Introducción a la deposición de energía dirigida
Índice
Imagine construir complejas estructuras metálicas capa a capa, con un control preciso de las propiedades de los materiales y un desperdicio mínimo. Esto no es ciencia ficción; es la realidad de Deposición de energía dirigida (DED), una revolucionaria tecnología de impresión 3D que está transformando el panorama de la fabricación.
La deposición de energía dirigida, también conocida por términos como Laser Engineered Net Shaping (LENS) o deposición directa de metal (DMD), es un proceso de fabricación aditiva que utiliza una fuente de energía focalizada, como un láser o un haz de electrones, para fundir y depositar material metálico de alimentación en un sustrato. Es como una pistola de soldar de alta tecnología con esteroides, que construye formas complejas en lugar de limitarse a unir piezas.
Esta guía se adentra en el mundo de la DED, explorando sus funcionalidades, los diversos polvos metálicos que utiliza, sus aplicaciones en distintos sectores y las ventajas y limitaciones que definen esta apasionante tecnología.
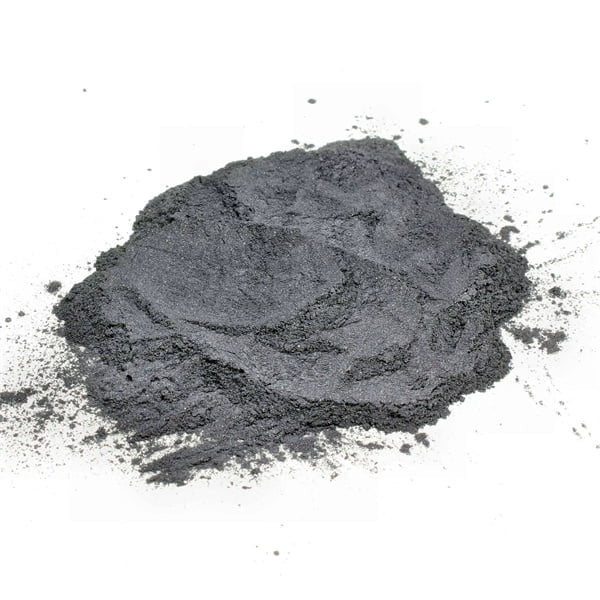
Cómo Deposición de energía dirigida Obras
El DED funciona con una sinergia de tres componentes clave:
- Fuente de energía: El corazón de la DED reside en su fuente de energía concentrada. Los láseres y los haces de electrones son las opciones más comunes y ofrecen distintas ventajas. Los láseres proporcionan gran precisión y control, pero pueden verse limitados por la reflectividad del material. Los haces de electrones, por su parte, profundizan más y penetran mejor en los materiales más gruesos, pero requieren una cámara de vacío para funcionar.
- Materia prima: El componente básico de su creación en 3D es el polvo metálico. DED utiliza una amplia gama de polvos metálicos, cada uno con propiedades y aplicaciones únicas. Profundizaremos en el fascinante mundo de los polvos metálicos en una sección específica más adelante.
- Sistema de entrega: La magia no se produce sin un mecanismo de suministro. El DED emplea una boquilla que introduce el polvo metálico en el baño de fusión creado por la fuente de energía. Esta precisa coordinación garantiza un proceso de deposición capa a capa sin fisuras.
Toda la operación está orquestada por software de diseño asistido por ordenador (CAD), que traduce su plano digital en instrucciones precisas para el sistema DED. Esto permite crear geometrías complejas, estructuras huecas y características que serían imposibles con las técnicas de fabricación tradicionales.
Un mundo de polvos metálicos: Combustible DED Creaciones
El éxito de la DED depende de la selección del polvo metálico adecuado. Al igual que la elección de los ingredientes perfectos para una receta, las propiedades del polvo influyen significativamente en las características del producto final. He aquí diez polvos metálicos muy utilizados en DED:
1. Titanio (Ti): Ligero, fuerte y resistente a la corrosión, el titanio es una elección popular para aplicaciones aeroespaciales, implantes médicos y artículos deportivos. Su biocompatibilidad lo hace ideal para prótesis e implantes dentales.
2. Inconel (aleación de níquel y cromo): Conocido por su excepcional resistencia a altas temperaturas y a la oxidación y la corrosión, el Inconel se utiliza en motores a reacción, intercambiadores de calor y equipos de procesamiento químico.
3. Acero inoxidable (SS): El acero inoxidable, una opción versátil y rentable, ofrece un buen equilibrio entre solidez, resistencia a la corrosión y asequibilidad. Se utiliza mucho en piezas de automoción, dispositivos médicos y aplicaciones industriales generales.
4. Aluminio (Al): Ligero y fácil de conseguir, el aluminio es una opción popular para aplicaciones en las que la reducción de peso es fundamental, como los componentes aeroespaciales y las piezas de automoción.
5. Níquel (Ni): El níquel, que ofrece buena resistencia a la corrosión y conductividad eléctrica, se utiliza en electrónica, equipos de procesamiento químico e incluso en algunas aplicaciones de acuñación de monedas.
6. Cromo-cobalto (CoCr): Esta aleación biocompatible presenta una gran solidez y resistencia al desgaste, lo que la convierte en la opción preferida para implantes ortopédicos y prótesis articulares.
7. Cobre (Cu): Excelente conductor del calor y la electricidad, el cobre se utiliza en disipadores de calor, componentes eléctricos e incluso para crear intrincados canales microfluídicos.
8. Tungsteno (W): Conocido por su punto de fusión increíblemente alto y su excepcional resistencia al desgaste, el tungsteno se utiliza para aplicaciones como electrodos de soldadura, proyectiles perforantes y componentes de hornos de alta temperatura.
9. Molibdeno (Mo): Al igual que el wolframio, el molibdeno ofrece resistencia a altas temperaturas y se utiliza en componentes aeroespaciales, reactores nucleares y filamentos para aplicaciones de iluminación.
10. Hastelloy: Esta familia de superaleaciones con base de níquel presenta una resistencia excepcional a una amplia gama de entornos corrosivos, lo que las hace ideales para aplicaciones en las industrias de procesamiento químico, petróleo y gas, y generación de energía.
Esta lista es sólo una pequeña muestra de la amplia gama de polvos metálicos disponibles para DED. La elección del polvo depende de las propiedades deseadas del producto final, como la fuerza, el peso, la resistencia a la corrosión y la conductividad térmica.
Más allá de lo básico: Las propiedades de los polvos metálicos
Propiedad | Descripción | Importancia en DED |
---|---|---|
Tamaño y distribución de partículas: | Se refiere al tamaño y la variación de tamaño de las partículas de polvo metálico. | Influye en la fluidez, la densidad de empaquetamiento y el acabado superficial del producto final. El tamaño uniforme de las partículas garantiza una deposición uniforme y minimiza la porosidad. |
Esfericidad: | Grado de semejanza de una partícula con una esfera perfecta. | Las partículas esféricas fluyen más fácilmente, se empaquetan más densamente y dan como resultado un mejor acabado superficial en comparación con las partículas de forma irregular. |
Fluidez: | La facilidad con la que fluye el polvo. | Fundamental para una alimentación consistente del material en el sistema DED. Una mala fluidez puede provocar problemas de alimentación e incoherencias en el producto final. |
Densidad aparente: | La densidad aparente del polvo. | влияет (vliyaniyet) en (en) la cantidad de material necesario para construir una pieza y puede repercutir en los costes de producción. |
Punto de fusión: | Temperatura a la que el polvo pasa de sólido a líquido. | Debe ser compatible con la fuente de energía elegida para garantizar una fusión y deposición adecuadas. |
Composición química: | La composición elemental del polvo. | Dicta las propiedades finales de la pieza impresa, como la solidez, la resistencia a la corrosión y la conductividad eléctrica. |
Elegir el polvo adecuado: Un acto de equilibrio
La selección del polvo metálico óptimo para su proyecto de DED requiere una cuidadosa consideración de varios factores. He aquí un desglose que le ayudará a tomar esta decisión:
- Requisitos de la solicitud: El uso previsto del producto final es primordial. Por ejemplo, un componente para un motor a reacción necesitará un polvo resistente a altas temperaturas como el Inconel, mientras que un implante médico puede requerir una opción biocompatible como el titanio o el cromo-cobalto.
- Propiedades deseadas: Identifique las características cruciales que necesita en la pieza acabada. ¿Es la resistencia la máxima prioridad? Tal vez sea esencial la resistencia a la corrosión o la construcción ligera. Comprender estas necesidades guiará su selección de polvo.
- Compatibilidad con el sistema DED: Asegúrese de que el polvo elegido se ajusta a las capacidades de su máquina DED. Tenga en cuenta factores como la potencia del láser o la disponibilidad de una cámara de vacío para DED por haz de electrones.
- Coste y disponibilidad: El precio de los polvos metálicos puede variar considerablemente. Equilibre sus limitaciones presupuestarias con las propiedades deseadas y explore la disponibilidad del polvo para evitar retrasos en la producción.
Consideraciones adicionales para Deposición de energía dirigida
Aunque los polvos metálicos reinan en la DED, el futuro es prometedor para la incorporación de otros materiales. Los investigadores están estudiando la posibilidad de utilizar:
- Compuestos: Mezcla de polvos metálicos con partículas cerámicas o poliméricas para crear materiales con combinaciones únicas de propiedades, como una mayor resistencia al desgaste o conductividad eléctrica.
- Materiales funcionalmente graduados (MGF): Transición gradual entre diferentes materiales dentro de una misma construcción para lograr funcionalidades específicas en diferentes regiones de la pieza. Imagine una herramienta con una punta resistente al desgaste en transición a un mango más ligero, todo ello impreso de una sola vez con DED.
Estos avances abren interesantes posibilidades para la DED, ampliando los límites del diseño y la funcionalidad en futuras aplicaciones.
Aplicaciones de Deposición de energía dirigida
La versatilidad del DED brilla a través de su diversa gama de aplicaciones en numerosas industrias. He aquí algunos ejemplos convincentes:
- Aeroespacial: DED destaca en la creación de componentes ligeros y de alta resistencia para aeronaves, como costillas de alas, piezas de trenes de aterrizaje e incluso componentes de motores de cohetes. La capacidad de producir geometrías complejas con el mínimo desperdicio convierte a DED en un revolucionario en esta industria de peso crítico.
- Implantes médicos: La capacidad de la DED para crear piezas biocompatibles con diseños intrincados la hace ideal para prótesis a medida, implantes dentales e incluso implantes craneales. Esta tecnología personaliza la atención médica, mejorando los resultados y la calidad de vida de los pacientes.
- Automóvil: El sector de la automoción está adoptando el DED para la creación de prototipos y la producción de piezas de alto rendimiento en pequeñas cantidades. La DED permite crear componentes ligeros y estructuras internas complejas con las que la fabricación tradicional podría tener problemas.
- Utillaje y reparación: DED ofrece una forma rápida y rentable de crear y reparar plantillas, utillajes y herramientas de corte. Imagine reparar un molde dañado o crear una herramienta personalizada bajo demanda: DED lo hace posible.
- Petróleo y gas: El DED se utiliza para crear componentes resistentes a la corrosión para herramientas de fondo de pozo y otros equipos utilizados en los duros entornos del petróleo y el gas.
- Bienes de consumo: Desde monturas de gafas personalizadas hasta componentes de bicicleta basados en el diseño, el DED se está abriendo paso en el mercado de bienes de consumo, permitiendo la creación de productos únicos e innovadores.
Estos son sólo algunos ejemplos y, a medida que la tecnología DED madure, cabe esperar que surjan aplicaciones aún más revolucionarias en diversos sectores.
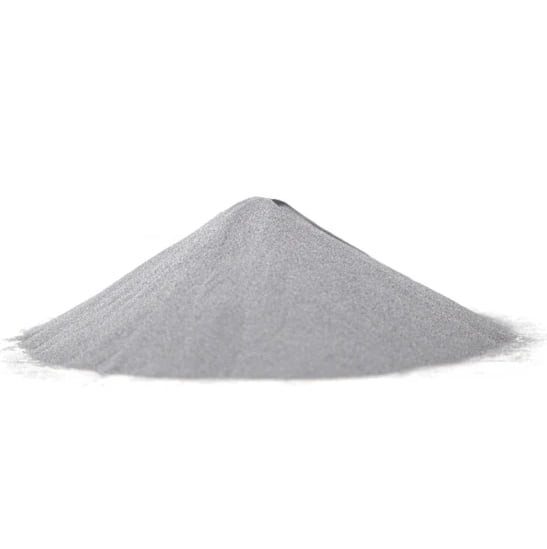
Ventajas y limitaciones de Deposición de energía dirigida
La DED ofrece una serie de ventajas que la convierten en una fuerza disruptiva en la fabricación. Pero, como cualquier tecnología, tiene sus propias limitaciones. Analicemos las dos caras de la moneda.
Ventajas de la deposición de energía dirigida:
- Libertad de diseño: ¡Dé rienda suelta a su creatividad! El DED permite crear geometrías complejas, como paredes finas, celosías y entalladuras que serían imposibles o muy difíciles con las técnicas tradicionales. Esto abre las puertas a diseños ligeros y muy funcionales.
- Eficiencia del material: El DED es un proceso de fabricación casi neto, lo que significa que se desperdicia un mínimo de material. A menudo, el polvo no utilizado puede reciclarse, lo que minimiza los residuos y los costes de producción.
- Creación rápida de prototipos: La capacidad de DED para crear rápidamente prototipos funcionales acelera el ciclo de desarrollo del producto, lo que permite iteraciones de diseño y plazos de comercialización más rápidos.
- Personalización: El DED brilla en la creación de piezas a medida, perfectamente adaptadas a necesidades específicas. Esto es especialmente valioso en sectores como el de los implantes médicos y el aeroespacial.
- Consolidación de piezas: El DED puede combinar varios componentes en una sola pieza, lo que simplifica los diseños, reduce el tiempo de montaje y mejora potencialmente el rendimiento de la pieza.
- Versatilidad: Una amplia gama de polvos metálicos, y potencialmente otros materiales en el futuro, amplía el panorama de aplicaciones de la DED.
Limitaciones de Deposición de energía dirigida:
- Velocidad de construcción: En comparación con técnicas tradicionales como la fundición o el moldeo por inyección, la DED puede ser más lenta, sobre todo en piezas grandes. Se trata de un área de desarrollo en curso, con investigaciones centradas en velocidades de deposición más rápidas.
- Rugosidad superficial: La naturaleza por capas de la DED puede producir un efecto escalonado en el acabado de la superficie. Para conseguir un acabado más liso, pueden ser necesarias técnicas de tratamiento posterior, como el mecanizado o el pulido.
- Propiedades del material: Aunque las piezas DED pueden alcanzar excelentes propiedades mecánicas, no siempre se ajustan perfectamente a las de los metales forjados o forjados debido a la naturaleza inherente del proceso de fabricación aditiva. Se están llevando a cabo nuevas investigaciones y desarrollos para optimizar los procesos DED para diversos materiales.
- Costo: Los sistemas DED pueden ser caros y el coste de los polvos metálicos puede variar considerablemente. Esto podría limitar su adopción para la producción de grandes volúmenes de piezas de bajo coste.
- Tensión residual: Los rápidos ciclos de calentamiento y enfriamiento durante el DED pueden introducir tensiones residuales en la pieza. Un diseño y unas técnicas de postprocesado adecuados pueden ayudar a mitigar este problema.
PREGUNTAS FRECUENTES
Estas son algunas de las preguntas más frecuentes sobre la DED:
P: ¿Cuáles son las ventajas del DED frente a otras tecnologías de impresión 3D como el FDM (modelado por deposición fundida)?
R: El DED ofrece varias ventajas sobre el FDM. En primer lugar, el DED utiliza polvos metálicos, lo que permite crear piezas metálicas funcionales. La FDM, por su parte, suele limitarse a plásticos y otros polímeros. En segundo lugar, las piezas DED suelen tener unas propiedades mecánicas superiores a las de las piezas FDM. Por último, el DED permite una mayor libertad de diseño con la capacidad de crear geometrías complejas.
P: ¿Se puede utilizar DED para reparar piezas metálicas?
R: ¡Por supuesto! La capacidad del DED para depositar material con precisión lo hace ideal para reparar componentes metálicos dañados. Puede ser una solución rentable y que ahorra tiempo en comparación con los métodos de sustitución tradicionales.
P: ¿Cuál es el futuro de la deposición dirigida de energía?
R: ¡El futuro del DED es brillante! Podemos esperar avances en varios ámbitos:
- Mayor velocidad de construcción: Los investigadores desarrollan continuamente métodos para aumentar las tasas de deposición, lo que hace que la DED sea más competitiva para la producción a gran escala.
- DED multimaterial: La capacidad de combinar a la perfección diferentes polvos metálicos o incluso materiales metálicos y no metálicos en una misma construcción abre interesantes posibilidades para crear piezas con propiedades adaptadas en diferentes regiones.
- Normalización: A medida que madure la tecnología DED, la normalización de procesos y materiales desempeñará un papel crucial para garantizar la calidad y la repetibilidad.
- Costes reducidos: Con los avances tecnológicos y el aumento de la adopción, se espera que el coste de los sistemas de DED y los polvos metálicos se reduzca, lo que hará que la DED sea más accesible a una gama más amplia de fabricantes.
La DED tiene un inmenso potencial para revolucionar diversos sectores. Su capacidad para crear piezas metálicas complejas y funcionales con un mínimo de residuos y una gran libertad de diseño la convierten en una tecnología a tener en cuenta. A medida que la DED siga evolucionando, podemos esperar que surjan aplicaciones aún más revolucionarias que darán forma al futuro de la fabricación.
Compartir
MET3DP Technology Co., LTD es un proveedor líder de soluciones de fabricación aditiva con sede en Qingdao, China. Nuestra empresa está especializada en equipos de impresión 3D y polvos metálicos de alto rendimiento para aplicaciones industriales.
Solicite información para obtener el mejor precio y una solución personalizada para su empresa.
Artículos relacionados
Acerca de Met3DP
Actualización reciente
Nuestro producto
CONTACTO
¿Tiene alguna pregunta? ¡Envíenos un mensaje ahora! Atenderemos su solicitud con todo un equipo tras recibir su mensaje.
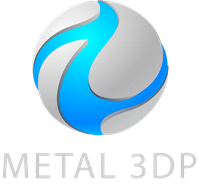
Polvos metálicos para impresión 3D y fabricación aditiva