impresión 3D de disipadores de calor personalizados para electrónica
Índice
Introducción: Revolucionando la gestión térmica con disipadores personalizados impresos en 3D
En la búsqueda incesante de dispositivos electrónicos más pequeños, más rápidos y más potentes, la gestión del calor generado se ha convertido en un reto de ingeniería crítico en innumerables sectores. Desde bastidores de servidores densamente empaquetados y clústeres informáticos de alto rendimiento hasta sistemas avanzados de asistencia al conductor (ADAS) en vehículos, sofisticados equipos médicos de diagnóstico por imagen y potentes conjuntos de iluminación LED, la gestión térmica eficaz ya no es sólo una característica deseable, sino una necesidad absoluta para garantizar el rendimiento, la fiabilidad y la longevidad. Las soluciones de refrigeración tradicionales, a menudo basadas en disipadores de calor de aluminio extruido o mecanizado, han dado buenos resultados durante décadas. Sin embargo, a medida que se disparan las densidades de potencia y las geometrías de los componentes se hacen cada vez más complejas y limitadas en espacio, estos métodos convencionales alcanzan a menudo sus límites en cuanto a flexibilidad de diseño, optimización del rendimiento y posibilidades de integración. Los ingenieros y especialistas en adquisiciones buscan constantemente soluciones de gestión térmica que pueden superar estas limitaciones, ampliando los límites de lo que es posible en el diseño electrónico.
Entre en el transformador mundo de la fabricación aditiva (AM) de metales, comúnmente conocida como Impresión 3D. Esta tecnología está pasando rápidamente de la creación de prototipos a la producción de piezas funcionales, ofreciendo capacidades sin precedentes para crear componentes de gran complejidad y rendimiento optimizado. Una de las aplicaciones más prometedoras reside en la producción de disipadores de calor personalizados. A diferencia de los métodos tradicionales de fabricación sustractiva, que tallan el material a partir de un bloque sólido, la AM metálica construye piezas capa a capa directamente a partir de polvo metálico, guiada por un archivo de diseño digital. Esta diferencia fundamental abre un nuevo paradigma en el diseño de componentes térmicos, ya que permite crear geometrías cuya fabricación era antes imposible o prohibitivamente cara. Imagine disipadores de calor con intrincados canales internos que imitan estructuras vasculares orgánicas para mejorar el flujo de fluidos, complejas estructuras reticulares que maximizan la superficie al tiempo que minimizan el peso, o componentes perfectamente conformados a la forma única del dispositivo electrónico que deben refrigerar. No se trata de conceptos futuristas, sino tangibles ventajas de la impresión metálica en 3D hoy en día.
La capacidad de adaptar los diseños de los disipadores de calor a la carga térmica, las condiciones de flujo de aire y las limitaciones espaciales específicas de una aplicación cambia las reglas del juego. Tecnología de refrigeración avanzada gracias a la AM metálica, los ingenieros pueden ir más allá de las soluciones estándar y desarrollar componentes térmicos realmente optimizados. Esto se traduce directamente en ventajas B2B tangibles: mejora del rendimiento de los productos, mayor eficiencia energética, reducción del tamaño y el peso de los componentes (fundamental en los sectores aeroespacial y automovilístico), mayor libertad de diseño que da lugar a sistemas más integrados y un plazo de comercialización potencialmente más rápido para productos electrónicos innovadores. Empresas especializadas en fabricación aditiva electrónica están proporcionando a los ingenieros las herramientas y los materiales necesarios para afrontar los retos térmicos más exigentes.
Met3dp está a la vanguardia de este cambio tecnológico. Como proveedor líder de fabricación aditiva de metales met3dp, con sede en Qingdao (China), no sólo ofrece equipos de impresión de última generación para la fusión selectiva por haz de electrones (SEBM) y la fusión de lecho de polvo por láser (LPBF), reconocidos por su volumen de impresión, precisión y fiabilidad líderes en el sector, sino también una cartera de polvos metálicos de alto rendimiento optimizados específicamente para los procesos de AM. Nuestros conocimientos, basados en décadas de experiencia colectiva, abarcan todo el ecosistema de la AM, desde la producción avanzada de polvos mediante tecnologías propias de atomización con gas y proceso de electrodo giratorio de plasma (PREP) hasta el apoyo al desarrollo de aplicaciones y la producción de piezas finales. Colaboramos con empresas de los sectores aeroespacial, médico, automovilístico y de fabricación industrial para aprovechar el poder de la AM de metales, lo que permite la creación de piezas de misión crítica como los disipadores de calor personalizados de nueva generación. Esta entrada de blog profundizará en el mundo de los disipadores de calor personalizados impresos en 3D, explorando sus aplicaciones, las ventajas que ofrece la AM, materiales adecuados como AlSi10Mg y CuCrZr, consideraciones cruciales de diseño y cómo asociarse con el proveedor de servicios adecuado, como Met3dp, para dar vida a sus proyectos de gestión térmica avanzada. Para los responsables de compras y los compradores al por mayor, comprender las capacidades y el potencial de los disipadores de calor producidos por AM es crucial para abastecerse de componentes que ofrezcan una ventaja competitiva en rendimiento y diseño.
Aplicaciones: ¿Dónde tienen impacto los disipadores de calor personalizados impresos en 3D?
La versatilidad y libertad de diseño que ofrece la fabricación aditiva de metales permite crear disipadores de calor a medida para una amplia gama de aplicaciones exigentes en las que las soluciones convencionales se quedan cortas. La capacidad de optimización para cargas térmicas, trayectorias de flujo y restricciones geométricas específicas hace que los disipadores de calor impresos en 3D resulten especialmente valiosos en sectores que amplían los límites del rendimiento y la miniaturización. Los responsables de compras que buscan mayoristas de disipadores de calor capaces de ofrecer soluciones personalizadas de alto rendimiento deberían prestar mucha atención a la creciente adopción de la AM en estos sectores críticos.
He aquí un desglose de las principales áreas de aplicación:
1. Refrigeración de electrónica de alta potencia:
- Aplicaciones: Convertidores de potencia, inversores (por ejemplo, para energía solar o eólica, vehículos eléctricos), amplificadores de alta frecuencia, componentes de RF, fuentes de alimentación para centros de datos y automatización industrial.
- Desafíos: Estos componentes generan mucho calor en zonas concentradas. Los disipadores térmicos tradicionales pueden tener problemas con el elevado flujo de calor y la refrigeración uniforme, lo que provoca estrangulamiento térmico o fallos en los componentes. Las limitaciones de espacio suelen ser graves.
- Ventaja AM: La impresión metálica en 3D permite crear disipadores de calor con geometrías de aletas optimizadas (por ejemplo, aletas en espiga, celosías complejas), microcanales integrados para refrigeración líquida o tubos de calor incrustados directamente en la estructura. La optimización de la topología puede colocar el material exactamente donde se necesita para conseguir la máxima disipación del calor y minimizar el peso y el volumen. Para los proveedores B2B, ofrecer soluciones de AM supone una clara ventaja de rendimiento para los clientes que desarrollan sistemas de alimentación de nueva generación.
2. Gestión térmica avanzada de LED:
- Aplicaciones: Módulos LED de alto brillo para faros de automóviles, iluminación arquitectónica, luces de cultivo hortícola, iluminación industrial e iluminación escénica.
- Desafíos: La eficacia y la vida útil de los LED dependen en gran medida de la temperatura de unión. El sobrecalentamiento reduce la potencia luminosa, cambia el color y provoca fallos prematuros. Los diseños compactos suelen limitar el flujo de aire y el tamaño del disipador de calor.
- Ventaja AM: La AM permite crear disipadores de calor altamente conformados que se integran a la perfección con los módulos LED y las carcasas de las luminarias. Las complejas estructuras de aletas pueden maximizar la refrigeración convectiva incluso en espacios reducidos. Los diseños ligeros, especialmente con materiales como AlSi10Mg, son beneficiosos para grandes conjuntos o aplicaciones sensibles al peso. Gestión térmica de los LED producidas mediante AM pueden mejorar significativamente la fiabilidad del producto y las métricas de rendimiento, un argumento de venta clave para fabricantes y distribuidores de iluminación.
3. Refrigeración de la electrónica del automóvil:
- Aplicaciones: Unidades de control del motor (ECU), controladores de transmisión, procesadores ADAS, sistemas de infoentretenimiento, sistemas de gestión de baterías (BMS) en vehículos eléctricos (EV), electrónica de potencia para transmisiones de EV.
- Desafíos: Los entornos de funcionamiento difíciles (vibraciones, temperaturas extremas), las estrictas limitaciones de espacio y peso y la necesidad de una alta fiabilidad son primordiales. Los procesadores y componentes de potencia, cada vez más potentes, generan un calor considerable.
- Ventaja AM: Refrigeración de la electrónica del automóvil se beneficia enormemente de la capacidad de la AM para producir disipadores de calor ligeros, complejos y robustos. La optimización de la topología es clave para reducir el peso del vehículo, mejorar la eficiencia del combustible o la autonomía de los vehículos eléctricos. Los canales de refrigeración conformados o las placas de refrigeración líquida integradas pueden diseñarse para lograr la máxima eficacia en los espacios reducidos del chasis o el vano motor de un vehículo. La fiabilidad se mejora mediante un diseño térmico optimizado y materiales robustos como AlSi10Mg o incluso aleaciones de cobre para aplicaciones de potencia exigentes. Los proveedores de automoción que aprovechan la AM pueden ofrecer soluciones térmicas superiores para clientes Tier 1 y OEM.
4. Componentes aeroespaciales y de defensa:
- Aplicaciones: Refrigeración de aviónica, sistemas de radar, sistemas de guerra electrónica (EW), fuentes de alimentación para satélites y aeronaves, refrigeración para sistemas de energía dirigida.
- Desafíos: Las condiciones de funcionamiento extremas (oscilaciones de temperatura, cambios de presión, fuerzas G elevadas, vibraciones), los estrictos requisitos de reducción de peso (relación entre compra y vuelo) y la necesidad de una fiabilidad excepcionalmente alta definen este sector. La integración de sistemas complejos requiere a menudo formas de componentes muy personalizadas.
- Ventaja AM: La AM metálica encaja a la perfección en componentes aeroespaciales. Permite crear disipadores de calor de gran complejidad y forma orgánica que integran múltiples funciones, maximizan la relación superficie-volumen y reducen drásticamente el peso mediante estructuras reticulares y la optimización de la topología. La capacidad de imprimir aleaciones de alto rendimiento garantiza la durabilidad y fiabilidad en entornos exigentes. Empresas como Met3dp, con experiencia en materiales y procesos de grado aeroespacial, son socios cruciales para los contratistas de defensa y los fabricantes aeroespaciales que buscan soluciones térmicas de vanguardia.
5. Informática industrial y de alto rendimiento (HPC):
- Aplicaciones: Refrigeración de blades de servidores de alta densidad, CPU y GPU en centros de datos, procesadores en sistemas de control industrial, ordenadores robustos para uso en campo, instrumentación científica.
- Desafíos: Enormes cargas térmicas generadas por los procesadores modernos, densidad extrema de los envases que limita el flujo de aire, necesidad de eficiencia energética (reducción de los costes de refrigeración) y alta fiabilidad para un funcionamiento continuo.
- Ventaja AM: La AM permite soluciones de refrigeración avanzadas, como colectores de refrigeración por inmersión de dos fases, complejos disipadores de calor refrigerados por aire y optimizados para patrones de flujo de aire específicos dentro de bastidores de servidores, o placas frías líquidas muy compactas con intrincadas redes de canales internos. Para informática industrial y centros de datos, incluso mejoras marginales en la eficiencia de la refrigeración, posibilitadas por disipadores de calor AM optimizados, pueden traducirse en importantes ahorros de costes operativos y un mayor rendimiento del procesamiento. Los proveedores que ofrecen estas soluciones térmicas avanzadas proporcionan una ventaja competitiva en el mercado de HPC.
6. Productos sanitarios:
- Aplicaciones: Refrigeración para sistemas de imagen médica (resonancia magnética, tomografía computarizada), sistemas láser para cirugía o diagnóstico, dispositivos médicos portátiles, unidades de procesamiento para equipos de diagnóstico complejos.
- Desafíos: Requisitos estrictos de biocompatibilidad (a veces), necesidad de un funcionamiento silencioso, alta fiabilidad, huellas de dispositivo a menudo compactas y necesidades específicas de control térmico para componentes electrónicos o detectores sensibles.
- Ventaja AM: La AM permite crear disipadores de calor miniaturizados y muy eficientes adaptados a las formas únicas de los dispositivos médicos. Pueden utilizarse materiales como aleaciones de aluminio o incluso titanio (si se requiere biocompatibilidad o una resistencia específica). Las complejas estructuras internas pueden facilitar una refrigeración pasiva y silenciosa o una refrigeración líquida muy eficaz cuando sea necesario.
En todos estos sectores, el denominador común es la necesidad de soluciones de gestión térmica que superen las limitaciones de la fabricación tradicional. La impresión metálica en 3D ofrece la libertad de diseño y las capacidades materiales necesarias para crear.. soluciones térmicas personalizadas B2B que los compradores necesitan para sus aplicaciones más exigentes. Asociarse con un proveedor de AM experimentado como Met3dp garantiza el acceso a la tecnología, los materiales y la experiencia necesarios para aprovechar estas ventajas de forma eficaz.
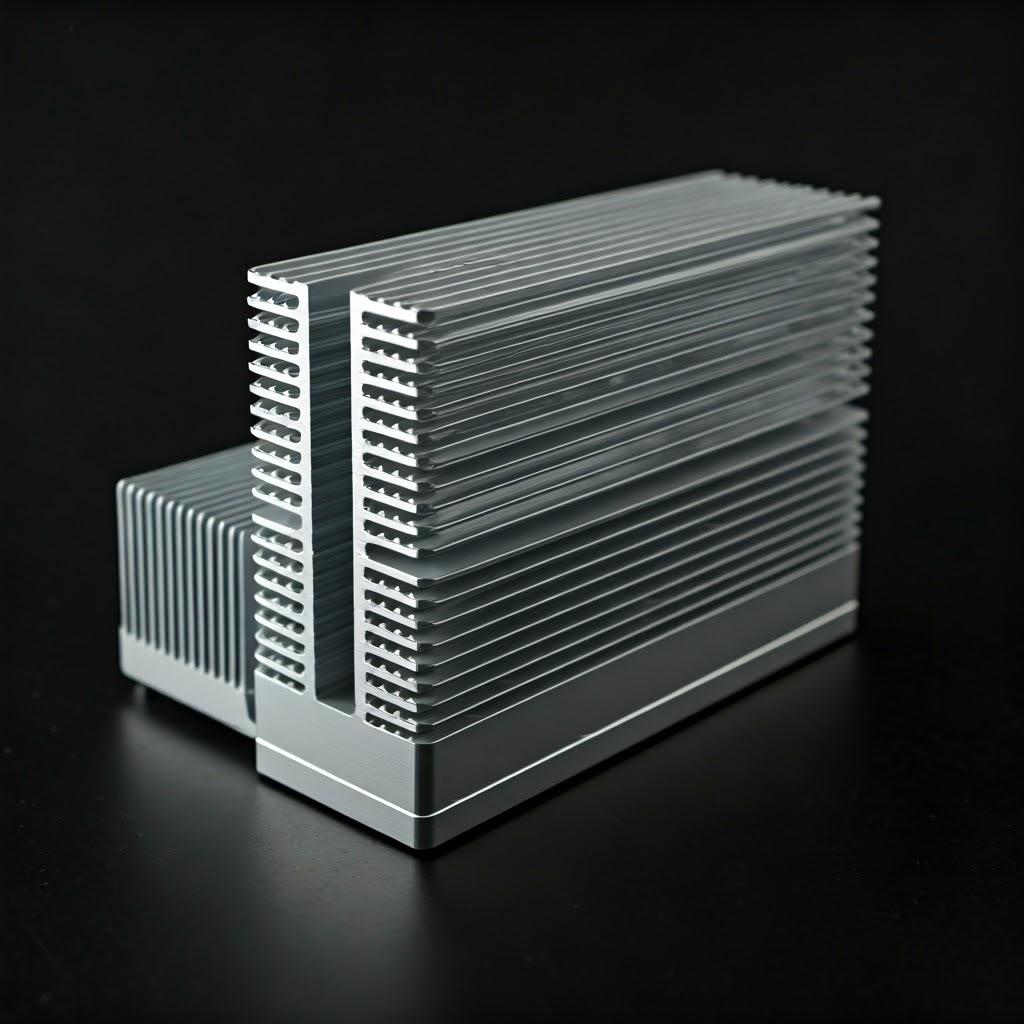
¿Por qué la impresión 3D en metal para disipadores de calor personalizados? Libertad de diseño y rendimiento
Aunque los métodos de fabricación tradicionales, como el mecanizado CNC, la extrusión o la fundición, han sido durante mucho tiempo la norma para producir disipadores de calor, conllevan intrínsecamente restricciones de diseño que pueden limitar el rendimiento térmico, las posibilidades de integración y la eficiencia general, especialmente cuando se trata de requisitos complejos. La fabricación aditiva de metales cambia radicalmente la ecuación y ofrece ventajas convincentes que la convierten en una opción cada vez más atractiva para los ingenieros y responsables de compras que buscan productos de vanguardia soluciones térmicas personalizadas B2B. En fabricación aditiva frente a mecanizado el debate sobre los disipadores térmicos suele girar en torno a los requisitos de complejidad, volumen y rendimiento.
A continuación se explica con detalle por qué la AM metálica es una opción superior para muchas aplicaciones de disipadores de calor personalizados:
1. Libertad de diseño y complejidad geométrica sin precedentes:
- Limitaciones tradicionales: La extrusión limita los diseños a formas 2,5D con secciones transversales uniformes. El mecanizado, aunque versátil, resulta exponencialmente más caro y lento a medida que aumenta la complejidad (por ejemplo, socavados, canales profundos, características finas). Las estructuras internas complejas suelen ser imposibles.
- Ventaja AM: La AM metálica construye piezas capa a capa, liberando a los diseñadores de muchas limitaciones tradicionales. Esto permite:
- Geometrías complejas de aletas: Creación de formas de aletas muy optimizadas, como aletas en espiga, aletas onduladas o estructuras de celosía complejas (por ejemplo, giroscópicas, octeto-cerchas) que maximizan la superficie de convección en un volumen determinado, lo que aumenta considerablemente el rendimiento térmico.
- Canales de refrigeración internos: Integración de intrincados canales de refrigeración conformados directamente en el cuerpo del disipador de calor para una refrigeración líquida de alta eficiencia, eliminando la necesidad de ensamblaje y los posibles puntos de fuga. Estos canales pueden seguir trayectorias curvas y adaptarse a la disposición de los componentes.
- Diseños conformes: Los disipadores pueden diseñarse para adaptarse perfectamente a las superficies curvas o irregulares de los componentes que deben refrigerar, lo que mejora el contacto térmico y la integración general del sistema.
- Consolidación de piezas: Varios componentes (por ejemplo, disipador de calor, colector de flujo, soportes de montaje) pueden consolidarse en una única pieza compleja impresa en 3D, lo que reduce el tiempo de montaje, el peso y los posibles puntos de fallo.
- Beneficio: Este geometría compleja del disipador de calor permite a los ingenieros diseñar para obtener un rendimiento térmico óptimo en lugar de estar limitados por restricciones de fabricación.
2. Optimización de la topología para mejorar el rendimiento y reducir el peso:
- Concepto: El software de optimización topológica utiliza algoritmos (a menudo, análisis de elementos finitos) para determinar la distribución de material más eficaz dentro de un espacio de diseño definido, sujeto a cargas (térmicas o mecánicas) y restricciones específicas. Básicamente, elimina el material innecesario y deja únicamente las estructuras portantes o térmicamente críticas.
- Ventaja AM: La AM es la única capaz de producir las formas orgánicas, a menudo complejas, resultantes de optimización topológica térmica análisis. Esto permite:
- Máximo rendimiento: Colocación de material conductor térmico precisamente allí donde el calor debe transferirse y disiparse con mayor eficacia.
- Aligeramiento significativo: La eliminación de material no esencial reduce drásticamente el peso de los componentes, un factor crítico en aplicaciones aeroespaciales, de automoción y de electrónica portátil. Disipador de calor ligero es uno de los principales motores de la adopción de la AM.
- Beneficio: Conseguir un rendimiento térmico óptimo con la mínima masa posible, lo que a menudo es inalcanzable con los métodos tradicionales debido a las limitaciones de fabricación o al coste.
3. Creación rápida de prototipos e iteración:
- Limitaciones tradicionales: Crear herramientas personalizadas (por ejemplo, matrices de extrusión) o complejas configuraciones de mecanizado para prototipos puede llevar mucho tiempo y resultar caro, lo que ralentiza el ciclo de iteración del diseño.
- Ventaja AM: La AM metálica no requiere herramientas específicas para cada pieza. Los diseños pueden pasar directamente de un archivo CAD a una pieza física con relativa rapidez. Esto facilita:
- Ciclos de diseño más rápidos: Los ingenieros pueden producir y probar rápidamente múltiples variaciones de diseño (por ejemplo, diferentes estructuras de aletas, disposiciones de canales) para determinar empíricamente la solución de mejor rendimiento.
- Reducción de los costes de desarrollo: Evitar costes de utillaje para prototipos hace más factible explorar diseños innovadores.
- Beneficio: Acelera el desarrollo de productos y permite una validación más exhaustiva del diseño, lo que se traduce en mejores productos finales. Este electrónica de prototipado rápido es inestimable en los mercados en rápida evolución.
4. Personalización y producción a la carta:
- Limitaciones tradicionales: Producir pequeños lotes o disipadores de calor altamente personalizados mediante métodos tradicionales puede resultar económicamente complicado debido a los costes de preparación y los requisitos de utillaje.
- Ventaja AM: La naturaleza digital de la AM la hace muy adecuada para:
- Producción de volumen bajo a medio: Fabricación rentable de lotes que van desde prototipos únicos hasta cientos o miles de piezas sin inversión en utillaje.
- La personalización en masa: Adaptar fácilmente los diseños de los disipadores de calor a los requisitos específicos del cliente o a las variaciones de la aplicación sin cambios significativos en el proceso.
- Fabricación a la carta: Producir piezas según las necesidades, reduciendo los requisitos de inventario y permitiendo una respuesta más rápida a la fluctuación de la demanda.
- Beneficio: Proporciona flexibilidad para aplicaciones especializadas, equipos personalizados y gestión de las incertidumbres de la cadena de suministro, ofreciendo un valor significativo para la contratación B2B.
5. Potencial de mejora del rendimiento térmico:
- Más allá de la geometría: Aunque las geometrías complejas son el motor principal, a veces puede manipularse el propio proceso capa por capa (aunque es necesario un control cuidadoso) para influir en la microestructura, lo que puede repercutir en las propiedades térmicas. Y lo que es más importante, la AM permite utilizar materiales y geometrías que maximizan los mecanismos de transferencia de calor (conducción, convección, radiación) de formas que los métodos tradicionales no pueden reproducir eficazmente. La capacidad de crear microcaracterísticas o texturas superficiales específicas puede potenciar la transferencia de calor por convección o mejorar el contacto del material con la interfaz térmica (TIM).
- Beneficio: Superar los límites absolutos del rendimiento térmico combinando las propiedades de los materiales con una libertad geométrica sin precedentes.
Met3dp aprovecha sus avanzadas tecnologías de impresión SEBM y LPBF y sus polvos metálicos de alta calidad para ofrecer todas estas ventajas a sus clientes. Nuestro equipo de ingeniería puede ayudar a optimizar los diseños para la fabricación aditiva (DfAM), garantizando que la transición del concepto al disipador de calor personalizado funcional y de alto rendimiento sea fluida y eficiente. Al adoptar la AM metálica, las empresas pueden obtener soluciones de gestión térmica superiores que impulsen la innovación en sus respectivos sectores.
Profundización en materiales: AlSi10Mg y CuCrZr para un rendimiento óptimo del disipador de calor
Seleccionar el material adecuado es primordial para diseñar un disipador de calor eficaz, independientemente del método de fabricación. Sin embargo, la fabricación aditiva de metales abre la puerta al uso de aleaciones específicas que ofrecen un excelente equilibrio entre conductividad térmica, propiedades mecánicas, peso y procesabilidad mediante la fusión capa a capa. Para los disipadores de calor personalizados impresos en 3D, hay dos materiales que destacan como principales opciones ofrecidas por los principales polvo metálico para impresión 3D proveedores como Met3dp: AlSi10Mg (una aleación de aluminio) y CuCrZr (una aleación de cobre). Conocer sus propiedades es crucial para los ingenieros que diseñan soluciones térmicas y para los responsables de compras que se abastecen de estos componentes avanzados.
Met3dp se toma muy en serio la calidad de los materiales y emplea técnicas de fabricación de polvo líderes en el sector, como la atomización de gas por fusión por inducción en vacío (VIGA) y el proceso PREP (Plasma Rotating Electrode Process). Nuestros avanzados sistemas de fabricación de polvo utilizan diseños exclusivos de boquillas y flujo de gas en la atomización con gas para producir polvos metálicos altamente esféricos con una excelente fluidez y mínimas partículas satélite. La tecnología PREP produce polvos con una pureza y esfericidad aún mayores, ideales para las aplicaciones más exigentes. Este compromiso garantiza polvos Met3dp utilizadas en nuestras impresoras proporcionan la base para piezas metálicas densas y de alta calidad con propiedades mecánicas y térmicas superiores y constantes, fundamentales para un rendimiento fiable del disipador térmico.
Examinemos los polvos recomendados:
1. Aleación de aluminio-silicio-magnesio (AlSi10Mg): El caballo de batalla ligero
- Composición: Principalmente aluminio, con adiciones significativas de silicio (alrededor del 10%) y magnesio (alrededor del 0,3-0,5%).
- Propiedades clave:
- Conductividad térmica: Buena, normalmente en el rango de 120-180 W/(m-K) tras un tratamiento térmico adecuado. Aunque es inferior a la del aluminio puro o el cobre, es significativamente mejor que la de los aceros o las aleaciones de titanio.
- Densidad: Baja densidad (aprox. 2,67 g/cm³), lo que la hace ideal para aplicaciones en las que el ahorro de peso es fundamental (aeroespacial, automoción, dispositivos portátiles).
- Resistencia mecánica: Ofrece buena resistencia y dureza, especialmente tras el tratamiento térmico (condición T6), lo que hace que los disipadores térmicos resultantes sean robustos.
- Procesabilidad: Una de las aleaciones más maduras y mejor comprendidas para la fusión por lecho de polvo láser (LPBF/SLM), que permite obtener características finas y un buen acabado superficial.
- Resistencia a la corrosión: Buena resistencia general a la corrosión atmosférica, que puede mejorarse mediante anodizado.
- Costo: Relativamente rentable en comparación con las aleaciones de cobre u otros materiales exóticos.
- Por qué es importante para los disipadores de calor: El AlSi10Mg ofrece un excelente equilibrio entre buena conductividad térmica, bajo peso, buena resistencia mecánica y procesabilidad. Suele ser la elección por defecto cuando la conductividad térmica extrema no es el factor principal, pero se requiere una combinación de rendimiento, peso y facilidad de fabricación. Su uso generalizado significa que los parámetros de procesamiento están bien establecidos, lo que permite obtener resultados fiables y repetibles. La capacidad de conseguir diseño ligero del disipador de calor lo hace muy valioso.
- Ventaja de Met3dp: Met3dp produce polvo de AlSi10Mg de alta calidad optimizado para los procesos LPBF, garantizando un comportamiento uniforme del baño de fusión, una alta densidad de las piezas (>99,8%) y unas propiedades finales predecibles tras el postprocesado adecuado, incluido el tratamiento térmico T6 para mejorar la resistencia y el rendimiento térmico.
Tabla: Propiedades de AlSi10Mg (valores típicos para piezas AM)
Propiedad | Valor típico (tras tratamiento térmico, por ejemplo, T6) | Unidad | Importancia de los disipadores de calor |
---|---|---|---|
Conductividad térmica | 120 – 180 | W/(m-K) | Buena capacidad de transferencia de calor |
Densidad | ~2.67 | g/cm³ | Excelente para diseños ligeros |
Límite elástico | 230 – 300 | MPa | Proporciona integridad estructural y robustez |
Resistencia a la tracción | 350 – 450 | MPa | Indica la fuerza global |
Alargamiento a la rotura | 3 – 10 | % | Indica la ductilidad (resistencia a la fractura frágil) |
Procesabilidad (LPBF) | Excelente | – | Permite geometrías complejas, características finas, buen acabado superficial |
Coste relativo | Moderado | – | Equilibrio rentable de las propiedades |
Exportar a hojas
2. Aleación de cobre-cromo-circonio (CuCrZr): La campeona de la alta conductividad
- Composición: Principalmente cobre, con pequeñas adiciones de cromo (Cr) y circonio (Zr).
- Propiedades clave:
- Conductividad térmica: Excelente, aproximándose a la del cobre puro (típicamente >300 W/(m-K) después del tratamiento térmico). Este valor es significativamente superior al de las aleaciones de aluminio.
- Conductividad eléctrica: También es muy alto, lo que puede ser relevante si el disipador de calor también cumple una función eléctrica.
- Densidad: Alta densidad (aprox. 8,9 g/cm³), similar a la del cobre puro. Esta es una consideración clave cuando el peso es una limitación importante.
- Resistencia mecánica: Buena resistencia y dureza, especialmente tras tratamientos térmicos de endurecimiento por precipitación (envejecimiento), significativamente mejor que el cobre puro. Conserva bien la resistencia a temperaturas moderadamente elevadas.
- Procesabilidad: Más difícil de procesar mediante LPBF que AlSi10Mg debido a la alta reflectividad y conductividad térmica del cobre, lo que requiere una mayor potencia láser y un cuidadoso control de los parámetros. Susceptible a la oxidación. A menudo se procesa en condiciones atmosféricas específicas.
- Resistencia a la corrosión: Buena, pero puede deslustrarse u oxidarse en determinados entornos.
- Costo: Significativamente más caro que el AlSi10Mg, tanto por el coste del polvo bruto como por la dificultad de procesamiento.
- Por qué es importante para los disipadores de calor: El CuCrZr es el material elegido cuando la prioridad absoluta es maximizar el rendimiento térmico y el peso es una preocupación secundaria. Su elevada conductividad térmica permite una rápida propagación y disipación del calor, por lo que es ideal para aplicaciones con un flujo de calor muy elevado o en las que se requieren las temperaturas más bajas posibles de los componentes (por ejemplo, electrónica de alta potencia, componentes de RF exigentes, diodos láser). El Propiedades del CuCrZrespecíficamente su conductividad térmica, permiten niveles de rendimiento inalcanzables con el aluminio.
- Ventaja de Met3dp: El procesamiento de aleaciones de cobre requiere conocimientos y equipos especializados. La experiencia y los avanzados sistemas de impresión de Met3dp’ son capaces de tratar materiales difíciles como el CuCrZr. Proporcionamos polvo de CuCrZr de gran pureza y utilizamos parámetros de proceso optimizados desarrollados mediante un riguroso proceso de I+D para lograr una alta densidad y unas propiedades óptimas tras el tratamiento térmico, lo que garantiza que nuestros clientes puedan aprovechar el rendimiento térmico superior de esta aleación para sus aplicaciones más exigentes.
Tabla: Propiedades del CuCrZr (Valores típicos para piezas AM)
Propiedad | Valor típico (después del tratamiento térmico) | Unidad | Importancia de los disipadores de calor |
---|---|---|---|
Conductividad térmica | 300 | W/(m-K) | Excelente transferencia de calor, ideal para flujos térmicos elevados |
Densidad | ~8.9 | g/cm³ | Pesado, posible inconveniente para aplicaciones sensibles al peso |
Límite elástico | 350 – 500 | MPa | Buena resistencia, conserva sus propiedades a temperaturas moderadas |
Resistencia a la tracción | 450 – 550 | MPa | Alta resistencia global para una aleación de cobre |
Alargamiento a la rotura | 10 – 20 | % | Buena ductilidad |
Procesabilidad (LPBF) | Desafío | – | Requiere alta potencia, optimización de parámetros, control de la atmósfera |
Coste relativo | Alta | – | Mayores costes de material y transformación |
Exportar a hojas
Consideraciones sobre la selección de materiales:
La elección entre AlSi10Mg y CuCrZr depende en gran medida de los requisitos específicos de la aplicación:
- Elija AlSi10Mg cuando:
- La reducción de peso es un objetivo primordial.
- Un rendimiento térmico bueno (pero no extremo) es suficiente.
- El coste es un factor importante.
- Se necesitan geometrías complejas con características finas, aprovechando su excelente procesabilidad.
- Elija CuCrZr cuando:
- La máxima conductividad térmica y disipación del calor son primordiales.
- Es necesario gestionar eficazmente el elevado flujo de calor.
- El peso no es la principal limitación (o el aumento de prestaciones justifica el peso).
- Un coste más elevado es aceptable para lograr un rendimiento térmico de primer nivel.
Al ofrecer aleaciones de alto rendimiento como el AlSi10Mg y el CuCrZr, fabricados utilizando calidad de atomización del gas met3dp ofrece a los ingenieros y responsables de compras las opciones de materiales necesarias para crear disipadores de calor personalizados de alto rendimiento realmente optimizados gracias al poder de la fabricación aditiva metálica. Nuestro equipo puede ayudarle a seleccionar el material ideal en función de sus requisitos térmicos, mecánicos y económicos específicos.
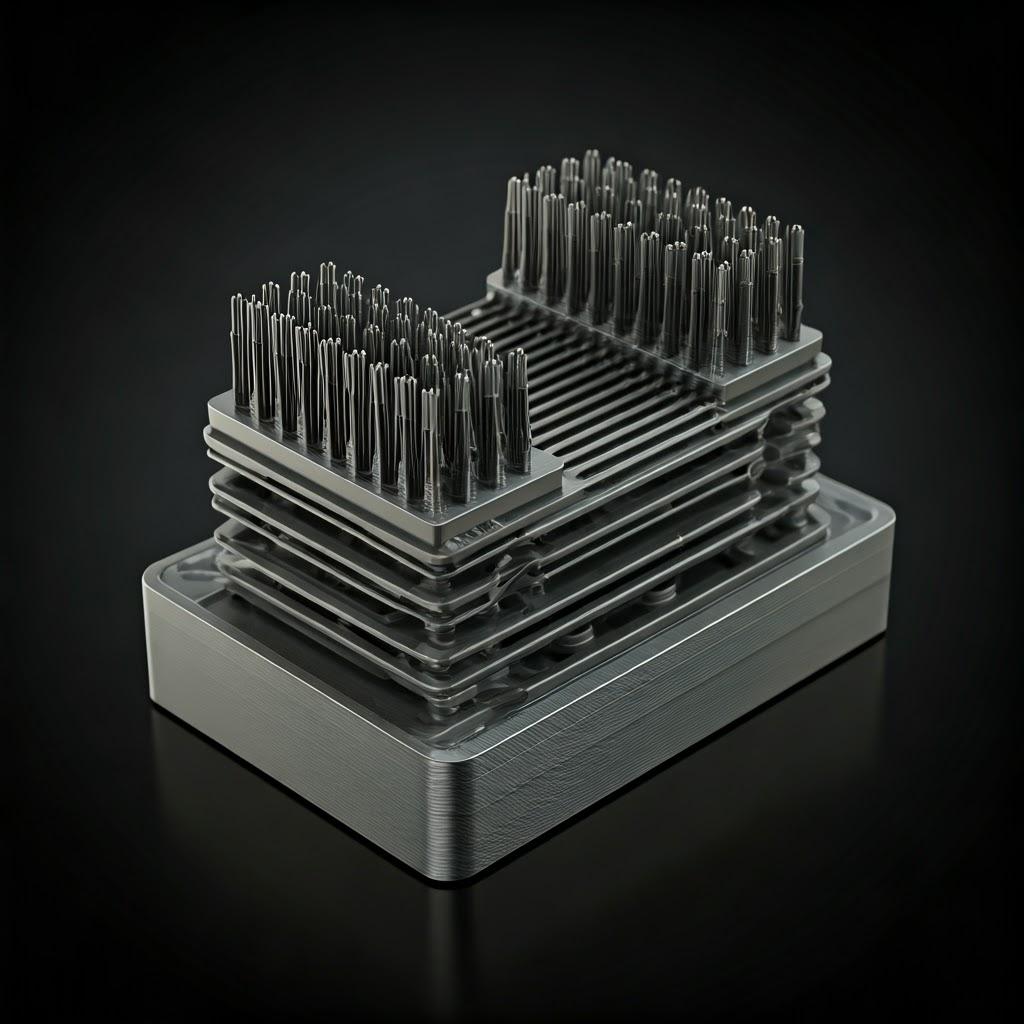
Diseño para la fabricación aditiva (DfAM): Optimización de disipadores de calor para impresión 3D
La mera reproducción de un diseño de disipador térmico concebido para el mecanizado o la extrusión mediante fabricación aditiva rara vez libera todo el potencial de la tecnología. Para aprovechar realmente las ventajas de la impresión metálica en 3D -complejidad geométrica sin precedentes, ligereza y rendimiento térmico potencialmente superior-, los ingenieros deben adoptar el diseño para la fabricación aditiva (DfAM). El DfAM no es sólo un conjunto de reglas, sino un cambio de mentalidad que anima a los diseñadores a pensar capa por capa y a utilizar las capacidades únicas de los procesos de AM, como la fusión selectiva por láser (SLM), la fusión de lecho de polvo por láser (LPBF) o la fusión selectiva por haz de electrones (SEBM). En el caso de los disipadores de calor personalizados, la aplicación de Gestión térmica DfAM es crucial para crear componentes que superen a sus homólogos tradicionales.
Estas son las consideraciones clave de DfAM específicas para optimizar los disipadores de calor:
1. Aprovechamiento de geometrías complejas: Más allá de las aletas simples
- Estructuras reticulares: La AM destaca en la creación de estructuras complejas y periódicas dentro de un volumen. Para los disipadores de calor, esto significa:
- Tipos: Superficies mínimas triplemente periódicas (TPMS), como los giroscopios o las estructuras Schwarz-P, o entramados basados en puntales, como los cúbicos centrados en el cuerpo (BCC) o los Octet-truss.
- Ventajas: Estas estructuras ofrecen una relación superficie/volumen excepcionalmente alta, lo que mejora significativamente la transferencia de calor por convección en comparación con las aletas tradicionales. También favorecen la mezcla de fluidos en aplicaciones refrigeradas por líquido y contribuyen a aligerar considerablemente el peso.
- Consideraciones: El tamaño de las celdas, el grosor de los puntales/paredes y la densidad general deben elegirse cuidadosamente en función de los requisitos térmicos, el flujo de fluidos (caída de presión) y las limitaciones de la capacidad de impresión (tamaño mínimo de las características, eliminación del polvo). El diseño de un disipador de calor con estructura reticular requiere herramientas informáticas especializadas y conocer las limitaciones del AM.
- Biomímesis y formas orgánicas: La naturaleza suele optimizar el transporte eficiente y la integridad estructural. DfAM permite a los diseñadores inspirarse en estructuras biológicas (por ejemplo, redes vasculares, alvéolos pulmonares) para crear trayectorias de flujo o geometrías de propagación del calor altamente eficientes y no intuitivas.
- Integración de funciones: Combine elementos como puntos de montaje, distribuidores de caudal o carcasas de sensores directamente en la estructura del disipador de calor, reduciendo el número de piezas y la complejidad del montaje.
2. Paredes delgadas, relaciones de aspecto elevadas y optimización de aletas:
- La AM permite obtener paredes y aletas más finas de lo que suele ser práctico con el mecanizado o la fundición. Esto puede aumentar la densidad de la superficie. Sin embargo, existen límites:
- Espesor mínimo: Determinado por el proceso de AM (tamaño del punto láser, características del polvo), normalmente en torno a 0,3-0,5 mm para una impresión fiable, aunque pueden conseguirse características más finas con un ajuste cuidadoso de los parámetros.
- Relación de aspecto: Las aletas muy altas y finas pueden ser propensas a las vibraciones durante la impresión o a la distorsión inducida por tensiones residuales. Las directrices de diseño suelen sugerir que se limiten las relaciones de aspecto (altura/espesor) o que se incorporen elementos de refuerzo.
- Rendimiento térmico: Mientras que las aletas más finas aumentan la densidad, las aletas demasiado finas pueden sufrir una mala conducción del calor desde la base hasta la punta (eficiencia de la aleta). La DfAM implica equilibrar la superficie con la eficacia de la vía de conducción. Diseño de pared delgada AM requiere una simulación minuciosa (CFD/FEA).
3. Diseño de canales internos (refrigeración líquida):
- La AM permite fabricar placas frías monolíticas con canales internos complejos.
- Formas autosoportadas: El diseño de canales con secciones transversales en forma de lágrima o diamante (ángulos normalmente > 45° respecto a la horizontal) permite imprimirlos sin estructuras de soporte internas, lo que simplifica considerablemente el postprocesado.
- Consideraciones de apoyo: Si se necesitan canales internos complejos horizontales o de ángulo bajo, puede ser necesario utilizar soportes internos. Estos pueden ser extremadamente difíciles o imposibles de eliminar por completo. DfAM se centra en evitar los soportes internos siempre que sea posible.
- Eliminación del polvo: Los canales deben diseñarse con orificios de entrada/salida adecuados y trayectorias suaves para facilitar la eliminación completa del polvo no fundido después de la impresión. Deben evitarse los canales sin salida o las esquinas afiladas que atrapan el polvo.
- Optimización del flujo: Las trayectorias de los canales, las secciones transversales y las características internas (como los turbuladores, que pueden conseguirse con AM) pueden optimizarse mediante la Dinámica Computacional de Fluidos (Simulación CFD AM) para maximizar la transferencia de calor y minimizar la caída de presión.
4. Optimización de la topología para el rendimiento térmico:
- Como ya se ha mencionado, el software de optimización topológica es una potente herramienta de DfAM. Para los disipadores de calor, identifica las vías más eficientes para la conducción del calor y la colocación del material para las superficies convectivas.
- Flujo de trabajo: Defina el espacio de diseño, las fuentes de calor, las condiciones de contorno (flujo de aire, temperatura ambiente), el objetivo de reducción de masa y los objetivos de rendimiento. El software genera una forma optimizada, a menudo de aspecto orgánico.
- Ventajas: Crea la estructura más rígida y térmicamente eficiente posible para una masa o volumen determinados. Ideal para diseño ligero del disipador de calor en los sectores aeroespacial y automovilístico.
- Consideraciones: Las formas optimizadas pueden ser complejas y requerir cierto suavizado o interpretación para su fabricación. Garantizar la imprimibilidad (p. ej., tamaños mínimos de las características, ausencia de huecos cerrados que atrapen el polvo) es fundamental.
5. Diseño y minimización de la estructura de apoyo estratégico:
- Los procesos de AM metálica requieren estructuras de soporte para los elementos que sobresalen (normalmente por debajo de 45° con respecto a la horizontal) y para anclar la pieza a la placa de construcción, gestionando la tensión térmica.
- Minimización: El principal objetivo del DfAM es minimizar la necesidad de soportes mediante una orientación inteligente del diseño y la modificación de las características (por ejemplo, utilizando chaflanes en lugar de salientes pronunciados).
- Colocación: Evite los soportes en superficies funcionales críticas (por ejemplo, interfaces TIM, superficies de aletas), ya que su retirada puede estropear la superficie. Colóquelos en zonas menos críticas o donde sea fácil acceder a ellos y retirarlos.
- Tipo: Elija los tipos de soporte adecuados (por ejemplo, bloque macizo, celosía, cono, soportes de árbol) en función de la geometría y de las necesidades de facilidad de desmontaje. Algunos tipos de soporte utilizan menos material y son más fáciles de desmontar.
- Facilidad de extracción: Diseñe soportes con puntos de conexión adecuados (por ejemplo, contactos perforados o cónicos) para facilitar su rotura sin dañar la pieza. Tenga en cuenta el acceso para las herramientas. Optimización de la estructura de soporte es fundamental para una AM rentable.
6. Construir una estrategia de orientación:
- La forma en que se orienta una pieza en la plataforma de construcción influye significativamente:
- Requisitos de soporte: Influye directamente en la cantidad y la ubicación de los apoyos necesarios.
- Acabado superficial: Las superficies orientadas hacia abajo tienden a ser más rugosas que las orientadas hacia arriba o las verticales. Lo ideal es que las superficies críticas estén orientadas hacia arriba o verticalmente.
- Tiempo de construcción: Las construcciones más altas suelen tardar más. Orientar para minimizar la altura Z puede acelerar la impresión.
- Tensión residual & amortiguación; alabeo: La orientación afecta a los gradientes térmicos y a la acumulación de tensiones. La orientación estratégica puede ayudar a mitigar el alabeo.
- Anisotropía: Las propiedades mecánicas y, en ocasiones, térmicas pueden variar ligeramente en función de la dirección de fabricación con respecto a la geometría de la pieza. Esto debe tenerse en cuenta en las aplicaciones de rendimiento crítico.
- En construir orientación impacto requiere una cuidadosa consideración durante las fases de diseño y preparación de la impresión.
7. Cumplimiento de las limitaciones del proceso:
- Los diseñadores deben conocer las capacidades específicas de la máquina de AM:
- Tamaño mínimo de característica: La característica fiable más pequeña (pared, agujero, puntal) que se pueda conseguir.
- Diámetro mínimo del orificio: Los agujeros pequeños pueden ser difíciles de imprimir con precisión y sin polvo.
- Tamaño máximo de construcción: Asegúrese de que la pieza cabe en el volumen de impresión.
- Grosor de la capa: Afecta a la resolución, al acabado superficial y a la velocidad de construcción.
Aplicar estos directrices para el diseño de disipadores de calor para la AM requiere la colaboración entre diseñadores y especialistas en AM. El equipo de ingeniería de aplicaciones de Met3dp’ colabora estrechamente con los clientes, aportando su experiencia en DfAM para optimizar sus diseños de disipadores de calor para nuestros avanzados sistemas SEBM y LPBF. Al aprovechar el DfAM, las empresas pueden liberar todo el potencial de la fabricación aditiva, creando disipadores de calor personalizados que se ven en nuestro escaparate de productos que ofrecen un rendimiento superior, un peso reducido y una mayor integración en comparación con las alternativas tradicionales. Los responsables de compras deben favorecer a los proveedores que demuestren una gran capacidad de DfAM, ya que esto se traduce directamente en piezas finales mejores y más rentables.
Alcanzar la precisión: Tolerancia, acabado superficial y precisión en disipadores de calor impresos en 3D
Aunque la fabricación aditiva de metales ofrece una increíble libertad de diseño, los usuarios potenciales, especialmente los ingenieros y responsables de compras acostumbrados a la precisión del mecanizado CNC, suelen tener dudas sobre los niveles de tolerancia, acabado superficial y precisión dimensional general que pueden alcanzarse. Comprender estos aspectos es crucial para gestionar las expectativas, diseñar con eficacia y determinar los pasos de posprocesamiento necesarios para obtener disipadores de calor funcionales. Fabricación de precisión en AM implica un control minucioso de toda la cadena del proceso, desde la calidad del polvo hasta la calibración de la máquina y el postprocesado.
1. Tolerancias dimensionales:
- Valores típicos: Los procesos de AM metálica como LPBF y SEBM suelen alcanzar tolerancias dimensionales del orden de ±0,1 mm a ±0,2 mm para piezas pequeñas (por ejemplo, hasta 50-100 mm), o de ±0,1% a ±0,2% de la dimensión nominal para piezas más grandes. Se trata de directrices generales que pueden variar considerablemente en función de:
- Calibración de la máquina: Las máquinas bien mantenidas y de alta calidad, como las que utiliza Met3dp, ofrecen una mayor precisión.
- Geometría y tamaño de la pieza: Las piezas más grandes y complejas son más susceptibles a la distorsión térmica, lo que puede afectar a la precisión general.
- Material: Los distintos materiales presentan diferentes comportamientos de contracción y tensión durante la impresión.
- Orientación de construcción: Afecta al historial térmico y al potencial de distorsión.
- Estrategia de apoyo: La colocación eficaz de los apoyos es crucial para mantener la precisión durante la construcción.
- Post-procesamiento: Los tratamientos térmicos de alivio de tensión pueden provocar a veces pequeños cambios dimensionales.
- Comparación: Aunque impresionantes para un proceso de fusión por capas, estas tolerancias suelen ser inferiores a las que se consiguen con el mecanizado de precisión CNC (que puede alcanzar ±0,01 mm o más para las características críticas).
- Implicación: En el caso de las características del disipador de calor que requieren tolerancias muy estrictas (por ejemplo, orificios de montaje, superficies que se acoplan con componentes sensibles, interfaces TIM), puede que no sea suficiente confiar únicamente en las tolerancias de AM as-built. A menudo es necesario el mecanizado posterior de estas características críticas.
2. Acabado superficial (rugosidad):
- Estado As-Built: La naturaleza de la fusión del polvo capa por capa da lugar a una textura superficial característica. La rugosidad superficial (Ra) de las piezas metálicas de AM suele oscilar entre 5 µm y 20 µm (micrómetros). Esto depende en gran medida de:
- Orientación:
- Superficies orientadas hacia arriba (Top): Generalmente las más suaves, ya que están formadas por la capa superior de polvo fundido.
- Paredes verticales (laterales): Muestran líneas de capa, lo que provoca una rugosidad moderada.
- Superficies orientadas hacia abajo: Suelen ser los más ásperos debido a los puntos de fijación de las estructuras de soporte y a la interacción con el polvo parcialmente sinterizado que se encuentra debajo.
- Parámetros del proceso: El grosor de la capa, la potencia del haz láser/electrón y la velocidad de escaneado influyen en la dinámica del baño de fusión y en la superficie resultante.
- Material & Tamaño del polvo: Los polvos más finos pueden dar lugar a superficies más lisas, pero plantean otros problemas.
- Orientación:
- Impacto en el rendimiento del disipador de calor:
- Compatibilidad del material de interfaz térmica (TIM): La rugosidad de la superficie puede ser demasiado alta para un contacto térmico óptimo con componentes planos, lo que puede hacer que el aire quede atrapado o que se necesiten capas de TIM más gruesas, aumentando la resistencia térmica. A menudo se recomienda pulir o mecanizar la superficie de contacto para obtener el mejor rendimiento.
- Transferencia de calor por convección: Aunque la suavidad extrema no siempre es necesaria para la convección, una rugosidad muy elevada (especialmente en los canales internos) puede aumentar la resistencia al flujo (caída de presión) en sistemas de refrigeración por líquido o aire forzado. Sin embargo, una rugosidad moderada puede mejorar ligeramente el flujo turbulento, favoreciendo la transferencia de calor en determinados regímenes.
- Radiación: El acabado de la superficie y los revestimientos posteriores (como las pinturas de alta emisividad o el anodizado) influyen significativamente en la transferencia de calor por radiación, lo que puede ser relevante en entornos de vacío o convección natural.
- Enfoque de Met3dp: Met3dp utiliza parámetros de proceso optimizados y polvos esféricos de alta calidad producidos a través de métodos avanzados de atomización con gas y PREP para lograr el mejor acabado superficial posible dentro de las capacidades inherentes de los procesos LPBF y SEBM. Nuestras medidas de control de calidad garantizan la uniformidad en todas las fabricaciones.
3. Precisión dimensional & Alabeo:
- Desafío: Los rápidos ciclos de calentamiento y enfriamiento inherentes a la fusión de capas de polvo pueden generar importantes tensiones internas en la pieza. Si no se gestionan adecuadamente, estas tensiones pueden provocar alabeos o distorsiones, sobre todo después de cortar la pieza de la placa de impresión y aliviar la tensión de forma desigual.
- Estrategias de mitigación:
- Simulación del proceso: La simulación previa del proceso de fabricación puede predecir las zonas de mayor tensión y distorsión potencial, lo que permite ajustar la orientación o la estrategia de apoyo.
- Parámetros optimizados: El ajuste de los parámetros de fusión minimiza los gradientes térmicos.
- Estructuras de soporte robustas: El anclaje seguro de la pieza evita que se mueva durante la construcción y ayuda a controlar la tensión.
- Tratamiento térmico antiestrés: Antes de retirar el soporte, se realiza una fase de postprocesado crítica (que se describe a continuación) para homogeneizar la microestructura y reducir la tensión interna, estabilizando las dimensiones de la pieza.
- Resultado: Mediante el empleo de estas estrategias, los proveedores de AM reputados como Met3dp pueden alcanzar altos niveles de precisión dimensional AM para minimizar la desviación del modelo CAD previsto. Sin embargo, los diseñadores deben tener en cuenta las tolerancias estándar de la AM y planificar el mecanizado posterior cuando se necesite la máxima precisión.
Tabla: Resumen de precisión AM para disipadores de calor
Parámetro | Gama típica as-built (LPBF/SEBM) | Factores clave que influyen | Impacto en los disipadores de calor & Soluciones |
---|---|---|---|
Tolerancia dimensional | ±0,1 a ±0,2 mm o ±0,1% a ±0,2% | Máquina, material, geometría, tamaño, orientación, soportes | Suficiente para muchas características; las interfaces críticas suelen requerir un mecanizado posterior. |
Rugosidad superficial (Ra) | 5 - 20 µm | Orientación, parámetros, polvo, material | Afecta al contacto TIM (superficies de contacto pulido/máquina), resistencia al flujo (considerar en CFD). |
Deformación/Distorsión | Puede ocurrir si no se gestiona | Estrés térmico, estrategia de apoyo, geometría de la pieza, alivio de tensiones | Mitigado por simulación, soportes, orientación, tratamiento térmico esencial de alivio de tensiones. |
Control de calidad Metal AM | Crucial en todo | Manipulación de polvos, calibrado de máquinas, supervisión de procesos | Garantiza la coherencia y la fiabilidad; suministrado por proveedores experimentados como Met3dp. |
Exportar a hojas
En resumen, aunque la impresión metálica en 3D no pueda igualar la precisión submicrónica del mecanizado especializado en su estado bruto, ofrece una precisión notable para un proceso de fabricación digital directa. Si se conocen las tolerancias y los acabados superficiales típicos, se diseña en consecuencia (DfAM) y se incorporan los pasos de posprocesamiento adecuados, los ingenieros pueden utilizar con confianza la AM metálica para producir disipadores de calor personalizados complejos y altamente funcionales que cumplan los exigentes requisitos de rendimiento. Asociarse con un proveedor centrado en control de calidad metal AM garantiza el cumplimiento sistemático de estos niveles de precisión.
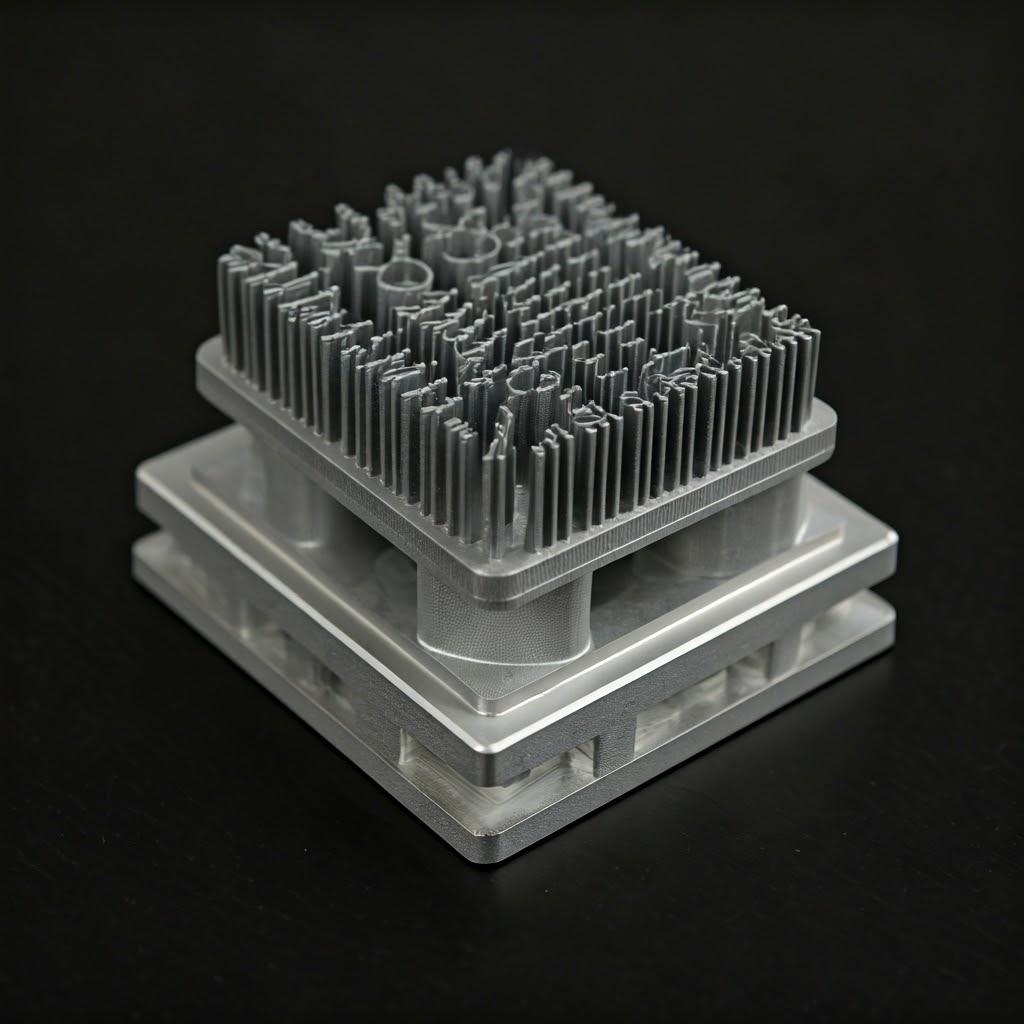
Más allá de la impresión: Postprocesado esencial para disipadores de calor funcionales
La creación de un disipador de calor personalizado mediante fabricación aditiva metálica implica algo más que darle a "imprimir". La pieza recién fabricada, recién salida de la impresora, rara vez está lista para su uso inmediato. Suelen ser necesarios una serie de pasos cruciales de posprocesamiento para transformar el componente impreso en bruto en un disipador de calor totalmente funcional, fiable y de alto rendimiento que cumpla las especificaciones de ingeniería. Comprender estos pasos es vital para los responsables de compras que presupuestan los proyectos y para los ingenieros que diseñan las piezas, ya que los requisitos de posprocesamiento pueden influir significativamente en el coste final, el plazo de entrega y el rendimiento del componente. Los proveedores de servicios de AM de renombre ofrecen soluciones integrales que incluyen estos pasos de acabado esenciales, a menudo proporcionando a medida servicios de acabado B2B.
He aquí un desglose de las fases habituales de posprocesamiento de los disipadores térmicos metálicos impresos en 3D:
1. Tratamiento térmico antiestrés:
- Propósito: Para aliviar las tensiones internas acumuladas durante los rápidos ciclos de calentamiento y enfriamiento del proceso de fusión capa a capa. Esto es especialmente importante en materiales como el AlSi10Mg impreso mediante LPBF. Sin el alivio de tensiones, las piezas pueden alabearse o deformarse cuando se cortan de la placa de impresión o durante el mecanizado posterior.
- Proceso: La placa de impresión completa, con las piezas aún fijadas, se introduce en un horno y se calienta a una temperatura específica (por debajo de la temperatura de envejecimiento del material, por ejemplo, alrededor de 300 °C para AlSi10Mg) durante un periodo definido, seguido de un enfriamiento controlado. Esto permite que la microestructura del material se relaje y se reduzcan las tensiones residuales.
- Importancia: Absolutamente esencial para la estabilidad dimensional y la prevención de fallos prematuros. Suele ser el primer paso una vez finalizada la construcción y enfriada la cámara.
2. Extracción de la pieza de la placa de construcción:
- Propósito: Para separar el disipador o disipadores de calor impresos de la placa base metálica sobre la que se construyeron.
- Métodos: Suele realizarse mediante electroerosión por hilo (EDM) o sierra de cinta. Hay que tener cuidado de no dañar las piezas. Se cortan las estructuras de soporte que conectan la pieza a la placa.
- Consideraciones: El método de extracción puede influir en el acabado superficial de la base de la pieza.
3. Eliminación de la estructura de soporte:
- Propósito: Para eliminar las estructuras temporales que soportaban los elementos salientes y anclaban la pieza durante la impresión.
- Métodos: Éste puede ser uno de los pasos más laboriosos, especialmente en el caso de geometrías complejas.
- Eliminación manual: Los soportes suelen estar diseñados con puntos de conexión debilitados y pueden romperse manualmente con alicates o herramientas manuales.
- Mecanizado/Rectificado: Los soportes más resistentes o los que se encuentran en superficies críticas pueden tener que eliminarse mediante mecanizado CNC o esmerilado/lijado manual.
- Electroerosión por hilo: A veces se utiliza para una extracción precisa en zonas estrechas.
- Desafíos: Acceder a los soportes internos de canales complejos o estructuras reticulares puede resultar extremadamente difícil. Eliminación de soportes metálicos AM requiere una planificación cuidadosa durante la fase de DfAM para garantizar la accesibilidad y minimizar la cantidad de apoyo necesario. Pueden producirse daños si la retirada no se realiza con cuidado.
4. Eliminación de polvo (Depowdering):
- Propósito: Para eliminar el polvo metálico sin fundir atrapado en la pieza, especialmente en canales internos, entramados o huecos complejos. El polvo residual puede añadir peso, comprometer potencialmente el rendimiento térmico si bloquea las vías de flujo y soltarse posteriormente.
- Métodos: Se utilizan soplado de aire comprimido, mesas vibratorias, baños de limpieza por ultrasonidos y, a veces, sistemas de lavado especializados.
- Importancia: Es fundamental para piezas con características internas, como placas frías refrigeradas por líquido o disipadores de calor con estructuras reticulares densas. El DfAM también desempeña un papel importante en este caso: el diseño de orificios de escape y vías internas fluidas facilita el vaciado.
5. Tratamiento térmico adicional (envejecimiento/endurecimiento):
- Propósito: Para optimizar las propiedades mecánicas del material (resistencia, dureza) y, lo que es más importante para los disipadores térmicos, a menudo su conductividad térmica.
- AlSi10Mg: Suele someterse a un tratamiento térmico en solución T6 y a un proceso de envejecimiento artificial. Esto implica calentar a una temperatura más alta (alrededor de 500-540°C) para disolver los precipitados, enfriar rápidamente y después envejecer a una temperatura más baja (alrededor de 150-170°C) para formar precipitados finos que refuerzan el material. El sitio tratamiento térmico AlSi10Mg recibe influye significativamente en sus propiedades finales. El estado T6 suele ofrecer la mejor combinación de resistencia y conductividad térmica para esta aleación.
- CuCrZr: Requiere endurecimiento por precipitación (envejecimiento) a temperaturas específicas (por ejemplo, 450-500°C) para formar precipitados de Cr y Zr, que aumentan drásticamente la resistencia y la dureza, conservando en gran medida la alta conductividad térmica y eléctrica de la matriz de cobre.
- Importancia: Esencial para alcanzar las especificaciones de material objetivo indicadas en las hojas de datos y garantizar que el disipador de calor tenga la resistencia y el rendimiento térmico requeridos.
6. Acabado de superficies:
- Propósito: Modificar la textura de la superficie para mejorar la estética, la función o el procesamiento posterior.
- Granallado/chorro de arena: Crea un acabado mate uniforme y no direccional mediante la propulsión de medios finos (perlas de vidrio, grano) en la superficie. Elimina pequeñas imperfecciones y puede proporcionar una base limpia para revestimientos.
- Acabado por volteo/vibración: Las piezas se colocan en un bombo con material para desbarbar los bordes afilados y proporcionar un acabado más suave y uniforme, especialmente en el caso de piezas pequeñas o con características externas complejas.
- Pulido: El pulido mecánico o electroquímico puede utilizarse para conseguir superficies muy lisas y reflectantes (Ra bajo). Suele aplicarse selectivamente a las zonas de interfaz TIM para minimizar la resistencia térmica de contacto.
- Opciones: La elección depende del resultado deseado: uniformidad estética, valor específico de rugosidad o preparación para el revestimiento. Existe una gama de opciones de acabado superficial están disponibles.
7. Mecanizado CNC:
- Propósito: Para conseguir tolerancias más estrictas, acabados superficiales específicos o características que no son posibles sólo con AM.
- Aplicaciones:
- Interfaces críticas: Mecanizado de superficies que se acoplan con TIMs u otros componentes para garantizar la planitud y la rugosidad requerida.
- Tolerancias ajustadas: Conseguir tolerancias dimensionales mejores que ±0,1 mm.
- Roscado/roscado: Creación de orificios roscados para el montaje.
- Perfeccionamiento de funciones: Afilar bordes o crear características difíciles de definir con precisión en AM.
- Integración: Mecanizado CNC de impresiones 3D es un enfoque híbrido común, que aprovecha la AM para geometrías complejas y el mecanizado para características de precisión.
8. Revestimiento / Tratamiento de superficie:
- Propósito: Para añadir más funcionalidad o protección.
- Anodizado (para aleaciones de aluminio): Proporciona una mayor resistencia a la corrosión, aislamiento eléctrico, resistencia al desgaste y permite la coloración (estética). Anodizado del disipador térmico es habitual en las piezas de AlSi10Mg.
- Revestimiento (por ejemplo, níquel, oro): Puede mejorar la resistencia a la corrosión, la soldabilidad o la conductividad superficial.
- Pintura/Recubrimiento en polvo: Para la estética o la aplicación de revestimientos especializados (por ejemplo, pinturas de alta emisividad para mejorar la refrigeración radiativa).
9. Pruebas de control de calidad:
- Propósito: Para verificar que la pieza cumple todas las especificaciones antes del envío.
- Métodos: Inspección dimensional (MMC, escaneado láser), verificación de las propiedades de los materiales (por ejemplo, pruebas de dureza), medición del acabado superficial, pruebas de estanqueidad (para canales refrigerados por líquido), pruebas de rendimiento térmico (si es necesario), END (pruebas no destructivas como el escaneado CT) para estructuras internas críticas o comprobaciones de porosidad. Pruebas de control de calidad es la última puerta antes de la entrega.
Met3dp es consciente de que el posprocesamiento es esencial para obtener piezas funcionales fabricadas mediante aditivos. Ofrecemos o gestionamos un conjunto completo de servicios de posprocesamiento, que garantizan que los disipadores de calor personalizados que producimos cumplen los estrictos requisitos de sectores como el aeroespacial, la automoción y el médico, hasta la inspección final y la entrega. Contratar a un proveedor que tenga en cuenta todo el flujo de trabajo, incluido el posprocesamiento, es clave para el éxito del proyecto.
Superar los retos de la impresión 3D de disipadores de calor: Soluciones y mejores prácticas
Aunque la fabricación aditiva de metales ofrece enormes ventajas para los disipadores de calor personalizados, como cualquier proceso de fabricación avanzado, conlleva posibles retos. Conocer estos posibles obstáculos y comprender las soluciones y las mejores prácticas empleadas por proveedores de AM experimentados como Met3dp es crucial para mitigar los riesgos y garantizar resultados satisfactorios. Abordar estos retos de forma proactiva es clave para ofrecer los componentes fiables y de alto rendimiento que esperan los clientes B2B.
1. Deformación y tensión residual:
- Desafío: El calentamiento intenso y localizado y el enfriamiento rápido inherentes a LPBF/SEBM crean gradientes térmicos que conducen a la acumulación de tensiones internas. Si las tensiones superan el límite elástico del material a temperaturas elevadas, o si se alivian de forma desigual al retirarlo de la placa de impresión, la pieza puede deformarse o distorsionarse, comprometiendo la precisión dimensional. Deformación del metal Impresión 3D es una preocupación primordial, especialmente en el caso de piezas grandes o complejas.
- Soluciones y mejores prácticas:
- Simulación del proceso: Especializada Simulación del proceso de AM predice la acumulación de tensiones y la distorsión en función de la geometría, el material y la estrategia de escaneado, lo que permite una optimización previa.
- Orientación de construcción optimizada: Orientar la pieza para minimizar las grandes superficies planas paralelas a la placa de impresión, reducir las concentraciones de masa térmica y minimizar los voladizos sin soporte.
- Estrategia de apoyo sólida: Utilizar estructuras de soporte bien diseñadas para anclar firmemente la pieza, alejar el calor y contrarrestar las fuerzas de contracción.
- Estrategia de exploración optimizada: Utilización de técnicas como la exploración en isla o los patrones de tablero de ajedrez para gestionar la distribución del calor y reducir las pistas de fusión largas y continuas.
- Alivio de tensión obligatorio: Realización de un tratamiento térmico adecuado para aliviar el estrés antes de retirar la pieza de la placa de impresión no es negociable para la mayoría de las piezas metálicas de AM, especialmente las aleaciones de aluminio.
2. Dificultades para eliminar la estructura de soporte:
- Desafío: Los soportes, aunque necesarios, deben retirarse. Esto puede resultar difícil, llevar mucho tiempo y correr el riesgo de dañar la pieza, especialmente en el caso de:
- Soportes internos: Los soportes dentro de canales o estructuras de celosía pueden ser casi imposibles de acceder y eliminar por completo.
- Características delicadas: Retirar los soportes fijados a aletas finas o detalles intrincados requiere mucho cuidado.
- Materiales resistentes: Los soportes fabricados con aleaciones resistentes pueden ser más difíciles de romper o mecanizar.
- Soluciones y mejores prácticas:
- DfAM para la minimización de soportes: Lo mejor es diseñar la pieza para que sea autoportante en la medida de lo posible (utilizando ángulos >45°, diseñando una orientación óptima).
- Diseñar para el acceso: Si los soportes internos son inevitables, diseñe puertos de acceso o vías para herramientas de extracción o lavado.
- Diseño inteligente de soportes: Utilice tipos de soporte con puntos de contacto mínimos (por ejemplo, conexiones cónicas o perforadas) que se desprenden más fácilmente. Los soportes en forma de árbol suelen ofrecer una mejor accesibilidad.
- Técnicas de eliminación adecuadas: Utilización de las herramientas adecuadas (manual, electroerosión, mecanizado) en función de la ubicación del soporte y el material. Los técnicos con experiencia son cruciales.
3. Control de la porosidad:
- Desafío: A veces pueden formarse pequeños huecos o poros dentro del material impreso debido a gas atrapado, fusión incompleta entre capas o inconsistencias de polvo. La porosidad puede tener un impacto negativo:
- Conductividad térmica: Los poros interrumpen la trayectoria del flujo de calor, reduciendo la conductividad efectiva.
- Resistencia mecánica: Actúan como concentradores de tensiones, reduciendo la vida a fatiga y la resistencia general.
- Estanqueidad: Puede crear vías de fuga en canales refrigerados por líquido.
- Soluciones y mejores prácticas:
- Polvo de alta calidad: Utilizando polvos de alta esfericidad, distribución controlada del tamaño de las partículas, bajo contenido interno de gas y manipulación adecuada para evitar la contaminación por humedad (los polvos VIGA/PREP de Met3dp’ destacan en este aspecto).
- Parámetros de impresión optimizados: Desarrollo y control estricto de los parámetros del proceso (potencia del láser/rayo, velocidad, grosor de la capa, control de la atmósfera) validados para combinaciones específicas de material/máquina con el fin de garantizar la fusión completa. Met3dp invierte mucho en la optimización del proceso.
- Prensado isostático en caliente (HIP): Para aplicaciones críticas que exigen una densidad cercana al 100%, el postprocesado HIP (aplicando alta temperatura y presión de gas isostático) puede cerrar eficazmente los poros internos.
- Control de calidad: Utilización de métodos END como la tomografía computarizada para detectar y cuantificar la porosidad si la aplicación lo requiere. Control de la porosidad AM se basa en una gestión rigurosa de los procesos.
4. Eliminación de polvo de geometrías complejas:
- Desafío: El polvo sin fundir puede quedar atrapado en intrincados disipadores de calor con estructura reticular o canales internos largos y estrechos. La eliminación completa es vital para el rendimiento y para evitar la contaminación posterior por polvo suelto.
- Soluciones y mejores prácticas:
- DfAM para despolvoreado: Diseñar orificios de escape, garantizar la conectividad de los canales, evitar los callejones sin salida y utilizar curvas internas suaves.
- Métodos de limpieza eficaces: Empleando técnicas apropiadas como purga con aire comprimido/gas inerte, vibración, limpieza ultrasónica o sistemas especializados de lavado con disolventes/fluidos.
- Inspección: Verificación de la eliminación del polvo mediante inspección visual (boroscopio), pesaje de la pieza o tomografía computarizada si es necesario. Eliminación de polvo en piezas complejas requiere previsión en el diseño.
5. Conseguir un acabado superficial homogéneo:
- Desafío: El acabado de la superficie conforme a obra varía en función del ángulo de la superficie con respecto a la dirección de construcción. Esta inconsistencia puede ser inaceptable por razones estéticas o funcionales (por ejemplo, flujo de aire uniforme).
- Soluciones y mejores prácticas:
- Orientación estratégica: Dé prioridad a las superficies críticas orientándolas verticalmente o hacia arriba si es posible.
- Posprocesamiento consistente: El empleo de técnicas de acabado superficial como el granallado o el volteo proporciona un acabado más uniforme en todas las superficies.
- Criterios de aceptación: Definir claramente los requisitos de acabado superficial aceptables para las distintas características de las piezas.
6. Validación del rendimiento térmico:
- Desafío: Garantizar que el disipador de calor final, impreso y postprocesado, funcione térmicamente según lo previsto por las simulaciones o los cálculos de diseño. Las discrepancias pueden deberse a variaciones en las propiedades del material (afectadas por la porosidad o el tratamiento térmico), desviaciones geométricas o impactos en el acabado superficial.
- Soluciones y mejores prácticas:
- Datos precisos de los materiales: Utilización en las simulaciones de datos validados sobre las propiedades de los materiales (incluida la conductividad térmica tras tratamientos térmicos específicos).
- Simulación correlacionada: Calibrar los modelos CFD/FEA con datos de pruebas empíricas siempre que sea posible.
- Pruebas térmicas: Realización de pruebas de laboratorio (por ejemplo, utilizando vehículos de pruebas térmicas, termografía infrarroja) o pruebas in situ para medir la resistencia térmica real y los perfiles de temperatura bajo cargas operativas.
- Colaboración: En estrecha colaboración con un proveedor de AM fiable como Met3dp, que conoce los matices del rendimiento de las piezas de AM y puede orientar sobre los resultados esperados y los métodos de validación. Validación del rendimiento térmico cierra el círculo entre el diseño y la realidad.
Al anticiparse a estos retos y aplicar soluciones sólidas basadas en los principios DfAM, un control riguroso de los procesos, un posprocesamiento exhaustivo y una garantía de calidad minuciosa, la fabricación aditiva de metales puede ofrecer disipadores de calor personalizados que satisfagan y, a menudo, superen las demandas de las aplicaciones electrónicas más exigentes. Asociarse con un proveedor experimentado como Met3dp reduce significativamente el riesgo de adopción de esta tecnología transformadora para las necesidades críticas de gestión térmica. Comprender y solución de problemas metal AM cuestiones forma parte del valor que aporta un socio experto.
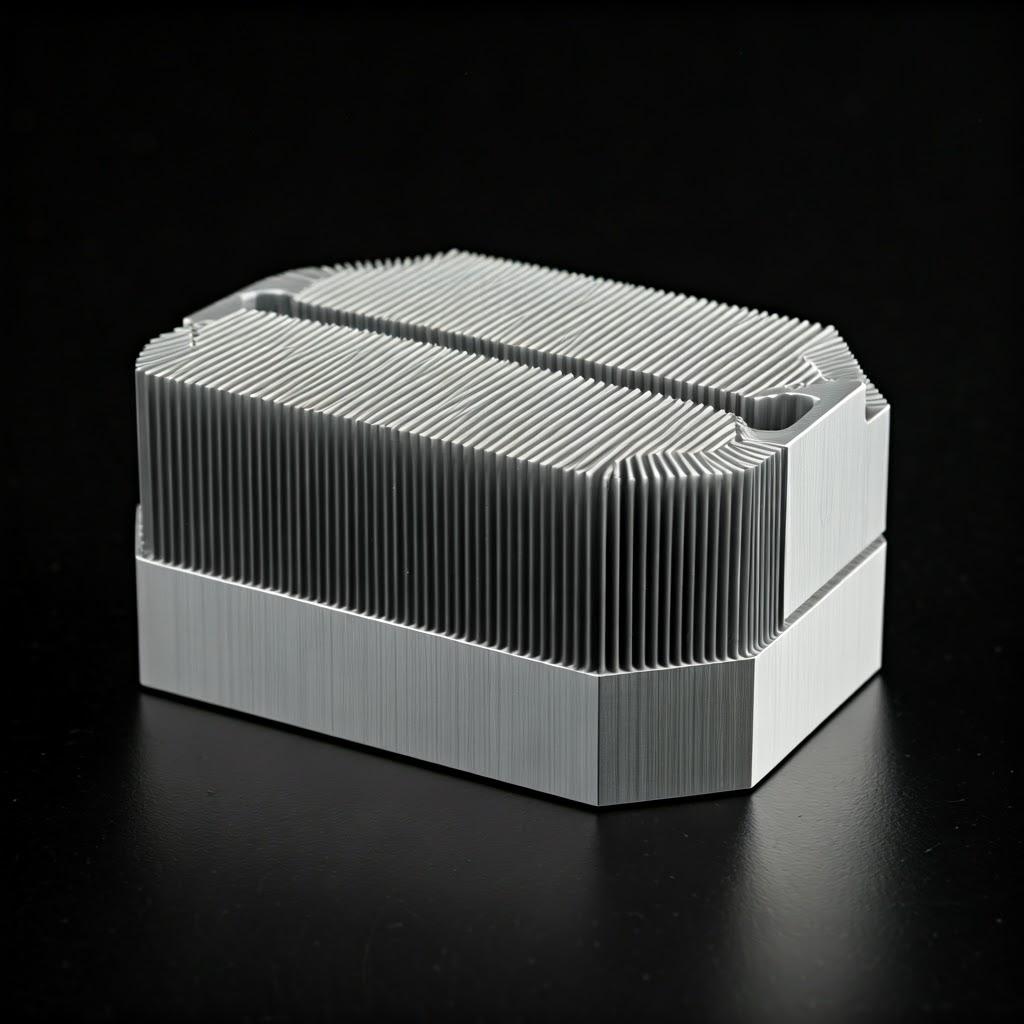
Cómo elegir a su socio: Selección del proveedor de servicios de impresión 3D de metal adecuado para disipadores de calor
Embarcarse en un proyecto que implique disipadores de calor personalizados impresos en 3D requiere algo más que el acceso a una impresora de metal; exige una asociación estratégica con un proveedor de servicios que posea la combinación adecuada de tecnología, conocimientos de ciencia de materiales, control de procesos y experiencia específica en aplicaciones. La calidad, el rendimiento y la fiabilidad de su solución final de gestión térmica están directamente relacionados con las capacidades del socio que elija. Para los responsables de compras y los ingenieros que evalúan a los posibles proveedores, realizar una minuciosa evaluación exhaustiva de la oficina de servicios de AM en metal es fundamental. No todos los proveedores son iguales, sobre todo cuando se trata de la complejidad de los componentes térmicos.
Estos son los criterios clave que debe tener en cuenta a la hora de elegir su proveedor de disipadores de calor mediante fabricación aditiva:
1. Experiencia demostrada en gestión térmica y materiales pertinentes:
- Más allá de la impresión general: ¿Tiene el proveedor experiencia demostrable en la impresión de disipadores térmicos u otros componentes térmicos complejos? Pida estudios de casos, ejemplos o datos relacionados con aplicaciones térmicas.
- Especialización en materiales: ¿Tratan habitualmente los materiales cruciales para los disipadores de calor, es decir, AlSi10Mg y aleaciones de cobre de alta conductividad como CuCrZr? Conozca su nivel de experiencia en la optimización de parámetros y postprocesado de estos metales específicos para conseguir las propiedades térmicas y mecánicas deseadas.
- Comprensión de la aplicación: ¿Comprenden sus ingenieros los matices de la transferencia de calor, la dinámica de fluidos (para la refrigeración líquida) y los retos específicos de la refrigeración electrónica en su sector (por ejemplo, aeroespacial, automoción)?
2. Tecnología y equipos avanzados:
- Cartera de máquinas: ¿Disponen de impresoras industriales de última generación (LPBF, SEBM)? ¿Cuál es el volumen de producción, la precisión y la fiabilidad de sus equipos? Los proveedores como Met3dp invierten en volumen de impresión, precisión y fiabilidad líderes en la industria para aplicaciones exigentes.
- Control de procesos: ¿Qué medidas se aplican para supervisar el proceso (por ejemplo, supervisión del baño de fusión, controles medioambientales)? Un control coherente del proceso es clave para una calidad repetible.
- Herramientas de software: ¿Utilizan software avanzado para la preparación de la construcción, la simulación (térmica/estrés) y la generación de soportes?
3. Calidad, control y trazabilidad de los materiales:
- Abastecimiento de polvo y calidad: Esto es primordial. ¿Fabrica el proveedor sus propios polvos de alta calidad utilizando métodos avanzados como VIGA o PREP (como hace Met3dp), o tiene controles estrictos para abastecerse de proveedores cualificados? Pregunte por la caracterización del polvo (esfericidad, distribución del tamaño de las partículas, pureza) y la consistencia de los lotes.
- Manipulación & Reciclaje: ¿Cuáles son sus procedimientos de almacenamiento, manipulación, tamizado y reciclado de polvos metálicos para evitar la contaminación y garantizar una calidad constante de la materia prima?
- Trazabilidad de los materiales: ¿Pueden proporcionar trazabilidad del material desde el lote de polvo en bruto hasta la pieza final, incluidas las certificaciones? Esto suele ser un requisito en las industrias reguladas.
4. Capacidades integrales de posprocesamiento:
- Servicios integrados: ¿Ofrece el proveedor los pasos de postprocesado necesarios en la propia empresa o a través de una red gestionada estrechamente? Esto incluye alivio de tensiones, eliminación de soportes, tratamiento térmico (con hornos calibrados para ciclos específicos como T6 para AlSi10Mg o envejecimiento para CuCrZr), mecanizado CNC para características críticas, varias opciones de acabado superficial (anodizado de disipadores de calorpulido, chorreado), y limpieza/desempolvado a fondo.
- Experiencia: ¿Disponen de los conocimientos necesarios para realizar estos pasos correctamente sin dañar la pieza y conseguir las propiedades y acabados especificados?
5. Sistema de gestión de calidad (QMS) y certificaciones robustos:
- Certificación base: La certificación ISO 9001 demuestra el compromiso con los procesos de calidad y la mejora continua.
- Certificaciones específicas del sector: Dependiendo de su aplicación, pueden ser necesarias certificaciones como AS9100 (aeroespacial), ISO 13485 (médica) o IATF 16949 (automoción). Aunque no sean estrictamente necesarias, los proveedores que poseen estas certificaciones suelen tener procedimientos más rigurosos de control de calidad, documentación y validación de procesos, lo que los convierte en los preferidos aM con certificación aeroespacial o proveedor de grado médico.
6. Ingeniería & Apoyo DfAM:
- Asociación colaborativa: ¿Ofrece el proveedor asesoramiento sobre diseño para fabricación aditiva (DfAM)? ¿Pueden sus ingenieros revisar su diseño, sugerir optimizaciones para la imprimibilidad, el rendimiento, la reducción del soporte y la rentabilidad? Este experiencia en fabricación aditiva es inestimable.
- Capacidades de simulación: ¿Pueden ayudar con la simulación térmica o de tensión para predecir el rendimiento o identificar posibles problemas antes de imprimir?
- Resolución de problemas: ¿Cuentan con ingenieros experimentados que puedan ayudar a resolver problemas de diseño o fabricación?
7. Comunicación, transparencia y gestión de proyectos:
- Cita clara: ¿Es el citando la impresión 3D en metal ¿El proceso es directo y transparente, con una descripción clara de todos los costes y pasos?
- Capacidad de respuesta: ¿Es el equipo receptivo a las preguntas y proactivo en la comunicación a lo largo del proyecto?
- Seguimiento de proyectos: ¿Pueden proporcionar información actualizada sobre el estado del proyecto y los plazos estimados de finalización?
8. Capacidad, plazos y escalabilidad:
- Velocidad de creación de prototipos: ¿Pueden ofrecer plazos de entrega rápidos para los prototipos?
- Capacidad de producción: ¿Disponen de la capacidad de maquinaria y la gestión del flujo de trabajo para gestionar posibles volúmenes de producción en serie en caso necesario?
- Plazos de entrega fiables: ¿Tienen un historial de cumplimiento de los plazos de entrega prometidos?
Por qué destaca Met3dp: Met3dp se ha diseñado específicamente para cumplir estos exigentes criterios. Con décadas de experiencia colectivaofrecemos soluciones integrales que abarcan:
- Sistemas AM avanzados: Impresoras SEBM y LPBF líderes del sector.
- Polvos de alta calidad: Fabricación propia con tecnologías VIGA y PREP para aleaciones superiores de AlSi10Mg, CuCrZr, Ti, etc.
- Servicios integrales: Desde el asesoramiento de DfAM y el apoyo a la simulación hasta la impresión, el posprocesamiento completo y una estricta garantía de calidad.
- Trayectoria probada: Sirviendo con éxito a aplicaciones de misión crítica en los sectores aeroespacial, médico, automovilístico e industrial.
- Obtenga más información sobre nuestra empresa, nuestros valores y nuestro compromiso con la calidad en nuestro Quiénes somos.
Elegir al socio adecuado es invertir en el éxito de su proyecto. Si evalúa cuidadosamente a los posibles proveedores en función de estos criterios, podrá encontrar un proveedor como Met3dp que posea las necesarias Met3dp y actúa como un verdadero socio en innovación, ayudándole a aprovechar todo el potencial de la AM metálica para sus necesidades de disipadores térmicos personalizados.
Factores de coste y plazos de entrega de los disipadores térmicos impresos en 3D
Una de las principales consideraciones a la hora de adoptar cualquier tecnología de fabricación es conocer los costes asociados y los plazos de producción. La fabricación aditiva de metales, aunque ofrece capacidades únicas, tiene su propio conjunto de factores de coste y plazos de entrega que difieren de los métodos tradicionales. Proporcionar transparencia en estimación de costes de impresión 3D de metales y Plazo de producción AM ayuda a los ingenieros y responsables de compras a tomar decisiones informadas y evaluar la propuesta de valor global.
Factores clave del coste de los disipadores térmicos impresos en 3D:
- Tipo de material y consumo:
- Coste del polvo: El coste de las materias primas varía considerablemente. Las aleaciones de cobre de alto rendimiento, como CuCrZr, son considerablemente más caras que las aleaciones de aluminio, como AlSi10Mg. Las aleaciones exóticas aumentarían aún más los costes.
- Volumen: El volumen total de la pieza, más las estructuras de soporte necesarias, influye directamente en la cantidad de polvo consumido y fundido. Las piezas más grandes y densas cuestan más. Las técnicas DfAM, como la optimización topológica y las estructuras reticulares, pueden reducir considerablemente el uso de material y, por tanto, los costes.
- Tiempo de máquina (tiempo de construcción):
- Factor principal: El tiempo de fabricación viene determinado en gran medida por la altura de la(s) pieza(s) en el eje Z (número de capas) y el área total que necesita ser explorada por el láser o el haz de electrones para cada capa.
- Complejidad: Las geometrías muy complejas pueden requerir trayectorias de escaneado más complejas, lo que aumenta ligeramente el tiempo por capa.
- Nesting & Utilización de la plataforma: La impresión simultánea de varias piezas (anidamiento) en una única plataforma de fabricación mejora drásticamente la utilización de la máquina y reduce el coste por pieza. Maximizar el número de piezas dentro del volumen de fabricación es clave para economías de escala AM.
- Costes laborales:
- Preprocesamiento: La preparación de archivos CAD, la optimización de la orientación, la generación de estructuras de soporte y la configuración de archivos de construcción requieren el tiempo de técnicos cualificados.
- Funcionamiento de la máquina: Configurar la impresora, supervisar la construcción (aunque a menudo muy automatizada) y retirar la plataforma de construcción.
- Post-procesamiento: Esto puede suponer un importante componente de mano de obra, especialmente para la retirada de soportes de piezas complejas, el acabado manual y la inspección.
- Estructuras de apoyo:
- Uso del material: Los soportes consumen material, lo que aumenta el coste.
- Esfuerzo de retirada: El tiempo y el esfuerzo necesarios para retirar los soportes (manual o mecanizado) repercuten directamente en los costes de mano de obra. Minimizar los soportes mediante DfAM es crucial para reducir costes.
- Requisitos de postprocesamiento:
- Tratamiento térmico: Costes asociados al tiempo de horno, consumo de energía y manipulación para aliviar tensiones y/o ciclos de envejecimiento.
- Mecanizado: El tiempo de mecanizado CNC de las características críticas añade costes en función de la complejidad y el tiempo necesario.
- Acabado superficial: Los costes varían en función del método (granallado, pulido, volteo, anodizado) y del nivel de acabado requerido.
- HIP (Prensado isostático en caliente): Si se exige la máxima densidad, el HIP añade un importante componente de coste.
- Control de calidad e inspección:
- El nivel de inspección necesario (visual, comprobaciones dimensionales con MMC/escaneado, END como escaneado CT para integridad interna) repercute en los costes de mano de obra y equipos. Los requisitos varían en función de la criticidad de la aplicación.
- Gastos de instalación e ingeniería:
- Algunos proveedores pueden cobrar gastos de instalación inicial, especialmente para proyectos complejos o si se requiere un apoyo importante de DfAM.
Plazos de entrega típicos:
Los plazos de entrega de los disipadores térmicos metálicos impresos en 3D pueden variar mucho:
- Prototipos: Para piezas individuales o lotes muy pequeños, los plazos de entrega pueden oscilar entre unos pocos días laborables y 2 ó 3 semanas, en función de la complejidad, el material, la disponibilidad de la máquina y el tratamiento posterior necesario. Los servicios acelerados pueden tener un coste adicional.
- Producción de bajo volumen: Para lotes de decenas a cientos de piezas, los plazos de entrega suelen oscilar entre 3 y 8 semanas, muy influidos por el tiempo total de máquina necesario, la complejidad del postprocesado y la capacidad/programación general.
- Factores que influyen en el plazo de entrega:
- Cola de pedidos actual: La carga de trabajo de las oficinas de servicios es un factor importante.
- Tiempo de construcción: Según cálculos basados en la altura y el volumen de la pieza.
- Complejidad del postprocesado: El posprocesamiento en varios pasos o intrincado añade un tiempo considerable.
- Disponibilidad de material: Asegurarse de que el polvo específico está en stock.
- Requisitos de inspección: Las pruebas exhaustivas añaden tiempo.
Consideraciones sobre el retorno de la inversión (ROI):
Mientras que el análisis de costes por pieza de AM pueden parecer a veces más elevados que los métodos tradicionales de simple geometrías en grandes volúmenes, la ROI fabricación aditiva ofertas se convierte en convincente cuando se considera:
- Complejidad gratis: La AM gestiona una gran complejidad geométrica con un coste añadido mínimo o nulo en comparación con el mecanizado, en el que la complejidad aumenta los costes exponencialmente.
- Sin costes de utillaje: Elimina la importante inversión inicial y los plazos de entrega asociados a los moldes o matrices, por lo que resulta ideal para piezas personalizadas y volúmenes bajos o medios.
- Ganancias de rendimiento: Un rendimiento térmico superior conseguido mediante diseños optimizados puede traducirse en una mayor fiabilidad, eficiencia o capacidad del producto, proporcionando un retorno indirecto de la inversión.
- Aligeramiento: La reducción del peso de los componentes se traduce en un ahorro de combustible (automoción/aeroespacial) o en una mejora de la maniobrabilidad.
- Tiempo de comercialización más rápido: La creación rápida de prototipos y la transición más rápida a la producción de piezas complejas pueden suponer una ventaja competitiva.
- Flexibilidad de la cadena de suministro: La producción bajo demanda reduce las necesidades de inventario y permite actualizar el diseño.
Comprender estos factores de coste y las expectativas de plazos de entrega permite elaborar presupuestos y planificar proyectos con precisión. Para las empresas que se plantean precios al por mayor impresión 3D o la producción regular, discutir los requisitos de volumen y las estrategias de optimización con un proveedor como Met3dp es esencial para conseguir el mejor valor posible. La elección de métodos de impresión (como LPBF frente a SEBM) también pueden tener sutiles implicaciones de coste en función del proveedor y la aplicación, aunque el material y la geometría suelen ser factores dominantes.
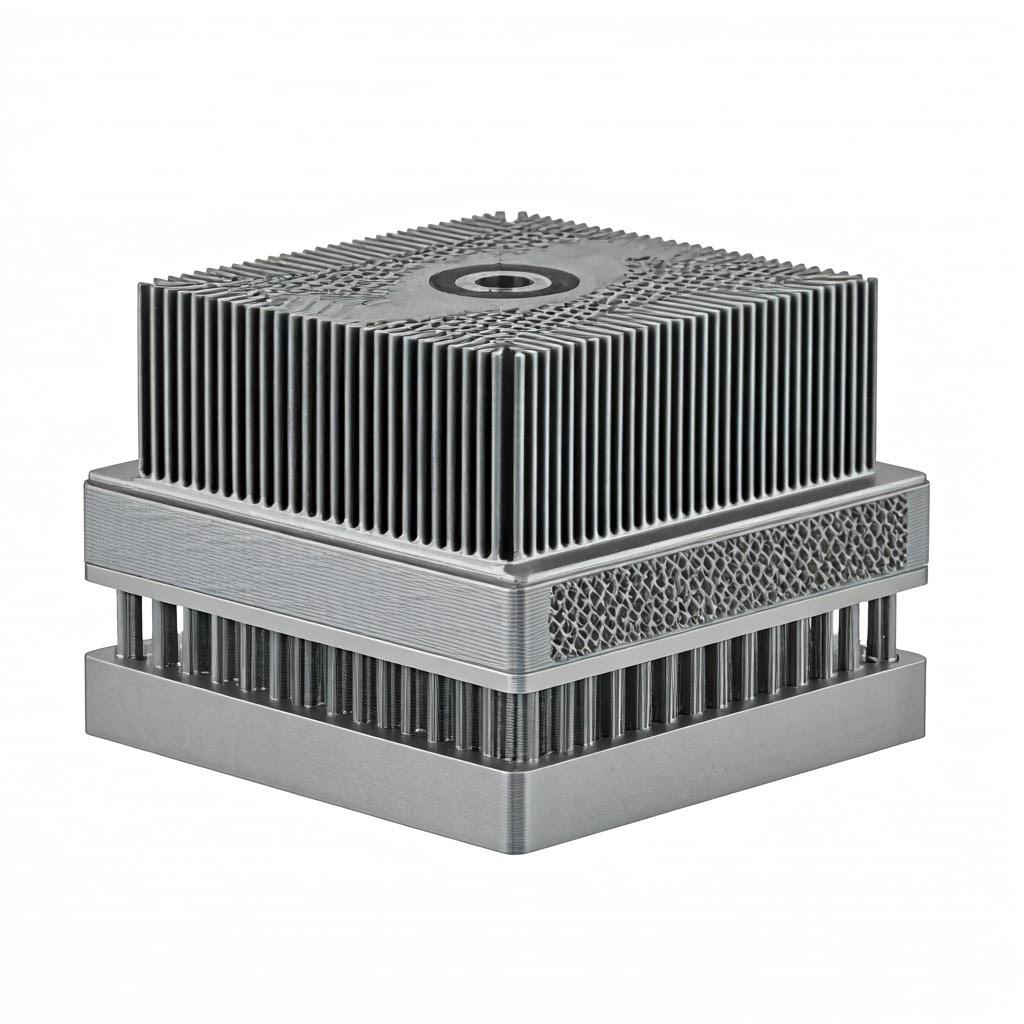
Preguntas frecuentes sobre disipadores de calor personalizados impresos en 3D
A medida que se consolida la fabricación aditiva de metales para producir componentes funcionales como disipadores térmicos, los ingenieros, diseñadores y especialistas en compras suelen plantearse preguntas específicas. He aquí las respuestas a algunas de las preguntas más frecuentes:
P1: ¿Cómo se compara el rendimiento térmico de un disipador de calor impreso en 3D con uno mecanizado del mismo ¿diseño y material?
A: Suponiendo que la pieza impresa en 3D alcance la densidad total (normalmente el 99,5%, a menudo alcanzable con un control adecuado del proceso y potencialmente HIP para casos críticos) y se someta a un tratamiento térmico adecuado para optimizar la conductividad térmica, su rendimiento debería ser muy similar al de su homóloga mecanizada de exactamente la misma geometría. Sin embargo, la principal ventaja de la AM no consiste únicamente en reproducir diseños tradicionales, sino en permitir optimizado geométricamente diseños (utilizando celosías, canales complejos, optimización de la topología) que significativamente superan a diseños tradicionales limitados por la fabricabilidad. Así, mientras que un simple disipador de calor de aletas en bloque podría tener un rendimiento similar tanto si se imprime como si se mecaniza, un rendimiento del disipador de calor impreso en 3D brilla cuando se utilizan diseños específicos de AM para maximizar la superficie, mejorar las vías de flujo o adaptarse perfectamente a las fuentes de calor.
P2: ¿Cuál es el coste habitual de un prototipo de disipador de calor metálico impreso en 3D?
A: Resulta difícil ofrecer una horquilla de costes única, ya que depende en gran medida de varios factores específicos de cada proyecto. Las variables clave son:
- Tamaño & Volumen: Las piezas más grandes consumen más material y tiempo de máquina.
- Material: El CuCrZr es bastante más caro que el AlSi10Mg.
- Complejidad: Aunque la AM maneja bien la complejidad, las características muy intrincadas o las grandes necesidades de soporte pueden aumentar el trabajo de postprocesado.
- Post-procesamiento: Los pasos necesarios, como el mecanizado, el pulido o los revestimientos específicos, añaden costes.
- Cantidad: Un solo prototipo tendrá un coste por pieza más elevado que un lote pequeño en el que se amortizan los costes de preparación. En general, el coste de un prototipo puede oscilar entre varios cientos y varios miles de dólares (USD o equivalente). Lo mejor es enviar siempre un modelo CAD 3D (por ejemplo, un archivo STEP) y los requisitos detallados a un proveedor como Met3dp para obtener un presupuesto preciso y específico del proyecto. Este comparación de costes AM vs tradicional a menudo favorece la AM para prototipos complejos debido a que evita el mecanizado.
P3: ¿Qué información debo proporcionar para obtener un presupuesto exacto de un disipador de calor impreso en 3D?
A: Para garantizar un presupuesto exacto y puntual, facilite la siguiente información:
- Archivo CAD 3D: Un modelo 3D de alta calidad en un formato estándar (preferiblemente STEP; STL también es habitual, pero carece de algunos metadatos).
- Especificación del material: Indique claramente la aleación deseada (por ejemplo, AlSi10Mg, CuCrZr) o los requisitos de rendimiento.
- Cantidad requerida: Número de piezas necesarias (para prototipo o tirada de producción).
- Tolerancias críticas & Características: Indique las dimensiones o superficies con requisitos de tolerancia específicos más estrictos que las capacidades estándar de AM (±0,1-0,2 mm). Indique las superficies que necesitan valores específicos de rugosidad (Ra).
- Requisitos de postprocesamiento: Especifique los tratamientos térmicos necesarios (p. ej., T6 para AlSi10Mg), los acabados superficiales (p. ej., granallado, anodizado, pulido de la superficie de contacto), las necesidades de mecanizado (p. ej., orificios roscados) y las pruebas o certificaciones necesarias.
- Contexto de la aplicación (opcional, pero útil): Describir brevemente la aplicación puede ayudar al proveedor a ofrecer sugerencias de DfAM o confirmar la idoneidad del material.
P4: ¿Se pueden imprimir en 3D disipadores de calor con tubos de calor o cámaras de vapor integrados?
A: La impresión directa en 3D de tubos de calor o cámaras de vapor funcionales y sellados con fluido de trabajo mediante procesos estándar de AM metálica es actualmente muy experimental y, por lo general, no comercialmente viable. Estos dispositivos dependen de estructuras internas específicas (estructuras de mecha) y de la física del cambio de fase, que son difíciles de reproducir monolíticamente con AM. Sin embargo, la AM metálica desempeña un papel crucial en habilitar soluciones térmicas avanzadas incorporando estas tecnologías. Por ejemplo, la AM puede utilizarse para imprimir:
- Complejas carcasas exteriores o condensadores para tubos de calor/cámaras de vapor, que permiten integrarlos sin problemas en espacios reducidos o ajustarlos a fuentes de calor.
- Disipadores de calor con canales internos diseñados con precisión en los que se pueden insertar y unir tubos de calor en miniatura durante el montaje.
- Colectores y estructuras para sistemas avanzados de refrigeración líquida o bifásica. AM permite la recinto y integración aspectos de estas tecnologías térmicas avanzadas se puedan personalizar y optimizar de formas antes imposibles.
P5: ¿Cuáles son las cantidades mínimas de pedido (MOQ) habituales para las series de producción de disipadores térmicos impresos en 3D?
A: Una de las principales ventajas de la fabricación aditiva es su flexibilidad en cuanto al tamaño de los lotes. A diferencia de los métodos tradicionales, que requieren costosos utillajes (como matrices de extrusión o moldes de fundición), la AM prácticamente no tiene costes de utillaje. Esto significa que cantidad mínima de pedido AM suelen ser muy bajos o inexistentes. Es económicamente viable imprimir prototipos individuales, pequeños lotes de decenas o cientos, o incluso miles de piezas. El coste por pieza suele disminuir con lotes más grandes debido a una mejor utilización de la máquina (anidamiento) y a la amortización de los costes de configuración/programación. Esto hace que la AM sea ideal para soluciones B2B personalizadas, aplicaciones nicho e industrias que requieren una producción de alta mezcla y bajo volumen. Comente sus previsiones de volumen con su socio de AM para optimizar la planificación de la producción y la fijación de precios.
Conclusiones: El futuro de la refrigeración electrónica pasa por la personalización y la fabricación aditiva
La incesante marcha hacia una electrónica más pequeña, más potente y más integrada plantea retos de gestión térmica que ponen cada vez más al límite los métodos de fabricación tradicionales. Como ya hemos analizado, la fabricación aditiva de metales ofrece una potente alternativa que permite un cambio de paradigma en la forma de diseñar y producir disipadores de calor personalizados y otros componentes térmicos críticos. La capacidad de crear geometrías muy complejas, aprovechar la optimización topológica para aligerar peso y mejorar el rendimiento, integrar características y utilizar materiales avanzados como AlSi10Mg y CuCrZr proporciona a los ingenieros herramientas sin precedentes para resolver los exigentes problemas de refrigeración en los sectores aeroespacial, automovilístico, médico, informático e industrial.
En ventajas de los disipadores de calor AM son claras:
- Libertad de diseño sin igual: Geometrías optimizadas para el rendimiento térmico, no sólo para la fabricación.
- Rendimiento mejorado: Gracias a características como estructuras reticulares, conjuntos de aletas optimizados y canales de refrigeración conformados.
- Aligeramiento: Crítico para aplicaciones donde la masa es una penalización.
- Consolidación de piezas: Reducción de la complejidad del montaje y de los posibles puntos de fallo.
- Personalización y velocidad: Ideal para soluciones a medida, creación rápida de prototipos y producción bajo demanda sin limitaciones de utillaje.
Sin embargo, para obtener estas ventajas no basta con tener acceso a una impresora. Exige un enfoque holístico que abarque el diseño para la fabricación aditiva (DfAM), una cuidadosa selección de materiales, un meticuloso control del proceso, un postprocesado exhaustivo y una rigurosa garantía de calidad. Superar retos como la tensión residual, la eliminación de soportes y la porosidad requiere experiencia y buenas prácticas.
Elegir al socio adecuado es primordial. Met3dp es líder en el suministro de soluciones avanzadas de fabricacióncombinando la tecnología de impresión SEBM y LPBF más avanzada con la producción propia de polvos metálicos especializados de alta calidad y décadas de experiencia colectiva en AM metálica. Nuestro compromiso va más allá de la impresión para ofrecer asistencia integral, desde el asesoramiento en DfAM hasta la validación de la pieza final, garantizando que nuestros clientes reciban componentes funcionales, fiables y de alto rendimiento. Nos consideramos un facilitador clave de refrigeración de última generación tecnologías.
El camino hacia una gestión térmica optimizada pasa cada vez más por la fabricación aditiva. Tanto si se está desarrollando electrónica de alta densidad de potencia, buscando soluciones ligeras para la industria aeroespacial o diseñando dispositivos médicos compactos, la AM metálica ofrece posibilidades que antes eran inalcanzables. El sitio futura gestión térmica sin duda, la capacidad de crear componentes altamente personalizados y de alto rendimiento bajo demanda determinará el panorama actual.
Le invitamos a explorar cómo un Asociación Met3dp puede elevar su estrategia de gestión térmica. Si se enfrenta a retos de refrigeración complejos o desea investigar el potencial de la impresión 3D componentes electrónicos personalizados para sus aplicaciones, póngase en contacto con Met3dp hoy mismo. Visite nuestro sitio web principal en https://met3dp.com/ para obtener más información sobre nuestras capacidades o póngase en contacto con nuestro equipo de expertos para hablar de los requisitos específicos de su proyecto. Permítanos ayudarle a descubrir el futuro de la refrigeración electrónica: personalizada, optimizada y fabricada de forma aditiva.
Compartir
MET3DP Technology Co., LTD es un proveedor líder de soluciones de fabricación aditiva con sede en Qingdao, China. Nuestra empresa está especializada en equipos de impresión 3D y polvos metálicos de alto rendimiento para aplicaciones industriales.
Solicite información para obtener el mejor precio y una solución personalizada para su empresa.
Artículos relacionados
Acerca de Met3DP
Actualización reciente
Nuestro producto
CONTACTO
¿Tiene alguna pregunta? ¡Envíenos un mensaje ahora! Atenderemos su solicitud con todo un equipo tras recibir su mensaje.
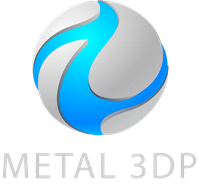
Polvos metálicos para impresión 3D y fabricación aditiva