Protectores térmicos personalizados para motores mediante impresión 3D de metales
Índice
Introducción: Revolución en la gestión térmica de motores con protectores térmicos personalizados impresos en 3D de metal
En los entornos de alto riesgo de las aplicaciones aeroespaciales, automotrices e industriales, la gestión térmica eficaz no es solo un potenciador del rendimiento, sino una necesidad crítica. Los motores, por su propia naturaleza, generan un calor inmenso, lo que plantea riesgos importantes para los componentes circundantes, comprometiendo la eficiencia y, potencialmente, provocando fallos catastróficos si no se gestionan correctamente. Los protectores térmicos del motor son los héroes anónimos en este campo de batalla térmico, actuando como barreras cruciales que protegen los componentes electrónicos sensibles, las líneas de fluidos, los elementos estructurales e incluso los compartimentos de pasajeros de temperaturas excesivas. Tradicionalmente, la fabricación de estos componentes vitales, especialmente aquellos con geometrías complejas requeridas para los compartimentos de motor modernos y compactos, ha implicado herramientas costosas, largos plazos de entrega y compromisos de diseño inherentes a métodos como el estampado o el hidroformado. Sin embargo, se está produciendo un cambio de paradigma, impulsado por los avances en fabricación aditiva (AM) de metalescomúnmente conocido como metal Impresión 3D.
Esta tecnología transformadora desbloquea una libertad de diseño sin precedentes, lo que permite la creación de protectores térmicos de motor que antes eran imposibles o prohibitivamente caros de producir. Al construir piezas capa por capa directamente a partir de diseños digitales utilizando polvos metálicos de alto rendimiento, AM de metales elimina la necesidad de herramientas tradicionales, reduce drásticamente los plazos de entrega de prototipos y series personalizadas, y facilita la integración de características complejas como canales de enfriamiento internos o estructuras de celosía que ahorran peso. Para los ingenieros que se esfuerzan por lograr un embalaje y una eficiencia térmica óptimos, y para los gerentes de adquisiciones que buscan componentes personalizados , la impresión 3D de metales ofrece una solución convincente para la próxima generación gestión térmicaEmpresas como Met3dp, con una profunda experiencia tanto en polvos metálicos avanzados como en sistemas de impresión industrial, están a la vanguardia, lo que permite a las industrias aprovechar AM de metales para obtener soluciones superiores de protección térmica. Este artículo profundiza en el papel fundamental de los protectores térmicos del motor, explora las limitaciones de la fabricación convencional, destaca las convincentes ventajas de la impresión 3D de metales y le guía a través de la selección de materiales para estas aplicaciones exigentes.
¿Qué son los protectores térmicos del motor y por qué son críticos?
Un protector térmico del motor es esencialmente una barrera térmica diseñada para reflejar, absorber o disipar el calor generado por un motor y sus componentes asociados, principalmente el sistema de escape (colectores, convertidores catalíticos, silenciadores). Su función principal es proteger las piezas y sistemas circundantes de los efectos dañinos de las altas temperaturas. La importancia de estos protectores no puede exagerarse en varios sectores:
- Automóvil: En los vehículos, los protectores térmicos protegen los componentes bajo el capó, como los mazos de cables, las tuberías de combustible, las tuberías de freno, los depósitos de plástico, los sensores y las unidades de control electrónico (ECU). También evitan que el calor se irradie hacia el habitáculo, garantizando la comodidad y la seguridad, y protegen la parte inferior de la carrocería y los componentes del chasis. El protector térmico automotriz es fundamental para la longevidad, la fiabilidad y el cumplimiento de las normas de seguridad del vehículo.
- Aeroespacial: Dentro de los motores de las aeronaves y las unidades de potencia auxiliar (APU), los componentes de los motores aeroespaciales funcionan bajo variaciones extremas de temperatura. Los protectores térmicos son vitales para proteger la aviónica sensible, las tuberías hidráulicas, los elementos estructurales (como los mamparos y las góndolas) y garantizar la integridad y la seguridad generales de los sistemas de vuelo. Desempeñan un papel crucial en la prevención de los daños por calor que podrían comprometer la seguridad del vuelo.
- Fabricación industrial: Los motores estacionarios, los generadores, la maquinaria pesada y los equipos de generación de energía también dependen en gran medida de los protectores térmicos. Protegen a los operadores, los equipos circundantes, los sistemas de control y la infraestructura del calor intenso, garantizando la seguridad operativa y evitando el desgaste prematuro o el fallo de la maquinaria adyacente.
- Automovilismo: Las aplicaciones de carreras de alto rendimiento llevan los motores al límite, generando un calor extremo. Los protectores térmicos personalizados son esenciales para proteger los sistemas críticos, optimizar el flujo de aire en el compartimento del motor y garantizar un rendimiento constante en condiciones de carrera exigentes.
Funciones clave de los protectores térmicos del motor:
- Protección térmica: Bloqueo de la transferencia de calor radiante y convectivo para evitar el sobrecalentamiento de los componentes cercanos.
- Mantenimiento del rendimiento: Garantizar que los componentes como los sensores y los dispositivos electrónicos funcionen dentro de su rango de temperatura óptimo.
- Seguridad: Prevención de incendios mediante la protección de materiales inflamables (fluidos, aislamiento) y la protección del personal contra quemaduras.
- Mejora de la durabilidad: Reducción del estrés térmico en las piezas circundantes, lo que prolonga su vida útil.
- Cumplimiento de la normativa: Cumplimiento de las normas del sector en materia de gestión del calor y límites de temperatura de los materiales.
La geometría de los protectores térmicos suele ser compleja, dictada por las estrictas limitaciones de embalaje dentro de los compartimentos del motor. Deben ajustarse estrechamente a la fuente de calor (por ejemplo, el colector de escape) manteniendo al mismo tiempo espacios de aire o aislamiento suficientes para bloquear eficazmente la transferencia de calor a los componentes protegidos. Esta complejidad presenta importantes desafíos para los métodos de fabricación tradicionales.
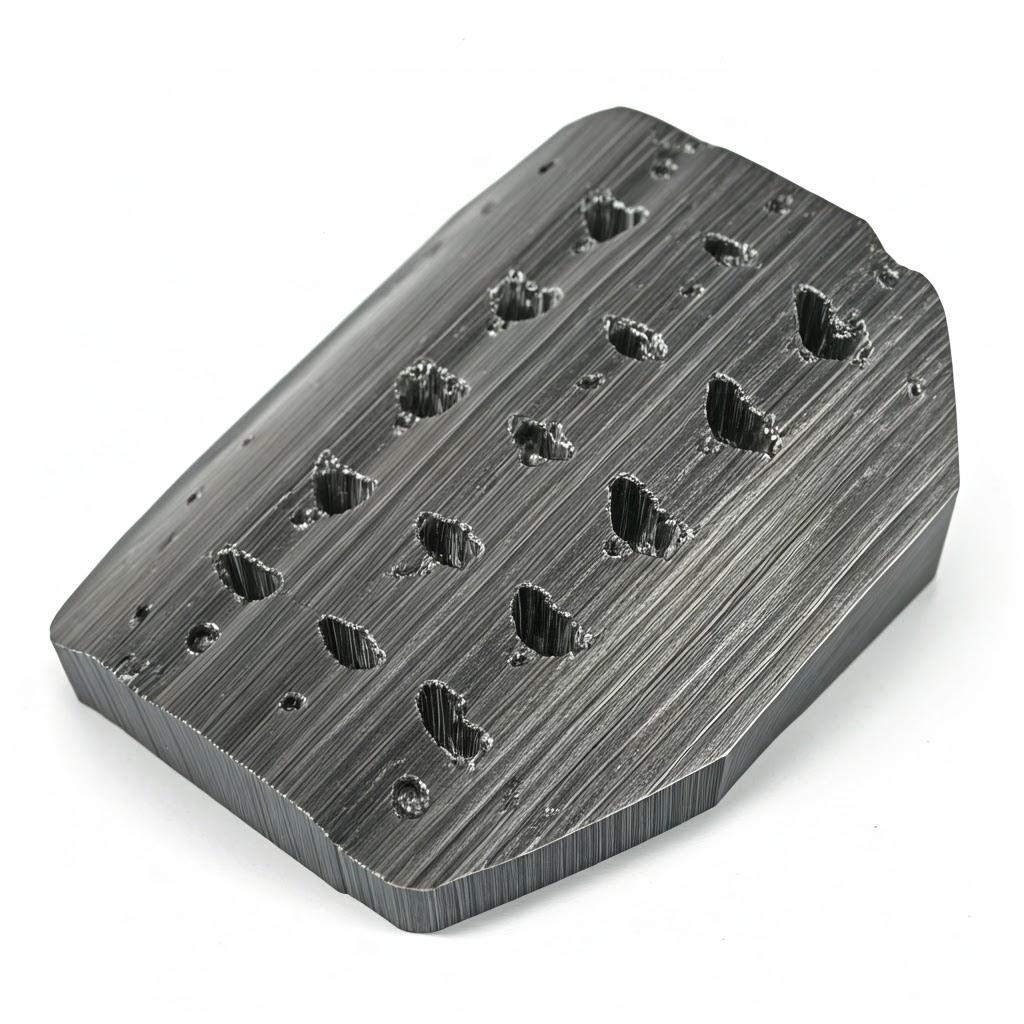
Limitaciones de la fabricación tradicional para protectores térmicos complejos
Durante décadas, los protectores térmicos de los motores se han fabricado predominantemente utilizando técnicas convencionales de chapa metálica como el estampado, el hidroconformado y el embutido profundo. Aunque son eficaces para la producción de gran volumen de diseños relativamente sencillos, estos métodos encuentran importantes limitaciones cuando se enfrentan a la creciente complejidad y a las exigencias de personalización de los motores modernos:
- Altos costos de herramientas: La creación de las matrices y los moldes necesarios para el estampado o el conformado es extremadamente costosa y requiere mucho tiempo. Esto hace que las tiradas de producción de bajo volumen o la fabricación de protectores térmicos personalizados no sean económicamente viables. Cualquier modificación del diseño requiere una costosa re-herramienta.
- Largos plazos de entrega: El proceso de diseño, fabricación y validación de herramientas puede tardar semanas o incluso meses, lo que retrasa significativamente los ciclos de desarrollo de productos y dificulta los esfuerzos de creación rápida de prototipos.
- Restricciones de diseño: Los métodos de conformado tradicionales tienen limitaciones inherentes en cuanto a la complejidad geométrica. Conseguir embuticiones profundas, ángulos agudos, rebajes o características integradas como los salientes de montaje o las estructuras internas suele ser difícil o imposible, lo que obliga a los ingenieros a comprometer el rendimiento térmico o el embalaje óptimos. A menudo, los diseños deben simplificarse para que sean fabricables.
- Residuos materiales: Los procesos de chapa metálica suelen generar una cantidad significativa de material de desecho, especialmente con formas complejas, lo que aumenta los costes generales de los materiales y el impacto medioambiental.
- Complejidad del montaje: Los protectores térmicos complejos suelen requerir que varias piezas estampadas se suelden o se sujeten entre sí, lo que añade pasos de montaje, posibles puntos de fallo y un mayor peso.
- Peso: Las piezas de chapa metálica, aunque son relativamente finas, pueden no estar diseñadas de forma óptima para un peso mínimo, un factor crítico en las aplicaciones aeroespaciales y de automoción de alto rendimiento. Conseguir diseños ligeros a menudo requiere el uso de calibres más finos, lo que puede comprometer la rigidez o el rendimiento térmico.
Estas limitaciones dificultan que los fabricantes puedan iterar rápidamente en los diseños, producir soluciones personalizadas para aplicaciones de nicho u optimizar los protectores térmicos para obtener la máxima eficiencia térmica y un peso mínimo utilizando los enfoques tradicionales. Aquí es precisamente donde surge el potencial disruptivo de impresión 3D en metal la fabricación aditiva.
La ventaja de la fabricación aditiva: ¿Por qué elegir la impresión 3D de metal para los protectores térmicos del motor?
La fabricación aditiva de metales ofrece una potente alternativa para producir protectores térmicos de motor, superando muchas limitaciones de los métodos convencionales y desbloqueando importantes beneficios para los ingenieros y fabricantes:
- Libertad de diseño sin igual: La fabricación aditiva construye las piezas capa por capa directamente a partir de un archivo CAD, lo que permite la creación de geometrías muy complejas sin las limitaciones de las herramientas tradicionales. Esto permite:
- Diseños conformes: Protectores que siguen perfectamente los contornos de los componentes del motor para obtener la máxima eficiencia en espacios reducidos.
- Características integradas: Los puntos de montaje, los soportes, las nervaduras de refuerzo e incluso los logotipos pueden integrarse directamente en la pieza, lo que reduce la complejidad del montaje.
- Estructuras Internas: Ligero estructuras reticulares o los canales de refrigeración internos pueden incorporarse para mejorar el rendimiento térmico y reducir la masa simultáneamente.
- Optimización de la topología: Se pueden utilizar algoritmos para eliminar material de las zonas de baja tensión, creando estructuras de forma orgánica, muy eficientes y ligeras, imposibles de fabricar de otro modo.
- Creación rápida de prototipos e iteración: Los nuevos diseños de protectores térmicos pueden imprimirse y probarse en días en lugar de semanas o meses. Esto acelera los ciclos de desarrollo, permite una rápida validación del rendimiento térmico y permite a los ingenieros refinar los diseños rápidamente basándose en pruebas en el mundo real. La creación rápida de prototipos de protectores térmicos se vuelve factible y rentable.
- Eliminación de herramientas: La fabricación aditiva no requiere herramientas específicas para las piezas (matrices, moldes). Esto reduce drásticamente los costes iniciales y los plazos de entrega, lo que la hace ideal para:
- Producción personalizada y de bajo volumen: Fabricación de protectores térmicos a medida para vehículos especializados, prototipos o aplicaciones del mercado de accesorios.
- Fabricación a la carta: Producción de piezas sólo cuando se necesitan, lo que reduce los costes de inventario y permite el almacenamiento virtual.
- Potencial de aligeramiento: Mediante la optimización de la topología y el uso de estructuras reticulares, la fabricación aditiva de metales puede producir protectores térmicos que son significativamente más ligeros que sus homólogos fabricados tradicionalmente, manteniendo o incluso mejorando la integridad estructural y el rendimiento térmico. Esto es crucial para los sectores aeroespacial y de automoción de alto rendimiento, donde cada gramo cuenta.
- Versatilidad de materiales: Los procesos de fabricación aditiva pueden utilizar una amplia gama de polvos metálicos de alto rendimiento, incluyendo aleaciones de aluminio, aleaciones de titanio y superaleaciones de níquel (como las producidas por expertos por Met3dp utilizando la atomización avanzada con gas), lo que permite a los ingenieros seleccionar el material óptimo en función de los requisitos de temperatura específicos, los objetivos de peso y las condiciones ambientales.
- Consolidación de piezas: Los conjuntos complejos que antes requerían múltiples componentes y sujetadores a menudo pueden consolidarse en una sola pieza integrada impresa en 3D, simplificando el montaje, reduciendo el número de piezas y, potencialmente, mejorando la fiabilidad.
- Optimización del rendimiento: La libertad de diseño permite la creación de protectores térmicos con propiedades superiores de aislamiento o disipación térmica, adaptadas con precisión a las necesidades específicas de la aplicación.
Al aprovechar estas ventajas, los fabricantes pueden producir protectores térmicos de motor personalizados que ofrecen un rendimiento superior, un peso reducido y plazos de desarrollo más rápidos en comparación con los métodos tradicionales, lo que proporciona una importante ventaja competitiva en las industrias exigentes.
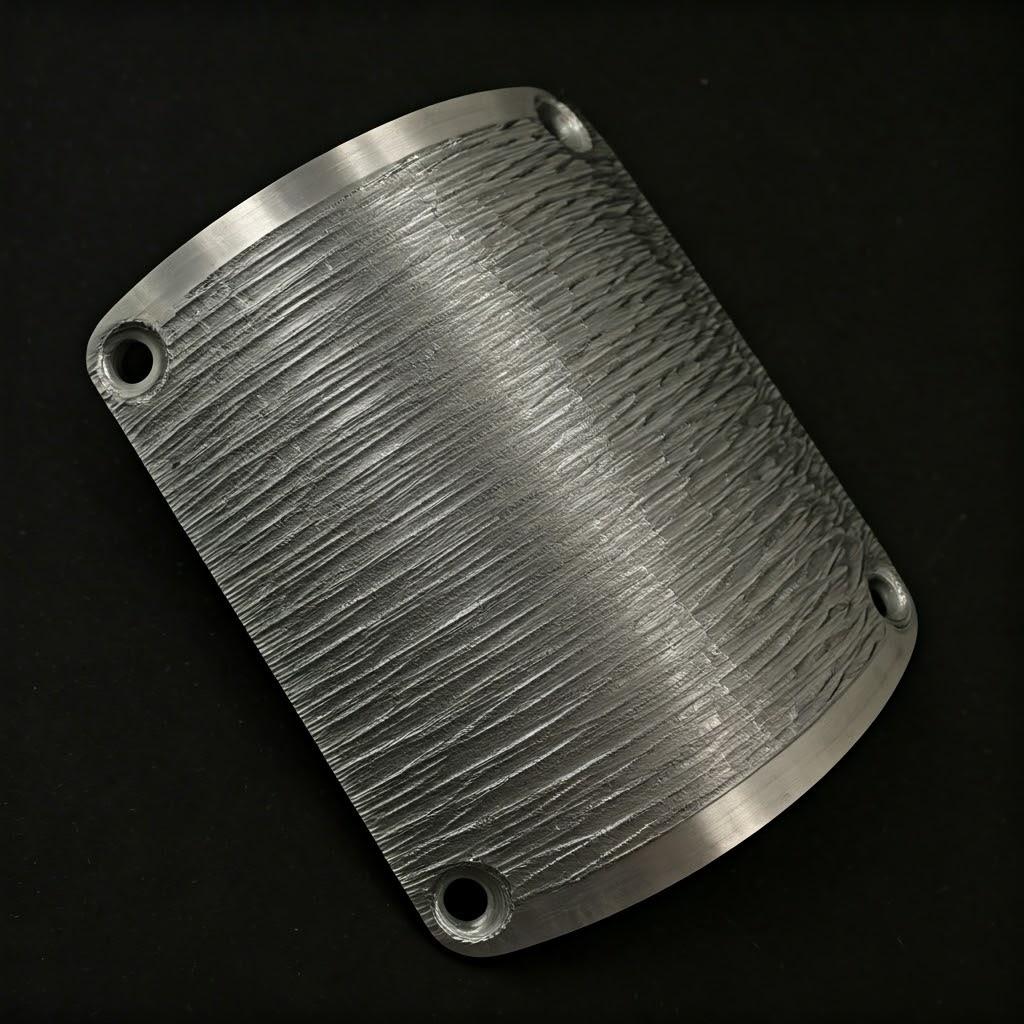
Inmersión profunda en los materiales: Selección de los polvos metálicos adecuados para un rendimiento óptimo (AlSi10Mg, Ti-6Al-4V, IN625)
La elección del material correcto es primordial para el rendimiento y la longevidad de un protector térmico del motor. La fabricación aditiva de metales ofrece una diversa gama de materiales, pero para las aplicaciones de protectores térmicos, propiedades específicas como la resistencia a la temperatura, el peso, la resistencia a la corrosión y la conductividad térmica son factores clave en la toma de decisiones. Los polvos recomendados – AlSi10Mg, Ti-6Al-4V e IN625 – representan un espectro de capacidades adecuadas para diversos entornos de motor. El suministro de polvos metálicos consistentes y de alta calidad es crucial para una impresión exitosa, y empresas como Met3dp, que utilizan tecnología avanzada tecnologías de atomización de gas y PREP, aseguran la producción de polvos altamente esféricos con excelente fluidez, esencial para lograr piezas densas y de alto rendimiento. Examinemos las características de estos materiales clave para protectores térmicos.:
- AlSi10Mg (Aleación de aluminio):
- Propiedades: Esta aleación de aluminio-silicio-magnesio es conocida por su buena relación resistencia-peso, excelente conductividad térmica y resistencia a la corrosión relativamente buena. Es una de las aleaciones de aluminio más utilizadas en la fabricación aditiva.
- Idoneidad para protectores térmicos: Más adecuado para aplicaciones con requisitos de temperatura moderados (típicamente hasta 150-200°C, aunque la idoneidad depende de la carga y la duración). Su alta conductividad térmica se puede aprovechar en diseños que buscan disipar el calor rápidamente. Su principal ventaja es su baja densidad, lo que lo hace ideal para aligeramiento componentes en aplicaciones automotrices o aeroespaciales donde las temperaturas no son extremas.
- Consideraciones: Su punto de fusión más bajo en comparación con las aleaciones de titanio o níquel restringe su uso cerca de fuentes de muy alta temperatura, como colectores de escape o turbocompresores, sin espacios de aire significativos o características de diseño de aislamiento.
- Ventaja de Met3dp: El suministro de polvo AlSi10Mg consistente con una distribución de tamaño de partícula controlada, como el que ofrece Met3dp, es vital para lograr propiedades mecánicas y un acabado superficial óptimos en las piezas impresas.
- Ti-6Al-4V (Aleación de titanio – Grado 5):
- Propiedades: Esta es la aleación de titanio por excelencia, que ofrece una excelente combinación de alta resistencia, baja densidad (aproximadamente un 40% más ligera que el acero), excelente resistencia a la corrosión y buen rendimiento a temperaturas elevadas (temperaturas de servicio típicamente hasta 350-400°C, potencialmente más altas para duraciones cortas).
- Idoneidad para protectores térmicos: El Ti-6Al-4V es una excelente opción para aplicaciones que requieren un ahorro de peso significativo combinado con una mayor resistencia a la temperatura que la que pueden ofrecer las aleaciones de aluminio. Se utiliza ampliamente en los componentes de los motores aeroespaciales y sistemas de escape automotrices de alto rendimiento donde tanto la tolerancia al calor como la masa mínima son fundamentales. Su baja conductividad térmica también lo hace efectivo como barrera térmica, lo que ralentiza la transferencia de calor.
- Consideraciones: Las aleaciones de titanio son más caras que el aluminio y requieren un manejo y un posprocesamiento específicos (como el alivio de tensiones en vacío o atmósfera inerte) para mantener propiedades óptimas. La impresión requiere un control cuidadoso de los parámetros para gestionar las tensiones residuales.
- Ventaja de Met3dp: Met3dp posee una experiencia significativa en el procesamiento de materiales reactivos como las aleaciones de titanio, ofreciendo polvo de Ti-6Al-4V de alta pureza y parámetros de impresión optimizados en sus sistemas avanzados para garantizar la integridad de los componentes.
- IN625 (Inconel 625 – Superaleación de níquel):
- Propiedades: Inconel 625 es una superaleación de níquel-cromo reconocida por su excepcional resistencia a altas temperaturas, excelente resistencia a la corrosión y a la oxidación, y resistencia a la fatiga. Mantiene sus propiedades en un rango de temperatura muy amplio, funcionando de forma fiable a temperaturas criogénicas de hasta 980°C (1800°F) o incluso superiores para exposiciones cortas.
- Idoneidad para protectores térmicos: IN625 es el material de referencia para las aplicaciones más exigentes aplicaciones de alta temperatura. Es ideal para protectores térmicos colocados muy cerca de colectores de escape, turbocompresores, componentes de turbinas de gas y otras fuentes de calor extremo. Su combinación de estabilidad térmica y resistencia a entornos de gases de escape agresivos lo hace excepcionalmente duradero.
- Consideraciones: El IN625 es más denso y significativamente más caro que las aleaciones de aluminio o titanio. También requiere una cuidadosa optimización de los parámetros de impresión y tratamientos térmicos específicos para lograr la microestructura y las propiedades deseadas. Su menor conductividad térmica en comparación con el aluminio es beneficiosa para los protectores térmicos de tipo barrera.
- Ventaja de Met3dp: La fabricación e impresión de superaleaciones de níquel como el IN625 exigen técnicas avanzadas de producción de polvo y equipos de impresión sofisticados. Las capacidades de Met3dp en la producción de polvos de superaleación de alta calidad y sus impresoras líderes en la industria garantizan la fabricación fiable de piezas de misión crítica a partir de materiales como el IN625.
Tabla resumen de selección de materiales:
Característica | AlSi10Mg | Ti-6Al-4V | IN625 (Inconel 625) |
---|---|---|---|
Beneficio principal | Ligero, rentable | Alta resistencia-peso, buena resistencia a la temperatura | Excelente resistencia a altas temperaturas y a la corrosión |
Densidad | Baja (~2,68 g/cm³) | Media (~4,43 g/cm³) | Alta (~8,44 g/cm³) |
Temperatura máx. de servicio | Moderada (~150-200°C) | Alta (~350-400°C) | Muy alta (~980°C+) |
Cond. térmica | Alta | Bajo | Bajo |
Corrosion Res. | Bien | Excelente | Excelente |
Coste relativo | Bajo | Medio-Alto | Alta |
Caso de uso típico | Automoción general, zonas de temperatura moderada | Aeroespacial, automoción de alto rendimiento, componentes de escape | Zonas de calor extremo (turbocompresores, colectores, turbinas) |
Exportar a hojas
La selección del material adecuado implica equilibrar los requisitos de rendimiento (temperatura, resistencia, corrosión), los objetivos de peso y las limitaciones presupuestarias. Consultar con expertos proveedores de servicios de metal AM como Met3dp puede proporcionar información valiosa sobre la idoneidad del material y la optimización del proceso para su aplicación específica de protector térmico.
Diseño para la fabricación aditiva (DfAM): Optimización de los protectores térmicos para la imprimibilidad y la función
La simple conversión de un protector térmico de diseño convencional a un formato imprimible en 3D rara vez desbloquea todo el potencial de la fabricación aditiva. El diseño para la para Fabricación aditiva (DfAM) implica aprovechar las capacidades únicas del proceso al tiempo que se mitigan sus limitaciones. La aplicación de Principios de DfAM es crucial para crear protectores térmicos de motor que no solo sean fabricables, sino también funcionalmente superiores y rentables.
Consideraciones clave de DfAM para protectores térmicos:
- Optimización de la topología: Utilice herramientas de software para eliminar algorítmicamente material de las áreas que experimentan baja tensión, lo que da como resultado estructuras orgánicas y ligeras que cumplen los requisitos de rendimiento con la mínima masa. Esto es ideal para crear protectores térmicos muy eficientes, rígidos y ligeros.
- Estructuras reticulares: Incorpore estructuras reticulares internas o externas para reducir significativamente el peso manteniendo la integridad estructural. Estos también se pueden diseñar para manipular el flujo de aire para mejorar la refrigeración o el aislamiento, agregando beneficios funcionales más allá de la simple reducción de masa.
- Consolidación de piezas: Rediseñe conjuntos que comprenden múltiples piezas de chapa y sujetadores en una sola pieza AM integrada. Esto reduce el tiempo de montaje, elimina posibles puntos de fallo en las uniones y, a menudo, da como resultado un componente más ligero y rígido.
- Diseño conforme: Aproveche la capacidad de AM para crear formas de forma libre. Diseñe protectores térmicos que se adapten perfectamente a geometrías complejas de motor o escape, maximizando la utilización del espacio y la eficacia del blindaje térmico.
- Espesor de pared: Mantenga el mínimo apropiado espesor de pared adecuado para el material elegido y el proceso de fabricación aditiva (por ejemplo, Fusión de lecho de polvo por láser - LPBF). Las paredes delgadas pueden ser difíciles de imprimir sin deformaciones o defectos, mientras que las secciones excesivamente gruesas aumentan el tiempo de impresión y el consumo de material. Los protectores térmicos a menudo se benefician de paredes delgadas para el peso, pero el diseño debe asegurar la imprimibilidad y la estabilidad estructural.
- Estructuras de apoyo: Los procesos de fabricación aditiva de metales típicamente requieren estructuras de soporte para anclar la pieza a la placa de construcción, gestionar las tensiones térmicas y soportar las características salientes (típicamente ángulos menores de 45 grados desde la horizontal).
- Minimice la necesidad de soportes orientando la pieza estratégicamente en la placa de construcción.
- Diseñe los soportes para una fácil extracción sin dañar las superficies críticas.
- Considere ángulos autosoportados (mayores de 45 grados) siempre que sea posible.
- Gestión térmica durante la impresión: Las secciones grandes y planas comunes en los protectores térmicos pueden ser propensas a deformarse debido a las tensiones térmicas durante el proceso de impresión. La incorporación de características de diseño como nervaduras de refuerzo u optimizar la orientación de impresión puede ayudar a mitigar esto.
- Orientación y tamaño de los agujeros: Los agujeros pequeños, especialmente los horizontales, pueden ser difíciles de imprimir con precisión sin soportes. Considere diseñar los agujeros verticalmente o usar formas de lágrima para agujeros horizontales autosoportados si las dimensiones precisas no son críticas.
- Características de la superficie: Integre montajes, pasadores de posicionamiento, nervaduras de refuerzo o incluso características de dirección del flujo de aire directamente en el diseño.
Se recomienda encarecidamente la participación de expertos en fabricación aditiva al principio de la fase de diseño. Met3dp ofrece servicios de desarrollo de aplicaciones, ayudando a los clientes a optimizar sus diseños de protectores térmicos para la fabricación aditiva, asegurando la imprimibilidad, el rendimiento y la rentabilidad mediante el aprovechamiento de técnicas avanzadas como la optimización topológica y la simulación.
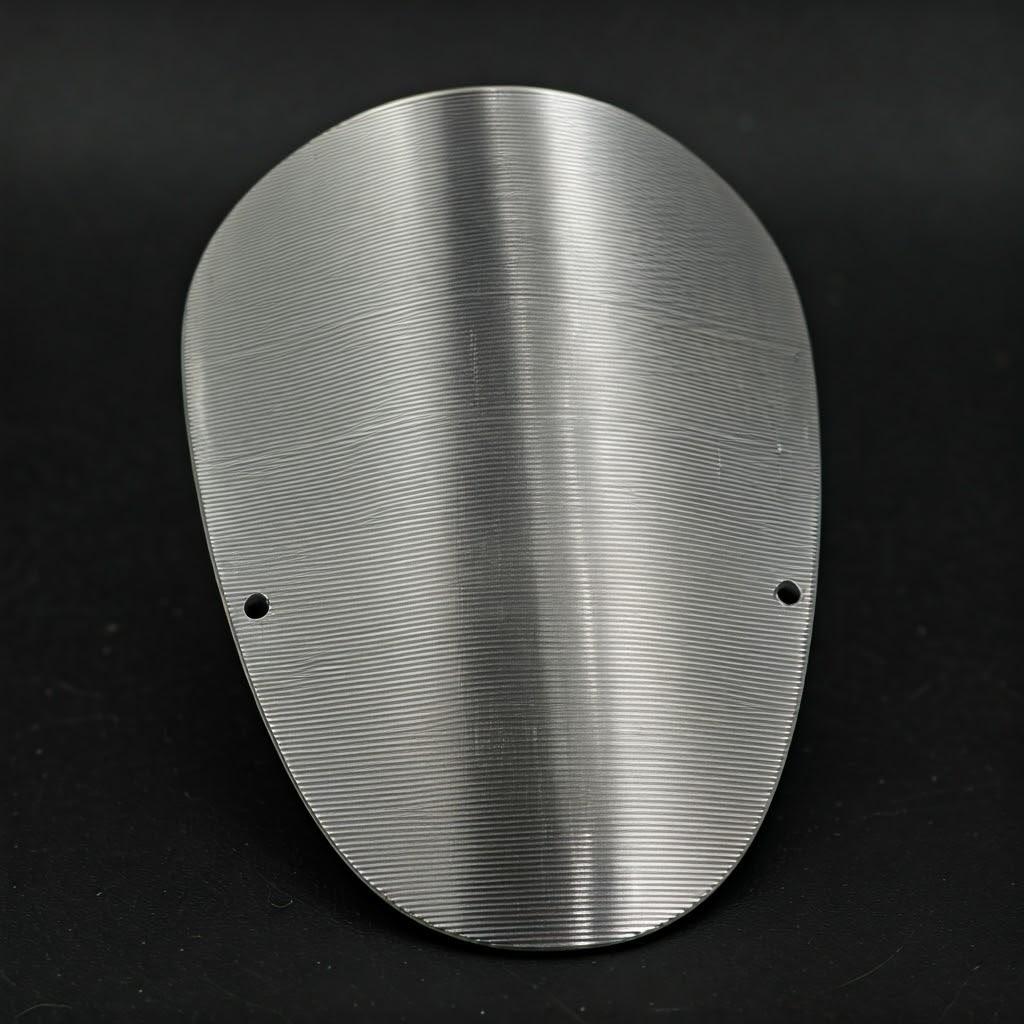
Tolerancias alcanzables, acabado superficial y precisión dimensional en protectores térmicos de fabricación aditiva de metales
Comprender la precisión alcanzable es crucial al especificar protectores térmicos impresos en 3D de metal. Si bien la fabricación aditiva de metales ofrece capacidades notables, es importante tener expectativas realistas con respecto a las tolerancias y el acabado superficial en comparación con el mecanizado CNC de alta precisión.
- Tolerancias: La precisión dimensional típica para los procesos de fabricación aditiva de metales como la Fusión de lecho de polvo por láser (LPBF) o la Fusión por haz de electrones (EBM) suele estar en el rango de ±0,1 mm a ±0,2 mm o ±0,1% a ±0,2% de la dimensión nominal, lo que sea mayor. Es posible obtener tolerancias más estrictas, pero pueden requerir controles de proceso específicos o mecanizado posterior. Los factores que influyen en la precisión final incluyen:
- Las propiedades del material (expansión térmica, contracción)
- Geometría y tamaño de la pieza
- Calibración y estado de la impresora (impresoras Met3dp, conocidas por su precisión y fiabilidad líderes en la industria, ayudan a garantizar resultados consistentes)
- Parámetros de impresión y estrategia de soporte
- Pasos de post-procesamiento (el tratamiento térmico puede causar una ligera distorsión)
- Acabado superficial (rugosidad): El acabado superficial tal como se construye de las piezas de fabricación aditiva de metales es inherentemente más rugoso que las superficies mecanizadas debido al proceso capa por capa y a las partículas de polvo parcialmente fundidas que se adhieren a la superficie.
- La rugosidad superficial típica tal como se construye (Ra) oscila entre 6 µm y 25 µm, dependiendo del material, el proceso, la orientación de la superficie en relación con la dirección de construcción (las superficies orientadas hacia arriba son generalmente más lisas que las orientadas hacia abajo) y los parámetros de impresión.
- Para muchas aplicaciones de protectores térmicos, el acabado tal como se construye puede ser perfectamente aceptable, especialmente en superficies no críticas.
- Si se requiere un acabado más suave por razones estéticas, una mayor vida útil a la fatiga o superficies de acoplamiento específicas, son necesarias técnicas de post-procesamiento como granallado, pulido, pulido o mecanizado CNC.
- Dimensionamiento y tolerancias geométricas (GD&T): Aplique GD&T especificaciones a los dibujos tal como lo haría para piezas fabricadas convencionalmente, indicando claramente las dimensiones críticas, los datos y las tolerancias requeridas. Esto asegura que el proveedor de fabricación aditiva comprenda las características críticas y pueda planificar el proceso de fabricación en consecuencia.
Es esencial discutir los requisitos específicos de tolerancia y acabado superficial con su proveedor de servicios de fabricación aditiva desde el principio. Pueden asesorar sobre la precisión alcanzable con su equipo y procesos y recomendar los pasos de post-procesamiento apropiados si se necesitan especificaciones más estrictas. El enfoque de Met3dp en fabricación de precisión garantiza que las piezas cumplan con los exigentes requisitos de la industria, aprovechando sus sistemas de impresión avanzados y el control del proceso.
Pasos esenciales de post-procesamiento para protectores térmicos de metal impresos en 3D
La mayoría de las piezas metálicas impresas en 3D, incluidos los protectores térmicos, requieren alguna forma de post-procesamiento después de la extracción de la placa de construcción para lograr las propiedades finales, tolerancias y acabado superficial deseados. Los pasos específicos dependen del material, la complejidad del diseño y los requisitos de la aplicación.
Operaciones comunes de post-procesamiento:
- Alivio del estrés / Tratamiento térmico: Este suele ser el primer y el paso más crucial. Los ciclos rápidos de calentamiento y enfriamiento durante la impresión inducen tensiones internas dentro de la pieza. Tratamiento térmico en un horno de atmósfera controlada (vacío o gas inerte para materiales reactivos como Ti-6Al-4V) alivia estas tensiones, evitando la distorsión o el agrietamiento durante la extracción del soporte o el mecanizado posterior, y estabilizando la microestructura del material. También pueden ser necesarios ciclos de tratamiento térmico específicos (por ejemplo, recocido, tratamiento de solución, envejecimiento) para lograr las propiedades mecánicas finales deseadas (resistencia, dureza, ductilidad) para la aleación elegida.
- Retirada del soporte: Las estructuras que soportan la pieza durante la impresión deben eliminarse cuidadosamente. Esto se puede hacer manualmente (usando alicates, cortadores) o mediante mecanizado (fresado, rectificado, electroerosión por hilo), dependiendo del diseño del soporte, la ubicación y la accesibilidad. Es necesaria una cuidadosa extracción para evitar dañar la superficie de la pieza.
- Extracción de la placa de construcción: La pieza debe separarse de la placa de construcción, normalmente mediante electroerosión por hilo o aserrado con cinta.
- Acabado superficial:
- Limpieza/Granallado: El granallado, el arenado o el granallado se utilizan comúnmente para eliminar el polvo suelto, alisar ligeramente las superficies y crear un acabado mate uniforme.
- Acabado por volteo/vibración: Útil para alisar superficies y desbarbar bordes en lotes de piezas más pequeñas.
- Pulido: El pulido manual o automatizado puede lograr superficies muy lisas y reflectantes si es necesario por razones estéticas o funcionales específicas (por ejemplo, reflejar el calor radiante).
- Mecanizado CNC: Si las dimensiones críticas requieren tolerancias más estrictas que las que se pueden lograr solo con la fabricación aditiva, o si se necesitan características específicas (por ejemplo, superficies de acoplamiento, diámetros de agujeros precisos), Mecanizado CNC se emplea. Esto elimina selectivamente material de la pieza de fabricación aditiva para lograr las especificaciones finales.
- Prensado isostático en caliente (HIP): Para aplicaciones críticas, especialmente en la industria aeroespacial, se puede utilizar HIP. Este proceso aplica alta temperatura y presión de gas isostática para eliminar cualquier microporosidad interna residual, mejorando la vida útil a la fatiga, la ductilidad y asegurando la máxima densidad.
- Revestimiento: Dependiendo de la aplicación, recubrimientos de protectores térmicos (por ejemplo, recubrimientos de barrera térmica cerámicos - TBC, recubrimientos de alta emisividad) pueden aplicarse para mejorar aún más el rendimiento térmico o proporcionar protección ambiental adicional.
- Inspección y control de calidad: Se pueden realizar comprobaciones dimensionales (utilizando CMM, escáneres), pruebas de materiales y pruebas no destructivas (END), como el escaneo CT, para garantizar que la pieza cumpla con todas las especificaciones.
Comprender estos servicios de posprocesamiento y su impacto en el costo y el plazo de entrega es esencial al planificar un proyecto. Colaborar con un proveedor de servicio completo como Met3dp, que posee experiencia en todo el flujo de trabajo de AM, desde el polvo hasta la pieza terminada, garantiza que todos los pasos necesarios se realicen correctamente para entregar un escudo térmico que cumpla con los estándares requeridos.
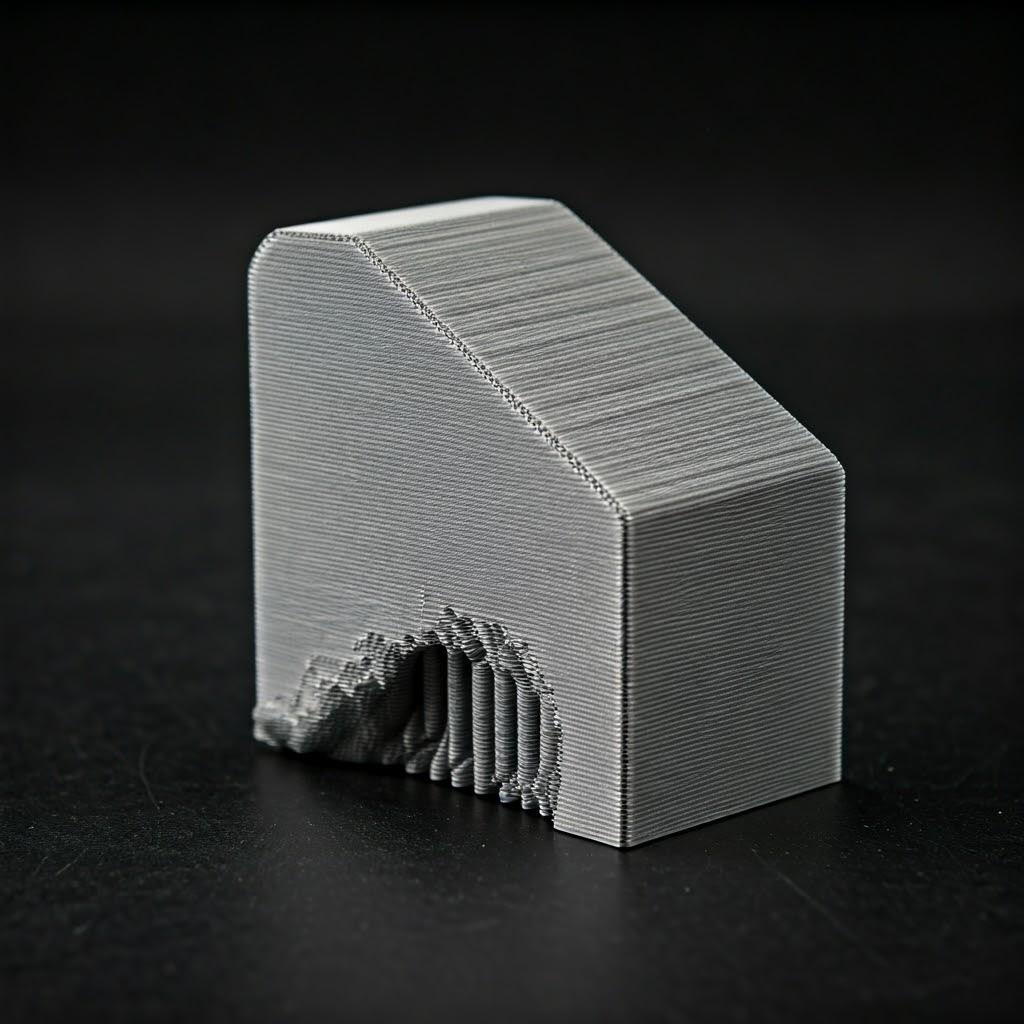
Navegando por los desafíos: Superar los obstáculos potenciales en la fabricación aditiva de metales para escudos térmicos
Si bien la fabricación aditiva de metales ofrece ventajas significativas para la producción de escudos térmicos de motores, no está exenta de desafíos. Comprender estos posibles obstáculos y colaborar con un socio de AM experimentado es clave para una implementación exitosa. Hombre prevenido vale por dos, y la planificación proactiva puede mitigar la mayoría de los problemas.
Desafíos comunes y estrategias de mitigación:
- Deformación y distorsión:
- Desafío: Los gradientes de temperatura significativos durante la impresión pueden causar tensiones internas, lo que hace que las secciones delgadas y planas características de muchos escudos térmicos se deformen o distorsionen, especialmente al retirarlos de la placa de construcción.
- Mitigación:
- Orientación optimizada: Seleccionar cuidadosamente la orientación de la pieza en la placa de construcción puede minimizar la acumulación de tensión en áreas críticas.
- Simulación térmica: Utilizar software de simulación para predecir la acumulación de tensión y optimizar la estrategia de impresión.
- Estrategia de apoyo: Emplear estructuras de soporte robustas pero estratégicamente ubicadas para anclar la pieza y disipar el calor de manera efectiva.
- Características de diseño: La incorporación de ligeras curvas, nervaduras de refuerzo o corrugaciones en el diseño puede aumentar la rigidez y resistir la deformación.
- Control de los parámetros del proceso: Utilizar parámetros de impresión optimizados desarrollados para el material y la geometría específicos, aprovechando el control de precisión que ofrecen sistemas como los de Met3dp.
- Alivio del estrés: Realización de un tratamiento térmico adecuado para aliviar el estrés antes de retirar la pieza de la placa de construcción es crucial.
- Retirada de la estructura de soporte:
- Desafío: Los soportes son necesarios, pero deben retirarse sin dañar la superficie de la pieza ni dejar marcas residuales, especialmente en áreas funcionales o visibles. Los soportes densos o mal diseñados pueden ser difíciles y llevar mucho tiempo retirarlos.
- Mitigación:
- DfAM para soportes: Diseñar piezas para minimizar la necesidad de soportes en áreas críticas (por ejemplo, utilizando ángulos autoportantes >45°).
- Diseño de soporte optimizado: Utilizar estructuras de soporte especializadas (por ejemplo, soportes de árbol, soportes de bloque con perforación) diseñadas para una extracción más fácil y puntos de contacto mínimos en la superficie de la pieza.
- Técnicas de eliminación adecuadas: Emplear una extracción manual cuidadosa o un mecanizado preciso (EDM, fresado) basado en el tipo y la ubicación del soporte.
- Acabado superficial: Planificar los pasos de acabado de la superficie posteriores (granallado, pulido) para abordar cualquier marca menor que quede después de la eliminación del soporte.
- Control de la porosidad:
- Desafío: A veces, se pueden formar vacíos o poros microscópicos dentro del material impreso si los parámetros de impresión no están totalmente optimizados, lo que puede afectar las propiedades mecánicas, particularmente la vida útil a la fatiga.
- Mitigación:
- Polvo de alta calidad: Es fundamental utilizar polvos metálicos esféricos de alta calidad con una distribución consistente del tamaño de las partículas y bajo contenido de gas, como los producidos a través de los procesos de atomización avanzados de Met3dp. Explore Met3dp’s Ofertas de productos para polvos adecuados.
- Parámetros de impresión optimizados: Controlar con precisión la potencia del láser/haz de electrones, la velocidad de escaneo, el grosor de la capa y las condiciones de la atmósfera para garantizar la fusión y consolidación completas.
- Prensado isostático en caliente (HIP): Para aplicaciones críticas que exigen la máxima densidad y rendimiento a la fatiga, el post-procesamiento HIP puede eliminar eficazmente la porosidad residual.
- Lograr el acabado superficial deseado:
- Desafío: La naturaleza inherente de capa por capa de la AM da como resultado un acabado superficial más rugoso en comparación con el mecanizado. Cumplir con los estrictos requisitos de rugosidad superficial a menudo requiere pasos adicionales.
- Mitigación:
- Orientación: Imprimir superficies críticas en ángulos óptimos en relación con la dirección de construcción puede mejorar su acabado tal como se construyen.
- Ajuste de parámetros: El ajuste fino de los parámetros de impresión puede influir en la rugosidad de la superficie resultante.
- Post-procesamiento: Implementar técnicas de acabado de superficie apropiadas (granallado, volteo, pulido, mecanizado) adaptadas a los requisitos específicos.
- Gestión de la tensión residual:
- Desafío: Más allá de la deformación, las tensiones residuales pueden afectar la estabilidad dimensional y el rendimiento mecánico de la pieza con el tiempo si no se gestionan correctamente.
- Mitigación:
- Estrategias de exploración optimizadas: Utilizar patrones de escaneo láser/haz específicos (por ejemplo, escaneo de islas) para distribuir el calor de manera más uniforme.
- Mayor dureza y resistencia: Algunos procesos (como EBM) utilizan precalentamiento de la cámara de construcción para reducir los gradientes térmicos.
- Alivio de tensión obligatorio: La implementación de un ciclo de tratamiento térmico de alivio de tensión validado apropiado para la aleación no es negociable para la mayoría de las piezas de AM de metal.
Superar con éxito estos desafíos requiere un profundo conocimiento del proceso, un sólido control de calidad y equipos avanzados. La asociación con un proveedor de servicios de FA de metales muy capaz con experiencia probada en los materiales específicos y los tipos de aplicaciones es la forma más eficaz de garantizar escudos térmicos fiables y de alta calidad.
Selección de su socio de AM de metales: Criterios para elegir un proveedor de escudos térmicos
Elegir el socio de fabricación aditiva adecuado es tan crítico como seleccionar el material adecuado u optimizar el diseño. La calidad de sus escudos térmicos impresos en 3D depende en gran medida de las capacidades, la experiencia y los sistemas de calidad de su proveedor de servicios de impresión 3D de metales. Al evaluar a los posibles proveedores, considere los siguientes criterios:
- Experiencia y conocimientos técnicos:
- ¿El proveedor tiene experiencia demostrada en la impresión de las aleaciones metálicas específicas requeridas (AlSi10Mg, Ti-6Al-4V, IN625)?
- ¿Tienen ingenieros de aplicaciones que comprendan los desafíos de la gestión térmica y puedan brindar soporte DfAM?
- ¿Han producido con éxito piezas para industrias exigentes similares (aeroespacial, automotriz)? Busque estudios de casos o referencias.
- Equipos y tecnología:
- ¿Qué tipo de tecnología AM de metales utilizan (por ejemplo, LPBF, EBM)? ¿Es adecuado para sus requisitos? Obtenga más información sobre los diferentes Métodos de impresión.
- ¿Operan impresoras industriales modernas y bien mantenidas conocidas por su precisión y fiabilidad?
- ¿Cuál es su capacidad de volumen de construcción? ¿Pueden adaptarse al tamaño de su escudo térmico?
- Capacidades y calidad de los materiales:
- ¿Ofrecen los polvos metálicos específicos y de alta calidad que necesita?
- ¿Pueden proporcionar certificaciones de materiales y trazabilidad para los polvos utilizados?
- ¿Tienen procesos sólidos para la manipulación y el reciclaje de polvos para garantizar la consistencia del material? El enfoque integrado de Met3dp, que fabrica tanto polvos como impresoras, ofrece ventajas significativas aquí.
- Capacidades de postprocesado:
- ¿Pueden proporcionar los pasos de post-procesamiento necesarios internamente o a través de socios calificados (tratamiento térmico, mecanizado, acabado de superficies, HIP)?
- ¿Tienen experiencia en los requisitos específicos para cada paso (por ejemplo, tratamiento térmico al vacío para titanio)?
- Sistemas de gestión de calidad:
- ¿Están certificados según las normas de calidad pertinentes (por ejemplo, ISO 9001, AS9100 para la industria aeroespacial)?
- ¿Qué procesos de control de calidad e inspección emplean (por ejemplo, CMM, NDT, pruebas de materiales)?
- Plazo de entrega y capacidad:
- ¿Cuáles son sus plazos de entrega ¿Para prototipos y tiradas de producción?
- ¿Tienen la capacidad suficiente para satisfacer sus requisitos de volumen y plazos?
- Servicio al cliente y comunicación:
- ¿Son receptivos, comunicativos y colaborativos?
- ¿Proporcionan presupuestos y actualizaciones de proyectos claros?
- Rentabilidad:
- Si bien el costo es importante, evalúelo en el contexto de la calidad, la fiabilidad y el valor general. La opción más barata puede no ser la mejor si compromete el rendimiento de las piezas o los plazos de entrega.
Met3dp destaca como un proveedor integral soluciones de AM de metal que ofrece no solo impresoras SEBM de última generación y una amplia gama de polvos metálicos de alto rendimiento producidos internamente, sino también una profunda experiencia en aplicaciones y servicios de desarrollo. Su compromiso con la calidad y la innovación los convierte en un socio sólido para aplicaciones exigentes de protección térmica en diversas industrias.
Comprensión de los factores de costo y los plazos de entrega para protectores térmicos impresos en 3D
Una pregunta común de ingenieros y gerentes de adquisiciones gira en torno al costo y el tiempo de respuesta de los componentes metálicos impresos en 3D. La comprensión de los factores clave que influyen en estimación de costes de impresión 3D de metales y el plazo de fabricación ayuda en la planificación y presupuestación de proyectos.
Principales factores de coste:
- Tipo de material y consumo:
- Elección de materiales: Las aleaciones de alto rendimiento como IN625 y Ti-6Al-4V son significativamente más caras por kilogramo que AlSi10Mg o los aceros.
- Volumen de la pieza: El volumen real de material utilizado en la pieza impacta directamente en el costo. La optimización del diseño (por ejemplo, optimización topológica, enrejados) puede reducir el volumen y, por lo tanto, el costo.
- Volumen de la estructura de soporte: El material utilizado para las estructuras de soporte también se suma al costo. Un diseño eficiente minimiza las necesidades de soporte.
- Tiempo de impresión:
- Tamaño de la pieza y complejidad: Las piezas más grandes y complejas tardan más en imprimirse, ocupando un tiempo de máquina costoso. La altura total (dimensión Z) en la cámara de construcción es a menudo un factor principal de la duración de la impresión.
- Densidad de construcción: Imprimir varias piezas simultáneamente en un solo trabajo de construcción puede reducir el costo del tiempo de máquina por pieza.
- Requisitos de postprocesamiento:
- Cada paso de post-procesamiento (alivio de tensión, eliminación de soporte, mecanizado, acabado, HIP, recubrimiento) agrega mano de obra, tiempo de máquina y, potencialmente, costos de proveedores especializados. Los acabados complejos o los requisitos de tolerancia ajustada aumentan significativamente los costos.
- Mano de obra e ingeniería:
- Incluye la preparación de archivos, la configuración de la construcción, la operación de la máquina, la extracción de piezas, la inspección de calidad y cualquier soporte de DfAM o ingeniería requerido.
- Garantía de calidad:
- Los costos asociados con los requisitos de inspección específicos (escaneo TC, informes CMM detallados, pruebas de materiales) se suman al precio total.
Factores que influyen en el plazo de entrega:
- Tiempo de impresión: Como se mencionó, este es a menudo el paso individual más largo del proceso.
- Disponibilidad de la máquina: Tiempos de espera para las impresoras disponibles en el proveedor de servicios.
- Duración del post-procesamiento: Los ciclos de tratamiento térmico, la configuración y el tiempo de ejecución del mecanizado, los procesos de acabado, todo se suma al tiempo total. HIP puede agregar varios días.
- Complejidad y cantidad de piezas: Las piezas más complejas pueden requerir un post-procesamiento más intrincado; las cantidades más grandes, naturalmente, tardan más en producirse.
- Envío: Tiempo requerido para el transporte del proveedor de AM a sus instalaciones.
Plazos de entrega típicos:
- Prototipos: A menudo se pueden producir en cuestión de días (por ejemplo, 3-10 días hábiles), según la complejidad, el material y el post-procesamiento requerido.
- Producción de bajo volumen: Puede oscilar entre 2 y 6 semanas, según la cantidad y los requisitos del proceso.
Es crucial obtener presupuestos detallados de los posibles proveedores como Met3dp que desglosen los costos y proporcionen estimaciones realistas de los plazos de entrega en función de sus archivos de diseño y requisitos específicos. Proporcionar información completa (archivos CAD, especificaciones de materiales, requisitos de tolerancia, cantidad) permitirá una cotización más rápida y precisa.
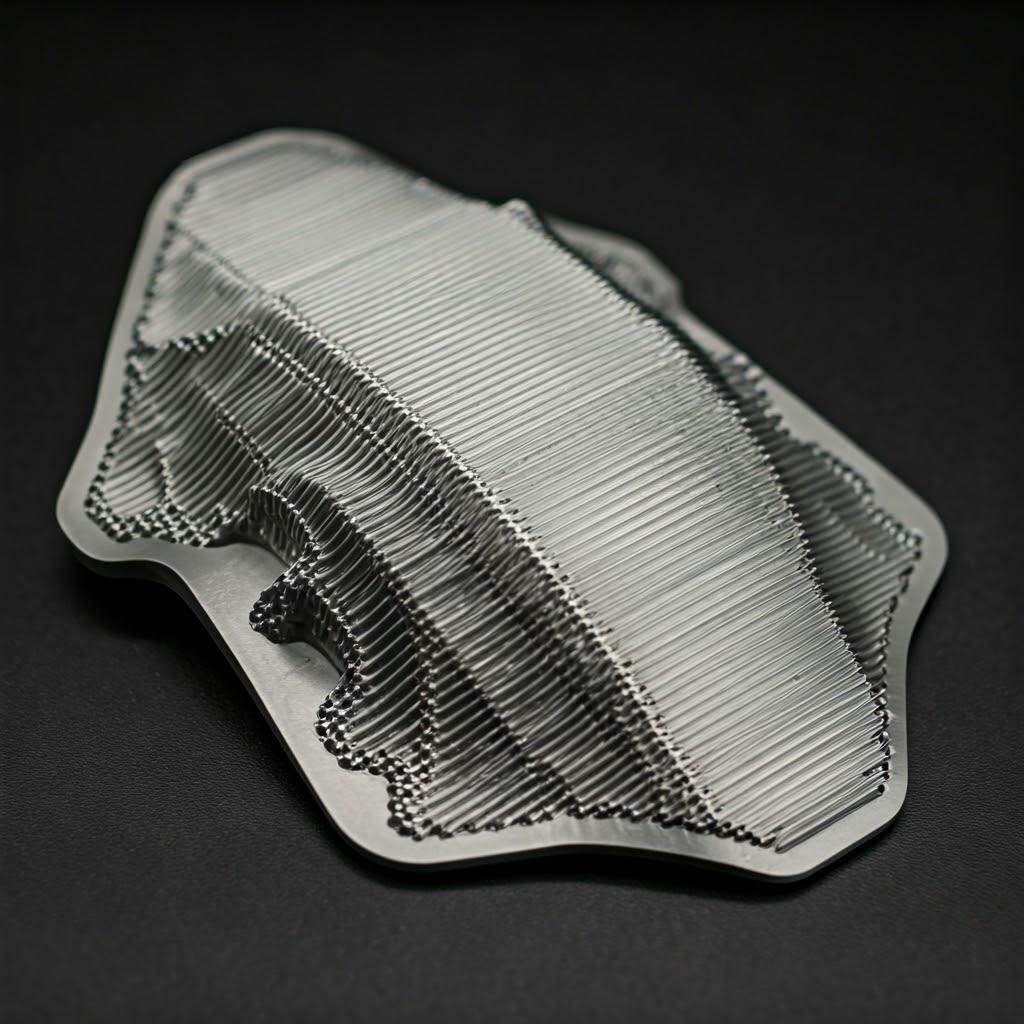
Preguntas frecuentes (FAQ) sobre protectores térmicos de motor impresos en metal en 3D
Aquí hay respuestas a algunas preguntas comunes con respecto al uso de la fabricación aditiva de metales para protectores térmicos de motores:
- P1: ¿Cuál es la temperatura máxima que puede soportar un protector térmico de metal impreso en 3D?
- A: Esto depende completamente del material elegido. AlSi10Mg es adecuado para temperaturas más bajas (hasta ~200 °C). Ti-6Al-4V funciona bien hasta ~400 °C. Para calor extremo cerca de los colectores de escape o turbocompresores, se requieren superaleaciones de níquel como IN625, capaces de soportar temperaturas superiores a 900 °C. El diseño (espacios de aire, recubrimientos) también juega un papel.
- P2: ¿Cuánto peso se puede ahorrar utilizando un protector térmico impreso en 3D en comparación con uno tradicional?
- A: Es posible un ahorro de peso significativo, especialmente cuando se utiliza la optimización topológica y materiales como AlSi10Mg o Ti-6Al-4V. Se pueden lograr ahorros del 30-60% o incluso más en comparación con los protectores de acero o incluso de aluminio diseñados y fabricados tradicionalmente, según el diseño original y el nivel de optimización. Esta es una gran ventaja en aplicaciones aeroespaciales y automotrices de alto rendimiento.
- P3: ¿Es la impresión 3D de metales adecuada tanto para prototipos como para la producción en serie de protectores térmicos?
- A: Absolutamente. La AM de metales es ideal para la creación rápida de prototipos debido a la eliminación de los costos de herramientas y la velocidad. También es cada vez más viable para la producción en serie de bajo a mediano volumen, particularmente para protectores térmicos complejos, de alto valor o personalizados donde los beneficios de la libertad de diseño, la reducción de peso y la optimización del rendimiento superan los costos potencialmente más altos por pieza en comparación con las piezas estampadas producidas en masa. Para volúmenes muy altos de diseños simples, los métodos tradicionales aún pueden ser más económicos.
Conclusión: Adopte el futuro de la gestión térmica con Met3dp
Los protectores térmicos de los motores son componentes indispensables, fundamentales para la seguridad, la fiabilidad y el rendimiento de los sistemas en los sectores automotriz, aeroespacial e industrial. Si bien los métodos de fabricación tradicionales han cumplido su propósito, a menudo no cumplen con las demandas de mayor complejidad, personalización, aligeramiento y ciclos de desarrollo rápidos característicos de la ingeniería moderna.
La fabricación aditiva de metales ha surgido como una tecnología transformadora, que ofrece una libertad de diseño sin precedentes para crear protectores térmicos altamente optimizados, complejos y ligeros, adaptados a desafíos térmicos específicos. Al aprovechar materiales como el versátil AlSi10Mg, el Ti-6Al-4V de alta resistencia y el IN625 resistente a temperaturas extremas, la AM de metales permite la producción de protectores térmicos con características de rendimiento superiores. La capacidad de crear prototipos rápidamente, eliminar los costos de herramientas y consolidar los ensamblajes mejora aún más su propuesta de valor.
La implementación exitosa de la AM de metales para protectores térmicos requiere una cuidadosa consideración de los principios de diseño (DfAM), las propiedades de los materiales, las tolerancias alcanzables, las necesidades de post-procesamiento y los posibles desafíos. La asociación con un proveedor capacitado y capaz es primordial. Met3dp, con sus capacidades integradas verticalmente que abarcan la producción avanzada de polvos metálicos utilizando tecnologías de atomización de gas y PREP, sistemas de impresión 3D líderes en la industria y soporte integral de aplicaciones, está listo para ayudar a ingenieros y gerentes de adquisiciones.
Al adoptar impresión 3D en metal, las empresas pueden revolucionar su enfoque de la gestión térmica del motor, logrando niveles de rendimiento, personalización y eficiencia previamente inalcanzables. Póngase en contacto con Met3dp hoy mismo para explorar cómo sus sistemas de vanguardia, materiales de alta calidad y profunda experiencia pueden impulsar sus soluciones de protectores térmicos de próxima generación y acelerar los objetivos de fabricación aditiva de su organización.
Compartir
MET3DP Technology Co., LTD es un proveedor líder de soluciones de fabricación aditiva con sede en Qingdao, China. Nuestra empresa está especializada en equipos de impresión 3D y polvos metálicos de alto rendimiento para aplicaciones industriales.
Solicite información para obtener el mejor precio y una solución personalizada para su empresa.
Artículos relacionados
Acerca de Met3DP
Actualización reciente
Nuestro producto
CONTACTO
¿Tiene alguna pregunta? ¡Envíenos un mensaje ahora! Atenderemos su solicitud con todo un equipo tras recibir su mensaje.
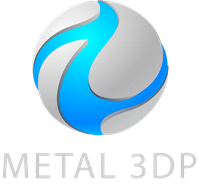
Polvos metálicos para impresión 3D y fabricación aditiva