Lightweight Enclosures for UAV Payload Systems
Índice
Lightweight Enclosures for UAV Payload Systems: The Metal 3D Printing Advantage
Unmanned Aerial Vehicles (UAVs), commonly known as drones, have transcended their military origins to become indispensable tools across a vast spectrum of industries. From precision agriculture and infrastructure inspection to defense surveillance and commercial delivery, UAVs are performing tasks faster, safer, and more efficiently than ever before. At the heart of these advanced capabilities lies the payload – the sophisticated sensors, cameras, communication arrays, or specialized equipment that enable the UAV to perform its designated mission. Protecting this critical, often delicate and expensive, payload is paramount, and this responsibility falls upon the payload enclosure.
A UAV payload enclosure is far more than just a box. It is a meticulously engineered component designed to shield sensitive electronics and optics from harsh environmental conditions (temperature extremes, moisture, dust, vibration), electromagnetic interference (EMI), radio frequency interference (RFI), and physical impacts. Traditionally, designing these enclosures involved a significant engineering challenge: balancing the need for robust protection and structural integrity with the absolute necessity of minimizing weight. Every gram saved on a UAV component translates directly into longer flight times, increased payload capacity, or enhanced maneuverability – critical performance metrics in any UAV application. This weight versus strength conundrum has often forced compromises using conventional manufacturing methods like CNC machining or injection molding.
However, the advent of impresión 3D en metal, also known as metal additive manufacturing (AM), offers a transformative solution. This technology allows for the creation of highly complex, lightweight, yet strong metal enclosures that were previously impossible or prohibitively expensive to manufacture. By building parts layer by layer directly from digital designs using advanced metal powders like Aluminum alloys (AlSi10Mg and A6061 being prime examples), metal AM unlocks unprecedented design freedom. Engineers can now integrate advanced features such as topology-optimized geometries, internal lattice structures, conformal cooling channels, and consolidated assemblies – all contributing to significant weight reduction without sacrificing performance or protection.
This shift is particularly impactful for B2B suppliers, manufacturers, and procurement managers in sectors demanding high-performance UAV components, including:
- Aeroespacial y defensa: Requiring rugged, reliable, and often custom enclosures for ISR (Intelligence, Surveillance, Reconnaissance) sensors, communication links, and electronic warfare (EW) payloads.
- Automotive (Testing & Development): Utilizing UAVs for various testing scenarios where specialized sensor protection is needed.
- Medical (Delivery & Logistics): Exploring UAVs for time-sensitive deliveries requiring secure and potentially climate-controlled payload compartments.
- Industrial Manufacturing & Inspection: Deploying drones equipped with thermal cameras, LiDAR scanners, or NDT sensors for asset monitoring and quality control.
- Commercial Surveying & Mapping: Integrating high-resolution cameras and geospatial sensors demanding stable, vibration-dampened enclosures.
Companies like Met3dp are at the forefront of this technological revolution, providing not only state-of-the-art metal Impresión 3D systems like Selective Electron Beam Melting (SEBM) but also producing high-quality, application-optimized metal powders such as AlSi10Mg and A6061. Leveraging decades of collective expertise, Met3dp partners with organizations to harness the full potential of metal AM, transforming the design and production of critical components like UAV payload enclosures. This blog post will delve deep into the world of metal 3D printed UAV payload enclosures, exploring their applications, the advantages of using AM, the optimal materials, design considerations, quality aspects, and how to partner with the right service provider to elevate your UAV systems’ performance and mission capabilities. Whether you are an engineer designing the next generation of UAVs or a procurement manager sourcing high-quality, lightweight components, understanding the potential of metal AM is crucial for staying competitive.
Defining UAV Payload Enclosures: Critical Components for Unmanned Systems Protection and Performance
The payload enclosure is an integral, mission-critical component of any sophisticated UAV system. While the airframe provides the primary structure and propulsion systems enable flight, the enclosure serves as the dedicated housing and protective shell for the valuable payload elements. Its design and material composition directly influence the UAV’s overall performance, reliability, and mission success rate. Simply put, without a properly designed enclosure, the expensive and sensitive payload is vulnerable to damage or malfunction, rendering the entire UAV mission ineffective.
Core Functions of a UAV Payload Enclosure:
The role of a payload enclosure extends far beyond simple containment. It performs several vital functions simultaneously:
- Structural Support & Integration: Provides secure mounting points for the payload elements (sensors, cameras, PCBs, antennas) and integrates them seamlessly with the UAV airframe. It must withstand the static and dynamic loads experienced during flight, takeoff, and landing.
- Environmental Protection: Shields the payload from a range of environmental hazards:
- Moisture & Humidity: Prevents water ingress from rain, fog, or condensation, which can cause short circuits or corrosion. Sealing strategies (gaskets, conformal coatings) are often designed in conjunction with the enclosure.
- Dust & Particulates: Keeps fine particles from infiltrating sensitive optical or electronic components, particularly important in industrial, agricultural, or desert environments.
- Temperature Extremes: Protects components from overheating due to internal electronics or external solar radiation, and from performance degradation or failure in extreme cold. Thermal management features are often integrated.
- Pressure Differentials: Maintains integrity during rapid changes in altitude.
- Gestión térmica: Facilitates the dissipation of heat generated by the payload electronics. This can involve passive methods (heat sinks integrated into the enclosure walls, high thermal conductivity materials) or active methods (air vents, cooling channels for forced air or liquid cooling), often enabled by the design freedom of metal AM.
- Electromagnetic Compatibility (EMC): Provides EMI/RFI shielding to protect sensitive payload electronics from external electromagnetic interference (e.g., radar, communication signals) and to prevent the payload itself from interfering with the UAV’s own navigation and communication systems. Metal enclosures inherently offer good shielding properties, which can be further optimized through design and material choice.
- Impact & Vibration Resistance: Protects the payload from shocks, vibrations, and G-forces encountered during turbulent flight, hard landings, or transportation. The enclosure’s structural design and material dampening properties are crucial. Metal AM allows for integrated dampening structures or optimized ribbing for stiffness.
- Security & Tamper Resistance: In defense or high-security applications, the enclosure may need to provide a degree of tamper evidence or resistance.
Types of Payloads Housed:
The specific design of an enclosure is heavily influenced by the type of payload it needs to accommodate. Common examples include:
- Imaging Systems:
- Electro-Optical (EO) Cameras (Visible spectrum, high resolution)
- Infrared (IR) / Thermal Cameras
- Multispectral / Hyperspectral Cameras
- LiDAR (Light Detection and Ranging) Systems
- Sensors:
- Gas Detectors (Methane, CO, Volatiles)
- Environmental Sensors (Temperature, Humidity, Pressure)
- Radiation Sensors
- Magnetic Sensors (Magnetometers)
- Acoustic Sensors
- Communication Equipment:
- Antennas (Directional, Omni-directional)
- Transponders (ADS-B)
- Data Links & Modems
- Satellite Communication (SATCOM) Terminals
- Specialized Instrumentation:
- Scientific measurement devices
- Sampling equipment
- Small manipulators or delivery mechanisms
Industry Applications & Requirements:
The demands placed on UAV payload enclosures vary significantly depending on the industry and specific application. B2B suppliers and manufacturers must cater to these diverse needs:
Sector industrial | Typical Payloads Housed | Key Enclosure Requirements | B2B Keywords |
---|---|---|---|
Aeroespacial y defensa | ISR sensors, targeting pods, SIGINT/ELINT, communication relays, EW packages | Extreme ruggedness, high reliability (MIL-STD), EMI/RFI shielding, thermal management, low observability (sometimes), custom designs | Defense UAV enclosure supplier, Military drone parts manufacturer, ISR payload housing |
Commercial Surveying | High-res cameras, LiDAR scanners, GNSS receivers | High stability, vibration damping, precise mounting, environmental sealing (IP rating), light weight | Surveying drone component wholesale, LiDAR enclosure manufacturer, Mapping UAV parts |
Agricultura | Multispectral cameras, environmental sensors, spray nozzles | Environmental sealing (dust, moisture, chemicals), light weight, cost-effectiveness, durability | Precision agriculture drone parts, Ag drone component supplier |
Infrastructure Inspection | Thermal cameras, high-zoom EO cameras, ultrasonic sensors | Durability, environmental sealing, thermal management, precise sensor alignment, potential for impact resistance | Inspection UAV parts distributor, Thermal camera drone enclosure |
Energy (Oil & Gas/Wind) | Gas detectors, thermal cameras, visual inspection cameras | Intrinsic safety (potentially), chemical resistance, robust environmental sealing, thermal management | Oil & Gas drone component supplier, Wind turbine inspection UAV parts |
Emergency Services/SAR | EO/IR cameras, communication equipment, small drop mechanisms | Reliability, rapid deployment, ease of integration, moderate ruggedness, light weight | SAR drone enclosure manufacturer, Public safety UAV component wholesale |
Logística y Entrega | Secure compartments, potentially climate-controlled | Security features, insulation (if needed), light weight, aerodynamic efficiency, durability for repeated use | Drone delivery pod supplier, UAV logistics component manufacturer |
Exportar a hojas
Understanding these diverse functional requirements and industry-specific demands is crucial for designing and manufacturing effective UAV payload enclosures. Metal additive manufacturing provides the technological capability to meet these often-conflicting requirements – achieving robustness, complex functionality, environmental resistance, and critical weight savings simultaneously – making it an increasingly vital technology for UAV component suppliers and manufacturers aiming to serve these demanding B2B markets.
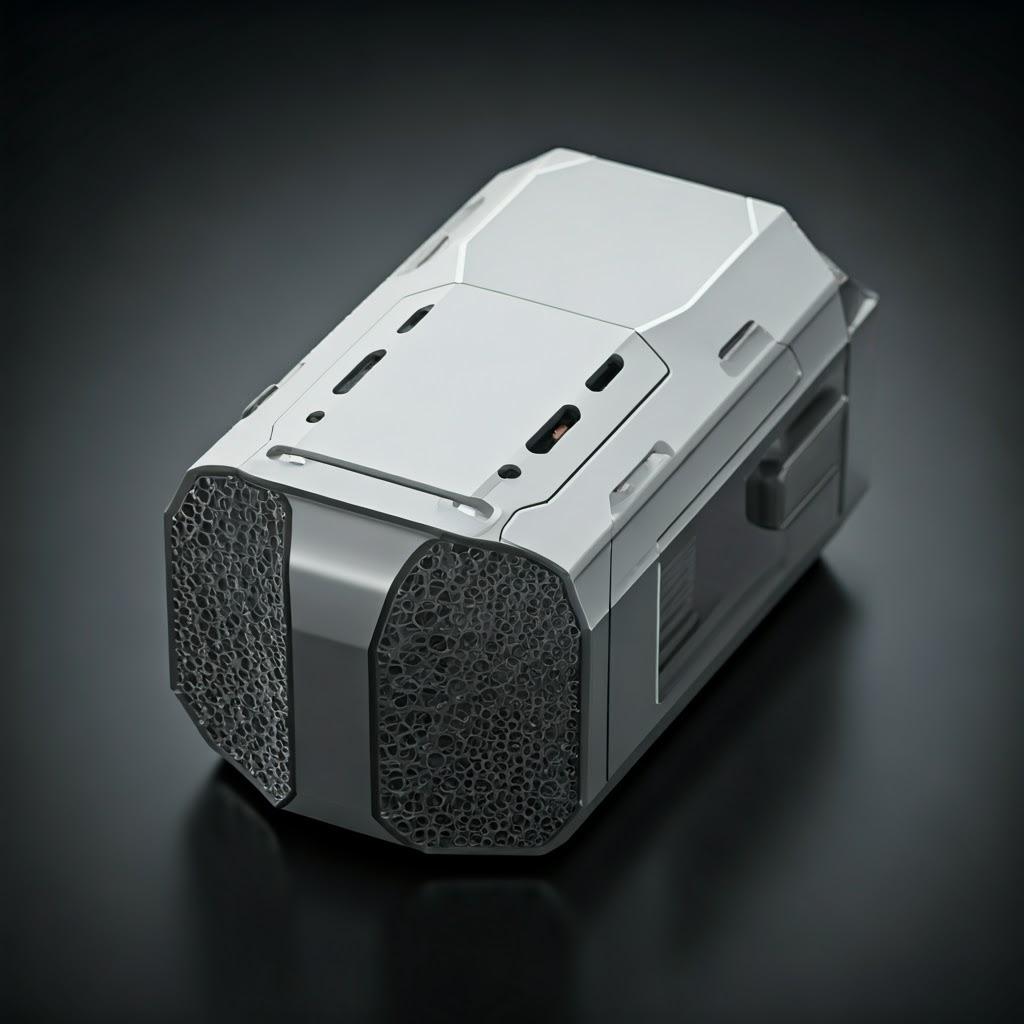
Why Metal 3D Printing is Revolutionizing UAV Enclosure Design and Manufacturing
The shift towards metal additive manufacturing for UAV payload enclosures isn’t just an alternative production method; it represents a fundamental paradigm shift in how these critical components are designed, optimized, and produced. Traditional manufacturing techniques like CNC machining, sheet metal fabrication, and injection molding, while mature and suitable for many applications, often impose significant constraints, particularly when dealing with the unique challenges of UAV design – namely the relentless pursuit of lower weight and higher performance. Metal AM directly addresses these limitations, offering compelling advantages that are driving its adoption among leading UAV manufacturers and B2B component suppliers.
Overcoming Traditional Manufacturing Constraints:
- Mecanizado CNC: While capable of high precision and good surface finishes, CNC machining is a subtractive process. It starts with a solid block of material and removes excess, often leading to significant material waste, especially for complex or hollowed-out geometries typical of lightweight enclosures. Achieving complex internal features or undercuts can require multiple setups, specialized tooling, and long machining times, increasing costs. Thin walls, critical for weight saving, can be challenging to machine without distortion.
- Sheet Metal Fabrication: Suitable for simpler box-like enclosures, sheet metal involves cutting, bending, and joining metal sheets. It’s generally cost-effective for basic shapes but struggles with complex curves, integrated features (like heat sinks or complex mounting bosses), and achieving high levels of environmental sealing without additional complex gaskets or welding. Structural rigidity often requires thicker gauges or reinforcing elements, adding weight.
- Injection Molding (Metals – MIM): Metal Injection Molding can produce complex parts in high volumes but requires extremely expensive tooling (molds). This makes it uneconomical for the low-to-medium volume production runs typical of specialized UAV payloads or for prototyping and design iteration. The process also involves binders that need to be removed and subsequent sintering, which can introduce dimensional variability.
- Reparto: While capable of complex shapes, casting often results in lower material properties compared to wrought or AM materials and may require significant post-machining for critical tolerances. Porosity can be a concern, and tooling costs are substantial, limiting its use for custom or low-volume UAV parts.
The Transformative Advantages of Metal Additive Manufacturing:
Metal AM processes, such as Selective Laser Melting (SLM), Direct Metal Laser Sintering (DMLS), and Selective Electron Beam Melting (SEBM) – a technology where Met3dp holds significant expertise – build parts layer-by-layer from fine metal powder, offering distinct advantages for UAV enclosures:
- Unparalleled Design Freedom & Complexity: AM removes many traditional manufacturing constraints. Engineers can design highly organic shapes, intricate internal channels for cooling or wiring, thin walls with complex stiffening ribs, and integrated mounting features precisely where needed. This allows for designs dictated by functional requirements rather than manufacturing limitations.
- Massive Weight Reduction Potential: This is arguably the most significant benefit for UAVs. Metal AM enables:
- Optimización de la topología: Software algorithms remove material from non-critical areas, leaving load-bearing structures optimized for maximum strength-to-weight ratio. This results in organic, skeletal-looking parts that are significantly lighter but just as strong.
- Estructuras reticulares: Internal lattice or gyroid structures can fill volumes, providing excellent stiffness and energy absorption at a fraction of the weight of solid material. These are virtually impossible to create with traditional methods.
- Thin-Walled Designs: AM allows for the creation of very thin, yet structurally sound walls (down to sub-millimeter, depending on material and design), directly reducing component mass.
- Consolidación de piezas: Complex assemblies previously made from multiple individual components (e.g., a housing, brackets, heat sink, fasteners) can often be redesigned and printed as a single, monolithic part. This dramatically reduces:
- Peso: Eliminates fasteners (screws, rivets) and joining interfaces.
- Assembly Time & Cost: Simplifies the manufacturing workflow.
- Potential Failure Points: Fewer joints mean higher structural integrity and reliability.
- Supply Chain Complexity: Fewer individual part numbers to manage and source.
- Creación rápida de prototipos e iteración: AM allows engineers to move from a digital design to a physical metal prototype in days rather than weeks or months (associated with tooling for molding/casting or complex CNC setups). This accelerates design validation, functional testing, and optimization cycles, leading to better final products developed faster. Multiple design variations can be tested concurrently.
- Customization and Low-Volume Production: AM is inherently tool-less. This makes it economically viable to produce highly customized enclosures tailored to specific payload dimensions, mounting requirements, or thermal profiles, even for single units or small batches. This is ideal for specialized UAVs, prototypes, or adapting existing platforms for new missions – a key advantage for B2B suppliers offering bespoke solutions.
- Rendimiento del material: Metal AM processes, when properly controlled using high-quality powders like those produced by Met3dp using advanced gas atomization, can create fully dense parts with mechanical properties comparable or even superior to cast or sometimes wrought equivalents, especially after appropriate post-processing like heat treatment. Alloys like AlSi10Mg and A6061 offer excellent performance characteristics suitable for demanding aerospace applications.
- Reducción de los residuos materiales: As an additive process, AM uses only the material needed to build the part and its supports, resulting in significantly less waste compared to subtractive CNC machining, which can generate substantial scrap material (chips). This improves material efficiency and contributes to sustainability.
Comparison Summary: AM vs. Traditional for UAV Enclosures
Característica | Metal Additive Manufacturing (SLM/DMLS/SEBM) | Mecanizado CNC | Sheet Metal Fabrication | Injection Molding (MIM) | Fundición |
---|---|---|---|---|---|
Complejidad geométrica | Very High (Internal features, lattices, organic) | High (Limited by tool access) | Low (Primarily 2.5D shapes) | Alta | Alta |
Reducción de peso | Excellent (Topology opt., lattices, thin walls) | Moderate (Pocketing) | Limitado | Moderado | Moderado |
Consolidación de piezas | Excelente | Limitado | Pobre | Bien | Bien |
Coste de utillaje | Ninguno | Low (Fixturing) | Low (Dies for high vol.) | Very High (Molds) | High (Patterns/Molds) |
Plazo de entrega (Proto) | Fast (Days) | Moderate (Days/Weeks) | Moderado | Very Slow (Months – tooling) | Slow (Weeks/Months – tooling) |
Optimal Volume | Low to Medium, Custom | Low to High | Media a alta | Muy alta | Media a alta |
Residuos materiales | Low (Powder recycling possible) | Alta | Moderado | Bajo | Moderado |
Personalización | Excelente | Good (Requires reprogramming) | Pobre | Very Poor | Pobre |
Exportar a hojas
In conclusion, metal 3D printing offers a compelling value proposition for manufacturers and suppliers of UAV payload enclosures. It directly addresses the critical need for lightweighting while enabling unprecedented design complexity, part consolidation, and customization. While traditional methods retain their place, particularly for very high volumes of simple parts, metal AM is rapidly becoming the technology of choice for high-performance, mission-critical UAV components where weight savings and optimized functionality are paramount. Companies investing in robust AM capabilities, from advanced printers to high-quality powder production like Met3dp, are well-positioned to lead the market for next-generation UAV systems.
Optimal Metal Powders for UAV Enclosures: AlSi10Mg and A6061 Deep Dive
The success of metal additive manufacturing relies heavily on the quality and properties of the raw material: the fine metal powder feedstock. For UAV payload enclosures, where the primary drivers are low weight, sufficient strength, thermal conductivity, and environmental resistance, aluminum alloys are often the materials of choice. Among the most widely used and proven aluminum alloys for AM processes like SLM and DMLS are AlSi10Mg and A6061. Understanding their distinct characteristics is crucial for selecting the right material to meet specific enclosure performance requirements.
Choosing the optimal powder goes beyond just the alloy type; it involves considering powder characteristics influenced by the production method. Met3dp utilizes industry-leading techniques like Vacuum Induction Melting Gas Atomization (VIGA) and Plasma Rotating Electrode Process (PREP) to produce polvos metálicos de alta calidad. These advanced methods ensure:
- Esfericidad alta: Smooth, spherical powder particles flow easily and pack densely in the powder bed, leading to more uniform layers and predictable melting behavior. This results in parts with higher density and better mechanical properties.
- Low Porosity: Minimizing internal pores within the powder particles reduces the risk of porosity in the final printed part.
- Controlled Particle Size Distribution (PSD): A specific range of particle sizes optimized for the AM process (e.g., SLM typically uses 15-53 µm) ensures good flowability and resolution.
- Alta pureza: Minimizing contaminants and controlling oxygen/nitrogen content is critical for achieving desired material properties and preventing defects during printing.
Met3dp’s commitment to advanced powder manufacturing ensures that engineers and procurement managers have access to reliable, high-performance feedstock for demanding applications like UAV enclosures.
AlSi10Mg: The Workhorse for Complex Geometries
- Composición: Primarily Aluminum (Al), with approximately 9-11% Silicon (Si) and 0.2-0.45% Magnesium (Mg). It is essentially an aluminum casting alloy adapted for additive manufacturing.
- Key Properties & Characteristics:
- Excelente imprimibilidad: The high silicon content gives AlSi10Mg fluidity characteristics similar to casting alloys, making it relatively easy to process with SLM/DMLS. It allows for the reliable creation of fine features, thin walls, and complex geometries with minimal cracking susceptibility during printing.
- Buena relación resistencia-peso: Offers a good balance of strength and low density (approx. 2.67 g/cm³), making it ideal for lightweight structural components. Its properties are often compared to A360 cast aluminum.
- Good Thermal Conductivity: Suitable for enclosures requiring passive heat dissipation from internal electronics (approx. 130-150 W/m·K).
- Buena resistencia a la corrosión: Performs well in typical atmospheric conditions.
- Tratable térmicamente: Mechanical properties can be significantly enhanced through stress relief annealing or T6 heat treatment (solutionizing + artificial aging), increasing yield strength and ultimate tensile strength, although typically reducing elongation (ductility).
- Advantages for UAV Enclosures:
- Ideal for highly complex, topology-optimized designs with intricate features or internal lattice structures.
- Cost-effective choice for enclosures where moderate strength is sufficient.
- Suitable for parts requiring integrated heat sinking features.
- Proven track record in AM applications.
- Limitaciones:
- Lower ductility and fracture toughness compared to A6061, especially in the as-built state. May not be suitable for enclosures subjected to very high impact loads or requiring significant deformation before failure.
- Mechanical properties can be slightly lower than optimized wrought alloys.
- Met3dp Expertise: Met3dp produces high-sphericity, high-purity AlSi10Mg powder optimized for laser powder bed fusion processes, ensuring consistent printing results and dense, high-quality parts suitable for aerospace and industrial UAV applications.
A6061: The Choice for Higher Strength and Toughness
- Composición: Primarily Aluminum (Al), alloyed with Magnesium (Mg, approx. 0.8-1.2%), Silicon (Si, approx. 0.4-0.8%), Copper (Cu, approx. 0.15-0.4%), and Chromium (Cr, approx. 0.04-0.35%). This composition is closer to traditional wrought 6061 aluminum.
- Key Properties & Characteristics:
- Higher Strength & Toughness: Especially after T6 heat treatment, A6061 typically exhibits higher yield strength, ultimate tensile strength, and significantly better elongation (ductility) and fracture toughness compared to AlSi10Mg. This makes it more resistant to fatigue and impacts.
- Buena resistencia a la corrosión: Similar to AlSi10Mg.
- Excelente maquinabilidad: Post-print machining for critical tolerances or features is generally easier than with AlSi10Mg.
- Buena soldabilidad: Although less relevant for monolithic AM parts, it indicates good material joining characteristics.
- Moderate Printability: While printable, A6061 can be more challenging to process via AM than AlSi10Mg. It requires carefully controlled parameters to avoid issues like solidification cracking due to its wider freezing range. Advances in machine parameters and powder quality have significantly improved its processability.
- Tratable térmicamente: Requires T6 heat treatment to achieve its optimal mechanical properties, significantly boosting strength and hardness.
- Advantages for UAV Enclosures:
- Suitable for structural enclosures requiring higher load-bearing capacity, fatigue resistance, or impact tolerance.
- Better choice when significant post-machining is anticipated.
- Provides properties closer to traditionally manufactured 6061 parts, simplifying qualification in some cases.
- Limitaciones:
- Can be more challenging and potentially more expensive to print reliably than AlSi10Mg, especially for very intricate geometries or thin features.
- Achieving optimal properties absolutely requires proper heat treatment, adding a necessary post-processing step.
- Met3dp Capability: Met3dp possesses the expertise and advanced powder production capabilities (like VIGA and PREP) to manufacture high-quality A6061 powder suitable for AM, addressing the process challenges and enabling customers to leverage the superior mechanical properties of this alloy for demanding structural UAV components.
Comparison Table: AlSi10Mg vs. A6061 for AM UAV Enclosures
Propiedad | AlSi10Mg (Typical AM, Heat Treated) | A6061 (Typical AM, T6 Heat Treated) | Notes for UAV Enclosures |
---|---|---|---|
Densidad | ~2,67 g/cm³ | ~2,70 g/cm³ | Very similar, both excellent for lightweighting. |
Printability / Complexity | Excelente | Good / Moderate | AlSi10Mg preferred for highly intricate designs, thin walls, fine features. A6061 printability improving but may require more careful design/processing. |
Límite elástico (0,2%) | ~230-290 MPa | ~240-300 MPa | A6061 generally slightly higher after proper T6 treatment. |
Resistencia a la tracción | ~360-440 MPa | ~290-340 MPa | Varies significantly with heat treatment; consult specific datasheets. A6061 can be competitive. [Self-correction: Initial values might be off, check typical AM data. A6061 often shows UTS ~310MPa, YS ~275MPa after T6. AlSi10Mg YS ~250MPa, UTS ~400MPa after T6. A6061 generally higher YS, AlSi10Mg higher UTS but less ductile] Let’s refine: A6061-T6 often has better YS/UTS combination with ductility. |
Yield Strength (0.2%) – Refined | ~230-280 MPa | ~250-290 MPa | A6061 typically achieves comparable or slightly higher yield strength post-T6. |
Ultimate Tensile Strength – Refined | ~330-430 MPa | ~290-330 MPa | AlSi10Mg can achieve higher UTS, but often at the expense of ductility. |
Alargamiento a la rotura | ~3-10% | ~8-15% | A6061 generally offers significantly better ductility/toughness, crucial for impact resistance and fatigue life. |
Conductividad térmica | ~130-150 W/m·K | ~150-180 W/m·K | Both good, A6061 slightly better for heat dissipation. |
Resistencia a la corrosión | Bien | Bien | Similar performance in typical environments. |
Maquinabilidad | Feria | Excelente | A6061 is preferred if significant post-machining is required. |
Tratamiento térmico | Recommended (Stress Relief or T6) | Required (T6 for optimal props) | An essential consideration for process planning and cost. |
Mejores casos de uso | Complex geometries, heat sinks, moderate loads, cost-sensitive parts | Structural parts, higher impact/fatigue loads, parts requiring significant post-machining | Select based on primary performance driver (complexity vs. toughness). |
Exportar a hojas
Choosing the Right Powder Supplier:
For procurement managers and engineers sourcing materials or services, partnering with a knowledgeable supplier is key. Look for:
- Powder Quality & Consistency: Certification of powder chemistry, sphericity, PSD, and low contamination levels. Ask about the atomization process used (e.g., VIGA, PREP).
- Experiencia en materiales: Ability to provide detailed datasheets for as-built and heat-treated properties specific to their powder and recommended process parameters.
- Process Support: Guidance on optimal printing parameters and required post-processing (like heat treatment schedules) for their powders.
- Reliable Supply Chain: Consistent availability and batch-to-batch traceability.
Met3dp, with its vertically integrated approach encompassing both advanced powder production and SEBM printing technology, embodies these qualities, offering high-quality AlSi10Mg and A6061 powders backed by deep expertise in metal additive manufacturing. Selecting the right aluminum alloy, sourced from a reputable supplier like Met3dp, is a critical first step in leveraging metal AM to produce lightweight, high-performance enclosures that meet the demanding requirements of modern UAV systems.
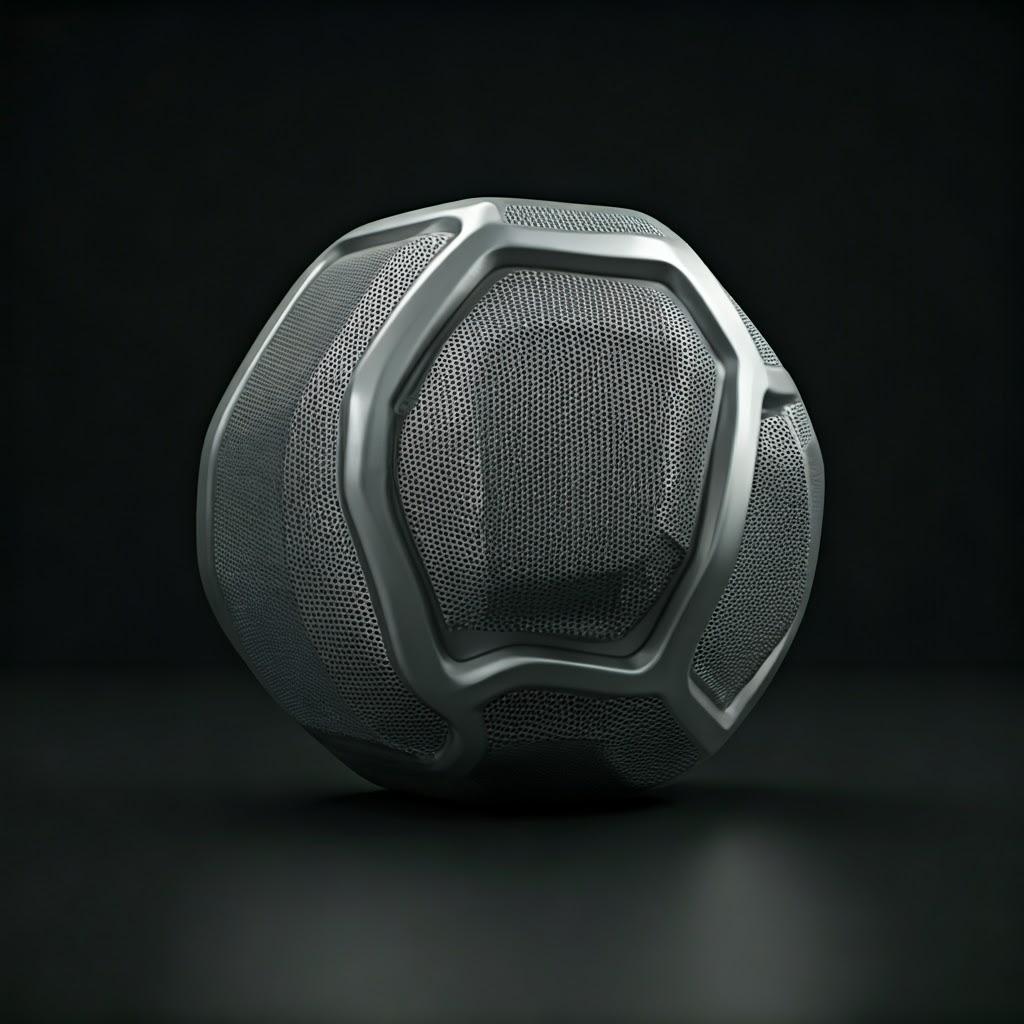
Design for Additive Manufacturing (DfAM) Principles for High-Performance UAV Payload Enclosures
Transitioning to metal additive manufacturing for UAV payload enclosures requires more than simply taking a design intended for CNC machining or casting and sending it to a 3D printer. To truly unlock the transformative benefits of AM – significant weight reduction, enhanced performance through complex geometries, and consolidated assemblies – engineers must embrace Design for Additive Manufacturing (DfAM). DfAM is a methodology that involves designing components specifically considering the capabilities, constraints, and nuances of the chosen AM process (like SLM, DMLS, or SEBM) and material (like AlSi10Mg or A6061). Failing to apply DfAM principles often leads to suboptimal results: parts that are unnecessarily heavy, difficult to print successfully, require excessive post-processing, or fail to leverage the unique advantages AM offers. For B2B suppliers and manufacturers aiming to deliver cutting-edge, lightweight UAV enclosures, mastering DfAM is not just beneficial; it’s essential for competitive differentiation.
Why is DfAM so critical? Metal AM builds parts layer by layer, fusing fine powder particles with a high-energy source (laser or electron beam). This process has unique physical characteristics related to heat transfer, solidification, residual stress buildup, and the need for support structures, all of which must be considered during the design phase. Effective DfAM proactively addresses these factors, leading to parts that are:
- Optimized for Function: Meeting or exceeding performance requirements (strength, stiffness, thermal management, RF shielding).
- Ligero: Maximizing weight savings through topology optimization, lattice structures, and thin-walled designs.
- Printable: Ensuring the design can be reliably manufactured with minimal risk of build failures (warping, cracking, collapse).
- Efficiently Post-Processed: Minimizing the need for and difficulty of removing support structures and performing finishing operations.
- Rentable: Reducing material consumption, build time, and post-processing labor.
Key DfAM Principles for Metal AM UAV Enclosures:
- Strategic Build Orientation:
- Impacto: The orientation of the enclosure on the build platform significantly influences support structure requirements, surface finish quality on different faces, dimensional accuracy (due to thermal gradients and shrinkage), build time (height is a major factor), and potentially anisotropic material properties (though less pronounced in metals compared to polymers, slight variations can exist).
- Considerations for Enclosures:
- Critical Surfaces: Orient the part so that critical functional surfaces (e.g., sealing faces, mounting interfaces intended for post-machining, aerodynamically sensitive exteriors) are either self-supporting (facing upwards) or oriented vertically for better finish and accuracy. Downward-facing surfaces supported by structures will inevitably have lower surface quality.
- Support Minimization: Choose an orientation that minimizes the volume and complexity of required support structures, especially in hard-to-reach internal areas.
- Gestión térmica: Consider how orientation affects heat buildup and dissipation during the build. Tall, thin features are more susceptible to thermal stresses.
- Recotaer Interaction: Ensure the orientation doesn’t present features that could interfere with the powder recoating mechanism during the build.
- Contrapartidas: Often, optimizing for one factor (e.g., minimizing supports) might negatively impact another (e.g., surface finish on a key face). Careful analysis and simulation are often required to find the best compromise.
- Intelligent Support Structure Design & Minimization:
- Necesidad: Metal AM processes require support structures primarily for two reasons: anchoring the part to the build plate and supporting overhanging features or bridges that would otherwise collapse or distort due to gravity and thermal stresses before solidifying.
- Desafíos: Supports consume extra material, increase build time, require significant effort to remove (often manually), and leave witness marks or rougher surfaces where they connect to the part.
- DfAM Strategies:
- Maximize Self-Supporting Angles: Design overhangs to be less severe than the critical angle (typically around 45° from the horizontal for many metal AM processes/materials, though this varies). Features steeper than this generally don’t require support.
- Use Fillets and Chamfers: Gradually transitioning overhangs using fillets or chamfers instead of sharp 90-degree angles can often make them self-supporting. Chamfers are often preferred as they create planar surfaces that print well.
- Design for Support Removal: If supports are unavoidable, ensure adequate access for tools to remove them. Avoid placing supports in deep, enclosed internal cavities where removal is impossible.
- Características de sacrificio: Incorporate features designed to be machined away later, which can also serve as supports during the build.
- Leverage Part Geometry: Sometimes, features like internal ribs or channels can be designed to provide support for other sections of the part.
- Feature Design & Dimensional Considerations:
- Espesor mínimo de pared: AM can produce very thin walls, crucial for lightweighting enclosures. However, there’s a practical limit based on the material, machine resolution, and thermal stability. For AlSi10Mg/A6061 using typical laser powder bed fusion, this might be around 0.4-0.8 mm, but thicker walls (1mm+) are generally more robust and easier to print reliably. Consult your AM provider (like Met3dp) for specific guidelines based on their equipment and process parameters.
- Minimum Hole/Channel Diameter: Small holes (both vertical and horizontal) can be challenging. Very small vertical holes might seal themselves shut due to melt pool dynamics. Horizontal holes inherently form an overhang and require support or specific shaping (e.g., teardrop or diamond shape) to be self-supporting below a certain diameter (often a few mm). Trapped powder removal is also a concern for blind holes or long, narrow channels.
- Tamaño mínimo de característica: Very small pins, bosses, or lettering may not resolve properly. Again, consult provider guidelines (often >0.5mm).
- Stress Concentrations: Avoid sharp internal corners; use generous fillet radii to distribute stress, improving fatigue life and reducing cracking risk during printing and service.
- Eliminación del polvo: For enclosures with internal cavities or channels, design in escape holes at strategic locations to allow unfused powder to be removed after the build.
- Leveraging Topology Optimization & Lattice Structures:
- Optimización de la topología: Use FEA-based software to analyze the load paths within the enclosure and remove material from areas that don’t contribute significantly to stiffness or strength. This generates organic, highly efficient structures that maintain performance while drastically reducing weight – ideal for UAV components. The resulting complex shapes are often only manufacturable via AM.
- Estructuras reticulares: Replace solid volumes with internal periodic lattice structures (e.g., cubic, octet-truss, gyroid). These offer excellent stiffness-to-weight ratios, energy absorption (good for vibration damping or impact protection), and increased surface area (potentially beneficial for passive thermal management). They are uniquely enabled by AM. Design considerations include cell size, beam/wall thickness, and ensuring powder can be removed from the lattice.
- Embracing Part Consolidation:
- Mindset Shift: Instead of designing an assembly of multiple simple parts (e.g., housing shells, mounting brackets, stiffening ribs, heat sink) that will be joined later, actively look for opportunities to combine these elements into a single, monolithic AM component.
- Benefits Revisited: Reduces part count, eliminates fasteners and joints (reducing weight and failure points), simplifies assembly, shortens supply chains.
- Examples for Enclosures: Integrate mounting bosses directly into the housing walls; design snap-fit features (use with caution in metals); combine a structural element with a complex heat sink geometry; incorporate conformal channels for wiring or cooling directly within the enclosure walls.
- Integrating Thermal Management Features:
- Payload Heat: Many UAV payloads generate significant heat that must be managed to ensure operational reliability.
- AM Capabilities: Design complex, high-surface-area heat sink fins directly integrated into the enclosure exterior or interior. Create conformal cooling channels precisely following heat sources for targeted air or liquid cooling, impossible with traditional methods. Optimize wall thickness and material selection (AlSi10Mg/A6061 have good thermal conductivity) for efficient heat transfer paths.
- Designing for Post-Processing:
- Anticipate Needs: Recognize that post-processing (support removal, heat treatment, machining, finishing) is part of the workflow.
- Consideraciones sobre el diseño:
- Support Access: Ensure clear line-of-sight and physical access for support removal tools.
- Material de mecanizado: Add extra material (e.g., 0.5-1.0 mm) specifically on surfaces that require tight tolerances, specific flatness, or smooth finishes via CNC machining after printing. Clearly indicate these surfaces on drawings.
- Heat Treatment Fixturing: Consider how the part will be fixtured during heat treatment to minimize distortion. Add locating features if necessary.
- Handling Features: Incorporate features that aid in handling the part during various post-processing steps.
DfAM Implementation:
Successfully implementing DfAM requires collaboration between design engineers, manufacturing engineers, and the AM service provider. Utilizing CAD software with integrated simulation, topology optimization, and lattice generation tools is crucial. Partnering with an experienced AM provider like Met3dp, who understands the nuances of their métodos de impresión and materials (AlSi10Mg, A6061), can provide invaluable feedback during the design phase, ensuring the final enclosure design is optimized for performance, weight, manufacturability, and cost. Iterative design reviews focusing on DfAM principles are key to maximizing the potential of metal AM for demanding UAV applications.
Achieving Precision: Tolerances, Surface Finish, and Dimensional Accuracy in 3D Printed Enclosures
When engineers and procurement managers consider metal additive manufacturing for critical components like UAV payload enclosures, questions surrounding achievable precision are paramount. Can metal AM meet the required dimensional tolerances? What kind of surface finish can be expected? How accurate will the final part be compared to the original CAD model? Understanding the capabilities and limitations of metal AM processes (SLM, DMLS, SEBM) in terms of accuracy, tolerances, and surface finish is essential for setting realistic expectations and designing parts appropriately. While metal AM offers incredible geometric freedom, it typically does not match the out-of-the-box precision of high-end CNC machining across all dimensions and surfaces, often necessitating a combination of AM and subtractive finishing for optimal results.
Precisión dimensional:
- Definición: How closely the dimensions of the printed part match the nominal dimensions specified in the digital CAD file.
- Valores típicos: For well-controlled industrial metal AM systems, like those developed by Met3dp focused on reliability and precision, general achievable accuracy is often cited in the range of:
- ± 0.1 mm to ± 0.2 mm for small features (e.g., up to 50-100 mm).
- ± 0.1% to ± 0.2% of the nominal dimension for larger features.
- Nota: These are general guidelines and can vary significantly. Always consult with the AM provider for machine- and material-specific data.
- Factores que influyen en la precisión:
- Calibración de la máquina: Precise laser/electron beam positioning, scanning speed, and layer thickness control are crucial. Regular calibration is essential.
- Propiedades del material: Each alloy (like AlSi10Mg or A6061) has specific thermal expansion and contraction characteristics during melting and solidification, leading to shrinkage that must be compensated for in the build preparation software. Inconsistent powder properties can affect accuracy.
- Thermal Stresses: Uneven heating and cooling during the layer-by-layer process induce internal stresses. These can cause warping or distortion, especially in large or geometrically complex parts, affecting final dimensions.
- Geometría y tamaño de la pieza: Larger parts and complex geometries with varying cross-sections are generally more prone to thermal distortion.
- Orientación de construcción: Orientation affects heat distribution and support needs, influencing accuracy.
- Estrategia de apoyo: Inadequate or poorly placed supports can allow the part to shift or warp during the build.
- Post-procesamiento: Stress relief and heat treatment cycles can cause further dimensional changes (shrinkage or distortion) that need to be predicted and accounted for, often requiring specialized fixtures. Part removal from the build plate can also release stresses.
Tolerances:
- As-Built Tolerances: The dimensional range achievable directly from the AM process without secondary machining. Based on the accuracy figures above, as-built tolerances are typically suitable for non-critical features or surfaces where ±0.1mm or ±0.2% is acceptable.
- Achieving Tighter Tolerances: For features requiring higher precision – such as:
- Mounting interfaces connecting to the airframe or payload.
- Sealing surfaces for environmental protection (e.g., O-ring grooves).
- Bearing or shaft fits.
- Precise alignment features for optical payloads. – post-print CNC machining is almost always required.
- Designing for Machining: It is standard DfAM practice to design critical features slightly oversized (adding ‘machining stock’ or ‘green stock’, typically 0.5 mm to 1.5 mm) in the AM design file. This extra material is then precisely removed via CNC milling, turning, or grinding to achieve final tolerances, which can be as tight as ±0.01 mm or better, depending on the machining process. Clearly identifying these critical dimensions and surfaces on engineering drawings is essential communication for the manufacturing process.
Acabado superficial (rugosidad):
- Superficie as-built: Metal AM parts inherently have a rougher surface finish compared to machined or polished surfaces. This is due to:
- Layer Lines: The nature of the layer-by-layer construction creates visible steps on curved or angled surfaces.
- Partially Melted Particles: Some powder particles may adhere loosely to the surface without being fully melted, contributing to roughness.
- Efecto Escalera: On shallow angles, the approximation of the curve by discrete layers becomes more pronounced.
- Typical Ra Values: Surface roughness (Ra – arithmetic average roughness) for as-built metal AM parts typically ranges from 5 µm to 25 µm (or roughly 200 to 1000 µin).
- Factors Influencing As-Built Ra:
- Orientación:
- Top Surfaces: Generally have the lowest Ra as they are the last layer melted.
- Vertical Walls: Tend to have intermediate Ra, showing layer lines.
- Up-Facing Angled Surfaces: Ra increases as the angle relative to the build plate decreases (more pronounced stair-stepping).
- Down-Facing Surfaces (Supported): Typically have the highest Ra due to contact with support structures, which leave witness marks upon removal.
- Parámetros del proceso: Laser/electron beam power, scan speed, layer thickness, and beam focus influence the melt pool characteristics and resulting surface texture.
- Características del polvo: Particle size distribution and morphology affect packing density and melting behavior. High-quality spherical powders, like those from Met3dp, contribute to better surface finish.
- Orientación:
- Mejora del acabado superficial: While the as-built finish is suitable for many internal features or non-critical surfaces of a UAV enclosure, smoother finishes are often required for sealing, aerodynamics, aesthetics, or subsequent coating. This is achieved through post-processing methods detailed in the next section, such as:
- Bead Blasting (improves uniformity, typical Ra 3-10 µm)
- Tumbling/Vibratory Finishing (Ra 1-5 µm)
- CNC Machining (Ra < 1.6 µm easily achievable, down to ~0.4 µm)
- Polishing (Ra < 0.1 µm possible)
Summary Table: Precision Expectations for Metal AM (AlSi10Mg/A6061)
Parámetro | As-Built Condition (Typical) | After Post-Machining | Notes for UAV Enclosures |
---|---|---|---|
Precisión dimensional | ±0.1 to ±0.2 mm or ±0.1% to ±0.2% | Process Dependent (±0.01 mm+) | Use as-built for general form, machine critical interfaces. |
Achievable Tolerance | Moderate (Suitable for non-critical features) | Tight (As required by machining) | Specify critical tolerances clearly on drawings; design with machining stock. |
Rugosidad superficial (Ra) | 5 µm – 25 µm (Highly dependent on orientation) | < 1.6 µm typical, < 0.1 µm possible | As-built often acceptable internally; requires finishing for sealing, external surfaces. |
Exportar a hojas
Conclusion on Precision:
Metal additive manufacturing delivers good baseline dimensional accuracy and a characteristic surface finish suitable for many aspects of a UAV payload enclosure. However, achieving the tight tolerances and smooth surface finishes required for critical interfaces and optimal performance typically necessitates targeted post-processing, particularly CNC machining. Engineers designing these components must understand this interplay, apply DfAM principles to plan for necessary finishing steps, and collaborate closely with their AM provider. Reputable providers like Met3dp, focused on industrial applications, invest in high-precision equipment and process control to maximize as-built accuracy, providing a solid foundation for creating highly precise and functional final components. Procurement managers should ensure potential suppliers can demonstrate consistent accuracy and have robust capabilities for any required secondary finishing operations.
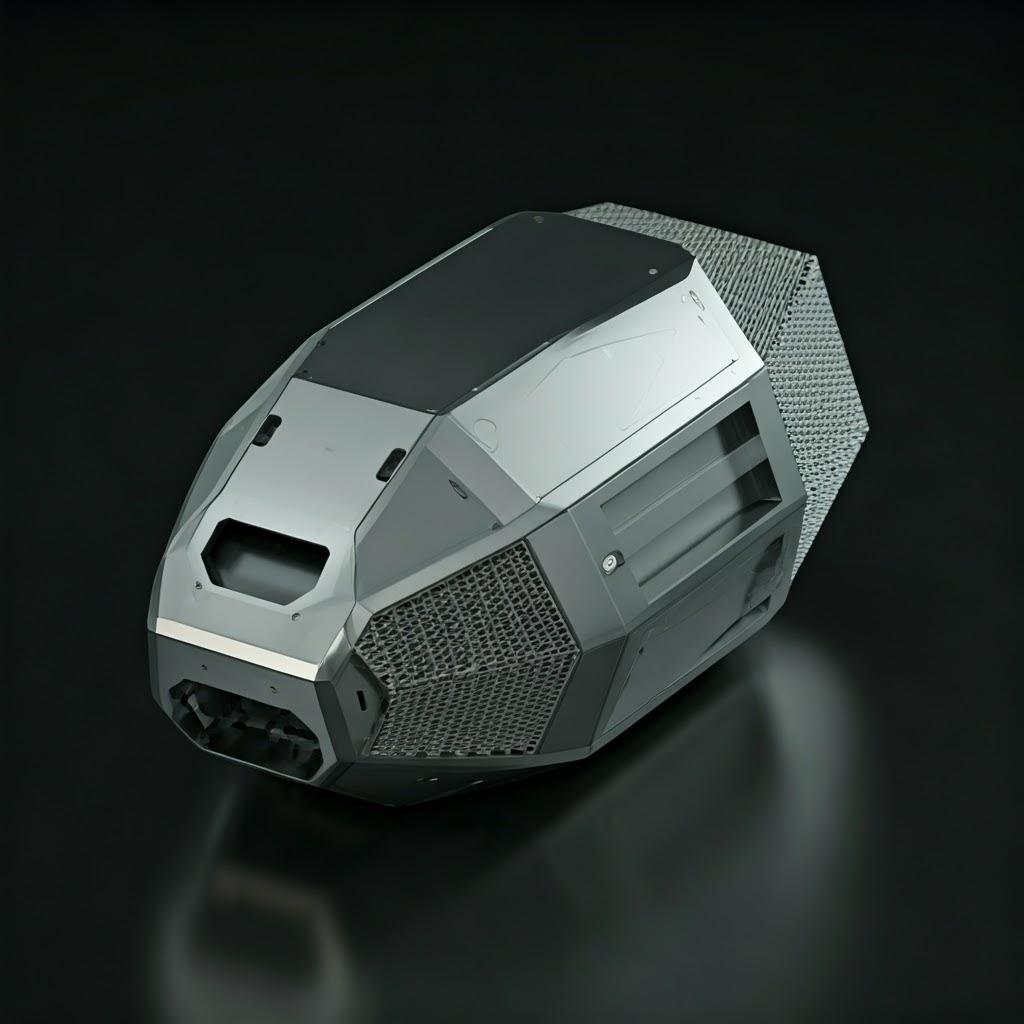
Essential Post-Processing Steps for Functionalizing Metal 3D Printed UAV Enclosures
A common misconception about metal additive manufacturing is that parts come out of the printer ready to use. In reality, for virtually all functional engineering applications, especially demanding ones like aerospace components including UAV payload enclosures, the printing process is just the first step. A series of crucial post-processing steps are required to transform the raw printed part into a functional, reliable component that meets all design specifications. These steps address residual stresses, remove temporary structures, achieve required material properties, attain necessary tolerances and surface finishes, and prepare the part for assembly and service. Understanding this workflow is vital for engineers designing the parts and for procurement managers estimating true costs and lead times.
The specific post-processing chain can vary depending on the AM process (SLM, DMLS, SEBM), the material (AlSi10Mg, A6061), the complexity of the part, and the final application requirements. However, a typical workflow for a metal 3D printed UAV enclosure involves several common stages:
- Recocido antiestrés:
- Propósito: The rapid heating and cooling cycles inherent in powder bed fusion processes create significant internal residual stresses within the printed part. These stresses can cause distortion or cracking when the part is removed from the rigid build plate or during subsequent processing. Stress relief involves heating the part (often while still attached to the build plate) to a moderate temperature (below critical transformation points, e.g., ~300°C for Al alloys) and holding it for a specific duration, followed by slow cooling. This allows the microstructure to relax, significantly reducing internal stresses.
- Importancia: Considered a mandatory first step for most metal AM parts to ensure dimensional stability and prevent unexpected failures.
- Extracción de la pieza de la placa de montaje:
- Proceso: Once stress relieved, the part(s) must be separated from the metal build plate they were printed on. Common methods include:
- Wire Electrical Discharge Machining (Wire EDM): Offers high precision and a clean cut with minimal mechanical stress, ideal for delicate parts or when a precise separation surface is needed.
- Sierra de cinta: Faster and lower cost but less precise and induces more mechanical stress. Suitable for less critical parts or where the base surface will be machined later.
- Machining (Milling): Can also be used to separate parts, potentially combining it with initial roughing operations.
- Consideración: The chosen method depends on part geometry, required precision, and cost factors.
- Proceso: Once stress relieved, the part(s) must be separated from the metal build plate they were printed on. Common methods include:
- Retirada de la estructura de soporte:
- Propósito: Removing the temporary support structures required during the build to anchor the part and support overhangs.
- Métodos: This is often the most labor-intensive post-processing step.
- Eliminación manual: Using pliers, cutters, grinders, or chisels. Requires skill to avoid damaging the part surface.
- Mecanizado CNC: Can be used for more controlled removal, especially for large or easily accessible supports.
- Electroerosión por hilo: Sometimes used for intricate support removal in tight spaces.
- Desafíos: Access to internal supports can be difficult or impossible if not considered during DfAM. Support removal inevitably leaves witness marks or scars on the part surface, which may require further finishing.
- Heat Treatment (Thermal Processing for Properties):
- Propósito: To achieve the desired final mechanical properties (strength, hardness, ductility, toughness) and microstructural characteristics for the chosen alloy. As-built metal AM parts often have non-equilibrium microstructures and suboptimal properties.
- Common Cycles for AlSi10Mg & A6061:
- Recocido de soluciones: Heating the part to a high temperature (e.g., ~515-540°C for A6061, ~525°C for AlSi10Mg) to dissolve alloying elements into a solid solution, followed by rapid quenching (cooling) to lock them in.
- Artificial Aging (Precipitation Hardening – T6 Temper): Reheating the quenched part to a lower temperature (e.g., ~160-190°C) for an extended period. This allows controlled precipitation of strengthening phases within the aluminum matrix, significantly increasing yield strength and hardness. This is essential for achieving the full potential of A6061 and significantly improves AlSi10Mg.
- Consideraciones: Heat treatment requires calibrated ovens, precise temperature/time control, and often protective atmospheres (inert gas or vacuum) to prevent oxidation. Parts can distort during heat treatment, potentially requiring specialized fixtures. Guidance from material suppliers like Met3dp on optimized heat treatment cycles for their specific powders is invaluable.
- HIP (Hot Isostatic Pressing) – Optional but Beneficial:
- Proceso: Simultaneously applying high temperature (just below melting point) and high isostatic pressure (using an inert gas like Argon, typically 100 MPa or more) in a specialized vessel.
- Beneficio: Effectively eliminates internal microporosity (gas pores, lack-of-fusion voids) by causing diffusion bonding across void surfaces. This significantly improves fatigue life, ductility, impact toughness, and property consistency, making it highly desirable for critical, fatigue-sensitive aerospace components.
- Drawback: Adds significant cost and lead time. Often specified only when required by performance or certification standards.
- Surface Finishing & Refinement:
- Propósito: To improve surface quality (smoothness, uniformity), remove support witness marks, achieve specific aesthetic requirements, or prepare the surface for coating.
- Common Methods:
- Abrasive Blasting (Bead/Sand Blasting): Propelling abrasive media against the surface. Cleans the part, removes loose powder, creates a uniform matte finish, and can induce beneficial compressive residual stresses on the surface, improving fatigue life. Different media (glass beads, aluminum oxide) create different finishes.
- Tumbling / Vibratory Finishing: Placing parts in a tub with abrasive media that vibrates or tumbles. Good for smoothing surfaces and edges, particularly for batches of smaller parts. Can reach complex geometries.
- Manual Grinding/Deburring: Targeted material removal using hand tools to smooth specific areas or remove support remnants.
- Pulido: Using progressively finer abrasives (manual or automated) to achieve very smooth, mirror-like finishes on specific surfaces if required (less common for entire enclosures).
- Electropulido: An electrochemical process that preferentially removes material from peaks, resulting in a smoother, brighter, and often more corrosion-resistant surface. Works well on complex shapes but requires specific electrolytes.
- Precision Machining (CNC):
- Propósito: To achieve tight dimensional tolerances, critical flatness/parallelism, specific surface finishes (Ra), or features that cannot be adequately formed by AM alone (e.g., precise bores, threaded holes, O-ring grooves).
- Proceso: Using CNC milling, turning, or grinding machines to selectively remove material from the AM part.
- Requirements: Requires careful part fixturing to hold the potentially complex AM geometry securely without distortion. DfAM planning (adding machining stock) is essential.
- Cleaning & Inspection:
- Propósito: Removing any residual powder, machining fluids, or debris. Verifying dimensional accuracy, surface finish, and integrity.
- Métodos: Ultrasonic cleaning, compressed air blow-off, visual inspection, Coordinate Measuring Machine (CMM) checks, surface profilometry, potentially Non-Destructive Testing (NDT) like CT scanning for internal defects if required.
- Coating / Surface Treatment:
- Propósito: To provide enhanced corrosion protection, wear resistance, electrical conductivity/insulation, specific thermal properties, or desired aesthetics.
- Common Options for Aluminum Alloys:
- Anodizing (Type II / Type III Hardcoat): Electrochemical process that grows a controlled oxide layer. Improves corrosion and wear resistance, provides electrical insulation, and can be dyed various colors. Type III (Hardcoat) is thicker and harder.
- Chromate Conversion Coating (Alodine / Chem Film): Provides excellent corrosion resistance and serves as a good base for paint adhesion. Often required by MIL-SPEC standards.
- Painting / Powder Coating: For specific colors or enhanced environmental protection.
- Plating (e.g., Nickel, Electroless Nickel): For wear resistance, lubricity, or specific conductivity requirements.
Workflow Integration:
These steps are often interdependent. For example, machining might be done before or after heat treatment depending on the material and desired outcome. Surface finishing might precede or follow coating. Developing an optimized post-processing workflow requires expertise and careful planning. Partnering with a full-service provider or coordinating effectively between different specialized suppliers is crucial for success. Companies like Met3dp, with deep expertise in both AM processes and material science, can provide critical guidance on integrating these steps effectively to produce functional, high-quality UAV payload enclosures.
Overcoming Common Challenges in Metal Additive Manufacturing for UAV Enclosures
While metal additive manufacturing offers tremendous advantages for producing lightweight, complex UAV payload enclosures, the technology is not without its challenges. Being aware of potential pitfalls and understanding how to mitigate them through careful design, process control, and post-processing is crucial for successfully implementing metal AM. Engineers and procurement managers should engage with AM service providers proactively to address these challenges, ensuring reliable production of high-quality components. Experienced providers like Met3dp leverage their process knowledge and advanced equipment to anticipate and overcome many of these common issues.
Here are some of the key challenges encountered when 3D printing metal UAV enclosures (particularly with AlSi10Mg and A6061) and strategies to address them:
- Deformación y distorsión:
- Problema: The part lifts from the build plate, curls, or deviates significantly from its intended geometry due to the buildup and release of thermal stresses during the layer-by-layer heating and cooling process. This is a major cause of build failures and dimensional inaccuracy.
- Causes: High thermal gradients, insufficient support allowing movement, large flat surfaces prone to differential shrinkage, inadequate stress relief.
- Solutions:
- Orientación de construcción optimizada: Orienting the part to minimize large flat areas parallel to the build plate and reduce overall height can help.
- Estrategia de apoyo sólida: Using well-designed supports (potentially solid block supports at the base) to firmly anchor the part and manage thermal contraction. Simulation tools can help optimize support placement.
- Process Parameter Control: Utilizing optimized parameters (scan speed, power, layer thickness, preheating) developed for the specific alloy and geometry. Met3dp’s focus on system reliability includes developing stable process parameters.
- Effective Stress Relief: Performing a proper stress relief cycle immediately after printing and before removing the part from the build plate is critical.
- DfAM: Designing features like sacrificial ribs or altering geometry to inherently resist warping.
- Difficulty with Support Structure Removal:
- Problema: Supports are necessary but can be time-consuming and difficult to remove without damaging the part, especially if located in complex internal cavities or on delicate features common in lightweight enclosures. Residual marks (witness scars) can affect surface quality.
- Causes: Supports placed in inaccessible areas, using overly dense or strong support structures, delicate part features adjacent to supports.
- Solutions:
- DfAM for Support Minimization: Design self-supporting angles (>45°), use chamfers/fillets, orient the part intelligently to reduce reliance on supports.
- Design for Access: If supports are unavoidable, ensure clear pathways and line-of-sight for removal tools (manual or automated).
- Optimized Support Types: Using appropriate support structures (e.g., finer, easily breakable supports vs. solid blocks) based on location and requirement. Software often allows customization.
- Planning for Finishing: Anticipate that support contact points will require surface finishing (grinding, blasting, machining) and plan accordingly.
- Internal Porosity:
- Problema: Small voids or pores trapped within the bulk material, which can reduce density, degrade mechanical properties (especially fatigue life and ductility), and potentially compromise sealing integrity.
- Causes: Trapped gas within the powder feedstock (lower quality powder), insufficient energy density during printing leading to incomplete melting (lack-of-fusion voids), unstable melt pool dynamics, keyhole porosity (at excessive energy density).
- Solutions:
- Polvo de alta calidad: Using powder with high sphericity, controlled PSD, and low internal gas content, produced via advanced methods like Met3dp’s VIGA or PREP systems, is crucial. Powder handling (storage, recycling) procedures must minimize moisture and oxygen pickup.
- Parámetros de proceso optimizados: Developing and meticulously controlling parameters (laser/beam power, scan speed, hatch spacing, layer thickness) to ensure complete melting and fusion between layers without introducing excessive instability.
- Prensado isostático en caliente (HIP): The most effective method for eliminating residual porosity post-print, often specified for critical applications.
- Supervisión de procesos: Advanced AM systems may incorporate in-situ monitoring to detect potential porosity issues during the build.
- Solidification Cracking (Especially in Alloys like A6061):
- Problema: Cracks forming along grain boundaries as the metal solidifies, particularly in alloys with a wide freezing range (like A6061) that are susceptible to thermal stresses.
- Causes: High thermal stresses during rapid cooling, specific alloy chemistry, part geometry concentrating stress.
- Solutions:
- Careful Parameter Development: Utilizing specific scan strategies (e.g., island scanning, optimized hatch overlap), adjusted power/speed settings, and potentially build plate preheating (common in EBM, possible in some SLM systems) to manage thermal gradients.
- Powder Chemistry Control: Ensuring powder composition is within tight specifications. Sometimes minor modifications or specific grain refiners can improve resistance.
- DfAM: Avoiding sharp internal corners and designing features to minimize stress concentration.
- Alivio del estrés: Prompt stress relief after printing is vital.
- Achieving Consistent Surface Finish:
- Problema: Variability in surface roughness across different faces of the part due to orientation, support contact, and inherent process characteristics, potentially failing to meet requirements for sealing, aerodynamics, or aesthetics.
- Causes: Layered nature of AM, stair-stepping on shallow angles, support interactions, partially melted powder adherence.
- Solutions:
- Orientación estratégica: Prioritizing critical surfaces for optimal orientation (up-facing or vertical).
- Optimized Parameters: Fine-tuning parameters can sometimes improve surface finish, though often at the expense of build speed.
- Planned Post-Processing: Recognizing that consistent and smooth finishes usually require secondary operations like bead blasting, tumbling, or machining, and incorporating these into the production plan.
- Meeting Tight Dimensional Tolerances:
- Problema: Difficulty achieving the required precision for mating interfaces, fits, or overall geometry directly from the printer.
- Causes: Unmanaged thermal effects (shrinkage, warping), machine calibration drift, distortion during post-processing (heat treatment, part removal).
- Solutions:
- Accurate Shrinkage Compensation: Using correct material-specific compensation factors in build preparation software.
- Process Simulation: Advanced simulation tools can predict distortion and allow for pre-compensation in the CAD model or optimization of support structures.
- Control robusto de procesos: Utilizing well-maintained, calibrated machines with stable parameters. Met3dp emphasizes the accuracy and reliability of its printing systems.
- Careful Post-Processing: Using fixtures during heat treatment to minimize distortion, employing precise methods for part/support removal.
- Designing for Machining: The most reliable method – incorporate machining stock on critical features and finish them subtractively.
- Residual Powder Removal:
- Problema: Unfused powder becoming trapped inside internal channels, lattice structures, or complex cavities within the enclosure, which can add weight, cause contamination, or interfere with function.
- Causes: Complex internal geometries without adequate drainage paths.
- Solutions:
- DfAM for Powder Removal: Designing escape holes or drainage channels at the lowest points of internal cavities. Optimizing lattice structures for powder flow-through.
- Post-Build Cleaning: Utilizing compressed air, vibration, or ultrasonic cleaning methods to dislodge and remove trapped powder. Careful inspection is needed.
By acknowledging these challenges and working with an experienced metal AM partner who employs rigorous process controls, high-quality materials, and effective DfAM strategies, manufacturers can successfully leverage the power of additive manufacturing to produce superior lightweight UAV payload enclosures. Proactive communication between designers, procurement teams, and the AM provider is key to navigating these potential issues and achieving optimal results.
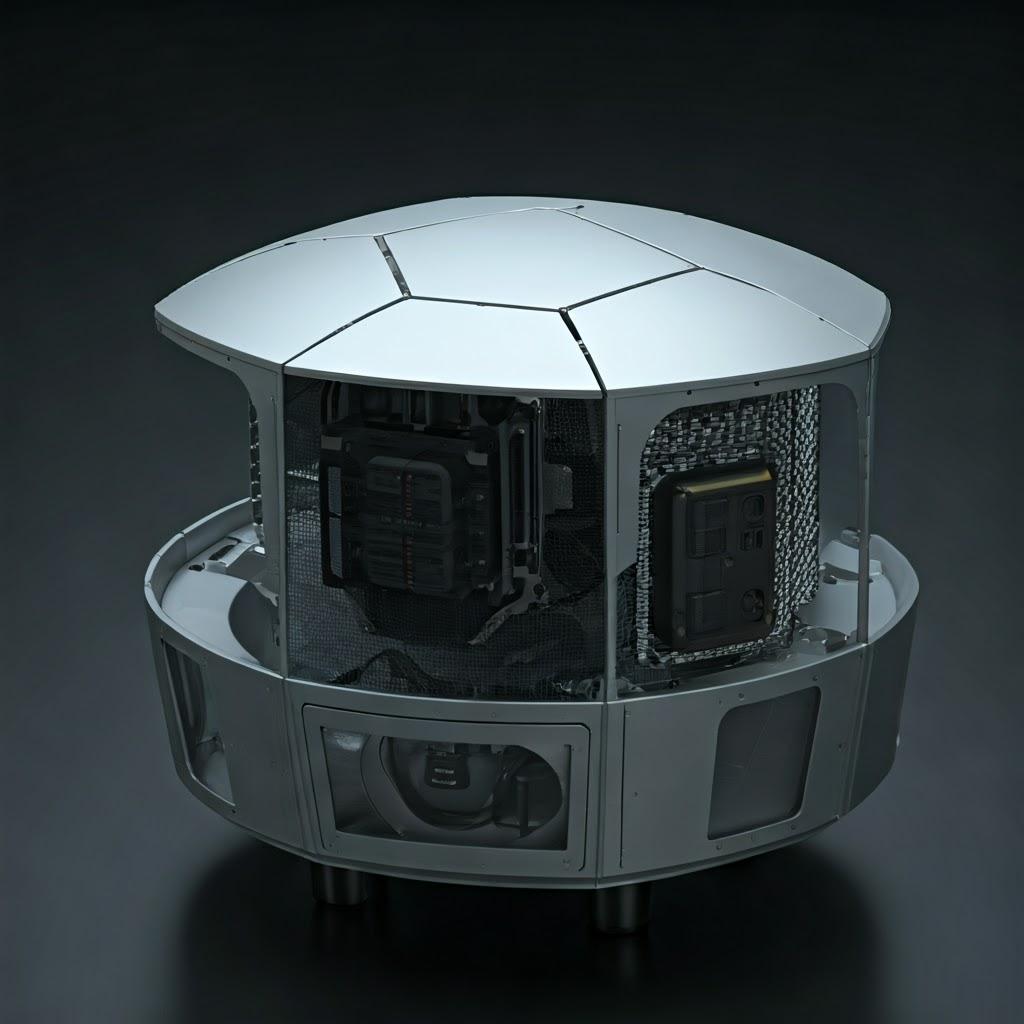
Selecting the Right Metal Additive Manufacturing Partner: A Guide for UAV Component Procurement
The decision to leverage metal additive manufacturing for critical components like UAV payload enclosures is just the beginning. Realizing the full potential of this technology – achieving lightweight designs, complex geometries, reliable performance, and cost-effectiveness – hinges significantly on selecting the right manufacturing partner. This choice is particularly critical for B2B relationships where consistency, quality, scalability, and technical support are paramount. For procurement managers and engineering leads tasked with sourcing these advanced components, conducting thorough due diligence on potential suppliers is not just recommended, it’s essential for mitigating risks and ensuring project success.
Choosing an AM partner is different from selecting a traditional machine shop or injection molder. The relative novelty of industrial metal AM, the complexity of the processes, the importance of material science, and the necessity of integrated post-processing capabilities require a specific set of evaluation criteria. A subpar partner can lead to failed prints, missed deadlines, parts that don’t meet specifications, unexpected costs, and ultimately, compromised UAV performance and reliability. Conversely, a strong partner acts as a collaborator, offering expertise that enhances the design, optimizes the manufacturing process, and delivers high-quality, reliable components.
Key Evaluation Criteria for Metal AM Service Providers:
When evaluating potential partners for producing metal 3D printed UAV enclosures using materials like AlSi10Mg or A6061, consider the following crucial factors:
- Demonstrated Technical Expertise and Experience:
- Process Specialization: Do they have deep experience with the specific AM process most suitable for your needs (e.g., Laser Powder Bed Fusion – SLM/DMLS, or Electron Beam Melting – SEBM)? Some processes offer advantages for certain materials or applications.
- Materials Knowledge: Have they successfully printed extensively with the chosen aluminum alloy (AlSi10Mg, A6061)? Can they provide material datasheets based on their actual process parameters and post-processing, not just generic powder specs?
- Application Experience: Have they manufactured parts for similar demanding applications, ideally within the aerospace, defense, or UAV industries? Ask for relevant case studies, examples of past work, or references. Look for partners like Met3dp, which highlights decades of collective expertise in metal additive manufacturing for mission-critical parts.
- Advanced Equipment and Technology:
- Industrial-Grade Machinery: Do they operate modern, industrial-grade metal AM systems known for reliability and precision? What is the build volume capacity – can it accommodate your enclosure size?
- Machine Maintenance & Calibration: What are their procedures for machine maintenance and calibration to ensure consistent results?
- Technology Portfolio: Do they offer complementary technologies or different types of AM machines that might provide flexibility or specific advantages? Met3dp, for instance, offers cutting-edge SEBM printers alongside their materials expertise.
- Material Quality, Control, and Sourcing:
- Calidad del polvo: This is fundamental. Do they use high-quality, certified metal powders with controlled sphericity, particle size distribution (PSD), and low contamination/gas content? Where do they source their powder?
- In-House Powder Production: Suppliers like Met3dp, who produce their own high-performance metal powders using advanced techniques like VIGA or PREP, often have greater control over quality and consistency.
- Material Traceability & Handling: What are their procedures for lot traceability, powder storage, handling, and recycling to prevent contamination and ensure consistent material properties batch-to-batch? Can they provide Certificates of Conformance (CoC) or Analysis (CoA) for the powder used?
- Sólido sistema de gestión de la calidad (SGC):
- Certificaciones: Are they certified to relevant quality standards? ISO 9001 is a baseline. For aerospace components, AS9100 certification is highly desirable, indicating a rigorous QMS tailored to the aerospace industry’s stringent requirements for traceability, process control, and risk management.
- Control de procesos: What measures do they take to monitor and control the printing process (e.g., melt pool monitoring, atmospheric control)?
- Inspection & Documentation: What are their standard inspection procedures? Can they provide detailed documentation, including build logs, material certifications, heat treatment records, and final inspection reports?
- Comprehensive In-House Capabilities (End-to-End Solutions):
- Integrated Services: Does the provider offer a full suite of services beyond just printing? This includes DfAM consultation, stress relief, heat treatment, HIP (if required), support removal, CNC machining, various surface finishing options, and inspection.
- Minimizing Subcontracting: While some specialized subcontracting is normal, relying heavily on external vendors for core post-processing steps can add significant lead time, cost, logistical complexity, and potential quality control gaps. Providers with strong in-house capabilities, like Met3dp’s comprehensive solutions approach, offer a more streamlined and controlled process.
- Design for Additive Manufacturing (DfAM) Support:
- Collaborative Approach: Are they willing and able to work collaboratively with your engineering team to review designs and suggest modifications that optimize for printability, weight reduction, performance, and cost-effectiveness?
- Expertise & Tools: Do they have engineers experienced in DfAM principles, topology optimization, and lattice structure generation? Do they utilize relevant software tools?
- Post-Processing Expertise and Capacity:
- Tratamiento térmico: Do they have properly calibrated ovens and established, validated heat treatment cycles (e.g., T6 for A6061/AlSi10Mg) specific to AM materials? Can they manage potential distortion with appropriate fixturing?
- Machining & Finishing: Do they have the necessary CNC machining capabilities (e.g., 5-axis milling) and finishing equipment (blasting, tumbling, etc.) in-house or through tightly managed partners?
- Support Removal Skills: Do they have experienced technicians and appropriate tools for careful and efficient support removal, especially for complex internal structures?
- Metrology and Inspection Capabilities:
- Equipamiento: What inspection tools do they possess? Coordinate Measuring Machines (CMMs) for dimensional verification, surface profilometers for roughness checks, potentially NDT equipment like CT scanners for internal integrity checks if required for critical parts.
- Informar: Can they provide comprehensive inspection reports tailored to your requirements?
- Capacidad, plazo de entrega y escalabilidad:
- Plazos de entrega realistas: Do they provide clear and realistic estimates for lead times, considering the entire workflow from order to delivery?
- Capacidad de producción: Do they have sufficient machine capacity and personnel to handle your prototype and potential low-to-medium volume production needs without excessive delays? Can they scale production if required?
- Cost Structure and Transparency:
- Detailed Quotations: Do they provide transparent, itemized quotes that clearly break down the costs associated with material, printing, each post-processing step, NDT, certifications, etc.? Beware of overly simplistic quotes that might hide later charges.
- Value Proposition: Consider the total value offered, including technical support, quality assurance, and reliability, not just the lowest price.
- Communication, Responsiveness, and Support:
- Canales de comunicación claros: Is it easy to communicate with their technical and project management teams?
- Capacidad de respuesta: Are they prompt in responding to inquiries, providing quotes, and giving project updates?
- Resolución de problemas: How do they handle issues or unexpected challenges during the manufacturing process?
Procurement Checklist Snippet:
Criteria Checklist | Ideal Provider Attributes | Notes / Questions to Ask |
---|---|---|
Experience & Expertise | Proven track record in relevant AM process, material (AlSi10Mg/A6061), and industry (Aerospace/UAV). Case studies available. | How many years printing this alloy? Examples of similar parts? References? |
Material Quality & Control | Certified powder, ideally in-house production (e.g., Met3dp VIGA/PREP), traceability, controlled handling. CoA provided. | Powder source? Production method? Certification provided? Recycling process? |
Quality Management System | ISO 9001 minimum, AS9100 preferred for aerospace. Documented process controls & inspection procedures. | QMS Certifications? Standard inspection report format? Process monitoring used? |
Capacidades internas | DfAM, Printing, Stress Relief, Heat Treat, Machining, Finishing, Inspection under one roof or tightly managed. | What % of post-processing is done in-house? What equipment do you have? |
Post-Processing Expertise | Validated heat treat cycles for AM Al alloys, skilled support removal, appropriate CNC & finishing tech. | Details on heat treat oven calibration? Examples of machined AM parts? |
Capacity & Lead Time | Realistic lead time quotes, sufficient capacity for required volume, scalability options. | Current machine queue time? Typical lead time for similar parts? Capacity limits? |
Cost Transparency | Detailed, itemized quotations. Clear pricing structure. | Request sample quote breakdown. Are NDT/Cert costs included? |
Communication & Support | Responsive points of contact (Technical/PM), proactive updates, collaborative approach. | Main point of contact? Typical response time? How are project updates provided? |
Exportar a hojas
Selecting the right metal AM partner is a strategic decision. By carefully evaluating potential suppliers against these criteria, procurement managers and engineers can build strong relationships with capable partners like Met3dp, ensuring the successful production of high-performance, lightweight UAV payload enclosures that meet the demanding requirements of modern unmanned systems.
Understanding Cost Drivers and Lead Times for Custom 3D Printed UAV Enclosures
One of the most common questions from engineers and procurement managers exploring metal additive manufacturing for components like UAV payload enclosures relates to cost and lead time. While AM offers significant advantages in terms of design freedom and eliminating tooling costs, understanding the factors that influence pricing and delivery schedules is crucial for accurate project planning, budgeting, and managing expectations. Unlike traditional high-volume manufacturing where tooling amortization dominates, AM costs are more closely tied to material consumption, machine time, and the extent of required post-processing.
Key Cost Drivers for Metal AM UAV Enclosures:
The final price of a 3D printed metal enclosure is influenced by a combination of factors:
- Part Design – Volume & Bounding Box:
- Material Consumption: The physical volume of the final part directly impacts the amount of expensive metal powder consumed. Larger volume = higher material cost.
- Machine Time (Printing): Larger parts, particularly those with a large footprint or overall bounding box (the smallest cube the part fits inside), occupy more space on the build plate and generally take longer to print. Machine time on industrial metal AM systems is a significant cost component.
- Machine Time (Support): The volume of support structures needed also consumes material and adds to the print time.
- Material Type and Cost:
- Elección de aleación: The cost per kilogram of metal powder varies between alloys. While AlSi10Mg and A6061 are relatively common aluminum alloys for AM, their cost is still significantly higher than bulk casting or wrought aluminum. Specialized alloys would be even more expensive.
- Calidad del polvo: High-quality powder with controlled characteristics (sphericity, PSD, purity) produced by advanced methods commands a higher price but is essential for reliable, high-performance parts.
- Part Complexity and Features:
- Imprimibilidad: While AM excels at complexity, extremely intricate designs poder sometimes increase print time due to complex laser/beam scanning paths.
- Post-Processing Difficulty: Complex internal channels or features might make support removal or powder cleaning more challenging and labor-intensive, adding to cost.
- Benefit of Consolidation: However, it’s crucial to remember that AM’s ability to handle complexity allows for part consolidation, which often reduces the overall system cost by eliminating assembly labor and fasteners, even if the single printed part seems relatively expensive on its own.
- Support Structure Requirements:
- Volume & Removal: As mentioned, support structures consume material and print time. More importantly, their removal is often a manual or semi-automated process requiring significant labor time, which directly adds to cost. Designs optimized using DfAM to minimize supports will be more cost-effective.
- Build Height and Packing Efficiency:
- Print Time Correlation: The dominant factor determining print time is usually the number of layers, i.e., the height of the part(s) in the build orientation. Taller builds take longer.
- Nesting/Packing: AM providers try to maximize the number of parts printed simultaneously on a single build plate (“nesting”). Efficient packing utilizes the machine time effectively, reducing the per-part cost contribution from machine amortization and setup. Designs with awkward shapes that pack poorly can increase per-part costs.
- Required Post-Processing Steps:
- Mandatory vs. Optional: Every post-processing step adds cost (labor, machine time, consumables, energy).
- Mandatory (usually): Stress Relief, Part Removal, Support Removal, Basic Cleaning.
- Often Required for Properties: Heat Treatment (Solution & Ageing).
- Application-Dependent: HIP (significant cost addition), CNC Machining (cost depends on complexity and amount of material removed), Surface Finishing (Blasting, Tumbling, Polishing), Coating (Anodizing, Painting, etc.).
- Labor Intensity: Manual steps like support removal or polishing can be major cost contributors.
- Mandatory vs. Optional: Every post-processing step adds cost (labor, machine time, consumables, energy).
- Quality Assurance and Inspection Requirements:
- Standard vs. Enhanced QA: Basic dimensional checks are standard. More rigorous inspection requirements, such as detailed CMM reports for multiple features, surface roughness measurements, or NDT (like CT scanning for internal porosity analysis), add significant cost due to specialized equipment and operator time.
- Certification Needs: Parts requiring certification (e.g., to AS9100 standards) involve more stringent process controls, documentation, and traceability throughout the entire workflow, which increases overhead and thus cost.
- Volumen del pedido (cantidad):
- Setup Amortization: While AM avoids hard tooling costs, there are still setup costs associated with file preparation, build planning, machine setup, and post-processing protocols. These setup costs are amortized over the number of parts in the batch. Therefore, the per-part cost generally decreases as the quantity increases.
- Economías de escala: Higher volumes allow for more efficient machine utilization (full build plates), dedicated post-processing setups, and potentially bulk material purchasing, leading to better per-part pricing. However, the cost reduction curve is typically flatter than with traditional high-volume methods like casting or molding. Discussing wholesale UAV component pricing with suppliers is important for larger batch orders.
Factors Influencing Lead Time:
Lead time, the duration from order placement to part delivery, is equally critical for project scheduling. Key influencing factors include:
- Design Review & Preparation: Initial DfAM review, potential design adjustments, generation of support structures, slicing the model into layers, and planning the build layout takes time (typically 1-3 days, depending on complexity and communication).
- Machine Availability (Queue Time): This can be a major variable. Industrial metal AM machines are expensive assets, and service providers often have a queue of jobs. Lead time can significantly increase if machines are fully booked (can range from days to weeks).
- Tiempo de impresión: Purely the time the machine is running to print the part(s). Highly dependent on the build height and volume. Can range from 12 hours to several days, or even over a week for very large or tall builds.
- Cooling & De-powdering: Time for the build chamber and parts to cool down sufficiently before the parts can be safely removed and excess powder recovered (can take several hours).
- Post-Processing Operations: Each step adds to the overall lead time:
- Stress Relief/Heat Treatment: Oven cycles can take hours to days, including controlled heating, soaking, and cooling ramps.
- HIP: Typically requires sending parts to a specialized facility and can add 1-2 weeks to the lead time.
- Part Removal/Support Removal: Can take hours depending on complexity and method.
- Mecanizado CNC: Setup and machining time varies greatly with complexity (hours to days).
- Surface Finishing/Coating: Can range from hours (blasting) to days (some coating processes with curing times).
- Inspection: Time required depends on the level of inspection needed (hours to days for complex CMM programming and measurement).
- Logistics and Shipping: Transit time from the AM provider to the customer’s facility.
Typical Lead Time Ranges (Estimates):
- Prototypes (1-5 units): Often possible within 1 to 3 weeks, assuming rapid DfAM review, machine availability, and standard post-processing (e.g., stress relief, support removal, basic finish). Complex parts or those needing extensive post-processing will take longer.
- Low-Volume Production (10-100 units): Normalmente oscila entre De 3 a 6 semanas, allowing for more optimized build layouts, batch post-processing, and scheduling of resources. Again, complexity, HIP, or extensive machining can extend this.
Getting Accurate Estimates:
The best way to understand cost and lead time for a specific UAV payload enclosure is to request detailed quotes from qualified metal AM service providers like Met3dp. Providing a mature 3D CAD model, specifying the material (AlSi10Mg or A6061), clearly defining critical tolerances and required post-processing steps, stating the quantity needed, and outlining any specific inspection or certification requirements will enable suppliers to provide the most accurate estimates. Understanding these cost and lead time drivers allows engineers and procurement managers to engage more effectively with suppliers and make informed decisions about leveraging metal AM for their UAV component needs.
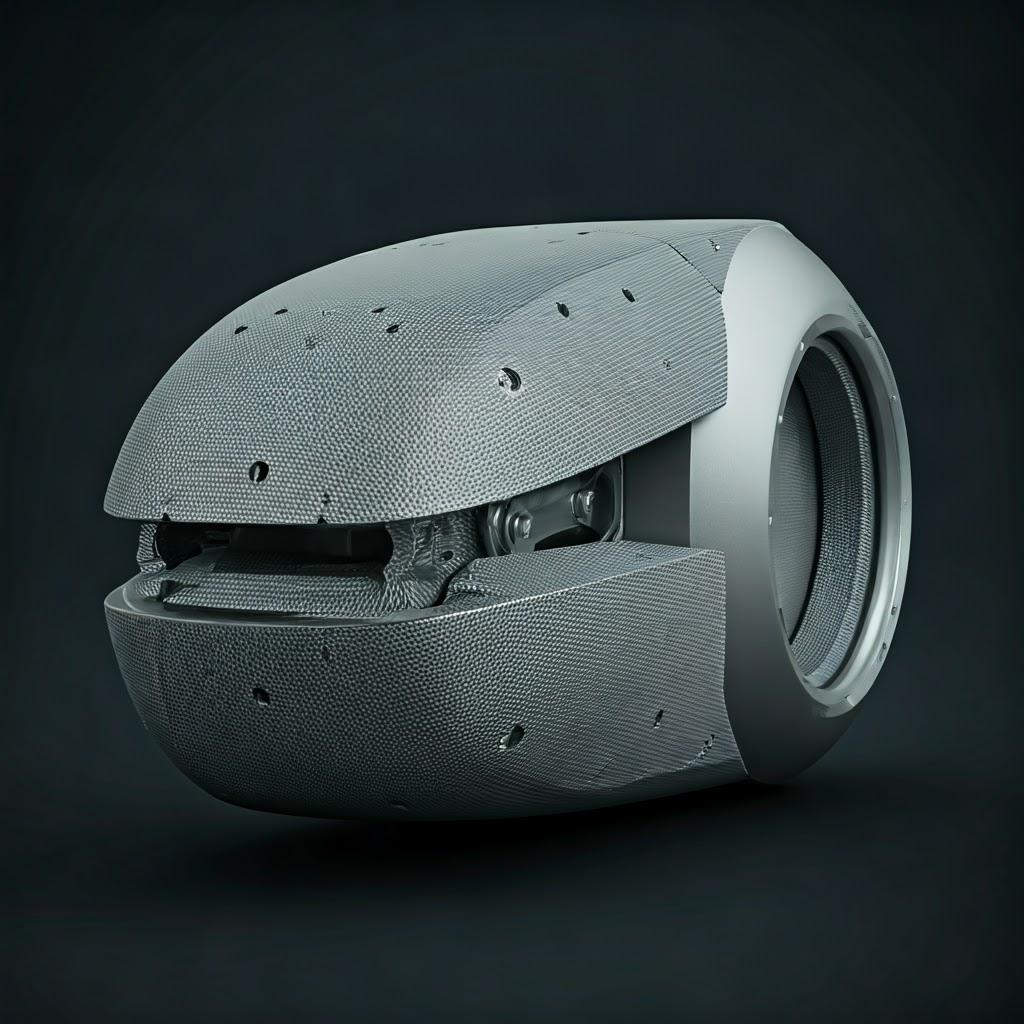
Frequently Asked Questions (FAQ) about Metal 3D Printed UAV Enclosures
Here are answers to some common questions engineers and procurement managers have when considering metal additive manufacturing for UAV payload enclosures using aluminum alloys like AlSi10Mg and A6061:
Q1: How does the strength of 3D printed AlSi10Mg or A6061 compare to the same alloys produced by traditional casting or forging/extrusion (wrought)?
A: This is a critical question, and the answer requires some nuance:
- vs. Casting: Metal AM parts (SLM/DMLS/SEBM) made from AlSi10Mg or A6061, especially after proper heat treatment and potentially HIP, generally exhibit mechanical properties (yield strength, ultimate tensile strength, fatigue life) that are comparable or often superior to traditional casting methods (like die casting or investment casting). This is due to the fine microstructure typically achieved in AM.
- vs. Wrought (Forged/Extruded): Traditionally wrought materials (like extruded 6061-T6) typically represent the benchmark for strength and ductility due to their highly worked microstructure. As-built or heat-treated AM parts may approach, but often slightly underperform compared to, wrought properties, particularly in terms of ductility and fatigue strength. However, advanced AM process optimization, high-quality powders, and post-processing like HIP can significantly close this gap. Furthermore, AM’s ability to create optimized geometries (topology optimization, part consolidation) means the final component performance can often exceed that of a conventionally designed wrought part, even if the base material properties are slightly different. Always refer to specific datasheet values from the AM provider for their process/material combination and consider performance testing for critical applications.
Q2: Can complex internal features, like cooling channels or integrated wiring pathways, be reliably printed and cleaned of residual powder?
A: Yes, the ability to create complex internal geometries is one of the primary advantages of metal AM.
- Printing Reliability: Modern AM systems can reliably produce intricate internal channels, conformal cooling passages, and hollow structures. The minimum size and complexity achievable depend on the specific machine resolution and process parameters.
- Eliminación del polvo: This is a crucial DfAM consideration. For internal channels or cavities to be cleared of unfused powder, escape holes must be designed into the part at strategic locations (usually the lowest points in the build orientation). The size and placement of these holes are critical. Without proper escape routes, powder can become trapped permanently. Post-print cleaning processes (compressed air, vibration, sometimes ultrasonic cleaning) are used to remove the loose powder through these designed openings. For very complex internal networks, validating the cleaning process might be necessary.
Q3: What is the practical minimum wall thickness achievable when designing a lightweight UAV enclosure with AlSi10Mg or A6061?
A: Achieving minimum weight often involves designing thin walls, but there are practical limits:
- Theoretical Minimum: Depending on the specific metal AM system (laser spot size or electron beam diameter) and process parameters, theoretical minimum wall thicknesses might be cited around 0.3 mm to 0.5 mm.
- Practical Minimum: Printing such thin walls reliably over large areas or complex geometries can be challenging due to thermal stability issues and handling fragility. A more practical and robust minimum wall thickness for structural integrity and reliable printing is generally considered to be in the range of 0.8 mm to 1.0 mm or greater for AlSi10Mg and A6061 enclosures.
- DfAM is Key: Rather than uniformly thin walls, DfAM techniques like topology optimization or adding localized stiffening ribs often provide better structural efficiency and manufacturability, allowing targeted lightweighting while maintaining robustness where needed. Always consult with your AM provider, like Met3dp, for guidance based on their specific equipment and experience.
Q4: Is metal AM only suitable for prototypes, or can it be used for serial production of UAV components?
A: Metal AM has evolved significantly beyond just prototyping and is increasingly being adopted for serial production, especially in industries like aerospace and for components like UAV enclosures where its benefits are compelling:
- Low-to-Medium Volumes: AM is highly cost-effective for low-to-medium production volumes (tens to thousands of parts per year, depending on size and complexity) where the cost of tooling for traditional methods (casting, molding) would be prohibitive.
- High Complexity / High Value: For parts where AM enables significant performance gains (e.g., massive weight reduction through topology optimization, integrated functionality through part consolidation) that cannot be achieved conventionally, AM can be the preferred production method even if the per-part print cost seems high.
- Personalización: AM is ideal for producing customized enclosure variations tailored to specific payload integrations without requiring new tooling for each variant.
- Bridge Production: It can also serve as a “bridge” to higher volume traditional methods, allowing products to launch faster while tooling is being prepared. The decision depends on a techno-economic analysis comparing the total cost of ownership (including design benefits) of AM versus traditional methods for the required production volume.
Q5: What information does an AM service provider typically need to provide an accurate quote for printing a UAV payload enclosure?
A: To get the most accurate and timely quote, provide potential suppliers with as much clear information as possible:
- Modelo CAD en 3D: A high-quality 3D model in a standard format like STEP (.stp or .step) is essential. Ensure the model is watertight and represents the final desired geometry.
- Material Specification: Clearly state the desired alloy (e.g., AlSi10Mg or A6061).
- Cantidad: Specify the number of parts required (for prototypes or production batches).
- Critical Dimensions & Tolerances: Provide a 2D drawing or annotated 3D model highlighting any critical dimensions, required tolerances (specify if tighter than standard AM tolerances), and critical functional surfaces. Indicate surfaces requiring specific Ra values.
- Requisitos de postprocesamiento: Clearly list all required steps:
- Stress Relief (usually assumed unless specified otherwise).
- Heat Treatment (specify temper, e.g., T6).
- HIP requirement (Yes/No).
- Support Removal level (e.g., basic removal vs. fully smoothed).
- Surface Finish (e.g., as-built, bead blast matte, specific Ra target on certain faces).
- Machining needs (highlight areas needing machining, provide final dimensions).
- Coating/Anodizing (specify type and standard if applicable).
- Inspection Requirements: Detail any specific inspection needs beyond standard dimensional checks (e.g., CMM report on specific features, NDT requirements, material certifications).
- Desired Lead Time: Indicate your required delivery date, if known.
Providing comprehensive information upfront allows the AM service provider to accurately assess the manufacturing effort, plan the workflow, and deliver a reliable quote reflecting the true scope of work.
Conclusion: Elevating UAV Performance and Mission Capability with Custom Metal 3D Printed Enclosures
The landscape of unmanned aerial vehicle technology is one of constant evolution, driven by the demand for greater endurance, higher payload capacities, enhanced mission capabilities, and increased operational reliability. In this pursuit of performance, the optimization of every component is critical, and the payload enclosure – the guardian of the UAV’s valuable sensors and electronics – plays a pivotal role. As we’ve explored throughout this post, metal additive manufacturing, particularly using advanced aluminum alloys like AlSi10Mg and A6061, offers a revolutionary approach to designing and producing these vital components.
Metal AM fundamentally overcomes many limitations of traditional manufacturing, empowering engineers to:
- Achieve Unprecedented Lightweighting: Through topology optimization and lattice structures, significantly reducing enclosure weight without compromising strength, directly translating to longer flight times or increased payload capacity.
- Realize Complex Geometries: Enabling the creation of highly integrated designs with features like conformal cooling channels, optimized heat sinks, internal mounting points, and consolidated assemblies that improve thermal management, reduce part count, and enhance overall system efficiency.
- Enable Rapid Customization and Iteration: Facilitating the cost-effective production of bespoke enclosures tailored to specific payload requirements and allowing for rapid design validation and improvement cycles.
However, harnessing these benefits requires more than just access to a 3D printer. It demands a strategic approach encompassing:
- Design for Additive Manufacturing (DfAM): Thinking differently about design to leverage AM’s unique capabilities and account for its specific constraints.
- Material Science Understanding: Selecting the optimal high-quality metal powder and understanding its properties in the as-built and post-processed states.
- Comprehensive Post-Processing: Recognizing that printing is just the first step, followed by essential thermal treatments, finishing, and machining to achieve functional requirements.
- Riguroso control de calidad: Implementing robust processes to ensure dimensional accuracy, material integrity, and overall component reliability.
Critically, success in leveraging metal AM for demanding applications like UAV payload enclosures relies heavily on choosing the right manufacturing partner. Look for providers like Met3dp who offer not just printing services, but a vertically integrated solution encompassing deep expertise in material science (including advanced powder production), state-of-the-art printing technology (like SEBM and L-PBF systems), comprehensive post-processing capabilities, robust quality management systems (like AS9100), and collaborative DfAM support. Such a partner acts as an extension of your engineering team, helping navigate the complexities of AM and ensuring the delivery of components that meet the highest standards of performance and reliability.
By embracing metal additive manufacturing and partnering with knowledgeable experts, organizations developing advanced UAV systems can create payload enclosures that are lighter, stronger, more functional, and tailored precisely to mission needs. This technological shift is not merely an incremental improvement; it is a key enabler for the next generation of unmanned aerial vehicles, pushing the boundaries of what’s possible in aerospace, defense, industrial inspection, and beyond.
Ready to explore how metal 3D printing can elevate your UAV components? Póngase en contacto con Met3dp hoy mismo to discuss your project requirements with our additive manufacturing specialists and discover how our advanced powders and printing solutions can power your innovation.
Compartir
MET3DP Technology Co., LTD es un proveedor líder de soluciones de fabricación aditiva con sede en Qingdao, China. Nuestra empresa está especializada en equipos de impresión 3D y polvos metálicos de alto rendimiento para aplicaciones industriales.
Solicite información para obtener el mejor precio y una solución personalizada para su empresa.
Artículos relacionados
Acerca de Met3DP
Actualización reciente
Nuestro producto
CONTACTO
¿Tiene alguna pregunta? ¡Envíenos un mensaje ahora! Atenderemos su solicitud con todo un equipo tras recibir su mensaje.
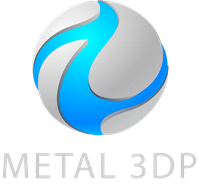
Polvos metálicos para impresión 3D y fabricación aditiva