Oxicorte a alta velocidad (HVOF)
Índice
Introducción
¿Alguna vez se ha preguntado cómo algunos materiales pueden resistir condiciones extremas mientras otros fracasan estrepitosamente? El secreto reside a menudo en las tecnologías avanzadas de revestimiento, y una de las más destacadas es Oxicorte a alta velocidad (HVOF). Pero, ¿qué es exactamente la pulverización HVOF? ¿Cómo funciona? ¿Por qué es tan especial? Sumerjámonos en este fascinante mundo en el que la ciencia se une al alto rendimiento.
Descripción general de la pulverización de oxicombustible a alta velocidad (HVOF)
La pulverización de oxicombustible a alta velocidad (HVOF) es un proceso de revestimiento por pulverización térmica que produce revestimientos excepcionalmente fuertes, densos y resistentes al desgaste. A diferencia de otros métodos de revestimiento, la pulverización HVOF utiliza un chorro de gas de alta velocidad para acelerar materiales de revestimiento en polvo a velocidades supersónicas, que luego se depositan sobre un sustrato. El resultado son revestimientos que no sólo son increíblemente duraderos, sino también muy precisos y uniformes.
Características principales de la pulverización HVOF
- Velocidades supersónicas: Los materiales de revestimiento se aceleran a velocidades de hasta Mach 2.
- Revestimientos densos: Los bajos niveles de porosidad dan lugar a revestimientos resistentes y duraderos.
- Versatilidad: Puede utilizarse con una amplia gama de materiales, incluidos metales, cerámica y carburos.
- Alta adherencia: Fuerte unión entre el revestimiento y el sustrato.
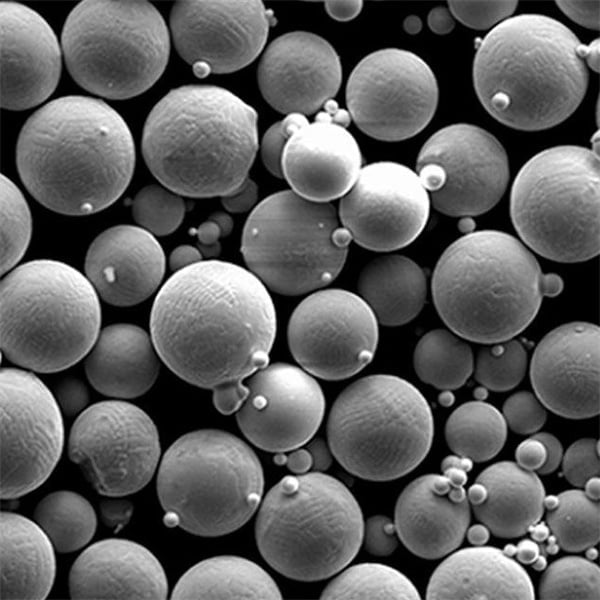
Composición y propiedades de los polvos metálicos HVOF
En la pulverización HVOF se utilizan diferentes polvos metálicos, cada uno con propiedades únicas adaptadas a aplicaciones específicas. Veamos algunos de los más populares:
Polvo metálico | Composición | Propiedades | Aplicaciones |
---|---|---|---|
Carburo de wolframio (WC) | WC-Co, WC-CoCr | Extremadamente duro, resistente al desgaste, alto punto de fusión | Herramientas de corte, piezas de desgaste, componentes aeroespaciales |
Carburo de cromo (CrC) | Cr3C2-NiCr, CrC-NiCr | Resistencia a altas temperaturas, resistencia a la corrosión | Turbinas de gas, motores, procesamiento químico |
Óxido de aluminio (Al2O3) | Al2O3 puro | Alta dureza, aislamiento eléctrico, resistencia al desgaste | Componentes eléctricos, revestimientos aislantes |
Níquel-cromo (NiCr) | NiCr, NiCrMo | Alta resistencia a la corrosión, estabilidad térmica | Equipos marinos, maquinaria industrial |
Molibdeno (Mo) | Mo puro, Mo-NiCr | Alto punto de fusión, excelente conductividad térmica | Aeroespacial, automoción, electrónica |
Stellite | Co-Cr-W, Co-Cr-Mo | Alta resistencia al desgaste, buena resistencia a la corrosión | Válvulas, rodamientos, herramientas de corte |
Inconel | Ni-Cr-Fe, Ni-Cr-Mo | Excelente resistencia a altas temperaturas y a la corrosión | Álabes de turbinas, intercambiadores de calor, motores de cohetes |
Acero inoxidable | 316L, 304 | Resistencia a la corrosión, buenas propiedades mecánicas | Dispositivos médicos, procesamiento de alimentos, aplicaciones marinas |
Dióxido de titanio (TiO2) | TiO2 puro | Gran dureza, estabilidad química | Revestimientos ópticos, revestimientos resistentes al desgaste |
Dióxido de circonio (ZrO2) | ZrO2 puro | Alta tenacidad a la fractura, aislamiento térmico | Revestimientos de barrera térmica, cerámica estructural |
Descripciones detalladas de los polvos metálicos seleccionados
- Carburo de wolframio (WC): Compuesto principalmente de carburo de wolframio y cobalto (WC-Co) o carburo de wolframio y cromo (WC-CoCr), este polvo es famoso por su dureza y resistencia al desgaste. Es la mejor elección para aplicaciones que exigen una durabilidad extrema, como las herramientas de corte y los componentes aeroespaciales.
- Carburo de cromo (CrC): Con composiciones como Cr3C2-NiCr, este polvo destaca en entornos corrosivos y de alta temperatura, por lo que es ideal para turbinas de gas y motores.
- Óxido de aluminio (Al2O3): Conocido por su gran dureza y sus propiedades de aislamiento eléctrico, el óxido de aluminio se utiliza ampliamente en componentes eléctricos y revestimientos aislantes.
- Níquel-cromo (NiCr): Las aleaciones de NiCr ofrecen una magnífica resistencia a la corrosión y estabilidad térmica, perfectas para equipos marinos y maquinaria industrial.
- Molibdeno (Mo): El molibdeno puro o las mezclas de Mo-NiCr proporcionan una excelente conductividad térmica y un alto punto de fusión, adecuados para aplicaciones aeroespaciales y de automoción.
- Stellite: La estelita, una aleación a base de cobalto, es muy resistente al desgaste y a la corrosión, y suele utilizarse en válvulas, cojinetes y herramientas de corte.
- Inconel: Esta aleación de níquel y cromo es conocida por su resistencia a altas temperaturas y a la oxidación y la corrosión. Se usa mucho en turbinas, intercambiadores de calor y motores de cohetes.
- Acero inoxidable: Grados comunes como el 316L y el 304 ofrecen un equilibrio entre resistencia a la corrosión y propiedades mecánicas, lo que los hace adecuados para dispositivos médicos y aplicaciones marinas.
- Dióxido de titanio (TiO2): Por su gran dureza y estabilidad química, el TiO2 se utiliza en revestimientos ópticos y aplicaciones resistentes al desgaste.
- Dióxido de circonio (ZrO2): Conocido por su alta resistencia a la fractura y sus propiedades de aislamiento térmico, el ZrO2 es ideal para revestimientos de barrera térmica y cerámicas estructurales.
Aplicaciones de Oxicorte a alta velocidad (HVOF)
La versatilidad de la pulverización HVOF la hace adecuada para una amplia gama de aplicaciones en diversas industrias. Exploremos dónde está teniendo un impacto significativo esta tecnología:
Industria | Aplicaciones | Beneficios |
---|---|---|
Aeroespacial | Palas de turbina, trenes de aterrizaje, componentes de motor | Mayor resistencia al desgaste y rendimiento a altas temperaturas |
Automoción | Piezas de motor, pistones, turbocompresores | Mayor durabilidad, menor fricción |
Petróleo y gas | Tubos de perforación, válvulas, bombas | Resistencia a la corrosión, mayor vida útil |
Generación de energía | Componentes de turbinas, tubos de calderas | Recubrimientos de barrera térmica, resistencia a la oxidación |
Médico | Implantes ortopédicos, instrumentos quirúrgicos. | Biocompatibilidad, mayor resistencia al desgaste |
Procesado químico | Recipientes de reactores, intercambiadores de calor | Resistencia a la corrosión, estabilidad química |
Marina | Ejes de hélice, timones, estructuras offshore | Protección contra la corrosión, mantenimiento reducido |
Electrónica | Equipos semiconductores, conectores eléctricos | Aislamiento eléctrico, resistencia al desgaste |
Minería | Brocas, trituradoras, componentes de transportadores | Mayor resistencia al desgaste, menor tiempo de inactividad |
Fabricación | Moldes, matrices, herramientas de corte | Mayor vida útil de la herramienta, mayor precisión |
Ventajas de los revestimientos HVOF en diferentes industrias
- Aeroespacial: Los revestimientos HVOF son esenciales para mejorar el rendimiento y la longevidad de los álabes de las turbinas, los trenes de aterrizaje y los componentes de los motores, ya que ofrecen resistencia al desgaste y a las altas temperaturas.
- Automóvil: Las piezas del motor, los pistones y los turbocompresores se benefician de los revestimientos HVOF al conseguir una mayor durabilidad y una reducción de la fricción, lo que se traduce en una mayor eficiencia del combustible y un mejor rendimiento.
- Petróleo y gas: En este sector, los revestimientos HVOF protegen de la corrosión las tuberías, válvulas y bombas de perforación, prolongando considerablemente su vida útil y reduciendo los costes de mantenimiento.
- Generación de energía: Los componentes de las turbinas y los tubos de las calderas revestidos con materiales HVOF presentan propiedades superiores de barrera térmica y resistencia a la oxidación, lo que mejora la eficiencia global.
- Médico: Los implantes ortopédicos y los instrumentos quirúrgicos recubiertos con materiales HVOF biocompatibles experimentan una mayor resistencia al desgaste y longevidad, lo que garantiza mejores resultados para los pacientes.
- Procesamiento químico: Los recipientes de reactores y los intercambiadores de calor se benefician de los revestimientos HVOF por su excelente resistencia a la corrosión y estabilidad química, lo que garantiza un funcionamiento seguro y eficaz.
- Marina: Los revestimientos HVOF protegen los ejes de las hélices, los timones y las estructuras marinas de las inclemencias del entorno marino, reduciendo las necesidades de mantenimiento y prolongando la vida útil.
- Electrónica: Los equipos semiconductores y los conectores eléctricos se benefician del aislamiento eléctrico y la resistencia al desgaste que proporcionan los revestimientos HVOF, garantizando un rendimiento fiable.
- Minería: Las brocas de perforación, las trituradoras y los componentes de las cintas transportadoras revestidos con materiales HVOF presentan una mayor resistencia al desgaste, lo que reduce el tiempo de inactividad y mejora la productividad.
- Fabricación: Los moldes, matrices y herramientas de corte con recubrimientos HVOF disfrutan de una mayor vida útil y una mayor precisión, lo que se traduce en productos de mayor calidad y menores costes operativos.
Ventajas y desventajas de Oxicorte a alta velocidad (HVOF)
Ventajas | Desventajas |
---|---|
Gran resistencia al desgaste | Elevado coste de instalación inicial |
Excelente fuerza de adherencia | Requiere operarios cualificados |
Revestimientos de baja porosidad | El mantenimiento de los equipos puede ser complejo |
Versatilidad de materiales | Limitado a aplicaciones con visibilidad directa |
Alta resistencia térmica y a la corrosión | Posibilidad de tensiones térmicas en algunos materiales |
Control preciso del espesor del revestimiento | Requiere una preparación minuciosa del sustrato |
Respetuoso con el medio ambiente en comparación con otros métodos | No apto para piezas muy grandes |
Mínima preparación de la superficie necesaria para algunos revestimientos | El proceso puede ser ruidoso y producir humos |
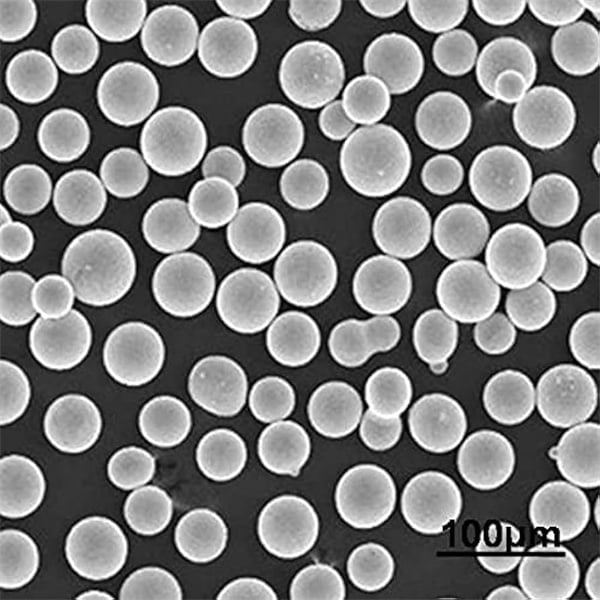
Análisis detallado de la pulverización HVOF
- Ventajas:
- Alta resistencia al desgaste: Los revestimientos HVOF son conocidos por su excepcional resistencia al desgaste, lo que los hace ideales para aplicaciones sometidas a alta abrasión y fricción.
- Excelente fuerza de adherencia: Las velocidades supersónicas que se alcanzan en la pulverización HVOF dan como resultado revestimientos con una excelente fuerza de adherencia, lo que garantiza que se adhieran bien al sustrato.
- Revestimientos de baja porosidad: El proceso produce revestimientos con baja porosidad, lo que aumenta su durabilidad y resistencia a los factores ambientales.
- Opciones de materiales versátiles: La pulverización HVOF puede utilizarse con una amplia gama de materiales, incluidos metales, cerámicas y carburos, lo que la hace adecuada para diversas aplicaciones.
- Alta resistencia térmica y a la corrosión: Los revestimientos HVOF ofrecen una resistencia superior a las altas temperaturas y los entornos corrosivos, lo que prolonga la vida útil de los componentes revestidos.
- Control preciso del grosor del revestimiento: El proceso permite controlar con precisión el grosor del revestimiento, garantizando su uniformidad y consistencia.
- Respetuoso con el medio ambiente: En comparación con otros métodos de revestimiento, la pulverización HVOF es relativamente respetuosa con el medio ambiente, ya que produce menos contaminantes.
- Mínima preparación de la superficie: Para algunos revestimientos, se necesita una preparación mínima de la superficie, lo que simplifica el proceso de aplicación.
- Desventajas:
- Alto coste inicial de instalación: El equipo y la configuración necesarios para la pulverización HVOF pueden ser caros, lo que puede suponer un obstáculo para algunas empresas.
- Se necesitan operarios cualificados: El proceso requiere operarios cualificados para garantizar la calidad y consistencia de los revestimientos.
- Mantenimiento de equipos complejos: El mantenimiento de los equipos de pulverización HVOF puede ser complejo y requiere una atención periódica para garantizar un rendimiento óptimo.
- Aplicación limitada a la línea de visión: La pulverización HVOF está limitada a aplicaciones en línea recta, lo que puede restringir su uso en determinadas geometrías complejas.
- Potencial de tensiones térmicas: Algunos materiales pueden sufrir tensiones térmicas durante el proceso de pulverización HVOF, lo que puede afectar a su rendimiento.
- Se requiere una preparación minuciosa del sustrato: A menudo es necesaria una preparación minuciosa del sustrato para obtener los mejores resultados de revestimiento, lo que aumenta el tiempo del proceso.
- No apto para piezas muy grandes: El proceso puede no ser adecuado para piezas muy grandes, lo que limita su uso en determinadas aplicaciones.
- Ruidoso y productor de humos: La pulverización HVOF puede ser ruidosa y producir humos, por lo que es necesario adoptar medidas de seguridad y ventilación adecuadas.
Especificaciones y normas para la pulverización HVOF
Especificación | Detalles |
---|---|
Espesor del revestimiento | Normalmente oscila entre 50 micras y varios milímetros |
Porosidad | Generalmente inferior a 1% |
Fuerza de adhesión | Supera los 10.000 psi (68,95 MPa) |
Dureza | Varía en función del material, por ejemplo, los revestimientos de WC-Co pueden alcanzar hasta 1500 HV |
Acabado superficial | Valores Ra alcanzables tan bajos como 0,5 micras |
Tasa de deposición | Normalmente 1-10 kg/hora, dependiendo del material y los parámetros |
Temperatura máxima de funcionamiento | Puede superar los 1000°C, dependiendo del material |
Resistencia medioambiental | Excelente resistencia a la corrosión, la oxidación y el desgaste |
Tolerancias de aplicación | Puede controlarse dentro de ±0,025 mm para dimensiones críticas |
Cumplimiento de las normas | Cumple normas como ASTM, ISO, AMS y requisitos industriales específicos. |
Normas y certificaciones para revestimientos HVOF
Estándar | Descripción |
---|---|
ASTM C633 | Método de ensayo estándar para la resistencia a la adherencia o cohesión de revestimientos de proyección térmica |
ISO 14922 | Proyección térmica - Requisitos de calidad para los fabricantes |
AMS 2447 | Revestimientos por pulverización térmica, requisitos generales para aplicaciones aeroespaciales |
DIN EN 657 | Rociado térmico - Equipos, procesos y ensayos |
NACE RP0502 | Metodología de evaluación directa de la corrosión externa de tuberías |
SAE J2237 | Procesos de oxicorte de alta velocidad (HVOF) |
Proveedores y precios de los polvos metálicos HVOF
Proveedor | Polvo metálico | Precio (por kg) | Región | Datos de contacto |
---|---|---|---|---|
Tecnologías de superficie Praxair | Carburo de wolframio (WC) | $150 – $200 | Norteamérica, Europa | [email protected], +1-800-772-9247 |
Oerlikon Metco | Carburo de cromo (CrC) | $120 – $170 | Global | [email protected], +41-58-360-9600 |
Höganäs AB | Óxido de aluminio (Al2O3) | $50 – $80 | Global | [email protected], +46-10-516-5000 |
Kennametal Stellite | Stellite | $200 – $250 | Norteamérica, Europa | [email protected], +1-800-446-7738 |
Tecnología Carpenter | Inconel | $180 – $220 | Global | [email protected], +1-610-208-2000 |
HC Starck | Molibdeno (Mo) | $100 – $150 | Norteamérica, Europa | [email protected], +1-617-630-5800 |
AMETEK Metales especiales | Níquel-cromo (NiCr) | $130 – $170 | Norteamérica | [email protected], +1-610-647-2121 |
Materiales Sandvik | Acero inoxidable (316L, 304) | $80 – $120 | Global | [email protected], +46-8-456-1100 |
Treibacher Industrie AG | Dióxido de titanio (TiO2) | $70 – $110 | Europa | [email protected], +43-42-77-2666-0 |
Saint-Gobain | Dióxido de circonio (ZrO2) | $90 – $140 | Global | [email protected], +33-1-47-62-30-00 |
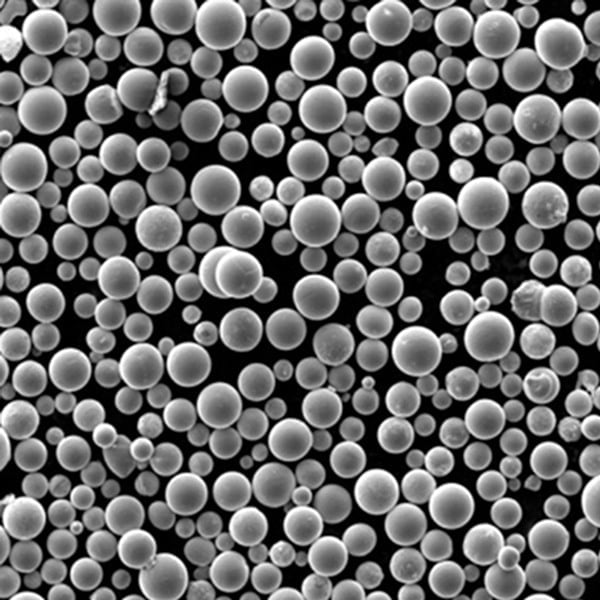
Comparación de la pulverización HVOF con otros métodos de recubrimiento
Método de recubrimiento | Ventajas | Desventajas |
---|---|---|
Pulverización HVOF | Alta resistencia al desgaste, baja porosidad, versátil | Coste inicial elevado, se necesitan operarios cualificados |
Pulverización de plasma | Puede alcanzar temperaturas más altas, bueno para la cerámica | Mayor porosidad, menor fuerza de adherencia |
Pulverización en frío | Oxidación mínima, baja tensión térmica | Menor fuerza de adherencia, opciones de material limitadas |
Rociado con llama | Equipos rentables y sencillos | Mayor porosidad, menor fuerza de adherencia |
Pulverización por detonación | Velocidades extremadamente altas, revestimientos muy densos | Proceso complejo, coste elevado |
Galvanoplastia | Excelente resistencia a la corrosión, rentable | Limitado a materiales conductores, problemas medioambientales |
Deposición física de vapor (PVD) | Alta precisión, revestimientos finos | Caro, grosor limitado |
Deposición química en fase vapor (CVD) | Bueno para formas complejas, revestimientos uniformes | Proceso a alta temperatura, caro |
Galvanización | Excelente resistencia a la corrosión, rentable | Limitado a zinc y aleaciones, problemas de control de espesor |
Pulverización HVOF vs. Plasma
- Ventajas: La pulverización HVOF proporciona revestimientos más densos con menor porosidad en comparación con la pulverización de plasma, lo que se traduce en una resistencia al desgaste y una fuerza de adherencia superiores.
- Desventajas: La pulverización de plasma puede alcanzar temperaturas más elevadas, lo que la hace más adecuada para determinados revestimientos cerámicos. Sin embargo, los revestimientos pulverizados con plasma suelen tener mayor porosidad y menor fuerza de adherencia.
HVOF frente a pulverización en frío
- Ventajas: La pulverización HVOF ofrece una mayor fuerza de adherencia y una gama más amplia de opciones de materiales en comparación con la pulverización en frío.
- Desventajas: La pulverización en frío induce una tensión térmica y una oxidación mínimas, lo que la hace adecuada para materiales sensibles, pero generalmente proporciona una menor fuerza de adherencia.
Preguntas frecuentes
Pregunta | Respuesta |
---|---|
¿Qué es la pulverización HVOF? | Oxicorte a alta velocidad (HVOF) es un proceso de revestimiento por pulverización térmica que utiliza chorros de gas de alta velocidad para aplicar revestimientos duraderos y densos. |
¿Qué materiales pueden utilizarse en la pulverización HVOF? | Una variedad de materiales que incluyen metales, cerámicas y carburos como el carburo de tungsteno, el carburo de cromo, el óxido de aluminio, etc. |
¿Cuáles son las ventajas de los revestimientos HVOF? | Entre sus ventajas se incluyen una elevada resistencia al desgaste, excelente fuerza de adherencia, baja porosidad y alta resistencia térmica y a la corrosión. |
¿Qué industrias utilizan la pulverización HVOF? | Industrias como la aeroespacial, automoción, petróleo y gas, generación de energía, médica, procesamiento químico, marina, electrónica y minería. |
¿Cómo se compara la pulverización HVOF con otros métodos? | El HVOF ofrece revestimientos más densos y una mayor resistencia al desgaste en comparación con métodos como la pulverización de plasma, aunque tiene unos costes iniciales más elevados. |
¿Cuáles son las limitaciones de la pulverización HVOF? | Limitaciones |
Compartir
MET3DP Technology Co., LTD es un proveedor líder de soluciones de fabricación aditiva con sede en Qingdao, China. Nuestra empresa está especializada en equipos de impresión 3D y polvos metálicos de alto rendimiento para aplicaciones industriales.
Solicite información para obtener el mejor precio y una solución personalizada para su empresa.
Artículos relacionados
Acerca de Met3DP
Actualización reciente
Nuestro producto
CONTACTO
¿Tiene alguna pregunta? ¡Envíenos un mensaje ahora! Atenderemos su solicitud con todo un equipo tras recibir su mensaje.
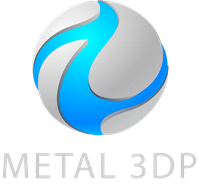
Polvos metálicos para impresión 3D y fabricación aditiva