Introducción al sinterizado directo de metales por láser (DMLS)
Índice
La magia de imprimir metal en 3D
Imagine un mundo en el que complejas piezas metálicas se materializan a partir de un lecho de polvo, capa a capa, con precisión láser. Esto no es ciencia ficción; es la realidad del sinterizado directo de metales por láser (DMLS), una revolucionaria tecnología de impresión 3D que está transformando nuestra forma de diseñar y fabricar componentes metálicos.
El DMLS, también conocido como fusión selectiva por láser (SLM) o fusión por lecho de polvo láser (LPBF), es un proceso de fabricación aditiva que utiliza un láser de alta potencia para fundir y fusionar selectivamente partículas metálicas, construyendo un objeto 3D a partir de un plano digital. Esta tecnología ofrece una libertad de diseño sin precedentes, permitiendo la creación de geometrías intrincadas y características internas que son imposibles con técnicas tradicionales como la fundición o el mecanizado.
Pero el DMLS no se limita a dar formas geniales. Presume de una serie de ventajas, entre las que se incluyen:
- Fuerza y precisión excepcionales: El DMLS produce piezas con propiedades mecánicas excepcionales, que rivalizan con las de los componentes fabricados tradicionalmente. Además, el método capa por capa garantiza una precisión dimensional excepcional.
- Potencial de aligeramiento: Al incorporar celosías internas y estructuras huecas, el DMLS permite crear piezas ligeras pero robustas, una gran ventaja en sectores como el aeroespacial y la automoción.
- Libertad de diseño: Dé rienda suelta a su creatividad El DMLS elimina las limitaciones de los métodos convencionales, permitiendo la producción de geometrías complejas y características internas que serían increíblemente difíciles o incluso imposibles de conseguir de otro modo.
- Creación rápida de prototipos: El DMLS permite crear prototipos funcionales de forma rápida y eficaz, acelerando el proceso de diseño y desarrollo.
- La personalización en masa: El DMLS permite fabricar piezas personalizadas en lotes pequeños, perfectos para aplicaciones de bajo volumen o productos personalizados.
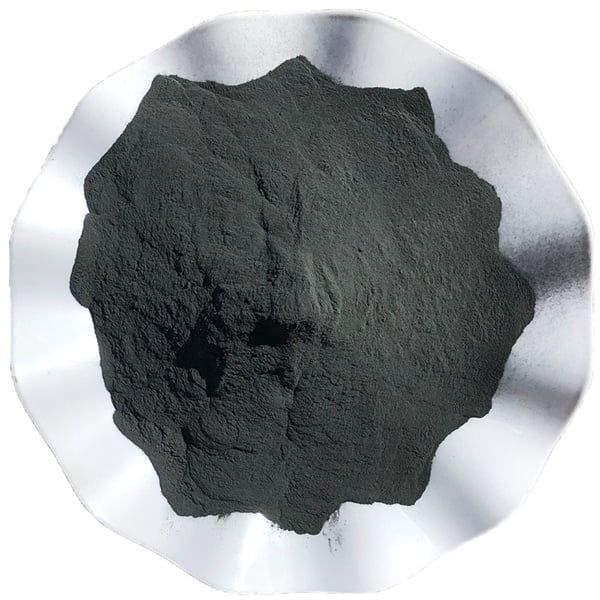
Los pilares de la DMLS
El corazón del proceso DMLS reside en los polvos metálicos utilizados. Estas finas partículas metálicas, cuyo tamaño suele oscilar entre 20 y 40 micrómetros, se eligen meticulosamente en función de las propiedades deseadas de la pieza final. A continuación le presentamos algunos de los polvos metálicos más utilizados en DMLS, junto con sus características únicas:
Polvos metálicos DMLS comunes:
Polvo metálico | Descripción | Propiedades | Aplicaciones |
---|---|---|---|
Aleaciones de titanio (Ti-6Al-4V, Ti-6Al-4V ELI) | El caballo de batalla del DMLS, que ofrece un buen equilibrio entre fuerza, peso y resistencia a la corrosión. | Elevada relación resistencia/peso, excelente biocompatibilidad (grado ELI). | Aeroespacial, implantes médicos, artículos deportivos |
Acero inoxidable (316L, 17-4PH) | Versátil y rentable, con buenas propiedades mecánicas y resistencia a la corrosión. | Excelente resistencia a la corrosión (316L), alta resistencia y dureza (17-4PH). | Componentes industriales, equipos de procesamiento químico, joyería |
Aleaciones de aluminio (AlSi10Mg, AlSi7Mg0,3) | Son ligeras y ofrecen una buena maquinabilidad para el tratamiento posterior. | Excelente relación resistencia/peso, buena colabilidad (AlSi7Mg0,3). | Piezas de automóvil, componentes aeroespaciales, intercambiadores de calor |
Inconel (IN625, 718) | Superaleaciones famosas por su resistencia a altas temperaturas y a la corrosión. | Rendimiento excepcional a temperaturas elevadas, buena resistencia a la oxidación. | Componentes de turbinas de gas, motores de cohetes, intercambiadores de calor |
Cromo-cobalto (CoCr) | Biocompatible y resistente al desgaste, ideal para implantes médicos. | Excelente biocompatibilidad, alta resistencia y resistencia al desgaste. | Prótesis articulares, implantes dentales, instrumentos quirúrgicos |
Cobre (Cu) | Altamente conductor, lo que lo hace perfecto para aplicaciones eléctricas. | Excelente conductividad térmica y eléctrica. | Disipadores térmicos, componentes electrónicos, guías de ondas |
Níquel (Ni) | El níquel puro ofrece una combinación de fuerza, ductilidad y resistencia a la corrosión. | Alta resistencia, buena ductilidad y resistencia a la corrosión. | Electrodos, equipos de procesamiento químico, materiales de soldadura fuerte |
Acero para herramientas (H13, M2) | Diseñado para ofrecer una gran resistencia al desgaste y tenacidad. | Excelente resistencia al desgaste, gran dureza (H13), buena tenacidad (M2). | Herramientas de corte, moldes y matrices, placas de desgaste |
Metales preciosos (oro, plata, platino) | Apreciados por su atractivo estético y sus propiedades únicas. | Alto valor, excelente conductividad eléctrica (Oro, Plata), estabilidad a altas temperaturas (Platino). | Joyería, piezas decorativas, contactos eléctricos |
Metales refractarios (wolframio, tantalio) | Ofrecen una excepcional resistencia a altas temperaturas y a entornos agresivos. | Puntos de fusión muy elevados, excelente resistencia al desgaste (Tungsteno |
El proceso de DMLS
Ahora que hemos explorado los componentes básicos del DMLS, profundicemos en el fascinante proceso en sí. He aquí un desglose del flujo de trabajo típico que implica la creación de una pieza metálica mediante DMLS:
- Diseño digital: El viaje comienza con un modelo 3D de diseño asistido por ordenador (CAD) de la pieza deseada. Este modelo define la geometría exacta, las dimensiones y las características internas del componente final. A menudo se utiliza software diseñado específicamente para la fabricación aditiva con el fin de garantizar que el modelo está optimizado para la impresión DMLS.
- Separación de datos: A continuación, el modelo CAD 3D se corta en una serie de secciones transversales extremadamente finas, cuyo grosor suele oscilar entre 20 y 100 micrómetros. Cada corte representa una única capa sobre la que la máquina DMLS construirá. Imagine una pila digital de planos, cada uno de los cuales detalla una capa específica de la pieza.
- Preparación del lecho de polvo: Dentro de la máquina DMLS, se deposita uniformemente una capa de fino polvo metálico sobre una plataforma de construcción. Esta capa corresponde al primer corte del modelo digital. La plataforma puede moverse hacia arriba y hacia abajo con precisión, lo que permite crear capas posteriores.
- Fusión selectiva por láser: Un rayo láser de alta potencia, normalmente un láser de fibra, recorre el lecho de polvo según los datos del modelo rebanado. El láser funde las partículas metálicas en las zonas designadas, fusionándolas y creando la primera capa sólida de la pieza.
- Construcción por capas: El proceso se repite: se deposita una nueva capa de polvo y el láser funde selectivamente las secciones necesarias, uniéndolas a la capa anterior. Este ciclo continúa meticulosamente, construyendo la pieza capa a capa hasta completar todo el objeto.
- Retirada del soporte: Una vez finalizado el proceso de impresión, la plataforma de construcción desciende y deja al descubierto la pieza metálica recién formada. Sin embargo, la pieza puede estar rodeada de estructuras de soporte que se imprimieron junto con ella para evitar cualquier hundimiento o deformación durante la construcción. Estas estructuras de soporte se eliminan cuidadosamente mediante técnicas como el mecanizado o el corte por chorro de agua.
- Post-procesamiento: Dependiendo de la aplicación y del acabado superficial deseado, la pieza DMLS puede someterse a pasos adicionales de postprocesado, como tratamiento térmico, prensado isostático en caliente (HIP) o chorro de arena. Estos procesos pueden mejorar las propiedades mecánicas, aliviar las tensiones residuales y mejorar la calidad de la superficie del componente final.
Características técnicas de DMLS
El DMLS ofrece un conjunto único de características técnicas que lo convierten en una potente herramienta para diversas aplicaciones. He aquí un análisis más detallado de algunos de los aspectos clave a tener en cuenta:
- Resolución y precisión: El DMLS ofrece una resolución y una precisión dimensional excepcionales, normalmente con espesores de capa que oscilan entre 20 y 100 micrómetros. Esto permite crear características muy intrincadas y geometrías complejas.
- Acabado superficial: El acabado superficial de las piezas DMLS puede variar en función del polvo metálico utilizado y de las técnicas de postprocesado empleadas. Sin embargo, la naturaleza por capas inherente al proceso puede dar lugar a un acabado superficial algo escalonado en comparación con los métodos de mecanizado tradicionales.
- Propiedades del material: Las piezas DMLS presentan excelentes propiedades mecánicas, a menudo comparables a las de los componentes fabricados convencionalmente. Factores como el polvo metálico específico, los parámetros de fabricación y el posprocesamiento pueden influir en las propiedades finales de la pieza.
- Construir volumen: El volumen de construcción de una máquina DMLS determina el tamaño máximo de la pieza que puede imprimirse en una sola construcción. Los volúmenes de construcción pueden oscilar entre unos pocos centímetros cúbicos y varios metros cúbicos, lo que permite una amplia gama de aplicaciones.
- Velocidad de construcción: En comparación con otras tecnologías de fabricación aditiva, el DMLS puede ser un proceso relativamente lento. Los tiempos de fabricación dependen del tamaño y la complejidad de la pieza, así como del grosor de la capa y de los ajustes de potencia del láser.
- Residuos materiales: A diferencia de las técnicas de fabricación sustractiva, que generan una gran cantidad de material de desecho, el DMLS ofrece unos residuos mínimos. El polvo metálico no utilizado puede reciclarse y reutilizarse en construcciones posteriores, lo que minimiza el consumo de material.
Ámbitos de aplicación del DMLS
El DMLS está transformando rápidamente una amplia gama de industrias gracias a sus capacidades únicas. Estas son algunas de las principales áreas de aplicación en las que brilla el DMLS:
- Aeroespacial: El DMLS cambia las reglas del juego en el sector aeroespacial, ya que permite crear componentes ligeros y robustos para aviones y naves espaciales. Se pueden incorporar estructuras internas complejas y diseños reticulares para optimizar el rendimiento y reducir el peso, un factor crucial para la eficiencia del combustible.
- Implantes médicos: La naturaleza biocompatible de ciertos polvos metálicos, como el titanio y el cromo cobalto, hace que el DMLS sea ideal para producir implantes médicos personalizados. Estos implantes pueden adaptarse con precisión a la anatomía del paciente, ofreciendo un ajuste perfecto y una funcionalidad mejorada.
- Automóvil: (Continuación) La industria del automóvil está aprovechando el DMLS para crear componentes de alto rendimiento como pistones, culatas y piezas de engranajes. La capacidad de diseñar estructuras ligeras y complejas permite reducir el peso y mejorar la eficiencia del combustible, una gran ventaja en el mercado actual, preocupado por el medio ambiente. Además, el DMLS permite crear piezas personalizadas para aplicaciones de carreras o vehículos de edición limitada.
- Fabricación de moldes y matrices: El DMLS está revolucionando el sector de la fabricación de moldes y matrices al permitir la producción de canales de refrigeración complejos y conformados dentro de los moldes. Estos canales mejoran la transferencia de calor durante el proceso de moldeo por inyección, lo que agiliza los ciclos, mejora la calidad de las piezas y reduce los costes de producción.
- Bienes de consumo: El DMLS se está abriendo camino en el mercado de bienes de consumo, permitiendo la creación de productos únicos y personalizados como joyas, gafas y artículos deportivos. La capacidad de producir geometrías complejas abre nuevas posibilidades de diseño, mientras que la naturaleza bajo demanda del DMLS responde a la tendencia a la personalización.
- Creación de prototipos: El DMLS es una potente herramienta de prototipado rápido que permite a ingenieros y diseñadores crear rápidamente prototipos funcionales de nuevos productos. Este rápido ciclo de iteración acelera el proceso de diseño y desarrollo, lo que se traduce en una innovación de productos y un plazo de comercialización más rápidos.
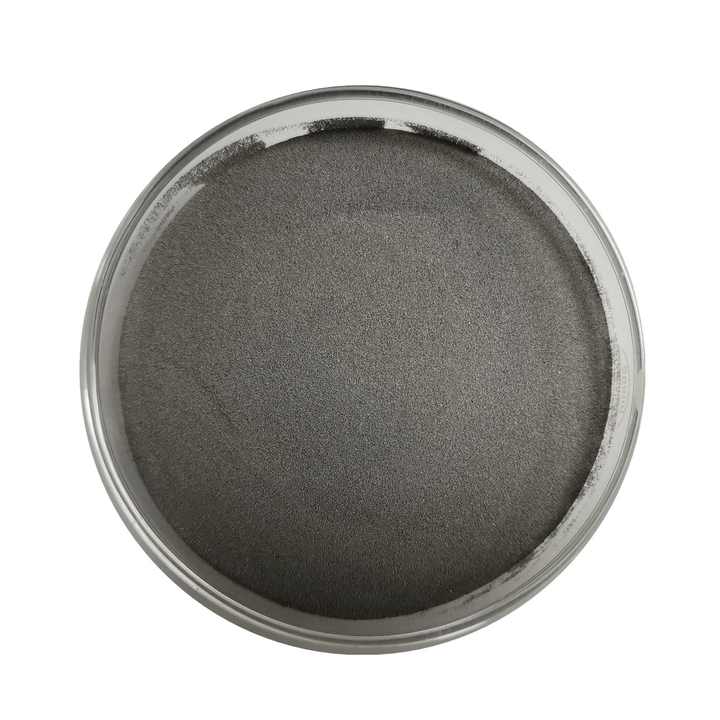
Limitaciones y consideraciones de DMLS
Aunque el DMLS ofrece un sinfín de ventajas, es esencial reconocer sus limitaciones y consideraciones:
- Costo: Las máquinas DMLS y los polvos metálicos pueden ser caros en comparación con los equipos y materiales de fabricación tradicionales. Esto puede hacer que el DMLS sea una opción menos adecuada para la producción de grandes volúmenes de piezas sencillas.
- Acabado superficial: Como ya se ha mencionado, la naturaleza por capas del DMLS puede dar lugar a un acabado superficial algo escalonado. Aunque las técnicas de postprocesado pueden mejorar la calidad de la superficie, conseguir un acabado perfectamente liso podría requerir pasos de mecanizado adicionales, lo que aumentaría el coste y la complejidad del proceso.
- Tiempo de construcción: El DMLS puede ser un proceso lento, especialmente para piezas grandes o complejas. Esto debe tenerse en cuenta a la hora de considerar los plazos de entrega y los programas de producción.
- Estructuras de apoyo: La necesidad de estructuras de soporte durante el proceso DMLS puede añadir complejidad y aumentar potencialmente el tiempo de postprocesado. Un diseño cuidadoso puede minimizar la necesidad de estructuras de soporte complejas.
- Cualificación parcial: Para aplicaciones críticas en sectores como el aeroespacial y el médico, las piezas de DMLS pueden requerir procedimientos de prueba y cualificación adicionales para garantizar que cumplen las estrictas normas de rendimiento y seguridad.
DMLS frente a otras tecnologías de fabricación aditiva
El DMLS no es el único jugador en el juego de la impresión 3D. He aquí una rápida comparación del DMLS con otras destacadas tecnologías de fabricación aditiva para ayudarle a elegir la herramienta adecuada para el trabajo:
- Estereolitografía (SLA): La SLA utiliza un láser para curar resina líquida y convertirla en un objeto sólido, capa a capa. En comparación con el DMLS, el SLA ofrece mayor resolución y acabados superficiales más suaves, pero está limitado a una gama más reducida de materiales, principalmente plásticos.
- Sinterización selectiva por láser (SLS): El SLS funciona de forma similar al DMLS, pero utiliza un láser para sinterizar partículas de polvo de plástico. El SLS suele ser más rápido y rentable que el DMLS para producir piezas de plástico, pero ofrece menor resistencia y opciones de material limitadas en comparación con el DMLS para aplicaciones metálicas.
- Modelado por deposición fundida (FDM): El FDM funciona mediante la extrusión de filamento de plástico fundido para construir el objeto capa a capa. El FDM es una tecnología muy utilizada y relativamente barata, pero ofrece menor resolución y resistencia que el DMLS.
- Fusión por haz de electrones (EBM): Similar al DMLS, el EBM utiliza un haz de electrones para fundir polvo metálico. La EBM es excelente para procesar metales reactivos como el titanio, pero requiere un entorno de vacío, lo que la convierte en un proceso más complejo y costoso que el DMLS. DMLS.
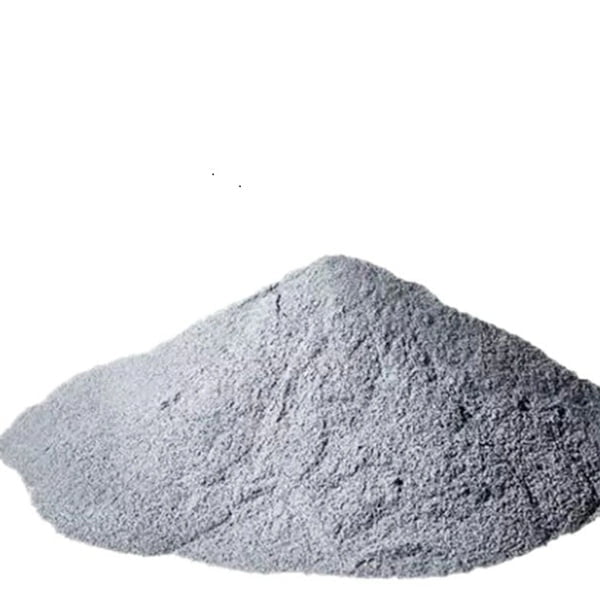
PREGUNTAS FRECUENTES
Estas son algunas de las preguntas más frecuentes sobre DMLS:
P: ¿Cuáles son las ventajas del DMLS?
R: El DMLS ofrece varias ventajas, como una excepcional libertad de diseño, gran resistencia y precisión de las piezas, potencial de aligeramiento, capacidad de creación rápida de prototipos y mínimo desperdicio de material.
P: ¿Cuáles son las limitaciones del DMLS?
R: Las limitaciones del DMLS incluyen su coste relativamente elevado en comparación con la fabricación tradicional, posibles problemas con el acabado superficial, tiempos de fabricación más lentos en comparación con otras tecnologías de impresión 3D y la necesidad de consideraciones adicionales como estructuras de soporte y cualificación de piezas para determinadas aplicaciones.
P: ¿Qué materiales pueden utilizarse con el DMLS?
R: Con el DMLS puede utilizarse una amplia gama de polvos metálicos, como aleaciones de titanio, acero inoxidable, aleaciones de aluminio, Inconel, cromo-cobalto, cobre, níquel, acero para herramientas, metales preciosos y metales refractarios.
P: ¿Cuáles son algunas de las aplicaciones del DMLS? (Continuación)
R: El DMLS tiene aplicaciones en diversos sectores, como el aeroespacial, los implantes médicos, la automoción, la fabricación de moldes y matrices, los bienes de consumo y la creación de prototipos, entre otros.
P: ¿Cuánto cuesta una máquina DMLS?
R: El coste de una máquina DMLS puede variar mucho en función del volumen de fabricación, las capacidades y la marca. Los precios pueden oscilar entre las decenas de miles de dólares de las máquinas más pequeñas y los millones de dólares de los sistemas industriales de gama alta.
P: ¿Puedo utilizar el DMLS en casa?
R: Aunque están surgiendo impresoras 3D de sobremesa para metal, las máquinas DMLS de calidad industrial no suelen ser adecuadas para uso doméstico debido a su complejidad, coste, consideraciones de seguridad y requisitos especializados de manipulación del polvo.
P: ¿Cuál es el futuro del DMLS?
R: El futuro del DMLS es brillante. A medida que avanza la tecnología, podemos esperar ver máquinas DMLS más asequibles, una gama más amplia de polvos metálicos compatibles y velocidades de impresión aún más rápidas. El DMLS está preparado para desempeñar un papel cada vez más importante en la fabricación, permitiendo la creación de piezas innovadoras y de alto rendimiento en diversos sectores.
Conclusión
El DMLS representa un salto revolucionario en la fabricación, ya que ofrece una libertad de diseño sin precedentes y la capacidad de crear piezas metálicas complejas con una resistencia y una precisión excepcionales. Desde componentes aeroespaciales ligeros hasta implantes médicos personalizados, el DMLS está cambiando la forma de diseñar y fabricar una amplia gama de productos. Aunque existen limitaciones que hay que tener en cuenta, como el coste y el tiempo de fabricación, el DMLS sigue evolucionando y haciéndose más accesible, lo que lo convierte en una potente herramienta para ingenieros, diseñadores y fabricantes por igual. A medida que la tecnología DMLS madura y sus capacidades se amplían, podemos esperar que surjan aplicaciones aún más revolucionarias en los próximos años.
Compartir
MET3DP Technology Co., LTD es un proveedor líder de soluciones de fabricación aditiva con sede en Qingdao, China. Nuestra empresa está especializada en equipos de impresión 3D y polvos metálicos de alto rendimiento para aplicaciones industriales.
Solicite información para obtener el mejor precio y una solución personalizada para su empresa.
Artículos relacionados
Acerca de Met3DP
Actualización reciente
Nuestro producto
CONTACTO
¿Tiene alguna pregunta? ¡Envíenos un mensaje ahora! Atenderemos su solicitud con todo un equipo tras recibir su mensaje.
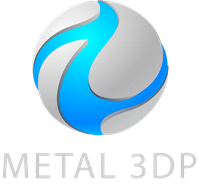
Polvos metálicos para impresión 3D y fabricación aditiva