End Cap Components for Motors 3D Printed in Aluminum
Índice
Introduction: Revolutionizing Motor Design with 3D Printed Aluminum End Caps
The electric motor, a cornerstone of modern industry and technology, is undergoing a quiet revolution. While the fundamental principles remain, the demand for higher efficiency, greater power density, reduced weight, and application-specific customization is driving innovation in every component. Among these critical parts are the motor end caps – often overlooked, yet essential for structural integrity, bearing support, environmental protection, and thermal management. Traditionally manufactured through methods like casting or machining, end caps are now prime candidates for the transformative capabilities of fabricación aditiva (AM) de metales, particularly using lightweight and versatile aluminum alloys. This shift isn’t just about adopting a new production technique; it’s about unlocking unprecedented design possibilities and performance levels previously unattainable. Imagine motor end caps not just as passive structural elements, but as highly engineered components with intricate internal cooling channels, optimized geometries for minimal weight, and features consolidated to simplify assembly – all made possible through aluminio Impresión 3D.
Electric motor end caps, also known as end shields or bearing housings, serve multiple crucial functions. They precisely locate and support the motor shaft bearings, maintain the correct air gap between the rotor and stator, provide mounting points for the motor assembly, and seal the motor internals from contaminants like dust and moisture. In many designs, they also play a role in heat dissipation, conducting thermal energy away from the bearings and windings. The performance demands on these components are significant; they must withstand operational loads, vibrations, thermal cycling, and environmental exposure while maintaining tight tolerances for bearing fits and alignment.
For decades, die casting and CNC machining have been the go-to methods for producing end caps. Casting offers cost-effectiveness for high volumes but often entails significant tooling investment, longer lead times for initial production, and limitations in geometric complexity and achievable thin walls. Porosity can also be a concern in cast parts, potentially impacting structural integrity or sealing. CNC machining, while capable of high precision and good material properties, is inherently subtractive, leading to material waste, and can be time-consuming and costly for complex geometries or low-to-mid-volume runs.
Enter metal additive manufacturing, specifically Laser Powder Bed Fusion (LPBF), often referred to as Selective Laser Melting (SLM) or Direct Metal Laser Sintering (DMLS). This technology builds parts layer by layer directly from a fine metal powder, guided by a digital CAD model. When applied to motor end caps using high-performance aluminum alloys like AlSi10Mg y A6061, AM opens a new frontier.
Why Aluminum? Aluminum alloys are highly attractive for motor applications due to their excellent thermal conductivity (crucial for heat dissipation), low density (enabling significant component lightweighting), good corrosion resistance, and favorable strength-to-weight ratio. Combining these material benefits with the geometric freedom of 3D printing allows engineers to:
- Integrate Complex Features: Design intricate internal cooling channels precisely following heat-generating zones, drastically improving thermal management and potentially increasing motor power density or lifespan.
- Optimize for Weight: Utilize topology optimization algorithms and lattice structures to remove material from low-stress areas, creating end caps that are significantly lighter than their traditionally manufactured counterparts without sacrificing stiffness or strength. This is particularly critical in automoción (especially EVs) and aeroespacial applications where every gram matters.
- Consolidate Parts: Combine multiple functions or adjacent components into a single printed end cap, reducing part count, simplifying assembly, and minimizing potential failure points.
- Enable Rapid Prototyping & Customization: Quickly produce and test different end cap designs, accelerating development cycles. AM also makes low-volume production of customized end caps for specialized automatización industrial o robótica applications economically viable.
This blog post delves into the specifics of leveraging aluminum 3D printing for electric motor end caps. We will explore the core functions and diverse applications, dissect the compelling advantages AM offers over traditional methods, compare the recommended aluminum alloys (AlSi10Mg y A6061), and provide insights into design considerations, achievable precision, post-processing requirements, and potential challenges. Furthermore, we will guide procurement managers and engineers in selecting the right B2B manufacturing partner and understanding the cost and lead time implications. Whether you are developing next-generation EV powertrains, advanced aerospace actuators, or highly specialized industrial machinery, understanding the potential of 3D printed aluminum end caps is crucial for staying ahead in the competitive landscape. Companies seeking reliable wholesale motor parts suppliers or fabricación bajo demanda solutions for specialized components will find AM offers compelling flexibility and performance benefits. Partnering with an experienced provider like Met3dp, with its deep expertise in impresión 3D en metal and high-quality powder production, can unlock the full potential of this technology for your motor applications.
Core Functions & Applications: Where are 3D Printed Aluminum End Caps Used?
The seemingly simple motor end cap performs a surprising number of critical functions vital to the motor’s overall performance, reliability, and longevity. Understanding these roles clarifies why optimizing their design and manufacturing process through technologies like aluminum 3D printing offers such significant potential.
Core Functions of Motor End Caps:
- Bearing Support and Alignment: This is perhaps the most critical function. End caps house the motor bearings (typically ball or roller bearings) that support the rotating shaft (rotor). They must provide a precise, rigid mounting surface (the bearing seat or bore) to ensure the bearings are correctly aligned, minimizing friction, wear, and vibration. Misalignment can lead to premature bearing failure, increased noise, and reduced motor efficiency. The precision required for bearing seats often necessitates post-machining, even on 3D printed parts.
- Maintaining Rotor-Stator Air Gap: The end caps, in conjunction with the motor housing, define the precise axial and radial position of the rotor relative to the stator. Maintaining the designed air gap is critical for electromagnetic performance. An inconsistent or incorrect air gap leads to efficiency losses, torque ripple, and potential rotor-stator contact.
- Structural Integrity: End caps contribute significantly to the overall structural rigidity of the motor assembly. They must withstand forces generated during operation, including torque reactions, vibration, and any external loads if the motor is part of a larger structure. They essentially “cap” the motor housing, tying the stator core and housing together.
- Sealing and Environmental Protection: End caps prevent contaminants such as dust, dirt, moisture, and chemicals from entering the sensitive internal components of the motor (windings, rotor, bearings). They often incorporate features for seals (like O-ring grooves or lip seal surfaces) or are designed for tight interference fits with the motor housing. The level of sealing required (e.g., IP rating) depends heavily on the operating environment.
- Heat Dissipation: Motors generate heat during operation, primarily from electrical losses in the windings (I²R losses) and iron losses in the core, as well as frictional losses in the bearings. End caps, particularly those made from thermally conductive materials like aluminum, help dissipate this heat to the surrounding environment. They conduct heat away from the bearings and contribute to overall thermal management, preventing overheating which can damage insulation and reduce motor life. AM allows for the integration of cooling fins or internal channels to dramatically enhance this function.
- Mounting and Interface: End caps often provide mounting features (flanges, tapped holes, feet) for installing the motor onto machinery or equipment. They serve as the primary interface between the motor and the system it drives.
Given these critical functions, the applications for high-performance end caps, especially those benefiting from the advantages of aluminum 3D printing, are diverse and span numerous demanding industries.
Applications Across Industries:
- Automoción (especialmente vehículos eléctricos): The drive towards lighter, more powerful, and efficient electric powertrains makes aluminum AM ideal for EV motor end caps.
- Aligeramiento: Reducing the mass of components like end caps directly contributes to extending vehicle range and improving handling dynamics. Topology optimization can yield significant weight savings.
- Gestión térmica: Higher power density motors generate more heat. 3D printed end caps with integrated, complex cooling channels (using liquid or air) can manage this heat more effectively than traditional designs, allowing motors to run harder or enabling more compact motor designs.
- Creación rápida de prototipos: AM allows automotive engineers to quickly iterate on motor designs during the R&D phase.
- Personalización: Facilitates the production of end caps for specialized or low-volume performance vehicle motors. B2B suppliers focusing on the EV market can leverage AM for niche component requirements.
- Aeroespacial: Weight reduction is paramount in aerospace applications, making aluminum AM a natural fit for components like end caps in actuators, generators, pumps, and environmental control systems.
- Extreme Lightweighting: Every kilogram saved translates to fuel efficiency or increased payload capacity. AM enables highly optimized, lightweight end cap designs impossible to manufacture conventionally.
- Alto rendimiento: Aerospace components often operate in demanding environments requiring robust performance and reliability. AM allows for designs optimized for specific load cases and thermal conditions.
- Geometrías complejas: Integration of cooling features, sensor mounts, or fluid passages directly into the end cap structure reduces part count and potential leak paths.
- Opciones de material: While aluminum is common, aerospace might also explore titanium alloys (using technologies like Electron Beam Melting, where Met3dp also has expertise) for specific high-temperature or high-strength requirements, though aluminum remains key for many motor applications.
- Industrial Automation and Machinery: This broad sector includes everything from factory robots to CNC machines, pumps, and conveyor systems. AM offers benefits for both standard and custom motor solutions.
- Personalización: Manufacturing specialized end caps for unique machine requirements or environmental conditions (e.g., food-grade, washdown) becomes more feasible, even in lower volumes. Wholesale motor parts distributors can partner with AM providers to offer tailored solutions.
- Mejora del rendimiento: Integrating cooling features can allow standard motor frames to operate at higher duty cycles or in hotter environments.
- Replacement Parts: On-demand production of obsolete or hard-to-find end caps for legacy machinery, minimizing downtime.
- Noise/Vibration Reduction: Optimized structural design through AM could potentially lead to end caps that help dampen motor vibration and noise.
- Robótica: Particularly in collaborative robots (cobots) and mobile robotics, low weight and high power density are critical.
- Compact & Lightweight Joints: 3D printed aluminum end caps contribute to lighter, more agile robotic arms and mobile platforms.
- Integrated Features: End caps can be designed to incorporate mounting points for encoders, brakes, or other joint components, simplifying the overall robot design.
- Thermal Performance: Efficient heat removal is essential for actuators operating continuously within confined spaces.
- Productos sanitarios: While perhaps less common than in other sectors, specific medical equipment utilizing motors (e.g., surgical tools, pumps, diagnostic equipment) might benefit from the design freedom and material properties offered by AM.
- Biocompatibility (if needed): While standard aluminum alloys may not be suitable for direct implantable use, specific alloys or coatings can be considered for external device components. Titanium alloys are more common for implantable applications.
- Miniaturization: AM can potentially enable the production of very small, complex end caps for miniaturized medical motors.
- Research and Development / Prototyping: Across all sectors, AM provides an unparalleled tool for rapidly prototyping and testing new motor concepts. Different end cap designs with varying bearing arrangements, sealing methods, or cooling strategies can be produced and evaluated quickly and cost-effectively compared to tooling up for casting or complex machining setups.
In essence, 3D printed aluminum end caps are particularly well-suited for applications demanding:
- Alto rendimiento: Where enhanced thermal management or structural optimization is needed.
- Low Weight: Critical for mobile, aerial, or performance-driven systems.
- Geometría compleja: When integrated features like cooling channels, unique mounting points, or non-standard shapes are required.
- Personalización: For bespoke motor designs or low-volume production runs.
- Rapid Development: When speed in prototyping and iteration is essential.
As the technology matures and costs continue to evolve, the scope of applications is expected to broaden further, making aluminum AM a standard tool in the motor designer’s arsenal, supported by capable proveedores de servicios de metal AM y proveedores de polvo de metal like Met3dp.
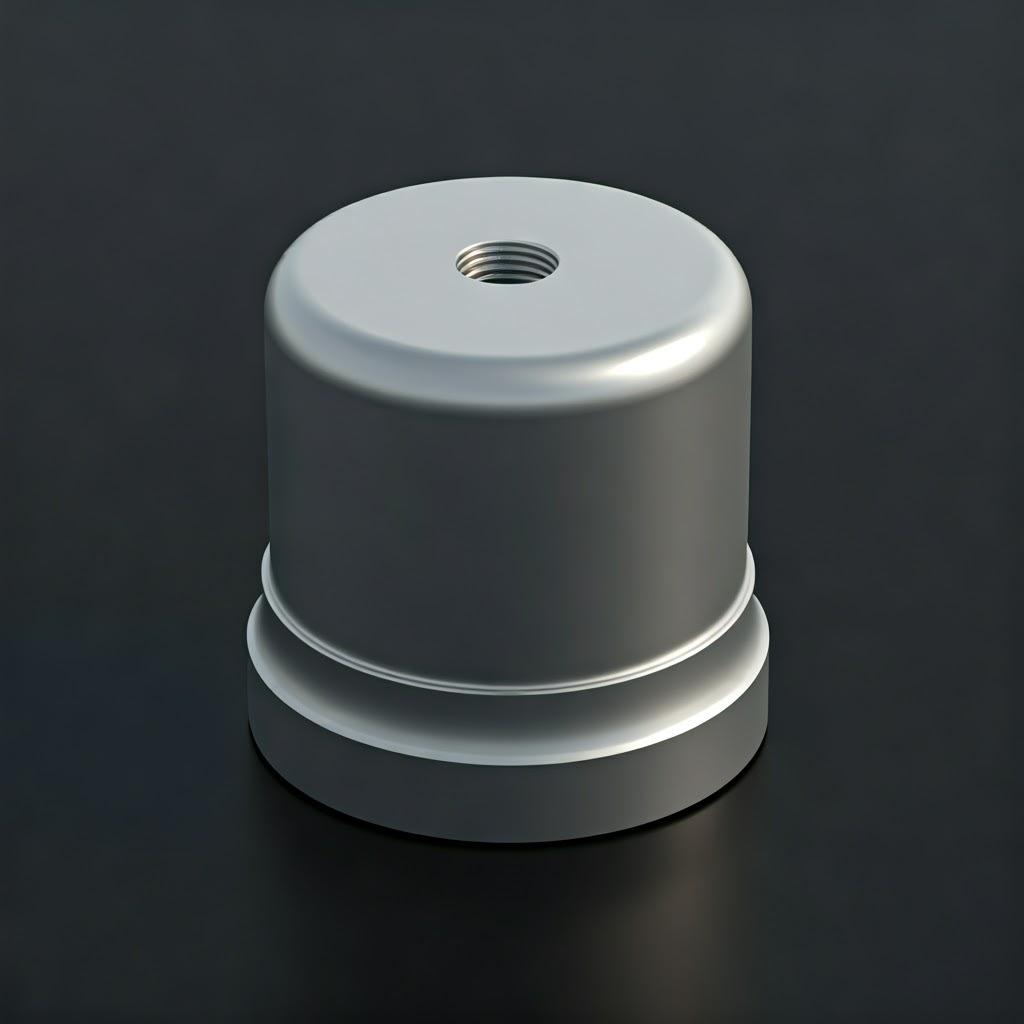
The Additive Advantage: Why Metal 3D Printing for Motor End Caps?
While traditional manufacturing methods like casting and CNC machining have served the industry well for producing motor end caps, metal additive manufacturing (AM), specifically using aluminum alloys via Laser Powder Bed Fusion (LPBF), offers a suite of compelling advantages that address the growing demands for higher performance, lighter weight, and greater design flexibility. Choosing AM isn’t just about replacing an old process with a new one; it’s about enabling designs and production strategies that were previously impossible or impractical. Let’s compare AM with traditional methods and highlight its key benefits for motor end cap production.
Traditional Methods vs. Metal AM:
- Fundición a presión:
- Pros: Excellent for very high volumes, relatively low part cost at scale, good surface finish.
- Contras: Extremely high initial tooling costs, long lead times for tool creation (months), design limitations (draft angles required, difficulty with complex internal features, minimum wall thickness constraints), potential for porosity, design changes are expensive and time-consuming.
- Sand Casting:
- Pros: Lower tooling costs than die casting, suitable for larger parts and complex shapes (to an extent), good for prototypes or low volumes.
- Contras: Poorer surface finish and dimensional accuracy (often requires significant machining), slower cycle times than die casting, limitations on thin walls and intricate details.
- CNC Machining (from Billet/Stock):
- Pros: High precision and accuracy, excellent material properties (wrought or forged stock), no tooling costs, good for prototypes and low-to-mid volumes, design changes are relatively easy to implement.
- Contras: Can be slow and costly for complex geometries, significant material waste (subtractive process), limitations on internal features (tool access), cost increases significantly with complexity.
- Metal Additive Manufacturing (LPBF):
- Pros: Unprecedented libertad de diseño for complex geometries (internal channels, lattices), enables aligeramiento through topology optimization, ideal for part consolidation, prototipado rápido and iteration, no tooling costs, efficient material usage (additive process), facilitates fabricación bajo demanda and customization, potential for improved performance (e.g., thermal management).
- Contras: Can have higher per-part cost compared to high-volume casting, typically requires post-processing (heat treatment, support removal, machining for critical surfaces), surface finish may be rougher than machining (as-printed), build sizes can be limited by machine volume, requires specialized design knowledge (DfAM).
Key Advantages of Metal AM for Motor End Caps:
- Unmatched Design Freedom & Complexity: This is arguably the most significant advantage. AM builds parts layer by layer, freeing designers from the constraints imposed by molding, casting, or tool access in machining.
- Integrated Cooling Channels: Designers can create intricate, conformal cooling channels that precisely follow the heat sources within the end cap (like bearing seats) or maximize surface area for air cooling. This leads to vastly superior thermal management compared to simple fins or solid caps, enabling higher power density or improved reliability.
- Optimized Internal Structures: Features like internal ribbing or honeycombs can be designed for maximum stiffness with minimal material usage.
- Consolidación de piezas: Brackets, sensor mounts, cable guides, or even elements of the motor housing could potentially be integrated directly into the end cap design, reducing the total number of parts in the motor assembly. This simplifies logistics for Proveedores B2B, reduces assembly time and cost, and eliminates potential failure points or tolerance stack-up issues.
- Significant Lightweighting Potential: AM paired with computational design tools enables dramatic weight reduction.
- Optimización de la topología: Software analyzes the stress distribution within the end cap under operational loads and removes material from non-critical areas, leaving behind an organic-looking, highly efficient load-bearing structure.
- Estructuras reticulares: Internal lattice or gyroid structures can replace solid material, providing good structural support and stiffness at a fraction of the weight.
- Beneficio: This is crucial for automotive (EV), aeroespacialy robótica applications, improving overall system efficiency, range, or payload capacity.
- Accelerated Prototyping and Development (Rapid Prototyping): AM allows engineers to move from a CAD design to a physical metal prototype in days rather than the weeks or months required for casting tooling.
- Faster Iteration: Multiple design variations (e.g., different cooling channel layouts, bearing fits, mounting options) can be printed and tested quickly.
- Reduced Development Costs: Problems can be identified and fixed early in the design cycle, avoiding costly rework later.
- Tiempo de comercialización más rápido: Products can be developed and launched more quickly.
- Eficiencia material y reducción de residuos: As an additive process, LPBF typically uses only the material necessary to build the part and its support structures.
- Sostenibilidad: Compared to CNC machining, which can waste a significant percentage of the initial material block as chips, AM is inherently less wasteful. While powder recycling is crucial, the buy-to-fly ratio is generally much better.
- Cost Savings (Material): Especially relevant for more expensive alloys (though aluminum is relatively cost-effective), using less raw material can impact overall cost.
- On-Demand Manufacturing & Supply Chain Flexibility: AM eliminates the need for physical tooling, making it ideal for flexible production scenarios.
- Personalización: Producing unique end cap designs for specific customer requirements or niche applications becomes economically viable, even at low volumes.
- Piezas de repuesto: Legacy or obsolete end caps can be produced on-demand from digital files, reducing the need for large inventories of physical spares. This is a significant advantage for wholesale distributors and maintenance operations.
- Decentralized Production: Parts can potentially be printed closer to the point of need, shortening supply chains.
- Potential for Enhanced Performance: The ability to create optimized geometries directly translates to improved motor performance.
- Better Cooling: Leads to higher power output, longer motor life, or more compact designs.
- Improved Structural Integrity: Optimized designs can be stiffer or stronger where needed, potentially improving bearing life or reducing vibration.
While AM presents a paradigm shift with numerous benefits, it’s important to acknowledge the need for expertise in Design for Additive Manufacturing (DfAM) and careful consideration of post-processing requirements to achieve the desired tolerances and material properties. Partnering with an experienced metal AM service provider like Met3dp, who possesses not only advanced printing technology but also deep materials science knowledge and robust process control, is key to successfully leveraging the additive advantage for demanding applications like electric motor end caps. Met3dp’s focus on industry-leading accuracy and reliability ensures that the potential benefits of AM are realized in the final producto.
Material Focus: AlSi10Mg vs. A6061 for Optimal Motor End Cap Performance
Choosing the right material is fundamental to the success of any engineering component, and 3D printed motor end caps are no exception. Aluminum alloys are often the preferred choice due to their favorable combination of low density, good thermal conductivity, adequate strength, and corrosion resistance. Within the realm of aluminum alloys suitable for Laser Powder Bed Fusion (LPBF), two stand out as common and effective options for applications like motor end caps: AlSi10Mg y A6061. While both are aluminum-based, their specific alloying elements (Silicon and Magnesium in AlSi10Mg; Magnesium and Silicon in A6061, along with Chromium and Copper) impart distinct properties that make them suitable for different operational requirements. Understanding these differences is crucial for selecting the optimal material for your specific motor design.
Introduction to the Alloys:
- AlSi10Mg: This is one of the most widely used aluminum alloys in additive manufacturing. It’s essentially a casting alloy composition adapted for LPBF. The relatively high silicon content (around 10%) provides excellent fluidity in the melt pool during printing, leading to good printability with fewer defects like cracking. It generally exhibits good strength, hardness, and dynamic load resistance in the as-built and heat-treated conditions. Its casting heritage means it flows well during the layer-by-layer fusion process.
- A6061 (or variants like 6061-RAM2): A6061 is a precipitation-hardening aluminum alloy, traditionally known and widely used in wrought forms (extrusions, plates) for its good mechanical properties, excellent corrosion resistance, and good weldability. Adapting it for LPBF has been more challenging than AlSi10Mg due to its wider solidification range, which can make it more susceptible to hot cracking during printing. However, specialized variants (like Scalmalloy® or specific parameter sets for standard 6061) and robust process control have made its reliable printing feasible. Its key advantage lies in its excellent mechanical properties, particularly ductility and fracture toughness, especially after appropriate heat treatment (like T6). 6061-RAM2 is a specific LPBF-optimized variant containing Copper and Zirconium additions to improve printability and high-temperature performance.
Property Comparison: AlSi10Mg vs. A6061 (Typical LPBF Properties)
The following table provides a general comparison. Note that exact values can vary significantly based on the specific LPBF machine, process parameters, powder quality, build orientation, and post-processing (especially heat treatment). Values are often presented for the heat-treated condition (e.g., T6 for 6061, stress relief or other treatments for AlSi10Mg) as this is common for optimizing mechanical properties.
Propiedad | AlSi10Mg (Heat Treated) | A6061 / Variants (T6 Heat Treated) | Significance for Motor End Caps |
---|---|---|---|
Imprimibilidad | Excelente | Good to Very Good (with optimized parameters) | AlSi10Mg is generally easier to print defect-free, potentially leading to lower costs/faster prints. |
Tensile Strength (UTS) | 330 - 450 MPa | 290 – 350 MPa | Both offer good strength, sufficient for most end cap structural loads. AlSi10Mg can be stronger. |
Límite elástico | 230 – 300 MPa | 240 – 310 MPa | Similar yield strengths, indicating resistance to permanent deformation. |
Alargamiento a la rotura | 3 – 10% | 8 – 15% | A6061 generally offers significantly better ductility, making it tougher and less brittle. |
Dureza (Brinell) | 90 – 120 HBW | 90 – 105 HBW | Similar hardness, indicating good wear resistance for bearing seats (though coatings help). |
Densidad | ~2,67 g/cm³ | ~2,70 g/cm³ | Both are lightweight; difference is negligible. |
Conductividad térmica | 120 – 180 W/m·K | 150 – 180 W/m·K | Both offer good thermal conductivity for heat dissipation. A6061 might have a slight edge. |
Resistencia a la corrosión | Bien | Excelente | A6061 generally has superior corrosion resistance, important for harsh environments. |
Tratamiento térmico | Typically stress relief; T6 possible but less common | Standard T6 tempering is very effective | A6061 responds very well to standard T6 heat treatment to achieve optimal properties. |
Soldabilidad | Fair (can be tricky due to Si content) | Bien | Relevant if post-print welding modifications are ever needed (rare for end caps). |
Typical Application | General purpose, complex geometries, castings | Higher toughness needs, corrosion resistance | AlSi10Mg often chosen for ease of printing complex parts; A6061 for toughness & environment. |
Exportar a hojas
Choosing the Right Alloy for Your Motor End Cap:
The decision between AlSi10Mg and A6061 depends heavily on the specific performance priorities for the motor:
- Choose AlSi10Mg if:
- The design involves extremely complex geometries where ease of printing is paramount.
- High strength is the primary driver, and slightly lower ductility is acceptable.
- The operating environment is relatively benign regarding corrosion.
- Cost sensitivity is high (it might be slightly cheaper due to easier processing).
- Rapid prototyping where achieving final T6 properties isn’t immediately critical.
- Choose A6061 (or variants) if:
- Higher ductility and fracture toughness are required (e.g., resistance to impact or high vibration).
- Superior corrosion resistance is needed due to the operating environment (e.g., marine, chemical exposure, outdoor).
- The component requires properties closely matching traditional wrought 6061-T6 specifications.
- Optimal thermal conductivity is a critical design factor.
- You are working with a supplier (like Met3dp) experienced in reliably printing A6061 with optimized parameters and appropriate heat treatment protocols.
La importancia de los polvos metálicos de alta calidad:
Regardless of the alloy chosen, the quality of the raw material – the metal powder – is critical for achieving consistent, high-quality results in LPBF. The powder characteristics directly impact the printing process and the final part’s properties. Key powder attributes include:
- Esfericidad: Highly spherical powder particles flow better, leading to uniform powder bed density and consistent melting.
- Distribución del tamaño de las partículas (PSD): A controlled PSD ensures good packing density and predictable melting behavior. Fines can cause issues, while overly large particles may not melt completely.
- Fluidez: Good flowability (measured by Hall flow rate or similar) is essential for evenly spreading thin powder layers.
- Purity/Chemistry: The powder must meet strict chemical composition standards for the alloy, with low levels of impurities (especially oxygen and nitrogen) that can degrade mechanical properties.
- Low Porosity: Gas trapped within powder particles (internal porosity) can transfer to the final part, creating defects.
This is where partnering with a company like Met3dp provides a distinct advantage. Met3dp not only offers servicios de impresión 3D de metal but also specializes in manufacturing high-performance metal powders. Utilizing industry-leading gas atomization and Plasma Rotating Electrode Process (PREP) technologies, Met3dp produces metallic powders with high sphericity, excellent flowability, controlled PSD, and high purity. Their unique gas atomization nozzle and flow design are specifically engineered to create powders optimized for AM processes like LPBF. While their portfolio includes advanced materials like Titanium alloys (TiNi, TiTa, TiAl, TiNbZr), superalloys, and specialized steels (CoCrMo), their expertise extends to producing high-quality aluminum powders like AlSi10Mg and ensuring reliable printing processes for alloys like A6061. By controlling the powder production process, Met3dp ensures a consistent and high-quality feedstock, which is the foundation for printing dense, reliable aluminum end caps with superior mechanical and thermal properties, meeting the stringent demands of the aerospace, automotive, medical, and industrial sectors. Choosing a partner with vertically integrated capabilities from powder production to finished part offers greater control and confidence in the final component quality. Consider exploring Met3dp’s comprehensive product offerings for both powders and printing solutions.
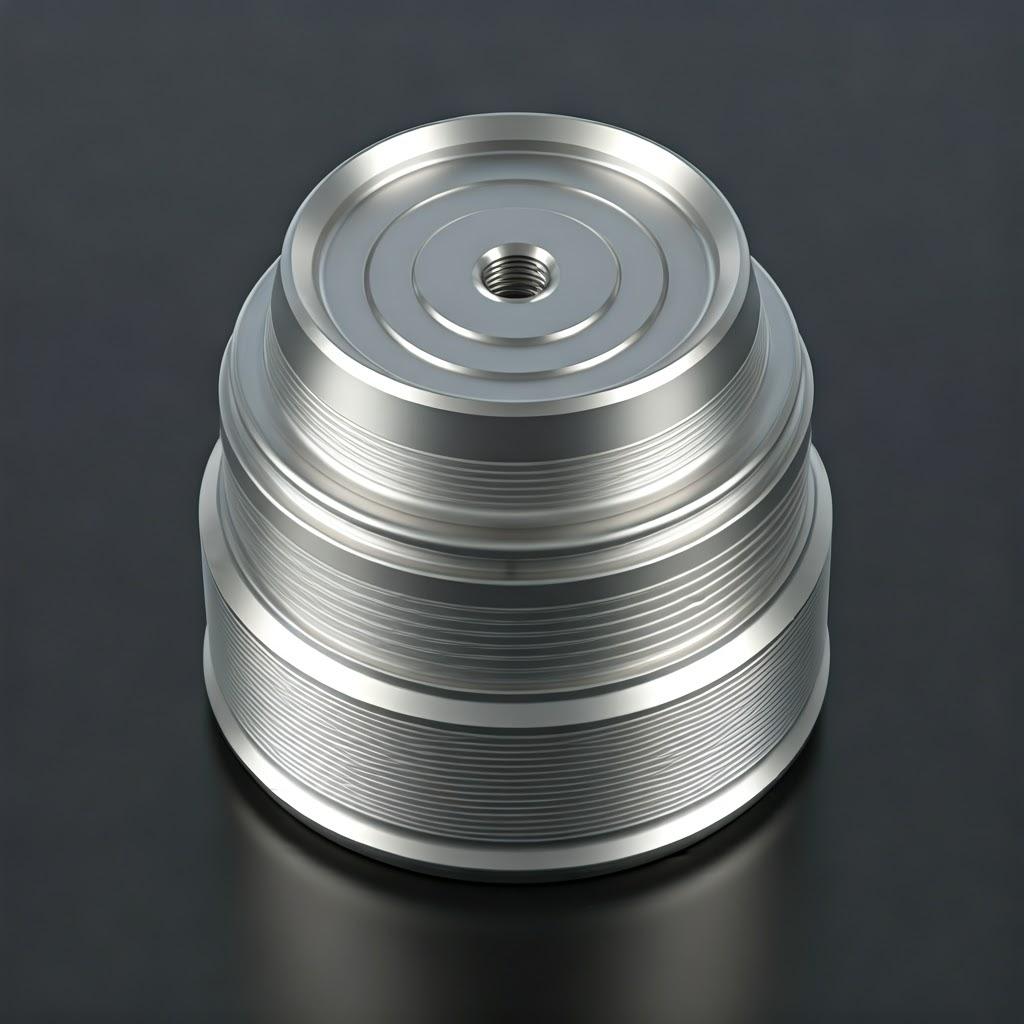
Design for Additive Manufacturing (DfAM): Optimizing End Caps for 3D Printing
Simply taking a design intended for casting or machining and sending it to a 3D printer rarely yields optimal results. To truly harness the power of metal additive manufacturing for components like electric motor end caps, engineers must embrace Diseño para fabricación aditiva (DfAM) principles. DfAM is not just a set of rules but a mindset shift, encouraging designers to think additively – leveraging the layer-by-layer build process to create geometries that maximize performance, minimize weight, reduce post-processing, and consolidate assembly steps. Applying DfAM to aluminum motor end caps can transform them from simple structural elements into highly integrated, performance-enhancing components.
Key DfAM Principles for Aluminum Motor End Caps:
- Leveraging Geometric Freedom for Performance: This is where AM truly shines. Forget the limitations of draft angles or tool access.
- Canales de refrigeración conformados: Instead of simple drilled passages or external fins, design intricate channels that precisely follow the contours of heat-generating areas, such as the bearing seats or near the stator interface. These channels can have optimized cross-sections (e.g., tear-drop shapes for better flow) and complex paths to maximize heat extraction using liquid or air cooling. This can lead to cooler bearing temperatures, extending motor life, or allowing for higher power density. Simulation tools (Computational Fluid Dynamics – CFD) are invaluable here.
- Vías de flujo optimizadas: If the end cap includes ports for lubrication or sealing fluids, AM allows these internal passages to be designed with smooth curves and transitions, minimizing pressure drop and improving flow efficiency.
- Topology Optimization and Lightweighting: Reducing mass is critical in many motor applications (EVs, aerospace, robotics). DfAM enables intelligent lightweighting far beyond simple material removal.
- Stress-Based Optimization: Using Finite Element Analysis (FEA) simulation, identify low-stress regions within the end cap design. Topology optimization algorithms then automatically remove material from these areas, leaving behind an organic, load-bearing structure that meets stiffness and strength requirements with minimum mass. This often results in designs that look unconventional but are highly efficient.
- Estructuras reticulares: Replace solid volumes with internal lattice or gyroid structures. These repeating unit cells provide excellent stiffness-to-weight ratios and can also enhance energy absorption or thermal dissipation due to increased surface area. They are particularly useful for filling larger volumes within the end cap design where solid material isn’t structurally necessary.
- Designing for Self-Support and Reduced Print Time: Support structures are often necessary in LPBF to anchor overhangs and manage thermal stress, but they add print time, consume material, and require removal effort.
- Overhang Angles: Design features with overhang angles typically less than 45 degrees from the build plate whenever possible, as these often print reliably without supports. Avoid large, flat horizontal surfaces facing down.
- Orientación de las características: Consider the build orientation early in the design phase. Orienting the part strategically can minimize the need for supports on critical surfaces or internal features. For example, orienting bearing bores vertically often yields better roundness and surface finish, potentially reducing machining needs.
- Características de sacrificio: Sometimes, small design modifications (like adding a chamfer instead of a sharp edge on a downward-facing surface) can eliminate the need for supports.
- Minimum Feature Size and Wall Thickness: LPBF has limitations on the minimum size of features it can reliably produce.
- Espesor de pared: Ensure walls are thick enough to print reliably and handle operational loads. For aluminum LPBF, minimum wall thickness is typically around 0.4mm to 0.8mm, depending on the feature’s height and geometry, but thicker walls (1mm+) are generally recommended for robustness. Thin, tall walls can be prone to distortion or failure during printing.
- Holes and Channels: Small holes (typically <0.5mm) can be challenging to print accurately and keep clear of powder. Consider minimum diameters for cooling channels or pilot holes intended for later tapping.
- Embossed/Engraved Details: Fine text or logos need sufficient depth and width to be resolved clearly.
- Consolidación de piezas: Leverage AM’s capability to create complex single pieces.
- Integrating Adjacent Components: Can brackets, mounting flanges, sensor housings, terminal boxes, or even parts of the motor casing be integrated into the end cap design? This reduces part count, simplifies assembly for B2B manufacturers and end-users, eliminates potential leak paths or tolerance stack-up issues, and streamlines the supply chain for compradores mayoristas.
- Complexity is (Almost) Free: In AM, adding geometric complexity doesn’t necessarily increase manufacturing cost significantly (unlike machining). This encourages designers to integrate functionality wherever possible.
- Considering Post-Processing: Design with downstream steps in mind.
- Tolerancias de mecanizado: If surfaces like bearing seats or mounting faces require high precision or specific finishes, add extra material (machining stock, typically 0.5mm to 1mm) in the CAD model specifically for post-machining.
- Support Removal Access: Ensure support structures, especially internal ones (e.g., inside cooling channels), are accessible for removal tools or processes like chemical etching. Avoid creating “powder traps” – enclosed voids where unfused powder cannot be removed.
- Consideraciones sobre el tratamiento térmico: Understand how the chosen alloy (AlSi10Mg or A6061) will respond to heat treatment and if the design needs features to prevent warping during these high-temperature cycles.
Partnering for DfAM Expertise:
Successfully implementing DfAM requires not only the right software tools but also experience and understanding of the nuances of the LPBF process. Many product engineers may not yet be fully proficient in designing for additive. This is where collaborating with an experienced metal AM service provider like Met3dp becomes invaluable. Met3dp’s team, with decades of collective expertise in metal additive manufacturing, can provide crucial DfAM consultation. They can review initial designs, suggest modifications to improve printability, reduce cost, enhance performance, and ensure the final part meets all functional requirements. Their understanding of material behavior, process parameters, and post-processing implications allows them to guide clients towards designs that truly exploit the benefits of aluminum 3D printing for motor end caps. Engaging with such experts early in the design phase often leads to the most successful outcomes.
Achieving Precision: Tolerance, Surface Finish, and Dimensional Accuracy
While metal additive manufacturing offers incredible geometric freedom, achieving the high levels of precision often required for components like motor end caps necessitates a clear understanding of the technology’s capabilities and limitations regarding tolerance, surface finish, and overall dimensional accuracy. Engineers and procurement managers must know what to expect from as-printed parts and where secondary operations like CNC machining are necessary.
Understanding Tolerances in Aluminum LPBF:
Laser Powder Bed Fusion can achieve reasonably good dimensional accuracy, but it’s not inherently as precise as high-end CNC machining across all features.
- Tolerancias generales: For general dimensions on aluminum LPBF parts, achievable tolerances often fall within the range of ISO 2768-m (medium) or sometimes ISO 2768-f (fine). This typically translates to:
- ±0.1 mm to ±0.3 mm for smaller features (up to ~100 mm).
- ±0.3 mm or ±0.2% of the nominal dimension for larger features.
- Factores que influyen en la tolerancia:
- Calibración de la máquina: Accuracy heavily depends on the precise calibration of the laser scanning system, Z-axis movement, and thermal stability of the machine. Reputable providers like Met3dp invest in maintaining meticulously calibrated equipment.
- Parámetros del proceso: Laser power, scan speed, layer thickness, and scan strategy significantly impact melt pool dynamics, shrinkage, and residual stress, all affecting final dimensions. Optimized parameters for specific alloys (AlSi10Mg, A6061) are crucial.
- Efectos térmicos: Shrinkage during cooling and residual stress build-up can cause warping and distortion, particularly in large or geometrically complex parts. Simulation, careful support strategies, and post-print stress relief are used to mitigate this.
- Part Size and Geometry: Larger parts or those with significant variations in cross-section are generally harder to hold to tight tolerances due to cumulative thermal effects.
- Orientación de construcción: The orientation of a feature relative to the build direction (X, Y, Z axes) can influence its achievable accuracy. Vertical walls often have better accuracy than angled or horizontal surfaces.
Acabado superficial (rugosidad):
The layer-by-layer nature of LPBF results in a characteristic surface texture.
- As-Printed Surface Roughness (Ra):
- Top Surfaces: Typically smoother, often in the range of Ra 5-15 µm (micrometers).
- Vertical Walls: Usually slightly rougher, Ra 8-20 µm.
- Upward-Facing Angled/Curved Surfaces: Similar to vertical walls.
- Downward-Facing (Overhang) Surfaces: Tend to be the roughest due to the interaction with support structures or the direct exposure of powder undersides to the laser, potentially Ra 15-30 µm or higher.
- Comparación: This is significantly rougher than typical machined finishes (Ra 0.8-3.2 µm) or cast finishes (depending on the casting method).
- Mejora del acabado superficial: Post-processing methods like bead blasting, tumbling, chemical polishing, or CNC machining are required to achieve smoother surfaces. Anodizing A6061 can also provide a smooth, protective layer.
Critical Dimensions and the Need for Machining:
For motor end caps, certain features demand much tighter tolerances and smoother surface finishes than LPBF can typically achieve in the as-printed state. These invariably require post-machining:
- Bearing Seats/Bores: These require very precise diameters (often H6 or H7 tolerance fits) and excellent roundness and surface finish (typically Ra < 1.6 µm, sometimes < 0.8 µm) to ensure proper bearing function, minimize friction, and maximize life.
- Mounting Faces: Surfaces that mate with the motor housing or the driven equipment usually require flatness tolerances and specific surface finishes to ensure proper alignment and sealing.
- Seal Grooves: O-ring grooves or surfaces for lip seals need precise dimensions and smooth finishes to prevent leakage.
- Alignment Features: Dowel pin holes or locating features used for aligning the end cap to the motor housing often require tight positional and diameter tolerances.
Ensuring Accuracy:
Achieving the required final precision involves a combination of factors:
- DfAM for Accuracy: Designing parts with machining stock on critical surfaces.
- Control de procesos: Utilizing high-quality, well-maintained printers (Met3dp emphasizes industry-leading accuracy and reliability in its systems), optimized and validated print parameters, and controlled thermal management during the build. Exploring different métodos de impresión and technologies like SEBM (offered by Met3dp for other materials) also broadens the scope of achievable properties, though LPBF is standard for aluminum.
- Alivio del estrés: Performing appropriate heat treatment immediately after printing and before support removal helps minimize distortion.
- Precision Post-Machining: Using high-quality CNC machining centers and appropriate workholding strategies to finish critical features after heat treatment.
- Quality Control & Inspection: Employing metrology tools like Coordinate Measuring Machines (CMMs), 3D scanners, and surface profilometers to verify dimensions and surface finish against specifications. Reputable manufacturing partners will have robust quality management systems (e.g., ISO 9001).
Engineers specifying 3D printed aluminum end caps should clearly define the required tolerances and surface finishes on their drawings, distinguishing between as-printed acceptable values and those requiring post-machining. Procurement managers should ensure their chosen proveedor has both the printing expertise and the necessary post-machining and inspection capabilities to meet these critical requirements reliably.
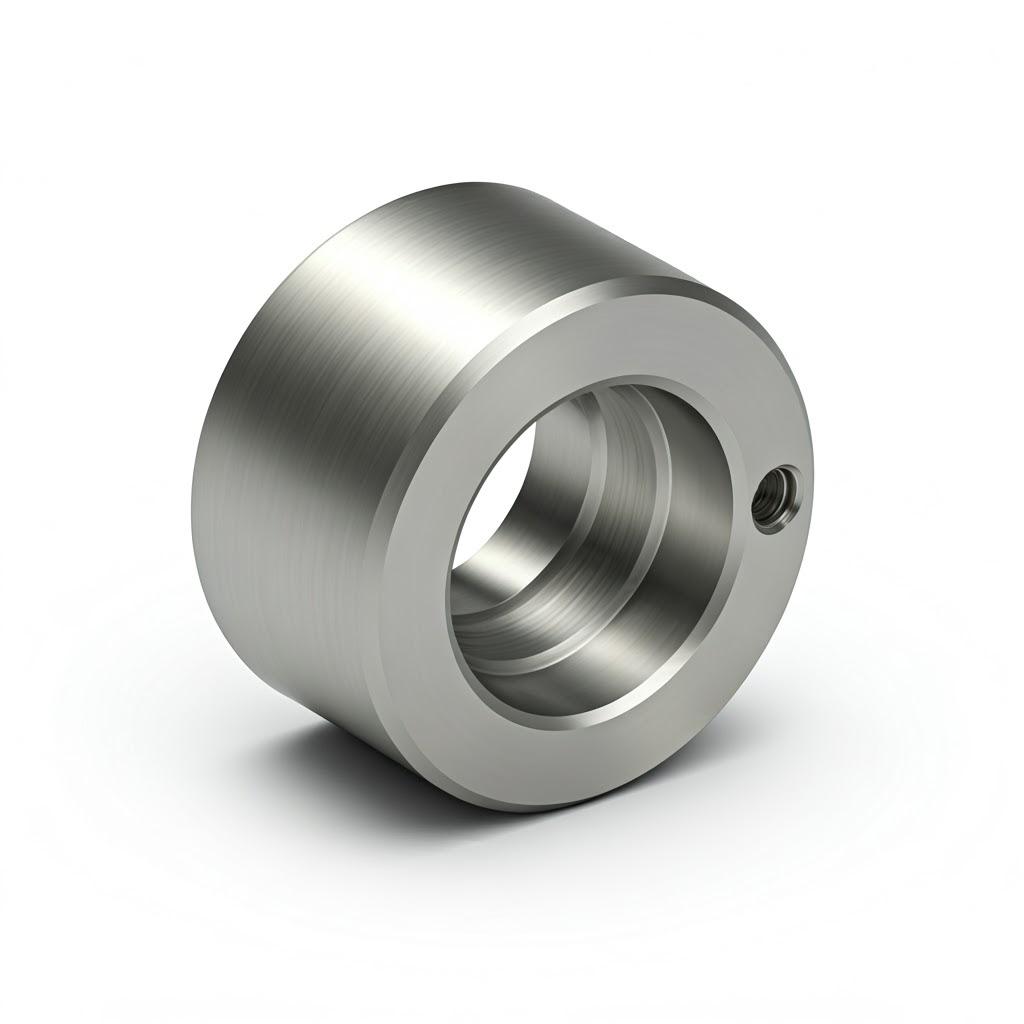
Beyond Printing: Essential Post-Processing Steps for Aluminum End Caps
Receiving a motor end cap directly off the 3D printer is only part of the manufacturing journey. To transform the raw printed part into a functional, reliable component meeting engineering specifications, a series of crucial post-procesamiento steps are typically required. These steps address residual stresses, remove support structures, achieve final dimensional accuracy and surface finish, and optimize material properties. Understanding this workflow is essential for project planning, cost estimation, and selecting a capable manufacturing partner who can manage the entire process chain.
Common Post-Processing Workflow for LPBF Aluminum End Caps:
- Eliminación del polvo:
- Bulk Depowdering: Once the build platform is removed from the printer, the surrounding unfused powder is carefully removed, often through vacuuming and sieving for reuse.
- Detail Depowdering: Compressed air, brushes, and sometimes vibration are used to remove powder trapped in channels, crevices, or internal features. Ensuring complete powder removal is critical, especially from internal cooling channels, as trapped powder can hinder performance or dislodge during operation. Designing for depowderability (avoiding inescapable voids) is a key DfAM consideration.
- Tratamiento térmico antiestrés: (Often performed before removing the part from the build plate)
- Propósito: The rapid heating and cooling cycles inherent in LPBF create significant residual stresses within the printed part. These stresses can cause warping or distortion, especially once the part is removed from the rigid build plate, and can negatively impact mechanical properties.
- Proceso: The entire build plate with the attached parts is placed in a furnace and heated to a specific temperature (typically 200-350°C for aluminum alloys, depending on the specific alloy and desired outcome), held for a period (e.g., 1-4 hours), and then slowly cooled. This allows the internal stresses to relax without significantly altering the microstructure (unlike full annealing or T6 tempering).
- Importancia: This step is crucial for dimensional stability during subsequent steps like support removal and machining.
- Extracción de la pieza de la placa de montaje:
- Métodos: Parts are typically removed using wire EDM (Electrical Discharge Machining), band sawing, or sometimes manually breaking off purpose-designed support interfaces. Wire EDM generally imparts less stress and provides a cleaner cut surface.
- Retirada de la estructura de soporte:
- Necesidad: Supports anchor the part to the build plate, manage thermal stress, and support overhanging features during the build.
- Métodos: Removal can be manual (using pliers, cutters, grinders – labor-intensive and can damage surfaces), CNC machining (precise but requires setup), or sometimes wire EDM. The ease and method of removal depend heavily on the support design and accessibility. Complex internal supports can be particularly challenging. DfAM plays a vital role in designing supports that are effective yet easier to remove.
- Solution Treatment and Aging (e.g., T6 Temper for A6061 or potentially AlSi10Mg): (If required for enhanced mechanical properties)
- Propósito: To achieve the desired final mechanical properties (strength, ductility, hardness) specified for the alloy, particularly for precipitation-hardening alloys like A6061.
- T6 Process (Typical for A6061):
- Solución Tratamiento: Heating the part to a high temperature (e.g., ~530°C) to dissolve alloying elements (like Mg and Si) into the aluminum matrix.
- Enfriamiento: Rapidly cooling (quenching) the part, usually in water, to trap the alloying elements in a supersaturated solid solution.
- Artificial Aging: Reheating the part to a lower temperature (e.g., 160-190°C) and holding it for a specific duration (e.g., 8-18 hours). This allows the dissolved elements to precipitate out as fine, dispersed particles, significantly strengthening the material.
- Consideraciones: Heat treatment can potentially cause some distortion, which needs to be accounted for (e.g., by machining después de heat treatment). It adds time and cost but is often essential for meeting performance requirements. Met3dp possesses expertise in optimizing heat treatment cycles for its AM materials.
- Mecanizado CNC:
- Propósito: To achieve tight tolerances, specific surface finishes, and precise geometric features (like flatness or perpendicularity) on critical surfaces that cannot be met by the as-printed part.
- Areas Machined: As discussed previously, this typically includes bearing seats, mounting faces, seal grooves, and alignment features.
- Importancia: Essential for ensuring proper fit, function, and reliability of the motor end cap.
- Acabado superficial:
- Propósito: To improve surface smoothness, enhance appearance, improve wear resistance, or add corrosion protection.
- Common Methods for Aluminum:
- Bead Blasting/Shot Peening: Propels media (glass beads, ceramic shot) at the surface. Smooths texture, removes loose particles, provides a uniform matte finish. Shot peening can also impart beneficial compressive residual stress.
- Tumbling/Vibratory Finishing: Parts are placed in a tub with abrasive media, which tumbles or vibrates against the parts to deburr edges and smooth surfaces. Good for batch processing.
- Pulido: Mechanical or chemical polishing can achieve very smooth, reflective surfaces if required (less common for standard end caps unless aesthetics are critical).
- Anodizing: An electrochemical process primarily for A6061 (less effective on high-Si alloys like AlSi10Mg) that creates a hard, durable, corrosion-resistant aluminum oxide layer. Can also be dyed various colors. Improves wear resistance and prevents galling.
- Painting/Powder Coating: For aesthetic or specific environmental protection needs.
- Inspection and Quality Control (QC):
- Propósito: To verify that the finished end cap meets all dimensional, material, and functional specifications.
- Métodos: Dimensional inspection (CMM, 3D scanning, calipers, gauges), surface roughness measurement, material property testing (if required, often done on test coupons printed alongside the parts), visual inspection, NDT (Non-Destructive Testing like CT scanning for internal defects if critical).
Integrated Solutions:
The complexity of this multi-stage process highlights the value of working with a full-service manufacturing partner. Companies like Met3dp, which offer comprehensive solutions spanning DfAM support, high-quality powder production, advanced printing (SEBM and LPBF systems), and potentially managing or coordinating necessary post-processing steps, provide a streamlined experience for clients. They understand the interactions between each stage and can optimize the entire workflow for quality, cost, and lead time. Procurement managers seeking al por mayor o distribuidor partnerships should prioritize suppliers who demonstrate mastery over the complete process chain, ensuring consistent delivery of high-quality, finished aluminum end caps.
Navigating Challenges: Common Issues in Aluminum End Cap Printing & Solutions
While aluminum Laser Powder Bed Fusion (LPBF) offers tremendous advantages for producing complex motor end caps, it’s not without its challenges. Achieving consistent, high-quality results requires careful control over the entire process, from design to post-processing. Understanding potential pitfalls and how experienced providers mitigate them is crucial for engineers and procurement managers considering this technology.
Common Challenges in LPBF of Aluminum Alloys (AlSi10Mg, A6061):
- Deformación y distorsión:
- Causa: Significant temperature gradients between the molten pool (~700°C+) and the surrounding powder/solidified material (~150-500°C build chamber/plate temp) create internal stresses. As layers build up, these stresses accumulate and can cause the part to warp, curl away from the build plate, or distort from its intended geometry. Thin walls and large flat areas are particularly susceptible.
- Mitigación:
- Simulación térmica: Simulating the build process beforehand can predict high-stress areas and potential distortion, allowing for design modifications or optimized support strategies.
- Estrategias de exploración optimizadas: Using specific laser scanning patterns (e.g., island scanning, checkerboard patterns) helps distribute heat more evenly and reduce localized stress build-up.
- Construir calefacción de placas: Maintaining a consistently high build plate temperature (up to 200°C or more for aluminum) reduces the thermal gradient and minimizes stress.
- Estructuras de soporte robustas: Properly designed supports anchor the part securely and act as heat sinks, drawing heat away and resisting warping forces.
- Immediate Stress Relief: Performing stress relief heat treatment before removing the part from the build plate is critical for dimensional stability.
- Tensión residual:
- Causa: Even if warping is controlled, significant residual stress can remain locked within the part after printing. This can negatively impact fatigue life, lead to cracking during post-processing (machining), or cause long-term dimensional instability.
- Mitigación:
- Optimización de los parámetros del proceso: Fine-tuning laser power, scan speed, and layer thickness affects the cooling rate and stress development.
- Tratamiento térmico antiestrés: As mentioned, this is the primary method for significantly reducing residual stress to manageable levels. The specific cycle (temperature and time) is crucial.
- Consideraciones sobre el diseño: Avoiding sharp internal corners and abrupt changes in cross-section can help minimize stress concentrations.
- Porosidad:
- Causa: Small voids or pores within the solidified material can compromise mechanical properties (especially fatigue strength and ductility) and leak tightness. Causes include:
- Porosidad del gas: Hydrogen gas, which aluminum readily absorbs when molten, can become trapped during rapid solidification. Sourcing high-quality powder with low dissolved gas content (like those produced via Met3dp’s advanced atomization) and maintaining a clean inert gas atmosphere (Argon) in the build chamber are key.
- Porosidad por falta de fusión: Insufficient energy input (laser power too low or scan speed too high) prevents complete melting and fusion between powder particles or successive layers, leaving irregular voids.
- Porosidad del ojo de la cerradura: Excessive energy density can create an unstable, deep melt pool (keyhole mode) that traps gas bubbles during collapse.
- Mitigación:
- Polvo de alta calidad: Using powder with low internal gas porosity and controlled particle size distribution. Met3dp’s focus on powder quality using gas atomization and PREP technologies is a significant advantage here.
- Parámetros de proceso optimizados: Developing and validating robust parameter sets that ensure full melting and fusion without inducing keyhole instability. This requires significant material science expertise.
- Control de la atmósfera inerte: Maintaining a high-purity Argon atmosphere with low oxygen levels (<0.1%) prevents oxidation and reduces gas pickup.
- Prensado isostático en caliente (HIP): For critical applications demanding near-zero porosity, HIP (high temperature and isostatic pressure) can be used as a post-processing step to close internal voids (adds significant cost and time).
- Causa: Small voids or pores within the solidified material can compromise mechanical properties (especially fatigue strength and ductility) and leak tightness. Causes include:
- Support Removal Difficulty:
- Causa: Supports need to be strong enough to function during the build but easy enough to remove afterward without damaging the part. Internal supports (e.g., inside cooling channels) can be particularly problematic. Poorly designed supports can fuse strongly to the part or be located in inaccessible areas.
- Mitigación:
- DfAM for Supports: Designing parts to minimize the need for supports (self-supporting angles) is the first line of defense.
- Estructuras de apoyo especializadas: Using support types with smaller contact points (e.g., conical or perforated supports) or specific materials designed to break away more easily.
- Accessibility Planning: Ensuring tools or processes (manual, machining, chemical etching) can reach the supports.
- Supplier Experience: Experienced providers have refined techniques for designing and removing supports effectively.
- Achieving Consistent Material Properties:
- Causa: Variations in powder quality, machine calibration, process parameters, or heat treatment can lead to inconsistencies in mechanical properties (strength, ductility, hardness) between builds or even within a single large part.
- Mitigación:
- Stringent Powder Quality Control: Testing and certifying each batch of powder. Vertically integrated suppliers like Met3dp have an advantage here.
- Robust Machine Calibration and Maintenance: Regular checks and calibration of laser power, spot size, scanner accuracy, and gas flow.
- Supervisión de procesos: In-situ monitoring tools (melt pool monitoring, thermal imaging) can help detect anomalies during the build.
- Standardized Post-Processing: Implementing tightly controlled and validated heat treatment cycles and machining procedures.
- Pruebas de materiales: Regularly printing and testing standardized coupons alongside production parts to verify material properties meet specifications.
Partnering to Overcome Challenges:
Successfully navigating these challenges requires deep expertise, advanced equipment, and rigorous process control. This is why selecting the right metal AM service provider is paramount. Companies like Met3dp, with their foundation in materials science, advanced powder manufacturing (gas atomization, PREP), state-of-the-art printing equipment (including systems offering industry-leading print volume, accuracy, and reliability), and comprehensive understanding of the entire AM workflow, are well-positioned to mitigate these risks. They invest in research and development to optimize processes for materials like AlSi10Mg and A6061, implement stringent quality management systems, and offer technical consultation to ensure clients achieve high-quality, reliable aluminum end caps that meet the demanding requirements of aerospace, automotive, medical, and industrial applications. Engaging with such a partner significantly increases the likelihood of a successful project outcome for both engineers designing the parts and procurement managers sourcing them.
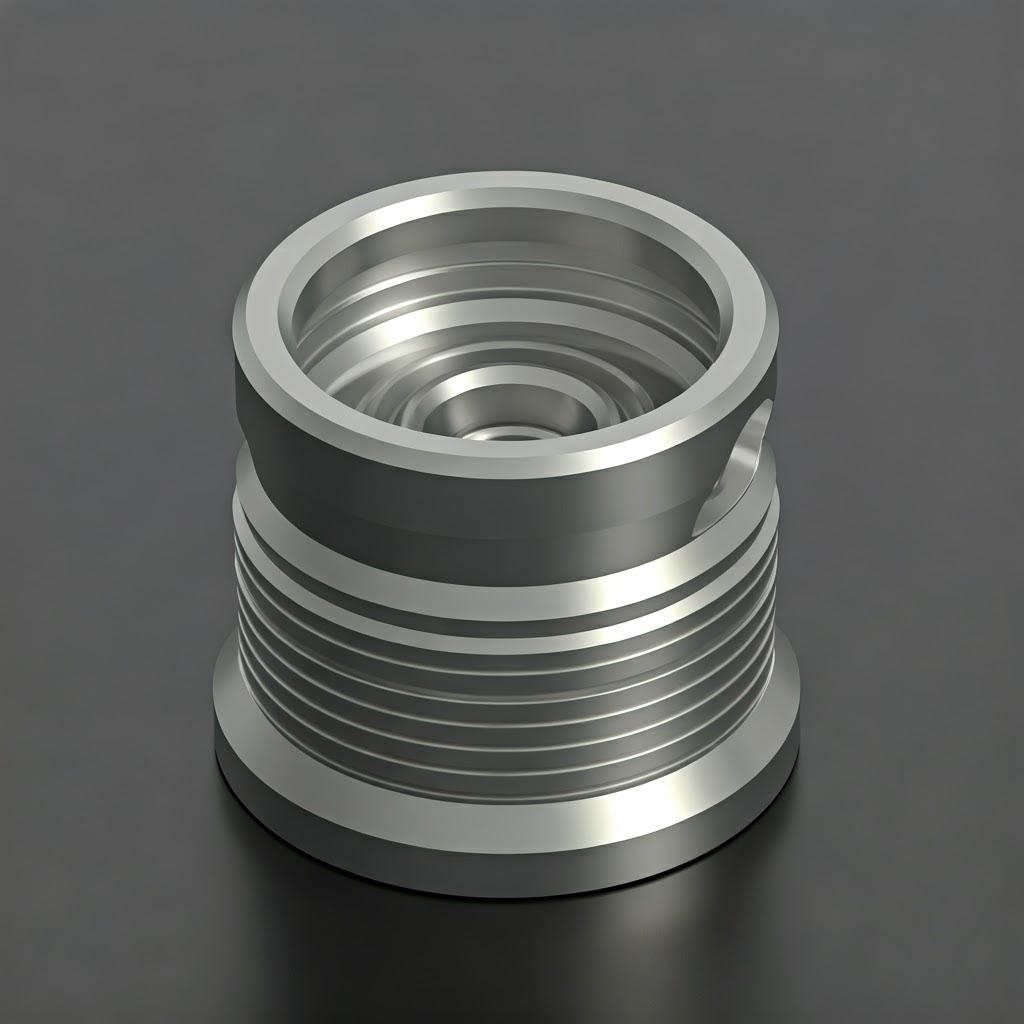
Supplier Selection: Choosing the Right Metal 3D Printing Service Partner
Seleccionar el metal AM service provider is arguably as critical as the design and material choices themselves when embarking on a project like producing aluminum motor end caps via additive manufacturing. The quality, reliability, cost-effectiveness, and ultimately the success of your project hinge on the capabilities and expertise of your chosen partner. For engineers focused on performance and procurement managers tasked with sourcing reliable B2B manufacturing partners, evaluating potential suppliers requires looking beyond just quoted price and considering a range of crucial factors. Making an informed decision ensures you partner with a supplier who can not only print the part but also contribute to its success from concept to delivery.
Key Criteria for Evaluating Metal AM Suppliers for Aluminum End Caps:
- Technical Expertise & Proven Experience:
- Material Specialization: Does the supplier have deep experience specifically with printing aluminum alloys like AlSi10Mg and A6061? Ask for case studies or examples of similar components they have produced. Aluminum alloys have unique challenges (thermal conductivity, oxidation risk, stress development) that require specialized process knowledge.
- Application Knowledge: Do they understand the functional requirements of motor components? Familiarity with aspects like bearing fits, thermal management, and structural loads in rotating machinery is a significant advantage.
- Apoyo al DfAM: Can they provide meaningful Design for Additive Manufacturing consultation? A good partner should be able to analyze your design, suggest improvements for printability and performance, and help you leverage the full potential of AM.
- Problem-Solving: How do they address potential issues like warping, porosity, or support removal challenges discussed earlier? Look for evidence of robust process control and troubleshooting capabilities.
- Machine Capabilities & Technology:
- Appropriate Technology: For aluminum end caps, Laser Powder Bed Fusion (LPBF/SLM/DMLS) is the primary technology. Ensure the supplier operates well-maintained, industrial-grade LPBF machines from reputable manufacturers.
- Machine Fleet & Capacity: Do they have sufficient machine capacity to handle your project’s volume (prototypes, low-volume production, potential al por mayor orders) and meet your lead time requirements? Redundancy (multiple machines) is beneficial to avoid delays due to maintenance.
- Construir volumen: Can their machines accommodate the size of your end cap design? Met3dp, for instance, highlights its printers’ industry-leading print volume, offering flexibility for larger components or batch production.
- Process Monitoring & Control: Do their machines incorporate features like melt pool monitoring or advanced sensor capabilities to ensure build consistency and quality?
- Material Portfolio & Quality Control:
- Powder Sourcing & Handling: Where do they source their aluminum powders? Do they have stringent quality control procedures for incoming powder (chemistry verification, particle size analysis, flowability testing)? How is powder handled and stored to prevent contamination and degradation?
- In-House Powder Production: A los proveedores les gusta Met3dp who manufacture their own high-quality metal powders using advanced methods like Atomización de gas y PREP have a distinct advantage. This vertical integration allows for tighter control over powder characteristics (sphericity, purity, PSD) crucial for consistent printing results and superior material properties. Knowing the powder is optimized for AM directly from the source provides greater confidence. You can learn more about Met3dp’s approach and values on their Quiénes somos página.
- Certificación de materiales: Can they provide material certifications tracing the powder batch to the final part, verifying its chemical composition and potentially key mechanical properties via test coupons?
- Capacidades de postprocesado:
- Integrated Services: Does the supplier offer essential post-processing steps in-house (stress relief, heat treatment, basic support removal, bead blasting) or have established partnerships for services like CNC machining, advanced surface finishing (anodizing), and HIP?
- Managed Workflow: A supplier who can manage the entire workflow, from printing through all necessary post-processing and final inspection, simplifies logistics and ensures accountability. Coordinating multiple vendors for different steps increases complexity and potential for delays or quality issues. Met3dp emphasizes providing soluciones integrales.
- Quality Management System & Certifications:
- ISO 9001: This certification indicates a commitment to standardized quality management processes, ensuring consistency and traceability.
- Industry-Specific Certifications (if required): For aerospace applications, AS9100 certification is often necessary. For medical, ISO 13485 might be relevant (though less common for external motor components). Ask potential suppliers about the certifications they hold relevant to your industry.
- Capacidad de inspección: Do they have the necessary metrology equipment (CMM, 3D scanners, surface profilometers) and trained personnel to verify parts meet your dimensional and surface finish specifications?
- Capacity, Lead Times & Communication:
- Plazos de entrega realistas: Can they provide clear and realistic lead time estimates based on current capacity and project complexity?
- Capacidad de respuesta: How quickly do they respond to inquiries and provide quotes? Is communication clear and professional?
- Gestión de proyectos: Do they assign a dedicated point of contact for your project? How do they handle project updates and communication?
- Cost vs. Value:
- Cita transparente: Is the quote detailed, breaking down costs for printing, material, support removal, post-processing, etc.? Beware of quotes that seem too low – they might compromise on quality control, powder quality, or necessary post-processing.
- Overall Value: Consider the supplier’s expertise, quality assurances, reliability, and support capabilities, not just the per-part price. Partnering with a slightly more expensive but highly capable and reliable supplier often provides better long-term value, especially for critical components like motor end caps.
Elegir bien industrial supplier for 3D printed aluminum end caps is a strategic decision. Look for a partner who acts as an extension of your engineering and procurement teams, offering expertise, reliability, and a commitment to quality. Companies like Met3dp, with their dual expertise in advanced powder manufacturing and high-performance additive manufacturing systems, coupled with a focus on accuracy, reliability, and comprehensive customer support, represent the type of partner capable of delivering on the demanding requirements of modern motor applications across aerospace, automotive, medical, and industrial sectors.
Understanding Investment: Cost Factors and Typical Lead Times for Production
One of the most pressing questions for engineers and procurement managers considering metal additive manufacturing for components like aluminum motor end caps revolves around the investment required – both in terms of cost and time. While AM offers compelling technical advantages, understanding the factors that drive metal 3D printing cost and influence plazos de entrega is essential for accurate budgeting, project planning, and managing expectations. Unlike traditional high-volume methods where tooling dominates initial costs, AM costs are more closely tied to the part itself and the resources consumed during its production.
Key Cost Drivers for 3D Printed Aluminum End Caps:
- Material Consumption:
- Part Volume: The primary driver is the actual volume of aluminum powder (AlSi10Mg or A6061) fused to create the part. Larger or denser parts naturally cost more.
- Volumen de la estructura de soporte: Material used for support structures also contributes to the cost. Efficient DfAM aims to minimize support needs.
- Coste del polvo: The market price of high-quality, AM-grade aluminum powder fluctuates, but it’s a direct input cost. Different alloys might have slightly different costs.
- Print Time (Machine Utilization):
- Part Height (Z-Height): Since printing occurs layer by layer, the height of the part in the build orientation is a major factor determining print duration. Taller parts take longer.
- Part Volume & Cross-Sectional Area: Larger volumes and wider cross-sections require more laser scanning per layer, increasing time.
- Complejidad: Highly intricate features or extensive lattice structures can increase the scanning path length and overall print time.
- Number of Parts per Build: Printing multiple end caps simultaneously in a single build (batching) optimizes machine utilization and can reduce the per-part cost compared to printing one at a time. This is key for wholesale 3D printing quotes.
- Grosor de la capa: Thicker layers (e.g., 50-60 µm) print faster but result in rougher surfaces and potentially lower resolution than thinner layers (e.g., 20-30 µm).
- Machine Cost & Overhead:
- Industrial metal AM systems represent a significant capital investment for service providers. The hourly rate charged for machine time includes depreciation, maintenance, energy consumption, inert gas (Argon) usage, facility costs, and operator labor.
- Costes laborales:
- Setup: Preparing the build file, setting up the machine, loading powder.
- Monitoring: Overseeing the print process.
- Post-procesamiento: Powder removal, stress relief, support removal (can be very labor-intensive depending on complexity), managing heat treatment cycles, setting up and running CNC machining, performing surface finishing, inspection, and packaging. Labor associated with manual steps like support removal and finishing can be a significant cost component.
- Post-Processing Complexity:
- The extent and type of post-processing required heavily influence the final cost.
- Tratamiento térmico: Adds furnace time and energy costs.
- Retirada del soporte: Simple supports are cheaper to remove than complex internal ones requiring careful manual work or specialized machining.
- Mecanizado CNC: The number of features requiring machining, the tolerances involved, and the setup complexity directly impact machining costs.
- Acabado superficial: Basic bead blasting is relatively inexpensive, while extensive polishing or specialized coatings like anodizing add cost.
- Inspection: Basic dimensional checks vs. comprehensive CMM reports or NDT (like CT scanning) have different cost implications.
- Volumen del pedido:
- While AM doesn’t have the extreme volume dependency of casting (due to no hard tooling), economies of scale still apply. Setup costs are amortized over more parts in larger batches. Suppliers may offer discounted pricing for al por mayor or higher volume orders compared to single prototypes.
Typical Lead Times for Production:
Lead time is the total duration from order placement to receiving the finished parts. It’s influenced by several stages:
- Design & File Preparation (1-3 days): Finalizing the CAD model, potentially performing DfAM checks/modifications, creating the build file with support structures, and slicing.
- Queue Time (Variable: 1 day to 2+ weeks): The time until the build can be scheduled on an available machine. This depends heavily on the supplier’s current workload and capacity.
- Printing Time (1-5+ days): The actual duration of the LPBF build process. This depends primarily on the factors influencing machine utilization (part height, volume, complexity, batch size). A single end cap might print in less than a day, while a full build plate of multiple caps could take several days.
- Post-Processing (2-10+ days): This is often the most variable part of the lead time.
- Cooling & Depowdering: <1 day
- Stress Relief: 1 day (including furnace cycle and cooling)
- Support Removal & Basic Finishing: 1-3 days (depending on complexity)
- Heat Treatment (e.g., T6): 1-2 days (including furnace cycles and handling)
- CNC Machining: 1-5+ days (depending on complexity, number of setups, machine availability)
- Surface Finishing (Anodizing, etc.): 1-3 days (often outsourced)
- Quality Control & Inspection (1-2 days): Final checks and report generation.
- Shipping (Variable): Depends on location and shipping method.
Overall Estimated Lead Time: For a typical batch of 3D printed aluminum end caps requiring standard post-processing including heat treatment and machining, a realistic total lead time might range from 2 to 5 weeks. Prototypes requiring less post-processing might be faster, while very complex parts or large orders could take longer.
Managing Expectations:
It’s crucial for B2B procurement teams and engineers to get detailed, custom quotes that outline both cost components and estimated lead times for each stage. Discussing priorities (e.g., speed vs. cost vs. specific properties) with the supplier can help optimize the production plan. Reputable suppliers like Met3dp strive for efficiency but will provide realistic estimates based on the specific project requirements, ensuring transparency throughout the process.
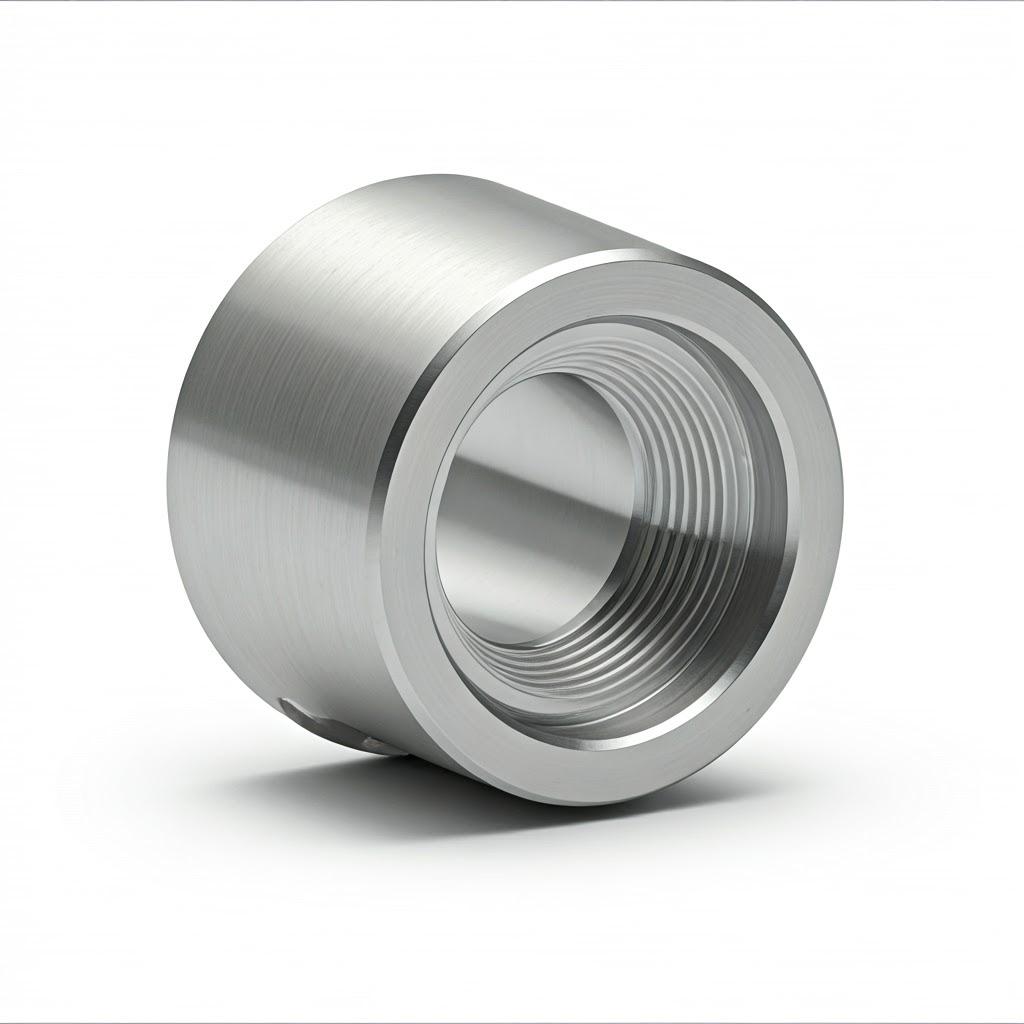
Preguntas más frecuentes (FAQ)
Here are answers to some common questions regarding the use of aluminum 3D printing for electric motor end caps:
Q1: Is 3D printed aluminum strong enough for motor end caps?
A: Absolutely. Aluminum alloys commonly used in LPBF, such as AlSi10Mg y A6061, exhibit excellent mechanical properties that are often comparable or even superior to cast aluminum alloys and can approach wrought specifications, especially after appropriate post-processing like heat treatment.
- AlSi10Mg: Offers good strength and hardness, suitable for many structural applications.
- A6061: When properly heat treated (T6 temper), it provides a great combination of strength, ductility, and toughness, making it very robust. The key is selecting the right alloy for the load case and ensuring proper printing process control and post-processing (like heat treatment) are performed by a qualified supplier like Met3dp to achieve the desired material properties consistently. DfAM can also be used to optimize the structure for required strength while minimizing weight.
Q2: How does the cost of 3D printing compare to CNC machining for end caps?
A: The cost comparison depends heavily on several factors:
- Complejidad: For highly complex geometries (e.g., intricate internal cooling channels, topology-optimized shapes, integrated features), 3D printing often becomes more cost-effective than CNC machining, as machining complexity drives costs up significantly.
- Volumen: For single prototypes or very low volumes (e.g., < 10-20 units), 3D printing is typically cheaper due to the absence of setup complexity and tooling costs associated with machining intricate parts from scratch. For mid-volumes (e.g., 50-500 units), the comparison becomes closer and depends on the specific geometry and post-processing needs. For very high volumes (thousands), traditional methods like die casting are usually cheaper per part (if the geometry allows), though AM can still be competitive if its unique advantages (like integrated cooling) provide significant downstream value.
- Residuos materiales: AM is generally less wasteful than subtractive CNC machining, which can be a cost factor, especially with more expensive materials.
- Conclusión: AM is often cost-competitive or advantageous for prototypes, low-to-mid volumes, and parts with high geometric complexity where its design freedom adds value. For simple shapes in high volumes, machining or casting might be cheaper per part.
Q3: What are the typical lead times for receiving 3D printed aluminum end caps?
A: As detailed in the previous section, typical lead times range from 2 to 5 weeks for a finished part requiring standard post-processing (printing, stress relief, support removal, heat treatment, CNC machining, basic finishing, QC).
- Prototipos: Might be faster (e.g., 1-3 weeks) if extensive post-processing isn’t needed.
- Complex Parts/Large Orders: Could extend beyond 5 weeks. Factors influencing lead time include design complexity, supplier queue time, print duration, the extent of post-processing required, and shipping. Always get a specific estimate from your chosen supplier based on your project details.
Q4: Can complex internal cooling channels be effectively printed in aluminum end caps?
A: Yes, this is one of the primary advantages of using metal 3D printing. LPBF allows for the creation of highly complex, freeform internal channels that closely follow heat sources (conformal cooling) or maximize surface area within a given volume.
- Effectiveness: These channels can significantly improve heat dissipation compared to solid end caps or those with simple drilled passages, leading to cooler operation, higher power density, or longer motor life.
- Consideraciones: Design for powder removal is crucial – channels must be accessible for cleaning unfused powder. Minimum channel diameter (typically > 0.8-1.0 mm) and surface roughness need consideration during design. Simulation (CFD) is recommended to optimize channel design for flow and heat transfer.
Q5: Which aluminum alloy (AlSi10Mg or A6061) is better for high-temperature motor applications?
A: Neither AlSi10Mg nor standard A6061 are considered high-temperature aluminum alloys; their mechanical properties tend to degrade significantly at temperatures above ~150-200°C.
- Comparación: Both have broadly similar operating temperature limits in their typical heat-treated states. Some specific LPBF-optimized variants like 6061-RAM2 (with Cu and Zr additions) may offer slightly improved performance at moderately elevated temperatures compared to standard 6061 or AlSi10Mg.
- Recommendation: For applications involving continuous operation at temperatures significantly exceeding 150°C, other materials might need consideration (e.g., specific high-temperature aluminum alloys if available for AM, or potentially even titanium or steel alloys depending on requirements, though these add weight and cost). However, for most standard electric motor operating ranges, both AlSi10Mg and A6061 (especially when combined with AM-enabled enhanced cooling) perform well. Discuss your specific thermal requirements with your material and AM experts like the team at Met3dp.
Conclusion: Partnering for Advanced Motor Components with Aluminum AM
The landscape of electric motor design and manufacturing is rapidly evolving, driven by relentless demands for higher performance, reduced weight, improved thermal management, and greater customization. As we’ve explored, fabricación aditiva de metales, specifically leveraging the capabilities of Laser Powder Bed Fusion with advanced aluminum alloys like AlSi10Mg y A6061, offers a powerful pathway to meeting these demands for critical components like motor end caps.
The transition from traditional manufacturing methods to AM for end caps is not merely a substitution; it’s an upgrade. It unlocks a new dimension of libertad de diseño, enabling engineers to craft highly optimized structures with integrated conformal cooling channels, topologically minimized weight, and consolidated features – designs previously confined to the realm of imagination. The benefits are tangible: lighter motors for EVs and aerospace, more power-dense actuators for robotics, enhanced reliability for industrial machinery, and the agility to prototype and produce custom solutions faster than ever before.
We’ve delved into the core functions of end caps, the specific advantages AM brings, the nuances of material selection between AlSi10Mg and A6061, the critical importance of Diseño para fabricación aditiva (DfAM), the achievable precision, the essential post-processing steps, and the common challenges that require expertise to navigate. Understanding these facets empowers engineers and procurement managers to make informed decisions.
However, realizing the full potential of aluminum AM hinges on collaboration with the right manufacturing partner. The journey requires more than just access to a printer; it demands deep material science knowledge, meticulous process control, advanced powder technology, robust post-processing capabilities, and a commitment to quality and reliability.
Aquí es donde Met3dp stands out. Headquartered in Qingdao, China, Met3dp is not just a service provider but a leader in additive manufacturing solutions, specializing in both high-performance metal 3D printing equipment (SEBM and LPBF systems renowned for industry-leading print volume, accuracy, and reliability) and the polvos metálicos avanzados that fuel them. Their expertise in powder production, utilizing cutting-edge gas atomization and PREP technologies, ensures a foundation of high-quality, spherical aluminum powders optimized for AM. With decades of collective expertise, Met3dp provides comprehensive solutions – from DfAM consultation to finished part production – partnering with organizations across aerospace, automotive, medical, and industrial manufacturing to accelerate their digital manufacturing transformations.
If you are looking to push the boundaries of motor performance, achieve significant lightweighting, or develop customized motor solutions, aluminum additive manufacturing presents a compelling opportunity. We invite engineers, designers, and procurement professionals to explore how 3D printed aluminum end caps can elevate your next project.
Póngase en contacto con Met3dp hoy mismo to discuss your application and discover how our cutting-edge systems, advanced metal powders, and expert services can power your organization’s additive manufacturing goals. Visit our website at https://met3dp.com/ to learn more. Let’s build the future of advanced motor components, together.
Compartir
MET3DP Technology Co., LTD es un proveedor líder de soluciones de fabricación aditiva con sede en Qingdao, China. Nuestra empresa está especializada en equipos de impresión 3D y polvos metálicos de alto rendimiento para aplicaciones industriales.
Solicite información para obtener el mejor precio y una solución personalizada para su empresa.
Artículos relacionados
Acerca de Met3DP
Actualización reciente
Nuestro producto
CONTACTO
¿Tiene alguna pregunta? ¡Envíenos un mensaje ahora! Atenderemos su solicitud con todo un equipo tras recibir su mensaje.
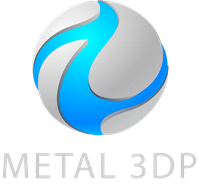
Polvos metálicos para impresión 3D y fabricación aditiva