Disipadores térmicos de alta conductividad mediante impresión 3D basada en cobre
Índice
Introducción: El papel crítico de la gestión térmica en la electrónica de alta densidad
En la incesante búsqueda de avances tecnológicos, los dispositivos electrónicos de todos los sectores son cada vez más pequeños, rápidos y potentes. Desde la compleja aviónica que guía los aviones hasta los potentes procesadores de los centros de datos, y desde los sofisticados sistemas de los vehículos eléctricos hasta los equipos médicos que salvan vidas, la tendencia es universal: mayor densidad funcional. Sin embargo, este progreso conlleva un importante reto de ingeniería: gestionar el considerable calor que se genera en estos espacios compactos. Una gestión térmica inadecuada ya no es sólo un obstáculo para el rendimiento; es un factor crítico que afecta a la fiabilidad, la longevidad e incluso la seguridad. Un calor excesivo puede provocar la degradación de los componentes, problemas de integridad de la señal, fallos prematuros y, en casos extremos, una avería catastrófica del sistema. Para los responsables de adquisiciones y los ingenieros de diseño, la búsqueda de soluciones eficaces de gestión térmica es primordial para garantizar la viabilidad del producto y la competitividad en el mercado.
¿Qué son los disipadores térmicos y por qué son esenciales?
En esencia, un disipador térmico es un intercambiador de calor pasivo diseñado para absorber el calor generado por un dispositivo electrónico o mecánico y disiparlo en un medio fluido circundante, normalmente aire o un refrigerante líquido. El principio fundamental se basa en aumentar la superficie disponible para la transferencia de calor y optimizar el recorrido térmico desde la fuente de calor hasta el refrigerante. Los disipadores tradicionales, a menudo fabricados en aluminio o cobre mediante procesos como la extrusión, la fundición, el mecanizado o el rebajado, han prestado un buen servicio a la industria durante décadas. Son rentables para geometrías estándar y grandes volúmenes de producción.
Las limitaciones de la fabricación tradicional
Sin embargo, a medida que se disparan las densidades de potencia y se reducen los factores de forma, los métodos de fabricación convencionales se topan cada vez más con un muro. Pensemos en estas limitaciones:
- Restricciones geométricas: La extrusión limita los diseños a formas 2,5D con secciones transversales constantes. El mecanizado, aunque versátil, resulta increíblemente complejo y caro en el caso de características complejas como conjuntos densos de aletas o canales internos complejos, sobre todo con materiales como el cobre puro, que es muy difícil de mecanizar debido a su blandura y gomosidad. La fundición puede crear formas complejas, pero a menudo da como resultado materiales de menor conductividad térmica o requiere un importante mecanizado posterior. El raspado es eficaz para aletas finas, pero su complejidad geométrica global es limitada.
- Techos de alto rendimiento: Estas limitaciones de fabricación a menudo conducen a diseños subóptimos que no pueden proporcionar la refrigeración necesaria para los componentes de vanguardia. Los ingenieros se ven obligados a comprometer el rendimiento o el tamaño de los dispositivos para mantenerse dentro de los límites térmicos.
- Retos de la integración: Los métodos tradicionales dificultan y encarecen la creación de disipadores que se ajusten con precisión a superficies no planas de los componentes o se integren a la perfección en conjuntos complejos.
- Obstáculos para la creación de prototipos: Iterar los diseños tradicionales de disipadores térmicos implica cambios de herramientas costosos y lentos o complejas configuraciones de mecanizado, lo que dificulta los ciclos rápidos de innovación.
Fabricación aditiva de metales: Una solución transformadora
Aquí es donde la fabricación aditiva de metales (AM), a menudo denominada metal Impresión 3Dse perfila como una tecnología revolucionaria. Al construir piezas capa por capa directamente a partir de modelos digitales utilizando polvos metálicos de alto rendimiento, la AM supera muchas limitaciones de la fabricación tradicional. Específicamente para la gestión térmica, tecnologías como la Fusión de Lecho de Polvo Láser (LPBF) permiten crear disipadores con una complejidad geométrica sin precedentes y un rendimiento térmico optimizado. Utilizando materiales como el cobre puro (Cu) y aleaciones de cobre de alta conductividad como el cobre-cromo-circonio (CuCrZr), la AM permite a los ingenieros diseñar y producir disipadores que antes eran imposibles de fabricar.
Esta capacidad está revolucionando las estrategias de gestión térmica en los exigentes sectores B2B. Empresas como Met3dpGracias a su amplia experiencia en procesos de AM metálica y en la producción de polvos metálicos de alta calidad, están a la vanguardia de esta transformación, proporcionando las herramientas y los materiales necesarios para liberar todo el potencial de las soluciones térmicas impresas en 3D. Para las empresas que buscan una ventaja competitiva a través de un rendimiento y una fiabilidad superiores del producto, cada vez es más importante comprender y aprovechar la AM basada en cobre para los disipadores térmicos.
¿Para qué se utilizan los disipadores térmicos de cobre impresos en 3D? Aplicaciones e industrias clave
Las capacidades únicas de la fabricación aditiva de metales, en particular con aleaciones de cobre de alta conductividad, desbloquean niveles de rendimiento y posibilidades de diseño esenciales para una gama cada vez mayor de aplicaciones exigentes. Los disipadores térmicos impresos en 3D a base de cobre no son meras mejoras incrementales; son tecnologías habilitadoras para sistemas de próxima generación en múltiples mercados B2B. Su función principal sigue siendo la transferencia y disipación eficientes del calor, pero la AM permite que esta función se realice con una eficacia significativamente mayor y en entornos o factores de forma más difíciles.
Industrias destinatarias y casos de uso específicos:
- Aeroespacial y defensa:
- Aplicaciones: Refrigeración de componentes de radar de alta potencia (módulos T/R), procesadores de aviónica, sistemas de guerra electrónica, sistemas de puntería láser, fuentes de alimentación en espacios reducidos.
- Ventajas: Alta fiabilidad en entornos difíciles (vibraciones, temperaturas extremas), reducción del peso mediante la optimización de la topología, refrigeración conforme para componentes electrónicos densamente empaquetados, cumplimiento de estrictos requisitos de rendimiento. Los proveedores B2B de este sector valoran la trazabilidad y la garantía de calidad que ofrece la AM.
- Automoción (especialmente vehículos eléctricos):
- Aplicaciones: Refrigeración de módulos de potencia SiC/GaN en inversores y cargadores de a bordo, sistemas de gestión térmica de baterías, ECU de alto rendimiento, procesadores de sistemas avanzados de asistencia al conductor (ADAS), iluminación LED de alta potencia.
- Ventajas: Aumento de la densidad de potencia para una mayor autonomía y una carga más rápida en los vehículos eléctricos, mejora de la fiabilidad de la electrónica de potencia crítica, diseños compactos que se adaptan al espacio limitado del vehículo, soluciones personalizadas para modelos de alto rendimiento. Los responsables de compras de automoción buscan soluciones sólidas y rentables a gran escala, en las que las ventajas de diseño de la AM puedan justificar los costes de los componentes críticos.
- Computación de alto rendimiento (HPC) y centros de datos:
- Aplicaciones: Refrigeración directa de chips (CPU, GPU, aceleradores de IA), soluciones de refrigeración de bastidores de servidores, placas frías de refrigeración líquida con complejos microcanales internos, componentes de conmutación de redes.
- Ventajas: Maximización de la potencia de procesamiento mediante la prevención del estrangulamiento térmico, el aumento de la densidad de rack, la mejora de la eficiencia energética (PUE), permitiendo soluciones de refrigeración líquida con un rendimiento superior en comparación con las placas frías mecanizadas. Los operadores de centros de datos y los constructores de HPC requieren el máximo rendimiento y fiabilidad, por lo que las soluciones térmicas avanzadas son una inversión clave.
- Productos sanitarios:
- Aplicaciones: Componentes de refrigeración en bobinas de gradiente de resonancia magnética, tubos de rayos X, sistemas de diagnóstico por imagen, láseres terapéuticos de alta potencia, electrónica de robótica quirúrgica.
- Ventajas: Garantizar la seguridad de los pacientes y la eficacia de los dispositivos mediante un control preciso de la temperatura, posibilitar la miniaturización de dispositivos portátiles o implantables, crear soluciones de refrigeración biocompatibles (si son necesarias y están debidamente postprocesadas/revestidas) y un funcionamiento silencioso (refrigeración pasiva). Los fabricantes de dispositivos médicos requieren una fiabilidad extrema y a menudo diseños personalizados, áreas en las que destaca la AM. Los proveedores mayoristas necesitan una calidad constante.
- Sistemas de energía industrial y fabricación:
- Aplicaciones: Convertidores de potencia de refrigeración, variadores de frecuencia (VFD), fuentes de alimentación de equipos de soldadura, controles de automatización industrial, diodos láser de alta potencia utilizados en fabricación.
- Ventajas: Aumentar la fiabilidad y la vida útil de los equipos industriales críticos que funcionan en condiciones exigentes, mejorando la eficiencia energética, reduciendo la huella de los equipos y permitiendo un mayor rendimiento energético. El aprovisionamiento industrial se centra en la durabilidad, el tiempo de actividad y el coste total de propiedad, donde la mejora de la gestión térmica desempeña un papel crucial.
- Telecomunicaciones:
- Aplicaciones: Gestión térmica para amplificadores de alta potencia en estaciones base 5G (gNodeB), refrigeración de transceptores ópticos, gestión del calor en equipos de red densamente empaquetados.
- Ventajas: Garantizar la integridad de la señal y la fiabilidad de la red, permitir mayores velocidades de transmisión de datos gracias a componentes más potentes, hacer frente a las condiciones ambientales exteriores, facilitar diseños de estaciones base más pequeños y estéticamente más aceptables. Los proveedores de telecomunicaciones necesitan una refrigeración fiable y eficiente para los despliegues generalizados.
En esencia, los disipadores térmicos impresos en 3D a base de cobre se emplean allí donde convergen cargas térmicas elevadas, espacios compactos, geometrías complejas o la necesidad de un rendimiento térmico máximo. Van más allá de la simple disipación de calor para convertirse en componentes integrales y de alto rendimiento dentro de sistemas sofisticados. Para los clientes B2B, el valor radica en la consecución de métricas de rendimiento, objetivos de fiabilidad e integraciones de diseño inalcanzables con los métodos convencionales de fabricación de disipadores.
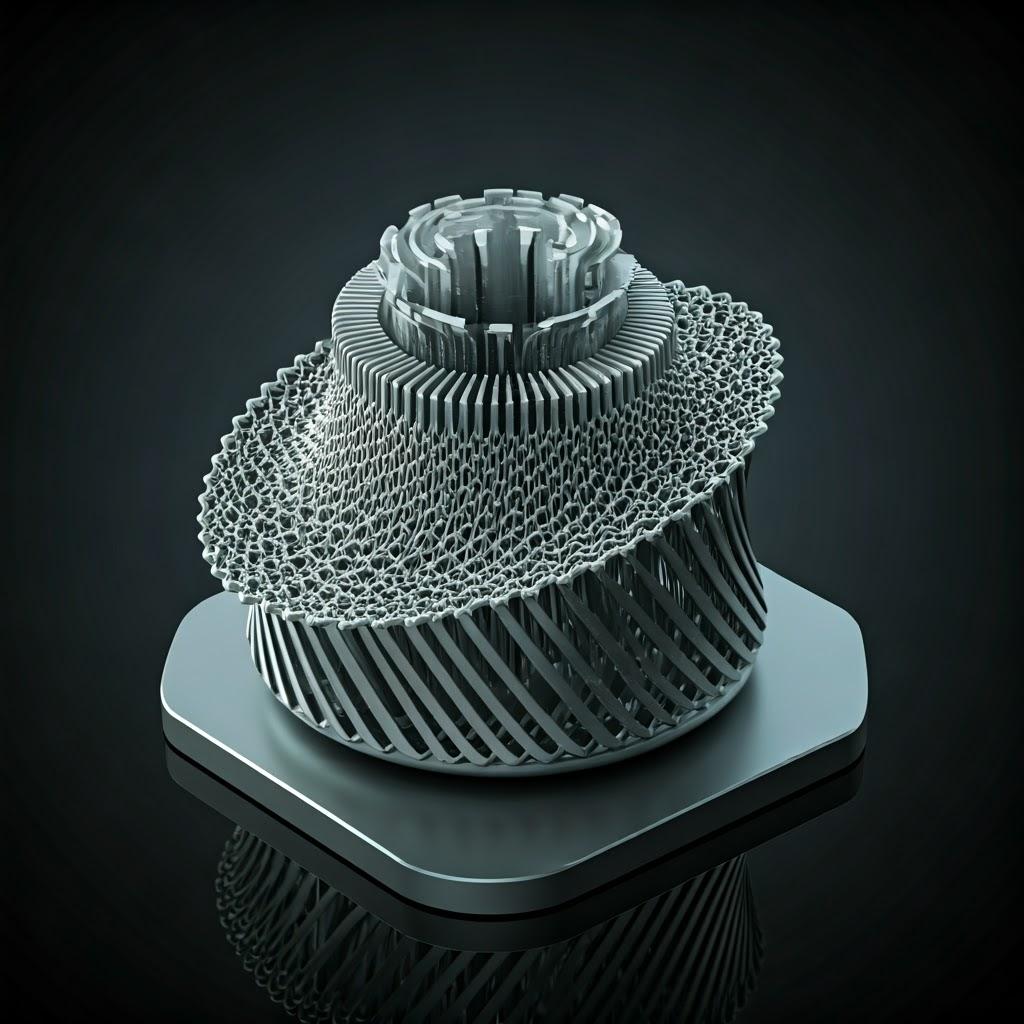
¿Por qué utilizar la impresión metálica en 3D para disipadores de alta conductividad? Ventajas sobre los métodos tradicionales
Optar por la fabricación aditiva de metales, concretamente utilizando cobre o sus aleaciones de alta conductividad, supone un cambio de paradigma en el diseño y la producción de disipadores térmicos. No se trata simplemente de un método de producción alternativo, sino de un medio para obtener un rendimiento superior y un diseño innovador. Para los ingenieros que se esfuerzan por encontrar soluciones térmicas óptimas y los responsables de compras que buscan componentes fiables y de alto valor, es fundamental comprender las ventajas de la AM.
- Libertad geométrica y complejidad sin precedentes: Esta es sin duda la ventaja más significativa de la AM.
- Canales internos intrincados: La AM permite crear canales internos complejos y tortuosos, aletas con micropines y estructuras reticulares (como Gyroids o TPMS - Triply Periodic Minimal Surfaces) dentro del volumen del disipador. Estas características aumentan drásticamente la superficie de transferencia de calor y pueden inducir un flujo turbulento en aplicaciones de refrigeración líquida, maximizando la eficiencia del intercambio de calor de formas imposibles con taladrado o fundición.
- Optimización de la topología: El software puede utilizarse para determinar computacionalmente la distribución de material más eficiente para la transferencia de calor y la integridad estructural. A continuación, la AM puede producir directamente estas formas ligeras y altamente orgánicas, colocando el material sólo donde más se necesita. Esto es ideal para aplicaciones sensibles al peso, como la aeroespacial o la automoción de alto rendimiento.
- Consolidación de piezas: Los disipadores térmicos pueden diseñarse e imprimirse como partes integrantes de componentes más grandes, como carcasas electrónicas, soportes o colectores de fluidos. Esto reduce la complejidad del montaje, elimina posibles puntos de resistencia térmica (interfaces), minimiza el número de piezas y simplifica la cadena de suministro.
- Refrigeración conforme: Los disipadores pueden diseñarse para adaptarse perfectamente a la topología del componente generador de calor (por ejemplo, una superficie curva del procesador). Esto minimiza la resistencia de la interfaz y garantiza una extracción del calor más uniforme y eficaz que con disipadores planos que hacen contacto parcialmente. Los métodos tradicionales tienen enormes dificultades para crear superficies verdaderamente conformadas de forma rentable.
- Rendimiento térmico mejorado: La libertad geométrica se traduce directamente en una mayor capacidad de refrigeración.
- Superficie maximizada: Las estructuras internas complejas y los diseños optimizados de las aletas externas aumentan significativamente la relación superficie-volumen en comparación con las aletas extruidas o esquirladas simples.
- Vías de flujo optimizadas: En el caso de la refrigeración por líquido, los canales internos pueden diseñarse para minimizar la caída de presión y maximizar la transferencia de calor, guiando con precisión el refrigerante por las zonas más calientes. Para la refrigeración por aire, los diseños de las aletas pueden optimizarse para condiciones específicas de flujo de aire.
- Resistencia térmica reducida: Al permitir el contacto conformado y optimizar las trayectorias térmicas mediante la optimización de la topología, la AM puede minimizar la resistencia térmica global desde la fuente de calor hasta el entorno ambiental.
- Prototipado rápido e iteración del diseño: La AM acelera considerablemente el ciclo de innovación.
- Eliminación de herramientas: A diferencia de la fundición o la extrusión, la AM no requiere utillaje específico. Los diseños pueden pasar directamente del CAD a la pieza física.
- Entrega rápida: A menudo, los prototipos pueden fabricarse en días en lugar de semanas o meses. Esto permite a los ingenieros probar múltiples variaciones de diseño de forma rápida y asequible, convergiendo en una solución óptima mucho más rápido.
- Bajos volúmenes rentables: La AM es económicamente viable para producir disipadores a medida o en lotes de volumen bajo o medio, como suele ser el caso de las aplicaciones industriales, médicas o aeroespaciales especializadas. Los clientes B2B que necesitan soluciones únicas se benefician enormemente.
- Utilización eficaz de materiales de alto rendimiento:
- Impresión de materiales difíciles: Aunque el cobre puro ofrece la mayor conductividad térmica, su alta reflectividad a los láseres infrarrojos y su tendencia a oxidarse lo convierten en un reto para los sistemas LPBF tradicionales. Sin embargo, los avances en la tecnología de AM (por ejemplo, láseres verdes, parámetros optimizados) y la ciencia de los materiales (por ejemplo, aleaciones CuCrZr) han hecho que la AM basada en cobre sea cada vez más factible y eficaz. Met3dp, por ejemplo, se centra en la producción de polvos optimizados específicamente para los procesos de AM, mejorando la capacidad de impresión.
- Propiedades del material: La AM puede producir piezas de cobre densas (densidad >99,5%) que conservan la excelente conductividad térmica del material base, mientras que aleaciones como CuCrZr ofrecen un equilibrio convincente de rendimiento térmico y una resistencia mecánica significativamente mejorada adecuada para entornos exigentes.
- Flexibilidad de la cadena de suministro y producción bajo demanda:
- Inventario digital: Los diseños se almacenan digitalmente, lo que permite imprimir piezas en cualquier lugar con el equipo y los materiales adecuados, potencialmente más cerca del punto de necesidad.
- Inventario reducido: La producción bajo demanda minimiza la necesidad de grandes inventarios físicos de diversos diseños de disipadores.
- Personalización a escala: La AM permite la personalización en masa, con lo que se pueden fabricar disipadores únicos adaptados a las necesidades específicas del cliente sin las tradicionales penalizaciones de costes asociadas a la personalización.
En resumen, la AM metálica permite a los ingenieros diseñar disipadores basados en un rendimiento térmico óptimo en lugar de estar condicionados por las limitaciones de fabricación. Para los profesionales de las compras, esto se traduce en el suministro de componentes que ofrecen un valor superior a través de la mejora del rendimiento del producto, la fiabilidad y los procesos de montaje potencialmente simplificados, incluso si el coste por pieza puede ser más alto que un disipador de calor simple y tradicional para aplicaciones no exigentes.
Materiales recomendados: Cobre puro (Cu) y CuCrZr para un rendimiento térmico óptimo
La elección del material es fundamental para el rendimiento de cualquier disipador térmico. Para las aplicaciones que exigen los niveles más altos de disipación de calor, el cobre y sus aleaciones son las principales opciones debido a su excepcional conductividad térmica. La fabricación aditiva abre la puerta a la utilización eficaz de estos materiales en geometrías complejas, pero la selección del derecha El polvo a base de cobre es crucial para el éxito. Los dos principales candidatos para disipadores térmicos de alto rendimiento impresos en 3D son el cobre puro (Cu) y el cobre-cromo-circonio (CuCrZr).
Introducción a los polvos de cobre en AM
La propiedad más destacada del cobre es su conductividad térmica, sólo superada por la de la plata. Esto lo hace ideal para transferir calor rápidamente. Sin embargo, el cobre puro presenta dificultades en los sistemas habituales de fusión por lecho de polvo láser (LPBF):
- Alta reflectividad: El cobre refleja fuertemente las longitudes de onda infrarrojas (IR) utilizadas por muchos láseres LPBF estándar, lo que significa que el polvo absorbe menos energía, dificultando la fusión y requiriendo una mayor potencia láser o tipos de láser especializados (como los láseres verdes, que tienen una mejor absorción).
- Alta conductividad térmica (¡también un reto!): La misma propiedad que lo hace deseable también hace que el calor se disipe rápidamente del baño de fusión, lo que dificulta el mantenimiento de unas condiciones de fusión estables y puede provocar una fusión incompleta o porosidad.
- Oxidación: El cobre se oxida fácilmente, por lo que requiere un excelente control atmosférico (gas inerte como el argón) durante la impresión para evitar la captación de oxígeno, que degrada las propiedades.
A pesar de estos retos, los avances en la tecnología de las máquinas y la optimización de los parámetros del proceso, junto con los polvos de alta calidad, han hecho viable la impresión de cobre puro. Las aleaciones de cobre, como CuCrZr, se desarrollaron en parte para mejorar la capacidad de impresión sin perder sus excelentes propiedades térmicas.
Enfoque del material: Cobre puro (Cu)
A menudo designado como C10100 o CW004A (OF-Cu: cobre sin oxígeno), el cobre puro ofrece el máximo potencial térmico.
- Propiedades:
- Pros: Insuperable conductividad térmica (~390-400 W/m-K), excelente conductividad eléctrica.
- Contras: Difícil y más lento de imprimir de forma fiable mediante LPBF en comparación con las aleaciones, menor resistencia mecánica y dureza, susceptible de reblandecimiento a temperaturas elevadas, mayor coste de material dificultad de procesamiento.
- Imprimibilidad: Requiere máquinas LPBF optimizadas (a menudo con láseres de mayor potencia o verdes) y parámetros bien ajustados. Susceptible a defectos como la porosidad si no se procesa correctamente.
- Los mejores casos de uso: Aplicaciones en las que lograr la menor resistencia térmica posible es el objetivo principal absoluto, y en las que las cargas mecánicas o las elevadas temperaturas de funcionamiento (>200 °C) no son preocupaciones significativas. Algunos ejemplos son las placas frías de computación de rendimiento extremo o la refrigeración de instrumentación científica especializada.
Material Focus: Cobre-Cromo-Zirconio (CuCrZr)
Esta aleación endurecible por precipitación (a menudo UNS C18150 o CW106C) ofrece una convincente combinación de propiedades que la hacen muy atractiva para muchas aplicaciones exigentes de disipadores térmicos. Las pequeñas adiciones de cromo (Cr) y circonio (Zr) alteran significativamente sus características en comparación con el cobre puro.
- Propiedades:
- Pros: Conductividad térmica muy elevada (normalmente ~300-340 W/m-K, aproximadamente 80-85% del Cu puro), resistencia a la tracción, límite elástico y dureza significativamente superiores (especialmente tras el tratamiento térmico), buena resistencia al reblandecimiento a temperaturas moderadamente elevadas (hasta ~450-500°C), imprimibilidad mucho mejor en sistemas LPBF en comparación con el Cu puro, buena resistencia al desgaste.
- Contras: La conductividad térmica es inferior a la del cobre puro, requiere un tratamiento térmico posterior a la impresión (disolución y envejecimiento) para conseguir unas propiedades mecánicas óptimas.
- Los mejores casos de uso: Una elección versátil para aplicaciones que requieren tanto una alta disipación de calor como una buena robustez mecánica. Ideal para componentes aeroespaciales, electrónica de potencia de automoción (inversores, convertidores), equipos industriales, componentes orientados al plasma en la investigación de la fusión y cualquier disipador térmico que sufra vibraciones, tensiones de montaje o temperaturas de funcionamiento moderadas.
Panorama comparativo:
Propiedad | Cobre puro (OF-Cu, según estimación) | CuCrZr (C18150, tratado térmicamente) | Unidades | Notas |
---|---|---|---|---|
Conductividad térmica | ~390 – 400 | ~300 – 340 | W/(m-K) | Diferenciador principal. CuCrZr sigue siendo excelente. |
Conductividad eléctrica | ~100% IACS | ~80-85% IACS | % IACS | Ambos son altamente conductores de la electricidad. |
Límite elástico (0,2%) | ~70 – 100 | ~350 – 450 | MPa | Aumento significativo de la resistencia en CuCrZr tras el tratamiento térmico. |
Resistencia a la tracción | ~200 – 250 | ~450 – 550 | MPa | El CuCrZr es mucho más resistente y duradero. |
Dureza | ~40 - 50 HV | ~140 - 170 HV | alto voltaje | CuCrZr ofrece una resistencia al desgaste mucho mayor. |
Temperatura máxima de funcionamiento | < 200°C (Ablandamiento significativo por encima) | ~450 - 500°C | °C | El CuCrZr conserva su resistencia a temperaturas más elevadas. |
Imprimibilidad LPBF | Desafío | Bien | – | La optimización de los parámetros es clave para ambos, pero más fácil para CuCrZr. |
Req. postproceso | Alivio del estrés (recomendado) | Solución y Edad Harden (Obligatorio) | – | El tratamiento térmico es esencial para las propiedades mecánicas del CuCrZr. |
Exportar a hojas
La importancia de la calidad del polvo: La contribución de Met3dp
El éxito de la impresión de disipadores térmicos de cobre de alto rendimiento depende en gran medida de la calidad del polvo metálico de partida. Las características del polvo, como la distribución del tamaño de las partículas (PSD), la morfología (esfericidad), la fluidez y la pureza (especialmente el bajo contenido de oxígeno) influyen directamente en la densidad, las propiedades finales y la consistencia de la pieza impresa.
Met3dp se especializa en la producción de polvos metálicos de alto rendimiento adaptados a la fabricación aditiva. Utilizando tecnologías líderes en la industria como Atomización de gas de fusión por inducción al vacío (VIGA) y el Proceso de electrodos rotativos de plasma (PREP)Met3dp fabrica polvos de Cu y CuCrZr con:
- Esfericidad alta: Garantiza una excelente fluidez del polvo y una alta densidad de empaquetamiento en el lecho de polvo, lo que da lugar a piezas más densas y uniformes.
- Distribución optimizada del tamaño de las partículas: PSD adaptados a procesos específicos de AM (como LPBF) para garantizar un buen comportamiento de fusión y extensión de capas.
- Bajo contenido de oxígeno y alta pureza: Minimiza la oxidación durante la impresión y garantiza que la pieza final alcance las propiedades intrínsecas deseadas del material (térmicas y mecánicas).
- Coherencia entre lotes: Crucial para una producción fiable, especialmente para aplicaciones certificadas en los campos aeroespacial o médico.
Gracias a sus avanzadas técnicas de fabricación de polvos, Met3dp proporciona las materias primas de alta calidad esenciales para imprimir con éxito componentes exigentes como disipadores de cobre de alta conductividad. Su experiencia va más allá de los polvos y abarca todo el ecosistema de la AM, incluidos los equipos de impresión líderes del sector, conocidos por su precisión y fiabilidad. Para las empresas que buscan la AM de cobre, asociarse con un proveedor experto tanto en materiales como en máquinas, como Met3dp, es una ventaja significativa. Puede obtener más información sobre su completa oferta, incluida su gama de polvos metálicos de alto rendimiento, explorando su página web producto cartera.
Criterios de selección de materiales:
La elección entre Cu puro y CuCrZr implica un análisis de compromiso:
- ¿Priorizar la conductividad térmica máxima absoluta? Elija Pure Cu (si el proveedor de AM puede gestionar los problemas de imprimibilidad).
- ¿Necesita alta resistencia, dureza o temperaturas de funcionamiento más elevadas? Elija CuCrZr.
- ¿Busca una mejor imprimibilidad y fiabilidad del proceso? Generalmente se prefiere CuCrZr.
- ¿Es viable el tratamiento térmico posterior a la impresión? Necesario para que el CuCrZr alcance sus propiedades máximas.
- ¿Sensibilidad a los costes? Ambos son materiales de primera calidad, pero las dificultades de procesamiento del Cu puro pueden influir en el coste total. Consulte con su proveedor de servicios AM.
Al considerar cuidadosamente los requisitos de la aplicación y comprender las propiedades y los matices de procesamiento de estos materiales, los ingenieros y los responsables de compras pueden seleccionar el polvo con base de cobre óptimo para sus necesidades de disipadores térmicos impresos en 3D, aprovechando las capacidades transformadoras de la fabricación aditiva.

Consideraciones de diseño para la fabricación aditiva (DfAM) de disipadores térmicos
Aprovechar con éxito la fabricación aditiva basada en cobre para disipadores de alto rendimiento requiere algo más que convertir un modelo CAD existente. Exige un cambio fundamental en el pensamiento de diseño, alejándose de las limitaciones de los métodos tradicionales (Diseño para Fabricación - DfM) para abrazar las posibilidades de la AM (Diseño para Fabricación Aditiva - DfAM). Los ingenieros deben diseñar activamente para el proceso capa a capa para liberar todo el potencial de complejidad geométrica y rendimiento térmico.
Principios clave de DfAM para disipadores térmicos impresos en 3D:
- Abrace la libertad geométrica: Esta es la piedra angular de la ventaja de AM.
- Canales internos complejos: Diseñe microcanales (<1 mm de diámetro), redes intrincadas y estructuras ramificadas bioinspiradas para aplicaciones de refrigeración líquida. Considerar formas de canal (por ejemplo, onduladas o retorcidas) que induzcan turbulencias para mejorar la transferencia de calor, imposibles de perforar o moldear. Asegúrese de que los canales tengan un diámetro adecuado y curvas suaves para una eliminación eficaz del polvo tras la impresión.
- Estructuras de aletas optimizadas: Vaya más allá de las simples aletas rectas. Diseñe conjuntos de aletas densas con formas optimizadas (elípticas, aerodinámicas) y espaciado para maximizar la superficie y gestionar el flujo de aire de forma eficiente. Explore estructuras reticulares (por ejemplo, giroscopios, Schwarz-P) dentro del volumen del disipador. Estas superficies mínimas tri-periódicas (TPMS) ofrecen una relación superficie-volumen extremadamente alta y una eficiencia estructural excelente, lo que resulta beneficioso tanto para la refrigeración por aire como por líquido.
- Superficies conformes: Diseñe la base del disipador para que se adapte con precisión al contorno de los componentes curvos o de forma irregular (por ejemplo, módulos de alimentación, procesadores). Así se minimiza la resistencia de la interfaz térmica, uno de los principales cuellos de botella de muchos sistemas.
- Tamaños mínimos y espesores de pared: Todos los procesos AM tienen limitaciones.
- Resolución: Para LPBF, el grosor de pared mínimo imprimible típico para aleaciones de cobre es de unos 0,3-0,5 mm, y los elementos positivos (como los pasadores) pueden necesitar diámetros similares para imprimirse de forma fiable. Los elementos muy finos y altos pueden ser propensos a distorsiones o fallos durante la impresión.
- Contrapartidas: Equilibre el deseo de paredes finas (para reducir el peso y la resistencia térmica) con la necesidad de integridad estructural, imprimibilidad y garantía de una sección transversal suficiente para la conducción del calor. Utilice la simulación térmica para orientar estas decisiones.
- Diseño de estructuras estratégicas de apoyo: Las ayudas suelen ser necesarias, pero añaden costes y complejidad.
- Propósito: Los soportes anclan la pieza a la placa de impresión, evitan el alabeo debido a la tensión térmica y proporcionan una base para los elementos que sobresalen (normalmente superficies con un ángulo inferior a 45∘ respecto a la horizontal).
- Minimización: Oriente la pieza estratégicamente en la placa de construcción para minimizar la extensión de los voladizos. En la medida de lo posible, diseñe elementos autoportantes (por ejemplo, utilice chaflanes en lugar de salientes horizontales pronunciados, diseñe canales internos con forma de lágrima).
- Desmontabilidad: Esto es fundamental, especialmente en el caso de las aleaciones de cobre, que pueden ser más duras que los aceros. Diseñe los soportes de modo que sean accesibles para su retirada manual o con herramientas. En la medida de lo posible, evite colocar soportes en superficies funcionales críticas o prevea el mecanizado posterior. En el caso de los canales internos, la eliminación de los soportes es un reto importante: considere la posibilidad de utilizar estructuras de sacrificio o consulte a su proveedor de servicios de AM sobre estrategias viables. Empresas como Met3dp, con amplios conocimientos del proceso, pueden aportar información valiosa sobre estrategias de orientación y soporte durante la fase de diseño.
- Aproveche la optimización de la topología: Utilice programas informáticos para conseguir un alto rendimiento con el mínimo material.
- Flujo de trabajo: Defina el espacio de diseño, las condiciones de contorno (fuentes de calor, puntos de montaje), los casos de carga (térmica, mecánica) y los objetivos de optimización (por ejemplo, minimizar la resistencia térmica, minimizar la masa). A continuación, el software elimina iterativamente el material de las zonas no críticas.
- Beneficio: El resultado son disipadores ligeros y de forma orgánica, perfectamente adaptados a la aplicación específica, que ofrecen el máximo rendimiento con el mínimo peso y uso de material, lo que resulta ideal para sectores B2B como el aeroespacial y la automoción.
- Integrar la simulación térmica (FEA/CFD): La validación del diseño es crucial antes de pasar a la impresión.
- Predecir el rendimiento: Utilizar la dinámica de fluidos computacional (CFD) para simular el flujo de fluidos (aire o líquido) a través de canales complejos y estructuras de aletas, prediciendo la caída de presión y los coeficientes de transferencia de calor. Utilice el análisis de elementos finitos (FEA) para modelar la conducción de calor a través del cuerpo sólido y predecir las distribuciones de temperatura y las tensiones térmicas.
- Iterar digitalmente: Identifique posibles puntos calientes, zonas de estancamiento del flujo o áreas de gran tensión en las primeras fases del ciclo de diseño. Modificar la geometría basándose en los resultados de la simulación y volver a analizar, optimizando el diseño digitalmente antes de incurrir en costes de impresión. Este enfoque basado en la simulación es esencial para el diseño de disipadores AM complejos.
- Diseño para la integración: Reducir la complejidad general del sistema.
- Características de montaje: Integre los orificios de montaje, los resaltes y las características de alineación directamente en el diseño del disipador térmico, eliminando potencialmente los soportes independientes. Asegúrese de que estos elementos tienen en cuenta las tolerancias de AM o especifique los requisitos de mecanizado posterior.
- Conectores de fluidos: Para la refrigeración líquida, diseñe conexiones de puerto de fluido estándar o personalizadas directamente en el cuerpo del disipador térmico.
- Funcionalidad combinada: Diseñe el disipador para que también forme parte de la carcasa del dispositivo o como elemento estructural, reduciendo el número de piezas y el esfuerzo de montaje.
Aplicando cuidadosamente estos principios de DfAM, los ingenieros pueden ir más allá de la mera réplica de los diseños tradicionales y aprovechar realmente el poder de la AM para crear disipadores de cobre con un rendimiento térmico superior, un peso reducido y una integración mejorada, aportando un valor significativo en los competitivos mercados B2B.
Tolerancia, acabado superficial y precisión dimensional en disipadores AM de cobre
Aunque la fabricación aditiva ofrece una increíble libertad de diseño, los ingenieros y los responsables de compras deben tener expectativas realistas en cuanto a la precisión alcanzable de los disipadores térmicos de cobre y CuCrZr impresos en 3D. Comprender las tolerancias, el acabado superficial y la precisión dimensional general es crucial para garantizar un ajuste y un ensamblaje adecuados, así como un rendimiento térmico óptimo en las exigentes aplicaciones B2B. Estos factores dependen en gran medida del proceso de AM elegido (normalmente LPBF para el cobre), la calibración de la máquina, las propiedades del material, los parámetros de impresión y los pasos posteriores al procesamiento.
Tolerancias alcanzables:
- Tolerancias generales: Las piezas de cobre asimétricas producidas mediante LPBF suelen alcanzar tolerancias dimensionales comprendidas entre ±0,1 mm y ±0,2 mm para las características más pequeñas, o entre ±0,1% y ±0,2% de la dimensión total para las piezas más grandes. Esto suele corresponder a grados de tolerancia como ISO 2768-m (medio) o a veces -f (fino) para determinadas características.
- Factores que influyen:
- Calibración de la máquina: Es fundamental calibrar periódicamente el tamaño del punto láser, la precisión del escáner y la deposición del grosor de capa.
- Efectos térmicos: Las altas temperaturas y el rápido enfriamiento pueden provocar tensiones internas que provoquen pequeñas deformaciones o contracciones, sobre todo en geometrías grandes o complejas. Es esencial una gestión térmica cuidadosa durante la fabricación y unas estrategias de soporte adecuadas.
- Geometría y tamaño de la pieza: Las piezas más grandes o las que tienen vanos importantes sin apoyo son más propensas a la desviación.
- Post-procesamiento: Los tratamientos térmicos de alivio de tensiones pueden provocar a veces ligeros cambios dimensionales. El mecanizado, por supuesto, permite tolerancias mucho más estrictas en características específicas.
- Características críticas: En el caso de las interfaces que requieren un acoplamiento preciso o un sellado hermético, confiar únicamente en las tolerancias de impresión puede no ser suficiente. Es práctica común diseñar estas características con material de reserva adicional y especificar el mecanizado CNC posterior a la impresión para lograr tolerancias en el rango de ±0,01 mm a ±0,05 mm o mejores.
Acabado superficial (rugosidad):
- Superficie as-built: La naturaleza de la fusión del lecho de polvo, en la que las partículas de polvo se funden y fusionan, da lugar a una rugosidad superficial característica.
- Valores típicos: Las superficies as-printed en piezas de cobre/CuCrZr suelen presentar valores de rugosidad (Ra) que oscilan entre $10 \mu$m y $25 \mu$m, dependiendo de la orientación de la superficie con respecto a la dirección de construcción (las superficies orientadas hacia arriba tienden a ser más lisas que las paredes laterales o las superficies orientadas hacia abajo influidas por los soportes).
- Impacto: Esta rugosidad inherente afecta significativamente al rendimiento térmico en las interfaces. Los picos y valles microscópicos crean entrehierros al acoplar el disipador a un componente, lo que aumenta drásticamente la resistencia al contacto térmico y dificulta la transferencia de calor. En los canales internos de los disipadores refrigerados por líquido, la elevada rugosidad puede aumentar la caída de presión y afectar a las características del flujo.
- Superficies postprocesadas: Varias técnicas pueden mejorar el acabado de la impresión:
- Explosión mediática/Tumbling: El uso de abrasivos (por ejemplo, microesferas cerámicas, microesferas de vidrio) puede proporcionar un acabado mate uniforme, reduciendo normalmente Ra a $5 - 10 \mu$m. Bueno para la limpieza general y el aspecto cosmético.
- Pulido/grabado químico: Puede suavizar características externas complejas y a veces internas, alcanzando potencialmente valores Ra de unos pocos micrómetros, pero el control puede ser difícil.
- Pulido mecánico/lapeado: Esencial para interfaces críticas. El pulido manual o automatizado puede conseguir acabados de espejo con Ra $< 0,8 \mu$m o incluso $< 0,1 \mu$m, reduciendo drásticamente la resistencia térmica de contacto.
- Micromecanizado: Puede conseguir superficies muy lisas y precisas en zonas concretas.
Garantía de calidad y precisión dimensional:
Conseguir una precisión dimensional constante y el acabado superficial deseado requiere un enfoque sólido por parte del proveedor de servicios de AM.
- Control de procesos: Es fundamental utilizar máquinas bien mantenidas y calibradas. La aplicación de parámetros de impresión optimizados desarrollados específicamente para Cu y CuCrZr es crucial. Proveedores como Met3dp, que fabrican tanto impresoras como polvos, poseen conocimientos profundos sobre la optimización de diversos parámetros de impresión. métodos de impresión para materiales y resultados específicos.
- Sistemas de gestión de la calidad (SGC): Busque proveedores con certificaciones como ISO 9001. Esto indica procedimientos establecidos para el control de procesos, la manipulación de materiales, la trazabilidad y la inspección. Para sectores específicos, puede exigirse AS9100 (aeroespacial) o ISO 13485 (médico).
- Inspección y metrología: Los proveedores reputados emplean diversas herramientas de metrología:
- MMC (máquina de medición por coordenadas): Para la verificación dimensional precisa de características críticas.
- Escaneado 3D: Comparar la geometría final de la pieza con el modelo CAD original y evaluar la desviación global.
- Rugosímetros de superficie (perfilómetros): Para verificar que se han alcanzado los valores Ra especificados en las superficies críticas.
Los ingenieros deben definir claramente las tolerancias y acabados superficiales requeridos en los planos y especificaciones, sobre todo en las interfaces críticas. Los responsables de compras deben asegurarse de que los posibles proveedores cuentan con el equipo, la experiencia y los sistemas de calidad necesarios para cumplir estos requisitos de forma coherente. Aunque es posible que las piezas de cobre de AM no se ajusten a las tolerancias predeterminadas del mecanizado en serie, un diseño estratégico y un postprocesado adecuado permiten obtener componentes de alta precisión aptos para las aplicaciones B2B más exigentes.
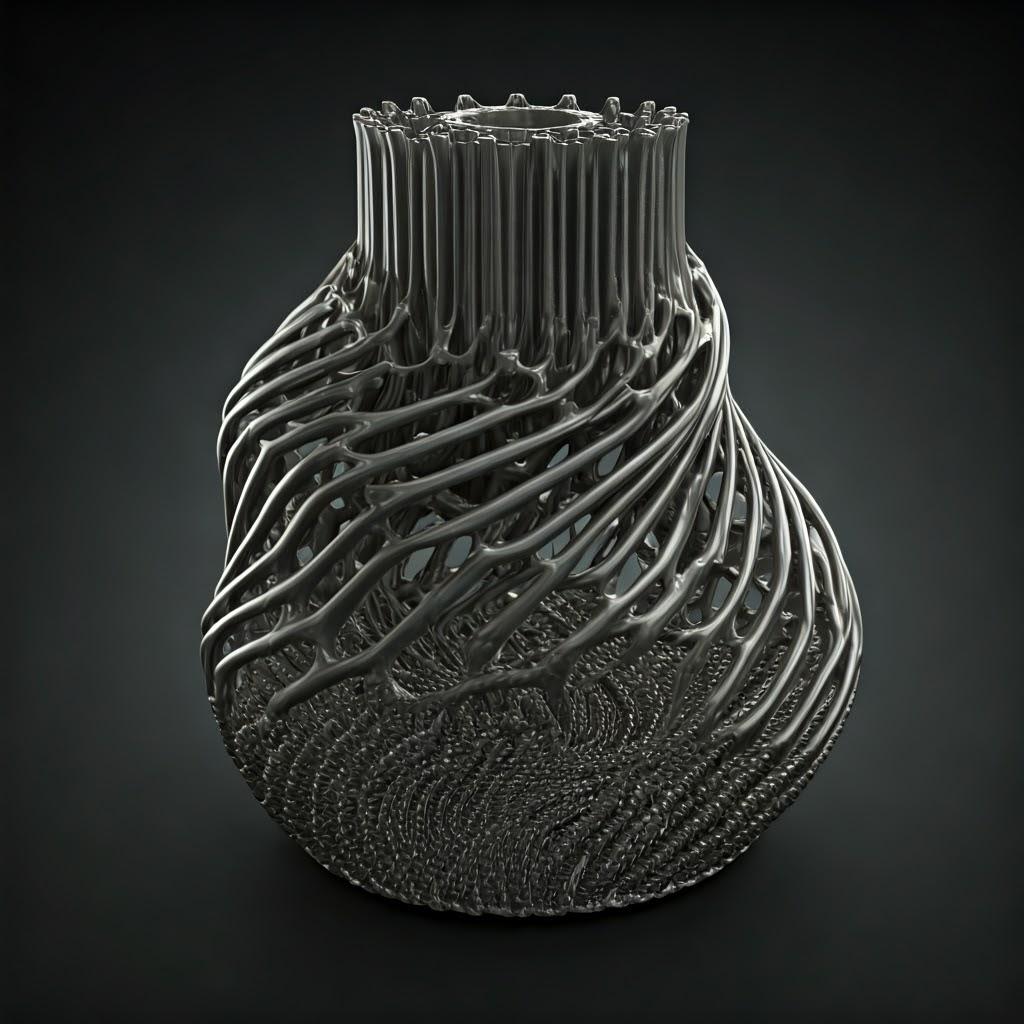
Requisitos de postprocesado para disipadores térmicos de cobre impresos en 3D
A diferencia de la impresión 3D de plásticos, en la que las piezas pueden utilizarse directamente desde la impresora, la fabricación aditiva de metales, especialmente con materiales de alto rendimiento como el cobre y el CuCrZr, casi siempre requiere una serie de pasos de posprocesamiento. Estos pasos son fundamentales para conseguir la precisión dimensional, el acabado superficial, las propiedades mecánicas y la funcionalidad general del disipador térmico deseados. Ignorar o ejecutar incorrectamente el postprocesado puede comprometer gravemente el rendimiento y la fiabilidad.
Pasos comunes de postprocesado para disipadores de cobre AM:
- Alivio del estrés / Tratamiento térmico:
- Propósito: Los rápidos ciclos de calentamiento y enfriamiento inherentes al LPBF crean importantes tensiones residuales dentro de la pieza impresa. Estas tensiones pueden provocar distorsiones con el tiempo o durante el mecanizado posterior. El alivio de tensiones implica calentar la pieza a una temperatura específica por debajo de su punto crítico de transformación y mantenerla, permitiendo que las tensiones se relajen, seguido de un enfriamiento controlado.
- CuCrZr Endurecimiento por precipitación: En el caso de las aleaciones CuCrZr, el tratamiento térmico no sólo sirve para aliviar tensiones, sino que es esencial para desarrollar su gran resistencia y dureza. Esto suele implicar un proceso en dos fases:
- Recocido de soluciones: Calentamiento a alta temperatura (~950-1000°C) para disolver el Cr y el Zr en la matriz de cobre, seguido de un enfriamiento rápido.
- Endurecimiento por envejecimiento (precipitación): El recalentamiento a una temperatura más baja (~450-550°C) durante un tiempo específico permite que se formen precipitados finos de Cr y Zr dentro de la matriz de cobre, lo que aumenta significativamente la resistencia y la dureza al tiempo que mantiene una buena conductividad.
- Ambiente: Los tratamientos térmicos de las aleaciones de cobre deben realizarse en vacío o en una atmósfera inerte controlada (como argón o nitrógeno) para evitar la oxidación, que degradaría la calidad de la superficie y podría afectar a las propiedades.
- Extracción de la pieza de la placa de montaje:
- Las piezas suelen imprimirse en una placa metálica gruesa. Para retirarlas suele ser necesario cortarlas, a menudo mediante electroerosión por hilo (EDM) o sierra de cinta. La electroerosión por hilo proporciona un corte más limpio con menos tensión mecánica.
- Retirada de la estructura de soporte:
- Método: Dependiendo del diseño y la accesibilidad, los soportes pueden retirarse manualmente (rompiéndolos o cortándolos), mediante mecanizado CNC o utilizando electroerosión por hilo para zonas intrincadas o de difícil acceso. Este puede ser uno de los pasos más laboriosos y complicados, sobre todo en el caso de geometrías internas complejas.
- Importancia para los insertos de moldes Diseñar los soportes para facilitar su retirada (por ejemplo, con puntos de contacto más pequeños, vías de acceso planificadas) durante la fase inicial de diseño reduce significativamente el tiempo y el coste de los procesos posteriores.
- Limpieza y eliminación de polvo:
- Necesidad: Es absolutamente fundamental eliminar todo el polvo suelto y parcialmente sinterizado, especialmente de los canales internos o de las estructuras reticulares complejas. El polvo residual puede obstruir el flujo, reducir el rendimiento térmico y actuar como contaminación.
- Técnicas: Entre los métodos habituales se incluyen el chorreado con aire comprimido o gas inerte, la limpieza por ultrasonidos en disolventes adecuados y, en ocasiones, técnicas especializadas como el mecanizado por flujo abrasivo (AFM) para pulir los canales internos al tiempo que se elimina el polvo. Puede ser necesaria una verificación (por ejemplo, inspección visual con boroscopios, pruebas de flujo o escáner CT para piezas críticas).
- Acabado superficial:
- Propósito: Reducir la rugosidad de la superficie para mejorar el contacto térmico, la dinámica de fluidos, el aspecto estético o la preparación para el revestimiento.
- Métodos (Reiteración): Granallado (arena, microesferas), volteo, pulido mecánico (esencial para las interfaces), electropulido o grabado químico. El método elegido depende del valor de Ra final requerido y de la geometría de la pieza.
- Mecanizado CNC:
- Cuando sea necesario: Para conseguir tolerancias estrictas en dimensiones críticas, superficies de contacto, ranuras de sellado, orificios roscados o cualquier característica que requiera una precisión superior a la capacidad de impresión.
- Consideraciones: Requiere un cuidadoso diseño de la fijación para sujetar de forma segura y sin distorsión formas AM potencialmente complejas. El mecanizado de CuCrZr tratado térmicamente es más fácil que el de cobre puro.
- Chapado o revestimiento (opcional):
- Aplicaciones: Aumentar la resistencia a la corrosión (por ejemplo, niquelado), mejorar la soldabilidad o la unión de alambres (por ejemplo, níquel/oro), aumentar la resistencia al desgaste o proporcionar propiedades superficiales específicas.
- Proceso: Los procesos estándar de galvanoplastia o electrodeposición pueden aplicarse tras una preparación adecuada de la superficie.
Los responsables de compras y los ingenieros deben tener en cuenta el tiempo y el coste de estos pasos de postprocesamiento en su planificación de proyectos y evaluación de proveedores. Un proveedor integrado verticalmente o con una sólida red de socios cualificados de postprocesado puede agilizar considerablemente este flujo de trabajo. Si se descuidan estos pasos, las capacidades geométricas avanzadas de la AM resultarán ineficaces si la pieza final no cumple los requisitos funcionales.
Desafíos comunes en el disipador térmico de cobre AM y cómo evitarlos
Aunque la fabricación aditiva basada en cobre ofrece un enorme potencial para los disipadores térmicos de alto rendimiento, no está exenta de dificultades. Comprender estos posibles obstáculos y aplicar estrategias de mitigación -mediante un diseño cuidadoso, el control de procesos y la colaboración con socios experimentados- es clave para adoptar con éxito las exigentes aplicaciones B2B.
- Deformación y distorsión:
- Causa: Los elevados gradientes térmicos entre el baño de fusión y el material circundante provocan dilataciones y contracciones diferenciales, lo que genera tensiones residuales que pueden deformar la pieza, sobre todo los elementos finos o las grandes zonas planas. La elevada conductividad térmica del cobre puede agravar esta situación.
- Evitación/Mitigación:
- Estrategia de apoyo sólida: Los soportes bien diseñados anclan firmemente la pieza y ayudan a evacuar el calor.
- Estrategia de exploración optimizada: El uso de técnicas como los patrones de barrido en isla o en damero puede distribuir el calor de forma más uniforme.
- Construir calefacción de placas: El precalentamiento de la placa de impresión reduce la diferencia de temperatura.
- Simulación térmica: Predecir las zonas de mayor tensión durante la fase de diseño.
- Alivio del estrés: El tratamiento térmico posterior a la impresión es crucial para aliviar las tensiones acumuladas.
- Modificaciones de diseño: Añadir nervaduras de sacrificio o modificar la geometría a veces puede ayudar.
- Alcanzar la plena densidad / porosidad:
- Causa: La porosidad (pequeños huecos en el material) puede deberse al gas atrapado en el polvo (porosidad gaseosa) o a una fusión incompleta entre capas o pistas de barrido (porosidad por falta de fusión). La alta reflectividad y conductividad del láser de cobre dificultan la consecución de una fusión uniforme.
- Impacto: La porosidad reduce significativamente la conductividad térmica y la resistencia mecánica (límite elástico, vida a la fatiga).
- Evitación/Mitigación:
- Polvo de alta calidad: Es primordial utilizar polvo altamente esférico con un bajo contenido interno de gas y una distribución controlada del tamaño de las partículas. Aquí es donde proveedores como Met3dp, centrados en técnicas de atomización avanzadas (atomización con gas, PREP), aportan un valor significativo. Obtenga más información sobre su compromiso con la calidad y la experiencia visitando la página sobre nosotros página.
- Parámetros de impresión optimizados: Ajuste de la potencia del láser, la velocidad de escaneado, la separación entre tramas y el grosor de la capa para la aleación de cobre utilizada. Esto suele requerir una amplia experimentación y experiencia.
- Control de la atmósfera inerte: Mantener un entorno de gas inerte de alta pureza (por ejemplo, Argón < 1000 ppm O2) minimiza la oxidación y la captación de gas durante la impresión.
- Tecnología de maquinaria adecuada: Utilizando máquinas diseñadas o adaptadas para materiales reflectantes (por ejemplo, con suficiente potencia láser, potencialmente láseres verdes).
- Dificultades para retirar la ayuda:
- Causa: Los canales internos complejos, las estructuras reticulares densas o los soportes situados en lugares inaccesibles hacen que la extracción sea extremadamente difícil, lleve mucho tiempo y pueda dañar la pieza. Las aleaciones de cobre pueden ser relativamente duras, lo que dificulta la extracción manual.
- Evitación/Mitigación:
- DfAM para la eliminación: Dé prioridad a las opciones de diseño que minimicen la necesidad de soportes o garanticen su fácil acceso (por ejemplo, orientación, ángulos autoportantes, puertos de acceso más grandes para las características internas).
- Técnicas de eliminación especializadas: Asociarse con proveedores experimentados en técnicas como el micromecanizado, la electroerosión por hilo o, potencialmente, el mecanizado electroquímico para la eliminación de soportes.
- Elementos de diseño sacrificiales: Diseñar elementos destinados a ser mecanizados posteriormente, que también sirven de soporte durante la impresión.
- Manipulación y seguridad del polvo:
- Asunto: Los polvos metálicos finos, incluido el cobre, son respirables y pueden plantear riesgos para la salud. También pueden ser inflamables o explosivos en determinadas condiciones (nube de polvo). El polvo de cobre requiere una manipulación cuidadosa para evitar una oxidación excesiva.
- Evitación/Mitigación: Esto es principalmente responsabilidad del proveedor de servicios AM. Asegúrese de que disponen de:
- Controles técnicos adecuados (sistemas cerrados, ventilación).
- Sistemas de manipulación de gas inerte para almacenamiento y transferencia de polvo.
- Protocolos de EPI estrictos para los operarios.
- Conexión a tierra para evitar descargas estáticas.
- Procedimientos de limpieza y eliminación de residuos establecidos.
- Impacto de la rugosidad superficial:
- Asunto: Como ya se ha comentado, la rugosidad inherente a la impresión aumenta la resistencia térmica de contacto.
- Evitación/Mitigación: Especifique claramente los acabados superficiales requeridos para las interfaces críticas y asegúrese de que los métodos de postprocesado elegidos (pulido, lapeado, mecanizado) son adecuados y se aplican de forma coherente. Tenga en cuenta el coste de conseguir superficies lisas en el presupuesto general.
- Gestión de costes:
- Asunto: Los polvos de cobre son caros, y el equipo especializado y el procesamiento en varios pasos contribuyen a un mayor coste en comparación con la fabricación tradicional de disipadores simples o el uso de otros metales como el aluminio.
- Evitación/Mitigación:
- Justificar la complejidad: Utilice la AM cuando su libertad geométrica proporcione una ventaja de rendimiento o integración inalcanzable de otro modo. No utilice la AM para formas sencillas en las que baste con la extrusión o el mecanizado.
- Optimizar el diseño para AM: Utilice la optimización topológica para minimizar el uso de material. Diseñe para una impresión eficiente (orientación, anidamiento de piezas) y una fácil retirada del soporte.
- Consideraciones sobre el volumen: Discutir con los proveedores las posibles reducciones de costes en la producción por lotes.
- Especificaciones claras: Facilitar los requisitos detallados por adelantado permite a los proveedores ofrecer presupuestos precisos y evitar costes inesperados más adelante.
Superar con éxito estos retos requiere una combinación de diseño inteligente, ciencia avanzada de materiales, control preciso del proceso y sólidas capacidades de postprocesamiento. Asociarse con un proveedor de servicios de AM metálica experimentado y bien equipado que entienda los matices de la impresión de cobre es crucial para mitigar los riesgos y conseguir disipadores de alta calidad y fiables para aplicaciones B2B críticas.
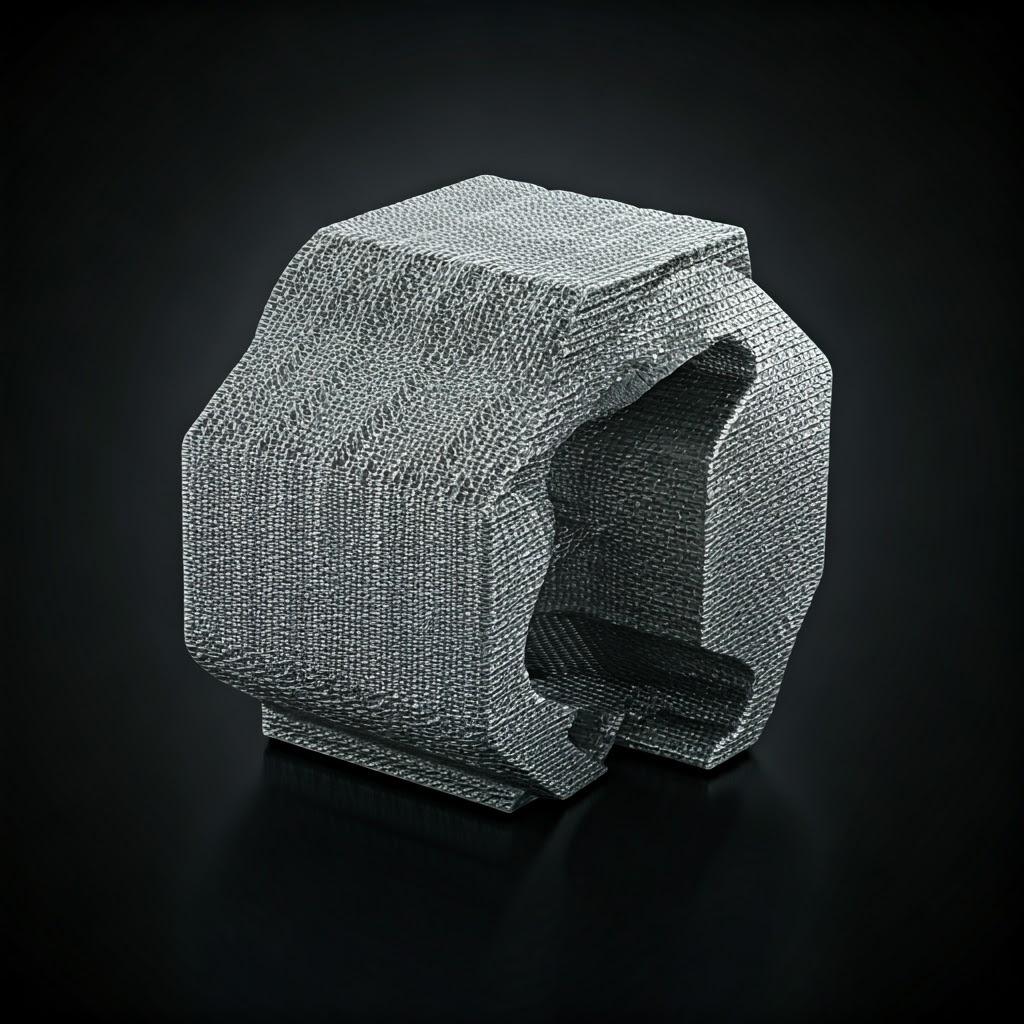
Cómo elegir el proveedor de servicios de impresión 3D sobre metal adecuado para disipadores térmicos
La selección del socio adecuado para la fabricación aditiva es posiblemente tan importante como el propio diseño, especialmente cuando se trata de materiales difíciles como el cobre y el CuCrZr para aplicaciones de alto rendimiento. La calidad, la fiabilidad y el rendimiento del disipador térmico impreso en 3D dependen en gran medida de la experiencia, el equipo y los procesos del proveedor elegido. Para los ingenieros y responsables de compras que navegan por el panorama B2B, he aquí una lista de comprobación de los factores clave que deben evaluarse:
- Experiencia demostrada en materiales (Cu y CuCrZr):
- Ir más allá de las reclamaciones: No acepte sin más que un proveedor le diga que poder imprimir cobre. Pida pruebas. Solicite estudios de casos, piezas de muestra (idealmente de cobre o CuCrZr) u hojas de datos de materiales derivadas de sus componentes impresos realesno sólo las especificaciones genéricas de la pólvora.
- Desarrollo de parámetros: ¿Disponen de parámetros de impresión desarrollados y validados internamente para Cu y CuCrZr, o se basan en ajustes genéricos? Los parámetros optimizados son cruciales para la densidad y las propiedades.
- Experiencia en resolución de problemas: ¿Han superado con éxito los retos habituales de la impresión en cobre, como la porosidad o el agrietamiento?
- Capacidades adecuadas de la máquina:
- Tecnología: Asegúrese de que utilizan la fusión por lecho de polvo láser (LPBF), el estándar para la AM metálica de alta resolución.
- Especificaciones de la máquina: Pregunte por sus máquinas específicas. Entre las características beneficiosas para el cobre se incluyen una potencia láser suficiente (por ejemplo, 500 W o 1 kW), opciones de láser potencialmente verde (mejor absorción por el cobre), control preciso de la atmósfera inerte (bajos niveles de oxígeno) y un volumen de construcción adecuado para el tamaño de su pieza.
- Calibración y mantenimiento: Pregunte por la frecuencia de calibración de la máquina y los programas de mantenimiento para garantizar una precisión y un rendimiento constantes.
- Sólido sistema de gestión de la calidad (SGC):
- Certificaciones: Busque la ISO 9001 como indicador básico de los procesos de calidad. Si su aplicación es aeroespacial o médica, exija la certificación AS9100 o ISO 13485, respectivamente.
- Control de procesos: ¿Qué medidas se han adoptado para supervisar el proceso de construcción? (por ejemplo, control del baño de fusión, registro de datos de sensores). ¿Cómo garantizan la calidad y la trazabilidad del polvo a lo largo de todo el flujo de trabajo?
- Capacidad de inspección: Compruebe que disponen del equipo de metrología necesario (MMC, escáneres 3D, perfilómetros de superficie) y de los procedimientos para inspeccionar las piezas según sus especificaciones. Pregunte por las capacidades de ensayos no destructivos (END), como el escaneado CT, si la verificación de la integridad interna es crítica.
- Amplias funciones de posprocesamiento:
- En casa o en red: ¿Realiza el proveedor internamente los pasos críticos del postprocesado, como el tratamiento térmico (con hornos de vacío/atmósfera inerte), el mecanizado CNC, la eliminación de soportes y el acabado de superficies? Si subcontrata, compruebe que recurre a socios cualificados y con experiencia.
- Habilidades especializadas: Confirmar la experiencia en el tratamiento térmico correcto de CuCrZr (disolución y envejecimiento), la eliminación segura de soportes complejos y la obtención de acabados superficiales especificados en cobre.
- Asistencia técnica y experiencia en DfAM:
- Colaboración: ¿Trabajarán con su equipo de ingeniería para proporcionar información sobre el diseño para la fabricación aditiva (DfAM)? Un buen socio puede ofrecer sugerencias sobre orientación, estrategia de soporte, optimización de características y selección de materiales para mejorar la imprimibilidad y el rendimiento, reduciendo potencialmente los costes.
- Resolución de problemas: ¿Son receptivos y capaces de ayudar a resolver los problemas que puedan surgir durante la creación de prototipos o la producción?
- Capacidad, plazo de entrega y escalabilidad:
- Plazos realistas: Obtenga estimaciones claras de los plazos de prototipo y de producción potencial. Entender su carga de trabajo y capacidad actuales.
- Escalabilidad: Si prevé pasar de los prototipos a la producción de bajo volumen, asegúrese de que el proveedor dispone de la capacidad y los sistemas necesarios para gestionar el aumento de volumen de forma coherente.
- Transparencia y comunicación de costes:
- Presupuestos detallados: Asegúrese de que los presupuestos desglosan claramente los costes (material, tiempo de máquina, postprocesado, NRE, control de calidad). Cuidado con los presupuestos demasiado simplificados que puedan ocultar gastos futuros.
- Capacidad de respuesta: Evalúe su estilo de comunicación y su capacidad de respuesta durante el proceso de cotización y evaluación.
- Reputación y estabilidad de los proveedores:
- Busque proveedores establecidos con un historial de éxito en sectores exigentes. Tenga en cuenta su estabilidad financiera, especialmente en el caso de asociaciones B2B a largo plazo.
Considerar a los socios integrados verticalmente: Empresas como Met3dpque poseen una gran experiencia en la fabricación avanzada de polvo metálico y ofrecen una ventaja única. Su conocimiento intrínseco de la ciencia de los materiales, las características del polvo (gracias a sus capacidades de atomización con gas y PREP) y la tecnología de las impresoras permite adoptar un enfoque más holístico para optimizar toda la cadena de procesos de materiales como el cobre y el CuCrZr. La elección de un socio con un conocimiento tan exhaustivo puede reducir significativamente el riesgo de adopción de esta tecnología avanzada para componentes críticos como los disipadores térmicos de alto rendimiento.
Tomar la decisión correcta requiere la debida diligencia. No dude en hacer preguntas detalladas, solicitar visitas a las instalaciones (virtuales o físicas) y, posiblemente, ejecutar piezas de referencia para comparar capacidades antes de comprometerse con un proveedor para sus necesidades críticas de disipadores de cobre.
Factores de coste y plazos de entrega de los disipadores térmicos de cobre impresos en 3D
Aunque la fabricación aditiva de metales ofrece importantes ventajas de rendimiento y diseño para los disipadores de cobre, es esencial que los clientes B2B conozcan la estructura de costes asociada y los plazos de entrega habituales. Estos factores difieren considerablemente de los métodos tradicionales de fabricación de grandes volúmenes y deben tenerse en cuenta en la planificación y el presupuesto del proyecto.
Principales factores de coste:
En el precio final de un disipador de cobre o CuCrZr impreso en 3D influyen numerosos factores:
Costes | Descripción | Nivel de impacto | Notas |
---|---|---|---|
Costo material | Precio por kilogramo de polvo de Cu o CuCrZr de calidad AM. | Alta | Las aleaciones de cobre son materiales de primera calidad. Incluye el polvo consumido + los residuos del proceso. |
La hora de las máquinas | Coste por hora de funcionamiento de la sofisticada máquina LPBF multiplicado por la duración total de la impresión. | Alta | Influyen el volumen de la pieza, la altura (número de capas) y la complejidad (tiempo de escaneado). |
Trabajo de postprocesado | Esfuerzo manual para la retirada de soportes, acabado de superficies, limpieza, inspección, etc. | Medio-Alto | Puede ser sustancial para piezas complejas o especificaciones ajustadas. |
Servicios de posprocesamiento | Coste de los pasos especializados como el tratamiento térmico (tiempo de horno, atmósfera), mecanizado CNC, chapado. | Medio-Alto | Depende mucho de los requisitos específicos. |
Estructuras de apoyo | El material utilizado suele ser menor, pero el diseño, la impresión y la mudanza esfuerzo contribuyen significativamente. | Medio | Los complejos soportes internos encarecen los costes de retirada. |
Mano de obra (instalación y funcionamiento) | Tiempo de técnico cualificado para la preparación de la construcción, el funcionamiento de la máquina, la manipulación del polvo y la retirada de piezas. | Medio | Componentes fijos y variables. |
Complejidad de las piezas | Los diseños muy complejos pueden requerir tiempos de impresión más largos y un posprocesamiento y control de calidad más intensivos. | Medio | Afecta al tiempo de máquina, a la retirada de soportes y al esfuerzo de inspección. |
Garantía de calidad | Coste de la inspección, metrología (MMC, escaneado), posibles END, documentación. | Bajo-Medio | Aumenta con tolerancias más estrictas y requisitos de certificación. |
Ingeniería no recurrente | Costes de configuración inicial, consulta DfAM, desarrollo de parámetros personalizados (si es necesario), diseño de la fijación. | Bajo-Medio | Suele amortizarse en el primer lote o prototipos. |
Volumen del pedido | Las economías de escala son menos pronunciadas que en la producción en serie, pero existen para lotes más grandes (amortización de la preparación). | Bajo | Afecta principalmente a los costes de preparación por pieza. |
Exportar a hojas
Estimación de los plazos de entrega:
El plazo de entrega de las piezas AM es secuencial y depende de varios factores. Rara vez es solo el tiempo de impresión.
- Flujo de trabajo típico y duración estimada:
- Cotización y confirmación del pedido: 1 - 5 días laborables (requiere el paquete completo de datos técnicos).
- Revisión del diseño y preparación de la impresión: 1 - 3 días laborables (incluye comprobaciones DfAM, orientación, generación de soporte).
- Cola de máquinas: Muy variable, de días a varias semanas en función de la carga de trabajo del proveedor.
- Imprimiendo: De horas (para piezas pequeñas) a varios días (para construcciones grandes, complejas o anidadas).
- Enfriamiento y retirada de la placa de construcción: 0,5 - 1 día.
- Alivio del estrés / Tratamiento térmico: 1 - 3 días (incluyendo el tiempo de ciclo del horno y la manipulación).
- Retirada del soporte: 0,5 - 5+ días (muy dependiente de la complejidad y el método).
- Mecanizado (si es necesario): 1 - 10+ días (depende de la complejidad, las características y la programación del taller).
- Acabado y limpieza de superficies: 1 - 5 días.
- Inspección de calidad: 1 - 3 días.
- Embalaje y envío: 1 - 5+ días (depende de la ubicación y el método).
- Estimaciones generales:
- Prototipos: Normalmente oscilan entre De 1 a 4 semanas.
- Lotes de producción de bajo volumen: Normalmente oscilan entre De 4 a 10 semanas, a veces más largo en función de la complejidad y la cantidad.
Obtención de presupuestos y plazos precisos:
Para recibir estimaciones fiables de costes y plazos de entrega de posibles proveedores como Met3dp, facilite un paquete completo de datos técnicos que incluya:
- Modelo CAD en 3D: Formato nativo o archivo STEP.
- Dibujo técnico: Especificación de materiales (por ejemplo, CuCrZr C18150), dimensiones críticas con tolerancias (utilizando GD&T), acabados superficiales requeridos (valores Ra en superficies específicas), especificaciones de tratamiento térmico (si procede) y cualquier requisito de ensayo/inspección.
- Cantidad: Número de piezas necesarias (prototipo frente a producción).
- Contexto de aplicación: Describir brevemente el uso final puede a veces ayudar al proveedor a ofrecer un mejor asesoramiento DfAM.
Al conocer los factores de coste y el flujo de trabajo habitual, los clientes B2B pueden planificar mejor los proyectos, gestionar los presupuestos y establecer expectativas realistas a la hora de incorporar disipadores de cobre impresos en 3D de alto rendimiento a sus productos.
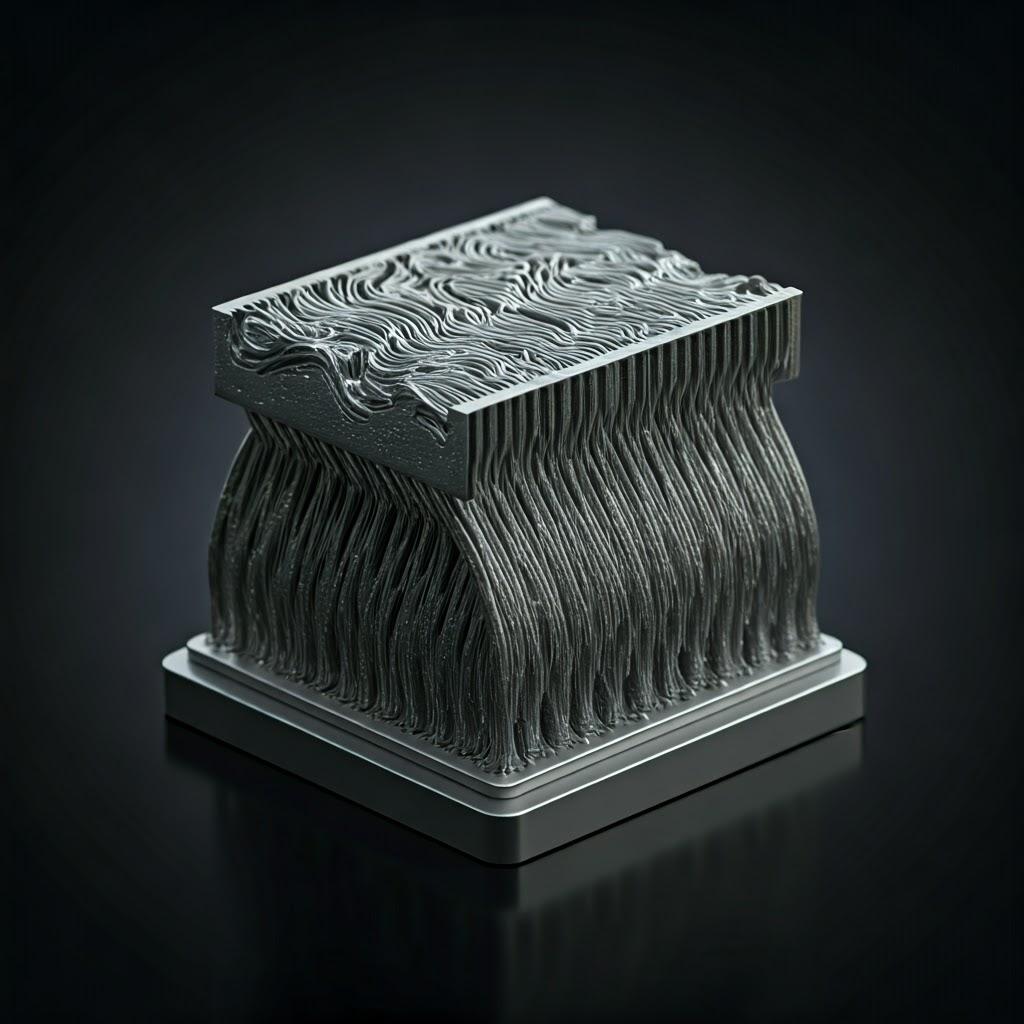
Preguntas más frecuentes (FAQ)
Aquí encontrará respuestas a algunas de las preguntas más habituales que se hacen los ingenieros y responsables de compras sobre los disipadores de cobre impresos en 3D:
- P1: ¿Cuál es el rendimiento térmico de un disipador de cobre impreso en 3D en comparación con uno fabricado de forma tradicional (por ejemplo, mecanizado o rebajado)?
- A: Depende mucho de la complejidad del diseño. Para geometrías sencillas, los métodos tradicionales pueden ser más rentables y ofrecer un rendimiento similar. Sin embargo, en el caso de diseños complejos que aprovechen los puntos fuertes de la AM (por ejemplo, canales internos intrincados, entramados TPMS, superficies conformadas), un disipador térmico impreso en 3D bien diseñado y fabricado con polvo de Cu o CuCrZr de alta calidad puede superar significativamente a sus homólogos tradicionales. Lograr una alta densidad (>99,5%) durante la impresión y un procesamiento posterior adecuado (especialmente el acabado superficial de las interfaces) es fundamental para aprovechar este potencial.
- P2: ¿Es el CuCrZr impreso en 3D lo suficientemente resistente para aplicaciones aeroespaciales o de automoción exigentes?
- A: Sí, normalmente. Cuando se somete a un tratamiento térmico adecuado (disolución y envejecimiento), el CuCrZr impreso en 3D (como el C18150) alcanza propiedades mecánicas (resistencia a la tracción, límite elástico, dureza) significativamente superiores a las del cobre puro y comparables a las de algunos aceros, al tiempo que conserva ~80-85% de la conductividad térmica del cobre. También mantiene razonablemente bien la resistencia a temperaturas elevadas (hasta ~450-500°C). Este excelente equilibrio lo convierte en un candidato idóneo para muchas aplicaciones de gestión térmica estructuralmente exigentes en el sector aeroespacial, la electrónica de potencia de automoción y los sistemas industriales. Verifique siempre las propiedades en función de los requisitos específicos de la aplicación. El enfoque de Met3dp en polvos de alta calidad ayuda a garantizar que estas propiedades óptimas se puedan conseguir de forma consistente.
- P3: ¿Cuáles son los principales retos a la hora de pasar de un disipador fabricado tradicionalmente a uno impreso en 3D?
- A: Entre los principales retos figuran: 1) Cambio de paradigma en el diseño: Los ingenieros deben aprender y aplicar los principios del DfAM, no limitarse a replicar diseños antiguos. 2) Diferencias de especificación: Comprender y especificar las tolerancias y los acabados superficiales adecuados que pueden conseguirse con la AM. 3) Incorporación del postprocesado: Planificación de los pasos necesarios, como el tratamiento térmico, la eliminación de soportes y el acabado superficial. 4) Validación del rendimiento: Probar y validar el rendimiento térmico y mecánico de la pieza AM. 5) Estructura de costes: Los costes de la AM dependen de factores diferentes (material, tiempo de mecanizado, complejidad) a los de los métodos tradicionales, lo que puede influir en la rentabilidad en función del volumen y la complejidad del diseño. Asociarse con un proveedor de AM experimentado puede facilitar esta transición.
- P4: ¿Pueden limpiarse eficazmente de polvo residual los canales de refrigeración internos de los disipadores térmicos impresos en 3D?
- A: Sí, pero requiere una cuidadosa consideración durante la fase de diseño y procesos de limpieza especializados por parte del proveedor de servicios. Los factores clave incluyen el diseño de canales con un diámetro suficiente (por ejemplo, a menudo se recomienda > 0,8-1,0 mm), curvas suaves (evitando esquinas afiladas donde el polvo pueda quedar atrapado) y posibles puertos de acceso. Los métodos de limpieza eficaces implican el flujo de gas inerte a alta presión, potencialmente combinado con la limpieza ultrasónica en fluidos específicos, o técnicas de flujo microabrasivo. La verificación de la limpieza (por ejemplo, inspección boroscópica, pruebas de flujo, tomografía computarizada) suele ser necesaria en aplicaciones críticas para garantizar que no queden obstrucciones. Se trata de un ámbito en el que la experiencia del proveedor de servicios AM es crucial.
Conclusiones: Revolucionando la gestión térmica con la fabricación aditiva de cobre
El incesante avance hacia mayores densidades de potencia y la miniaturización de la electrónica plantea importantes retos de gestión térmica en sectores que van desde la industria aeroespacial a la automovilística, pasando por la tecnología médica. Los métodos tradicionales de fabricación de disipadores están alcanzando cada vez más sus límites en términos de complejidad geométrica y rendimiento alcanzable. La fabricación aditiva de metales, sobre todo con materiales de alta conductividad como el cobre puro (Cu) y el cobre, cromo y circonio (CuCrZr), ofrece una potente solución.
Al permitir la creación de disipadores con intrincados canales internos, estructuras de topología optimizada, superficies conformadas y características integradas, la AM permite a los ingenieros diseñar para obtener un rendimiento térmico óptimo en lugar de estar limitados por la fabricabilidad. Las ventajas son tangibles: mejor disipación del calor, mayor fiabilidad de los componentes, mayor vida útil de los productos y la posibilidad de miniaturizar aún más los sistemas. Mientras que el cobre puro proporciona la máxima conductividad térmica, el CuCrZr ofrece un equilibrio excepcional de alto rendimiento térmico y resistencia mecánica significativamente mejorada, lo que lo hace ideal para aplicaciones exigentes.
Aplicar con éxito la AM del cobre requiere un enfoque holístico. Esto incluye adoptar los principios del Diseño para la Fabricación Aditiva (DfAM), comprender las tolerancias y los acabados superficiales alcanzables, planificar los pasos esenciales del postprocesamiento, como el tratamiento térmico y la eliminación de soportes, y gestionar cuidadosamente los costes y los plazos de entrega. Para tener éxito, es fundamental asociarse con el proveedor de servicios de impresión 3D de metales B2B adecuado, con experiencia demostrada en aleaciones de cobre, sistemas de calidad sólidos, equipos adecuados y capacidades completas de posprocesamiento.
Empresas como Met3dpcon su base en la producción avanzada de polvo metálico y su profundo conocimiento de los procesos de fabricación aditiva, representan el tipo de socio experimentado necesario para sortear las complejidades y liberar todo el potencial de esta tecnología. Salvan la distancia crítica entre la ciencia de los materiales y la ejecución de la fabricación.
Para los ingenieros y responsables de compras que buscan ampliar los límites de la gestión térmica y obtener una ventaja competitiva, la fabricación aditiva basada en cobre ha dejado de ser una tecnología de nicho para convertirse en una herramienta vital. Le animamos a explorar cómo la AM puede resolver sus problemas de disipación térmica más desafiantes.
¿Está listo para revolucionar su estrategia de gestión térmica? Visite Met3dp.com para obtener más información sobre sus polvos metálicos avanzados, soluciones de impresión y cómo pueden colaborar con usted en su próximo proyecto.
Compartir
MET3DP Technology Co., LTD es un proveedor líder de soluciones de fabricación aditiva con sede en Qingdao, China. Nuestra empresa está especializada en equipos de impresión 3D y polvos metálicos de alto rendimiento para aplicaciones industriales.
Solicite información para obtener el mejor precio y una solución personalizada para su empresa.
Artículos relacionados
Acerca de Met3DP
Actualización reciente
Nuestro producto
CONTACTO
¿Tiene alguna pregunta? ¡Envíenos un mensaje ahora! Atenderemos su solicitud con todo un equipo tras recibir su mensaje.
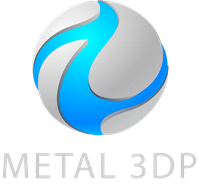
Polvos metálicos para impresión 3D y fabricación aditiva