Chaquetas de refrigeración fabricadas aditivamente para motores eléctricos
Índice
Introducción: El papel fundamental de la gestión térmica en los motores eléctricos de alto rendimiento
Los motores eléctricos son los caballos de batalla de la industria moderna, que alimentan todo, desde vehículos eléctricos (VE) y robots industriales hasta sistemas aeroespaciales críticos y dispositivos médicos de precisión. A medida que los ingenieros superan los límites de la densidad de potencia y el rendimiento, la gestión del calor generado durante el funcionamiento se vuelve primordial. La disipación ineficiente del calor conduce a una reducción de la eficiencia, la degradación de los componentes, una vida útil operativa más corta e incluso fallos catastróficos. Esto hace que la gestión térmica eficaz no sea solo una característica deseable, sino una necesidad absoluta para la fiabilidad y el rendimiento, especialmente en aplicaciones B2B exigentes donde el tiempo de inactividad se traduce directamente en pérdida de ingresos.
Entrar en el camisa de refrigeración del motor eléctrico. Este componente crítico actúa como un intercambiador de calor, que normalmente envuelve la carcasa del motor (estator) o se integra directamente en su estructura. Utiliza un refrigerante circulante (como mezclas de agua y glicol o fluidos dieléctricos especializados) para absorber el exceso de calor de los componentes principales del motor (bobinados, rotor, rodamientos) y transferirlo a un radiador u otro sistema de disipación de calor. Una camisa de refrigeración bien diseñada es esencial para:
- Mantener temperaturas de funcionamiento óptimas: Evitar que los motores superen sus límites de temperatura críticos.
- Mejorar la eficiencia: Los motores funcionan de manera más eficiente dentro de su rango de temperatura diseñado.
- Aumentar la densidad de potencia: Permitir que los motores más pequeños y ligeros ofrezcan mayores potencias sin sobrecalentamiento.
- Extender la vida útil del motor: Reducir el estrés térmico en el aislamiento, los rodamientos y otros componentes sensibles.
- Mejorar la fiabilidad: Minimizar el riesgo de fallos causados por la acumulación excesiva de calor en sistemas industriales y de misión crítica.
Tradicionalmente, las camisas de refrigeración se han fabricado utilizando métodos como el fundido, la extrusión, la fabricación (soldadura/soldadura fuerte de múltiples piezas) o el mecanizado sustractivo a partir de material de palanquilla. Si bien son efectivos hasta cierto punto, estos enfoques convencionales a menudo enfrentan limitaciones, particularmente cuando se trata de geometrías internas complejas necesarias para una transferencia de calor altamente eficiente o cuando se requiere personalización e iteración rápida. Las restricciones de diseño inherentes al fundido (espesor mínimo de pared, ángulos de desmoldeo) o al mecanizado (limitaciones de acceso a herramientas) pueden restringir la optimización de las trayectorias de flujo del refrigerante y el contacto con la superficie. Los conjuntos fabricados introducen posibles puntos de fuga y añaden complejidad a la fabricación.
Aquí es donde fabricación aditiva (AM) de metales, a menudo denominada metal Impresión 3D, emerge como una tecnología transformadora. Al construir piezas capa por capa directamente a partir de diseños digitales utilizando polvos metálicos de alto rendimiento, la FA desbloquea una libertad de diseño sin precedentes. Esto permite a los ingenieros crear camisas de refrigeración altamente complejas y optimizadas para la topología con intrincados canales internos que se adaptan con precisión a las fuentes de calor del motor. El resultado es una mejora significativa del rendimiento térmico, la reducción de peso, la consolidación de piezas y la capacidad de producir diseños personalizados rápidamente, ventajas muy buscadas por los gerentes de adquisiciones y los equipos de ingeniería en el fabricación de automóviles, ingeniería aeroespacialy sectores de automatización industrial.
Las empresas que buscan una ventaja competitiva recurren cada vez más a proveedores de servicios de fabricación aditiva y proveedores de polvo de metal para aprovechar esta tecnología. La capacidad de producir camisas de refrigeración personalizadas y de alto rendimiento a pedido se alinea perfectamente con las necesidades de la fabricación moderna, ofreciendo soluciones que antes eran imposibles o prohibitivamente caras. Esta publicación de blog profundizará en los detalles del uso de la FA metálica para camisas de refrigeración de motores eléctricos, explorando aplicaciones, beneficios, materiales recomendados como AlSi10Mg y CuCrZr, consideraciones de diseño y cómo asociarse con el proveedor B2B adecuado para sus necesidades de gestión térmica.
Aplicaciones e industrias: ¿Dónde se implementan las camisas de refrigeración de FA?
Las ventajas de la fabricación aditiva para los componentes de gestión térmica, particularmente las camisas de refrigeración, resuenan en una amplia gama de industrias donde el rendimiento y la fiabilidad de los motores eléctricos son críticos. Los profesionales de adquisiciones e ingenieros que buscan componentes para aplicaciones de alto riesgo especifican cada vez más soluciones de FA para satisfacer los exigentes desafíos térmicos. Los sectores clave incluyen:
- Automoción (especialmente vehículos eléctricos):
- Motores de tracción: Los vehículos eléctricos (VE) dependen de potentes motores eléctricos que operan bajo cargas muy variables. La refrigeración eficiente es vital para maximizar la autonomía, el rendimiento (aceleración, velocidad máxima) y la vida útil de la batería. La FA permite camisas de refrigeración compactas y ligeras con canales internos altamente optimizados que se adaptan a las formas del estator y el rotor, lo cual es crucial para las restricciones de embalaje en los vehículos.
- Refrigeración de la electrónica de potencia: Los inversores y convertidores también generan una cantidad significativa de calor. La FA puede crear soluciones de refrigeración integradas o placas frías dedicadas con geometrías complejas.
- Automovilismo: Las aplicaciones de competición exigen el máximo rendimiento y el mínimo peso. Las camisas de refrigeración de FA personalizadas proporcionan una ventaja competitiva a través de una disipación de calor superior en condiciones de funcionamiento extremas. Proveedores B2B centrados en soluciones de fabricación automotriz encuentran una demanda significativa aquí.
- Aeroespacial y defensa:
- Sistemas de accionamiento: Los motores eléctricos accionan las superficies de control de vuelo, el tren de aterrizaje y otros sistemas críticos. La fiabilidad y el ahorro de peso son primordiales. La FA permite camisas de refrigeración ligeras y optimizadas para la topología que cumplen con los estrictos requisitos aeroespaciales (por ejemplo, la certificación AS9100 a menudo requerida del proveedor de FA).
- Unidades de potencia auxiliar (APU) y generadores: Garantizar la estabilidad térmica para los sistemas de generación de energía en aeronaves.
- UAV/Drones: El peso es un factor crítico. Las soluciones de refrigeración de FA ligeras ayudan a prolongar los tiempos de vuelo y la capacidad de carga útil. Los especialistas en adquisiciones aeroespaciales buscan socios de FA con experiencia probada y trazabilidad de materiales.
- Automatización industrial y robótica:
- Servomotores de alta precisión: Los robots y las máquinas CNC utilizan motores que requieren un control preciso y ciclos de trabajo elevados. El rendimiento térmico constante garantiza la precisión y evita el sobrecalentamiento durante el funcionamiento continuo. La FA permite canales de refrigeración integrados directamente en las carcasas de los motores o camisas externas altamente eficientes.
- Motores industriales de servicio pesado: Las camisas de refrigeración para motores grandes utilizados en plantas de fabricación, instalaciones de procesamiento y extracción de recursos mejoran la fiabilidad y reducen el tiempo de inactividad por mantenimiento, una preocupación clave para los departamentos de adquisiciones industriales.
- Maquinaria personalizada: Los fabricantes de equipos originales (OEM) que construyen equipos industriales especializados pueden aprovechar la FA para obtener soluciones de refrigeración a medida, adaptadas a diseños de motores y entornos operativos únicos.
- Productos sanitarios:
- Robots y equipos quirúrgicos: Los motores de la robótica médica requieren alta precisión y fiabilidad. La gestión térmica eficaz evita la degradación del rendimiento durante los procedimientos.
- Sistemas de imagen (IRM/TC): Componentes de refrigeración para motores dentro de pórticos o sistemas de posicionamiento. La biocompatibilidad podría ser un factor, dependiendo de la aplicación específica, que influye en la elección del material y el post-procesamiento.
- Sector energético:
- Motores de perforación de fondo de pozo: El funcionamiento en entornos de alta temperatura y alta presión exige una gestión térmica robusta.
- Accionamientos de bombas y compresores: Garantizar la fiabilidad en aplicaciones de infraestructura crítica.
¿Por qué la demanda de los compradores B2B?
Los gerentes de adquisiciones e ingenieros de estos sectores se sienten atraídos por las camisas de refrigeración de FA por varias razones clave:
- Mejora del rendimiento: Ganancias demostrables en la disipación de calor en comparación con los diseños convencionales.
- Reducción de peso: Crítico para la industria aeroespacial, automotriz y robótica.
- Consolidación de piezas: Reducción de la complejidad del montaje, los posibles puntos de fuga y el recuento de piezas.
- Personalización y creación rápida de prototipos: Capacidad de iterar rápidamente los diseños y producir soluciones a medida para requisitos específicos del motor sin los altos costos de herramientas asociados con el fundido.
- Resiliencia de la cadena de suministro: Las capacidades de producción bajo demanda pueden acortar los plazos de entrega y reducir la dependencia de las complejas cadenas de suministro tradicionales, un factor cada vez más valorado por compradores mayoristas y distribuidores que buscan un suministro fiable de componentes.
La asociación con un experto impresión 3D en metal el proveedor de servicios es clave para obtener estos beneficios en diversas aplicaciones industriales.
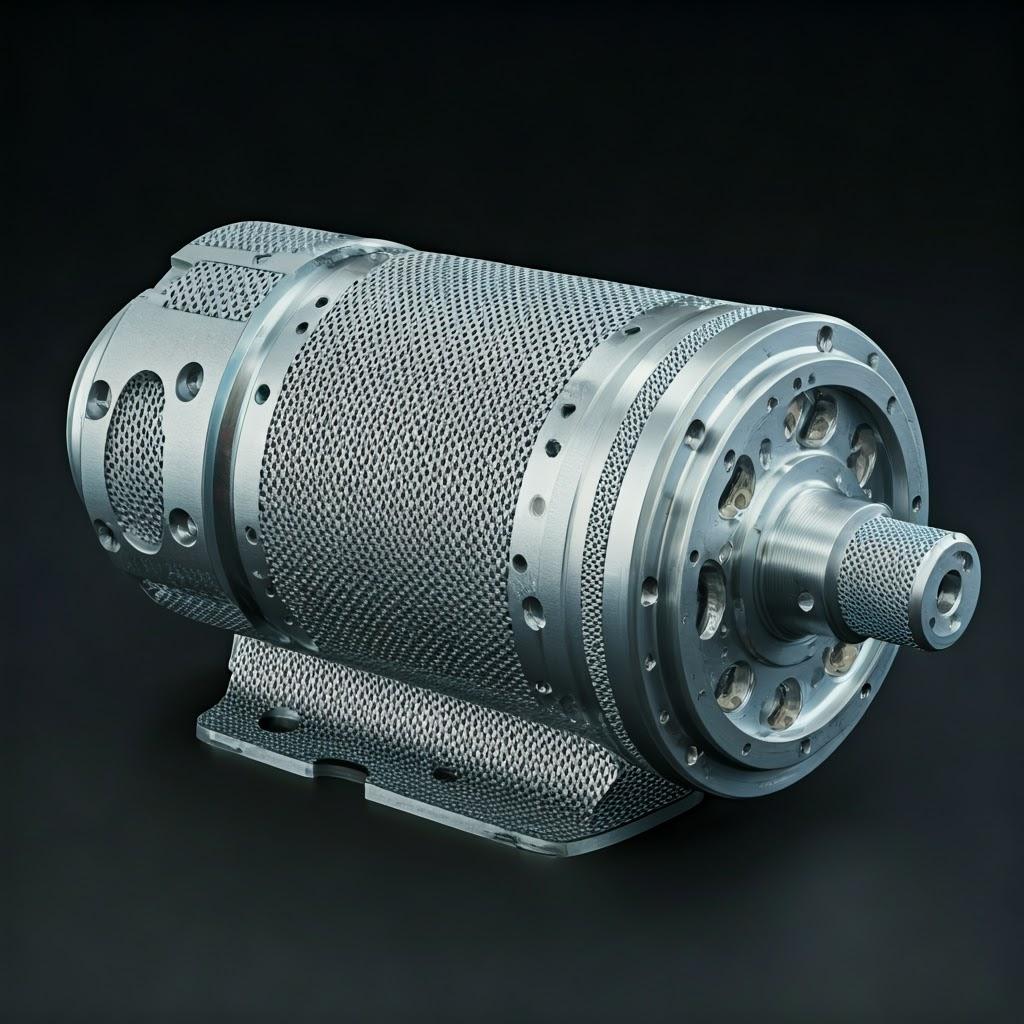
¿Por qué la fabricación aditiva de metales para camisas de refrigeración? Desbloqueo de las ganancias de rendimiento
Si bien los métodos de fabricación tradicionales han servido a la industria durante décadas, la fabricación aditiva de metales ofrece ventajas convincentes que abordan directamente las limitaciones del fundido, el mecanizado y la fabricación, particularmente para componentes complejos de gestión térmica como las camisas de refrigeración de motores eléctricos. Para los ingenieros que se esfuerzan por obtener un rendimiento óptimo y los gerentes de adquisiciones que buscan valor y fiabilidad, la FA presenta un cambio de paradigma.
Comparación: Fabricación aditiva de metal vs. métodos tradicionales para camisas de refrigeración
Característica | Fabricación aditiva de metal (LPBF/SLM) | Fundición tradicional | Mecanizado tradicional (sustractivo) | Fabricación tradicional (soldadura/soldadura fuerte) |
---|---|---|---|---|
Complejidad del diseño | Muy alto: Permite canales internos intrincados, paredes delgadas, formas orgánicas, estructuras reticulares, optimización topológica. | Moderado: Limitado por ángulos de desmoldeo, limitaciones de espesor de pared, complejidad de las herramientas. | Bajo a moderado: Limitado por el acceso a las herramientas, la complejidad de las características aumenta significativamente el costo. | Bajo: Típicamente geometrías más simples unidas. |
Canales internos | Altamente optimizado: Canales conformados que siguen las fuentes de calor, posibles trayectorias complejas no lineales. | Simple: Típicamente pasajes rectos o suavemente curvados, complejidad limitada. | Muy limitado: Principalmente canales rectos perforados/fresados. Canales profundos/complejos difíciles. | Simple: Tubos o placas soldados entre sí. |
Espesor de pared | Muy delgado: Puede lograr paredes submilimétricas (dependiendo del diseño). | Limitado: Espesor mínimo de pared requerido para el flujo de metal. | Flexible: Pero las características delgadas pueden ser propensas a la vibración/traqueteo. | Depende de la lámina/tubo: Puede ser delgado. |
Consolidación de piezas | Excelente: Múltiples componentes pueden integrarse en una sola pieza impresa. | Bueno: Puede producir piezas únicas complejas. | Pobre: Típicamente comienza con un solo bloque. | Pobre: Implica la unión de múltiples piezas. |
Reducción de peso | Excelente: La optimización topológica y las estructuras reticulares reducen significativamente el peso. | Regular: Puede ser pesado debido a las restricciones de espesor mínimo. | Regular: La eliminación de material es ineficiente para el aligeramiento complejo. | Regular: Depende del diseño y los materiales utilizados. |
Opciones de material | Rango creciente: Incluye aleaciones de aluminio (AlSi10Mg), aleaciones de cobre (CuCrZr), aceros inoxidables, aleaciones de níquel, titanio. | Amplio rango: Aleaciones de fundición establecidas. | Amplio rango: Cualquier material mecanizable. | Amplio rango: Aleaciones soldables/soldables. |
Coste de utillaje | Ninguna: Fabricación digital directa. | Alto: Se requieren moldes y patrones. | Bajo/Ninguno: Herramientas estándar, pero pueden ser necesarias fijaciones. | Bajo/Moderado: A menudo se requieren fijaciones. |
Plazo de entrega (prototipo) | Rápido: Días a semanas. | Lento: Semanas a meses (dependiendo de las herramientas). | Moderado: Días a semanas. | Moderado: Días a semanas. |
Plazo de entrega (producción) | Escalable: Puede ser competitivo dependiendo del volumen/complejidad. | Rápido (alto volumen): Una vez que existen las herramientas. | Lento (piezas complejas): Puede llevar mucho tiempo. | Moderado: Depende de la complejidad/automatización. |
Personalización | Excelente: Fácil de modificar diseños sin cambios de herramientas. | Pobre: Requiere modificación de herramientas costosas. | Bueno: Relativamente fácil de cambiar programas. | Regular: Las modificaciones pueden requerir cambios en los accesorios. |
Puntos de fuga potenciales | Minimizada: Posible construcción de una sola pieza. | Bajo: Generalmente monolítico. | N/A (Monolítico): Si se mecaniza a partir de un sólido. | Alto: Las soldaduras/soldaduras fuertes son posibles puntos de fallo. |
Exportar a hojas
Ventajas clave de la FA para las camisas de refrigeración:
- Libertad geométrica sin precedentes: El enfoque de la FA capa por capa libera a los diseñadores de las limitaciones de la fabricación tradicional. Esto permite:
- Canales de refrigeración conformados: Trayectorias que siguen con precisión los contornos de las zonas más calientes del motor (por ejemplo, los devanados del estator), maximizando la eficiencia de la transferencia de calor.
- Redes internas complejas: Diseñar enrejados intrincados, aletas o características que promuevan la turbulencia dentro de los canales para mejorar el intercambio de calor con el refrigerante, algo imposible con la perforación o el fundido.
- Optimización de la topología: Utilizar software para diseñar computacionalmente la estructura más eficiente en función de las trayectorias de carga y los requisitos térmicos, lo que a menudo da como resultado diseños de aspecto orgánico, ligeros y, sin embargo, resistentes.
- Rendimiento térmico mejorado: La capacidad de colocar los canales de refrigeración exactamente donde se necesitan y maximizar la superficie para el intercambio de calor conduce a un rendimiento térmico significativamente mejor en comparación con las camisas con trayectorias de refrigeración más simples y menos específicas. Esto se traduce directamente en menores temperaturas de funcionamiento del motor, mayor eficiencia y mayor densidad de potencia.
- Consolidación de piezas: Lo que tradicionalmente podría requerir múltiples componentes fundidos, mecanizados y soldados (por ejemplo, la carcasa de la camisa, los racores de entrada/salida, los deflectores internos) a menudo puede consolidarse en una sola pieza monolítica producida mediante FA. Esto reduce drásticamente el tiempo de montaje, elimina los posibles puntos de fuga en las juntas/soldaduras, simplifica la gestión del inventario para Compradores B2B, y mejora la fiabilidad general del sistema.
- Creación rápida de prototipos e iteración: La FA permite a los ingenieros pasar de un diseño digital a un prototipo físico de metal en cuestión de días. Esto acelera el ciclo de desarrollo, lo que permite realizar pruebas y validaciones rápidas de diferentes estrategias de refrigeración sin incurrir en los altos costes y los largos plazos de entrega asociados a las herramientas tradicionales. Se pueden probar simultáneamente múltiples variantes de diseño.
- La personalización en masa: La producción de diseños de camisas de refrigeración a medida para variantes o aplicaciones específicas de motores es económicamente viable con la FA, ya que no es necesario cambiar las herramientas físicas. Esto es ideal para los fabricantes de equipos originales que producen equipos especializados o para el sector de piezas de repuesto y posventa.
- Reducción de peso: Mediante la optimización topológica y el uso de estructuras de enrejado internas cuando procede, la FA puede crear camisas de refrigeración que son significativamente más ligeras que sus homólogas fabricadas tradicionalmente, manteniendo al mismo tiempo la integridad estructural y el rendimiento térmico. Esta es una ventaja fundamental en aplicaciones sensibles al peso como la aeroespacial y los vehículos eléctricos de automoción.
Aunque la FA ofrece estas importantes ventajas, es importante asociarse con un proveedor de servicios con conocimientos que comprenda los matices del proceso, la ciencia de los materiales y el post-procesamiento necesarios para ofrecer camisas de refrigeración fiables y de alta calidad, listas para un uso industrial exigente.
Enfoque en los materiales: AlSi10Mg y CuCrZr para un rendimiento térmico óptimo
La selección del material adecuado es fundamental para el rendimiento de una camisa de refrigeración de motor eléctrico fabricada de forma aditiva. La función principal es la transferencia de calor, lo que convierte a la conductividad térmica en una propiedad clave. Sin embargo, la resistencia mecánica, el peso, la resistencia a la corrosión, la imprimibilidad y el coste también son consideraciones cruciales para los ingenieros y especialistas en adquisiciones. Dos materiales destacan para esta aplicación en la FA de metales: AlSi10Mg (una aleación de aluminio-silicio-magnesio) y CuCrZr (una aleación de cobre-cromo-circonio).
Met3dp, aprovechando su experiencia en sistemas avanzados de fabricación de polvos, incluyendo tecnologías líderes en la industria de atomización por gas y Proceso de Electrodo Rotatorio de Plasma (PREP), produce polvos metálicos esféricos de alta calidad, ideales para procesos de FA como la Fusión Selectiva por Láser (SLM) / Fusión por Lecho de Polvo con Láser (LPBF). Nuestra atención a las características del polvo, como la alta esfericidad y la buena fluidez, garantiza un procesamiento óptimo y da como resultado piezas impresas densas y de alto rendimiento. Ofrecemos polvos de AlSi10Mg y CuCrZr optimizados para la fabricación aditiva.
AlSi10Mg (Aleación de aluminio): El todoterreno ligero
AlSi10Mg es una de las aleaciones de aluminio más comunes y conocidas utilizadas en la fabricación aditiva de metales. Esencialmente, es una aleación de fundición adaptada a los procesos de fusión en lecho de polvo.
- Propiedades y ventajas clave:
- Buena conductividad térmica: Aunque no es tan alta como las aleaciones de aluminio o cobre puro, su conductividad térmica (normalmente 120-150 W/m·K después del tratamiento térmico adecuado) es suficiente para muchas aplicaciones de refrigeración de motores.
- Excelente relación resistencia-peso: Las aleaciones de aluminio son significativamente más ligeras que el cobre o el acero, lo que hace que el AlSi10Mg sea ideal para aplicaciones sensibles al peso (automoción, aeroespacial).
- Buena imprimibilidad: Se procesa relativamente fácil en los sistemas LPBF, lo que permite obtener características finas y geometrías complejas.
- Buena resistencia a la corrosión: Presenta buena resistencia a la corrosión en entornos de refrigerante típicos (por ejemplo, mezclas de agua y glicol).
- Rentabilidad: Generalmente más asequible que las aleaciones de cobre.
- Post-procesamiento: Puede mecanizarse, pulirse y tratarse térmicamente fácilmente (por ejemplo, tratamiento térmico T6 para mejorar la resistencia y la ductilidad).
- Consideraciones:
- Menor conductividad térmica absoluta en comparación con las aleaciones de cobre.
- Requiere un tratamiento térmico adecuado después de la impresión para lograr propiedades mecánicas y conductividad térmica óptimas.
- Aplicaciones típicas: Camisas de refrigeración de motores de vehículos eléctricos, componentes aeroespaciales, motores industriales donde el peso es un factor importante, intercambiadores de calor que requieren formas complejas.
CuCrZr (Aleación de cobre): El campeón de la alta conductividad
El CuCrZr es una aleación de cobre de alto rendimiento diseñada específicamente para aplicaciones que requieren una excelente conductividad térmica y eléctrica combinada con una buena resistencia mecánica, especialmente a temperaturas elevadas.
- Propiedades y ventajas clave:
- Excelente conductividad térmica: Significativamente mayor que las aleaciones de aluminio (normalmente >300 W/m·K), lo que la hace extremadamente eficiente en la transferencia de calor. Ideal para motores de muy alta densidad de potencia o aplicaciones con cargas térmicas extremas.
- Buena resistencia a altas temperaturas: Mantiene mejor las propiedades mecánicas que el cobre puro a temperaturas elevadas.
- Buena resistencia al desgaste: Ofrece mejores características de desgaste que el cobre puro.
- Imprimibilidad: Aunque es más difícil de imprimir que el AlSi10Mg debido a la alta reflectividad y conductividad térmica del cobre (que requiere una mayor potencia del láser y parámetros de proceso específicos), los sistemas de FA especializados y los polvos optimizados, como los de Met3dp, permiten una impresión exitosa.
- Consideraciones:
- Mayor densidad: Significativamente más pesadas que las aleaciones de aluminio (aprox. 8,9 g/cm³ frente a 2,67 g/cm³).
- Mayor coste de los materiales: Las aleaciones de cobre son generalmente más caras que las aleaciones de aluminio.
- Impresión más desafiante: Requiere parámetros de proceso optimizados y potencialmente configuraciones específicas de la máquina (por ejemplo, los láseres verdes o azules pueden ser ventajosos). El acabado de la superficie podría ser más rugoso en el estado de construcción en comparación con el AlSi10Mg.
- Aplicaciones típicas: Refrigeración de motores de alto rendimiento para deportes de motor, componentes de refrigeración para electrónica de potencia, disipadores de calor que requieren la máxima disipación de calor, bobinas de inducción, electrodos de soldadura por resistencia (aunque las camisas de refrigeración son el foco aquí).
Guía de selección de materiales:
Propiedad | AlSi10Mg | CuCrZr | Consideración clave para las camisas de refrigeración |
---|---|---|---|
Conductividad térmica | Buena (120-150 W/m·K post-HT) | Excelente (>300 W/m·K) | Función principal; CuCrZr ofrece ~2x rendimiento pero puede ser excesivo. |
Densidad | Bajo (~2,67 g/cm³) | Alta (~8,9 g/cm³) | El ahorro de peso es fundamental en la automoción/aeroespacial; favorecer AlSi10Mg. |
Resistencia mecánica | Buena (especialmente post-HT) | Buena (mantiene la resistencia a la temperatura) | Debe soportar las presiones y vibraciones de funcionamiento. |
Imprimibilidad | Excelente | Moderada (requiere optimización) | Afecta a la resolución de las características alcanzables, al acabado de la superficie y al coste. |
Resistencia a la corrosión | Bien | Bien | Importante para la longevidad con refrigerantes específicos. |
Coste | Baja | Más alto | Factor importante para la adquisición B2B y la producción en volumen. |
El más adecuado para | Rendimiento equilibrado, aplicaciones sensibles al peso, proyectos conscientes de los costes. | Máximo rendimiento térmico, aplicaciones de alta densidad de potencia donde el peso es secundario. | Adapte el material a los requisitos de rendimiento y al presupuesto específicos. |
Exportar a hojas
El papel de Met3dp: Como proveedor de ambos productos avanzados polvos metálicos y soluciones de fabricación aditiva, Met3dp puede ayudar a los clientes a seleccionar el material óptimo para su aplicación de camisa de refrigeración. Nuestros polvos de alta calidad AlSi10Mg y CuCrZr, producidos utilizando técnicas de atomización de última generación, garantizan el mejor punto de partida posible para lograr componentes de fabricación aditiva de alto rendimiento y fiabilidad. Entendemos los requisitos de procesamiento específicos de cada material, lo que garantiza impresiones exitosas y propiedades optimizadas de las piezas finales.
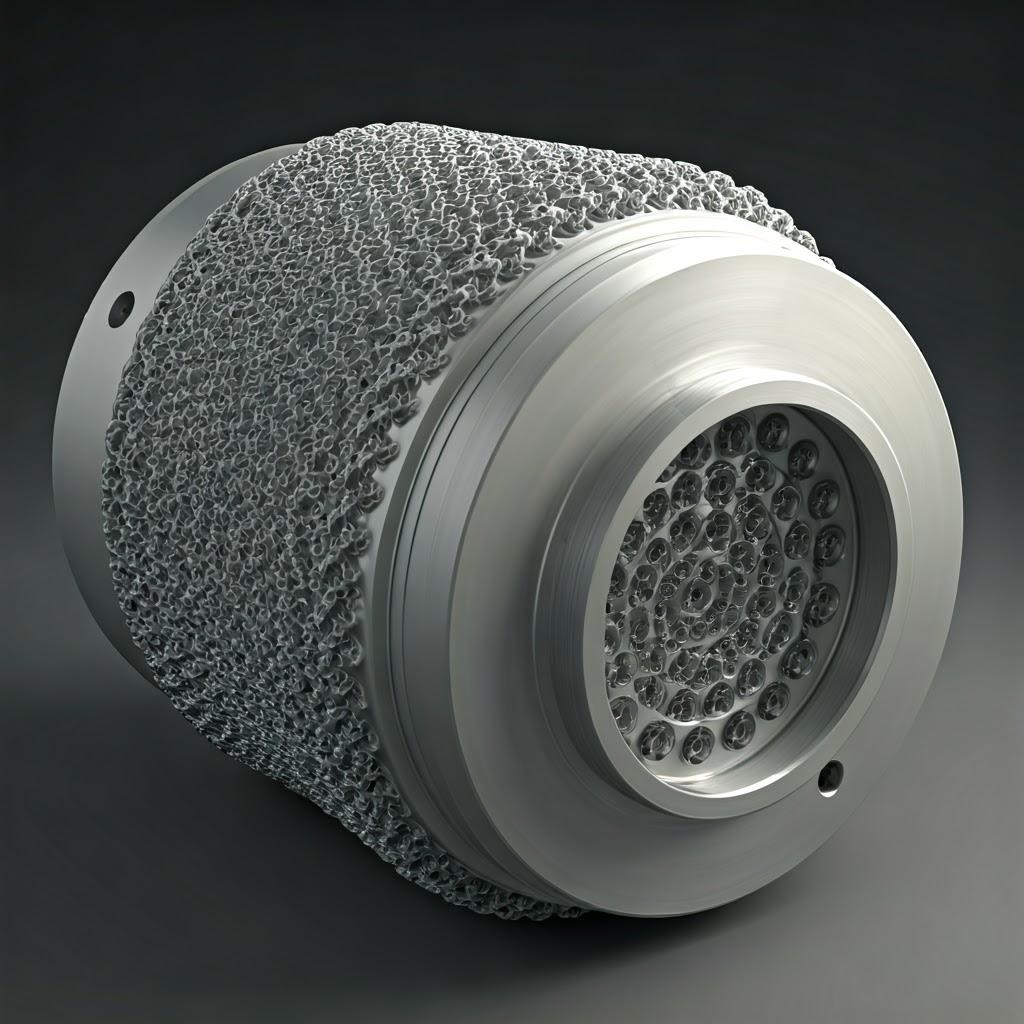
Diseño para la fabricación aditiva (DfAM): Optimización de la geometría de la camisa de refrigeración
La simple replicación de una camisa de refrigeración diseñada tradicionalmente utilizando la fabricación aditiva a menudo no aprovecha el verdadero potencial de la tecnología. Para desbloquear los importantes beneficios de rendimiento, peso y consolidación discutidos anteriormente, los ingenieros deben adoptar Diseño para fabricación aditiva (DfAM) principios. DfAM no se trata sólo de hacer que una pieza sea imprimible; se trata de replantear fundamentalmente el diseño para aprovechar las capacidades únicas de la fabricación aditiva, en particular la libertad de crear geometrías internas y externas complejas. Para componentes como las camisas de refrigeración de los motores eléctricos, donde el flujo de fluidos y la transferencia de calor son primordiales, DfAM es fundamental.
Principios clave de DfAM para camisas de refrigeración de fabricación aditiva:
- Adoptar la complejidad geométrica para la función:
- Canales conformados: Diseñar canales de refrigerante que sigan con precisión la forma de la fuente de calor (por ejemplo, laminaciones del estator o curvas de la carcasa). Esto minimiza la trayectoria térmica y maximiza el área de contacto, mejorando drásticamente la eficiencia de la transferencia de calor en comparación con los canales rectos y perforados comunes en los diseños tradicionales.
- Optimizadores de flujo interno: Integrar características dentro de los canales para mejorar el rendimiento térmico. Esto puede incluir:
- Turbuladores: Pequeñas nervaduras o protuberancias que interrumpen intencionadamente el flujo laminar, promoviendo la turbulencia, lo que aumenta el coeficiente de transferencia de calor entre el refrigerante y la pared del canal.
- Aletas internas/matrices de pasadores: Estructuras que aumentan la superficie interna disponible para el intercambio de calor dentro del conducto del refrigerante.
- Secciones transversales de canales variables: Optimización de la velocidad del flujo y la caída de presión en todo el circuito de refrigeración.
- Entradas/salidas optimizadas: Diseñar transiciones suaves y eficientes hacia y desde la camisa de refrigeración para minimizar las pérdidas de presión y garantizar una distribución uniforme del flujo. Considere la posibilidad de integrar interfaces de ajuste estándar directamente en el diseño de la fabricación aditiva.
- Aprovechar la optimización de la topología y el diseño generativo:
- Utilizar herramientas de software especializadas para determinar computacionalmente la distribución de material más eficiente para la camisa de refrigeración en función de los casos de carga definidos (estructurales y térmicos), las condiciones de contorno (puntos de montaje, conexiones de fluidos) y los objetivos de rendimiento (temperatura máxima, peso mínimo).
- Esto a menudo da como resultado estructuras orgánicas, "biónicas" que eliminan material de las zonas de baja tensión, al tiempo que refuerzan las trayectorias de carga críticas, lo que conduce a importantes ahorros de peso sin comprometer la resistencia o la función térmica. Esto es inestimable para la adquisición de la automoción y la aeroespacial donde la reducción de peso es un factor principal.
- Diseño para el autosoporte y la minimización de las estructuras de soporte:
- Voladizos y ángulos: Comprender las limitaciones del ángulo de autosoporte del material elegido (AlSi10Mg, CuCrZr) y el proceso de fabricación aditiva (LPBF). Normalmente, los ángulos superiores a 45 grados desde la horizontal pueden construirse sin estructuras de soporte. Diseñar características como canales internos con secciones transversales en forma de lágrima o diamante en lugar de secciones puramente circulares o rectangulares horizontales para minimizar la necesidad de soportes internos, que pueden ser muy difíciles o imposibles de eliminar.
- Orientación de construcción: Considerar la orientación de construcción óptima al principio de la fase de diseño. Esto afecta al acabado de la superficie en diferentes caras, a la ubicación y cantidad de estructuras de soporte necesarias, a la acumulación de tensiones residuales y, potencialmente, al tiempo y al coste de impresión. La orientación estratégica de las superficies críticas o de las complejas redes de canales puede simplificar la impresión y el post-procesamiento.
- Características de sacrificio: A veces, se pueden añadir pequeñas características específicamente para soportar una sección más crítica durante la construcción, diseñadas para ser fácilmente mecanizadas posteriormente.
- Consolidar piezas:
- Buscar activamente oportunidades para combinar múltiples componentes (por ejemplo, carcasa, accesorios, soportes, deflectores internos) en una única pieza impresa monolítica. Esto reduce la mano de obra de montaje, el recuento de piezas, la complejidad del inventario para proveedores y distribuidores B2B, y elimina posibles vías de fuga asociadas a juntas, soldaduras o sellos.
- Optimización del espesor de pared y la resolución de las características:
- La FA permite paredes muy finas (hasta ~0,4-0,5 mm, dependiendo de la geometría y el proceso), lo que permite diseños ligeros. Sin embargo, asegúrese de que las paredes sean lo suficientemente gruesas para soportar las presiones de funcionamiento, manejar las posibles vibraciones y permitir una transferencia de calor eficaz sin una resistencia térmica excesiva.
- Tenga en cuenta el tamaño mínimo de la característica imprimible por el sistema LPBF específico (~0,2-0,4 mm). Evite las características más pequeñas que este límite de resolución.
- Diseño para el posprocesamiento:
- Tolerancias de mecanizado: Si ciertas superficies requieren alta precisión o acabados específicos (por ejemplo, caras de sellado, interfaces de montaje, orificios roscados), agregue material adicional (tolerancia de mecanizado) en el diseño de FA para el mecanizado CNC posterior.
- Eliminación del polvo: Diseñe canales internos con curvas suaves y evite las esquinas afiladas o los callejones sin salida donde el polvo pueda quedar atrapado y ser difícil de eliminar después de la impresión. Considere la posibilidad de agregar puertos de acceso para la limpieza si es necesario, que se pueden taponar más tarde.
- Acceso al soporte: Asegúrese de que las estructuras de soporte sean accesibles para su eliminación, especialmente crucial para geometrías internas complejas.
Colaboración con expertos en FA:
La aplicación exitosa de los principios de DfAM a menudo requiere la colaboración con proveedores de servicios de FA con experiencia como Met3dp. Nuestros ingenieros comprenden los matices de varios métodos de impresión 3D de metales y materiales (AlSi10Mg, CuCrZr) y pueden proporcionar información valiosa durante la fase de diseño para garantizar la fabricabilidad, optimizar el rendimiento y minimizar los costos. Aprovechar esta experiencia desde el principio puede evitar costosos rediseños y acelerar el tiempo de comercialización de las soluciones de refrigeración de alto rendimiento.
Precisión alcanzable: Tolerancia, acabado superficial y precisión dimensional en las camisas de refrigeración de FA
Si bien la FA ofrece una increíble libertad geométrica, comprender los niveles de precisión alcanzables es crucial para los ingenieros que diseñan componentes funcionales como las camisas de refrigeración, especialmente para la integración en conjuntos más grandes. Los responsables de compras también necesitan garantías con respecto a la consistencia y la calidad de las piezas entregadas por proveedores industriales de FA. Los aspectos clave incluyen las tolerancias dimensionales, el acabado superficial (rugosidad) y la precisión general.
Tolerancias dimensionales:
- Tolerancias típicas de LPBF: Para los procesos de fusión por lecho de polvo láser (LPBF) bien controlados que utilizan materiales como AlSi10Mg o CuCrZr, las tolerancias dimensionales típicas alcanzables para piezas más pequeñas (por ejemplo, < 100 mm) suelen estar en el rango de ±0,1 mm a ±0,2 mm (±0,004″ a ±0,008″). Para dimensiones mayores, una tolerancia de ±0,1% a ±0,2% de la dimensión nominal es una guía común.
- Factores que influyen en la tolerancia:
- Tamaño y geometría de la pieza: Las piezas más grandes o aquellas con características complejas pueden mostrar una mayor desviación debido al estrés térmico y la contracción acumulados.
- Material: Los diferentes materiales se contraen y se deforman de manera diferente durante la impresión y el enfriamiento.
- Orientación de construcción: La orientación en la placa de construcción afecta a la precisión, particularmente en la dirección Z (altura de construcción).
- Gestión térmica: La estabilidad de la máquina y el control del proceso (parámetros del láser, flujo de gas) son críticos.
- Estrategia de apoyo: La forma en que se apoya la pieza influye en la estabilidad durante la construcción.
- Post-procesamiento: Los tratamientos térmicos de alivio de tensión pueden causar cambios dimensionales menores. Las operaciones de mecanizado logran tolerancias mucho más estrictas en características específicas.
- Lograr tolerancias más ajustadas: Cuando se requieren tolerancias más estrictas (por ejemplo, superficies de acoplamiento, interfaces de cojinetes, ranuras de sellado), es práctica estándar diseñar la pieza de FA con material adicional (material de mecanizado) y utilizar mecanizado CNC posterior al proceso para lograr tolerancias de hasta ±0,01 mm a ±0,05 mm (±0,0004″ a ±0,002″) o incluso mejores, comparables al mecanizado convencional.
Acabado superficial (rugosidad):
- Rugosidad superficial tal como se construyó: El acabado superficial de las piezas directamente de la máquina de FA es inherentemente más rugoso que las superficies mecanizadas. Esto se debe al proceso capa por capa y a las partículas de polvo parcialmente fundidas que se adhieren a la superficie.
- Valores Ra típicos: La rugosidad de la superficie tal como se construye (Ra - rugosidad media aritmética) para LPBF suele oscilar entre 8 µm a 20 µm (315 µin a 787 µin), dependiendo en gran medida de:
- Orientación: Las superficies orientadas hacia arriba y las paredes verticales tienden a ser más lisas que las superficies orientadas hacia abajo (que muestran escalonamiento de capas) y las superficies que dependen de soportes (que dejan marcas de testigo al retirarlos).
- Material: Los polvos más finos y los parámetros optimizados pueden conducir a acabados más suaves.
- Parámetros del proceso: La potencia del láser, la velocidad y el grosor de la capa juegan un papel importante.
- Valores Ra típicos: La rugosidad de la superficie tal como se construye (Ra - rugosidad media aritmética) para LPBF suele oscilar entre 8 µm a 20 µm (315 µin a 787 µin), dependiendo en gran medida de:
- Canales internos: La rugosidad de los canales internos es fundamental para la dinámica de fluidos (caída de presión) y la transferencia de calor. Las superficies internas construidas tendrán valores de rugosidad similares. Esta rugosidad inherente a veces puede ser beneficiosa, ya que promueve la turbulencia y mejora la transferencia de calor, pero una rugosidad excesiva aumenta la caída de presión.
- Mejora del acabado superficial: Para aplicaciones que requieren superficies más lisas (por ejemplo, caras de sellado, reducción de la fricción, estética), se emplean diversas técnicas de posprocesamiento:
- Mecanizado CNC: Proporciona el acabado más suave y controlado en las superficies accesibles.
- Mecanizado por flujo abrasivo (AFM) o Extrude Hone: Empujar una masilla abrasiva a través de los canales internos para alisarlos.
- Pulido químico: Uso de grabadores químicos para alisar las superficies (dependiendo del material).
- Acabado por volteo/vibración: Uso de medios para alisar las superficies externas de lotes de piezas.
- Micro-mecanizado/Pulido: Pulido manual o automatizado para áreas específicas.
Precisión dimensional y control de calidad:
- Es fundamental garantizar que la camisa de refrigeración final cumpla con todas las especificaciones dimensionales y de superficie. Los proveedores de fabricación aditiva B2B emplean rigurosas medidas de control de calidad:
- Supervisión de procesos: La supervisión in situ durante la construcción (por ejemplo, la supervisión de la piscina de fusión) puede ayudar a detectar anomalías.
- Máquinas de medición por coordenadas (MMC): Se utiliza para la inspección dimensional precisa de características críticas después de la impresión o el mecanizado.
- Escaneado 3D: Comparar la geometría final de la pieza con el modelo CAD original para verificar la precisión general e identificar las desviaciones.
- Medición de la rugosidad superficial: Uso de perfilómetros para cuantificar el acabado de la superficie.
- Tomografía computarizada: Se puede utilizar para la inspección no destructiva de canales internos y la detección de defectos internos como la porosidad.
La comprensión de estos aspectos de precisión permite a los ingenieros diseñar eficazmente, especificando tolerancias más estrictas solo cuando es funcionalmente necesario (a menudo confiando en el posmecanizado) y aceptando los acabados tal como se construyen cuando es apropiado, optimizando así los costos y los plazos de entrega.
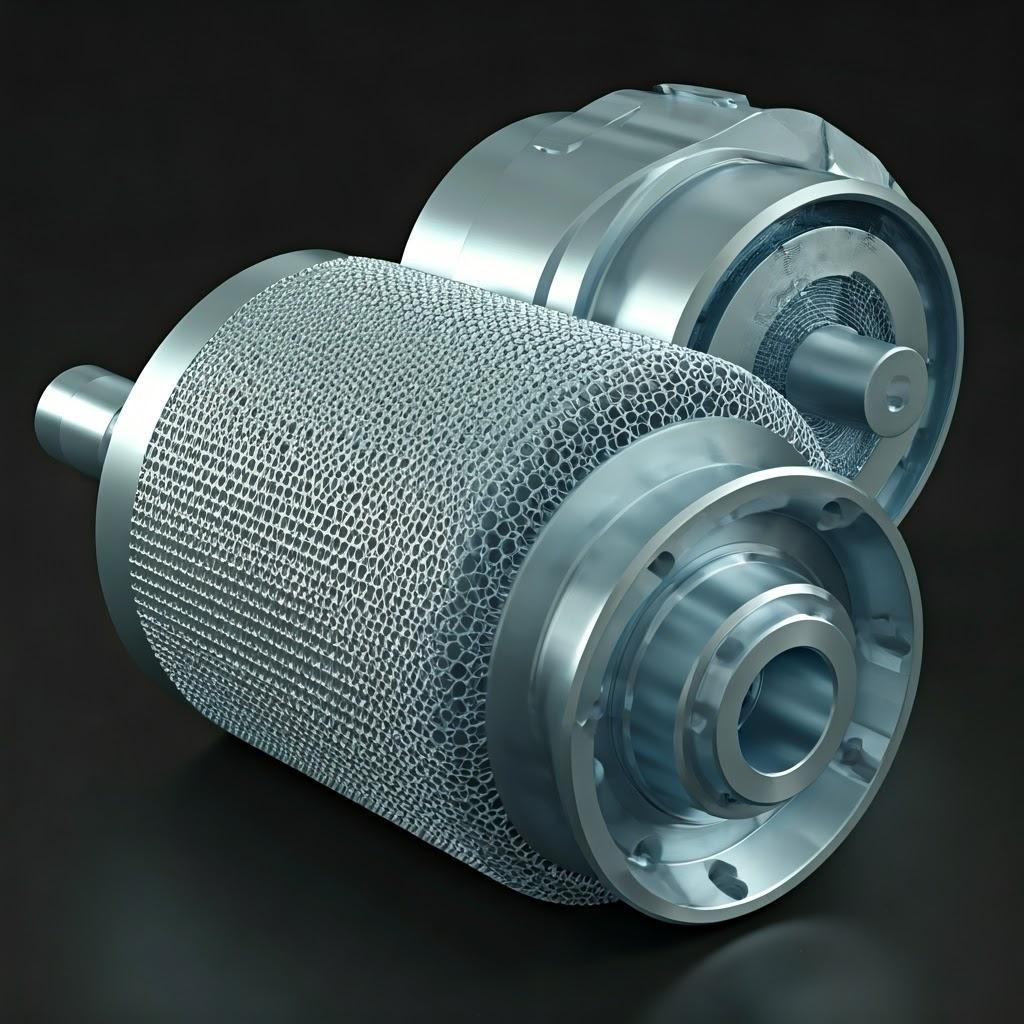
Vías de posprocesamiento: De la pieza impresa al componente terminado
Una pieza metálica fabricada aditivamente, tal como sale de la impresora, rara vez está lista para su uso final, especialmente para aplicaciones exigentes como las camisas de refrigeración de motores eléctricos. Por lo general, se requiere una serie de pasos de posprocesamiento para lograr las propiedades del material, la precisión dimensional, el acabado superficial y la funcionalidad general deseadas. La vía específica depende del material (AlSi10Mg o CuCrZr), la complejidad del diseño y los requisitos de la aplicación.
Pasos comunes de post-procesamiento para camisas de enfriamiento de AM:
- Alivio del estrés / Tratamiento térmico:
- Propósito: Los ciclos rápidos de calentamiento y enfriamiento inherentes a LPBF crean tensiones internas significativas dentro de la pieza impresa. Un tratamiento térmico de alivio de tensiones (típicamente realizado mientras la pieza aún está adherida a la placa de construcción) es crucial para reducir estas tensiones, evitando la distorsión o el agrietamiento durante los pasos posteriores (como la extracción de la placa) y mejorando la estabilidad dimensional.
- Proceso: Implica calentar la pieza en un horno de atmósfera controlada a una temperatura específica (por debajo de la temperatura de envejecimiento o de solución), mantenerla durante un tiempo determinado y luego enfriarla lentamente.
- Tratamientos térmicos adicionales (por ejemplo, T6 para AlSi10Mg): Se pueden requerir tratamientos térmicos adicionales para lograr las propiedades mecánicas finales deseadas (resistencia, ductilidad, dureza) y optimizar la conductividad térmica. Para AlSi10Mg, es común un ciclo T6 (tratamiento de solución seguido de envejecimiento artificial). CuCrZr también puede someterse a tratamientos de envejecimiento específicos para optimizar su resistencia y conductividad. Los parámetros deben controlarse cuidadosamente en función de la especificación de la aleación.
- Extracción de la placa de construcción:
- Métodos: Las piezas se separan típicamente de la placa de construcción mediante electroerosión por hilo (EDM) o aserrado con cinta. Se debe tener cuidado para evitar dañar la pieza.
- Retirada de la estructura de soporte:
- Propósito: Las estructuras de soporte son necesarias durante la construcción para anclar la pieza y soportar los voladizos. Estos deben eliminarse con cuidado.
- Métodos: Los soportes a menudo se eliminan manualmente con herramientas manuales (alicates, cortadores) o se mecanizan (fresado, rectificado). El acceso puede ser difícil, especialmente para los soportes internos dentro de las complejas redes de canales (lo que destaca la importancia de DfAM para minimizar los soportes internos). Las marcas residuales de testigo donde se adjuntaron los soportes son comunes y pueden requerir un acabado adicional.
- Eliminación de polvo/limpieza:
- Propósito: Asegurarse de que todo el polvo suelto o parcialmente sinterizado se elimine de la pieza, especialmente dentro de los intrincados canales de enfriamiento internos, es fundamental para evitar la contaminación del sistema de enfriamiento y garantizar un flujo sin obstrucciones.
- Métodos: Se utilizan chorreado con aire comprimido, chorreado con perlas, baños de limpieza por ultrasonidos y sistemas de enjuague especializados. Es fundamental diseñar para la eliminación del polvo (evitando callejones sin salida, esquinas internas afiladas).
- Mecanizado CNC:
- Propósito: Para lograr tolerancias ajustadas, acabados superficiales específicos y características que no se pueden producir con precisión solo mediante AM.
- Aplicaciones: Mecanizado de superficies de acoplamiento para sellos herméticos, creación de ranuras precisas para juntas tóricas, perforación y roscado de orificios roscados para accesorios, aplanamiento de bridas, logro de diámetros de alta precisión para ajustes de rodamientos. Requiere un diseño cuidadoso de la fijación para sujetar de forma segura la pieza AM, a menudo compleja.
- Acabado/suavizado de la superficie:
- Propósito: Para mejorar la rugosidad de la superficie más allá del estado de construcción para razones funcionales (sellado, dinámica de fluidos) o estéticas.
- Métodos: Como se discutió anteriormente: volteo, chorreado con perlas (puede proporcionar un acabado mate uniforme), mecanizado por flujo abrasivo (para canales internos), pulido químico, electropulido, pulido manual. La elección depende del nivel de acabado deseado, la accesibilidad de la geometría y el material.
- Prueba de fugas:
- Propósito: Absolutamente crítico para una camisa de enfriamiento. Verifica la integridad de la estructura impresa y asegura que no pueda escapar refrigerante.
- Métodos: Típicamente implica presurizar los canales de enfriamiento con aire o helio mientras la pieza está sumergida en agua (prueba de burbujas) o usar un detector de fugas de espectrómetro de masas de helio para una mayor sensibilidad. Los protocolos de prueba de presión deben reflejar las condiciones de funcionamiento previstas.
- Inspección y control de calidad:
- Propósito: Verificación final de que la pieza cumple con todos los requisitos dimensionales, de material y funcionales antes del envío.
- Métodos: CMM, escaneo 3D, perfilometría de superficie, inspección visual, revisión de la certificación de materiales, escaneo TC (para comprobaciones de integridad interna si es necesario).
Ejemplo de flujo de trabajo (simplificado):
Fragmento de código
graph TD
Comprender este flujo de trabajo ayuda a los ingenieros a diseñar piezas compatibles con el post-procesamiento necesario y permite a los gerentes de adquisiciones tener en cuenta estos pasos en las estimaciones de costos y plazos de entrega al contratar a un fabricante por contrato de AM.
Navegando por los desafíos en la producción de camisas de enfriamiento de AM y soluciones
Si bien la fabricación aditiva de metales ofrece enormes ventajas para la producción de camisas de enfriamiento de alto rendimiento, el proceso no está exento de desafíos. La conciencia de los posibles problemas y la asociación con un proveedor experimentado como Met3dp, que emplea procesos y controles de calidad sólidos, es clave para obtener resultados exitosos.
Desafíos comunes y estrategias de mitigación:
- Tensión residual, deformación y distorsión:
- Desafío: El calentamiento y enfriamiento rápidos y localizados inherentes a las construcciones LPBF acumulan tensiones internas. Si no se gestionan, estas tensiones pueden hacer que las piezas se deformen durante la impresión, se distorsionen después de retirarlas de la placa de construcción o incluso se agrieten. Esto es particularmente relevante para las secciones planas grandes o los diseños asimétricos comunes en algunos estilos de camisa.
- Soluciones:
- Simulación del proceso: El uso de software para predecir las tensiones térmicas y la distorsión antes de la impresión permite la optimización de la orientación de la construcción y las estructuras de soporte.
- Estrategia de soporte optimizada: Los soportes bien diseñados anclan la pieza firmemente y ayudan a disipar el calor.
- Construir calefacción de placas: Las temperaturas elevadas de la placa de construcción reducen los gradientes térmicos.
- Estrategias de exploración optimizadas: El uso de patrones de escaneo láser específicos (por ejemplo, escaneo de islas) puede ayudar a distribuir el calor de manera más uniforme.
- Alivio de tensión eficaz: Realizar un ciclo de alivio de tensión adecuado inmediatamente después de la impresión es crucial.
- Eliminación de la estructura de soporte (especialmente interna):
- Desafío: Los soportes dentro de canales de enfriamiento complejos y estrechos pueden ser extremadamente difíciles o imposibles de eliminar por completo, lo que podría obstruir el flujo o desprenderse más tarde.
- Soluciones:
- Enfoque DfAM: Priorice los diseños de canales autosoportados (por ejemplo, formas de lágrima, diamante) durante la fase de diseño. Minimice los voladizos que requieran soporte interno.
- Soportes solubles/desmontables (menos comunes en metal): La investigación continúa, pero típicamente los soportes son de metal denso.
- Diseño para el acceso: Asegúrese de que los canales sean lo suficientemente grandes y que las vías sean lo suficientemente suaves para el acceso de herramientas manuales o métodos efectivos de flujo a través de abrasivos/químicos si los soportes son inevitables.
- Planificación cuidadosa: Requiere una planificación meticulosa y, a menudo, mano de obra manual calificada o post-procesamiento especializado como AFM.
- Lograr una integridad a prueba de fugas:
- Desafío: Asegurar que las paredes delgadas y las geometrías complejas de la camisa de enfriamiento sean completamente densas y estén libres de microporosidad o grietas que podrían provocar fugas de refrigerante bajo presión.
- Soluciones:
- Parámetros de proceso optimizados: El uso de parámetros validados (potencia del láser, velocidad, espaciado de trama, espesor de capa) específicos del material (AlSi10Mg, CuCrZr) y la máquina es fundamental para lograr una densidad >99,5%.
- Polvo de alta calidad: El uso de polvos metálicos de alta esfericidad, bajo contenido de oxígeno y libres de contaminación, como los producidos por Met3dp utilizando atomización avanzada, es fundamental. Un polvo inconsistente conduce a un comportamiento de fusión inconsistente y posibles defectos. (Enlace a la página de inicio de Met3dp)
- Control de calidad robusto: La implementación de pruebas de fugas rigurosas (pruebas de presión, detección de fugas de helio) en el 100% de las piezas es esencial.
- Posible HIP (Prensado isostático en caliente): Para aplicaciones críticas, se puede utilizar HIP después de la impresión para cerrar la porosidad interna, aunque agrega costos y plazos de entrega.
- Eliminación completa del polvo:
- Desafío: Asegurarse de que todo el polvo no fusionado se elimine de los intrincados canales internos después de la impresión. El polvo atrapado puede impedir el flujo o contaminar el sistema de enfriamiento.
- Soluciones:
- DfAM para el drenaje: Diseñe canales con curvas suaves, diámetro suficiente y potencialmente orificios de drenaje/acceso (que se pueden tapar más tarde). Evite las trampas de polvo.
- Procedimientos de limpieza a fondo: Utilización de aire comprimido, vibración, limpieza por ultrasonidos y, posiblemente, lavado con disolvente.
- Inspección: Uso de boroscopios o escaneo TC (para piezas críticas) para verificar la limpieza de los canales.
- Acabado superficial y marcas de soporte:
- Desafío: La rugosidad superficial tal como se construye, especialmente en los canales internos, puede afectar a la caída de presión y a los coeficientes de transferencia de calor. Las marcas dejadas después de la eliminación del soporte pueden afectar al sellado o a la estética.
- Soluciones:
- Orientación optimizada: Posicionar las superficies críticas de forma óptima durante la configuración de la construcción.
- Postprocesamiento selectivo: Utilizar métodos apropiados (mecanizado, AFM, pulido) específicamente en superficies donde el acabado es crítico. Aceptar el acabado tal como se construye cuando no afecte a la función para controlar los costes.
- Eliminación experta de soportes: La eliminación cuidadosa minimiza las cicatrices en la superficie.
- Coste y plazo de entrega:
- Desafío: La fabricación aditiva de metales a veces puede percibirse como más cara o lenta que los métodos tradicionales, especialmente para volúmenes muy altos de piezas sencillas.
- Soluciones:
- Centrarse en el valor, no solo en el costo: Destacar las mejoras de rendimiento, el ahorro de peso y los beneficios de consolidación que justifican la inversión.
- Optimizar el diseño para AM: Los diseños eficientes minimizan el uso de material y el tiempo de impresión.
- Asóciese con proveedores experimentados: Un flujo de trabajo eficiente, la utilización de la máquina y las cadenas de post-procesamiento establecidas en proveedores experimentados como Met3dp ayudan a gestionar los costes y los plazos de entrega de forma eficaz para Pedidos de producción B2B.
- Consideraciones sobre el volumen: Discutir las posibles reducciones de costes para tamaños de lote más grandes o pedidos recurrentes.
Al comprender estos posibles retos y trabajar con un socio de fabricación aditiva capacitado y con conocimientos, equipado con materiales de alta calidad y procesos robustos, los ingenieros y los responsables de compras pueden aprovechar con confianza la fabricación aditiva para producir chaquetas de refrigeración de motores eléctricos superiores.
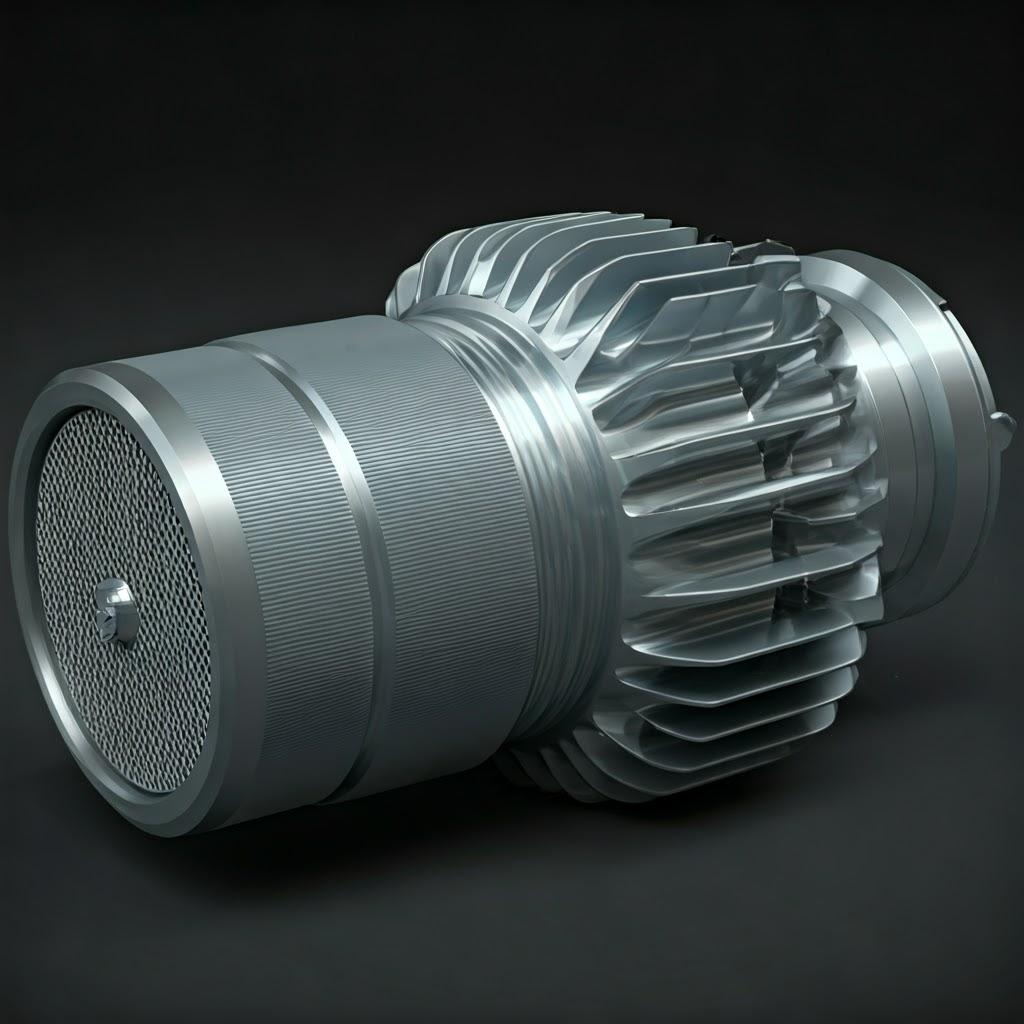
Selección de su socio B2B: Elección del proveedor de servicios de fabricación aditiva de metales adecuado
El éxito de su proyecto de chaqueta de refrigeración fabricada de forma aditiva depende no solo de un diseño bien optimizado y de la correcta selección de materiales, sino también significativamente de las capacidades y la experiencia de su proveedor de servicios de FA de metales muy capaz. La selección del socio B2B adecuado es una decisión crítica para los responsables de compras y los equipos de ingeniería que buscan componentes fiables y de alta calidad que se entreguen a tiempo y dentro del presupuesto. Más allá del precio, una evaluación exhaustiva debe abarcar la experiencia técnica, los sistemas de calidad, la capacidad y el potencial general de asociación.
Criterios clave para evaluar a los proveedores de fabricación aditiva de metales:
- Experiencia demostrada:
- Especificidad de la aplicación: ¿Tiene el proveedor experiencia demostrada con componentes de gestión térmica como intercambiadores de calor o chaquetas de refrigeración? ¿Puede mostrar estudios de casos o ejemplos relevantes?
- Experiencia en materiales: ¿Tienen un profundo conocimiento y procesos validados para los materiales específicos requeridos (AlSi10Mg, CuCrZr)? Esto incluye la comprensión de los parámetros de impresión óptimos, los tratamientos térmicos y las propiedades alcanzables. Pregunte sobre su experiencia en el manejo de los matices de la impresión de aleaciones de cobre si CuCrZr es su elección.
- Experiencia en el sector: ¿Han trabajado con clientes de su sector (automoción, aeroespacial, industrial)? Es crucial comprender los requisitos y las normas específicas del sector.
- Tecnología y parque de máquinas:
- Tecnología adecuada: Asegúrese de que utilizan la tecnología de fabricación aditiva adecuada, principalmente la fusión en lecho de polvo láser (LPBF/SLM) para estos materiales y aplicaciones.
- Calidad y capacidad de la máquina: ¿Cuál es la marca, el modelo y la antigüedad de sus impresoras? Un parque de máquinas moderno y bien mantenido (como los sistemas utilizados por Met3dp) a menudo se traduce en una mayor consistencia y fiabilidad. ¿Tienen suficiente capacidad para gestionar sus volúmenes de prototipado y producción potenciales? Evalúe la redundancia en caso de inactividad de la máquina.
- Control de procesos: ¿Qué medidas se aplican para el control y la supervisión del proceso durante la construcción?
- Calidad y manipulación de materiales:
- Abastecimiento de polvo: ¿De dónde obtienen sus polvos metálicos? ¿Tienen un estricto control de calidad de los materiales entrantes? Met3dp, por ejemplo, fabrica sus propios polvos metálicos esféricos de alta calidad utilizando tecnologías avanzadas de atomización con gas y PREP, lo que garantiza la consistencia desde la fuente. Obtenga más información sobre el compromiso de Met3dp con la calidad aquí.
- Manipulación y reciclaje de polvos: ¿Cuáles son sus procedimientos de almacenamiento, manipulación, tamizado y reciclaje de polvos para evitar la contaminación y garantizar la trazabilidad?
- Capacidades internas de posprocesamiento:
- Servicios integrales: ¿El proveedor ofrece los pasos de post-procesamiento necesarios internamente (alivio de tensiones, tratamiento térmico, eliminación de soportes, acabado básico)? Aunque la externalización de algunos pasos como el mecanizado CNC complejo o las pruebas especializadas es común, tener las capacidades básicas internamente a menudo agiliza el flujo de trabajo, mejora el control de calidad y reduce los plazos de entrega.
- Red de socios: Si subcontratan ciertos pasos, ¿tienen una red de socios cualificados y de confianza?
- Sistema de gestión de la calidad (SGC) & Certificaciones:
- SGC robusto: Un sólido sistema de gestión de la calidad es esencial para garantizar la consistencia y la repetibilidad. Pregunte sobre sus procedimientos de calidad, procesos de inspección y prácticas de documentación.
- Certificaciones relevantes: Busque certificaciones como ISO 9001 (gestión general de la calidad). Para aplicaciones aeroespaciales, AS9100 suele ser necesario. Las certificaciones indican un compromiso con los procesos de calidad estandarizados, un factor clave para las compras industriales.
- Soporte de diseño y experiencia en DfAM:
- Enfoque Colaborativo: ¿Están sus ingenieros disponibles para colaborar en el diseño para la fabricación aditiva (DfAM)? ¿Pueden proporcionar comentarios sobre la imprimibilidad de su diseño, sugerir optimizaciones para el rendimiento o la reducción de costes y ayudar a afrontar los retos específicos de la fabricación aditiva? Esta asociación puede ser inestimable, especialmente si su equipo es nuevo en la fabricación aditiva de metales.
- Gestión de proyectos y comunicación:
- Comunicación clara: ¿Qué capacidad de respuesta y transparencia tiene el proveedor? ¿Tendrá un punto de contacto dedicado? La comunicación clara es vital durante todo el ciclo de vida del proyecto.
- Presupuestos y plazos de entrega: ¿Son sus presupuestos detallados y fáciles de entender? ¿Se cumplen de forma realista y constante sus estimaciones de plazos de entrega?
- Referencias y trayectoria:
- Testimonios de clientes/Estudios de casos: Solicite referencias o ejemplos de proyectos similares que hayan completado con éxito.
- Estabilidad financiera: Para acuerdos de suministro B2B a largo plazo B2B, también es prudente evaluar la estabilidad del proveedor.
Al evaluar cuidadosamente a los potenciales proveedores de fabricación aditiva con estos criterios, puede seleccionar un socio como Met3dp, que no solo posee las capacidades técnicas, sino que también se alinea con sus expectativas de calidad y los objetivos del proyecto, asegurando un camino fluido desde el diseño hasta las camisas de enfriamiento de alto rendimiento terminadas.
Comprensión de los factores de costo y los plazos de entrega para las camisas de enfriamiento de AM
La fabricación aditiva ofrece importantes ventajas de diseño y rendimiento, pero comprender los factores que influyen en el costo y el plazo de entrega es esencial para la presupuestación, la planificación y la toma de decisiones informadas, particularmente para la adquisición B2B actividades que involucran producción personalizada o en volumen.
Principales factores de coste:
- Tipo y Volumen de Material:
- Coste del material: El costo de la materia prima en polvo varía significativamente. Las aleaciones de cobre como el CuCrZr son sustancialmente más caras por kilogramo que las aleaciones de aluminio como el AlSi10Mg.
- Volumen y peso de la pieza: La cantidad de material utilizado impacta directamente en el costo. Las piezas más grandes o densas consumen más polvo. Las prácticas de DfAM como la optimización topológica pueden reducir significativamente el uso de material y, por lo tanto, el costo.
- Complejidad de la pieza y tiempo de impresión:
- Altura de construcción (altura Z): El tiempo de impresión está determinado en gran medida por el número de capas requeridas, lo que hace que las piezas más altas generalmente tarden más (y cuesten más) que las más cortas, suponiendo un volumen similar.
- Volumen y densidad de la pieza: El volumen total de material a fundir afecta el tiempo empleado por el láser en escanear cada capa.
- Complejidad y soportes: Los diseños intrincados pueden requerir estructuras de soporte extensas, lo que aumenta tanto el tiempo de impresión (los soportes también deben imprimirse) como la mano de obra de post-procesamiento para la eliminación. DfAM optimizado minimiza las necesidades de soporte.
- Anidación/Utilización de la máquina: Los proveedores de servicios buscan maximizar el número de piezas impresas simultáneamente en una sola placa de construcción (anidamiento). La eficiencia del anidamiento impacta en el costo del tiempo de máquina asignado por pieza.
- Costes de la máquina:
- Máquina Tarifa por hora: Los proveedores de servicios de AM tienen en cuenta el costo de capital de las sofisticadas máquinas LPBF, el mantenimiento, los consumibles (filtros, gas) y el tiempo del operador en una tarifa horaria de la máquina.
- Requisitos de postprocesamiento:
- Mano de obra y equipo: Cada paso de post-procesamiento (alivio de tensión, eliminación de soportes, mecanizado, acabado, pruebas) agrega costo en función de la intensidad de la mano de obra, el nivel de habilidad requerido y el uso de equipos especializados (por ejemplo, tiempo de horno, tiempo de máquina CNC, AFM).
- Impacto de la complejidad: Los canales internos complejos que requieren una difícil eliminación de soportes o un suavizado especializado (como AFM) incurrirán en mayores costos de post-procesamiento. El mecanizado de múltiples características de tolerancia ajustada también agrega un costo significativo en comparación con las piezas que requieren un acabado mínimo.
- Aseguramiento de la calidad e inspección:
- Nivel de inspección: El nivel requerido de control de calidad impacta en el costo. Las comprobaciones dimensionales básicas son estándar, pero los requisitos como las pruebas de fugas al 100%, la exploración TC para la integridad interna, los informes CMM detallados o las certificaciones de materiales agregan tiempo y costo.
- Volumen del pedido y configuración:
- Costes de configuración: Hay costos fijos asociados con la configuración de cada construcción (programación, preparación de la máquina, carga de polvo). Estos costos de configuración se amortizan sobre el número de piezas en un lote.
- Descuentos por volumen: Para mayores pedidos al por mayor o ejecuciones de producción recurrentes, los costos por pieza generalmente disminuyen debido a la amortización de los costos de configuración y las posibles eficiencias en la impresión y el procesamiento por lotes. Discuta los niveles de precios por volumen con su proveedor.
Componentes típicos del plazo de entrega:
El plazo de entrega es el tiempo total desde la colocación del pedido hasta la recepción de las piezas terminadas. Comprende varias etapas:
- Cotización y confirmación del pedido: (1-3 días)
- Revisión de ingeniería y preparación de archivos: Comprobaciones de DfAM, planificación de la estrategia de soporte, generación de archivos de construcción. (1-2 días)
- Cola de máquinas: Esperando una ranura de máquina disponible. (Variable: días a semanas, dependiendo de la carga de trabajo del proveedor)
- Imprimiendo: El tiempo de construcción real. (Horas a varios días, dependiendo del tamaño/complejidad/anidamiento)
- Enfriamiento y despolvoreo: Dejar que la cámara de construcción se enfríe, retirar la placa de construcción, eliminación inicial del polvo. (Varias horas a 1 día)
- Alivio del estrés / Tratamiento térmico: Tiempo de ciclo del horno. (1-2 días, incluyendo calentamiento/enfriamiento)
- Retiro de la placa y eliminación del soporte: (Horas a días, muy dependiente de la complejidad)
- Post-procesamiento: Mecanizado, acabado, limpieza, etc. (Días a semanas, dependiendo de los requisitos)
- Inspección de calidad y pruebas: (1-3 días)
- Embalaje y envío: (1-2 días + tiempo de tránsito)
Cronogramas estimados:
- Prototipos (1-5 unidades): Normalmente De 1 a 3 semanas, dependiendo en gran medida de la complejidad, el material, la carga actual de la máquina y el post-procesamiento requerido.
- Producción de bajo volumen (10-100 unidades): A menudo De 3 a 6 semanas.
- Producción de mayor volumen: Requiere una planificación cuidadosa con el proveedor; los plazos de entrega dependen de la capacidad, los recursos dedicados y la posible necesidad de múltiples máquinas.
Es crucial discutir las expectativas específicas de costos y plazos de entrega con su fabricante por contrato de AM elegido en función de su diseño final y requisitos. Proporcionar especificaciones claras y plazos realistas facilita la cotización y la planificación precisas.
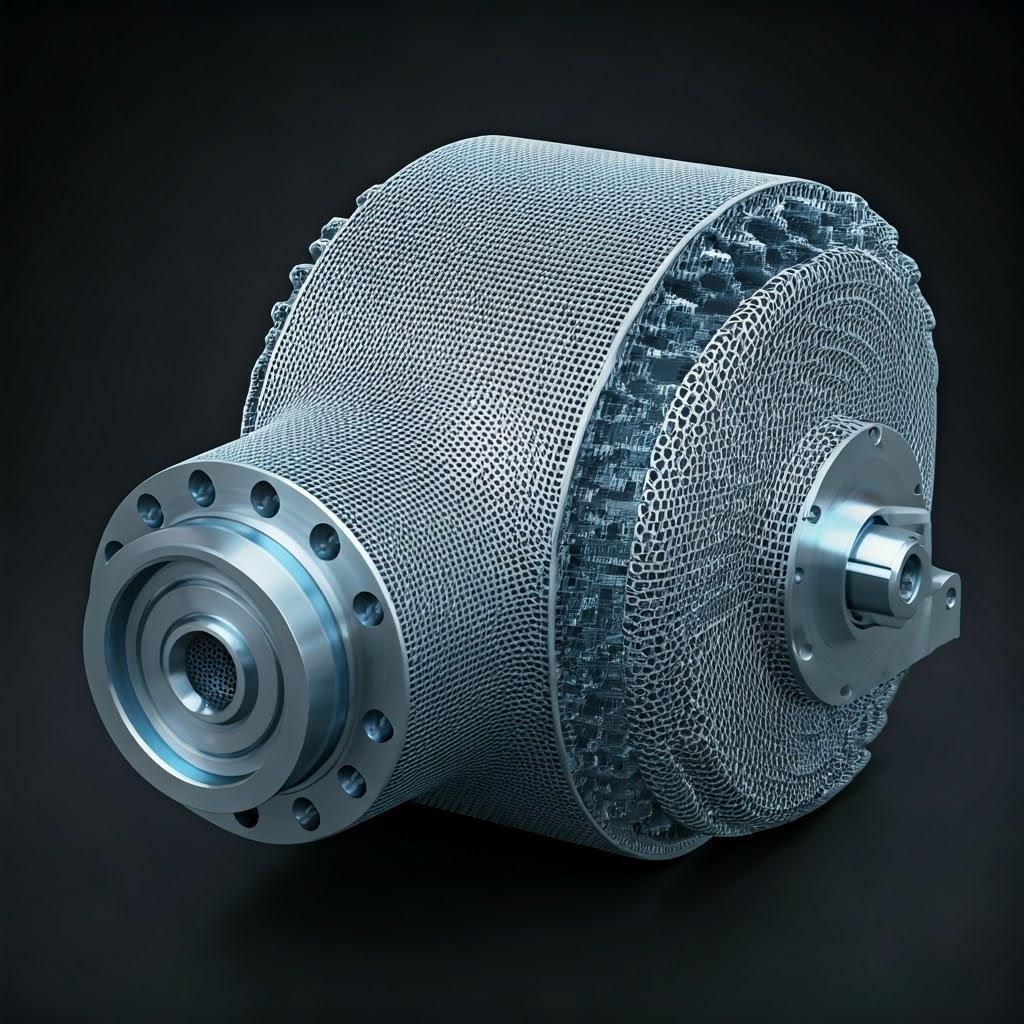
Preguntas frecuentes (FAQ) sobre las camisas de enfriamiento de motores AM
Aquí hay respuestas a algunas preguntas comunes que los ingenieros y especialistas en adquisiciones tienen sobre el uso de la fabricación aditiva para las camisas de enfriamiento de motores eléctricos:
- P1: ¿Cómo se compara el rendimiento de las camisas de enfriamiento de AM con las tradicionales (fundidas, fabricadas)?
- A: Las camisas de enfriamiento fabricadas aditivamente a menudo demuestran un rendimiento térmico significativamente mejorado en comparación con sus contrapartes tradicionales. La principal ventaja radica en la libertad de diseño que ofrece AM. Los ingenieros pueden crear canales de enfriamiento internos altamente complejos que se ajustan con precisión a las fuentes de calor del motor (enfriamiento conforme) e incorporar características como turbuladores o aletas internas para maximizar el área de superficie y los coeficientes de transferencia de calor. Los estudios y ejemplos de aplicaciones han demostrado mejoras potenciales de 20-50% o incluso superior en la capacidad de disipación de calor, lo que lleva a temperaturas de funcionamiento más bajas, una mayor densidad de potencia o una vida útil prolongada del motor. Sin embargo, la ganancia de rendimiento exacta depende en gran medida de la optimización específica del diseño lograda a través de DfAM en comparación con el diseño tradicional de referencia.
- P2: ¿Cuáles son los límites típicos de temperatura y presión de funcionamiento máximos para las camisas de enfriamiento de AlSi10Mg o CuCrZr?
- A: Los límites operativos dependen en gran medida del diseño específico (especialmente el espesor de la pared), el tratamiento térmico posterior a la impresión aplicado y la integración general del sistema..
- Temperatura: El AlSi10Mg funciona bien hasta aproximadamente 150°C (302°F), con propiedades mecánicas que comienzan a degradarse significativamente por encima de los 200°C (392°F). El CuCrZr procesado correctamente conserva una buena resistencia y una excelente conductividad térmica a temperaturas más altas, potencialmente utilizable hasta 300-400°C (572-752°F) o superior, dependiendo del tratamiento de envejecimiento específico y los niveles de tensión.
- Presión: El límite de presión es principalmente una función de la integridad estructural del diseño (espesor de la pared, geometría, elementos de soporte) y la resistencia a la fluencia del material. Las camisas de AM pueden diseñarse y validarse mediante simulación (FEA) y pruebas de presión rigurosas (incluidas pruebas de explosión) para soportar las presiones típicas del circuito de refrigerante (por ejemplo, 2-10 bar o superior). Es fundamental definir los requisitos operativos y realizar las pruebas de validación adecuadas en el diseño final de la pieza. Las propiedades generales del material por sí solas no garantizan el rendimiento; la implementación del diseño es clave.
- A: Los límites operativos dependen en gran medida del diseño específico (especialmente el espesor de la pared), el tratamiento térmico posterior a la impresión aplicado y la integración general del sistema..
- P3: ¿Se pueden convertir fácilmente los diseños de camisas de refrigeración existentes, originalmente fabricados para fundición o mecanizado, para la fabricación aditiva?
- A: Si bien es técnicamente posible imprimir un diseño originalmente destinado a la fundición o el mecanizado, hacerlo a menudo no aprovecha las principales ventajas de la AM e incluso puede ser subóptimo o más caro. Imprimir directamente un diseño optimizado para fundición, por ejemplo, podría incluir características como ángulos de desmoldeo o paredes gruesas que son innecesarias e ineficientes para la AM. Generalmente no se recomienda una conversión simple. Para lograr los beneficios de un mejor rendimiento, un peso reducido y la consolidación de piezas, la camisa de refrigeración debería, idealmente, ser rediseñada o adaptada significativamente utilizando los principios de Diseño para la Fabricación Aditiva (DfAM). Esto implica repensar las trayectorias de los canales, optimizar la topología, minimizar los soportes y, potencialmente, consolidar los ensamblajes. Un proveedor de servicios de AM puede ayudar a evaluar un diseño existente y recomendar modificaciones para una producción óptima de AM.
- P4: ¿Es la AM de metales adecuada para la producción de alto volumen de camisas de refrigeración?
- A: La FA de metal es cada vez más viable para producción en serie, no solo prototipos. Si bien los métodos tradicionales como la fundición sobresalen en volúmenes extremadamente altos (cientos de miles a millones) de piezas idénticas debido al bajo costo por pieza una vez que se fabrica la herramienta, la AM puede ser muy competitiva para volúmenes bajos a medianos (decenas a miles), especialmente cuando la complejidad, la personalización o el rendimiento son factores clave. El punto de "equilibrio" depende de la complejidad de la pieza, el material y los costos de las herramientas tradicionales. Para camisas de refrigeración complejas y altamente optimizadas que ofrecen importantes ganancias de rendimiento, la AM puede ser la solución más económica incluso en volúmenes moderados al considerar el valor total del sistema. Discuta sus requisitos de volumen con posibles Proveedores B2B como Met3dp para evaluar la viabilidad y la economía de la producción.
Conclusión: Revolución de la refrigeración de motores eléctricos con fabricación aditiva
El desafío de gestionar el calor en motores eléctricos cada vez más potentes y compactos es un obstáculo crítico en industrias exigentes como la automotriz, la aeroespacial y la automatización industrial. Los métodos de fabricación tradicionales para camisas de refrigeración, aunque establecidos, a menudo imponen limitaciones a la complejidad del diseño y la eficiencia térmica. La fabricación aditiva de metales emerge como una solución poderosa, cambiando fundamentalmente la forma en que los ingenieros pueden abordar el diseño de la gestión térmica.
Al aprovechar el proceso de construcción capa por capa de tecnologías como la Fusión de Lecho de Polvo Láser, la AM permite la creación de camisas de refrigeración de motores eléctricos con una libertad geométrica sin precedentes. Esto se traduce directamente en beneficios tangibles:
- Rendimiento térmico superior: A través de canales de refrigeración conformes y características internas complejas optimizadas para la transferencia de calor.
- Reducción significativa del peso: Mediante la optimización de la topología y el uso eficiente de los materiales, cruciales para las aplicaciones móviles.
- Consolidación de piezas: Reducir la complejidad del ensamblaje, los posibles puntos de fuga y simplificar la cadena de suministro.
- Prototipado rápido y personalización: Acelerar los ciclos de desarrollo y permitir soluciones a medida sin costos de herramientas.
Materiales como el ligero AlSi10Mg y el altamente conductivo CuCrZr, cuando se procesan utilizando polvos de alta calidad y parámetros de AM optimizados, proporcionan la base para estos componentes de alto rendimiento. Sin embargo, la obtención de estos beneficios requiere la adopción de los principios de Diseño para la Fabricación Aditiva (DfAM) y la navegación de los posibles desafíos de producción a través de una cuidadosa planificación y ejecución.
Elegir bien socio de fabricación aditiva B2B es primordial. La experiencia en ciencia de materiales, el control de procesos robusto, las capacidades integrales de posprocesamiento y el compromiso con la calidad, sellos distintivos de un proveedor como Met3dp , son esenciales para transformar diseños innovadores en componentes fiables y de uso final. Con décadas de experiencia colectiva y capacidades avanzadas en ambos producción de polvo metálico y sistemas de fabricación aditiva, Met3dp está en una posición única para apoyar sus proyectos de gestión térmica más exigentes.
La AM de metales ya no es solo una herramienta de prototipado; es un método de producción viable y de valor añadido listo para revolucionar la refrigeración de motores eléctricos. Al implementar estratégicamente esta tecnología, las empresas pueden desbloquear nuevos niveles de rendimiento, eficiencia y fiabilidad para sus aplicaciones de motores eléctricos.
¿Está listo para explorar cómo la fabricación aditiva puede optimizar sus soluciones de refrigeración de motores eléctricos? Póngase en contacto con Met3dp hoy mismo para discutir los requisitos de su proyecto con nuestros expertos.
Compartir
MET3DP Technology Co., LTD es un proveedor líder de soluciones de fabricación aditiva con sede en Qingdao, China. Nuestra empresa está especializada en equipos de impresión 3D y polvos metálicos de alto rendimiento para aplicaciones industriales.
Solicite información para obtener el mejor precio y una solución personalizada para su empresa.
Artículos relacionados
Acerca de Met3DP
Actualización reciente
Nuestro producto
CONTACTO
¿Tiene alguna pregunta? ¡Envíenos un mensaje ahora! Atenderemos su solicitud con todo un equipo tras recibir su mensaje.
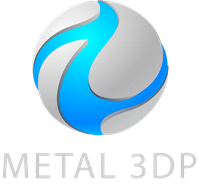
Polvos metálicos para impresión 3D y fabricación aditiva