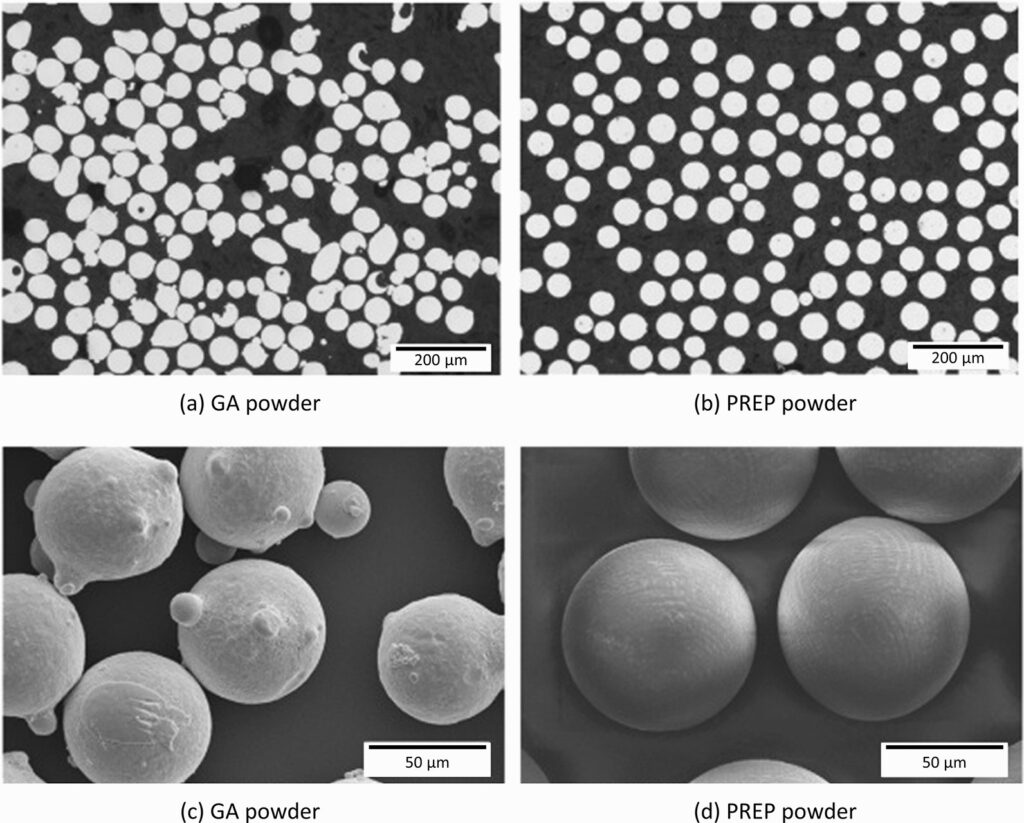
Polvo IN600: descubra sus propiedades superiores y sus infinitos usos
MOQ bajo
Proporcionamos una cantidad mínima de pedido baja para satisfacer diferentes necesidades.
OEM Y ODM
Proporcionar productos y servicios de diseño personalizados para satisfacer las necesidades exclusivas de los clientes.
Existencias adecuadas
Garantizar una tramitación rápida de los pedidos y ofrecer un servicio fiable y eficaz.
Satisfacción del cliente
Ofrecer productos de alta calidad centrados en la satisfacción del cliente.
compartir este artículo
Índice
Cuando se trata de materiales de alto rendimiento que puedan soportar entornos extremos, Polvo IN600 es una de las mejores opciones disponibles hoy en día. Conocida por su notable resistencia a oxidación, corrosióny altas temperaturasEsta aleación a base de níquel es una solución ideal para industrias como procesamiento químico, aeroespacial, energía nuclear, y muchos más.
En este guía completaVamos a profundizar en todo lo que necesitas saber sobre Polvo IN600-de su composición y propiedades mecánicas a su aplicaciones, preciosy comparaciones con otros materiales. Ya sea ingeniero, especialista en adquisiciones o alguien interesado en materiales avanzados, esta guía le ayudará a comprender por qué Polvo IN600 Es una aleación muy versátil y ampliamente utilizada.
Descripción general del polvo IN600
Polvo IN600 También se conoce como Aleación 600 o Níquel 600Es un aleación de níquel-cromo-hierro que es altamente resistente a una amplia variedad de corrosivo medios de comunicación y ambientes oxidantesSu capacidad para funcionar en condiciones extremas lo convierte en una opción popular para aplicaciones en tratamiento térmico, manipulación de productos químicosy operaciones de alta temperatura.
Características principales
- Resistencia a la corrosión: Excelente resistencia a cloruros, ácidos oxidantesy compuestos orgánicos/inorgánicos.
- Estabilidad térmica:Mantiene la fuerza y la integridad en temperaturas elevadas hasta 1093°C (2000°F).
- Aplicaciones versátiles: Adecuado para pulvimetalurgia, Impresión 3D, pulverización térmicay fundición.
- Robustez mecánica:Ofrece buenas propiedades mecánicas incluso bajo estrés y entornos de alta temperatura.
Vamos a profundizar en el tema. composición y propiedades de Polvo IN600 para entender lo que lo hace tan único.
Composición y propiedades clave del polvo IN600
En composición química de Polvo IN600 es lo que le da su alto rendimiento en diversos entornos exigentes. Se compone principalmente de níquel, con cantidades significativas de cromo y hierro, entre otros elementos que contribuyen a su fuerza y resistencia a la oxidación.
Composición química
Elemento | Porcentaje (%) | Papel en la aleación |
---|---|---|
Níquel (Ni) | 72.0 min | Elemento base que proporciona una superioridad resistencia a la corrosión y propiedades a alta temperatura. |
Cromo (Cr) | 14.0-17.0 | Proporciona resistencia a la oxidación y mejora el rendimiento en corrosivo entornos. |
Hierro (Fe) | 6.0-10.0 | Añade mecánica fuerza y contribuye a la capacidad de la aleación para manejar estrés a temperaturas elevadas. |
Manganeso (Mn) | 1,0 máx. | Mejora soldabilidad y ayuda a mantener integridad estructural. |
Silicio (Si) | 0,5 máx. | Mejora la resistencia de la aleación a oxidación y mejora colabilidad. |
Carbono (C) | 0,15 máx. | Ayuda a mejorar dureza mecánica y fuerzaespecialmente en altas temperaturas. |
Azufre (S) | 0,015 máx. | Se mantiene al mínimo para evitar fragilización y mantener ductilidad. |
Cobre (Cu) | 0,5 máx. | Proporciona resistencia a la corrosiónespecialmente en entornos marinos. |
Propiedades mecánicas y térmicas
Polvo IN600 está diseñado para mantener su integridad en alto estrés y alta temperatura aplicaciones. A continuación se muestran las mecánico y propiedades térmicas que lo convierten en uno de los materiales más confiables para condiciones extremas.
Propiedad | Valor/Descripción |
---|---|
Densidad | 8,42 g/cm³ |
Punto de fusión | 1370-1425°C |
Resistencia a la tracción | 550 MPa a temperatura ambiente |
Límite elástico | 240 MPa a temperatura ambiente |
Alargamiento a la rotura | 35% |
Resistencia a la fluencia | Excelente, hasta 870°C |
Conductividad térmica | 14,9 W/m·K |
Resistencia a la oxidación | Funciona bien en entornos oxidativos hasta 1093 °C |
Soldabilidad | Bueno, pero requiere precalentamiento y tratamientos térmicos post-soldadura para evitar el agrietamiento |
Ventajas del polvo IN600: ¿Qué lo hace destacar?
Quizá se pregunte qué hace que Polvo IN600 ¿Es tan especial y por qué deberías considerarlo para tu próximo proyecto? Bueno, hay varias... principales ventajas que lo diferencian de otras aleaciones.
1. Excelente resistencia a la corrosión
Gracias a su alto níquel y cromo contenido, Polvo IN600 es altamente resistente a una amplia gama de ambientes corrosivosincluyendo cloruros, vapory ácidos oxidantes. Esto lo hace ideal para plantas de transformación química, reactores nuclearesy aplicaciones marinas donde los materiales están constantemente expuestos a elementos agresivos.
2. Rendimiento a altas temperaturas
Polvo IN600 puede mantener integridad mecánica y resistencia a la oxidación a temperaturas de hasta 1093 °C (2000 °F). Esto lo hace invaluable para aplicaciones como turbinas de gas, hornosy intercambiadores de calor, donde los materiales deben soportar una exposición prolongada al calor extremo.
3. Opciones de fabricación versátiles
Tanto si utiliza fundición tradicional, pulvimetalurgiao fabricación aditiva técnicas como Impresión 3D, Polvo IN600 es altamente adaptable. Su morfología esférica y granulometría homogénea Su distribución lo hace ideal para pulverización térmica procesos y sinterizado directo de metales por láser (DMLS).
4. Excelente resistencia mecánica
Incluso en entornos de alta temperatura, Polvo IN600 conserva su integridad estructuralEsto lo convierte en un material de referencia para aplicaciones de alto estrés donde resistencia al deslizamiento y durabilidad a largo plazo son fundamentales.
Aplicaciones del polvo IN600: ¿Dónde se utiliza?
Dadas sus propiedades excepcionales, el polvo IN600 se utiliza en algunas de las industrias más sectores exigentes. Echemos un vistazo más de cerca al aplicaciones Donde esta aleación realmente brilla.
Usos comunes por industria
Industria | Aplicación |
---|---|
Aeroespacial | Palas de turbina de gas, postquemadoresy sistemas de escape requiriendo resistencia a la oxidación a alta temperatura. |
Procesado químico | Tuberías, vasosy intercambiadores de calor utilizado en el manejo productos químicos corrosivos como ácido sulfúrico y cloruros. |
Energía nuclear | Generadores de vapor, barras de controly intercambiadores de calor en reactores nucleares donde tanto la resistencia a la corrosión como al calor son cruciales. |
Tratamiento térmico | Componentes del horno, silenciadoresy retortas utilizados en entornos de alta temperatura. |
Industria naval | Intercambiadores de calor, válvulasy tuberías sistemas expuestos a agua de mar y atmósferas marinas. |
Impresión 3D | Fabricación aditiva de geometrías complejas para piezas de alto rendimiento en aeroespacial y sectores energéticos. |
Especificaciones, tamaños y estándares del polvo IN600
Antes de decidirte a comprar Polvo IN600es importante comprender los distintos especificaciones, tallasy normas que se aplican a este material. Estos factores pueden influir significativamente en su rendimiento y idoneidad para su aplicación específica.
Especificaciones
Especificación | Detalles |
---|---|
Tamaño de las partículas | Normalmente oscila entre 15 a 45 micras para pulvimetalurgia y fabricación aditiva. |
Morfología del polvo | En general esférica para una fluidez superior en Impresión 3D y pulverización térmica aplicaciones. |
Normas ASTM | ASTM B168 Para láminas y placas de aleaciones de níquel-cromo-hierro. |
Normas ISO | ISO 15156 para aleaciones resistentes a la corrosión utilizadas en entornos de gas ácido. |
Número UNS | UNS N06600 |
Normas AMS | AMS 5540, para aleaciones de níquel-cromo-hierro utilizadas en aeroespacial y aplicaciones de alta temperatura. |
Estas normas garantizan que Polvo IN600 que está comprando cumple con los umbrales requeridos para rendimiento y fiabilidad en su industria específica.
Proveedores y precios del polvo IN600
Precios para Polvo IN600 Puede variar en función de varios factores como proveedor, tamaño de las partículasy volumen de pedidosA continuación se presentan algunos de los proveedores más conocidos y sus rangos de precios aproximados para esta aleación de alto rendimiento.
Proveedores y precios
Proveedor | Gama de precios (por kg) | Notas |
---|---|---|
Höganäs AB | $600 – $850 | Se especializa en polvos metálicos para fabricación aditiva y pulverización térmica aplicaciones. |
Tecnología Carpenter | $620 – $880 | Ofrece tamaños de partículas y formulaciones personalizadas para pulvimetalurgia y Impresión 3D. |
Oerlikon Metco | $610 – $870 | Proporciona polvo IN600 para pulverización térmica recubrimientos y fabricación aditiva. |
Sandvik | $630 – $890 | Suministra materiales avanzados para industrias como aeroespacial y petróleo y gas. |
Kennametal | $620 – $880 | Se centra en aleaciones de níquel de alto rendimiento para aplicaciones exigentes. |
El precio por Polvo IN600 suele oscilar entre $600 a $890 por kilogramoen función del proveedor y específico tamaño de las partículas requisitos.
Comparación de las ventajas y desventajas del polvo IN600
Antes de tomar una decisión, es importante sopesar las ventajas y limitaciones de Polvo IN600Si bien ofrece numerosos beneficios, hay algunos inconvenientes que deben tenerse en cuenta dependiendo de su aplicación.
Ventajas
Ventaja | Descripción |
---|---|
Resistencia a la corrosión:Rendimiento superior en una amplia gama de ambientes corrosivos. | Ideal para su uso en procesamiento químico y aplicaciones marinas. |
Estabilidad a altas temperaturas: Mantiene las propiedades mecánicas a temperaturas elevadas. | Perfecto para turbinas de gas, intercambiadores de calory componentes del horno. |
Fabricación versátil: Adecuado para Impresión 3D, pulverización térmicay pulvimetalurgia. | Permite geometrías complejas y piezas de alto rendimiento. |
Resistencia a la oxidación:Se desempeña bien en ambientes oxidativos hasta 1093 °C. | Útil en aplicaciones de alta temperatura como hornos y turbinas de gas. |
Resistencia mecánica:Mantiene las propiedades mecánicas bajo estrés y calor intenso. | Garantiza durabilidad a largo plazo en aplicaciones exigentes. |
Limitaciones
Limitación | Descripción |
---|---|
Coste elevado: Más caro que muchos otros materiales. | Puede no ser adecuado para presupuesto sensible aplicaciones. |
Disponibilidad limitada: No siempre disponible en grandes cantidades. | Puede dar lugar a plazos de entrega más largosespecialmente para fórmulas personalizadas o grandes pedidos. |
Desafío para la máquina: Requiere herramientas especializadas para el mecanizado de precisión. | Puede aumentar tiempo de mecanizado y costesespecialmente para piezas complejas. |
Oxidación a temperaturas muy elevadas: La oxidación puede convertirse en un problema por encima de 1093 °C. | Puede ser necesario revestimientos o tratamientos especiales para límites extremos de temperatura superior. |
Preguntas frecuentes
A continuación se presentan algunas de las preguntas más frecuentes sobre Polvo IN600, junto con respuestas breves pero informativas para ayudarle a comprender mejor este material.
Pregunta | Respuesta |
---|---|
¿Para qué se utiliza el polvo IN600? | Suele utilizarse en aeroespacial, procesamiento químicoy energía nuclear aplicaciones donde alta temperatura y resistencia a la corrosión son necesarios. |
¿Cuanto cuesta el polvo IN600? | El precio del mismo oscila entre $600 a $890 por kilogramoen función del proveedor y tamaño de las partículas. |
¿Se puede utilizar el polvo IN600 en la impresión 3D? | Sí, se utiliza mucho en fabricación aditiva procesos como sinterizado directo de metales por láser (DMLS) y fusión por haz de electrones (EBM). |
¿Qué industrias utilizan el polvo IN600? | Industrias como aeroespacial, procesamiento químico, energía nucleary aplicaciones marinas Lo uso comúnmente para alto rendimiento aplicaciones. |
¿Qué hace que el polvo IN600 sea resistente a la corrosión? | La alta níquel y cromo El contenido de IN600 proporciona una excelente resistencia a ácidos oxidantes, clorurosy entornos de alta temperatura. |
¿Cuáles son las principales ventajas del polvo IN600? | Ofrece estabilidad a altas temperaturas, resistencia a la corrosióny resistencia mecánicapor lo que es ideal para entornos extremos. |
¿Cuáles son las limitaciones del uso del polvo IN600? | Las principales limitaciones son alto coste y dificultad de mecanizadoque puede aumentar tiempo de producción y costes. |
¿El polvo IN600 es adecuado para entornos de alta temperatura? | Sí, el polvo IN600 puede soportar temperaturas de hasta 1093 °Cpor lo que es ideal para turbinas de gas, hornosy intercambiadores de calor. |
¿Puede el polvo IN600 soportar ambientes corrosivos? | Absolutamente. Gracias a su alto níquel y cromo contenido, IN600 proporciona una excelente resistencia a la corrosión en química y atmósferas marinas. |
Reflexiones finales: ¿Es el polvo IN600 adecuado para su proyecto?
Si busca un material que ofrezca excepcional resistencia a la corrosión, rendimiento a altas temperaturasy resistencia mecánica, Polvo IN600 es una de las mejores opciones del mercado. Su versatilidad en procesos de fabricación como Impresión 3D, pulverización térmicay fundición tradicional lo hace adaptable para diversas industrias, desde aeroespacial a procesamiento químico.
Aunque Polvo IN600 Puede que tenga un precio más alto en comparación con otros materiales, durabilidad a largo plazo y fiabilidad A menudo superan la inversión inicial. Ya sea que esté diseñando componentes de alto rendimiento para turbinas de gas, reactores nucleareso entornos químicos corrosivos, Polvo IN600 Puede satisfacer las demandas de sus proyectos más desafiantes.
En conclusión, si su proyecto requiere de materiales que puedan soportar condiciones extremas al tiempo que ofrece rendimiento duradero, Polvo IN600 es un contendiente de primer nivel que cumple en todos los frentes.
Obtener el último precio
Acerca de Met3DP
Categoría de productos
OFERTAS
CONTACTO
¿Tiene alguna pregunta? ¡Envíenos un mensaje ahora! Atenderemos su solicitud con todo un equipo tras recibir su mensaje.
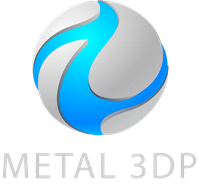
Polvos metálicos para impresión 3D y fabricación aditiva