Protective Shrouds for Rocket Sensors via Metal AM
목차
Advancing Rocketry: Metal Additive Manufacturing for Protective Sensor Shrouds
The relentless pursuit of space exploration and satellite deployment demands continuous innovation in rocket technology. Every component, from the largest engine structures to the smallest sensor housings, plays a critical role in mission success. Among these vital elements are rocket sensor shrouds – protective enclosures designed to shield delicate sensing instruments from the extreme conditions encountered during launch and operation. These shrouds are not mere covers; they are precisely engineered components that ensure the integrity and accuracy of data crucial for navigation, telemetry, system monitoring, and scientific measurement. Failure to adequately protect these sensors can lead to mission compromise or catastrophic failure, making the design and manufacture of their shrouds a paramount concern for aerospace engineers and procurement managers.
Traditionally, manufacturing these specialized shrouds involved subtractive methods like CNC machining from billet stock or complex casting processes. While effective, these approaches often come with significant limitations, particularly concerning design complexity, material waste, long lead times, and cost, especially for the low-volume, high-customization requirements typical in the aerospace industry. Enter 금속 적층 제조(AM), more commonly known as metal 3D 프린팅. This transformative technology is revolutionizing how high-performance components like sensor shrouds are designed and produced. By building parts layer-by-layer directly from digital models using high-performance metal powders, AM offers unprecedented design freedom, enables significant weight reduction through optimized geometries, drastically shortens development cycles, and allows for the use of advanced materials specifically suited for the harsh environments of space.
The application of metal AM to rocket sensor shrouds addresses several key challenges faced by the aerospace sector. It allows engineers to:
- Integrate complex features: Create intricate internal channels for cooling or wiring, mounting points, and aerodynamic profiles that are difficult or impossible to achieve with traditional methods.
- Optimize for weight: Employ topology optimization and lattice structures to minimize mass without compromising structural integrity – a critical factor where every gram saved translates to significant launch cost reductions or increased payload capacity.
- Consolidate parts: Redesign assemblies previously made of multiple components into a single, unified printed part, reducing complexity, potential points of failure, and assembly time.
- Accelerate prototyping and production: Rapidly iterate designs and produce functional prototypes or final parts in days rather than weeks or months, speeding up development timelines.
- Utilize advanced materials: Leverage materials like Titanium alloys (e.g., Ti-6Al-4V) 및 high-grade Stainless Steels (e.g., 316L), known for their excellent strength-to-weight ratio, corrosion resistance, and performance at extreme temperatures – properties readily achievable with AM processes like Selective Electron Beam Melting (SEBM) and Laser Powder Bed Fusion (LPBF).
Companies specializing in aerospace component manufacturing and wholesale distribution are increasingly turning to metal AM service providers to leverage these benefits. Finding a reliable aerospace metal AM supplier capable of delivering consistent quality, material expertise, and certified processes is crucial. Met3dp, headquartered in Qingdao, China, stands at forefront of this technological shift. With decades of collective expertise in 금속 적층 제조, Met3dp provides comprehensive solutions, including industry-leading SEBM printers known for their large build volumes, exceptional accuracy, and reliability, alongside a portfolio of high-performance metal powders optimized for demanding applications. Our advanced powder manufacturing systems, utilizing Gas Atomization and Plasma Rotating Electrode Process (PREP) technologies, ensure the production of highly spherical, flowable metal powders – the foundation for dense, high-quality printed parts with superior mechanical properties essential for mission-critical components like rocket sensor shrouds.
This article delves into the specifics of using metal AM for producing protective shrouds for rocket sensors. We will explore the applications, the distinct advantages over traditional manufacturing, recommended materials like Ti-6Al-4V and 316L, critical design considerations (DFAM), achievable precision, post-processing needs, potential challenges, and guidance for procurement managers and engineers on selecting the right AM partner and understanding cost drivers. Whether you are an aerospace engineer designing next-generation launch vehicles, a procurement specialist sourcing reliable wholesale rocket components, or a distributor seeking innovative manufacturing solutions, understanding the capabilities of metal AM for sensor shrouds is key to staying competitive and ensuring mission success.
Critical Applications: What Are Rocket Sensor Shrouds Used For?
Rocket sensor shrouds are indispensable guardians of sensitive instruments, ensuring their functionality amidst the chaos of a rocket launch and the unforgiving environment of space or high-altitude flight. Their primary purpose is to physically protect sensors from a barrage of detrimental factors while allowing them to perform their designated measurements accurately. Understanding the specific applications and the environments these shrouds endure highlights the critical need for robust design and advanced manufacturing techniques like metal AM.
Types of Sensors Protected:
Rocket sensor shrouds are designed to house a diverse array of sensors, each critical for different aspects of flight control, system monitoring, and data acquisition. Common examples include:
- Pressure Transducers: Measure ambient atmospheric pressure, chamber pressure in engines, or pressure within propellant tanks. Shrouds protect the delicate diaphragms and electronics from impacts, extreme temperatures, and corrosive propellants.
- Temperature Sensors (Thermocouples, RTDs): Monitor temperatures on the rocket skin, within engine components, electronics bays, or propellant lines. Shrouds provide thermal insulation or controlled thermal conductivity while protecting against vibration and physical damage.
- Inertial Measurement Units (IMUs): Contain accelerometers and gyroscopes crucial for navigation and attitude control. Shrouds protect these highly sensitive instruments from shock, vibration, and thermal fluctuations that could corrupt readings.
- GPS/GNSS Receivers: Provide positioning data. Shrouds, often requiring specific RF-transparent materials or designs, protect the antennas and electronics from the launch environment while ensuring signal reception.
- Strain Gauges: Measure stress and strain on structural components. Shrouds protect the gauges and their delicate wiring from abrasion, impact, and thermal extremes.
- Optical Sensors/Cameras: Used for navigation, observation, or stage separation confirmation. Shrouds protect lenses and sensors from debris, aerodynamic heating, and contamination.
- Acoustic Sensors: Monitor engine noise or structural vibrations. Shrouds protect microphones and related electronics from intense sound pressure levels and physical damage.
- Proximity Sensors: Detect the relative position of components, crucial for stage separation or docking maneuvers. Shrouds protect against impact and environmental factors.
Hostile Operating Environments:
The environments encountered by rocket sensor shrouds are among the most extreme engineered systems face:
- Extreme Vibration & Shock: Launch generates intense, multi-frequency vibrations and high-G shocks that can easily damage unprotected sensors or dislodge components. Shrouds must provide secure mounting and dampening.
- Acoustic Loads: The sound pressure levels during launch can exceed 150 dB, capable of causing significant structural fatigue and damaging sensitive electronics.
- Thermal Extremes: Components experience rapid temperature swings, from cryogenic propellant temperatures to extreme aerodynamic heating during atmospheric ascent and the intense heat of engine operation. Shrouds must maintain sensor operational temperature ranges.
- High G-Forces: Acceleration during launch imposes significant structural loads on all components.
- Pressure Differentials: Rapid changes from sea-level pressure to the vacuum of space require robust sealing and structural integrity.
- Debris & Contamination: Micrometeoroids, orbital debris, ice shedding, and engine exhaust particulates pose impact risks. Shrouds act as a physical barrier.
- Corrosive Atmospheres: Exposure to propellants (like RP-1, hydrazine, NTO), exhaust gases, and potentially salt spray in launch site environments necessitates corrosion-resistant materials.
- Radiation (Space Applications): For missions beyond Earth’s atmosphere, shrouds may need to offer some level of protection against cosmic rays and solar radiation, potentially influencing material selection.
Industries and Broader Applications:
While the primary focus here is rocketry (launch vehicles, missiles, spacecraft), the principles behind designing and manufacturing protective shrouds using metal AM extend to other industries facing harsh environments:
- Aerospace (Aircraft): Protecting sensors on jet engines, landing gear, and control surfaces from vibration, temperature, and debris.
- 방어: Shielding sensitive electronics and sensors on military vehicles, aircraft, and munitions.
- Automotive (Motorsport & Testing): Protecting sensors in high-performance engines, exhaust systems, and chassis during racing or rigorous testing conditions.
- Oil & Gas Exploration: Housing downhole sensors exposed to high pressure, temperature, and corrosive fluids.
- 산업 제조: Protecting sensors in heavy machinery, high-temperature furnaces, or chemically aggressive processing lines.
- 해병: Shielding sensors on submersibles or surface vessels from pressure, saltwater corrosion, and biofouling.
대상 procurement managers 및 유통업체 serving these diverse sectors, understanding the versatility of metal AM in producing custom protective enclosures is key. The ability to rapidly prototype and produce highly optimized shrouds using materials like Ti-6Al-4V or 316L makes it an attractive solution for suppliers aiming to provide cutting-edge components. Partnering with an experienced 금속 AM 서비스 제공업체 like Met3dp ensures access to the necessary technology, materials, and expertise to meet the stringent demands of these critical applications. Met3dp’s focus on high-quality 금속 분말 and reliable printing processes translates directly into robust, dependable sensor shrouds capable of performing flawlessly in the most challenging conditions.
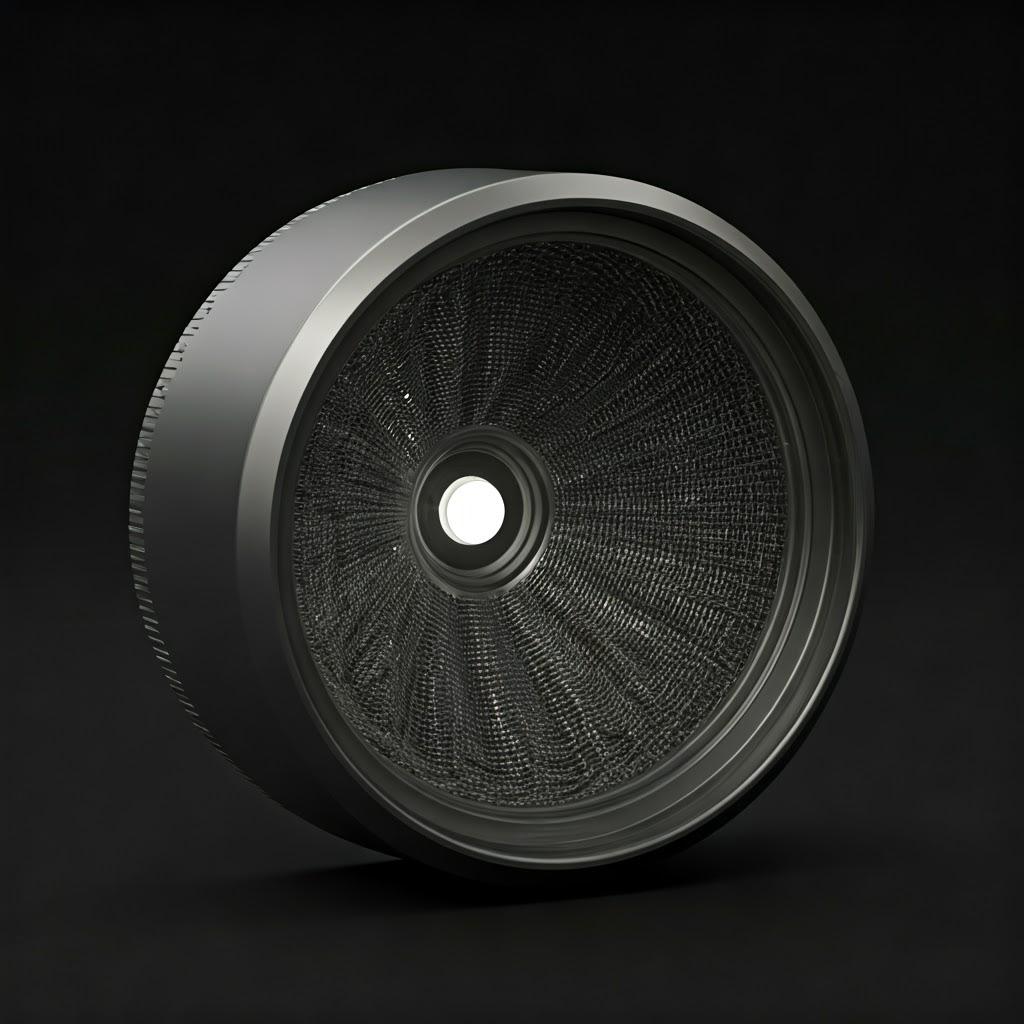
The Additive Advantage: Why Metal 3D Printing for Rocket Sensor Shrouds? Insights for Aerospace Suppliers
The decision to adopt metal additive manufacturing for critical components like rocket sensor shrouds isn’t merely about embracing new technology; it’s a strategic choice driven by tangible engineering and business advantages, particularly compelling for 항공우주 공급업체 및 제조업체. Compared to traditional subtractive manufacturing (like CNC machining) or formative processes (like casting or forging), metal AM offers a unique combination of benefits perfectly suited to the demanding requirements of the aerospace industry.
1. 독보적인 디자인 자유도 및 복잡성:
- Traditional: CNC machining is limited by tool access, making complex internal features, undercuts, or thin-walled curved geometries difficult, time-consuming, or impossible to produce as a single piece. Casting offers more shape freedom but often requires expensive tooling and struggles with very fine details or thin walls.
- 메탈 AM: Builds parts layer-by-layer, freeing designers from many traditional manufacturing constraints. This enables:
- 토폴로지 최적화: Algorithms determine the most efficient material distribution for load-bearing requirements, resulting in lightweight, organic-looking shapes impossible to machine.
- 격자 구조: Internal lattices can significantly reduce weight while maintaining structural integrity or providing specific dampening characteristics.
- 파트 통합: Multiple components of a sensor shroud assembly (e.g., housing, bracket, fasteners) can be redesigned and printed as a single, integrated unit. This reduces part count, assembly time, weight, and potential failure points (like joints or welds).
- Conformal Channels: Internal channels for cooling, heating, or wiring can be designed to follow the contours of the shroud, improving thermal management or simplifying integration.
2. Significant Weight Reduction:
- Traditional: Weight reduction often involves extensive machining, leading to material waste and increased processing time. Achieving optimal lightweighting is constrained by manufacturing limitations.
- 메탈 AM: Enables weight reduction through topology optimization and the use of lattice structures, directly translating to lower launch costs or increased payload capacity. For aerospace applications, every kilogram saved is critical. This is a major driver for aerospace metal AM adoption.
3. Rapid Prototyping & Accelerated Development Cycles:
- Traditional: Creating prototypes often involves dedicated tooling (casting) or significant machine setup and programming time (CNC). Design iterations can take weeks or months.
- 메탈 AM: Allows engineers to go directly from a CAD model to a physical metal part in a matter of days. This facilitates:
- Faster Iteration: Multiple design variations can be printed and tested quickly, leading to optimized solutions faster.
- 리드 타임 단축: For low-volume production or unique parts, AM can often deliver finished components much faster than traditional methods, which may involve complex supply chains and long tooling lead times. This speed is vital for aerospace component suppliers facing tight project deadlines.
4. Efficient Material Usage & Reduced Waste:
- Traditional: Subtractive manufacturing, particularly CNC machining, starts with a solid block of material and removes large amounts to achieve the final shape. This can result in significant material waste (buy-to-fly ratio), especially with expensive aerospace alloys like Titanium.
- 메탈 AM: An additive process that uses only the material needed to build the part (plus support structures, which are often recyclable). This results in a much better buy-to-fly ratio, reducing raw material costs and environmental impact, a key consideration for sustainable manufacturing initiatives.
5. Suitability for Low-Volume, High-Mix Production:
- Traditional: Setting up for machining or creating molds for casting incurs significant upfront costs, making low-volume production runs or highly customized parts economically challenging.
- 메탈 AM: Requires no part-specific tooling. The primary cost drivers are material volume, machine time, and post-processing. This makes it highly cost-effective for:
- 프로토타입: Producing functional metal prototypes without investing in tooling.
- Customized Parts: Manufacturing unique shroud designs tailored to specific sensors or mission requirements.
- 소량 생산: Economically producing the small quantities often needed in specialized aerospace projects. This flexibility benefits wholesale rocket component distributors who need to cater to diverse customer needs.
6. Access to Advanced Materials:
- Traditional: Some advanced alloys can be difficult or costly to machine or cast.
- 메탈 AM: Processes like SEBM and LPBF are well-suited for processing high-performance materials critical for aerospace, including:
- 티타늄 합금(Ti-6Al-4V): Excellent strength-to-weight ratio, corrosion resistance, and high-temperature performance.
- Stainless Steels (316L): Good corrosion resistance, strength, and cost-effectiveness for less demanding thermal environments.
- Superalloys (Inconel): Used for extremely high-temperature applications near engines.
- 알루미늄 합금(AlSi10Mg): Lightweight option where high strength is less critical. Met3dp specializes in producing high-quality powders of these materials and optimizing printing processes for them, ensuring reliable material properties in the final shroud. Our expertise in different 3D 프린팅 방법 allows us to select the best approach for specific material and application needs.
Comparative Overview:
기능 | 금속 적층 제조(AM) | 전통적인 CNC 가공 | 전통 주조 |
---|---|---|---|
디자인 복잡성 | Very High (Internal channels, lattices, organic shapes) | Moderate to High (Limited by tool access) | High (Requires tooling) |
Weight Optimization | Excellent (Topology opt., lattices) | Moderate (Subtractive removal) | Moderate to Good |
부품 통합 | 우수 | 제한적 | 제한적 |
리드 타임(프로토) | Fast (Days) | Moderate (Weeks) | Slow (Weeks/Months – Tooling) |
Lead Time (Low Vol) | Fast to Moderate | Moderate to Slow | Slow (Requires tooling) |
재료 낭비 | Low (Additive) | High (Subtractive) | Moderate (Gates, runners) |
툴링 비용 | 없음 | Low (Fixturing) | High (Molds/Patterns) |
Cost (Low Volume) | Potentially Lower | 잠재적으로 더 높음 | 높음 |
머티리얼 옵션 | Growing range of weldable alloys | 넓은 범위 | Castable alloys |
시트로 내보내기
대상 항공우주 공급업체 및 procurement managers, the message is clear: metal AM isn’t just an alternative; it’s often a superior method for producing complex, lightweight, high-performance components like rocket sensor shrouds. It offers a pathway to innovation, efficiency, and competitiveness in a demanding industry. Partnering with a knowledgeable provider like Met3dp ensures access to state-of-the-art equipment, optimized materials, and the engineering support needed to fully realize the additive advantage. Explore the possibilities further by learning more 우리에 대하여.
Material Matters: Recommended Powders (Ti-6Al-4V & 316L) for Demanding Launch Environments
Selecting the right material is fundamental to the performance and reliability of any aerospace component, especially one subjected to the extreme conditions faced by rocket sensor shrouds. Metal additive manufacturing offers the flexibility to work with a range of high-performance alloys, but for this application, two materials stand out due to their exceptional properties and proven track record in aerospace: Titanium alloy Ti-6Al-4V (Grade 5) 및 Austenitic Stainless Steel 316L. Understanding their characteristics is crucial for engineers designing the shrouds and for procurement specialists sourcing 금속 AM 서비스 또는 고순도 금속 분말.
Why Material Selection is Critical for Sensor Shrouds:
The chosen material must withstand:
- Mechanical Loads: Vibration, shock, acoustic energy, and G-forces during launch.
- Thermal Stresses: Extreme temperatures, from cryogenic fuels to aerodynamic heating and engine proximity.
- 부식: Exposure to propellants, exhaust gases, and atmospheric conditions.
- Vacuum (Space): Outgassing concerns and material stability in the vacuum of space.
- 무게 제약: The perpetual drive to minimize mass in aerospace components.
Ti-6Al-4V (Grade 5 Titanium): The Aerospace Workhorse
Ti-6Al-4V, often simply called Ti64, is the most widely used titanium alloy, accounting for more than 50% of all titanium tonnage worldwide. Its popularity in aerospace is well-deserved due to an outstanding combination of properties, making it an ideal candidate for demanding sensor shroud applications, particularly where weight is a primary concern.
- Key Properties & Benefits:
- 높은 중량 대비 강도 비율: Ti64 offers strength comparable to many steels but at roughly 56% of the density. This is its most significant advantage in aerospace, enabling substantial weight savings.
- 뛰어난 내식성: Forms a stable, protective oxide layer, providing exceptional resistance to atmospheric corrosion, saltwater, and many chemical environments, including oxidizing acids and chlorides. Critical for exposure to various propellants and launch site conditions.
- Good High-Temperature Performance: Retains significant strength up to approximately 315°C (600°F) and can withstand intermittent service at higher temperatures. Suitable for many locations on a launch vehicle, though superalloys might be needed closer to engine hot sections.
- 낮은 열 팽창: Exhibits lower thermal expansion compared to steels and aluminum alloys, reducing thermal stress issues in assemblies experiencing temperature gradients.
- 생체 적합성: While not typically relevant for shrouds, its biocompatibility makes it a standard in medical implants.
- Good AM Processability: Ti-6Al-4V is well-characterized and readily processed using both Laser Powder Bed Fusion (LPBF) and Selective Electron Beam Melting (SEBM) techniques, achieving near-full density and excellent mechanical properties that can meet or exceed wrought material specifications after appropriate post-processing (like Hot Isostatic Pressing – HIP).
- 고려 사항:
- 더 높은 비용: Titanium alloys are significantly more expensive than stainless steels or aluminum alloys, both in terms of raw material and processing.
- 반응성: Titanium can be reactive at high temperatures, particularly with oxygen and nitrogen, requiring controlled atmosphere or vacuum environments during AM processing and heat treatment.
- Lower Thermal Conductivity: Compared to aluminum or steel, which can be a factor in thermal management design.
316L Stainless Steel: The Robust & Versatile Option
316L is an austenitic chromium-nickel stainless steel containing molybdenum, which enhances its corrosion resistance, particularly against chlorides and non-oxidizing acids. It’s a widely available, cost-effective, and well-understood material frequently used in demanding industrial and aerospace applications where extreme weight saving is less critical than durability and cost-effectiveness.
- Key Properties & Benefits:
- 뛰어난 내식성: Superior to standard 304 stainless steel, especially in marine environments and against pitting/crevice corrosion due to its molybdenum content. The “L” designation indicates low carbon content (≤0.03%), which minimizes carbide precipitation during welding or thermal cycles, preserving corrosion resistance.
- Good Strength & Ductility: Offers a good balance of tensile strength, toughness, and ductility across a wide temperature range, from cryogenic temperatures up to moderately elevated temperatures (typically up to ~500-600°C, though strength decreases significantly above 425°C).
- Ease of Manufacturing & Weldability: Readily processable using various AM techniques (especially LPBF) and easily weldable for potential assembly or repair operations.
- 비용 효율성: Significantly less expensive than titanium alloys, making it attractive for shrouds where the extreme weight savings of Ti64 are not strictly necessary or economically justifiable.
- 가용성: Widely available as high-quality powder suitable for AM.
- 고려 사항:
- Higher Density: Roughly 7.99 g/cm³, significantly denser than Ti-6Al-4V (approx. 4.43 g/cm³). This makes it less suitable for applications where minimizing weight is the absolute top priority.
- Lower Strength-to-Weight Ratio: Compared to Ti64, its strength is good, but the higher density results in a less favorable strength-to-weight ratio.
- Magnetic Permeability: While generally non-magnetic in the annealed state, cold working or some phases formed during AM can induce slight magnetism, which might be a consideration near sensitive magnetic sensors.
Material Selection Summary Table:
기능 | Ti-6Al-4V(5등급) | 316L 스테인리스 스틸 | Recommendation Context for Sensor Shrouds |
---|---|---|---|
Primary Advantage | 높은 중량 대비 강도 비율 | Corrosion Resistance & Cost-Effectiveness | Choose Ti64 for maximum weight saving. Choose 316L for cost-sensitive or less weight-critical parts. |
밀도 | ~4.43g/cm³ | ~7.99 g/cm³ | Significant weight difference. |
내식성 | Excellent (Oxidizing, Chlorides, Marine) | Excellent (General, Pitting, Crevice) | Both are excellent; 316L slightly better in some specific chemical environments. |
Usable Temp. Range | Good up to ~315°C (600°F) | Good up to ~425°C (800°F) (strength drops) | Consider location relative to heat sources. |
상대적 비용 | 높음 | 보통 | Significant factor in procurement decisions. |
AM Processability | Excellent (LPBF, SEBM) | Excellent (LPBF primarily) | Both well-suited for AM. |
시트로 내보내기
Met3dp’s Role in Material Excellence:
The ultimate performance of an AM sensor shroud relies heavily on the quality of the metal powder used. Met3dp leverages industry-leading Gas Atomization and PREP technologies to produce metallic powders, including Ti-6Al-4V and 316L, characterized by:
- 높은 구형성: Ensures good powder flowability and uniform spreading during the AM process.
- Controlled Particle Size Distribution (PSD): Optimized for specific AM processes (LPBF, SEBM) to achieve high packing density and minimize porosity.
- 고순도: Low levels of impurities (like Oxygen and Nitrogen, especially critical for Titanium) ensure optimal material properties and performance.
- Batch Consistency: Rigorous quality control guarantees reliable and repeatable results from build to build.
By controlling the powder production process, Met3dp provides aerospace manufacturers 및 component suppliers with the confidence that the materials used for their critical sensor shrouds meet the highest standards. Our comprehensive solutions span not only advanced metal powders but also state-of-the-art SEBM printers and application development services, making Met3dp a valuable partner for organizations embracing metal AM for demanding applications like rocket sensor shrouds. Explore our range of 고품질 금속 분말 suitable for your aerospace needs.
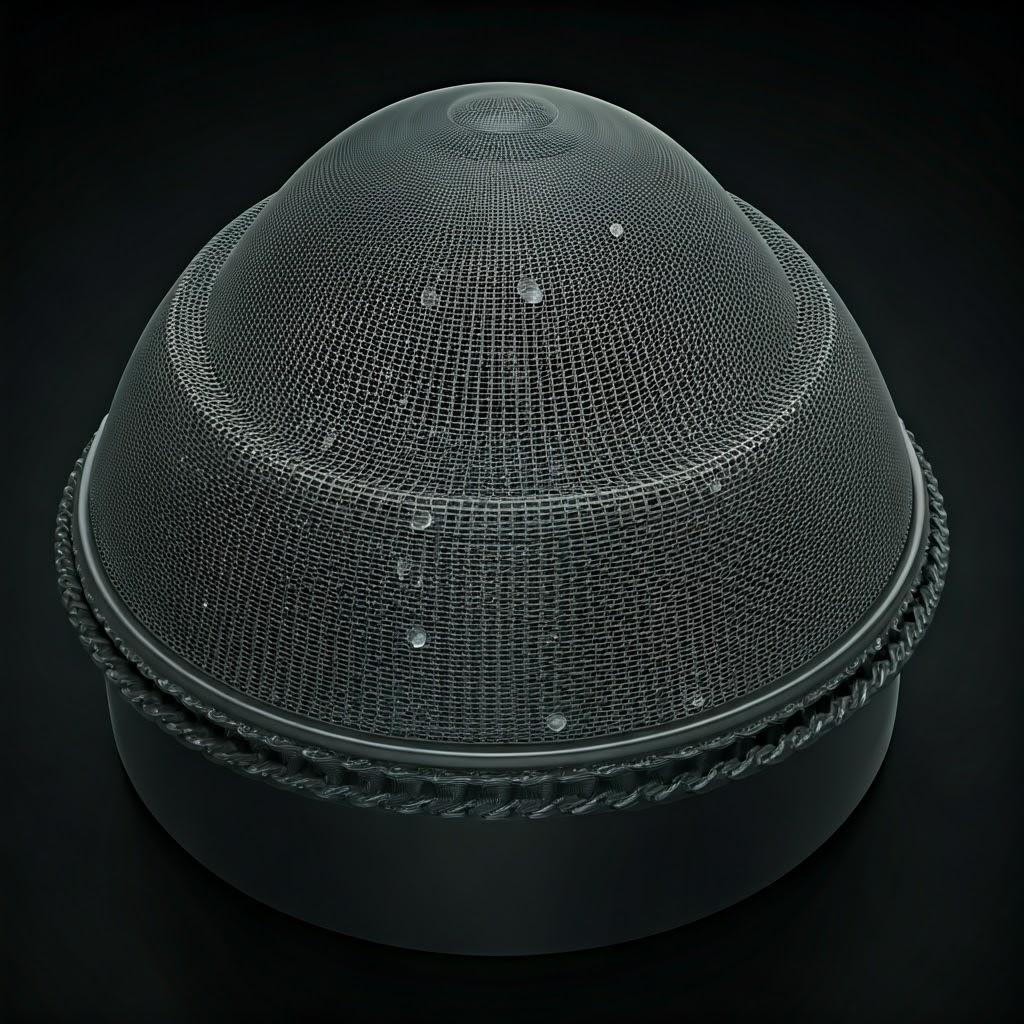
Designing for Additive: Engineering Superior Sensor Shrouds with DFAM
Simply replicating a design intended for machining or casting using metal additive manufacturing rarely unlocks the full potential of the technology. To truly leverage the benefits of AM – particularly weight reduction, performance enhancement, and cost-efficiency – engineers must embrace Design for Additive Manufacturing (DFAM) principles. DFAM involves rethinking component design from the ground up, considering the unique capabilities and constraints of layer-by-layer fabrication. For rocket sensor shrouds, applying DFAM can lead to significantly superior components compared to traditionally manufactured counterparts.
Why DFAM is Crucial for Sensor Shrouds:
- Weight Optimization: In aerospace, mass is a critical parameter. DFAM enables radical weight savings through topology optimization and lattice structures, directly impacting launch costs and vehicle performance.
- 기능 통합: AM allows complex features like conformal cooling channels, integrated mounts, or optimized internal routing for wiring to be built directly into the shroud, reducing part count and assembly complexity.
- 성능 향상: Designs can be optimized for specific load cases, vibration damping, or thermal management in ways impossible with subtractive methods.
- Manufacturing Efficiency: Designing with AM process limitations in mind (e.g., minimizing supports, optimizing orientation) reduces print time, material usage, and post-processing effort, leading to lower costs and faster turnaround.
Key DFAM Techniques for Sensor Shrouds:
- 토폴로지 최적화:
- What it is: Software algorithms that optimize material distribution within a defined design space based on applied loads, constraints, and performance objectives (e.g., minimize mass, maximize stiffness).
- 애플리케이션: Ideal for load-bearing elements of the shroud or mounting brackets. It removes material from non-critical areas, resulting in efficient, often organic-looking structures that are lightweight yet strong.
- 혜택: Significant weight reduction (often 20-50% or more) while meeting or exceeding structural requirements. Vital for aerospace component suppliers aiming for performance leadership.
- Lattice Structures & Cellular Materials:
- What they are: Engineered porous structures (e.g., strut-based, skeletal-TPMS, sheet-TPMS) used to infill solid volumes or create lightweight components.
- 애플리케이션: Can replace solid sections within the shroud walls for weight reduction, provide tailored vibration damping characteristics, enhance thermal insulation or heat dissipation (depending on design), or improve impact absorption.
- 혜택: Further weight savings beyond topology optimization alone, multi-functional capabilities (structural + thermal/damping), potential for improved impact resistance. Design requires specialized software modules.
- 파트 통합:
- What it is: Redesigning an assembly of multiple parts into a single, monolithic component fabricated through AM.
- 애플리케이션: A sensor shroud assembly might originally consist of a housing, a separate mounting bracket, fasteners, and perhaps a cover plate. DFAM allows engineers to potentially combine these into one printed part.
- 혜택: Reduces part count, eliminates fasteners/joints (potential failure points), simplifies assembly, shortens supply chain, potentially reduces overall weight and manufacturing cost. A key strategy for wholesale rocket component distributors looking to offer streamlined solutions.
- Feature Design for Printability & Performance:
- 자립 각도: Design overhangs typically below 45 degrees from the horizontal to minimize the need for support structures, which add print time, material cost, and post-processing effort.
- Minimum Wall Thickness: Respect the minimum printable wall thickness for the chosen material and AM process (e.g., typically 0.3-0.5 mm for LPBF, potentially thicker for SEBM).
- Hole Design: Orient holes vertically whenever possible to ensure roundness and avoid internal supports. Design horizontal holes as teardrops or diamonds if supports must be avoided. Consider adding sacrificial material for later machining if precise dimensions are critical.
- Fillets and Radii: Incorporate generous fillets at sharp corners to reduce stress concentrations and improve fatigue life, a common practice in aerospace design but easily achievable with AM.
- Designing for Post-Processing: Ensure critical features requiring high precision or smooth surface finish are accessible for machining or polishing. Design support structures for easy removal without damaging the part surface.
- Build Orientation Strategy:
- What it is: Deciding how the part will be positioned on the build plate.
- Impact: Orientation significantly affects:
- Support Requirements: Steeper overhangs require more supports.
- 표면 마감: Downward-facing surfaces and side walls typically have rougher finishes than upward-facing surfaces.
- 치수 정확도: Thermal stresses can cause warping differently based on orientation.
- 기계적 속성: Anisotropy (direction-dependent properties) can occur, though often minimized with proper parameters and post-processing like HIP.
- Build Time & Cost: Taller builds generally take longer. Nesting multiple parts efficiently depends on their orientation.
- Collaboration: Determining the optimal orientation often requires collaboration between the designer and the AM service provider, like Met3dp. Our engineers leverage simulation tools and extensive process experience to find the best orientation balancing printability, performance, and cost. Explore our comprehensive 금속 3D 프린팅 서비스 to see how we integrate DFAM.
By thoughtfully applying these DFAM principles, engineers can transform a standard rocket sensor shroud into a highly optimized, lightweight, and integrated component that fully capitalizes on the unique advantages of metal additive manufacturing. This design-led approach is essential for pushing the boundaries of aerospace performance and efficiency.
Precision Engineered: Tolerance, Surface Finish, and Dimensional Accuracy in AM Shrouds
While metal AM offers incredible design freedom, understanding the achievable levels of precision is crucial for engineers and procurement managers specifying rocket sensor shrouds. Tolerance, surface finish, and dimensional accuracy are key parameters that define the quality and functionality of the final part, especially for components requiring precise fits, seals, or specific surface characteristics. These aspects are influenced by the chosen AM process (SEBM vs. LPBF), material, part geometry, build parameters, and post-processing steps.
Defining the Terms:
- Tolerance: The allowable deviation from a specified nominal dimension. Defines how much variation is acceptable for a part feature (e.g., diameter, length, flatness). Often specified according to standards like ISO 2768 (general tolerances).
- Surface Finish (Surface Roughness): Measures the fine-scale irregularities on a part’s surface. Commonly quantified by Ra (average roughness). Affects friction, wear, fatigue life, sealing, and aesthetics.
- 치수 정확도: How closely the printed part conforms to the original CAD model dimensions overall. Affected by shrinkage, warping, and process variations.
Achievable Precision in Metal AM:
- General Tolerances:
- As-built tolerances for metal AM processes like LPBF and SEBM are typically in the range of ±0.1 mm to ±0.3 mm for smaller features, plus a percentage of the dimension for larger features (e.g., ±0.1% to ±0.2%).
- A common reference point might be ISO 2768-m (medium) or sometimes ISO 2768-f (fine) for general dimensions, but tighter tolerances often require post-machining.
- Factors influencing tolerance include machine calibration, thermal stability during the build, material properties (shrinkage), part size and geometry complexity, and support strategy. SEBM, operating at higher temperatures, can sometimes exhibit less internal stress but may have slightly looser as-built tolerances than optimized LPBF for fine features.
- Surface Finish (Ra):
- As-Built Ra: Varies significantly depending on orientation, process, and material:
- Upward-facing surfaces: Generally the smoothest, potentially 5-15 µm Ra for LPBF, slightly higher for SEBM.
- Side walls (Vertical): Roughness influenced by layer lines, typically 10-25 µm Ra.
- Downward-facing surfaces (Support Interface): Usually the roughest due to support contact points, often >20-30 µm Ra.
- 파우더 특성: Finer powder particles generally lead to smoother finishes but may affect flowability and require different process parameters. Met3dp’s high-quality, spherical powders with controlled PSD contribute to achieving consistent and optimal surface finishes for the chosen process.
- 후처리: As-built finishes are often insufficient for critical aerospace applications. Post-processing steps like bead blasting, tumbling, polishing, or CNC machining are used to achieve desired Ra values (down to <1 µm Ra with polishing).
- As-Built Ra: Varies significantly depending on orientation, process, and material:
- 치수 정확도:
- Overall accuracy depends on meticulous process control, including thermal management to minimize warping and distortion caused by residual stresses.
- Simulation tools are increasingly used to predict and compensate for potential distortions before printing.
- Verification is crucial. Coordinate Measuring Machines (CMM) 및 3D scanning are used to compare the final part dimensions against the original CAD data and ensure critical features are within tolerance. This is a standard Quality Assurance step for aerospace metal AM suppliers.
Achieving Tighter Specifications:
For sensor shrouds requiring high precision (e.g., mating flanges, sensor mounting interfaces, sealing surfaces), a hybrid approach combining AM with traditional machining is common:
- Print Near-Net Shape: Use AM to create the complex overall geometry of the shroud, leveraging DFAM for weight reduction and part consolidation. Leave extra material (machining allowance, typically 0.5-2 mm) on critical surfaces.
- Post-Machining: Use CNC machining to achieve final tolerances (potentially down to ±0.01 mm or tighter) and specific surface finish requirements on those critical features.
Met3dp’s Commitment to Precision:
At Met3dp, we understand the stringent requirements of the aerospace industry.
- 우리의 업계를 선도하는 SEBM 프린터 are designed for accuracy and reliability, ensuring consistent build conditions.
- 우리는 활용합니다 high-quality, optimized metal powders manufactured in-house, contributing to predictable shrinkage and good surface quality.
- Our engineering team works closely with clients to optimize designs and build orientations for dimensional stability.
- We implement rigorous 품질 관리 프로토콜, including in-process monitoring and post-build inspection using CMM and other metrology tools, ensuring that the final sensor shrouds meet the specified tolerances and accuracy demands.
Summary Table: Precision Expectations:
매개변수 | As-Built Metal AM (Typical Range) | Achievable with Post-Processing | Key Influencing Factors |
---|---|---|---|
허용 오차 | ±0.1 to ±0.3 mm + % of dimension | Down to ±0.01 mm (Machining) | Machine, Material, Geometry, Supports, Thermal Control |
Surface Finish (Ra) | 5 – 30+ µm | <1 µm (Polishing/Machining) | Orientation, Process (LPBF/SEBM), Powder Size, Parameters |
치수 정확도 | Good (Process dependent) | Very High (Verified by CMM) | Warpage Control, Simulation, Machine Calibration, QC |
시트로 내보내기
Engineers and procurement managers should clearly define the required tolerances and surface finishes on drawings, identifying critical features that may necessitate post-machining. Open communication with the AM provider is essential to ensure expectations are aligned and achievable within the project scope and budget.
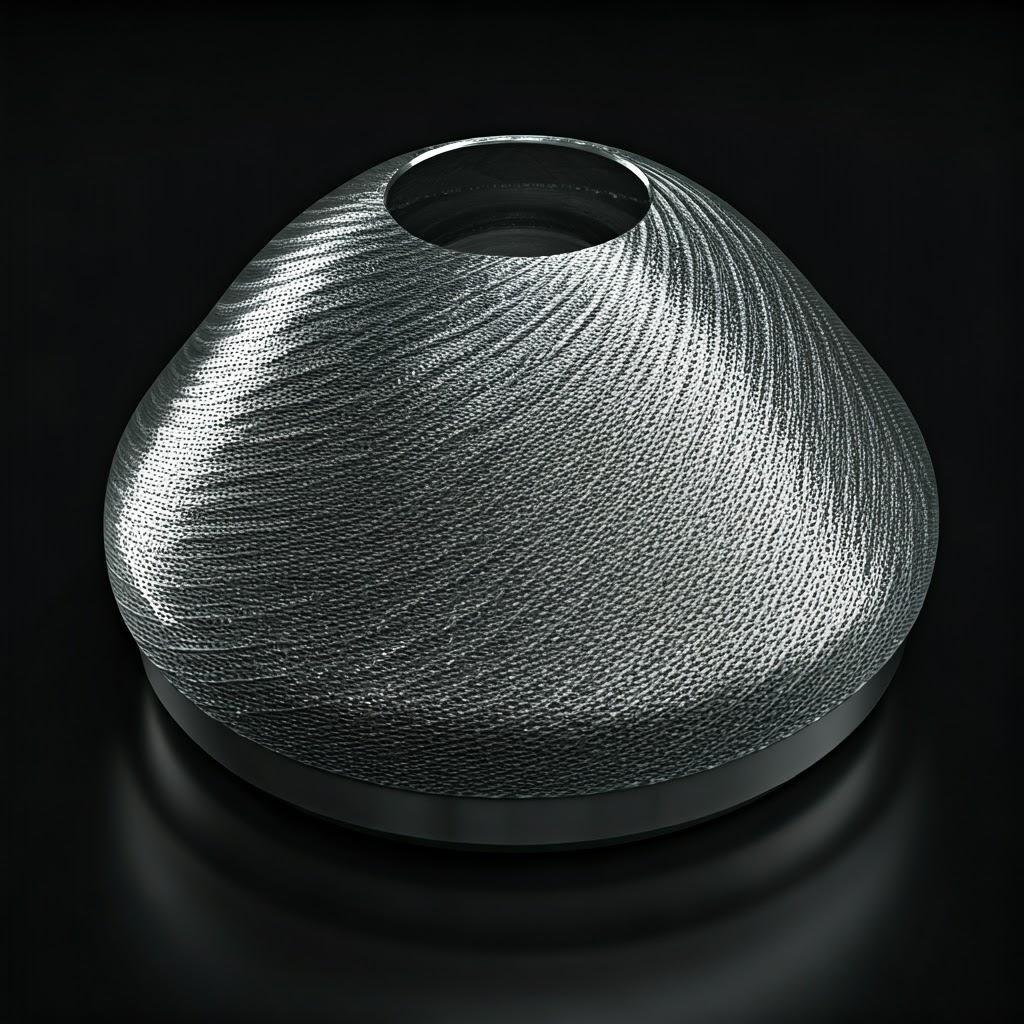
Mission-Ready Finish: Essential Post-Processing Steps for Metal AM Sensor Shrouds
Creating a rocket sensor shroud via metal additive manufacturing doesn’t end when the printer stops. The “green” part, fresh off the build plate, requires a series of post-processing steps to transform it into a functional, reliable, mission-ready component. These steps are crucial for relieving internal stresses, removing support structures, achieving dimensional tolerances and surface finish requirements, ensuring material integrity, and verifying quality. For critical aerospace components like sensor shrouds, post-processing is not optional; it’s an integral part of the manufacturing workflow.
Why Post-Processing is Non-Negotiable:
- Residual Stresses: The rapid heating and cooling cycles inherent in AM create internal stresses that can cause warping or cracking if not relieved.
- 지원 구조: Overhanging features require support structures during the build, which must be removed.
- 표면 마감: As-built surfaces are often too rough for sealing, fatigue-critical areas, or aerodynamic requirements.
- 다공성: While minimized with optimized parameters, some micro-porosity can remain, potentially affecting fatigue life. HIP treatment can eliminate this.
- Tolerances: As-built parts may not meet the tight tolerances required for interfaces and fits.
- Cleanliness: Residual powder must be thoroughly removed.
Common Post-Processing Workflow for AM Sensor Shrouds (Ti-6Al-4V / 316L):
- 스트레스 완화 열처리:
- 목적: To reduce internal stresses locked into the part during the printing process, minimizing the risk of distortion during subsequent steps (like removal from the build plate) and improving dimensional stability.
- 프로세스: Performed while the part may still be attached to the build plate, typically in a vacuum or inert atmosphere furnace. Cycles vary based on material and geometry (e.g., for Ti-6Al-4V, typically 595-840°C followed by controlled cooling; for 316L, often higher temperatures ~850-1150°C for solution annealing, if required, though simple stress relief might be lower).
- Importance: Absolutely critical first step for most metal AM parts, especially complex geometries or titanium alloys.
- 빌드 플레이트에서 제거:
- 목적: To separate the printed shroud(s) from the metal plate they were built upon.
- 방법: Commonly done using Wire Electrical Discharge Machining (Wire EDM) or a bandsaw. Care must be taken not to damage the parts.
- 지원 구조 제거:
- 목적: To remove the temporary structures that supported overhangs and complex features during the build.
- 방법: Can range from manual breaking (for easily accessible, frangible supports) to machining, grinding, or using specialized hand tools. This can be labor-intensive and requires careful execution to avoid damaging the part surface. DFAM plays a key role in designing supports for easier removal.
- 열간 등방성 프레싱(HIP):
- 목적: To eliminate internal microporosity, densify the material to near 100%, and improve mechanical properties, particularly fatigue strength, ductility, and fracture toughness. Often mandatory for critical aerospace components.
- 프로세스: Parts are subjected to high temperature (below melting point) and high isostatic pressure (using an inert gas like Argon) simultaneously in a specialized HIP vessel. Typical HIP cycles for Ti-6Al-4V are around 900-950°C and 100-150 MPa.
- 혜택: Results in material properties that can meet or exceed those of wrought or cast equivalents. Essential for ensuring the reliability of shrouds under cyclic loading (vibration).
- Machining (CNC):
- 목적: To achieve tight dimensional tolerances, specific surface finishes, and features that are difficult to produce accurately with AM alone (e.g., precise mating surfaces, O-ring grooves, threaded holes).
- 프로세스: Uses traditional CNC milling or turning operations on the AM part. Requires careful fixture design to hold the potentially complex AM geometry. Material allowance must be included in the AM design stage.
- Surface Finishing & Cleaning:
- 목적: To achieve the required surface roughness (Ra), remove contaminants, and prepare for any subsequent coatings or inspections.
- 방법:
- Abrasive Methods: Bead blasting, sand blasting, or tumbling can provide a uniform matte finish and remove loose particles (Ra typically 3-10 µm).
- 연마: Manual or automated polishing for very smooth, mirror-like finishes (Ra < 0.8 µm) on specific areas.
- 전기 연마: Electrochemical process to smooth surfaces, particularly effective for stainless steels like 316L.
- Abrasive Flow Machining (AFM): Pushing abrasive media through internal channels to smooth them.
- Cleaning: Ultrasonic cleaning or solvent washing to remove all residual powder and machining fluids.
- Inspection and Non-Destructive Testing (NDT):
- 목적: To verify dimensions, detect surface or internal defects, and ensure the part meets all specifications before deployment.
- 방법:
- Dimensional: CMM, 3D scanning.
- Surface: Visual inspection, dye penetrant testing (DPT), microscopic examination.
- Internal: Computed Tomography (CT) scanning (excellent for detecting internal porosity or defects in complex AM parts), X-ray radiography.
- Material: Hardness testing, potentially witness coupons tested for tensile properties.
Integrating Post-Processing into Design:
Successful and cost-effective post-processing starts at the design stage. Engineers must consider:
- How will supports be removed? Is access available?
- Which surfaces require machining? Is there sufficient material allowance and can the part be fixtured easily?
- Are internal channels designed for cleaning and inspection?
- Are post-processing requirements clearly communicated to the 금속 AM 서비스 제공업체?
Met3dp offers end-to-end solutions, including consultation on DFAM that incorporates post-processing considerations. Our network and expertise ensure that your sensor shrouds undergo the necessary finishing and quality verification steps to be truly mission-ready. Understanding the necessity and complexity of these steps is vital for procurement managers budgeting and scheduling aerospace projects involving metal AM.
Overcoming Hurdles: Common Challenges & Mitigation Strategies in 3D Printing Sensor Shrouds
Metal additive manufacturing is a powerful technology, but it’s not without its complexities. Producing high-quality, reliable rocket sensor shrouds requires careful control over the entire process, from design and simulation to printing and post-processing. Anticipating and mitigating common challenges is key to successful implementation and avoiding costly delays or component failures. Aerospace engineers and suppliers need to be aware of these potential hurdles.
1. Warping and Distortion:
- 도전: The significant temperature gradients during printing generate residual stresses within the part. As these stresses relax, they can cause the part to warp or distort, deviating from the intended geometry, especially in thin-walled or large, flat sections common in shrouds.
- 완화 전략:
- Thermal Simulation: Using Finite Element Analysis (FEA) tools to predict stress accumulation and distortion based on geometry and process parameters.
- Optimized Build Orientation: Positioning the part to minimize large flat areas parallel to the build plate and manage heat distribution.
- Intelligent Support Structures: Designing supports not just for gravity but also to anchor the part firmly and counteract shrinkage/warping forces. Simulation often guides optimal support placement and type.
- 프로세스 매개변수 최적화: Fine-tuning laser/electron beam power, scan speed, and layer thickness to manage the thermal profile.
- Build Plate Heating: Maintaining an elevated temperature in the build chamber (especially in SEBM) reduces thermal gradients and minimizes stress.
- Immediate Stress Relief: Performing a stress relief heat treatment cycle immediately after printing, often before removing the part from the build plate.
2. Residual Stress:
- 도전: Even if significant warping is avoided, high levels of residual stress can remain within the printed shroud. This can lead to premature cracking, reduced fatigue life, or distortion during post-machining when material layers are removed.
- 완화 전략:
- All strategies for mitigating warping also help reduce residual stress.
- Careful Post-Processing: Performing stress relief heat treatments is paramount. For materials like Ti-6Al-4V, multiple heat treatments (stress relief, potentially solution treatment and aging, HIP) might be necessary depending on the required final properties.
- 디자인 고려 사항: Avoiding sharp internal corners where stress can concentrate; using fillets helps.
3. Support Removal Difficulty and Surface Damage:
- 도전: Supports must be strong enough to work during the build but easy enough to remove afterward without damaging the shroud’s surface, especially on complex or delicate geometries. Incomplete or aggressive removal can leave blemishes or scratches, impacting fatigue life or aesthetics.
- 완화 전략:
- DFAM: Designing parts with self-supporting angles (typically >45°) minimizes the need for supports. Orienting the part to reduce overhangs.
- Optimized Support Design: Using specialized support structures (e.g., tree supports, thin-walled supports, supports with specific contact points) that provide adequate anchoring but break away more easily. Software tools offer various support strategies.
- Process Parameter Tuning: Adjusting parameters where supports connect to the part to create a weaker interface.
- Appropriate Removal Techniques: Using the right tools (pliers, cutters, grinders, potentially EDM or machining for stubborn supports) and careful manual labor. Planning for access during the design phase.
4. Porosity (Gas and Lack-of-Fusion):
- 도전: Small voids can form within the printed material due to trapped gas (gas porosity) or incomplete melting/fusion between layers or scan tracks (lack-of-fusion porosity). Porosity acts as a stress concentrator, significantly reducing fatigue life and mechanical properties.
- 완화 전략:
- High-Quality Powder: Using powder with controlled sphericity, low internal gas content, and appropriate particle size distribution. Met3dp’s advanced atomization processes (Gas Atomization, PREP) are designed to produce such high-quality powders.
- Optimized Process Parameters: Ensuring correct energy density (power, speed, hatch spacing) to fully melt the powder layers and allow trapped gas to escape. This requires extensive process development and characterization for each material/machine combination.
- Controlled Atmosphere: Maintaining a high-purity inert gas atmosphere (Argon or Nitrogen) or vacuum (SEBM) to prevent oxidation and contamination.
- 열간 등방성 프레싱(HIP): The most effective way to eliminate remaining internal porosity post-build, densifying the part and healing defects. Often mandatory for critical aerospace metal AM 부품.
5. Surface Roughness:
- 도전: As-built surfaces, particularly on overhangs and vertical walls, can be rougher than desired for functional requirements like sealing or fatigue resistance.
- 완화 전략:
- 매개변수 최적화: Fine-tuning layer thickness, contour scan parameters.
- 빌드 오리엔테이션: Prioritizing critical surfaces to be upward-facing if possible.
- 후처리: Employing appropriate finishing techniques (blasting, polishing, machining, etc.) as described in the previous section.
6. Achieving Fine Features and Thin Walls:
- 도전: There’s a limit to the minimum feature size and wall thickness that can be reliably produced due to melt pool size, powder particle size, and heat diffusion. Sensor shrouds might require thin walls for weight or small intricate details for mounting sensors.
- 완화 전략:
- Adhering to Design Rules: Following manufacturer-recommended minimum feature sizes for the chosen process (LPBF generally offers finer resolution than SEBM).
- Process Selection: Choosing the AM process best suited for the required resolution.
- Careful Parameter Tuning: Specific parameters can be developed for fine features, sometimes at the expense of build speed.
Partnering for Success:
Overcoming these challenges requires deep expertise in materials science, process physics, simulation, and quality control. Partnering with an experienced metal AM solution provider like Met3dp is crucial. We bring:
- 프로세스 전문성: Decades of collective experience in optimizing SEBM and other AM processes for materials like Ti-6Al-4V and 316L.
- Advanced Equipment: Utilizing reliable, industry-leading printers designed for consistent results.
- Material Control: In-house production of high-quality powders tailored for AM.
- Engineering Support: Assisting with DFAM, simulation, and troubleshooting throughout the project lifecycle.
By acknowledging potential hurdles and leveraging expert partnerships, aerospace companies can confidently utilize metal AM to produce robust, high-performance rocket sensor shrouds.
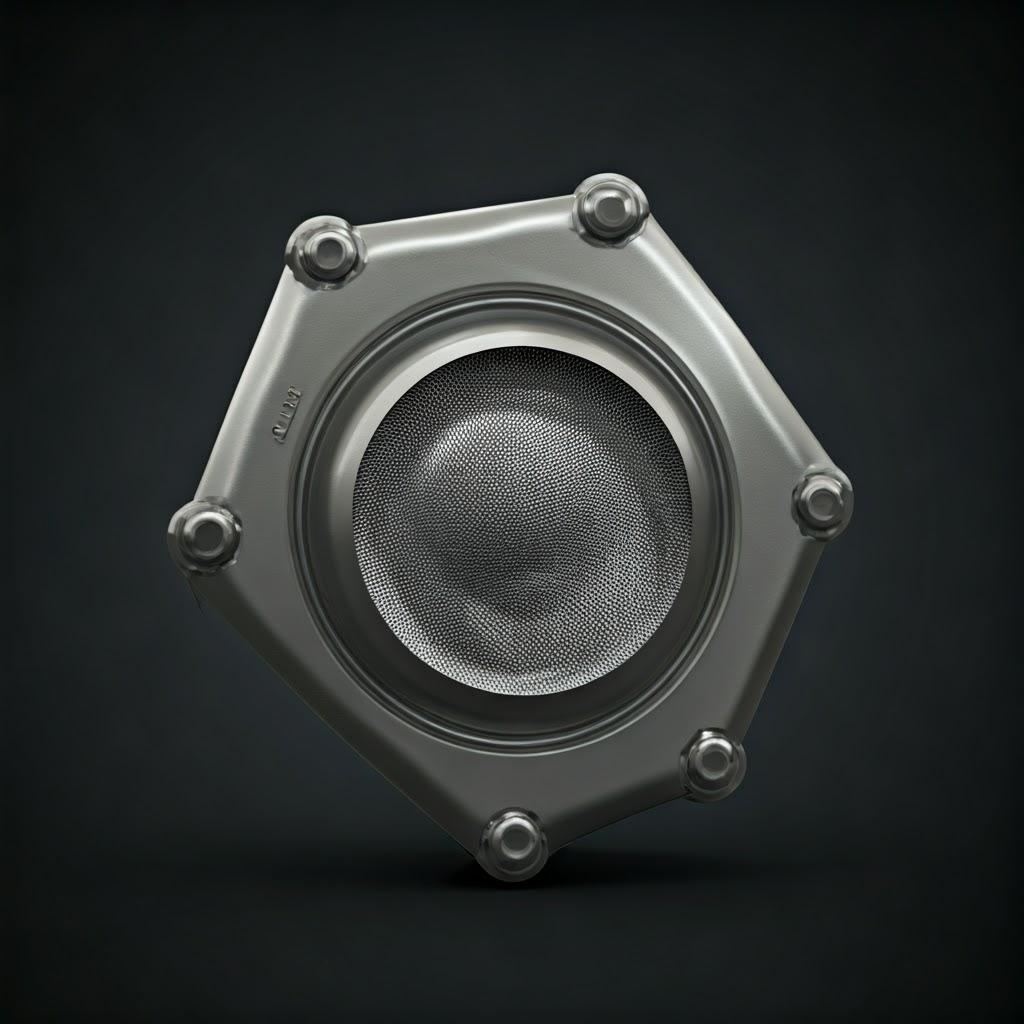
Strategic Sourcing: Choosing the Right Metal AM Partner for Rocket Component Supply
Selecting a manufacturing partner for critical aerospace components like rocket sensor shrouds is a decision that carries significant weight. The quality, reliability, and performance of these parts depend heavily on the capabilities and expertise of the chosen supplier. Simply opting for the lowest bidder or the provider with the quickest advertised lead time can introduce unacceptable risks in the demanding aerospace sector. Strategic sourcing requires a thorough evaluation process to identify a metal additive manufacturing partner – not just a vendor – who can consistently deliver mission-ready components and act as an extension of your engineering team.
Key Criteria for Evaluating Metal AM Suppliers for Aerospace:
- Aerospace Experience & Certifications:
- Track Record: Does the supplier have demonstrable experience manufacturing parts for aerospace or defense applications? Can they provide relevant case studies or references?
- 인증: AS9100 certification is paramount. This standard builds upon ISO 9001, adding specific requirements for quality management within the aviation, space, and defense industries. Compliance indicates a robust QMS tailored to aerospace demands. Other certifications (NADCAP for special processes like heat treatment or NDT) might also be relevant depending on the required scope.
- Technical Expertise & Engineering Support:
- Materials Science: Deep understanding of the specified materials (Ti-6Al-4V, 316L) in their AM-processed state, including microstructure, mechanical properties, and appropriate post-processing.
- 프로세스 지식: Expertise in the specific AM technologies (SEBM, LPBF) required, including parameter optimization for density, accuracy, and surface finish.
- DFAM Capability: Ability to provide constructive feedback on designs, suggest optimizations for additive manufacturing, and collaborate on achieving weight reduction or performance goals.
- Simulation Skills: Use of thermal and process simulation tools to predict and mitigate warping, stress, and optimize support strategies.
- Equipment Capabilities & Capacity:
- Technology Match: Do they operate the appropriate AM systems (e.g., SEBM for certain Ti64 benefits, LPBF for fine features) with well-maintained, calibrated machines?
- 볼륨을 구축합니다: Can their machines accommodate the size of the required sensor shrouds?
- Material Dedication: For sensitive materials like Titanium, are machines dedicated to specific alloys to prevent cross-contamination?
- 용량 및 중복성: Do they have sufficient machine capacity to meet deadlines and potentially scale production? Is there redundancy in case of machine downtime?
- Material Quality Control:
- Powder Sourcing & Handling: Rigorous controls for sourcing, testing, storing, handling, and recycling metal powders to ensure purity, consistency, and traceability. Contamination control is critical.
- Traceability: Ability to trace powder batches used for specific parts back to their source and testing certifications.
- Robust Quality Management System (QMS):
- Documentation: Clear, documented procedures for all stages: order review, build preparation, machine operation, post-processing, inspection, and shipping.
- 프로세스 제어: In-process monitoring and data logging to ensure builds run according to validated parameters.
- Inspection & Testing: Calibrated metrology equipment (CMM, scanners) and established NDT procedures (visual, DPT, CT scanning).
- Non-Conformance Handling: A defined process for identifying, documenting, and addressing any parts or processes that fall outside specifications.
- Comprehensive Post-Processing:
- In-House vs. Partnered: Does the supplier manage all necessary post-processing steps (stress relief, HIP, machining, finishing, NDT) either in-house or through qualified, audited partners? Ensure seamless integration and quality control throughout.
- Communication & Project Management:
- 투명성: Clear communication regarding capabilities, timelines, costs, and potential challenges.
- 응답성: Dedicated points of contact and timely responses to inquiries and technical questions.
Why Partner with Met3dp?
Met3dp embodies the qualities of a strategic aerospace additive manufacturing partner. Headquartered in Qingdao, China, we offer:
- Decades of Collective Expertise: Our team possesses deep knowledge across metal AM, materials science, and aerospace applications.
- Industry-Leading Equipment: We utilize advanced SEBM printers known for large build volumes, accuracy, and reliability, ideal for robust aerospace components.
- Advanced Powder Technology: Our unique advantage lies in our in-house manufacturing of high-quality metal powders using Gas Atomization and PREP technologies. This ensures optimal powder characteristics (sphericity, purity, flowability) and complete material traceability, forming the foundation for superior printed parts.
- 종합 솔루션: We provide end-to-end support, from DFAM consultation and printing to post-processing management and quality assurance.
- Commitment to Quality: We operate with rigorous quality control protocols tailored to demanding industries.
Choosing the right partner mitigates risk and maximizes the benefits of AM. Engage with potential suppliers early, conduct thorough audits if necessary, and prioritize demonstrated expertise and quality systems over solely cost or speed. Visit https://met3dp.com/ to learn more about our capabilities.
Procurement Insights: Cost Factors & Lead Time Estimation for AM Sensor Shrouds
For procurement managers and engineers budgeting for aerospace projects, understanding the cost structure and typical lead times associated with metal additive manufacturing is essential. Unlike traditional manufacturing where tooling often dominates initial costs, AM pricing is driven by different factors. Transparency from the AM service provider is key to accurate budgeting and scheduling.
Key Cost Drivers for Metal AM Sensor Shrouds:
- 재료비:
- 볼륨: Calculated based on the final part volume 플러스 the volume of support structures needed. Efficient design (DFAM) minimizing supports helps reduce cost.
- 머티리얼 유형: There’s a significant cost difference between aerospace-grade metal powders. Ti-6Al-4V powder is considerably more expensive than 316L stainless steel powder. Exotic superalloys would be even higher.
- 파우더 품질: High-purity, highly spherical powders optimized for AM typically command a premium but are necessary for consistent, high-quality results.
- AM Machine Time:
- Build Height: This is often the primary driver of print time. Taller parts take longer, regardless of how many are nested on the plate.
- Part Volume & Density: Larger or denser parts require more material deposition and potentially longer scanning times.
- 복잡성: Intricate features might require slower scan speeds for accuracy.
- Machine Rate: An hourly rate charged for using the industrial AM machine, which varies based on machine type, size, and provider.
- Setup & Labor:
- 빌드 준비: Time taken to slice the CAD model, generate support structures, plan the build layout (nesting), and prepare the machine. This cost is often amortized over the number of parts in a build.
- Machine Operation: Monitoring the build process.
- Post-Processing Labor: Significant labor can be involved in part breakout, support removal, basic finishing, and inspection. Complex support removal is a major labor cost driver.
- 후처리 비용:
- Heat Treatment (Stress Relief, Annealing): Requires furnace time and controlled atmospheres (vacuum/inert gas).
- 열간 등방성 프레싱(HIP): A specialized process often outsourced, adding significant cost per cycle (costs are lower per part if a full HIP batch can be run).
- 가공: Costs depend on the complexity of the features being machined, the number of setups required, and the required tolerance/finish.
- 표면 마감: Bead blasting, tumbling, polishing – costs vary with the method and required outcome.
- NDT & Inspection: Costs associated with CMM time, CT scanning (can be expensive), DPT, etc.
- Non-Recurring Engineering (NRE):
- If significant design assistance, simulation work, or specific process development is required for a new part, these upfront engineering costs may be quoted separately.
Estimating Lead Times:
Lead time is the total time from order placement to part delivery. It’s influenced by several factors:
- Print Time: Can range from hours to several days, primarily dependent on build height.
- Queue Time: The supplier’s current machine backlog. High-demand periods can extend lead times.
- 후처리: Each step adds time:
- Heat Treatment: Typically 1-2 days (including furnace time and cooling).
- HIP: Can add 3-7 days (including shipping to/from HIP provider if outsourced, plus cycle time).
- Machining: Highly variable, from 1 day to several weeks depending on complexity.
- Support Removal/Finishing: Can range from hours to days depending on complexity.
- Inspection: 1-3 days typically.
- 해운: Time for transportation to the customer’s facility.
Typical Lead Time Ranges (Estimates):
- Prototypes (1-5 units): Often 1 to 4 weeks, depending heavily on complexity, material, and required post-processing (especially if HIP or extensive machining is needed). Expedited options may be available at a premium.
- Low-Volume Production (5-50 units): 일반적으로 3 to 8 weeks or more, influenced by batching efficiency, machine availability, and the full post-processing workflow.
Tips for Procurement:
- Request Detailed Quotes: Ask for quotes that break down costs (material, machine time, post-processing steps) for better transparency.
- Clarify Lead Times: Discuss lead time expectations upfront and understand the impact of different post-processing choices.
- 디자인 최적화: Collaborate with engineering and the AM provider to optimize the shroud design for manufacturability (e.g., minimize supports, reduce build height if possible) to potentially lower costs and speed up production.
- Volume Breaks: Inquire about potential price reductions for larger batch sizes, as setup costs are amortized and machine/post-processing utilization can be more efficient.
Understanding these cost and time factors allows for more accurate project planning and budgeting when incorporating metal AM sensor shrouds into aerospace programs.
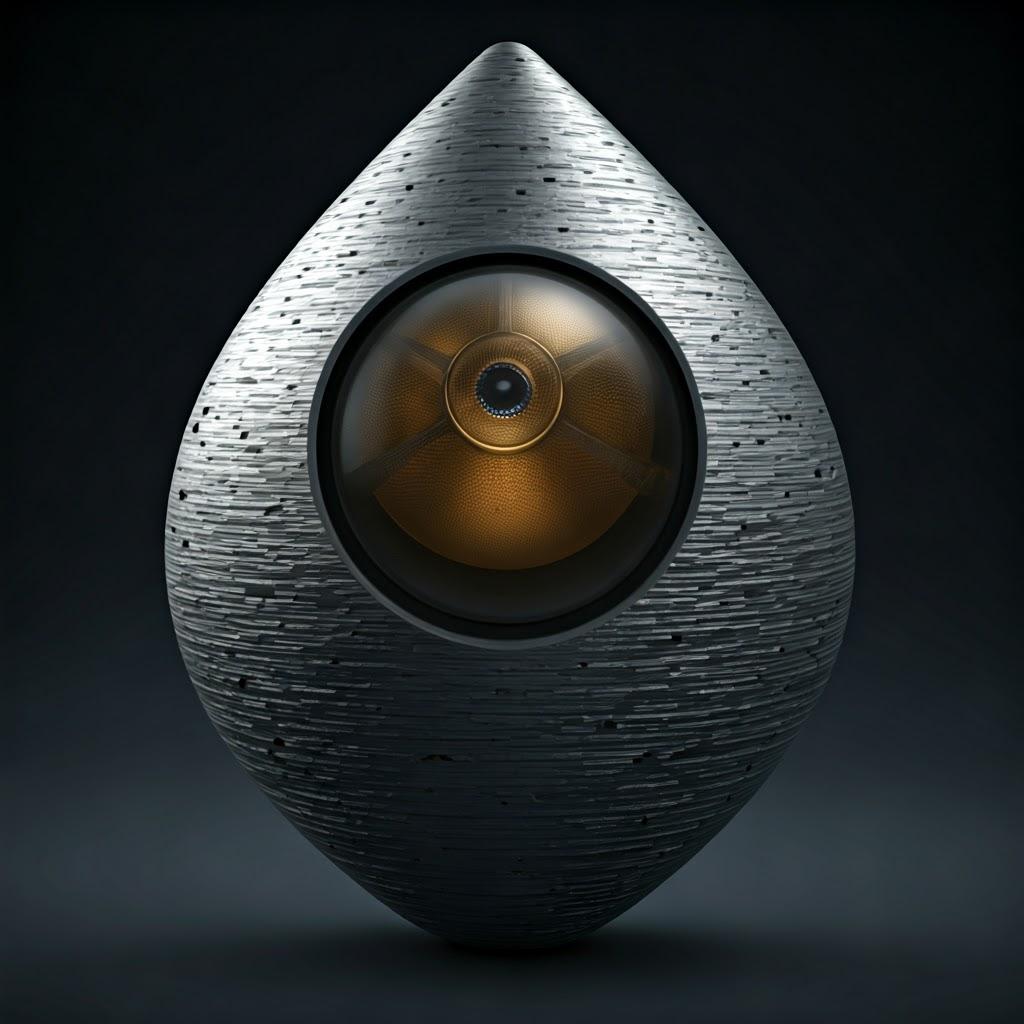
Frequently Asked Questions (FAQ) about Metal AM Rocket Sensor Shrouds
Here are answers to some common questions engineers and procurement specialists have when considering metal additive manufacturing for rocket sensor shrouds:
Q1: What is the typical lead time for a prototype vs. a production run of AM sensor shrouds?
A1: Lead times vary significantly based on complexity, size, material, required post-processing, and supplier queue.
- Prototypes (1-5 units): Expect roughly 1 to 4 weeks. This allows for printing, basic support removal, stress relief, and initial inspection. Lead times increase considerably if HIP treatment or complex multi-axis CNC machining is required for the prototype.
- Low-Volume Production (5-50 units): 일반적으로 다음과 같은 범위입니다. 3 to 8 weeks or more. This accounts for potential batching for efficiency, the full suite of post-processing steps (including potentially longer processes like HIP and extensive machining if needed for all parts), and comprehensive quality assurance across the batch. Always confirm specific lead times with your chosen supplier based on the final part design and requirements.
Q2: Can metal AM shrouds meet the stringent quality and traceability requirements of the aerospace industry?
A2: Yes, absolutely, but it requires partnering with a capable and certified supplier. Meeting aerospace standards involves:
- Robust Quality Management System: Suppliers certified to AS9100 have demonstrated QMS processes specifically for aerospace.
- 프로세스 제어: Strict control and validation of printing parameters for consistent material properties.
- 재료 추적성: Documented tracking of metal powder batches from sourcing through production. Met3dp’s in-house powder production provides excellent control here.
- Comprehensive NDT: Utilizing methods like CT scanning, CMM, and DPT to verify internal integrity and dimensional accuracy.
- Documentation: Providing material certifications, inspection reports, and certificates of conformity. When these elements are in place, metal AM parts can meet and even exceed the quality requirements for many demanding aerospace applications.
Q3: How does the cost of a metal AM sensor shroud compare to one made by CNC machining?
A3: There’s no simple answer, as it depends heavily on several factors:
- 복잡성: For highly complex geometries with internal features, undercuts, or topology-optimized designs, AM is often more cost-effective, especially in low volumes, as it avoids complex machining setups or tooling.
- 볼륨: For very simple shroud designs produced in higher quantities, CNC machining from billet or casting may be cheaper due to faster cycle times per part once set up. However, AM avoids tooling costs associated with casting.
- Material: Material cost per unit volume is similar, but AM’s better buy-to-fly ratio (less waste) can be advantageous for expensive materials like Ti-6Al-4V, although powder cost can be higher than bar stock.
- Weight Savings: If AM enables significant weight reduction (via topology optimization/lattices), the higher manufacturing cost per part might be offset by lower launch costs or improved vehicle performance – a crucial factor in aerospace TCO (Total Cost of Ownership).
- 리드 타임: AM’s ability to produce parts quickly without tooling can provide significant cost savings in terms of project timelines and accelerating development. 결론: Get quotes for both methods based on your specific design, volume, and material to make an informed decision. AM often wins for complexity, customization, and low-to-medium volumes where its unique capabilities provide value.
Q4: What information is needed to get an accurate quote for printing a sensor shroud?
A4: To provide an accurate quote, a metal AM service provider like Met3dp typically needs:
- 3D CAD 모델: A high-quality model in a standard format (e.g., STEP, Parasolid).
- Material Specification: Clearly defined material (e.g., Ti-6Al-4V Grade 5, Stainless Steel 316L) and any specific standard it must meet (e.g., ASTM, AMS).
- 수량: Number of parts required (for prototypes and potential production runs).
- Technical Drawing (Recommended): A 2D drawing defining critical dimensions, tolerances (using GD&T), required surface finishes on specific features, and any threads or interfaces.
- 사후 처리 요구 사항: Specify necessary steps like heat treatment (stress relief, HIP, annealing), machining requirements, surface finish targets (Ra values), and any coating needs.
- Testing & Certification: Detail any required NDT (CT, DPT), dimensional inspection reports (CMM), material testing, or certification paperwork (e.g., Certificate of Conformity). Providing comprehensive information upfront enables the supplier to generate a precise quote and realistic lead time estimate.
Conclusion: Launching the Future of Sensor Protection with Metal Additive Manufacturing
The journey of a rocket from the launchpad to orbit or deep space is a testament to precision engineering operating under extreme duress. Protecting the sensitive instruments that guide, monitor, and gather data during this journey is paramount, and rocket sensor shrouds are the unsung heroes performing this critical task. As we’ve explored, 금속 적층 제조(AM) has emerged as a transformative technology for producing these essential components, offering compelling advantages over traditional methods.
By leveraging AM, aerospace engineers gain unprecedented 디자인의 자유 to create shrouds that are not only protective but also highly optimized. Techniques like topology optimization and lattice structures enable significant weight reduction – a primary driver in aerospace – without compromising structural integrity. The ability to consolidate multiple parts into a single printed component reduces complexity, assembly time, and potential failure points. Furthermore, AM accelerates development cycles through 신속한 프로토타이핑 and facilitates the use of advanced, high-performance materials like Ti-6Al-4V 및 316L 스테인리스 스틸, perfectly suited for the harsh thermal, mechanical, and corrosive environments of rocketry.
However, realizing these benefits requires a holistic approach. Success hinges on implementing Design for Additive Manufacturing (DFAM) principles, understanding and planning for essential post-processing steps (like heat treatment, HIP, machining, and NDT), and anticipating potential manufacturing 도전 과제. Most importantly, it demands strategic sourcing – selecting a metal AM partner with proven aerospace expertise, robust quality systems (AS9100), advanced equipment, superior material control, and the technical capability to deliver mission-ready parts.
Met3dp stands ready to be that partner. With our state-of-the-art SEBM printing technology, in-house production of high-purity metal powders, and decades of collective expertise, we provide comprehensive solutions tailored to the demanding needs of the aerospace industry. We collaborate with clients from design through final inspection, ensuring that the metal AM sensor shrouds we produce meet the highest standards of quality, reliability, and performance.
Metal additive manufacturing is no longer just a prototyping tool; it is a viable, powerful production method enabling the next generation of aerospace innovation. For protective sensor shrouds and countless other critical components, AM offers a pathway to lighter, stronger, more complex, and rapidly developed parts, truly launching the future of sensor protection and space exploration.
Ready to explore how metal AM can optimize your rocket sensor shrouds or other critical aerospace components? Contact Met3dp today to discuss your project requirements with our expert team.
공유
중국 칭다오에 본사를 둔 선도적인 적층 제조 솔루션 제공업체인 MET3DP Technology Co. 당사는 산업용 3D 프린팅 장비와 고성능 금속 분말을 전문으로 합니다.
관련 기사
Met3DP 소개
최근 업데이트
제품
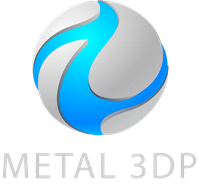
3D 프린팅 및 적층 제조용 금속 분말