Patient-Specific Knee Implants via Metal 3D Printing: Revolutionizing Orthopedic Care
Índice
Introduction – The Paradigm Shift in Knee Replacement with Metal 3D Printing
The landscape of orthopedic surgery is undergoing a significant transformation, driven by advancements in additive manufacturing, commonly known as metal 3D printing. Among the most impactful applications is the production of patient-specific knee implants. Traditional, off-the-shelf knee replacements often require surgeons to adapt a limited range of sizes and shapes to a patient’s unique anatomy, potentially leading to suboptimal fit, reduced comfort, and a higher risk of revision surgery. Metal Impresión 3D overcomes these limitations by enabling the creation of implants precisely tailored to an individual’s bone structure, offering a new era of personalized orthopedic care. This blog post delves into the significance of patient-specific knee implants manufactured via metal 3D printing, exploring their uses, advantages, material considerations, design aspects, and the critical factors for choosing a reliable manufacturing service like Metal3DP.
What are Patient-Specific Knee Implants Used For? – Tailoring Solutions for Diverse Needs
Patient-specific knee implants, created through metal 3D printing, are revolutionizing the treatment of a wide array of knee conditions. Their primary application lies in total knee arthroplasty (TKA), where the damaged cartilage and bone of the knee joint are replaced with artificial components. However, the benefits of customization extend to various scenarios:
- Complex Primary TKA: In cases with significant bone deformities, previous trauma, or unusual anatomy, standard implants may not provide an adequate fit. Patient-specific implants ensure optimal coverage and alignment, leading to improved biomechanics and longevity of the implant.
- Revision TKA: When a previous knee replacement fails, often due to loosening, wear, or infection, the bone structure can be compromised. Patient-specific implants can be designed to address these unique challenges, filling bone defects and providing a stable foundation for the new implant.
- Partial Knee Replacement (Unicompartmental Knee Arthroplasty): For patients with arthritis affecting only one compartment of the knee, custom implants can precisely resurface the damaged area while preserving healthy tissue, potentially leading to a more natural feel and faster recovery.
- Oncology: In cases where bone tumors affect the knee joint, patient-specific implants can be designed to replace the resected bone, restoring function and mobility with a precise anatomical fit.
- Sports Medicine: For athletes with specific knee injuries requiring surgical intervention, customized implants can cater to their unique biomechanical demands and facilitate a return to high-impact activities.
By addressing the individual anatomical nuances of each patient, these 3D-printed implants aim to improve surgical outcomes, reduce post-operative pain, enhance implant stability, and ultimately extend the lifespan of the replacement.
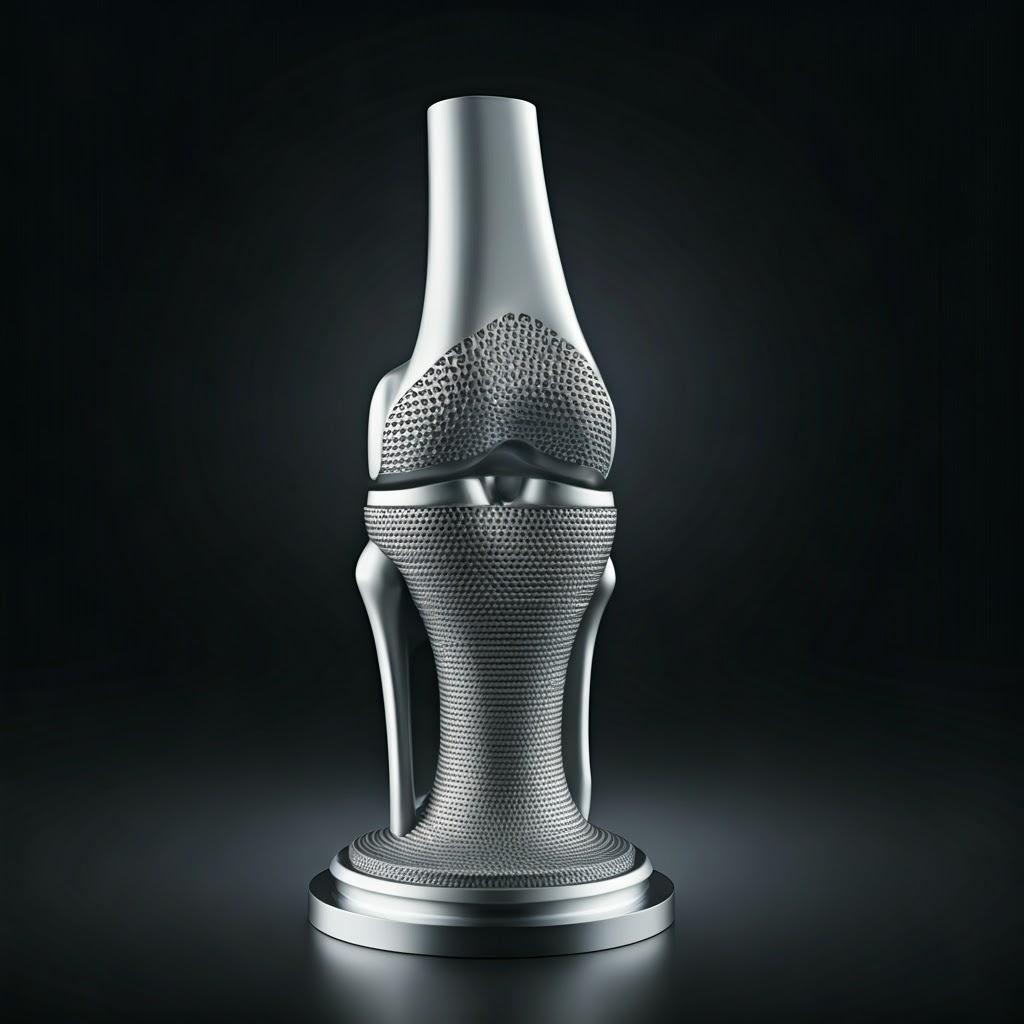
Why Use Metal 3D Printing for Patient-Specific Knee Implants? – Advantages Over Traditional Methods
The adoption of metal 3D printing for the fabrication of patient-specific knee implants offers a multitude of advantages over conventional manufacturing techniques:
- Enhanced Anatomical Fit: The most significant benefit is the ability to create implants that perfectly match the patient’s unique bone geometry, derived from CT or MRI scans. This precise fit minimizes the need for intraoperative bone removal and soft tissue adjustments, potentially leading to better alignment, stability, and a more natural feeling knee.
- Improved Surgical Accuracy: Pre-operative planning using 3D models and patient-specific cutting guides (often also 3D-printed) enhances surgical precision. Surgeons can visualize the implant placement and bone preparation in advance, leading to more accurate resections and implant positioning.
- Reduced Risk of Implant Failure: A well-fitting implant distributes stress more evenly across the bone-implant interface, reducing the risk of loosening, wear, and subsequent revision surgery.
- Bone Preservation: The precise fit often requires less bone removal compared to standard implants, preserving the patient’s natural bone stock, which is crucial for potential future revisions.
- Complex Geometries and Porous Structures: Metal 3D printing allows for the creation of intricate implant designs, including porous structures that promote osseointegration – the ingrowth of bone into the implant. This biological fixation enhances long-term stability and implant longevity. Metal3DP’s advanced printing technologies excel in producing such complex geometries.
- Faster Turnaround Times: While customization might seem time-consuming, advancements in 3D printing and digital workflows can often lead to faster design and manufacturing cycles compared to fully custom implants made with traditional methods.
- Optimización de materiales: Metal 3D printing allows for the precise control of material distribution, potentially optimizing the implant’s weight and mechanical properties.
Recommended Materials and Why They Matter – Biocompatibility and Performance
The choice of metal powder is paramount in the 3D printing of patient-specific knee implants, as it directly impacts the implant’s biocompatibility, mechanical strength, corrosion resistance, and long-term performance within the human body. Two primary materials are recommended for this application:
1. Ti-6Al-4V ELI (Extra-Low Interstitial):
- Propiedades: This titanium alloy is renowned for its exceptional biocompatibility, high strength-to-weight ratio, excellent corrosion resistance, and low modulus of elasticity (closer to that of bone compared to other metals). The ELI grade has lower levels of interstitial elements (oxygen, nitrogen, carbon, and iron), which further enhances its ductility and fracture toughness – crucial for load-bearing implants. You can find more information about the properties of titanium alloy powders at Página de productos de Metal3DP.
- Por qué es importante: The biocompatibility of Ti-6Al-4V ELI ensures minimal adverse reactions within the body, promoting osseointegration and long-term acceptance of the implant. Its high strength and low density allow for the creation of lightweight yet durable implants capable of withstanding the stresses of daily activity. The corrosion resistance prevents degradation of the implant in the bodily environment.
2. CoCrMo (Cobalt-Chromium-Molybdenum):
- Propiedades: CoCrMo alloys are known for their high wear resistance, excellent corrosion resistance, high strength, and biocompatibility. They have been used in orthopedic implants for decades and have a proven track record of clinical success.
- Por qué es importante: The exceptional wear resistance of CoCrMo is particularly important in articulating surfaces of the knee implant, minimizing the generation of wear debris that can lead to inflammation and implant loosening. Its high strength provides the necessary structural support for the joint. While its modulus of elasticity is higher than titanium alloys, advancements in design and porous structures can help mitigate stress shielding. Metal3DP offers high-quality CoCrMo powders specifically optimized for additive manufacturing.
The selection between Ti-6Al-4V ELI and CoCrMo often depends on the specific design requirements, the patient’s individual needs, and the surgeon’s preference. Both materials offer a robust combination of biocompatibility and mechanical properties suitable for long-term use in knee replacement.
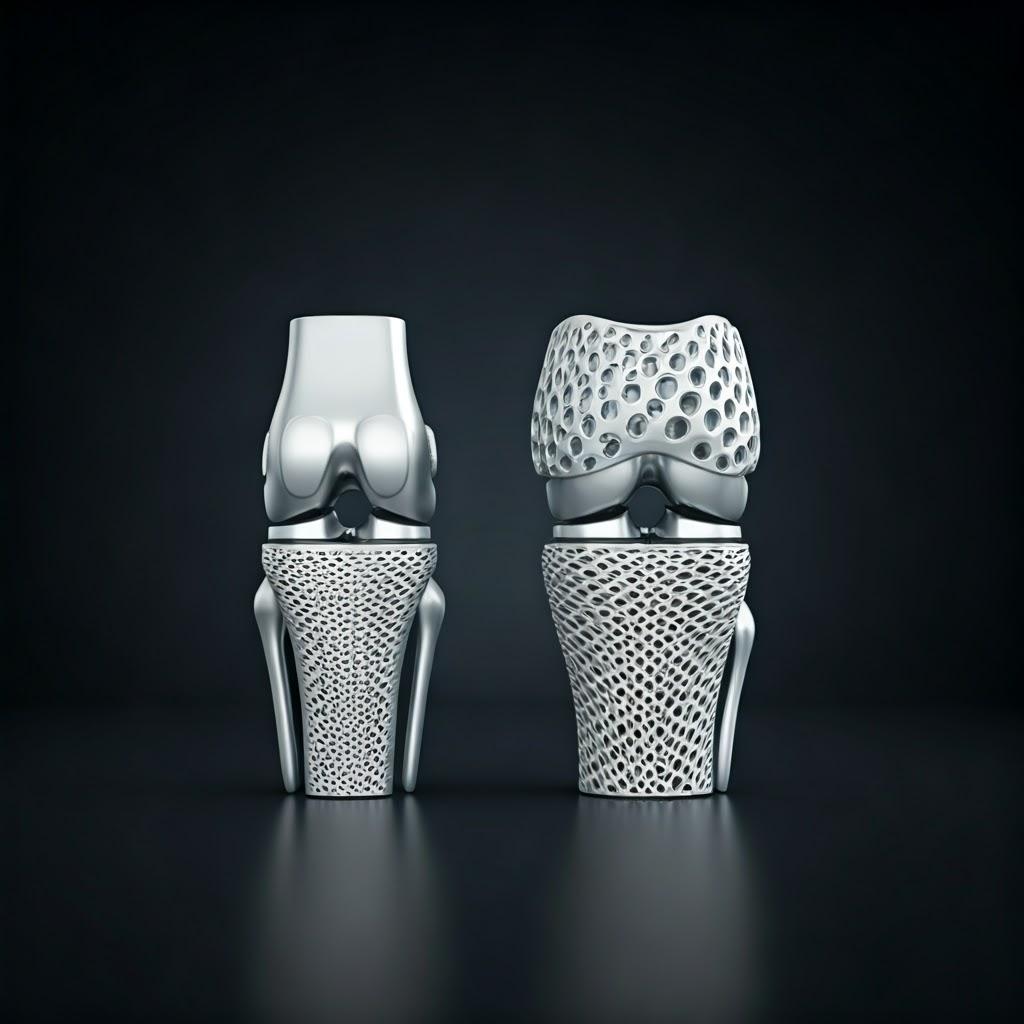
Design Considerations for Additive Manufacturing – Optimizing for Performance and Printability
Designing patient-specific knee implants for metal 3D printing requires a different mindset compared to traditional manufacturing. Optimizing the design for the additive process is crucial for achieving the desired mechanical properties, surface finish, and dimensional accuracy while minimizing material usage and print time. Key design considerations include:
- Optimización de la topología: This computational method can be employed to identify areas of high stress within the implant and optimize the material distribution accordingly. By removing material from low-stress regions, the implant’s weight can be reduced without compromising its structural integrity. This is particularly relevant for large, customized implants.
- Lattice Structures and Porous Designs: Incorporating lattice structures or controlled porosity within non-load-bearing regions can further reduce weight and promote osseointegration. The pore size, shape, and interconnectivity can be tailored to encourage bone ingrowth and enhance long-term fixation. Metal3DP’s expertise in advanced powder metallurgy allows for the creation of intricate porous structures with high precision.
- Textura de la superficie: The surface finish of the implant plays a critical role in osseointegration. 3D printing allows for the creation of tailored surface textures, such as micro-roughness, which has been shown to enhance bone cell attachment and proliferation.
- Wall Thickness and Support Structures: Careful consideration of wall thickness is essential to ensure sufficient strength while minimizing material consumption and print time. Support structures are often necessary to prevent deformation during the printing process, especially for overhanging features. The design should aim to minimize the need for extensive support structures and facilitate their easy removal post-printing.
- Minimización de las concentraciones de tensión: Sharp corners and abrupt transitions in geometry can lead to stress concentrations, potentially increasing the risk of fatigue failure. The design should incorporate smooth transitions and fillets to distribute stress more evenly.
- Modularity: In some cases, patient-specific solutions might involve modular designs, allowing for intraoperative adjustments or the replacement of individual components if necessary. 3D printing enables the creation of complex interlocking features for modularity.
By considering these design principles, engineers can leverage the unique capabilities of metal 3D printing to create patient-specific knee implants that are not only anatomically accurate but also optimized for mechanical performance and long-term biological integration.
Tolerance, Surface Finish, and Dimensional Accuracy – Achieving Precision in Custom Implants
In the realm of medical implants, precision is paramount. Patient-specific knee implants manufactured via metal 3D printing must adhere to strict tolerance, surface finish, and dimensional accuracy requirements to ensure proper fit, function, and longevity.
- Tolerancia: Tolerance refers to the allowable variation in the dimensions of the printed part. Metal 3D printing technologies, particularly Powder Bed Fusion (PBF) processes like Selective Laser Melting (SLM) and Electron Beam Melting (EBM) offered by Metal3DP, can achieve tight tolerances, typically in the range of pm0.05 to pm0.1 mm, depending on the material, part geometry, and build parameters. These levels of accuracy are crucial for ensuring a precise fit with the patient’s bone structure and proper articulation with other implant components.
- Acabado superficial: The surface finish of a knee implant influences its interaction with the surrounding tissue and its wear characteristics. Metal 3D-printed parts typically have a rougher surface finish compared to machined parts. However, this surface roughness can be beneficial for osseointegration. Post-processing techniques, such as polishing, blasting, or chemical etching, can be employed to achieve the desired surface finish for specific areas of the implant, balancing the need for biological fixation and smooth articulation.
- Precisión dimensional: Dimensional accuracy refers to how closely the printed part matches the intended design dimensions. Factors influencing dimensional accuracy in metal 3D printing include material shrinkage during solidification, thermal gradients during the build process, and the accuracy of the 3D printer itself. Calibration of the printing system, optimized build parameters, and careful part orientation are essential to achieve high dimensional accuracy. Advanced scanning technologies and quality control procedures are employed by reputable manufacturers like Metal3DP to verify the dimensional accuracy of their printed implants.
Achieving the required tolerance, surface finish, and dimensional accuracy necessitates a combination of advanced 3D printing technology, optimized process parameters, skilled engineers, and rigorous quality control measures. This ensures that the patient-specific knee implant meets the stringent demands of orthopedic applications.
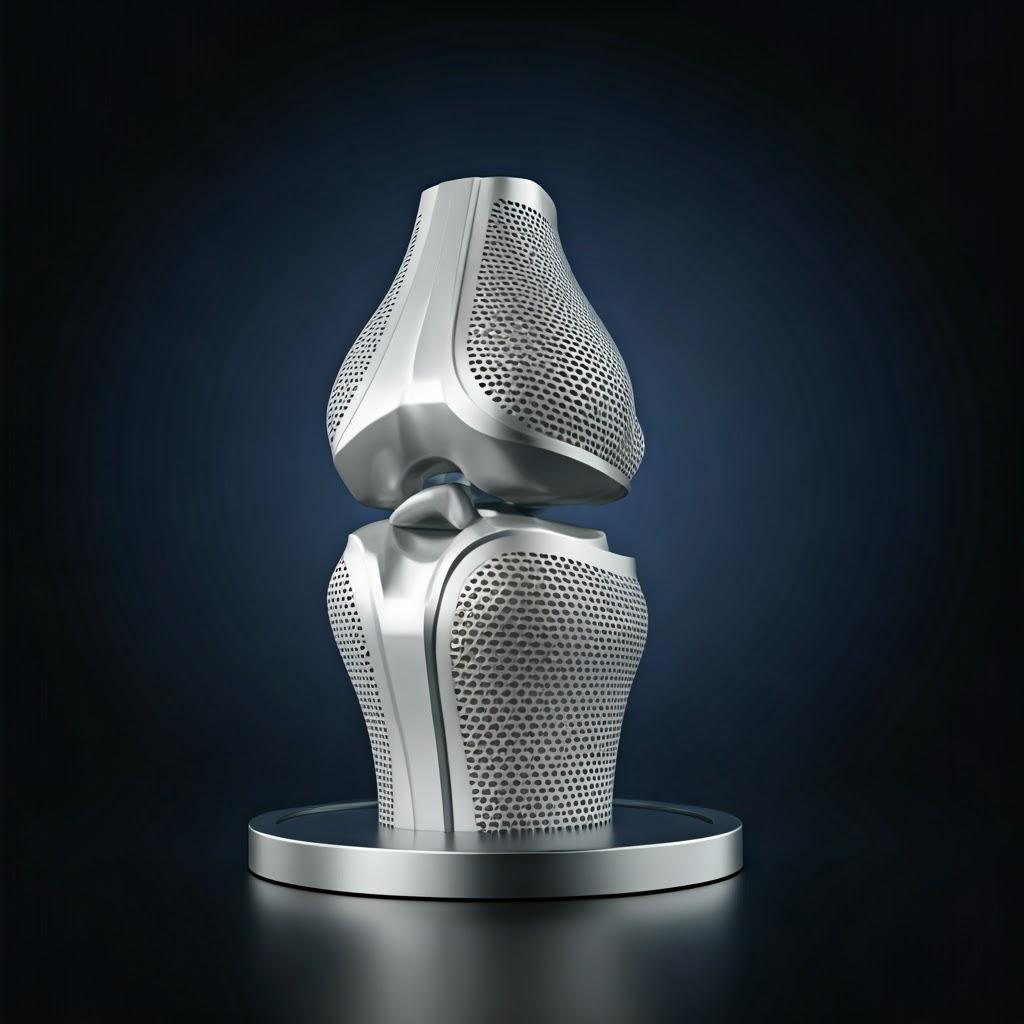
Post-Processing Requirements – Enhancing Functionality and Biocompatibility
While metal 3D printing offers significant advantages in creating complex geometries, post-processing steps are often necessary to achieve the final desired properties and surface finish of patient-specific knee implants. Common post-processing requirements include:
- Retirada del soporte: Support structures, essential for preventing deformation during printing, must be carefully removed without damaging the implant. Techniques include manual removal, machining, wire Electrical Discharge Machining (EDM), or chemical dissolution, depending on the material and support geometry.
- Stress Relief and Heat Treatment: Metal 3D-printed parts can have residual stresses due to the rapid heating and cooling cycles during the printing process. Heat treatment processes, such as annealing or hot isostatic pressing (HIP), are often employed to relieve these stresses, improve the material’s mechanical properties (e.g., strength, ductility, fatigue resistance), and reduce porosity.
- Acabado superficial: As mentioned earlier, surface finishing techniques like polishing, grit blasting, or chemical etching may be applied to specific areas of the implant to achieve the desired surface roughness for osseointegration or smooth articulation.
- Mecanizado: In some cases, critical features requiring very tight tolerances, such as bearing surfaces or connection points, may undergo precision machining after the initial 3D printing process.
- Cleaning and Sterilization: Thorough cleaning is essential to remove any residual powder or contaminants from the implant surface. Medical-grade sterilization processes are then performed to ensure the implant is safe for surgical implantation.
- Revestimiento (opcional): In certain applications, coatings may be applied to enhance biocompatibility, wear resistance, or provide antimicrobial properties. Examples include hydroxyapatite coatings to promote bone bonding or diamond-like carbon coatings to improve wear resistance.
The specific post-processing steps required depend on the material, the intended function of the implant, and the regulatory requirements for medical devices. A comprehensive understanding of these requirements and the appropriate post-processing techniques is crucial for delivering high-quality, patient-specific knee implants.
Common Challenges and How to Avoid Them – Ensuring Successful Outcomes
While metal 3D printing offers immense potential for patient-specific knee implants, several challenges can arise during the design and manufacturing process. Understanding these potential pitfalls and implementing strategies to avoid them is crucial for ensuring successful outcomes:
- Deformación y distorsión: Thermal stresses during the printing process can lead to warping or distortion of the implant, affecting its dimensional accuracy. Prevention: Optimizing part orientation, using appropriate support structures, and carefully controlling the build parameters can minimize these issues. Simulation software can also help predict and mitigate potential distortion.
- Porosidad: Internal porosity within the printed part can compromise its mechanical strength and fatigue resistance. Prevention: Selecting high-quality metal powders, optimizing laser or electron beam parameters (power, speed, hatch spacing), and employing post-processing techniques like Hot Isostatic Pressing (HIP) can reduce porosity. Metal3DP’s advanced powder making system ensures high powder sphericity and flowability, contributing to denser prints.
- Support Structure Removal Damage: Aggressive removal of support structures can damage delicate features of the implant. Prevention: Designing self-supporting geometries where possible, optimizing support structure design for easy removal, and using appropriate removal techniques are essential.
- Problemas de acabado superficial: Achieving the desired surface finish directly from the 3D printer can be challenging. Prevention: Optimizing print parameters and employing appropriate post-processing techniques like polishing or blasting can achieve the required surface roughness.
- Biocompatibility Concerns: Inadequate material selection or contamination during the manufacturing process can lead to biocompatibility issues. Prevention: Using certified medical-grade powders, maintaining a clean manufacturing environment, and adhering to strict quality control procedures are crucial.
- Cumplimiento de la normativa: Medical devices are subject to stringent regulatory requirements. Prevention: Working with a manufacturing partner like Metal3DP that has experience in medical device manufacturing and adheres to relevant standards (e.g., ISO 13485) is essential for navigating the regulatory landscape.
By proactively addressing these potential challenges through careful design, optimized manufacturing processes, and stringent quality control, the successful production of high-quality patient-specific knee implants via metal 3D printing can be ensured.
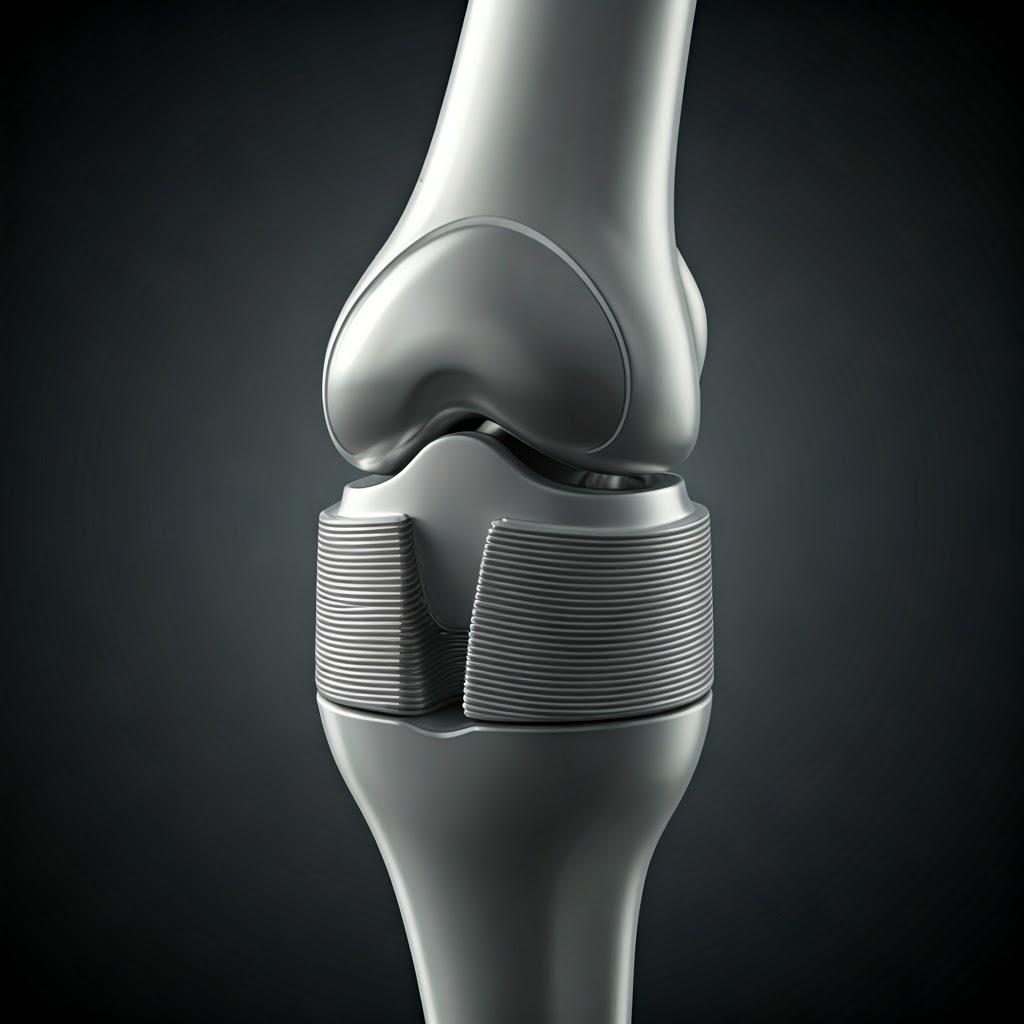
How to Choose the Right Metal 3D Printing Service Provider – Selecting a Trusted Partner
The selection of a metal 3D printing service provider is a critical decision for companies seeking patient-specific knee implants. The quality, accuracy, and biocompatibility of these medical devices directly impact patient outcomes. Therefore, a thorough evaluation of potential suppliers is essential. Key factors to consider include:
- Experience and Expertise in Medical Device Manufacturing: Look for a provider with a proven track record in manufacturing medical implants, ideally orthopedic devices. Experience with the specific materials (Ti-6Al-4V ELI and CoCrMo) and the regulatory requirements for medical devices is crucial. Metal3DP has decades of collective expertise in metal additive manufacturing and partners with organizations in the medical field.
- Material Capabilities and Certifications: Ensure the provider offers the recommended metal powders with appropriate medical-grade certifications and has expertise in processing these materials for implant applications. Inquire about their material testing and quality control procedures.
- Printing Technology and Equipment: The type of metal 3D printing technology employed (e.g., SLM, EBM) and the capabilities of their equipment (build volume, accuracy) are important considerations. Industry-leading print volume, accuracy, and reliability are hallmarks of Metal3DP’s printing solutions.
- Design and Engineering Support: A strong service provider will offer design optimization services tailored for additive manufacturing, including topology optimization, lattice design, and support structure optimization. Their engineers should be knowledgeable in the specific requirements of orthopedic implants.
- Capacidades de postprocesado: Verify that the provider has the necessary in-house or partnered capabilities for essential post-processing steps such as support removal, heat treatment, surface finishing, cleaning, and sterilization.
- Sistema de gestión de calidad: A robust quality management system, such as ISO 13485 certification for medical devices, is a strong indicator of the provider’s commitment to quality and regulatory compliance.
- Traceability and Documentation: The provider should have systems in place for comprehensive material traceability and documentation throughout the manufacturing process, which is essential for regulatory compliance and accountability.
- Comunicación y Colaboración: Effective communication and a willingness to collaborate closely on design iterations and project requirements are vital for a successful partnership.
- Lead Times and Scalability: Evaluate the provider’s typical lead times for patient-specific implants and their capacity to scale production as needed.
By carefully assessing these factors, companies can select a metal 3D printing service provider that can reliably produce high-quality, patient-specific knee implants that meet the stringent demands of the medical industry.
Cost Factors and Lead Time – Understanding the Economics of Customization
The cost and lead time associated with metal 3D-printed patient-specific knee implants can vary depending on several factors:
- Complexity of the Design: More intricate geometries, including those with complex lattice structures or requiring extensive support structures, will generally incur higher design and printing costs.
- Volumen de material: The amount of metal powder used to print the implant directly impacts the material cost. Optimized designs that minimize material usage can help control expenses.
- Tiempo de construcción: Longer print times on the 3D printer translate to higher machine usage costs. Factors influencing build time include part size, complexity, and layer thickness.
- Requisitos de postprocesamiento: The extent and complexity of post-processing steps, such as extensive machining or specialized coatings, will add to the overall cost and lead time.
- Customization Level: Highly individualized implants requiring significant design iterations and pre-operative planning may have higher upfront costs compared to more standardized custom solutions.
- Costes de material: The cost of the specific metal powder (e.g., Ti-6Al-4V ELI or CoCrMo) can fluctuate based on market conditions and supplier pricing. Metal3DP offers a range of high-quality metal powders at competitive prices.
- Quality Assurance and Regulatory Compliance: The stringent quality control measures and documentation required for medical devices contribute to the overall cost.
- Service Provider’s Pricing Structure: Different service providers have varying pricing models based on factors like machine hourly rates, material markups, and engineering fees.
Plazo de entrega: The lead time for patient-specific knee implants encompasses several stages:
- Design and Planning: This includes the time taken for image processing (CT/MRI scans), 3D model creation, implant design, and surgical planning.
- Manufacturing (3D Printing): The actual printing time depends on the size and complexity of the implant.
- Post-procesamiento: The duration of post-processing steps like support removal, heat treatment, and surface finishing varies based on the requirements.
- Control de Calidad e Inspección: Thorough quality checks are essential before the implant can be released.
- Shipping and Delivery: The time taken for the finished implant to reach the medical facility.
While patient-specific implants may have a higher initial cost compared to off-the-shelf options, the potential benefits of improved surgical outcomes, reduced revision rates, and enhanced patient satisfaction can offer long-term value. Engaging with a transparent and experienced service provider like Metal3DP early in the process can help in understanding the cost drivers and optimizing the design and manufacturing workflow to meet both clinical and economic objectives.
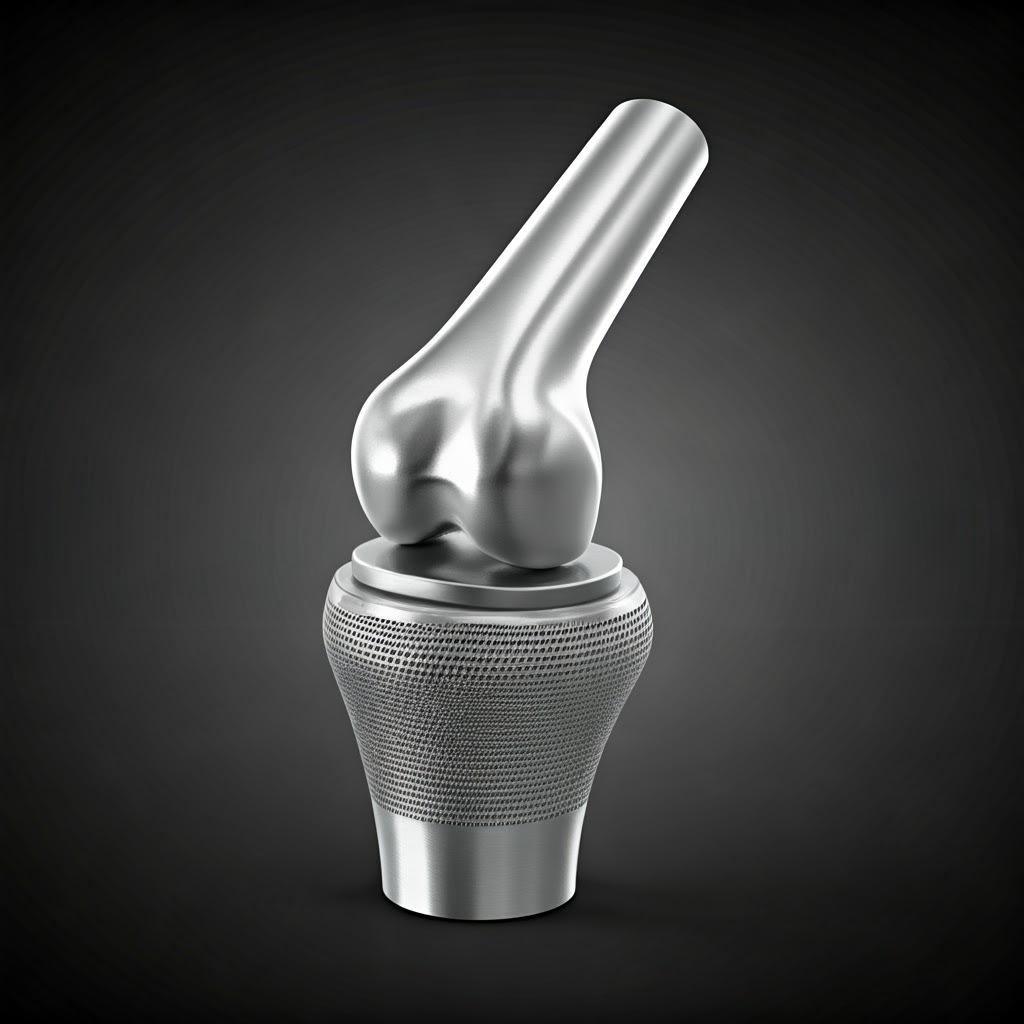
Preguntas más frecuentes (FAQ)
- Q: How long does it take to receive a patient-specific knee implant?
- A: The total lead time can vary depending on the complexity of the case, the design process, printing time, and post-processing requirements. Typically, it can range from a few weeks to a couple of months. Factors like the responsiveness of the service provider and the efficiency of the digital workflow also play a role.
- Q: Are patient-specific knee implants more expensive than standard implants?
- A: Generally, patient-specific implants have a higher upfront cost due to the customization involved in design, manufacturing, and quality control. However, the potential for improved outcomes and reduced revision surgeries may offer long-term cost benefits.
- Q: What type of imaging is required to create a patient-specific knee implant?
- A: Computed Tomography (CT) scans are the most common imaging modality used to capture the detailed bone anatomy required for designing patient-specific knee implants. Magnetic Resonance Imaging (MRI) may also be used in certain cases to assess soft tissue conditions.
Conclusion – Embracing the Future of Personalized Orthopedics
Metal 3D printing is revolutionizing the field of orthopedic surgery, and the application to patient-specific knee implants represents a significant leap forward in personalized medicine. By enabling the creation of implants that precisely match an individual’s unique anatomy, this technology offers the potential for improved surgical accuracy, enhanced implant stability, reduced risk of failure, and ultimately, better patient outcomes. Companies like Metal3DP are at the forefront of this innovation, providing the expertise, advanced materials, and cutting-edge printing technologies necessary to bring these customized solutions to patients in need. As the technology continues to evolve and become more accessible, patient-specific knee implants manufactured via metal 3D printing are poised to become an increasingly integral part of orthopedic care, ushering in a new era of tailored and effective joint replacement.
Compartir
MET3DP Technology Co., LTD es un proveedor líder de soluciones de fabricación aditiva con sede en Qingdao, China. Nuestra empresa está especializada en equipos de impresión 3D y polvos metálicos de alto rendimiento para aplicaciones industriales.
Solicite información para obtener el mejor precio y una solución personalizada para su empresa.
Artículos relacionados
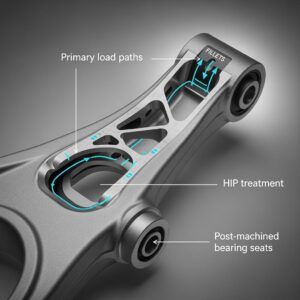
Metal 3D Printing for U.S. Automotive Lightweight Structural Brackets and Suspension Components
Leer Más "Acerca de Met3DP
Actualización reciente
Nuestro producto
CONTACTO
¿Tiene alguna pregunta? ¡Envíenos un mensaje ahora! Atenderemos su solicitud con todo un equipo tras recibir su mensaje.