material de grado de forja
Índice
En el ámbito de la metalurgia, donde las materias primas se transforman en objetos de utilidad y belleza, materiales de forja reinan en el mundo. Imagínese a un escultor moldeando meticulosamente la arcilla, pero a escala industrial, con un calor y una presión inmensos que dan forma a estos materiales en componentes complejos de gran resistencia. Ésa es la esencia de la forja, y la base de este proceso se encuentra en los mismos materiales en los que vamos a profundizar.
Una visión general: Forjando el camino hacia la fortaleza
Los materiales de forja son metales especialmente formulados para soportar el calor intenso, las fuerzas de compresión y las deformaciones que implica el proceso de forja. A diferencia de la fundición, en la que el metal fundido llena un molde, la forja manipula el material sólido, refinando su estructura de grano y mejorando sus propiedades mecánicas. Esto se traduce en componentes más fuertes y fiables que pueden soportar aplicaciones exigentes.
Estos materiales se presentan en una gran variedad de sabores, cada uno con su propia mezcla única de propiedades. La elección del material depende en gran medida de la aplicación prevista. ¿Necesita un componente increíblemente fuerte y resistente al desgaste? ¿O tal vez uno que ofrezca una resistencia superior a la corrosión? El mundo de los materiales de forja tiene una respuesta para cada necesidad.
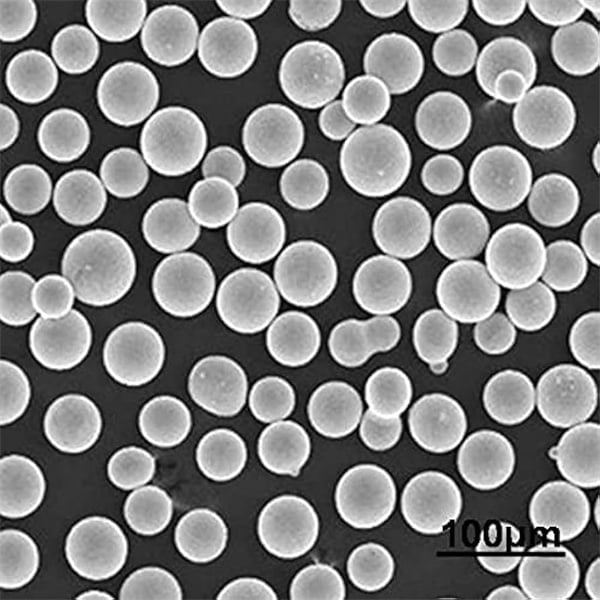
Común Materiales de forja
Entremos ahora en el meollo de la cuestión: los materiales específicos que hacen posible la forja. Veamos algunos de los más utilizados:
Tabla: Materiales de forja comunes
Material | Composición | Propiedades clave | Aplicaciones |
---|---|---|---|
Acero al carbono | Principalmente hierro con contenido variable de carbono (bajo, medio, alto) | Asequible, buena maquinabilidad, la resistencia aumenta con el contenido de carbono | Cigüeñales, engranajes, bielas, llaves |
Acero aleado | Hierro con carbono y elementos adicionales como cromo, níquel o molibdeno | Alta resistencia, tenacidad, resistencia al desgaste, puede someterse a tratamiento térmico para obtener propiedades específicas. | Ejes, engranajes, componentes aeronáuticos, herramientas |
Acero inoxidable | Hierro con cromo para resistir a la corrosión, a menudo incluye níquel y molibdeno. | Excelente resistencia a la corrosión, buena resistencia y conformabilidad | Válvulas, bombas, elementos de fijación, instrumental médico |
Aleaciones de níquel | Alto contenido en níquel, a menudo con cromo y hierro | Excepcional resistencia a la corrosión a altas temperaturas, excelente resistencia | Álabes de turbina, intercambiadores de calor, recipientes a presión |
Aleaciones de aluminio | Principalmente aluminio con elementos como cobre, magnesio o silicio | Ligero, buena resistencia a la corrosión, resistencia moderada | Componentes de aeronaves, piezas de automóviles, conductores eléctricos |
Aleaciones de titanio | Principalmente titanio con elementos como aluminio, vanadio o molibdeno | Elevada relación resistencia/peso, excelente resistencia a la corrosión | Componentes aeroespaciales, implantes médicos, artículos deportivos |
Aleaciones de cobre | Principalmente cobre con elementos como zinc, estaño o plomo | Excelente conductividad eléctrica, buena conformabilidad, resistencia moderada | Cables eléctricos, tuberías, intercambiadores de calor |
Aleaciones de magnesio | Principalmente magnesio con elementos como aluminio, manganeso o zinc | Muy ligero, buena relación resistencia-peso | Componentes de aeronaves, cajas electrónicas, artículos deportivos |
Superaleaciones | Combinaciones complejas de elementos como níquel, cobalto, cromo y otros | Excepcional resistencia a altas temperaturas y a la oxidación | Componentes de motores a reacción, motores de cohetes, turbinas de gas |
Aceros para herramientas | Alto contenido de carbono con elementos como cromo, tungsteno o vanadio | Dureza excepcional, resistencia al desgaste | Herramientas de corte, punzones, matrices |
Polvos metálicos específicos
Aunque la tabla anterior proporciona una base sólida, el mundo de los materiales de forja va más allá de las formas forjadas tradicionales. Los polvos metálicos son cada vez más populares en las aplicaciones de forja, ya que ofrecen ventajas únicas como la fabricación de formas casi netas y la reducción de residuos. He aquí algunos polvos metálicos destacados utilizados en forja:
- Polvos de acero atomizados con gas: Se producen enfriando rápidamente gotas de acero fundido, lo que da como resultado polvos muy esféricos con una excelente fluidez y densidad de empaquetamiento. Estos polvos son ideales para geometrías complejas y ofrecen propiedades mecánicas superiores a las del material de forja tradicional.
- Polvos de acero atomizados con agua: Una alternativa rentable a los polvos atomizados por gas, producidos por chorros de agua a alta presión que descomponen corrientes de acero fundido. Estos polvos suelen ser menos esféricos, pero siguen siendo adecuados para diversas aplicaciones de forja, sobre todo para geometrías más sencillas.
- Polvos de aleaciones a base de níquel: Similares en sus métodos de producción a los polvos de acero, ofrecen una excepcional resistencia a las altas temperaturas y a la corrosión, por lo que son ideales para las exigentes aplicaciones aeroespaciales y energéticas.
- Polvos de aleación de aluminio: La naturaleza ligera del aluminio brilla en forma de polvo, lo que permite crear componentes complejos y de alta resistencia para las industrias automovilística y aeroespacial.
- Polvos de aleación de titanio: A pesar de los retos que plantea el procesamiento debido a la reactividad del titanio, los avances en las técnicas de producción de polvo están haciendo que los polvos de aleaciones de titanio sean más viables para las aplicaciones de forja.
- Polvos de aleaciones de cobre: Estos polvos ofrecen una excelente conductividad eléctrica y pueden forjarse en formas intrincadas para aplicaciones en electrónica e intercambiadores de calor.
- Polvos de aleación de magnesio: La extrema ligereza del magnesio se traduce bien en la forja en polvo, lo que permite crear componentes ligeros de alta resistencia para aplicaciones en las que la reducción de peso es crucial, como en la industria aeroespacial y la electrónica portátil.
- Polvos de acero para herramientas: La dureza inherente y la resistencia al desgaste de los aceros para herramientas se conservan en forma de polvo, lo que los hace adecuados para forjar herramientas de corte y punzones complejos.
Aplicación de material de grado de forja
Con un elenco tan diverso de contendientes, la selección del material de forja adecuado se reduce a una cuidadosa evaluación de las exigencias de la aplicación. He aquí algunos factores clave a tener en cuenta:
- Fuerza: El componente debe soportar las fuerzas a las que se verá sometido durante su funcionamiento. Las aleaciones de alta resistencia, como las aleaciones de níquel y los aceros para herramientas, son ideales para aplicaciones exigentes.
- Dureza: La capacidad de absorber impactos sin fracturarse es crucial para los componentes que experimentan cargas de choque. Los aceros de medio y alto carbono, así como algunas aleaciones de aluminio, ofrecen una buena tenacidad.
- Resistencia a la corrosión: La exposición a entornos duros requiere materiales resistentes a la oxidación y la degradación. Los aceros inoxidables y las aleaciones de níquel destacan en este campo.
- Peso: Para aplicaciones en las que la reducción de peso es primordial, entran en juego materiales ligeros como el aluminio, el magnesio y las aleaciones de titanio.
- Maquinabilidad: La facilidad de mecanizado del material tras el forjado puede ser un factor decisivo. Los aceros al carbono y algunas aleaciones de aluminio ofrecen una buena mecanizabilidad.
- Costo: El coste del material siempre es un factor a tener en cuenta. Los aceros al carbono suelen ser la opción más asequible, mientras que las aleaciones exóticas, como las superaleaciones, tienen un precio más elevado.
Más allá de lo básico: Las propiedades de los materiales
El proceso de selección no se detiene en el tipo básico de material. Profundizar en las propiedades específicas del material proporciona una comprensión más matizada de su idoneidad. He aquí algunas propiedades cruciales que hay que tener en cuenta:
- Límite elástico: Es la tensión máxima que puede soportar un material antes de experimentar una deformación plástica. Un mayor límite elástico se traduce en un componente más resistente.
- Resistencia última a la tracción: Es la tensión máxima que puede soportar un material antes de romperse. Es importante para los componentes sometidos a grandes fuerzas de tracción.
- Elongación: La cantidad que un material puede estirarse antes de romperse. Un alargamiento elevado indica una buena ductilidad, lo que permite cierto moldeado tras la forja.
- Dureza: La resistencia a la indentación o al rayado. Los aceros para herramientas y algunos aceros con alto contenido en carbono poseen una dureza excepcional.
- Resistencia a la fatiga: Capacidad de soportar esfuerzos repetidos sin fallar. Esto es fundamental para los componentes sometidos a cargas cíclicas.
La comprensión de estas propiedades, junto con las exigencias de la aplicación, le permite tomar una decisión informada a la hora de seleccionar el material de forja óptimo.
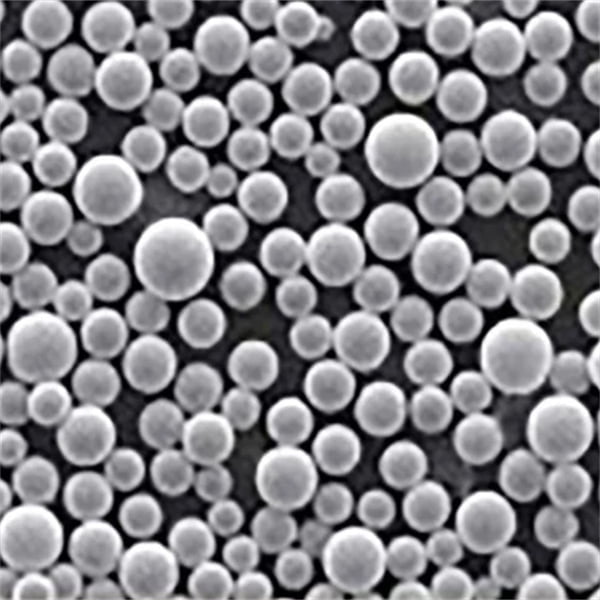
Ventajas y limitaciones
Ventajas de los materiales de grado de forja:
- Fuerza y resistencia superiores: El proceso de forja refina la estructura del grano, lo que da como resultado una resistencia y una tenacidad excepcionales en comparación con los componentes fundidos o mecanizados.
- Mayor resistencia a la fatiga: El flujo de grano controlado que se consigue mediante el forjado mejora la capacidad del material para soportar tensiones repetidas sin fallar.
- Flexibilidad de diseño: La forja permite crear formas complejas con características intrincadas, a diferencia de algunos procesos de fundición.
- Maquinabilidad mejorada: El proceso de forja puede mejorar la maquinabilidad de ciertos materiales, facilitando su acabado tras el forjado.
- Precisión dimensional: La forja puede producir componentes con tolerancias más estrictas que algunos métodos de fundición.
Limitaciones de los materiales de grado de forja:
- Coste elevado: El proceso de forja suele requerir más mano de obra y equipos especializados, lo que se traduce en costes de material más elevados en comparación con otros métodos de fabricación.
- Limitaciones de tamaño: El tamaño de las piezas forjadas está limitado por la capacidad del equipo de forja. Puede que no sea factible forjar componentes muy grandes o complejos.
- Generación de residuos: La forja puede generar una cantidad importante de material de desecho, sobre todo en el caso de formas complejas.
- Acabado superficial: Los componentes forjados pueden requerir un mecanizado adicional para conseguir un acabado superficial liso.
A pesar de estas limitaciones, la excepcional resistencia, tenacidad y flexibilidad de diseño que ofrecen los materiales de forja los convierten en una opción valiosa para una amplia gama de aplicaciones exigentes.
Aplicaciones de Materiales de forja
Los materiales de forja desempeñan un papel vital en innumerables industrias, dando forma a las herramientas y componentes que mueven nuestro mundo. He aquí algunas aplicaciones destacadas:
Industria | Ejemplos de componentes | Consideraciones materiales |
---|---|---|
Automoción | Cigüeñales, bielas, engranajes, componentes de suspensión | Alta resistencia, resistencia a la fatiga, buena maquinabilidad |
Aeroespacial | Componentes del tren de aterrizaje, largueros de las alas, discos del motor | Alta relación resistencia-peso, excelente resistencia a la corrosión, buena resistencia a la fatiga (aleaciones de aluminio, aleaciones de titanio, aleaciones de níquel) |
Petróleo y gas | Tubos de perforación, recipientes a presión, válvulas | Alta resistencia, buena resistencia a la corrosión a altas temperaturas (aceros aleados, aceros inoxidables) |
Construcción | Grúas, ganchos, cierres | Alta resistencia, buena tenacidad (aceros al carbono, aceros aleados) |
Médico | Instrumental quirúrgico, implantes | Alta resistencia, biocompatibilidad, resistencia a la corrosión (aceros inoxidables, aleaciones de titanio) |
Generación de energía | Álabes de turbina, ejes, recipientes a presión | Excepcional resistencia a altas temperaturas, resistencia a la fluencia, resistencia a la oxidación (superaleaciones, aleaciones de níquel) |
Bienes de consumo | Cuchillos, llaves inglesas, palos de golf | Alta resistencia, dureza, resistencia al desgaste (aceros para herramientas) |
Más allá de estas aplicaciones bien establecidas, los materiales de forja se exploran constantemente para usos nuevos e innovadores. Los avances en la ciencia de los materiales y las técnicas de forja están ampliando los límites de lo posible. Estas son algunas de las interesantes posibilidades que se vislumbran en el horizonte:
- Aligeramiento de vehículos: El uso de aleaciones avanzadas de aluminio y titanio en componentes forjados puede reducir significativamente el peso del vehículo, mejorando la eficiencia del combustible y las prestaciones.
- Integración de la fabricación aditiva: Combinar la forja con técnicas de fabricación aditiva como la impresión 3D permite crear componentes aún más complejos y ligeros.
- Exploración de nuevos materiales: Se siguen investigando nuevos materiales con propiedades excepcionales, lo que abre las puertas a componentes forjados aún más resistentes y duraderos.
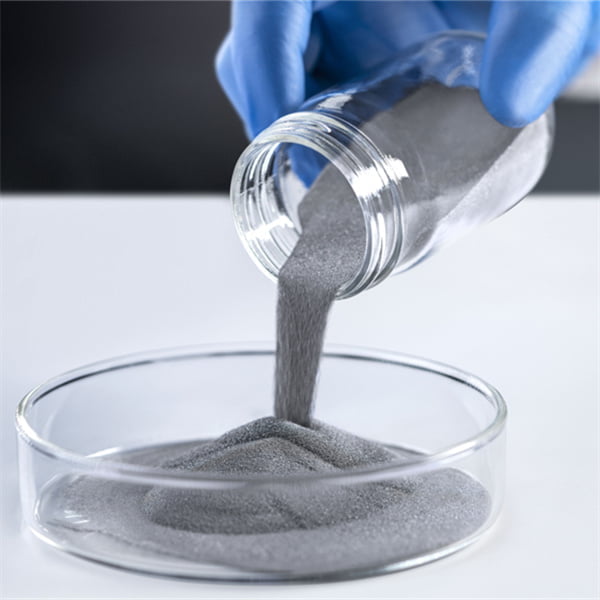
Preguntas frecuentes
Tabla: Preguntas frecuentes sobre materiales de grado de forja
Pregunta | Respuesta |
---|---|
¿Cuál es la diferencia entre el material de forja y el acero normal? | El material de forja está formulado específicamente para soportar las altas temperaturas y presiones que se dan en el proceso de forja. Suele tener una estructura de grano más fina y unas propiedades mecánicas superiores a las del acero normal. |
¿Puede forjar cualquier tipo de metal? | La mayoría de los metales pueden forjarse, pero algunos son más adecuados que otros. Factores como el punto de fusión, la trabajabilidad y la resistencia a la oxidación intervienen en la selección de un metal para forja. |
¿Cuáles son las ventajas de utilizar polvos metálicos en la forja? | Los polvos metálicos ofrecen varias ventajas, como la posibilidad de crear componentes con forma casi de red, la reducción de residuos y el potencial para geometrías más complejas. |
¿Cuáles son algunos de los retos asociados a la forja? | El elevado coste del equipo y la mano de obra, las limitaciones de tamaño y la generación de residuos son algunos de los retos asociados a la forja. |
¿Cómo influye la elección del material de forja en el producto acabado? | La elección del material influye considerablemente en la resistencia, la tenacidad, la resistencia a la corrosión, el peso y otras propiedades del componente forjado acabado. |
Compartir
MET3DP Technology Co., LTD es un proveedor líder de soluciones de fabricación aditiva con sede en Qingdao, China. Nuestra empresa está especializada en equipos de impresión 3D y polvos metálicos de alto rendimiento para aplicaciones industriales.
Solicite información para obtener el mejor precio y una solución personalizada para su empresa.
Artículos relacionados
Acerca de Met3DP
Actualización reciente
Nuestro producto
CONTACTO
¿Tiene alguna pregunta? ¡Envíenos un mensaje ahora! Atenderemos su solicitud con todo un equipo tras recibir su mensaje.
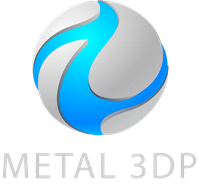
Polvos metálicos para impresión 3D y fabricación aditiva