레이저 기반 파우더 베드 융합
목차
레이저 기반 파우더 베드 융합 (PBF)는 제조 산업에 혁명을 일으키고 있으며, 전례 없는 정밀성, 효율성, 유연성을 제공합니다. 하지만 정확히 무엇이고, 왜 관심을 가져야 할까요? 이 혁신적인 기술을 깊이 파고들어 그 복잡성, 응용 분야, 그리고 생산 세계에서 게임 체인저가 되고 있는 이유를 살펴보겠습니다.
레이저 기반 파우더 베드 융합 개요
레이저 기반 파우더 베드 퓨전은 고출력 레이저를 사용하여 금속 파우더 입자를 층층이 융합하여 견고한 3차원 물체를 만드는 적층 제조 공정입니다. 3D 프린팅의 범주에 속하는 기술이지만 고품질 금속 구성 요소를 생산하도록 특별히 맞춤 제작되었습니다.
레이저 기반 파우더 베드 퓨전의 주요 특징:
- 정확성: 높은 정확도로 복잡한 세부 사항과 복잡한 기하학적 모양을 구현합니다.
- 재료 효율성: 필요한 양의 분말만 사용하여 낭비를 최소화합니다.
- 사용자 지정: 특정 요구 사항에 맞는 맞춤형 부품을 만들 수 있습니다.
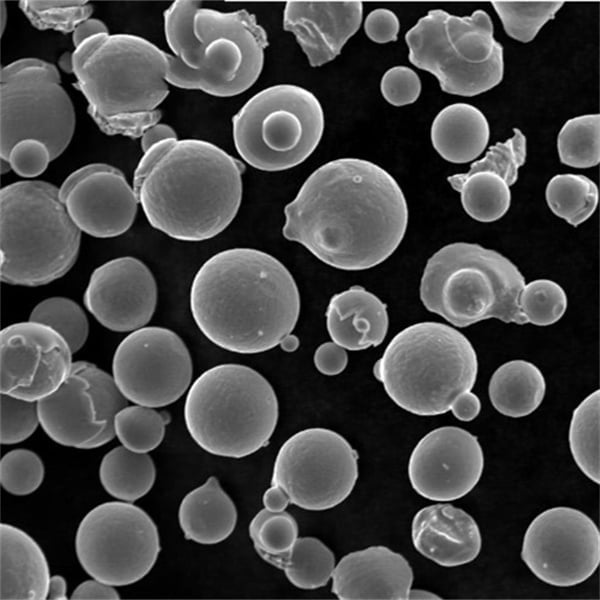
금속 분말의 종류 레이저 기반 파우더 베드 융합
올바른 금속 분말을 선택하는 것은 PBF 공정의 성공에 매우 중요합니다. 다음은 PBF에 사용되는 몇 가지 인기 있는 금속 분말과 그에 대한 설명입니다.
금속분말 | 설명 |
---|---|
티타늄 Ti-6Al-4V | 높은 강도 대 중량 비율, 뛰어난 내식성, 생체 적합성으로 유명하여 항공우주, 의료용 임플란트, 자동차 산업에 이상적입니다. |
알루미늄 AlSi10Mg | 가벼운 무게와 우수한 기계적 강도, 열 전도성을 결합하여 자동차 및 항공우주 부품에 적합합니다. |
스테인리스 스틸 316L | 뛰어난 내식성, 강도, 연성을 갖추고 있어 의료, 해양 및 화학 처리 분야에서 널리 사용됩니다. |
인코넬 718 | 고온 내구성과 인장 강도가 좋은 니켈-크롬 초합금으로, 항공우주, 가스터빈, 원자로 등에 사용됩니다. |
코발트크롬 | 높은 내마모성, 생체적합성, 강도를 지녔으며 치과 및 정형외과 임플란트와 항공우주 응용 분야에 일반적으로 사용됩니다. |
마레이징 스틸 (1.2709) | 열처리 후 뛰어난 강도와 인성으로 유명하며, 공구, 항공우주 및 고응력 부품에 사용됩니다. |
구리(Cu) | 뛰어난 열 및 전기 전도성으로 전기 부품 및 열교환기에 적합합니다. |
니켈 합금 (625) | 우수한 내식성 및 내산화성, 높은 강도를 제공하며 해양, 화학, 항공우주 산업에 사용됩니다. |
공구강(H13) | 경도, 강도, 내마모성이 뛰어나 금형 제작, 다이캐스팅, 공구 제작에 자주 사용됩니다. |
티타늄(Ti-5Al-2.5Sn) | 우수한 고온 성능과 크리프 저항성을 갖추고 있어 항공우주 및 고성능 자동차 분야에 활용됩니다. |
금속 분말의 특성 및 특성
금속분말 | 구성 | 속성 | 애플리케이션 |
---|---|---|---|
티타늄 Ti-6Al-4V | Ti, Al, V | 높은 중량 대비 강도, 내식성, 생체 적합성 | 항공우주, 의료용 임플란트, 자동차 |
알루미늄 AlSi10Mg | Al, Si, Mg | 가볍고, 기계적 강도가 좋으며, 열전도도가 좋다 | 자동차, 항공우주 |
스테인리스 스틸 316L | Fe, Cr, Ni, Mo | 내식성, 강도, 연성 | 의료, 해양, 화학 가공 |
인코넬 718 | Ni, Cr, Fe, Nb, Mo, Ti | 고온 저항성, 인장 강도 | 항공우주, 가스터빈, 원자로 |
코발트크롬 | Co, Cr, Mo | 내마모성, 생체 적합성, 강도 | 치과, 정형외과 임플란트, 항공우주 |
마레이징 스틸 (1.2709) | Fe, Ni, Co, Mo | 강도, 열처리 후 인성 | 공구, 항공우주, 고응력 부품 |
구리(Cu) | Cu | 열 및 전기 전도성 | 전기 부품, 열교환기 |
니켈 합금 (625) | Ni, Cr, Mo, Nb | 부식 및 산화 저항성, 고강도 | 해양, 화학, 항공우주 |
공구강(H13) | 철, 크롬, 몰리브덴, 규소, 바나듐 | 경도, 강도, 내마모성 | 금형 제작, 다이캐스팅, 툴링 |
티타늄(Ti-5Al-2.5Sn) | 티탄, 알루미늄, 주석 | 고온 성능, 크립 저항성 | 항공우주, 고성능 자동차 |
레이저 기반 파우더 베드 퓨전의 응용 분야
레이저 기반 PBF는 다재다능함과 정밀성 덕분에 다양한 산업에서 큰 인기를 끌고 있습니다. 레이저 기반 PBF가 어디에 적용되고 왜 그렇게 효과적인지 살펴보겠습니다.
산업 | 애플리케이션 |
---|---|
항공우주 | 엔진 부품, 구조 부품, 경량 브라켓 |
의료 | 맞춤형 임플란트, 보철물, 수술 기구 |
자동차 | 가벼운 구성 요소, 맞춤형 부품, 성능 향상 |
툴링 | 사출금형, 다이캐스팅금형, 맞춤형 툴링 |
보석 | 맞춤형 디자인, 복잡한 패턴, 신속한 프로토타입 제작 |
에너지 | 터빈 블레이드, 열교환기, 연료 노즐 |
전자 제품 | 방열판, 전기 부품, 맞춤형 인클로저 |
치과 | 크라운, 브릿지, 치과 임플란트 |
해양 | 부식 방지 부품, 경량 구성 요소 |
아키텍처 | 맞춤형 고정물, 디자인 프로토타입 |
장점 레이저 기반 파우더 베드 융합
레이저 기반 파우더 베드 퓨전이 왜 이렇게 많은 주목을 받고 있을까요? 몇 가지 설득력 있는 이유가 있습니다.
- 정밀도와 세부 사항: 기존 제조 방법으로는 생산하기 어려운 복잡하고 정교한 기하학적 형태를 생산할 수 있습니다.
- 재료 효율성: 필요한 양의 금속 분말만을 사용하여 폐기물을 최소화합니다.
- 사용자 지정: 특정 요구 사항에 맞는 맞춤형 부품을 쉽게 제작할 수 있습니다.
- 속도와 효율성: 기존 방식에 비해 생산 시간이 더 빠릅니다.
- 강도와 내구성: 우수한 기계적 성질을 가진 부품을 생산합니다.
레이저 기반 파우더 베드 퓨전의 단점
많은 이점에도 불구하고 레이저 기반 PBF에는 몇 가지 제한 사항도 있습니다.
- 비용: 장비 및 자재에 대한 초기 투자 비용이 높습니다.
- 복잡성: 효과적으로 운영하려면 전문적인 지식과 기술이 필요합니다.
- 크기 제한: 일반적으로 빌드 챔버 크기로 인해 작은 부품으로 제한됩니다.
- 표면 마감: 원하는 표면 품질을 얻으려면 후처리가 필요할 수 있습니다.
사양, 크기, 등급 및 표준
금속분말 | 사양 | 크기 | 성적 | 표준 |
---|---|---|---|---|
티타늄 Ti-6Al-4V | ASTM B348, ASTM F1472 | 15-45 µm, 45-106 µm | 5학년 | ISO 5832-3, AMS 4928 |
알루미늄 AlSi10Mg | EN AC-43400 | 20~63마이크로미터, 45~90마이크로미터 | ||
스테인리스 스틸 316L | ASTM A276, ASTM F138 | 15-45 µm, 45-106 µm | ISO 5832-1 | |
인코넬 718 | AMS 5662, ASTM B637 | 15-45 µm, 45-106 µm | ||
코발트크롬 | ASTM F75, ASTM F1537 | 15-45 µm, 45-106 µm | ||
마레이징 스틸 (1.2709) | DIN 1.2709, AMS 6514 | 15-45 µm, 45-106 µm | ||
구리(Cu) | ASTM B170 | 20~63마이크로미터, 45~90마이크로미터 | ||
니켈 합금 (625) | AMS 5666, ASTM B443 | 15-45 µm, 45-106 µm | ||
공구강(H13) | ASTM A681 | 15-45 µm, 45-106 µm | ||
티타늄(Ti-5Al-2.5Sn) | ASTM B348 | 15-45 µm, 45-106 µm |
공급업체 및 가격 세부 정보
공급업체 | 금속 분말 사용 가능 | 가격(kg당) | 위치 |
---|---|---|---|
카펜터 기술 | 티타늄, 알루미늄, 스테인리스 스틸, 인코넬, 코발트-크롬 | $200 – $600 | 미국 |
샌드빅 | 티타늄, 알루미늄, 스테인리스 스틸, 인코넬, 코발트-크롬 | $250 – $700 | 스웨덴 |
GKN 첨가제 | 티타늄, 알루미늄, 스테인리스 스틸, 인코넬, 코발트-크롬 | $220 – $650 | 독일 |
LPW 기술 | 티타늄, 알루미늄, 스테인리스 스틸, 인코넬, 코발트-크롬 | $230 – $680 | UK |
회가나스 | 티타늄, 알루미늄, 스테인리스 스틸, 인코넬, 코발트-크롬 | $240 – $690 | 스웨덴 |
AP&C | 티타늄, 알루미늄, 스테인리스 스틸, 인코넬, 코발트-크롬 | $210 – $620 | 캐나다 |
오베르 & 듀발 | 티타늄, 알루미늄, 스테인리스 스틸, 인코넬, 코발트-크롬 | $220 – $640 | 프랑스 |
프렉스에어 표면 기술 | 티타늄, 알루미늄, 스테인리스 스틸, 인코넬, 코발트-크롬 | $230 – $660 | 미국 |
고급 분말 및 코팅(AP&C) | 티타늄, 알루미늄, 스테인리스 스틸, 인코넬, 코발트-크롬 | $220 – $650 | 캐나다 |
레니쇼 | 티타늄, 알루미늄, 스테인리스 스틸, 인코넬, 코발트-크롬 | $230 – $670 | UK |
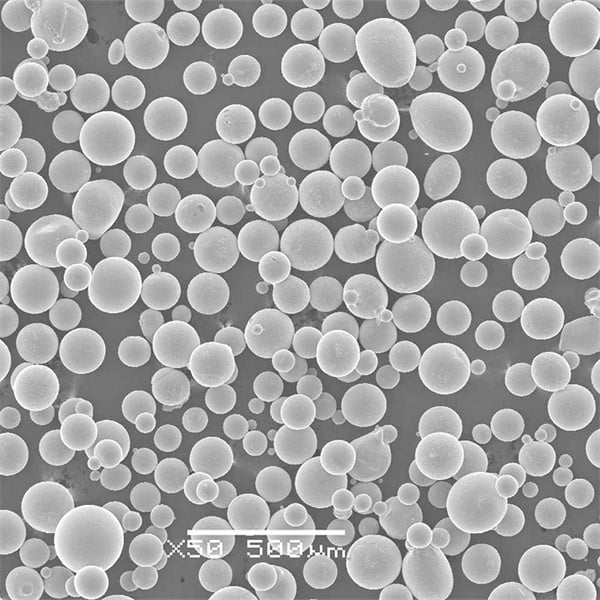
의 장단점 비교 레이저 기반 파우더 베드 융합
측면 | 장점 | 제한 사항 |
---|---|---|
정확성과 디테일 | 높은 정확도와 복잡한 형상을 생성할 수 있는 능력 | 표면 마감을 위해 후처리가 필요할 수 있습니다. |
재료 효율성 | 폐기물 최소화, 필요한 양의 파우더만 사용 | 금속 분말의 높은 비용 |
사용자 지정 | 특정 요구 사항에 맞춰 맞춤형 부품을 쉽게 제작할 수 있습니다. | 설계 및 운영의 복잡성 |
속도와 효율성 | 기존 방식에 비해 생산 시간이 더 빠름 | 초기 설정 시간 및 교정 |
강도 및 내구성 | 우수한 기계적 성질을 가진 부품을 생산합니다. | 빌드 챔버 제약으로 인한 크기 제한 |
비용 | 재료 및 생산 효율성 측면에서 장기적으로 비용 절감 | 장비 및 자재에 대한 초기 투자가 많음 |
자주 묻는 질문
레이저 기반 파우더 베드 퓨전이란?
레이저 기반 파우더 베드 퓨전(PBF)은 고출력 레이저를 사용하여 금속 분말 입자를 한 층씩 융합시켜 견고한 3차원 물체를 만드는 적층 제조 공정입니다.
PBF에서는 어떤 종류의 금속 분말을 사용할 수 있나요?
티타늄 Ti-6Al-4V, 알루미늄 AlSi10Mg, 스테인리스 스틸 316L, 인코넬 718, 코발트-크롬, 마르에이징강, 구리, 니켈 합금 625, 공구강 H13, 티타늄 Ti-5Al-2.5Sn 등 다양한 금속 분말을 사용할 수 있습니다.
레이저 기반 파우더 베드 퓨전의 장점은 무엇입니까?
장점으로는 높은 정밀도와 세부 묘사, 재료 효율성, 맞춤화, 속도 및 효율성, 그리고 뛰어난 기계적 성질을 가진 부품 생산이 있습니다.
레이저 기반 파우더 베드 융합의 한계는 무엇입니까?
제한 사항으로는 초기 비용이 높고, 작업이 복잡하며, 크기가 제한적이며, 원하는 표면 마감을 얻기 위해 후처리가 필요하다는 점이 있습니다.
어떤 산업이 레이저 기반 파우더 베드 융합의 혜택을 누리고 있습니까?
항공우주, 의료, 자동차, 공구, 보석, 에너지, 전자, 치과, 해양, 건축 등의 산업은 다재다능하고 정밀한 PBF 덕분에 이점을 얻고 있습니다.
PBF는 기존 제조 방식과 어떻게 비교됩니까?
PBF는 더 빠른 생산 시간, 더 높은 정밀도, 기존 방법으로는 어려운 복잡한 형상을 만드는 기능을 제공합니다. 그러나 더 높은 초기 비용과 운영 복잡성이 수반됩니다.
결론
레이저 기반 파우더 베드 퓨전은 제조의 미래를 위한 길을 열고 있습니다. 최소한의 폐기물로 고정밀 맞춤형 부품을 생산할 수 있는 능력은 항공우주에서 의료에 이르기까지 산업을 혁신하고 있습니다. 여러 가지 과제가 있지만, 이점이 한계를 훨씬 능가하여 현대 제조 툴킷에 귀중한 추가 기능이 됩니다. 엔지니어, 디자이너 또는 제조업체이든 PBF의 힘을 이해하고 활용하면 작업에서 혁신과 효율성의 새로운 문이 열릴 수 있습니다.
공유
중국 칭다오에 본사를 둔 선도적인 적층 제조 솔루션 제공업체인 MET3DP Technology Co. 당사는 산업용 3D 프린팅 장비와 고성능 금속 분말을 전문으로 합니다.
관련 기사
Met3DP 소개
최근 업데이트
제품
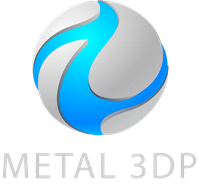
3D 프린팅 및 적층 제조용 금속 분말