적층 제조용 스테인리스강 분말
목차
스테인리스 스틸 파우더 기존 금속 제조 방식과 비교할 수 없는 적층 기술을 사용하여 복잡한 형상을 프린팅할 수 있습니다. 이 가이드에서는 스테인리스 파우더 조달에 필요한 합금 변형, 입자 사양, 특성 데이터, 가격 인사이트 및 비교 정보를 제공합니다.
스테인리스 스틸 파우더 소개
스테인리스 스틸 파우더가 제공하는 주요 기능:
- 복잡하고 가벼운 구성 요소 제작
- 우수한 내식성 달성
- 신속한 프로토타이핑 및 커스터마이징 지원
일반적으로 사용되는 합금은 다음과 같습니다:
- 304L - 뛰어난 내식성으로 비용 효율적임
- 316L - 몰리브덴을 첨가한 뛰어난 내식성
- 17-4PH - 고강도, 가장 단단한 스테인리스 분말
이 가이드는 스테인리스 파우더를 선택할 때 고려해야 할 사항을 제공합니다:
- 합금 구성 및 생산 방법
- 기계적 특성 테스트 데이터
- 입자 크기 분포 권장 사항
- 형태, 유량 및 겉보기 밀도
- 수량에 따른 공급업체 가격 범위
- 내식성 비교
- 솔리드 바스톡 관련 장단점
- 인쇄 매개변수 최적화에 대한 자주 묻는 질문
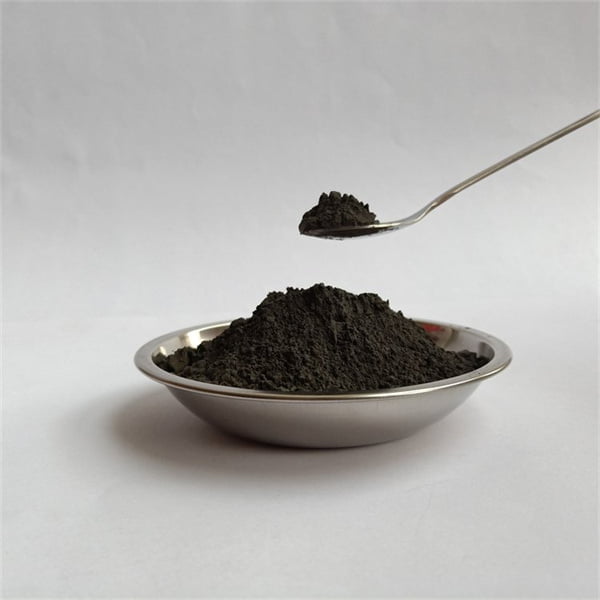
스테인리스 스틸 분말 조성물
표 1 은 주요 원소 첨가량에 따른 스테인리스 스틸 분말 합금 구성을 보여주며, 분말 제조업체마다 약간의 차이가 있습니다:
합금 | 주요 합금 원소 |
---|---|
304L | Cr, Ni |
316L | Cr, Ni, Mo |
17-4PH | Cr, Ni, Cu |
카바이드 침전을 방지하고 내식성 및 용접성을 유지하기 위해 304L 및 316L에는 탄소가 제한(≤0.03%)되어 있습니다.
17-4PH의 높은 탄소는 마르텐사이트 경화 열처리를 통해 강도를 높입니다.
기계적 특성 및 테스트 방법
속성 | 설명 | 테스트 방법(표준) | 적층 제조(AM)의 중요성 |
---|---|---|---|
겉보기 밀도 | 느슨하고 압축되지 않은 상태의 단위 부피당 분말 질량 | ASTM B922 | AM 공정에서 파우더 유동성 및 취급 용이성에 영향을 미칩니다. |
유동성 | 중력 하에서 분말 입자의 흐름 용이성 | ASTM B2132 | AM 빌드에서 패킹 밀도 및 파우더 레이어 균일성에 영향을 미칩니다. |
탭 밀도 | 표준화된 태핑 루틴 후 분말의 밀도 | ASTM B854 | 분말 포장 효율에 대한 기본 평가 제공 |
녹색 밀도 | 소결 전 압축된 파우더 본체의 밀도 | ASTM B970 | 3D 프린팅 부품의 최종 밀도 및 치수 정확도에 대한 영향(3D 프린팅 부품의 최종 밀도 및 치수 정확도에 대한 영향) |
소결 밀도 | 소결 후 분말 본체의 밀도 | ASTM B962 | 적층 가공 부품에서 원하는 기계적 특성과 내식성을 달성하는 데 필수적인 요소 |
입자 크기 분포 | 분말 집단에 존재하는 다양한 크기 | ASTM B822 | 분말 유동성, 패킹 거동 및 적층 제조 부품의 최종 미세 구조에 영향을 미칩니다. |
파티클 모양 | 개별 분말 입자의 형태학적 특성(구형, 각진 등) | 주사 전자 현미경(SEM) | 포장 밀도, 입자 간 결합 및 유동성에 대한 영향(포장 밀도, 입자 간 결합 및 유동성에 대한 영향) |
표면 거칠기 | 파우더 입자 표면의 미세한 변화 | 원자력 현미경(AFM) | 입자 간 결합 및 소결 거동에 영향을 줄 수 있습니다. |
화학 성분 | 파우더 소재의 원소 구성 | X선 형광(XRF) | 최종 재료 특성, 내식성 및 특정 응용 분야에 대한 적합성 결정 |
인장 강도 | 분말 야금(PM) 시편이 분리되기 전에 견딜 수 있는 최대 응력 | ASTM E8 | 높은 부하 지지 용량이 필요한 애플리케이션에 중요 |
수율 강도 | PM 시편이 소성 변형을 나타내는 응력 수준 | ASTM E8 | 소재의 탄성 한계를 이해하고 영구적인 변형을 예측하는 데 중요 |
신장 | 인장 시험에서 PM 시편이 파단되기 전에 경험하는 길이의 증가 비율 | ASTM E8 | 재료의 연성 및 파손되지 않고 변형되는 능력을 나타냅니다. |
압축 강도 | PM 시편이 압축 하중을 견디고 파쇄되기 전에 견딜 수 있는 최대 응력 | ASTM E9 | 압축력이 발생하는 애플리케이션에 필수 |
경도 | 단단한 물체에 의한 압흔에 대한 재료의 저항성 | ASTM E384 | 내마모성 및 표면 특성 관련 |
피로 강도 | 반복되는 로딩 및 언로딩 사이클에서 PM 시편이 고장 없이 견딜 수 있는 최대 응력 | ASTM E466 | 주기적인 스트레스를 받는 부품에 중요 |
골절 인성 | 크랙 전파에 저항하는 머티리얼의 능력 | ASTM E399 | 갑작스러운 장애를 용납할 수 없는 안전이 중요한 애플리케이션에 중요 |
스테인리스 스틸 분말 입자 크기 권장 사항
애플리케이션 | 입자 크기 중앙값(D₅₀) | 입자 크기 분포(PSD) | 모양 | 주요 고려 사항 |
---|---|---|---|---|
금속 적층 제조(레이저 용융, 전자빔 용융) | 15-45 미크론 | 좁음(D₅₀ 주변의 좁은 분포) | 구형 | – 흐름성: 구형 입자가 더 쉽게 흐르기 때문에 일관된 레이어 형성이 가능합니다. - 포장 밀도: 입자가 작을수록 더 단단하게 포장할 수 있어 최종 제품의 다공성을 줄일 수 있습니다. - 표면 마감: 극도로 미세한 입자(10마이크론 미만)는 표면 거칠기를 유발할 수 있습니다. - 레이저 흡수: 입자 크기는 레이저 흡수 효율에 영향을 미쳐 용융 거동에 영향을 줄 수 있습니다. |
금속 사출 성형(MIM) | 10-100 미크론 | 광범위(포장 및 소결에 더 넓은 분포) | 불규칙 | – 파우더 흐름: 불규칙한 모양이 서로 맞물려 사출 성형 시 파우더 흐름을 개선할 수 있습니다. - 포장 밀도: 더 넓은 크기 분포는 더 나은 패킹을 가능하게 하여 소결 중 수축을 줄입니다. - 소결 효율성: 입자가 클수록 완전한 소결을 방해하여 기계적 특성에 영향을 줄 수 있습니다. - 디바인딩: 입자가 크고 분포가 넓으면 결합제를 가두어 잔류 다공성을 유발할 수 있습니다. |
플라즈마 스프레이 | 45-150 미크론 | 광범위(MIM과 유사) | 불규칙 | – 내충격성: 입자가 클수록 최종 코팅의 내충격성이 향상됩니다. - 증착 효율성: 불규칙한 모양은 기계적 연동을 강화하여 코팅 접착력을 향상시킬 수 있습니다. - 스플랫 모폴로지: 입자 크기는 스프레이 중 스플랫 형성에 영향을 미쳐 코팅 미세 구조에 영향을 미칩니다. - 재코팅 가능성: 더 넓은 분포는 매끄럽고 레이어드된 코팅을 만드는 능력을 향상시킬 수 있습니다. |
열 분무(고속 산소 연료, 폭발 총) | 45-250 미크론 | 광범위(MIM과 유사) | 불규칙 | – 입금 비율: 입자가 클수록 증착 속도가 빨라집니다. - 파티클 속도: 고속 공정에서는 비행 중 파손을 최소화하기 위해 견고한 입자가 필요합니다. - 코팅 밀도: 분포가 넓으면 코팅 밀도가 높아지지만 입자 크기가 커지면 포장 효율에도 영향을 줄 수 있습니다. - 산화 저항: 입자 크기가 클수록 표면적이 줄어들어 잠재적으로 내산화성이 향상될 수 있습니다. |
적층 제조(바인더 제팅) | 10-50 미크론 | 좁음(레이저 용융과 유사) | 구형 | – 해상도: 입자가 작을수록 인쇄된 부품의 피처 디테일이 더욱 세밀해집니다. - 녹색 강도: 입자 크기와 분포는 소성되지 않은 부품의 강도에 영향을 줄 수 있습니다. - 바인더 호환성: 입자 표면적은 바인더 접착력과 인쇄성에 영향을 줄 수 있습니다. - 수분 민감도: 매우 미세한 분말은 수분 흡수에 더 취약하여 취급에 영향을 미칠 수 있습니다. |
분말 형태, 유량 및 밀도
속성 | 설명 | 분말 처리의 중요성 |
---|---|---|
분말 형태 | 개별 파우더 입자의 크기, 모양 및 표면 특성. | 형태는 적층 제조(AM)에서 패킹 밀도, 유동성 및 레이저 흡수성에 큰 영향을 미칩니다. 이상적으로는 표면이 매끄러운 구형 입자가 최상의 패킹 밀도와 흐름 특성을 제공합니다. 그러나 원자화 공정에서는 변화가 발생할 수 있습니다. 기체로 원자화된 분말은 더 구형인 경향이 있는 반면, 물로 원자화된 분말은 더 불규칙하고 흩어져 있는 형태를 나타냅니다. 또한 새틀라이트(큰 입자에 부착된 작은 입자) 및 새틀라이트와 같은 표면 특징은 흐름을 방해하고 적층 제조에서 레이저 용융 거동에 영향을 줄 수 있습니다. |
입자 크기 분포(PSD) | 파우더 배치 내의 입자 크기 변화를 통계적으로 표현한 것입니다. 일반적으로 누적 분포 곡선으로 표시하거나 특정 백분위수를 보고하여 표현합니다(예: d10 - 이 크기보다 작은 입자는 10%, d50 - 중앙값 입자 크기). | PSD는 파우더 베드 패킹에서 중요한 역할을 하며 AM 부품의 최종 밀도 및 기계적 특성에 영향을 미칩니다. 일관된 패킹과 레이저 용융 깊이를 위해서는 중간 크기(d50)가 잘 정의된 좁은 PSD가 선호됩니다. 반대로 분포가 넓으면 취급 시 분리(큰 입자가 미세한 입자에서 분리됨)가 발생하고 AM 공정에서 고르지 않은 용융이 발생할 수 있습니다. |
겉보기 밀도 및 탭 밀도 | * 겉보기 밀도: 용기에 자유롭게 부었을 때 단위 부피당 분말의 질량입니다. * 탭 밀도: 표준화된 탭핑 또는 진동 프로토콜을 통해 얻은 밀도입니다. | 이러한 특성은 분말의 포장 거동을 반영하며 효율적인 분말 취급 및 보관에 매우 중요합니다. 겉보기 밀도는 느슨한 패킹 상태를 나타내며, 탭 밀도는 기계적 교반을 통해 달성한 밀도 높은 패킹을 나타냅니다. 이 두 값의 차이를 Carr 각도라고 하며, 유동성을 간접적으로 측정할 수 있습니다. 카 각이 낮은 분말(탭 밀도가 높을수록 겉보기 밀도에 가까움)은 더 나은 유동 특성을 나타냅니다. |
유량 | 중력에 의해 분말이 오리피스 또는 호퍼를 통해 흐르는 속도입니다. | 유량은 적층 가공 및 금속 사출 성형(MIM)과 같은 다양한 분말 가공 기술에서 일관된 재료 공급을 위해 매우 중요합니다. 유동성이 좋으면 파우더 층이 원활하게 형성되고 빌드 프로세스 중 중단을 방지할 수 있습니다. 불규칙한 입자 모양, 새틀라이트의 존재, 수분 함량은 유동성을 저해할 수 있습니다. 제조업체는 파우더 흐름을 개선하기 위해 윤활제와 같은 유동성 첨가제를 사용하는 경우가 많습니다. |
파우더 밀도 | 입자 사이의 공극을 제외한 고체 입자 자체의 단위 부피당 분말의 질량입니다. | 분말 밀도는 특정 스테인리스 스틸 구성에 내재된 재료 특성입니다. 이는 소결 또는 용융 후 완제품에서 얻을 수 있는 최종 밀도에 영향을 미칩니다. 일반적으로 분말 밀도가 높을수록 최종 제품의 밀도가 높아지고 기계적 특성이 향상됩니다. |
스테인리스 스틸 파우더 가격
팩터 | 설명 | 가격에 미치는 영향 |
---|---|---|
등급 | 스테인리스 스틸의 특정 유형으로, 3자리 숫자로 표시됩니다(예: 304, 316L, 17-4PH). 등급에 따라 내식성, 강도 및 성형성이 다릅니다. | 몰리브덴을 첨가하여 내식성을 강화한 316L과 같은 고급 스테인리스 스틸 파우더는 일반적으로 304와 같은 기본 등급에 비해 프리미엄 가격이 책정됩니다. |
입자 크기 및 분포 | 분말 입자의 크기와 균일성. 미크론(μm) 또는 메쉬 크기(체의 선형 인치당 구멍의 수)로 측정되는 입자 크기는 최종 제품의 특성과 제조 공정에 큰 영향을 미칩니다. | 일반적으로 더 미세한 분말(더 작은 미크론/더 높은 메시 크기)은 더 좁은 입자 크기 분포를 달성하는 데 필요한 추가 처리로 인해 비용이 더 많이 듭니다. 하지만 더 미세한 파우더를 사용하면 3D 프린팅 부품에서 복잡한 디테일과 매끄러운 표면 마감을 구현할 수 있습니다. |
표면적 | 단위 중량당 분말 입자의 총 표면적인 입자 크기와 밀접한 관련이 있습니다. 표면적이 큰 분말은 반응성이 더 높으며 더 엄격한 취급 프로토콜이 필요한 경향이 있습니다. | 표면적이 넓은 분말은 오염이나 습기 흡수를 방지하기 위한 특수 취급 및 보관 요건으로 인해 추가 비용이 발생할 수 있습니다. |
제조 프로세스 | 스테인리스 분말을 생산하는 데 사용되는 방법. 일반적인 기술로는 원자화(가스 또는 물) 및 화학 기상 증착(CVD)이 있습니다. | 분무 공정은 일반적으로 더 안정적이고 비용 효율적인 반면, CVD는 더 미세하고 순수한 분말을 생산하지만 더 높은 가격대를 형성합니다. |
순도 | 원치 않는 원소의 존재를 최소화한 분말의 화학적 조성. | 산소, 질소 및 기타 불순물 함량이 낮은 고순도 분말은 제조 관리가 더 엄격하기 때문에 비용이 더 많이 드는 경우가 많습니다. |
구형 모폴로지 | 파우더 입자의 모양입니다. 구형 입자는 우수한 유동 특성과 패킹 밀도를 제공하여 인쇄성과 재료 활용도를 향상시킵니다. | 구형 스테인리스 스틸 분말은 일반적으로 추가 가공 단계가 필요하기 때문에 불규칙한 모양의 입자에 비해 가격이 더 비쌉니다. |
수량 | 구매한 스테인리스 스틸 파우더의 양입니다. | 대량 구매는 일반적으로 공급업체가 제공하는 규모의 경제로 인해 상당한 가격 인하 혜택을 누릴 수 있습니다. |
시장 변동 | 크롬과 니켈과 같은 원자재의 글로벌 수급 역학은 스테인리스 스틸 원료의 기본 가격에 큰 영향을 미칩니다. | 수요가 많거나 공급망에 차질이 생기면 스테인리스 분말의 가격이 인상될 수 있습니다. |
공급업체 | 파우더 제조업체의 평판과 전문성. 엄격한 품질 관리 절차를 갖춘 유명 브랜드는 잘 알려지지 않은 공급업체에 비해 약간 더 높은 가격을 책정할 수 있습니다. | 평판이 좋은 공급업체는 기술 지원 및 자재 인증과 같은 추가 서비스를 제공하는 경우가 많으므로 약간의 가격 프리미엄을 정당화할 수 있습니다. |
스테인리스 스틸 분말 내식성
속성 | 설명 | 내식성에 미치는 영향 |
---|---|---|
크롬 함량 | 스테인리스 스틸의 내식성의 핵심 요소입니다. 산소에 노출되면 표면에 얇고 보이지 않는 산화 크롬 층을 형성하여 추가 산화(녹)를 막는 장벽 역할을 합니다. | 크롬 함량(일반적으로 10.5% 이상)이 높을수록 내식성이 향상됩니다. 스테인리스 분말의 등급마다 크롬 함량이 다르기 때문에 특정 환경에 맞게 사용할 수 있습니다. |
몰리브덴 | 금속에 깊은 구멍을 만드는 국부적인 형태의 공격인 피팅 부식에 대한 저항력을 향상시키기 위해 종종 첨가됩니다. 몰리브덴은 특히 염화물이 포함된 환경(예: 바닷물)에서 산화 크롬 층의 안정성을 향상시킵니다. | 몰리브덴이 함유된 스테인리스강 분말은 해양 분야, 염화물이 포함된 화학 공정 및 염분이 높은 환경에 이상적입니다. |
니켈 | 특히 고온 환경에서 전반적인 내식성에 기여합니다. 니켈은 패시브 산화물 층의 안정성을 유지하고 환원산에 대한 저항성을 향상시킵니다. | 니켈 함유 스테인리스강 분말은 고온 산성 환경이나 고압 증기와 관련된 응용 분야에 적합합니다. |
분말 제조 방법 | 분말을 만드는 데 사용되는 공정은 미세 구조와 결과적으로 내식성에 영향을 미칠 수 있습니다. 일반적인 방법인 가스 분무는 입자 내에 산소를 가두어 잠재적으로 국부적인 부식을 일으킬 수 있습니다. | 물 분무와 같이 내부 산화를 최소화하는 방법으로 생산된 분말을 선택하면 부식 성능을 향상시킬 수 있습니다. |
다공성 | 분말 입자를 결합하는 공정인 소결은 최종 제품 내에 작은 구멍을 남길 수 있습니다. 이러한 기공이 오염 물질이나 습기를 가두면 부식이 시작되는 장소가 될 수 있습니다. | 최적화된 입자 크기 분포와 적절한 소결 파라미터를 갖춘 분말을 선택하면 다공성을 최소화하여 내식성을 향상시킬 수 있습니다. |
표면 마감 | 완성된 구성 요소의 표면 지형은 환경과 얼마나 쉽게 상호작용하는지에 영향을 미칠 수 있습니다. 표면이 거칠수록 오염 물질과 습기가 달라붙을 수 있는 면적이 넓어져 부식 위험이 높아집니다. | 연마 또는 특정 제조 기술을 통해 더 매끄러운 표면 마감을 구현하면 이러한 잠재적 부위를 최소화하여 내식성을 향상시킬 수 있습니다. |
입자 크기 | 소결된 부품 내 개별 금속 입자의 크기는 부식 거동에 영향을 미칠 수 있습니다. 일반적으로 입자 크기가 미세할수록 부식제에 대한 투과성이 낮은 장벽을 형성하기 때문에 내식성이 향상됩니다. | 소결 시 미세 입자 구조를 구현하는 데 최적화된 파우더를 선택하면 부품의 내식성을 향상시킬 수 있습니다. |
장단점: 파우더와 솔리드 바스톡
표 7
장점 | 단점 | |
---|---|---|
스테인리스 스틸 파우더 | 복잡한 모양 | 더 높은 비용 |
뛰어난 내식성 특성 | 후처리 | |
경량화 | 인쇄 매개변수 최적화 | |
스테인리스 스틸 솔리드 바 | 비용 효율적 | 모양 제한 |
가용성 | 훨씬 더 무겁습니다. | |
가공성 | 재료 낭비 |
일반적으로 스테인리스강 분말은 내식성과 경량화가 중요한 소량 복합 부품의 경우 더 높은 가격을 정당화합니다. 바 형태는 생산량이 많은 사용 사례에서 단순한 형상을 위한 경제성을 제공합니다.
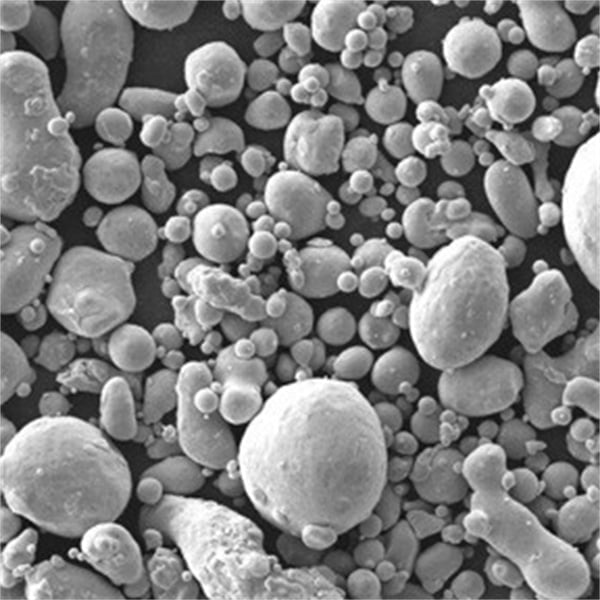
자주 묻는 질문
표 8 - 자주 묻는 질문:
자주 묻는 질문 | 답변 |
---|---|
테스트 보고서를 검토해야 하나요? | 예, 분말 인증 데이터를 면밀히 검토합니다. |
어떤 크기의 파우더 입자로 시작해야 하나요? | 견고한 인쇄를 위한 25-45 미크론 |
일관성에 영향을 미치는 요소는 무엇인가요? | 생분말 생산 기술이 변동성에 미치는 영향 |
처음에 파우더를 얼마나 구매해야 하나요? | 소규모로 시작하여 인쇄 프로세스 검증 |
표 9 - 애플리케이션 중심의 조언:
자주 묻는 질문 | 답변 |
---|---|
식품 등급의 스테인리스 장비를 인쇄하려면 매개 변수를 어떻게 조정해야 합니까? | 낮은 표면 거칠기를 위한 최적화 및 틈새 제거 |
해양 부품의 다공성을 줄일 수 있는 후처리에는 어떤 것이 있나요? | 내식성을 극대화하기 위해 열간 등방성 프레스를 고려하십시오. |
하중을 견디는 부품의 항복 강도를 극대화하는 합금은 무엇입니까? | 17-4PH 강수량 경화 스테인리스 스틸 |
고온 용광로 부품에 가장 적합한 스테인리스 분말은 무엇입니까? | 316L 파우더로 뛰어난 내산화성 제공 |
공유
페이스북
트위터
LinkedIn
WhatsApp
이메일
중국 칭다오에 본사를 둔 선도적인 적층 제조 솔루션 제공업체인 MET3DP Technology Co. 당사는 산업용 3D 프린팅 장비와 고성능 금속 분말을 전문으로 합니다.
관련 기사
Met3DP 소개
최근 업데이트
제품
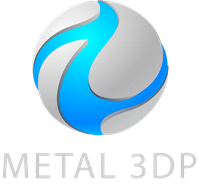
3D 프린팅 및 적층 제조용 금속 분말