pros y contras de los distintos procesos de producción de polvo metálico impreso en 3D
Índice
Imagine construir intrincados objetos metálicos capa a capa, con una libertad de diseño sin precedentes y un desperdicio mínimo. Esa es la magia de Polvos metálicos impresos en 3D. Pero antes de que estos minúsculos granos metálicos se conviertan en los componentes básicos de creaciones revolucionarias, deben producirse con un cuidado meticuloso.
Existen varios procesos de producción de polvo metálico, cada uno con sus propias ventajas e inconvenientes. La elección del más adecuado depende de las necesidades específicas de su proyecto impreso en 3D. Esta completa guía se adentra en el fascinante mundo de la producción de polvo metálico y le proporciona los conocimientos necesarios para tomar decisiones informadas para sus proyectos impresos en 3D.
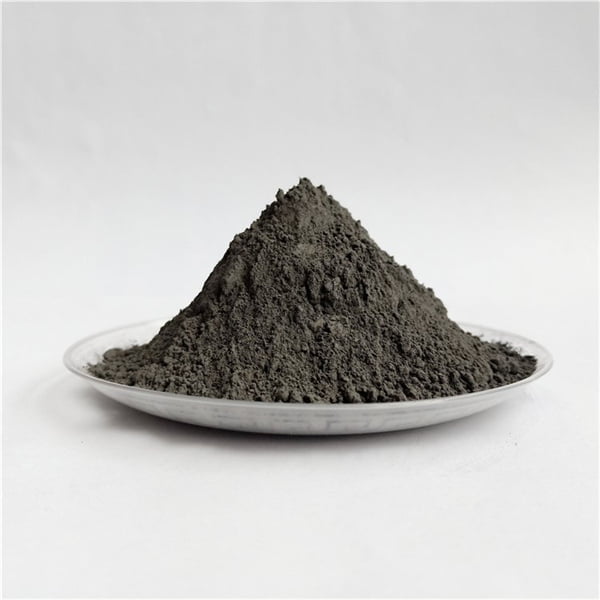
Polvos metálicos impresos en 3D
Los polvos metálicos son los héroes anónimos de la impresión 3D. Estas finas partículas metálicas de flujo libre, cuyo tamaño oscila entre 10 y 150 micrómetros, actúan como materia prima para diversas técnicas de fabricación aditiva (AM) de metales, como la fusión de lecho de polvo láser (LPBF) y el chorro de aglutinante.
La calidad y las propiedades del polvo metálico influyen significativamente en las características finales de la pieza impresa, incluida su resistencia, acabado superficial y rendimiento general. Por lo tanto, seleccionar el proceso óptimo de producción de polvo metálico resulta crucial para lograr los resultados deseados en la impresión 3D.
Exploración de métodos de producción de polvo metálico
La producción de polvo metálico utiliza diversas técnicas para descomponer el metal a granel en partículas del tamaño y la morfología deseados. Profundicemos en cuatro métodos principales, cada uno con su propia propuesta de venta y un conjunto de consideraciones:
1. Métodos de atomización: Descomposición de metales a granel con precisión
Los métodos de atomización son los caballos de batalla de la producción de polvo metálico. Consisten en transformar el metal fundido en una fina niebla de partículas mediante diversas técnicas:
- Ventajas y desventajas del método de atomización por plasma: La atomización por plasma utiliza una antorcha de plasma de alta temperatura para fundir la materia prima metálica. A continuación, el metal fundido se expulsa a una corriente de gas a alta velocidad, lo que provoca su descomposición en partículas finas. Este método ofrece un excelente control sobre el tamaño y la morfología de las partículas, lo que lo hace adecuado para producir polvos de alta calidad para aplicaciones exigentes como implantes aeroespaciales y médicos. Sin embargo, el elevado consumo de energía y la compleja configuración del equipo pueden hacer que sea una opción más cara.
- Ventajas y desventajas del método de atomización con electrodo rotatorio (REA): La REA emplea un electrodo que gira rápidamente sumergido en un baño de metal fundido. La fuerza centrífuga generada por la rotación lanza pequeñas gotas de metal que se solidifican en partículas esféricas al enfriarse en una corriente de gas. Este método ofrece altos índices de producción y un buen control de la forma de las partículas, por lo que es ideal para una amplia gama de polvos metálicos. Sin embargo, el proceso puede introducir algunas tensiones internas en las partículas, lo que puede afectar a las propiedades finales de la pieza impresa.
- Ventajas e inconvenientes del método de atomización con agua: La atomización con agua adopta un enfoque más sencillo. El metal fundido se vierte en un chorro de agua a alta presión, lo que provoca su desintegración en finas partículas. Este método es rentable y ofrece altos índices de producción, por lo que es muy adecuado para aplicaciones a granel. Sin embargo, las partículas resultantes pueden tener una forma irregular y una mayor cantidad de óxidos superficiales, lo que puede afectar a su fluidez e imprimibilidad.
Elegir el método de atomización adecuado:
El método de atomización óptimo depende de factores como el tamaño y la morfología deseados de las partículas, el tipo de material y los requisitos de la aplicación.
Por ejemplo, si necesita partículas esféricas de alta precisión para piezas aeroespaciales críticas, la atomización por plasma puede ser la opción preferida. En cambio, para aplicaciones sensibles a los costes en las que la forma de las partículas es menos crítica, la atomización con agua podría ser una opción viable.
2. Fresado mecánico: Moler el metal hasta convertirlo en polvo perfecto
La molienda mecánica adopta un enfoque más físico. El metal a granel se tritura y se muele en partículas finas mediante molinos de alta energía, como los molinos de bolas y los molinos attritor.
- Ventajas y desventajas del fresado mecánico: Este método ofrece un buen control sobre la distribución del tamaño de las partículas y puede tratar una amplia gama de materiales, incluidos los metales frágiles. Sin embargo, la molienda mecánica puede introducir tensiones internas y contaminación en el polvo debido al proceso de molienda. Además, puede ser difícil conseguir tamaños de partícula muy finos.
3. Métodos de reducción química: Un enfoque transformador
Los métodos de reducción química se basan en reacciones químicas para convertir los óxidos metálicos u otros compuestos en polvos metálicos.
- Ventajas e inconvenientes de los métodos de reducción química: Estos métodos ofrecen una gran pureza y pueden producir polvos con morfologías únicas. Sin embargo, pueden ser complejos, llevar mucho tiempo y generar subproductos peligrosos. Además, controlar el tamaño y la morfología de las partículas puede resultar complicado.
4. Electrólisis: La formación de partículas metálicas mediante la electricidad
La electrólisis aprovecha el poder de la electricidad para producir polvos metálicos. Se hace pasar una corriente eléctrica a través de una solución de sales metálicas, lo que hace que los iones metálicos se depositen en un cátodo en forma de partículas diminutas.
- Ventajas y desventajas de la electrólisis: La electrólisis ofrece una gran pureza y un buen control del tamaño y la morfología de las partículas. Sin embargo, el proceso puede ser lento y consumir mucha energía, lo que limita su uso para la producción a gran escala. Además, a menudo se limita a metales específicos que pueden depositarse fácilmente a partir de electrolitos.
Un nicho de aplicación para la impresión 3D:
La electrólisis tiene una aplicación limitada en la impresión 3D debido a su lenta velocidad de producción y a su idoneidad para una gama más reducida de metales en comparación con otros métodos.
Elección de un proceso de producción de polvo metálico
Seleccionar el proceso ideal de producción de polvo metálico va más allá de la técnica en sí. Hay otros factores que desempeñan un papel crucial:
- Compatibilidad de materiales: No todos los métodos son adecuados para todos los tipos de metales. Algunos métodos pueden no ser capaces de manejar el punto de fusión o la fragilidad de un material específico.
- Tamaño y morfología deseados de las partículas: El tamaño y la forma de las partículas metálicas influyen significativamente en su fluidez, su capacidad de impresión y las propiedades de la pieza final. Técnicas como la atomización por plasma ofrecen un mayor control sobre estos aspectos.
- Pureza del polvo: La presencia de impurezas como óxidos u otros contaminantes puede afectar a la imprimibilidad y a las propiedades mecánicas de la pieza final. Procesos como los métodos de reducción química pueden ofrecer polvos de gran pureza.
- Costo: Los costes de producción varían en función de la complejidad del método, el consumo de energía y los requisitos de manipulación del material. La atomización con agua suele ser una opción más rentable, mientras que la atomización con plasma puede resultar más cara.
- Impacto medioambiental: Algunos métodos, como los que implican subproductos peligrosos, pueden tener una mayor huella ambiental. Las prácticas sostenibles y la gestión responsable de los residuos son consideraciones cruciales.
Encontrar la pareja perfecta:
Si evalúa detenidamente estos factores y los ajusta a los requisitos específicos de su proyecto, podrá tomar una decisión informada sobre el proceso de producción de polvo metálico más adecuado para sus necesidades de impresión 3D.
Consideraciones adicionales para el éxito
Aunque el proceso de producción del polvo metálico desempeña un papel fundamental, la obtención de resultados óptimos en la impresión 3D va más allá del propio polvo. He aquí algunas consideraciones adicionales:
- Manipulación y almacenamiento de polvo: La manipulación y el almacenamiento adecuados son esenciales para mantener la calidad del polvo y evitar la absorción de humedad o la contaminación. Esto puede implicar el uso de entornos de gas inerte o el almacenamiento con humedad controlada, dependiendo del material.
- Postprocesado de polvos: Determinados procesos pueden requerir pasos adicionales, como el tamizado o el secado, para conseguir la distribución granulométrica o el contenido de humedad deseados para una imprimibilidad óptima.
- Compatibilidad con máquinas: El polvo metálico elegido debe ser compatible con la tecnología y los parámetros de fabricación específicos de su impresora 3D.
Si tiene en cuenta estos aspectos junto con el proceso de producción de polvo metálico, podrá garantizar una experiencia de impresión 3D fluida y satisfactoria, allanando el camino para la creación de objetos metálicos innovadores.
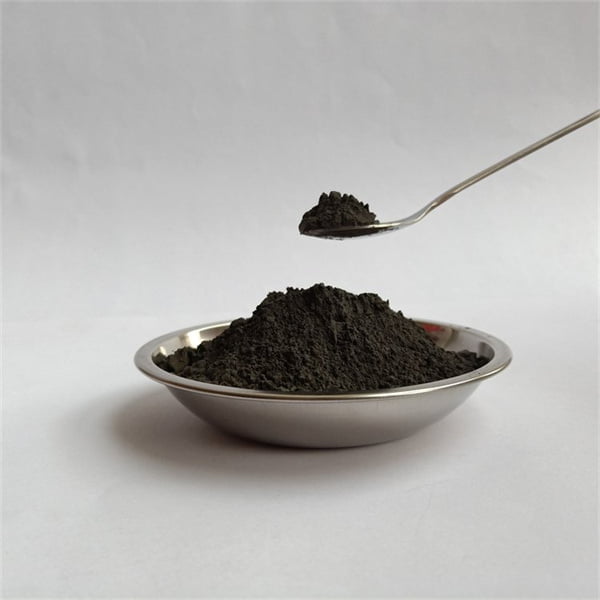
PREGUNTAS FRECUENTES
P: ¿Cuál es el método más habitual para producir polvos metálicos para impresión 3D?
R: Los métodos de atomización, en particular las técnicas de atomización con gas como la atomización con plasma y la atomización con electrodos giratorios, son los métodos más utilizados para producir polvos metálicos para impresión 3D debido a su capacidad para lograr un buen control del tamaño y la morfología de las partículas.
P: ¿Qué factores debo tener en cuenta al elegir un proceso de producción de polvo metálico?
R: Influyen varios factores, como el tipo de material, el tamaño y la morfología deseados de las partículas, los requisitos de pureza del polvo, los costes y el impacto medioambiental.
P: ¿Existe un único método "mejor" para la producción de polvo metálico?
R: No hay un único método que sea supremo. La elección óptima depende de los requisitos específicos de su proyecto y de las propiedades que busque en la pieza impresa final.
P: ¿Cuáles son algunos de los retos asociados a la producción de polvo metálico?
R: Mantener un tamaño de partícula y una morfología homogéneos, alcanzar altos niveles de pureza y equilibrar la rentabilidad con las características deseadas del polvo son algunos de los retos a los que se enfrenta la producción de polvo metálico.
P: ¿Cómo evolucionará la producción de polvo metálico en el futuro?
R: En el futuro de la producción de polvo metálico es probable que se produzcan avances tecnológicos que conduzcan a procesos más eficientes y sostenibles. Además, se están investigando nuevas técnicas de producción de polvo adaptadas a materiales y aplicaciones específicos.
Si conoce los entresijos de los procesos de producción de polvo metálico y su impacto en los resultados de la impresión 3D, podrá embarcarse en la creación de objetos metálicos innovadores y funcionales con mayor confianza y control.
Compartir
MET3DP Technology Co., LTD es un proveedor líder de soluciones de fabricación aditiva con sede en Qingdao, China. Nuestra empresa está especializada en equipos de impresión 3D y polvos metálicos de alto rendimiento para aplicaciones industriales.
Solicite información para obtener el mejor precio y una solución personalizada para su empresa.
Artículos relacionados
Acerca de Met3DP
Actualización reciente
Nuestro producto
CONTACTO
¿Tiene alguna pregunta? ¡Envíenos un mensaje ahora! Atenderemos su solicitud con todo un equipo tras recibir su mensaje.
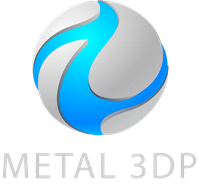
Polvos metálicos para impresión 3D y fabricación aditiva