3D Printed Custom Mounts for Electronic Devices
Índice
In the rapidly evolving landscape of technology, electronic devices are becoming increasingly sophisticated, powerful, and integrated into virtually every aspect of modern industry and life. From critical control systems in aerospace and automotive applications to life-saving medical equipment and the complex machinery driving industrial automation, the performance and reliability of these electronics are paramount. However, the optimal function of these devices often hinges on a seemingly simple, yet critically important component: the mount or bracket that secures them. Standard, off-the-shelf mounting solutions frequently fall short, unable to meet the unique demands of specialized equipment, harsh operating environments, or complex spatial constraints. This is where custom electronics mounts become essential, and where metal additive manufacturing (AM), or Impresión 3D, emerges as a revolutionary enabling technology.
Introduction: The Critical Role of Custom Mounts for Modern Electronics
At its core, a custom electronics mount is a bespoke piece of hardware designed specifically to hold, position, protect, and sometimes enhance the function of an electronic device or component within a larger system. Unlike mass-produced brackets designed for generic applications, custom mounts are engineered-to-order, taking into account the precise dimensions of the device, the specific environmental stresses it will encounter, the required orientation, necessary connections, thermal management needs, and integration with surrounding structures.
The Limitations of Standard Solutions
Procurement managers and engineers often face significant challenges when relying solely on standard mounting hardware sourced from general industrial suppliers or distributors. These challenges can compromise system performance, reliability, and even safety:
- Improper Fit: Standard brackets rarely match the exact form factor of specialized electronic modules, sensors, or circuit boards. This can lead to insecure mounting, wasted space, difficulty with cable management, or even damage to the device from concentrated stress points.
- Inadequate Performance in Harsh Environments: Off-the-shelf mounts, often made from basic stamped steel or injection-molded plastic, may not withstand the demanding conditions found in many B2B applications. Factors include:
- Vibraciones y choques: High vibration levels in automotive, aerospace, or heavy industrial machinery can cause standard mounts to fatigue, loosen, or fail, potentially leading to catastrophic failure of the electronics they hold. Custom mounts can be designed with specific damping properties or engineered for superior fatigue life.
- Temperature Extremes: Electronics generate heat, and operating environments can range from cryogenic lows to extreme highs. Standard mounts may lack the necessary thermal conductivity to act as effective heat sinks or may degrade under thermal cycling.
- Corrosión: Exposure to moisture, chemicals, or saline environments (common in marine, medical, or certain industrial settings) can quickly degrade standard materials. Custom mounts allow for the selection of specific corrosion-resistant alloys.
- Lack of Functional Integration: Modern electronic systems often require mounts that do more than just hold a device. They might need integrated heat sinks, specific vibration damping characteristics, channels for cable routing, precise alignment features for sensors, or even integrated shielding against electromagnetic interference (EMI). Standard solutions typically lack this level of functional integration.
- Design Constraints and Assembly Complexity: Trying to adapt standard brackets often leads to cumbersome workarounds, additional fasteners, adapter plates, and increased assembly time and complexity. This inflates labor costs and introduces potential points of failure.
- Supply Chain Issues for Niche Needs: Finding a reliable wholesale supplier for a very specific, non-standard bracket configuration can be difficult and lead times can be long, especially for low-volume requirements typical of specialized industrial equipment or aerospace projects.
Metal Additive Manufacturing: A Paradigm Shift for Custom Mounts
Metal 3D printing fundamentally changes the equation for creating custom electronics mounts. Instead of machining parts from solid blocks (subtractive manufacturing) or investing in expensive tooling for casting or molding, AM builds parts layer-by-layer directly from metal powder based on a digital design file. This additive approach unlocks unprecedented possibilities:
- Libertad de diseño sin igual: Engineers are no longer bound by the constraints of traditional manufacturing. Complex internal structures, organic shapes optimized for strength and weight, consolidated assemblies, and integrated functional features become feasible.
- Rapid Customization and Prototyping: New mount designs can be prototyped and tested in days, not weeks or months. This accelerates development cycles and allows for rapid iteration based on real-world performance feedback.
- Economical Low-to-Medium Volume Production: AM eliminates the need for tooling, making it highly cost-effective for producing custom mounts in quantities ranging from one-off prototypes to hundreds or even thousands of parts. This aligns perfectly with the needs of specialized equipment manufacturers and B2B projects requiring bespoke solutions.
- Rendimiento del material: A wide range of high-performance metal alloys can be utilized, allowing engineers to select the optimal material based on specific requirements for strength, weight, thermal conductivity, corrosion resistance, or biocompatibility.
Leading the charge in harnessing this potential is Met3dp Technology Co., LTD. As a premier provider of additive manufacturing solutions, Met3dp specializes in both industry-leading impresión 3D en metal equipment, including high-performance Selective Electron Beam Melting (SEBM) systems, and the development and production of advanced metal powders tailored for AM. Their expertise empowers engineers and procurement managers across demanding industries to leverage the transformative power of AM for creating superior custom electronics mounts. The procurement landscape is shifting; forward-thinking companies are moving beyond simply sourcing standard parts from distributors and are partnering with AM specialists like Met3dp to co-develop high-performance, application-specific hardware solutions.
Applications Across Industries: Where are Custom Metal 3D Printed Mounts Used?
The versatility and performance benefits of metal 3D printed custom mounts have led to their adoption across a diverse range of demanding B2B sectors. The ability to create highly specific, optimized, and durable mounting solutions solves critical challenges where off-the-shelf hardware simply cannot perform.
1. Aeroespacial y defensa:
The aerospace industry operates under the most stringent requirements for performance, reliability, and weight savings. Every gram saved translates to fuel efficiency or increased payload capacity. Furthermore, components must withstand extreme temperatures, high vibration, and significant G-forces.
- Avionics Bays: Securely mounting sensitive flight control computers, communication systems, and navigation equipment within tightly packed avionics bays. Metal AM allows for mounts conforming perfectly to complex internal aircraft structures, often integrating cooling channels or vibration damping features. Topology optimization plays a huge role in creating mounts that are incredibly strong yet lightweight.
- UAV/Drone Sensor Mounts: Unmanned Aerial Vehicles require lightweight, rigid mounts for high-resolution cameras, LiDAR units, and other sensors. Custom 3D printed mounts ensure precise alignment, crucial for data accuracy, while minimizing overall aircraft weight. The ability to rapidly prototype different sensor configurations is invaluable for UAV platform development. Sourcing such specialized components often requires engaging directly with an de componentes aeroespaciales specializing in AM.
- Ruggedized Enclosures & Brackets: Protecting electronics in harsh military environments requires robust mounting solutions. Metal AM can produce durable brackets and partial enclosures from high-strength alloys, capable of meeting rigorous MIL-STD specifications for shock, vibration, and environmental sealing. Considerations for ITAR compliance may also steer procurement towards specialized manufacturing partners.
- Componentes del satélite: In the vacuum of space, thermal management is critical, and outgassing must be minimized. Custom mounts made from materials like Aluminum alloys (e.g., AlSi10Mg) offer good thermal conductivity paths, while the AM process allows for designs that minimize trapped volumes.
2. Automotriz:
The automotive industry, particularly with the rise of electric vehicles (EVs) and advanced 1 driver-assistance systems (ADAS), faces increasing complexity in electronics integration. Components must endure constant vibration, varying temperatures, and potential exposure to fluids and impacts.
1. www.persistencemarketresearch.com
www.persistencemarketresearch.com
- ECU (Engine Control Unit) Brackets: Securely mounting ECUs in locations that optimize wiring and minimize exposure to heat or vibration. Custom mounts can be designed to fit specific under-hood or cabin locations, often incorporating features to aid thermal dissipation.
- Sensor Housings & Mounts: ADAS rely on numerous sensors (cameras, radar, LiDAR) precisely positioned around the vehicle. Metal AM enables the creation of rigid, complex mounts ensuring stable alignment, critical for system accuracy. Integration with vehicle bodywork or specific chassis points is simplified. Finding a Tier 1 automotive supplier capable of rapid prototyping and low-volume production of these custom mounts is crucial.
- Dashboard & Infotainment Integration: Creating bespoke brackets for integrating large display screens, control modules, or specialized communication equipment seamlessly into vehicle interiors. AM allows for aesthetically pleasing designs that match interior contours.
- EV Battery & Power Electronics: Mounting and managing components within EV battery packs and power electronics modules requires solutions that handle significant weight, provide thermal pathways, and ensure electrical isolation. Custom AlSi10Mg mounts are often used for their combination of low weight and good thermal conductivity, becoming essential EV thermal management wholesale components. Compliance with standards like IATF 16949 is a key consideration when selecting a manufacturing partner.
3. Medical:
The medical field demands high precision, reliability, biocompatibility, and often, sterilizability. Custom mounts are essential for integrating electronics into diagnostic equipment, surgical tools, and patient monitoring devices.
- Diagnostic Equipment Mounting: Securing circuit boards, power supplies, and sensors within MRI machines, CT scanners, ultrasound devices, and laboratory analysis equipment. Metal AM allows mounts to be designed around existing internal components, maximizing space utilization and ensuring rigidity. Materials like 316L stainless steel offer excellent cleanability and corrosion resistance.
- Surgical Tool & Robotic Integration: Mounting control electronics, sensors, or illumination sources onto surgical instruments or robotic arms. These mounts must often be lightweight, ergonomic, and capable of withstanding repeated sterilization cycles (e.g., autoclaving), making 316L a prime material choice. Procurement often involves sourcing from an ISO 13485 certified manufacturing compañero.
- Wearable & Patient Monitoring Devices: Creating custom, conformal housings and mounts for electronics worn by patients. While often polymer-based, metal AM can be used for structural elements or when specific properties like EMI shielding or durability are needed. Biocompatible materials are essential.
- Lab Automation: Mounting sensors, cameras, or dispensers within automated testing and analysis equipment. Precision and reliability are key, and custom mounts ensure components are held securely and accurately. Finding a reliable fabricante por contrato de productos sanitarios with AM capabilities is vital.
4. Industrial Manufacturing:
Factory floors and industrial facilities present environments with vibration, dust, moisture, temperature fluctuations, and potential chemical exposure. Custom mounts ensure the reliable operation of control systems, sensors, and IIoT devices.
- Control Panel Components: Creating custom DIN rail mounts, brackets for PLCs (Programmable Logic Controllers), HMIs (Human-Machine Interfaces), and power supplies within control cabinets, especially where space is limited or non-standard components are used.
- Robotic Arm & End-Effector Mounts: Securely attaching sensors, cameras, or specialized tooling to robotic arms. These mounts need to be rigid, lightweight (to maximize payload and speed), and often highly customized for the specific task and robot model.
- Rugged Sensor Brackets: Positioning and protecting sensors (proximity, photoelectric, vision systems) in harsh manufacturing environments. Custom mounts made from durable alloys like 316L can withstand washdowns, chemical exposure, and physical impacts, ensuring sensor longevity and accuracy. Sourcing these often involves looking for factory automation components distributors who partner with AM providers.
- Industrial IoT (IIoT) Device Housing: Creating custom enclosures and mounts for IIoT sensors deployed throughout a facility, potentially in difficult-to-access locations or areas requiring specific environmental protection (e.g., harsh environment enclosures B2B). Metal AM allows for integrated antennas, sealing features, and robust mounting points. In potentially explosive atmospheres, compliance with ATEX directives might necessitate specific design and material considerations.
Across all these industries, the core functions provided by custom metal 3D printed mounts remain consistent: secure fixation, vibration mitigation, thermal management, precise positioning, environmental protection, and enabling complex system integration. The ability to tailor the mount precisely to the application unlocks performance and reliability unattainable with standard hardware.
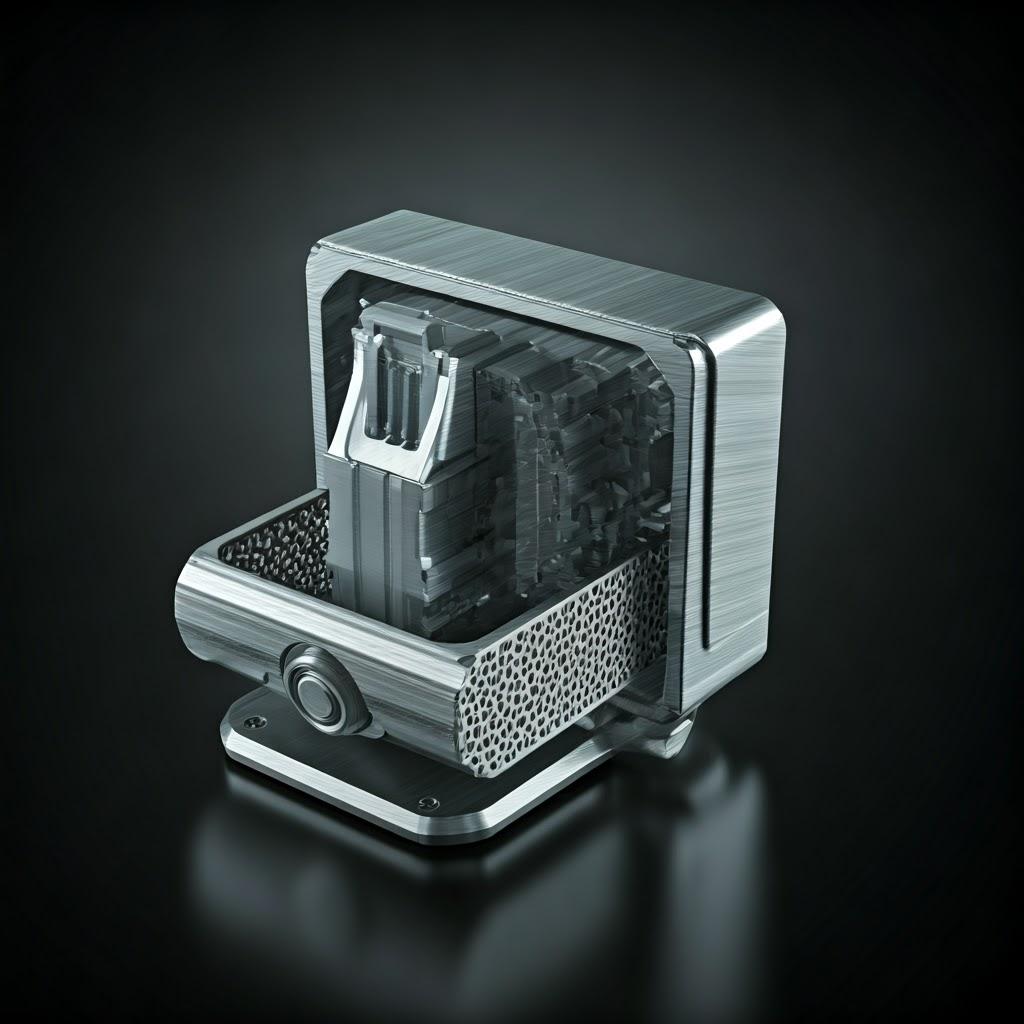
Why Metal 3D Printing? Unlocking Advantages for Custom Electronics Mounts
The decision to utilize metal additive manufacturing for custom electronics mounts stems from a clear set of advantages over traditional manufacturing techniques, particularly when dealing with complexity, customization, and speed. While methods like CNC machining, sheet metal fabrication, and injection molding have their places, they often present significant hurdles for producing the kind of optimized, bespoke mounting solutions required in modern B2B applications.
Limitations of Traditional Manufacturing Methods:
- Mecanizado CNC:
- Residuos materiales: Subtractive in nature, CNC machining starts with a solid block of material and removes excess. For complex mount geometries, this can result in significant material waste (poor Buy-to-Fly ratio), increasing costs, especially with expensive alloys.
- Restricciones geométricas: While multi-axis CNC machines are highly capable, creating deep pockets, internal channels (for cooling or wiring), undercuts, and truly complex organic shapes can be challenging, time-consuming, and may require multiple setups or specialized tooling.
- Plazos de entrega: Programming, fixture creation, and machining time can lead to longer lead times, especially for one-off prototypes or low-volume runs of highly complex parts.
- Costes de configuración: Each new custom design requires new programming and potentially new fixtures, adding upfront costs.
- Fabricación de chapa metálica:
- Geometric Limitations: Primarily suited for creating parts through bending, cutting, and punching flat sheets. Achieving true three-dimensional complexity, varying wall thicknesses, or intricate integrated features is difficult or impossible. Strength is often directional.
- Tooling Costs (for Forming/Stamping): While simple brackets can be made cost-effectively, any forming or stamping operations require dedicated tooling, which is only economical at higher volumes.
- Assembly Required: Complex mounts often need to be constructed from multiple bent and welded pieces, increasing assembly time, weight, and potential failure points compared to a consolidated AM part.
- Moldeo por inyección:
- Limitaciones materiales: Primarily used for plastics, which may not meet the strength, stiffness, thermal conductivity, or temperature resistance requirements for many demanding electronics mounting applications. Metal Injection Molding (MIM) exists but also requires expensive tooling.
- Extremely High Tooling Costs: The cost of creating molds is substantial, making injection molding completely unsuitable for prototypes, low-volume production, or parts requiring frequent design changes. Lead times for tool creation are also very long.
The Transformative Advantages of Metal Additive Manufacturing:
Metal AM overcomes many of these limitations, offering a suite of benefits perfectly suited for custom electronics mounts:
- Libertad de diseño sin precedentes: This is perhaps the most significant advantage. AM builds parts layer by layer, freeing engineers from the constraints of traditional methods.
- Geometrías complejas: Create intricate shapes, internal cooling channels, conformal designs that hug electronic components, and smooth, organic forms optimized for stress flow.
- Consolidación de piezas: Combine multiple individual components (e.g., a bracket, a heat sink, fastening features) into a single, monolithic printed part. This reduces assembly time, eliminates fasteners (potential failure points), improves structural integrity, and often lowers overall weight. Imagine replacing a 6-piece sheet metal assembly requiring welding and multiple fasteners with one integrated AM mount.
- Funcionalidad integrada: Directly incorporate features like optimized heat sink fins, vibration-damping lattice structures, cable management channels, snap-fits, or precisely aligned locating features.
- Creación rápida de prototipos e iteración: Need to test a new mount design? With AM, a functional metal prototype can often be produced in a matter of days.
- Ciclos de desarrollo acelerados: Quickly validate fit, form, and function. Make design modifications based on testing and print a revised version rapidly. This drastically reduces the time-to-market for new electronic systems.
- Riesgo reducido: Physical testing of prototypes early in the design phase minimizes the risk of costly errors discovered later in production. Compare this to the weeks or months required to get a prototype via traditional tooling methods. This capability is invaluable for rapid prototyping electronics hardware.
- Personalización Económica y Producción Bajo Demanda: AM excels where volumes are low, or designs are unique.
- Sin costes de utillaje: The primary cost drivers are material volume and print time, not expensive molds or fixtures. This makes producing one-offs, small batches, or families of similar but distinct parts highly cost-effective.
- Ideal for Low-to-Medium Volumes: Perfect for specialized industrial equipment, aerospace programs, medical devices, or automotive prototypes where production runs might be in the tens, hundreds, or low thousands.
- Inventario digital: Designs are stored digitally and can be printed whenever needed, reducing the need for physical inventory and enabling on-demand manufacturing supplier models. Parts can be produced closer to the point of need.
- Optimización del peso: Critical in aerospace, automotive, and portable applications.
- Optimización de la topología: Software tools analyze stress distributions and remove material from non-critical areas, creating lightweight yet strong, often organic-looking structures unattainable through other methods. This is ideal for designing a lightweight electronics mount.
- Estructuras reticulares: Incorporate internal lattice structures that significantly reduce weight while maintaining stiffness or providing specific damping or thermal properties.
- Rendimiento y selección de materiales: AM provides access to a growing range of high-performance metal powders.
- Propiedades a medida: Choose materials like AlSi10Mg for lightweight thermal management or 316L stainless steel for corrosion resistance and biocompatibility, matching the material precisely to the application’s demands.
- Microestructuras optimizadas: Depending on the AM process (like LPBF or Met3dp’s SEBM) and post-processing, unique and beneficial material microstructures can be achieved, sometimes exceeding the properties of traditional cast parts.
By leveraging these advantages, engineers and designers can create custom electronics mounts that are not just replacements for traditionally manufactured parts, but are fundamentally superior in terms of performance, integration, and efficiency. Partnering with an experienced AM service provider unlocks the full potential of this technology.
Material Selection Spotlight: AlSi10Mg and 316L for Optimal Performance
Choosing the right material is fundamental to the success of any engineering component, and custom electronics mounts are no exception. The operating environment, structural loads, thermal requirements, weight constraints, and potential regulatory needs (like biocompatibility) all dictate the ideal material choice. Metal additive manufacturing offers a diverse palette of alloys, but for a vast range of electronics mounting applications, two materials stand out due to their excellent balance of properties, processability, and availability: AlSi10Mg (una aleación de aluminio) y 316L (a stainless steel).
Understanding the characteristics of these materials is crucial for engineers designing mounts and for procurement managers sourcing proveedores de polvo de metal or AM services. The quality of the raw material – the metal powder – is paramount to achieving reliable, high-performance printed parts. This is where the expertise of companies like Met3dp becomes invaluable. Met3dp employs industry-leading powder production techniques, including advanced Gas Atomization and Plasma Rotating Electrode Process (PREP) technologies. Their focus on achieving high sphericity, good flowability, low satellite content, and high purity in their polvos metálicos de impresión 3D de alta calidad directly translates to denser, stronger, and more consistent final parts for their customers.
AlSi10Mg: The Lightweight Thermal Manager
AlSi10Mg is an aluminum alloy containing silicon (around 10%) and magnesium (less than 0.5%). It’s widely used in metal AM, often seen as an equivalent to casting aluminum alloys. Its popularity stems from a compelling combination of properties:
- Propiedades:
- Baja densidad: Approximately 2.67 g/cm³, making it significantly lighter than steels or titanium alloys. This is a primary driver for its use in weight-sensitive applications.
- Buena relación resistencia-peso: Offers respectable mechanical strength and stiffness, especially after appropriate heat treatment, relative to its low weight.
- Excelente conductividad térmica: Typically around 130-150 W/(m·K), allowing it to effectively dissipate heat generated by electronic components. This makes it ideal for mounts that double as heat sinks.
- Good Processability in AM: Melts and solidifies reliably in Laser Powder Bed Fusion (LPBF) systems, allowing for the creation of complex geometries.
- Resistencia a la corrosión: Offers moderate corrosion resistance, suitable for many environments, though not as robust as stainless steel in aggressive conditions. Can be enhanced with surface treatments like anodizing.
- Benefits for Electronics Mounts:
- Ahorro de peso: Ideal for aerospace, UAVs, automotive, and portable devices where minimizing mass is critical.
- Gestión térmica: Can be designed with integrated fins or channels to efficiently draw heat away from sensitive electronics, improving performance and longevity.
- Geometrías complejas: Enables lightweight, topology-optimized designs with integrated cooling features.
- Consideraciones:
- Lower absolute strength and stiffness compared to steels.
- Lower temperature resistance compared to steels or superalloys.
- Requires careful consideration of post-print heat treatment (e.g., T6 cycle) to achieve optimal mechanical properties.
- Corrosion resistance may be insufficient for very harsh chemical or marine environments without protective coatings.
316L Stainless Steel: The Durable & Resistant Workhorse
316L is a low-carbon version of 316 stainless steel, an austenitic chromium-nickel stainless steel containing molybdenum. The ‘L’ signifies low carbon content (typically <0.03%), which improves weldability and reduces susceptibility to sensitization (chromium carbide precipitation) during thermal cycles, making it highly suitable for AM and subsequent heat treatments or welding operations.
- Propiedades:
- Excelente resistencia a la corrosión: Highly resistant to a wide range of corrosive media, including acids, chlorides, and marine environments, due to its significant chromium and molybdenum content. Ideal for harsh industrial, chemical processing, or outdoor applications.
- Alta resistencia y ductilidad: Offers a good combination of tensile strength (typically >500 MPa after printing and stress relief) and elongation (>30-40%), resulting in tough and durable parts that can withstand significant loads and impacts.
- Biocompatibilidad: 316L is widely accepted for medical implants and devices (meeting standards like ISO 10993) due to its excellent corrosion resistance in bodily fluids and low reactivity. This makes it a go-to material for medical grade 316L printing.
- Buena soldabilidad: Can be easily welded if required for larger assemblies or repairs.
- Esterilizabilidad: Withstands common sterilization methods like autoclaving without degradation.
- Moderate Thermal Conductivity: Around 15 W/(m·K), significantly lower than aluminum. Not ideal for primary heat sinking applications but sufficient for structural integrity at moderate temperatures.
- Benefits for Electronics Mounts:
- Durability in Harsh Environments: Suitable for industrial machinery, marine equipment, chemical processing plants, and outdoor installations where resistance to moisture, chemicals, and salt spray is required. A key material for corrosion resistant bracket B2B supply.
- Aplicaciones médicas: The default choice for mounting electronics in or on medical devices requiring biocompatibility and sterilizability.
- Integridad estructural: Provides high strength and toughness for mounts subjected to significant mechanical loads or potential impacts.
- Food Grade Applications: Often acceptable for mounting components in food processing equipment due to its cleanability and corrosion resistance.
- Consideraciones:
- Higher Density: Approximately 7.99 g/cm³, nearly three times denser than AlSi10Mg. Not ideal where weight is the absolute primary concern.
- Lower Thermal Conductivity: Less effective than aluminum alloys for applications requiring significant heat dissipation through the mount itself.
- Requires appropriate stress relief heat treatment after printing to minimize residual stresses and ensure dimensional stability. Passivation is often recommended to optimize corrosion resistance.
Material Property Comparison (Typical Values for LPBF):
Propiedad | Unidad | AlSi10Mg (Tratado térmicamente – T6) | 316L (Stress Relieved) | Notas |
---|---|---|---|---|
Densidad | g/cm³ | ~2.67 | ~7.99 | 316L is significantly heavier. |
Tensile Strength (UTS) | MPa | 330 – 430 | 500 – 650 | Dependent on print parameters, orientation, and heat treatment. |
Límite elástico (0,2%) | MPa | 230 – 320 | 380 – 550 | Dependent on print parameters, orientation, and heat treatment. |
Alargamiento a la rotura | % | 3 – 10 | 30 – 50 | 316L is much more ductile. |
Dureza | HBW | 100 – 120 | 150 – 200 | |
Conductividad térmica | W/(m-K) | 130 – 150 | ~15 | AlSi10Mg is far superior for heat dissipation. |
Coefficient Thermal Exp. | µm/(m·°C) (at 20-100°C) | ~21 | ~16 | Important for designs involving different materials or temperature swings. |
Resistencia a la corrosión | General | Moderado | Excelente | 316L excels in harsh environments. |
Biocompatibilidad | ISO 10993 | No | Sí | Critical for medical applications. |
Exportar a hojas
(Note: These values are typical ranges and can vary based on the specific AM machine, process parameters, powder quality, build orientation, and post-processing treatments. Always consult specific material datasheets from the provider, like Met3dp, for design purposes.)
El papel fundamental de la calidad del polvo
The theoretical properties of an alloy are only achievable in a 3D printed part if the starting material – the metal powder – is of exceptionally high quality. Issues like:
- Irregular Powder Shape: Leads to poor flowability in the printer’s recoating mechanism and lower packing density on the build plate, potentially causing voids (porosity) in the final part.
- Satellite Particles: Small particles attached to larger spheres, common in lower-quality atomization, can melt differently and disrupt the process, affecting surface finish and density.
- Impurities/Oxidation: Contaminants or excessive oxygen content in the powder can lead to defects, embrittlement, and reduced mechanical performance or corrosion resistance.
This underscores the importance of sourcing materials from manufacturers with rigorous process control. Met3dp’s commitment to advanced powder manufacturing techniques like Gas Atomization (utilizing unique nozzle designs for optimal gas flow) and PREP (producing highly spherical powders with minimal satellites) ensures that the AlSi10Mg, 316L, and other advanced alloys (like TiNi, TiTa, CoCrMo, superalloys) they offer provide the ideal foundation for printing dense, reliable, high-performance custom electronics mounts. Choosing a partner like Met3dp, who controls powder quality from the source, significantly de-risks the manufacturing process and ensures the final component meets demanding specifications.
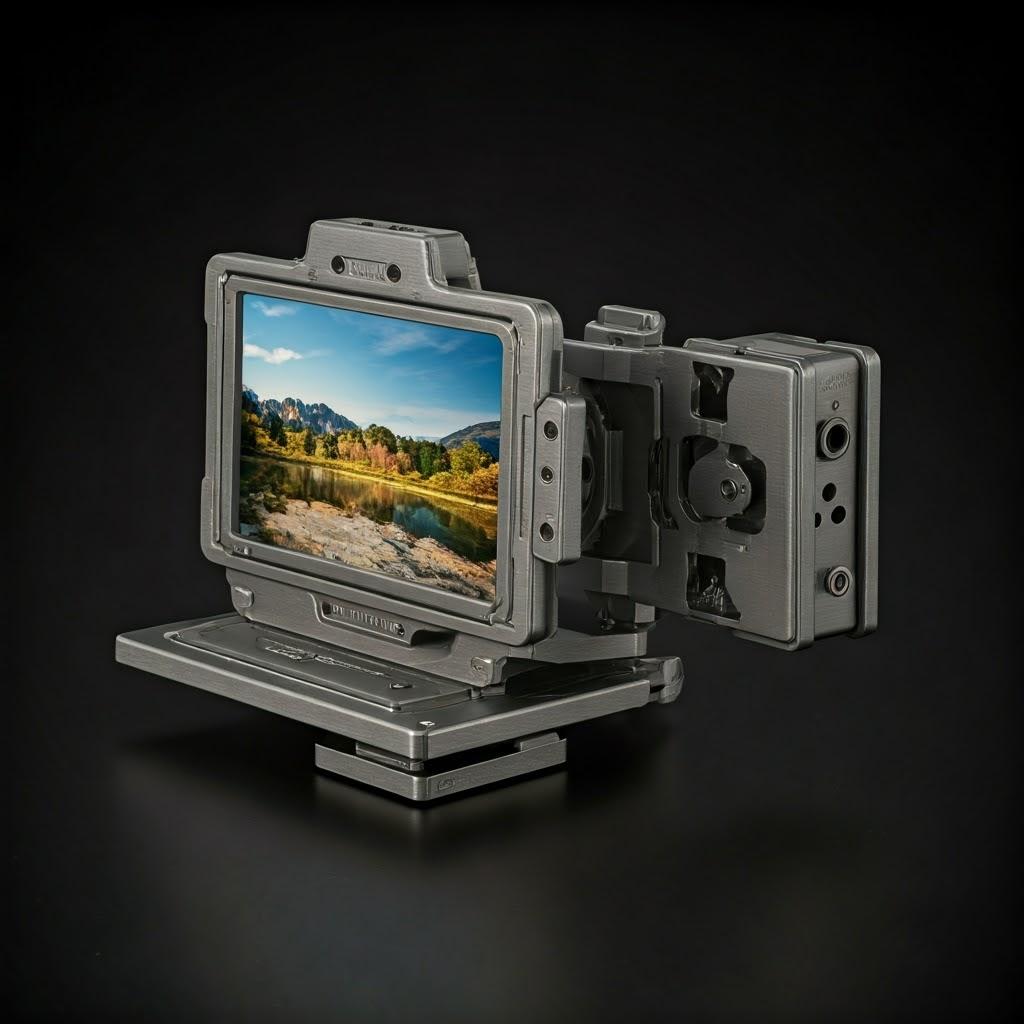
Designing for Additive: Optimizing Your Custom Electronics Mount for 3D Printing
Simply replicating a design intended for CNC machining or sheet metal fabrication using metal 3D printing often fails to capitalize on the technology’s true potential and can even lead to suboptimal results or manufacturing difficulties. To truly leverage the power of Additive Manufacturing (AM), engineers must embrace Diseño para fabricación aditiva (DfAM) principles. DfAM is not just a set of rules but a different way of thinking about part design, focusing on leveraging AM’s strengths (complexity, consolidation) while mitigating its constraints (support structures, residual stress). Optimizing your custom electronics mount design specifically for the chosen metal AM process, such as Laser Powder Bed Fusion (LPBF), is critical for achieving desired performance, minimizing cost, and ensuring manufacturability. Engaging with AM experts, potentially through B2B DfAM services, can significantly streamline this process.
Key DfAM Principles for Custom Electronics Mounts:
- Optimización de la topología: This is a powerful computational tool that optimizes material layout within a defined design space based on load conditions and constraints.
- Proceso: Finite Element Analysis (FEA) simulates how the mount behaves under expected loads (vibration, static forces, thermal loads). Algorithms then iteratively remove material from areas experiencing low stress, reinforcing high-stress regions.
- ~1600-1900 MPa The result is often an organic, skeletal-like structure that meets or exceeds the required stiffness and strength with significantly reduced mass compared to a conventionally designed part. This is paramount for aerospace and automotive applications seeking lightweight electronics mounts.
- Ejemplo: Imagine a solid, blocky bracket designed to hold an avionics box. Topology optimization might transform it into a web-like structure, retaining mounting points and structural ribs only where needed, potentially cutting weight by 30-60% while maintaining the required rigidity.
- Software & Expertise: Tools like Altair Inspire, Ansys Discovery, or Dassault Systèmes CATIA Generative Design facilitate this. Collaboration with AM service providers like Met3dp, who understand both the software and the manufacturing implications, ensures practical, printable optimized designs.
- Consolidación de piezas: AM’s ability to build complex geometries in a single process step allows designers to combine multiple simpler parts into one, monolithic component.
- Ventajas:
- Reducción del tiempo y los costes de montaje: Eliminates steps like fastening, welding, or bonding multiple pieces.
- Simplified Bill of Materials (BOM) & Procurement: Fewer part numbers to manage, track, and source from distribuidores de componentes industriales or manufacturers.
- Fiabilidad mejorada: Removes potential failure points associated with joints, fasteners, or welds.
- Peso reducido: Often eliminates the need for bulky flanges, overlapping sections, and fasteners.
- Ejemplo: A sensor mount assembly might traditionally consist of a base plate, a vertical arm, a sensor clamp, and multiple screws/bolts. Using AM, this could be redesigned as a single printed part incorporating the base, arm, and clamp features directly, potentially with optimized internal structures for stiffness.
- Ventajas:
- Estructuras de celosía y relleno: Instead of solid material, internal volumes can be filled with lattice structures – repeating networks of struts or complex surfaces.
- Types & Applications:
- Strut-Based Lattices (e.g., cubic, octet-truss): Excellent for significant weight reduction while maintaining structural stiffness. Can be tuned for specific compliance or energy absorption (vibration damping).
- Surface-Based Lattices (e.g., TPMS – Triply Periodic Minimal Surfaces like Gyroid): Offer very high surface area-to-volume ratios, making them ideal for enhancing heat transfer in mounts doubling as heat sinks. Also provide good energy absorption.
- Ventajas: Extreme lightweighting, tailored mechanical properties (stiffness, damping), enhanced thermal performance.
- Consideraciones sobre el diseño: Requires specialized software modules for generation. Cell size, strut/wall thickness, and junction design must be carefully considered based on material properties and print resolution. Analyzing the manufacturability of complex lattices is crucial.
- Types & Applications:
- Minimum Wall Thickness & Feature Size: Every AM process and material has limits on the smallest features it can reliably produce.
- Guidelines (LPBF examples):
- Espesor mínimo de pared: Typically 0.4mm – 1.0mm, depending on the wall’s height, orientation, and material (e.g., AlSi10Mg might allow slightly thinner walls than 316L due to lower melting point and thermal conductivity). Unsupported thin walls are prone to warping or incomplete formation.
- Diámetro mínimo del orificio: Horizontal holes (parallel to build plate) depend on the ability to bridge unmelted powder; vertical holes are generally limited by laser spot size and powder characteristics, often around 0.5mm minimum, though tapping requires larger pilot holes.
- Minimum Feature Size (e.g., pins, bosses): Often around 0.5mm – 1.0mm diameter/width.
- Importancia: Designing below these limits results in failed prints or weak, inaccurate features. Always consult the AM provider’s specific guidelines.
- Guidelines (LPBF examples):
- Estrategia de la estructura de soporte: AM processes like LPBF require support structures for overhanging features (typically below 45 degrees from the horizontal) and to anchor the part to the build plate, managing thermal stresses.
- Design Goals:
- Minimize Support Need: Orient the part strategically on the build plate. Utilize self-supporting angles (often >45°). Design smooth transitions and fillets instead of sharp overhangs where possible.
- Ensure Easy Removal: Design supports that are accessible and have minimal contact points with the part surface (e.g., using perforated or tapered contact points). Avoid placing supports on critical or cosmetic surfaces if possible.
- Maintain Part Accuracy: Supports prevent warping and ensure features are built in the correct location. Insufficient support can lead to build failures or distorted parts.
- Tipos: Block supports, line supports, tree/cone supports (often generated automatically by build preparation software but can be manually edited for optimization).
- Experiencia: Experienced AM service providers understand the nuances of support strategy for different geometries and materials, balancing minimization with stability and ease of removal. Understanding different AM processes and their support needs, as detailed under Met3dp’s overview of métodos de impresión, es clave.
- Design Goals:
- Incorporating Functional Features: Design features directly into the mount to enhance its utility.
- Hilos: It’s generally recommended to print pilot holes and tap them conventionally during post-processing for optimal strength and precision. Directly printed threads can be achieved but often lack the required tolerance and surface finish. Consider heat-set inserts or Heli-Coils for higher strength threads, designing appropriate receiving features.
- Ajustes a presión: Possible but require careful material selection (considering fatigue life and flexibility – less common in metals than polymers) and design (appropriate cantilever lengths, snap angles, tolerances).
- Enrutamiento de cables: Integrate channels, clips, or tie-down points directly into the mount design for clean and secure cable management. Ensure smooth paths and adequate bend radii.
- Heat Sink Fins: Optimize fin geometry (height, thickness, spacing, shape) and orientation relative to expected airflow (natural or forced convection) for maximum thermal performance. AM allows for complex fin shapes not possible with extrusion or machining.
- Orientation Considerations: How a part is oriented on the build plate significantly impacts several factors:
- Acabado superficial: Angled surfaces exhibit a “stair-stepping” effect related to the layer thickness. Vertical walls generally have better finish than shallow angles. Top-facing surfaces are typically smoother than down-facing surfaces that required support.
- Propiedades mecánicas: In LPBF, parts often exhibit slight anisotropy, typically being strongest and stiffest in the XY plane (parallel to the build plate). Critical load paths should ideally be aligned with this plane if possible.
- Requisitos de soporte: Orientation directly dictates the amount and location of required support structures. Minimizing supports usually reduces print time and post-processing effort/cost.
- Tiempo de impresión: Primarily driven by the Z-height (number of layers). Orienting the part with its shortest dimension vertical generally leads to faster prints.
- Tensión térmica: Orientation affects heat accumulation and dissipation during the build, influencing residual stress and potential warping. Build simulation software can help optimize orientation to mitigate these risks.
By thoughtfully applying these DfAM principles, engineers can design custom electronics mounts that are lighter, stronger, more functional, and more cost-effective to produce using metal AM, fully realizing the benefits of this advanced manufacturing technology.
Achieving Precision: Tolerance, Surface Finish, and Dimensional Accuracy in Metal AM Mounts
While metal AM offers incredible design freedom, understanding and specifying the achievable levels of precision is crucial for ensuring custom electronics mounts fit correctly and function as intended. Engineers and procurement managers must have realistic expectations regarding tolerances, surface finish, and overall dimensional accuracy, and communicate these requirements clearly to their B2B precision components supplier. Factors like the chosen AM process (e.g., LPBF), material, machine calibration, part complexity, and post-processing all play a role.
Tolerances in Metal Additive Manufacturing:
Tolerance refers to the permissible limit or limits of variation in a physical dimension. Metal AM processes, while increasingly precise, inherently have more sources of variation than high-precision CNC machining.
- Typical Achievable Tolerances (LPBF):
- Tolerancias generales: Often fall within ISO 2768 Class m (medium) or sometimes Class f (fine) for as-built parts, depending on geometry and size.
- Specific Dimensions: For well-controlled processes and smaller features (<100mm), tolerances of ±0.1mm to ±0.2mm (±0.004″ to ±0.008″) are often achievable. Larger dimensions may see tolerances scale proportionally (e.g., ±0.1% to ±0.2% of the length).
- Tolerancias críticas: Features requiring tighter tolerances (e.g., bearing fits, precise alignment features, mating surfaces) almost always necessitate post-print CNC machining.
- Sources of Variation:
- Efectos térmicos: Material shrinkage upon cooling, uneven cooling rates leading to warping, and residual stress accumulation can all affect final dimensions.
- Parámetros del proceso: Laser power stability, scan speed consistency, powder layer thickness accuracy, and gas flow within the build chamber influence melt pool stability and feature resolution.
- Propiedades del material: Different alloys exhibit different shrinkage behavior. Powder characteristics (size distribution, morphology) also play a role.
- Estructuras de apoyo: The location and effectiveness of supports impact stability during the build and potential distortion upon removal.
- Calibración de la máquina: Regular calibration of the laser system, optical components, and motion system is critical for accuracy. Reliable providers like Met3dp emphasize machine accuracy and reliability.
Acabado superficial (rugosidad):
Surface finish, often quantified by the average roughness (Ra), describes the texture of a part’s surface. Metal AM parts inherently have a rougher surface finish than machined parts due to the layer-by-layer nature of the process and the partially melted powder particles adhering to surfaces.
- Typical As-Built Ra Values (LPBF):
- AlSi10Mg: Often in the range of 8 – 15 µm (315 – 590 µin).
- Acero inoxidable 316L: Typically 10 – 20 µm (390 – 790 µin).
- Factors Influencing As-Built Ra:
- Grosor de la capa: Las capas más delgadas generalmente producen superficies más lisas, pero aumentan el tiempo de impresión.
- Orientación:
- Top surfaces (facing upwards) are generally the smoothest.
- Vertical walls have moderate roughness.
- Upward-facing curved or angled surfaces exhibit stair-stepping.
- Downward-facing surfaces (supported) are typically the roughest due to support contact points and partial sintering of powder trapped beneath overhangs.
- Parámetros del proceso: Laser parameters (power, speed, focus) and contour scan strategies can be tuned to optimize surface finish to some extent.
- Características del polvo: Particle size distribution affects achievable finish.
- Mejora del acabado superficial: If the as-built roughness is insufficient, post-processing is required. Common methods include: | Post-Processing Method | Typical Achievable Ra (µm) | Notes | | :————————– | :————————- | :———————————————————————– | | As-Built (LPBF) | 8 – 20+ | Highly dependent on material, orientation, parameters. | | Bead Blasting | 3 – 8 | Uniform matte finish, removes loose powder, can slightly reduce Ra. | | Tumbling/Vibratory Finish | 1 – 5 | Good for deburring, edge rounding, improving finish on external surfaces. | | Electropolishing (esp. 316L) | 0.5 – 2 | Smooths peaks and valleys electrochemically, bright finish. | | CNC Machining | 0.4 – 3.2 (or better) | Precise finish on specific features, can achieve very smooth surfaces. | | Manual Polishing | < 0.1 | Labor-intensive, used for mirror finishes on critical areas. |
Precisión dimensional:
This refers to how closely the final part conforms to the nominal dimensions specified in the CAD model or drawing. It’s influenced by both tolerance control and surface finish.
- Measurement & Verification: Dimensional accuracy is typically verified using:
- Calibradores/Micrómetros: For simple measurements.
- Máquinas de medición por coordenadas (MMC): For high-accuracy measurement of complex geometries and GD&T features.
- Escaneado 3D: To compare the overall shape of the printed part against the original CAD model.
- Lograr precisión: Requires a holistic approach:
- Good DfAM: Designing features within process limits, minimizing stress concentrations.
- Simulación del proceso: Predicting and compensating for shrinkage and distortion before printing.
- Control preciso de procesos: Using well-maintained, calibrated machines and optimized parameters.
- Estrategia de soporte efectiva: Ensuring stability during the build.
- Post-procesamiento controlado: Performing heat treatments correctly before final machining, using appropriate machining strategies and fixtures.
- Communication is Key: Providing clear engineering drawings with appropriate Geometric Dimensioning and Tolerancing (GD&T) callouts is essential when working with an AM service provider. This explicitly defines which features are critical and what level of precision is required, allowing the provider to plan the manufacturing and post-processing steps accordingly. Discussing requirements upfront with partners like Met3dp ensures alignment on achievable accuracy and necessary processing steps.
Understanding these aspects of precision allows engineers to design effectively for metal AM and set appropriate specifications, ensuring their custom electronics mounts meet the required fit and function standards.
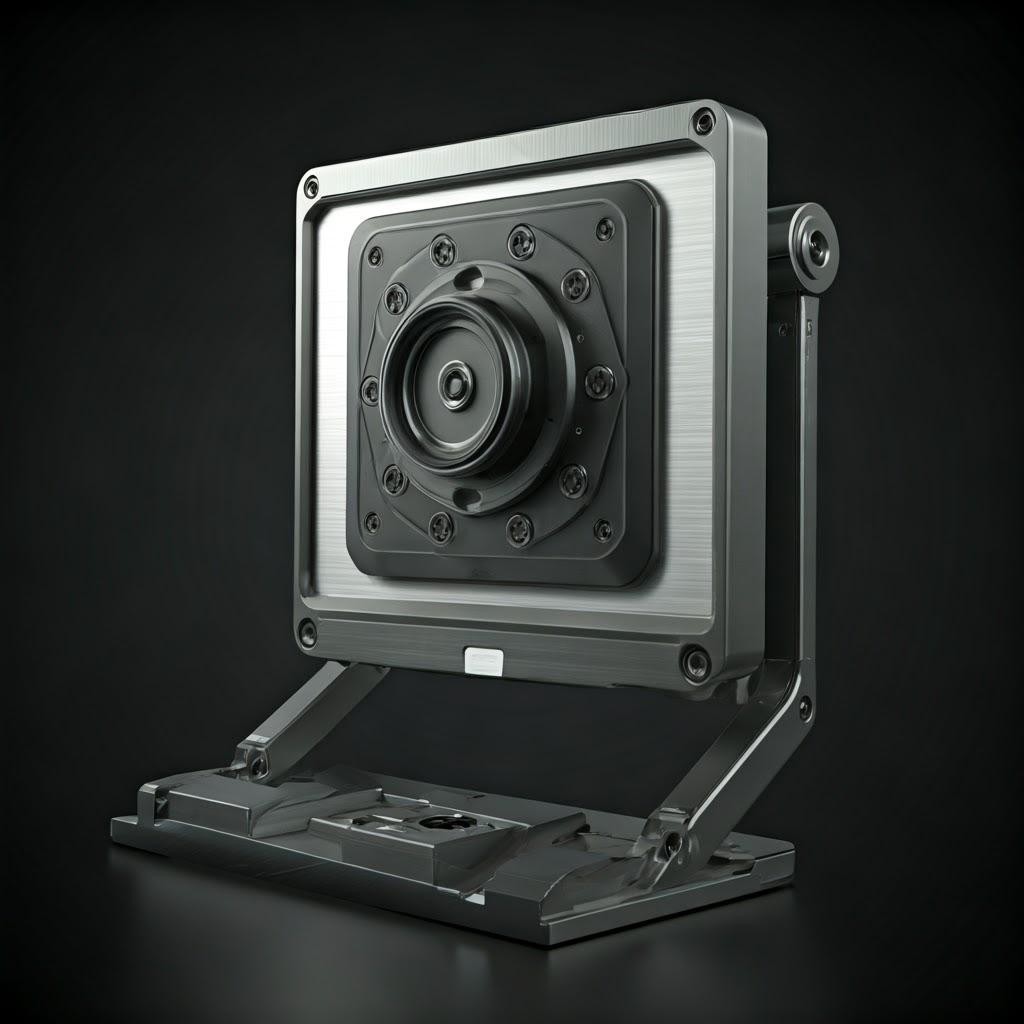
Beyond the Print: Essential Post-Processing Steps for Electronics Mounts
The journey of a metal 3D printed part doesn’t end when it comes off the build plate. For virtually all functional applications, especially demanding ones like custom electronics mounts, a series of pasos de post-procesamiento are necessary to achieve the required material properties, dimensional accuracy, surface finish, and overall quality. These steps are integral to the manufacturing workflow and must be considered during the design phase and when evaluating proveedores de servicios de impresión 3D de metal. Neglecting post-processing can lead to premature failure, poor fit, or compromised performance.
Common Post-Processing Requirements for Metal AM Mounts:
- Alivio del estrés / Tratamiento térmico: This is arguably the most critical post-processing step for parts made via Powder Bed Fusion (LPBF/SLM/SEBM). The rapid heating and cooling cycles inherent in these processes create significant internal residual stresses within the part.
- Por qué es crucial:
- Relieves Internal Stresses: Prevents distortion or cracking after the part is removed from the build plate or during subsequent machining.
- Achieves Desired Material Properties: Develops the optimal microstructure for strength, ductility, hardness, and fatigue life. As-built parts often have non-equilibrium microstructures.
- Improves Machinability: Homogenizes the microstructure, making subsequent CNC machining more predictable and consistent.
- Typical Cycles (Examples):
- AlSi10Mg: Often requires a solution treatment followed by artificial aging (T6 condition) to maximize strength. This might involve heating to ~530°C, quenching, and then aging at ~160°C for several hours.
- Acero inoxidable 316L: Typically requires a stress relief anneal in an inert atmosphere (like Argon) or vacuum. A common cycle is heating to 650°C – 900°C (depending on desired balance of stress relief vs. strength) and holding for 1-2 hours, followed by controlled cooling. Higher temperature annealing (~1050°C) can improve ductility but may reduce strength.
- Consideraciones: Must be performed antes de removing the part from the build plate if distortion is a major concern. Requires calibrated furnaces with controlled atmospheres to prevent oxidation.
- Por qué es crucial:
- Extracción de la pieza de la placa de montaje: Once heat treatments (if performed on the plate) are complete, the part needs to be separated from the metal build plate it was printed on.
- Métodos: Commonly done using wire EDM (Electrical Discharge Machining), band sawing, or sometimes CNC milling.
- Consideraciones: Must be done carefully to avoid damaging the part. The choice of method depends on part geometry, material, and required precision of the base surface.
- Retirada de la estructura de soporte: The temporary structures printed to support overhangs and anchor the part must be removed.
- Métodos: Can involve manual breaking/clipping (for well-designed supports), grinding, milling, or wire EDM for supports in difficult-to-reach areas.
- Consideraciones: This step can be labor-intensive and requires skill to avoid damaging the part surface. DfAM plays a huge role in designing supports for easy, clean removal. Witness marks (small blemishes where supports were attached) are common and may require further finishing if on a critical surface. Addressing support removal AM challenges starts at the design stage.
- Mecanizado CNC: Often required to achieve tight tolerances or specific features not perfectly rendered by the AM process.
- Aplicaciones comunes:
- Tolerancias críticas: Achieving dimensions tighter than ±0.1mm.
- Superficies de contacto: Ensuring flat, smooth surfaces for assembly.
- Precise Hole Diameters & Locations: For fasteners, bearings, or alignment pins.
- Agujeros roscados: Tapping printed pilot holes provides superior thread quality compared to directly printing threads.
- Acabado superficial mejorado: Achieving specific Ra values on functional surfaces.
- Consideraciones: Requires careful fixture design, as AM parts can have complex shapes. Machining allowances should be considered in the DfAM phase (adding extra material where machining is planned). Understanding how El mecanizado CNC de piezas impresas en 3D differs from machining wrought stock is important for machinists.
- Aplicaciones comunes:
- Acabado superficial: Various techniques are used to improve the as-built surface roughness, enhance cosmetic appearance, or provide specific functional properties.
- Granallado: Propels fine media (glass beads, ceramic) at the surface. Creates a uniform, non-directional matte finish, removes loose powder, and can provide minor peening effect.
- Acabado por volteo/vibración: Parts are placed in a tub with abrasive media, which vibrates or tumbles. Effective for deburring, edge rounding, and improving surface finish on external surfaces, especially for batches of smaller parts.
- Pulido: Manual or automated processes using progressively finer abrasives to achieve very smooth, often mirror-like finishes (Ra < 0.1 µm). Labor-intensive and typically reserved for specific critical areas.
- Anodizing (for Aluminum Alloys like AlSi10Mg): An electrochemical process that grows a durable, controlled oxide layer. Improves corrosion resistance, wear resistance, and allows for coloring. Type II (decorative/corrosion) and Type III (hardcoat for wear) are common.
- Passivation (for Stainless Steels like 316L): A chemical treatment (typically nitric or citric acid based) that removes free iron from the surface and enhances the natural passive chromium oxide layer. Crucial for maximizing corrosion resistance, especially for medical or food-grade applications. Passivation stainless steel is a standard step for 316L components.
- Pintura/recubrimiento: Applying specialized paints or coatings (e.g., powder coating, ceramic coatings) for enhanced environmental protection, specific colors, thermal barrier properties, or electrical insulation.
- Inspection & Quality Control (QC): Verifying that the finished part meets all specifications.
- Inspección dimensional: Using CMMs, 3D scanners, calipers, gauges.
- Pruebas de materiales: Often performed on sample coupons printed alongside the main parts (e.g., tensile testing to verify strength and ductility).
- Medición del acabado superficial: Uso de perfilómetros.
- Ensayos no destructivos (END): For critical components (especially aerospace/medical), methods like dye penetrant testing (surface defects) or X-ray/CT scanning (internal defects like porosity) may be required as part of the control de calidad de la fabricación aditiva proceso.
Integrating these post-processing steps into the production plan is essential for delivering functional, high-quality custom electronics mounts manufactured via metal AM.
Navigating Challenges: Common Issues in Metal AM for Mounts and How to Mitigate Them
While metal additive manufacturing offers significant advantages, it’s not without its potential challenges. Understanding these common issues and how to proactively mitigate them is crucial for successfully implementing AM for custom electronics mounts. This often involves a combination of good design practices (DfAM), optimized process parameters, high-quality materials, appropriate post-processing, and collaboration with experienced B2B AM consultation providers like Met3dp.
Desafíos comunes y estrategias de mitigación:
- Warping & Distortion:
- Causa: Significant thermal gradients during the layer-by-layer melting and solidification process lead to internal stresses. As these stresses try to relieve themselves, they can cause the part to warp or distort, especially after removal from the build plate. Thin features, large flat areas, and asymmetric designs are particularly susceptible. This is a primary metal 3D printing problem.
- Mitigación:
- DfAM: Design features to minimize stress concentrations (e.g., fillets instead of sharp corners). Avoid large, unsupported flat areas parallel to the build plate.
- Orientación: Optimize part orientation on the build plate to balance support needs and thermal stability.
- Estrategia de apoyo: Use robust support structures, particularly near edges and overhangs, to anchor the part effectively during the build.
- Simulación del proceso: Utilize software tools to predict thermal stresses and distortion, allowing for pre-compensation in the build file or adjustments to orientation/supports.
- Parámetros optimizados: Control build plate heating, laser scanning strategies (e.g., island scanning), and inter-layer time to manage heat accumulation.
- Alivio del estrés: Perform appropriate heat treatment cycles (often while still attached to the build plate) to relieve residual stresses before significant geometry changes occur.
- Porosidad:
- Causa: Voids within the printed material can compromise strength, fatigue life, and hermeticity. Causes include:
- Porosidad del gas: Trapped gas (e.g., Argon from the build chamber atmosphere, or dissolved gases in the powder) within the melt pool.
- Porosidad por falta de fusión: Insufficient melting and fusion between layers or adjacent scan tracks, often due to incorrect parameters (laser power too low, scan speed too high) or poor powder characteristics. This is a key challenge in porosidad AM de metales.
- Mitigación:
- Parámetros de impresión optimizados: Develop and utilize validated parameter sets (laser power, speed, hatch spacing, layer thickness) specific to the material and machine. This requires significant expertise.
- Polvo de alta calidad: Use powder with high sphericity, good flowability, controlled particle size distribution, and low trapped gas content. Met3dp’s advanced atomization processes are designed to minimize these risks.
- Proper Powder Handling: Prevent moisture absorption and contamination during storage and loading.
- Atmósfera controlada: Maintain high purity inert gas atmosphere within the build chamber.
- Prensado isostático en caliente (HIP): For critical applications demanding near-100% density, HIP post-processing (high temperature and high pressure) can effectively close internal pores.
- Causa: Voids within the printed material can compromise strength, fatigue life, and hermeticity. Causes include:
- Dificultades para retirar la ayuda:
- Causa: Supports are necessary but can be challenging to remove completely and cleanly, especially internal supports or those attached to delicate features or complex surfaces. This is a common support removal challenge.
- Mitigación:
- DfAM para la minimización de soportes: Design parts with self-supporting angles (>45°) where possible. Orient parts to reduce overhangs.
- DfAM for Easy Removal: Design supports with minimal contact points (e.g., perforated or tapered contacts). Ensure physical access for removal tools. Avoid placing supports on critical cosmetic or functional surfaces if feasible.
- Generación de soportes optimizada: Utilize advanced support generation software features (e.g., tree supports, specialized support profiles).
- Técnicas de eliminación adecuadas: Use careful manual removal, specialized tools, wire EDM, or CNC machining as needed. Budget adequate time and resources for this step.
- Rugosidad superficial:
- Causa: The inherent layer-wise building process leads to stair-stepping on angled surfaces and adherence of partially sintered powder, resulting in a rougher finish compared to machining.
- Mitigación:
- Orientación: Optimize part orientation to place critical surfaces vertically or horizontally (top-facing) if possible.
- Parámetros del proceso: Use thinner layers (increases print time) or optimized contour scan parameters.
- Post-procesamiento: Employ appropriate finishing techniques (bead blasting, tumbling, machining, polishing) as detailed previously, based on the required Ra value.
- Tensión residual:
- Causa: As mentioned under warping, the rapid heating/cooling cycles generate internal stresses even if they don’t cause immediate macroscopic distortion. Residual stress 3D printing can negatively impact fatigue life, dimensional stability over time, and susceptibility to stress corrosion cracking.
- Mitigación:
- Tratamiento térmico antiestrés: This is the primary method for significantly reducing residual stresses to acceptable levels. Performing this step correctly is non-negotiable for most functional metal AM parts.
- Optimización de procesos: Certain scanning strategies and thermal management techniques during the build can help minimize stress accumulation, but heat treatment remains essential.
- Diseño: Minimize abrupt changes in cross-section and large solid volumes where stress can concentrate.
Successfully navigating these challenges requires a deep understanding of the AM process, materials science, and robust quality control measures. Partnering with an experienced service provider like Met3dp, who possesses expertise in DfAM, process optimization, material science (including in-house powder production), and comprehensive post-processing, significantly increases the likelihood of achieving high-quality, reliable custom electronics mounts that meet demanding application requirements.
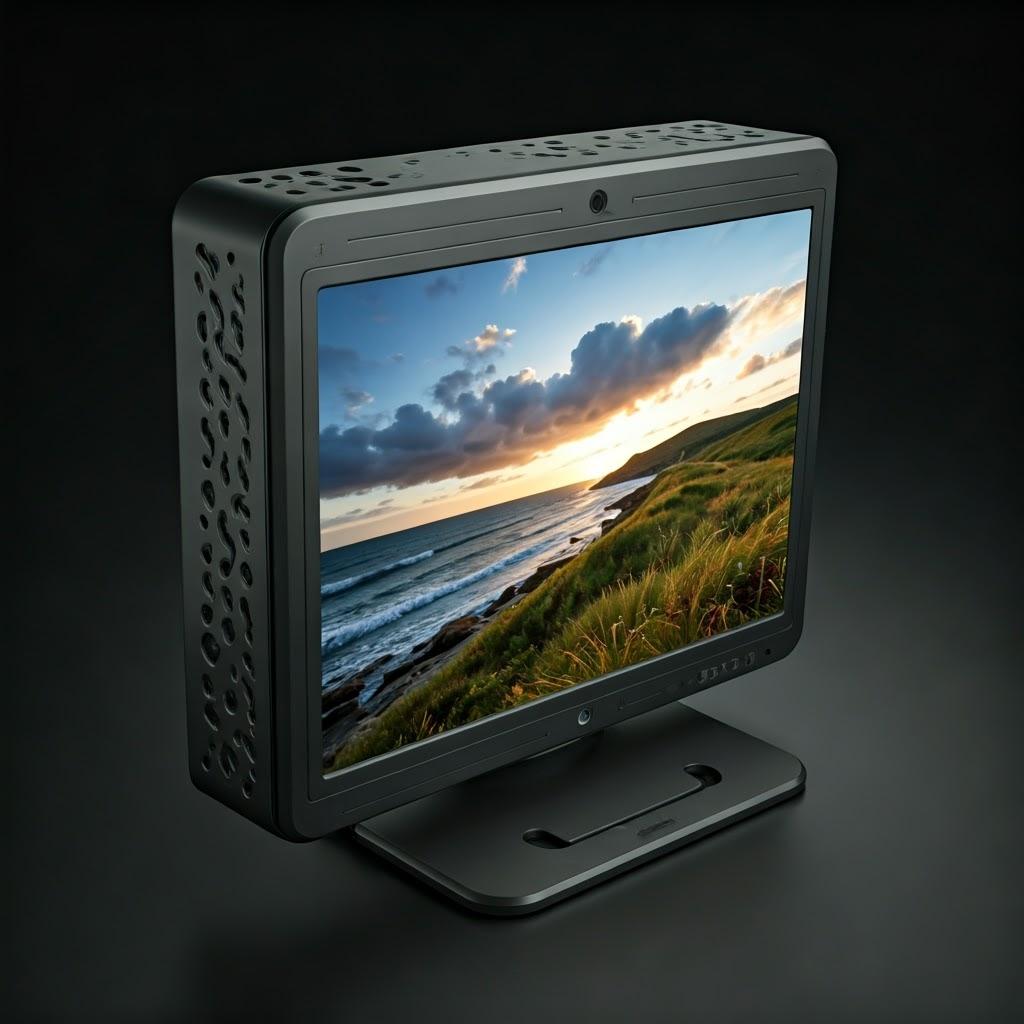
Elección de su socio: Selección del proveedor de servicios de impresión 3D en metal adecuado
The success of producing high-quality, reliable custom electronics mounts via metal additive manufacturing hinges significantly on the capabilities and expertise of your chosen manufacturing partner. Selecting the right proveedor de servicios de impresión 3D de metales is a critical decision for engineers and procurement managers, impacting not just the quality of the final part, but also lead times, cost-effectiveness, and the overall ease of the procurement process. This is more than just finding a supplier; it’s about establishing a partnership with a company that understands your technical requirements and business needs. When evaluating potential additive manufacturing contract manufacturing partners, consider the following crucial criteria:
- Proven Expertise & Industry Experience:
- Historial: Look for a provider with demonstrable experience in producing parts similar to your custom electronics mount (e.g., brackets, enclosures, heat sinks) using the specific materials you require (AlSi10Mg, 316L). Ask for case studies or examples relevant to your industry (aerospace, automotive, medical, industrial). Do they understand the unique challenges and standards of your sector?
- Profundidad técnica: Does the provider employ experienced AM engineers and metallurgists who can offer valuable DfAM consultation, material selection advice, and troubleshooting support? Access to knowledgeable personnel is invaluable.
- Company Background: Consider the provider’s history and focus. Are they specialists in metal AM? Companies like Met3dp Technology Co., LTD, with decades of collective expertise specifically in metal additive manufacturing, offer a depth of knowledge that broader manufacturing service bureaus might lack. Their focus extends from developing advanced SEBM printers to pioneering innovative metal powders, showcasing a comprehensive understanding of the entire AM ecosystem.
- Tecnología y equipo:
- Tecnología adecuada: While Laser Powder Bed Fusion (LPBF/SLM) is common for AlSi10Mg and 316L mounts, does the provider have well-maintained, industrial-grade machines from reputable manufacturers? Do they offer other technologies (like Met3dp’s SEBM) that might be relevant for other projects or materials?
- Construir volumen: Ensure the provider’s machines have a large enough build envelope to accommodate your largest mount design or to efficiently nest multiple smaller parts for production runs.
- Mantenimiento y calibración de la máquina: Industrial-grade AM requires rigorous maintenance and calibration schedules to ensure consistent accuracy and quality. Inquire about their procedures for machine upkeep, laser alignment, and process monitoring. Met3dp emphasizes the industry-leading print volume, accuracy, and reliability of its printers, suggesting a focus on robust equipment.
- Cartera de materiales y control de calidad:
- Disponibilidad de material: Confirm they routinely process AlSi10Mg and 316L and have established, validated parameters for these materials. Does their portfolio include other alloys that might be useful for future projects (e.g., Titanium alloys, Nickel superalloys, Copper alloys)?
- Calidad del polvo: This is paramount. Inquire about their powder sourcing and quality control procedures. Do they perform incoming powder inspection (chemistry, particle size distribution, morphology, flowability)? How do they handle powder storage, handling, and recycling to prevent contamination and ensure traceability?
- Producción interna de polvo: Providers like Met3dp, who manufacture their own high-quality metal powders using advanced Gas Atomization and PREP technologies, offer a distinct advantage. This vertical integration provides greater control over material quality, consistency between batches, and the ability to develop innovative or customized alloys tailored to specific application needs (e.g., TiNi, TiTa, TiAl, TiNbZr, CoCrMo). Sourcing from a partner with deep materials science expertise reduces risk significantly.
- Amplias funciones de posprocesamiento:
- Interno vs. Subcontratado: Does the provider have in-house capabilities for the essential post-processing steps required for your mount (stress relief/heat treatment, support removal, CNC machining, surface finishing, inspection)? In-house capabilities generally lead to better process control, integrated quality management, potentially shorter lead times, and simplified logistics compared to managing multiple subcontractors.
- Revestimiento o tratamiento de superficies: Verify they have the necessary equipment (e.g., calibrated vacuum/atmosphere furnaces for heat treatment, multi-axis CNC machining centers, various finishing tools, CMMs for inspection) and skilled technicians to perform these tasks to the required standards.
- Quality Certifications & Documentation:
- Certificaciones relevantes: Look for certifications appropriate to your industry and quality requirements.
- ISO 9001: Demonstrates a robust Quality Management System (QMS). (Fundamental requirement for most B2B suppliers).
- AS9100: Required for aerospace components, indicating adherence to stringent aerospace QMS standards.
- ISO 13485: Required for manufacturing medical devices, indicating a QMS tailored to medical device regulations.
- Traceability & Reporting: Ensure the provider can supply full material traceability documentation (powder batch certificates) and Certificates of Conformance (CoC) verifying that the parts meet specified requirements. Can they provide detailed inspection reports if needed?
- Certificaciones relevantes: Look for certifications appropriate to your industry and quality requirements.
- Engineering & Design Support:
- Consulta DfAM: Does the provider offer expert guidance on optimizing your design for additive manufacturing? Can they help identify opportunities for weight reduction, part consolidation, or performance improvement?
- Capacidades de simulación: Access to process simulation tools can help predict and mitigate issues like warping before printing begins.
- Enfoque Colaborativo: Look for a partner willing to work collaboratively to solve design challenges and ensure manufacturability.
- Lead Times, Communication & Scalability:
- Plazos de entrega realistas: Obtain clear estimates for quoting, production, and delivery. Understand the factors that influence lead times (complexity, quantity, machine availability, post-processing queue).
- Comunicación: Evaluate their responsiveness and communication clarity during the quoting process. Is there a dedicated point of contact (e.g., project manager) for B2B accounts?
- Escalabilidad: Can the provider handle your prototype needs as well as potential future increases in volume? Do they have the capacity and systems in place to manage larger B2B metal printing services orders reliably?
Choosing the right metal AM partner is a strategic decision. Thoroughly evaluating potential providers against these criteria will help ensure you select a capable, reliable partner like Met3dp, who can consistently deliver high-quality custom electronics mounts that meet your technical specifications and business objectives.
Understanding the Investment: Cost Factors and Lead Times for 3D Printed Mounts
One of the key considerations for adopting any manufacturing technology is understanding the associated costs and production timelines. Metal additive manufacturing presents a different cost structure compared to traditional methods like machining or injection molding, particularly advantageous for custom parts and lower volumes. Accurately estimating the el costo de la impresión 3D de metales y modelo de precios de fabricación aditiva requires considering several contributing factors.
Breakdown of Cost Drivers for Metal AM Mounts:
- Coste del material:
- Tipo de polvo: Different metal powders have vastly different costs per kilogram. High-performance alloys like titanium or nickel superalloys are significantly more expensive than stainless steel or aluminum alloys. Within our focus, 316L powder is generally more expensive than AlSi10Mg powder.
- Volumen utilizado: Calculated based on the volume of the final part más the volume of the support structures required. Efficient DfAM and support strategy directly impact material consumption.
- Reciclaje de polvo: Experienced providers recycle unused powder, which can help mitigate costs, but requires strict procedures to maintain quality. The efficiency and cost implications of recycling programs can factor into overall pricing.
- Tiempo de impresión: This is often a primary cost driver, determined by:
- Volumen de la pieza: Larger parts naturally take longer to melt and solidify.
- Altura de la pieza (altura Z): Each layer requires a recoating step, so taller parts (oriented vertically) take longer than flatter parts of the same volume.
- Complejidad: Intricate details and numerous disconnected features can increase the laser scanning time per layer.
- Eficiencia de anidamiento: Printing multiple parts simultaneously (nesting) improves overall machine utilization per build cycle, reducing the setup cost allocated per part, which is beneficial for wholesale 3D printing price calculations.
- Machine Usage: Calculated based on an hourly rate that covers:
- Machine Amortization: The cost of the expensive industrial AM equipment spread over its operational life.
- Costes operativos: Energy consumption (lasers, heaters, controls), inert gas (Argon/Nitrogen) consumption, filters, routine maintenance.
- Overhead: Facility costs, software licenses.
- Estructuras de apoyo:
- Volumen de material: Supports consume powder, adding to material cost.
- Esfuerzo de retirada: The labor and time required to remove supports post-print. Complex or poorly designed supports significantly increase this cost component.
- Post-procesamiento: The costs associated with necessary downstream steps can be substantial and vary greatly depending on requirements:
- Tratamiento térmico: Furnace time, energy, inert gas consumption, labor.
- Mecanizado CNC: Machine time (dependent on complexity, number of features, tolerance requirements), tooling, programming, labor.
- Acabado superficial: Labor, consumables (blasting media, polishing compounds), equipment time for each required step (blasting, tumbling, anodizing, passivation).
- Inspección: Time for dimensional checks (CMM), NDT, documentation.
- Trabajo: Skilled labor is required throughout the process:
- Engineering Review & Build Prep: DfAM checks, orientation optimization, support generation, slicing.
- Configuración y funcionamiento de la máquina: Loading powder, setting up the build, monitoring the print, unloading.
- Trabajo de postprocesado: Part removal, support removal, machining, finishing, inspection.
- Cantidad:
- Economías de escala: While AM doesn’t have the dramatic volume cost reductions seen with injection molding (due to tooling amortization), there are still benefits to batch production. Setup costs (engineering, machine setup) are spread over more parts. Batch processing in heat treatment, finishing, and QC can also improve efficiency. For larger B2B orders, discuss volume pricing with your provider.
Conceptual Cost Comparison (Custom Mount):
- Very Low Volume (1-10 units): AM is typically most cost-effective due to no tooling. CNC machining can be competitive if geometry is simple, but expensive for complex parts. Molding is prohibitive.
- Low-to-Medium Volume (10-1000 units): AM remains highly competitive, especially for complex designs or frequent iterations. CNC costs decrease but may still be higher for complexity. Molding puede start to break even at the higher end if the design is stable, but tooling is still a barrier.
- High Volume (1000+ units): For simple, stable designs, traditional methods like casting or stamping (if applicable) eventually become cheaper. However, if the mount retains high complexity or requires the specific performance benefits of AM (e.g., topology optimization), AM might remain a viable or even preferred industrial component cost solution depending on the value proposition.
Factores que influyen en los plazos de entrega:
The total time from order placement to receiving finished parts (3D printing lead time) involves multiple stages:
- Cotización: 1-3 business days (assuming complete technical data is provided).
- Engineering Review & Build Preparation: 1-2 business days.
- Cola de impresión: Highly variable, depends on the provider’s current workload (can range from 1 day to 1-2 weeks).
- Imprimiendo: 1-5+ business days, highly dependent on part size, height, complexity, and nesting.
- Post-procesamiento: 3-10+ business days, depending on the number and complexity of steps (heat treatment cycles, machining setup/runtime, finishing processes, inspection).
- Envío: Depends on location and chosen method.
Typical Total Lead Time: Puede variar entre 7 to 25 business days for standard projects. Expedited services may be available at a premium cost. Complex projects requiring extensive post-processing or facing queue backlogs can take longer. Clear communication with the provider is essential for managing expectations.
Getting Accurate Quotes: To receive prompt and accurate Presupuestos de FA B2B, provide your potential supplier with:
- Modelo CAD 3D (formato STEP preferido).
- 2D drawings (if specific tolerances, GD&T, or critical features are required).
- Clear material specification (e.g., AlSi10Mg-T6, 316L-Stress Relieved).
- Required quantity.
- Surface finish requirements (Ra values, specific treatments like anodizing/passivation).
- Post-processing requirements (e.g., specific machining operations, heat treatment specs).
- Testing or certification needs (CoC, material certs, inspection reports).
Understanding these cost factors and lead time components allows for better project planning, budgeting, and informed decision-making when considering metal AM for your custom electronics mounts.
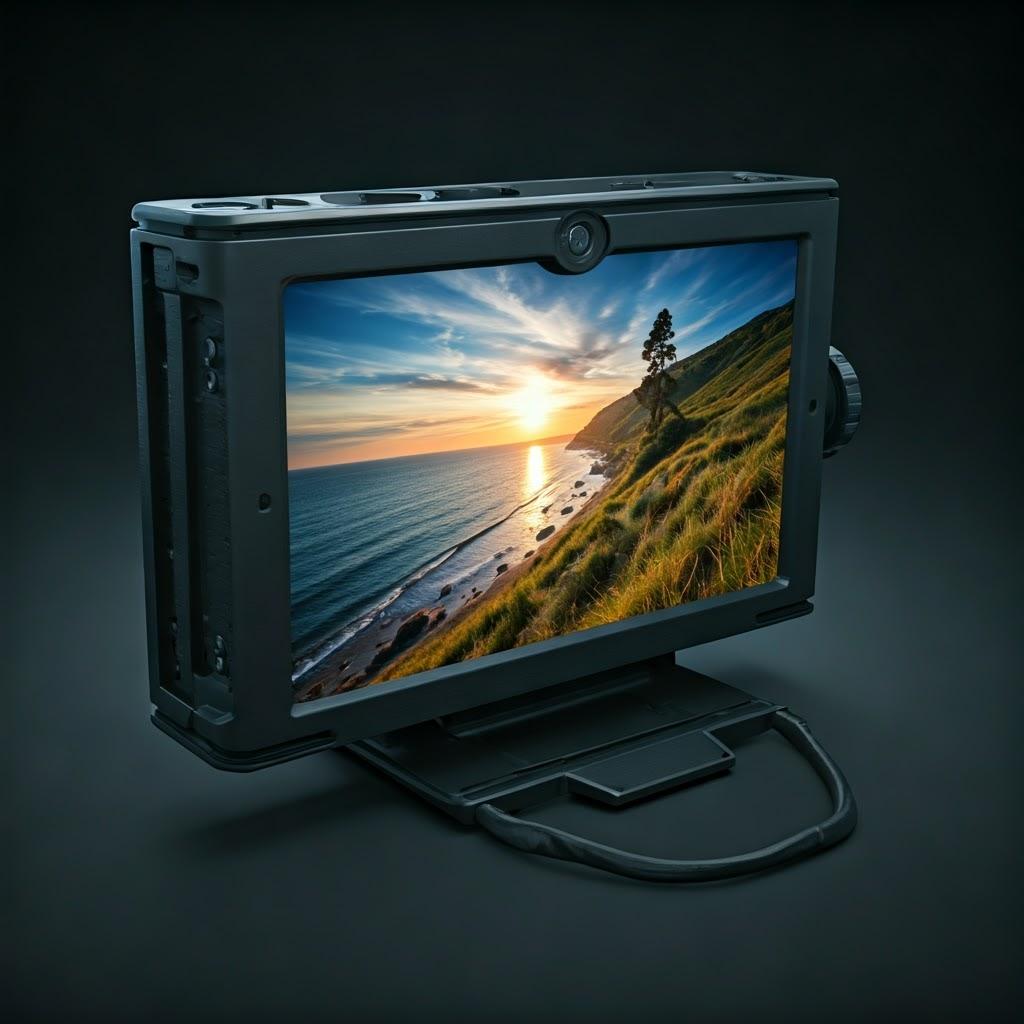
FAQ: Your Questions Answered on Custom Metal 3D Printed Electronics Mounts
Here are answers to some frequently asked questions regarding the use of metal additive manufacturing for custom electronics mounts:
Q1: What is the typical lead time for a custom metal 3D printed mount?
A: Lead times can vary significantly based on several factors, including part complexity, size, quantity, the specific AM process used, required post-processing steps, and the service provider’s current workload. However, for a typical project involving AlSi10Mg or 316L, expect a range of 7 to 25 business days from order confirmation to shipment. Simple prototypes might be faster (5-10 days), while complex parts requiring extensive machining or specialized finishing could take longer. Always confirm lead times with your chosen provider during the quoting stage.
Q2: How does the strength of 3D printed AlSi10Mg or 316L compare to wrought or cast equivalents?
A: Metal AM parts can exhibit excellent mechanical properties.
- AlSi10Mg: As-printed properties are typically comparable to or better than cast A360 aluminum. After proper T6 heat treatment, strength can approach that of some lower-strength wrought aluminum alloys, although ductility might be lower.
- 316L: Properties of LPBF-printed 316L (after stress relief) often exceed ASTM standards for cast 316L and can meet or exceed minimum requirements for wrought 316L, particularly in terms of yield and tensile strength. Ductility is generally very good (>30-40%). Achieving optimal properties depends heavily on high-quality powder (like Met3dp’s), validated process parameters, and correct post-processing (heat treatment, potentially HIP for critical applications). They are generally much stronger and more reliable than plastic counterparts.
Q3: Can threaded holes be directly printed into the mount?
A: While it’s technically possible to design and print internal thread geometries using high-resolution AM processes, it’s generally not recommended for functional metal threads. Directly printed threads often suffer from:
- Poor surface finish within the threads.
- Inaccurate thread profile dimensions.
- Reduced strength compared to conventionally cut threads due to the layer-wise structure and potential porosity. The best practice is to design and print pilot holes (appropriately sized for the desired tap) and then create the threads using conventional tapping during post-processing. This ensures accurate, strong, and standardized threads. Alternatively, designing pockets for threaded inserts (like Heli-Coils or heat-set inserts, though less common for metals) can be considered for specific applications.
Q4: Is metal 3D printing cost-effective for high-volume production of mounts?
A: The cost-effectiveness of metal AM is highly dependent on the part complexity, required customization, and the volume relative to traditional methods.
- Alta complejidad / Personalización: If the mount design is highly complex (e.g., topology optimized, consolidated assembly, internal channels), AM can remain cost-effective even at surprisingly high volumes because the alternative (e.g., complex multi-axis machining, multiple parts assembly, investment casting with intricate tooling) is also very expensive.
- Volúmenes bajos a medios: AM typically excels here (tens to low thousands) as it avoids high upfront tooling costs associated with injection molding or casting.
- Very High Volumes (tens of thousands+): For relatively simple mount designs that are stable (no frequent changes), traditional high-volume methods like stamping, die casting, or simplified machining will likely become more cost-effective per part. It’s essential to conduct a case-by-case analysis comparing the total cost of ownership (including design flexibility, lead time, assembly, performance benefits) when evaluating cost-effective additive manufacturing against traditional alternatives for your specific mount application and volume needs.
Conclusion: Elevate Your Designs with Precision Metal 3D Printed Mounts
In today’s demanding technological landscape, the reliable performance of sophisticated electronics relies heavily on robust, precisely engineered mounting solutions. As we’ve explored, custom electronics mounts manufactured using metal additive manufacturing offer a powerful alternative to the limitations of standard hardware and traditional fabrication methods. The ability to leverage libertad de diseño for complex geometries, achieve rapid prototyping and on-demand production, optimize for weight and performance, and utilize materiales de alto rendimiento like AlSi10Mg and 316L makes metal AM an indispensable tool for engineers across aerospace, automotive, medical, and industrial sectors.
From lightweight, thermally efficient brackets in avionics bays to durable, corrosion-resistant fixtures in harsh industrial environments, metal 3D printing enables the creation of mounting solutions perfectly tailored to the unique challenges of each application. Key advantages include:
- Personalización inigualable: Bespoke designs fitting exact component dimensions and complex integration requirements.
- Rendimiento mejorado: Optimization for thermal management, vibration damping, and structural integrity.
- Innovación acelerada: Faster design iteration and quicker deployment of new electronic systems.
- Eficiencia de la cadena de suministro: On-demand production reduces inventory needs and simplifies sourcing for specialized components.
Successfully harnessing these benefits requires careful consideration of DfAM principles, understanding achievable precision, planning necessary post-processing steps, and navigating potential manufacturing challenges. Critically, it demands partnering with a knowledgeable and capable metal AM service provider.
Look for providers with proven expertise, robust technology, stringent quality control (especially regarding materials), comprehensive post-processing capabilities, and relevant industry certifications. Met3dp Technology Co., LTD stands out as a leader in this field, offering comprehensive solutions that span cutting-edge SEBM and other AM printers, advanced metal powders manufactured in-house using state-of-the-art atomization techniques, and expert application development services. Their commitment to quality and innovation empowers organizations to implement 3D printing effectively and accelerate their digital manufacturing transformations.
Ready to elevate your next electronics project with custom, high-performance metal mounts? Explore the possibilities of additive manufacturing. We encourage you to contacte con Met3dp to discuss your specific requirements, request a quote, or learn more about how their capabilities in advanced printing systems and superior metal powders can power your organization’s additive manufacturing goals and deliver next-generation manufacturing solutions today.
Compartir
MET3DP Technology Co., LTD es un proveedor líder de soluciones de fabricación aditiva con sede en Qingdao, China. Nuestra empresa está especializada en equipos de impresión 3D y polvos metálicos de alto rendimiento para aplicaciones industriales.
Solicite información para obtener el mejor precio y una solución personalizada para su empresa.
Artículos relacionados
Acerca de Met3DP
Actualización reciente
Nuestro producto
CONTACTO
¿Tiene alguna pregunta? ¡Envíenos un mensaje ahora! Atenderemos su solicitud con todo un equipo tras recibir su mensaje.
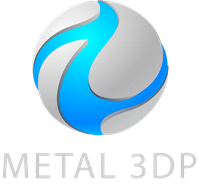
Polvos metálicos para impresión 3D y fabricación aditiva