3D Printed Corrosion-Resistant Valve Seats for Marine Applications
목차
Introduction: The Critical Role of Valve Seats in Marine Environments
The maritime industry, a cornerstone of global trade and transportation, operates within one of the most demanding and corrosive environments on Earth. Saltwater, constant humidity, fluctuating temperatures, biofouling, and immense pressures place extraordinary stress on every component aboard a vessel, from the hull plating to the most intricate internal engine parts. Among these critical components, valve seats play a vital, often unseen, role in ensuring the safety, efficiency, and reliability of numerous onboard systems. Whether controlling the flow of fuel in main propulsion engines, managing ballast water, regulating cooling systems, or handling corrosive cargo, the integrity of a valve seat is paramount. Failure is not merely an inconvenience; it can lead to catastrophic system breakdowns, costly downtime, environmental hazards, and even endangerment of the crew and vessel.
Traditionally, marine valve seats have been manufactured using methods like casting, forging, and machining. While these processes have served the industry for decades, they often come with limitations, particularly concerning material waste, design complexity, lead times for specialized components, and the ability to rapidly iterate or produce replacement parts on demand. Furthermore, achieving the specific material properties required for extreme corrosion resistance and durability against cavitation and wear in diverse marine applications can be challenging and costly with conventional manufacturing. The constant exposure to chloride-rich seawater, potentially combined with aggressive chemicals, high pressures, and mechanical stresses, demands materials and manufacturing processes that can deliver exceptional performance without compromise.
Enter metal additive manufacturing (AM), commonly known as 금속 3D 프린팅. This transformative technology offers a paradigm shift in how critical components like marine valve seats can be designed, produced, and maintained. By building parts layer by layer directly from digital designs using specialized metal powders, AM enables the creation of complex geometries, optimizes material usage, allows for rapid prototyping and production, and facilitates the use of advanced, highly corrosion-resistant alloys specifically tailored for harsh marine conditions. This technological leap empowers marine engineers and procurement managers to source or produce valve seats that not only meet but often exceed the performance of their traditionally manufactured counterparts, offering enhanced durability, potentially lower lifecycle costs, and greater design freedom.
Companies at the forefront of this revolution, such as Met3dp, are leveraging decades of expertise in metal additive manufacturing to provide comprehensive solutions. With advanced capabilities in producing high-quality metal powders using techniques like gas atomization and Plasma Rotating Electrode Process (PREP), and offering industry-leading printing equipment, Met3dp enables the production of dense, high-performance marine components. The focus is shifting towards materials specifically chosen for their resilience in saltwater, such as specialized copper-nickel alloys and marine-grade stainless steels. This blog post delves into the specifics of using metal 3D 프린팅 for manufacturing corrosion-resistant valve seats, exploring the applications, advantages, key materials like CuNi30Mn1Fe and 316L, design considerations, quality aspects, and how to partner with the right additive manufacturing supplier to navigate the unique challenges of the maritime sector. For procurement managers seeking reliable marine valve seat suppliers or engineers exploring advanced manufacturing solutions, understanding the potential of AM is becoming increasingly crucial.
Applications: Where are Corrosion-Resistant Valve Seats Essential at Sea?
Valve seats are fundamental components within virtually any system that controls the flow of liquids or gases. In the demanding marine environment, their function is amplified by the need for exceptional durability and resistance to aggressive corrosion and wear mechanisms. The failure of a valve seat can compromise critical operations, leading to potential safety hazards, operational inefficiencies, and significant maintenance costs. Metal 3D printing offers a powerful solution for producing high-performance, corrosion-resistant valve seats tailored for a wide array of specific maritime applications. Identifying where these components are most crucial helps underscore the value proposition of additive manufacturing for wholesale buyers, marine engineering firms, and ship maintenance operators looking for durable marine valve solutions.
Here’s a breakdown of key application areas where 3D printed corrosion-resistant valve seats offer significant advantages:
- Main Propulsion and Auxiliary Engines:
- Function: Control the intake of air/fuel mixture and the exhaust of combustion gases within the engine cylinders. Engine valve seats create the seal between the valve and the cylinder head.
- 도전 과제: Extreme temperatures, high pressures, constant mechanical impact, thermal cycling, and potential corrosion from fuel contaminants (like sulfur) and combustion byproducts. Seawater cooling systems adjacent to these components also introduce corrosive elements.
- AM 이점: Ability to print valve seats from high-temperature, wear-resistant alloys (potentially specialized superalloys or specific grades of steel/bronze not covered by the primary recommendation but possible with AM) that can withstand the harsh combustion environment. Geometric optimization via AM can potentially improve flow dynamics or cooling channel integration near the seat area. Using materials like specific grades of stainless steel (like 316L for adjacent cooling components) or potentially nickel-based superalloys (though CuNi is less common inside combustion chambers) ensures longevity. For auxiliary systems using seawater directly, CuNi alloys excel.
- Seawater Cooling Systems:
- Function: Regulate the flow of seawater used to cool engines, generators, HVAC systems, and other onboard equipment. Valves control intake, distribution, and discharge.
- 도전 과제: Direct and constant exposure to highly corrosive seawater, potential for biofouling (marine growth), erosion from suspended particles (sand, silt), and galvanic corrosion if dissimilar metals are used without proper design.
- AM 이점: 다음과 같은 재료 CuNi30Mn1Fe are specifically designed for outstanding resistance to seawater corrosion and biofouling. 3D printing allows for the creation of valve seats with optimized flow paths to minimize erosion and potentially integrated features that deter marine growth settlement. The ability to rapidly produce replacement seats for critical cooling systems minimizes vessel downtime. This is a prime area for CuNi valve seat manufacturers using AM.
- Ballast Water Management Systems (BWMS):
- Function: Control the intake, treatment, holding, and discharge of ballast water, essential for maintaining vessel stability. Modern BWMS often involve treatment processes (UV, electro-chlorination, chemical dosing) that can introduce additional corrosive elements.
- 도전 과제: Handling large volumes of seawater from varying global ports (different salinity, temperature, contaminants), potential exposure to treatment chemicals, and regulations requiring high reliability to prevent the transfer of invasive species.
- AM 이점: Production of valve seats from 316L 스테인리스 스틸 또는 CuNi30Mn1Fe, depending on the specific location within the BWMS and the treatment method used. AM allows for complex valve seat designs required for specialized control valves within the treatment process, ensuring compliance and system integrity. Sourcing marine grade 316L components via AM provides a reliable option.
- Fuel Handling and Transfer Systems:
- Function: Control the flow of various fuel types (MGO, HFO, potentially LNG or future fuels) from storage tanks to settling tanks, purifiers, and finally to the engines or boilers.
- 도전 과제: Exposure to different fuel chemistries, potential contaminants (water, microbes), varying temperatures, and the need for precise flow control and tight sealing to prevent leaks, which pose fire hazards.
- AM 이점: Ability to print valve seats from materials compatible with specific fuel types, ensuring chemical resistance and long-term sealing integrity. For systems involving seawater contamination risks (e.g., in purifiers), corrosion-resistant materials like 316L are crucial. Wholesale valve seat orders for fuel systems benefit from AM’s ability to produce consistent quality parts.
- Cargo Handling Systems (especially for chemical/product tankers):
- Function: Control the loading, unloading, and transfer of liquid or gaseous cargo, which can range from crude oil and refined products to highly corrosive chemicals.
- 도전 과제: Extreme chemical corrosion from diverse cargo types, potential for high pressures and temperatures, stringent safety requirements to prevent cargo contamination or environmental spills.
- AM 이점: Metal 3D printing allows for the selection of highly specialized alloys (potentially beyond CuNi and 316L, such as Hastelloy or Inconel, depending on the cargo – Met3dp’s portfolio includes various superalloys) offering superior resistance to specific chemical agents. AM enables the creation of custom valve seat designs tailored to unique cargo valve requirements, ensuring safety and efficiency. Additive manufacturing marine components suppliers like Met3dp can offer material expertise for such demanding applications.
- Firefighting Systems:
- Function: Control the distribution of seawater or foam through the ship’s firefighting mains and sprinkler systems. Reliability is absolutely critical.
- 도전 과제: Prolonged standby periods followed by sudden high-pressure operation, constant exposure to seawater within the pipes, and the absolute need for functionality in an emergency.
- AM 이점: CuNi30Mn1Fe 및 316L are excellent choices due to their resistance to seawater corrosion during standby. 3D printing ensures the valve seats maintain their integrity over long periods, guaranteeing the system’s readiness. The ability to quickly print replacement parts for critical safety systems is invaluable.
- Sanitary and Potable Water Systems:
- Function: Control the flow of fresh (potable) water and the discharge of grey/black water.
- 도전 과제: Need for materials safe for potable water contact (requiring specific certifications), resistance to scaling, and corrosion resistance, particularly in grey/black water systems which can be surprisingly corrosive.
- AM 이점: 316L 스테인리스 스틸 is widely accepted for potable water applications and offers good general corrosion resistance. AM allows for efficient production of valve seats for these essential domestic systems onboard.
Table: Marine Valve Seat Applications & AM Suitability
적용 분야 | 주요 과제 | Recommended AM Materials (Primary) | Why AM is Advantageous | Relevant Keywords for Sourcing |
---|---|---|---|---|
Main/Auxiliary Engines | High Temp, Pressure, Wear, Thermal Cycling | Specialized Alloys, 316L (cooling) | High-temp material capability, geometric optimization, potential cooling integration | Engine Valve Seat Supplier, High-Performance Seats |
Seawater Cooling Systems | Extreme Corrosion, Biofouling, Erosion | CuNi30Mn1Fe, 316L | Superior seawater resistance, anti-biofouling, custom flow paths, rapid replacement | CuNi Valve Seat Manufacturer, Marine Cooling Parts |
Ballast Water Management (BWMS) | Varying Seawater, Treatment Chemicals, Reliability | CuNi30Mn1Fe, 316L | Chemical resistance, complex geometries for treatment valves, regulatory compliance | BWMS Components Supplier, Marine Grade 316L |
Fuel Handling & Transfer | Fuel Compatibility, Contaminants, Leak Prevention | 316L, Other specific alloys | Chemical resistance, tight sealing, fuel compatibility, consistent quality | Marine Fuel Valve Parts, Wholesale Valve Seats |
Chemical Cargo Handling | Extreme Chemical Corrosion, High P/T, Safety | Specialized Alloys (e.g., Hastelloy), 316L | Superior chemical resistance, custom designs for specific cargo, safety assurance | Chemical Tanker Valve Components, AM Superalloys |
Firefighting Systems | Standby Corrosion, High Pressure, Reliability | CuNi30Mn1Fe, 316L | Long-term seawater resistance, guaranteed readiness, rapid critical part replacement | Marine Fire System Valves, Reliable Valve Seats |
Sanitary/Potable Water | Potable Water Safety, Scaling, Corrosion | 316L | Food/water grade material availability, efficient production, general corrosion resistance | Potable Water Valve Components, 316L Supplier |
시트로 내보내기
Understanding these diverse and demanding applications highlights why the selection of the right material and manufacturing process is critical. Metal 3D printing, particularly using highly corrosion-resistant powders like CuNi30Mn1Fe and 316L produced via advanced methods like those employed by Met3dp, offers tailored solutions that enhance the durability, reliability, and performance of valve seats across the full spectrum of marine operations. Procurement managers and engineers looking for bulk marine valve seat orders or specialized corrosion-resistant component manufacturing should strongly consider the capabilities of additive manufacturing.
Advancing Marine Engineering: Why Use Metal 3D Printing for Valve Seats?
The maritime industry, while steeped in tradition, is increasingly embracing technological innovation to enhance efficiency, safety, and sustainability. Metal additive manufacturing represents a significant leap forward, offering compelling advantages over conventional methods like casting, forging, and subtractive machining, especially for critical components like corrosion-resistant valve seats. These advantages resonate strongly with engineers seeking performance improvements and procurement managers focused on lifecycle costs, supply chain resilience, and sourcing from reliable 금속 3D 프린팅 서비스 제공업체.
Let’s explore the key reasons why metal AM is becoming the preferred choice for manufacturing high-performance marine valve seats:
- Unparalleled Design Freedom and Complexity:
- Traditional Limits: Casting and machining often restrict designs to what can be easily molded, cast, or reached with cutting tools. Complex internal channels, intricate sealing geometries, or weight-optimized structures can be difficult, costly, or impossible to produce.
- AM 이점: Metal 3D printing builds parts layer by layer, allowing for the creation of highly complex and organic shapes without the constraints of traditional tooling. This enables:
- Optimized Flow Paths: Designing valve seats with smoother internal transitions and geometries that minimize turbulence, pressure drop, and erosion, enhancing valve efficiency and longevity.
- Integrated Features: Incorporating features directly into the seat, such as enhanced sealing surfaces, anti-rotation locks, or even integrated cooling channels (in specific high-heat applications), reducing part count and assembly complexity.
- 토폴로지 최적화: Using software to remove material from low-stress areas, resulting in lighter components without compromising strength – particularly relevant for weight-sensitive applications on vessels.
- 사용자 지정: Easily tailoring valve seat designs for specific performance requirements or retrofitting into existing systems without extensive re-tooling.
- Access to Advanced Materials and Optimized Microstructures:
- Traditional Limits: While many alloys can be cast or forged, achieving fine-grained, homogenous microstructures optimized for specific properties like corrosion resistance and wear can be challenging. Certain advanced or difficult-to-machine alloys may be impractical or uneconomical to process conventionally.
- AM 이점: Metal AM processes, particularly Powder Bed Fusion (PBF) methods like Selective Laser Melting (SLM) and Electron Beam Melting (EBM – a specialty of providers like Met3dp), involve rapid melting and solidification. This can result in:
- Fine-Grained Microstructures: Often leading to superior mechanical properties (strength, fatigue resistance) compared to cast equivalents.
- 재료 효율성: Using only the material needed for the part, significantly reducing waste compared to subtractive machining, especially with expensive marine-grade alloys like CuNi or specialized steels.
- Wider Material Palette: Enabling the use of advanced alloys specifically designed for additive manufacturing, including those optimized for extreme corrosion resistance (like the recommended CuNi30Mn1Fe and 316L) or high-temperature performance. Met3dp’s expertise in producing high-quality powders, including innovative alloys like TiNi, TiTa, CoCrMo, and various superalloys, using advanced Gas Atomization and PREP technology ensures optimal material input for demanding applications.
- Supply Chain Agility and Reduced Lead Times:
- Traditional Limits: Manufacturing valve seats, especially custom or low-volume replacements, often involves long lead times due to tooling requirements (pattern making for casting, fixture setup for machining) and complex supply chains. This can lead to extended vessel downtime during repairs.
- AM 이점:
- Tooling Elimination: AM builds parts directly from digital files, eliminating the need for physical tooling, dramatically reducing setup time and cost for new or modified designs.
- 신속한 프로토타이핑: Quickly producing prototypes for fit and function testing before committing to larger production runs.
- 주문형 생산: Manufacturing parts when and where they are needed, enabling a “digital inventory” model. This reduces the need for large physical stocks of spares and allows for faster delivery of critical replacement parts, minimizing costly delays for marine component distributors and end-users.
- Decentralized Manufacturing: Potentially printing parts closer to the point of need (e.g., major ports or shipyards with AM facilities), further shortening logistics chains.
- Enhanced Performance and Durability:
- Traditional Limits: Achieving the ideal balance of corrosion resistance, wear resistance, and mechanical strength through conventional methods can involve compromises or costly multi-step processes. Inconsistent material properties in castings (e.g., porosity) can lead to premature failure.
- AM 이점:
- Optimized Material Properties: As mentioned, AM can produce dense parts with fine microstructures, leading to improved mechanical performance and potentially superior corrosion and wear resistance compared to some traditional methods, especially standard castings.
- Design for Performance: Leveraging design freedom to create seats with better sealing capabilities, reduced susceptibility to cavitation damage, and improved overall valve performance.
- Material Combinations (Future Potential): Advanced AM techniques may eventually allow for functionally graded materials, where different properties (e.g., high surface hardness with a tougher core) could be built into a single component, though this is still emerging for widespread industrial use.
- Lifecycle Cost Reduction:
- Traditional View: AM part cost might initially seem higher on a per-part basis compared to mass-produced cast items.
- AM Advantage (Lifecycle Perspective):
- 가동 중지 시간 감소: Faster availability of replacement parts significantly cuts costs associated with vessel inactivity.
- Increased Component Life: Superior materials and optimized designs can lead to longer-lasting valve seats, reducing the frequency of replacement and associated labor costs.
- Lower Inventory Costs: Shifting from physical to digital inventory reduces warehousing and management expenses.
- 재료 낭비 감소: Minimizing scrap, especially with expensive alloys, lowers overall material costs.
- Consolidated Assembly: Integrating features can reduce the number of components, simplifying assembly and reducing potential failure points.
Table: Comparing Traditional Manufacturing vs. Metal AM for Marine Valve Seats
기능 | Traditional Manufacturing (Casting/Machining) | Metal Additive Manufacturing (PBF) | Advantage for Marine Applications |
---|---|---|---|
자유로운 디자인 | Limited by tooling, mold constraints, tool access | High degree of geometric complexity, internal channels, optimization | Optimized flow, integrated features, weight reduction, customization |
자료 사용량 | High waste (machining), casting yield considerations | High efficiency, near-net shape production | Reduced cost for expensive alloys (CuNi, 316L), sustainability |
리드 타임 | Long (tooling, setup), especially for custom/low volume | Short (no tooling), rapid prototyping, on-demand production | Reduced vessel downtime, supply chain agility, faster repairs |
재료 | Established alloys, potential microstructure limitations (casting) | Wide range, including advanced/AM-specific alloys, fine microstructures | Access to optimal corrosion/wear-resistant materials (CuNi30Mn1Fe, 316L), enhanced properties |
Complexity Cost | Increases significantly with geometric complexity | Less dependent on complexity, more on volume/height | Economical production of complex, high-performance designs |
인벤토리 | Requires physical stock of spares | Enables digital inventory | Lower warehousing costs, reduced obsolescence risk |
프로토타이핑 | Slow and expensive | Fast and relatively inexpensive | Quicker design validation and iteration |
이상적인 볼륨 | High volume production often more cost-effective | Cost-effective for low-to-medium volumes, custom parts, replacements | Suits the need for specialized marine components and urgent spares, beneficial for AM service bureaus |
시트로 내보내기
In summary, metal 3D printing offers a compelling suite of technical and logistical advantages for producing corrosion-resistant marine valve seats. From enabling superior designs and materials to drastically improving supply chain responsiveness, AM empowers the maritime industry to build more reliable, efficient, and resilient vessels. Partnering with knowledgeable additive manufacturing solutions providers like Met3dp, who possess deep expertise in both materials science and printing processes, is key to unlocking the full potential of this technology for critical marine applications.
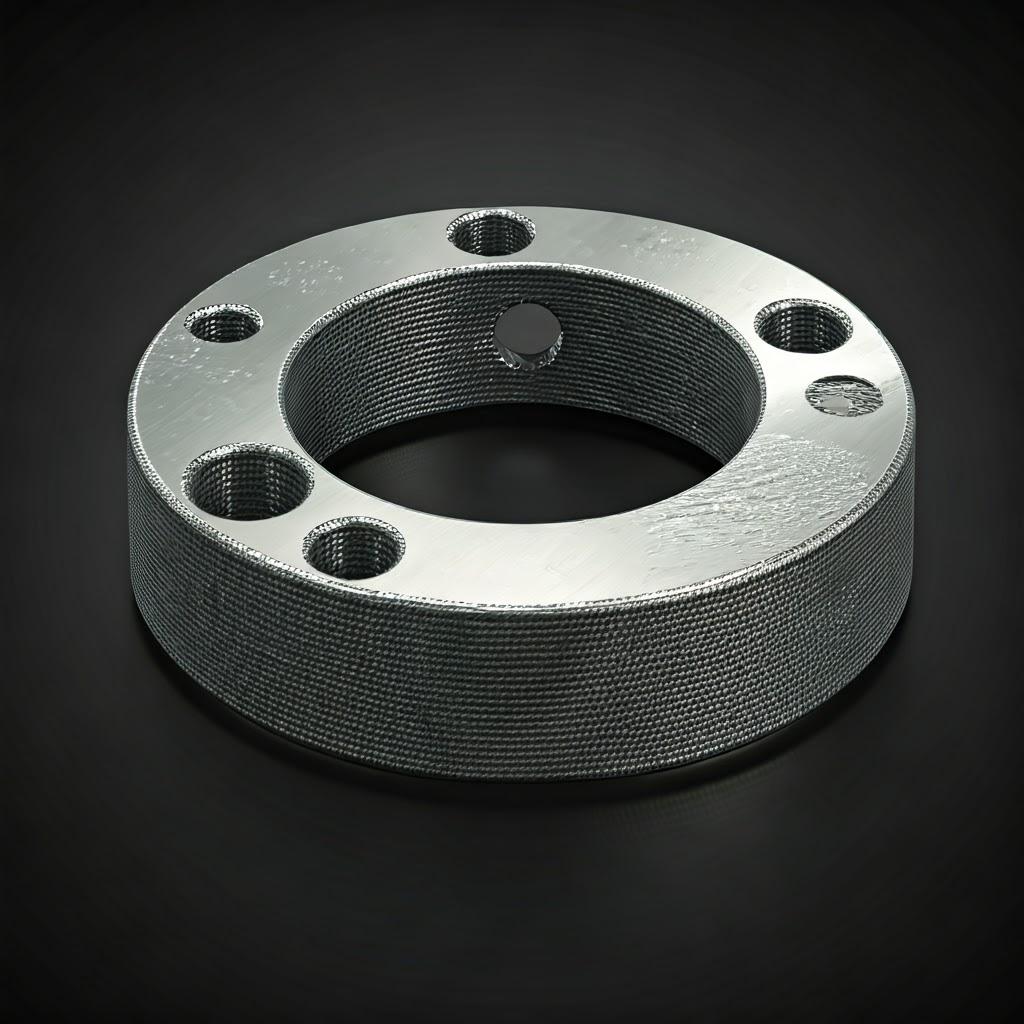
Material Focus: CuNi30Mn1Fe and 316L Stainless Steel for Optimal Marine Performance
The selection of the right material is arguably the most critical factor in ensuring the longevity and reliability of valve seats operating in the harsh marine environment. Constant exposure to corrosive seawater, along with potential biofouling, erosion, and varying chemical exposures, demands materials specifically engineered for these conditions. While metal additive manufacturing opens the door to a wide range of alloys, two stand out for their proven performance and suitability for 3D printing marine valve seats: Copper-Nickel alloy CuNi30Mn1Fe (often referred to as 90/10 Copper-Nickel with iron and manganese additions) 및 316L 스테인리스 스틸. Understanding their properties, benefits, and ideal applications is crucial for engineers designing systems and procurement managers sourcing marine grade metal components.
1. CuNi30Mn1Fe (C71500 type alloy): The Seawater Specialist
This copper-nickel alloy, typically containing around 30% nickel, 1% manganese, and 1% iron, is renowned for its exceptional resistance to seawater corrosion and biofouling. It’s a workhorse material in marine engineering, widely used for piping, heat exchangers, and valve components.
- Key Properties & Benefits for Marine Valve Seats:
- Outstanding Seawater Corrosion Resistance: CuNi alloys form a stable, adherent protective film when exposed to seawater. This film provides excellent resistance to general corrosion, pitting, and crevice corrosion, even in polluted or high-velocity seawater flows. The presence of iron and manganese further enhances its resistance to erosion-corrosion caused by turbulent flow or suspended solids.
- Inherent Biofouling Resistance: Copper ions that slowly leach from the surface are toxic to many marine organisms (algae, barnacles, mussels). This significantly reduces the attachment and growth of marine life on the valve seat surface, preventing blockages, maintaining sealing efficiency, and reducing the need for frequent cleaning or harsh anti-fouling treatments. This is a major advantage over stainless steels in static or low-flow conditions.
- Good Mechanical Strength and Ductility: While not as strong as high-strength steels, CuNi30Mn1Fe offers sufficient strength and toughness for many valve seat applications, capable of handling typical pressures found in seawater systems. Its ductility also makes it resistant to brittle fracture.
- Excellent Fabricability (Including AM): This alloy is readily weldable and processable using conventional methods, and it has proven highly suitable for metal AM processes like Powder Bed Fusion (PBF). High-quality, spherical CuNi30Mn1Fe powder is available from specialized suppliers like Met3dp, produced using advanced atomization techniques to ensure good flowability and high packing density during printing, leading to dense, reliable parts.
- Good Thermal Conductivity: Useful in applications where heat dissipation might be a factor, although less critical for typical valve seat functions compared to heat exchangers.
- Ideal Applications for 3D Printed CuNi30Mn1Fe Valve Seats:
- Seawater Cooling Systems (intake, circulation, discharge valves)
- Ballast Water Management Systems (especially intake and discharge sides)
- Firefighting Systems (seawater mains)
- Bilge Water Systems
- Certain low-pressure hydraulic systems using water-glycol fluids.
- 고려 사항:
- Lower strength compared to stainless steels or superalloys.
- Can be susceptible to galvanic corrosion if directly coupled with significantly more noble metals (like titanium or high-nickel alloys) in an electrolyte (seawater) without proper design considerations (e.g., insulation).
- Higher cost than standard stainless steels, making material efficiency through AM particularly attractive. Sourcing from a reliable CuNi powder supplier is essential for consistent quality.
2. 316L Stainless Steel (UNS S31603): The Versatile Corrosion Fighter
316L is an austenitic chromium-nickel stainless steel containing molybdenum, which significantly enhances its resistance to pitting and crevice corrosion, particularly in chloride-rich environments like seawater. The “L” denotes low carbon content (typically <0.03%), which minimizes sensitization (chromium carbide precipitation at grain boundaries) during welding or thermal cycles involved in AM, preserving its corrosion resistance.
- Key Properties & Benefits for Marine Valve Seats:
- Excellent General and Pitting Corrosion Resistance: The combination of chromium, nickel, and molybdenum provides robust resistance to corrosion from seawater, various chemicals, and process fluids encountered in marine applications. It significantly outperforms standard 304 stainless steel in marine environments.
- 높은 강도와 견고함: 316L offers good mechanical strength, ductility, and toughness across a wide temperature range, making it suitable for handling higher pressures and mechanical stresses compared to CuNi alloys.
- Good Fabricability and Weldability: Like CuNi, 316L is readily formable and weldable, and it is one of the most common and well-understood materials used in metal AM. High-quality, spherical 316L 파우더 is widely available, including from manufacturers like Met3dp who ensure optimal characteristics for PBF processes. Find more info on their 제품 페이지.
- Hygienic Properties: Its cleanability and corrosion resistance make it suitable for potable water, food processing (relevant for galleys), and some sanitary system applications onboard.
- 비용 효율성: Generally more affordable than copper-nickel alloys or higher superalloys, providing a good balance of performance and cost for many applications.
- Ideal Applications for 3D Printed 316L Valve Seats:
- Fuel Handling Systems (compatible with various fuel types)
- Potable Water Systems
- Sanitary Systems (grey/black water)
- Hydraulic Systems (using standard hydraulic oils)
- Chemical Cargo Handling (for compatible chemicals)
- Ballast Water Management Systems (especially internal components potentially exposed to treatment chemicals where biofouling is less critical than bulk chemical resistance)
- Structural components within valve assemblies.
- 고려 사항:
- Susceptible to Biofouling: Unlike CuNi alloys, 316L does not inherently resist marine growth. In stagnant or low-flow seawater conditions, biofouling can occur, potentially impacting sealing surfaces over time.
- Crevice Corrosion Risk: While resistant, 316L can still be susceptible to crevice corrosion in tight gaps (like under deposits or seals) in stagnant, chloride-rich environments, especially at elevated temperatures. Careful design is needed to minimize crevices.
- Requires appropriate post-processing (like passivation) to optimize corrosion resistance after printing and any machining.
Table: Comparison of CuNi30Mn1Fe vs. 316L for 3D Printed Marine Valve Seats
기능 | CuNi30Mn1Fe (C71500 type) | 316L Stainless Steel (S31603) | Key Takeaway for Marine Valve Seats |
---|---|---|---|
Seawater Corrosion | 우수 | Very Good (esp. pitting/crevice due to Mo) | CuNi generally superior in direct, continuous seawater exposure. |
생체 오염 저항성 | Excellent (Inherent) | Poor (Susceptible) | CuNi is the preferred choice where marine growth is a significant concern (cooling, ballast intake). |
기계적 강도 | 양호 | 매우 좋음 | 316L is better suited for higher pressure or higher mechanical stress applications. |
Temperature Limit | 보통 | Good (maintains strength at moderate temps) | Both suitable for typical marine system temperatures; specific limits depend on application stress. |
Erosion-Corrosion Resistance | Very Good (enhanced by Fe, Mn) | 양호 | CuNi often performs better in high-velocity or turbulent seawater flow. |
내화학성 | Good (general seawater, some chemicals) | Very Good (broader range, esp. acids, chlorides) | 316L often preferred for fuel or chemical handling systems (check specific compatibility). |
Suitability for AM | 우수 | 우수 | Both materials are well-suited for PBF processes using quality powders. |
상대적 비용 | 더 높음 | Lower | 316L offers a more cost-effective solution where its properties suffice. |
Typical AM Applications | Seawater Cooling, BWMS Intake, Fire Mains | Fuel, Potable Water, Hydraulics, BWMS Treatment | Choose based on the specific operating environment and primary challenges (corrosion vs. biofouling). |
소싱 고려 사항 | Need specialized CuNi powder supplier | 광범위하게 사용 가능 marine grade 316L source | Ensure powder quality from reputable suppliers like Met3dp for optimal AM results. |
시트로 내보내기
Met3dp’s Role in Material Excellence:
Choosing the right material is only half the battle; the quality of the metal powder used in the additive manufacturing process is equally critical. Companies like Met3dp play a vital role by employing advanced powder making systems, such as Vacuum Induction Melting Gas Atomization (VIGA) and Plasma Rotating Electrode Process (PREP).
- 가스 분무: Molten metal is atomized by high-pressure inert gas jets, creating rapidly solidified spherical powders. Met3dp utilizes unique nozzle and gas flow designs to achieve high sphericity and good flowability – essential for uniform layer spreading and high packing density in PBF machines.
- PREP: A rotating electrode of the desired alloy is melted by a plasma torch, flinging off molten droplets that solidify in flight into highly spherical powders with very low satellite content and high purity, often preferred for critical applications demanding the best possible material properties.
By controlling the powder production process, Met3dp ensures their 고품질 금속 분말, including grades suitable for CuNi30Mn1Fe and 316L, meet the stringent requirements for producing dense, defect-free, high-performance 3D printed components. Their portfolio extends to other innovative alloys potentially relevant for specialized marine needs, demonstrating a deep commitment to material science for additive manufacturing. Partnering with a supplier that controls powder quality provides confidence for procurement managers seeking reliable wholesale metal powder suppliers 또는 AM service bureaus focused on critical part production.
In conclusion, both CuNi30Mn1Fe and 316L stainless steel offer excellent properties for 3D printed corrosion-resistant marine valve seats, but their strengths lie in different areas. CuNi excels in direct seawater contact due to its combined corrosion and biofouling resistance, while 316L provides higher strength and broader chemical compatibility, making it versatile for fuel, water, and various process fluid applications. Selecting the optimal material, combined with high-quality AM processing using powders from expert manufacturers like Met3dp, is key to maximizing the performance and lifespan of these critical marine components.
Design for Additive Manufacturing (DfAM): Optimizing Marine Valve Seats for 3D Printing
Simply replicating a design intended for casting or machining often fails to leverage the true potential of metal additive manufacturing. To unlock the full benefits of AM – enhanced performance, reduced weight, consolidated parts, and potentially lower lifecycle costs – engineers must embrace Design for Additive Manufacturing (DfAM). DfAM is a methodology that considers the unique capabilities and constraints of the layer-by-layer building process right from the conceptual design stage. Applying DfAM principles is critical when developing high-performance, corrosion-resistant marine valve seats, allowing designers to create components that are not just manufacturable but truly optimized for their demanding maritime function and the AM process itself. Collaborating with experienced additive manufacturing design consultants or service providers like Met3dp, who understand the intricacies of metal AM, can significantly accelerate the DfAM learning curve and improve outcomes.
Here are key DfAM considerations specifically relevant for 3D printing marine valve seats using materials like CuNi30Mn1Fe and 316L:
- Leveraging Geometric Complexity for Function:
- 원칙: AM excels at creating complex shapes at little to no additional manufacturing cost compared to simple shapes (cost is driven more by volume/height). Use this freedom to enhance performance.
- Valve Seat Application:
- Optimized Flow Channels: Design internal passages or seat profiles with smooth, curved transitions rather than sharp angles typical of machining. This can minimize flow separation, reduce pressure drop across the valve, lower turbulence, and decrease the risk of erosion-corrosion, especially critical in high-velocity seawater systems using CuNi alloys.
- Advanced Sealing Geometries: Create non-planar or specially contoured sealing surfaces that might improve sealing efficiency or longevity, although these surfaces will likely still require post-machining for final finish and tolerance. The underlying AM structure can support more complex sealing concepts.
- Integrated Flow Straighteners/Conditioners: For certain valve types, small integrated features upstream or downstream of the seat could potentially improve flow characteristics within the valve body, designed directly into the printed part.
- 파트 통합:
- 원칙: Combine multiple components of an assembly into a single, more complex printed part. This reduces part count, eliminates assembly steps (labor, time), minimizes potential leak paths (joints, fasteners), and can often lead to a lighter, stiffer overall structure.
- Valve Seat Application: While the valve seat itself is often a distinct component, consider if adjacent elements (e.g., retainers, small guides, spacer elements) could be integrated directly into the seat design. This is highly application-specific but offers potential simplification for certain valve assembly designs. Evaluate if features traditionally added via secondary operations (e.g., small brackets for sensors) could be printed integrally.
- Support Structure Strategy:
- 원칙: Powder Bed Fusion processes require support structures for overhanging features (typically angles below 45 degrees from the horizontal) and to anchor the part to the build plate, managing thermal stresses. Supports consume material, add print time, and require removal. DfAM aims to minimize the need for supports or design them for easy removal.
- Valve Seat Application:
- 자립 각도: Wherever possible, design overhangs and internal channels with angles greater than 45 degrees to make them self-supporting, reducing the need for internal supports that can be difficult to remove and inspect.
- Orientation Optimization: The orientation of the valve seat on the build plate significantly impacts support requirements, surface finish on different faces, and potentially material properties due to anisotropy. Orient the part to minimize supports on critical surfaces (like the primary sealing face) or in hard-to-reach areas. Consider orienting critical sealing faces upwards or vertically if possible, although this needs balancing with other factors.
- Design for Support Removal: If supports are unavoidable (e.g., for horizontal internal channels or large overhangs), ensure there is clear line-of-sight and tool access for removing them during post-processing. Design support contact points to be minimal and on non-critical surfaces where possible. Break-away or easily machinable support designs can be employed.
- Designing for Target Tolerances and Surface Finish:
- 원칙: AM produces near-net-shape parts, but ‘as-printed’ tolerances and surface finishes may not meet the final requirements for all features, especially critical mating or sealing surfaces. DfAM involves designing with appropriate material allowances for post-machining.
- Valve Seat Application:
- Machining Allowances: Identify critical surfaces (e.g., the valve sealing face, mounting interfaces, threaded holes) that require tight tolerances and smooth finishes. Add extra stock material (typically 0.5mm – 2mm, depending on the feature and process) to these areas in the CAD model specifically for removal during final machining operations.
- Surface Finish Considerations: Understand the typical ‘as-printed’ surface roughness (Ra) achievable with the chosen process (e.g., Laser PBF often yields smoother surfaces than Electron Beam PBF) and material (powder characteristics matter). Design non-critical surfaces to function adequately with the as-printed finish to minimize post-processing needs. Explore different 인쇄 방법 and their inherent surface characteristics.
- Internal Channels and Passages:
- 원칙: AM allows for complex internal channels, but designing them effectively requires consideration of powder removal, inspection, and self-supporting angles.
- Valve Seat Application: If the valve seat design incorporates internal features (e.g., for pressure balancing, specialized flow control, or potential future cooling), ensure channel diameters are large enough for effective powder removal after printing (typically > 1-2mm, consult your AM provider). Design smooth bends rather than sharp corners. Ensure there are access points for inspection and cleaning. Avoid long, horizontal internal channels that would require extensive internal supports.
- Weight Reduction via Topology Optimization and Lattice Structures:
- 원칙: Use software tools to optimize the material distribution within the part, removing material from low-stress regions while maintaining structural integrity. Lattice structures can also be used to infill solid volumes for lightweighting.
- Valve Seat Application: While valve seats are often relatively small and density isn’t the primary driver, topology optimization could be applied to larger valve components or integrated seat/housing designs, particularly in weight-sensitive marine applications (e.g., performance craft, aerospace-derived systems). For standard valve seats, the benefit might be minimal compared to the design effort, but the capability exists.
- Feature Design Considerations:
- Minimum Wall Thickness: Design walls thick enough to be reliably printed and handle operational stresses (typically > 0.5mm – 1mm, depending on process and geometry).
- Hole Design: Small vertical holes print well; horizontal holes often print slightly elliptical and may require support. Consider designing holes slightly undersized for reaming or tapping post-print.
- Threads: External threads can sometimes be printed directly (coarse pitches), but internal threads are almost always best produced by printing a pilot hole and tapping it during post-processing.
- Sharp Edges/Corners: These can concentrate stress and may print with slight rounding. Consider designing in small radii or chamfers where appropriate.
- Part Identification: Integrate part numbers, supplier logos (e.g., Met3dp), or material identifiers directly into the CAD model to be printed onto non-critical surfaces.
Table: DfAM Checklist for 3D Printed Marine Valve Seats
DfAM Principle | Key Consideration for Valve Seats | 혜택 |
---|---|---|
Complexity for Function | Optimize flow paths (smooth curves), advanced sealing concepts | Improved valve efficiency, reduced erosion, better sealing |
부품 통합 | Integrate adjacent small components (retainers, guides)? | Reduced part count, simpler assembly, fewer leak paths |
Support Strategy | Minimize supports via orientation & self-supporting angles (>45°), access | Reduced print time/cost, easier post-processing, better surface quality |
Tolerance/Finish Design | Add machining stock (0.5-2mm) on critical faces (sealing, mating) | Achieves required precision where needed, minimizes overall machining |
Internal Channels | Ensure powder removal (dia > 1-2mm), smooth bends, inspection access | Enables complex internal features if required, ensures part quality |
무게 감소 | Apply topology optimization/lattices if weight is critical | Lighter components for specific applications |
Feature Design (Walls/Holes) | Respect minimum feature sizes, design holes for post-processing (ream/tap) | Ensures manufacturability and functional features |
스레드 | Print pilot holes for tapping internal threads | Reliable and accurate threads |
Edges/Corners | Add small radii/chamfers to reduce stress concentration | Improved durability |
Identification | Integrate part numbers, logos, material info directly | Traceability, branding |
시트로 내보내기
By thoughtfully applying these DfAM principles, engineers can move beyond simple replacement and create truly optimized 3D printed marine valve seats. This requires a shift in thinking, often facilitated by collaboration with AM experts. Engaging with a knowledgeable metal additive manufacturing service provider early in the design process ensures that the component is designed for successful, efficient, and high-performance production, maximizing the return on investment in this advanced manufacturing technology.
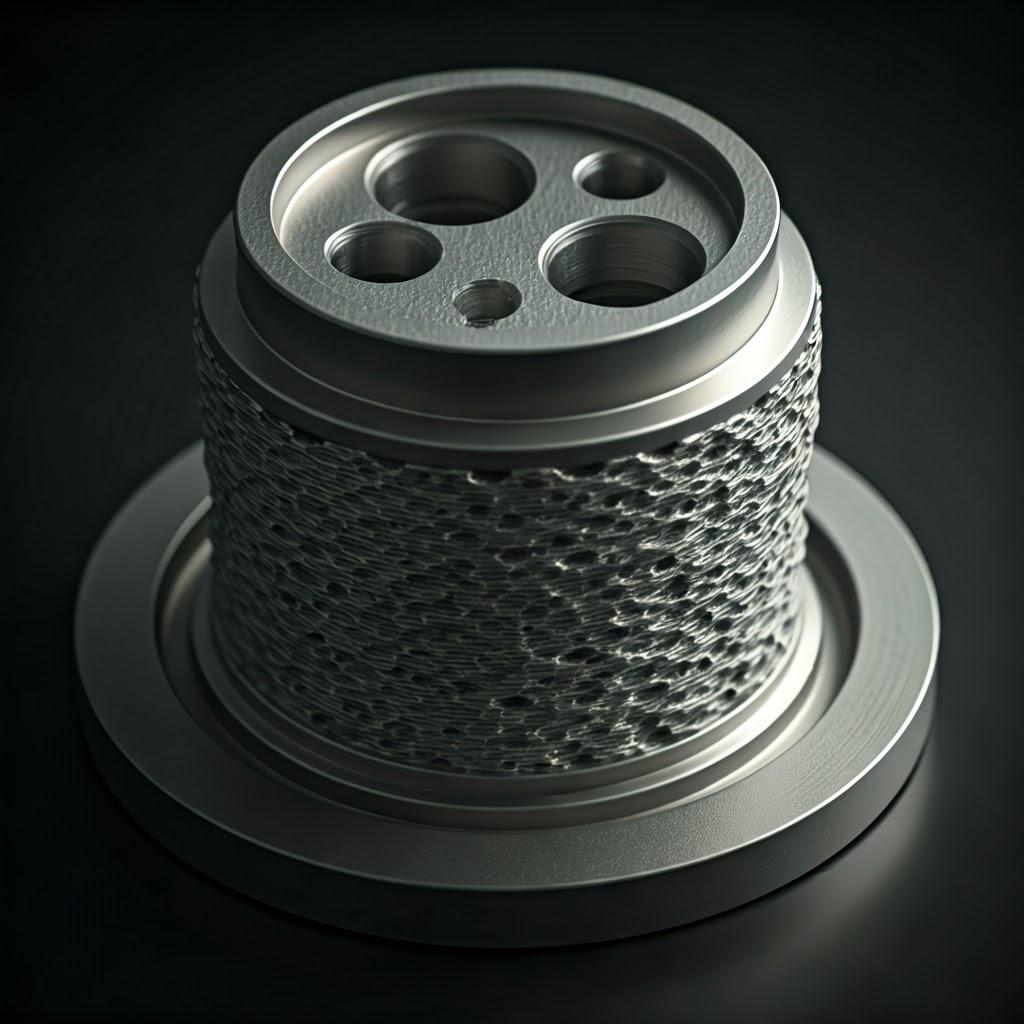
Achieving Precision: Tolerance, Surface Finish, and Dimensional Accuracy in 3D Printed Valve Seats
While metal 3D printing offers incredible design freedom, a common question from engineers and procurement managers, especially those accustomed to precision machining, concerns the achievable levels of tolerance, surface finish, and overall dimensional accuracy. For components like marine valve seats, where sealing integrity and proper fit within the valve assembly are critical, understanding these aspects is paramount. Achieving the required precision often involves a combination of controlling the AM process itself and implementing targeted post-processing steps. Sourcing from quality-focused AM suppliers who possess well-calibrated machines and robust process controls is essential.
1. Understanding Tolerances in Metal AM:
- 정의: Tolerance refers to the permissible range of variation in a dimension of a part.
- AM Capabilities: Metal Powder Bed Fusion (PBF) processes, such as Selective Laser Melting (SLM/LPBF) and Electron Beam Melting (EBM, like Met3dp’s SEBM systems), can typically achieve dimensional tolerances in the range of:
- General Features: ±0.1 mm to ±0.3 mm or ±0.1% to ±0.2% of the dimension (whichever is greater) for well-controlled processes on medium-sized features.
- Smaller Features (<20mm): Tolerances might be tighter, potentially down to ±0.05 mm in some cases, but this is highly dependent on the feature, orientation, and process calibration.
- Factors Influencing Tolerance:
- 머신 보정: Regular calibration of the laser/electron beam positioning systems, scanner fields, and Z-axis movement is crucial.
- 열 효과: The repeated heating and cooling cycles inherent in AM can cause internal stresses, leading to distortion (warping) or deviation from the intended geometry, especially in large or complex parts. Build strategy, support structures, and post-print stress relief are used to mitigate this.
- Part Geometry & Size: Large, bulky parts or those with significant variations in cross-section are more prone to thermal distortion.
- 빌드 오리엔테이션: The orientation on the build plate affects how thermal stresses accumulate and can influence the accuracy of specific features.
- 파우더 특성: The size distribution, morphology, and flowability of the metal powder (e.g., high-quality CuNi30Mn1Fe powder 또는 316L 파우더 from Met3dp) influence packing density and melt pool stability, impacting final part accuracy.
- 프로세스 매개변수: Laser/beam power, scan speed, layer thickness, and hatching strategy all affect the melt pool dynamics and resulting part density and accuracy.
2. Surface Finish (Roughness):
- 정의: Surface finish, often quantified by Ra (average roughness), describes the texture of a part’s surface.
- ‘As-Printed’ Surface Finish: The surface finish of an AM part directly after printing depends heavily on the process, material, layer thickness, and surface orientation:
- 상위 표면: Generally the smoothest, often Ra 5-15 µm (micrometers).
- Vertical Walls: Typically Ra 8-20 µm.
- Up-Facing/Overhanging Surfaces (Supported): Tend to be rougher due to support contact points and the nature of forming overhangs, potentially Ra 15-30 µm or more.
- Down-Facing Surfaces (Supported): Often the roughest due to interaction with support structures, potentially Ra 20-40 µm+.
- Process Influence: Laser PBF (LPBF/SLM) generally produces finer surface finishes than Electron Beam PBF (EBM) due to smaller powder particle sizes and layer thicknesses, although EBM can excel in reducing residual stress.
- Importance for Valve Seats:
- Sealing Faces: The primary sealing surface of a valve seat requires a very smooth finish (often Ra < 1.6 µm, sometimes much lower) to ensure a tight seal against the valve plug/disc. This level of finish is not typically achievable directly from the AM process and requires post-machining (grinding, lapping, polishing).
- Mating/Mounting Surfaces: Faces that interface with the valve body or other components may require good flatness and a controlled roughness for proper assembly and sealing (e.g., gasket surfaces). These often require post-machining.
- Flow Passages: While smoother is generally better for flow, the as-printed finish inside flow passages may be acceptable for many applications, avoiding the cost of internal polishing unless absolutely necessary for performance.
3. Ensuring Dimensional Accuracy:
- Clear Specifications: Provide clear engineering drawings with critical dimensions and tolerances clearly marked. Don’t rely solely on the CAD model; specify which features have tight tolerance requirements.
- Collaboration with AM Provider: Discuss critical tolerances and surface finishes with your chosen metal AM service bureau early on. They can advise on achievable limits for the as-printed part and recommend necessary post-processing.
- 프로세스 제어: Choose suppliers like Met3dp who demonstrate robust process control, machine maintenance schedules, and quality management systems (e.g., ISO 9001 or relevant industry certifications).
- Material Allowances: As discussed in DfAM, ensure sufficient material is added to critical surfaces in the design stage to allow for post-machining to final tolerances.
- Inspection and Metrology: Define inspection requirements. This may include:
- 치수 검사: Using calipers, micrometers, Coordinate Measuring Machines (CMM), or 3D scanning to verify critical dimensions against the drawing.
- 표면 거칠기 측정: Using a profilometer to check the Ra value on critical surfaces after any finishing operations.
Table: Typical Precision Levels in Metal PBF (Illustrative)
매개변수 | As-Printed (Typical PBF) | After Post-Machining | Relevance to Marine Valve Seats |
---|---|---|---|
General Tolerance | ±0.1 to ±0.3 mm / ±0.1-0.2% | As per machining capability | Overall fit within the valve body. |
Critical Tolerance | Unlikely to meet tight specs | Down to ±0.01 mm or better | Sealing face concentricity, mounting dimensions, pilot diameters. |
Surface Finish (Ra) | |||
– Top Surfaces | 5-15 µm | < 0.8 µm (polished/lapped) | Non-critical external faces. |
– Vertical Walls | 8-20 µm | < 1.6 µm (ground/machined) | Side faces, potentially needing cleanup for fit. |
– Supported Surfaces | 15-40+ µm | < 3.2 µm (machined) | Areas where supports were attached, often need machining if functional. |
Sealing Face Ra | 10-30+ µm (depending on orientation) | < 1.6 µm, often < 0.8 µm | Crucial for function. Requires grinding, lapping, or polishing. |
시트로 내보내기
In summary: While metal AM produces near-net-shape parts with good baseline accuracy, achieving the high precision required for critical features like marine valve sealing surfaces necessitates careful planning and post-processing. By understanding the capabilities and limitations, applying DfAM principles (especially adding machining stock), clearly specifying requirements, and partnering with a capable 첨가 제조 공급업체 focused on quality control, engineers can confidently leverage AM to produce dimensionally accurate and highly functional marine valve seats.
Beyond the Print: Essential Post-Processing for Marine Valve Seats
Producing a metal part layer by layer is just the first step in the additive manufacturing workflow, especially for demanding applications like marine valve seats. A series of crucial post-processing steps are typically required to transform the ‘green’ or ‘as-printed’ component into a finished product ready for installation and service. These steps are essential to relieve internal stresses, remove support structures, achieve critical tolerances and surface finishes, and ultimately ensure the component’s performance, reliability, and longevity in the corrosive maritime environment. Understanding these requirements is vital for budgeting, lead time estimation, and selecting a full-service metal AM provider or coordinating with specialist finishing shops.
Here’s a breakdown of common and often essential post-processing steps for 3D printed marine valve seats made from materials like CuNi30Mn1Fe or 316L:
- 스트레스 완화 열처리:
- Why it’s needed: The rapid heating and cooling cycles during the PBF process create significant residual stresses within the printed part. These stresses can lead to distortion (warping) during or after printing, cracking, reduced fatigue life, and unpredictable dimensional changes if machined before stress relief.
- 프로세스: The entire build plate with the parts still attached (or sometimes after removal) is placed in a furnace and heated to a specific temperature (below the material’s critical transformation points), held for a period, and then slowly cooled. The exact cycle (temperature, time, atmosphere – often vacuum or inert gas) depends heavily on the alloy (CuNi and 316L have different optimal cycles).
- Outcome: Reduces internal stresses, stabilizes the microstructure, and minimizes the risk of distortion during subsequent steps like support removal or machining. This is nearly always a mandatory first step after printing.
- 빌드 플레이트에서 파트 제거:
- Why it’s needed: Parts are typically printed on a thick metal build plate, often welded or strongly sintered to it via the initial layers and support structures.
- 프로세스: Commonly done using wire EDM (Electrical Discharge Machining) or a bandsaw to cut the part away from the plate at the base of the supports or the first layers. Care must be taken not to damage the part itself.
- 지원 구조 제거:
- Why it’s needed: The support structures required during printing are sacrificial and must be removed to reveal the final part geometry.
- 프로세스: Can involve manual breaking and chipping (for well-designed, accessible supports), cutting with hand tools, or machining (milling, grinding). Access can be challenging for internal supports. DfAM plays a crucial role here – designing supports for easy removal saves significant post-processing time and cost.
- Outcome: Reveals the intended part shape, but often leaves witness marks or rougher surfaces where supports were attached.
- Machining of Critical Features:
- Why it’s needed: As discussed previously, AM typically cannot achieve the tight tolerances (sub-0.1mm) and fine surface finishes (Ra < 1.6 µm) required for critical valve seat features directly.
- 프로세스: Utilizes traditional CNC machining methods:
- Turning/Lathing: For rotationally symmetric features like the main sealing face bore, outer diameters, and seating surfaces.
- 밀링: For creating flat mating surfaces, slots, non-round features, or cleaning up support witness marks.
- Grinding/Lapping/Polishing: Specialized processes to achieve very fine surface finishes and tight tolerances on the primary sealing face(s). Lapping uses an abrasive slurry between the part and a flat plate (lap) to achieve extreme flatness and smoothness.
- Outcome: Achieves the final required dimensions, tolerances, and surface finishes on critical interfacing and sealing surfaces, ensuring proper function and sealing performance. This is often the most critical post-processing step for valve seats.
- Surface Finishing / Cleaning:
- Why it’s needed: To improve the overall surface finish of non-machined areas, remove any partially sintered powder particles, clean the part, and create a uniform aesthetic.
- 프로세스: 일반적인 방법은 다음과 같습니다:
- Bead Blasting / Sand Blasting: Propelling abrasive media (glass beads, ceramic, aluminum oxide) at the surface to clean it, remove loose powder, and create a uniform matte finish. The media type and pressure influence the final texture.
- Tumbling / Vibratory Finishing: Placing parts in a tub with abrasive media and causing them to rub against each other and the media. Good for deburring edges and smoothing surfaces on batches of smaller parts, but less precise than machining.
- 전기 연마: An electrochemical process that removes a microscopic layer of material, preferentially smoothing peaks, resulting in a very smooth, clean, and often brighter surface. Particularly effective for stainless steels like 316L.
- Outcome: Improved surface quality, cleanliness, and aesthetics. Can sometimes slightly improve fatigue life by reducing surface stress concentrators.
- Passivation (Especially for 316L Stainless Steel):
- Why it’s needed: To enhance the natural corrosion resistance of stainless steel. Machining, handling, or even atmospheric exposure can embed free iron particles or disrupt the passive chromium oxide layer that protects the steel.
- 프로세스: Involves immersing the cleaned stainless steel part in a mild oxidant solution, typically nitric acid or citric acid based. This removes free iron and helps rebuild a thicker, more uniform passive oxide layer.
- Outcome: Maximizes the corrosion resistance of the 316L valve seat, crucial for longevity in the marine environment. Less common/necessary for CuNi alloys which form their protective film differently.
- Hot Isostatic Pressing (HIP) – Optional, for Critical Applications:
- Why it’s needed: Even with optimized AM parameters, microscopic internal pores (voids) can sometimes remain within the printed part. For highly critical applications where maximum fatigue strength, fracture toughness, and material integrity are essential, HIP can be used to eliminate this internal porosity.
- 프로세스: The part is subjected to high temperature (below melting point) and high isostatic pressure (using an inert gas like Argon) simultaneously in a specialized vessel. The pressure collapses internal voids, diffusion bonding the material across the void interfaces.
- Outcome: Achieves near 100% theoretical density, improving mechanical properties (especially fatigue and ductility) and ensuring maximum material integrity. Adds significant cost and lead time, so typically reserved for the most demanding applications (e.g., critical engine components, subsea).
- Inspection and Quality Control:
- Why it’s needed: To verify that all previous steps have been performed correctly and the final part meets all specifications.
- 프로세스: Includes dimensional checks (CMM, scanning), surface finish measurements, visual inspection, and potentially Non-Destructive Testing (NDT) such as X-ray or CT scanning (to check internal integrity/porosity, especially if HIP is not performed), dye penetrant testing (to check for surface cracks), or ultrasonic testing.
- Outcome: Ensures the valve seat meets all quality requirements before shipping and installation. Essential for reliable marine component suppliers.
Table: Post-Processing Steps for 3D Printed Marine Valve Seats
Post-Processing Step | 목적 | Typical Method(s) | Material Applicability | Necessity Level |
---|---|---|---|---|
Stress Relief Heat Treatment | Reduce residual stress, prevent distortion, stabilize microstructure | Furnace treatment (specific cycle per alloy) | Both CuNi & 316L | Mandatory |
Part Removal | Separate part from build plate | Wire EDM, Bandsaw | 둘 다 | Mandatory |
지지대 제거 | Remove sacrificial support structures | Manual breaking, Hand tools, Machining | 둘 다 | Mandatory |
Machining (Critical) | Achieve tight tolerances & fine surface finish on functional faces | CNC Turning, Milling, Grinding, Lapping | 둘 다 | Mandatory for Sealing/Mating Faces |
Surface Finishing/Cleaning | Improve overall Ra, remove loose powder, uniform appearance | Bead Blasting, Tumbling, Electropolishing (316L) | 둘 다 | Recommended (Application dependent) |
패시베이션 | Enhance corrosion resistance by restoring passive layer | Nitric/Citric Acid Bath | 316L primarily | Highly Recommended for 316L |
열간 등방성 프레스(HIP) | Eliminate internal porosity, maximize density & mechanical properties | High Temp + High Pressure Inert Gas | 둘 다 | Optional (Highly Critical Applications Only) |
Inspection & QC | Verify dimensions, finish, internal integrity, overall quality | CMM, Profilometer, Visual, NDT (X-ray, Dye Pen) | 둘 다 | Mandatory |
시트로 내보내기
Successfully implementing these post-processing steps requires expertise, appropriate equipment, and careful coordination. When selecting an AM manufacturing partner, inquire about their in-house post-processing capabilities or their network of trusted third-party providers. Companies like Met3dp, offering comprehensive solutions, understand the importance of this entire workflow, not just the printing stage, ensuring that the final 3D printed marine valve seat delivered meets the stringent requirements of the maritime industry.
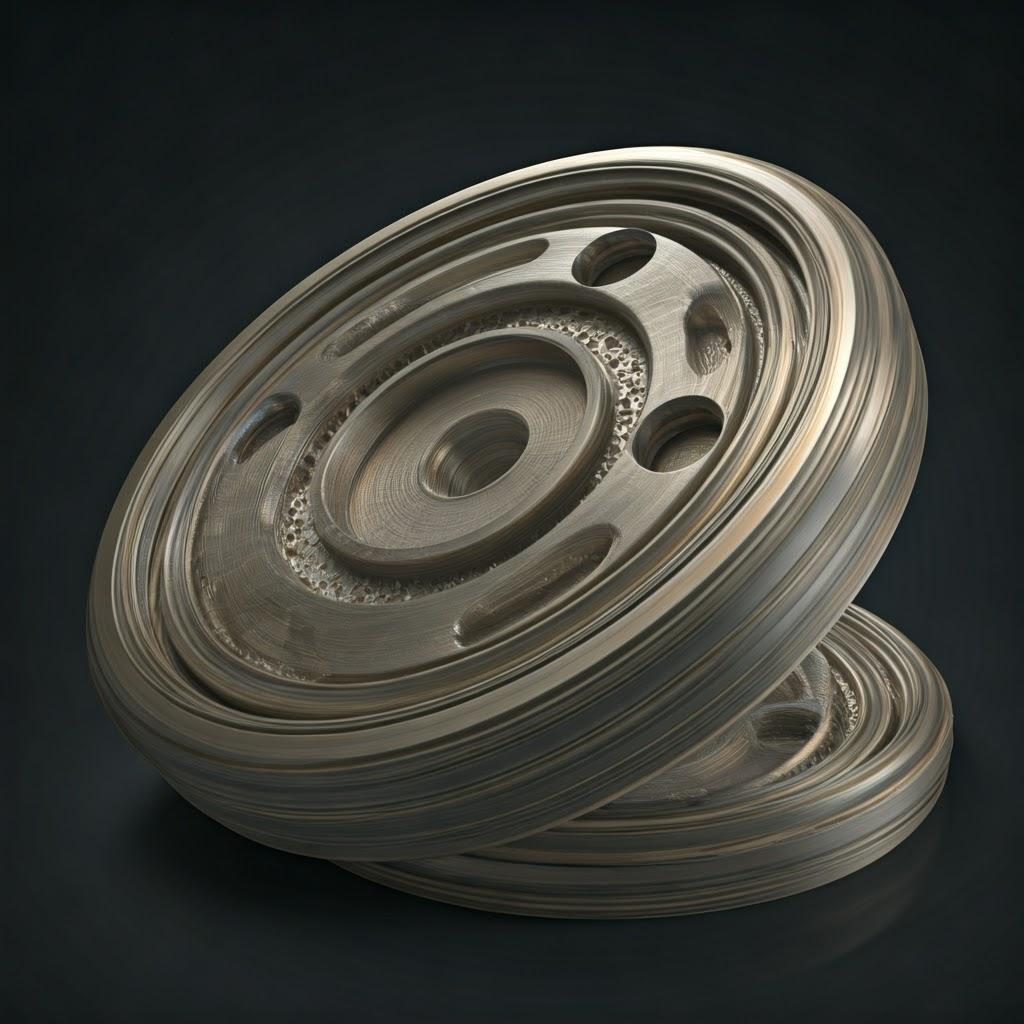
Navigating Challenges: Overcoming Hurdles in 3D Printing Marine Valve Seats
While metal additive manufacturing offers significant advantages for producing corrosion-resistant marine valve seats, it’s not without its challenges. Acknowledging these potential hurdles and understanding how to mitigate them is crucial for successful implementation. Engineers, designers, and procurement managers should be aware of these factors when specifying parts and selecting additive manufacturing partners. Addressing these challenges proactively ensures the delivery of high-quality, reliable components that meet the rigorous demands of the marine environment.
Here are some common challenges associated with 3D printing marine valve seats and strategies to overcome them:
- Residual Stress and Warping:
- 도전: The rapid heating and cooling inherent in PBF processes generate internal stresses. If not managed, these stresses can cause the part to warp or distort during printing, removal from the build plate, or even later in its lifecycle. Thin features, large flat areas, and asymmetric designs are particularly susceptible.
- 완화 전략:
- Optimized Build Strategy: Careful selection of scan patterns (e.g., island scanning, rotating layers), laser/beam parameters, and pre-heating (especially in EBM) can minimize stress build-up.
- Effective Support Structures: Well-designed supports anchor the part securely to the build plate, conduct heat away, and resist deformation forces during the build.
- DfAM Principles: Designing parts with gradual thickness transitions, avoiding large unsupported flat areas, and potentially adding sacrificial stiffening features (removed later) can help.
- Mandatory Stress Relief: Performing a proper stress relief heat treatment cycle immediately after printing and before support removal is critical to relax internal stresses and stabilize the part.
- Support Structure Removal Difficulties:
- 도전: Supports in intricate internal channels or hard-to-reach areas can be extremely difficult and time-consuming to remove completely. Incomplete removal can impede flow, trap debris, or act as corrosion initiation sites.
- 완화 전략:
- DfAM Focus: Design parts to be self-supporting wherever possible (using angles > 45°). Optimize part orientation to place supports on external, accessible surfaces.
- Support Design: Use support types designed for easier removal (e.g., perforated or thin-walled supports) where feasible. Ensure adequate access paths for tools.
- Process Selection: Consider processes that may require fewer supports (e.g., EBM often needs less support than LPBF due to higher process temperatures and powder sintering).
- Post-Processing Methods: Techniques like abrasive flow machining or electrochemical machining can sometimes be used for smoothing inaccessible internal channels, but add cost and complexity. Careful planning is key.
- Achieving Critical Surface Finish and Tolerances:
- 도전: As-printed surfaces, especially those affected by supports or layer stepping (‘staircase effect’ on shallow angles), are often too rough for sealing applications. Achieving micron-level tolerances and finishes requires additional steps.
- 완화 전략:
- Design for Finishing: Explicitly design-in machining allowances (stock) on all critical surfaces in the CAD model.
- Targeted Post-Machining: Employ precise CNC machining, grinding, and lapping/polishing operations specifically on the sealing faces and critical mating dimensions. Focus effort where it’s needed most.
- Process/Parameter Optimization: While it won’t eliminate the need for machining sealing faces, optimizing AM parameters (e.g., finer powder, thinner layers in LPBF) can improve the finish of non-critical surfaces.
- Clear Specifications: Provide unambiguous drawings detailing required Ra values and tolerances for specific features to the AM service provider.
- Porosity and Material Defects:
- 도전: Incomplete melting, gas entrapment during atomization or printing, or keyhole instability (in laser processes) can lead to microscopic pores within the printed material. While often low (<0.5% volume), porosity can reduce mechanical properties (especially fatigue strength and ductility) and potentially act as initiation sites for corrosion or cracks.
- 완화 전략:
- High-Quality Powder: Start with high-purity, spherical metal powders with low internal gas porosity and good flowability. Sourcing from reputable metal powder manufacturers like Met3dp, who utilize advanced atomization (Gas Atomization, PREP) and rigorous quality control, is crucial.
- Optimized Process Parameters: Develop and use validated parameter sets (laser/beam power, speed, hatching, etc.) specific to the material (CuNi30Mn1Fe, 316L) and machine to ensure complete melting and stable melt pool behavior.
- Robust Quality Control: Implement in-process monitoring (e.g., melt pool monitoring) if available, and post-build inspection (e.g., density checks, metallography on test coupons).
- 열간 등방성 프레싱(HIP): For the most critical applications where near-zero porosity is required, HIP post-processing effectively eliminates internal voids, ensuring maximum material integrity.
- Material Property Anisotropy:
- 도전: Due to the layer-by-layer build process and directional solidification, the mechanical properties (e.g., tensile strength, ductility) of an AM part can sometimes vary depending on the direction of testing relative to the build direction (X, Y vs. Z).
- 완화 전략:
- 특성화: Understand the degree of anisotropy for the specific material, process, and parameters being used. Reputable service providers should have this data.
- Orientation Optimization: Orient the part on the build plate so that the most critical stress directions align with the strongest build orientation (often horizontal, X-Y plane).
- 열처리: Appropriate heat treatments (beyond just stress relief, potentially solution annealing and aging for some alloys) can help homogenize the microstructure and reduce anisotropy.
- 비용 고려 사항:
- 도전: The initial per-part cost of metal AM can sometimes be higher than traditional methods like casting, especially for simpler parts produced in very high volumes. Factors include machine cost, skilled labor, powder cost, and post-processing requirements.
- 완화 전략:
- Focus on Total Cost of Ownership: Emphasize the lifecycle benefits – reduced downtime due to faster replacements, longer component life from better materials/design, lower inventory costs, reduced assembly time through part consolidation.
- Optimize Design for AM: Fully leverage DfAM to minimize material usage (e.g., topology optimization where appropriate), reduce support needs, and streamline post-processing.
- Select the Right Applications: Target AM for components where its benefits are most impactful – complex geometries, high-performance materials (like CuNi30Mn1Fe), low-to-medium volume production, rapid prototyping, and replacement parts.
- Partner Efficiency: Work with efficient wholesale AM providers who have optimized workflows and economies of scale.
- Quality Assurance, Certification, and Standardization:
- 도전: Ensuring consistent quality and meeting the stringent certification requirements of the marine industry (e.g., from classification societies like DNV, ABS, Lloyd’s Register) for critical components produced via relatively new AM processes requires robust quality management systems and process validation.
- 완화 전략:
- Choose Certified Suppliers: Partner with AM service providers who hold relevant quality certifications (e.g., ISO 9001, AS9100 for aerospace often translates to high rigor) and ideally have experience with marine industry requirements or are working towards marine certifications.
- Process Validation: Ensure the supplier uses validated processes with locked-down parameters, regular machine calibration, and material batch traceability.
- 엄격한 테스트: Implement a comprehensive testing plan, including material testing (tensile, chemistry), dimensional inspection, NDT, and potentially functional testing on prototypes or first articles.
- Collaboration with Classification Societies: Engage with marine classification societies early in the process for guidance on qualification procedures for AM parts in specific applications.
Table: Summary of AM Challenges for Marine Valve Seats & Solutions
도전 | 잠재적 인 영향 | Key Mitigation Strategies |
---|---|---|
Residual Stress / Warping | Distortion, Cracking, Dimensional Instability | Optimized Build Strategy, Supports, DfAM, Mandatory Stress Relief |
Support Removal Difficulty | Incomplete Removal, Damage, High Labor Cost | DfAM (Self-supporting, Access), Support Design, Process Choice, Specialized Finishing |
Tolerance / Surface Finish | Poor Sealing, Improper Fit | DfAM (Machining Stock), Precision Post-Machining (Grind/Lap), Clear Specs |
Porosity / Defects | Reduced Mechanical Properties, Corrosion/Crack Sites | High-Quality Powder (e.g., Met3dp), Optimized Parameters, QC, Optional HIP |
Property Anisotropy | Directional Weakness | Characterization, Orientation Optimization, Heat Treatment |
Cost Justification | Higher Initial Per-Part Cost | Focus on Lifecycle Cost, DfAM Optimization, Target High-Value Applications, Efficient Supplier |
QA / Certification / Standards | Ensuring Consistency, Meeting Marine Regulations | Certified Suppliers (ISO 9001+), Process Validation, Rigorous Testing, Classification Society Engagement |
시트로 내보내기
By acknowledging these challenges and proactively implementing mitigation strategies, often in close collaboration between designers, engineers, and expert additive manufacturing solutions providers like Met3dp, the hurdles to adopting metal AM for demanding marine applications like valve seats can be successfully overcome. The result is access to components with superior performance, enhanced reliability, and greater design possibilities, ultimately contributing to safer and more efficient maritime operations.
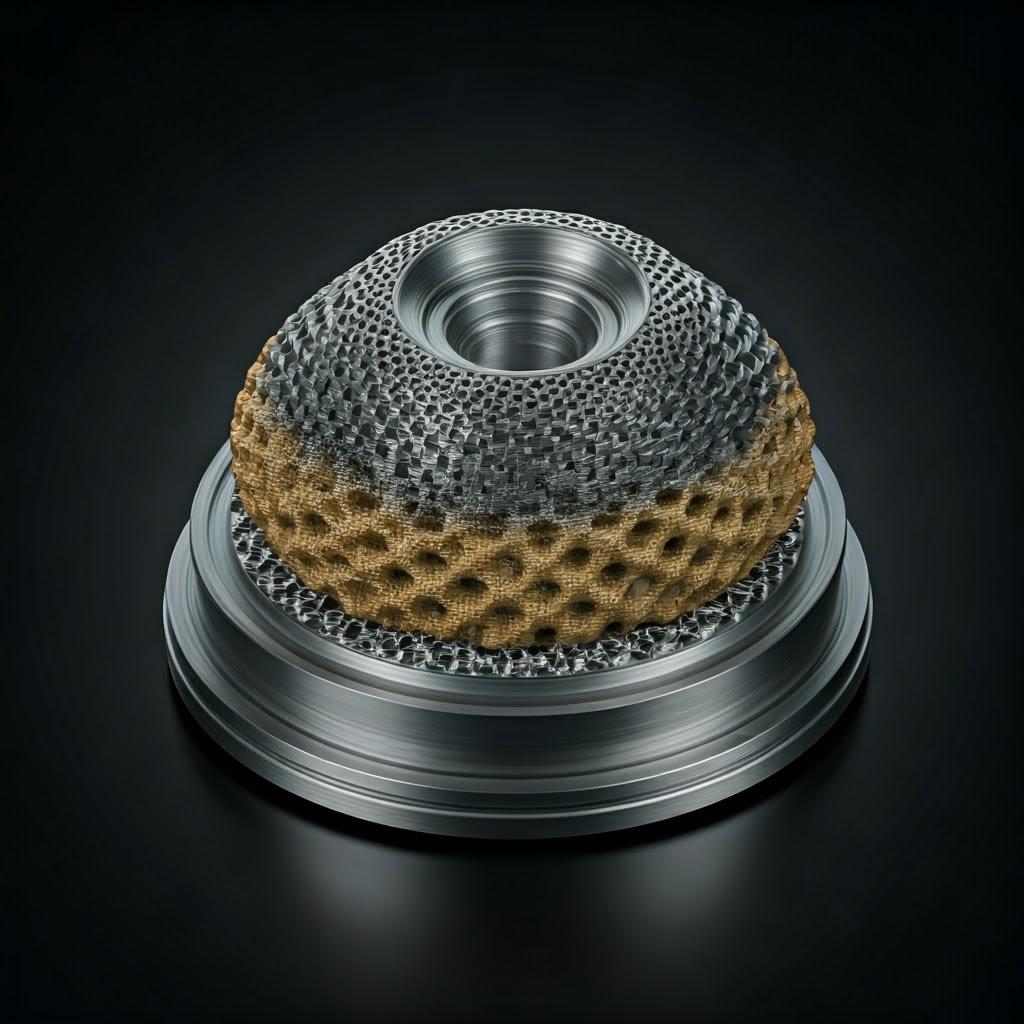
Supplier Selection: Choosing the Right Metal Additive Manufacturing Partner for Marine Components
The success of implementing metal 3D printing for critical components like marine valve seats hinges significantly on the capabilities and reliability of your chosen additive manufacturing partner. Not all AM service bureaus are created equal, especially when dealing with the demanding requirements of the maritime industry – harsh environments, high reliability needs, and often stringent quality and certification standards. Selecting the right supplier involves evaluating more than just price; it requires a thorough assessment of their technical expertise, quality systems, material capabilities, and experience. For procurement managers seeking a long-term marine component manufacturing partner or engineers needing deep technical collaboration, this selection process is critical.
Here are key criteria to consider when evaluating and selecting a metal additive manufacturing supplier for marine valve seats and other critical components:
- Technical Expertise and Engineering Support:
- Deep AM Knowledge: Does the supplier possess a fundamental understanding of the physics behind the AM processes they offer (e.g., Laser Powder Bed Fusion – LPBF/SLM, Electron Beam Melting – EBM)? Can they explain the nuances affecting part properties?
- Materials Science Acumen: Do they have expertise in the specific alloys required, such as CuNi30Mn1Fe 및 316L 스테인리스 스틸? Can they advise on material selection for specific marine applications, considering corrosion, biofouling, mechanical loads, and chemical compatibility? Companies like Met3dp, with roots in both 금속 3D 프린팅 equipment and advanced powder manufacturing, often possess this deep material science knowledge.
- DfAM Proficiency: Can the supplier provide meaningful input on Design for Additive Manufacturing? Can they help optimize your valve seat design for printability, performance, support minimization, and cost-effectiveness? True partners offer collaborative design support, not just print-to-file services.
- Post-Processing Know-How: Do they understand the critical post-processing steps (stress relief, machining, finishing, heat treatments) required for marine components and can they manage or advise on this workflow effectively?
- Equipment, Capacity, and Capabilities:
- Appropriate Technology: Does the supplier operate the right type of PBF machines (LPBF, EBM) suitable for the required materials and part specifications? Met3dp, for instance, offers SEBM (Selective Electron Beam Melting) printers, known for producing low-stress parts in certain materials, which can be advantageous.
- Machine Fleet & Build Volume: Do they have sufficient machine capacity to meet your volume requirements and lead time expectations? Are their machine build envelopes large enough for your components? Redundancy (multiple machines) can mitigate risks associated with machine downtime.
- In-House vs. Outsourced Services: What post-processing steps do they perform in-house versus outsourcing? While outsourcing is common, strong relationships and quality control with subcontractors are essential. A more integrated provider might offer greater control and potentially faster turnaround.
- Material Quality and Handling:
- Powder Sourcing & Control: Where does the supplier source their metal powders? Do they have rigorous quality control for incoming powder batches (chemistry, particle size distribution, morphology, flowability)? Suppliers like Met3dp who manufacture their own powders using advanced methods like Gas Atomization and PREP offer a higher degree of material consistency and traceability. Look for suppliers who manage powder storage, handling, and recycling meticulously to prevent contamination and ensure optimal printing conditions.
- Material Certifications: Can the supplier provide material certifications (e.g., Type 3.1 according to EN 10204) tracing the powder batch to the final part, confirming chemical composition and powder characteristics?
- Quality Management System (QMS) and Certifications:
- Formal QMS: Does the supplier operate under a robust QMS, ideally certified to standards like ISO 9001? For highly critical parts, certifications common in aerospace (AS9100) indicate a very high level of process control and traceability, often beneficial even for marine applications.
- Traceability: Can they demonstrate full traceability from raw material powder batch through printing parameters, post-processing steps, and final inspection results for each part?
- Marine-Specific Certification: While dedicated marine AM certifications are still evolving, inquire if the supplier has experience working with classification societies (DNV, ABS, LR, BV, etc.) or specific marine standards. Experience in other regulated industries (medical, aerospace) is often a good indicator of capability. This is crucial for certified marine part suppliers.
- Experience and Track Record:
- Proven Industry Experience: Has the supplier successfully produced parts for demanding industries? Do they have case studies or references, particularly for components used in corrosive or high-reliability environments? Specific marine application experience is ideal.
- 부품 복잡성: Have they demonstrated capability in producing parts with complex geometries, thin walls, or internal channels similar to your valve seat design?
- 문제 해결: Can they provide examples of how they’ve overcome technical challenges in previous projects?
- Customer Service, Communication, and Support:
- 응답성: 문의 및 견적 요청에 신속하게 응답하나요?
- Clear Communication: Is communication clear, professional, and technically sound? Do they provide regular updates during production?
- Collaboration: Are they willing to work collaboratively to solve design or manufacturing challenges? Do they offer proactive suggestions for improvement?
- 기술 지원: Can they provide technical support regarding material properties, design guidelines, and post-processing options?
- Cost and Lead Time:
- Transparent Pricing: Is the quoting process clear and detailed, breaking down costs where possible? (See next section for cost factors).
- Realistic Lead Times: Do they provide achievable lead time estimates and have a track record of on-time delivery? Understand their capacity planning.
- 가치 제안: Evaluate the overall value, considering quality, expertise, reliability, and support, not just the upfront price per part. A slightly cheaper supplier that delivers non-conforming parts or experiences delays can be far more costly in the long run.
Table: Key Criteria for Selecting a Metal AM Partner for Marine Components
기준 | Why It Matters for Marine Valve Seats | 무엇을 찾아야 하나요? | Ideal Partner Characteristics (e.g., Met3dp) |
---|---|---|---|
기술 전문성 | Ensures correct material/process selection, DfAM optimization, problem-solving capability. | Deep materials science (CuNi, 316L), DfAM support, understanding of PBF nuances, post-processing knowledge. | In-depth knowledge from equipment/powder background, collaborative engineering support. |
장비 및 기능 | Determines feasibility, quality (e.g., low stress EBM), capacity, and integration of workflow. | Suitable PBF machines (LPBF/EBM), adequate build volume, capacity, relevant in-house or managed post-processing. | Offering advanced systems like SEBM, potentially integrated workflow management. |
재료 품질 | Directly impacts final part properties, density, consistency, and performance (esp. corrosion resistance). | Controlled powder sourcing/production, rigorous QC, proper handling/storage, material certs (EN 10204 3.1). | Advanced in-house powder production (Gas Atomization, PREP), ensuring high sphericity, flowability, purity. |
Quality Management System | Guarantees process control, repeatability, traceability, and meets industry requirements. | ISO 9001 (minimum), AS9100 (preferred for rigor), path to marine certs, full traceability records. | Commitment to quality standards, potentially holding relevant certifications due to serving demanding industries. |
경험 및 실적 | Demonstrates ability to deliver complex, reliable parts in demanding environments. | Proven projects (marine, aerospace, medical), relevant case studies, experience with similar complexity/materials. | Decades of collective expertise in metal AM, serving mission-critical sectors. |
Customer Service & Support | Facilitates smooth project execution, collaboration, and problem resolution. | Responsiveness, clear communication, collaboration willingness, accessible technical support. | Focus on partnership and comprehensive solutions, providing application development services. |
비용 및 리드타임 | Impacts project budget and schedule adherence. | Transparent quoting, realistic lead times, focus on total value proposition (quality, reliability vs. just price). | Potential for efficiency through integrated solutions and optimized processes, offering competitive value. |
시트로 내보내기
올바른 선택 금속 첨가 제조 공급업체 is a strategic decision. It’s about finding a partner who not only possesses the necessary technology but also the expertise, quality commitment, and collaborative spirit to help you successfully leverage AM for critical marine components. Thorough vetting against these criteria will significantly increase the likelihood of receiving high-quality, reliable 3D printed valve seats that meet or exceed expectations.
Understanding Investment: Cost Factors and Lead Times for 3D Printed Marine Valve Seats
While the technical advantages of 3D printed marine valve seats are compelling, understanding the associated costs and typical lead times is crucial for project planning, budgeting, and managing expectations. The investment required is influenced by a complex interplay of factors related to design, material, processing complexity, and the chosen supplier’s operational structure. Both procurement managers looking for wholesale marine component pricing and engineers evaluating project feasibility need a clear picture of these drivers.
Key Cost Factors:
- 재료비:
- 파우더 가격: The cost per kilogram of the metal powder is a primary driver. Specialized marine alloys like CuNi30Mn1Fe are typically more expensive than common grades like 316L 스테인리스 스틸. Highly specialized superalloys, if needed for extreme applications, would be even more costly. The quality and production method (e.g., PREP vs. Gas Atomization) of the powder also influence its price. Sourcing from reliable metal powder distributors or direct manufacturers like Met3dp ensures quality but comes at a certain cost level.
- Material Consumption: This includes the volume of the final part plus the volume of any support structures required. DfAM efforts to minimize part volume (without compromising function) and reduce support needs directly impact material cost. Material lost during processing (e.g., powder degradation over reuse cycles) is also factored into the supplier’s pricing.
- Machine Operation Cost (Print Time):
- 구축 시간: The longer it takes to print the part(s), the higher the cost allocated to machine usage. Build time depends on:
- Part Volume: Larger parts naturally take longer.
- Part Height: Each layer adds time; taller parts take longer than flat parts of the same volume.
- 복잡성: Intricate features and numerous scan vectors can increase print time per layer.
- Nesting Density: How many parts can be efficiently packed onto a single build plate affects the per-part machine time allocation.
- 머신 시간당 요금: This rate reflects the amortization of the expensive AM machine, maintenance costs, energy consumption, facility overheads, and operator time. Rates vary significantly based on machine type, supplier location, and utilization.
- 구축 시간: The longer it takes to print the part(s), the higher the cost allocated to machine usage. Build time depends on:
- 인건비:
- 사전 처리: Engineering time for DfAM consultation, build preparation (orientation, support generation), and programming the machine.
- Machine Setup & Monitoring: Operator time for loading powder, setting up the build, monitoring the print process (though often highly automated), and unloading the finished build.
- 후처리: This can be a 중요한 labor component. Manual support removal, setup and operation of CNC machines for critical features, surface finishing (blasting, polishing), cleaning, passivation, and inspection all require skilled labor time. The more complex the part and the tighter the requirements, the higher the post-processing labor cost.
- Post-Processing Costs (Beyond Labor):
- Consumables: Cost of tooling for machining, abrasive media for blasting/tumbling, acids for passivation, gases for heat treatment/HIP.
- Equipment Time: Cost associated with using furnaces for stress relief/HIP, CNC machines, CMMs for inspection, NDT equipment.
- Outsourcing Fees: If certain steps (e.g., HIP, specialized NDT, complex machining) are outsourced, these costs are passed on.
- Quality Assurance and Inspection:
- Basic QA: Visual inspection, standard dimensional checks.
- Advanced QA: CMM programming and measurement time, surface roughness testing, NDT (X-ray, CT, dye penetrant), material testing (if required per batch or specification) – all add cost. The level of QA required by marine standards or classification societies will impact the final price.
- Supplier Overhead and Profit:
- Indirect Costs: Facility costs, administration, sales, R&D, certifications, insurance.
- Profit Margin: The margin the supplier needs to operate sustainably and reinvest in technology.
Table: Major Cost Drivers for 3D Printed Marine Valve Seats
Cost Driver Category | Specific Factors | Impact Level (Typical) | How to Potentially Mitigate / Optimize |
---|---|---|---|
재질 | Powder type (CuNi > 316L), Powder quality, Part volume, Support volume | 높음 | Choose cost-effective material where suitable, DfAM for volume/support reduction. |
Machine Operation | Build height, Part volume/complexity, Nesting efficiency, Machine hourly rate | 높음 | DfAM for print time reduction (e.g., flatter orientation if feasible), Efficient nesting by supplier. |
Labor (Post-Processing) | Support removal complexity, Machining requirements (tolerance/finish), Finishing effort, Inspection complexity | 높음 | DfAM for easier support removal & minimizing required machining, Specify finishes only where necessary. |
Labor (Other) | DfAM support needed, Build setup/monitoring | Medium | Provide clear design inputs, Batch production efficiencies. |
Post-Processing (Other) | Consumables, Furnace/CNC time, HIP (if required), Outsourcing | 중간-높음 | Avoid unnecessary high-end finishing or HIP unless critical, Choose supplier with integrated capabilities. |
품질 보증 | Level of inspection (visual, CMM, NDT), Certification requirements | Medium | Clearly define necessary QA level based on criticality, not over-specify. |
Overhead & Profit | Supplier’s business structure | Medium | Compare quotes, but prioritize value (quality, reliability) over lowest price from potentially less capable AM manufacturers. |
시트로 내보내기
Lead Time Factors:
Lead time, the duration from order placement to part delivery, is often as critical as cost, especially for urgent replacement parts needed to prevent vessel downtime.
- Engineering & Preparation: Time for final design review/optimization (DfAM), build file preparation, and scheduling the job into the production queue (can range from hours to days).
- Machine Queue Time: How busy the supplier’s relevant machines are. This can vary significantly, from days to weeks, depending on demand and supplier capacity.
- Print Time: The actual time the part spends printing in the machine. Can range from hours (for small, simple parts) to many days (for large, complex parts or full build plates). EBM processes are sometimes faster for bulk material deposition than LPBF.
- Cooling Time: Time required for the build plate and parts to cool down sufficiently before removal from the machine (typically several hours).
- 후처리 시간: This is often the most variable and potentially longest component.
- Stress Relief: Typically 8-24 hours (including heat-up/cool-down).
- Support Removal & Basic Finishing: Can range from hours to days depending on complexity.
- 가공: Setup and machining time for critical features can take days, especially if complex multi-axis machining or grinding/lapping is needed. Queues for machining centers also play a role.
- HIP/Heat Treatment: Can add several days (including shipping to/from specialized facilities if outsourced).
- QA/Inspection: From hours for basic checks to days for comprehensive NDT and CMM verification.
- 해운: Transit time from the supplier to the customer’s location.
Typical Lead Time Range:
For a moderately complex marine valve seat requiring standard post-processing (stress relief, support removal, machining of sealing faces, basic finishing, standard QA):
- Expedited (Priority Service): Potentially 1-2 weeks (if machine time is immediately available and post-processing is streamlined).
- Standard: More typically 3-6 weeks.
- Complex Parts / High QA / HIP: Can extend to 6-10 weeks or more.
It is crucial to discuss lead time requirements clearly with potential metal AM service providers and understand the breakdown of time estimates. Factors like batch size also influence lead time dynamics (e.g., printing multiple parts simultaneously saves relative machine time but might increase overall post-processing duration).
In conclusion, while metal AM offers transformative potential, it represents a significant investment. Costs are driven by material choices, processing time (print and post-print), labor intensity, and quality requirements. Lead times are influenced by machine availability, print duration, and particularly the extent of post-processing needed. By understanding these factors and working with transparent, efficient suppliers like Met3dp, who may offer advantages through integrated powder production and advanced printing systems, marine industry players can make informed decisions and effectively budget for leveraging this powerful technology.

Frequently Asked Questions (FAQ) about 3D Printed Marine Valve Seats
Here are answers to some common questions regarding the use of metal additive manufacturing for marine valve seats:
1. Are 3D printed marine valve seats as strong and reliable as traditionally cast or forged ones?
Yes, and potentially even superior in certain aspects, provided they are designed, manufactured, and post-processed correctly. Metal AM processes like PBF, when using high-quality powders (like CuNi30Mn1Fe 또는 316L from specialized producers such as Met3dp) and optimized parameters, can produce parts with near 100% density. This often results in fine-grained microstructures with mechanical properties (yield strength, tensile strength, fatigue resistance) that can match or exceed those of equivalent cast materials. Forged materials generally exhibit excellent strength due to grain flow alignment, but AM offers greater design freedom. The key lies in:
- Appropriate Material Selection: Choosing alloys with proven performance in marine environments.
- Design for Additive Manufacturing (DfAM): Optimizing the geometry for both function and the AM process.
- 프로세스 제어: Using validated printing parameters on well-maintained machines.
- 필수 후처리: Including stress relief, HIP (if necessary for critical fatigue life), and precision machining of sealing surfaces.
- Rigorous Quality Assurance: Implementing thorough inspection and testing protocols. When these conditions are met, 3D printed valve seats offer excellent reliability, often enhanced by superior material choices (like inherent biofouling resistance with CuNi) and optimized designs not possible with traditional methods. Collaboration with experienced AM solutions providers is crucial to ensure this level of quality.
2. What is the typical lead time for obtaining a set of replacement 3D printed marine valve seats?
Lead times can vary significantly based on several factors, but a typical range for standard production might be 3~6주. Here’s a breakdown of influences:
- Part Complexity & Size: Larger, more complex parts take longer to print and potentially post-process.
- Material: Some materials may have specific requirements (e.g., longer heat treatment cycles).
- 사후 처리 요구 사항: Extensive machining, polishing, or optional processes like HIP add considerable time. Machining sealing faces to tight tolerances is often a key time factor.
- Supplier Capacity & Queue: How busy the supplier’s machines and post-processing departments are.
- 수량: Printing a small batch might be faster per part than a single prototype due to shared setup/cooldown times, but the overall time will increase.
- Expedited Services: Many suppliers offer faster turnaround (potentially 1-2 weeks) for urgent needs, but this comes at a premium cost. It’s essential to get a specific quote with a lead time estimate from your chosen additive manufacturing partner based on your final design and requirements.
3. Can any existing valve seat design simply be 3D printed?
While it’s technically possible to print many existing designs, it’s often not optimal and may not yield the best results or cost-effectiveness. Directly printing a design created for casting or machining fails to leverage AM’s strengths and may even introduce challenges (e.g., features that are difficult to support or post-process). 적층 제조를 위한 설계(DfAM) is highly recommended. This involves reviewing and potentially modifying the design to:
- Leverage Complexity: Optimize internal flow paths or integrate features.
- Minimize Supports: Adjust angles and shapes to be more self-supporting.
- Add Machining Allowances: Ensure critical surfaces can be finished to required tolerances.
- Consolidate Parts: Combine adjacent components if feasible.
- Reduce Weight: Use topology optimization where beneficial. Collaborating with AM experts, like the application engineers at Met3dp, during the design or redesign phase is crucial to ensure the valve seat is optimized for printability, performance, and cost when using additive manufacturing. They can help adapt legacy designs or develop new ones that maximize the benefits of the technology.
4. How can I ensure the quality and consistency of 3D printed marine components like valve seats?
Ensuring quality for critical marine parts produced via AM requires a multi-faceted approach, focusing heavily on supplier selection and process control:
- Choose a Reputable Supplier: Select a partner with proven experience, robust Quality Management Systems (ISO 9001, AS9100 preferred), and ideally, familiarity with marine industry expectations or certifications. Look for suppliers like Met3dp who control critical inputs like high-quality metal powder production.
- Material Control & Traceability: Verify the supplier uses certified powder batches and maintains traceability throughout the process.
- 검증된 프로세스: Ensure the supplier uses validated and locked-down printing parameters for the specific material and machine combination.
- Comprehensive Post-Processing: Confirm all necessary steps (stress relief, machining, finishing, passivation for 316L) are performed correctly.
- Rigorous Inspection & Testing: Define clear acceptance criteria and ensure the supplier performs required dimensional checks, surface finish measurements, and potentially NDT (Non-Destructive Testing like X-ray or dye penetrant) to verify integrity. Request inspection reports and certificates of conformity.
- Collaboration & Communication: Maintain open communication with the supplier throughout the process. By focusing on these areas, particularly vetting the AM manufacturer’s quality systems and technical capabilities, you can gain confidence in the reliability and consistency of 3D printed marine valve seats.
Conclusion: The Future is Additive – Enhancing Marine Reliability with 3D Printed Valve Seats
The maritime industry operates at the confluence of immense operational demands and harsh environmental challenges. Ensuring the reliability of every component, particularly critical elements like valve seats within essential systems, is paramount for safety, efficiency, and environmental protection. While traditional manufacturing methods have long served the industry, metal additive manufacturing presents a powerful, modern alternative, offering transformative advantages specifically suited to overcoming the unique hurdles faced at sea.
As explored throughout this post, utilizing metal 3D printing – specifically Powder Bed Fusion techniques with high-performance, corrosion-resistant alloys like CuNi30Mn1Fe 및 316L 스테인리스 스틸 – enables the production of marine valve seats with characteristics often unattainable through conventional means. The ability to create complex geometries optimized for flow and sealing, coupled with the potential for enhanced material properties derived from controlled melting and solidification, directly translates to improved valve performance and extended component lifespan. The inherent resistance of CuNi alloys to both seawater corrosion and biofouling, readily printable via AM, offers a significant operational advantage in many marine systems.
Furthermore, the agility afforded by AM cannot be overstated. The capacity for 신속한 프로토타이핑, 주문형 생산 without dedicated tooling, and the creation of a digital inventory drastically reduces lead times for replacement parts. This supply chain revolution minimizes costly vessel downtime, a critical economic driver in the maritime sector. By leveraging DfAM principles, engineers can design lighter, consolidated, and more efficient components, pushing the boundaries of marine engineering.
However, realizing these benefits requires careful consideration and strategic implementation. Success hinges on understanding and applying Design for Additive Manufacturing, executing essential post-processing steps (particularly stress relief and precision machining of critical surfaces), and navigating potential challenges like residual stress and quality assurance. Critically, partnering with the right 금속 첨가 제조 공급업체 – one with deep technical expertise, robust quality systems, high-quality material control (like the advanced powder production capabilities of Met3dp), and a collaborative approach – is fundamental.
The journey towards broader adoption of AM in the marine industry is well underway. For engineers seeking performance breakthroughs and procurement managers aiming for improved lifecycle costs and supply chain resilience, 3D printed corrosion-resistant valve seats represent a compelling application of this technology. By embracing additive manufacturing, the maritime sector can enhance the reliability and efficiency of its vessels, paving the way for a more sustainable and technologically advanced future. Companies like Met3dp, with their comprehensive portfolio of printers, high-performance metal powders, and deep application expertise, stand ready to partner with the industry to navigate this transformation and unlock the full potential of additive manufacturing for the demanding world of marine operations.
공유
중국 칭다오에 본사를 둔 선도적인 적층 제조 솔루션 제공업체인 MET3DP Technology Co. 당사는 산업용 3D 프린팅 장비와 고성능 금속 분말을 전문으로 합니다.
관련 기사
Met3DP 소개
최근 업데이트
제품
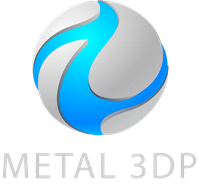
3D 프린팅 및 적층 제조용 금속 분말