Custom Enclosures for EV Power Units
Índice
Introduction: The Critical Role of EV Power Control Unit Enclosures
The global shift towards electric mobility is not just a trend; it’s a fundamental transformation of the automotive landscape. At the heart of every electric vehicle (EV) lies a sophisticated network of power electronics, managing everything from battery charging and energy distribution to motor control. Central to this network is the Power Control Unit (PCU), the brain and nerve center ensuring efficient, reliable, and safe operation. Protecting these critical components is paramount, and this is where the EV Power Control Unit Enclosure steps in. More than just a box, this enclosure is a multi-functional component crucial for the vehicle’s performance, safety, and longevity. Its primary roles include shielding sensitive electronics from harsh environmental conditions (moisture, dust, vibrations, impacts), managing the significant heat generated during operation, ensuring electromagnetic compatibility (EMC) by preventing interference, and providing structural integrity within the vehicle’s architecture. As EV technology advances, demanding higher power densities, faster charging, and more compact designs, the requirements placed upon these enclosures intensify. Traditional manufacturing methods like die casting or sheet metal fabrication, while established, often face limitations in creating the complex, lightweight, and thermally efficient designs needed for next-generation EVs. This burgeoning need for innovation opens the door for advanced manufacturing techniques, particularly fabricación aditiva (AM) de metales, also known as metal Impresión 3D. Metal AM offers unprecedented design freedom, enabling the creation of highly optimized, custom metal enclosures specifically tailored to the demanding requirements of modern EV power electronics. For engineers and procurement managers in the automotive sector, understanding the capabilities of metal AM for producing these critical componentes para vehículos eléctricos is no longer optional; it’s essential for staying competitive and driving innovation. Companies seeking reliable B2B EV parts suppliers are increasingly turning to partners proficient in additive manufacturing to deliver high-performance, lightweight, and cost-effective automotive electronics protection solutions. The ability to produce custom metal enclosures quickly and efficiently, without the traditional constraints of tooling, marks a significant leap forward in EV component manufacturing.
The enclosure surrounding an EV’s power control unit is far from a passive container. It actively contributes to the vehicle’s overall performance and safety ecosystem. Consider the challenges: power electronics like inverters and converters generate substantial heat loads, especially during rapid acceleration or fast charging. Inadequate thermal management can lead to component overheating, reduced efficiency, premature failure, and even safety risks. The enclosure must therefore be designed not just to contain heat, but to actively dissipate it, often requiring intricate features like cooling fins, internal channels for liquid cooling, or optimized airflow pathways. Furthermore, the high switching frequencies involved in power conversion generate electromagnetic noise. The enclosure must act as a Faraday cage, shielding the internal components from external electromagnetic interference (EMI) and preventing the PCU itself from interfering with other sensitive vehicle systems like radio communication or driver-assist sensors. This demands specific material properties and potentially complex geometries to ensure effective shielding across a wide frequency range. Structurally, the enclosure must withstand the constant vibrations and potential shocks inherent in a moving vehicle, protecting the delicate electronics within. All these requirements must be met while adhering to strict space and weight constraints, as every gram saved contributes to increased vehicle range and efficiency. This complex interplay of thermal, electrical, mechanical, and packaging requirements pushes the boundaries of conventional manufacturing. Metal AM, with its layer-by-layer fabrication process, allows designers to break free from the limitations of molds, dies, and machining constraints. It enables the integration of multiple functions into a single, optimized component, paving the way for superior EV power electronics housing designs that were previously unachievable. As the industry seeks partners capable of delivering these advanced solutions, exploring the potential of metal AM becomes a strategic imperative for sourcing high-quality, innovative componentes para vehículos eléctricos.
Applications and Functions of EV Power Control Unit Enclosures
The term “Power Control Unit” in an EV often encompasses several critical sub-systems, each requiring robust protection and specific environmental controls provided by the enclosure. Understanding these applications highlights the diverse functional demands placed on the housing:
- Inverter Housing: The inverter converts the DC power stored in the battery pack into the AC power needed to drive the electric motor(s). This high-power conversion process generates significant heat. Enclosures for inverters must prioritize excellent thermal management, often incorporating sophisticated cooling strategies (air or liquid), alongside structural rigidity and EMI shielding.
- DC-DC Converter Case: EVs operate various systems at different voltages (e.g., 12V for accessories, high voltage for the powertrain). The DC-DC converter manages these voltage transformations. While typically generating less heat than the main inverter, its enclosure still requires effective thermal dissipation, protection from the elements, and EMI containment.
- On-Board Charger (OBC) Housing: The OBC manages the process of charging the high-voltage battery from an external AC power source. It involves power conversion and generates considerable heat, especially during fast charging. OBC enclosures need robust thermal management, weather sealing (as they often interface with external charging ports), and structural integrity.
- Battery Management System (BMS) Enclosure: The BMS monitors and controls the health, charge level, and temperature of individual battery cells or modules. While not a high-power component itself, it’s critically sensitive to temperature fluctuations, vibration, and electrical noise. Its enclosure focuses on providing a stable operating environment, protection, and often integrates mounting points for sensors and connectors. It’s a key component sought by wholesale EV enclosure buyers.
- Integrated Power Electronics Modules: Increasingly, manufacturers are consolidating multiple functions (e.g., inverter, DC-DC converter, OBC) into a single, integrated module. This places even greater demands on the enclosure, requiring complex internal partitioning, multi-faceted thermal management solutions, and intricate designs to accommodate various connectors and interfaces while minimizing size and weight.
Across these applications, the fundamental functions of the enclosure remain consistent, though the emphasis may vary:
- Environmental Protection: Shielding sensitive electronics from moisture, dust, salt spray, automotive fluids, and physical impacts. This requires robust seals, durable materials, and potentially protective coatings.
- Gestión térmica: Dissipating heat generated by the power electronics to maintain optimal operating temperatures and prevent overheating. This is arguably one of the most critical functions, driving the need for materials with high thermal conductivity (like aluminum alloys) and designs incorporating cooling features (fins, heat pipes, liquid cooling channels). Effective automotive thermal management es clave.
- Electromagnetic Compatibility (EMC)/Shielding: Preventing electromagnetic interference (EMI) from disrupting the PCU’s operation and stopping the PCU from emitting noise that could affect other vehicle systems. This relies on the enclosure material’s conductivity and geometric design to create an effective shield.
- Structural Support & Vibration Damping: Providing a rigid mounting platform for the electronic components and PCBs, protecting them from road vibrations and shocks. The enclosure itself must withstand these loads without failure.
- Electrical Isolation: Ensuring proper electrical grounding and preventing short circuits.
- Serviceability: While providing protection, the enclosure design should also consider ease of assembly during manufacturing and potential access for servicing or diagnostics.
The specific requirements for EV powertrain components like PCU enclosures can differ significantly depending on the vehicle type – a high-performance sports car will have different thermal loads and vibration profiles than a commercial delivery van or a heavy-duty electric truck. Metal AM provides the flexibility to tailor enclosure designs precisely to the unique demands of each application, optimizing performance, weight, and packaging for diverse automotive electronics protection necesidades.
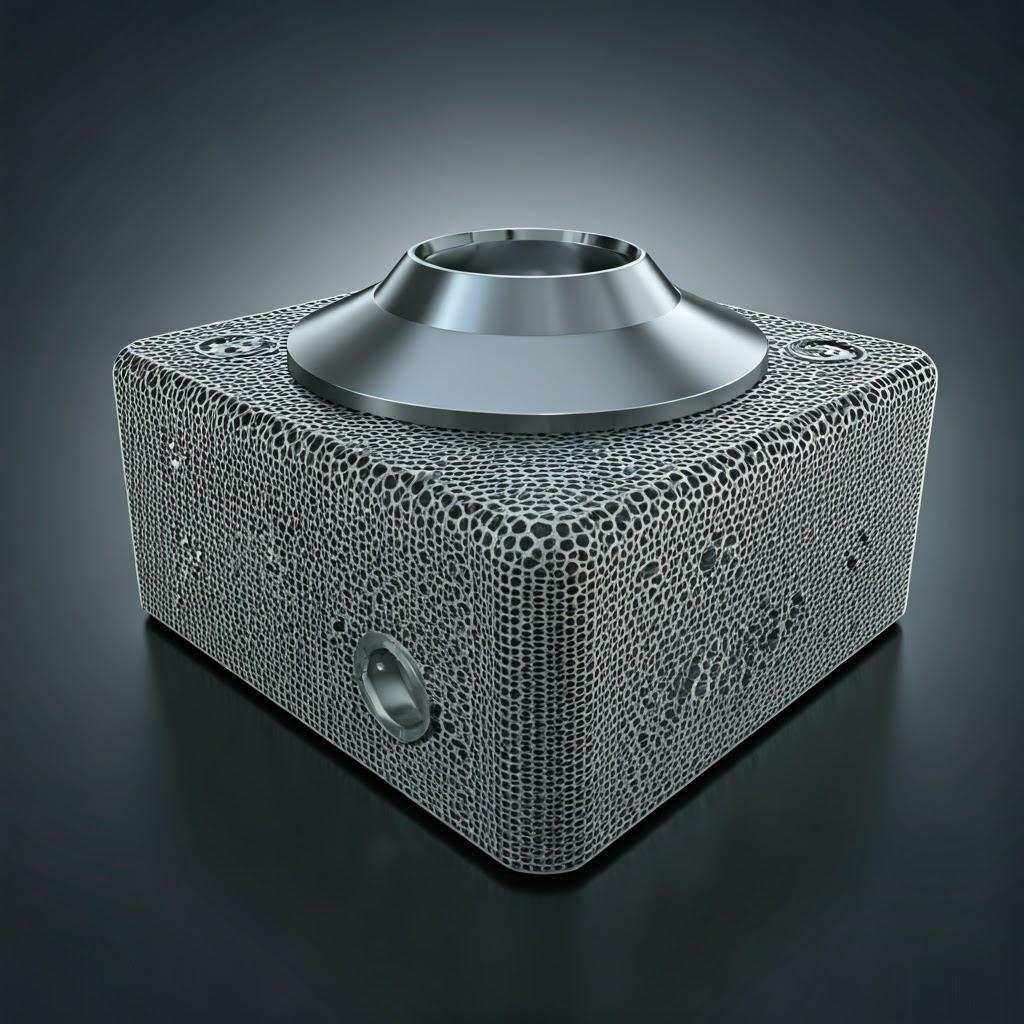
Why Metal 3D Printing for EV Power Unit Enclosures?
While traditional manufacturing methods like die casting, sheet metal fabrication, and CNC machining have long served the automotive industry, they present inherent limitations when designing and producing enclosures for modern, high-performance EV power electronics. Metal additive manufacturing offers a compelling alternative, overcoming many of these constraints and unlocking significant advantages, particularly for custom automotive parts manufacturing.
Comparison: Metal AM vs. Traditional Methods for EV Enclosures
Característica | Fundición a presión | Sheet Metal Fabrication | Mecanizado CNC | Metal Additive Manufacturing (L-PBF) |
---|---|---|---|---|
Complejidad del diseño | Moderate (requires draft angles, tooling constraints) | Low to Moderate (bending, stamping limits) | High (but subtractive, access limits) | Muy alta (complex internal channels, lattices) |
Coste de utillaje | Very High (dies) | Moderate (stamping dies, fixtures) | Low (fixtures, standard tools) | Ninguno (direct digital manufacturing) |
Plazo de entrega (Proto) | Long (tooling creation) | Moderado | Moderate to Fast | Very Fast (days) |
Plazo de entrega (Prod) | Fast (high volume) | Fast (high volume) | Moderate (depends on complexity) | Moderate (scaling up, multiple machines) |
Residuos materiales | Low (net shape potential) | Moderate (offcuts) | Alta (proceso sustractivo) | Bajo (powder recycling) |
Aligeramiento | Moderate (wall thickness limits) | Limited (sheet properties) | Moderate (material removal) | Excelente (topology optimization, lattices) |
Consolidación de piezas | Limitado | Limitado | Limitado | Excelente (integrating multiple parts) |
Personalización | Low (requires tooling changes) | Moderado | Alta | Muy alta (design changes via software) |
Volumen ideal | High Volume | High Volume | Low to Medium Volume | Prototype to Medium Volume |
Exportar a hojas
Key Advantages of Metal AM for EV Enclosures:
- Libertad de diseño sin igual: Metal AM, particularly Laser Powder Bed Fusion (L-PBF), builds parts layer by layer directly from a 3D CAD model. This eliminates the need for molds or dies, freeing designers from constraints like draft angles or limitations on undercuts. This enables:
- Complex Internal Geometries: Creation of intricate internal cooling channels precisely conforming to heat sources, significantly enhancing automotive thermal management.
- Optimización de la topología: Algorithmic design processes that remove material from non-critical areas, resulting in drastically lightweight EV components without compromising structural integrity.
- Estructuras reticulares: Internal or external lattice structures can further reduce weight while maintaining stiffness and potentially improving heat dissipation surface area.
- Consolidación de piezas: Multiple components (e.g., brackets, connectors, housing sections) can be redesigned and printed as a single, integrated part, reducing assembly time, potential leak paths, and overall weight.
- Creación rápida de prototipos e iteración: Producing a prototype enclosure using metal AM can take days instead of the weeks or months required for tooling development in die casting. This allows engineers to test and validate designs much faster, accelerating the development cycle for new EV powertrain components. Design modifications are easily implemented by changing the CAD file, enabling rapid iteration towards an optimal solution. This speed is invaluable in the fast-paced EV market.
- Aligeramiento: Weight reduction is critical for extending EV range. Metal AM excels at creating lightweight structures through topology optimization and the use of thin walls and internal lattices, often achieving weight savings of 20-50% or more compared to traditionally manufactured counterparts, while maintaining or even improving performance.
- Customization and Low-Volume Production: Metal AM is economically viable for producing highly customized enclosures or for low-to-medium volume production runs where the cost of tooling for traditional methods would be prohibitive. This is ideal for niche EV applications, performance variants, or early-stage production ramps.
- Eficiencia del material: While raw metal powders can be expensive, AM processes like L-PBF are highly efficient in their material usage. Unfused powder can typically be recycled and reused, leading to less material waste compared to subtractive methods like CNC machining.
- Flexibilidad de la cadena de suministro: AM enables decentralized manufacturing and on-demand production. This can shorten supply chains, reduce inventory requirements, and offer greater resilience against disruptions – crucial factors for procurement managers evaluating automotive component suppliers.
While metal AM might not always be the most cost-effective solution for extremely high-volume production runs where die casting excels, its advantages in design complexity, speed, lightweighting, and customization make it an increasingly vital tool for developing and manufacturing advanced custom enclosures for EV power units, especially when partnering with experienced providers like Met3dp, known for their advanced impresión 3D en metal capacidades.
Recommended Aluminum Alloys (AlSi10Mg, A6061) and Their Significance
Selecting the right material is fundamental to the success of any engineering application, and EV power control unit enclosures are no exception. Aluminum alloys are the go-to choice for these components due to their excellent balance of low density (lightweight), good thermal conductivity, adequate strength, corrosion resistance, and manufacturability via additive manufacturing. Two alloys stand out for L-PBF printing of EV enclosures: AlSi10Mg and A6061. Understanding their properties is crucial for engineers and proveedores de polvo de metal alike.
AlSi10Mg:
- Descripción: This is an aluminum alloy containing silicon (around 10%) and magnesium (small percentage). It’s often considered the AM equivalent of common casting alloys like A360.
- Propiedades clave:
- Excelente imprimibilidad: AlSi10Mg is one of the easiest aluminum alloys to process using L-PBF. It exhibits good flowability in powder form and solidifies with a fine microstructure, reducing the likelihood of defects like cracking during printing.
- Buena resistencia y dureza: In the as-built or stress-relieved state, it offers respectable mechanical properties suitable for many enclosure applications.
- Good Thermal Conductivity: While not as high as pure aluminum, its thermal conductivity (around 120-140 W/m·K) is generally sufficient for dissipating heat from power electronics, especially when combined with optimized designs (e.g., cooling fins).
- Resistencia a la corrosión: Ofrece una buena resistencia a la corrosión atmosférica.
- Ligero: Like all aluminum alloys, it has a low density (approx. 2.67 g/cm³).
- Why it Matters for EV Enclosures: Its ease of printing allows for the reliable production of complex geometries often required for integrated thermal management features. Its balance of strength, thermal properties, and weight makes it a workhorse alloy for many prototype and production EV power electronics housing applications where extreme mechanical loads are not the primary concern. It’s widely available from reputable proveedores de polvo de metal.
A6061 (Requires Specialized Processing/Parameters):
- Descripción: A precipitation-hardenable aluminum alloy containing magnesium and silicon as its major alloying elements. It’s a very common wrought alloy known for its versatility, good mechanical properties, weldability, and corrosion resistance. Printing A6061 via L-PBF was initially challenging but has become more feasible with optimized parameters and specialized powder/equipment.
- Key Properties (Requires Proper Heat Treatment, e.g., T6):
- Good Mechanical Properties: After appropriate heat treatment (solutionizing and aging, typically to a T6 temper), A6061 offers significantly better ductility and fracture toughness compared to AlSi10Mg, along with good strength. This makes it suitable for enclosures requiring higher structural integrity or impact resistance.
- Excelente resistencia a la corrosión: Generally offers better corrosion resistance than AlSi10Mg, particularly in marine or harsh environments.
- Good Thermal Conductivity: Similar or slightly better thermal conductivity compared to AlSi10Mg (around 150-170 W/m·K in T6 condition).
- Soldabilidad: Although less relevant for AM parts themselves, its base properties make it compatible with standard finishing/joining processes if needed.
- Material establecido: Engineers are often familiar with A6061 from traditional manufacturing, making property comparisons and acceptance easier.
- Why it Matters for EV Enclosures: For applications demanding higher durability, toughness, or meeting specifications directly calling for automotive grade aluminum like 6061-T6, this alloy is a strong candidate. Its superior mechanical properties after heat treatment can be crucial for safety-critical components or enclosures subjected to higher vibration or potential impacts. However, achieving optimal properties requires careful control over the printing process y post-print heat treatment, making supplier expertise critical.
Panorama comparativo:
Propiedad | AlSi10Mg (As-Built/Stress Relieved) | A6061 (Requires T6 Heat Treatment) | Significance for EV Enclosures |
---|---|---|---|
Imprimibilidad | Excelente | Moderate to Good (Process Sensitive) | AlSi10Mg allows easier printing of complex shapes reliably. |
Resistencia a la tracción | Bien | Good to Excellent (Post-T6) | A6061-T6 offers higher strength for demanding structural loads. |
Ductilidad | Baja | Higher (Post-T6) | A6061-T6 provides better toughness and impact resistance. |
Thermal Cond. | Good ( ~130 W/m·K) | Good (~160 W/m·K) | Both are suitable; A6061 slightly better for heat dissipation. |
Corrosion Res. | Bien | Excelente | A6061 preferred for harsher environments or longer life reqs. |
Tratamiento térmico | Optional (Stress Relief common) | Requerido (T6 for optimal props) | Adds complexity and cost for A6061 processing. |
Exportar a hojas
Supplier Role in Material Quality:
The performance of the final 3D printed enclosure heavily depends on the quality of the raw material – the aluminum 3D printing powder. Consistent particle size distribution, sphericity, flowability, and low levels of impurities (like oxygen or moisture) are essential for achieving dense, defect-free parts with predictable mechanical properties.
This is where partnering with a vertically integrated company like Met3dp provides significant advantages. Met3dp not only offers advanced metal 3D printing services but also specializes in producing high-performance metal powders. Employing industry-leading technologies like atomización de gas y proceso de electrodo giratorio de plasma (PREP), Met3dp ensures its aluminum alloy powders, including variants suitable for demanding applications like EV enclosures, possess the high sphericity, good flowability, and controlled chemistry necessary for successful L-PBF printing. Their commitment to quality control, from powder production to final printed part, gives engineers and procurement managers confidence in the material integrity and performance of the components. Choosing a supplier like Met3dp, with deep expertise in both materials science and additive manufacturing processes, is key to leveraging the full potential of alloys like AlSi10Mg and A6061 for demanding EV material selection challenges.
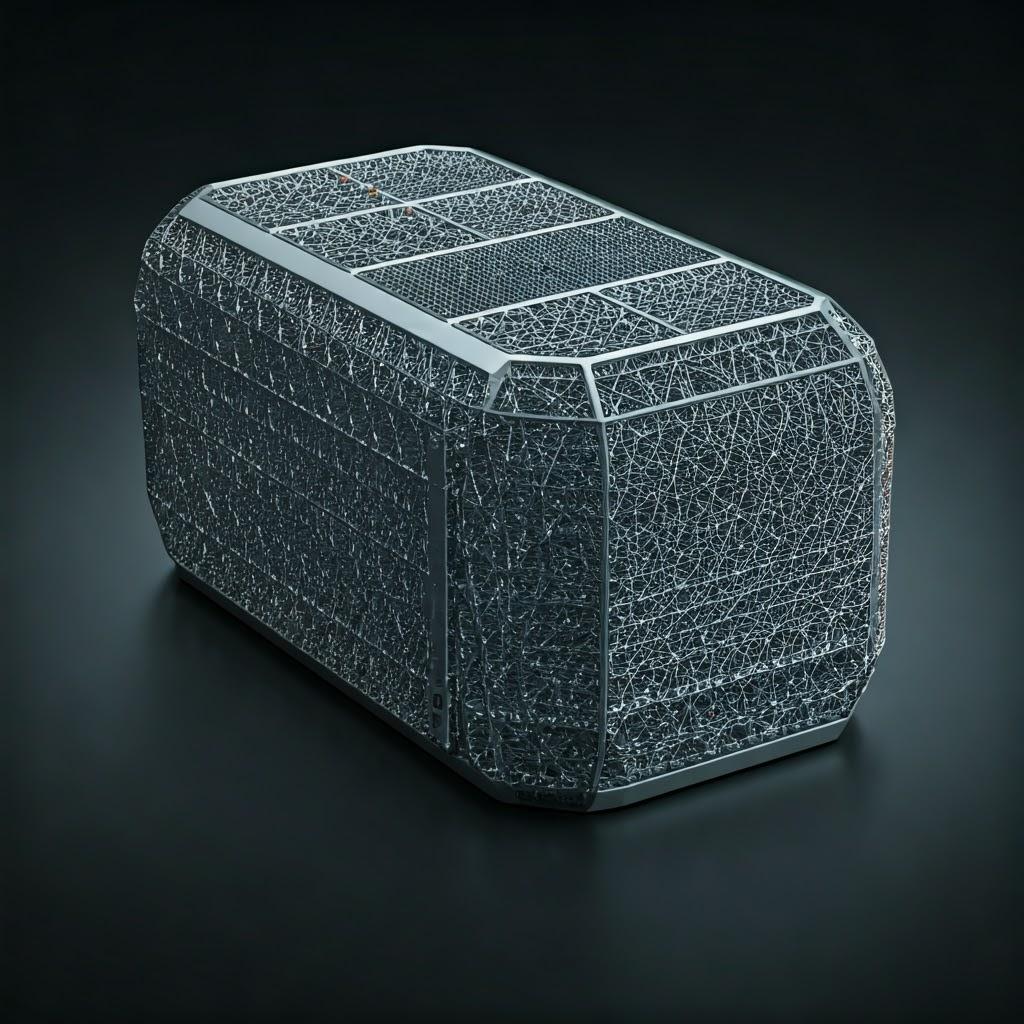
Design for Additive Manufacturing (DfAM) Principles for EV Enclosures
Simply taking a design intended for casting or machining and sending it to a metal 3D printer rarely unlocks the full potential of additive manufacturing. To truly harness the benefits of complexity, lightweighting, and performance enhancement offered by metal AM for EV power control unit enclosures, engineers must embrace Diseño para fabricación aditiva (DfAM) principles. DfAM is not just about ensuring printability; it’s a mindset focused on leveraging the unique capabilities of the layer-by-layer process to create superior components. Applying DfAM to EV enclosures can lead to significant improvements in thermal management, weight reduction, structural integrity, and overall system efficiency.
Here are key DfAM principles crucial for designing high-performance metal AM EV enclosures:
- Optimización de la topología:
- Concept: Using software algorithms to remove material from areas where it’s not structurally required, based on defined load cases, constraints, and performance targets (e.g., stiffness).
- Application for EV Enclosures: Significantly reduces weight while maintaining or even increasing stiffness. Ideal for creating organic, load-bearing structures that efficiently transfer mechanical stresses. Results in lightweight EV components that contribute directly to increased vehicle range.
- Consideraciones: Requires specialized software and engineering expertise. Optimized designs can be complex and may need minor adjustments for printability (e.g., avoiding overly thin features).
- Lattice Structures and Infill:
- Concept: Replacing solid volumes with internal lattice structures (e.g., honeycomb, gyroid, stochastic foams).
- Application for EV Enclosures:
- Aligeramiento: Drastically reduces material usage and weight.
- Enhanced Heat Dissipation: Open-cell lattice structures can increase surface area, potentially aiding passive air cooling or acting as turbulators within liquid cooling channels.
- Amortiguación de vibraciones: Certain lattice types can absorb mechanical energy, potentially reducing stress on sensitive electronics.
- Core Strength: Can provide high stiffness-to-weight ratios.
- Consideraciones: Requires careful selection of lattice type, cell size, and strut thickness based on structural and thermal requirements. Powder removal from complex internal lattices can be challenging and must be considered during the lattice structures design phase.
- Canales de refrigeración conformados:
- Concept: Designing internal cooling channels that precisely follow the contours of heat-generating components or critical areas, rather than being restricted to straight, drilled holes common in traditional manufacturing.
- Application for EV Enclosures: Enables highly efficient and targeted design for thermal management. Liquid coolant can flow closer to heat sources, reducing thermal resistance and improving heat extraction. Leads to more uniform temperature distribution, enhancing the reliability and performance of power electronics.
- Consideraciones: Channel diameter, path smoothness (avoiding sharp bends), surface roughness, and ensuring complete powder removal are critical design factors. Access points for coolant inlet/outlet and potential cleaning must be incorporated.
- Consolidación de piezas:
- Concept: Redesigning an assembly of multiple parts to be printed as a single, monolithic component.
- Application for EV Enclosures: Combining the main housing body with mounting brackets, heat sinks, connector housings, or fluid manifolds into one piece.
- Ventajas: Reduces part count, eliminates assembly steps and labor, removes potential leak paths (e.g., seals between parts), reduces weight by eliminating fasteners, and often improves overall structural integrity.
- Consideraciones: The consolidated part must still be manufacturable (printability, support removal, post-processing access).
- Designing for Self-Support and Minimizing Supports:
- Concept: Orienting the part on the build plate and designing features (e.g., using angles greater than ~45 degrees from the horizontal, incorporating chamfers instead of sharp overhangs) to minimize the need for sacrificial metal AM support structures.
- Application for EV Enclosures: Reduces print time, material consumption (supports are waste), and extensive post-processing effort required to remove supports. Improves surface finish on down-facing surfaces.
- Consideraciones: Requires understanding the specific printer’s capabilities regarding overhang angles. Sometimes supports are unavoidable, especially for complex internal features or large flat planes parallel to the build plate. Support strategy must allow for removal without damaging the part.
- Wall Thickness and Feature Resolution:
- Concept: Adhering to minimum printable wall thicknesses and feature sizes specific to the chosen material (AlSi10Mg, A6061) and L-PBF process.
- Application for EV Enclosures: Ensures structural integrity and prevents print failures. Typical minimum wall thickness for aluminum L-PBF is around 0.4-0.8 mm, though thicker walls (1 mm+) are often recommended for robustness. Small features like pins or holes also have minimum size limits. Aim for thin wall metal printing where appropriate but ensure mechanical stability.
- Consideraciones: Overly thin walls can warp during printing or be damaged during post-processing. Consult with the AM service provider, like Met3dp, for specific guidelines based on their métodos de impresión and equipment.
- Stress Reduction Features:
- Concept: Incorporating design elements like fillets and radii at sharp corners and edges.
- Application for EV Enclosures: Reduces stress concentrations, which can be points of failure under mechanical load or during thermal cycling. Improves fatigue life and overall durability. Smooth transitions also aid powder removal.
- Consideraciones: Apply generously where possible, especially at junctions between thin and thick sections or load-bearing features.
- Powder Removal Considerations:
- Concept: Designing internal channels and cavities with accessibility in mind to facilitate the removal of unfused powder after printing.
- Application for EV Enclosures: Crucial for components with internal cooling channels or complex hollow structures. Trapped powder can add weight, impede fluid flow, and potentially sinter during heat treatment, causing issues.
- Consideraciones: Include strategically placed access holes (that can potentially be plugged later), design channels with smooth paths and sufficient diameters, and avoid creating inescapable powder traps.
Applying these DfAM principles requires a collaborative approach between design engineers and AM specialists. Engaging with an experienced metal 3D printing service bureau early in the design process can provide invaluable feedback, ensuring the final EV enclosure design is optimized for performance, printability, and cost-effectiveness.
Achievable Tolerances, Surface Finish, and Dimensional Accuracy
Engineers and procurement managers accustomed to the precision of CNC machining or the consistency of high-volume casting need to understand the typical tolerances, surface finish, and dimensional accuracy achievable with metal additive manufacturing, specifically Laser Powder Bed Fusion (L-PBF) for aluminum alloys like AlSi10Mg and A6061. Setting realistic expectations is crucial for successful project outcomes and ensuring components meet automotive component specifications.
Dimensional Accuracy and Tolerances:
- As-Built Tolerances: The accuracy of a part directly after printing and stress relief, without secondary machining. For L-PBF aluminum parts, typical achievable tolerances are often cited in the range of:
- ± 0.1 mm to ± 0.3 mm for smaller features (e.g., up to 50 mm)
- ± 0.2% to ± 0.5% of nominal dimension for larger features
- A common general tolerance standard referenced is ISO 2768-m (medium class), although tighter tolerances are sometimes possible depending on geometry, orientation, and process control.
- Factores que influyen en la precisión:
- Printer Calibration & Quality: Higher-end industrial printers, like those utilized by Met3dp, offer better beam control, thermal management, and calibration, leading to higher accuracy. Met3dp’s focus on industry-leading print volume, accuracy, and reliability directly impacts the achievable precision for precision EV components.
- Part Size and Geometry: Larger parts are more susceptible to thermal distortion, potentially affecting overall accuracy. Complex geometries can also accumulate errors.
- Orientación de construcción: How the part is oriented on the build plate affects thermal behavior, support requirements, and ultimately, dimensional accuracy.
- Thermal Stress: Residual stress built up during printing can cause minor distortions, which are partially relieved during post-print heat treatment.
- Estrategia de apoyo: How supports are designed and attached can influence the final dimensions of supported features.
- Achieving Tighter Tolerances: For critical features requiring tolerances tighter than the as-built capability (e.g., mating surfaces, bearing bores, threaded holes), post-print CNC machining is typically employed. Machining specific features on an otherwise near-net-shape AM part allows for tolerances comparable to traditional CNC machining (e.g., ± 0.01 mm to ± 0.05 mm or better, depending on the operation).
Acabado superficial (rugosidad):
- As-Built Surface Finish: L-PBF creates parts layer by layer by melting powder particles, resulting in a characteristic surface texture. The surface roughness (typically measured as Ra – arithmetic average roughness) depends heavily on the orientation of the surface relative to the build direction:
- Top Surfaces (facing up): Generally smoother, Ra often 5-15 µm.
- Side Walls (vertical): Show layer lines, Ra typically 10-25 µm.
- Down-Facing Surfaces (supported): Tend to be rougher due to interaction with support structures or partially sintered powder, Ra can be 20-40 µm or higher. Steeper angles (closer to vertical) generally yield better finishes than shallow overhangs.
- Factors Influencing Surface Finish:
- Grosor de la capa: Thinner layers generally result in finer surface finish but increase print time.
- Distribución granulométrica del polvo: Finer, spherical powders tend to produce smoother surfaces. Met3dp’s advanced powder manufacturing ensures optimal powder characteristics.
- Laser Parameters: Beam spot size, energy density, and scanning strategy influence the melt pool characteristics and resulting surface.
- Orientación de construcción: As noted above, surface orientation is a primary driver of roughness.
- Mejora del acabado superficial: If the as-built finish is insufficient for the application (e.g., for sealing surfaces, aesthetic requirements, or fluid flow channels), various post-processing surface finishing metal AM techniques can be applied:
- Bead Blasting/Shot Peening: Creates a uniform, matte finish, typically Ra 5-10 µm. Can also induce compressive stress, improving fatigue life.
- Tumbling/Vibratory Finishing: Uses abrasive media to smooth surfaces and round edges, effective for batches of smaller parts.
- Mecanizado CNC: Provides smooth, precision surfaces on specific features.
- Polishing (Manual or Automated): Can achieve very smooth, mirror-like finishes (Ra < 1 µm) but is often labor-intensive and geometry-dependent.
- Chemical Polishing/Electro-polishing: Can smooth complex surfaces but requires careful process control.
Quality Control and Assurance:
Achieving consistent dimensional accuracy and surface finish requires robust quality control metal printing procedures. This includes:
- Regular printer calibration and maintenance.
- Powder quality management (testing, handling, recycling protocols).
- In-process monitoring (melt pool monitoring, thermal imaging – where available).
- Post-print inspection:
- Dimensional checks using CMM (Coordinate Measuring Machines), 3D scanners, or traditional metrology tools.
- Surface roughness measurements.
- Visual inspection for defects.
- Potentially NDT (Non-Destructive Testing) like CT scanning for internal integrity checks, especially for critical components.
Understanding these capabilities and limitations allows engineers to design parts effectively, specifying tolerances and finishes where they are truly needed and leveraging post-processing strategically. Procurement managers should ensure potential metal 3D printing service bureau partners have the necessary equipment, processes, and quality systems to meet the specific requirements of their EV enclosure applications.
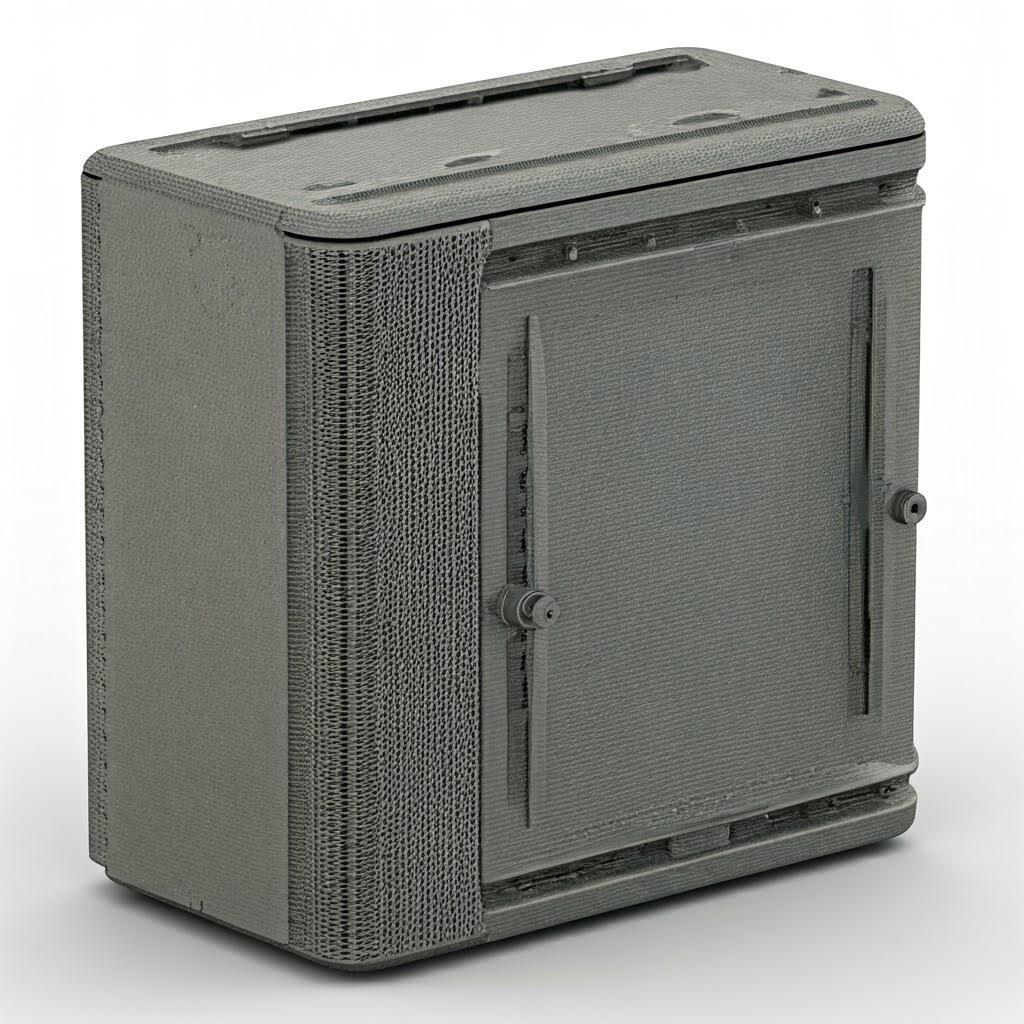
Essential Post-Processing Steps for Metal AM EV Enclosures
Creating a metal EV enclosure using L-PBF is only part of the manufacturing journey. The “green” part directly off the printer requires several crucial post-processing requirements to achieve the final desired properties, tolerances, and finish. These steps are integral to the workflow and significantly impact the final component’s performance, cost, and lead time. Engaging with a comprehensive post-processing services supplier, or a vertically integrated provider like Met3dp who manages these steps internally or through trusted partners, is essential.
Here’s a breakdown of common post-processing steps for L-PBF aluminum EV enclosures:
- Alivio del estrés / Tratamiento térmico:
- Propósito: The rapid heating and cooling cycles inherent in L-PBF induce significant residual stresses within the printed part. These stresses can cause distortion or warping, especially after the part is removed from the rigid build plate, and can negatively affect mechanical properties. Heat treatment is essential to relieve these stresses and, in the case of alloys like A6061, to achieve the desired mechanical properties (temper).
- Proceso:
- Stress Relief (Typically for AlSi10Mg and as an interim step for A6061): Heating the part (while often still attached to the build plate) to a moderate temperature (e.g., 200-300°C) for a specific duration, followed by controlled cooling. This relaxes internal stresses without significantly altering the microstructure.
- T6 Temper (Required for A6061): A more complex multi-stage process involving:
- Solución Tratamiento: Heating to a high temperature (around 520-540°C) to dissolve alloying elements into a solid solution.
- Enfriamiento: Rapidly cooling (typically in water) to lock the elements in solution.
- Artificial Aging: Reheating to a lower temperature (e.g., 160-190°C) for several hours to allow controlled precipitation of strengthening phases. This significantly increases strength and hardness.
- Importancia: Absolutely critical for dimensional stability and achieving target mechanical performance, especially for heat treatment aluminum alloys like A6061. Must be performed correctly to avoid part distortion or suboptimal properties.
- Extracción de la pieza de la placa de montaje:
- Propósito: Separating the printed enclosure(s) from the metal build plate they were fused onto during the printing process.
- Métodos: Typically done using:
- Electroerosión por hilo (EDM): Precise method, good for complex or delicate parts, minimal mechanical stress.
- Sierra de cinta: Faster and more cost-effective for simpler geometries, but less precise and induces more mechanical stress.
- Consideraciones: The removal method should minimize damage or distortion to the part. Often a small base or raft structure is printed beneath the part to facilitate easier removal.
- Retirada de la estructura de soporte:
- Propósito: Removing the temporary structures printed concurrently with the part to support overhangs and prevent distortion during the build.
- Métodos: Can range from simple manual breakaway (if supports are designed for it) to more involved mechanical methods:
- Hand Tools: Pliers, cutters, grinders for accessible supports.
- Mecanizado CNC: Milling or grinding away support structures, especially in critical areas or where a smooth surface is required post-removal.
- Specialized Tools: Custom tools, potentially electrochemical machining for difficult-to-reach internal supports.
- Desafíos: Can be labor-intensive, time-consuming, and potentially damaging to the part if not done carefully. Accessing internal supports within complex enclosure geometries is particularly challenging and highlights the importance of DfAM to minimize internal supports.
- Eliminación del polvo:
- Propósito: Ensuring all unfused metal powder is removed from the part, especially from internal channels, cavities, and complex lattice structures. Trapped powder adds weight and can cause issues later (e.g., sintering during heat treatment, contaminating fluid paths).
- Métodos:
- Compressed Air Blowing: Basic removal for accessible areas.
- Bead Blasting: Can help dislodge powder while also starting the surface finishing process.
- Vibration / Ultrasonic Cleaning: Shaking or vibrating the part to loosen trapped powder.
- Manual Cleaning: Using brushes, picks, and vacuum systems.
- Flow-Based Systems: Pumping liquids or gases through internal channels.
- Importancia: Crítico para fabricación aditiva parts with internal features, like conformal cooling channels in an EV enclosure. Incomplete powder removal is a common quality issue.
- Mecanizado CNC:
- Propósito: To achieve tight tolerances, specific surface finishes, or features that cannot be accurately produced by the L-PBF process alone.
- Applications for EV Enclosures:
- Mating Surfaces: Ensuring flat, smooth surfaces for sealing (e.g., lid interfaces).
- Critical Tolerances: Achieving precise dimensions for connector ports, mounting points, or bearing seats.
- Threaded Holes: Tapping threads for fasteners.
- Surface Finish Improvement: Creating smooth surfaces where needed.
- Consideraciones: Requires careful fixture design to hold the often complex AM part securely without distortion. Integration between AM and machining is key for CNC machining 3D printed parts.
- Acabado superficial:
- Propósito: To improve the surface roughness, appearance, wear resistance, or corrosion resistance of the printed enclosure.
- Methods (as discussed previously): Bead blasting (common for uniform matte finish), tumbling, polishing, anodizing (excellent for corrosion resistance and electrical insulation on aluminum), painting, powder coating. Appropriate coating solutions EV components might need include those providing dielectric strength or enhanced thermal emissivity.
- Selection: Depends on the specific functional and aesthetic requirements of the enclosure.
- Inspection and Quality Assurance (QA):
- Propósito: Verifying that the finished part meets all specified requirements.
- Métodos: Dimensional inspection (CMM, scanning), surface roughness measurement, visual inspection, leak testing (if applicable for liquid cooling), material certification verification, NDT if required.
The extent and combination of these post-processing steps depend heavily on the specific design and requirements of the EV enclosure. Understanding these steps helps engineers design appropriately and allows procurement managers to accurately assess the total cost and lead time associated with sourcing metal AM components.
Common Challenges in Printing EV Enclosures and Mitigation Strategies
While metal additive manufacturing offers transformative potential for EV enclosures, it’s not without its challenges. Understanding these potential hurdles and the strategies to mitigate them is crucial for successfully implementing the technology. Awareness helps manage expectations and ensures collaboration between designers and the AM service provider to proactively address issues.
1. Warping and Distortion:
- Desafío: The intense localized heating by the laser and subsequent rapid cooling creates significant thermal gradients within the part during the L-PBF process. This leads to internal stresses that can cause the part to warp, distort, or even detach from the build plate, especially in large, flat, or thin-walled structures common in enclosures.
- Estrategias de mitigación:
- Simulación térmica: Using Finite Element Analysis (FEA) software specialized for AM to predict thermal behavior and stress accumulation, allowing for design modifications or optimized build setup before impresión.
- Orientación de construcción: Strategically orienting the part to minimize large flat surfaces parallel to the build plate and manage heat distribution.
- Optimized Support Structures: Designing robust supports not just for overhangs but also to anchor the part securely to the build plate and act as heat sinks, counteracting warping forces.
- Optimización de los parámetros del proceso: Adjusting laser power, scan speed, and hatching strategies to minimize thermal gradients (requires significant expertise).
- Construir calefacción de placas: Maintaining an elevated temperature on the build plate can reduce the severity of thermal gradients.
- Appropriate Heat Treatment: Post-print stress relief is essential to relax residual stresses and stabilize the part’s geometry.
2. Residual Stress Management:
- Desafío: Even if significant warping is avoided, high levels of residual stress remain within the as-built part. This can lead to premature failure under load, reduced fatigue life, or distortion during subsequent machining operations.
- Estrategias de mitigación:
- Optimización de los parámetros del proceso: As above, tuning parameters can influence stress levels.
- Estrategias de exploración optimizadas: Using techniques like island scanning or checkerboard patterns can help distribute heat more evenly.
- Mandatory Heat Treatment: Proper stress relief or full heat treatment (like T6 for A6061) is the primary method for significantly reducing residual stress.
- Consideraciones sobre el diseño: Avoiding abrupt changes in cross-section and using fillets can help distribute stress more evenly.
3. Support Structure Removal Difficulty:
- Desafío: Supports are often necessary but removing them, especially dense supports or those located in complex internal geometries (like cooling channels or lattice structures), can be extremely difficult, time-consuming, and risks damaging the part. Support removal issues are a major post-processing bottleneck.
- Estrategias de mitigación:
- DfAM para el autoapoyo: Designing parts with overhang angles greater than the process limit (~45° for aluminum) minimizes the need for supports. Using chamfers instead of sharp overhangs.
- Optimized Support Design: Using support types that are easier to remove (e.g., tree supports, conical supports, block supports with perforation). Designing supports with specific breakaway points.
- Accessibility Planning: Ensuring tools can physically reach supports for removal. Designing access ports if necessary for internal supports.
- Advanced Removal Techniques: Utilizing CNC machining or potentially electrochemical methods for challenging supports.
- Consultation: Working closely with the AM provider, like Met3dp, whose engineers understand how to best orient parts and design effective yet removable supports using their specific producto capacidades.
4. Porosity Control:
- Desafío: Small voids or pores can form within the printed material due to trapped gas (gas porosity) or incomplete melting/fusion between layers (lack of fusion porosity). Porosity reduces the density, mechanical strength, fatigue life, and thermal conductivity of the enclosure. It can also create leak paths in enclosures designed for liquid cooling.
- Estrategias de mitigación:
- High-Quality Metal Powder: Using powder with high sphericity, good flowability, controlled particle size distribution, and low trapped gas/moisture content is crucial. Met3dp’s focus on advanced powder production (Gas Atomization, PREP) directly addresses this need.
- Parámetros de impresión optimizados: Carefully tuning laser power, scan speed, layer thickness, and hatch spacing to ensure complete melting and fusion. This often requires extensive process development by the AM provider.
- Controlled Build Environment: Maintaining proper inert gas atmosphere (e.g., Argon) within the build chamber to minimize oxidation and gas pickup.
- Prensado isostático en caliente (HIP): A post-processing step involving high temperature and high pressure, which can close internal pores. However, HIP is expensive, adds lead time, and can affect dimensions, so it’s typically reserved for highly critical applications, less common for standard enclosures unless extreme reliability is needed.
- Control de calidad: Implementing NDT methods like CT scanning to detect internal porosity if required by specifications.
5. Surface Finish Consistency:
- Desafío: Achieving a consistent surface finish across all surfaces of a complex enclosure can be difficult due to the orientation-dependent nature of L-PBF surface roughness. Down-facing surfaces and areas affected by support structures will inherently be rougher.
- Estrategias de mitigación:
- Strategic Build Orientation: Prioritizing critical surfaces to be oriented upwards or vertically if possible.
- Optimized Support Settings: Adjusting the interface between supports and the part to minimize witness marks (though this can make removal harder).
- Post-Processing Finishing: Implementing appropriate surface finishing steps (bead blasting, tumbling, machining) to achieve the desired uniform finish where required. Manage expectations – achieving a machined finish everywhere is usually impractical and costly.
6. Powder Removal from Internal Features:
- Desafío: As mentioned in DfAM and post-processing, completely removing unfused powder from long, narrow, or complex internal channels and lattices is a significant hurdle.
- Estrategias de mitigación:
- DfAM for Accessibility: Designing channels with sufficient diameter, smooth paths, and access ports.
- Specialized Cleaning Processes: Utilizing advanced techniques beyond compressed air, such as ultrasonic cleaning in specific solvents, vibration tables, or controlled fluid flushing systems.
- Inspection: Using borescopes or potentially CT scanning to verify powder removal from critical internal passages.
Successfully navigating these challenges requires a combination of smart design (DfAM), robust process control during printing, diligent post-processing, and strong collaboration with an experienced fabricación aditiva de metales partner equipped with the right technology and expertise. Troubleshooting additive manufacturing issues is part of the process, and working with a knowledgeable provider accelerates problem-solving.
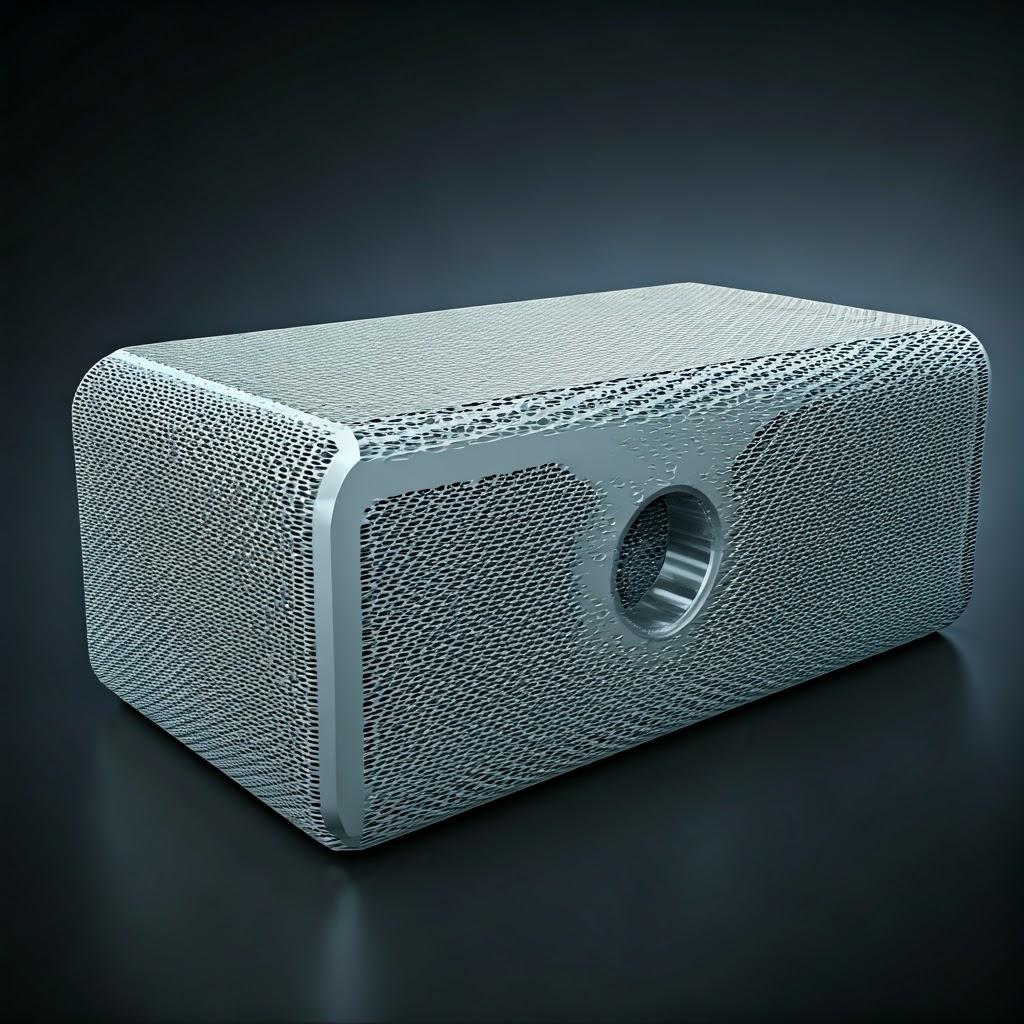
Selecting the Right Metal Additive Manufacturing Partner for Automotive Components
Choosing the right manufacturing partner is always critical, but it takes on heightened importance when dealing with advanced technologies like metal additive manufacturing for demanding applications such as EV power control unit enclosures. The capabilities, expertise, quality systems, and collaborative approach of your chosen metal 3D printing service bureau will directly impact the success of your project, from initial design optimization to the delivery of reliable, high-performance components. Selecting a partner solely based on the lowest quoted price can be a false economy if it leads to quality issues, delays, or parts that fail to meet performance requirements. For engineers and procurement managers sourcing B2B additive manufacturing solutions, a thorough evaluation process is essential.
Here are key criteria to consider when evaluating metal printing companies for automotive EV enclosure projects:
- Technical Expertise and Experience:
- Process Knowledge: Deep understanding of Laser Powder Bed Fusion (L-PBF) physics, parameter development, and the nuances of printing aluminum alloys like AlSi10Mg and A6061.
- Application Understanding: Familiarity with automotive requirements, particularly for electronic enclosures – thermal management, structural integrity, EMC shielding, vibration resistance, and relevant industry standards.
- DfAM Proficiency: Demonstrated ability to provide expert guidance on Design for Additive Manufacturing, helping optimize designs for printability, performance, and cost-effectiveness.
- Problem-Solving Skills: Experience in troubleshooting common AM challenges (warping, porosity, support issues) and implementing effective solutions.
- Quality Management Systems and Certifications:
- ISO 9001: A fundamental requirement, indicating a documented and implemented quality management system.
- IATF 16949 (Ideal): While not always feasible for all AM providers (especially smaller ones or those focused on prototyping), certification to this automotive-specific standard demonstrates a commitment to rigorous quality processes, defect prevention, and continual improvement required for series production parts. Enquire about their roadmap or compliance level if full certification isn’t present.
- Trazabilidad: Robust systems for tracking materials (powder batches) and process data throughout the manufacturing workflow, ensuring accountability and enabling root cause analysis if issues arise.
- Technology and Equipment:
- Industrial-Grade Printers: Access to well-maintained, industrial L-PBF machines known for reliability and accuracy (e.g., from manufacturers like EOS, SLM Solutions, Renishaw, Concept Laser/GE Additive, Farsoon). Assess the size of their fleet and printer build volumes to ensure capacity.
- Powder Management: Climate-controlled environments and proper procedures for handling, storing, sieving, and recycling metal powders to maintain quality and prevent contamination.
- Capacidades de postprocesado: In-house or tightly controlled access to essential post-processing equipment: heat treatment ovens (with proper atmosphere control and calibration for aluminum alloys), CNC machining centers (3-axis and ideally 5-axis), surface finishing tools (bead blasting, tumbling), and cleaning systems.
- Metrology and Inspection Lab: Comprehensive equipment for quality assurance, including CMMs, 3D scanners, surface profilometers, and potentially NDT equipment.
- Material Expertise and Supply:
- Portafolio de materiales: Offers the specific aluminum alloys required (AlSi10Mg, A6061) and potentially others relevant to automotive applications.
- Powder Quality Control: Rigorous testing and validation of incoming powder batches (chemistry, particle size distribution, morphology, flowability). Clear protocols for powder reuse and lifetime tracking.
- Vertically Integrated Advantage: Partners like Met3dp offer a distinct advantage here. As a company that not only provides printing services but also develops and manufactures its own high-quality metal powders using advanced Gas Atomization and PREP technologies, Met3dp has unparalleled control over material quality and a deeper understanding of material-process interactions. This integration ensures consistency and performance from raw material to final part. You can learn more about their comprehensive approach on their ‘Quiénes somos‘ page.
- Engineering and Design Support:
- DfAM Consultation: Willingness and capability to collaborate early in the design phase to optimize parts for AM.
- Simulation Capabilities: Offering services like build simulation (thermal, stress) to predict and mitigate potential issues before printing.
- Asistencia técnica: Responsive engineers available to discuss project details, challenges, and solutions.
- Capacity, Scalability, and Lead Times:
- Prototyping Speed: Ability to deliver prototypes quickly to support rapid development cycles.
- Capacidad de producción: Sufficient machine availability and workflow efficiency to handle low-to-medium volume production runs within agreed timelines. Understand their capacity planning and how they manage machine scheduling.
- Escalabilidad: A clear plan or capability to scale production if volumes increase.
- Track Record and References:
- Proven Experience: Demonstrated success with similar projects, ideally within the automotive sector or involving complex enclosures with thermal management requirements. Ask for case studies or non-confidential examples.
- Customer Testimonials/References: Willingness to provide references from satisfied clients.
- Comunicación y gestión de proyectos:
- Clear Communication: Designated points of contact, regular updates, and transparent communication regarding project status, potential issues, and timelines.
- Professionalism: Organized workflow, clear quotations, and reliable project management practices.
Seleccionar el automotive certified supplier (or one with equivalent quality rigor) for metal AM involves looking beyond the surface. It requires assessing their technical depth, quality commitment, technological infrastructure, and collaborative spirit. A strong partner acts as an extension of your engineering team, contributing expertise to ensure the successful realization of your advanced EV enclosure designs.
Cost Analysis and Lead Time Expectations for 3D Printed EV Enclosures
Understanding the cost structure and typical lead times associated with metal additive manufacturing is crucial for project planning, budgeting, and making informed decisions about when and where to apply this technology for EV power control unit enclosures. While AM eliminates tooling costs, the overall additive manufacturing pricing is influenced by a different set of factors compared to traditional methods.
Key Cost Drivers for Metal AM EV Enclosures:
- Material Consumption:
- Part Volume: The net volume of the final part directly translates to the amount of expensive metal powder consumed.
- Volumen de la estructura de soporte: Powder used for printing support structures adds to the material cost. Efficient DfAM aims to minimize this.
- Powder Type: Different metal powders have different base costs (e.g., specialized alloys might be more expensive than standard AlSi10Mg). Powder quality and processing also influence cost.
- Eficacia de reciclaje del polvo: The provider’s ability to efficiently recycle and reuse unfused powder impacts the effective material cost.
- Machine Time (Print Time):
- Part Height (Z-Height): L-PBF builds layer by layer, so the height of the part in the build orientation is a primary driver of print time.
- Part Volume/Cross-Sectional Area: Larger volumes and wider cross-sections require more laser scanning per layer, increasing time.
- Complejidad: Very intricate features might require slower scanning speeds or specific strategies, potentially increasing print time slightly.
- Máquina Tarifa por hora: Industrial metal AM machines represent significant capital investment, and their operating costs (energy, inert gas, maintenance, depreciation) contribute heavily to the hourly rate charged. This is often the largest single cost component.
- Costes laborales:
- Preparación de la construcción: CAD file processing, build layout planning, support structure generation, machine setup.
- Funcionamiento de la máquina: Monitoring the build process.
- Post-procesamiento: Significant labor is often involved in part removal, support removal (can be very intensive), powder removal, CNC machining setup and operation, surface finishing, and inspection. The complexity and requirements here heavily influence cost.
- Intensidad de postprocesado:
- Tratamiento térmico: Required cycles (simple stress relief vs. full T6 temper) add time and cost (furnace time, energy).
- Mecanizado CNC: The number of features requiring machining, the complexity of setups, and the required tolerances directly impact machining time and cost.
- Acabado superficial: The desired level of finish (basic bead blast vs. multi-step polishing or anodizing) dictates the processes, time, and cost involved.
- Garantía de calidad: The level of inspection required (basic dimensional check vs. CMM report, leak testing, NDT) adds labor and equipment time.
- Order Quantity and Build Density:
- Economías de escala: While AM doesn’t have the steep tooling amortization curve of casting, some economies exist. Setting up a build is largely a fixed cost, so printing multiple parts simultaneously (nesting) within the build chamber reduces the setup cost per part. Larger quantities might also allow for more optimized post-processing workflows.
- Nesting Efficiency: How efficiently multiple parts can be packed into a single build volume affects the machine time cost per part.
Comparing Costs:
- Prototypes & Low Volume: Metal AM is often highly cost-competitive, even cheaper than traditional methods, because it avoids tooling costs (which can be tens or hundreds of thousands of dollars for die casting).
- Medium Volume: The cost-effectiveness depends heavily on the part’s complexity and the specific traditional method being compared against. Optimized AM parts might still be competitive if they offer significant weight savings or performance benefits (like integrated thermal management) that offset a potentially higher piece price.
- High Volume: For relatively simple enclosure designs produced in very high volumes (tens or hundreds of thousands), traditional methods like die casting typically become more cost-effective per part due to lower cycle times and material costs, despite the initial tooling investment.
Lead Time Expectations:
Lead time is often a major advantage of metal AM, particularly for prototypes and initial production batches.
- Prototipos: Once the design is finalized, a typical lead time for a single or small batch of metal AM EV enclosures can range from 5 to 15 business days. This includes:
- File preparation and scheduling (~1-2 days)
- Printing (~1-5 days, depending on size/complexity/nesting)
- Post-processing (stress relief, removal, basic finishing) (~2-8 days, depending on complexity)
- QA and shipping (~1-2 days)
- Low-to-Medium Volume Production: Lead times will increase based on the number of parts, required machine time, post-processing intensity, and the provider’s capacity. This could range from 3 to 8 weeks or more, depending on the specifics. Clear communication with the custom metal fabrication supplier is crucial for establishing realistic timelines.
- Comparison to Traditional: This contrasts sharply with methods like die casting, where the initial tooling creation alone can take 8-16 weeks or longer, meaning the first parts are available much later, even if the subsequent per-part production rate is high.
Understanding these metal 3D printing cost factors y rapid prototyping lead time advantages allows teams to strategically deploy AM where it adds the most value – accelerating development, enabling complex designs, facilitating customization, and bridging the gap to higher volume production. Procurement managers seeking wholesale metal printing quotes should provide detailed specifications and expected volumes to get accurate pricing and timelines.
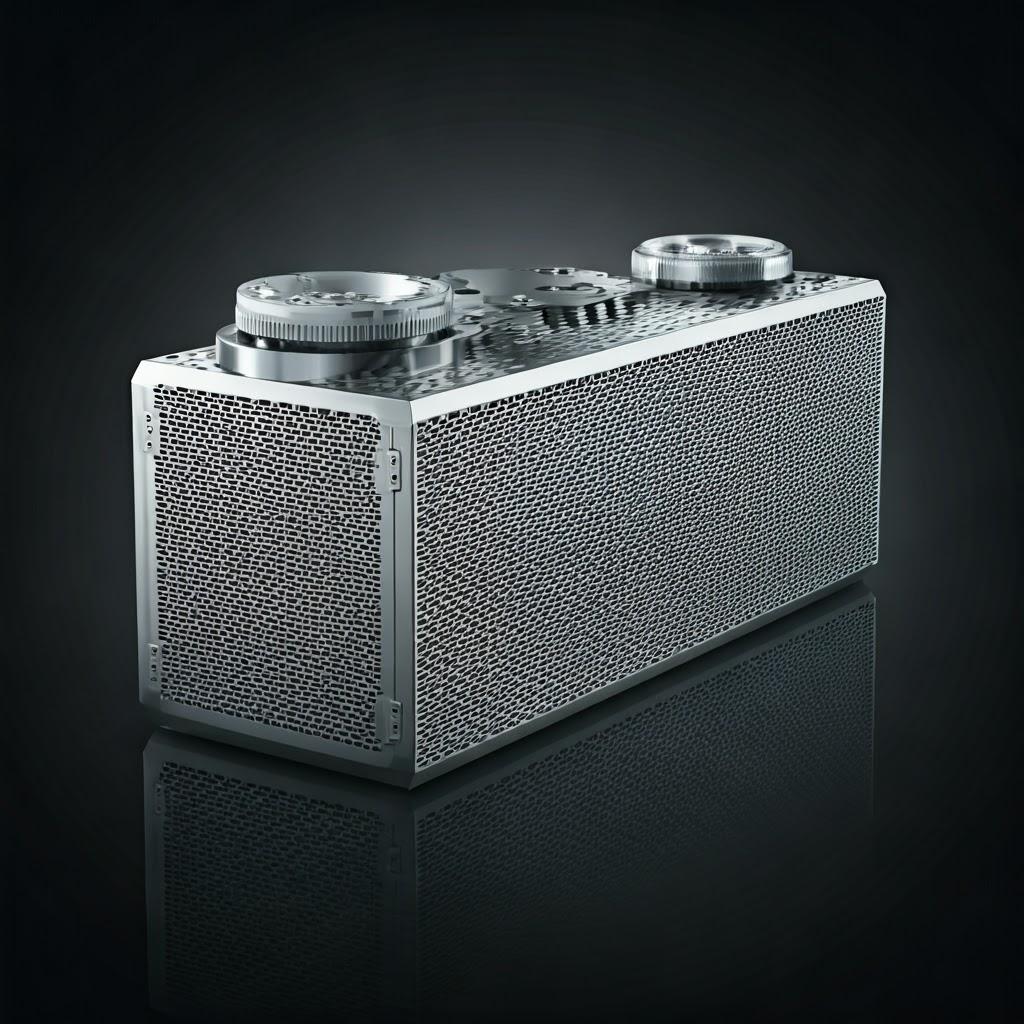
Frequently Asked Questions (FAQ) about Metal AM for EV Enclosures
Here are answers to some common questions engineers and procurement managers have when considering metal additive manufacturing for EV power control unit enclosures:
1. How does the performance (thermal, structural, EMC) of a 3D printed aluminum enclosure compare to a traditional cast or machined one?
- Thermal: Often superior. Metal AM allows for the creation of complex internal cooling channels (conformal cooling) and optimized fin structures that precisely match heat sources, leading to significantly better thermal dissipation than possible with the design constraints of casting or machining. Materials like AlSi10Mg and A6061 offer good intrinsic thermal conductivity.
- Structural: Comparable or potentially better. While cast alloys might have slightly different bulk properties, AM allows for topology optimization, placing material exactly where needed for stiffness and strength. This results in highly efficient, lightweight structures that meet or exceed the structural requirements. Post-T6 heat treatment for A6061 ensures excellent mechanical properties. Proper DfAM and process control are key to achieving desired strength and durability, making them suitable for high-vibration automotive environments.
- EMC Shielding: Generally comparable. Solid metal enclosures made from conductive aluminum alloys provide excellent EMI shielding. The layer-by-layer nature of AM doesn’t inherently compromise shielding effectiveness, provided the part achieves full density without significant porosity near the surfaces.
2. Is metal 3D printing cost-effective for more than just prototypes? What’s the typical cost difference?
- Metal AM is highly cost-effective for prototypes and low-volume production (tens to hundreds, sometimes thousands of parts) primarily because it eliminates tooling costs. For a complex enclosure, die casting tooling can cost $50,000 – $150,000+, making AM much cheaper for initial runs. The per-part cost in AM decreases moderately with volume due to build nesting and workflow efficiencies but remains significantly influenced by machine time and labor. In contrast, casting per-part cost drops dramatically once tooling is amortized. The crossover point where casting becomes cheaper depends heavily on part complexity, size, and annual volume, but AM is often competitive well into the hundreds or low thousands of units, especially if its design advantages (lightweighting, integration) provide added value.
3. How difficult is it to clean internal cooling channels or complex lattice structures after printing, and can we be sure they are clean?
- It can be challenging but is achievable with proper design and process control. DfAM is crucial: designing channels with adequate diameters, smooth paths, and access ports for cleaning is essential. Specialized Cleaning Processes are often required, going beyond simple compressed air to include vibration, ultrasonic cleaning in solvents, or controlled fluid flushing. Verification is key: providers may use methods like borescope inspection or airflow/pressure tests to ensure channels are clear. For highly critical applications, CT scanning can provide definitive confirmation of powder removal, though it adds cost. Discuss cleaning requirements and verification methods explicitly with your AM partner.
4. Are 3D printed aluminum enclosures durable enough for demanding automotive environments (vibration, temperature cycling, corrosion)?
- Yes, when designed, printed, and post-processed correctly.
- Vibración: Topology optimization and proper DfAM (using fillets, avoiding stress concentrators) create robust structures. Material properties of L-PBF AlSi10Mg and especially T6-treated A6061 offer good fatigue resistance.
- Temperature Cycling: Aluminum alloys handle typical automotive operating temperatures well. Proper stress relief minimizes internal stresses that could be exacerbated by thermal cycling.
- Corrosion: Aluminum naturally forms a protective oxide layer. A6061 generally offers better corrosion resistance than AlSi10Mg. For harsh environments, post-processing treatments like anodizing or painting provide excellent additional protection.
5. What certifications should we look for in a metal AM supplier for automotive components?
- ISO 9001: This is the baseline requirement, demonstrating a functional quality management system.
- IATF 16949: This is the automotive industry standard. Full certification is ideal for series production parts suppliers, indicating rigorous process control, traceability, and continuous improvement aligned with automotive expectations. If a supplier isn’t fully certified (common for newer tech providers), inquire about their quality system’s maturity, compliance efforts, and specific processes relevant to automotive needs (e.g., PPAP capabilities if required).
- Material Certifications: Ensure the supplier provides material traceability and certificates of conformity for the metal powders used, verifying chemistry and quality standards.
Conclusion: Accelerating EV Innovation with Custom Metal AM Enclosures
The relentless drive for higher performance, longer range, and faster charging in the electric vehicle market places unprecedented demands on components like power control unit enclosures. Traditional manufacturing methods, while mature, often struggle to deliver the intricate designs needed for optimal thermal management, lightweighting, and packaging efficiency. Metal additive manufacturing, particularly Laser Powder Bed Fusion using high-performance aluminum alloys like AlSi10Mg and A6061, offers a powerful solution to overcome these limitations.
As we’ve explored, the key benefits of leveraging metal AM for custom enclosures for EV power units are compelling:
- Unrivaled Design Freedom: Enabling complex geometries like conformal cooling channels and topology-optimized structures for superior thermal performance and significant weight reduction.
- Creación rápida de prototipos e iteración: Drastically accelerating development cycles by producing functional prototypes in days, not weeks or months.
- Consolidación de piezas: Integrating multiple functions into a single component, reducing assembly complexity, weight, and potential points of failure.
- Personalización: Enabling tailored enclosure designs for specific vehicle platforms or performance requirements without prohibitive tooling costs.
- Competitive Low-Volume Production: Providing a cost-effective manufacturing route for initial production ramps or niche vehicle applications.
However, realizing these benefits requires more than just access to a 3D printer. It demands a holistic approach encompassing Diseño para fabricación aditiva (DfAM) principles, careful material selection, meticulous process control, appropriate post-processing, and robust quality assurance. Perhaps most importantly, it requires collaboration with the right manufacturing partner – one with deep technical expertise, advanced technology, a commitment to quality, and a focus on the specific needs of the additive manufacturing automotive industry.
Empresas como Met3dp, with their integrated capabilities spanning advanced metal powder production and state-of-the-art soluciones de impresión 3D en metal, represent the future of advanced EV component manufacturing. Their expertise in materials science, coupled with industry-leading printing technology and a comprehensive understanding of post-processing, positions them as an ideal partner for automotive engineers and procurement managers looking to push the boundaries of EV design.
By embracing metal AM and partnering with knowledgeable suppliers, the automotive industry can unlock new levels of performance, efficiency, and innovation in electric vehicles. The journey involves navigating new design paradigms and manufacturing processes, but the rewards – lighter, cooler, and more integrated power electronic systems – are essential for accelerating the transition to a sustainable electric future.
Ready to explore how metal additive manufacturing can revolutionize your next EV project? Visit Met3dp to learn more about their capabilities and how they can power your organization’s additive manufacturing goals.
Compartir
MET3DP Technology Co., LTD es un proveedor líder de soluciones de fabricación aditiva con sede en Qingdao, China. Nuestra empresa está especializada en equipos de impresión 3D y polvos metálicos de alto rendimiento para aplicaciones industriales.
Solicite información para obtener el mejor precio y una solución personalizada para su empresa.
Artículos relacionados
Acerca de Met3DP
Actualización reciente
Nuestro producto
CONTACTO
¿Tiene alguna pregunta? ¡Envíenos un mensaje ahora! Atenderemos su solicitud con todo un equipo tras recibir su mensaje.
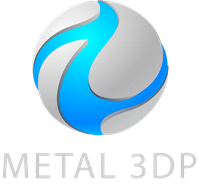
Polvos metálicos para impresión 3D y fabricación aditiva