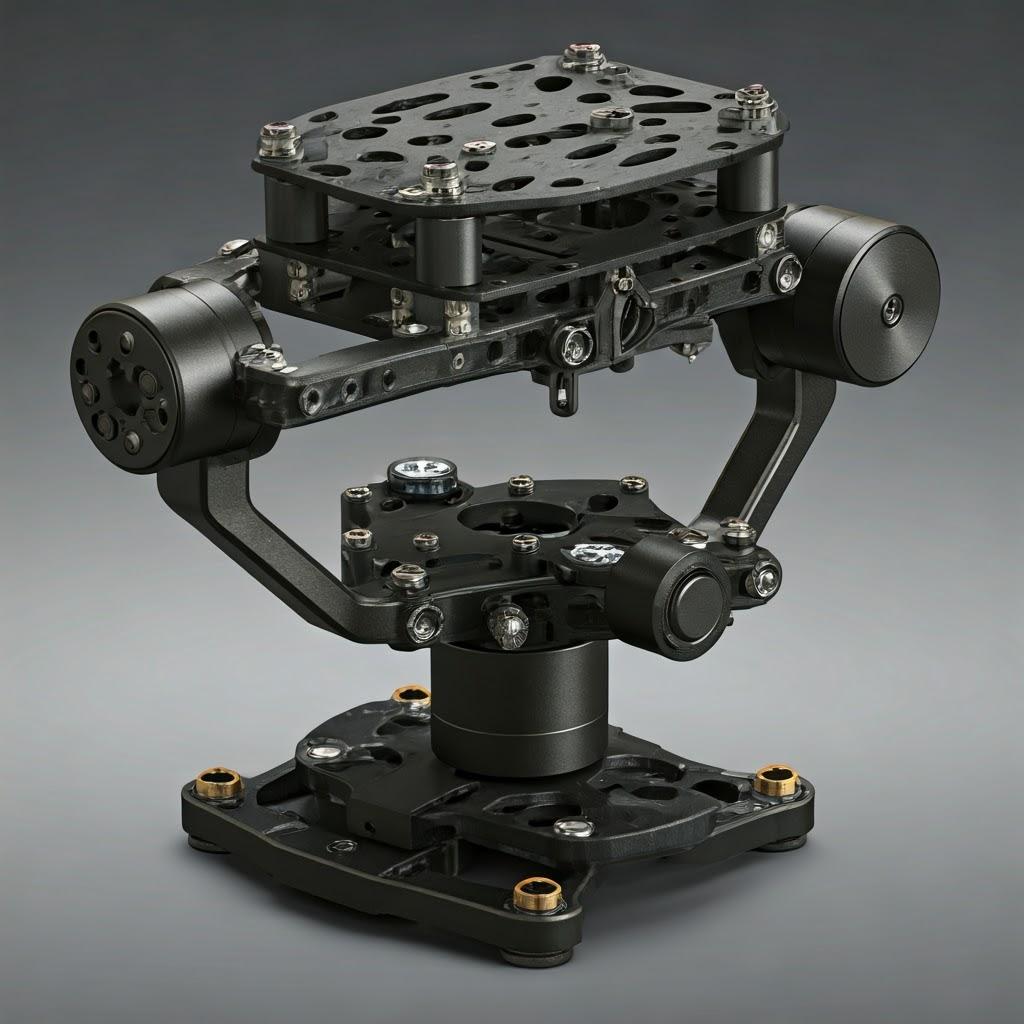
Essential Post-Processing Steps for 3D Printed Gimbal Frames
Producing a metal gimbal frame using additive manufacturing is rarely the end of the manufacturing journey. The ‘as-built’ part directly from the printer typically requires several 후처리 steps to meet the final engineering specifications for performance, dimensional accuracy, surface finish, and material properties. These steps are critical for ensuring the reliability and functionality demanded in aerospace applications. The specific sequence and necessity of these steps depend on the AM process used (e.g., SLM vs. SEBM), the material (Ti-6Al-4V vs. Invar), the part’s complexity, and its final application requirements.
Common Post-Processing Workflow for AM Metal Gimbals:
- Powder Removal (De-powdering):
- 프로세스: Removing unfused metal powder trapped within the part (especially in internal channels or complex lattice structures) and surrounding the part in the build chamber. This is typically done using compressed air, specialized vacuum systems, and manual brushing within a controlled environment to contain the potentially reactive metal powder.
- Importance: Ensures no loose powder interferes with subsequent steps or the final function. Critical for clearing internal channels designed for cooling or wiring. Thoroughness is key.
- 스트레스 완화 열처리:
- 프로세스: Heating the part (often while still attached to the build plate) in a vacuum or inert atmosphere furnace to a specific temperature profile, holding it, and then cooling it slowly.
- Importance: The rapid heating and cooling cycles inherent in Powder Bed Fusion processes induce residual stresses within the part. Stress relief minimizes distortion during removal from the build plate or subsequent machining and improves dimensional stability. Heat Treatment Aerospace Parts is a standard requirement for flight-critical components. SEBM, operating at higher build chamber temperatures, generally results in lower residual stress compared to SLM, potentially simplifying stress relief needs.
- 빌드 플레이트에서 파트 제거:
- 프로세스: Separating the printed part(s) from the metal build plate they were fused to. This is typically done using wire Electrical Discharge Machining (EDM), sawing, or sometimes milling/grinding.
- Importance: Frees the individual component for further processing. Care must be taken not to damage the part during removal.
- 지원 구조 제거:
- 프로세스: Removing the support structures designed to anchor the part to the build plate and support overhanging features during the build. This is usually done manually using pliers, cutters, and hand grinders, or sometimes via CNC machining or EDM for more delicate or inaccessible supports.
- Importance: Supports are sacrificial and not part of the final component. Removal can be labor-intensive and potentially damage the part surface if not done carefully. Marks or ‘witness lines’ are often left where supports were attached, requiring further finishing.
- Further Heat Treatments (Optional but Common):
- 프로세스: Depending on the material (especially Ti-6Al-4V) and desired properties, additional heat treatments like Hot Isostatic Pressing (HIP) or solution treatment and aging might be performed.
- HIP (Hot Isostatic Pressing): Combines high temperature and high inert gas pressure to close internal microporosity within the part, improving fatigue life, ductility, and overall material integrity. Often specified for critical aerospace components.
- Solution Treatment & Aging (for Ti-6Al-4V): Modifies the microstructure to enhance strength or other specific mechanical properties.
- Importance: Tailors the material’s microstructure and mechanical properties to meet final performance requirements, often exceeding those of cast or sometimes even wrought equivalents.
- Machining (Critical Feature Finishing):
- 프로세스: 사용 중 CNC Machining AM Components techniques (milling, turning, drilling, grinding) to achieve tight tolerances, specific surface finishes, and precise geometric features on critical surfaces (e.g., bearing bores, mounting interfaces, sealing surfaces).
- Importance: Bridges the gap between as-built AM tolerances/finish and the stringent requirements of aerospace interfaces. DfAM planning should incorporate extra material (machining stock) on these features.
- 표면 마감:
- 프로세스: Employing various Surface Finishing Options to achieve the desired surface texture, smoothness, or appearance on non-machined surfaces. This can include bead blasting (uniform matte finish), tumbling (deburring, smoothing edges), electropolishing (high smoothness, cleanability), or manual polishing.
- Importance: Improves aesthetics, can enhance fatigue resistance (shot peening), reduce friction, or prepare surfaces for coating.
- Cleaning and Inspection:
- 프로세스: Thoroughly cleaning the part to remove any machining fluids, polishing compounds, or debris. Final inspection using metrology tools (CMM, 3D scanning) verifies dimensional accuracy, and Non-Destructive Testing (NDT) methods (e.g., X-ray, CT scanning, FPI – Fluorescent Penetrant Inspection) may be used to check for internal defects or surface cracks.
- Importance: Ensures the part meets all specifications and is free from defects before assembly or deployment.
Post-Processing Step Summary:
단계 | 목적 | Typical Methods | Key Consideration |
---|---|---|---|
파우더 제거 | Remove unfused powder | Compressed Air, Vacuum, Brushing | Thoroughness, especially internal channels |
스트레스 풀기 | Reduce internal stress, prevent distortion | Vacuum Furnace Heat Treatment | Critical before build plate removal |
Part Removal | Separate part from build plate | Wire EDM, Sawing | Avoid part damage |
지지대 제거 | Remove temporary build supports | Manual Tools, CNC, EDM | Labor intensive, potential surface marks |
Further Heat Treatments | Improve density (HIP), enhance properties (Aging) | HIP Unit, Vacuum Furnace | Application-specific requirement |
가공 | Achieve tight tolerances & fine finish | CNC Milling, Turning, Grinding | Required for critical interfaces |
표면 마감 | Improve surface quality on non-machined areas | Blasting, Tumbling, Polishing, Electropolishing | Aesthetics, fatigue, coating prep |
Cleaning & Inspection | Ensure cleanliness & compliance | Solvents, Ultrasonic; CMM, 3D Scan, NDT | Final quality verification |
시트로 내보내기
The extent and complexity of post-processing significantly impact the final cost and lead time of an AM gimbal frame. Engaging with a full-service provider like Met3dp, who can manage or advise on this entire workflow from initial design through final inspection, is crucial for procurement managers and engineers seeking reliable, high-quality aerospace components.
Overcoming Common Challenges in Additive Manufacturing of Gimbals
While metal additive manufacturing offers transformative potential for aerospace gimbal frames, the process is not without its challenges. Understanding these potential hurdles and implementing strategies to overcome them is essential for successful production, particularly for demanding aerospace applications where quality and reliability are non-negotiable. Awareness of these issues allows engineers and procurement teams to work proactively with their AM partners.
Common Challenges and Mitigation Strategies:
- Warping and Distortion (Thermal Stress):
- 도전: The intense, localized heating and rapid cooling during PBF processes create significant thermal gradients, leading to internal stresses. If these stresses exceed the material’s yield strength, the part can warp or distort, especially thin or large flat features, potentially causing build failures or dimensional inaccuracies.
- 완화 전략:
- Process Selection: SEBM generally induces lower residual stress than SLM due to its higher, more uniform build chamber temperature and pre-sintering of the powder bed.
- Optimized Support Structures: Robust supports anchor the part effectively to the build plate, resisting distortion forces during the build.
- 빌드 오리엔테이션: Orienting the part to minimize large cross-sectional areas parallel to the build plate can reduce stress accumulation.
- 프로세스 매개변수 최적화: Fine-tuning laser/electron beam power, scan speed, and scan strategy (e.g., island scanning) helps manage heat input. Met3dp leverages deep AM Process Optimization expertise.
- 스트레스 완화 열처리: Performing this step immediately after printing (ideally before plate removal) is critical for Thermal Stress Management.
- Support Structure Removal Difficulties:
- 도전: Supports, while necessary, must be removed in post-processing. This can be time-consuming, labor-intensive, and risk damaging the part surface, especially for complex internal supports or delicate features. Support “witness marks” can negatively impact surface finish.
- 완화 전략:
- DfAM for Support Minimization: Designing parts with self-supporting angles (typically >45°) and optimizing build orientation reduces the need for supports.
- Intelligent Support Design: Using support structures with lower density or engineered break-points makes them easier to remove. Software tools are continually improving in this area.
- Process Selection: Some processes or parameter sets might allow for steeper overhangs with fewer supports.
- Advanced Removal Techniques: Utilizing wire EDM or specialized machining for support removal in critical or hard-to-reach areas.
- 다공성:
- 도전: Small voids or pores can form within the printed material due to incomplete fusion between layers, trapped gas, or powder inconsistencies. Porosity can detrimentally affect mechanical properties, particularly fatigue strength. Porosity Control 3D Printing is vital for critical parts.
- 완화 전략:
- Optimized Process Parameters: Ensuring sufficient energy density (beam power, speed) for full melting and fusion.
- High-Quality Powder: Using powder with high sphericity, controlled particle size distribution, good flowability, and low internal gas content (Met3dp’s focus on advanced powder production addresses this). Stringent Powder Quality Control 는 필수입니다.
- Controlled Build Environment: Maintaining proper vacuum levels (SEBM) or inert gas flow (SLM) to minimize oxidation and gas entrapment.
- 열간 등방성 프레싱(HIP): An effective post-processing step to close internal microporosity and significantly improve material density and fatigue performance.
- Surface Finish Roughness:
- 도전: As-built surfaces are inherently rougher than machined surfaces due to the layer-wise nature and partially melted powder particles. This can be problematic for sealing surfaces, bearing interfaces, or aerodynamic smoothness.
- 완화 전략:
- 매개변수 최적화: Using thinner layers generally improves finish but increases build time. Contour scanning can smooth vertical walls.
- 빌드 오리엔테이션: Prioritizing critical surfaces as upward-facing or vertical generally yields better finishes.
- 후처리: Implementing appropriate surface finishing steps (machining, polishing, blasting, etc.) as described previously.
- Achieving Material Properties (Especially for Sensitive Alloys like Invar):
- 도전: Ensuring the final AM part exhibits the desired microstructure and mechanical properties (e.g., the extremely low CTE of Invar) requires precise control over the entire process, from powder quality to print parameters and post-processing heat treatments. Deviations can lead to suboptimal performance.
- 완화 전략:
- Rigorous Material Characterization: Qualifying AM materials thoroughly through extensive testing.
- Strict Process Control: Utilizing machines with robust monitoring and control systems (like Met3dp’s industry-leading printers) and adhering to qualified build parameters.
- Tailored Heat Treatments: Developing and applying specific heat treatment cycles validated to achieve the target properties for the specific alloy and application.
- Supplier Expertise: Partnering with an AM provider possessing deep materials science knowledge and experience with the specific alloy.
Challenge Mitigation Summary:
도전 | Primary Cause | Key Mitigation Strategy | Met3dp Advantage |
---|---|---|---|
Warping/Distortion | Residual Thermal Stress | Process Choice (SEBM), Supports, Orientation, Heat Treatment | SEBM Expertise, Process Control |
지지대 제거 | Required for Overhangs | DfAM, Smart Supports, Orientation, Advanced Removal Tech | Design/Process Optimization Guidance |
다공성 | Incomplete Fusion, Gas, Powder Quality | Optimized Parameters, Quality Powder, HIP, Process Control | High-Quality Powders, Robust Printers, Process Control |
표면 마감 | Layer-wise Process, Powder Adhesion | Parameters, Orientation, Post-Processing Finishing | Guidance on Achievable Finishes & Post-Processing |
머티리얼 속성 | Process Variation, Microstructure Control | Material Qualification, Process Control, Heat Treatment | Materials Science Expertise, Qualified Processes |
시트로 내보내기
Overcoming these challenges requires a combination of robust technology, meticulous process control, materials science expertise, and adherence to DfAM principles. Engaging with a knowledgeable and experienced AM partner like Met3dp, equipped with advanced systems and a focus on quality from powder to final part inspection, is the most effective way to navigate these complexities and ensure the successful production of high-performance, reliable aerospace gimbal frames.
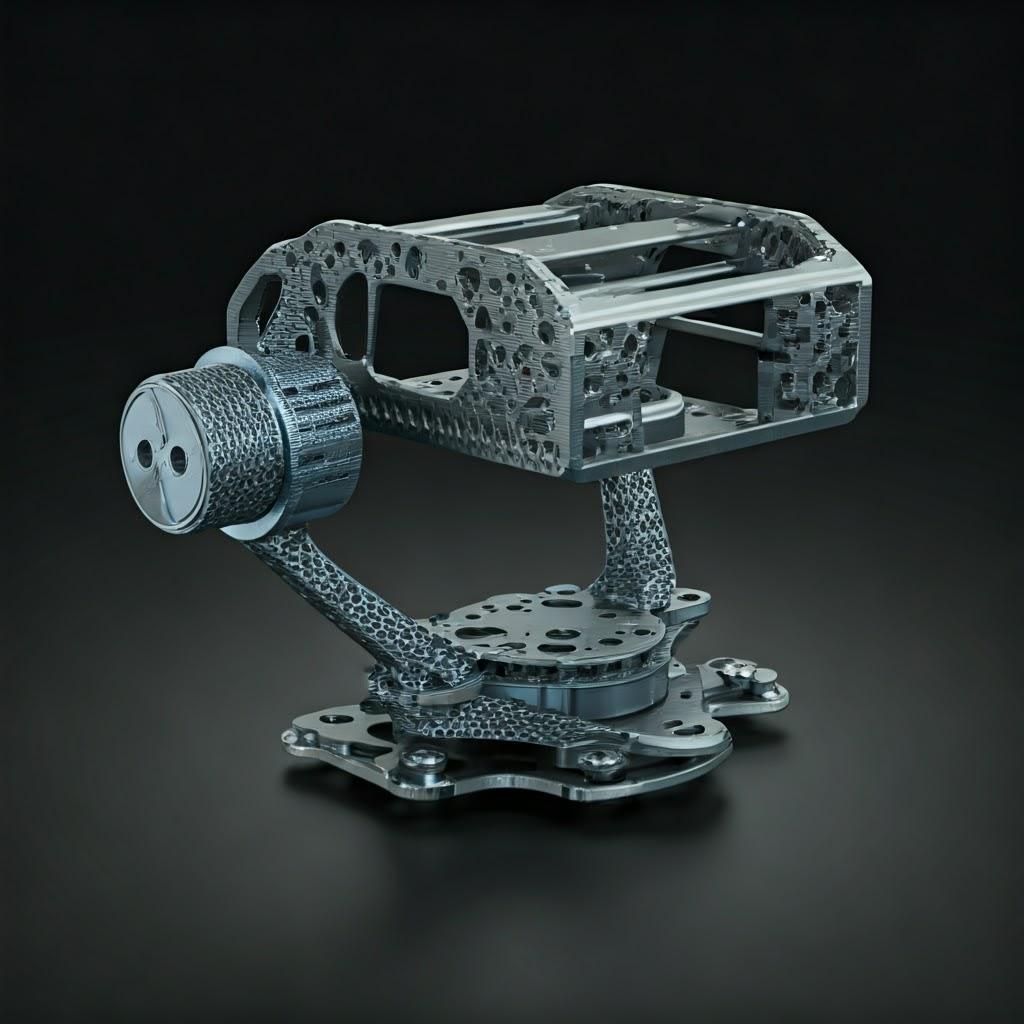
How to Choose the Right Metal 3D Printing Service Provider for Aerospace Gimbals
Selecting the right additive manufacturing partner is as critical as the design and material choices when producing high-stakes components like aerospace gimbal frames. The quality, reliability, and performance of the final part heavily depend on the supplier’s capabilities, expertise, and quality systems. For engineers and procurement managers navigating the Aerospace AM Supplier Qualification process, evaluating potential partners requires a thorough assessment beyond just quoting price. Choosing a capable and reliable B2B Metal Printing Service ensures project success and mitigates risks associated with flight-critical hardware.
Key Criteria for Evaluating AM Service Providers:
- Aerospace Experience and Certifications:
- Track Record: Does the supplier have demonstrable experience manufacturing components for the aerospace and defense industries? Can they provide case studies or references?
- 인증: Is the provider certified to relevant aerospace quality standards, primarily AS9100 Certified 3D Printing? This certification ensures robust quality management systems tailored for the demands of the aerospace sector. Other relevant certifications might include ISO 9001 or specific customer approvals. Compliance with regulations like ITAR (International Traffic in Arms Regulations) may be necessary for defense projects.
- Technical Expertise and Engineering Support:
- DfAM Knowledge: Does the provider offer Design for Additive Manufacturing (DfAM) support? Can their engineers collaborate effectively to optimize gimbal designs for printability, performance, and cost-effectiveness?
- Materials Science Expertise: Do they possess deep knowledge of the recommended materials (Ti-6Al-4V, Invar) and their specific processing requirements in AM? Can they advise on material selection trade-offs?
- Process Understanding: Do they have expert-level understanding of their specific AM processes (e.g., SLM, SEBM) and how parameters affect final part properties? Met3dp, for instance, has decades of collective expertise in Metal AM Expertise.
- Equipment and Technology:
- Process Capability: Does the supplier operate the appropriate metal AM technology (e.g., SEBM, SLM) best suited for the specific gimbal design and material? Do they have well-maintained, industrial-grade machines? Met3dp utilizes its own industry-leading SEBM printers known for accuracy and reliability.
- 볼륨을 구축합니다: Can their machines accommodate the size of the required gimbal frame?
- 파우더 처리: Do they have stringent procedures for handling, storing, and recycling metal powders to maintain purity and prevent contamination?
- Material Quality and Traceability:
- Powder Sourcing: Do they source high-quality metal powders from reputable suppliers, or, like Met3dp, manufacture their own powders using advanced methods like gas atomization or PREP?
- Material Certification: Can they provide material certifications (e.g., chemical composition, particle size distribution) with each batch of powder?
- Traceability: Is there full Material Traceability AM throughout the process, linking the final part back to the specific powder batch, machine, build parameters, and post-processing steps? This is crucial for aerospace quality control.
- Post-Processing Capabilities:
- In-house vs. Outsourced: Does the provider offer necessary post-processing steps (stress relief, HIP, machining, finishing, inspection) in-house, or do they manage a qualified network of subcontractors? In-house capabilities often streamline the workflow and improve quality control.
- 전문성: Do they have proven expertise in executing these post-processing steps to aerospace standards?
- Quality Management and Inspection:
- Quality System: Beyond AS9100, what does their overall Quality Management System (QMS) entail? How do they manage process control and documentation?
- 검사 기능: Do they possess advanced metrology equipment (CMM, 3D scanners) and NDT capabilities (X-ray/CT) for thorough part validation?
- Reporting: Can they provide comprehensive quality documentation, including build logs, material certs, inspection reports, and certificates of conformity?
- Communication and Project Management:
- 응답성: How responsive and transparent is the supplier during the quoting (RFQ Metal 3D Printing) and production process?
- 프로젝트 관리: Do they have dedicated project managers to ensure timelines and communication requirements are met?
공급업체 평가 체크리스트 요약:
기준 | 주요 질문 | Why It Matters for Gimbals |
---|---|---|
Aerospace Experience/Certs | AS9100? Proven aerospace projects? ITAR compliance? | Ensures understanding of stringent requirements & quality systems |
기술 전문성 | DfAM support? Materials/Process knowledge? Engineering collaboration? | Optimizes design for performance, manufacturability, cost |
Equipment/Technology | Right process (SEBM/SLM)? Build volume? Machine quality? Powder handling? | Ensures capability to produce the part reliably |
Material Quality/Traceability | Powder source/quality? Certifications? Full traceability? | Guarantees material integrity and compliance |
포스트 프로세싱 | In-house capabilities (Heat Treat, HIP, Machining)? Expertise? | Ensures final part meets all dimensional & property specs |
Quality Management | Robust QMS? Process control? Advanced inspection (CMM, NDT)? Documentation? | Verifies part quality and conformance |
Communication/PM | Responsiveness? Transparency? Dedicated project management? | Ensures smooth execution and timely delivery |
시트로 내보내기
Choosing a partner like Met3dp, which emphasizes comprehensive solutions spanning advanced SEBM printers, high-quality metal powders produced in-house, and deep application development expertise, significantly de-risks the adoption of AM for critical components. Learning more 우리에 대하여 reveals a commitment to partnership and enabling next-generation manufacturing.
Understanding Cost Factors and Lead Times for AM Gimbal Production
While metal additive manufacturing offers significant advantages, understanding the associated costs and production timelines is crucial for budgeting, project planning, and making informed decisions when comparing AM to traditional manufacturing methods. The Metal 3D Printing Cost Breakdown 및 Additive Manufacturing Lead Time are influenced by a multitude of factors specific to each project.
Key Cost Drivers for 3D Printed Gimbals:
- Material Type and Consumption:
- 재료비: High-performance aerospace alloys like Ti-6Al-4V and especially Invar have significantly different raw material powder costs. Specialty alloys command premium pricing.
- Part Volume & Support Volume: The total amount of material fused (part volume) and the material used for support structures directly impact cost. Larger or denser parts consume more expensive powder. DfAM efforts to lightweight the part and minimize supports yield direct cost savings.
- Part Complexity and Design:
- Geometric Complexity: Highly intricate designs with complex internal channels or fine features may require more sophisticated printing strategies and potentially increase build time or post-processing effort.
- 파트 통합: While consolidation reduces assembly costs, the resulting single complex part might have a longer print time or require more complex support/post-processing strategies compared to simpler individual components.
- 구축 시간:
- 파트 볼륨 및 높이: Larger parts or taller builds naturally take longer to print layer by layer.
- Number of Parts per Build: Printing multiple parts simultaneously (nesting) in a single build job can significantly reduce the cost per part by distributing machine setup and operation time. Bulk Order Metal AM often benefits from build platform optimization.
- 레이어 두께 및 매개변수: Thinner layers improve resolution and surface finish but increase build time. Optimized print parameters aim to balance speed and quality.
- 사후 처리 요구 사항:
- Mandatory Steps: Costs associated with powder removal, stress relief, part/support removal are generally standard.
- Optional/Advanced Steps: The need for HIP, extensive CNC machining for tight tolerances, specialized surface finishing (polishing, coating), or advanced NDT significantly adds to the final Aerospace Component Pricing. Labor-intensive steps like manual polishing or support removal for complex geometries are major cost contributors.
- Quality Assurance and Inspection:
- Level of Inspection: Basic dimensional checks cost less than comprehensive CMM inspection against full GD&T specifications or advanced NDT like CT scanning. Aerospace requirements often necessitate higher levels of inspection, impacting cost.
- Non-Recurring Engineering (NRE) Costs:
- Design Optimization (DfAM): If significant design work or optimization is required by the AM service provider.
- 프로세스 자격: For highly critical parts, specific process qualification or validation builds might be necessary.
Typical Lead Times:
Lead times for AM gimbal frames can vary significantly but are often faster than traditional methods involving complex tooling or casting, especially for prototypes or low volumes.
- 프로토타이핑: Typically ranges from a few days to 2-3 weeks, depending on complexity, machine availability, and basic post-processing needs.
- Production Parts: Can range from 2-3 weeks to several months for larger quantities or parts requiring extensive post-processing and rigorous quality assurance protocols.
- 리드 타임에 영향을 미치는 요인: Machine availability/scheduling, build time, complexity and duration of post-processing steps (HIP and machining are often bottlenecks), inspection requirements, and shipping logistics.
Lead Time Breakdown Example (Illustrative):
스테이지 | Typical Duration (Illustrative) | Key Factors Affecting Duration |
---|---|---|
사전 처리 | 1-3 Days | Design review, build preparation |
인쇄 | 1-7 Days | Part size/volume, nesting efficiency |
스트레스 풀기 | 1-2 Days | Furnace availability, cycle time |
Part/Support Removal | 1-3 Days | Complexity, manual effort required |
HIP (if needed) | 3-7 Days | Scheduling, cycle time, logistics |
가공 | 2-10+ Days | Complexity, number of setups, scheduling |
마무리 | 1-5 Days | Method used, surface area |
검사 | 1-5 Days | Level of inspection required |
해운 | 1-5 Days | Location, shipping method |
Total (Est.) | ~2 weeks to 2+ months | Sum of applicable stages |
시트로 내보내기
Obtaining accurate quotes and lead time estimates requires providing detailed CAD models, material specifications, tolerance requirements, post-processing needs, and quantity information to potential suppliers like Met3dp. Understanding these cost and time factors allows for better project planning and justification of AM adoption for aerospace gimbal production.
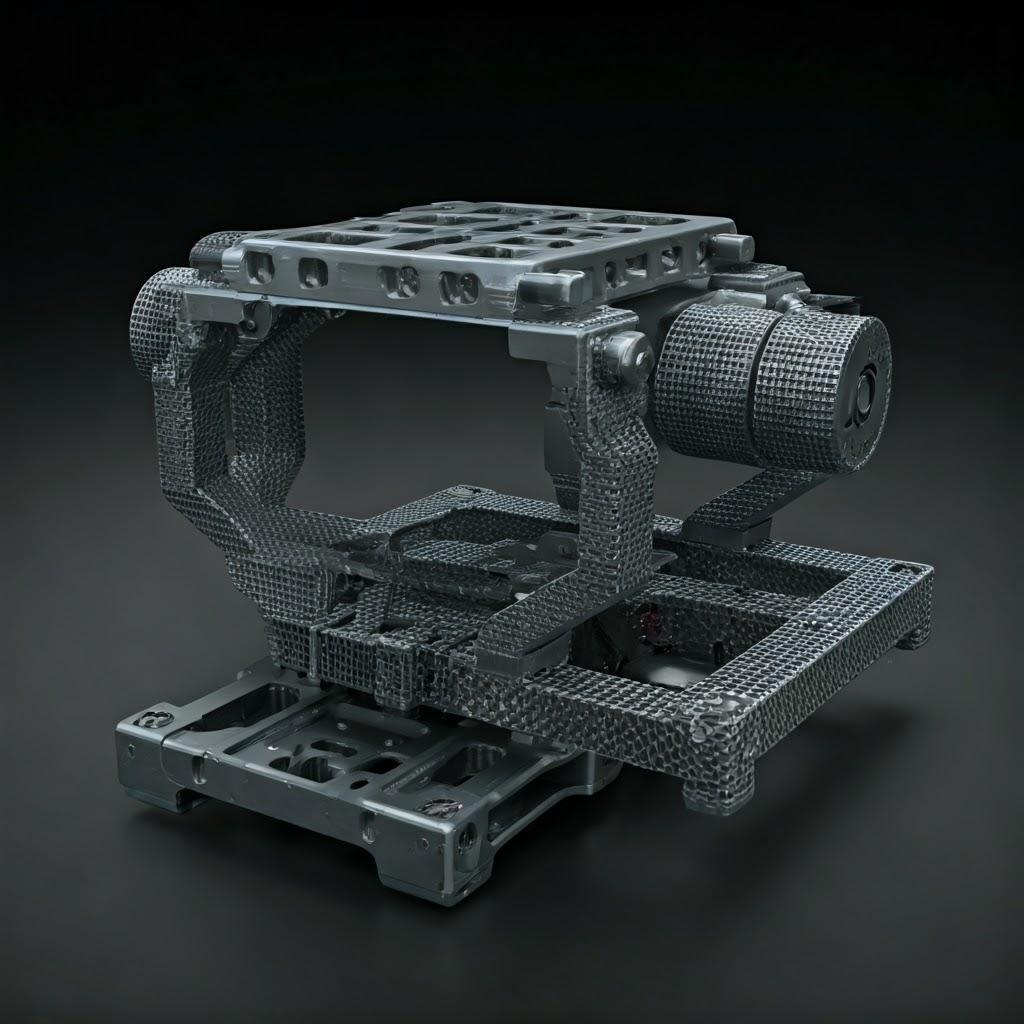
Frequently Asked Questions (FAQ) about 3D Printed Aerospace Gimbals
As metal additive manufacturing becomes more established for producing aerospace components, engineers and procurement managers often have specific questions regarding its application for gimbal frames. Here are answers to some common queries:
1. Are 3D printed metal gimbals as strong and reliable as machined ones?
Yes, when designed, manufactured, and post-processed correctly. Metal AM processes like SEBM and SLM can produce fully dense parts (often >99.9% density, especially after HIP) from high-performance alloys like Ti-6Al-4V. The mechanical properties (strength, fatigue life, ductility) of AM components can meet or even exceed those of cast parts and often rival wrought properties, especially after appropriate heat treatments. AM Gimbal Durability depends heavily on:
- Correct DfAM: Ensuring the design effectively manages operational loads.
- 프로세스 제어: Using optimized and validated printing parameters.
- 파우더 품질: Employing high-quality, aerospace-grade metal powders.
- 후처리: Implementing necessary steps like stress relief and potentially HIP to ensure material integrity and desired microstructure.
- 품질 보증: Rigorous inspection and testing to verify properties and detect defects.
Partnering with an experienced provider who controls these factors ensures the reliability required for aerospace applications.
2. What certifications are needed for 3D printed aerospace components like gimbals?
Metal AM Certification is crucial for flight-critical hardware. Key certifications and qualifications include:
- AS9100: The standard for Quality Management Systems for Aviation, Space, and Defense organizations. This is often a minimum requirement for suppliers.
- 재료 사양: Compliance with aerospace material standards (e.g., AMS specifications for Ti-6Al-4V). Material must be sourced and handled with full traceability.
- Process Specifications: Adherence to qualified and documented manufacturing processes, often including specific customer or regulatory body approvals (e.g., FAA, EASA).
- Part-Specific Qualification: Critical components may require individual qualification involving extensive testing (static, fatigue, environmental) of parts produced using the specific AM process and parameters.
- Supplier Audits: Customers typically conduct audits to verify the supplier’s QMS, process control, and traceability.
3. How does the cost of a 3D printed gimbal compare to a traditionally manufactured one (e.g., CNC machined)?
The Cost Comparison AM vs Traditional manufacturing is complex and depends heavily on the specific part and production volume:
- 복잡성: For highly complex geometries or parts requiring significant part consolidation, AM can be 더 비용 효율적 even at low volumes, as it avoids intricate machining setups or assembly labor. Traditional machining of very complex parts from billet can involve extremely high programming time, setup time, and material waste.
- 볼륨: For simpler geometries produced in high volumes, traditional CNC machining or casting may still be more economical due to faster cycle times per part once initial tooling/setup is complete. AM typically has a relatively flat cost-per-part regardless of volume (after initial NRE), making it highly competitive for low-to-medium volumes.
- 리드 타임: AM often offers significant lead time advantages for prototypes and initial production runs due to the absence of tooling, which can represent significant value (faster time-to-market).
- 경량화: If AM enables significant weight reduction (as is often the case with optimized gimbal designs), the lifetime operational cost savings (fuel, launch costs) can far outweigh any initial difference in manufacturing cost.
A detailed cost analysis comparing AM (including NRE, material, build time, post-processing) with traditional methods (tooling, material waste, machining time, assembly) is needed for a specific gimbal design to make an informed decision.
Conclusion: Partnering for Advanced Aerospace Gimbal Solutions with Met3dp
The landscape of 항공우주 제조 is undergoing a significant transformation, driven by the capabilities of metal additive manufacturing. For complex, performance-critical components like aerospace gimbal frames, metal 3D printing offers unparalleled advantages in lightweighting, design optimization, part consolidation, and accelerated development cycles. Utilizing advanced materials like Ti-6Al-4V for its strength-to-weight ratio or Invar for its exceptional thermal stability allows engineers to push the boundaries of optical system performance and reliability.
However, realizing the full potential of AM requires navigating challenges related to design optimization (DfAM), process control, material quality, post-processing, and rigorous quality assurance. Choosing the right manufacturing partner – one with proven aerospace expertise, advanced technology, robust quality systems, and a commitment to collaboration – is paramount to success.
Met3dp stands as a leader in this evolving field, offering comprehensive Met3dp Additive Solutions tailored for the demanding requirements of the aerospace industry. Our capabilities encompass:
- Industry-Leading Equipment: Utilizing advanced SEBM printers engineered for accuracy, reliability, and producing low-stress parts ideal for complex gimbal geometries.
- High-Performance Metal Powders: Manufacturing a wide range of high-quality, spherical metal powders (including Ti alloys, superalloys, and potentially specialty materials like Invar) using cutting-edge gas atomization and PREP technologies, ensuring optimal material properties.
- Deep Expertise: Decades of collective expertise in metal AM, materials science, and application development, enabling us to provide invaluable DfAM support and process optimization.
- End-to-End Support: Partnering with organizations from initial concept through design, prototyping, production, post-processing, and final qualification.
We understand the critical nature of aerospace components and are dedicated to helping our clients leverage Metal AM Innovation to achieve their goals, whether it’s reducing satellite mass, enhancing UAV surveillance capabilities, or ensuring the stability of space-based telescopes. As your Aerospace Manufacturing Partner, Met3dp is ready to support your Digital Manufacturing Transformation.
Explore how Met3dp’s cutting-edge systems and advanced materials can power your next-generation gimbal frame project and other demanding aerospace applications. We invite you to learn more about our 제품 and capabilities. Contact Met3dp today to discuss your specific requirements with a Contact Metal 3D Printing Supplier who understands the intricacies of aerospace manufacturing.
공유
중국 칭다오에 본사를 둔 선도적인 적층 제조 솔루션 제공업체인 MET3DP Technology Co. 당사는 산업용 3D 프린팅 장비와 고성능 금속 분말을 전문으로 합니다.
관련 기사
Met3DP 소개
최근 업데이트
제품
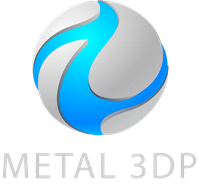
3D 프린팅 및 적층 제조용 금속 분말