AlSi10Mg para soportes automotrices en impresión 3D metálica
Índice
Introducción: Revolución de los soportes automotrices con la impresión 3D metálica AlSi10Mg
La industria automotriz opera a la vanguardia de la adopción tecnológica, impulsada constantemente por los imperativos de mejorar el rendimiento del vehículo, mejorar la eficiencia del combustible (o la autonomía eléctrica), garantizar la seguridad de los pasajeros y acelerar los ciclos de desarrollo de productos. En esta incesante búsqueda de la innovación, las metodologías de fabricación juegan un papel fundamental. Las técnicas tradicionales como la fundición, el estampado y el mecanizado, aunque maduras y fiables para la producción en masa, a menudo presentan limitaciones en términos de flexibilidad de diseño, optimización del peso y la velocidad requerida para la creación rápida de prototipos y la personalización de bajo volumen. Ingrese la fabricación aditiva metálica (AM), más comúnmente conocida como metal Impresión 3D – una tecnología transformadora destinada a redefinir cómo se conciben, diseñan y producen componentes automotrices críticos, como los soportes.
Los soportes automotrices, aunque a menudo discretos, son componentes fundamentales que desempeñan funciones esenciales. Sirven como interfaz estructural, puntos de montaje y estructuras de soporte para una amplia gama de sistemas dentro de un vehículo, desde componentes del motor y la transmisión hasta elementos del chasis, accesorios interiores y módulos electrónicos sensibles. Su rendimiento impacta directamente en la integridad del vehículo, las características de vibración, los niveles de ruido y la eficiencia general del montaje. Tradicionalmente, el diseño y la fabricación de estos soportes implicaban compromisos. Lograr la resistencia a menudo significaba agregar peso, las geometrías complejas requerían ensamblajes de múltiples piezas o herramientas intrincadas, y la producción de prototipos o lotes pequeños incurría en importantes penalizaciones de tiempo y costo asociadas con la configuración de herramientas.
Aquí es donde la sinergia entre los materiales avanzados y los procesos de fabricación de vanguardia crea un potencial disruptivo. AlSi10Mg, una aleación de aluminio-silicio-magnesio, se ha convertido en un material fundamental en el panorama de la AM metálica, particularmente para tecnologías de fusión de lecho de polvo como la fusión por láser selectiva (SLM) y la sinterización por láser directo de metales (DMLS). Reconocido por su excelente equilibrio de propiedades mecánicas, que incluyen una buena relación resistencia-peso, soldabilidad, resistencia a la corrosión y excelente procesabilidad en sistemas AM, AlSi10Mg ofrece una solución ideal para muchas aplicaciones de soportes automotrices. Sus propiedades se asemejan mucho a las de las aleaciones de fundición tradicionales, lo que proporciona a los ingenieros una línea de base de material familiar al tiempo que desbloquea la libertad de diseño sin precedentes que ofrece la impresión 3D.
La combinación de polvo AlSi10Mg y impresión 3D en metal técnicas capacita a los ingenieros y gerentes de adquisiciones de toda la cadena de valor automotriz, desde los fabricantes de equipos originales (OEM) y los proveedores de nivel 1/nivel 2 hasta los equipos de deportes de motor de nicho y los especialistas del mercado de accesorios, para reimaginar el diseño de los soportes. Permite la creación de estructuras ligeras y optimizadas por topología que antes eran imposibles de fabricar. Facilita la consolidación de múltiples componentes en una sola pieza impresa compleja, lo que reduce la complejidad del montaje y los posibles puntos de falla. Además, reduce drásticamente los plazos de entrega de prototipos funcionales y permite tiradas de producción de bajo volumen rentables sin la necesidad de herramientas costosas y dedicadas. Esta agilidad es primordial en el entorno de desarrollo automotriz de ritmo
Como proveedor líder de soluciones integrales de fabricación aditiva, Met3dp está a la vanguardia de este cambio tecnológico. Con sede en Qingdao, China, Met3dp se especializa no solo en equipos de impresión 3D de metal de última generación, conocidos por su volumen de impresión, precisión y fiabilidad líderes en la industria, sino también en la investigación, el desarrollo y la producción de polvos metálicos de alto rendimiento, incluido el AlSi10Mg de primera calidad optimizado para los procesos de fabricación aditiva. Nuestra profunda experiencia, cultivada durante décadas en la fabricación aditiva de metales, abarca todo el ecosistema, desde la atomización avanzada de polvos utilizando tecnologías únicas de atomización por gas y PREP hasta sofisticados sistemas de impresión como la fusión selectiva por haz de electrones (SEBM) y el soporte para el desarrollo de aplicaciones. Nos asociamos con organizaciones automotrices para aprovechar el poder de la fabricación aditiva, transformando sus capacidades de fabricación y acelerando su viaje hacia el diseño y la producción de vehículos de próxima generación. Este artículo profundiza en los detalles de la utilización de AlSi10Mg mediante la impresión 3D de metal para soportes automotrices, explorando aplicaciones, ventajas, consideraciones de materiales y mejores prácticas para el abastecimiento y la implementación, posicionando a Met3dp como su socio B2B de confianza para soluciones de fabricación aditiva de grado industrial. Para los equipos de ingeniería que buscan avances en el rendimiento y los gerentes de adquisiciones que buscan proveedores de impresión de metal B2B fiables y rentables, es crucial comprender los matices de AlSi10Mg en la fabricación aditiva.
Diversas aplicaciones: ¿Dónde se utilizan los soportes automotrices de AlSi10Mg impresos en 3D?
La versatilidad de AlSi10Mg combinada con la libertad de diseño de la impresión 3D de metal abre un vasto panorama de aplicaciones para los soportes automotrices, que se extiende mucho más allá de los simples reemplazos de piezas fabricadas convencionalmente. La capacidad de crear geometrías complejas, ligeras y personalizadas permite que estos soportes resuelvan desafíos de ingeniería específicos en prácticamente todos los sistemas dentro de un vehículo moderno. Los profesionales de adquisiciones e ingenieros que se abastecen de componentes para fabricantes de equipos originales, proveedores de nivel o sectores automotrices especializados deben reconocer la amplitud de estas aplicaciones para aprovechar al máximo el potencial de la tecnología.
Funciones principales y por qué la fabricación aditiva sobresale:
Los soportes automotrices sirven fundamentalmente para:
- Conectar componentes: Conectar diferentes piezas o subsistemas (por ejemplo, motor al chasis).
- Soportar cargas: Soportar cargas estáticas o dinámicas para mantener la integridad estructural (por ejemplo, soportes de suspensión).
- Montar sistemas: Proporcionar ubicaciones seguras para fijar componentes como sensores, actuadores, ECU, bombas o tuberías de fluidos.
- Gestionar la vibración: A veces diseñados con geometrías específicas para amortiguar o aislar las vibraciones.
La fabricación aditiva de metales, particularmente con AlSi10Mg, sobresale en estas funciones al permitir:
- Trayectorias de carga optimizadas: El software de optimización topológica puede generar diseños de soportes que colocan el material precisamente donde se necesita para manejar casos de carga específicos, minimizando el peso mientras se mantiene o mejora la resistencia.
- Funcionalidad integrada: Las características como los canales de fluidos, los conductos de cableado o los disipadores de calor se pueden integrar directamente en el diseño del soporte, lo que reduce el número de piezas y la complejidad del montaje.
- Interfaz compleja: La creación de soportes con superficies de montaje o características intrincadas para encajar en espacios estrechos se vuelve factible.
Ejemplos de aplicaciones específicas en los sistemas de vehículos:
Exploremos ejemplos concretos donde los soportes de AlSi10Mg impresos en 3D ofrecen un valor significativo:
- Motor y tren motriz:
- Soportes de alternador/motor de arranque: A menudo sujetos a vibraciones y temperaturas moderadas. La fabricación aditiva permite diseños ligeros optimizados para la rigidez y la amortiguación de vibraciones.
- Soportes de sensores (por ejemplo, sensores de detonación, sensores de temperatura): Se pueden requerir geometrías complejas para un posicionamiento preciso en espacios reducidos del compartimento del motor. La fabricación aditiva permite la creación rápida de prototipos y la producción de soportes personalizados.
- Colgadores/soportes del sistema de escape: Si bien las altas temperaturas cerca del colector pueden requerir diferentes aleaciones, los soportes más abajo pueden beneficiarse de la naturaleza ligera y la resistencia a la corrosión de AlSi10Mg. La fabricación aditiva permite diseños que se adaptan a la expansión térmica.
- Soportes de bomba de combustible/filtro: Se pueden diseñar con características integradas para el enrutamiento de mangueras o el aislamiento de vibraciones.
- Soportes de turbocompresor/sobrealimentador (secciones de baja temperatura): Los componentes que soportan piezas auxiliares de los sistemas de inducción forzada pueden aligerarse.
- Chasis y suspensión:
- Soportes de componentes de suspensión (por ejemplo, soportes de brazo de control superior/inferior, para creación de prototipos/bajo volumen): Si bien la producción de alto volumen podría utilizar forja/fundición, la fabricación aditiva es invaluable para la creación rápida de prototipos de geometrías de suspensión complejas y para vehículos de alto rendimiento de bajo volumen donde el aligeramiento es primordial. AlSi10Mg proporciona un buen equilibrio para las pruebas antes de pasar potencialmente a materiales de mayor resistencia si es necesario.
- Soportes de líneas de freno y sensores (ABS): El enrutamiento complejo y el posicionamiento preciso de los sensores se benefician de la libertad geométrica de la fabricación aditiva. La consolidación de piezas puede reducir los pasos de montaje.
- Soportes del sistema de dirección: Montaje de cremalleras de dirección o sensores asociados.
- Soportes de barra estabilizadora: Se pueden optimizar topológicamente para la rigidez y el peso.
- Carrocería y exterior:
- Soportes de montaje de parachoques: Especialmente para vehículos de bajo volumen o personalizados, la fabricación aditiva permite interfaces complejas con el chasis y la estructura del parachoques, optimizadas para las vías de absorción de energía (aunque la elección del material necesita una cuidadosa consideración para la resistencia a los choques).
- Soportes de alerones/elementos aerodinámicos: A menudo se requieren formas ligeras y complejas, lo que hace que la fabricación aditiva sea ideal para aplicaciones de rendimiento.
- Soportes del sistema de iluminación (faros, luces traseras): Pueden requerir formas intrincadas para encajar dentro de las señales de estilo de los vehículos modernos y las limitaciones de embalaje ajustadas.
- Soportes de espejo: Las estructuras internas se pueden optimizar para la amortiguación de vibraciones y la reducción de peso.
- Sistemas interiores:
- Soportes del marco del asiento: El aligeramiento de los componentes interiores contribuye significativamente a la reducción general de la masa del vehículo.
- Soportes de soporte del salpicadero/panel de instrumentos: A menudo se necesitan geometrías complejas para navegar por los conductos de climatización, los mazos de cables y los miembros estructurales. La fabricación aditiva permite la consolidación y el ahorro de peso.
- Soportes de componentes de climatización: Soportes para ventiladores, evaporadores o núcleos de calentamiento.
- Soportes de la consola central: Soporte de sistemas de infoentretenimiento, palancas de cambio, etc.
- Vehículos eléctricos (VE) e híbridos (HEV):
- Soportes de montaje de la batería/componentes del bastidor: El soporte de módulos de batería pesados requiere estructuras fuertes pero ligeras. AlSi10Mg ofrece un buen punto de partida, y la fabricación aditiva permite características integradas de gestión térmica (por ejemplo, canales para fluidos de refrigeración) dentro de los soportes.
- Soportes de motor eléctrico: Requisitos similares a los soportes del motor de combustión interna, pero con diferentes perfiles de vibración.
- Cargador de a bordo (OBC) y soportes de electrónica de potencia: A menudo requieren puntos de montaje específicos y, potencialmente, características de refrigeración integradas.
- Soportes del puerto de carga: Montaje seguro de la entrada de carga del vehículo.
- Aplicaciones de deportes de motor y rendimiento:
- Soportes altamente personalizados: Prácticamente cualquier soporte se puede diseñar, imprimir y probar rápidamente para coches de carreras o vehículos de alto rendimiento donde la velocidad de iteración y el máximo rendimiento superan las restricciones de costes.
- Soportes de sensores a medida: Para sistemas adicionales de adquisición de datos.
- Alternativas ligeras: Reemplazo de los soportes estándar con versiones de AlSi10Mg optimizadas topológicamente para obtener una ventaja competitiva.
Categorización de casos de uso para el abastecimiento B2B:
Los gerentes de adquisiciones y los compradores mayoristas deben considerar estas categorías de aplicaciones al interactuar con los proveedores de servicios de fabricación aditiva como Met3dp:
Categoría de caso de uso | Descripción | Beneficios clave para los clientes B2B automotrices | Volumen típico |
---|---|---|---|
Creación rápida de prototipos | Creación rápida de soportes funcionales para la validación del diseño, comprobaciones de ajuste y pruebas de rendimiento. | Ciclos de desarrollo acelerados, tiempo de iteración reducido, identificación temprana de fallas de diseño, menor riesgo. | Muy bajo (1-10) |
Producción de bajo volumen | Fabricación de soportes de uso final para vehículos de nicho, deportes de motor o tiradas de producción iniciales antes de escalar. | Evitar los altos costes de utillaje, permite la entrada en el mercado de vehículos especializados, flexibilidad de diseño. | Bajo (10-1000s) |
Personalización/a medida | Producción de soportes únicos para vehículos personalizados, modificaciones del mercado de accesorios o necesidades de rendimiento específicas. | Alta libertad de diseño, atiende a mercados de nicho, ofertas de productos premium. | Muy bajo a bajo |
Piezas del mercado de accesorios | Suministro de soportes de reemplazo o actualización de rendimiento para vehículos existentes. | Capacidad de ofrecer diseños mejorados (por ejemplo, menor peso), aborda la obsolescencia de las piezas. | Bajo a medio |
Reemplazo de piezas heredadas | Recreación de soportes para vehículos más antiguos donde el utillaje original ya no existe (inventario digital). | Resuelve los problemas de obsolescencia, apoya la restauración de coches clásicos, evita la costosa recreación de utillaje. | Muy bajo a bajo |
Consolidación de piezas | Rediseño de conjuntos para combinar múltiples soportes/componentes en una sola pieza impresa. | Tiempo/coste de montaje reducido, menor peso, mayor fiabilidad, cadena de suministro simplificada. | Bajo a medio |
Exportar a hojas
La comprensión de esta diversa gama de aplicaciones permite a las empresas automotrices implementar estratégicamente la impresión 3D de AlSi10Mg, apuntando a áreas donde ofrece el impacto más significativo, ya sea en la aceleración de la I+D, la habilitación de diseños innovadores o la provisión de soluciones rentables para necesidades de bajo volumen y personalizadas. Met3dp, con su sólida métodos de impresión y experiencia en materiales, está equipado para apoyar a los clientes B2B en todos estos escenarios de aplicación, desde el prototipo inicial hasta las piezas de producción en serie.
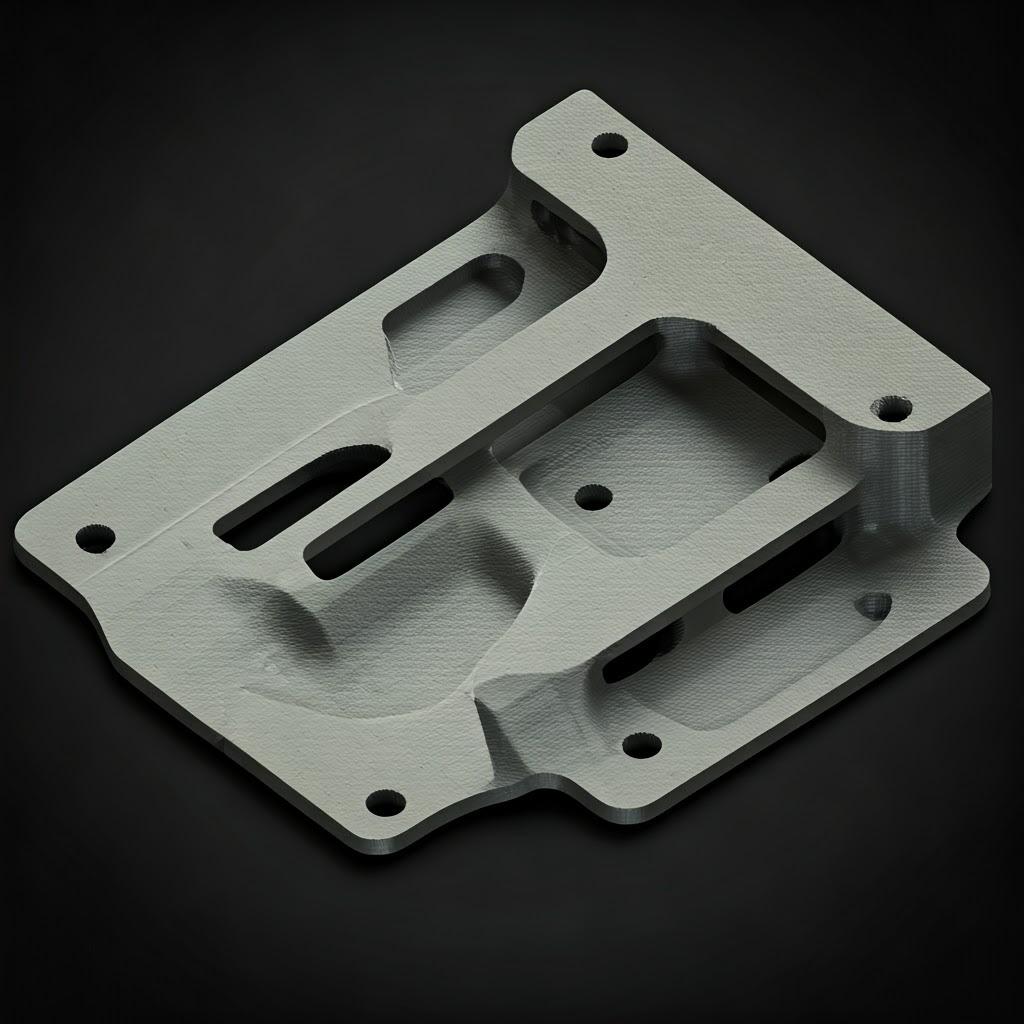
La ventaja aditiva: ¿Por qué elegir la impresión 3D de metal para la producción de soportes automotrices?
Si bien los métodos de fabricación tradicionales siguen siendo el estándar para la producción de soportes automotrices de alto volumen, la fabricación aditiva de metales, específicamente el uso de materiales como AlSi10Mg a través de procesos de fusión en lecho de polvo (PBF) (SLM/DMLS), ofrece ventajas convincentes, particularmente en contextos que exigen innovación, velocidad, personalización y rendimiento optimizado. Para los ingenieros que superan los límites del diseño y los gerentes de adquisiciones que buscan soluciones de abastecimiento eficientes y flexibles, comprender estos beneficios es clave para aprovechar la fabricación aditiva de manera efectiva. La decisión de adoptar la fabricación aditiva no se trata simplemente de reemplazar un proceso antiguo por uno nuevo; se trata de desbloquear capacidades previamente inalcanzables.
Comparación: Fabricación aditiva de metales (AlSi10Mg) frente a métodos tradicionales para soportes
Característica | Fabricación aditiva de metales (SLM/DMLS con AlSi10Mg) | Fundición tradicional (por ejemplo, fundición a presión) | Mecanizado tradicional (sustractivo) | Estampado/conformado tradicional |
---|---|---|---|---|
Complejidad del diseño | Extremadamente alto (canales internos, enrejados, formas orgánicas) | Moderado (Limitado por los ángulos de salida del molde, el grosor de la pared) | Alto (Limitado por el acceso a la herramienta, las características) | Bajo a moderado (formas de chapa metálica, dobleces, características simples) |
Aligeramiento | Excelente (Optimización topológica, material solo donde se necesita) | Bueno (Puede lograr una forma casi neta) | Moderado (Eliminación de material, pero comienza con un bloque sólido) | Moderado (Limitado por el grosor de la lámina) |
Consolidación de piezas | Excelente (Múltiples funciones integradas en una sola pieza) | Limitado (Difícil de integrar características internas complejas) | Limitado (Requiere mecanizado multi-eje complejo) | Muy limitado (Típicamente piezas de una sola función) |
Coste de utillaje | Ninguno (El archivo digital es la entrada) | Muy alto (Diseño y fabricación de moldes) | Bajo a moderado (Fijación, herramientas estándar) | Alto (Diseño y fabricación de matrices) |
Plazo de entrega (Proto) | Muy rápido (Días) | Muy lento (Semanas a meses para el utillaje) | Rápido (Días a semanas, depende de la complejidad) | Lento (Semanas a meses para el utillaje) |
Plazo de entrega (Prod) | Moderado (Depende del volumen de construcción, el posprocesamiento) | Rápido (Para grandes volúmenes una vez que existe el utillaje) | Moderado a lento (Depende de la complejidad, eliminación de material) | Muy rápido (Para grandes volúmenes una vez que existe el utillaje) |
Residuos materiales | Bajo (El polvo no utilizado es en gran medida reciclable) | Bajo (Uso eficiente del material en el molde) | Alto (Se elimina una cantidad significativa de material en forma de virutas) | Moderado (Recortes de la lámina) |
Coste unitario (Vol. bajo) | Competitivo a alto (Impulsado por el tiempo de máquina, el material) | Muy alto (La amortización del utillaje domina) | Alto (Tiempo de mecanizado por pieza) | Muy alto (La amortización del utillaje domina) |
Coste unitario (Vol. alto) | Alta | Muy bajo | Moderado a alto | Muy bajo |
Opciones de material | Gama creciente de aleaciones soldables/imprimibles | Amplia gama de aleaciones fundibles | Gama muy amplia de materiales mecanizables | Gama de metales en lámina conformables |
Exportar a hojas
Ventajas clave de la fabricación aditiva de metales para los soportes de automoción:
- Libertad de diseño y complejidad geométrica sin precedentes: Esta es posiblemente la ventaja más significativa. La fabricación aditiva libera a los diseñadores de las limitaciones impuestas por las herramientas y los procesos de fabricación tradicionales.
- Optimización de la topología: Los algoritmos pueden esculpir los soportes con formas óptimas basadas en las trayectorias de carga, minimizando el peso y cumpliendo los requisitos de rigidez. Esto se traduce en estructuras de aspecto orgánico y muy eficientes.
- Estructuras reticulares: Se pueden incorporar estructuras internas de celosía o celulares para reducir aún más el peso, gestionar la absorción de energía o alterar las características de vibración.
- Canales internos: Los conductos para los fluidos de refrigeración, el cableado o las tuberías hidráulicas pueden integrarse a la perfección en la estructura del soporte, consolidando las piezas y simplificando el montaje.
- Ángulos de salida negativos y socavaduras: Las características imposibles de conseguir con el fundido sin núcleos complejos o moldes de varias piezas se imprimen fácilmente.
- Potencial significativo de aligeramiento: En el mundo de la automoción, la reducción de masa se traduce directamente en una mejora del ahorro de combustible, un aumento de la autonomía de los vehículos eléctricos, una mejor dinámica de manejo y un mejor rendimiento. La fabricación aditiva permite el aligeramiento a través de:
- Optimización de la topología: Como se ha mencionado, colocando el material solo donde es estructuralmente necesario. A menudo se consiguen ahorros de peso del 20-60% en comparación con las contrapartes diseñadas tradicionalmente.
- Elección de materiales: Aunque el AlSi10Mg ya es ligero, la fabricación aditiva permite un control preciso sobre los grosores de las paredes y las estructuras internas que no son posibles con el fundido o el mecanizado a partir de material en bruto.
- Prototipado e iteración acelerados: La capacidad de pasar de un archivo CAD a un prototipo metálico funcional en días, en lugar de semanas o meses esperando el utillaje, revoluciona el ciclo de desarrollo del producto.
- Validación más rápida del diseño: Los ingenieros pueden probar rápidamente múltiples variaciones de diseño para el ajuste, la forma y la función.
- Reducción de los costes de desarrollo: Detectar los fallos de diseño al principio con prototipos de bajo coste ahorra costosas reelaboraciones posteriores.
- Mayor rapidez de comercialización: La reducción de los plazos de desarrollo proporciona una ventaja competitiva.
- Eliminación de los costes de utillaje: La importante inversión requerida para los moldes (fundición) o las matrices (estampación) se evita por completo con la fabricación aditiva.
- Producción de bajo volumen rentable: Hace que la fabricación de lotes de decenas, cientos o incluso unos pocos miles sea económicamente viable, ideal para vehículos de nicho, deportes de motor o rampas de producción iniciales.
- Permite la personalización: La producción de soportes a medida o personalizados es factible sin los prohibitivos gastos de utillaje para cada variante.
- Oportunidades de consolidación de piezas: La fabricación aditiva permite a los diseñadores replantearse los conjuntos. Múltiples soportes, sujetadores y conectores sencillos pueden rediseñarse e imprimirse como un único componente monolítico complejo.
- Reducción del tiempo y la mano de obra de montaje: Menos piezas que manipular, alinear y sujetar.
- Menores costes de inventario y logística: Gestión de un número de pieza en lugar de varios.
- Fiabilidad mejorada: Elimina los posibles puntos de fallo en las uniones e interfaces.
- Reducción de peso: A menudo, la pieza consolidada es más ligera que la suma de sus componentes originales.
- Fabricación bajo demanda e inventario digital: Las piezas pueden imprimirse según sea necesario, lo que reduce la necesidad de grandes inventarios físicos. Los diseños almacenados digitalmente pueden producirse en cualquier lugar con el equipo adecuado, lo que permite una fabricación descentralizada y la resistencia a las interrupciones de la cadena de suministro. Esto es especialmente valioso para los proveedores B2B que gestionan diversas carteras de piezas y para el suministro de componentes heredados.
- Eficiencia del material: En comparación con el mecanizado sustractivo, en el que gran parte del bloque de material inicial se convierte en virutas de desecho, los procesos PBF utilizan la materia prima en polvo de forma más eficiente. El polvo no fusionado dentro de la cámara de construcción puede, por lo general, tamizarse y reciclarse de nuevo en el proceso, minimizando el consumo de materia prima.
El compromiso de Met3dp de proporcionar un servicio robusto y de grado industrial soluciones de fabricación aditiva permite a los clientes de automoción capitalizar plenamente estas ventajas. Nuestras impresoras, reconocidas por su precisión y fiabilidad, garantizan que los soportes de AlSi10Mg complejos y optimizados para la topología cumplan los estrictos estándares de calidad de la automoción. Al asociarse con Met3dp, las empresas obtienen acceso no solo a los equipos y materiales, sino también a la experiencia necesaria para implementar la fabricación aditiva de forma eficaz, transformando su enfoque del diseño y la producción de soportes para obtener beneficios tangibles en rendimiento, coste y velocidad. Los equipos de compras que buscan socios de fabricación ágiles e innovadores encontrarán que la fabricación aditiva, especialmente a través de proveedores experimentados como Met3dp, ofrece una propuesta de valor convincente más allá de los métodos tradicionales para muchas aplicaciones de soportes.
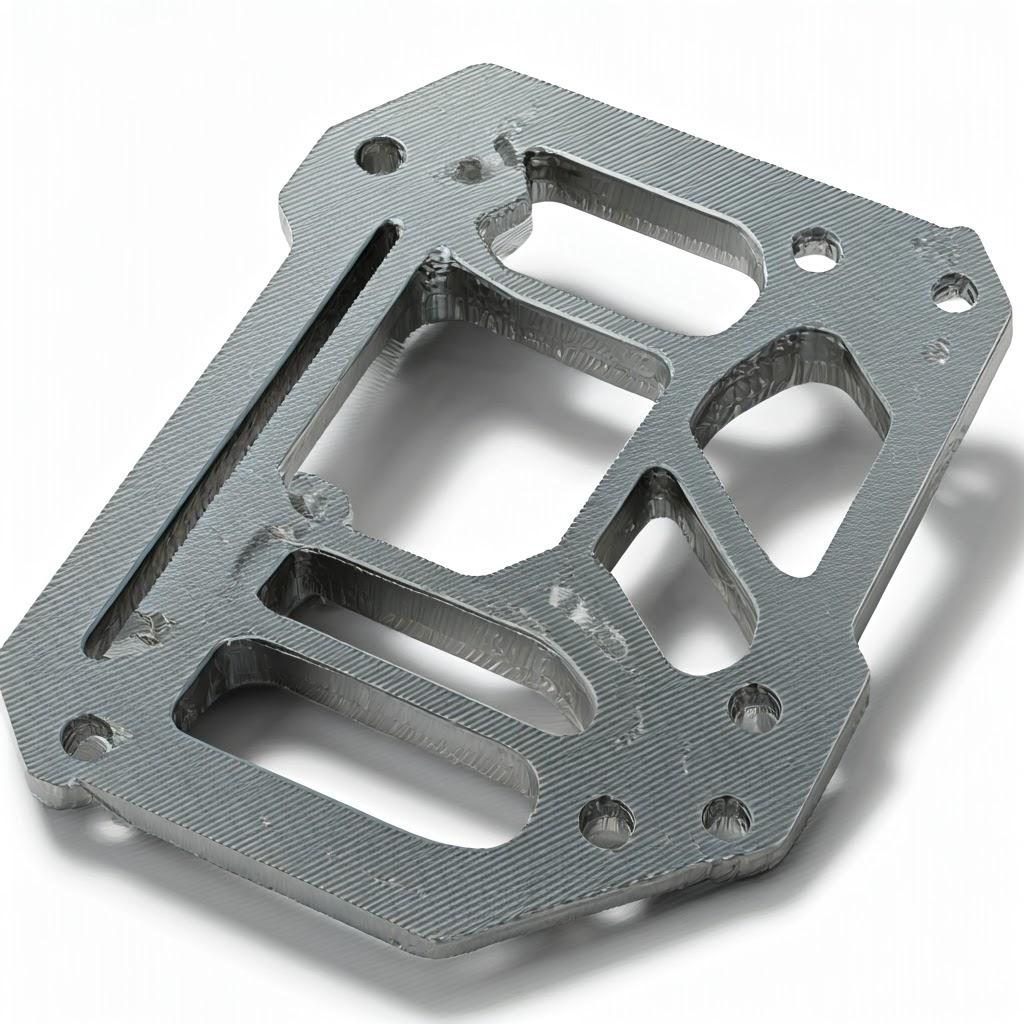
La materia prima importa: Selección de polvos de AlSi10Mg y A7075 para un rendimiento óptimo de los soportes
El éxito de un soporte de automoción impreso en 3D depende de forma crítica de la selección del material adecuado. Si bien la fabricación aditiva de metales ofrece compatibilidad con una gama creciente de aleaciones, las aleaciones de aluminio son especialmente atractivas para las aplicaciones de automoción debido a su naturaleza inherentemente ligera. Dentro de esta categoría, el AlSi10Mg destaca como un caballo de batalla, pero comprender sus características junto con alternativas potenciales como el A7075 es crucial para los ingenieros que diseñan piezas y los especialistas en compras que buscan materiales o servicios. La elección afecta a la imprimibilidad, el rendimiento mecánico, los requisitos de posprocesamiento y, en última instancia, la rentabilidad del componente final.
AlSi10Mg: El estándar versátil
- Composición: Principalmente aluminio (Al), con aproximadamente un 9-11% de silicio (Si) y un 0,2-0,45% de magnesio (Mg). También están presentes cantidades traza de otros elementos como hierro (Fe), manganeso (Mn) y titanio (Ti).
- Propiedades y características clave:
- Excelente imprimibilidad: El AlSi10Mg es una de las aleaciones de aluminio más procesables en los sistemas de fusión por lecho de polvo láser (L-PBF) como SLM/DMLS. Su naturaleza eutéctica conduce a una buena estabilidad del baño de fusión y a una menor susceptibilidad a las grietas durante los ciclos rápidos de calentamiento y enfriamiento inherentes a la fabricación aditiva.
- Buena relación resistencia-peso: Aunque no es la aleación de aluminio más resistente, ofrece un equilibrio favorable, adecuado para una amplia gama de aplicaciones de soportes estructurales y semiestructurales donde se esperan cargas moderadas.
- Alta conductividad térmica: Beneficioso para los soportes que pueden necesitar disipar el calor, como los que están cerca de los componentes del motor o de la electrónica de potencia.
- Buena resistencia a la corrosión: Adecuado para muchos entornos automovilísticos.
- Soldabilidad: Puede soldarse, aunque se recomiendan procedimientos específicos.
- Tratable térmicamente: El AlSi10Mg tal como se imprime tiene una resistencia moderada. Un tratamiento térmico T6 (solubilización seguida de envejecimiento artificial) aumenta significativamente su resistencia a la tracción, su límite elástico y su dureza, lo que lo hace comparable a las aleaciones de aluminio fundido como la A360.
- Ventajas para los soportes de automoción:
- Ideal para geometrías complejas habilitadas por la fabricación aditiva debido a su excelente imprimibilidad.
- Adecuado para iniciativas de aligeramiento en las que la resistencia extrema no es el principal impulsor.
- Rentable en comparación con las aleaciones de aluminio de mayor resistencia o el titanio.
- Material bien conocido con parámetros de impresión y protocolos de posprocesamiento establecidos.
- Consideraciones:
- Menor resistencia a la fatiga en comparación con las aleaciones forjadas como la A7075.
- Las propiedades mecánicas pueden ser anisótropas (dependientes de la dirección) en función de la orientación de la construcción.
- Requiere impresión en atmósfera controlada (normalmente argón) para evitar la oxidación.
- El tratamiento térmico T6 es generalmente necesario para un rendimiento óptimo en aplicaciones estructurales.
A7075: El contendiente de alta resistencia
- Composición: Una aleación de aluminio-zinc (Zn ~5,1-6,1%), que también contiene magnesio (Mg ~2,1-2,9%) y cobre (Cu ~1,2-2,0%).
- Propiedades y características clave:
- Muy alta resistencia: Una de las aleaciones de aluminio disponibles comercialmente de mayor resistencia, que se acerca a la resistencia de algunos aceros dulces, pero con aproximadamente un tercio de la densidad. Excelente resistencia a la tracción y al límite elástico, especialmente después del tratamiento térmico (por ejemplo, T6).
- Buena resistencia a la fatiga: Rendimiento a la fatiga significativamente mejor que el del AlSi10Mg, lo que lo hace adecuado para componentes sometidos a carga cíclica.
- Buena maquinabilidad: Puede mecanizarse fácilmente después de la impresión si es necesario.
- Menor imprimibilidad: Más difícil de procesar de forma fiable mediante L-PBF en comparación con el AlSi10Mg. Susceptible a la fisuración por solidificación y a la porosidad debido a su mayor rango de solidificación y a la vaporización de elementos de bajo punto de ebullición como el zinc bajo el láser. Requiere parámetros cuidadosamente optimizados y, posiblemente, equipos especializados.
- Menor resistencia a la corrosión: Especialmente susceptible a la fisuración por corrosión bajo tensión (SCC) en comparación con el AlSi10Mg. Puede requerir recubrimientos protectores.
- Mala soldabilidad: Generalmente se considera difícil de soldar.
- Ventajas para los soportes de automoción:
- Adecuado para soportes estructurales muy cargados donde la máxima resistencia y resistencia a la fatiga son críticas (por ejemplo, puntos de suspensión críticos, soportes de motor de alto rendimiento).
- Permite un mayor ahorro de peso en aplicaciones críticas para la resistencia en comparación con el AlSi10Mg, ya que podría necesitarse menos material.
- Consideraciones:
- Significativamente más difícil y potencialmente más costoso de imprimir de forma fiable.
- Requiere un control preciso de los parámetros de impresión y de la atmósfera.
- La susceptibilidad a defectos como la porosidad y las grietas necesita una gestión cuidadosa mediante el control del proceso y, posiblemente, el prensado isostático en caliente (HIP).
- Requiere un tratamiento térmico adecuado (por ejemplo, T6) para alcanzar su alto potencial de resistencia.
- A menudo son necesarias medidas de protección contra la corrosión.
Comparación de propiedades de los materiales (Valores típicos después del tratamiento térmico adecuado):
Propiedad | AlSi10Mg (condición T6) | A7075 (Condición T6) | Unidades | Notas |
---|---|---|---|---|
Densidad | ~2.67 | ~2.81 | g/cm³ | Ambas son aleaciones de aluminio ligeras. |
Resistencia a la tracción | 330 – 430 | 510 – 570 | MPa | A7075 significativamente más fuerte. Los valores de la fabricación aditiva pueden variar. |
Límite elástico (0,2%) | 230 – 320 | 450 – 500 | MPa | A7075 tiene una resistencia a la fluencia mucho mayor. |
Alargamiento a la rotura | 3 – 10 | 5 – 11 | % | La ductilidad puede ser menor en las piezas de fabricación aditiva frente a las forjadas/fundidas. |
Dureza | 90 – 120 | 140 – 150 | HV / HB | A7075 es más duro. |
Resistencia a la fatiga (R=-1) | 90 – 130 | 150 – 160 | MPa | A7075 generalmente superior bajo carga cíclica. Muy dependiente del acabado superficial. |
Conductividad térmica | 130 – 150 | 130 – 150 | W/(m-K) | Conductividad térmica similar. |
Imprimibilidad | Excelente | Desafío | – | Consideración principal del proceso. |
Resistencia a la corrosión | Bien | Regular (Susceptible a la SCC) | – | AlSi10Mg generalmente mejor en entornos corrosivos. |
Coste relativo (Polvo) | Baja | Más alto | – | El polvo de A7075 suele ser más caro. |
Coste relativo (Impresión) | Baja | Más alto | – | Debido a un control de parámetros más estricto, tasas de éxito potencialmente más bajas. |
Exportar a hojas
La importancia de la calidad del polvo: Ventaja de Met3dp
Independientemente de la aleación elegida, la calidad de la materia prima en polvo metálico es primordial para una fabricación aditiva exitosa y repetible. Las características del polvo influyen directamente en la fluidez en el sistema de recubrimiento, la densidad del lecho de polvo, el comportamiento del baño de fusión y, en última instancia, las propiedades mecánicas y los niveles de defectos en el soporte impreso final.
Met3dp aprovecha las tecnologías de producción de polvo líderes del sector:
- Atomización avanzada con gas: Nuestros sistemas utilizan diseños patentados de boquillas y flujo de gas para producir polvos metálicos con alta esfericidad (redondez) y distribuciones de tamaño de partícula estrechas. La alta esfericidad garantiza una excelente fluidez del polvo, lo que conduce a capas de polvo uniformes durante la impresión.
- Proceso de Electrodo Rotatorio de Plasma (PREP): Para ciertas aleaciones reactivas o de alto rendimiento, PREP puede producir polvos excepcionalmente limpios con una esfericidad aún mayor y un mínimo de partículas satélite.
Este enfoque en polvos metálicos de alta calidad, incluido el AlSi10Mg optimizado, garantiza que los clientes B2B de Met3dp, ya sea que compren polvos directamente o utilicen nuestros servicios de impresión, se beneficien de:
- Calidad de impresión constante: El comportamiento fiable del material conduce a propiedades de las piezas y precisión dimensional predecibles.
- Reducción de defectos: Los polvos esféricos de alta pureza minimizan problemas como la porosidad que pueden comprometer la integridad del soporte
- Rendimiento mecánico óptimo: La calidad constante del polvo se traduce en el logro de las especificaciones mecánicas deseadas en los componentes finales tratados térmicamente T6.
Tomando la decisión correcta para las necesidades B2B:
Para los gerentes de compras y los equipos de ingeniería que evalúan materiales para soportes automotrices impresos en 3D:
- AlSi10Mg es la opción predeterminada para una amplia gama de aplicaciones debido a su excelente capacidad de impresión, buenas propiedades generales y rentabilidad. Es ideal para la creación de prototipos, geometrías complejas, aligeramiento de estructuras no críticas y producción de bajo a mediano volumen donde su resistencia es suficiente.
- A7075 debe considerarse para aplicaciones muy exigentes que requieran la máxima resistencia y resistencia a la fatiga, siempre que se aborden los desafíos de la capacidad de impresión y la posible necesidad de protección contra la corrosión. Es más adecuado para piezas de bajo volumen y alto rendimiento donde sus propiedades mecánicas superiores justifican la mayor complejidad y costo del procesamiento.
La asociación con un proveedor experto como Met3dp, con experiencia tanto en ciencia de materiales como en procesamiento AM, es crucial. Podemos ayudar a los clientes B2B a seleccionar el polvo óptimo, ya sea AlSi10Mg estándar, alternativas de alta resistencia o incluso aleaciones personalizadas de nuestra extensa cartera (incluidos TiNi, TiTa, TiAl, CoCrMo, aceros inoxidables, etc.), lo que garantiza que el material elegido cumpla con el rendimiento específico, los requisitos de costo y producción para sus aplicaciones de soporte automotriz.
Diseño para la fabricación aditiva (DfAM): Optimización de soportes automotrices para el éxito de la impresión 3D
Simplemente tomar un diseño de soporte destinado a la fundición o el mecanizado y enviarlo a una impresora 3D de metal rara vez es el enfoque óptimo. Para aprovechar verdaderamente el poder de la fabricación aditiva y lograr resultados exitosos y rentables con los soportes automotrices AlSi10Mg, los ingenieros deben adoptar el Diseño para la fabricación aditiva (DfAM). DfAM no es solo un conjunto de reglas; es un cambio de mentalidad, que se centra en aprovechar las capacidades únicas de la fabricación capa por capa al tiempo que mitiga sus limitaciones inherentes. La aplicación de los principios de DfAM desde el principio es crucial para maximizar el potencial de aligeramiento, minimizar el tiempo y el costo de impresión, reducir el esfuerzo de posprocesamiento y garantizar la integridad estructural y la funcionalidad del componente final. Para los proveedores y fabricantes de equipos originales (OEM) automotrices B2B, dominar DfAM es clave para desbloquear las ventajas competitivas que ofrece AM de metal.
Por qué DfAM no es negociable para AM de metal:
A diferencia de la fabricación sustractiva (mecanizado) que elimina material o los procesos formativos (fundición, forja) que dan forma al material utilizando moldes o matrices, la fabricación aditiva construye piezas capa por capa desde cero. Esta diferencia fundamental introduce consideraciones específicas:
- Gravedad y voladizos: Cada nueva capa debe ser soportada por la capa que está debajo. Los voladizos pronunciados o las características horizontales requieren estructuras de soporte, que consumen material adicional, agregan tiempo de impresión y requieren eliminación en el posprocesamiento.
- Tensiones térmicas: El intenso calor del láser o del haz de electrones seguido de un enfriamiento rápido crea gradientes térmicos significativos y tensiones internas dentro de la pieza durante la construcción. Las malas elecciones de diseño pueden exacerbar estas tensiones, lo que lleva a deformaciones, distorsiones o incluso agrietamiento.
- Anisotropía: La construcción por capas puede conducir a propiedades mecánicas dependientes de la dirección (anisotropía). La resistencia y la ductilidad de una pieza de AlSi10Mg podrían diferir según si se carga paralela o perpendicularmente a las capas de construcción.
- Acabado superficial: La naturaleza inherente de la fusión de capas de polvo da como resultado una rugosidad superficial característica, que varía según la orientación de la superficie en relación con la dirección de construcción.
- Resolución de características: El tamaño del punto láser, el tamaño de las partículas de polvo y el grosor de la capa limitan el tamaño mínimo de las características (paredes, orificios, pasadores) que se pueden producir con precisión.
Principios clave de DfAM para soportes automotrices AlSi10Mg:
La aplicación de estos principios durante la fase de diseño, a menudo con el apoyo de proveedores de servicios AM experimentados como Met3dp, es fundamental:
- Orientación de construcción estratégica:
- Impacto: La orientación del soporte en la placa de construcción afecta significativamente las necesidades de soporte, la calidad del acabado de la superficie en diferentes caras, la posible anisotropía, el tiempo de construcción (la altura afecta más al tiempo) y la distribución de la tensión térmica.
- Estrategias:
- Minimice la altura Z (altura de construcción) para reducir el tiempo de impresión.
- Oriente las superficies críticas verticalmente o como "pieles superiores" (superficies orientadas hacia arriba) para un mejor acabado. Las "pieles inferiores" (superficies orientadas hacia abajo soportadas por polvo o soportes) tienden a ser más ásperas.
- Alinee las características críticas con el plano X-Y para una mejor precisión dimensional.
- Considere las condiciones de carga para orientar las capas favorablemente en relación con las direcciones de tensión primarias, aunque AlSi10Mg generalmente exhibe una anisotropía menos severa que algunos otros materiales AM después del tratamiento térmico adecuado.
- Utilice herramientas de simulación para predecir tensiones térmicas y distorsiones para diferentes orientaciones.
- Minimización y optimización de la estructura de soporte:
- Necesidad: Los soportes son cruciales para anclar la pieza a la placa de construcción, soportar voladizos que exceden un cierto ángulo (típicamente >45° desde la horizontal para AlSi10Mg) y conducir el calor lejos de áreas críticas para evitar el sobrecalentamiento y el colapso.
- Estrategias:
- Diseñar ángulos autosoportados: Siempre que sea posible, diseñe características con ángulos menores o iguales a 45° en relación con la placa de construcción. El chaflanado de los bordes en lugar de usar voladizos horizontales afilados es una técnica común.
- Optimizar los voladizos: Si los voladizos son inevitables, intente mantenerlos cortos o use nervaduras/características de sacrificio diseñadas para una fácil extracción.
- Tipos de soporte: Utilice software para generar estructuras de soporte apropiadas (por ejemplo, bloques, conos, soportes de árbol) que proporcionen un anclaje adecuado y disipación de calor al tiempo que minimizan el uso de material y los puntos de contacto con la superficie de la pieza. Los soportes perforados o enrejados pueden ahorrar material y facilitar la extracción.
- Accesibilidad: Diseñe la pieza de modo que las estructuras de soporte sean de fácil acceso para su extracción utilizando métodos manuales o de mecanizado. Evite los soportes en canales internos profundos a menos que sea absolutamente necesario y esté planificado.
- Grosor de pared adecuado:
- Espesor mínimo: Los procesos L-PBF tienen limitaciones en el grosor mínimo de pared imprimible, típicamente alrededor de 0,4-0,5 mm para AlSi10Mg, aunque a menudo se recomiendan 0,8-1,0 mm para mayor robustez.
- Integridad estructural: Asegúrese de que las paredes sean lo suficientemente gruesas para soportar las cargas esperadas, considerando las posibles concentraciones de tensión.
- Gestión térmica: Evite las secciones sólidas excesivamente gruesas, ya que estas pueden acumular calor y aumentar la tensión residual y la distorsión. Considere el uso de enrejados internos o estructuras huecas para secciones gruesas si la resistencia lo permite.
- Consideraciones de diseño de orificios:
- Orificios verticales: Generalmente se imprimen con precisión con un buen acabado superficial.
- Orificios horizontales: Propenso a la deformación (hundimiento en la parte superior) debido al voladizo. Diseñarlos con forma de "gota de lágrima" o diamante hace que la superficie superior sea autosoportante.
- Diámetro mínimo: Los orificios pequeños (típicamente < 0,5 mm) pueden ser difíciles de imprimir con precisión y sin polvo. A menudo es mejor diseñar orificios más pequeños ligeramente subdimensionados y perforarlos o escariarlos al tamaño final durante el posprocesamiento.
- Orificios roscados: Diseñe orificios destinados a roscar ligeramente subdimensionados para permitir un corte limpio de la rosca durante el mecanizado posterior a la impresión. La impresión directa de roscas es posible, pero a menudo da como resultado una calidad y resistencia deficientes.
- Aprovechando la optimización topológica y las estructuras de enrejado:
- Optimización de la topología: Utilice software especializado (por ejemplo, Altair Inspire, nTopology, Ansys Discovery) para definir casos de carga, restricciones y espacios de diseño. El software luego elimina iterativamente el material de áreas no críticas, generando diseños de soporte de apariencia orgánica y altamente eficientes optimizados para la relación rigidez-peso. Esta es una fortaleza fundamental de AM.
- Estructuras reticulares: Reemplace los volúmenes sólidos con estructuras de enrejado internas (por ejemplo, cúbicas, de armadura de octeto) para reducir drásticamente el peso al tiempo que mantiene un soporte estructural significativo o adapta las propiedades de amortiguación de vibraciones. Las herramientas de software facilitan la creación de enrejados complejos.
- Beneficios para los soportes: Ideal para los objetivos de aligeramiento automotriz, creando soportes de alto rendimiento que cumplen con los estrictos objetivos de peso sin comprometer la resistencia.
- Adoptando la consolidación de piezas:
- Concepto: Busque activamente oportunidades para rediseñar conjuntos que consisten en múltiples soportes, sujetadores y conectores en un solo componente AM integrado.
- Ejemplos: Integración de un canal de fluido directamente en un soporte de montaje, combinación de dos soportes entrelazados en una sola pieza, incorporación de encajes a presión o salientes de montaje directamente en la estructura.
- Proceso: Requiere repensar la función de todo el conjunto, no solo de las piezas individuales. La colaboración entre los ingenieros de diseño y los especialistas en AM suele ser beneficiosa.
- Gestión de las concentraciones de tensión:
- Fileteado: Agregue filetes generosos (bordes redondeados) a las esquinas internas y las transiciones bruscas en la geometría. Las esquinas afiladas actúan como concentradores de tensión, lo que aumenta el riesgo de agrietamiento durante la impresión o falla por fatiga durante el servicio.
- Transiciones suaves: Evite los cambios bruscos en el área de la sección transversal, que también pueden concentrar la tensión y causar problemas térmicos durante la impresión.
- Diseño para la disipación de calor:
- Gestión térmica: Considere cómo se acumulará y disipará el calor durante la impresión. Las características muy finas y delicadas pueden sobrecalentarse. Agregar pequeñas características de sacrificio u optimizar la orientación a veces puede ayudar a conducir el calor de manera más efectiva. Los soportes también juegan un papel crucial en la gestión del calor.
El papel de Met3dp en DfAM:
La implementación exitosa de DfAM requiere experiencia. Met3dp apoya a sus clientes B2B no solo con impresoras avanzadas y polvos de alta calidad, sino también a través de servicios de desarrollo de aplicaciones. Nuestro equipo, con décadas de experiencia colectiva, puede brindar una guía crucial sobre los principios de DfAM, ayudando a optimizar los diseños de soportes automotrices para la fabricación aditiva, garantizando el rendimiento funcional, la rentabilidad y la capacidad de fabricación. Ayudamos a cerrar la brecha entre el pensamiento de diseño tradicional y las posibilidades de AM.
Al adoptar estas estrategias de DfAM, los ingenieros automotrices y los especialistas en adquisiciones pueden garantizar que están explotando plenamente el potencial de la impresión 3D de metal AlSi10Mg, lo que resulta en soportes automotrices superiores, más ligeros y producidos de manera más eficiente.
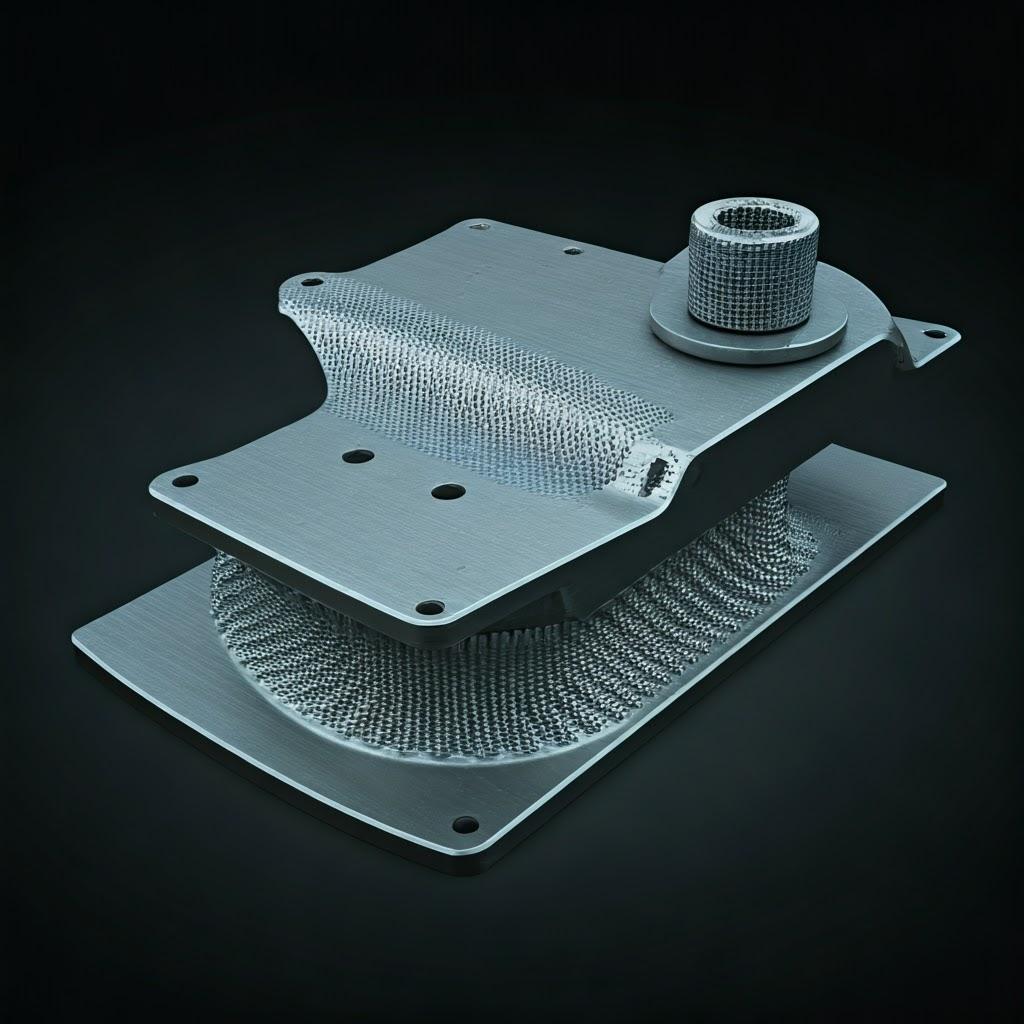
Lograr la precisión: comprensión de la tolerancia, el acabado de la superficie y la precisión dimensional en los soportes impresos
Si bien la fabricación aditiva de metales ofrece una libertad de diseño sin precedentes, lograr los altos niveles de precisión que a menudo se requieren para los componentes automotrices exige una comprensión clara de las tolerancias, el acabado de la superficie y la precisión dimensional inherentes al proceso, específicamente L-PBF para AlSi10Mg. Los ingenieros deben diseñar teniendo en cuenta estos factores, y los gerentes de adquisiciones necesitan expectativas realistas al especificar los requisitos para los soportes impresos en 3D. Es crucial reconocer tanto las capacidades como las limitaciones del estado tal como se imprime y planificar el posprocesamiento cuando se necesitan especificaciones más estrictas.
Factores que influyen en la precisión en L-PBF:
Varios elementos interactúan para determinar la precisión y el acabado final de una pieza impresa:
- Calibración de la máquina: La calibración regular de los láseres, escáneres (galvanómetros) y sistemas de movimiento de la impresora es esencial para la precisión.
- Tamaño del punto láser y grosor de la capa: Los puntos láser más finos y las capas más delgadas generalmente permiten una mayor resolución y un mejor acabado de la superficie en las superficies anguladas, pero aumentan el tiempo de construcción. Los espesores de capa típicos para AlSi10Mg oscilan entre 30 y 60 micras.
- Estrategia de escaneo: El patrón utilizado por el láser para fundir el polvo (por ejemplo, sombreado, contornos) afecta el acabado de la superficie, la tensión residual y la microestructura.
- Efectos térmicos: La contracción se produce a medida que el material fundido se enfría y se solidifica. El enfriamiento no uniforme conduce a tensiones residuales, que pueden causar deformaciones y distorsiones, lo que afecta la precisión dimensional general, especialmente en piezas más grandes o aquellas con variaciones significativas en la sección transversal. El calentamiento de la placa de construcción y los ciclos de alivio de tensión ayudan a mitigar esto.
- Características del polvo: La distribución del tamaño de las partículas, la forma (esfericidad) y la fluidez influyen en la densidad del lecho de polvo y el comportamiento de fusión, lo que afecta el acabado de la superficie y la porosidad interna.
- Geometría y tamaño de la pieza: Las piezas más grandes y las geometrías más complejas son generalmente más susceptibles a la distorsión térmica.
- Orientación de construcción: Afecta el acabado de la superficie de manera diferente en varias caras y puede influir en la estabilidad dimensional debido a la contracción anisotrópica y las interacciones de soporte.
Precisión dimensional y tolerancias:
- Tolerancias generales: Para piezas de AlSi10Mg producidas a través de L-PBF en máquinas industriales bien calibradas como las que ofrece Met3dp, las tolerancias dimensionales típicas alcanzables a menudo se citan en el rango de:
- ± 0,1 mm a ± 0,2 mm para características más pequeñas (por ejemplo, hasta 50-100 mm)
- ± 0,1 % a ± 0,2 % de la dimensión nominal para características más grandes.
- Comparación: Este nivel de precisión es generalmente mejor que la fundición en arena o la fundición a la cera perdida en el estado tal como se funde, pero menos preciso que el mecanizado CNC.
- Consideraciones clave:
- Dimensiones críticas: Las tolerancias no son uniformes en toda la pieza. Lograr las tolerancias más estrictas generalmente requiere mecanizado posterior en características críticas (por ejemplo, superficies de acoplamiento, orificios de cojinetes, ubicaciones precisas de orificios).
- Impacto de la deformación: La deformación general de la pieza debido a la tensión
- Medición: La verificación precisa requiere equipos de metrología sofisticados, como máquinas de medición por coordenadas (MMC) o escáneres 3D de alta resolución.
Acabado superficial (rugosidad):
- Acabado tal como se construyó: L-PBF produce piezas con una rugosidad superficial característica resultante de las partículas de polvo parcialmente fundidas que se adhieren a la superficie y la construcción por capas (efecto de escalonamiento en superficies anguladas).
- Valores Ra típicos: La rugosidad superficial (Ra – rugosidad media aritmética) para piezas de AlSi10Mg tal como se construyen suele oscilar entre 8 µm y 20 µm (micrómetros).
- Dependencia de la orientación:
- Paredes verticales (paralelas a la dirección de construcción): Tienden a tener el mejor acabado dentro del rango típico.
- Up-Skins (Superficies orientadas hacia arriba): Generalmente más suaves que las down-skins, a menudo hacia el extremo inferior del rango Ra.
- Down-Skins (Superficies orientadas hacia abajo): Tienden a ser más rugosas debido a la interacción con polvo suelto o estructuras de soporte, a menudo hacia el extremo superior del rango Ra o ligeramente por encima.
- Superficies anguladas: Exhiben el efecto de "escalonamiento", con una rugosidad que aumenta a medida que el ángulo se acerca a la horizontal.
- Áreas Soportadas: Las superficies donde se fijaron las estructuras de soporte mostrarán marcas o cicatrices después de la eliminación, lo que requerirá un acabado adicional si la suavidad es fundamental.
- Comparación: El acabado tal como se construyó es significativamente más rugoso que las superficies mecanizadas o pulidas, pero puede ser comparable o mejor que algunos acabados de fundición.
- Mejora del acabado superficial: Si se requiere un acabado más suave por razones funcionales (por ejemplo, flujo de fluidos, vida útil a la fatiga, estética) o requisitos de tolerancia, son necesarios métodos de postprocesamiento.
Lograr Especificaciones Más Estrictas:
Para los soportes automotrices que requieren tolerancias más estrictas que ±0,1-0,2 mm o acabados superficiales más suaves que Ra 8-10 µm en características específicas, el postprocesamiento es esencial:
- Diseño para Mecanizado: El enfoque más común es diseñar la pieza de fabricación aditiva con material adicional (tolerancia de mecanizado, típicamente 0,5-2 mm) en superficies críticas. Estas superficies se mecanizan luego con CNC para lograr las dimensiones, tolerancias y acabado superficial finales requeridos (capaces de alcanzar Ra < 1 µm).
- Técnicas de acabado de superficies: Métodos como el granallado con perlas, el volteo o el pulido pueden mejorar el acabado superficial general, pero típicamente no mejoran significativamente la precisión dimensional a grandes distancias. Son efectivos para eliminar el polvo suelto, mejorar la estética y potencialmente mejorar el rendimiento a la fatiga mediante la introducción de tensión de compresión (granallado con perlas).
Control de Calidad e Inspección:
Asegurar que los soportes cumplan con la precisión especificada requiere un control de calidad robusto:
- Inspección dimensional: Los CMM proporcionan mediciones de puntos de alta precisión para verificar dimensiones críticas, ubicaciones de orificios y dimensionamiento y tolerancias geométricas (GD&T). El escaneo 3D ofrece una captura rápida de la geometría general de la pieza para compararla con el modelo CAD, útil para identificar deformaciones o desviaciones mayores.
- Medición de la rugosidad superficial: Los perfilómetros se utilizan para cuantificar la rugosidad de la superficie (Ra, Rz, etc.) en áreas específicas.
- Integridad Interna: Para los soportes altamente críticos, se puede emplear el escaneo CT (tomografía computarizada) de forma no destructiva para inspeccionar defectos internos como la porosidad y verificar la geometría de los canales internos o las características complejas.
Compromiso de Met3dp con la precisión:
Met3dp comprende la importancia de la precisión en las aplicaciones industriales. Nuestras impresoras 3D de metal están diseñadas para la precisión y la fiabilidad, incorporando características diseñadas para mantener la estabilidad térmica y el control preciso del láser. Hacemos hincapié en la calibración rigurosa y el control del proceso. Además, nuestro enfoque integral incluye asesorar a los clientes sobre las tolerancias alcanzables, los pasos de postprocesamiento necesarios y las medidas adecuadas de garantía de calidad para garantizar que los soportes finales de AlSi10Mg cumplan con los exigentes requisitos de la industria automotriz. La asociación con proveedores B2B experimentados que priorizan el control de calidad es esencial para los gerentes de adquisiciones que buscan componentes de fabricación aditiva de precisión.
Tabla de Especificaciones de Precisión:
Parámetro | Como Fabricado L-PBF (AlSi10Mg) | Mecanizado CNC Típico | Fundición de Inversión Típica | Fundición a Presión Típica |
---|---|---|---|---|
Tol. Dimensional | ±0,1 a ±0,2 mm / ±0,1-0,2% | ±0,01 a ±0,05 mm | ±0,1 a ±0,4 mm | ±0,05 a ±0,2 mm |
Acabado superficial (Ra) | 8 – 20 µm | < 0,8 µm (fino) a 3,2 µm (estándar) | 1,6 – 6,3 µm | 0,8 – 3,2 µm |
Exportar a hojas
Nota: Los valores son típicos y pueden variar significativamente según el tamaño de la pieza, la geometría, los controles específicos del proceso y el postprocesamiento.
Al comprender estas capacidades y limitaciones, los diseñadores pueden crear dibujos con tolerancias apropiadas para las características impresas frente a las mecanizadas, y las adquisiciones pueden obtener piezas con confianza, sabiendo cuándo especificar pasos de acabado adicionales para cumplir con los requisitos de la aplicación.
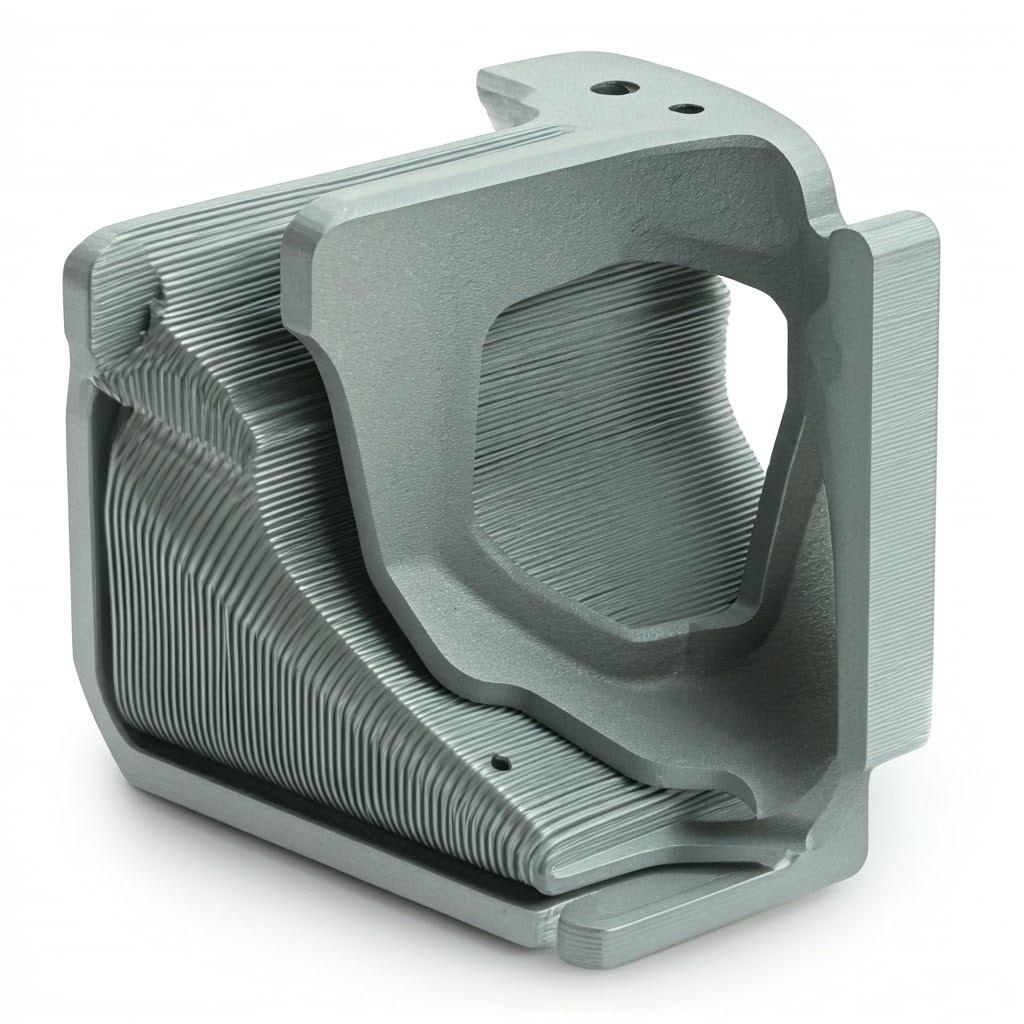
Más allá de la impresión: Pasos esenciales de postprocesamiento para soportes automotrices de AlSi10Mg
La creación de un soporte automotriz de AlSi10Mg utilizando la Fusión de lecho de polvo láser (L-PBF) es un proceso sofisticado, pero el viaje desde el archivo digital hasta el componente funcional no termina cuando la impresora se detiene. Normalmente, se requiere una serie de pasos cruciales de postprocesamiento para transformar la pieza en bruto, tal como se imprimió, en un producto terminado que cumpla con los estrictos estándares automotrices de rendimiento mecánico, precisión dimensional, calidad de la superficie y durabilidad. Comprender este flujo de trabajo es vital para los ingenieros que planifican la producción y para los gerentes de adquisiciones que contabilizan el tiempo de entrega y el costo totales al obtener piezas de metal impresas en 3D.
La cadena de postprocesamiento específica puede variar según la complejidad del soporte, su aplicación prevista y las especificaciones requeridas. Sin embargo, una secuencia típica para piezas estructurales de AlSi10Mg implica varias etapas clave:
Flujo de trabajo típico de postprocesamiento para soportes de AlSi10Mg L-PBF:
- Alivio de tensión (Opcional pero recomendado):
- Propósito: Para reducir las altas tensiones residuales internas acumuladas durante los ciclos rápidos de calentamiento y enfriamiento del proceso L-PBF. Estas tensiones pueden causar distorsión o agrietamiento cuando la pieza se retira de la placa de construcción.
- Procedimiento: Normalmente se realiza mientras la pieza aún está adherida a la placa de construcción en un horno de atmósfera controlada (generalmente argón para evitar la oxidación). El conjunto se calienta a una temperatura moderada (por ejemplo, 200-300 °C para AlSi10Mg), se mantiene durante un período (por ejemplo, 1-2 horas) y luego se enfría lentamente.
- Ventajas: Mejora la estabilidad dimensional después de la extracción de la placa, reduce el riesgo de agrietamiento.
- Extracción de la pieza de la placa de montaje:
- Propósito: Para separar los soportes impresos de la placa de construcción de metal a la que se fusionaron.
- Métodos: Comúnmente se hace usando electroerosión por hilo (EDM por hilo) o una sierra de cinta. La electroerosión por hilo proporciona un corte más limpio con un estrés mecánico mínimo, pero es más lento. El aserrado es más rápido, pero puede requerir el mecanizado posterior de la superficie base.
- Consideraciones: Requiere una manipulación cuidadosa para evitar dañar las piezas.
- Eliminación de polvo (Desempolvado):
- Propósito: Para eliminar cualquier polvo no fusionado atrapado dentro de los canales internos, cavidades o estructuras de soporte densamente empaquetadas.
- Métodos: Típicamente implica chorro de aire comprimido, cepillado manual y, a veces, baños de limpieza ultrasónica. La eliminación completa del polvo es fundamental, ya que el polvo atrapado puede comprometer el rendimiento o contaminar los procesos posteriores (como el tratamiento térmico).
- Desafíos: Las geometrías internas complejas pueden dificultar la eliminación completa del polvo. Los principios de DfAM (por ejemplo, el diseño de orificios de drenaje) pueden facilitar este paso.
- Retirada de la estructura de soporte:
- Propósito: Para eliminar las estructuras de soporte temporales requeridas durante el proceso de construcción.
- Métodos: Dependiendo del tipo y la ubicación de los soportes, la eliminación puede implicar:
- Rotura manual: Soportes fácilmente rompibles diseñados con interfaces de baja densidad.
- Herramientas manuales: Alicates, amoladoras, limas para soportes más resistentes.
- Mecanizado: Operaciones de fresado o rectificado, especialmente para soportes de bloque o áreas de contacto grandes.
- Electroerosión por hilo: Para la eliminación precisa de soportes en áreas delicadas.
- Desafíos: Puede requerir mucha mano de obra y tiempo. Riesgo de dañar la superficie de la pieza en los puntos de contacto del soporte. La accesibilidad planificada durante DfAM es clave. Las superficies donde se fijaron los soportes a menudo requieren un acabado adicional.
- Tratamiento térmico (Condición T6 - Crucial para AlSi10Mg):
- Propósito: Para mejorar significativamente las propiedades mecánicas (resistencia, dureza, ductilidad) del soporte de AlSi10Mg. La microestructura tal como se imprimió tiene una resistencia moderada; el tratamiento T6 la optimiza para aplicaciones estructurales.
- Procedimiento: Un proceso de varias etapas realizado en hornos calibrados de atmósfera controlada:
- Recocido de soluciones: Calentar la pieza a una temperatura alta (por ejemplo, ~515-540 °C) durante un período específico (por ejemplo, 1-6 horas, según el grosor de la pieza) para disolver los precipitados de Mg₂Si presentes en la matriz de aluminio en una solución sólida.
- Enfriamiento: Enfriar rápidamente la pieza (típicamente en agua o agente de enfriamiento de polímero) para "congelar" los elementos disueltos en la solución sólida sobresaturada. La velocidad de enfriamiento es crítica.
- Envejecimiento artificial (Endurecimiento por precipitación): Volver a calentar la pieza a una temperatura más baja (por ejemplo, ~160-180 °C) y mantenerla durante varias horas (por ejemplo, 4-12 horas). Esto permite la precipitación controlada de finas partículas de Mg₂Si en toda la matriz de aluminio, lo que impide el movimiento de dislocaciones y aumenta significativamente la resistencia y la dureza.
- Ventajas: Transforma el AlSi10Mg de un material de resistencia moderada a uno comparable a las aleaciones de fundición tradicionales, lo que lo hace adecuado para cargas automotrices exigentes.
- Consideraciones: Requiere un control preciso de la temperatura y la gestión de la atmósfera (argón o vacío) para evitar la oxidación y garantizar propiedades uniformes. Las piezas pueden distorsionarse ligeramente durante el tratamiento térmico, lo que debe tenerse en cuenta si se realiza el mecanizado.
- Prensado isostático en caliente (HIP) (Opcional):
- Propósito: Para cerrar la porosidad interna (microhuecos) que pueden estar presentes incluso en piezas bien impresas, mejorando así la vida útil a la fatiga, la ductilidad y la tenacidad a la fractura.
- Procedimiento: Las piezas se someten a alta presión (por ejemplo, 100-200 MPa) y temperatura elevada (por debajo del punto de fusión, a menudo integrado con o reemplazando el recocido de solución) en una unidad HIP especializada, utilizando típicamente gas argón como medio de presión. La presión colapsa los vacíos internos.
- Ventajas: Mejora la integridad del material, crucial para componentes altamente críticos sometidos a fatiga o estados de alta tensión. Puede mejorar la consistencia de las propiedades mecánicas.
- Consideraciones: Agrega un costo y un tiempo de entrega significativos. Típicamente reservado para aplicaciones aeroespaciales, médicas o automotrices de seguridad crítica donde los beneficios de rendimiento justifican el gasto.
- Acabado superficial:
- Propósito: Para lograr la textura superficial deseada, eliminar las marcas de testigo de soporte, mejorar la estética o preparar para el revestimiento.
- Métodos comunes para AlSi10Mg:
- Granallado abrasivo (granallado con perlas/arena): Proporciona un acabado mate, limpio y uniforme. Eficaz para eliminar el polvo suelto y mezclar imperfecciones menores de la superficie. Puede inducir tensiones residuales de compresión beneficiosas. Varios medios (perlas de vidrio, óxido de aluminio) ofrecen diferentes acabados.
- Acabado por volteo/vibración: Utiliza medios abrasivos en un recipiente giratorio o vibratorio para alisar superficies y desbarbar bordes. Adecuado para lotes de piezas más pequeñas.
- Rectificado/Pulido manual: Para requisitos específicos como acabados de espejo o alisado de radios críticos. Requiere mucha mano de obra.
- Selección: Depende de los requisitos funcionales y estéticos del soporte y de los objetivos de costo.
- Mecanizado CNC:
- Propósito: Para lograr tolerancias estrictas en características específicas, crear superficies de acoplamiento precisas, roscar o lograr acabados superficiales muy suaves cuando sea necesario.
- Procedimiento: Utiliza centros de fresado o torneado CNC tradicionales. Las piezas necesitan una fijación adecuada. Como se discutió en DfAM, se deben incluir tolerancias de mecanizado en el diseño de la pieza impresa.
- Integración: Combina la libertad geométrica de la fabricación aditiva con la precisión de la fabricación sustractiva para interfaces críticas.
- Revestimiento o tratamiento de superficies:
- Propósito: Para mejorar la resistencia a la corrosión, mejorar la resistencia al desgaste, proporcionar aislamiento eléctrico o lograr una apariencia específica (color).
- Métodos comunes para aluminio:
- Anodizado: Un proceso electroquímico que crea una capa de óxido dura y resistente a la corrosión. Se puede teñir de varios colores. Los tipos II (decorativo/corrosión) y III (capa dura) son comunes.
- Revestimiento de conversión de cromato (Alodine/Iridite): Proporciona resistencia a la corrosión y actúa como una buena imprimación para la pintura.
- Pintura/Recubrimiento en polvo: Para colores específicos y protección ambiental adicional.
- Selección: Basado en el entorno operativo y los requisitos funcionales del soporte.
Enfoque integral de Met3dp:
Met3dp reconoce que la entrega de un soporte automotriz funcional implica algo más que simplemente imprimir. Si bien nuestras principales fortalezas residen en las impresoras SEBM y L-PBF avanzadas y los polvos metálicos de primera calidad, ofrecemos soluciones integrales. Esto incluye brindar asesoramiento experto sobre los pasos de postprocesamiento necesarios y colaborar con una red de socios de confianza para servicios especializados como tratamiento térmico, HIP, mecanizado de precisión y revestimiento. Nos aseguramos de que nuestros clientes B2B reciban soporte integral, desde la optimización del diseño hasta la entrega de piezas terminadas.
Comprender este flujo de trabajo completo permite a las empresas automotrices presupuestar con precisión, planificar plazos y garantizar que los soportes finales de AlSi10Mg entregados por su proveedor de impresión de metales B2B cumplan con todas las especificaciones necesarias para una integración exitosa en sus vehículos.
Navegando por los desafíos: Superando los obstáculos en la impresión 3D de soportes automotrices
La fabricación aditiva de metales, particularmente la L-PBF de AlSi10Mg, es una tecnología poderosa, pero no está exenta de complejidades y desafíos potenciales. Ser consciente de estos obstáculos y comprender las estrategias para mitigarlos es crucial para lograr resultados consistentes y de alta calidad adecuados para aplicaciones automotrices exigentes. Los proveedores experimentados de fabricación aditiva como Met3dp invierten fuertemente en el control de procesos, la ciencia de los materiales y la experiencia en ingeniería para sortear estos problemas de manera efectiva, ofreciendo soluciones confiables a los clientes B2B. Los gerentes de adquisiciones deben asociarse con proveedores que demuestren
Áreas soportadas:
Desafío | Las superficies donde se adjuntaron estructuras de soporte mostrarán marcas o cicatrices después de la extracción, lo que requerirá un acabado adicional si la suavidad es fundamental. | El acabado tal como se construyó es significativamente más rugoso que las superficies mecanizadas o pulidas, pero puede ser comparable o mejor que algunos acabados de fundición. |
---|---|---|
Si se requiere un acabado más suave por razones funcionales (por ejemplo, flujo de fluidos, vida útil a la fatiga, estética) o requisitos de tolerancia, son necesarios métodos de posprocesamiento. | Lograr especificaciones más estrictas: | DfAM: Optimice la orientación de la pieza, minimice las áreas planas grandes paralelas a la placa, utilice la optimización de la topología para reducir el volumen. <br> Para los soportes automotrices que requieren tolerancias más estrictas que ±0,1-0,2 mm o acabados superficiales más suaves que Ra 8-10 µm en características específicas, el posprocesamiento es esencial: Estructuras de soporte robustas para anclar la pieza firmemente. <br> Control de procesos: Estrategias de escaneo optimizadas, calentamiento de la placa de construcción. <br> Post-procesamiento: Tratamiento térmico de alivio de tensión en la placa antes de retirar la pieza. <br> Simulación: Diseño para mecanizado: |
El enfoque más común es diseñar la pieza de AM con material adicional (margen de mecanizado, normalmente 0,5-2 mm) en superficies críticas. Luego, estas superficies se mecanizan con CNC para lograr las dimensiones, tolerancias y acabado superficial finales requeridos (capaces de alcanzar Ra < 1 µm). | Estructuras de soporte densas; soportes en áreas internas inaccesibles; fuerte unión entre los soportes y la pieza. | DfAM: Diseño para minimizar las necesidades de soporte (ángulos autosoportados), optimizar el tipo de soporte (por ejemplo, árbol, perforado) y las capas de interfaz para facilitar el desprendimiento, garantizar la accesibilidad para las herramientas de extracción. <br> Proceso: Utilice parámetros de soporte optimizados en el software de preparación de la construcción. <br> Métodos como el granallado, el pulido con tambor o el pulido pueden mejorar el acabado superficial general, pero normalmente no mejoran significativamente la precisión dimensional a grandes distancias. Son eficaces para eliminar el polvo suelto, mejorar la estética y, potencialmente, mejorar el rendimiento a la fatiga mediante la introducción de tensión de compresión (granallado). Control de calidad e inspección: |
Garantizar que los soportes cumplan con la precisión especificada requiere un control de calidad sólido: | Porosidad del gas: Gas disuelto (por ejemplo, hidrógeno en polvo) rechazado durante la solidificación, gas atrapado en la materia prima en polvo. <br> Porosidad del ojo de la cerradura: Las MMC proporcionan mediciones de puntos de alta precisión para verificar dimensiones críticas, ubicaciones de orificios y dimensionamiento y tolerancias geométricas (GD&T). El escaneo 3D ofrece una captura rápida de la geometría general de la pieza para compararla con el modelo CAD, útil para identificar deformaciones o desviaciones mayores. | Calidad del material: Utilice polvo esférico de alta calidad y baja atomización de gas (especialidad de Met3dp). Manipulación y almacenamiento adecuados del polvo para evitar la absorción de humedad. <br> Optimización de procesos: Parámetros láser calibrados con precisión (potencia, velocidad, distancia de escotilla), atmósfera inerte controlada (pureza del argón). <br> Post-procesamiento: Los perfilómetros se utilizan para cuantificar la rugosidad superficial (Ra, Rz, etc.) en áreas específicas. |
Integridad interna: | Para los soportes muy críticos, se puede emplear el escaneo CT (tomografía computarizada) de forma no destructiva para inspeccionar defectos internos como la porosidad y verificar la geometría de los canales internos o las características complejas. Ocurre en la zona pastosa durante la solidificación debido a que las tensiones térmicas desgarran las regiones interdentritas débiles. <br> comprende la importancia de la precisión en las aplicaciones industriales. Nuestras impresoras 3D de metal están diseñadas para brindar precisión y confiabilidad, e incorporan características diseñadas para mantener la estabilidad térmica y el control preciso del láser. Hacemos hincapié en la calibración rigurosa y el control del proceso. Además, nuestro enfoque integral incluye asesorar a los clientes sobre las tolerancias alcanzables, los pasos de posprocesamiento necesarios y las medidas adecuadas de garantía de calidad para garantizar que los soportes de AlSi10Mg finales cumplan con los exigentes requisitos de la industria automotriz. La asociación con proveedores B2B experimentados que priorizan el control de calidad es esencial para los gerentes de adquisiciones que buscan componentes de AM de precisión. Tabla de especificaciones de precisión: | Optimización de procesos: Parámetros láser y estrategias de escaneo ajustados para controlar los gradientes térmicos y las velocidades de enfriamiento. <br> DfAM: Evite las esquinas internas afiladas (use filetes), asegure transiciones suaves en la geometría. <br> Post-procesamiento: L-PBF tal como se construyó (AlSi10Mg) |
Mecanizado CNC típico | Fundición a la cera perdida típica | DfAM: Optimice la orientación de la pieza (superficies críticas verticales o de piel hacia arriba). <br> Proceso: Utilice un grosor de capa más fino (aumenta el tiempo), parámetros láser optimizados y escaneos de contorno. <br> Post-procesamiento: Fundición a presión típica |
Tensión residual | Tol. dimensional | Control de procesos: Calentamiento de la placa de construcción, estrategias de escaneo optimizadas para distribuir el calor de manera más uniforme. <br> Post-procesamiento: El tratamiento térmico de alivio de tensión (en o fuera de la placa) es muy eficaz. HIP también reduce la tensión residual. <br> DfAM: ±0,1 a ±0,2 mm / ±0,1-0,2 % |
±0,01 a ±0,05 mm | ±0,1 a ±0,4 mm | Control de calidad: Gestión estricta de la calidad del polvo, calibración y mantenimiento rigurosos de la máquina, parámetros de proceso validados/bloqueados, control preciso del tratamiento térmico (hornos calibrados, control de la atmósfera), END (por ejemplo, escaneo TC) para piezas críticas. <br> ±0,05 a ±0,2 mm 8 – 20 µm |
< 0,8 µm (fino) a 3,2 µm (estándar) | 1,6 – 6,3 µm | DfAM: Maximice el aligeramiento y la consolidación de piezas para agregar valor. Optimice la disposición de la construcción (anidamiento de múltiples piezas). <br> 0,8 – 3,2 µm Concéntrese en AM en piezas donde sus beneficios únicos (complejidad, velocidad, personalización) superan el costo: prototipos, volúmenes bajos, diseños altamente optimizados. <br> Eficiencia del proceso: Nota: Los valores son típicos y pueden variar significativamente según el tamaño de la pieza, la geometría, los controles específicos del proceso y el posprocesamiento. |
Al comprender estas capacidades y limitaciones, los diseñadores pueden crear dibujos con tolerancias apropiadas para las características impresas frente a las mecanizadas, y las adquisiciones pueden obtener piezas con confianza, sabiendo cuándo especificar pasos de acabado adicionales para cumplir con los requisitos de la aplicación. | Más allá de la impresión: Pasos esenciales de posprocesamiento para soportes automotrices de AlSi10Mg | La creación de un soporte automotriz de AlSi10Mg mediante la fusión de lecho de polvo láser (L-PBF) es un proceso sofisticado, pero el viaje desde el archivo digital hasta el componente funcional no termina cuando la impresora se detiene. Normalmente, se requiere una serie de pasos cruciales de posprocesamiento para transformar la pieza en bruto, tal como se imprime, en un producto terminado que cumpla con los estrictos estándares automotrices de rendimiento mecánico, precisión dimensional, calidad de la superficie y durabilidad. Comprender este flujo de trabajo es vital para los ingenieros que planifican la producción y para los gerentes de adquisiciones que contabilizan el tiempo de entrega y el costo totales al obtener piezas de metal impresas en 3D. Utilice AM para nichos adecuados (creación de prototipos, posventa, deportes de motor, series de bajo volumen, piezas complejas/consolidadas). <br> La cadena de posprocesamiento específica puede variar según la complejidad del soporte, su aplicación prevista y las especificaciones requeridas. Sin embargo, una secuencia típica para piezas estructurales de AlSi10Mg implica varias etapas clave: Combine AM para secciones complejas con métodos tradicionales para piezas más simples de un ensamblaje. <br> Flujo de trabajo típico de posprocesamiento para soportes de L-PBF AlSi10Mg: Alivio de tensión (Opcional pero recomendado): |
Exportar a hojas
Para reducir las altas tensiones residuales internas acumuladas durante los ciclos rápidos de calentamiento y enfriamiento del proceso L-PBF. Estas tensiones pueden causar distorsión o agrietamiento cuando la pieza se retira de la placa de construcción.
Normalmente se realiza mientras la pieza aún está adherida a la placa de construcción en un horno de atmósfera controlada (normalmente argón para evitar la oxidación). El conjunto se calienta a una temperatura moderada (por ejemplo, 200-300 °C para AlSi10Mg), se mantiene durante un período (por ejemplo, 1-2 horas) y luego se enfría lentamente.
- Ciencia de los materiales: Mejora la estabilidad dimensional después de la extracción de la placa, reduce el riesgo de agrietamiento.
- Optimización de procesos: Para separar los soportes impresos de la placa de construcción de metal a la que se fusionaron.
- Soporte de ingeniería: Comúnmente se realiza mediante mecanizado por descarga eléctrica por hilo (EDM por hilo) o una sierra de cinta. EDM por hilo proporciona un corte más limpio con una tensión mecánica mínima, pero es más lento. El aserrado es más rápido, pero puede requerir el mecanizado posterior de la superficie base.
- Requiere una manipulación cuidadosa para evitar dañar las piezas. Eliminación de polvo (Despolvoreo):
Para eliminar cualquier polvo no fusionado atrapado dentro de los canales internos, cavidades o estructuras de soporte densamente empaquetadas.
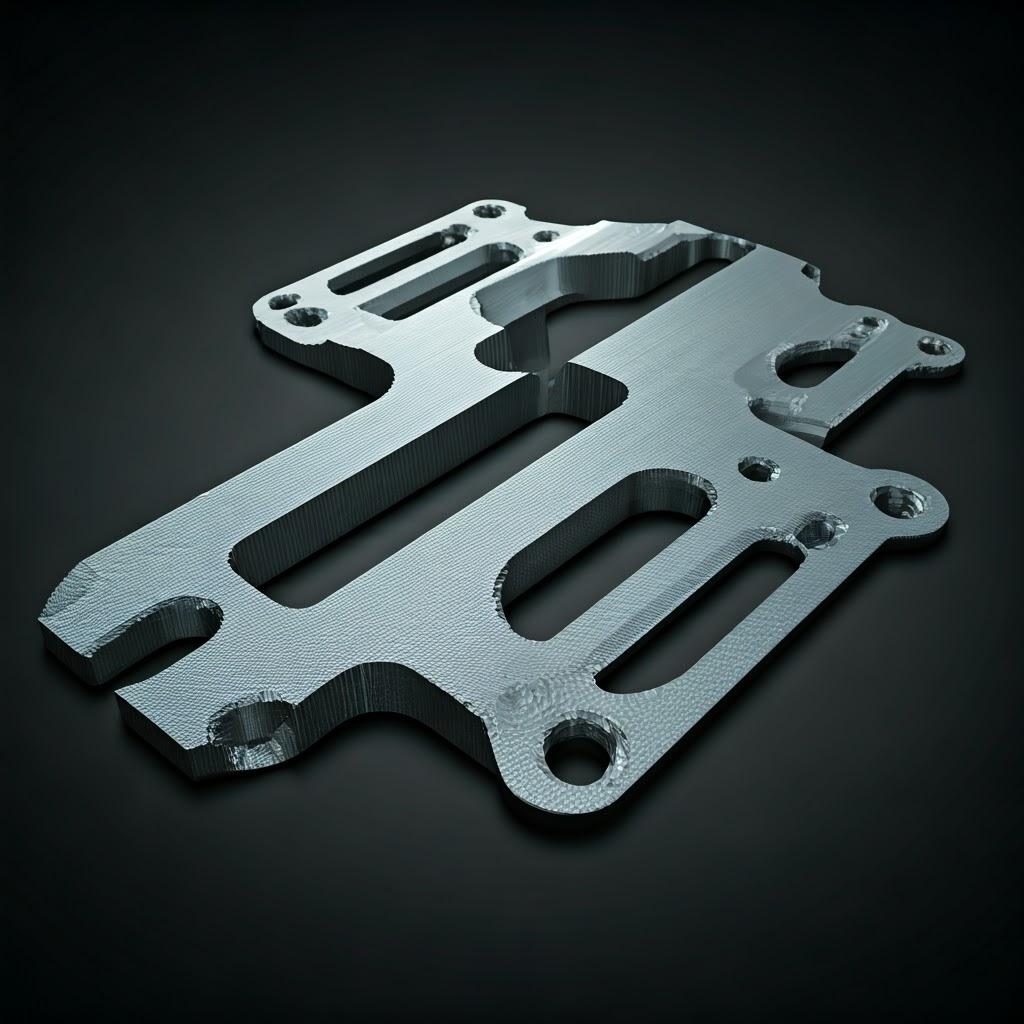
Normalmente implica granallado con aire comprimido, cepillado manual y, a veces, baños de limpieza por ultrasonidos. La eliminación completa del polvo es fundamental, ya que el polvo atrapado puede comprometer el rendimiento o contaminar los procesos posteriores (como el tratamiento térmico).
Las geometrías internas complejas pueden dificultar la eliminación completa del polvo. Los principios de DfAM (por ejemplo, el diseño de orificios de drenaje) pueden facilitar este paso.
Para eliminar las estructuras de soporte temporales necesarias durante el proceso de construcción.
- Dependiendo del tipo y la ubicación de los soportes, la extracción puede implicar: Rotura manual:
- Soportes fácilmente rompibles diseñados con interfaces de baja densidad. Herramientas manuales:
- Alicates, amoladoras, limas para soportes más resistentes. Operaciones de fresado o rectificado, especialmente para soportes de bloque o áreas de contacto grandes.
- Escalabilidad: Sus necesidades podrían evolucionar de prototipos a la producción en serie de bajo volumen. Su socio debe tener la capacidad y la infraestructura para escalar en consecuencia.
- Para la eliminación precisa de soportes en áreas delicadas. Puede requerir mucha mano de obra y tiempo. Riesgo de dañar la superficie de la pieza en los puntos de contacto de los soportes. La accesibilidad planificada durante DfAM es clave. Las superficies donde se adjuntaron los soportes a menudo requieren un acabado adicional.
Tratamiento térmico (Condición T6 – Crucial para AlSi10Mg):
Para mejorar significativamente las propiedades mecánicas (resistencia, dureza, ductilidad) del soporte de AlSi10Mg. La microestructura tal como se imprime tiene una resistencia moderada; el tratamiento T6 la optimiza para aplicaciones estructurales.
Un proceso de varias etapas realizado en hornos calibrados de atmósfera controlada: * [] Calentar la pieza a una temperatura alta (por ejemplo, ~515-540 °C) durante un período específico (por ejemplo, 1-6 horas, según el grosor de la pieza) para disolver los precipitados de Mg₂Si presentes en la matriz de aluminio en una solución sólida. Enfriar rápidamente la pieza (normalmente en agua o un agente de enfriamiento polimérico) para "congelar" los elementos disueltos en la solución sólida sobresaturada. La velocidad de enfriamiento es fundamental.] Apoyo al DfAM: Envejecimiento artificial (endurecimiento por precipitación):] Volver a calentar la pieza a una temperatura más baja (por ejemplo, ~160-180 °C) y mantenerla durante varias horas (por ejemplo, 4-12 horas). Esto permite la precipitación controlada de finas partículas de Mg₂Si en toda la matriz de aluminio, lo que impide el movimiento de las dislocaciones y aumenta significativamente la resistencia y la dureza. Transforma el AlSi10Mg de un material de resistencia moderada a uno comparable a las aleaciones de fundición tradicionales, lo que lo hace adecuado para cargas automotrices exigentes.] Requiere un control preciso de la temperatura y la gestión de la atmósfera (argón o vacío) para evitar la oxidación y garantizar propiedades uniformes. Las piezas pueden distorsionarse ligeramente durante el tratamiento térmico, lo que debe tenerse en cuenta si se realiza un mecanizado posterior. Prensado isostático en caliente (HIP) (Opcional): Para cerrar la porosidad interna (microhuecos) que podría estar presente incluso en piezas bien impresas, mejorando así la vida útil a la fatiga, la ductilidad y la tenacidad a la fractura. Las piezas se someten a alta presión (por ejemplo, 100-200 MPa) y temperatura elevada (por debajo del punto de fusión, a menudo integrado con o reemplazando el recocido de solución) en una unidad HIP especializada, normalmente utilizando gas argón como medio de presión. La presión colapsa los vacíos internos.
Mejora la integridad del material, fundamental para componentes muy críticos sometidos a fatiga o altos estados de tensión. Puede mejorar la consistencia de las propiedades mecánicas. * [] Agrega un costo y un tiempo de entrega significativos. Normalmente reservado para aplicaciones aeroespaciales, médicas o automotrices de seguridad crítica donde los beneficios de rendimiento justifican el gasto. Para lograr la textura superficial deseada, eliminar las marcas de testigos de soporte, mejorar la estética o preparar para el revestimiento.] Construir volumen: Métodos comunes para AlSi10Mg:] Calibración y mantenimiento de la máquina: Granallado abrasivo (granallado con perlas/arena):] Proporciona un acabado mate, limpio y uniforme. Eficaz para eliminar el polvo suelto y mezclar imperfecciones menores de la superficie. Puede inducir tensiones residuales de compresión beneficiosas. Varios medios (perlas de vidrio, óxido de aluminio) ofrecen diferentes acabados. Utiliza medios abrasivos en un recipiente giratorio o vibratorio para alisar superficies y desbarbar bordes. Adecuado para lotes de piezas más pequeñas.
Rectificado/pulido manual: * [] Portafolio de materiales: Para requisitos específicos como acabados de espejo o alisado de radios críticos. Requiere mucha mano de obra.] Selección: Depende de los requisitos funcionales y estéticos del soporte y de los objetivos de costos. Para lograr tolerancias ajustadas en características específicas, crear superficies de acoplamiento precisas, roscar o lograr acabados superficiales muy suaves cuando sea necesario. Utiliza centros de fresado o torneado CNC tradicionales. Las piezas necesitan una fijación adecuada. Como se analizó en DfAM, se deben incluir márgenes de mecanizado en el diseño de la pieza impresa.
Integración: * [] Interno vs. Subcontratado: Combina la libertad geométrica de AM con la precisión de la fabricación sustractiva para interfaces críticas.] Revestimiento o tratamiento de superficies: Para mejorar la resistencia a la corrosión, mejorar la resistencia al desgaste, proporcionar aislamiento eléctrico o lograr una apariencia específica (color).] Métodos comunes para aluminio: Anodizado:] Flujo de trabajo integrado: Un proceso electroquímico que crea una capa de óxido dura y resistente a la corrosión. Se puede teñir de varios colores. Los tipos II (decorativo/corrosión) y III (recubrimiento duro) son comunes.
Revestimiento de conversión de cromato (Alodine/Iridite): * [] Certificaciones: Proporciona resistencia a la corrosión y actúa como una buena imprimación para la pintura.] Documentación y trazabilidad: Pintura/recubrimiento en polvo:] Capacidad de inspección: Para colores específicos y protección ambiental adicional.] Control de procesos: Basado en el entorno operativo y los requisitos funcionales del soporte.
Enfoque integral de Met3dp: * [] Met3dp reconoce que la entrega de un soporte automotriz funcional implica algo más que la impresión. Si bien nuestras principales fortalezas residen en las impresoras SEBM y Suficiente capacidad de la máquina para manejar los volúmenes actuales y proyectados sin plazos de entrega excesivos. * [] Eficiencia operativa: Operaciones de múltiples turnos, planificación de construcción optimizada, flujos de trabajo eficientes. * [_] Potencial de crecimiento: Capacidad demostrada o planes para escalar las operaciones para satisfacer la creciente demanda de clientes B2B.
7. Plazos de entrega y capacidad de respuesta: * [] Velocidad de cotización: Capacidad para proporcionar cotizaciones precisas y oportunas. * [] Plazos de entrega indicados: Estimaciones realistas y fiables para las diferentes etapas de producción (prototipo frente a serie, diferentes niveles de post-procesamiento). * [_] Comunicación: Comunicación clara y proactiva con respecto al estado del proyecto, los posibles problemas y los plazos de entrega. ¿Gestores de proyectos dedicados?
8. Competitividad de costes: * [] Precios transparentes: Desglose claro de los costes (material, tiempo de máquina, mano de obra, post-procesamiento). * [] Propuesta de valor: Centrarse en el valor global (calidad, fiabilidad, experiencia, soporte) en lugar de únicamente en el precio unitario más bajo. ¿Son competitivos para el nivel de servicio ofrecido?
9. Ubicación y logística: * [] Ubicación geográfica: La proximidad podría ser un factor para reducir los tiempos de envío o facilitar la colaboración, pero la experiencia a menudo supera la ubicación. * [] Experiencia en envíos: Capacidad demostrada para embalar las piezas de forma segura y gestionar los envíos nacionales o internacionales de forma eficaz.
10. Atención al cliente y colaboración: * [] Asistencia técnica: Disponibilidad de ingenieros para responder a preguntas y proporcionar asistencia técnica. * [] Enfoque Colaborativo: Disposición a trabajar como socio, sugiriendo mejoras y resolviendo retos juntos. * [_] Visión a largo plazo: Interés en construir una relación B2B a largo plazo en lugar de solo pedidos transaccionales.
Por qué Met3dp destaca como su socio de AM para automoción:
Met3dp se distingue como un proveedor líder de fabricación aditiva B2B, que se alinea firmemente con estos criterios de selección críticos:
- Profunda experiencia: Décadas de experiencia colectiva centrada específicamente en la AM de metales, desde la producción de polvo hasta la ingeniería de aplicaciones.
- Soluciones integradas: Ofrecemos una cartera completa: impresoras avanzadas SEBM y L-PBF, polvos metálicos de alto rendimiento (incluidos AlSi10Mg, aleaciones de Ti, superaleaciones, etc.) fabricados internamente utilizando tecnologías de vanguardia de atomización por gas y PREP, y servicios expertos de desarrollo de aplicaciones.
- Enfoque en la calidad: Nuestro compromiso con la calidad comienza con el polvo y se extiende a través de un riguroso control de procesos en nuestras impresoras líderes en la industria, lo que garantiza la fiabilidad y la repetibilidad para piezas de misión crítica.
- Liderazgo tecnológico: Invertimos continuamente en I+D tanto para materiales como para equipos para proporcionar soluciones de última generación.
- Asociación colaborativa: Trabajamos en estrecha colaboración con nuestros clientes de automoción, proporcionando soporte DfAM y adaptando soluciones para satisfacer necesidades específicas, fomentando las transformaciones de la fabricación digital.
Elegir un proveedor es una decisión estratégica. Al evaluar cuidadosamente a los socios potenciales en función de estos criterios, las empresas de automoción pueden seleccionar con confianza a un proveedor como Met3dp que ofrece la destreza técnica, la garantía de calidad y el espíritu de colaboración necesarios para tener éxito en la implementación de soportes impresos en 3D de AlSi10Mg.
Análisis de costes y plazos de entrega: Factores que influyen en los plazos y presupuestos de producción de soportes de AlSi10Mg
La transición a la fabricación aditiva para soportes de automoción requiere una comprensión clara de los costes y los plazos de entrega asociados. A diferencia de los métodos tradicionales dominados por las inversiones en herramientas, los precios de la AM de metales se basan principalmente en el consumo de material, la utilización de la máquina y la extensión del post-procesamiento requerido. Para los gestores de compras que construyen presupuestos y los ingenieros que planifican los plazos de los proyectos, comprender estos factores es esencial para una estimación precisa y una contratación B2B eficaz.
Factores de coste para los soportes de automoción de AlSi10Mg impresos en 3D:
El precio final de un soporte impreso es una agregación de varios factores contribuyentes:
- Consumo de material:
- Volumen de la pieza: El volumen neto del diseño final del soporte.
- Volumen de la estructura de soporte: Material utilizado para los soportes, que se retira posteriormente. DfAM optimizado minimiza esto.
- Coste del polvo: El precio por kilogramo de polvo de AlSi10Mg de grado AM. Aunque es moderado en comparación con el titanio o las superaleaciones de níquel, es significativamente más caro que el lingote de fundición a granel. La calidad y la consistencia del polvo influyen en el coste.
- Eficiencia de reciclaje: La capacidad del proveedor para reciclar eficazmente el polvo no fusionado afecta al coste total del material atribuido a la pieza.
- Tiempo de máquina (utilización):
- Altura de construcción (altura Z): El principal impulsor del tiempo de impresión. Las piezas más altas tardan más, independientemente de su huella dentro de los límites. La optimización de la orientación es clave.
- Volumen de piezas y complejidad: Un mayor volumen y características intrincadas requieren más tiempo de escaneo láser por capa.
- Embalaje de la cámara de construcción: La impresión de múltiples piezas simultáneamente (anidamiento) utiliza el tiempo de la máquina de forma más eficiente, lo que reduce el coste por pieza asignado. Los proveedores suelen optimizar las construcciones de esta manera.
- Tasa de la máquina: Una tarifa por hora que refleja la amortización de la costosa máquina L-PBF, el mantenimiento, el consumo de energía, el uso de gas inerte y los gastos generales de las instalaciones.
- Costes laborales:
- Configuración de la construcción: Preparación del archivo de construcción (orientación, soportes, corte), carga de polvo, configuración de la máquina.
- Supervisión: Supervisión del proceso de impresión (a menudo mínimo para procesos estables).
- Retirada de piezas y despolvoreado: Mano de obra involucrada en sacar la pieza de la placa y limpiar el polvo suelto.
- Retirada del soporte: Puede ser un coste de mano de obra significativo, especialmente para piezas complejas o soportes mal diseñados.
- Acabado e inspección: Mano de obra manual para el acabado de la superficie, el funcionamiento de la MMC, la inspección visual, etc.
- Costes de postprocesamiento:
- Alivio de tensiones/tratamiento térmico: Tiempo de horno, consumo de energía, costes de atmósfera controlada. El tratamiento T6 para AlSi10Mg es esencial para las propiedades, pero añade costes.
- Prensado isostático en caliente (HIP): Un proceso especializado y relativamente caro, que añade un coste significativo si es necesario para la eliminación de la porosidad.
- Mecanizado CNC: Coste basado en el tiempo de máquina, las herramientas, la programación y la mano de obra necesarios para lograr tolerancias ajustadas o características específicas.
- Acabado superficial: Costes asociados al granallado, el volteo y el pulido (mano de obra, medios, tiempo de equipo).
- Recubrimiento/Anodizado: Costes de proveedores externos si no se realizan internamente.
- Aseguramiento de la calidad e inspección:
- El tiempo dedicado a las comprobaciones dimensionales (MMC, escaneo), las mediciones de la rugosidad de la superficie, la documentación y cualquier prueba NDT o de materiales requerida se suma al coste.
- Servicios de diseño e ingeniería (si procede):
- Si el proveedor proporciona consultoría DfAM, servicios de optimización de la topología o soporte de ingeniería significativo, esto puede tenerse en cuenta en el coste total del proyecto.
- Cantidad del pedido:
- Aunque la AM evita los costes de las herramientas, existen algunas economías de escala. Las cantidades más altas permiten una mejor utilización de la cámara de construcción y la amortización de los costes de configuración en más piezas, lo que lleva a un precio unitario más bajo en comparación con los pedidos de una sola pieza. Sin embargo, la curva de reducción de costes se aplana mucho más rápido que con los métodos tradicionales de alto volumen.
Desglose del plazo de entrega de los soportes de AlSi10Mg:
El plazo de entrega es a menudo una ventaja crítica de la AM, especialmente para prototipos y bajos volúmenes, pero es importante comprender las etapas que contribuyen:
Escenario | Duración típica | Factores clave que influyen |
---|---|---|
Cotización | Pocas horas - 2 días laborables | Complejidad de la solicitud, carga de trabajo del proveedor, claridad de la información proporcionada. |
Tramitación de pedidos y preparación de la construcción | 0,5 - 2 días laborables | Comprobaciones de archivos, revisión DfAM (si es necesario), generación de soporte, planificación de la disposición de la construcción. |
Impresión (L-PBF) | 1 - 5+ días | La altura de la pieza (altura Z) es dominante. Volumen de la pieza, complejidad, cantidad por construcción. |
Enfriamiento y despolvoreado | 0,5 - 1 día laborable | Tiempo de enfriamiento de la máquina, complejidad de la pieza (canales internos). |
El alivio del estrés | 0,5 - 1 día laborable | Tiempo de ciclo del horno (normalmente varias horas + enfriamiento). |
Retirada de piezas y soportes | 0,5 - 2+ días laborables | Tamaño de la pieza, complejidad del soporte, método de retirada (sierra, EDM, manual). |
Tratamiento térmico (T6) | 1 - 2 días laborables | Tiempo de ciclo del horno (la solución + el enfriamiento + el envejecimiento tarda >12-24 horas), programación por lotes. |
HIP (si es necesario) | 3 - 10 días laborables | Proceso especializado, a menudo subcontratado, programación por lotes. |
Mecanizado CNC | 2 - 10+ días laborables | Complejidad de las características, número de configuraciones, disponibilidad de la máquina, horarios de subcontratación. |
Acabado de superficies | 1 - 5 días laborables | Método utilizado, tamaño del lote, nivel de acabado requerido. |
Inspección y control de calidad | 0,5 - 2 días laborables | Nivel de inspección requerido (visual, MMC, escaneo), necesidades de documentación. |
Embalaje y envío | 1 - 5+ días laborables | Método de envío, destino (nacional/internacional). |
Exportar a hojas
Plazos de entrega generales estimados:
- Prototipos rápidos (tal como se imprimen o con acabado básico, post-proceso mínimo): Aproximadamente 5 - 12 días laborables.
- Prototipos funcionales / Bajo volumen (con tratamiento térmico, acabado básico): Aproximadamente 2 – 4 semanas.
- Piezas de producción (post-procesamiento completo, incluyendo mecanizado/recubrimiento): Aproximadamente 3 - 6+ semanas.
Lo más importante: Aunque la AM elimina semanas o meses de plazo de entrega de las herramientas asociadas con el fundido o el estampado, la impresión y el extenso post-procesamiento requerido significan que los plazos de entrega de las piezas de AM de metal totalmente acabadas se miden en semanas, no normalmente en días (a menos que se trate de piezas muy simples y sin terminar). Sin embargo, esto sigue siendo significativamente más rápido que las rutas tradicionales de herramientas para las piezas iniciales y los bajos volúmenes.
Enfoque de Met3dp en cuanto a costes y plazos de entrega:
Met3dp tiene como objetivo proporcionar precios claros y competitivos y estimaciones realistas de los plazos de entrega para los clientes B2B. Nuestras capacidades integradas, desde la producción de polvo de alta calidad hasta la impresión avanzada y las sólidas asociaciones de post-procesamiento, ayudan a agilizar el flujo de trabajo. Trabajamos con los clientes para comprender sus requisitos específicos y proporcionar presupuestos transparentes que reflejen los pasos necesarios para lograr la calidad y el rendimiento deseados para sus soportes de automoción de AlSi10Mg. La comprensión de estas dinámicas de costes y tiempo permite a los equipos de compras e ingeniería integrar eficazmente la AM de metales en sus estrategias de planificación y aprovisionamiento de proyectos.
Preguntas frecuentes (FAQ) sobre los soportes de automoción de AlSi10Mg impresos en 3D
Aquí tiene las respuestas a algunas preguntas comunes que los ingenieros y gestores de compras se plantean al considerar la impresión 3D de metales con AlSi10Mg para soportes de automoción:
1. ¿Es el AlSi10Mg impreso en 3D lo suficientemente resistente para los soportes estructurales de automoción?
Sí, en muchos casos. Cuando se procesa y se trata térmicamente correctamente a una condición T6, el AlSi10Mg impreso por L-PBF exhibe propiedades mecánicas (resistencia a la tracción, límite elástico) comparables a las aleaciones de fundición de aluminio comúnmente utilizadas como A360 o A356. Esto lo hace adecuado para una amplia gama de soportes estructurales y semiestructurales con carga moderada donde el aligeramiento es un objetivo clave.
- Consideraciones clave:
- Tratamiento térmico T6: Este paso es crucial para lograr una resistencia óptima. Las propiedades tal como se imprimen son significativamente más bajas.
- Diseño (DfAM): El uso de la optimización de la topología y el análisis de elementos finitos (FEA) garantiza que el diseño del soporte utilice eficazmente la resistencia y la rigidez del material donde sea necesario.
- Comparación: Generalmente no es tan resistente como las aleaciones de aluminio forjado de alta resistencia (como A7075) o los aceros. Para aplicaciones extremadamente exigentes o críticas para la fatiga, podría ser necesario un material o método de fabricación diferente. Siempre se recomienda la validación FEA para piezas estructurales críticas.
- Experiencia de Met3dp: Los proveedores como Met
2. ¿Cómo se compara el coste de un soporte de AlSi10Mg impreso en 3D con uno fundido o mecanizado?
La comparación de costes depende en gran medida del volumen, la complejidad y los requisitos de plazo de entrega:
- Prototipos y volúmenes muy bajos (<50 unidades): La impresión 3D es a menudo más rentable porque evita por completo los elevados costes iniciales de los moldes de fundición o las matrices de estampación (que pueden ascender a decenas o cientos de miles de dólares). El mecanizado de prototipos a partir de palanquilla puede ser comparable o más caro que la FA, dependiendo de la complejidad.
- Volúmenes bajos a medios (50 – 1000 unidades): La comparación se vuelve matizada. Los costes unitarios de la FA disminuyen lentamente con el volumen, mientras que los costes de fundición/estampación bajan significativamente una vez amortizado el utillaje. Los costes de mecanizado siguen siendo relativamente altos por pieza. La FA puede ser competitiva si la geometría del soporte es muy compleja (difícil/costoso de fundir o mecanizar) o si la consolidación de piezas lograda a través de la FA reduce los costes de montaje.
- Grandes volúmenes (más de 10.000 unidades): Los métodos tradicionales como la fundición a presión o el estampado son casi siempre significativamente más baratos por pieza debido a las economías de escala, a pesar de la inversión inicial en utillaje.
- Factores de valor: El valor de la FA suele residir más allá de la comparación directa de costes unitarios, teniendo en cuenta la reducción de los plazos de entrega para el desarrollo, lo que permite diseños complejos/ligeros de otro modo imposibles, y facilitando la producción o personalización bajo demanda.
3. ¿Qué información necesito proporcionar para obtener un presupuesto preciso para un soporte impreso en 3D?
Para garantizar un presupuesto preciso y puntual de un proveedor de servicios de FA de metales como Met3dp, debe proporcionar la mayor cantidad posible de la siguiente información:
- Modelo CAD en 3D: Un modelo 3D de alta calidad en un formato estándar (por ejemplo, se prefiere STEP, STP; STL también es común). Asegúrese de que el modelo sea estanco y represente la geometría final deseada.
- Especificación del material: Indique claramente "AlSi10Mg". Especifique la condición final deseada (por ejemplo, "Tratado térmicamente T6").
- Dibujos 2D (muy recomendables): Proporcione dibujos técnicos que indiquen claramente:
- Dimensiones y tolerancias críticas (utilizando símbolos GD&T).
- Requisitos específicos de acabado superficial (valores Ra) para toda la pieza o caras críticas.
- Ubicaciones para cualquier mecanizado, roscado u otras características específicas necesarias.
- Cualquier ensayo no destructivo (END) o requisitos de inspección específicos.
- Cantidad: Número de soportes necesarios. Indique si se trata de un prototipo único o de un posible pedido recurrente.
- Post-procesamiento necesario: Enumere todos los pasos necesarios más allá de la impresión (por ejemplo, alivio de tensiones, tratamiento térmico T6, granallado, operaciones de mecanizado específicas, tipo/color de anodizado).
- Fecha de entrega requerida: Su calendario objetivo.
- Contexto de la aplicación (opcional, pero útil): Describir brevemente la función del soporte y el entorno operativo puede ayudar al proveedor a proporcionar una mejor retroalimentación de DfAM o asesoramiento sobre materiales.
- Información de contacto: Su nombre, empresa, correo electrónico y número de teléfono.
4. ¿Se pueden imprimir y limpiar de forma fiable canales internos o características internas complejas?
Sí, la creación de características internas complejas es una gran ventaja de la FA de metales. Sin embargo, la ejecución exitosa requiere un diseño y un procesamiento cuidadosos:
- DfAM para características internas: Los canales necesitan un diámetro mínimo (normalmente >1-2 mm) para permitir que el polvo no fusionado escape durante el despolvoreado. Diseñe curvas suaves en lugar de esquinas afiladas. Incluya puertos de acceso si la red de canales es muy compleja. Considere formas de canal autoportantes siempre que sea posible.
- Eliminación del polvo: El despolvoreado a fondo mediante aire comprimido, vibración y, posiblemente, limpieza por ultrasonidos es esencial. El proveedor debe tener procedimientos sólidos.
- Verificación: Para aplicaciones críticas, la tomografía computarizada puede verificar de forma no destructiva que los canales internos están limpios y coinciden con la geometría prevista.
- Capacidad del proveedor: Discuta sus requisitos específicos de características internas con posibles proveedores como Met3dp para confirmar su capacidad de imprimir y limpiar dichas geometrías de forma eficaz.
Tener respuestas claras a estas preguntas ayuda a los profesionales de la automoción a tomar decisiones informadas sobre la adopción de la impresión 3D de AlSi10Mg y a relacionarse eficazmente con los proveedores B2B.
Conclusión: Impulsando la innovación en automoción con las soluciones de fabricación aditiva de AlSi10Mg de Met3dp
El impulso de la industria automovilística hacia vehículos más ligeros, rápidos y eficientes exige una innovación continua tanto en el diseño como en la fabricación. La fabricación aditiva de metales, en particular el uso de materiales versátiles y fiables como el AlSi10Mg, representa un importante paso adelante, ya que ofrece potentes herramientas para afrontar estos retos de frente. Como hemos explorado, la impresión 3D de soportes de automoción de AlSi10Mg proporciona una vía convincente para lograr geometrías complejas, reducciones sustanciales de peso mediante la optimización topológica y la consolidación de piezas, y ciclos de desarrollo drásticamente acelerados al eliminar las limitaciones de utillaje tradicionales para prototipos y producción de bajo volumen.
Sin embargo, la implementación exitosa de esta tecnología requiere algo más que el acceso a una impresora. Exige un enfoque holístico que abarque los principios expertos de Diseño para la Fabricación Aditiva (DfAM), una profunda comprensión de las propiedades de los materiales y el papel crucial del post-procesamiento como el tratamiento térmico T6, una meticulosa atención a la precisión y el control de calidad, y una selección estratégica de proveedores. Navegar por los posibles retos de la FA de metales, desde la gestión de las tensiones térmicas hasta la garantía de la calidad del polvo, exige asociarse con un proveedor que posea una amplia experiencia y procesos sólidos.
Met3dp es un socio B2B de primer nivel para las empresas de automoción que buscan aprovechar el poder transformador de la fabricación aditiva de metales. Nuestras soluciones integrales abarcan todo el ecosistema de la FA:
- Equipos avanzados: Impresoras L-PBF y SEBM líderes en la industria, diseñadas para la precisión, la fiabilidad y la producción industrial.
- Materiales de alto rendimiento: Producción interna de polvos metálicos de calidad superior, incluido el AlSi10Mg, utilizando tecnologías de atomización por gas y PREP de última generación, lo que garantiza la consistencia y un rendimiento óptimo. Nuestra cartera se extiende a aleaciones innovadoras como TiNi, TiTa, TiAl, CoCrMo, aceros inoxidables y superaleaciones.
- Décadas de experiencia: Nuestro equipo posee un profundo conocimiento colectivo en ciencia de materiales, optimización de procesos de FA, desarrollo de aplicaciones y garantía de calidad, lo que nos permite abordar retos complejos y ofrecer componentes de misión crítica.
- Soporte integral: Colaboramos estrechamente con los clientes, ofreciendo orientación DfAM, gestionando los requisitos de post-procesamiento y garantizando que las piezas cumplen las estrictas especificaciones, facilitando sus transformaciones de fabricación digital.
Tanto si es un ingeniero que busca aligerar un soporte crítico, consolidar un montaje o crear rápidamente un prototipo de un nuevo diseño, como si es un responsable de compras que busca un proveedor B2B fiable y de alta calidad para la fabricación aditiva de bajo a medio volumen, Met3dp tiene la capacidad y la experiencia para ayudarle a tener éxito.
Dé el siguiente paso en la innovación automotriz.
Explore el potencial de la impresión 3D de metal AlSi10Mg para sus aplicaciones de soportes automotrices. Póngase en contacto con Met3dp hoy mismo para:
- Discutir los requisitos específicos de su proyecto con nuestros ingenieros de aplicaciones.
- Solicitar un presupuesto para el diseño de su soporte.
- Obtener más información sobre nuestra completa gama de polvos metálicos y servicios de fabricación aditiva.
Asóciese con Met3dp y acelere su viaje hacia la fabricación de vehículos de última generación.
Compartir
MET3DP Technology Co., LTD es un proveedor líder de soluciones de fabricación aditiva con sede en Qingdao, China. Nuestra empresa está especializada en equipos de impresión 3D y polvos metálicos de alto rendimiento para aplicaciones industriales.
Solicite información para obtener el mejor precio y una solución personalizada para su empresa.
Artículos relacionados
Acerca de Met3DP
Actualización reciente
Nuestro producto
CONTACTO
¿Tiene alguna pregunta? ¡Envíenos un mensaje ahora! Atenderemos su solicitud con todo un equipo tras recibir su mensaje.
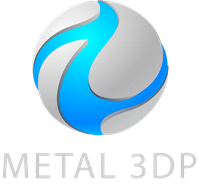
Polvos metálicos para impresión 3D y fabricación aditiva