Aplicación del DED en el ámbito aeroespacial
Índice
Imagine un mundo en el que los componentes complejos de los aviones puedan construirse capa por capa, a la carta y con el mínimo desperdicio. Esto no es ciencia ficción; es la realidad de la deposición de energía dirigida (DED), una tecnología puntera de fabricación aditiva (AM) que está transformando rápidamente la industria aeroespacial.
El DED, también conocido como Laser Engineered Net Shaping (LENS), utiliza una fuente de energía focalizada, como un láser o un haz de electrones, para fundir y depositar polvo metálico, construyendo meticulosamente un objeto tridimensional. Es como una impresora 3D de alta tecnología para metal, que ofrece una libertad de diseño y una personalización sin precedentes para aplicaciones aeroespaciales.
Pero, ¿cómo está arrasando la DED en la industria aeroespacial? Abróchese el cinturón para adentrarnos en el fascinante mundo de las aplicaciones DED, explorar los diversos polvos metálicos utilizados y responder a algunas preguntas candentes sobre esta revolucionaria tecnología.
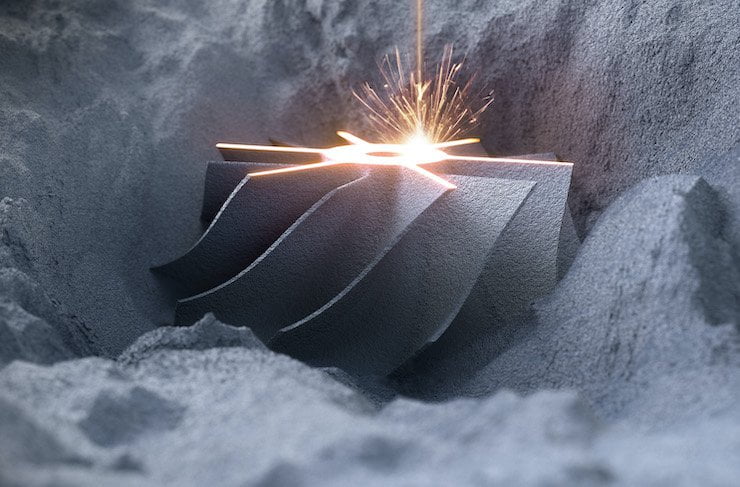
DED: Un cambio de juego para la fabricación aeroespacial
Tradicionalmente, los componentes aeroespaciales se fabricaban mediante métodos convencionales como la fundición, la forja y el mecanizado. Estos procesos suelen dar lugar a un importante desperdicio de material y a limitaciones en la complejidad del diseño. El DED rompe este paradigma al ofrecer multitud de ventajas:
- Aligeramiento: El DED permite crear estructuras intrincadas y huecas, lo que reduce significativamente el peso, un factor crítico para la eficiencia del combustible y la capacidad de carga útil de las aeronaves.
- Libertad de diseño: Sin las limitaciones de la fabricación tradicional, el DED permite crear geometrías complejas con canales internos y celosías, optimizando el rendimiento y la distribución del peso.
- Creación rápida de prototipos: El DED permite fabricar prototipos con rapidez, lo que acelera el ciclo de diseño y desarrollo de nuevos componentes aeroespaciales.
- Fabricación a la carta: El DED facilita la creación de piezas de repuesto en el punto de necesidad, lo que reduce la dependencia de componentes prefabricados y minimiza el tiempo de inactividad.
- Eficiencia del material: El DED utiliza un enfoque de forma casi neta, lo que minimiza el desperdicio de material en comparación con los métodos tradicionales.
- Reparación y restauración: La DED puede utilizarse para reparar componentes dañados, alargando su vida útil y reduciendo la necesidad de costosas sustituciones.
Estas ventajas se traducen en una serie de interesantes aplicaciones en el campo aeroespacial:
- Fabricación de componentes de motores de aviación: El DED está causando sensación en la producción de componentes complejos de motores, como álabes de turbina, cámaras de combustión e intercambiadores de calor. La DED permite crear componentes con canales de refrigeración internos avanzados, lo que mejora la eficiencia y el rendimiento.
- DED para fuselaje de aeronaves y otros componentes estructurales: La capacidad del DED para crear estructuras ligeras y de alta resistencia lo hace ideal para fabricar secciones de fuselajes de aviones, componentes de trenes de aterrizaje y otros elementos estructurales.
- Personalización y reparación: El DED permite la personalización bajo demanda de las piezas de las aeronaves, lo que permite realizar modificaciones para cumplir requisitos específicos de la misión. Además, el DED puede utilizarse para reparar in situ componentes dañados, lo que reduce el tiempo de inactividad y los costes de mantenimiento.
Polvos metálicos: Los pilares del éxito del DED
El éxito de la DED depende de los polvos metálicos específicos que se utilicen. Estos polvos, cuyo tamaño y morfología (forma) se controlan con precisión, desempeñan un papel crucial en la calidad y el rendimiento del producto final. A continuación presentamos algunos de los polvos metálicos más utilizados en las aplicaciones DED aeroespaciales:
**Polvo metálico | Descripción | Propiedades |
---|---|---|
Inconel 625 | Superaleación versátil a base de níquel-cromo conocida por su excepcional resistencia a altas temperaturas, resistencia a la oxidación y buena soldabilidad. | Ofrece excelentes propiedades mecánicas a temperaturas elevadas, por lo que es ideal para álabes de turbinas, cámaras de combustión y otros componentes de sección caliente. |
Titanio 6Al-4V | Aleación de titanio de alta resistencia y bajo peso muy utilizada en la industria aeroespacial. | Proporciona un buen equilibrio entre resistencia, ductilidad y ahorro de peso, por lo que es adecuado para componentes de fuselajes, piezas de trenes de aterrizaje y soportes de motores. |
Aleaciones de aluminio | Familia de aleaciones ligeras de aluminio con propiedades variables en función de su composición específica. | Ofrecen una excelente relación resistencia-peso y una buena resistencia a la corrosión, por lo que son adecuados para componentes estructurales no críticos y cajas ligeras. |
Acero inoxidable 316L | Acero inoxidable austenítico versátil conocido por su excelente resistencia a la corrosión. | Ofrece buenas propiedades mecánicas y resistencia a la corrosión, por lo que es adecuado para diversas aplicaciones como componentes de conducción de fluidos y piezas no estructurales. |
Inconel 718 | Superaleación a base de níquel-cromo endurecida por precipitación, de gran resistencia y buena maquinabilidad. | Ofrece una combinación de alta resistencia, buena resistencia a la corrosión y excelente maquinabilidad, por lo que es ideal para diversos componentes estructurales y aplicaciones de alta presión. |
Acero martensítico envejecido | Familia de aceros de alta resistencia y baja aleación con excelente tenacidad y estabilidad dimensional. | Proporcionan una resistencia y tenacidad excepcionales, por lo que son adecuados para componentes de trenes de aterrizaje y elementos estructurales sometidos a grandes esfuerzos. |
Aleaciones de níquel | Amplia categoría de aleaciones a base de níquel con propiedades diversas en función de su composición específica. | Ofrecen una amplia gama de propiedades, como resistencia a altas temperaturas, resistencia a la corrosión y resistencia al desgaste, lo que las hace adecuadas para diversos componentes del motor y aplicaciones de alto desgaste. |
Aleaciones de cobalto-cromo | Familia de aleaciones de cobalto-cromo conocidas por su gran resistencia al desgaste y biocompatibilidad. | Ofrecen una excepcional resistencia al desgaste y una buena biocompatibilidad, por lo que son ideales para aplicaciones como cojinetes de motores a reacción e implantes biomédicos (aunque las aplicaciones de DED en biomedicina quedan fuera del ámbito de este artículo). |
Aleaciones de cobre | Familia de aleaciones de cobre con propiedades variables en función de su composición específica. | Ofrecen una elevada conductividad eléctrica y una buena conductividad térmica, lo que las hace adecuadas para intercambiadores de calor y componentes eléctricos. |
Metales refractarios | Grupo de metales de alto punto de fusión, como el wolframio, el tántalo y el molibdeno. | Poseen una excepcional resistencia a altas temperaturas y a entornos agresivos, lo que los hace idóneos para aplicaciones como toberas de motores de cohetes y vehículos de reentrada. |
Es importante señalar que ésta no es una lista exhaustiva, y que la investigación en curso está desarrollando constantemente nuevos y mejores polvos metálicos específicamente adaptados para DED aplicaciones. La selección del polvo metálico óptimo depende de varios factores, como las propiedades finales deseadas del componente, el entorno operativo y consideraciones de coste.
Ventajas y limitaciones de DED
Aunque el DED ofrece un sinfín de ventajas para la industria aeroespacial, no está exento de limitaciones. He aquí una visión equilibrada de las dos caras de la moneda:
Ventajas:
- Libertad de diseño: Como ya se ha mencionado, el DED abre un mundo de posibilidades de diseño, permitiendo la creación de geometrías complejas antes inimaginables con las técnicas tradicionales.
- Aligeramiento: La capacidad de crear estructuras huecas con celosías internas se traduce en un importante ahorro de peso, un factor crítico para el rendimiento de los aviones.
- Reducción de residuos: El DED utiliza un enfoque de forma casi neta, lo que minimiza el desperdicio de material en comparación con los métodos tradicionales.
- Creación rápida de prototipos: El DED facilita la creación rápida de prototipos, acelerando el ciclo de diseño y desarrollo de nuevos componentes aeroespaciales.
- Fabricación a la carta: El DED permite la producción bajo demanda de piezas de repuesto, lo que reduce la dependencia de componentes prefabricados y minimiza el tiempo de inactividad.
- Reparación y restauración: La DED puede utilizarse para reparar componentes dañados, alargando su vida útil y reduciendo la necesidad de costosas sustituciones.
Limitaciones:
- Tiempo de construcción: Aunque es más rápido que los métodos tradicionales, el DED puede seguir siendo un proceso relativamente lento en comparación con algunas técnicas sustractivas, especialmente para componentes de mayor tamaño.
- Acabado superficial: Los componentes fabricados con DED suelen requerir pasos adicionales de postprocesado para conseguir el acabado superficial deseado.
- Disponibilidad de material: La disponibilidad de determinados polvos metálicos, en particular las aleaciones de alto rendimiento, puede ser limitada y cara.
- Control de procesos: La DED es un proceso complejo que requiere un control minucioso de parámetros como la potencia del láser, la velocidad de escaneado y el avance del polvo para garantizar una calidad uniforme y evitar defectos.
- Cualificación y certificación: Los componentes DED requieren rigurosas pruebas y certificaciones para cumplir las estrictas normas de seguridad aeroespacial.
El futuro del DED en el sector aeroespacial
A pesar de estas limitaciones, el futuro de la DED en el sector aeroespacial es prometedor. A medida que avance la tecnología, disminuirán los tiempos de fabricación, mejorará la calidad de las superficies y aumentará la disponibilidad de polvos metálicos de alto rendimiento. Además, la investigación en curso se centra en el desarrollo de nuevas técnicas de DED, como la impresión multimaterial y la supervisión in situ del proceso, lo que ampliará aún más sus capacidades.
El impacto potencial de DED en la industria aeroespacial es enorme. Puede revolucionar el diseño y la fabricación de aeronaves, dando lugar a vehículos más ligeros, eficientes y rentables. Además, el DED puede permitir reparaciones a demanda sobre el terreno, reduciendo el tiempo de inactividad por mantenimiento y mejorando la disponibilidad operativa.
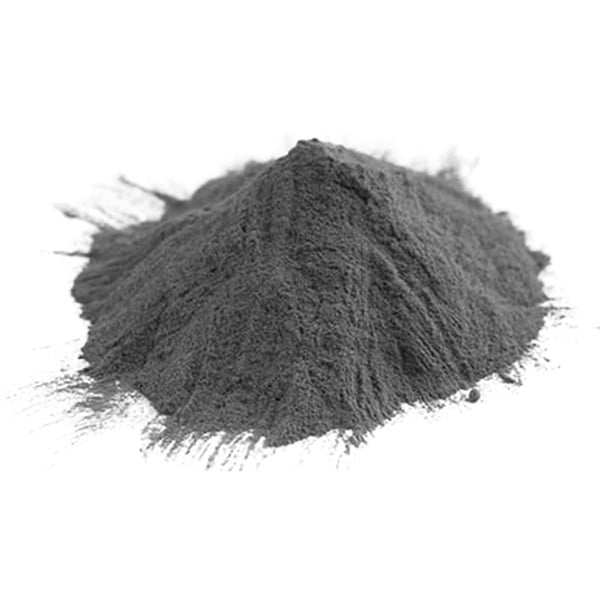
Preguntas frecuentes
A continuación figuran algunas preguntas frecuentes sobre DED en la industria aeroespacial, presentadas en forma de tabla para facilitar su consulta:
Pregunta | Respuesta |
---|---|
¿Cuáles son las principales ventajas de utilizar DED en aplicaciones aeroespaciales? | DED ofrece libertad de diseño, aligeramiento, reducción de residuos, creación rápida de prototipos, fabricación bajo demanda y capacidad de reparación. |
¿Cuáles son algunos de los retos asociados a la DED? | El tiempo de fabricación, el acabado superficial, la disponibilidad de materiales, el control de procesos y la cualificación para aplicaciones aeroespaciales son algunas de las principales limitaciones. |
¿Cuáles son los polvos metálicos más utilizados en DED para el sector aeroespacial? | Inconel 625, titanio 6Al-4V, aleaciones de aluminio, acero inoxidable 316L, Inconel 718, acero martensítico envejecido, aleaciones de níquel, aleaciones de cobalto-cromo, aleaciones de cobre y metales refractarios son algunas de las principales opciones. |
¿Cómo influirá el DED en el futuro de la fabricación aeroespacial? | El DED tiene el potencial de revolucionar la fabricación aeroespacial al permitir la creación de aeronaves más ligeras, eficientes y rentables. Las reparaciones a la carta y la reducción del tiempo de inactividad son ventajas adicionales. |
¿Es la DED una tecnología madura para aplicaciones aeroespaciales? | El DED aún está en fase de desarrollo, pero está madurando rápidamente. Las investigaciones en curso abordan limitaciones como el tiempo de fabricación y el acabado superficial. |
¿Cuáles son los mayores obstáculos para la adopción generalizada del DED en el sector aeroespacial? | La cualificación y certificación de los componentes DED para su uso en vuelo es un obstáculo importante. Además, se necesita una mayor disponibilidad de polvos metálicos de alto rendimiento a precios competitivos. |
¿Puede utilizarse el DED para reparaciones fuera de entornos controlados? | Se están investigando sistemas móviles de DED que permitan realizar reparaciones sobre el terreno. Sin embargo, esta tecnología está aún en sus primeras fases. |
El elemento humano: Por qué es importante el DED
Más allá de los avances técnicos, el DED representa un cambio en la forma de concebir la fabricación aeroespacial. Permite un enfoque más ágil y receptivo, que fomenta la innovación y la personalización. Imaginemos un mundo en el que las piezas de repuesto puedan imprimirse bajo demanda en ubicaciones remotas, o los componentes dañados puedan repararse sobre el terreno, minimizando el tiempo de inactividad y maximizando la eficiencia operativa. Esto no sólo se traduce en un ahorro de costes, sino que también mejora la seguridad y la preparación de las misiones.
La historia del DED en el sector aeroespacial no trata sólo de tecnología, sino del ingenio humano y el espíritu de resolución de problemas que impulsan los avances. Se trata de superar los límites de lo posible y crear un futuro en el que el transporte aéreo no sólo sea más rápido y eficiente, sino también menos perjudicial para el medio ambiente. Mientras el DED sigue evolucionando, una cosa es segura: su impacto potencial en la industria aeroespacial no tiene límites.
Compartir
MET3DP Technology Co., LTD es un proveedor líder de soluciones de fabricación aditiva con sede en Qingdao, China. Nuestra empresa está especializada en equipos de impresión 3D y polvos metálicos de alto rendimiento para aplicaciones industriales.
Solicite información para obtener el mejor precio y una solución personalizada para su empresa.
Artículos relacionados
Acerca de Met3DP
Actualización reciente
Nuestro producto
CONTACTO
¿Tiene alguna pregunta? ¡Envíenos un mensaje ahora! Atenderemos su solicitud con todo un equipo tras recibir su mensaje.
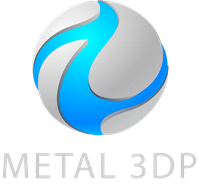
Polvos metálicos para impresión 3D y fabricación aditiva