Battery Frame Components for EV Cooling via Metal 3D Printing
Índice
Introduction: Revolutionizing EV Thermal Management with Metal 3D Printed Battery Cooling Frames
The electric vehicle (EV) revolution is accelerating, driven by advancements in battery technology, powertrain efficiency, and a global push towards sustainable transportation. At the heart of every high-performing EV lies its battery pack – a sophisticated energy storage system demanding precise control over its operating environment. Effective thermal management is paramount, directly impacting battery lifespan, performance, safety, and charging speed. Traditional manufacturing methods often struggle to produce the complex, lightweight, and highly efficient cooling components required to meet the ever-increasing demands of modern EVs. This is where fabricación aditiva (AM) de metales, commonly known as metal Impresión 3D, emerges as a transformative technology.
Specifically, the battery cooling frame, a critical component responsible for dissipating heat generated during charging and discharging cycles, stands to benefit significantly from AM. By utilizing advanced metal powders like Aluminum Silicon Magnesium alloys (AlSi10Mg) and Copper Chromium Zirconium (CuCrZr), manufacturers can now create cooling frames with intricate internal channel designs, optimized fluid flow paths, and significantly reduced weight compared to conventionally produced parts. Metal 3D printing enables the integration of complex features, consolidation of multiple parts into a single component, and rapid design iteration, accelerating development cycles and unlocking new levels of performance. For engineers and procurement managers in the competitive automotive sector, understanding the potential of metal AM for components like battery cooling frames is no longer optional; it’s essential for staying ahead. This technology offers a pathway to enhanced EV battery cooling, improved vehicle range, and greater overall system reliability, representing a significant leap forward in automotive innovation. Companies seeking reliable fabricación aditiva de metales solutions are increasingly turning to experienced partners capable of delivering high-quality components consistently.
As a leader in metal AM, Met3dp provides comprehensive solutions, leveraging decades of expertise in both advanced printing technologies and high-performance material science. Our commitment to quality, from powder production to final part verification, ensures that automotive clients receive components that meet the rigorous demands of the EV industry. Explore how our capabilities can power your next-generation thermal management systems.
The Critical Role of Battery Cooling Frames in Electric Vehicles
The battery pack is arguably the most critical and expensive component of an electric vehicle. Its health and efficiency directly dictate the vehicle’s range, acceleration, charging time, and overall longevity. Lithium-ion batteries, the current standard for EVs, are sensitive to temperature fluctuations. Operating outside their optimal temperature window (typically 15°C to 35°C) can lead to accelerated degradation, reduced capacity, thermal runaway risks, and compromised EV battery performance. Therefore, an effective thermal management system (BTMS) is not just beneficial; it’s fundamental to electric vehicle safety and reliability.
En battery cooling frame often serves a multi-functional role within the BTMS and the overall battery pack structure. Its primary function is heat dissipation. It typically incorporates channels or plates through which a coolant (liquid or sometimes air) circulates, absorbing excess heat from the battery cells and transferring it away to a radiator or heat exchanger. The design of these cooling channels is critical for ensuring uniform temperature distribution across all cells, preventing localized hot spots that can trigger degradation or failure.
Beyond thermal regulation, the cooling frame can also contribute to the structural integrity of the battery pack. It may form part of the enclosure, protecting the cells from external impacts and vibrations, and providing mounting points for other components. This structural integration aspect makes aligeramiento a key design driver. Reducing the frame’s weight directly contributes to improving the vehicle’s overall energy efficiency and range – crucial metrics in the competitive EV market.
The functions of a battery cooling frame can be summarized as:
- Heat Dissipation: Efficiently removing heat generated by battery cells during operation and charging.
- Temperature Uniformity: Ensuring consistent temperatures across the entire battery module to maximize lifespan and performance.
- Structural Support: Providing mechanical support and protection for the battery cells.
- Component Integration: Serving as a mounting point for sensors, wiring harnesses, and other battery management system components.
- Sealing and Containment: Preventing coolant leakage and protecting cells from environmental factors.
Given these critical roles, the design and manufacture of battery cooling frames demand high precision, specific material properties (like high thermal conductivity and good strength-to-weight ratio), and complex geometries. Traditional methods like casting, extrusion, or machining often face limitations in producing the intricate internal channels and thin walls required for optimal thermal performance and lightweighting. This is where the unique capabilities of automotive component manufacturing via metal 3D printing provide a distinct advantage, enabling designs previously considered impossible and enhancing overall powertrain efficiency. Procurement managers seeking reliable suppliers for these critical components must consider manufacturers with proven expertise in advanced materials and processes.
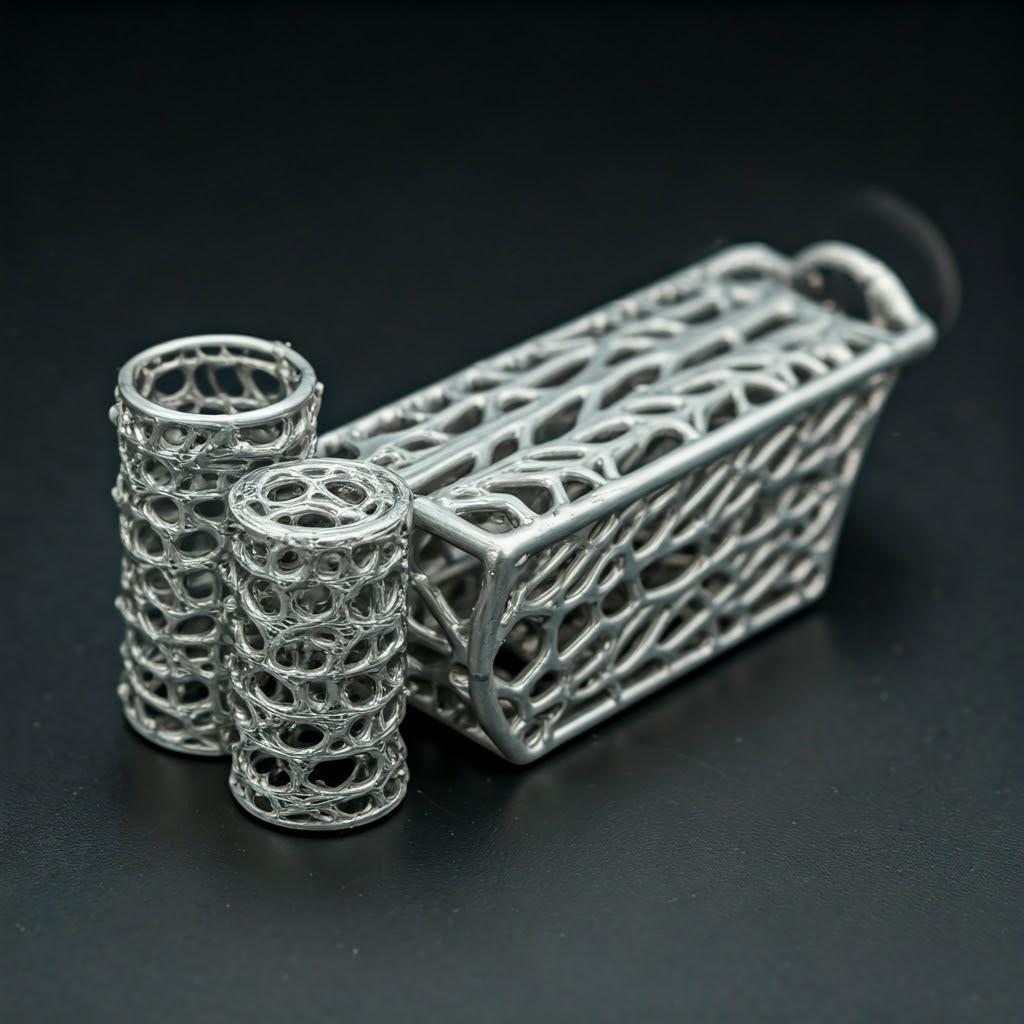
Why Metal Additive Manufacturing is Ideal for EV Battery Cooling Components
The transition towards electrification presents automotive manufacturers with significant engineering challenges, particularly in thermal management and lightweighting. Metal additive manufacturing offers compelling solutions to these challenges, making it an increasingly attractive option for producing components like EV battery cooling frames. The advantages over traditional manufacturing methods (casting, CNC machining, stamping, brazing) are numerous and impactful:
- Unparalleled Design Freedom & Complexity:
- Intricate Cooling Channels: AM allows for the creation of highly complex internal cooling channel geometries, including conformal channels that precisely follow the contours of battery cells, maximizing surface area contact and heat transfer efficiency. Designs can incorporate features like turbulators or optimized flow paths that are impossible or prohibitively expensive to achieve with traditional methods. Think micro-channels, variable cross-sections, and bio-inspired structures for maximum thermal performance.
- Optimización de la topología: Engineers can use computational tools to optimize the frame’s structure, removing material from low-stress areas while reinforcing critical points. This results in significantly lighter parts (**lightweight structures**) without compromising structural integrity – crucial for extending EV range.
- Consolidación de piezas: Multiple components (e.g., flow distributors, mounting brackets, frame sections) that would traditionally be manufactured separately and then assembled (often requiring brazing or welding, which can be failure points) can be integrated and printed as a single, monolithic part. This reduces assembly time, cost, weight, and potential leak paths, leading to more robust consolidated parts.
- Accelerated Development & Prototyping:
- Iteración rápida: Metal AM enables rapid prototyping automotive components directly from CAD data. Design modifications for cooling channels or structural elements can be implemented and tested within days, rather than the weeks or months required for tooling modifications in casting or extrusion. This dramatically speeds up the development cycle for new battery pack designs.
- Tool-Less Production: AM eliminates the need for expensive and time-consuming tooling (molds, dies). This is particularly beneficial for low-to-mid volume production runs, customization, or producing legacy parts where original tooling no longer exists.
- Material Advantages & Optimization:
- Aleaciones avanzadas: AM processes can effectively utilize high-performance alloys specifically chosen for their thermal conductivity (like Copper alloys) or strength-to-weight ratio (like Aluminum alloys), tailored precisely to the application’s needs. Met3dp specializes in processing materials like AlSi10Mg and offers expertise in developing parameters for alloys like CuCrZr.
- Optimized Material Usage: AM is an additive process, meaning material is only placed where needed. This often results in less material waste compared to subtractive methods like CNC machining, contributing to cost savings and sustainability.
- Flexibilidad de la cadena de suministro y producción bajo demanda:
- Decentralized Manufacturing: Parts can potentially be printed closer to the point of assembly, reducing shipping costs and lead times.
- Inventario digital: Designs are stored digitally, allowing parts to be printed on-demand, reducing the need for large physical inventories.
While traditional methods remain suitable for very high-volume production of simpler designs, the unique metal AM benefits – complexity, consolidation, speed, and optimization – make it exceptionally well-suited for the demanding requirements of next-generation EV battery cooling frames. As the industry pushes for higher energy densities and faster charging, the ability to create highly optimized thermal management components through AM will become increasingly critical. Choosing a knowledgeable impresión 3D en metal partner like Met3dp, with expertise in relevant materials and processes, is key to leveraging these advantages effectively.
Material Deep Dive: AlSi10Mg and CuCrZr for Optimal Thermal Performance
The choice of material is fundamental to the performance of an EV battery cooling frame. The material must possess a combination of properties: high thermal conductivity to efficiently draw heat away from the cells, good mechanical strength to handle structural loads and vibrations, low density for lightweighting, corrosion resistance against coolants, and excellent processability via additive manufacturing. Two standout candidates often considered for this application are AlSi10Mg (an aluminum alloy) and CuCrZr (a copper alloy). Understanding their respective strengths and weaknesses is crucial for automotive materials selection.
1. AlSi10Mg (Aluminum-Silicon-Magnesium Alloy): The Lightweight Workhorse
AlSi10Mg is one of the most widely used aluminum alloys in metal additive manufacturing, particularly Laser Powder Bed Fusion (LPBF). Its popularity stems from its excellent balance of properties and good processability.
- Propiedades:
- Good Thermal Conductivity: While not as high as pure aluminum or copper alloys, AlSi10Mg offers respectable thermal conductivity (typically 120-140 W/m·K after heat treatment), sufficient for many liquid cooling applications.
- Excelente relación resistencia-peso: This is a major advantage. Aluminum alloys are significantly lighter than steel or copper, contributing directly to vehicle lightweighting and improved range. AlSi10Mg offers good mechanical strength and hardness, especially after appropriate heat treatment.
- Buena resistencia a la corrosión: Aluminum naturally forms a protective oxide layer, providing decent resistance to common automotive coolants.
- Excelente imprimibilidad: AlSi10Mg is well-understood and relatively easy to process using LPBF systems, exhibiting good melt pool stability and resulting in dense parts.
- Rentabilidad: Compared to copper alloys, aluminum powders are generally more cost-effective.
- Suitability for Cooling Frames: AlSi10Mg is an excellent choice when lightweighting is a primary driver and the thermal loads are manageable. Its processability allows for the complex geometries needed for efficient cooling channels. It’s often the default choice for structural components with integrated cooling functions. Post-processing, including heat treatment (like T6 aging) is typically required to achieve optimal mechanical properties.
- Met3dp’s Offering: Met3dp possesses extensive experience in processing AlSi10Mg powder, utilizing advanced gas atomization techniques to produce highly spherical powders with excellent flowability, crucial for achieving consistent density and mechanical properties in printed parts. Our rigorous quality control ensures powder batches meet stringent automotive specifications.
Table: AlSi10Mg Properties (Typical Values for AM)
Propiedad | Typical Value (Post Heat Treatment) | Unidad | Significance for Cooling Frames |
---|---|---|---|
Densidad | ~2.67 | g/cm³ | Excellent for Lightweighting |
Conductividad térmica | 120 – 140 | W/(m-K) | Good heat dissipation capability |
Límite elástico | 230 – 280 | MPa | Good structural integrity |
Resistencia a la tracción | 330 – 400 | MPa | Robustness against mechanical loads |
Alargamiento a la rotura | 6 – 10 | % | Ductility, resistance to fracture |
Imprimibilidad | Excelente | N/A | Enables complex designs, reliable manufacturing |
Coste relativo | Moderado | N/A | Cost-effective solution |
Exportar a hojas
2. CuCrZr (Copper-Chromium-Zirconium Alloy): The Thermal Conductivity Champion
When maximum heat dissipation is the absolute priority, copper alloys like CuCrZr come into play. Copper boasts significantly higher thermal conductivity than aluminum.
- Propiedades:
- Exceptional Thermal Conductivity: This is the primary advantage of CuCrZr. Its thermal conductivity (typically >300 W/m·K) is more than double that of AlSi10Mg, enabling extremely efficient heat transfer, crucial for high-power battery packs or fast-charging scenarios.
- Good High-Temperature Strength: CuCrZr maintains reasonable strength at elevated temperatures compared to pure copper.
- Buena conductividad eléctrica: While less critical for cooling frames, its high electrical conductivity is notable.
- Higher Density: Copper alloys are significantly denser (~8.9 g/cm³) than aluminum alloys, posing a challenge for lightweighting objectives. The weight penalty must be justified by the superior thermal performance.
- Retos de procesamiento: Copper alloys are notoriously more challenging to process via laser-based AM due to their high reflectivity and thermal conductivity, which can lead to process instabilities and defects like porosity if not handled with expertise and optimized equipment. Electron Beam Melting (EBM/SEBM), like the systems potentially offered or utilized by Met3dp partners, can sometimes offer advantages for processing copper due to better energy absorption.
- Mayor coste: Copper alloy powders are generally more expensive than aluminum alloy powders.
- Suitability for Cooling Frames: CuCrZr is the preferred material when thermal performance is paramount and outweighs the concerns of added weight and cost. It’s ideal for localized high-heat flux areas or demanding applications requiring the rapid removal of large amounts of heat. The design must leverage the material’s thermal properties to justify its use, often requiring highly optimized, thin-walled structures achievable through AM.
- Met3dp’s Approach: While copper alloys present challenges, Met3dp’s focus on advanced powder production and process control through its SEBM printers and expertise positions it to tackle demanding materials. We work closely with clients to determine the feasibility and optimize parameters for materials like CuCrZr, ensuring parts meet stringent thermal and mechanical requirements. Access to high-quality, gas-atomized CuCrZr powder with controlled characteristics is key, an area where Met3dp’s Sistema avanzado de fabricación de polvo sobresale.
Table: CuCrZr Properties (Typical Values for AM)
Propiedad | Typical Value (Post Heat Treatment) | Unidad | Significance for Cooling Frames |
---|---|---|---|
Densidad | ~8.9 | g/cm³ | Significant Weight Penalty vs. Aluminum |
Conductividad térmica | >300 | W/(m-K) | Exceptional heat dissipation capability |
Límite elástico | 350 – 450 | MPa | Buena resistencia mecánica |
Resistencia a la tracción | 450 – 550 | MPa | High robustness |
Alargamiento a la rotura | 10 – 20 | % | Buena ductilidad |
Imprimibilidad | Challenging (Requires Expertise) | N/A | Process control is critical for part quality |
Coste relativo | Alta | N/A | Cost justified by performance needs |
Exportar a hojas
Conclusion on Materials:
The choice between AlSi10Mg and CuCrZr depends heavily on the specific requirements of the EV battery cooling frame application.
- Elija AlSi10Mg if: Lightweighting is critical, thermal loads are moderate, cost is a major factor, and ease of processing is desired.
- Elija CuCrZr if: Maximum thermal dissipation is the primary goal, higher weight is acceptable, and the budget allows for a more premium material and potentially more complex processing.
Often, hybrid approaches or localized use of copper inserts within an aluminum frame might be considered, though AM allows for monolithic designs in either material. Working with a high-performance alloys supplier and AM expert like Met3dp ensures that the material selection is optimized for performance, cost, and manufacturability, leveraging the full potential of metal 3D printing for advanced EV thermal management.
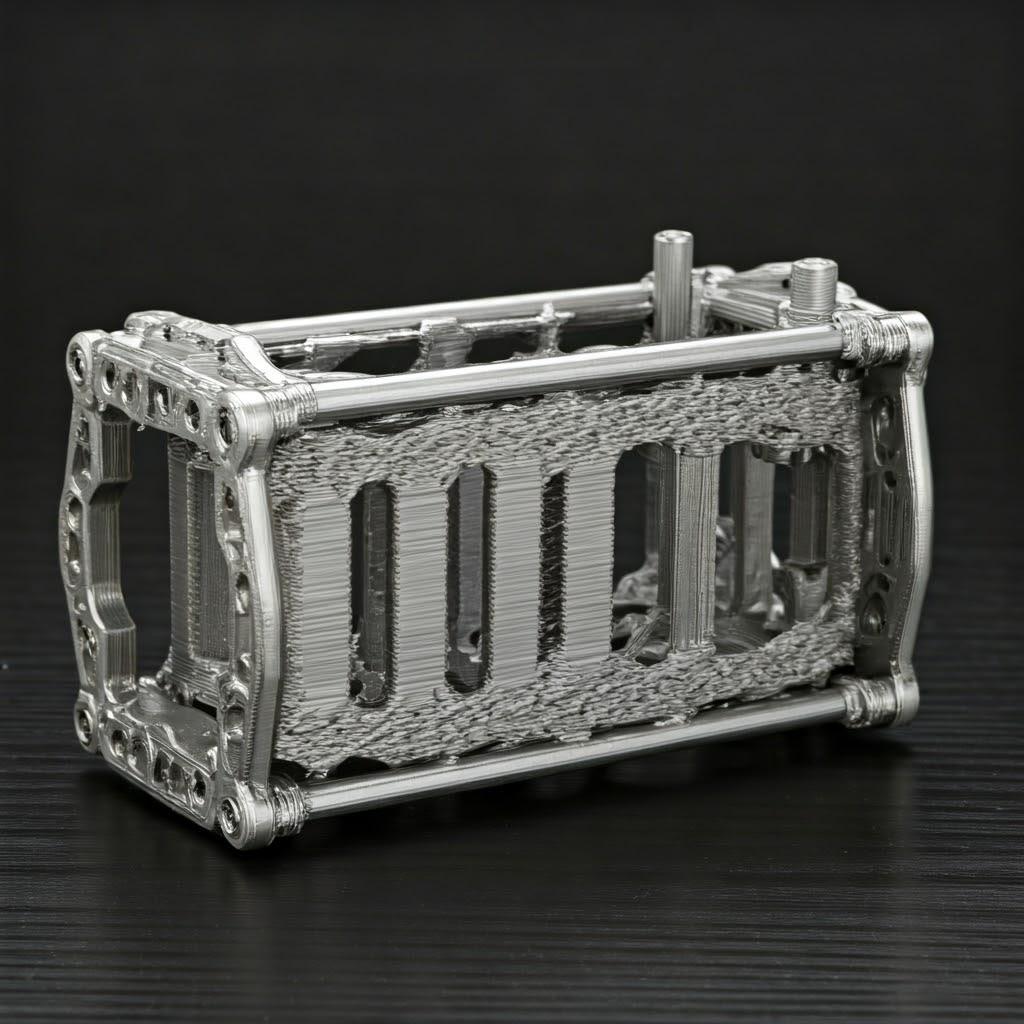
Design for Additive Manufacturing (DfAM) Principles for Battery Cooling Frames
Simply replicating a design intended for traditional manufacturing using metal 3D printing rarely unlocks the full potential of additive technology. To truly leverage the benefits of AM for components like EV battery cooling frames, engineers must embrace Diseño para fabricación aditiva (DfAM) principles. DfAM involves rethinking the design process to maximize the advantages offered by layer-by-layer fabrication, such as geometric complexity, part consolidation, and lightweighting, while also considering the constraints of the specific AM process (e.g., Laser Powder Bed Fusion – LPBF, or Selective Electron Beam Melting – SEBM). Applying DfAM automotive strategies is crucial for developing high-performance, cost-effective cooling solutions.
Key DfAM principles relevant to EV battery cooling frames include:
- Optimizing Internal Cooling Channels:
- Geometrías complejas: Move beyond simple straight or circular channels. AM allows for smoothly curved paths, variable cross-sections, and conformal channels that precisely follow the shape of battery cells or modules. This maximizes the contact area for heat transfer and can reduce pressure drop.
- Flow Optimization Features: Integrate features like internal fins, turbulators, or optimized manifolds directly into the design to enhance coolant mixing and heat transfer efficiency. Computational Fluid Dynamics (CFD) simulations become powerful tools when combined with the geometric freedom of AM for optimizing cooling channels.
- Self-Supporting Channels: Design internal channels with cross-sections (e.g., teardrop, diamond) and orientations that minimize or eliminate the need for internal support structures, which can be very difficult or impossible to remove after printing. Angles greater than 45 degrees from the horizontal are generally self-supporting.
- Lightweighting Strategies:
- Optimización de la topología: Utilize software tools to analyze the structural loads on the frame and automatically remove material from non-critical areas, resulting in organic-looking, highly efficient structures. This is a cornerstone of lightweight component design for EVs.
- Estructuras reticulares: Incorporate internal lattice or cellular structures within thicker sections of the frame. These structures significantly reduce weight and material consumption while maintaining required stiffness and strength. They can also potentially enhance crash performance through energy absorption.
- Thin Walls: AM allows for the creation of very thin, yet structurally sound walls (down to approx. 0.3-0.5 mm depending on material and machine), further reducing weight compared to the minimum wall thicknesses achievable with casting.
- Consolidación de piezas:
- Integrated Features: Design mounting brackets, sensor housings, flow connectors, and structural elements as integral parts of the cooling frame. This eliminates assembly steps, reduces part count, minimizes potential leak points (like seals or brazed joints), and often decreases overall weight and cost.
- Minimizing Support Structures:
- Orientación: Carefully consider the part’s orientation on the build plate. Orienting features to be self-supporting (generally >45° overhangs) reduces the volume of support structures needed.
- Support Optimization: Where supports are unavoidable (e.g., large flat undersides), design them for easy removal and minimal impact on critical surfaces. Utilize specialized support types (e.g., tree supports, block supports) offered by AM preparation software.
- Stress Reduction: Consider how part geometry and orientation influence residual stress build-up during printing. Large flat areas or abrupt transitions can increase stress and warping potential.
- Process-Specific Considerations:
- Tamaño mínimo de característica: Understand the resolution limits of the chosen AM process (LPBF typically offers finer features than SEBM). Ensure that critical features like thin walls or small channel details are within the machine’s capability.
- Eliminación del polvo: Ensure the design includes pathways or openings to allow unfused powder to be easily removed from internal channels and cavities after printing. Trapped powder can add weight and potentially interfere with operation.
By applying these DfAM principles, engineers can move beyond incremental improvements and achieve step-changes in cooling performance, weight reduction, and component integration. Collaborating with an AM expert like Met3dp during the design phase can provide invaluable insights into process capabilities and constraints, ensuring the design is optimized for manufacturability and performance. Met3dp’s team can assist with DfAM, leveraging various métodos de impresión to best suit the specific requirements of your EV battery cooling frame.
Achieving Precision: Tolerances, Surface Finish, and Accuracy in Metal AM
While metal additive manufacturing offers unprecedented design freedom, it’s crucial for engineers and procurement managers to understand the levels of precision achievable regarding dimensional accuracy, tolerances, and surface finish. These factors directly impact the functionality, assembly, and performance of EV battery cooling frames, particularly concerning sealing surfaces, interfaces with battery modules, and coolant flow characteristics. Achieving the required metal 3D printing tolerances y surface finish standards automotive applications demand requires careful control over the entire AM workflow.
Dimensional Accuracy and Tolerances:
The accuracy of a metal AM part refers to how closely its final dimensions match the original CAD model. Tolerances define the permissible variation for specific dimensions. Typical achievable accuracy and tolerances depend on several factors:
- Proceso AM: LPBF generally offers higher accuracy and finer detail compared to SEBM, although SEBM can be faster for certain geometries and materials.
- Calibración de la máquina: The precision and calibration of the 3D printer are critical. Well-maintained, high-quality machines, like those utilized by Met3dp, are essential.
- Material: Different materials behave differently during melting and solidification, influencing shrinkage and potential distortion. AlSi10Mg and CuCrZr have different thermal properties that affect final accuracy.
- Part Size and Geometry: Larger parts or complex geometries are more prone to thermal stresses and potential deviation.
- Orientación de construcción: The orientation of the part on the build plate affects accuracy due to the anisotropic nature of the layer-by-layer process.
- Post-procesamiento: Steps like heat treatment can cause slight dimensional changes, while CNC machining is often used to achieve very tight tolerances on critical features.
Valores típicos:
- General Tolerances (As-Printed): For well-controlled LPBF processes, general dimensional tolerances are often in the range of ±0.1 mm to ±0.2 mm for smaller features (e.g., up to 50-100 mm), potentially increasing slightly for larger dimensions (e.g., ±0.2% of the nominal dimension).
- Tighter Tolerances (with Machining): For critical interfaces, mounting points, or sealing surfaces requiring tighter control, post-process CNC machining is typically employed. Machining can easily achieve tolerances of ±0.025 mm to ±0.05 mm or even tighter, matching conventional manufacturing standards.
Acabado superficial (rugosidad):
Surface finish, often quantified by the arithmetic average roughness (Ra), is another crucial aspect, especially for internal cooling channels and sealing surfaces.
- As-Printed Surface Roughness: The surface finish of AM parts is inherently rougher than machined surfaces due to the layer-wise buildup and partially melted powder particles adhering to the surface.
- Top Surfaces: Generally smoother (Ra 5-10 µm).
- Vertical Walls: Moderate roughness (Ra 8-15 µm).
- Up-facing/Down-facing Surfaces: Roughness depends heavily on the angle relative to the build plate. Down-facing surfaces (<45°) require support structures, and their removal leaves witness marks, increasing roughness significantly (Ra > 15-20 µm).
- Canales internos: The roughness inside narrow or complex internal channels is particularly challenging to control and improve. As-printed roughness can impact fluid dynamics, potentially increasing pressure drop or affecting heat transfer coefficients. DfAM considerations (e.g., channel shape, orientation) play a role here.
- Mejora del acabado superficial: Post-processing methods are essential for achieving smoother surfaces:
- Mecanizado por flujo abrasivo (AFM): Can be used to smooth internal channels.
- Bead Blasting/Sandblasting: Provides a uniform matte finish and removes loose powder but only moderately reduces Ra.
- Tumbling/Vibratory Finishing: Effective for smoothing external surfaces of smaller parts.
- Pulido: Manual or automated polishing for achieving very smooth, mirror-like finishes (Ra < 0.8 µm) on specific areas.
- Mecanizado: Provides the best surface finish control on accessible features.
Control de calidad:
Ensuring consistent dimensional accuracy metal AM parts requires rigorous quality control throughout the process. This includes:
- Powder quality verification.
- Calibrado y mantenimiento periódicos de las máquinas.
- In-process monitoring (e.g., melt pool monitoring).
- Post-build dimensional inspection using CMM (Coordinate Measuring Machines) or 3D scanning.
- Surface roughness measurements.
Met3dp places a strong emphasis on quality control, employing advanced metrology equipment and stringent process monitoring to ensure that EV battery cooling frames meet the precise specifications required by automotive clients. Understanding the achievable precision and planning for necessary post-processing steps are key parts of the procurement process for impresión 3D en metal componentes.

Essential Post-Processing Steps for 3D Printed Cooling Frames
Metal 3D printed parts, including EV battery cooling frames made from AlSi10Mg or CuCrZr, rarely come off the printer ready for final use. Post-processing is a critical stage in the manufacturing workflow, necessary to achieve the required material properties, dimensional tolerances, surface finish, and overall functionality. Understanding these steps is vital for procurement managers and engineers when planning production schedules and estimating costs.
Common post-processing steps for metal AM battery cooling frames include:
- Alivio del estrés / Tratamiento térmico:
- Propósito: The rapid heating and cooling cycles inherent in AM processes (especially LPBF) induce internal stresses within the printed part. These residual stresses can cause distortion or cracking during printing, support removal, or later in the part’s lifecycle. Heat treatment relieves these stresses and, importantly, modifies the material’s microstructure to achieve desired mechanical properties (strength, hardness, ductility).
- Procedimiento:
- Alivio del estrés: Typically performed while the part is still attached to the build plate, involving heating the part to a specific temperature (below the aging temperature for AlSi10Mg) and holding it for a defined period, followed by slow cooling.
- Solution Annealing & Aging (e.g., T6 for AlSi10Mg): For alloys like AlSi10Mg, a multi-stage heat treatment (solutionizing at high temperature, quenching, then artificial aging at a lower temperature) is often required to significantly increase strength and hardness. Specific heat treatment AlSi10Mg cycles depend on the desired final properties. CuCrZr also benefits from specific heat treatments to optimize its strength and conductivity.
- Consideraciones: Heat treatment must be carefully controlled (atmosphere, temperature ramps, hold times) to achieve consistent results. It can cause slight dimensional changes that need to be accounted for.
- Extracción de la pieza de la placa de montaje:
- Propósito: Separating the printed component(s) from the metal build plate they were fused to during printing.
- Procedimiento: Typically done using wire EDM (Electrical Discharge Machining) or a bandsaw. Care must be taken not to damage the part.
- Retirada de la estructura de soporte:
- Propósito: Removing the temporary structures printed to support overhangs and complex features during the build process.
- Procedimiento: This can be a challenging and labor-intensive step, especially for complex internal geometries. Methods include:
- Manual removal using pliers, cutters, or grinders.
- CNC machining.
- Sometimes electrochemical machining or other methods for hard-to-reach areas.
- Consideraciones: Support removal can leave witness marks or burrs on the surface, often requiring further finishing steps. DfAM plays a crucial role in minimizing the need for supports and designing them for easier removal.
- Mecanizado CNC:
- Propósito: To achieve tight tolerances on critical dimensions, create precise mating surfaces, ensure flatness for sealing, or improve surface finish on specific features.
- Procedimiento: Using standard CNC milling or turning operations to machine specific areas of the AM part.
- Aplicaciones: Machining bolt holes to precise diameters and positions, creating O-ring grooves, flattening sealing surfaces, achieving specific Ra values on interfacing features. CNC machining metal AM parts is very common for functional components.
- Acabado y limpieza de superficies:
- Propósito: To remove loose powder, improve surface smoothness, achieve a desired aesthetic appearance, or prepare the surface for coating.
- Procedures:
- Eliminación del polvo: Depowdering using compressed air, vibration, or specialized equipment, particularly crucial for internal channels.
- Blasting: Bead blasting or sandblasting creates a uniform matte finish.
- Tumbling/Vibratory Finishing: Smooths external surfaces and edges.
- Pulido: For very low Ra values on specific areas.
- Mecanizado por flujo abrasivo (AFM) / Rectificado por extrusión: Used to smooth internal channels by flowing abrasive media through them.
- Leak Testing:
- Propósito: Absolutely critical for any component designed to carry coolant. Ensures the integrity of the cooling channels and prevents leaks.
- Procedimiento: Involves pressurizing the cooling channels (typically with air or helium underwater or using pressure decay sensors) to detect any leaks or porosity that breaches the channel walls. Leak testing cooling systems is a non-negotiable quality assurance step.
- Inspection and Quality Control:
- Propósito: Verifying that the part meets all dimensional, material, and functional specifications.
- Procedimiento: Dimensional inspection (CMM, 3D scanning), surface roughness measurement, material property testing (if required), final visual inspection.
El específico servicios de posprocesamiento required will depend on the complexity of the cooling frame design, the material used, and the application’s specific requirements. Partnering with a full-service provider like Met3dp, which understands the intricacies of both printing and post-processing, ensures a streamlined workflow and high-quality final components ready for integration into the EV battery pack.
Overcoming Challenges in Metal 3D Printing for Automotive Applications
While metal additive manufacturing offers significant advantages for producing complex components like EV battery cooling frames, it’s not without its challenges. Successfully implementing AM for demanding automotive applications requires expertise, careful process control, and an understanding of potential pitfalls. Addressing these challenges proactively is key to ensuring part quality, reliability, and cost-effectiveness.
Common challenges and mitigation strategies include:
- Tensión residual y alabeo:
- Desafío: The rapid, localized heating and cooling inherent in powder bed fusion processes create thermal gradients, leading to internal stresses within the part. Excessive residual stress metal AM parts can cause warping during the build, distortion after removal from the build plate, or even cracking. Large, flat sections or sharp geometric transitions exacerbate this.
- Mitigación:
- DfAM: Designing parts with stress-reducing features (e.g., avoiding large solid blocks, using lattice structures, adding sacrificial ribs).
- Build Strategy: Optimizing part orientation, using appropriate support structures (which also help anchor the part and dissipate heat), and optimizing laser/electron beam scan strategies.
- Parámetros del proceso: Fine-tuning parameters like layer thickness, energy input, and platform heating (especially relevant in SEBM).
- Post-procesamiento: Performing effective stress relief heat treatments immediately after printing, often before removing the part from the build plate.
- Porosidad:
- Desafío: Small voids or pores can form within the printed material due to trapped gas, incomplete fusion between layers, or keyholing phenomena (vapor depressions collapsing). Porosity can compromise mechanical properties (especially fatigue life) and, critically for cooling frames, can create leak paths if pores link up or breach a surface.
- Mitigación:
- Calidad del polvo: Using high-quality, spherical metal powders with low internal porosity and controlled particle size distribution, like those produced using Met3dp’s advanced gas atomization. Ensuring proper powder handling and storage to prevent moisture absorption.
- Parameter Optimization: Developing and validating robust process parameters (laser power, scan speed, hatch spacing, layer thickness) specific to the material and machine to ensure complete melting and fusion. Met3dp invests heavily in process parameter development.
- Supervisión de procesos: Utilizing in-situ monitoring systems (e.g., melt pool monitoring) to detect potential anomalies during the build.
- Post-procesamiento: Hot Isostatic Pressing (HIP) can be used in some cases to close internal pores, although it adds cost and complexity. Proper leak testing is essential to detect critical porosity.
- Retirada de la estructura de soporte:
- Desafío: While necessary, support structures add time and cost to both the printing and post-processing stages. Removing them, especially from complex internal channels or delicate features, can be difficult, labor-intensive, and risks damaging the part surface.
- Mitigación:
- DfAM: Designing for self-supporting angles (>45°) wherever possible, optimizing internal channel shapes, and strategically orienting the part.
- Support Design: Using specialized software features to generate supports that are effective yet easier to remove (e.g., thinner contact points, perforated structures).
- Técnicas de postprocesado: Employing appropriate removal methods (manual, CNC, potentially electrochemical) based on support location and part geometry.
- Acabado superficial:
- Desafío: The inherent layer-by-layer nature and powder adhesion result in a rougher surface finish compared to traditional machining. This can be problematic for sealing surfaces or inside cooling channels where it affects fluid flow.
- Mitigación:
- Parameter Optimization: Fine-tuning parameters can slightly improve as-built surface finish.
- Orientación: Orienting critical surfaces optimally on the build plate.
- Post-procesamiento: Implementing necessary finishing steps like machining, polishing, blasting, or AFM, as discussed previously.
- Consistency and Scalability:
- Desafío: Ensuring consistent part quality across multiple builds and different machines, and scaling production efficiently to meet automotive volume demands, requires robust process control and quality management systems.
- Mitigación:
- Normalización: Implementing standardized workflows, rigorous machine calibration, and consistent powder management protocols.
- Quality Management Systems: Adhering to relevant certifications (e.g., ISO 9001, potentially IATF 16949 for automotive suppliers).
- Process Monitoring & Data Analysis: Continuously monitoring build data to ensure consistency and identify potential deviations.
- Partnerships: Working with experienced AM providers like Met3dp who have established quality systems and experience in scaling production.
- Costo:
- Desafío: Metal AM can have higher upfront costs per part compared to traditional methods, especially for simple designs at high volumes, due to machine investment, material costs, and process time.
- Mitigación:
- DfAM: Leveraging part consolidation and lightweighting to offset costs through reduced assembly time and material usage.
- Optimización de procesos: Minimizing build time and support structures.
- Volumen: Costs per part decrease significantly as production volume increases.
- Total Cost of Ownership: Considering savings from faster development, improved performance, and supply chain flexibility, not just the individual part cost.
Overcoming these challenges requires a deep understanding of materials science, AM process physics, DfAM principles, and rigorous quality control. Partnering with an experienced impresión 3D en metal service provider like Met3dp, which possesses the necessary technology, expertise, and commitment to quality assurance automotive AM demands, is crucial for successfully implementing metal AM for critical components like EV battery cooling frames. Our team works collaboratively with clients to navigate these complexities and deliver optimized, reliable solutions.
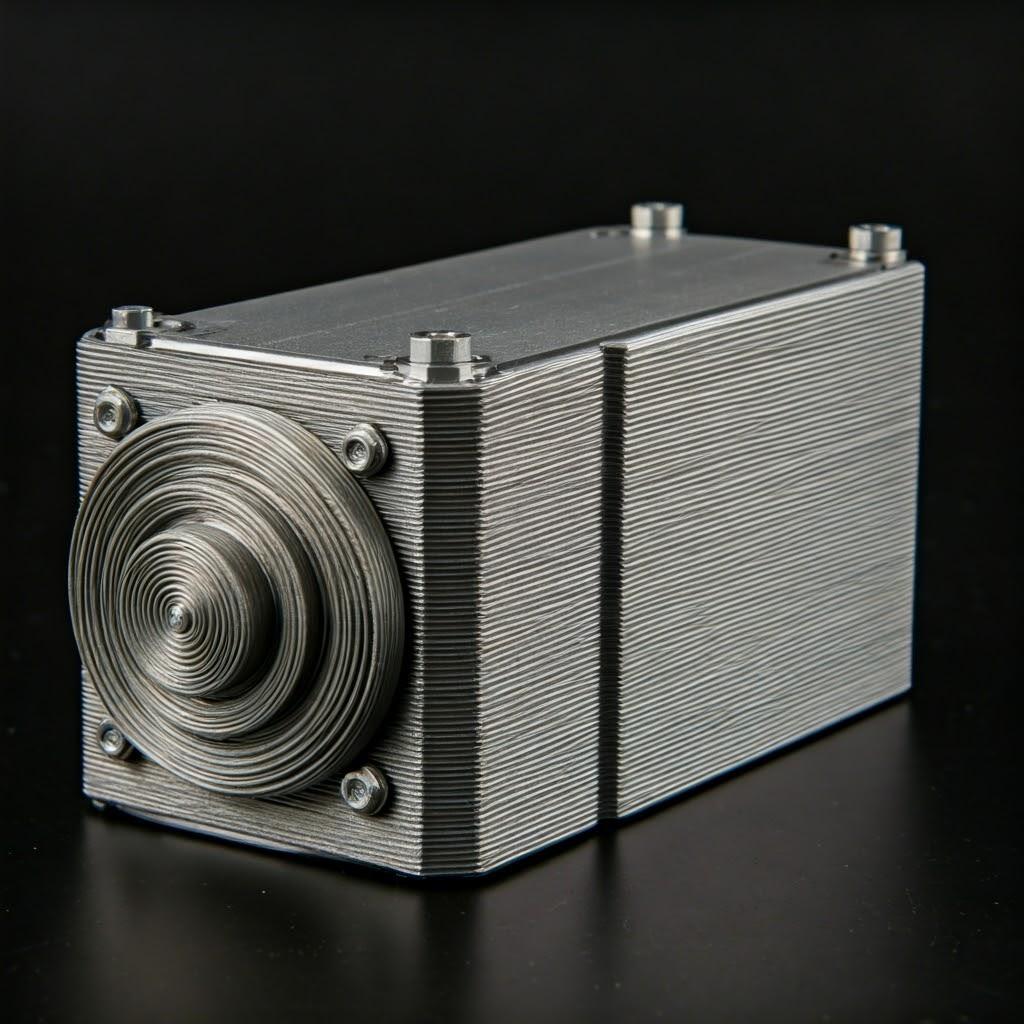
Selecting Your Metal Additive Manufacturing Partner: Key Considerations for EV Suppliers
Choosing the right manufacturing partner is as critical as the technology itself, especially when dealing with demanding automotive components like EV battery cooling frames. The success of your project hinges on the provider’s expertise, reliability, and ability to meet stringent quality standards. For engineers and procurement managers navigating the metal 3D printing service provider landscape, several key factors should guide the automotive AM supplier evaluation process:
- Technical Expertise and Experience:
- Material Specialization: Does the provider have proven experience with the specific alloys you require (e.g., AlSi10Mg, CuCrZr)? Ask for case studies or examples of similar projects. Deep material expertise AM is crucial, covering powder handling, parameter development, and understanding material behavior during printing and post-processing.
- Process Knowledge: Are they proficient in the most suitable AM process (LPBF, SEBM) for your application? Do they understand the nuances of achieving optimal density, accuracy, and material properties?
- Experiencia en el sector: Have they worked within the automotive sector or other demanding industries (aerospace, medical) with similar quality expectations? Understanding automotive component manufacturing requirements is key.
- Technology and Equipment:
- Machine Quality & Capability: What types of printers do they operate? Are they well-maintained and calibrated? Do they have machines capable of handling the required build volume and achieving the necessary precision? Met3dp utilizes industry-leading printers known for their accuracy and reliability.
- Powder Quality Control: How do they source and manage their metal powders? Do they have robust quality control for incoming materials? Met3dp’s advantage lies in its in-house production of high-quality, spherical metal powders using advanced atomization techniques.
- Software & Simulation: Do they utilize advanced build preparation software and potentially simulation tools to optimize orientation, supports, and predict potential issues like distortion?
- Quality Management Systems:
- Certificaciones: Does the provider hold relevant quality certifications, such as ISO 9001? While IATF 16949 (the automotive standard) is still emerging for many AM providers, demonstrating adherence to rigorous quality protocols is essential.
- Control de procesos: What measures are in place for in-process monitoring and quality checks throughout the manufacturing workflow (powder handling, printing, post-processing, inspection)?
- Trazabilidad: Can they provide full traceability for materials and process parameters for each part produced?
- Capacity and Scalability:
- Volumen de producción: Can the provider handle your required production volumes, from prototyping to potentially low- or mid-series production? Do they have sufficient machine capacity and skilled personnel?
- Plazos de entrega: Can they meet your project timelines? Do they have a track record of reliable delivery?
- Engineering and Support Services:
- Apoyo al DfAM: Can they offer expert advice on Design for Additive Manufacturing to help optimize your cooling frame design for performance, cost, and manufacturability?
- Capacidades de postprocesado: Do they offer a comprehensive range of in-house or closely managed post-processing services (heat treatment, machining, finishing, testing)?
- Communication & Collaboration: Are they responsive, transparent, and willing to work collaboratively to solve challenges? Choosing AM partner is about building a relationship, not just a transaction.
- Total Value Proposition:
- Rentabilidad: While cost is a factor, evaluate the total value, considering quality, reliability, expertise, speed, and support, not just the price per part.
- Location & Logistics: Consider the provider’s location relative to your assembly facilities and their logistical capabilities.
Met3dp embodies these qualities, positioning itself not just as a supplier but as a strategic partner. With deep roots in both additive manufacturing solutions and advanced metal powder production, we offer a unique blend of material science expertise and printing process mastery. Our commitment to quality, investment in industry-leading technology, and collaborative approach make us an ideal partner for automotive companies seeking to leverage metal AM for critical EV components like battery cooling frames.
Understanding Cost Drivers and Lead Times for 3D Printed Battery Frames
While metal AM enables significant performance gains and design possibilities for EV battery cooling frames, understanding the associated costs and production timelines is crucial for project planning and procurement. Both metal 3D printing cost analysis y lead time estimation automotive parts depend on a variety of interconnected factors.
Principales factores de coste:
- Tipo de material y consumo:
- Coste del polvo: The raw material cost varies significantly between alloys. Copper alloys like CuCrZr are substantially more expensive than aluminum alloys like AlSi10Mg.
- Volumen y peso de la pieza: Larger, denser parts naturally consume more powder, directly impacting material cost. DfAM techniques like topology optimization and lattice structures can significantly reduce material usage.
- Estructuras de apoyo: Material used for support structures adds to the overall consumption and needs to be factored in. Minimizing supports through DfAM reduces this cost.
- La hora de las máquinas:
- Tiempo de construcción: This is often the most significant cost driver. It depends on the part’s volume (specifically its height in the build chamber), the complexity, the layer thickness used, and the efficiency of the machine’s laser/electron beam scanning strategy. Taller parts or parts requiring very fine layers take longer to print.
- Machine Rate: The hourly operating cost of the industrial metal 3D printer, factoring in depreciation, energy, consumables (filters, gases), and maintenance.
- Design Complexity & Build Setup:
- Supports: Complex geometries requiring extensive support structures increase both print time (more material to deposit) and post-processing labor (support removal).
- Nesting & Build Density: How efficiently multiple parts can be nested within a single build volume affects the per-part machine time cost. Experienced providers optimize build layouts.
- Preparation Time: Time taken by engineers to prepare the build file (orientation, support generation, slicing).
- Post-procesamiento:
- Labor & Equipment: Each post-processing step (stress relief, heat treatment, support removal, machining, finishing, inspection) adds labor and equipment time costs.
- Complejidad: Intricate internal channels requiring specialized finishing (like AFM) or tight tolerances demanding extensive CNC machining will increase costs significantly.
- Quality Requirements: Higher inspection levels (e.g., extensive CMM, CT scanning) add to the cost.
- Volumen del pedido:
- Economías de escala: As with most manufacturing processes, higher volumes generally lead to lower per-part costs due to amortization of setup costs, optimized build nesting, and more efficient workflows. Volume production AM is becoming increasingly viable, though cost structures differ from traditional high-volume methods.
Factors Influencing Lead Times:
- Design Finalization & Preparation: Time required for DfAM consultation (if needed) and build file preparation.
- Print Queue: Availability of suitable machines at the service provider. High demand can lead to queues.
- Print Time: The actual time the part spends printing in the machine (can range from hours to several days depending on size and complexity).
- Post-procesamiento: The cumulative time required for all necessary steps after printing (heat treatment cycles, machining, finishing, inspection). This can often take as long or longer than the print time itself.
- Shipping & Logistics: Time required for transportation to the final destination.
Typical Timelines:
While highly project-dependent, simple prototypes might be produced in 1-2 weeks. More complex components requiring significant post-processing or parts made from challenging materials could have lead times ranging from 3 to 8 weeks or more, especially for initial production runs. Establishing a relationship with a provider like Met3dp allows for better planning and potentially expedited timelines once processes are validated. Accurate quotes for both cost and lead time require a detailed review of the final part CAD data, material specifications, and quality requirements. Effective procurement metal 3D printing involves providing clear specifications to potential suppliers.
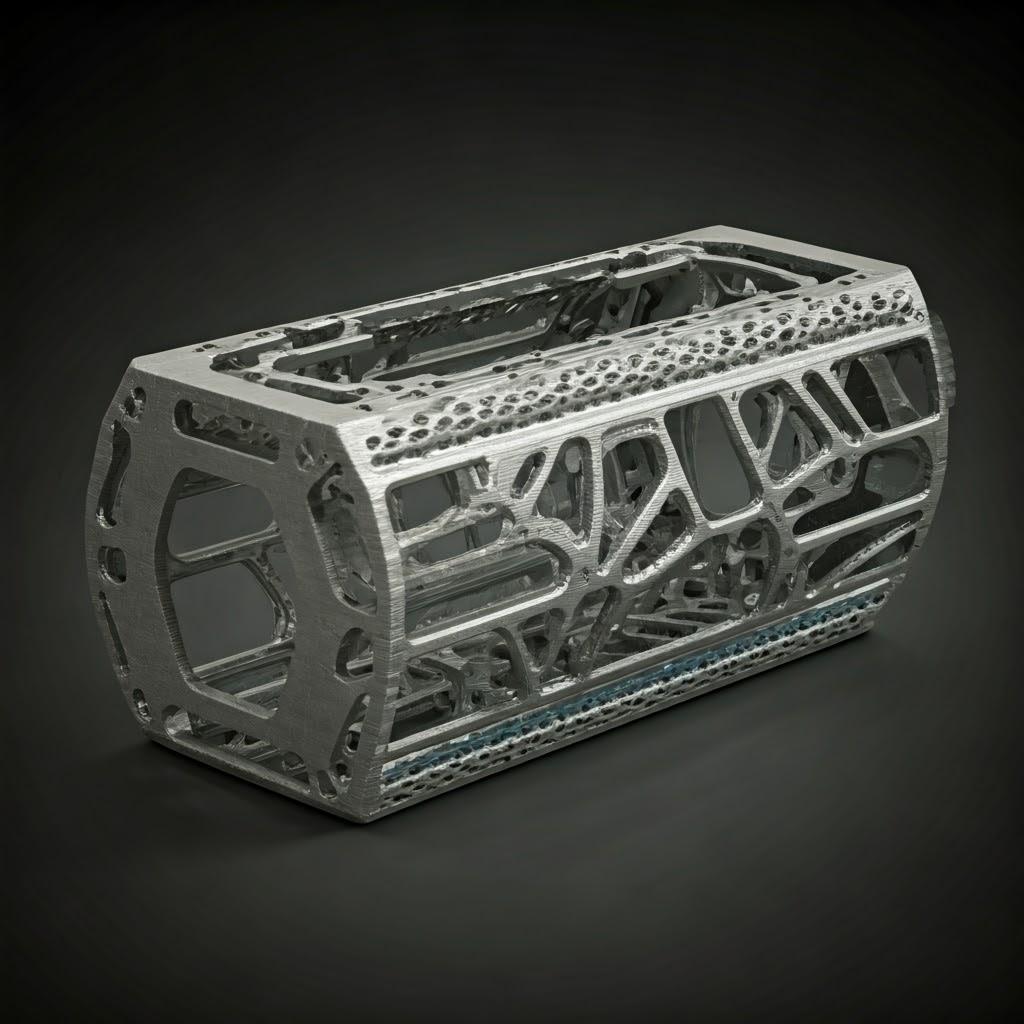
Frequently Asked Questions (FAQ) about Metal 3D Printed EV Cooling Frames
Here are answers to some common questions engineers and procurement managers have about using metal AM for EV battery cooling components:
1. What are the main advantages of using metal AM for cooling frames compared to traditional methods like casting or brazed assemblies?
Metal AM offers several key advantages:
- Geometric Complexity: Ability to create highly intricate internal cooling channels (e.g., conformal, optimized flow paths) that are impossible or impractical with casting or machining, leading to superior thermal performance.
- Aligeramiento: Enables topology optimization and lattice structures, significantly reducing component weight compared to solid cast parts, which boosts EV range.
- Consolidación de piezas: Allows integration of multiple functions (cooling, structure, mounting) into a single printed part, reducing assembly complexity, potential leak points, and often weight/cost.
- Speed for Prototypes/Low Volumes: Faster iteration during development and quicker production for low-to-mid volumes as no tooling is required.
- Opciones de material: Facilitates the use of high-performance alloys like AlSi10Mg for lightweighting or CuCrZr for maximum thermal conductivity.
2. How leak-proof are the cooling channels in 3D printed frames?
Achieving leak-proof integrity is paramount and highly achievable with proper process control. Key factors include:
- Parameter Optimization: Using validated print parameters to ensure full densification (>99.5%, often higher) and minimize porosity within the material.
- Calidad del polvo: Starting with high-quality, low-porosity metal powder is essential.
- Diseño: Avoiding design features that are prone to defects (e.g., very thin walls without proper support).
- Post-procesamiento: While HIP can close internal pores, it’s often not required if printing parameters are well-controlled.
- Rigorous Testing: Implementing mandatory leak testing (e.g., pressure decay, helium leak testing) as a standard quality control step for every cooling component produced. When manufactured correctly by an experienced provider like Met3dp, metal AM cooling frames meet stringent leak-proof requirements.
3. Can metal AM achieve the required surface finish inside the cooling channels for efficient fluid flow?
The as-printed surface finish inside AM channels is inherently rougher (typically Ra 10-20 µm or higher) than conventionally machined channels. While this might slightly increase pressure drop compared to a perfectly smooth tube, the performance gains from optimized channel geometry often outweigh the surface roughness effect. For applications demanding smoother internal surfaces:
- Diseño: Orienting channels and using specific shapes (e.g., teardrop) can improve the finish of certain internal surfaces.
- Post-procesamiento: Techniques like Abrasive Flow Machining (AFM) or chemical polishing can be employed to significantly improve the internal surface finish, albeit at an additional cost. The required internal finish should be specified and discussed with the AM provider.
4. What information does Met3dp typically need to provide a quote for a 3D printed battery cooling frame?
To provide an accurate quote, we typically require:
- Modelo CAD en 3D: STEP or STL file of the final part design.
- Material Specification: Desired alloy (e.g., AlSi10Mg, CuCrZr) and any specific material property requirements.
- Dibujo técnico: Indicating critical dimensions, tolerances, required surface finishes (especially on sealing/mating surfaces), and any specific features to be machined.
- Cantidad: Number of parts required (for prototype, low-volume, or series production).
- Requisitos de postprocesamiento: Details on heat treatment, specific surface finishes, testing needs (e.g., leak test parameters).
- Delivery Timeline: Required delivery date.
5. Is metal AM suitable for high-volume automotive production of these frames?
Metal AM is rapidly evolving, and while it excels in prototyping, customization, and low-to-mid volume production, its suitability for traditional high-volume automotive scales (hundreds of thousands or millions per year) is still developing compared to casting or stamping for simple designs. However, for complex, high-performance cooling frames where AM provides significant performance or consolidation benefits unattainable otherwise, it is becoming a viable option even for series production in the thousands or tens of thousands. The cost-effectiveness depends heavily on the design complexity and the value derived from AM’s unique capabilities. Met3dp works with clients to evaluate the business case for volume production using AM.
Conclusion: Driving the Future of EV Performance with Met3dp’s Additive Manufacturing Solutions
The relentless pursuit of higher performance, longer range, and faster charging in the electric vehicle market places immense pressure on battery thermal management systems. Metal additive manufacturing has unequivocally emerged as a key enabling technology, offering unprecedented capabilities to design and produce EV battery cooling frames that are lighter, more complex, and thermally superior to those made by conventional methods. By leveraging the design freedom of AM with advanced materials like lightweight AlSi10Mg or highly conductive CuCrZr, automotive manufacturers can achieve significant improvements in battery pack efficiency, longevity, and safety – critical factors for success in the competitive EV landscape.
From optimizing intricate internal cooling channels via DfAM to ensuring precision through meticulous process control and post-processing, metal AM provides a powerful toolkit for advanced manufacturing automotive applications. However, navigating the complexities of material selection, design optimization, process parameters, and quality assurance requires deep expertise.
Choosing the right partner is paramount. Met3dp stands at the forefront of this technological wave, combining industry-leading SEBM/LPBF printing technology with unparalleled expertise in high-performance metal powder production. Our integrated approach, from atomized powder to finished and tested component, ensures the quality, reliability, and performance demanded by the automotive industry. We are more than just a service provider; we are a collaborative partner dedicated to helping you unlock the full potential of additive manufacturing for your most critical EV components.
Ready to revolutionize your EV thermal management? Póngase en contacto con Met3dp hoy mismo to discuss your battery cooling frame project and explore how our cutting-edge systems, advanced materials, and application development services can accelerate your journey towards next-generation electric vehicles. Let’s drive the future EV technology together.
Compartir
MET3DP Technology Co., LTD es un proveedor líder de soluciones de fabricación aditiva con sede en Qingdao, China. Nuestra empresa está especializada en equipos de impresión 3D y polvos metálicos de alto rendimiento para aplicaciones industriales.
Solicite información para obtener el mejor precio y una solución personalizada para su empresa.
Artículos relacionados
Acerca de Met3DP
Actualización reciente
Nuestro producto
CONTACTO
¿Tiene alguna pregunta? ¡Envíenos un mensaje ahora! Atenderemos su solicitud con todo un equipo tras recibir su mensaje.
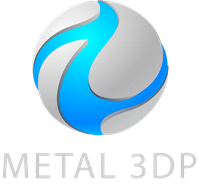
Polvos metálicos para impresión 3D y fabricación aditiva