Precisión y biocompatibilidad: Aprovechamiento de la impresión metálica en 3D para marcos de sensores biomédicos
Índice
El panorama de la tecnología médica evoluciona constantemente, impulsado por la búsqueda incesante de diagnósticos más precisos, tratamientos personalizados y un mejor seguimiento de los pacientes. En el corazón de muchos dispositivos médicos innovadores se encuentran sensores sofisticados, capaces de detectar cambios fisiológicos sutiles, transmitir datos vitales y permitir intervenciones oportunas. Sin embargo, la eficacia de estos sensores depende a menudo de la precisión, estabilidad y biocompatibilidad de las estructuras que los rodean, es decir, los marcos que los alojan, protegen y posicionan. Tradicionalmente, la fabricación de estos intrincados armazones requería complejos procesos de mecanizado o moldeado, a menudo limitados por restricciones geométricas, opciones de materiales y plazos de producción. Hoy en día, la fabricación aditiva (AM) de metales, conocida comúnmente como Impresión 3Destá revolucionando la forma de diseñar y producir estos componentes críticos, ofreciendo ventajas sin precedentes a ingenieros, diseñadores y fabricantes de dispositivos médicos. Este artículo se adentra en el mundo de los marcos de sensores biomédicos impresos en 3D, explorando sus aplicaciones, las razones de peso para adoptar la AM metálica y el papel crucial de la selección de materiales para garantizar la seguridad y el rendimiento.
Introducción: El papel fundamental de los marcos en la tecnología de detección biomédica
Los sensores biomédicos son los héroes anónimos de la medicina moderna. Desde el control de los niveles de glucosa en pacientes diabéticos hasta el seguimiento del ritmo cardíaco mediante dispositivos implantables o la utilización de herramientas quirúrgicas mínimamente invasivas, estos sensores proporcionan datos críticos en tiempo real que sirven de base para el diagnóstico y orientan el tratamiento. Un sensor biomédico es, en esencia, una estructura de ingeniería que desempeña varias funciones vitales:
- Vivienda y protección: Envuelve los delicados elementos sensores, protegiéndolos de daños físicos, fluidos corporales y factores ambientales que podrían comprometer su funcionamiento o longevidad.
- Posicionamiento y estabilidad: El marco garantiza que el sensor esté situado con precisión en relación con el tejido, órgano o fluido que se desea monitorizar. Esto es crucial para obtener lecturas precisas, especialmente en entornos dinámicos dentro del cuerpo humano o durante el movimiento del paciente.
- Integración: A menudo facilita la integración del sensor con otros componentes, como fuentes de alimentación, unidades de transmisión de datos o el conjunto más amplio del dispositivo médico. Esto incluye proporcionar puntos de montaje seguros, canales para el cableado o características para el sellado.
- Biocompatibilidad: Para aplicaciones implantables o en contacto con el cuerpo, el material del armazón debe ser biocompatible, es decir, no provocar respuestas inmunitarias nocivas ni efectos tóxicos al interactuar con tejidos biológicos.
La demanda de dispositivos médicos más pequeños, inteligentes y personalizados está aumentando en diversos sectores sanitarios:
- Tecnología vestible: Las pulseras de fitness se han convertido en sofisticados monitores de salud capaces de controlar el ECG, la saturación de oxígeno en sangre e incluso los niveles continuos de glucosa. Los armazones de estos sensores deben ser ligeros, duraderos, respetuosos con la piel y capaces de albergar componentes electrónicos complejos en formas compactas.
- Dispositivos implantables: Marcapasos, implantes cocleares, neuroestimuladores y sistemas implantables de administración de fármacos dependen de sensores integrados en carcasas biocompatibles de alta fiabilidad, diseñadas para permanecer durante largo tiempo en el cuerpo humano. La miniaturización y la conformidad anatómica son retos fundamentales.
- Equipo de diagnóstico: Los sensores de alta precisión forman parte integral de los equipos de laboratorio, los sistemas de imagen (como los escáneres de resonancia magnética o tomografía computarizada) y las herramientas de diagnóstico en el punto de atención. Sus armazones deben garantizar la estabilidad, la precisión y, en ocasiones, la resistencia a procesos de limpieza o esterilización agresivos.
- Herramientas quirúrgicas: Los instrumentos quirúrgicos modernos incorporan cada vez más sensores para la navegación, la caracterización de tejidos o la retroalimentación de fuerza. Los armazones deben ser robustos, esterilizables y, a menudo, de formas intrincadas para encajar en herramientas mínimamente invasivas.
Cumplir los complejos requisitos geométricos, de material y de rendimiento de estas diversas aplicaciones utilizando métodos de fabricación tradicionales como el mecanizado CNC o el moldeo por inyección puede resultar difícil y costoso. El mecanizado de elementos internos intrincados o socavados es difícil, el utillaje para el moldeo es caro y requiere mucho tiempo (sobre todo para volúmenes bajos o medios o diseños personalizados), y las opciones de materiales pueden ser limitadas.
Aquí es donde la fabricación aditiva de metales emerge como un potente facilitador. Impresión 3D en metal como la fusión selectiva por láser (SLM) o la fusión por haz de electrones (EBM) -tecnologías básicas utilizadas por proveedores líderes como Met3dp- construyen piezas capa a capa directamente a partir de un modelo CAD 3D utilizando polvos metálicos de alto rendimiento. Este enfoque cambia radicalmente el paradigma del diseño y la producción, ofreciendo soluciones especialmente adaptadas a las exigencias de las estructuras de los sensores biomédicos:
- Complejidad geométrica: La AM destaca en la creación de canales internos complejos, estructuras reticulares para reducir el peso y formas orgánicas que se ajustan a la anatomía, características a menudo imposibles o prohibitivamente caras de mecanizar.
- Personalización: Las estructuras de sensores específicas para cada paciente o los dispositivos adaptados a requisitos anatómicos únicos son factibles sin necesidad de herramientas personalizadas.
- Creación rápida de prototipos: Las iteraciones de diseño pueden imprimirse y probarse rápidamente, lo que acelera drásticamente el ciclo de desarrollo de nuevos dispositivos médicos.
- Versatilidad de materiales: Los procesos de AM funcionan con una gama de metales biocompatibles como las aleaciones de titanio y los aceros inoxidables, esenciales para las aplicaciones médicas.
Como líder en AM metálica, Met3dp no sólo proporciona equipos de impresión líderes en el sector, conocidos por su precisión y fiabilidad, sino que también se especializa en la producción de polvos metálicos de alto rendimiento optimizados para estas exigentes aplicaciones. Comprender el papel fundamental de los bastidores de sensores y el potencial transformador de la AM metálica sienta las bases para explorar dónde está teniendo un impacto más significativo esta tecnología.
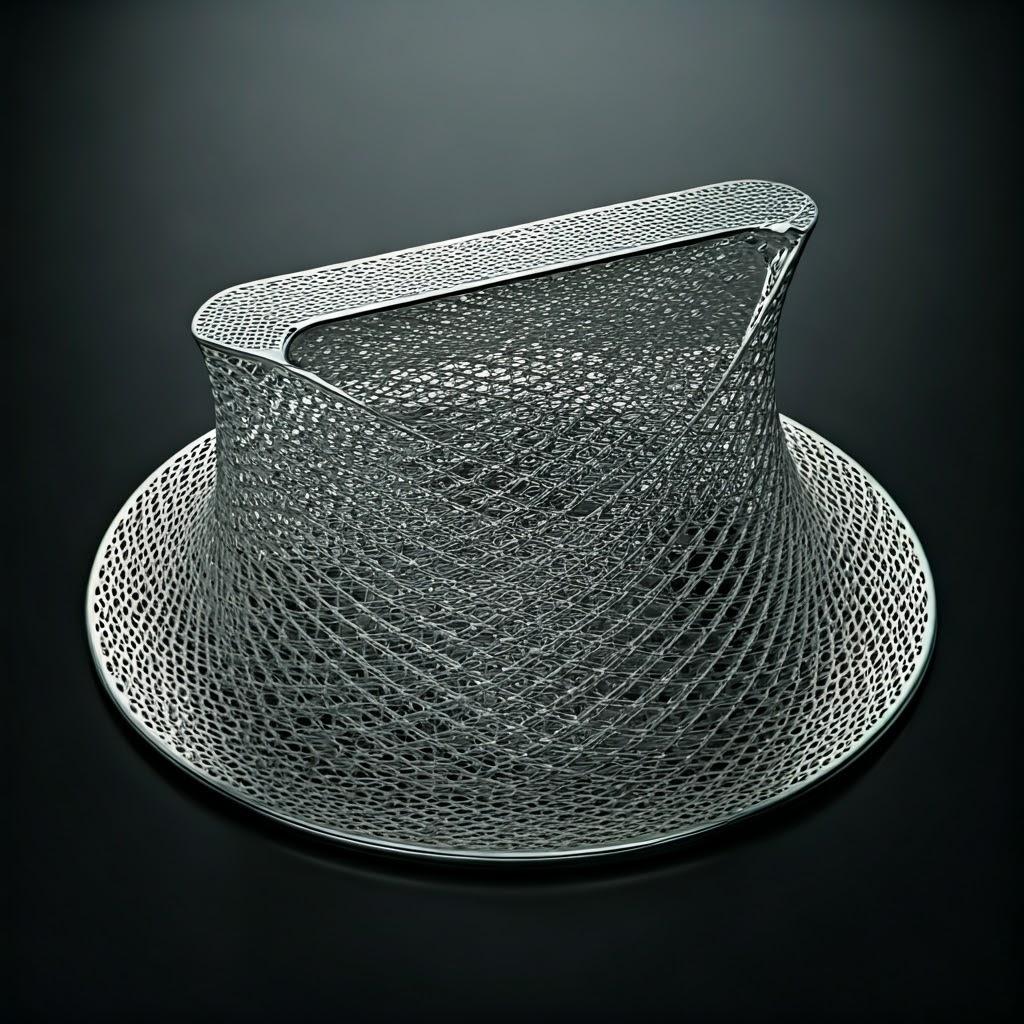
Aplicaciones: ¿Dónde están teniendo impacto los marcos de sensores impresos en 3D?
La versatilidad de la fabricación aditiva metálica le permite responder a las necesidades específicas de diversas aplicaciones de sensores biomédicos, impulsando la innovación en todo el espectro sanitario. Los responsables de compras y los ingenieros de los fabricantes de equipos originales (OEM) de dispositivos médicos, las organizaciones de fabricación por contrato (CMO) y los laboratorios de investigación recurren cada vez más a las estructuras metálicas impresas en 3D para superar las limitaciones de fabricación tradicionales y desbloquear nuevas capacidades de los dispositivos.
1. Monitores de salud portátiles: La tendencia a la monitorización continua y remota de los pacientes impulsa el crecimiento de sofisticados dispositivos vestibles. Estos dispositivos requieren armazones de sensores que:
- Ligero y cómodo: Para un uso prolongado sin molestias para el usuario. La AM permite crear complejas estructuras reticulares dentro del armazón, lo que reduce significativamente el peso al tiempo que mantiene la integridad estructural.
- Duradero y robusto: Para soportar el desgaste diario. Metales como el acero inoxidable 316L ofrecen una excelente durabilidad y resistencia a la corrosión.
- Compacto e integrado: Alojamiento de sensores, baterías y microelectrónica en un espacio reducido. La AM permite consolidar piezas e integrar elementos de montaje y carcasas directamente en el diseño del bastidor.
- No entra en contacto con la piel: Utilización de materiales biocompatibles, como aleaciones de titanio o 316L de calidad médica, cuando sea necesario.
- Ejemplo: Armazones para monitores de ECG portátiles que requieren una colocación precisa de los electrodos, o carcasas para sensores de monitorización continua de glucosa que deben ser robustas pero discretas. Proveedores B2B centrados en componentes de dispositivos médicos portátiles encuentran que la AM es ideal para producir estas piezas personalizadas y complejas de forma eficiente.
2. Sensores y dispositivos implantables: Podría decirse que es aquí donde la AM metálica ofrece las ventajas más profundas debido a los estrictos requisitos de biocompatibilidad, fiabilidad a largo plazo y ajuste anatómico.
- Biocompatibilidad: Materiales como el Ti-6Al-4V ELI (Extra Low Interstitials) se utilizan mucho por su perfil de seguridad demostrada en el cuerpo humano. Los procesos de AM metálica, cuando se controlan adecuadamente, pueden producir piezas densas y no corrosivas a partir de estos materiales. Met3dp’ se centra en polvos de gran pureza y libres de contaminación.
- Personalización y ajuste anatómico: La AM permite crear marcos de implante específicos para cada paciente a partir de datos de imágenes médicas (tomografías computarizadas o resonancias magnéticas). Esto mejora el ajuste del dispositivo, reduce el tiempo de cirugía y mejora potencialmente los resultados terapéuticos. Piense en cajas de marcapasos personalizadas o implantes craneales con soportes de sensores integrados.
- Miniaturización y complejidad: Alojamiento de sensores cada vez más complejos (por ejemplo, para interfaces neuronales o control de la presión intraocular) en un espacio mínimo. La AM puede crear estructuras internas complejas y las características necesarias para estos implantes avanzados.
- Osteointegración: En el caso de los implantes que interactúan con el hueso, la AM puede crear estructuras superficiales porosas o celosías diseñadas para favorecer el crecimiento óseo, lo que mejora la estabilidad a largo plazo.
- Ejemplo: Carcasas para cables de neuroestimuladores que incorporan bucles de retroalimentación de sensores, armazones para sistemas implantables de administración de fármacos que requieren un posicionamiento preciso o componentes estructurales para implantes cocleares. Empresas que buscan fabricación de implantes a medida o carcasa de sensor implantable son los principales candidatos para los servicios de AM metálica.
3. Componentes de equipos de diagnóstico: Aunque no están implantados, los sensores de los equipos de diagnóstico y laboratorio requieren una precisión y estabilidad extremas.
- Alta precisión y estabilidad: Los bastidores deben sujetar los sensores con rigidez y precisión, a menudo dentro de conjuntos complejos. La AM metálica puede conseguir tolerancias muy ajustadas y producir piezas dimensionalmente estables. Las impresoras Met3dp, por ejemplo, destacan por su precisión, líder en el sector.
- Geometrías complejas: Integración de canales de refrigeración, puntos de montaje para componentes ópticos o electrónicos, o vías de flujo para sensores de fluidos. La AM gestiona esta complejidad con facilidad en comparación con los ensamblajes mecanizados de varias piezas.
- Compatibilidad de materiales: Es posible que los marcos deban ser resistentes a los productos de limpieza o a las sustancias químicas específicas utilizadas en los ensayos. el acero inoxidable 316L suele ser una opción adecuada.
- Ejemplo: Soportes de montaje para sensores dentro de una máquina de resonancia magnética que requieren propiedades no magnéticas (grados específicos de titanio), marcos que sostienen sensores ópticos en equipos de análisis de sangre o componentes para chips de diagnóstico microfluídico que requieren dimensiones precisas de los canales. Equipos de aprovisionamiento que buscan un proveedor de piezas para equipos de diagnóstico pueden beneficiarse de la flexibilidad de AM’.
4. Sensores para instrumentos quirúrgicos: La cirugía moderna aprovecha la tecnología de sensores para mejorar la información y la navegación.
- Robustez y esterilizabilidad: Los marcos deben resistir los rigores de la cirugía y los repetidos ciclos de esterilización (autoclave). Tanto el Ti-6Al-4V ELI como el 316L son adecuados y pueden esterilizarse fácilmente.
- Miniaturización: Integración de sensores en las puntas de catéteres o instrumentos quirúrgicos mínimamente invasivos. La AM destaca en la creación de estos pequeños e intrincados componentes.
- Integración: Diseñar marcos que integren a la perfección los sensores, el cableado y la estructura mecánica de la herramienta.
- Ejemplo: Armazones que alojan sensores de fuerza en brazos quirúrgicos robotizados, soportes para sensores de navegación en guías quirúrgicas ortopédicas o alojamientos para sensores de presión en puntas de catéter. Las empresas de productos sanitarios que desarrollan sistemas quirúrgicos avanzados confían en socios fabricantes capaces de producir estas sensores médicos personalizados y componentes.
En estas diversas aplicaciones, la impresión metálica en 3D proporciona a ingenieros y fabricantes un potente conjunto de herramientas. Permite crear armazones de sensores biomédicos que no sólo son funcionales y fiables, sino que también están optimizados para requisitos de rendimiento específicos, necesidades de los pacientes y retos de integración, allanando el camino para la próxima generación de dispositivos médicos. Identificación de sensores fiables fabricación por contrato de productos sanitarios para los fabricantes de equipos originales que deseen aprovechar eficazmente esta tecnología es fundamental contar con socios con experiencia demostrada en AM.
¿Por qué elegir la impresión metálica en 3D para los marcos de los sensores? Ventajas clave
Aunque los métodos de fabricación tradicionales, como el mecanizado CNC y el moldeo por inyección de metal (MIM), han sido muy útiles en el sector de los dispositivos médicos, la fabricación aditiva de metales presenta una atractiva propuesta de valor específica para los bastidores de sensores biomédicos, impulsada por las ventajas en libertad de diseño, velocidad, personalización y eficiencia de la cadena de suministro. Para los ingenieros que diseñan intrincados componentes médicos y los responsables de compras que buscan productos rentables y de alta calidad soluciones avanzadas de fabricación médicacomprender estas ventajas es fundamental.
1. Libertad de diseño y complejidad inigualables:
- Límites tradicionales: El mecanizado CNC tiene dificultades con las cavidades internas, los rebajes y las formas orgánicas muy complejas, por lo que a menudo es necesario fabricar las piezas en varias piezas y luego ensamblarlas. El MIM requiere herramientas caras, lo que hace que los diseños complejos sean costosos e inflexibles a la hora de cambiarlos.
- Ventaja AM: La AM construye piezas capa a capa, lo que permite crear prácticamente cualquier geometría imaginable directamente a partir de un archivo CAD. Esto permite:
- Canales internos: Para la refrigeración, el cableado o el flujo de fluidos dentro del marco del sensor.
- Estructuras reticulares: Reducir significativamente el peso manteniendo la resistencia, crucial para wearables e implantes.
- Consolidación de piezas: Combinación de varios componentes de un conjunto de sensores en una única pieza impresa, lo que reduce el tiempo de montaje, los posibles puntos de fallo y el coste global.
- Orgánica & Formas conformes: Diseñar monturas que se adapten perfectamente a la anatomía del paciente (para implantes) o a los requisitos ergonómicos (para wearables).
- Impacto: Los ingenieros ya no se ven constreñidos por las limitaciones de fabricación, lo que permite diseños de bastidores de sensores más innovadores y optimizados.
2. Creación rápida de prototipos y desarrollo acelerado:
- Límites tradicionales: La creación de prototipos mediante mecanizado puede llevar mucho tiempo, y la creación de moldes para MIM es lenta y cara, por lo que la iteración del diseño es un proceso largo.
- Ventaja AM: La AM metálica permite la impresión directa de prototipos funcionales a partir de datos CAD, a menudo en cuestión de días. Esto facilita:
- Validación rápida del diseño: Los ingenieros pueden probar rápidamente la forma, el ajuste y la función con materiales reales.
- Ciclos de iteración más rápidos: Se pueden imprimir y evaluar múltiples variaciones de diseño en paralelo o en secuencia, lo que permite obtener diseños optimizados mucho más rápidamente.
- Reducción del plazo de comercialización: Acelerar la fase de creación de prototipos acorta considerablemente el plazo total de desarrollo de un dispositivo médico.
- Impacto: Las empresas de productos sanitarios pueden innovar más rápido, responder con mayor celeridad a la información clínica y comercializar antes dispositivos que pueden salvar vidas. Se trata de una ventaja crucial para las empresas dedicadas a creación de prototipos de dispositivos médicos.
3. Personalización y soluciones específicas para cada paciente:
- Límites tradicionales: La personalización masiva o la creación de dispositivos únicos específicos para cada paciente suelen ser económicamente inviables con los métodos tradicionales debido al elevado coste de las herramientas personalizadas o las complejas configuraciones de mecanizado.
- Ventaja AM: Dado que la AM no requiere herramientas, imprimir piezas únicas es esencialmente tan fácil como imprimir piezas estándar. Esto permite:
- Implantes específicos para cada paciente: Marcos de sensores integrados en implantes que se adaptan perfectamente a la anatomía del individuo a partir de tomografías computarizadas y resonancias magnéticas.
- Wearables personalizados: Dispositivos adaptados a grupos de usuarios específicos o a necesidades ergonómicas individuales.
- Tiradas de producción de bajo volumen: Producción económica de dispositivos o componentes especializados en pequeños lotes.
- Impacto: La AM permite un cambio hacia la medicina personalizada, en la que los dispositivos se adaptan a cada persona, lo que puede mejorar los resultados y la satisfacción del paciente. Esta capacidad está transformando fabricación de implantes a medida.
4. Eficiencia material y reducción de residuos:
- Límites tradicionales: La fabricación sustractiva (mecanizado) parte de un bloque sólido de material y elimina el sobrante, lo que a menudo genera importantes residuos (hasta un 80-90% en piezas complejas), sobre todo con materiales caros como el titanio de uso médico.
- Ventaja AM: La fabricación aditiva utiliza únicamente el material necesario para construir la pieza y sus soportes. Aunque se utiliza parte del material de soporte y parte del polvo queda sin fundir, la utilización total de material suele ser muy superior a la de los métodos sustractivos. A menudo, el polvo no fundido puede reciclarse y reutilizarse en construcciones posteriores (con un control de calidad adecuado).
- Impacto: La reducción del consumo de materiales permite ahorrar costes, sobre todo con aleaciones biocompatibles de alto coste, y contribuye a unas prácticas de fabricación más sostenibles. Se trata de una consideración clave para las organizaciones preocupadas por los costes y el medio ambiente.
5. Producción a la carta y flexibilidad de la cadena de suministro:
- Límites tradicionales: La dependencia de las herramientas y los largos tiempos de preparación del mecanizado pueden dar lugar a largos plazos de entrega y a la necesidad de grandes reservas de existencias.
- Ventaja AM: El inventario digital (archivos CAD) puede imprimirse según las necesidades, lo que permite:
- Inventario reducido: Minimizar la necesidad de existencias físicas y los costes de almacenamiento.
- Fabricación distribuida: Las piezas pueden imprimirse potencialmente más cerca del punto de necesidad.
- Respuesta más rápida a las fluctuaciones de la demanda: La producción puede aumentarse o reducirse más fácilmente sin limitaciones de utillaje.
- Impacto: La AM ofrece una mayor agilidad y resistencia en la cadena de suministro de productos sanitarios, lo que permite producción de piezas a la carta y reducir los riesgos asociados a la obsolescencia de las existencias o las interrupciones del suministro.
Tabla comparativa: AM frente a métodos tradicionales para marcos de sensores
Característica | Fabricación aditiva de metales (AM) | Mecanizado CNC | Moldeo por inyección de metal (MIM) |
---|---|---|---|
Complejidad del diseño | Muy alto (rasgos internos, entramados, orgánicos) | Moderado (limitado por el acceso a las herramientas) | Alta (pero requiere herramientas complejas) |
Personalización | Alta (ideal para pacientes específicos) | Bajo a moderado (instalación costosa) | Muy bajo (requiere moldes nuevos) |
Velocidad de creación de prototipos | Muy rápido (Días) | Moderado (días a semanas) | Lento (Semanas a meses para el utillaje) |
Coste de utillaje | Ninguno | Bajo (accesorios) | Muy alto (mohos) |
Residuos materiales | De bajo a moderado (posibilidad de reciclado de polvo) | Alta (sustractiva) | Bajo (forma casi neta) |
Volumen ideal | Bajo-medio, Personalizado, Prototipos | De menor a mayor (piezas más sencillas) | Alto volumen |
Plazo de entrega (Prod.) | Moderado | Moderado-alto | Alta (inicial), Baja (repetición) |
Consolidación de piezas | Excelente | Limitado | Moderado |
Exportar a hojas
Si se consideran detenidamente estas ventajas, los ingenieros y especialistas en adquisiciones pueden aprovechar estratégicamente los servicios de impresión metálica en 3D, como los que ofrece Met3dp con sus avanzados equipos y experiencia en materiales, para producir armazones de sensores biomédicos superiores que cumplan los exigentes requisitos de la atención sanitaria moderna.
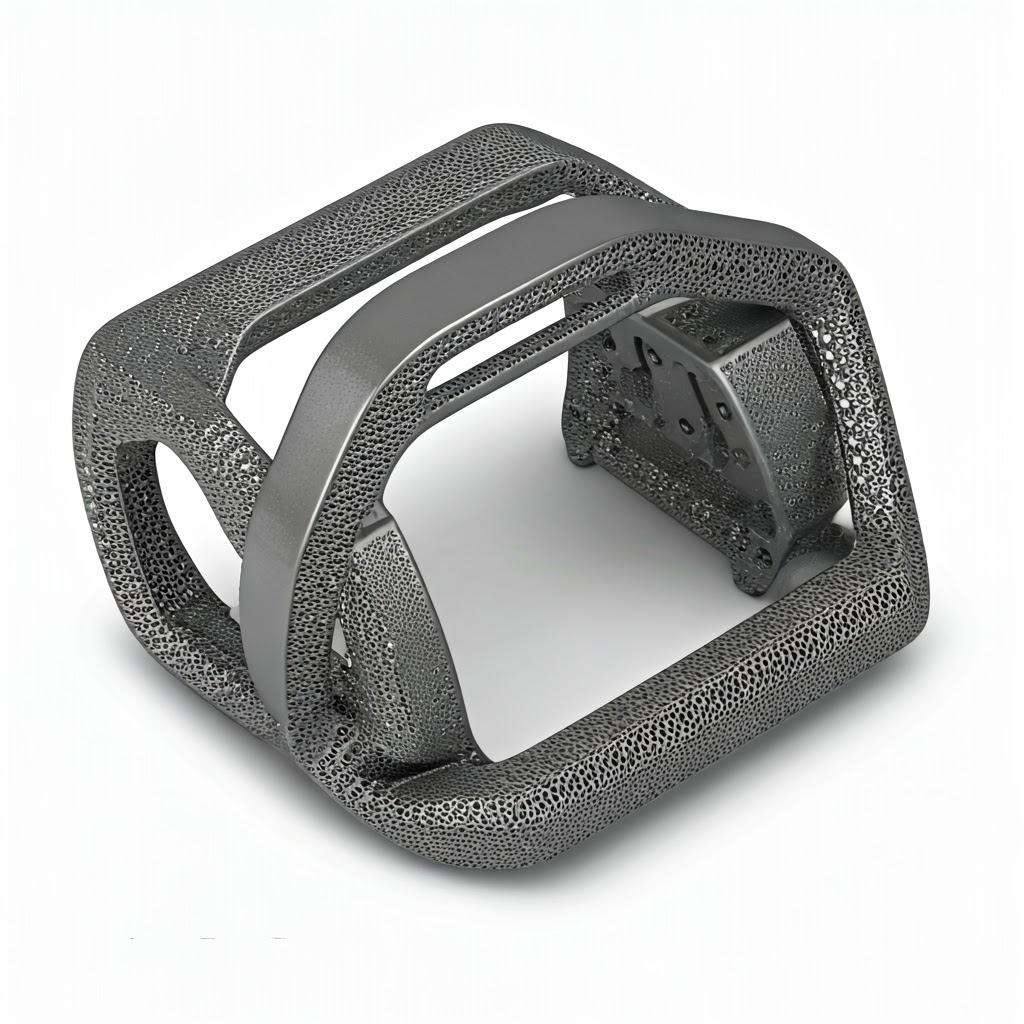
Enfoque en los materiales: Selección de metales biocompatibles para la integridad del marco del sensor
La elección del material del armazón de un sensor biomédico es primordial. No sólo determina el rendimiento mecánico y la longevidad del dispositivo, sino también su interacción con el cuerpo humano. En el caso de los armazones destinados a ser implantados o a estar en contacto prolongado con tejidos y fluidos, la biocompatibilidad no es negociable. La fabricación aditiva de metales ofrece compatibilidad con varias aleaciones clave de grado médico, entre las que destacan el titanio Ti-6Al-4V ELI y el acero inoxidable 316L. Adquisición de polvos certificados de alta calidad de una empresa fiable proveedor de polvos metálicos biocompatibles es el primer paso para garantizar la seguridad y eficacia de los productos.
1. Aleación de titanio: Ti-6Al-4V ELI (Grado 23) El Ti-6Al-4V ELI (Extra Low Interstitials) se considera a menudo el material de trabajo para implantes médicos, y con razón. Se trata de una aleación de titanio alfa-beta procesada específicamente para reducir los niveles de oxígeno, nitrógeno, carbono y hierro en comparación con el Ti-6Al-4V estándar (Grado 5). Esta reducción de los elementos intersticiales mejora significativamente su ductilidad y resistencia a la fractura, sobre todo a temperaturas criogénicas, aunque su principal ventaja en aplicaciones médicas es una mayor biocompatibilidad y resistencia a la fatiga.
- Propiedades clave:
- Excelente biocompatibilidad: Forma una capa de óxido pasiva y estable (TiO2) al exponerse al aire o a los fluidos corporales, lo que evita la fuga de iones y las reacciones adversas de los tejidos. Ampliamente aceptado para la implantación a largo plazo (norma ISO 5832-3).
- Alta relación resistencia-peso: Ofrece una resistencia comparable a la de muchos aceros, pero con casi la mitad de densidad, lo que resulta crucial para reducir el peso de implantes y wearables.
- Excelente resistencia a la corrosión: Alta resistencia a la corrosión por fluidos corporales, agentes de limpieza y procesos de esterilización.
- Buena resistencia a la fatiga: Importante para dispositivos sometidos a cargas cíclicas dentro del cuerpo (por ejemplo, componentes cerca de articulaciones o del corazón).
- No ferromagnético: Seguro para su uso en entornos de resonancia magnética.
- Potencial de Oseointegración: Pueden adherirse directamente al tejido óseo, especialmente cuando están tratados superficialmente o diseñados con estructuras porosas que pueden obtenerse mediante AM.
- Aplicaciones típicas del marco de sensores:
- Carcasas de sensores implantables (marcapasos, neuroestimuladores, implantes cocleares).
- Monturas integradas en implantes ortopédicos o dentales.
- Componentes para monitores portátiles de larga duración que requieren la máxima biocompatibilidad.
- Marcos para biosensores implantables (por ejemplo, glucosa, presión).
- Consideraciones de FA: El Ti-6Al-4V ELI es adecuado para los procesos de fusión por lecho de polvo láser (LPBF/SLM) y de fusión por haz de electrones (EBM). La EBM suele dar como resultado una menor tensión residual pero un acabado superficial más rugoso que la LPBF. Para optimizar las propiedades mecánicas y reducir la porosidad interna suele ser necesario un tratamiento posterior, como el tratamiento térmico de alivio de tensiones y, potencialmente, el prensado isostático en caliente (HIP). Para obtener unos resultados de impresión uniformes, es fundamental abastecerse de polvo con una composición química y una distribución del tamaño de las partículas controladas. La experiencia de Met3dp en la producción de aleaciones de titanio especializadas, como TiNi, TiTa, TiAl y TiNbZr, junto con las calidades estándar, pone de manifiesto su capacidad para tratar estos materiales avanzados.
2. Acero inoxidable: 316L el 316L es una aleación austenítica de acero inoxidable al cromo-níquel con molibdeno añadido, que mejora su resistencia a la corrosión, en particular frente a los cloruros (como los que se encuentran en los fluidos corporales). La “L” designa el bajo contenido de carbono (normalmente <0,03%), que minimiza la precipitación de carburos durante la soldadura o los tratamientos térmicos, preservando así la resistencia a la corrosión, especialmente en los límites de grano.
- Propiedades clave:
- Buena Biocompatibilidad: Aunque generalmente se considera menos biocompatible que el Ti-6Al-4V ELI para implantes permanentes debido a la posible liberación de iones de níquel en personas sensibles durante periodos prolongados, el 316L (que cumple normas como la ISO 5832-1) está ampliamente aceptado para implantes temporales, instrumentos quirúrgicos y dispositivos de contacto externo o de corta duración.
- Excelente resistencia a la corrosión: Alta resistencia a la corrosión general, a las picaduras y a la corrosión por intersticios en entornos fisiológicos.
- Buena resistencia y ductilidad: Ofrece un buen equilibrio de propiedades mecánicas.
- Rentable: Generalmente menos costoso que las aleaciones de titanio.
- Facilidad de procesamiento: Fácilmente imprimible mediante LPBF y relativamente fácil de posprocesar (pulido, mecanizado).
- Esterilizable: Compatible con los métodos de esterilización habituales, como el autoclave.
- Aplicaciones típicas del marco de sensores:
- Marcos para sensores externos vestibles (donde el contacto con la piel es controlado o breve).
- Componentes de equipos de diagnóstico que no están en contacto directo a largo plazo con el paciente.
- Carcasas para sensores en instrumentos quirúrgicos.
- Componentes de dispositivos implantables temporales o de corta duración (por ejemplo, dispositivos de fijación con detección integrada).
- Prototipos en los que el material final podría ser titanio, pero el coste es un factor inicial.
- Consideraciones de FA: el 316L es uno de los materiales más comunes impresos con LPBF. Generalmente se imprime bien, alcanzando una alta densidad. El postprocesado suele incluir el alivio de tensiones y el acabado de la superficie (por ejemplo, pulido, electropulido) para mejorar la resistencia a la corrosión y la estética. Garantizar que el polvo cumple acero inoxidable de calidad médica especificaciones es crucial.
La importancia de la calidad y el suministro del polvo Independientemente de la aleación elegida, la calidad del polvo metálico utilizado en el proceso de AM es fundamental, especialmente para aplicaciones médicas. Factores como:
- Pureza y química: Deben cumplir estrictas normas médicas (por ejemplo, ASTM F136 para Ti-6Al-4V ELI, ASTM F138 para 316L). Los contaminantes pueden comprometer la biocompatibilidad y las propiedades mecánicas.
- Distribución del tamaño de las partículas (PSD): Afecta a la fluidez del polvo, la densidad de empaquetado y la resolución alcanzable durante la impresión.
- Esfericidad: Las partículas esféricas fluyen mejor y se empaquetan más densamente, lo que da lugar a capas más uniformes y piezas finales más densas.
- Ausencia de satélites: Las partículas pequeñas que se adhieren a las grandes pueden afectar negativamente a la fluidez y la capacidad de extensión.
- Baja porosidad: La porosidad interna del gas dentro de las partículas de polvo puede traducirse en porosidad en la pieza final.
Empresas como Met3dp, que emplean técnicas avanzadas de fabricación en polvo como Atomización de gas de fusión por inducción al vacío (VIGA) y Proceso de electrodos rotativos de plasma (PREP)el objetivo es producir polvos metálicos esféricos de alta calidad con características controladas con precisión. Sus diseños exclusivos de boquillas y flujo de gas en la atomización de gas, por ejemplo, buscan una alta esfericidad y una buena fluidez, que son esenciales para imprimir productos densos y de alta calidad polvo metálico para productos sanitarios. Asociarse con un proveedor que comprenda y controle estas características del polvo, y que proporcione certificaciones de materiales y trazabilidad, es fundamental para cualquier fabricante de productos sanitarios que utilice AM metálica.
Resumen de la tabla de selección de materiales
Característica | Ti-6Al-4V ELI (Grado 23) | Acero inoxidable 316L |
---|---|---|
Ventaja principal | Biocompatibilidad superior, resistencia/peso | Excelente resistencia a la corrosión, coste |
Biocompatibilidad | Excelente (implante a largo plazo) | Bueno (a corto plazo/externo, instrumentos) |
Densidad | ~4,43 g/cm³ | ~8,0 g/cm³ |
Fuerza | Alta | Moderado-alto |
Resistencia a la corrosión | Excelente | Excelente (especialmente frente a cloruros) |
Compatibilidad con RM | Sí (no ferromagnético) | No (generalmente paramagnético/férrico débil) |
Coste | Alta | Moderado |
Proceso AM común | LPBF, EBM | LPBF |
Clave Estándar | ISO 5832-3, ASTM F136 | ISO 5832-1, ASTM F138 |
Uso típico | Implantes permanentes, wearables de alto rendimiento | Instrumentos quirúrgicos, diagnósticos, dispositivos ext |
Exportar a hojas
Seleccionar el material adecuado implica equilibrar los requisitos técnicos del armazón del sensor (cargas mecánicas, entorno), el nivel necesario de biocompatibilidad en función de la aplicación (implante frente a externo), las vías de regulación y las limitaciones presupuestarias. Consultar con expertos en materiales y proveedores de servicios de AM experimentados como Met3dp es crucial para hacer la elección óptima para su aplicación específica de armazón de sensor biomédico.
Diseño para la fabricación aditiva (DfAM): Optimización de los marcos de los sensores para la impresión 3D
Tomar simplemente un diseño destinado al mecanizado y enviarlo a una impresora 3D de metal rara vez produce resultados óptimos. Para aprovechar realmente el potencial de la AM, los ingenieros deben adoptar los principios del diseño para la fabricación aditiva (DfAM). DfAM no consiste sólo en garantizar que una pieza poder se trata de diseñarlo de forma inteligente para aprovechar al máximo las ventajas de la AM, como la complejidad, la consolidación y la ligereza, minimizando al mismo tiempo posibles problemas, como estructuras de soporte excesivas, tensiones residuales o un posprocesamiento difícil. En el caso de componentes complejos como las estructuras de los sensores biomédicos, la AMD es fundamental.
Principios clave de DfAM para los marcos de sensores:
- Aprovechamiento de la complejidad geométrica: El mayor punto fuerte de AM’ es su capacidad para crear formas complejas. Para los marcos de los sensores, esto se traduce en:
- Canales internos & Cavidades: Diseñe canales integrados para cableado, fibra óptica o incluso vías microfluídicas directamente dentro de la estructura del marco. Esto protege los componentes delicados y reduce la complejidad del montaje. Considere canales suaves y curvos en lugar de ángulos agudos para facilitar la eliminación del polvo durante el posprocesamiento.
- Diseño conforme: Modele las monturas para que sigan contornos anatómicos (para implantes) o formas ergonómicas (para wearables). Esto mejora el ajuste, la comodidad y, potencialmente, el rendimiento del sensor al garantizar un contacto o posicionamiento óptimos. Utilizar datos de imagen específicos del paciente (TC/IRM) para crear monturas realmente personalizadas.
- Integración de características: Incorpore puntos de montaje, encajes a presión, características de alineación o conectores directamente en el marco impreso, eliminando la necesidad de componentes y elementos de fijación independientes.
- Aligeramiento con estructuras reticulares y optimización de la topología:
- Estructuras reticulares: Sustituya los volúmenes sólidos del bastidor por estructuras internas de celosía o giroides. Estas geometrías porosas de gran complejidad, fáciles de fabricar con AM, reducen drásticamente el peso y el uso de materiales, al tiempo que mantienen la rigidez y resistencia estructurales necesarias. Esto es vital para los implantes (que reducen la tensión) y los dispositivos portátiles (que mejoran la comodidad). Los distintos tipos de celdas reticulares (por ejemplo, cúbicas, octeto-truss) ofrecen propiedades mecánicas variables.
- Optimización de la topología: Utilice herramientas de software para determinar algorítmicamente la distribución de material más eficiente dentro de un espacio de diseño definido, en función de las cargas y restricciones aplicadas. Esto suele dar lugar a estructuras de aspecto orgánico y muy optimizadas que eliminan material de las zonas sometidas a poca tensión, logrando el máximo rendimiento con el mínimo peso, lo que resulta ideal para armazones de sensores de alto rendimiento en aplicaciones exigentes.
- Consolidación de piezas:
- Analizar los conjuntos de sensores existentes diseñados para la fabricación tradicional. Identificar oportunidades para combinar múltiples componentes individuales (soportes, carcasas, fijaciones) en una única pieza impresa monolítica.
- Ventajas: Reduce el número de piezas, simplifica el montaje, disminuye las necesidades de inventario, elimina posibles puntos de fallo en uniones o interfaces y, a menudo, reduce el peso total y el coste de producción.
- Ejemplo: Una carcasa de sensor que antes constaba de un cuerpo mecanizado, una tapa independiente y varios tornillos podría rediseñarse como una única unidad impresa con encajes a presión integrados o un mecanismo de cierre de bayoneta.
- Diseño para estructuras de soporte mínimas:
- Las estructuras de soporte suelen ser necesarias en la AM metálica (especialmente LPBF) para anclar la pieza a la placa de impresión, soportar los elementos que sobresalen y conducir el calor para evitar deformaciones. Sin embargo, los soportes consumen material adicional, aumentan el tiempo de impresión y deben retirarse en el postprocesado, lo que puede suponer un reto y dañar las características o superficies finas.
- Estrategias:
- Orientación: Seleccione cuidadosamente la orientación de la pieza en la placa de impresión para minimizar los salientes que requieren soporte. Analice la relación entre la minimización del soporte, la calidad de la superficie en las caras críticas y el tiempo de impresión.
- Ángulos autoportantes: Diseñe los salientes por debajo del ángulo crítico (normalmente alrededor de 45 grados desde la horizontal para muchos procesos de AM de metal, pero depende del proceso/material) para que puedan imprimirse sin soportes. Utilice chaflanes o filetes en lugar de salientes horizontales afilados siempre que sea posible.
- Soportes internos: Minimizar o evitar los soportes internos complejos, ya que pueden ser extremadamente difíciles o imposibles de retirar, especialmente en canales pequeños. Diseñe los elementos internos para que sean autoportantes o prevea puertos de acceso para retirar los soportes y evacuar el polvo.
- Teniendo en cuenta el grosor de la pared y las características finas:
- Los procesos de AM metálica tienen limitaciones en cuanto al grosor mínimo de la pared y el tamaño de la característica que pueden producir de forma fiable (influidos por el tamaño del punto del láser/haz, el tamaño de las partículas de polvo y el grosor de la capa).
- Directrices: Normalmente, el grosor mínimo de las paredes puede rondar los 0,3-0,5 mm, pero esto varía considerablemente. Consulte con su proveedor de servicios de AM, como Met3dp, sobre las capacidades específicas de sus métodos de impresión y materiales. Evite diseñar características cercanas a los límites del proceso a menos que sea absolutamente necesario y esté validado.
- Garantizar un espesor de pared suficiente para la integridad estructural, especialmente después de posibles operaciones de acabado superficial que eliminen material.
- Diseño para el posprocesamiento:
- Anticipar los pasos posteriores durante la fase de diseño.
- Acceso para la eliminación de soportes: Asegúrese de que las zonas donde se fijan los soportes son físicamente accesibles para su retirada manual o mediante CNC sin dañar la pieza.
- Evacuación de polvo: En el caso de piezas con canales o cavidades internas, diseñe orificios de escape estratégicamente situados (que puedan taponarse o soldarse posteriormente en caso necesario) para facilitar la eliminación completa del polvo no fundido. El polvo atrapado es inaceptable en los productos sanitarios.
- Tolerancias de mecanizado: Si se requieren tolerancias estrictas o acabados superficiales específicos en determinadas características, diseñe material de reserva adicional en esas superficies para eliminarlo mediante mecanizado CNC después de la impresión.
- Acabado superficial: Considere qué superficies requieren un pulido intenso (por ejemplo, para la biocompatibilidad o la reducción de la fricción) y diséñelas de modo que sean accesibles para las herramientas de pulido.
La colaboración es clave: Aplicar eficazmente directrices de diseño de fabricación aditiva requiere la colaboración entre ingenieros de diseño y expertos en procesos de AM. La colaboración con proveedores de servicios experimentados como Met3dp en las primeras fases del diseño puede proporcionar información muy valiosa sobre la posibilidad de fabricación, la selección de materiales, las estrategias de orientación y las posibles repercusiones en los costes, lo que en última instancia conduce a un diseño más sólido y optimizado de la estructura del sensor biomédico. Su experiencia en productos y aplicaciones garantiza una aplicación práctica y eficaz de la DfAM.
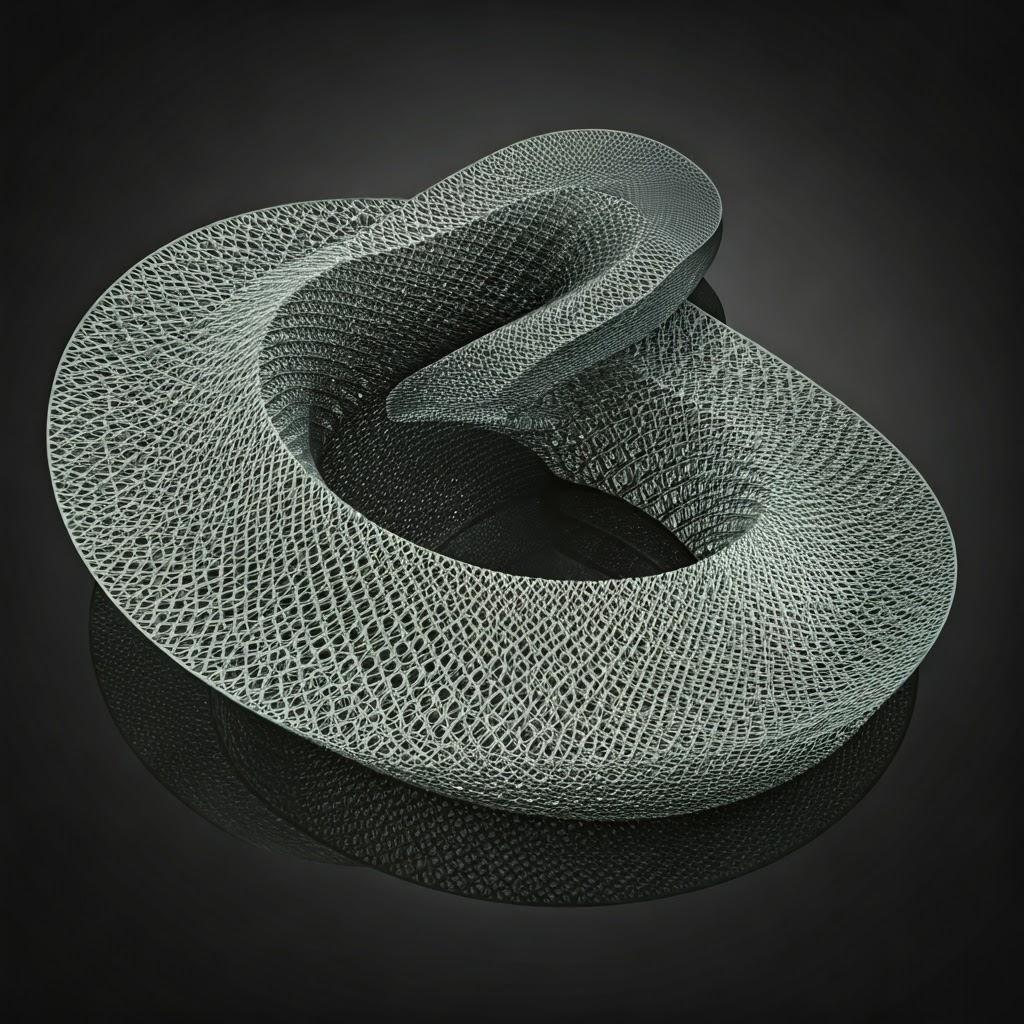
Alcanzar la precisión: Normas de tolerancia, acabado superficial y precisión dimensional
En el caso de los marcos de sensores biomédicos, la precisión suele ser primordial. El armazón debe colocar con precisión el elemento sensor, sellar potencialmente contra fluidos o tejidos y encajar correctamente en un conjunto mayor o en un lugar anatómico. Comprender los niveles de tolerancia, acabado superficial y precisión dimensional general que se pueden conseguir con la AM metálica es crucial para establecer expectativas realistas y garantizar que la pieza final cumpla los requisitos funcionales.
1. Tolerancias: La tolerancia se refiere al límite o límites permisibles de variación en una dimensión física. Los procesos de AM metálica, aunque son capaces de alcanzar una gran complejidad, no son intrínsecamente tan precisos como el mecanizado CNC de alta gama en su estado as-built.
- Tolerancias típicas de construcción:
- Fusión láser en lecho de polvo (LPBF/SLM): Generalmente ofrece mayor precisión. Las tolerancias típicas pueden oscilar entre ±0,1 mm y ±0,2 mm para dimensiones más pequeñas (por ejemplo, hasta 50-100 mm), pudiendo aumentar ligeramente para piezas más grandes (por ejemplo, entre ±0,1% y ±0,2% de la dimensión). A veces, las tolerancias de características específicas pueden ser más estrictas.
- Fusión por haz de electrones (EBM): A menudo tiene tolerancias ligeramente más holgadas que LPBF, quizás en el rango de ±0,2 mm a ±0,4 mm o ±0,4% de la dimensión, debido al mayor aporte de energía y a las diferentes características del polvo.
- Factores que influyen en la tolerancia:
- Calibración de la máquina: La calibración periódica y precisa del sistema AM es esencial.
- Propiedades del material: La dilatación y la contracción térmicas varían según los materiales (por ejemplo, Ti-6Al-4V frente a 316L).
- Geometría y tamaño de la pieza: Las piezas grandes o complejas con secciones transversales variables pueden sufrir más tensión térmica y distorsión.
- Orientación y soportes: La forma en que se orienta y apoya la pieza influye significativamente en la precisión y el posible alabeo.
- Gestión térmica: El calentamiento de la placa de construcción, los parámetros del proceso (potencia del láser, velocidad de escaneado) y el flujo de gas influyen en el historial térmico y en las tensiones/precisión resultantes.
- Post-procesamiento: El tratamiento térmico de alivio de tensiones puede provocar pequeños cambios dimensionales; el mecanizado introduce sus propias tolerancias.
- Lograr tolerancias más ajustadas: Cuando las tolerancias as-built son insuficientes para las características críticas (por ejemplo, superficies de contacto, interfaces de sellado, localizadores de sensores precisos), mecanizado secundario . Las piezas se imprimen con material adicional (margen de mecanizado) en las superficies críticas y, a continuación, se mecanizan con CNC para conseguir tolerancias tan ajustadas como ±0,01 mm a ±0,05 mm o mejores, comparables a las de la fabricación tradicional. Es fundamental especificar claramente estos requisitos en los planos de ingeniería.
2. Acabado superficial: El acabado superficial, a menudo cuantificado por la rugosidad media (Ra), describe la textura de la superficie de una pieza. Es fundamental para las aplicaciones biomédicas por su impacto en la biocompatibilidad, la fricción, el sellado, la resistencia a la fatiga y la facilidad de limpieza.
- Acabado superficial de construcción:
- Las piezas metálicas de AM suelen tener un acabado superficial más rugoso que las piezas mecanizadas. La rugosidad depende del proceso, el material, el grosor de la capa, el tamaño de las partículas y la orientación de la superficie con respecto a la dirección de fabricación.
- LPBF: Los valores de Ra suelen oscilar entre 6 µm y 15 µm (o más) en función del ángulo de la superficie (las superficies orientadas hacia arriba suelen ser más lisas que las orientadas hacia abajo o las paredes laterales).
- EBM: Tiende a producir superficies más rugosas, potencialmente Ra 20 µm a 35 µm o más.
- Efecto Escalera: Las superficies curvadas o en ángulo presentan una textura "escalonada" característica debido a la naturaleza estratificada del proceso.
- Mejora del acabado superficial: Para la mayoría de las aplicaciones médicas, especialmente implantes o superficies en contacto con fluidos, el acabado tal cual es insuficiente. Se utilizan diversas técnicas de postratamiento:
- Granallado de medios (por ejemplo, granallado de perlas): Proporciona un acabado mate uniforme, elimina las partículas semi-sinterizadas, pero sólo mejora ligeramente Ra (por ejemplo, hasta Ra 3-6 µm).
- Acabado por volteo/vibración: Utiliza medios abrasivos en un tambor giratorio o vibratorio para alisar superficies y desbarbar bordes. Puede alcanzar Ra ~1-3 µm.
- Pulido manual o CNC: El pulido mecánico mediante abrasivos progresivamente más finos puede lograr acabados muy lisos, similares a los de un espejo (Ra < 0,1 µm), a menudo necesarios para que las superficies de los implantes maximicen la biocompatibilidad y reduzcan la adhesión bacteriana.
- Electropulido: Proceso electroquímico que elimina una capa microscópica de material, preferentemente de los picos, dando como resultado una superficie muy lisa, limpia y, a menudo, más resistente a la corrosión (común para 316L). Puede alcanzar Ra ~0,2-0,8 µm.
- Especificación de requisitos: Definir claramente el acabado superficial requerido (por ejemplo, especificando Ra máx.) en los planos de ingeniería de las superficies críticas. Comprender que conseguir acabados muy finos añade costes y plazos de entrega.
3. Precisión dimensional: La precisión dimensional se refiere al grado de conformidad de la pieza final con las dimensiones nominales especificadas en el modelo CAD. Abarca tanto la tolerancia (variación) como las desviaciones sistemáticas.
- Asegurando la precisión:
- Control de procesos: Los proveedores de servicios de AM fiables como Met3dp hacen hincapié en el control riguroso de los procesos, la calibración de las máquinas y los conjuntos de parámetros optimizados desarrollados a través de la experiencia para minimizar las desviaciones. Sus impresoras suelen destacar por volumen de impresión, precisión y fiabilidad líderes en la industria.
- Simulación: En ocasiones, las herramientas de simulación térmica pueden predecir posibles distorsiones, lo que permite ajustar el diseño o la estrategia de soporte de forma preventiva.
- Control de calidad e inspección: La medición posterior a la impresión mediante MMC (máquinas de medición por coordenadas), escaneado 3D o herramientas de metrología tradicionales es esencial para verificar las dimensiones críticas con respecto a las especificaciones. El escaneado por TC puede verificar las características y dimensiones internas.
- Refinamiento iterativo: En el caso de piezas muy críticas, las impresiones iniciales podrían utilizarse para caracterizar las desviaciones del proceso, lo que permitiría realizar ajustes de compensación en el modelo CAD para las impresiones posteriores con el fin de mejorar la precisión.
Cuadro sinóptico: Métricas de precisión en Metal AM
Métrica | Gama típica as-built (LPBF) | Alcance típico as-built (EBM) | Alcanzable con post-procesamiento | Consideraciones clave para los marcos de sensores |
---|---|---|---|---|
Tolerancia | ±0,1 a ±0,2 mm (±0,1-0,2%) | ±0,2 a ±0,4 mm (±0,4%) | ±0,01 a ±0,05 mm (mediante mecanizado) | Colocación de sensores, superficies de contacto, interfaces de estanqueidad |
Acabado superficial (Ra) | 6 µm a 15+ µm | 20 µm a 35+ µm | < 0,1 µm (Pulido), ~0,4 µm (EP) | Biocompatibilidad, fricción, estanqueidad, facilidad de limpieza, fatiga |
Tamaño mínimo de la característica | ~0,3 a 0,5 mm | Ligeramente mayor que LPBF | Limitado principalmente por el proceso AM | Miniaturización, paredes finas, detalles del conector |
Exportar a hojas
Los ingenieros y los responsables de compras deben conocer estos niveles de precisión alcanzables. Especifique claramente las tolerancias críticas y los acabados superficiales, y discuta las expectativas con el proveedor de AM elegido para asegurarse de que el resultado final es el adecuado precisión dimensional piezas AM satisfacer los exigentes requisitos de las aplicaciones de sensores biomédicos.
Más allá de la impresión: Pasos esenciales del posprocesamiento de fotogramas de sensores biomédicos
La creación de un armazón de sensor biomédico no termina cuando se detiene la impresora 3D. La pieza "tal cual", aunque geométricamente completa, requiere varios pasos cruciales de posprocesamiento para conseguir las propiedades deseadas del material, las características de la superficie, la limpieza y, en última instancia, la idoneidad para su uso en un dispositivo médico. Estos pasos no son extras opcionales, sino que forman parte integral para garantizar la seguridad, el rendimiento y la biocompatibilidad del componente final. Comprender estos post-procesamiento de piezas de fabricación aditiva de metales requisitos es vital para la planificación de proyectos, el cálculo de costes y la evaluación de proveedores.
Etapas comunes de posprocesamiento:
- Tratamiento térmico antiestrés:
- Por qué: Los rápidos ciclos de calentamiento y enfriamiento inherentes a los procesos de fusión de lecho de polvo (especialmente LPBF) inducen importantes tensiones residuales en la pieza impresa. Estas tensiones pueden provocar distorsiones durante o después de la retirada de la placa de impresión, reducir la vida a fatiga y, potencialmente, provocar un fallo prematuro.
- Proceso: Las piezas se calientan en una atmósfera controlada (vacío o gas inerte como el argón) a una temperatura específica por debajo del punto de transformación de la aleación, se mantienen durante un tiempo y, a continuación, se enfrían lentamente. Esto permite que la microestructura del material se relaje, aliviando las tensiones internas sin alterar significativamente las propiedades mecánicas del núcleo.
- Importancia: Absolutamente esencial para la estabilidad dimensional y la integridad mecánica, en particular para materiales como el Ti-6Al-4V. Protocolos específicos (tratamiento térmico Ti-6Al-4V) dependen de la aleación y de los requisitos de la aplicación.
- Extracción de la pieza de la placa de montaje:
- Proceso: Normalmente, las piezas se separan de la placa metálica mediante electroerosión por hilo (EDM) o una sierra de cinta.
- Consideraciones: Requiere una manipulación cuidadosa para evitar dañar la pieza. Es probable que la superficie de separación requiera un acabado posterior.
- Retirada de la estructura de soporte:
- Por qué: Los soportes son necesarios durante la impresión, pero deben retirarse después.
- Proceso: Puede ir desde la simple rotura manual (para soportes bien diseñados y accesibles) hasta el intrincado trabajo manual con herramientas de mano, o el mecanizado CNC para soportes más robustos o de difícil acceso.
- Desafíos: Puede requerir mucho trabajo y tiempo, especialmente en el caso de geometrías complejas con soportes internos. Riesgo de dañar la superficie de la pieza o las características finas durante la retirada. DfAM contribuye enormemente a simplificar este paso. Las superficies donde se fijaron los soportes suelen ser de menor calidad y requieren un acabado adicional.
- Prensado isostático en caliente (HIP):
- Por qué: Aunque los procesos de AM persiguen la densidad total, a veces pueden quedar poros internos microscópicos (debidos al gas atrapado o a una fusión incompleta). Estos poros pueden actuar como concentradores de tensiones, reduciendo significativamente la vida a fatiga y la resistencia a la fractura, aspectos críticos para los implantes a largo plazo.
- Proceso: Las piezas se someten simultáneamente a alta temperatura (por debajo del punto de fusión) y alta presión isostática (normalmente utilizando un gas inerte como el argón) en un recipiente especializado. Esta combinación colapsa los vacíos internos y permite alcanzar la densidad teórica total (normalmente >99,9%).
- Importancia: Suele ser obligatorio para aplicaciones críticas y sensibles a la fatiga, como implantes ortopédicos o cardiovasculares fabricados con Ti-6Al-4V ELI. Mejora significativamente las propiedades mecánicas, especialmente la resistencia a la fatiga y la ductilidad. Aumenta el coste y el plazo de entrega.
- Acabado superficial:
- Por qué: Para conseguir la suavidad, limpieza, biocompatibilidad y aspecto estético requeridos, ya que la superficie tal cual suele ser demasiado rugosa para la mayoría de las aplicaciones médicas.
- Procesos: Como se ha detallado anteriormente: granallado, volteo, pulido manual/CNC, electropulido. El método o métodos elegidos dependen del material, la geometría y los requisitos específicos de la superficie (valor Ra, aspecto visual). Acabado de superficies de productos sanitarios a menudo requiere múltiples pasos para lograr el resultado deseado.
- Limpieza y pasivación:
- Por qué: Para los dispositivos médicos es extremadamente crítico eliminar todos los contaminantes del proceso de fabricación. Esto incluye partículas de polvo sin fundir (especialmente de canales internos), residuos de mecanizado o pulido (aceites, abrasivos), huellas dactilares y cualquier otro material extraño.
- Proceso de limpieza: Suele constar de varias fases, que pueden incluir la limpieza por ultrasonidos con detergentes específicos, el aclarado con disolventes y el secado a fondo. Los procedimientos de limpieza validados son esenciales. En el caso de piezas con geometrías internas complejas, puede ser difícil garantizar la eliminación completa del polvo y puede requerir métodos específicos de limpieza por flujo o verificación mediante escaneado CT.
- Pasivado (especialmente para aceros inoxidables): Proceso químico (a menudo con ácido nítrico o cítrico) que elimina el hierro libre de la superficie del acero inoxidable y mejora la capa de óxido pasiva natural rica en cromo. Esto mejora significativamente la resistencia a la corrosión y la biocompatibilidad al reducir el potencial de lixiviación de iones.
- Inspección final y control de calidad:
- Por qué: Verificar que el bastidor del sensor acabado cumple todas las especificaciones dimensionales, de acabado superficial, de limpieza y de propiedades del material.
- Métodos: Inspección dimensional (MMC, escaneado 3D), medición de la rugosidad superficial, inspección visual (incluido el examen microscópico), END (ensayos no destructivos) como escaneado CT para integridad interna/eliminación de polvo, revisión de certificación de materiales, pruebas de limpieza (por ejemplo, pruebas de carga biológica).
Integración del flujo de trabajo: Estos pasos de postprocesado están interconectados y deben planificarse como parte del flujo de trabajo global de fabricación. Por ejemplo, el mecanizado puede realizarse después de la eliminación de tensiones, pero antes del pulido y la limpieza finales. La secuencia específica depende de la pieza, el material y los requisitos. La asociación con un proveedor de servicios de AM como Met3dp, que ofrece soluciones integrales que incluyen el posprocesamiento y la garantía de calidad a medida para sectores como el médico, garantiza que estos pasos críticos se gestionen de forma eficaz.
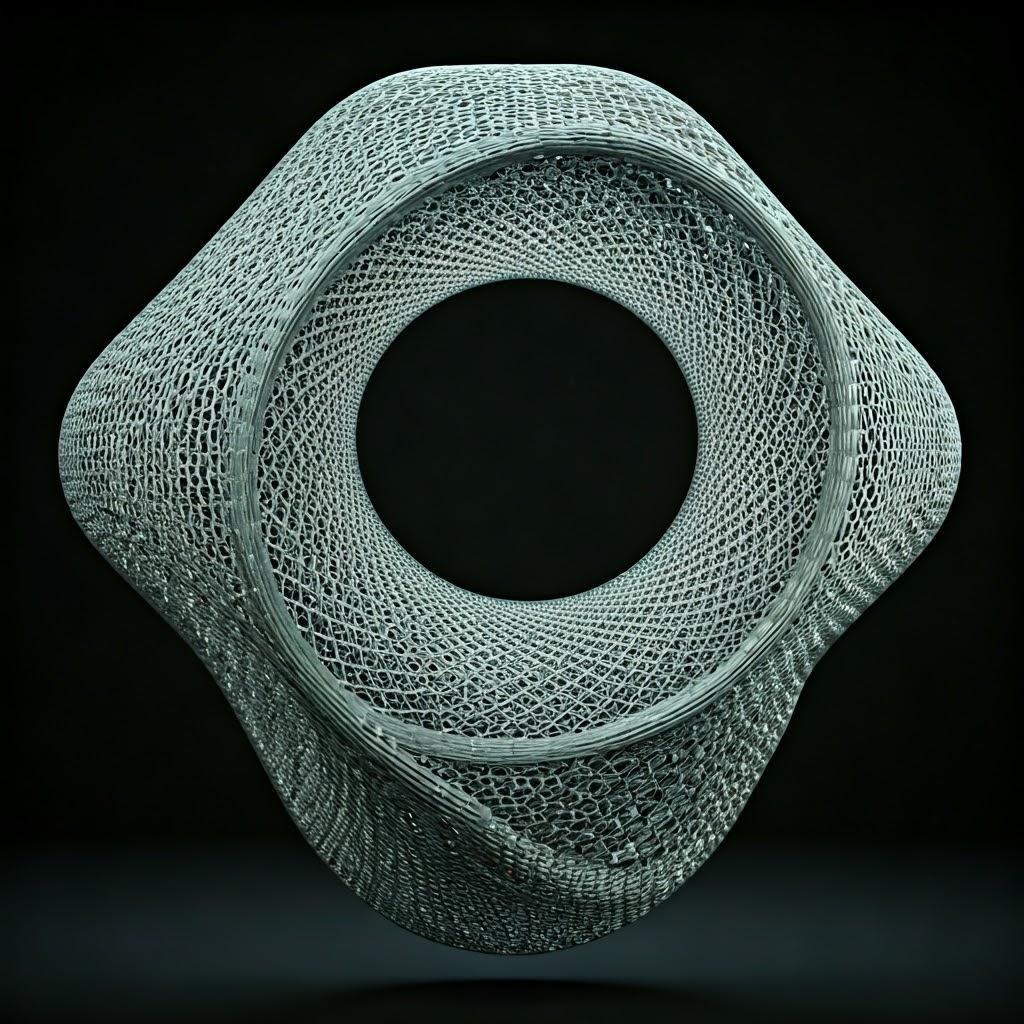
Afrontar los retos: Problemas comunes en la impresión 3D de marcos de sensores y soluciones
Aunque la AM metálica ofrece enormes ventajas, no está exenta de dificultades, sobre todo en la producción de componentes complejos de alta precisión, como los bastidores de sensores biomédicos. El conocimiento de los posibles problemas y la aplicación proactiva de estrategias de mitigación son fundamentales para obtener resultados satisfactorios. Fiable protocolos de control de calidad de fabricación aditiva los protocolos son esenciales a lo largo de todo el proceso.
1. Deformación y distorsión:
- Asunto: El calentamiento y el enfriamiento desiguales durante la impresión provocan tensiones internas que pueden hacer que las piezas se deformen o se deformen, especialmente las estructuras planas finas o grandes.
- Causas: Gradientes térmicos elevados, soporte insuficiente, calentamiento inadecuado de la placa de impresión, estrategia de escaneado subóptima.
- Soluciones:
- DfAM: Modificaciones de diseño para reducir las grandes zonas planas o añadir elementos de refuerzo.
- Orientación: Elija una orientación que minimice la acumulación de tensiones.
- Estrategia de apoyo: Utilice soportes robustos diseñados para anclar la pieza de forma eficaz y gestionar la disipación del calor.
- Parámetros del proceso: Optimice la potencia del láser/rayo, la velocidad de escaneado y los patrones de eclosión. Utilice el calentamiento de la placa de impresión.
- Alivio del estrés: Realice el tratamiento térmico de alivio de tensiones inmediatamente después de la impresión, a menudo antes de retirar la pieza de la placa de impresión.
2. Dificultades para eliminar la estructura de soporte:
- Asunto: Los soportes en zonas de difícil acceso (canales internos, características delicadas) pueden ser difíciles o imposibles de eliminar por completo sin dañar la pieza. El material de soporte residual es inaceptable.
- Causas: Geometría compleja de la pieza, orientación subóptima, soportes demasiado densos o mal diseñados.
- Soluciones:
- DfAM: Diseño para soporte mínimo (ángulos autoportantes, orientación de las características). Diseñe puntos de acceso para la retirada de soportes internos. Utilizar la optimización topológica, que suele dar lugar a diseños que necesitan menos soporte.
- Diseño de soportes: Utilizar estructuras de soporte especializadas (por ejemplo, puntos de conexión más finos, soportes perforados) que sean más fáciles de retirar.
- Orientación: Dar prioridad a las orientaciones que minimicen los soportes internos o los sitúen en lugares accesibles.
- Técnicas de eliminación: Emplee una cuidadosa eliminación manual, micromecanizado o, potencialmente, métodos electroquímicos cuando proceda. Presupueste tiempo y recursos suficientes para este paso.
3. Resolución de rasgos finos y paredes delgadas:
- Asunto: Dificultad para producir de forma coherente y precisa características muy pequeñas (por ejemplo, clavijas, pequeños orificios) o paredes finas por debajo de los límites de capacidad del proceso. Las características pueden estar incompletas, distorsionadas o carecer de definición.
- Causas: Limitaciones del tamaño del punto láser/rayo, tamaño de las partículas de polvo, acumulación de calor en características pequeñas, ajustes del grosor de la capa.
- Soluciones:
- DfAM: Evite diseñar características por debajo de los límites de proceso establecidos. Utilice filetes en lugar de esquinas afiladas en secciones finas.
- Selección de máquina/proceso: Elija una máquina y un conjunto de parámetros optimizados para alta resolución si las características finas son críticas. La EBM suele tener una resolución menor que la LPBF.
- Optimización de parámetros: Ajuste con precisión la potencia del láser, la velocidad de escaneado y el enfoque específicamente para características pequeñas (a menudo requiere conocimientos de expertos).
- Elección de materiales: Algunos materiales pueden resolver las características mejor que otros.
4. Eliminación incompleta del polvo:
- Asunto: Polvo residual sin fundir atrapado en canales internos, cavidades o estructuras reticulares complejas tras la impresión y la limpieza estándar. Se trata de un riesgo importante para la biocompatibilidad de los productos sanitarios.
- Causas: Geometrías internas complejas sin vías de escape, procedimientos de limpieza insuficientes, adhesión/sinterización de partículas de polvo.
- Soluciones:
- DfAM: Diseñe canales internos con curvas suaves, diámetro suficiente y puertos de entrada/salida específicos para la eliminación del polvo y la circulación del líquido de limpieza. Evite las cavidades sin salida.
- Orientación: Oriente la pieza para facilitar el drenaje del polvo durante el proceso de construcción y arranque.
- Procedimientos de limpieza: Emplear protocolos de limpieza rigurosos y validados que pueden implicar vibración, flujo de aire/gas comprimido, limpieza ultrasónica en disolventes específicos y múltiples ciclos de aclarado.
- Inspección: Utilice métodos como la endoscopia o el escaneado micro-CT para verificar la eliminación completa del polvo de las zonas internas críticas.
5. Calidad y rugosidad de las superficies:
- Asunto: La rugosidad de la superficie, el escalonamiento en superficies curvas o las partículas parcialmente sinterizadas adheridas a la superficie pueden ser inaceptables para la función o la biocompatibilidad.
- Causas: Naturaleza del proceso estratificado, tamaño de las partículas de polvo, dinámica del baño de fusión, puntos de contacto del soporte, superficies orientadas hacia abajo.
- Soluciones:
- Orientación: Optimice la orientación de la pieza para colocar las superficies críticas en posiciones orientadas hacia arriba o verticales siempre que sea posible.
- Optimización de parámetros: Un grosor de capa más fino y unos parámetros de escaneado de contornos optimizados pueden mejorar la calidad de las paredes laterales.
- Post-procesamiento: Aplicar técnicas adecuadas de acabado de superficies (granallado, volteo, pulido, electropulido) según sea necesario para cumplir las especificaciones.
- DfAM: Utilice filetes en lugar de bordes afilados donde se necesite un acabado alto para mitigar los efectos de escalonamiento.
6. Garantizar la biocompatibilidad y la limpieza:
- Asunto: Garantizar que la pieza final esté libre de contaminantes (polvo, fluidos de procesamiento, endotoxinas bacterianas) y que el propio material no lixivie iones nocivos ni provoque reacciones adversas.
- Causas: Limpieza inadecuada, manipulación incorrecta del material, contaminación cruzada, elección o procesamiento subóptimo del material.
- Soluciones:
- Certificación de materiales: Utilizar únicamente polvos certificados de calidad médica de proveedores acreditados como Met3dp. Mantenga una estricta trazabilidad de los materiales.
- Control de procesos: Implemente controles rigurosos en todo el flujo de trabajo de AM y postprocesamiento para evitar la contaminación. Si es posible, utilice equipos específicos para piezas médicas.
- Limpieza validada: Desarrollar y validar procedimientos de limpieza específicos para la geometría y el material de la pieza con el fin de garantizar la eliminación de todos los residuos hasta niveles aceptables (que a menudo requieren análisis químicos o pruebas biológicas).
- Pruebas de biocompatibilidad: Realice las pruebas de biocompatibilidad necesarias (por ejemplo, citotoxicidad, sensibilización, pruebas de implantación según ISO 10993) en piezas finales esterilizadas o cupones representativos producidos a través de exactamente la misma cadena de proceso.
Con éxito solución de problemas de impresión 3D y desafíos requiere una combinación de experiencia en AMD, un meticuloso control del proceso, un postprocesado adecuado y una rigurosa garantía de calidad. Asociarse con un proveedor de AM experimentado que entienda las demandas específicas de la industria médica es crucial para sortear estas complejidades y ofrecer estructuras de sensores biomédicos seguras y eficaces.
Selección de socios: Cómo elegir el proveedor de servicios de impresión 3D sobre metal adecuado
No todos los proveedores de servicios de AM metálica son iguales, especialmente cuando se trata de los estrictos requisitos del sector de dispositivos médicos. Seleccionar un socio implica evaluar mucho más que sus capacidades de impresión; requiere una evaluación exhaustiva de sus sistemas de calidad, experiencia en materiales, cumplimiento de la normativa, asistencia técnica y experiencia general con aplicaciones médicas. Encontrar una empresa capaz y de confianza fabricante por contrato de productos sanitarios especializarse en AM es clave.
Criterios de evaluación crítica:
- Sistema de gestión de la calidad (SGC) y certificaciones:
- Certificación ISO 13485: Se trata de la norma internacional de SGC para la fabricación de productos sanitarios. Aunque no todos los proveedores de AM tienen esta certificación (ya que pueden suministrar componentes a fabricantes de dispositivos certificados), un proveedor con ISO 13485 demuestra su compromiso con los rigurosos controles de procesos, documentación, trazabilidad y gestión de riesgos que requieren los componentes médicos. Además, agiliza considerablemente el proceso de cualificación de los fabricantes de dispositivos médicos. Aunque no esté certificado, investigue a fondo la estructura de su SGC y cómo se ajusta a los principios de la norma ISO 13485.
- Certificación ISO 9001: Una certificación fundamental para la gestión de la calidad, que indica procesos establecidos para la coherencia y la satisfacción del cliente. Es un requisito mínimo para cualquier socio serio de fabricación industrial.
- Elementos sólidos del SGC: Busque pruebas de procedimientos bien documentados de entrada de pedidos, validación de procesos, formación de operarios, calibración y mantenimiento de equipos, manipulación y trazabilidad de materiales, gestión de no conformidades, acciones correctivas y preventivas (CAPA) e inspección final. Garantía de calidad de la fabricación aditiva deben estar profundamente arraigadas en sus operaciones.
- Experiencia en materiales y trazabilidad:
- Manipulación de materiales de grado médico: ¿Tienen experiencia en la impresión con las aleaciones biocompatibles específicas que necesita (por ejemplo, Ti-6Al-4V ELI según ASTM F136, 316L según ASTM F138)?
- Abastecimiento y control de polvos: ¿De dónde proceden sus polvos? ¿Utilizan polvos certificados de calidad médica? ¿Cuáles son sus procedimientos de inspección del polvo entrante, manipulación, almacenamiento (para evitar la contaminación y la degradación) y reciclado/reutilización (incluido el seguimiento de los lotes de polvo y la limitación de los ciclos de reutilización)? Los proveedores reputados como Met3dp, que fabrican sus propios polvos metálicos esféricos de alta calidad utilizando las avanzadas tecnologías VIGA y PREP, ofrecen una clara ventaja a la hora de controlar la calidad del polvo desde el origen.
- Certificaciones de materiales y trazabilidad: ¿Pueden proporcionar certificaciones completas de los materiales (certificados de conformidad/análisis) para cada lote de polvo utilizado? ¿Mantienen una trazabilidad que vincule la pieza final con el lote de polvo específico, el funcionamiento de la máquina y los parámetros de procesamiento utilizados? Esto no es negociable en el caso de los productos sanitarios.
- Capacidades de los equipos y control de procesos:
- Coincidencia tecnológica: ¿Operan con la tecnología de AM adecuada (por ejemplo, LPBF, EBM) que mejor se adapte al material, la complejidad y las características necesarias de la estructura del sensor?
- Calidad y mantenimiento de la máquina: ¿Utilizan sistemas AM industriales conocidos por su fiabilidad y precisión? ¿Cuáles son sus programas de calibración y mantenimiento preventivo? Met3dp hace hincapié en su volumen de impresión, precisión y fiabilidad líderes en la industria para piezas de misión crítica.
- Supervisión y validación de procesos: ¿Emplean capacidades de supervisión in situ (por ejemplo, supervisión del baño de fusión)? ¿Han validado sus procesos de impresión para los materiales y parámetros específicos utilizados para los componentes médicos? Pida pruebas de la estabilidad y repetibilidad del proceso.
- Capacidades de postprocesamiento y validación:
- Interno vs. Subcontratado: ¿Realizan los pasos críticos de postprocesado (alivio de tensiones, HIP, mecanizado, pulido, limpieza) internamente o a través de subcontratistas cualificados? Las capacidades internas suelen ofrecer un mejor control de todo el flujo de trabajo y plazos de entrega potencialmente más cortos.
- Experiencia y equipamiento: ¿Disponen del equipo y los conocimientos necesarios para pasos como el mecanizado CNC de alta precisión, diversas técnicas de acabado de superficies y procesos de limpieza validados adecuados para dispositivos médicos?
- Validación: ¿Se han validado sus pasos posteriores al tratamiento, especialmente la limpieza y, potencialmente, la compatibilidad con la esterilización?
- Apoyo de ingeniería y experiencia en DfAM:
- Colaboración: ¿Están dispuestos a colaborar con su equipo de ingenieros desde las primeras fases del diseño?
- Orientación del DfAM: ¿Pueden proporcionar asesoramiento experto sobre la optimización del diseño del bastidor del sensor para la fabricación aditiva (DfAM), incluida información sobre la orientación, las estrategias de soporte, la viabilidad de las características y las oportunidades de reducción de costes?
- Resolución de problemas: ¿Disponen de ingenieros de aplicaciones experimentados que puedan ayudar a resolver posibles problemas de fabricación? Met3dp, con sus décadas de experiencia colectiva, ofrece explícitamente servicios de desarrollo de aplicaciones junto con sus impresoras y polvos.
- Experiencia con productos sanitarios:
- Historial: ¿Pueden demostrar que tienen experiencia en la fabricación de componentes para aplicaciones médicas, en particular piezas de complejidad o requisitos de material similares? Solicite estudios de casos o ejemplos (no confidenciales).
- Comprensión del panorama normativo: ¿Comprenden el contexto normativo (por ejemplo, los requisitos de la FDA, MDR en Europa) y la importancia de la documentación y la validación de los componentes de los productos sanitarios?
- Capacidades de inspección y metrología:
- Equipamiento: ¿Disponen de equipos de inspección adecuados (MMC, escáneres 3D, perfilómetros de superficie, herramientas de inspección visual y, potencialmente, END como la tomografía computarizada) para verificar que las piezas cumplen todas las especificaciones?
- Informar: ¿Pueden proporcionar informes de inspección detallados que documenten el cumplimiento de las dimensiones críticas, las tolerancias y los requisitos de acabado superficial?
- Confidencialidad y protección de la propiedad intelectual:
- NDA: ¿Están dispuestos a firmar acuerdos de confidencialidad para proteger su propiedad intelectual sensible?
- Seguridad: ¿De qué medidas disponen para garantizar la seguridad de los datos de los archivos CAD y la información del proyecto?
- Comunicación, gestión de proyectos y logística:
- Capacidad de respuesta: ¿Responden a las preguntas y ofrecen una comunicación clara durante todo el ciclo de vida del proyecto?
- Gestión de proyectos: ¿Asignan un punto de contacto específico? ¿Cómo gestionan los plazos del proyecto y proporcionan actualizaciones?
- Localización y envío: Tenga en cuenta su ubicación con respecto a la suya para conocer los plazos y costes de envío, aunque en el caso de los componentes médicos de alto valor, las capacidades suelen tener más peso que la proximidad.
Auditoría de proveedores: En el caso de los componentes médicos críticos, es muy recomendable realizar una auditoría in situ o a distancia exhaustiva de los posibles proveedores en función de estos criterios antes de establecer una asociación. Elegir al socio adecuado es invertir en calidad, fiabilidad y, en última instancia, en la seguridad del paciente. Empresas como Met3dp, que se posicionan como proveedores de soluciones integrales que abarcan impresoras, polvos avanzados y servicios de aplicación, pretenden cumplir estos exigentes criterios para sectores como el aeroespacial, el médico y el de automoción.

Comprender la inversión: Factores de coste y plazos típicos de producción
Aunque la AM metálica ofrece ventajas significativas, es esencial conocer los factores que determinan el coste y el plazo de producción de los bastidores de sensores biomédicos. Esto permite elaborar presupuestos precisos, planificar proyectos realistas y tomar decisiones con conocimiento de causa a la hora de comparar la AM con los métodos tradicionales o evaluar presupuestos de distintos proveedores de servicios. Solicitud de presupuestos detallados para estimación de costes de impresión 3D de metales es una práctica estándar.
Principales factores de coste:
- Coste del material:
- Tipo de aleación: Los metales biocompatibles como el Ti-6Al-4V ELI son significativamente más caros por kilogramo que el acero inoxidable 316L de calidad médica u otras aleaciones no médicas.
- Consumo de polvo: Esto depende del volumen de la pieza (incluido el material de mecanizado) y del volumen de las estructuras de soporte necesarias. Un DfAM eficiente (por ejemplo, aligeramiento, minimización de soportes) reduce directamente el consumo de material.
- Calidad del polvo: Los polvos de gran pureza y riguroso control necesarios para aplicaciones médicas suelen tener un precio elevado.
- Tiempo de máquina / Tiempo de impresión:
- Volumen y altura de la pieza: Las piezas más grandes o más altas (en la orientación de construcción) tardan más en imprimirse.
- Número de capas: Determinado por la altura de la pieza y el grosor de capa seleccionado (las capas más finas aumentan el tiempo de impresión pero mejoran el acabado superficial/la resolución).
- Estrategia de escaneo: La complejidad de la trayectoria de exploración del láser/rayo afecta al tiempo.
- Máquina Tarifa por hora: Los proveedores de servicios tienen en cuenta la amortización, el mantenimiento, el funcionamiento y los gastos generales de sus costosos sistemas AM industriales. Las tarifas varían en función del tipo de máquina, el tamaño y la ubicación.
- Eficiencia de anidamiento: La impresión simultánea de varias piezas en una fabricación (anidado) puede reducir significativamente el coste de tiempo de máquina por pieza al compartir los tiempos de preparación y ciclo. Esto es crucial para servicios de impresión 3D al por mayor con vistas a la producción en serie.
- Costes laborales:
- Configuración: Preparación del archivo de construcción, configuración de la máquina, carga de polvo.
- Breakout: Desmontaje de la placa de impresión, separación de las piezas, limpieza y eliminación inicial del polvo.
- Retirada del soporte: Suele ser un proceso manual o semiautomatizado que requiere técnicos cualificados; la complejidad influye mucho en este coste.
- Post-procesamiento: Mano de obra de mecanizado, pulido, limpieza, inspección, etc. La mano de obra altamente cualificada para tareas como el pulido complejo puede ser un factor de coste significativo.
- Ingeniería/Programación: El asesoramiento DfAM, la optimización de la preparación de la construcción o la programación CNC para el mecanizado posterior pueden conllevar gastos aparte o estar incluidos en el coste total.
- Estructuras de apoyo:
- Volumen de material: Los soportes consumen material, lo que aumenta el coste.
- Coste de retirada: Como ya se ha señalado, la mano de obra y el tiempo necesarios para la retirada constituyen un coste directo. Los soportes difíciles de retirar lo aumentan considerablemente.
- Costes de postprocesamiento:
- Tratamiento térmico: Tiempo del horno, consumo de energía, uso de gas inerte.
- HIP: Se trata de un proceso especializado de alto coste que suele subcontratarse y que aumenta considerablemente el coste por pieza, pero que resulta esencial para aplicaciones críticas.
- Mecanizado: Tiempo de máquina CNC, herramientas, programación y costes de mano de obra. El coste depende en gran medida del grado de mecanizado necesario y de las exigencias de tolerancia.
- Acabado superficial: Los costes varían mucho en función del método (el granallado es relativamente barato, el pulido manual en varias etapas es caro) y del valor Ra final requerido.
- Limpieza y pasivado: Costes asociados a equipos especializados, productos químicos, procesos validados y mano de obra.
- Garantía de calidad e inspección:
- Nivel de inspección: Controles dimensionales básicos frente a informes exhaustivos de MMC, mediciones de rugosidad superficial, END (escaneado por TC), pruebas de limpieza... cada uno de ellos añade costes.
- Documentación: Generar la documentación detallada de trazabilidad y calidad que requieren los productos sanitarios requiere tiempo y recursos.
- Cantidad del pedido:
- Amortización de la configuración: Los costes fijos de preparación se amortizan sobre el número de piezas de un lote. A mayores cantidades, menores costes por pieza.
- Descuentos por volumen: Los proveedores pueden ofrecer precios escalonados para grandes tiradas de producción.
Plazos de entrega típicos:
Plazos de entrega de la fabricación aditiva se ven influidas por varios factores, y es fundamental comprender su desglose:
- Presupuesto y procesamiento de pedidos: Puede oscilar entre horas (para presupuestos automatizados en línea de piezas sencillas) y varios días (para piezas complejas que requieren revisión manual y consulta a DfAM).
- Tiempo de cola: Dependiendo de la disponibilidad de las máquinas y de la acumulación de trabajo del proveedor de servicios, su trabajo puede esperar en una cola antes de que se inicie la impresión. Este tiempo puede variar de días a semanas.
- Tiempo de impresión: Muy variable en función del tamaño de la pieza, la complejidad y el anidado. Puede variar desde varias horas para piezas pequeñas hasta varios días para piezas grandes o placas de construcción completas.
- Tiempo de post-procesamiento: Esto a menudo puede llevar mucho tiempo más largo que el propio tiempo de impresión. El alivio de tensiones, el HIP (si es necesario, a menudo requiere una programación por lotes), la eliminación de soportes, el mecanizado, el pulido exhaustivo y los rigurosos ciclos de limpieza/inspección pueden añadir días o incluso semanas al plazo total de entrega.
- Envío: Los plazos de envío estándar dependen de la ubicación.
Plazos estimados (Orientaciones generales):
- Prototipos (Simples, post-procesamiento mínimo): 5 – 15 días laborables
- Prototipos (Complejo, amplio post-procesamiento): 2 – 4 semanas
- Producción de bajo volumen (por ejemplo, < 50 unidades): 3 – 6 semanas
- Producción de volumen medio (por ejemplo, cientos de unidades): 5 – 10 semanas+ (muy dependiente de la complejidad de la pieza y el proceso)
Lo más importante: Obtenga presupuestos detallados en los que se especifiquen todas las etapas incluidas y los costes asociados. Discuta con antelación los plazos de entrega y conozca el tiempo necesario para cada etapa, en particular el postprocesamiento, a fin de elaborar calendarios de proyecto realistas.
Preguntas frecuentes sobre marcos de sensores biomédicos impresos en 3D
He aquí las respuestas a algunas de las preguntas más frecuentes que se hacen los ingenieros y responsables de compras cuando se plantean la AM metálica para armazones de sensores biomédicos:
P1: ¿Son realmente biocompatibles las estructuras metálicas de los sensores impresos en 3D? A: Sí, siempre que se sigan los procedimientos correctos. La biocompatibilidad depende principalmente de:
- Elección de materiales: La base es utilizar aleaciones certificadas de calidad médica conocidas por su biocompatibilidad (como Ti-6Al-4V ELI conforme a ASTM F136 o 316L de calidad para implantes conforme a ASTM F138).
- Control de procesos: Garantizar que el propio proceso de AM no introduzca contaminantes y alcance una alta densidad para evitar la lixiviación no deseada. Es fundamental asociarse con proveedores con experiencia en aplicaciones médicas, como Met3dp, que hacen hincapié en la pureza del polvo y el control del proceso.
- Post-procesamiento: Una limpieza minuciosa y validada es absolutamente crítica para eliminar todas las partículas de polvo residuales y los fluidos de procesamiento. Los tratamientos superficiales como el pulido o el electropulido pueden mejorar aún más la biocompatibilidad al crear superficies más lisas y pasivas.
- Pruebas: La confirmación final a menudo requiere pruebas de biocompatibilidad (según las normas ISO 10993) en piezas producidas utilizando el proceso de fabricación exacto (impresión + todos los pasos posteriores al procesamiento), especialmente para dispositivos implantables.
P2: ¿Qué nivel de detalle, miniaturización y paredes finas puede alcanzarse de forma realista en los bastidores de los sensores? A: El nivel alcanzable depende del proceso específico de AM (LPBF suele ofrecer mayor resolución que EBM), la máquina utilizada, el material y los parámetros optimizados del proceso.
- Tamaño mínimo de característica: Normalmente, entre 0,2 mm y 0,4 mm, pero puede variar. Los elementos positivos muy pequeños (como los pasadores) pueden resultar difíciles debido a la concentración de calor. Los orificios pequeños pueden requerir un taladrado o escariado secundario para obtener una mayor precisión.
- Espesor mínimo de pared: Por lo general, entre 0,3 mm y 0,5 mm, pero se recomiendan paredes más gruesas por razones de integridad estructural, sobre todo si es necesario un tratamiento posterior importante (como el pulido). El diseño por debajo de estos límites requiere una cuidadosa validación.
- Miniaturización general: La AM destaca en la creación de geometrías complejas en paquetes pequeños, lo que permite una miniaturización significativa en comparación con el ensamblaje de múltiples piezas mecanizadas. Comente los requisitos específicos con su proveedor de AM al principio de la fase de diseño.
P3: ¿Cuál es el coste de la impresión metálica en 3D en comparación con la fabricación tradicional (mecanizado CNC, MIM) para armazones de sensores? A: La comparación de costes depende en gran medida de complejidad de las piezas y volumen de producción:
- Complejidad: Para geometrías muy complejas (canales internos, celosías, formas orgánicas) que son difíciles o imposibles de mecanizar, la AM suele ser más rentable incluso con volúmenes bajos, ya que evita complejas configuraciones, utillajes y pasos de montaje.
- Volumen:
- Prototipos & Bajo volumen (1-100s): La AM suele ser muy competitiva o más barata que la CNC (debido a la ausencia de utillaje y a la mínima configuración por su complejidad) y mucho más barata que el MIM (que tiene unos costes de utillaje muy elevados).
- Volumen medio (100s-1000s): Esta suele ser la zona de transición. Las piezas muy complejas pueden seguir favoreciendo la AM, mientras que las más sencillas pueden abaratarse mediante CNC. El MIM empieza a ser viable si la complejidad no es extrema.
- Gran volumen (10.000+): Para geometrías más sencillas, el mecanizado CNC o, sobre todo, el MIM (si la pieza es adecuada) serán, por lo general, más rentables que los actuales procesos de AM metálica, debido a los tiempos de ciclo más rápidos y a los menores costes por pieza a escala.
- Otros factores: La capacidad de la AM para consolidar piezas puede suponer un ahorro de costes a nivel de sistema (reducción del ensamblaje y del inventario). Las ventajas de la AM en cuanto a plazos de entrega para la creación de prototipos también pueden representar un valor significativo.
P4: ¿Son compatibles los marcos de sensores Ti-6Al-4V ELI y 316L impresos en 3D con los métodos de esterilización médica estándar? A: Sí. Tanto el Ti-6Al-4V ELI como el acero inoxidable 316L, ya sean forjados o producidos mediante AM con un postprocesado adecuado (especialmente la limpieza), son compatibles con los métodos de esterilización médica habituales, incluidos:
- Autoclavado (esterilización por vapor): El método más común.
- Esterilización por gas de óxido de etileno (EtO): Adecuado, pero requiere una correcta aireación posterior.
- Esterilización por radiación gamma: Generalmente compatible, aunque dosis muy elevadas podrían afectar mínimamente a las propiedades de algunos materiales (menos preocupante para los metales que para los polímeros).
- Plasma de gas de peróxido de hidrógeno a baja temperatura: También suelen ser compatibles. Es crucial que las piezas se limpien a fondo antes de esterilización, ya que cualquier contaminante residual podría comprometer el proceso o provocar el fallo del dispositivo.
P5: ¿Cómo podemos verificar que los complejos canales internos de un marco de sensor están libres de polvo residual? A: Se trata de una preocupación fundamental, especialmente en el caso de los dispositivos implantables. Los métodos de verificación incluyen:
- Diseño para inspección (DfI): Cuando sea posible, diseñe canales con puertos de entrada/salida lo suficientemente grandes como para permitir la inspección visual mediante boroscopios o microcámaras.
- Validación del proceso: Validar rigurosamente el proceso de limpieza utilizando cupones de prueba o piezas representativas, analizando potencialmente los fluidos de aclarado para determinar el recuento de partículas.
- Ensayos no destructivos (END): Alta resolución Microtomografía computarizada (Micro-CT scanning) es el método más eficaz para visualizar y confirmar de forma no destructiva la ausencia de polvo en geometrías internas complejas. Aunque supone un coste adicional, proporciona pruebas definitivas y suele emplearse en componentes médicos críticos durante la validación del proceso o en un muestreo durante la producción.
Abordar estos FAQ metal impresión 3D médica destaca la importancia de la comprensión técnica y la estrecha colaboración con socios expertos en AM.
Conclusiones: El futuro es preciso: fabricación aditiva para sensores biomédicos avanzados
El intrincado mundo de los sensores biomédicos exige soluciones de fabricación que ofrezcan precisión, integridad de los materiales, libertad de diseño y la capacidad de crear componentes cada vez más complejos y personalizados. Como hemos analizado a lo largo de este artículo, la fabricación aditiva de metales está a la altura de este reto y ofrece un potente conjunto de herramientas a los ingenieros y fabricantes de dispositivos médicos que se esfuerzan por innovar.
Desde la fabricación de armazones de implantes ligeros y específicos para cada paciente en Ti-6Al-4V ELI hasta la producción de robustas carcasas de sensores integrados en 316L para herramientas de diagnóstico, las ventajas del impresión 3D en metal son claras:
- Libertad de diseño sin precedentes: Creación de canales internos complejos, características integradas y formas orgánicas antes inalcanzables.
- La personalización en masa: Soluciones específicas para cada paciente y producción de bajo volumen económicamente viable.
- Innovación acelerada: La creación rápida de prototipos acorta drásticamente los ciclos de desarrollo.
- Rendimiento optimizado: El aligeramiento mediante celosías y la optimización de la topología mejoran la función del dispositivo y la comodidad del paciente.
- Materiales de alto rendimiento: Compatibilidad con aleaciones biocompatibles probadas como Ti-6Al-4V ELI y 316L.
Sin embargo, aprovechar este potencial requiere algo más que el acceso a una impresora. Exige un enfoque holístico que abarque el diseño estratégico para la fabricación aditiva (DfAM), una atención meticulosa al control del proceso, un posprocesamiento riguroso y validado (especialmente la limpieza) y una garantía de calidad estricta. Para hacer frente a los posibles retos, desde la gestión de la tensión residual hasta la eliminación completa del polvo, se requiere experiencia y diligencia.
La selección de un socio de fabricación se convierte en un factor crítico para el éxito. Busque proveedores que demuestren no sólo competencia técnica, sino también un profundo conocimiento de los requisitos exclusivos del sector médico en materia de calidad, trazabilidad y conformidad. Socios como Met3dp, que ofrecen soluciones integrales -desde el desarrollo y la fabricación de polvos metálicos esféricos avanzados de gran pureza y sistemas de impresión líderes del sector hasta la prestación de servicios expertos de desarrollo de aplicaciones- son aliados inestimables en este camino. Su compromiso con la calidad y la innovación encaja a la perfección con las necesidades del sector futuro de la fabricación médica.
La fabricación aditiva de metales ya no es una novedad futurista, sino una realidad actual que está dando forma a la próxima generación de sensores y dispositivos biomédicos. Al adoptar la AM, las empresas pueden crear herramientas de diagnóstico más eficaces, instrumentos quirúrgicos menos invasivos, dispositivos portátiles más cómodos e implantes verdaderamente personalizados, lo que en última instancia contribuye a mejorar los resultados de los pacientes. A medida que la tecnología siga madurando, ofreciendo mayor precisión, velocidades más rápidas y una cartera de materiales cada vez más amplia, su impacto en la innovación sanitaria no dejará de crecer.
Para saber cómo los sistemas de vanguardia, los polvos metálicos de alto rendimiento y la amplia experiencia en fabricación aditiva de Met3dp’ pueden potenciar el desarrollo en su organización de estructuras de sensores biomédicos avanzados y otros componentes médicos críticos, visite Met3dp o póngase en contacto con su equipo hoy mismo. Construyamos juntos el futuro de la asistencia sanitaria de precisión.
Compartir
MET3DP Technology Co., LTD es un proveedor líder de soluciones de fabricación aditiva con sede en Qingdao, China. Nuestra empresa está especializada en equipos de impresión 3D y polvos metálicos de alto rendimiento para aplicaciones industriales.
Solicite información para obtener el mejor precio y una solución personalizada para su empresa.
Artículos relacionados
Acerca de Met3DP
Actualización reciente
Nuestro producto
CONTACTO
¿Tiene alguna pregunta? ¡Envíenos un mensaje ahora! Atenderemos su solicitud con todo un equipo tras recibir su mensaje.
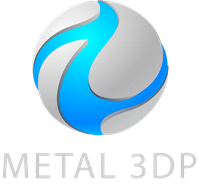
Polvos metálicos para impresión 3D y fabricación aditiva