Precision Instrument Cases 3D Printed in Stainless Steel
목차
Introduction: The Crucial Role of Precision Instrument Cases in Advanced Industries
In the intricate landscape of modern technology, sensitive instruments are the unsung heroes. From guiding spacecraft through the cosmos and monitoring vital signs in operating rooms to controlling complex processes in automated factories and enabling groundbreaking scientific research, these instruments are fundamental to progress. However, their sophisticated nature often renders them incredibly vulnerable. Environmental factors like shock, vibration, temperature fluctuations, moisture, electromagnetic interference (EMI), and corrosive elements can compromise their accuracy, shorten their lifespan, or lead to catastrophic failure. This underscores the paramount importance of robust, reliable, and precisely engineered instrument cases.
An instrument case, often referred to as an enclosure or housing, is far more than just a box. It’s a critical component designed to shield delicate internal electronics, sensors, optics, and mechanisms from the harsh realities of their operating environments. The demands placed on these protective shells are intensifying. Miniaturization trends require compact yet highly protective designs. Increased performance generates more heat, necessitating effective thermal management. Furthermore, the need for customization to accommodate unique instrument geometries and functionalities is growing, particularly for specialized applications in sectors like aerospace, medical technology, automotive engineering, and advanced industrial manufacturing.
Traditionally, instrument cases have been manufactured using methods like CNC machining from billet material, casting (investment or die casting), or sheet metal fabrication. While effective for many applications, these methods face limitations, especially when dealing with complex geometries, thin walls, internal features, rapid prototyping needs, or low-to-medium volume production runs. Machining can be subtractive and generate significant material waste, especially for intricate designs. Casting requires expensive tooling and may struggle with very fine details or thin sections. Sheet metal fabrication often involves compromises in terms of structural rigidity, sealing capabilities, and geometric freedom.
입력하다 금속 적층 제조(AM), commonly known as metal 3D 프린팅. This transformative technology offers a revolutionary approach to producing high-performance instrument cases. By building parts layer by layer directly from digital models using specialized metal powders, AM overcomes many traditional manufacturing constraints. It enables the creation of highly complex, lightweight, and customized enclosures with unprecedented design freedom. Materials like 316L 스테인리스 스틸 offer exceptional corrosion resistance and durability, making them ideal for demanding industrial and medical applications, while Ti-6Al-4V 티타늄 합금 provides an outstanding strength-to-weight ratio crucial for aerospace and portable medical devices.
The ability to consolidate multiple parts into a single printed component, integrate features like internal channels for cooling or conformal shielding, and rapidly iterate designs makes metal AM particularly compelling for instrument case manufacturing. Procurement managers and engineers are increasingly recognizing the strategic advantages: faster time-to-market for new products, optimized performance through tailored designs, enhanced protection for valuable instruments, and potentially lower overall costs for complex or low-volume parts. This technology isn’t just about making existing case designs differently; it’s about enabling entirely new possibilities in instrument protection and functionality, tailored precisely to the application’s needs. Companies seeking B2B manufacturing solutions, wholesale instrument enclosures, or reliable industrial suppliers are finding metal 3D printing to be a game-changing resource for producing mission-critical components.
Applications Across Industries: Where are Metal 3D Printed Instrument Cases Used?
The versatility of metal additive manufacturing, combined with the robust properties of materials like 316L stainless steel and Ti-6Al-4V, makes 3D printed instrument cases suitable for a diverse array of demanding applications across multiple high-stakes industries. Engineers and procurement specialists sourcing custom instrument cases, protective enclosures또는 specialized housings are increasingly turning to metal AM to meet stringent performance requirements that traditional methods struggle to achieve efficiently or economically.
1. Aerospace and Defense: The aerospace sector demands components that are lightweight, incredibly strong, resistant to extreme temperatures and vibrations, and often feature highly complex geometries for packaging sensitive avionics, sensors, and communication equipment. * Avionics Enclosures: Protecting flight control systems, navigation units (GPS, INS), and communication modules from harsh flight conditions (vibration, G-forces, temperature swings). Ti-6Al-4V is often preferred for its high strength-to-weight ratio. * Sensor Housings: Cases for optical sensors, radar components, and telemetry equipment often require intricate internal features, specific mounting points, and EMI shielding, all achievable with AM. * Satellite Components: Enclosures for sensitive electronics on satellites must withstand the vacuum of space, radiation, and extreme thermal cycling. Metal AM allows for complex, weight-optimized designs crucial for launch cost reduction. * Defense Applications: Ruggedized cases for field communication gear, targeting systems, and surveillance equipment benefit from the durability and customization potential of 3D printed stainless steel or titanium. B2B suppliers providing MIL-SPEC compliant enclosures find AM a valuable tool.
2. Medical Technology: The medical field requires biocompatibility (for implantable or skin-contact devices), sterilizability, chemical resistance, and often intricate designs for surgical tools, diagnostic equipment, and patient monitoring devices. * Surgical Instrument Housings: Cases for powered surgical tools (drills, saws) or controllers require ergonomic designs, sealing against bodily fluids, and the ability to withstand repeated sterilization cycles (autoclaving). 316L stainless steel is a common choice due to its proven biocompatibility and corrosion resistance. * Diagnostic Equipment Enclosures: Housings for portable ultrasound devices, handheld scanners, or laboratory analysis equipment benefit from the design freedom to create compact, ergonomic, and durable cases. * Implantable Device Casings: While less common for external cases, the principles apply to casings for pacemakers or internal monitoring devices where biocompatibility (Ti-6Al-4V) and hermetic sealing are critical. * Custom Bracing and Fixture Components: Though not strictly ‘cases’, related applications include custom-printed housings for components within exoskeletons or patient-specific therapeutic devices.
3. Automotive: In the automotive industry, particularly in performance vehicles, electric vehicles (EVs), and autonomous driving systems, instrument cases must protect sensitive electronics from vibration, heat, moisture, and impacts. * Sensor Housings: Cases for LiDAR, radar, cameras, and various powertrain sensors require precise mounting, thermal management features (e.g., integrated heat sinks), and environmental sealing. * ECU (Electronic Control Unit) Enclosures: Protecting the ‘brains’ of the vehicle requires robust housings, often with complex connector integration and heat dissipation strategies. AM allows for optimized, potentially conformal designs. * Battery Management System (BMS) Housings: Cases for EV battery monitoring electronics need to be durable, potentially lightweight, and offer specific mounting and cooling provisions. * Motorsport Applications: High-performance racing demands lightweight yet extremely durable enclosures for data loggers, telemetry systems, and control modules, often requiring rapid prototyping and custom designs – areas where AM excels.
4. Industrial Manufacturing and Automation: Factory floors and industrial sites present challenges like high temperatures, chemical exposure, dust, moisture, and heavy vibrations. Instrument cases here need to be exceptionally rugged and reliable. * Process Control Sensor Housings: Protecting sensors monitoring temperature, pressure, flow, or chemical composition in harsh industrial processes. 316L stainless steel offers excellent chemical resistance. * Robotics Component Enclosures: Housings for controllers, sensors, or connectors on robotic arms need to withstand continuous motion, potential impacts, and industrial contaminants. * Test and Measurement Equipment Cases: Portable or benchtop equipment used for quality control, calibration, or R&D requires durable, often custom-fitted cases. * Harsh Environment Electronics: Enclosures for electronics deployed in oil and gas exploration, mining, or marine environments where corrosion resistance and sealing are paramount. Wholesale suppliers often seek robust, standardized designs achievable with repeatable AM processes.
5. Scientific Research and Exploration: From deep-sea exploration to particle accelerators, scientific instruments often operate at the extremes, requiring highly specialized protection. * Deep-Sea Equipment Housings: Cases must withstand immense pressure and corrosive seawater. Titanium alloys are often necessary. * Vacuum Chamber Components: Housings for instruments inside vacuum systems require specific material properties and leak-tight designs. * Field Research Equipment: Portable instruments for environmental monitoring, geological surveys, or biological research need rugged, weather-resistant cases.
The common thread across these diverse applications is the need for precision, protection, and often, customization. Metal 3D printing provides a powerful manufacturing solution capable of meeting these complex requirements, enabling engineers to design and procure instrument cases that are perfectly optimized for their specific function and operating environment. For B2B buyers looking for industrial instrument suppliers 또는 custom enclosure manufacturers, partnering with a knowledgeable metal AM provider like Met3dp unlocks access to these advanced manufacturing capabilities.
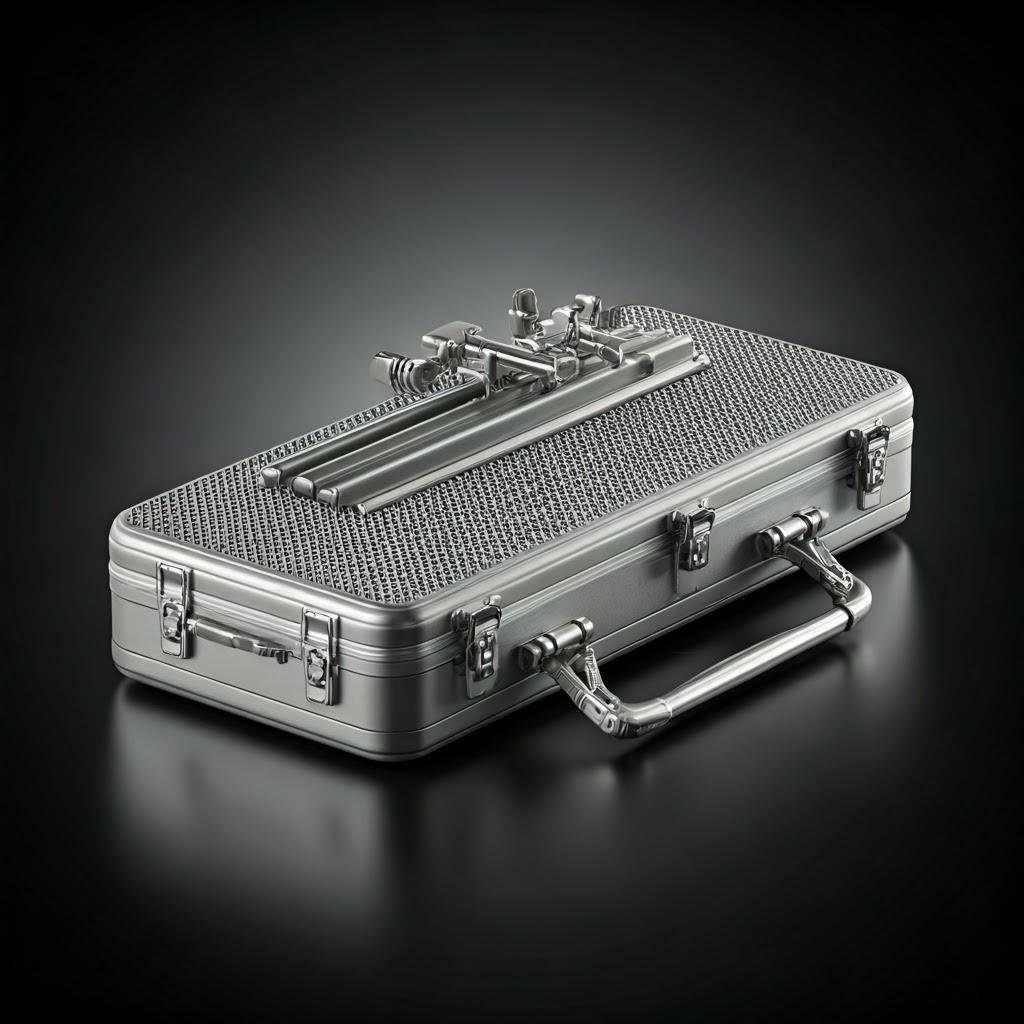
Why Choose Metal Additive Manufacturing for Instrument Case Production?
While traditional manufacturing methods like CNC machining, casting, and sheet metal forming have long served the purpose of creating instrument cases, metal additive manufacturing (AM) presents a compelling suite of advantages, particularly when complexity, customization, speed, or unique material properties are required. Engineers, designers, and procurement managers evaluating manufacturing options for precision enclosures, custom instrument housings또는 protective cases for sensitive equipment should carefully consider the distinct benefits offered by metal 3D printing.
1. Unparalleled Design Freedom and Geometric Complexity: This is arguably the most significant advantage of AM. Traditional methods are inherently subtractive (machining) or formative (casting, stamping), imposing limitations on achievable geometries. * 복잡한 내부 기능: AM can create intricate internal channels for cooling fluids or air, integrated mounting bosses, partitions, or complex pathways for wiring, all within a single, monolithic part. This is extremely difficult or impossible with machining or casting. * Conformal Designs: Cases can be designed to conform precisely to the shape of the internal components, minimizing wasted space and potentially reducing overall device size and weight. * Organic Shapes and Topology Optimization: AM enables the creation of complex, curved, and organic shapes driven by structural or thermal optimization software. This allows for highly efficient designs that place material only where it’s needed, significantly reducing weight without compromising strength – crucial for aerospace and portable devices. * 파트 통합: Multiple components that would traditionally need to be manufactured separately and then assembled (e.g., a case body, lid, internal brackets, heat sink) can often be consolidated into a single 3D printed part. This reduces assembly time, eliminates potential failure points at joints, and simplifies the supply chain.
2. Customization and Rapid Prototyping: AM is inherently digital, making it ideal for producing unique or low-volume parts without the high tooling costs associated with casting or injection molding. * 주문형 생산: Cases can be printed as needed, reducing inventory requirements and facilitating just-in-time manufacturing strategies. * Patient-Specific Medical Devices: For medical applications, AM allows for the creation of truly unique housings tailored to individual patient anatomy or specific surgical needs. * 신속한 반복: Design changes can be implemented quickly by modifying the CAD file and printing a new iteration. This accelerates the product development cycle, allowing engineers to test and refine designs much faster than with methods requiring new tooling or complex reprogramming. Procurement managers benefit from faster validation of designs before committing to larger volumes. * Low-Volume Viability: Producing small batches (even single units) of custom cases is economically feasible with AM, whereas setting up for traditional methods can be cost-prohibitive for low volumes. This is ideal for specialized industrial equipment or R&D projects.
3. Material Properties and Selection: Metal AM processes work with specialized, high-performance metal powders, offering properties suitable for demanding applications. * High-Strength Alloys: Materials like Ti-6Al-4V titanium offer exceptional strength-to-weight ratios, ideal for aerospace and lightweight applications. * 내식성: 316L stainless steel provides excellent resistance to corrosion and chemicals, making it suitable for medical, marine, and industrial environments. Met3dp specialises in producing high-quality metal powders like these, ensuring optimal material properties. * 그물 모양에 가까운 모양: AM typically produces parts very close to their final dimensions (near-net shape), reducing the amount of post-process machining required compared to starting with a large billet, thus saving material and machining time. * Potential for Unique Alloys: AM platforms, particularly Electron Beam Melting (EBM) systems like those potentially used or researched by Met3dp, can sometimes process materials that are difficult or impossible to work with using traditional methods.
4. Reduced Lead Times (Especially for Complex Parts): While the printing process itself can take hours or days depending on part size and complexity, the overall lead time from design finalization to finished part can often be significantly shorter with AM compared to traditional methods, especially when tooling is involved. * No Tooling Required: Eliminating the need to design, manufacture, and wait for molds or dies (which can take weeks or months) dramatically shortens the initial production timeline. * Faster First Articles: Getting the first functional prototype or production part can be achieved much more quickly, accelerating validation and market entry. * Supply Chain Simplification: Consolidating parts and using on-demand production can simplify logistics and reduce reliance on multiple suppliers.
5. Potential for Weight Reduction: Through topology optimization and the ability to create complex internal lattice structures, AM can produce instrument cases that are significantly lighter than their traditionally manufactured counterparts while maintaining or even improving structural integrity. This is a critical advantage in weight-sensitive applications like aerospace, automotive, and portable equipment.
Comparison Table: Metal AM vs. Traditional Methods for Instrument Cases
기능 | 금속 적층 제조(AM) | CNC 가공 | Casting (Investment/Die) | Sheet Metal Fabrication |
---|---|---|---|---|
기하학적 복잡성 | Very High (Internal features, lattices, organic shapes) | Moderate to High (Limited by tool access) | Moderate (Requires draft angles, wall thickness limits) | Low to Moderate (Bends, folds, seams) |
사용자 지정 | Very High (Economical for single units/low volume) | High (Requires reprogramming) | Low (Requires expensive tooling per design) | Moderate (Tooling often required) |
Lead Time (Initial) | Fast (No tooling) | Moderate (Programming, setup) | Slow (Tooling creation) | Moderate to Fast (Depending on complexity) |
재료 낭비 | Low (Near-net shape, powder recyclability) | High (Subtractive process) | Low (Near-net shape) | Moderate (Offcuts) |
부품 통합 | 높은 잠재력 | 낮음 | Moderate (Can create complex single pieces) | 낮음 |
툴링 비용 | 없음 | Low (Fixturing may be needed) | 매우 높음 | Moderate (Dies, punches may be needed) |
가장 적합한 대상 | Complex, custom, low-volume, lightweight, rapid prototypes | High precision, moderate complexity, various volumes | High volume, moderate complexity | Lower cost, simple geometries, high volume |
머티리얼 예시 | 316L, Ti-6Al-4V, Inconel, Aluminum Alloys | Most machinable metals | Casting alloys (Aluminum, Zinc, Steel, etc.) | Steel, Stainless Steel, Aluminum |
시트로 내보내기
While metal AM offers compelling advantages, it’s essential to partner with an experienced provider. Companies like Met3dp, with their focus on 금속 3D 프린팅 solutions, possess the expertise in equipment operation, material science, and post-processing necessary to realize the full potential of this technology for producing high-quality, reliable instrument cases. They understand the nuances of processes like Laser Powder Bed Fusion (LPBF) and Electron Beam Melting (EBM), ensuring parts meet the stringent requirements of demanding industries.
Material Spotlight: 316L Stainless Steel and Ti-6Al-4V for Optimal Performance
Choosing the right material is fundamental to the success of any engineered component, and instrument cases are no exception. The operating environment, structural requirements, weight constraints, and necessary certifications all dictate the ideal material choice. For metal 3D printed instrument cases targeting demanding applications, two materials stand out for their exceptional balance of properties: 316L 스테인리스 스틸 및 Ti-6Al-4V 티타늄 합금. Understanding their characteristics is crucial for engineers designing protective enclosures and for procurement managers sourcing B2B manufacturing solutions.
316L Stainless Steel: The Versatile Workhorse
316L is an austenitic stainless steel alloy containing chromium, nickel, and molybdenum. The “L” signifies low carbon content (typically <0.03%), which minimizes carbide precipitation during welding or heat treatments, thereby enhancing its corrosion resistance, particularly in chloride environments. It is one of the most widely used materials in metal additive manufacturing due to its excellent processability, well-understood properties, and cost-effectiveness compared to more exotic alloys.
Key Properties and Benefits for Instrument Cases:
- 뛰어난 내식성: This is perhaps the most significant advantage of 316L. It exhibits outstanding resistance to atmospheric corrosion, as well as a wide range of chemicals, acids, and saltwater. This makes it ideal for:
- Medical devices requiring sterilization and resistance to bodily fluids.
- Marine applications exposed to saltwater spray and immersion.
- Industrial environments with chemical fumes or wash-down procedures.
- Food processing equipment requiring hygienic, non-reactive surfaces.
- Good Strength and Ductility: 316L offers a good combination of tensile strength and toughness, allowing cases to withstand impacts and stresses encountered in industrial or field use. Its ductility allows for some deformation before fracture, providing a degree of resilience.
- 생체 적합성: 316L is widely accepted for medical applications involving contact with skin or bodily fluids (though not typically for permanent implants without specific surface treatments or certifications). It meets standards like ISO 10993 for many applications.
- Sterilizability: Cases made from 316L can be repeatedly sterilized using common methods like autoclaving (steam sterilization), gamma radiation, or ethylene oxide (EtO) without significant degradation of properties.
- Weldability and Machinability: Although AM reduces the need for welding, the inherent weldability of 316L is useful if attachments or modifications are needed post-printing. It can also be readily machined for critical tolerance features or surface finishes.
- 비용 효율성: Compared to titanium or nickel superalloys, 316L powder is relatively economical, making it a cost-effective choice for many applications where extreme weight saving isn’t the primary driver.
Met3dp’s Commitment: Utilizing high-quality, gas-atomized 316L powder is crucial for achieving dense, defect-free parts with consistent properties. Met3dp’s advanced powder manufacturing systems, employing technologies like gas atomization, ensure the production of spherical 316L powders with excellent flowability – a key factor for reliable and high-resolution printing in Laser Powder Bed Fusion (LPBF) systems. This commitment to powder quality translates directly into superior final part integrity for instrument cases.
Ti-6Al-4V (Grade 5) Titanium Alloy: The High-Performance Lightweight Champion
Ti-6Al-4V, often referred to as Ti64 or Grade 5 titanium, is the most widely used titanium alloy. It’s an alpha-beta alloy known for its exceptional combination of high strength, low density, and excellent corrosion resistance. While more expensive than stainless steel, its properties make it indispensable in applications where weight is a critical factor.
Key Properties and Benefits for Instrument Cases:
- 뛰어난 무게 대비 강도 비율: Ti-6Al-4V is approximately 40% lighter than steel but offers comparable or even superior strength. This makes it the material of choice for:
- Aerospace components where every gram saved translates to fuel efficiency or increased payload capacity.
- Portable medical devices where reduced weight enhances usability and patient comfort.
- Automotive applications, particularly in motorsport, where reducing unsprung mass or overall vehicle weight is critical.
- Man-portable military or field research equipment.
- High Strength and Fatigue Resistance: It maintains good strength at moderately elevated temperatures (up to around 300-400°C) and exhibits excellent resistance to fatigue failure, crucial for components subjected to cyclic loading or vibration.
- 뛰어난 내식성: Ti-6Al-4V offers exceptional resistance to a wide range of corrosive environments, including seawater, chlorides, and many industrial chemicals. Its performance often exceeds that of stainless steels in aggressive media.
- 생체 적합성: Grade 5 titanium is highly biocompatible and is extensively used for medical implants (orthopedic, dental) due to its excellent integration with bone and resistance to corrosion by bodily fluids. This makes it suitable for housings of implantable electronics or long-term skin-contact devices.
- 낮은 열 팽창: Titanium has a relatively low coefficient of thermal expansion, which can be beneficial in applications requiring dimensional stability across a range of temperatures.
처리 고려 사항: Printing Ti-6Al-4V requires careful control of the build environment (typically an inert argon atmosphere) to prevent oxygen pickup, which can embrittle the material. Post-processing often involves stress relief heat treatments to minimize residual stresses built up during the rapid heating and cooling cycles of the AM process. Met3dp’s expertise likely extends to managing these process intricacies, potentially utilizing systems like SEBM (Selective Electron Beam Melting) which operates under vacuum and at higher temperatures, often reducing residual stress in titanium parts. Their experience ensures that Ti-6Al-4V instrument cases meet the stringent mechanical property requirements.
Material Comparison Table:
기능 | 316L 스테인리스 스틸 | Ti-6Al-4V 티타늄 합금 |
---|---|---|
Primary Advantage | Corrosion Resistance, Cost-Effectiveness | Strength-to-Weight Ratio, Biocompatibility |
Density (approx.) | ~8.0g/cm³ | ~4.43g/cm³ |
Tensile Strength (Typical AM) | 500-650 MPa | 900-1100 MPa |
내식성 | Excellent (General, Chlorides) | Outstanding (Seawater, Wide Range) |
생체 적합성 | Good (Non-implant, skin contact) | Excellent (Implant grade) |
최대 사용 온도 | Moderate (~400-500°C, application dependent) | Moderate-High (~300-400°C continuous) |
상대적 비용 | Lower | 더 높음 |
일반적인 애플리케이션 | Medical Devices, Industrial, Marine, Food | Aerospace, Medical Implants, Performance Auto |
시트로 내보내기
선택하기:
The selection between 316L and Ti-6Al-4V for a 3D printed instrument case ultimately depends on the specific application requirements:
- 선택 316L 스테인리스 스틸 when:
- Excellent corrosion resistance in general industrial or medical environments is key.
- Cost is a major driving factor.
- Extreme weight saving is not the primary goal.
- Sterilizability is required.
- 선택 Ti-6Al-4V 티타늄 합금 when:
- Minimizing weight is critical (aerospace, portable devices).
- The highest strength-to-weight ratio is needed.
- Exceptional corrosion resistance, especially in aggressive media like seawater, is required.
- Biocompatibility for implantation or long-term contact is necessary.
- Performance at moderately elevated temperatures is a factor.
Partnering with a knowledgeable additive manufacturing provider like Met3dp, who not only operates advanced 인쇄 방법 but also manufactures high-quality powders like 316L and potentially Ti-6Al-4V and other innovative alloys (TiNi, TiTa, TiAl, TiNbZr, CoCrMo), ensures that the selected material is processed optimally to deliver instrument cases with the desired performance and reliability. Their expertise guides customers in selecting the most appropriate material and process for their unique needs, from initial design consultation through to finished part delivery. Procurement managers seeking reliable B2B suppliers for wholesale instrument cases or custom enclosure projects can leverage this material and process expertise for superior outcomes. Sources and related content
Design for Additive Manufacturing (DfAM): Optimizing Instrument Cases for 3D Printing
Simply taking a design intended for CNC machining or casting and sending it to a metal 3D printer rarely yields optimal results. To truly leverage the power of additive manufacturing for instrument cases, engineers must embrace 적층 제조를 위한 설계(DfAM) principles. DfAM is a methodology that focuses on designing parts specifically for the layer-by-layer fabrication process, taking into account its unique capabilities and constraints. Applying DfAM not only improves the printability and quality of the final part but also unlocks opportunities for enhanced performance, reduced weight, and lower costs that are unachievable with traditional design approaches. Optimizing an instrument case design for AM requires considering geometry, support structures, material properties, and the specific printing process being used (e.g., Laser Powder Bed Fusion – LPBF, or Electron Beam Melting – EBM).
Key DfAM Principles for Instrument Cases:
1. Geometric Considerations and Feature Design: AM excels at complexity, but certain geometric features print more reliably and efficiently than others. * 벽 두께: While AM can produce very thin walls, extremely thin sections (<0.4-0.5mm, depending on process and machine) can be prone to warping or incomplete formation. Conversely, very thick sections can accumulate residual stress and increase print time and cost. Aim for consistent, moderate wall thicknesses where possible, or use internal lattice structures to support thicker sections while saving weight and material. Design guides from service providers like Met3dp often provide specific recommendations based on their equipment (e.g., their industry-leading print volume printers) and materials. * Holes and Channels: Horizontal holes or channels often print well without supports up to a certain diameter (self-supporting). Vertical or angled holes are generally less problematic. Teardrop shapes are often preferred over simple circles for horizontally oriented holes to avoid the need for internal supports on the “roof” of the hole. Internal channels for cooling or wiring should be designed with smooth transitions and consideration for powder removal after printing. * Overhangs and Angles: Surfaces angled relative to the build plate require careful consideration. Steep angles (typically >45 degrees from the horizontal) are generally self-supporting. Shallow overhangs require support structures to prevent sagging or collapse during printing. Designing parts with self-supporting angles where possible minimizes the need for supports, reducing post-processing effort and material waste. * Minimum Feature Size: AM processes have limitations on the smallest features they can accurately resolve (e.g., small pins, thin ribs, sharp corners). Consult the specifications of the chosen printing system and material. Sharp internal corners can act as stress concentrators and may benefit from small radii (fillets).
2. Support Structures: Support structures are often necessary evils in metal AM. They anchor the part to the build plate, support overhanging features, and help dissipate heat during the printing process. However, they consume extra material, add print time, and require removal during post-processing, which can leave witness marks on the surface. * Designing for Minimal Supports: Orienting the part strategically on the build plate can significantly reduce the need for supports. Analyze the geometry to identify overhangs and choose an orientation that minimizes shallow angles. Sometimes, minor design modifications (e.g., adding a chamfer instead of a sharp overhang) can eliminate the need for supports altogether. * Support Accessibility: When supports are unavoidable, design them (or ensure your AM partner designs them) for easy removal. Avoid placing supports in hard-to-reach internal cavities or on critical functional surfaces where witness marks would be unacceptable. Specialized support structures (e.g., tree supports, block supports) can be employed depending on the geometry and process. * Impact on Surface Finish: Support contact points will typically have a rougher surface finish after removal compared to unsupported or upward-facing surfaces. Factor this into design considerations for critical surfaces, potentially adding extra stock material in supported areas if subsequent machining is planned.
3. Topology Optimization and Lightweighting: This is where DfAM truly shines for applications like aerospace or portable devices where weight is critical. Topology optimization software uses algorithms (like Finite Element Analysis – FEA) to determine the most efficient material distribution to withstand specific loads, removing unnecessary material while maintaining structural integrity. * Organic and Lattice Structures: AM is uniquely capable of producing the complex, often organic-looking shapes and internal lattice structures that result from topology optimization. These structures are impossible or prohibitively expensive to create with traditional methods. For an instrument case, this could mean a lightweight internal rib structure or a selectively densified shell, providing strength only where needed. * Load Path Optimization: Designing the case structure to follow the primary load paths ensures maximum efficiency and minimizes stress concentrations. * Integration with Thermal Management: Topology optimization can be combined with thermal analysis to create designs with integrated heat sinks or optimized airflow channels, formed as part of the main case structure.
4. Part Consolidation: As mentioned earlier, AM allows multiple components of an assembly to be combined into a single printed part. * Reducing Assembly: Analyze the instrument case assembly (body, lid, internal brackets, fasteners). Can any of these be integrated into a single, more complex print? This reduces part count, assembly labor, inventory management, and potential points of failure (like seals or joints). * Simplifying Supply Chain: Fewer parts mean fewer suppliers, less procurement overhead, and a simpler bill of materials (BOM). This is a significant advantage for procurement managers seeking efficiency.
5. Designing for Post-Processing: Consider how the part will be finished after printing. * Machining Allowances: If critical dimensions require high precision achievable only through machining, add extra stock material (e.g., 0.5-1.0mm) to those specific surfaces in the CAD model. * Access for Support Removal and Inspection: Ensure internal features are accessible for powder removal (compressed air, vibration) and support structure removal (manual or CNC). Design access ports if necessary, which might be sealed later. * 표면 마감 요구 사항: Specify which surfaces require particular finishes (e.g., smooth for sealing, textured for grip) and account for how post-processing (polishing, blasting, coating) will achieve this.
DfAM Checklist for Instrument Cases:
- Orientation: How will the part be oriented on the build plate to minimize supports and optimize feature resolution?
- 지원: Where are supports necessary? Can they be minimized through redesign? Are they accessible for removal?
- 벽 두께: Are wall thicknesses appropriate (not too thin, not excessively thick)? Is thickness consistent where possible?
- 오버행: Are there shallow overhangs? Can they be made self-supporting (e.g., >45 degrees) or redesigned (e.g., using chamfers)?
- Holes/Channels: Are horizontal holes designed optimally (e.g., teardrop shape)? Are internal channels designed for powder removal?
- Minimum Features: Do small features meet the minimum resolution capabilities of the AM process? Are sharp internal corners filleted?
- 경량화: Can topology optimization or lattice structures be used to reduce weight without compromising function?
- 파트 통합: Can multiple components be integrated into a single printed part?
- 후처리: Are allowances made for machining? Is access provided for support/powder removal and inspection? Are surface finish requirements considered in the design?
Successfully implementing DfAM requires collaboration between designers and AM experts. Engaging with a service provider like Met3dp early in the design process allows engineers to leverage their deep understanding of specific printing processes, material behaviors, and optimization techniques. Their expertise ensures that the final instrument case design is not only manufacturable but also fully optimized for performance, weight, and cost using additive manufacturing. Exploring the various product offerings, including powders and potential printing services, can provide further insight into achievable specifications.
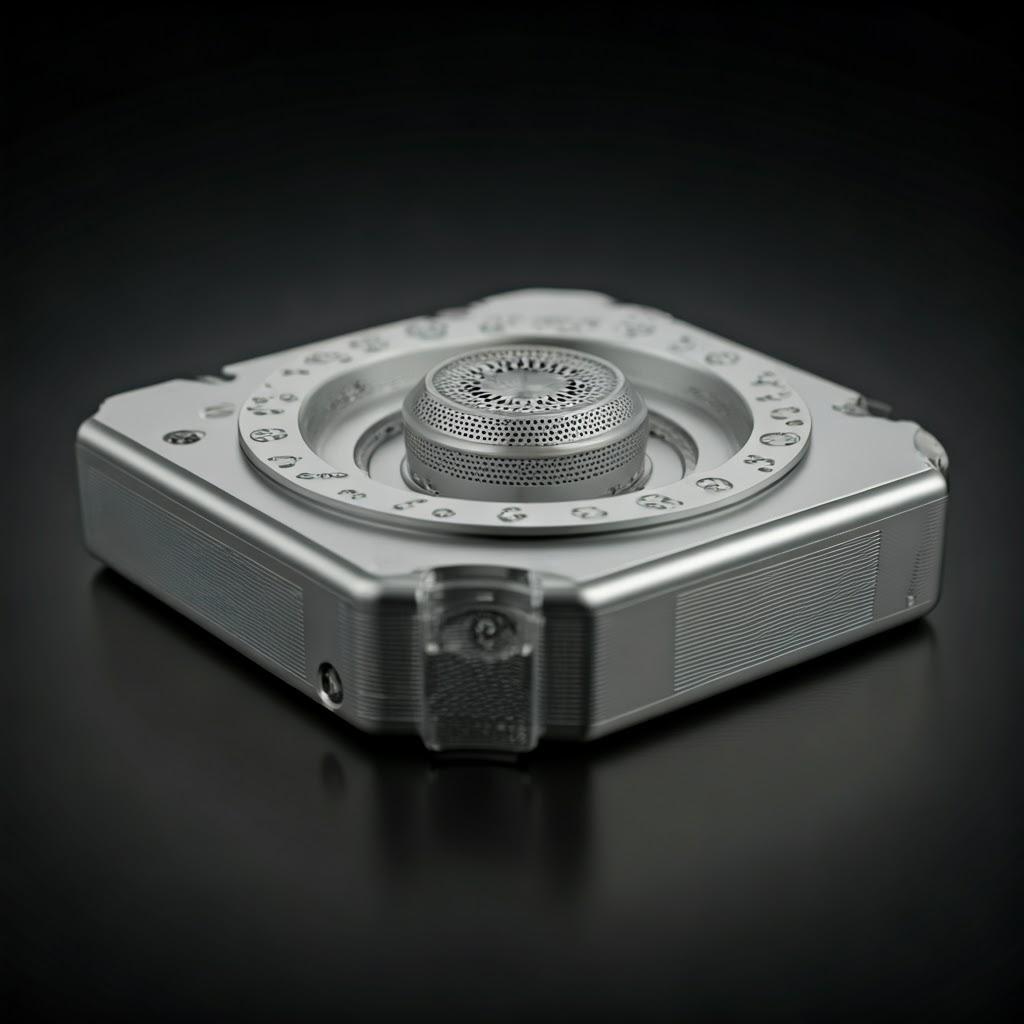
Achieving Precision: Tolerance, Surface Finish, and Dimensional Accuracy in 3D Printed Cases
While metal additive manufacturing offers incredible design freedom, understanding the achievable levels of precision, surface finish, and dimensional accuracy is crucial for managing expectations and ensuring the final instrument case meets its functional requirements. These aspects are influenced by the specific AM process (LPBF, EBM), the material used (316L, Ti-6Al-4V), the printer’s calibration, part geometry, orientation, and post-processing steps. Engineers designing cases and procurement managers sourcing them need clarity on what tolerances and finishes are typical “as-printed” and what can be achieved through secondary operations.
Dimensional Accuracy and Tolerances:
Dimensional accuracy refers to how closely the printed part conforms to the dimensions specified in the CAD model. Tolerances define the permissible variation in those dimensions. * 일반적인 인쇄물 허용 오차: Metal AM processes like LPBF typically achieve dimensional tolerances in the range of ±0.1 mm to ±0.2 mm (or ±0.1% to ±0.2% of the dimension, whichever is greater) for well-controlled processes and moderate-sized parts. EBM processes might have slightly looser tolerances due to the higher processing temperatures but often exhibit lower residual stress. However, these are general guidelines, and accuracy can vary significantly based on: * Part Size and Geometry: Larger parts or complex geometries with thin walls or overhangs may experience more distortion (due to thermal stresses) and thus exhibit larger deviations. * Orientation: The orientation on the build plate affects thermal gradients and support locations, influencing accuracy in different axes (X, Y, Z). Z-axis accuracy (layer height) is often different from X-Y accuracy. * Material: Different materials shrink or warp differently during cooling. * 머신 보정: The accuracy and calibration of the specific 3D printer play a significant role. Providers like Met3dp emphasize the accuracy and reliability of their equipment for mission-critical parts. * 더 엄격한 허용 오차 달성: For critical features requiring tolerances tighter than ±0.1 mm (e.g., mating surfaces, bearing bores, precise mounting points), post-process machining (CNC milling, turning, grinding) is typically required. DfAM principles dictate adding extra stock material (machining allowance) to these specific features in the design phase. * Repeatability: While achieving very tight tolerances as-printed can be challenging, the repeatability of AM processes is generally good once process parameters are dialed in. This means that subsequent parts printed under the same conditions will have similar dimensional characteristics, which is important for series production.
표면 마감(거칠기):
Surface finish, often quantified by Ra (average roughness), describes the texture of the part’s surfaces. As-printed metal AM parts inherently have a rougher surface finish compared to machined or polished components. * As-Printed Surface Roughness (Ra): * LPBF: Typically ranges from 6 µm to 15 µm Ra, depending on material, layer thickness, orientation, and specific parameters. Upward-facing surfaces tend to be smoother than downward-facing or side surfaces. * EBM: Generally produces rougher surfaces than LPBF, often in the range of 20 µm to 40 µm Ra, due to larger powder particle sizes and partial sintering. * Factors Influencing As-Printed Finish: * 레이어 두께: Thinner layers generally result in smoother surfaces but increase print time. * 파우더 입자 크기: Finer powders can lead to smoother finishes. Met3dp’s focus on high-quality, spherical powders produced via gas atomization contributes to better surface quality compared to lower-quality powders. * Orientation: Surfaces parallel to the build layers (upward/downward facing) have different roughness characteristics than vertical walls due to the stair-stepping effect. Overhanging surfaces supported by structures will have the roughest finish after support removal. * Laser/Beam Parameters: Energy density, scan speed, and hatching patterns influence the melt pool characteristics and resulting surface texture. * 표면 마감 개선: For applications requiring smoother surfaces (e.g., sealing faces, aesthetic requirements, improved fatigue life, fluid flow), various post-processing techniques are employed: * Abrasive Blasting (Bead Blasting, Sand Blasting): Provides a uniform matte finish, removes loose powder, and can slightly improve Ra (e.g., down to 5-10 µm Ra). * 텀블링/진동 마감: Uses abrasive media in a tumbling barrel or vibratory bowl to deburr edges and achieve a smoother, more uniform finish over the entire part. Effective for batches of smaller parts. * CNC 가공: Can achieve very smooth finishes (Ra < 1 µm) on specific critical surfaces. * Polishing (Manual or Automated): Can achieve mirror-like finishes (Ra << 0.1 µm) for aesthetic or optical applications, but is often labor-intensive. * 전기 연마: An electrochemical process that removes a thin layer of material, smoothing surfaces and enhancing corrosion resistance, particularly effective for 316L stainless steel.
Table: Typical Tolerances and Surface Finishes for Metal AM Instrument Cases
기능 | As-Printed (Typical LPBF) | After Machining | After Polishing/Electropolishing | 참고 |
---|---|---|---|---|
치수 허용 오차 | ±0.1 to ±0.2 mm | < ±0.025 mm | N/A | Tighter tolerances require machining; varies with size/geometry. |
표면 거칠기(Ra) | 6 µm to 15 µm | < 1.6 µm (typical) | < 0.1 µm | Lower Ra requires specific post-processing; supported areas rougher. |
최상의 대상 | General form, fit, non-critical faces | Mating surfaces, seals | Aesthetics, sealing, optics | Choose finish based on functional requirement. |
시트로 내보내기
Managing Expectations:
It is crucial for engineers and procurement managers to clearly define the tolerance and surface finish requirements for different features of the instrument case early in the process. * Identify Critical Features: Determine which dimensions and surfaces are functionally critical and require tighter control. * Specify Requirements Clearly: Use standard engineering drawings with appropriate GD&T (Geometric Dimensioning and Tolerancing) callouts. Specify Ra values for surfaces requiring controlled finishes. * Discuss with AM Provider: Collaborate with the additive manufacturing service provider (like Met3dp) to understand their specific capabilities and limitations. They can advise on achievable tolerances and finishes based on their equipment, processes, and experience with materials like 316L and Ti-6Al-4V. * Balance Cost and Requirements: Tighter tolerances and smoother finishes invariably add cost due to additional post-processing steps. Specify tighter controls only where functionally necessary.
By understanding the inherent capabilities and limitations of metal AM regarding precision and finish, and by planning for necessary post-processing steps, companies can successfully leverage the technology to produce high-quality, functional instrument cases that meet demanding specifications.
Beyond the Print: Essential Post-Processing Steps for Instrument Cases
The journey of a metal 3D printed instrument case doesn’t end when the printer stops. The “green” part, fresh off the build plate, requires a series of post-processing steps to transform it into a functional, finished component ready for assembly and deployment. These steps are critical for achieving the desired mechanical properties, dimensional accuracy, surface finish, and overall quality. Understanding these common procedures is essential for planning production timelines, estimating costs, and ensuring the final case meets all specifications.
1. Stress Relief / Heat Treatment: This is often one of the first and most crucial steps, especially for parts printed using high-energy processes like LPBF and for materials like Ti-6Al-4V. * Why it’s needed: The rapid heating and cooling cycles inherent in powder bed fusion processes create significant internal stresses within the printed part. These residual stresses can cause warping or distortion after the part is removed from the build plate, or even lead to cracking later in the part’s life, especially under load or thermal cycling. * 프로세스: Parts (often while still attached to the build plate) are heated in a controlled atmosphere furnace (vacuum or inert gas like argon) to a specific temperature below the material’s transformation point, held for a period, and then slowly cooled. This allows the material’s microstructure to relax, significantly reducing internal stresses. * Material Specifics: Heat treatment cycles (temperature, time, atmosphere) are specific to the alloy. 316L stainless steel typically requires stress relief, while Ti-6Al-4V almost always requires it to ensure dimensional stability and optimal mechanical properties. Other heat treatments like Hot Isostatic Pressing (HIP) might be used for critical applications to close internal voids (porosity) and further improve fatigue life, although this adds significant cost. HIP involves applying high pressure and temperature simultaneously.
2. Part Removal from Build Plate: Once stress relief is complete (if required), the printed case needs to be separated from the build plate it was fused to during printing. * 방법: This is typically done using wire EDM (Electrical Discharge Machining) or a band saw. Wire EDM provides a cleaner, more precise cut with minimal mechanical stress on the part, while sawing is faster but may require more finishing on the separated surface. * 고려 사항: The removal method can influence the need for subsequent finishing on the base surface of the case.
3. Support Structure Removal: As discussed under DfAM, support structures must be removed. * 방법: This is often done manually using pliers, cutters, grinders, or small chisels. For complex internal supports or high-volume production, CNC machining or EDM might be employed for more precise and automated removal. * 도전 과제: Support removal can be labor-intensive and time-consuming, especially for complex geometries or strong support connections. It inevitably leaves witness marks or burrs on the contact surfaces, which usually require further finishing. Designing supports for easy removal is a key DfAM consideration.
4. Cleaning and Powder Removal: Loose or partially sintered powder trapped within the case, especially in internal channels or complex features, must be removed. * 방법: Compressed air blowing, ultrasonic cleaning baths, and abrasive flow machining (extrude honing) can be used. Bead blasting or sand blasting also helps remove trapped powder while improving surface finish. * Importance: Incomplete powder removal can contaminate the final instrument assembly or interfere with functionality (e.g., blocking cooling channels). Thorough inspection is often required.
5. Machining for Critical Tolerances: As mentioned previously, if the instrument case requires high-precision features (e.g., sealing surfaces, bearing seats, alignment features, threaded holes) beyond the typical as-printed tolerances of AM, CNC machining is necessary. * 프로세스: The 3D printed case is fixtured onto a CNC milling machine or lathe, and specific surfaces are machined to the required dimensions and tolerances based on the engineering drawing. * DfAM Link: The design must include sufficient extra material (machining stock) on these surfaces to allow for clean-up during machining.
6. Surface Finishing: Depending on the application’s requirements for aesthetics, sealing, wear resistance, or friction, various surface finishing techniques may be applied after initial cleaning and support removal. * Abrasive Blasting: Common for a uniform matte finish (e.g., bead blasting). * 텀블링/진동 마감: Smooths surfaces and deburrs edges, good for batches. * 수동 연마/연마: For achieving specific local finishes or high-gloss appearances. * 전기 연마: Smooths and passivates stainless steel surfaces, enhancing corrosion resistance and cleanability – often used for medical or food-grade applications. * Anodizing (for Titanium): Can provide color, improved wear resistance, and enhanced biocompatibility for Ti-6Al-4V cases. * Coating (e.g., PVD, Cerakote): Applied for enhanced wear resistance, specific colors, chemical resistance, or electrical insulation/conductivity.
7. Inspection and Quality Control: Throughout the post-processing workflow, inspection is critical. * 방법: Visual inspection, dimensional measurement (calipers, CMM – Coordinate Measuring Machine), surface roughness testing, NDT (Non-Destructive Testing like CT scanning or X-ray) to check for internal defects or porosity, and pressure testing (if sealing is required). * Importance: Ensures the final instrument case meets all dimensional, material, and functional specifications before shipment or assembly. Companies like Met3dp, focused on mission-critical parts, integrate rigorous quality control throughout their manufacturing process.
Workflow Integration:
The sequence and selection of these post-processing steps depend heavily on the specific requirements of the instrument case. A typical workflow might look like this:
Print -> Stress Relief -> Part Removal -> Support Removal -> Basic Cleaning/Blasting -> (Optional: Machining) -> (Optional: Advanced Surface Finishing) -> Final Cleaning -> Inspection
Understanding this workflow helps procurement managers and engineers appreciate the full manufacturing process beyond just the printing stage. It highlights the importance of partnering with a full-service provider who has in-house capabilities or strong partnerships for managing these critical post-processing steps efficiently and cost-effectively. This integrated approach ensures that the final 3D printed instrument case delivers the required performance and quality.
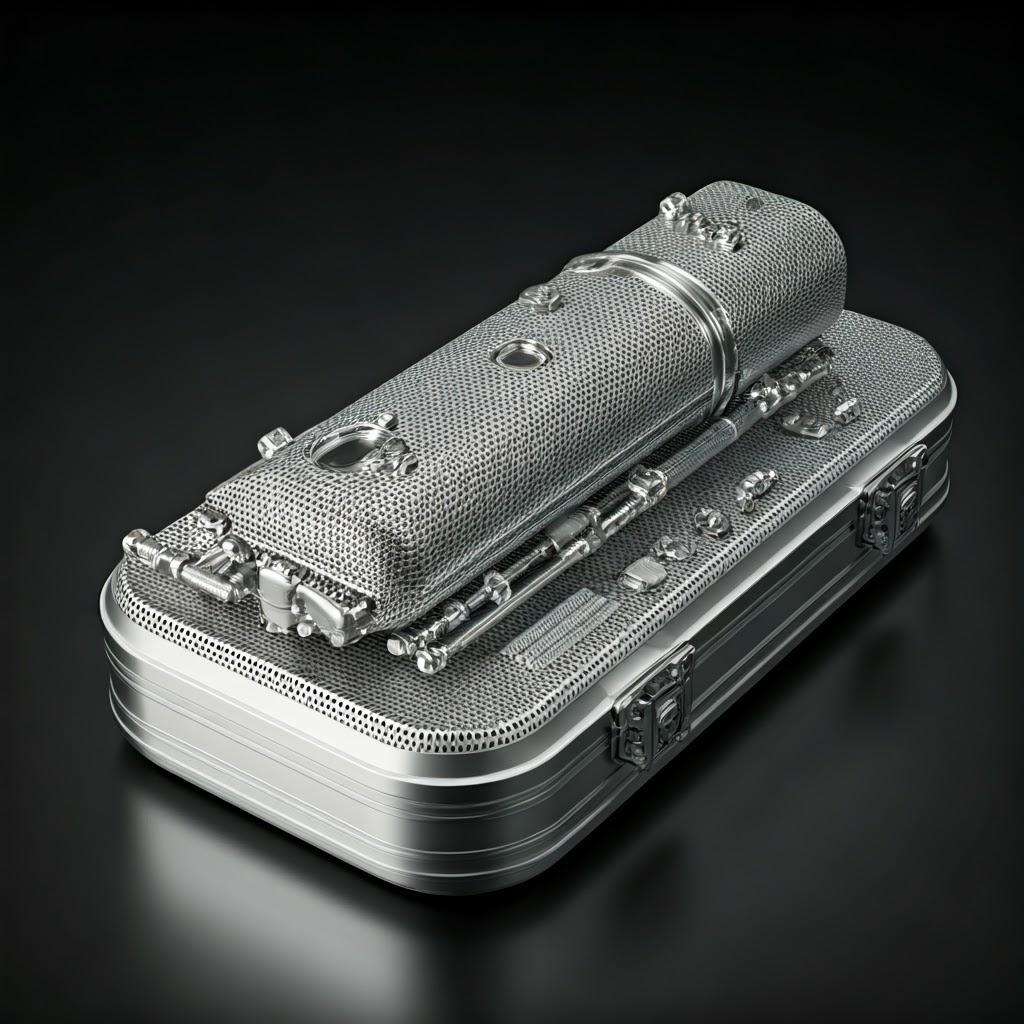
Navigating Potential Hurdles: Common Challenges in Printing Instrument Cases and Solutions
While metal 3D printing offers transformative advantages for producing instrument cases, it’s not without its challenges. Understanding potential issues during the printing and post-processing stages allows engineers and manufacturers to proactively address them through careful design (DfAM), process control, and material selection. Awareness of these hurdles helps set realistic expectations and ensures a smoother path to successful component production.
1. Warping and Distortion: * 도전: Due to the high temperatures involved and rapid heating/cooling cycles, significant thermal gradients develop during the build. This can cause internal stresses that lead to warping or distortion of the case, especially in large, flat sections or thin-walled structures, either during the print or after removal from the build plate. * Solutions: * 열 관리: Utilizing optimized scan strategies (e.g., island scanning, varied patterns) helps distribute heat more evenly. Proper machine calibration and environmental control are crucial. * 지원 구조: Well-designed supports anchor the part securely to the build plate, counteracting warping forces during the print. * 스트레스 해소: Performing a stress relief heat treatment cycle (often while the part is still attached to the build plate) is highly effective in minimizing residual stresses and preventing post-print distortion. * DfAM: Designing parts with features that mitigate stress build-up (e.g., avoiding large, flat unsupported areas, using ribbed structures instead of solid thick sections) can help. Strategic part orientation also plays a role. * Process Selection: EBM typically operates at higher temperatures, which can result in lower residual stress compared to LPBF for some geometries and materials like Ti-6Al-4V.
2. Residual Stress: * 도전: Closely related to warping, residual stress remains locked within the part even if visible distortion doesn’t occur. High residual stress can reduce the part’s fatigue life, affect dimensional accuracy over time, and potentially lead to cracking, especially under load or thermal cycling. * Solutions: * 스트레스 완화 열처리: This is the primary method for significantly reducing residual stress to acceptable levels. The specific cycle (temperature, time) depends on the alloy (e.g., 316L vs. Ti-6Al-4V). * Optimized Print Parameters: Fine-tuning laser/beam power, scan speed, and scan strategy can influence the thermal history and resulting stress state. * Build Plate Heating: Pre-heating the build plate (common in LPBF, inherent in EBM) reduces the thermal gradient between the deposited material and the underlying layers/plate, lowering stress.
3. Porosity: * 도전: Small voids or pores can form within the printed material due to incomplete fusion between layers, gas entrapment from the powder or atmosphere, or keyholing effects (where excessive energy density vaporizes material). Porosity can compromise the mechanical properties (strength, fatigue life) and leak-tightness of the instrument case. * Solutions: * Optimized Process Parameters: Careful control over laser/beam power, scan speed, layer thickness, and hatching overlap is critical to achieve full melting and fusion without vaporization. Parameter development is key for achieving >99.5% density. * High-Quality Powder: Using spherical powders with consistent particle size distribution and low internal porosity, like those produced using Met3dp’s advanced gas atomization or PREP technologies, is crucial. Powders with poor flowability or irregular shapes can lead to uneven powder bed density and porosity. Ensuring powder is dry and handled correctly prevents moisture-related porosity. * Controlled Atmosphere: Maintaining a high-purity inert gas atmosphere (Argon or Nitrogen for LPBF) or vacuum (EBM) prevents oxidation and gas entrapment. * 열간 등방성 프레싱(HIP): For critical applications demanding near-zero porosity, HIP post-processing can effectively close internal voids, achieving full theoretical density.
4. Support Removal Difficulties and Surface Quality: * 도전: Supports, while necessary, can be difficult and time-consuming to remove, especially from complex internal geometries. Removal processes invariably leave witness marks or rougher surfaces where the supports were attached, potentially impacting sealing or aesthetics. * Solutions: * DfAM for Support Minimization: Designing parts with self-supporting angles (>45 degrees) and choosing optimal build orientations significantly reduces support requirements. * Smart Support Design: Using specialized support structures (e.g., thin contact points, break-away structures, soluble supports in some polymer processes, though less common in metal) can ease removal. Collaboration with the AM service provider on support strategy is vital. * 접근성: Designing access points for tool reach if internal supports are unavoidable. * 후처리: Allocating sufficient time and resources for careful support removal and subsequent surface finishing (blasting, machining, polishing) in affected areas. Specify surface finish requirements clearly on drawings.
5. Achieving Tight Tolerances and Sealing: * 도전: As-printed tolerances may not be sufficient for features requiring high precision, such as O-ring grooves, mating flanges, or bearing fits. Ensuring a reliable seal (e.g., IP67 rating) requires precise dimensions and smooth surface finishes on sealing faces. * Solutions: * Post-Process Machining: Designate critical features for CNC machining and include appropriate stock material in the AM design. This is the most reliable way to achieve tight tolerances (< ±0.05 mm). * 표면 마감: Employ appropriate finishing techniques (machining, grinding, polishing, electropolishing) on sealing surfaces to achieve the required smoothness (typically Ra < 1.6 µm or better). * Seal Design: Select appropriate seal types (O-rings, gaskets) compatible with the achievable tolerances and surface finishes. Consider wider O-ring grooves to accommodate slightly larger tolerance ranges if machining is not feasible. * Leak Testing: Implement rigorous leak testing protocols as part of the quality control process to validate seal integrity.
6. Powder Removal from Internal Channels: * 도전: Complex internal channels designed for cooling or wiring can trap loose or partially sintered powder, which can be difficult to remove completely. * Solutions: * DfAM: Design channels with sufficient diameter, smooth bends (avoiding sharp corners), and potentially multiple access ports for cleaning. Avoid dead-end cavities where powder can become permanently trapped. * Cleaning Methods: Utilize thorough cleaning procedures like high-pressure air/liquid flushing, ultrasonic cleaning, or abrasive flow machining. * Inspection: Use borescopes or CT scanning (for critical parts) to verify complete powder removal from internal passages.
Addressing these challenges requires a combination of robust design practices, meticulous process control during printing, appropriate material selection and handling, and well-planned post-processing steps. Partnering with an experienced additive manufacturing provider like Met3dp, who understands these potential hurdles and has established processes and quality systems to mitigate them, is crucial for successfully producing high-quality, reliable 3D printed instrument cases for demanding B2B applications. Their expertise spans the entire workflow, from design consultation to finished part validation.
Selecting Your Partner: How to Choose the Right Metal 3D Printing Service Provider for Instrument Cases
Choosing the right manufacturing partner is as critical as perfecting the design itself, especially when dealing with advanced technologies like metal additive manufacturing for precision instrument cases. The quality, reliability, cost-effectiveness, and timely delivery of your components hinge on the capabilities and expertise of your chosen service provider. For procurement managers sourcing B2B manufacturing services, engineers seeking expert AM consultation, or companies looking for a reliable industrial supplier of custom metal enclosures, evaluating potential partners requires a thorough assessment of several key factors.
Key Criteria for Evaluating Metal AM Service Providers:
1. Technical Expertise and Experience: * 프로세스 지식: Does the provider have deep expertise in the specific AM process (e.g., LPBF, EBM) best suited for your instrument case design and material? Do they understand the nuances of parameter settings, thermal management, and process control? * Materials Science: What is their level of understanding regarding the metallurgy of the materials you intend to use (e.g., 316L, Ti-6Al-4V)? Can they advise on material selection, expected properties, and necessary heat treatments? Providers like Met3dp, who not only use but also manufacture high-performance metal powders, possess an inherent advantage in material science expertise. * DfAM Capabilities: Can they offer Design for Additive Manufacturing support? Do they have engineers who can collaborate with your team to optimize the case design for printability, performance, and cost-effectiveness? * 업계 경험: Have they successfully produced parts for your specific industry (aerospace, medical, automotive, industrial)? Do they understand the relevant standards and requirements?
2. Equipment and Technology: * Printer Fleet: What types of metal AM systems do they operate? Do they have machines suitable for your required part size, material, and precision level? Look for providers with well-maintained, industrial-grade equipment. Met3dp highlights its industry-leading print volume, accuracy, and reliability, suggesting investment in high-caliber machinery potentially including advanced SEBM printers. * 파우더 처리: How do they manage metal powders? Proper storage, handling, sieving, and traceability are crucial for maintaining powder quality and ensuring consistent part properties. Companies manufacturing their own powders often have rigorous internal controls. * Post-Processing Capabilities: Do they offer comprehensive in-house post-processing services (stress relief, machining, surface finishing, inspection)? Or do they rely on external subcontractors? In-house capabilities generally offer better control over quality, lead time, and cost.
3. Material Portfolio and Quality: * Range of Materials: Do they offer the specific alloys you need (316L, Ti-6Al-4V)? Do they also work with other relevant metals that might offer alternative solutions (e.g., Aluminum alloys, Nickel superalloys, Copper alloys)? Met3dp boasts a portfolio including standard alloys plus innovative ones like TiNi, TiTa, TiAl, TiNbZr, and CoCrMo. * Powder Quality Control: How do they ensure the quality and consistency of the metal powders used? Do they provide material certifications tracing powder batches back to their source? Providers using high-sphericity powders from advanced atomization processes (like Gas Atomization or PREP mentioned by Met3dp) typically yield higher quality parts.
4. Quality Management System and Certifications: * QMS: Does the provider operate under a robust Quality Management System (QMS)? * 인증: Are they certified to relevant industry standards? ISO 9001 (General Quality Management) is a minimum expectation. For specific industries, look for: * AS9100 (Aerospace) * ISO 13485 (Medical Devices) * IATF 16949 (Automotive) * 검사 기능: What metrology and inspection equipment do they possess (CMMs, scanners, surface profilometers, NDT equipment)? How do they document and report quality data?
5. Capacity and Lead Time: * 생산 능력: Can they handle your required production volume, whether it’s prototypes, low-volume series, or potentially higher volumes? Do they have sufficient machine capacity to meet your timelines? * Quoted Lead Times: Are their quoted lead times realistic and competitive? How reliable are they at meeting deadlines? Understand their process for scheduling and managing production flow.
6. Communication and Support: * 응답성: Are they responsive to inquiries and requests for quotes? * 기술 지원: Is knowledgeable technical staff readily available to discuss design considerations, material options, and project progress? * 투명성: Are they transparent about their processes, capabilities, and potential challenges?
7. Cost and Value: * Pricing Structure: Is their pricing clear and competitive? Do they offer volume discounts or specific pricing models for B2B wholesale or long-term supply agreements? * Total Value: Consider the overall value proposition, not just the per-part price. Factor in quality, reliability, expertise, lead time, and support. The cheapest option may not offer the best long-term value if it compromises quality or delivery.
Why Consider Met3dp?
Based on their stated capabilities, Met3dp positions itself as a strong contender, particularly for companies seeking a partner with deep materials expertise and a focus on high-quality industrial applications.
- Integrated Solution: They offer a comprehensive approach, spanning advanced SEBM printers, high-performance metal powders manufactured in-house using leading technologies (Gas Atomization, PREP), and application development services.
- Material Focus: Their specialization in metal powders, including standard and innovative alloys, suggests a strong foundation in materials science crucial for demanding applications.
- Quality Emphasis: Their focus on powder sphericity, flowability, and printer accuracy/reliability indicates a commitment to producing dense, high-quality parts suitable for mission-critical applications in aerospace, medical, and automotive sectors.
- 전문성: Decades of collective expertise in metal AM provides a solid base for technical support and collaboration.
When selecting your partner, conducting thorough due diligence is essential. Request quotes, ask detailed questions about their processes and quality control, consider a pilot project or site visit if feasible, and learn more 우리에 대하여 pages on potential suppliers’ websites to understand their company culture and values. Choosing the right partner is an investment in the success of your instrument case project.
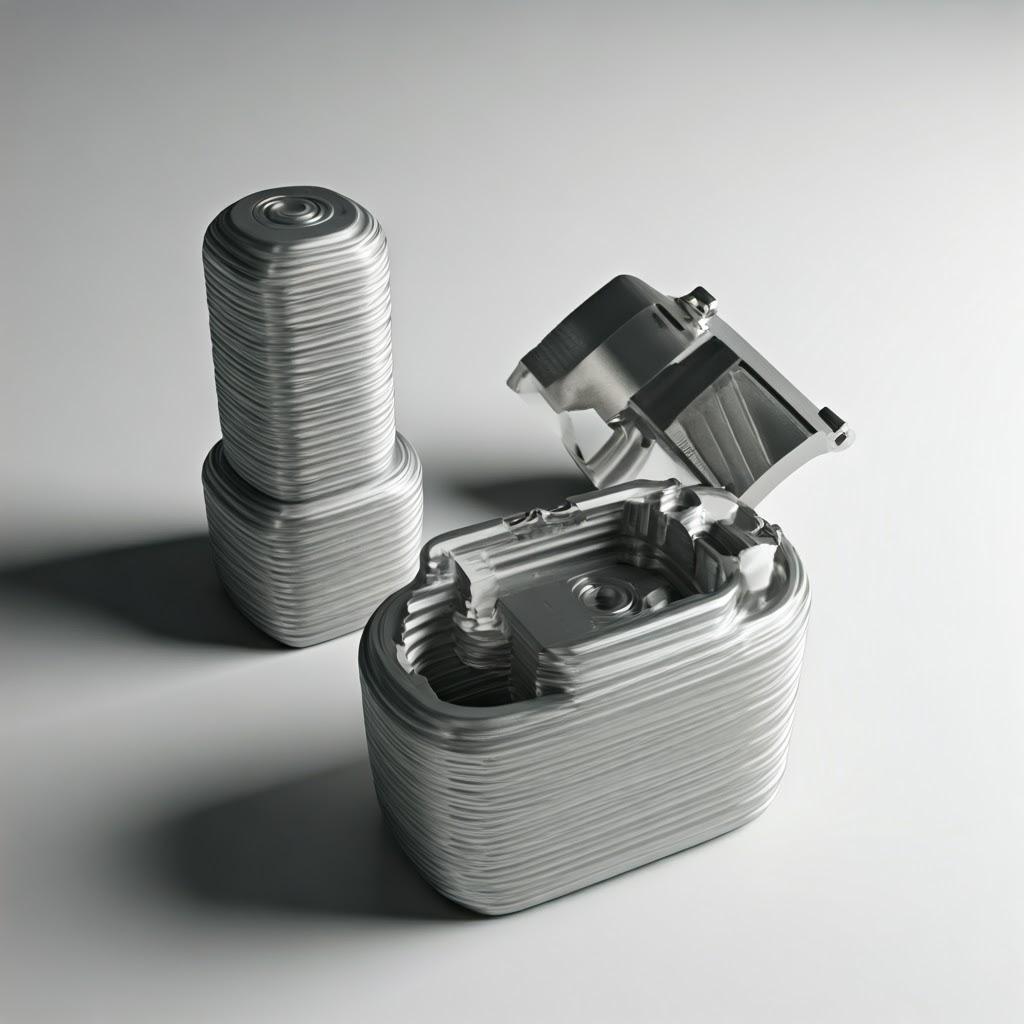
Understanding the Investment: Cost Factors and Lead Times for 3D Printed Instrument Cases
One of the primary considerations for any manufacturing project is the cost and the time it takes to receive the finished parts. Metal additive manufacturing, while offering unique advantages, has its own specific cost drivers and lead time components that differ from traditional methods. Understanding these factors allows engineers and procurement managers to budget effectively, optimize designs for cost-effectiveness, and plan project timelines realistically when sourcing 3D printed metal enclosures, custom housings또는 wholesale instrument cases.
Key Cost Factors:
1. Material Cost: * 파우더 가격: The raw material powder is a significant cost component. Prices vary greatly depending on the alloy: * 316L 스테인리스 스틸: Relatively cost-effective. * Ti-6Al-4V Titanium Alloy: Significantly more expensive than 316L due to raw material costs and processing difficulty. * Other Alloys (Inconel, Copper, etc.): Can range from moderate to very high cost. * 볼륨: The total volume of material used directly impacts cost. This includes the part itself and any support structures.
2. Print Time (Machine Utilization): * Build Height & Volume: The taller the part (in the build orientation) and the larger its overall volume, the longer it takes to print, directly increasing machine time cost. Industrial metal AM machines are expensive assets, and their operating time is a major cost factor. * 복잡성: While AM handles complexity well, highly intricate features or numerous thin walls can sometimes slow down the scanning process compared to simpler, solid sections covering the same area. * 중첩: Service providers often print multiple parts simultaneously on a single build plate (nesting) to maximize machine utilization. How efficiently your part can be nested with others can influence per-part cost, especially for smaller components.
3. Support Structures: * 볼륨: Supports consume material and add print time. * Removal Labor: Removing supports requires manual labor or additional processing steps, adding to the cost. Designs requiring extensive or difficult-to-remove supports will be more expensive. DfAM principles focused on minimizing supports directly reduce cost.
4. Post-Processing: * Heat Treatment (Stress Relief/HIP): Furnace time, energy consumption, and controlled atmosphere requirements add cost. HIP is a particularly expensive step reserved for highly critical applications. * 가공: CNC machining time for critical tolerances adds significant cost due to machine setup, operation, and programming. The more features requiring machining, the higher the cost. * 표면 마감: Each finishing step (blasting, tumbling, polishing, coating) adds labor and/or machine time costs. High-gloss polishing or specialized coatings can be particularly costly. * Inspection: Basic dimensional checks are standard, but advanced inspection like CMM or NDT adds cost.
5. Design Complexity & Optimization: * 토폴로지 최적화: While potentially reducing material volume (saving material cost and print time), the complex geometries generated may sometimes require more extensive support structures or more complex post-processing, creating a trade-off. * 파트 통합: Consolidating multiple parts into one print can reduce assembly costs but may increase the complexity and print time of the single AM part. A careful cost-benefit analysis is needed.
6. Labor and Overheads: * Setup & Programming: Preparing the build file, setting up the machine, and programming post-processing steps require skilled labor. * 품질 관리: Labor involved in inspection and documentation. * General Overheads: Facility costs, machine maintenance, R&D, etc., are factored into pricing.
7. Order Volume (Quantity): * 규모의 경제: While AM is cost-effective for prototypes and low volumes due to the lack of tooling, some economies of scale exist. Larger batch sizes allow for better machine utilization (nesting), more efficient post-processing setups, and potential volume discounts on powder. B2B wholesale pricing for larger quantities will typically be lower per part than single-piece prototype pricing.
Lead Time Components:
Lead time is the total time from order placement to receiving the finished parts. It’s not just the print time.
1. Quoting and Order Processing: Initial communication, design review (for manufacturability), quote generation, and order confirmation take time (typically 1-5 business days). 2. Queue Time: Your job needs to be scheduled into the production plan. Depending on the service provider’s backlog and machine availability, this can range from a few days to several weeks. 3. Build Preparation: Preparing the build file, nesting parts on the build plate, and setting up the machine (loading powder, preparing the plate) takes several hours. 4. Print Time: This can vary significantly based on part size, height, and complexity. Small cases might print in 10-20 hours, while large or numerous nested cases could take several days (48-100+ hours). 5. Cooling: After printing, the build chamber needs to cool down before the build plate can be safely removed (several hours). 6. Post-Processing: This often takes a significant portion of the lead time: * Stress Relief/Heat Treatment: Can take 12-48 hours (including furnace time and cooling). * Part/Support Removal & Cleaning: Highly variable, from hours to days depending on complexity and quantity. * Machining & Finishing: Depends heavily on the extent required, potentially adding several days to weeks for complex requirements or high volumes. * Inspection: Adds time depending on the level of inspection needed. 7. Shipping: Transit time to your facility (1 day to a week or more, depending on location and shipping method).
Typical Lead Times:
- Prototypes (Simple, minimal post-processing): 1-3주
- Prototypes (Complex, requiring machining/finishing): 3~6주
- Low-Volume Production (Depending on complexity & post-processing): 4-8 weeks or more
Lead Time Estimation Table:
스테이지 | Estimated Time Range | 참고 |
---|---|---|
Quoting & Order | 1-5 Business Days | Depends on complexity and responsiveness. |
Queue Time | 2 Business Days – 3 Weeks | Highly variable based on provider backlog. |
Build Prep & Print | 1 – 5+ Days | Depends on part size, height, quantity. |
냉각 | 4 – 12 Hours | Standard machine cycle time. |
포스트 프로세싱 | 2 Business Days – 3+ Weeks | Major variable. Depends heavily on requirements. |
해운 | 1 – 7+ Business Days | Depends on location and method. |
Total Estimated Lead Time | ~2 Weeks – 8+ Weeks | Highly dependent on specifics. |
시트로 내보내기
Managing Cost and Lead Time:
- Optimize Design (DfAM): Minimize supports, reduce unnecessary material (topology optimization), consider post-processing needs early.
- Clear Specifications: Provide clear drawings and requirements to avoid delays and misinterpretations. Define critical vs. non-critical tolerances and finishes.
- 재료 선택: Select the most cost-effective material that meets requirements (e.g., 316L if Ti-6Al-4V’s properties aren’t essential).
- Communicate Early: Discuss timelines and cost drivers with your AM provider early in the project.
- Volume Planning: Discuss potential volume discounts or long-term agreements for ongoing B2B supply needs.
By understanding these cost and lead time dynamics, companies can make informed decisions, optimize their projects for efficiency, and leverage the benefits of metal AM for instrument cases effectively.
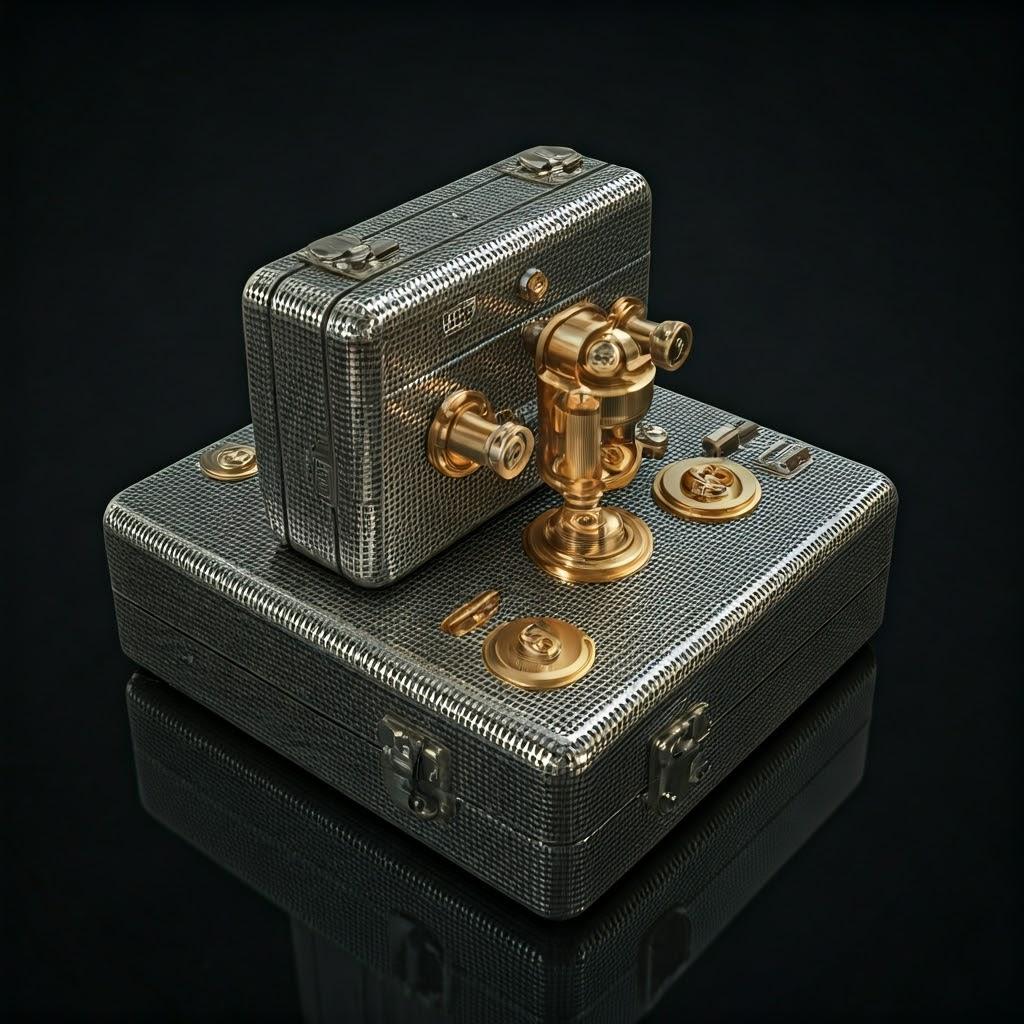
Frequently Asked Questions (FAQ) about 3D Printed Metal Instrument Cases
As engineers and procurement managers explore the use of metal additive manufacturing for instrument cases, several common questions arise. Here are answers to some frequently asked questions:
1. Can 3D printed metal instrument cases achieve specific IP (Ingress Protection) ratings like IP67?
- 답변: Yes, achieving high IP ratings like IP67 (dust-tight and resistant to immersion up to 1 meter) or even IP68 is definitely possible with 3D printed metal cases, but it requires careful design and manufacturing considerations. It’s not guaranteed by simply printing the case.
- 디자인: The case must be designed with appropriate sealing features, typically grooves for O-rings or channels for form-in-place gaskets. Lid and body interfaces, cable glands, and connector openings are critical areas. DfAM principles should ensure these features are printable and functional.
- Tolerances: Achieving the precise dimensions required for seal grooves often necessitates post-process CNC machining of the sealing surfaces to ensure proper compression of the O-ring or gasket. As-printed tolerances might not be sufficient for reliable high-IP sealing.
- 표면 마감: The surface finish of the sealing faces is crucial. A smooth, uniform surface (typically Ra < 1.6 µm, often achieved via machining or potentially electropolishing for 316L) is needed to prevent leak paths. As-printed surfaces are generally too rough for reliable high-IP sealing without secondary finishing.
- Material Integrity: The printed material must be dense and free from significant porosity that could create leak paths through the case walls themselves. Using high-quality powders and optimized print parameters, potentially combined with HIP for critical applications, ensures material integrity. Providers like Met3dp, focusing on high-density parts through quality powders and processes, are well-positioned to achieve this.
- Assembly: Proper selection and installation of seals, connectors, and fasteners during assembly are critical.
- 테스트: Rigorous IP testing according to the relevant standards (IEC 60529) is essential to validate the final assembled case’s performance.
- In summary: While metal AM provides the means to create the complex geometry, achieving a certified IP rating relies heavily on DfAM focused on sealing, post-process machining/finishing of sealing surfaces, and proper assembly/testing. Discuss your specific IP rating requirements with your AM service provider early on.
2. Are 3D printed 316L stainless steel or Ti-6Al-4V cases compatible with common sterilization methods used in the medical industry?
- 답변: Yes, both 316L stainless steel and Ti-6Al-4V titanium alloy, when processed correctly via additive manufacturing, are generally compatible with common medical sterilization methods.
- Autoclaving (Steam Sterilization): This is the most common method (typically 121°C or 134°C saturated steam under pressure). Both 316L and Ti-6Al-4V exhibit excellent resistance to steam sterilization and can withstand numerous cycles without significant degradation of their mechanical properties or corrosion resistance. The low carbon content (“L”) in 316L is particularly important for maintaining corrosion resistance after exposure to elevated temperatures.
- Gamma Radiation: Both materials show good stability when exposed to typical doses of gamma radiation used for sterilizing medical devices. There is generally no significant impact on their bulk mechanical properties, although some minor surface effects or discoloration could potentially occur at very high doses over long periods.
- Ethylene Oxide (EtO): EtO gas sterilization is also compatible with both 316L and Ti-6Al-4V. The materials are resistant to the chemical action of EtO gas at typical sterilization temperatures and concentrations. Proper aeration after the cycle is crucial to remove residual EtO.
- Vaporized Hydrogen Peroxide (VHP) / Plasma Sterilization: These lower-temperature methods are also generally compatible with both alloys.
- Surface Finish Consideration: While the bulk materials are compatible, the surface finish of the AM part can influence cleanability. Rougher as-printed surfaces might be harder to clean thoroughly compared to smoother, polished, or electropolished surfaces. For medical applications requiring high levels of cleanliness and sterilizability, post-processing to achieve smoother surfaces is often recommended. Electropolishing 316L can further enhance its cleanability and passive layer stability.
- Validation: As with any medical device component, it’s essential to validate the sterilization process for the specific 3D printed case design and material to ensure sterility assurance levels are met according to regulatory requirements (e.g., ISO 17665 for steam, ISO 11135 for EtO, ISO 14937 general).
3. How does the cost of a 3D printed metal instrument case compare to one made via CNC machining, especially for low-to-medium volumes?
- 답변: The cost comparison between metal AM and CNC machining for instrument cases is highly dependent on geometry complexity, material, and volume. There’s a crossover point where one method becomes more economical than the other.
- Low Volume (Prototypes, 1-10 units):
- Simple Geometry: CNC machining from stock material might be cheaper if the design is relatively simple (e.g., a basic milled box) as setup time is minimal and material removal is straightforward.
- 복소 기하학: Metal AM is often significantly more cost-effective for highly complex geometries (internal features, organic shapes, consolidated parts). Machining such features from a solid block would involve extensive machine time, complex setups (e.g., 5-axis machining), significant material waste, and potentially multiple operations, driving costs up considerably. AM avoids tooling costs and handles complexity efficiently.
- Medium Volume (10s to low 100s units):
- Simple Geometry: CNC machining often becomes more cost-effective as programming and setup costs are amortized over more units, and machining cycle times for simple parts can be fast.
- 복소 기하학: Metal AM often remains competitive or even cheaper in this range for highly complex parts where machining times and material waste remain high, or where part consolidation benefits are significant. The lack of tooling costs for AM is still an advantage over methods like casting.
- High Volume (100s to 1000s+ units):
- CNC machining or traditional methods like die casting (if geometry allows, despite high initial tooling cost) usually become more economical for simpler to moderately complex parts due to optimized cycle times and established high-throughput processes.
- Metal AM is generally less competitive for very high volumes of simple parts but might still be considered for highly complex or customized components where its unique capabilities provide ongoing value (e.g., performance improvements through topology optimization).
- Other Factors:
- 재료 낭비: Machining subtracts material, often leading to significant waste, especially for complex parts starting from large billets. AM is additive, using material more efficiently.
- 리드 타임: AM can often deliver initial complex prototypes faster than machining complex parts from scratch or waiting for casting tooling.
- 결론: For typical instrument cases involving moderate to high complexity, internal features, or the need for customization/rapid iteration, metal AM is often more cost-effective at prototype and low-volume stages (1-50 units approximately). For simpler designs or higher volumes, CNC machining likely becomes more economical. A detailed quote comparison based on the specific geometry and quantity is always recommended.
- Low Volume (Prototypes, 1-10 units):
Conclusion: Securing Your Sensitive Instruments with Advanced Metal 3D Printing
In today’s demanding technological landscape, ensuring the safety, reliability, and optimal performance of sensitive instruments is non-negotiable. The protective case is the first line of defense against environmental hazards and operational stresses. While traditional manufacturing methods have served well, metal additive manufacturing has emerged as a powerful and versatile solution, enabling the creation of precision instrument cases with capabilities previously unattainable.
Leveraging materials like robust 316L 스테인리스 스틸 for its exceptional corrosion resistance and sterilizability, or high-performance Ti-6Al-4V 티타늄 합금 for its unparalleled strength-to-weight ratio, metal 3D printing allows engineers to design and produce enclosures perfectly tailored to the unique demands of industries ranging from aerospace and medical technology to automotive and industrial automation. The key advantages are compelling:
- 독보적인 디자인 자유도: Create complex internal structures for cooling or mounting, consolidate multiple assembly components into a single part, and achieve optimized, lightweight designs through topology optimization – features impossible or impractical with conventional methods.
- Rapid Customization & Prototyping: Quickly iterate designs, produce custom-fit enclosures for specialized equipment, and move from concept to functional part faster, accelerating product development cycles without prohibitive tooling costs.
- Enhanced Performance & Protection: Manufacture cases from high-strength, corrosion-resistant alloys, ensuring superior durability and longevity even in harsh environments. Optimized designs can improve thermal management and structural integrity.
- Supply Chain Efficiency: On-demand production, part consolidation, and reduced material waste contribute to a more agile and potentially cost-effective supply chain, particularly for low-to-medium volume B2B requirements.
Successfully navigating the world of metal AM requires careful consideration of Design for Additive Manufacturing (DfAM) principles, understanding achievable tolerances and finishes, planning for necessary post-processing steps, and mitigating potential challenges like warping or porosity. Most importantly, it requires choosing the right manufacturing partner – one with proven expertise, advanced equipment, robust quality systems, and a commitment to collaboration.
Met3dp, with its foundation in high-performance metal powder manufacturing using industry-leading technologies and its focus on providing comprehensive additive manufacturing solutions including advanced printing systems, stands as a knowledgeable and capable partner. Their expertise in materials like 316L, Ti-6Al-4V, and other specialized alloys, combined with their commitment to accuracy and reliability, makes them well-suited to tackle the challenges of producing mission-critical instrument cases for demanding applications.
Whether you are an engineer designing the next generation of medical devices, an aerospace procurement manager sourcing lightweight avionics enclosures, or an industrial automation specialist needing rugged sensor housings, metal additive manufacturing offers a pathway to superior performance and protection.
Ready to explore how metal 3D printing can revolutionize your instrument case design and production? 방문하다 Met3dp to learn more about their capabilities and contact their team to discuss your specific project requirements. Embrace the future of manufacturing and secure your sensitive instruments with the precision and performance of additive manufacturing.
공유
중국 칭다오에 본사를 둔 선도적인 적층 제조 솔루션 제공업체인 MET3DP Technology Co. 당사는 산업용 3D 프린팅 장비와 고성능 금속 분말을 전문으로 합니다.
관련 기사
Met3DP 소개
최근 업데이트
제품
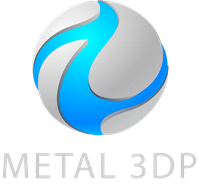
3D 프린팅 및 적층 제조용 금속 분말