Descripción general del polvo Inconel 718
Índice
Visión general de Inconel 718 Polvo
Inconel 718 es un polvo de superaleación a base de níquel-cromo que se utiliza para aplicaciones de alta resistencia a temperaturas elevadas. Las propiedades clave incluyen:
- Excelente resistencia hasta 700°C
- Alta resistencia a la corrosión y a la oxidación
- Buena resistencia a la fatiga y a la fluencia
- Capacidad para soportar temperaturas criogénicas.
- Compatibilidad con postprocesamiento como prensado isostático en caliente.
El polvo de Inconel 718 se usa ampliamente para fabricar componentes para la industria aeroespacial, de petróleo y gas, nuclear y otras industrias exigentes mediante la fabricación de aditivos metálicos o la pulvimetalurgia.
Tipos de polvo de Inconel 718
El polvo de Inconel 718 está disponible en diferentes distribuciones de tamaño de partículas, formas y métodos de producción:
Tipo | Descripción | Tamaño de las partículas | Forma | Método de producción |
---|---|---|---|---|
Gas atomizado | Polvo esferoidal irregular | 15-75 micras | Mayormente esférico | Atomización de gas |
Plasma atomizado | Polvo muy esférico | 15-45 μm | Muy esférica | Atomización por plasma |
Mezclado | Mezcla de polvos pulverizados y triturados con gas. | 15-150 μm | Morfología mixta | Mezcla mecánica |
aleado | Polvo prealeado con composición uniforme. | 15-105 micras | Esférica o irregular | Atomización por gas/plasma de masa fundida prealeada |
Los polvos esféricos y prealeados brindan mayor calidad pero cuestan más que las opciones mezcladas o atomizadas con gas. La elección depende de los requisitos de la aplicación.
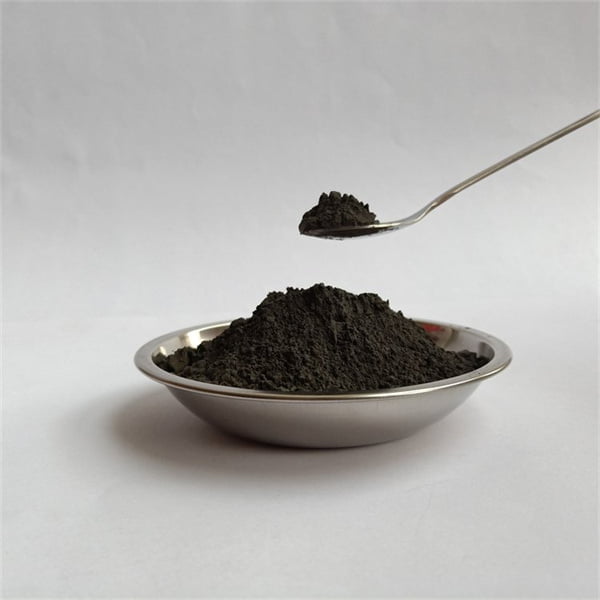
Propiedades y Composición del Inconel 718
Inconel 718 posee una combinación excepcional de propiedades mecánicas y resistencia a la corrosión:
Propiedad | Valor |
---|---|
Densidad | 8,19 g/cm3 |
Punto de fusión | 1260-1336°C |
Resistencia a la tracción | 1.103 – 1.551 MPa |
Límite elástico | 758 – 1.379 MPa |
Alargamiento | 12% mínimo |
Módulo de Young | 205 GPa |
Relación de Poisson | 0.29 |
Módulo de cizallamiento | 79 GPa |
Resistencia a la fatiga | 517 – 1.034MPa |
La composición nominal del Inconel 718 es:
- Níquel: 50-55%
- Cromo: 17-21%
- Hierro: Equilibrio
- Niobio: 4,75-5,5%
- Molibdeno: 2,8-3,3%
- Titanio: 0,65-1,15%
- Aluminio: 0,2-0,8%
Esta combinación de adiciones de níquel, cromo y niobio le da a Inconel 718 sus excelentes propiedades mecánicas a altas temperaturas.
Aplicaciones del polvo de Inconel 718
El polvo de Inconel 718 se usa ampliamente en:
- Aeroespacial: componentes del motor como palas de turbina, discos y sujetadores.
- Petróleo y gas: herramientas de fondo de pozo, válvulas y componentes de boca de pozo
- Generación de energía: piezas de la sección caliente de turbinas de gas, sujetadores
- Automoción: ruedas de turbocompresor, válvulas y componentes de motor.
- Procesamiento químico: recipientes de reactores, intercambiadores de calor, tuberías.
- Herramientas: moldes de inyección, matrices, accesorios de herramientas.
- Médico – Implantes ortopédicos por biocompatibilidad
Su alta resistencia a temperaturas elevadas, resistencia a la corrosión y estabilidad hacen de Inconel 718 un material ideal para componentes críticos en todas las industrias.
Beneficios del polvo Inconel 718
Las ventajas clave de usar el polvo Inconel 718 incluyen:
- Las piezas mantienen una alta resistencia y tenacidad hasta 700°C
- Resiste ambientes oxidantes, corrosivos y criogénicos.
- El doble de resistencia a la tracción en comparación con el acero inoxidable 316L.
- Excelentes propiedades de fatiga y rotura por fluencia.
- Se puede reforzar la precipitación mediante un tratamiento de envejecimiento.
- Fácilmente soldable para reparaciones y uniones.
- Resiste el agrietamiento durante el prensado isostático en caliente.
- Puede reutilizarse hasta 10 veces con un deterioro mínimo.
- Permite geometrías complejas que no son posibles mediante mecanizado.
- Reduce el peso de los componentes en comparación con las formas sólidas.
- Disminuye la relación compra-vuelo en relación con la palanquilla o las piezas forjadas.
Estas propiedades permiten mejoras sustanciales de rendimiento y ahorros de peso en los componentes.
Limitaciones de Inconel 718 Polvo
Algunas limitaciones al trabajar con polvo Inconel 718 incluyen:
- Alto coste de material en comparación con el acero y las aleaciones de titanio.
- Tamaño de pieza restringido según el volumen de construcción de la máquina aditiva
- Susceptible a la oxidación y la corrosión por encima de 700°C
- Requiere prensado isostático en caliente después de la fabricación aditiva para aliviar las tensiones.
- Difícil de densificar completamente durante la fusión del lecho de polvo con láser
- El posprocesamiento, como el mecanizado, puede ser un desafío debido al endurecimiento por trabajo.
- Se requiere acabado de superficie para lograr la rugosidad deseada.
- Requiere manipulación y almacenamiento de polvo seco para evitar la contaminación.
- Número limitado de proveedores calificados en comparación con aleaciones más comunes
Principios de diseño para piezas de Inconel 718
Pautas de diseño clave para componentes de Inconel 718 fabricados a partir de polvo:
- Se recomienda un espesor mínimo de pared de 2 mm para una resistencia adecuada.
- Incluya chaflanes y filetes para minimizar las concentraciones de tensión.
- Los canales internos deben tener ≥ 2 mm de diámetro para la eliminación del polvo.
- Limitar los voladizos sin soportes a no más de 10 mm.
- Optimice la orientación de la construcción para minimizar los soportes y la altura total.
- Permitir una contracción isotrópica de ~20% durante la sinterización
- Tiene en cuenta una menor precisión y una mayor rugosidad superficial que las piezas mecanizadas.
- Diseño para una eliminación más sencilla del polvo al incluir aberturas
- Permitir stock de mecanizado adicional si se necesita alta precisión dimensional o acabado superficial.
La simulación de construcciones en las primeras etapas del proceso de diseño ayuda a identificar cualquier problema antes de la fabricación.
Parámetros de proceso para Inconel 718 AM
Los parámetros críticos para la fabricación aditiva de Inconel 718 incluyen:
- Potencia del láser: 100-500 W
- Velocidad de escaneo: Hasta 10 m/s
- Diámetro del haz: 50-100 μm
- Grosor de la capa: 20-50 μm
- Espacio entre escotillas: 50-200 μm
- Estrategia de escaneo: alternar entre capas
- Gas de protección: argón o nitrógeno
- Caudal de gas: 2-8 L/min
- Temperatura de la placa de construcción: 60-100°C
- Postprocesamiento: prensado isostático en caliente, tratamiento térmico.
Estos parámetros deben optimizarse con precisión para obtener componentes densos con la microestructura y propiedades mecánicas deseadas.
Postprocesamiento de piezas de Inconel 718
Los pasos típicos de posprocesamiento para los componentes de Inconel 718 AM incluyen:
- Eliminación de polvo suelto mediante granallado con perlas de plástico
- Tratamiento térmico para aliviar el estrés a 1080°C durante 1 hora seguido de enfriamiento por aire
- Prensado isostático en caliente a 1120°C durante 4 horas bajo una presión de 100 MPa
- Electroerosión por hilo para retirar piezas de la placa de construcción
- Mecanizado CNC: fresado, taladrado y torneado para mejorar el acabado y la precisión
- Mejora de la superficie: esmerilado, lijado, pulido
- Granallado para inducir tensiones de compresión en superficies.
- Pruebas de calidad: tracción, dureza, microestructura, fractografía.
Un posprocesamiento adecuado es vital para lograr las propiedades del material requeridas por la aplicación.
Pruebas de control de calidad para Inconel 718
Las pruebas integrales de control de calidad garantizan la calidad del polvo y de las piezas impresas:
- Análisis químico: ICP-OES confirma que la composición del polvo cumple con la especificación AMS
- Distribución del tamaño de partículas de polvo: analizador de tamaño de partículas por difracción láser
- Morfología del polvo: las imágenes SEM verifican la forma esférica del polvo
- Microestructura del polvo: mapeo EBSD de la estructura del grano
- Fluidez del polvo: medida mediante pruebas de embudo Hall y Carney
- Análisis de densidad: la picnometría de helio y el método de Arquímedes verifican una densidad >99,51 TP3T
- Ensayos mecánicos: ensayos de tracción, fatiga, tenacidad a la fractura y dureza.
- Microestructura: tamaño de grano y distribución de fases mediante microscopía óptica y SEM.
- Análisis de defectos: las radiografías y las tomografías computarizadas verifican si hay defectos internos
- Rugosidad de la superficie: medida con un lápiz óptico o un perfilómetro óptico
Las pruebas exhaustivas garantizan que las piezas de Inconel 718 cumplan con estrictos estándares aeroespaciales e industriales.
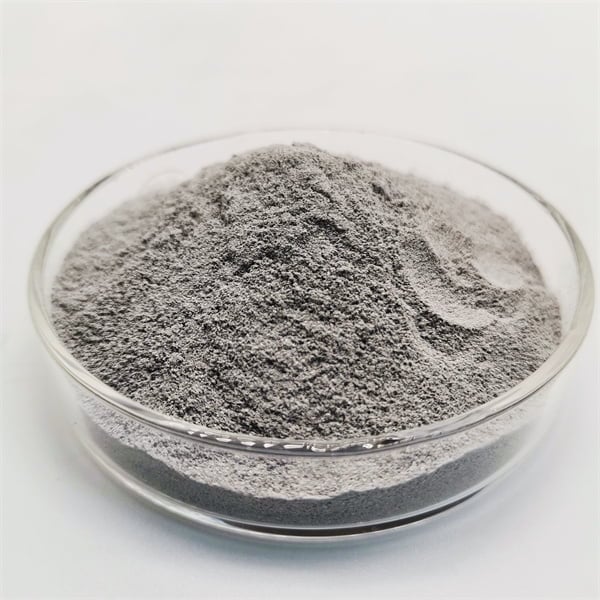
Análisis de Costos Inconel 718 AM
Los costos asociados con la producción de Inconel 718 AM incluyen:
- Costo de la máquina – $500.000 a $1 millones para un sistema AM de calidad
- Coste del material – $350-500/kg para polvo virgen Inconel 718
- Coste laboral – Operadores capacitados para ejecutar la construcción y el posprocesamiento
- Costo energético – Gran consumo de electricidad durante las construcciones.
- Tratamiento posterior – HIP, mecanizado y otros costos de acabado
- Control de calidad – Gastos de ensayos y caracterización.
- Reutilizabilidad – El polvo no utilizado se puede reciclar para reducir los costos de material.
- Volumen de pedidos – Los pedidos de mayor volumen proporcionan beneficios de economía de escala
- Ratio de compra por vuelo – Debe considerar el polvo no utilizado que debe reciclarse.
- Geometría de la pieza – Las piezas bien diseñadas maximizan la utilización del material
Para la producción de volumen medio-bajo, la fabricación aditiva se vuelve rentable en comparación con el mecanizado sustractivo debido al ahorro de material y la reducción de la relación compra-venta.
Seleccionando un Inconel 718 Polvo Proveedor
Factores clave al seleccionar un proveedor de polvo Inconel 718:
- Experiencia técnica en atomización por gas y plasma de superaleaciones de níquel.
- Gama de tamaños y morfologías de polvo disponibles: esféricos, mezclados y aleados
- Procedimientos y certificaciones de aseguramiento de la calidad: ISO 9001, AS9100, etc.
- Capacidad para realizar análisis químicos y pruebas de distribución del tamaño de partículas.
- Capacidad para entregar grandes cantidades de polvo con plazos de entrega cortos
- Capacidades de personalización, como el tamizado según distribuciones de tamaño de partículas específicas.
- Precios competitivos y estables, especialmente para pedidos de grandes cantidades.
- Capacidad para cumplir con las normativas si es necesario: ITAR, REACH, RoHS
- Muestras para la calificación y pruebas de polvo del cliente.
- Soporte técnico para manipulación y almacenamiento de polvo.
- Proximidad geográfica para una logística y soporte más rápidos
Los proveedores establecidos con experiencia especializada en polvos de aleaciones de níquel tienden a satisfacer mejor las necesidades de los usuarios en términos de calidad, personalización, precios y soporte.
Pros y contras del Inconel 718 frente al acero inoxidable
Ventajas del Inconel 718:
- El doble de resistencia a la tracción que el acero inoxidable 316L.
- Resistencia a la fluencia y a la fatiga significativamente mayor
- Resiste la oxidación y la corrosión hasta 700°C.
- Mejor vida a fatiga de ciclos elevados que los aceros
- Propiedades consistentes debido a la composición de la aleación de níquel.
- Puede endurecerse por envejecimiento a diferencia de los aceros inoxidables estándar.
- Produce enlaces más fuertes cuando se aplica como recubrimiento de materia prima.
- Más fácil de reciclar y reutilizar el polvo no utilizado
Desventajas del Inconel 718:
- Costo de material mucho mayor que el de los aceros inoxidables.
- Temperatura máxima de funcionamiento más baja que la del acero inoxidable.
- Más difícil de densificar completamente durante la impresión AM
- Desafiante para la máquina debido al endurecimiento por trabajo
- Número limitado de proveedores cualificados
- Susceptible a la fragilización del metal líquido durante la mañana.
- Mayores requisitos de posprocesamiento: HIP, tratamiento térmico
- Requiere procesamiento en atmósfera inerte controlada
Para aplicaciones críticas donde el rendimiento supera las consideraciones de costo, Inconel 718 proporciona propiedades de alta temperatura notablemente superiores en comparación con los aceros inoxidables.
Comparación de Inconel 718 vs Inconel 625
Inconel 718 y 625 tienen las siguientes características distintivas:
Aleación | Fuerza | Resistencia a la corrosión | Soldabilidad | Coste | Usar temperatura |
---|---|---|---|---|---|
Inconel 718 | Muy alta | Moderado | Feria | Alta | Hasta 700°C |
Inconel 625 | Medio | Excelente | Excelente | Muy alta | Hasta 980°C |
- Inconel 718 ofrece una resistencia a la tracción, a la fluencia y a la fatiga mucho mayor.
- Inconel 625 proporciona una mejor resistencia general a la corrosión y la oxidación.
- Inconel 625 tiene una soldabilidad excepcional, mientras que Inconel 718 es más desafiante.
- Inconel 625 es más costoso debido a las amplias adiciones de aleación de columbium.
- Inconel 625 tiene una temperatura máxima de servicio más alta.
Se prefiere Inconel 718 para las aplicaciones de alta resistencia más exigentes, como componentes aeroespaciales, mientras que se selecciona Inconel 625 cuando la resistencia a la corrosión es el requisito principal.
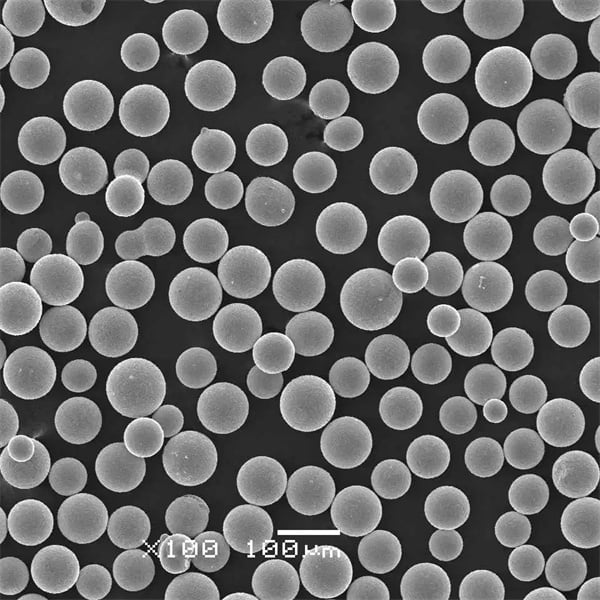
PREGUNTAS FRECUENTES
¿Qué distribución de tamaño de partícula se recomienda para AM con polvo de Inconel 718?
Generalmente se recomienda un rango de tamaño de partícula de 15 a 45 micrones con una mayoría entre 20 y 35 micrones para la fusión de lecho de polvo por láser con Inconel 718 para permitir una buena fluidez y una compactación densa.
¿Cuáles son algunos tratamientos térmicos de posprocesamiento utilizados para las piezas de Inconel 718 AM?
Los tratamientos térmicos comunes incluyen recocido en solución a 1270 °C, endurecimiento por precipitación a 960 °C y alivio de tensiones a 1080 °C. Los tratamientos de envejecimiento en varios pasos pueden mejorar aún más la resistencia y la ductilidad.
¿Cuáles son algunas aplicaciones típicas del polvo Inconel 718 en el sector aeroespacial?
Inconel 718 se usa ampliamente para fabricar componentes de motores de aviones como palas, discos, sujetadores, carcasas y piezas de trenes de aterrizaje que requieren alta resistencia a temperaturas elevadas y en ambientes corrosivos.
¿Inconel 718 requiere prensado isostático en caliente después de la mañana?
Sí, se recomienda encarecidamente HIP después de la fusión del lecho de polvo con láser o haz de electrones con Inconel 718 para eliminar los huecos y poros internos y mejorar la resistencia a la fatiga mediante la homogeneización de la microestructura.
¿Cómo se debe manipular el polvo de Inconel 718 no utilizado?
Todo el polvo no utilizado debe manipularse en una atmósfera inerte para evitar la oxidación y la contaminación. El polvo se puede reutilizar hasta 10 veces si se mantiene en un ambiente controlado. Más allá de 10 reciclajes, se recomienda polvo nuevo.
Compartir
MET3DP Technology Co., LTD es un proveedor líder de soluciones de fabricación aditiva con sede en Qingdao, China. Nuestra empresa está especializada en equipos de impresión 3D y polvos metálicos de alto rendimiento para aplicaciones industriales.
Solicite información para obtener el mejor precio y una solución personalizada para su empresa.
Artículos relacionados
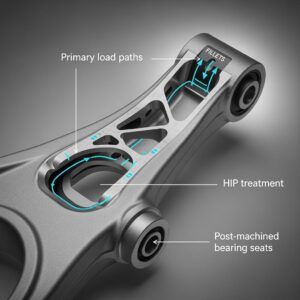
Metal 3D Printing for U.S. Automotive Lightweight Structural Brackets and Suspension Components
Leer Más "Acerca de Met3DP
Actualización reciente
Nuestro producto
CONTACTO
¿Tiene alguna pregunta? ¡Envíenos un mensaje ahora! Atenderemos su solicitud con todo un equipo tras recibir su mensaje.