3D Printed Custom Enclosures: Design Freedom and Performance
Índice
Introduction to Custom Electronics Enclosures via Metal 3D Printing
In today’s rapidly evolving technological landscape, the demand for customized electronic devices and systems is surging across various sectors, from aerospace and automotive to medical devices and industrial automation. Protecting the intricate and sensitive internal components of these electronics is paramount, and the enclosure plays a critical role in ensuring their longevity, reliability, and performance. Traditionally, manufacturing custom electronics enclosures often involved lengthy lead times and significant tooling costs associated with methods like machining or injection molding. However, the advent of metal Impresión 3D, also known as metal additive manufacturing (AM), has revolutionized this landscape, offering unprecedented design freedom, rapid prototyping capabilities, and the potential for cost-effective production of complex geometries. At Metal3DP, we are at the forefront of this innovation, providing cutting-edge metal 3D printing services that empower engineers and procurement managers to realize their most demanding enclosure designs with exceptional precision and material integrity. Our advanced Selective Electron Beam Melting (SEBM) printers and a comprehensive portfolio of high-performance metal powders, including AlSi10Mg and 316L, enable the creation of custom electronics enclosures that meet the stringent requirements of diverse industrial applications. This blog post will delve into the myriad benefits of utilizing metal 3D printing for custom electronics enclosures, explore the ideal materials for such applications, discuss crucial design considerations, and guide you in selecting the right partner, like Metal3DP, to bring your innovative designs to life.
Diverse Applications of 3D Printed Enclosures Across Industries
The versatility of metal 3D printed custom electronics enclosures opens up a vast array of applications across numerous industries. The ability to create complex geometries tailored to specific electronic components and environmental conditions makes this technology invaluable for:
- Aeroespacial: In aerospace, electronics enclosures often need to withstand extreme temperatures, vibrations, and electromagnetic interference. 3D printing allows for the creation of lightweight yet robust enclosures for avionics, sensors, and control systems, potentially utilizing materials like AlSi10Mg for its excellent strength-to-weight ratio. Imagine custom housings for satellite communication modules or protective cases for in-flight entertainment systems, all manufactured with the precision and reliability offered by Metal3DP’s advanced printing technology.
- Automóvil: The automotive industry demands electronics enclosures that can endure harsh operating environments, including exposure to moisture, chemicals, and mechanical stress. From housings for advanced driver-assistance systems (ADAS) sensors to enclosures for electric vehicle (EV) battery management systems, metal 3D printing with materials like 316L offers the necessary durability and corrosion resistance. Consider the possibilities for creating custom-fit enclosures for in-cabin electronics or ruggedized housings for under-the-hood control units, all achievable with the high accuracy of Metal3DP’s SEBM process.
- Productos sanitarios: In the medical field, electronics enclosures for diagnostic equipment, monitoring systems, and implantable devices often require biocompatibility, sterilization capabilities, and intricate designs to fit specific anatomical contours. Metal 3D printing allows for the creation of such complex and highly customized enclosures, potentially using materials like 316L stainless steel, which is known for its biocompatibility and corrosion resistance. Think of patient-specific enclosures for wearable health monitors or protective housings for sensitive medical imaging electronics.
- Fabricación industrial: Industrial environments often present challenges such as dust, humidity, and physical impacts. Custom 3D printed enclosures can provide robust protection for control panels, sensors, and automation equipment. Materials like AlSi10Mg offer a good balance of strength and thermal conductivity, suitable for heat-dissipating enclosures for industrial control units. Envision creating custom housings for robotic control systems or ruggedized enclosures for field-deployed sensors.
- Investigación y desarrollo: The rapid prototyping capabilities of metal 3D printing make it an ideal solution for creating custom enclosures for experimental setups and specialized scientific instruments. Researchers can quickly iterate on designs and produce enclosures tailored to their unique requirements, accelerating the pace of innovation.
The ability to tailor the design and material of the enclosure to the specific application requirements offers significant advantages in terms of performance, durability, and integration.
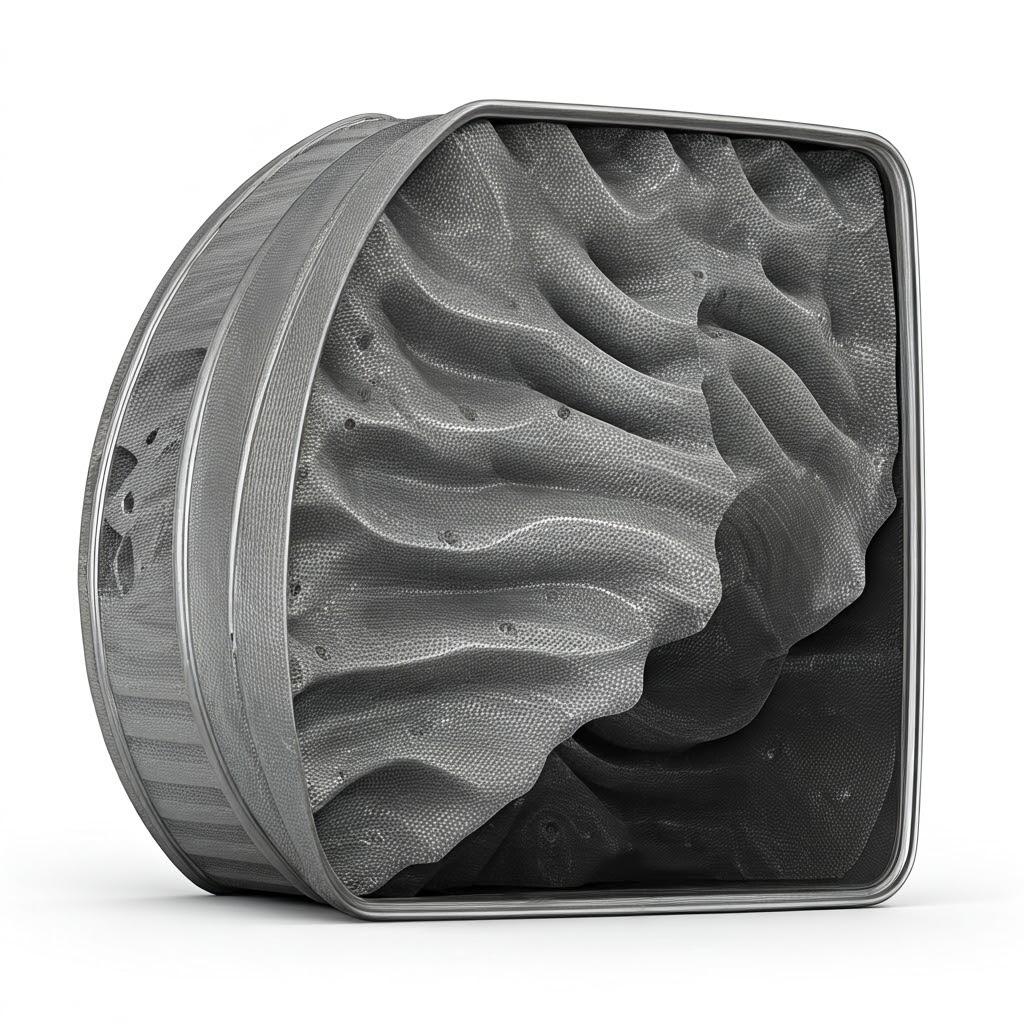
Unlocking Design Innovation with Metal Additive Manufacturing for Enclosures
Traditional manufacturing methods for electronics enclosures often impose significant design constraints. Tooling limitations, undercuts, and complex internal features can be costly or even impossible to achieve. Metal 3D printing, however, liberates engineers from these restrictions, offering unparalleled design freedom. This allows for the creation of enclosures with:
- Geometrías complejas: Metal 3D printing enables the fabrication of intricate internal channels for optimized thermal management, integrated mounting features, and customized shapes that perfectly fit the enclosed electronics. Imagine designing an enclosure with internal cooling fins precisely positioned to dissipate heat from critical components, a feat that would be challenging and expensive with traditional methods.
- Aligeramiento: By optimizing the internal structure and material distribution, 3D printing can produce enclosures with reduced weight without compromising structural integrity. Lattice structures and topologically optimized designs can be implemented to minimize material usage, which is particularly beneficial in aerospace and automotive applications where weight savings are critical. Metal3DP’s expertise in material science and advanced printing techniques allows us to create lightweight yet robust enclosures.
- Adaptación y personalización: Metal 3D printing allows for the creation of truly custom enclosures tailored to the specific dimensions and requirements of the enclosed electronics. This is particularly valuable for low-volume production or specialized applications where off-the-shelf enclosures are not suitable. Whether it’s a unique shape to fit a specific space constraint or personalized features for a medical device, 3D printing offers unmatched flexibility.
- Creación rápida de prototipos e iteración: The speed and agility of metal 3D printing significantly accelerate the prototyping process. Engineers can quickly translate their designs into physical prototypes, test their functionality and fit, and iterate on the design based on the results. This rapid feedback loop reduces development time and costs, allowing for faster time-to-market for innovative electronic products. Metal3DP’s rapid prototyping services empower our clients to quickly validate their designs.
- Integration of Multiple Functions: Metal 3D printing allows for the integration of multiple functionalities directly into the enclosure design. This could include integrated heat sinks, mounting bosses, connectors, and even shielding features, reducing the need for secondary assembly processes and improving overall system reliability.
By embracing the design freedom offered by metal 3D printing, engineers can create electronics enclosures that are not only protective but also optimized for performance, weight, and integration.
AlSi10Mg and 316L: Ideal Materials for High-Performance Enclosures
The choice of material is crucial for the performance and durability of a custom electronics enclosure. Metal3DP offers a range of high-performance metal powders optimized for additive manufacturing, and for custom electronics enclosures, AlSi10Mg and 316L stand out as particularly suitable options.
AlSi10Mg: This aluminum alloy is characterized by its excellent combination of properties, making it ideal for a wide range of electronics enclosure applications:
- Ligero: Aluminum alloys are significantly lighter than steel, which is a critical advantage in applications where weight is a concern, such as aerospace and portable electronics.
- Buena resistencia y ductilidad: AlSi10Mg offers a good balance of strength and ductility, providing structural integrity and resistance to fracture under stress.
- Excelente conductividad térmica: Aluminum alloys have high thermal conductivity, making AlSi10Mg an excellent choice for enclosures that require efficient heat dissipation from internal electronic components. This is crucial for maintaining the performance and lifespan of sensitive electronics.
- Buena resistencia a la corrosión: AlSi10Mg exhibits good resistance to corrosion in many environments, ensuring the long-term protection of the enclosed electronics.
- Soldabilidad y mecanizabilidad: Post-processing operations such as welding and machining can be performed on AlSi10Mg parts, offering flexibility in manufacturing and assembly.
Acero inoxidable 316L: This austenitic stainless steel is renowned for its exceptional corrosion resistance and biocompatibility, making it suitable for demanding environments and specific applications:
- Excelente resistencia a la corrosión: 316L exhibits superior resistance to corrosion, even in harsh environments with exposure to moisture, chemicals, and saline solutions. This makes it ideal for enclosures used in marine, medical, and industrial applications.
- Alta resistencia y tenacidad: 316L offers high strength and toughness, providing robust protection for sensitive electronic components against mechanical impacts and vibrations.
- Biocompatibilidad: The biocompatibility of 316L makes it a suitable material for enclosures used in medical devices and healthcare applications where contact with biological tissues or fluids is possible.
- Buena soldabilidad y conformabilidad: 316L can be easily welded and formed, allowing for complex enclosure designs and integration with other components.
- Esterilizabilidad: 316L can withstand common sterilization methods used in the medical industry, making it suitable for enclosures that need to be sterilized.
The table below summarizes the key properties of AlSi10Mg and 316L for custom electronics enclosures:
Propiedad | AlSi10Mg | Acero inoxidable 316L |
---|---|---|
Densidad | ∼2.67g/cm3 | ∼8.0g/cm3 |
Resistencia a la tracción (UTS) | ∼350−450MPa | ∼550−650MPa |
Límite elástico | ∼200−300MPa | ∼200−300MPa |
Alargamiento a la rotura | ∼5−10% | ∼40−50% |
Conductividad térmica | ∼120−160W/mK | ∼15−20W/mK |
Resistencia a la corrosión | Bien | Excelente |
Biocompatibilidad | Generalmente bueno | Excelente |
Aplicaciones típicas | Aerospace, Automotive, Industrial, Heat Sinks | Medical, Marine, Chemical Processing, Food |
Exportar a hojas
En Metal3DP, our expertise in processing both AlSi10Mg and 316L using our advanced SEBM technology ensures that you receive custom electronics enclosures with optimal material properties, dimensional accuracy, and surface finish to meet your specific application requirements.
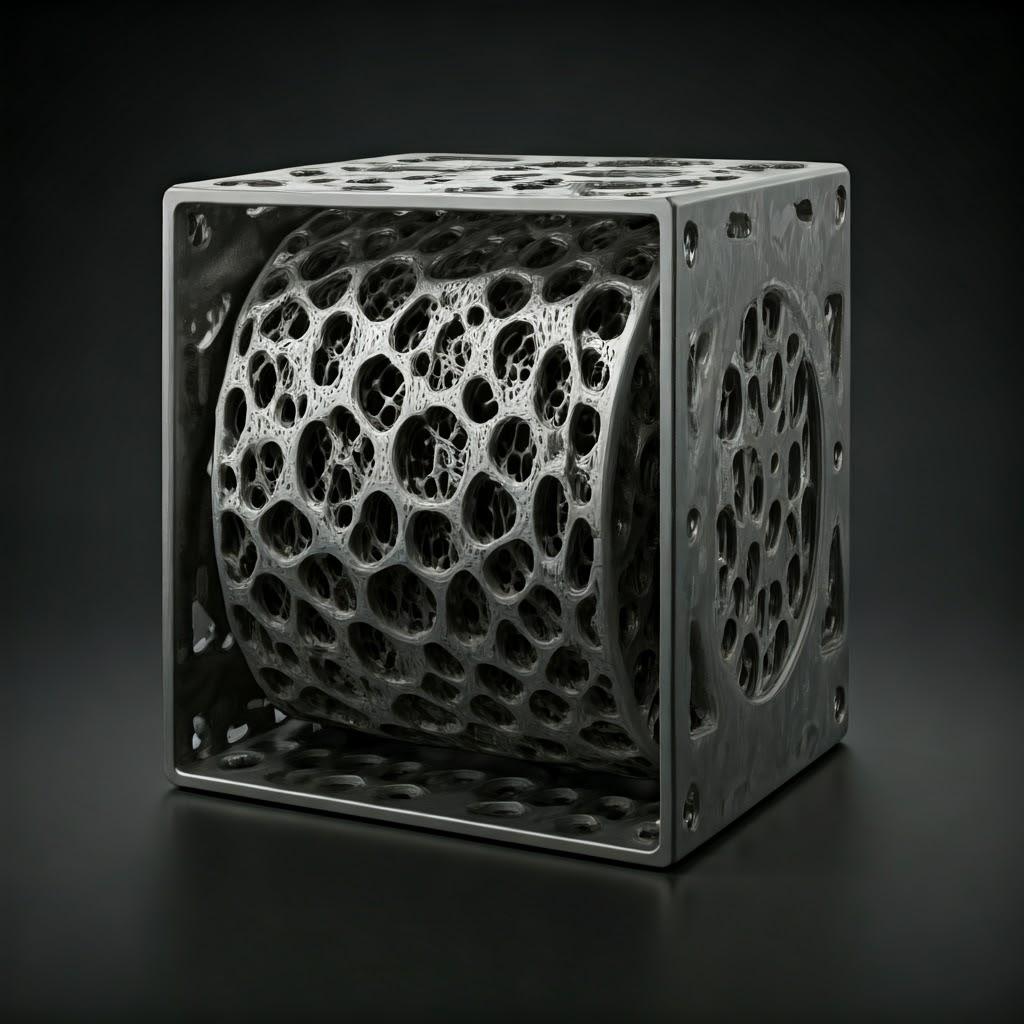
Key Design Considerations for Optimal 3D Printed Enclosure Functionality
Designing for metal 3D printing requires a different mindset compared to traditional manufacturing methods. To achieve optimal functionality and manufacturability of custom electronics enclosures, several key design considerations must be taken into account:
- Orientation and Support Structures: The orientation of the part during the 3D printing process significantly impacts surface finish, support structure requirements, and build time. Optimizing the orientation can minimize the need for extensive support structures, which can be challenging to remove and may leave surface artifacts. Careful consideration of overhang angles and critical surfaces is essential. Metal3DP’s experienced engineers can advise on the optimal build orientation for your enclosure design.
- Wall Thickness and Ribs: Determining the appropriate wall thickness is crucial for ensuring the structural integrity and rigidity of the enclosure while minimizing material usage and weight. Incorporating ribs and gussets can significantly enhance stiffness without increasing overall wall thickness. These features can be strategically placed to provide support in areas subjected to stress or to prevent warping during the printing process.
- Características de gestión térmica: For electronics enclosures housing heat-generating components, integrating thermal management features directly into the design is highly beneficial. This can include internal cooling channels, external fins, or mounting surfaces designed for thermal interface materials. Metal 3D printing allows for the creation of complex internal geometries that optimize heat dissipation.
- Assembly and Integration Features: Designing features that facilitate easy assembly and integration with other components is essential. This can include threaded holes, snap-fit features, alignment pins, and mounting bosses. Incorporating these features directly into the 3D printed enclosure can reduce the need for secondary operations and improve overall system integration.
- Minimización de las concentraciones de tensión: Sharp corners and abrupt changes in geometry can lead to stress concentrations, potentially weakening the enclosure under load. Designing with smooth transitions and fillets can help distribute stress more evenly and improve the overall durability of the part.
- Material Considerations in Design: The chosen material will influence design decisions. For instance, the higher thermal conductivity of AlSi10Mg might lead to different thermal management design approaches compared to 316L. Similarly, the higher ductility of 316L might allow for thinner walls in certain applications where impact resistance is important.
By carefully considering these design factors and leveraging the unique capabilities of metal 3D printing, engineers can create custom electronics enclosures that are not only functional and protective but also optimized for performance and manufacturability.
Alcanzar la precisión: Tolerancia, acabado superficial y exactitud dimensional en carcasas impresas en 3D
In many electronics applications, particularly in aerospace and medical devices, tight tolerances and high dimensional accuracy are critical. Metal 3D printing, especially Metal3DP’s SEBM technology, offers a high degree of precision in manufacturing complex geometries. However, achieving the desired tolerance, surface finish, and dimensional accuracy requires careful process control and consideration of several factors:
- Calibración y mantenimiento de máquinas: Regular calibration and maintenance of the 3D printer are essential to ensure consistent and accurate results. Factors such as laser or electron beam power, scanning speed, and powder delivery must be precisely controlled.
- Material Properties and Process Parameters: The inherent properties of the metal powder and the specific process parameters used during printing can influence the final dimensions and surface finish of the part. Optimized parameter sets for materials like AlSi10Mg and 316L are crucial for achieving the desired accuracy.
- Build Orientation and Support Structures (Revisited): As mentioned earlier, the orientation of the part during printing can affect dimensional accuracy, particularly for features oriented in the build direction. Support structures can also influence surface finish in areas where they are attached.
- Shrinkage and Distortion: During the solidification process, metal parts can experience shrinkage and distortion due to thermal gradients. Compensating for these effects through design adjustments and process optimization is crucial for achieving accurate dimensions.
- Técnicas de postprocesado: In some cases, post-processing techniques such as CNC machining, grinding, or polishing may be required to achieve very tight tolerances or specific surface finish requirements. Metal3DP offers comprehensive post-processing services to meet demanding specifications.
While metal 3D printing offers significant advantages in creating complex geometries with reasonable accuracy, it’s important to understand the achievable tolerances and surface finishes for a given material and process. Working with an experienced service provider like Metal3DP ensures that your custom electronics enclosures are manufactured to the highest possible standards of precision. Typical tolerances achievable with metal 3D printing can range from pm0.1,textmm to pm0.05,textmm, depending on the geometry and size of the part, and surface finishes can range from 5−20,mum,Ra before post-processing.
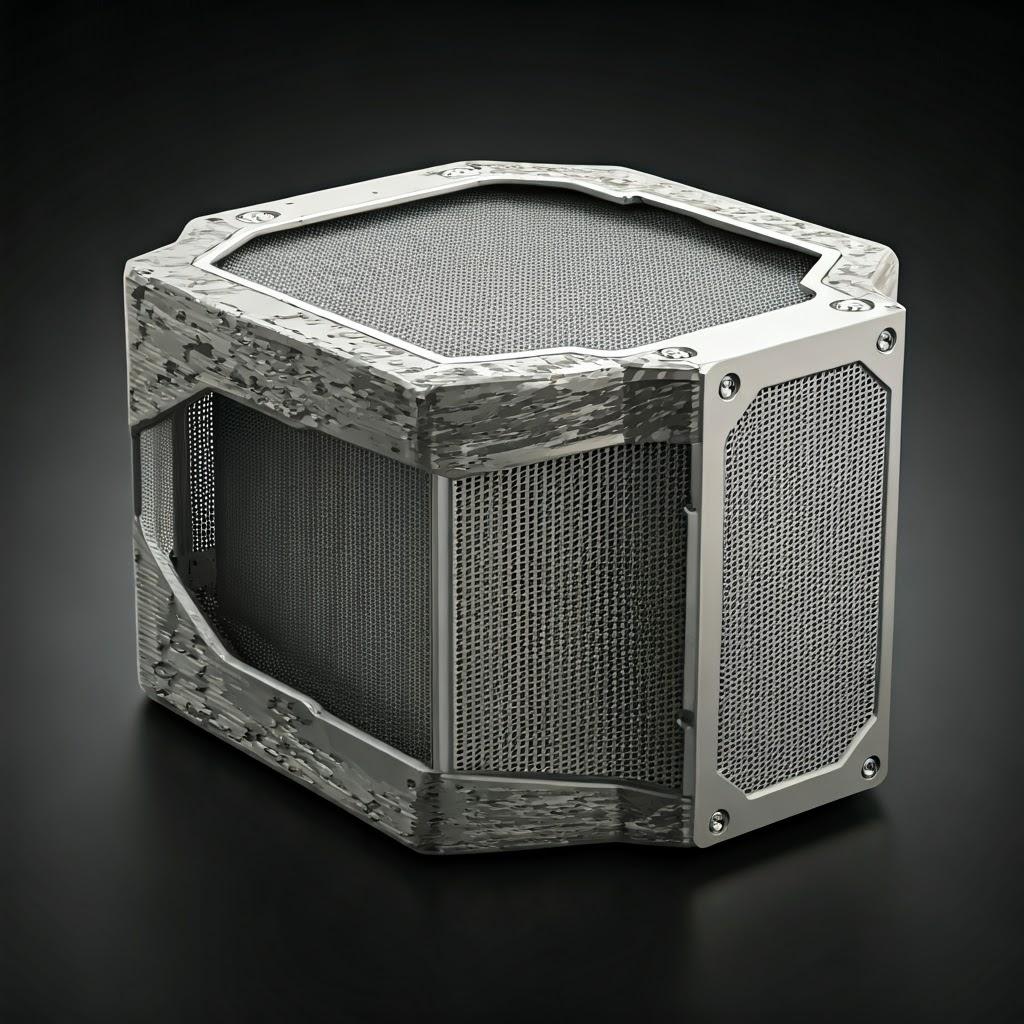
Essential Post-Processing for Durable and Functional Enclosures
While metal 3D printing produces near-net-shape parts, post-processing steps are often necessary to achieve the desired final properties, surface finish, and functionality of custom electronics enclosures. Common post-processing requirements include:
- Retirada de la estructura de soporte: Support structures are often required to prevent collapse or distortion during the printing process, especially for complex geometries with overhangs. These structures need to be carefully removed after printing, which can be a manual or automated process depending on the design and material.
- Tratamiento térmico antiestrés: To alleviate internal stresses that may have built up during the rapid heating and cooling cycles of the 3D printing process, a stress relief heat treatment is often performed. This improves the mechanical properties and dimensional stability of the enclosure.
- Acabado superficial: Depending on the application requirements, various surface finishing techniques can be employed to improve the aesthetic appearance, corrosion resistance, or functionality of the enclosure. These can include:
- Granallado: To achieve a uniform matte finish and remove minor surface imperfections.
- Pulido: To obtain a smooth, reflective surface, often required for aesthetic or functional reasons.
- Painting or Coating: To provide additional corrosion protection, electrical insulation, or a specific color.
- Mecanizado CNC: For critical features requiring very tight tolerances, such as mounting holes or connector interfaces, CNC machining can be used as a secondary operation to achieve the desired precision.
- Heat Treatment for Enhanced Properties: Depending on the material and application, further heat treatments can be performed to enhance specific mechanical properties such as hardness or strength. For example, age hardening of AlSi10Mg can significantly increase its strength.
- Inspección y control de calidad: Thorough inspection using techniques such as coordinate measuring machines (CMM) or non-destructive testing (NDT) is essential to ensure that the final enclosure meets the required dimensional accuracy and quality standards.
Metal3DP offers a comprehensive suite of post-processing services to ensure that your 3D printed custom electronics enclosures meet the most demanding specifications. Our expertise in material science and manufacturing processes allows us to tailor the post-processing steps to optimize the performance and durability of your parts.
Overcoming Common Challenges in Metal 3D Printing of Enclosures
While metal 3D printing offers numerous advantages, there are also potential challenges that need to be addressed to ensure successful fabrication of custom electronics enclosures:
- Deformación y distorsión: Thermal stresses during the printing process can lead to warping or distortion of the part, especially for large or thin-walled enclosures. Optimizing build orientation, using appropriate support structures, and controlling process parameters can mitigate these issues.
- Porosidad: Internal porosity can affect the mechanical strength and hermeticity of the enclosure. Ensuring the use of high-quality metal powders and optimizing the printing parameters to achieve full density are crucial. Metal3DP’s advanced powder making system ensures the high quality and density of our metal powders.
- Rugosidad superficial: As-printed metal parts typically have a rougher surface finish compared to machined parts. Depending on the application, post-processing steps may be required to achieve a smoother surface.
- Dificultades para retirar la estructura de soporte: Removing support structures from complex internal features or delicate geometries can be challenging and may leave surface artifacts. Careful design and selection of appropriate support strategies are essential.
- Material Property Variations: Achieving consistent material properties throughout the printed part can be challenging. Optimizing process parameters and ensuring proper atmospheric control during printing are crucial for homogeneity.
- Cost Considerations for Low Volumes: While metal 3D printing can be cost-effective for complex geometries and low to medium volumes, the initial investment in equipment and materials can be higher than traditional methods for very high volumes of simple parts. However, the benefits of customization and rapid iteration often outweigh this for specialized enclosures.
By understanding these potential challenges and working with an experienced metal 3D printing service provider like Metal3DP, which possesses the expertise in process optimization, material selection, and post-processing techniques, you can effectively overcome these hurdles and realize the full potential of metal 3D printing for your custom electronics enclosure needs.
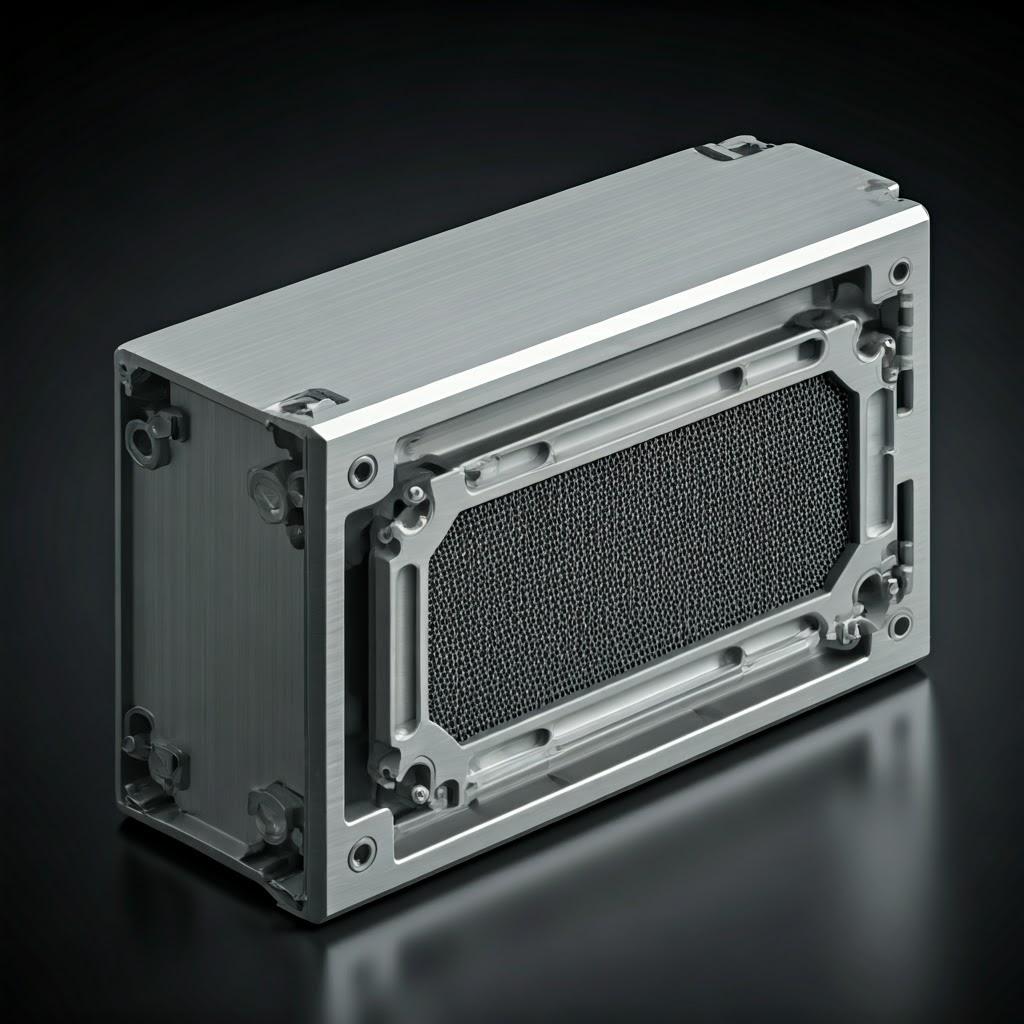
Selecting a Reliable Metal 3D Printing Service Provider for Your Enclosure Needs
Choosing the right metal 3D printing service provider is crucial for the success of your custom electronics enclosure project. A reliable partner will possess the expertise, equipment, and quality control processes necessary to deliver high-performance parts that meet your specific requirements. Here are key factors to consider when evaluating potential suppliers:
- Capacidades de los materiales: Ensure the provider offers the materials suitable for your application, such as AlSi10Mg and 316L, and has experience processing them. Metal3DP boasts a comprehensive portfolio of high-quality metal powders, including these and other advanced alloys.
- Tecnología y equipamiento: The type of metal 3D printing technology employed by the service provider can significantly impact the accuracy, surface finish, and material properties of the final part. Metal3DP utilizes advanced Selective Electron Beam Melting (SEBM) technology, known for its accuracy and ability to produce dense, high-quality metal parts.
- Design and Engineering Support: An experienced service provider should offer design consultation and engineering support to optimize your enclosure design for additive manufacturing, ensuring manufacturability and performance. Our team at Metal3DP has decades of collective expertise in metal additive manufacturing and can provide valuable insights throughout the design process.
- Post-Processing Services: Determine if the provider offers the necessary post-processing services, such as support removal, heat treatment, surface finishing, and CNC machining, to meet your final part specifications. Metal3DP provides comprehensive post-processing solutions to ensure your enclosures are delivered ready for integration.
- Quality Assurance and Certifications: Inquire about the provider’s quality management system and any relevant certifications (e.g., ISO 9001, AS9100 for aerospace). Robust quality control processes are essential for ensuring the reliability and consistency of the printed enclosures.
- Lead Times and Production Capacity: Understand the provider’s typical lead times for similar projects and their production capacity to ensure they can meet your project timelines and volume requirements.
- Communication and Customer Support: Effective communication and responsive customer support are vital for a smooth and successful collaboration. Choose a provider that is proactive, transparent, and dedicated to understanding your needs.
By carefully evaluating these factors, you can select a metal 3D printing service provider like Metal3DP that will be a valuable partner in bringing your custom electronics enclosure designs to fruition.
Comprensión de los factores de costo y los plazos de entrega para las carcasas impresas en 3D
The cost and lead time for manufacturing custom electronics enclosures using metal 3D printing are influenced by several factors. Understanding these drivers can help you plan your project effectively:
- Coste del material: The type and quantity of metal powder used directly impact the cost. Materials like 316L are generally more expensive than AlSi10Mg. Optimizing the design to minimize material usage, while maintaining structural integrity, can help control costs.
- Build Volume and Complexity: Larger and more complex enclosures that require more build time and support structures will generally be more expensive. The height of the part in the build direction also affects the build time and thus the cost.
- Requisitos de postprocesamiento: The extent of post-processing required, such as extensive machining or specialized coatings, will add to the overall cost and lead time. Designing for minimal post-processing can be a cost-saving strategy.
- La hora de las máquinas: The duration of the printing process itself contributes to the cost. This is influenced by the size and complexity of the part, as well as the layer height and scanning speed used.
- Cantidad: While metal 3D printing can be cost-effective for low to medium volumes and highly complex parts, the unit cost may not be as competitive as traditional methods for very high volumes of simple geometries. However, factors like tooling costs and design flexibility often make 3D printing a compelling option even for moderate volumes.
- Service Provider’s Pricing Structure: Different service providers have varying pricing models. It’s essential to obtain clear and detailed quotes that outline all costs involved, including material, printing, post-processing, and any design or engineering fees.
Lead times for metal 3D printed enclosures can vary depending on the complexity of the part, the chosen material, the service provider’s workload, and the required post-processing. Simple enclosures might be produced in a few days, while more complex parts requiring extensive post-processing could take several weeks. It’s crucial to discuss lead times upfront with your chosen provider, such as Metal3DP, to align expectations with your project schedule.
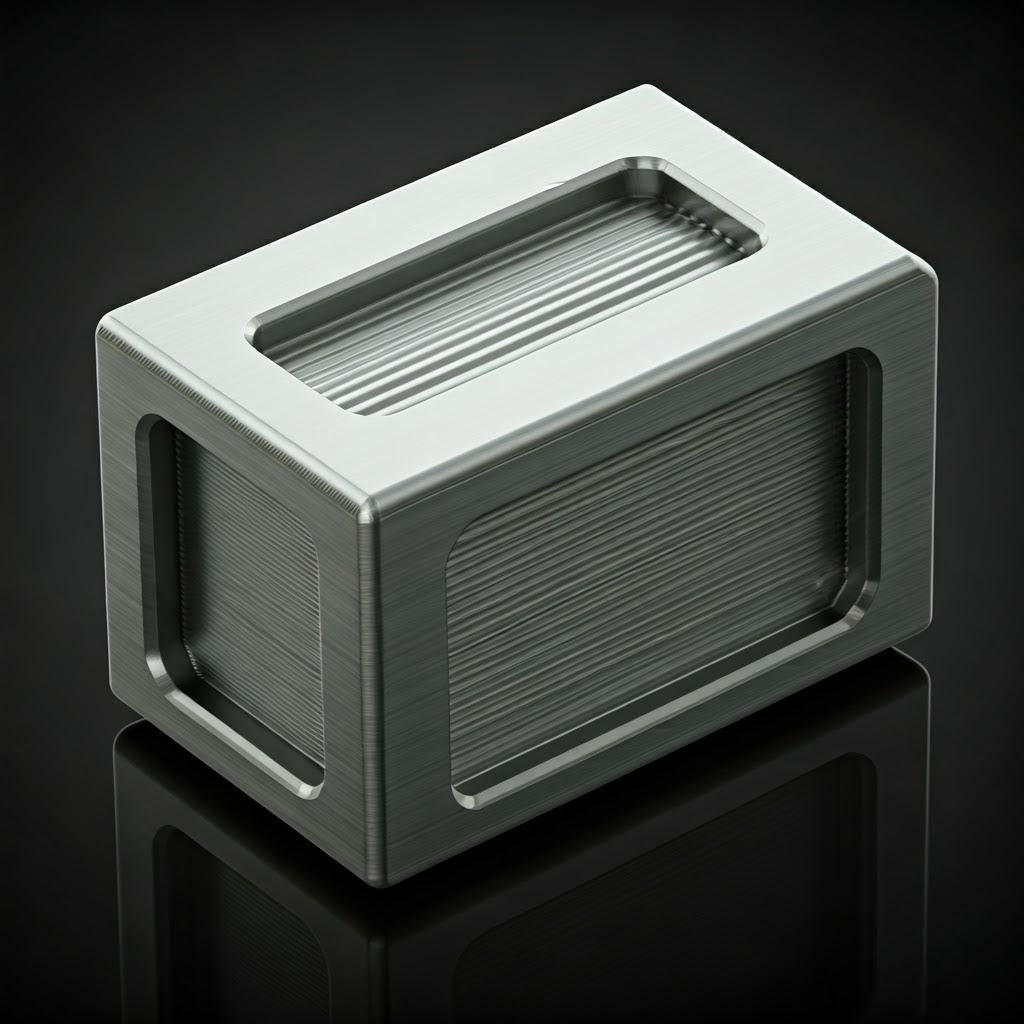
Frequently Asked Questions (FAQ) About Metal 3D Printed Enclosures
Here are some common questions engineers and procurement managers have regarding metal 3D printed electronics enclosures:
- Q: What are the typical tolerances achievable with metal 3D printing for enclosures? A: Typical tolerances range from ±0.1mm to ±0.05mm, depending on the part geometry, size, and the specific printing process and material used by the service provider like Metal3DP. Tighter tolerances can be achieved through post-processing like CNC machining.
- Q: Can metal 3D printed enclosures provide adequate shielding against electromagnetic interference (EMI)? A: Yes, metal materials inherently offer good EMI shielding properties. The effectiveness of the shielding depends on the material’s conductivity and the enclosure’s design, including wall thickness and the presence of any gaps or seams. Specific EMI shielding requirements should be discussed with your service provider.
- Q: Is metal 3D printing cost-effective for producing custom electronics enclosures in low volumes? A: Yes, metal 3D printing can be highly cost-effective for low to medium volumes of custom enclosures, especially those with complex geometries that would be expensive or impossible to produce using traditional methods involving tooling. It eliminates the upfront costs and lead times associated with mold creation.
Conclusion: Empowering Electronics with Advanced 3D Printed Enclosure Solutions
Metal 3D printing has emerged as a transformative technology for the design and manufacture of custom electronics enclosures. Its ability to unlock design freedom, enable rapid prototyping, and produce functional parts with tailored material properties like those offered by AlSi10Mg and 316L makes it an invaluable tool for engineers and procurement managers across diverse industries. By partnering with a reliable and experienced metal 3D printing service provider like Metal3DP, you can leverage our advanced SEBM technology, comprehensive material portfolio, and expert support to create high-performance, custom electronics enclosures that meet the unique demands of your applications. Embrace the power of metal additive manufacturing and unlock new possibilities for your electronic innovations. Contact Metal3DP today to explore how our capabilities can empower your organization’s additive manufacturing goals.
Compartir
MET3DP Technology Co., LTD es un proveedor líder de soluciones de fabricación aditiva con sede en Qingdao, China. Nuestra empresa está especializada en equipos de impresión 3D y polvos metálicos de alto rendimiento para aplicaciones industriales.
Solicite información para obtener el mejor precio y una solución personalizada para su empresa.
Artículos relacionados
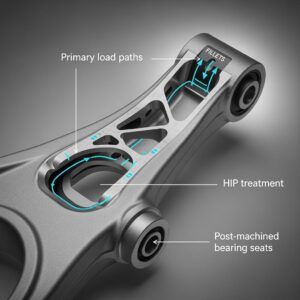
Metal 3D Printing for U.S. Automotive Lightweight Structural Brackets and Suspension Components
Leer Más "Acerca de Met3DP
Actualización reciente
Nuestro producto
CONTACTO
¿Tiene alguna pregunta? ¡Envíenos un mensaje ahora! Atenderemos su solicitud con todo un equipo tras recibir su mensaje.