Sistema de depuración
Índice
La fabricación aditiva, más conocida como impresión 3D, ha arrasado en todo el mundo. Desde la creación de prototipos hasta la producción a gran escala, ofrece una flexibilidad y eficiencia sin precedentes. Un aspecto crucial de este proceso, pero que a menudo se pasa por alto, es la eliminación de polvo. Adentrémonos en el mundo de la sistemas de depuración, explorar diversos polvos metálicos, sus modelos específicos y comprender las aplicaciones, ventajas y limitaciones de estos sistemas.
Visión general de los sistemas de depuración
Los sistemas de desempolvado son esenciales para eliminar el exceso de polvo de las piezas impresas en 3D, garantizando un producto limpio y acabado. Este proceso es especialmente vital en industrias en las que la precisión y la limpieza son primordiales, como los sectores aeroespacial, médico y de automoción. Estos sistemas ayudan a reducir el trabajo manual, aumentar la eficiencia y mejorar la calidad general de las piezas impresas.
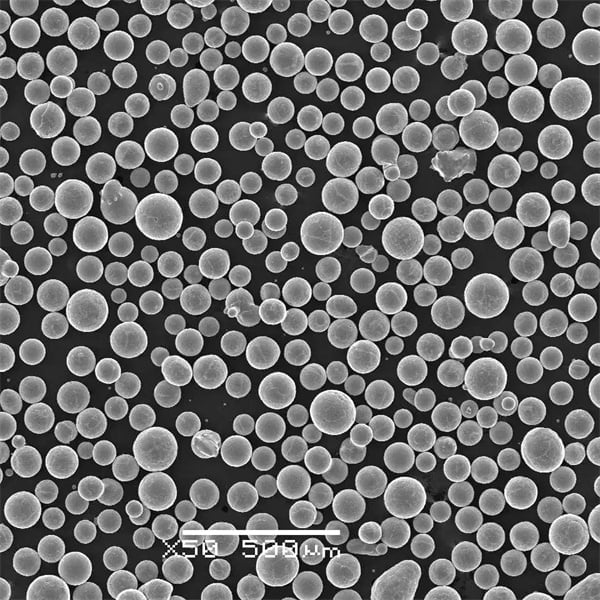
Tipos de polvos metálicos para Sistemas de depuración
En la fabricación aditiva se utilizan diferentes polvos metálicos, cada uno con propiedades y aplicaciones únicas. Veamos algunos modelos concretos y sus características:
Modelo de polvo metálico | Composición | Propiedades | Características |
---|---|---|---|
AlSi10Mg | Aluminio, silicio, magnesio | Ligero, de gran resistencia | Excelentes propiedades térmicas, resistente a la corrosión |
Ti6Al4V | Titanio, Aluminio, Vanadio | Alta resistencia y ligereza | Biocompatible, utilizado en implantes médicos |
Inconel 718 | Níquel, cromo, hierro | Resistente a altas temperaturas y a la corrosión | Utilizado en entornos aeroespaciales y de alta tensión |
Acero inoxidable 316L | Hierro, cromo, níquel | Alta resistencia a la corrosión, fuerza | Ideal para aplicaciones médicas y alimentarias |
CoCr | cobalto, cromo | Alta resistencia al desgaste, biocompatible | Se utiliza en implantes dentales y médicos |
Acero martensítico envejecido | Hierro, níquel, cobalto, molibdeno | Alta resistencia, tenacidad | Se utiliza en utillaje y piezas de alto rendimiento |
Cobre C18150 | Cobre, cromo, circonio | Excelente conductividad eléctrica | Se utiliza en aplicaciones eléctricas y térmicas |
AlSi7Mg | Aluminio, silicio, magnesio | Ligero y duradero | Se utiliza en componentes de automoción y aeroespaciales |
Hastelloy X | Níquel, cromo, molibdeno | Resistente a la oxidación, alta resistencia | Utilizado en equipos de procesamiento químico |
Acero inoxidable 17-4 PH | Hierro, cromo, níquel, cobre | Alta resistencia, resistente a la corrosión | Utilizado en la industria aeroespacial y petroquímica |
Aplicaciones de los sistemas de depuración
Los sistemas de depowdering se utilizan en diversos sectores, mejorando la calidad y la funcionalidad de las piezas impresas en 3D. Echemos un vistazo a sus aplicaciones:
Aplicación | Industria | Detalles |
---|---|---|
Componentes aeroespaciales | Aeroespacial | Piezas de precisión como álabes de turbina y componentes estructurales. |
Implantes médicos | Médico | Implantes limpios y biocompatibles, como articulaciones de cadera y coronas dentales. |
Piezas de automóviles | Automoción | Piezas duraderas y ligeras para motores, escapes y componentes del chasis. |
Conductores eléctricos | Electrónica | Piezas eficientes y de alta conductividad para la gestión eléctrica y térmica. |
Herramientas y prototipos | Fabricación | Herramientas de alta resistencia y prototipos rápidos para el desarrollo de productos. |
Equipos de procesamiento químico | Procesado químico | Piezas resistentes a la corrosión y de alta resistencia para reactores y sistemas de tuberías. |
Equipos de procesamiento de alimentos | Industria alimentaria | Componentes higiénicos y resistentes a la corrosión para la producción y el envasado de alimentos. |
Implantes dentales | Dental | Coronas dentales, puentes y aparatos de ortodoncia de precisión. |
Aplicaciones de alta temperatura | Energía | Componentes para turbinas y otros entornos de alta tensión y temperatura. |
Piezas resistentes al desgaste | Maquinaria industrial | Piezas de alta resistencia al desgaste para maquinaria y equipos pesados. |
Especificaciones, tamaños, calidades y normas de los polvos metálicos
Cada polvo metálico utilizado en la fabricación aditiva tiene normas y especificaciones específicas que garantizan un rendimiento y una calidad óptimos.
Modelo de polvo metálico | Gama de tamaños (micras) | Grado | Normas |
---|---|---|---|
AlSi10Mg | 15-45 | Grados AM | ASTM F3318 |
Ti6Al4V | 15-53 | Grado 23 (ELI) | ASTM F1472, ASTM F2924 |
Inconel 718 | 15-45 | UNS N07718 | ASTM F3055 |
Acero inoxidable 316L | 15-45 | UNS S31603 | ASTM F3184 |
CoCr | 10-50 | Aleación de CoCrMo | ASTM F75, ASTM F1537 |
Acero martensítico envejecido | 15-45 | 18Ni300 | AMS 6514, ASTM A538 |
Cobre C18150 | 15-45 | C18150 | ASTM B631 |
AlSi7Mg | 15-45 | Grados AM | DIN EN 1706 |
Hastelloy X | 15-45 | UNS N06002 | ASTM F3055 |
Acero inoxidable 17-4 PH | 15-45 | UNS S17400 | ASTM A564, AMS 5604 |
Proveedores y precios
A la hora de abastecerse de polvos metálicos para la fabricación aditiva, es esencial tener en cuenta los proveedores y los precios. A continuación se ofrece un análisis detallado de algunos proveedores destacados y sus estructuras de precios:
Proveedor | Modelo de polvo metálico | Gama de precios (por kg) | Servicios adicionales |
---|---|---|---|
Tecnologías de superficie Praxair | AlSi10Mg | $70 – $90 | Mezclas de polvos personalizadas, asistencia técnica |
Tecnología Carpenter | Ti6Al4V | $300 – $400 | Tratamiento térmico, ensayo de materiales |
Sandvik | Inconel 718 | $200 – $250 | Tamaños de polvo personalizados, opciones de entrega |
Oerlikon | Acero inoxidable 316L | $100 – $150 | Revestimiento de superficies, ayuda a la aplicación |
Arcam | CoCr | $200 – $300 | Desarrollo de procesos, asistencia a la certificación |
EOS GmbH | Acero martensítico envejecido | $150 – $200 | Amplias bibliotecas de material, asistencia |
Höganäs | Cobre C18150 | $90 – $120 | Propiedades del polvo a medida, apoyo logístico |
Renishaw | AlSi7Mg | $70 – $90 | Ingeniería de aplicaciones, soluciones de software |
VDM Metales | Hastelloy X | $250 – $300 | Mezclas en polvo especializadas, asesoramiento técnico |
Aditivos GKN | Acero inoxidable 17-4 PH | $120 – $160 | Soluciones avanzadas de pulvimetalurgia |
Comparación de pros y contras de Sistemas de depuración
Los sistemas de depuración ofrecen numerosas ventajas, pero también tienen algunas limitaciones. Comparemos los pros y los contras:
Ventajas | Limitaciones |
---|---|
Mayor eficacia | Inversión inicial elevada |
Mejora de la calidad de las piezas | Requisitos de mantenimiento |
Reducción del trabajo manual | Espacio necesario |
Seguridad reforzada | Se necesitan conocimientos técnicos |
Resultados coherentes | Posible tiempo de inactividad por reparaciones |
Adecuado para geometrías complejas | Específico para determinados polvos metálicos |
Contaminación reducida | Curva de aprendizaje para operadores |
Escalabilidad | Posibilidad de daños en las piezas |
Rentable a largo plazo | Generación de ruido y polvo |
Beneficios medioambientales | Disponibilidad limitada de algunos sistemas |
Entender los sistemas de depuración: En profundidad
¿Cómo funcionan los sistemas de depuración?
Los sistemas de eliminación de polvo utilizan varias técnicas para eliminar el exceso de polvo de las piezas impresas en 3D. Entre ellas se incluyen:
- Soplado de aire: Los chorros de aire a alta presión eliminan el polvo suelto de la pieza.
- Vibración: Las vibraciones mecánicas eliminan el exceso de polvo.
- Vacío: Los sistemas de aspiración eliminan el polvo, a menudo se utilizan junto con el soplado de aire.
- Cepillos automatizados: Los cepillos mecánicos eliminan suavemente el polvo de la superficie.
- Limpieza por ultrasonidos: Las ondas ultrasónicas agitan y desprenden las partículas de polvo.
Ventajas de los sistemas de depuración
Los sistemas de depowdering aportan varias ventajas al proceso de fabricación aditiva:
- Eficacia: La automatización del proceso de limpieza reduce significativamente el tiempo necesario en comparación con la limpieza manual.
- Precisión: Garantiza que las geometrías intrincadas y complejas se limpien a fondo sin dañar la pieza.
- Seguridad: Reduce la exposición de los operarios a polvos potencialmente peligrosos, mejorando la seguridad en el lugar de trabajo.
- Consistencia: Proporciona resultados uniformes en las distintas piezas, garantizando estándares de alta calidad.
- Escalabilidad: Ideal para la producción a gran escala, donde la consistencia y la velocidad son cruciales.
Desventajas de los sistemas de depuración
Sin embargo, estos sistemas también tienen sus inconvenientes:
- Coste: La elevada inversión inicial y los costes de mantenimiento pueden ser un obstáculo para las pequeñas empresas.
- Conocimientos técnicos: Requiere operadores cualificados para gestionar y solucionar los problemas de los sistemas con eficacia.
- Espacio: Algunos sistemas requieren mucho espacio
- Diseño del sistema: Un sistema de eliminación de polvo bien diseñado incorporará características como flujos de aire ajustables, ajustes de vibración personalizables y mecanismos precisos de recogida de polvo. Estas características ayudan a adaptar el sistema a distintas geometrías de piezas y tipos de polvo.
- Integración de la tecnología: Los sistemas avanzados de depuración suelen integrar tecnologías como el cepillado automático, los aspiradores de alta eficacia y los limpiadores ultrasónicos para garantizar un proceso de limpieza exhaustivo y eficaz.
- Mantenimiento y durabilidad: El mantenimiento regular es crucial para que el sistema funcione al máximo rendimiento. Los componentes duraderos y los puntos de mantenimiento accesibles pueden reducir el tiempo de inactividad y prolongar la vida útil del sistema.
- Consideraciones medioambientales: Los sistemas eficaces se diseñan teniendo en cuenta el medio ambiente. Esto incluye características como sistemas de recogida de polvo, medidas de reducción del ruido y operaciones energéticamente eficientes.
Elección del sistema de depuración adecuado a sus necesidades
La selección de un sistema de depowdering depende de varios factores, como el tamaño de sus tiradas de producción, la complejidad de las piezas que imprime y su presupuesto. Estas son algunas pautas que le ayudarán a elegir el sistema adecuado:
- Complejidad de las piezas: Para piezas complejas con detalles finos, elija un sistema con capacidad de limpieza de alta precisión, como limpiadores ultrasónicos o sistemas avanzados de soplado de aire.
- Volumen de producción: Para grandes volúmenes de producción, opte por sistemas automatizados que ofrezcan escalabilidad y eficacia, como sistemas vibratorios a gran escala o sistemas de vacío de alta velocidad.
- Limitaciones presupuestarias: Si tiene un presupuesto ajustado, piense en sistemas básicos que ofrezcan funciones básicas de almacenamiento, pero que satisfagan sus necesidades.
Aplicaciones y casos de uso de los sistemas de depuración
Exploremos algunos casos de uso y escenarios específicos en los que se emplean sistemas de depowdering.
Industria aeroespacial
En la industria aeroespacial, componentes como los álabes de las turbinas y las piezas estructurales deben estar libres de cualquier exceso de polvo para cumplir las estrictas normas de seguridad y rendimiento. Los sistemas de desempolvado garantizan que estos componentes se limpien a fondo antes de someterlos a un procesamiento posterior.
Ejemplo: Limpieza de álabes de turbina
- Desafío: Los álabes de las turbinas tienen intrincados canales de refrigeración y finas características que requieren una limpieza cuidadosa.
- Solución: Los sistemas de desempolvado de alta precisión utilizan una combinación de soplado de aire y aspiración al vacío para eliminar el polvo sin dañar la cuchilla.
Ámbito médico
Para los implantes y dispositivos médicos, la limpieza y la biocompatibilidad son de suma importancia. Los sistemas de depuración ayudan a cumplir las normas exigidas para implantes como articulaciones de cadera, coronas dentales y dispositivos de ortodoncia.
Ejemplo: Implantes de articulación de cadera
- Desafío: Los implantes deben estar libres de contaminantes para garantizar su seguridad para uso humano.
- Solución: Se utilizan sistemas especializados con filtración de partículas finas y cuidadosos procesos de manipulación para garantizar que los implantes estén limpios y listos para la esterilización.
Fabricación de automóviles
En la fabricación de automóviles, piezas como los componentes del motor y los elementos del chasis deben ser a la vez ligeras y resistentes. Los sistemas de depuración contribuyen a producir piezas de alta calidad que cumplen las exigentes especificaciones de la industria del automóvil.
Ejemplo: Componentes del motor
- Desafío: Las piezas deben limpiarse eficazmente para eliminar el exceso de polvo de geometrías complejas.
- Solución: Los sistemas automatizados de depuración con parámetros ajustables se encargan de la limpieza de diversas piezas del motor.
Electrónica
En el caso de los componentes electrónicos, como conectores y placas de circuitos, la eliminación del exceso de polvo es fundamental para garantizar unas conexiones eléctricas adecuadas y la funcionalidad del dispositivo.
Ejemplo: Conectores eléctricos
- Desafío: El exceso de polvo puede interferir con las conexiones eléctricas.
- Solución: Los sistemas de desempolvado con precisos chorros de aire y sistemas de vacío eliminan el polvo sin afectar a los conectores.
Procesado de alimentos
En la industria alimentaria, las piezas y equipos utilizados para el procesado de alimentos deben cumplir estrictas normas de higiene y seguridad. Los sistemas de depuración ayudan a mantener estas normas.
Ejemplo: Equipos de envasado de alimentos
- Desafío: El equipo debe estar limpio y libre de contaminantes para garantizar la seguridad alimentaria.
- Solución: Para los equipos de envasado de alimentos se utilizan sistemas diseñados con materiales higiénicos y superficies fáciles de limpiar.
Ventajas e inconvenientes de las distintas técnicas de depuración
He aquí un análisis detallado de las distintas técnicas de depuración, comparando sus pros y sus contras.
Soplado de aire frente a sistemas de vacío
Técnica | Pros | Contras |
---|---|---|
Soplado de aire | - Rápido y eficaz para piezas grandes. | - Puede ser menos eficaz para geometrías finas o complejas. |
- Sencillo y fácil de configurar. | - Potencial de dispersión de polvo en el medio ambiente. | |
Sistemas de vacío | - Eficaz para eliminar polvos finos. | - Puede ser más caro. |
- Minimiza la dispersión del polvo y el impacto medioambiental. | - Puede requerir un mantenimiento frecuente y cambios de filtro. |
Limpieza por ultrasonidos frente a sistemas vibratorios
Técnica | Pros | Contras |
---|---|---|
Limpieza por ultrasonidos | - Alta precisión para piezas complejas. | - Mayor coste y requisitos de mantenimiento. |
- Eficaz para alcanzar rasgos intrincados. | - Requiere una manipulación cuidadosa para evitar daños. | |
Sistemas vibratorios | - Escalable para grandes volúmenes de producción. | - Puede no ser tan preciso para piezas muy delicadas. |
- Puede manipular una gran variedad de formas y tamaños de piezas. | - Puede generar ruido y polvo. |
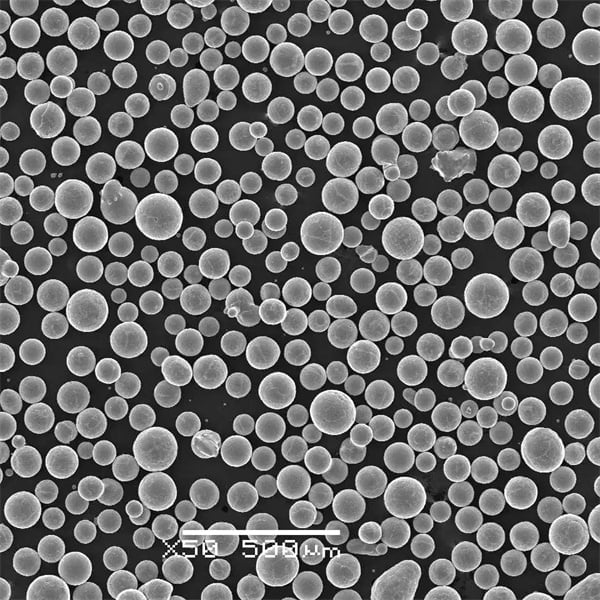
Preguntas frecuentes
Aquí tiene una completa sección de preguntas frecuentes sobre sistemas de depuración:
Pregunta | Respuesta |
---|---|
¿Qué es un sistema de depuración? | Un sistema de eliminación de polvo es una herramienta utilizada para eliminar el exceso de polvo de las piezas impresas en 3D y garantizar un acabado limpio. |
¿Por qué es importante la eliminación de residuos en la fabricación aditiva? | El desempolvado garantiza que el producto final esté limpio, sea funcional y cumpla las normas de calidad requeridas para su aplicación. |
¿Cuáles son los principales métodos utilizados en la depuración? | Entre los métodos más comunes se encuentran el soplado de aire, la succión por vacío, la limpieza por ultrasonidos y los sistemas vibratorios. |
¿Cómo elegir el sistema de depuración adecuado a mis necesidades? | Tenga en cuenta factores como la complejidad de las piezas, el volumen de producción y su presupuesto a la hora de seleccionar un sistema de depowdering. |
¿Existen problemas medioambientales con los sistemas de depuración? | Sí, la dispersión del polvo y el consumo de energía son motivo de preocupación, pero los sistemas modernos incorporan funciones para resolver estos problemas. |
¿Pueden los sistemas de desempolvado tratar todo tipo de polvos metálicos? | La mayoría de los sistemas son versátiles, pero debe verificar la compatibilidad con polvos y geometrías de piezas específicas. |
¿Con qué frecuencia necesita mantenimiento un sistema de depuración? | La frecuencia de mantenimiento varía según el sistema y el uso, pero suele incluir la limpieza de filtros, la inspección de componentes y la comprobación del rendimiento. |
¿Cuáles son algunos ejemplos de sistemas avanzados de depuración? | Entre los sistemas avanzados se incluyen los que cuentan con cepillado automático, aspiradores de alta eficiencia y funciones de limpieza por ultrasonidos integradas. |
Conclusión
Los sistemas de depowdering desempeñan un papel vital en el proceso de fabricación aditiva, ya que ofrecen una serie de soluciones para garantizar que las piezas impresas en 3D cumplan los más altos estándares de calidad y rendimiento. Desde la industria aeroespacial hasta las aplicaciones médicas, estos sistemas son esenciales para producir componentes fiables y precisos.
Tanto si desea invertir en un nuevo sistema como mejorar el que ya tiene, conocer los distintos tipos de polvos metálicos, sus aplicaciones y las diferentes técnicas de desempolvado le ayudará a tomar una decisión informada. Tenga en cuenta factores como la eficacia, el coste y los requisitos técnicos para elegir la mejor solución para sus necesidades específicas.
Compartir
MET3DP Technology Co., LTD es un proveedor líder de soluciones de fabricación aditiva con sede en Qingdao, China. Nuestra empresa está especializada en equipos de impresión 3D y polvos metálicos de alto rendimiento para aplicaciones industriales.
Solicite información para obtener el mejor precio y una solución personalizada para su empresa.
Artículos relacionados
Acerca de Met3DP
Actualización reciente
Nuestro producto
CONTACTO
¿Tiene alguna pregunta? ¡Envíenos un mensaje ahora! Atenderemos su solicitud con todo un equipo tras recibir su mensaje.
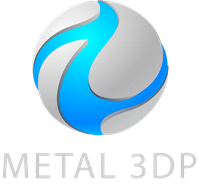
Polvos metálicos para impresión 3D y fabricación aditiva