Sistemas de atomización de metales
Índice
La atomización de metales es un proceso de fabricación en el que el metal se convierte en polvo rompiendo el metal fundido en pequeñas gotas. Este polvo puede utilizarse después para fabricar piezas mediante métodos como el moldeo por inyección de metal, el prensado isostático en caliente y la fabricación aditiva, entre otros. Sistemas de atomización de metales son los equipos utilizados para llevar a cabo este proceso.
Visión general de los sistemas de atomización de metales
Los sistemas de atomización de metales constan de mecanismos para fundir el metal en bruto, suministrar el metal fundido a una zona de atomización, romper el metal en finas gotas y recoger el polvo solidificado. Los componentes clave incluyen hornos, artesas, mecanismos de suministro, atomizadores, cámaras de refrigeración, separadores ciclónicos, filtros de mangas y sistemas de recogida de polvo.
Existen dos tipos principales de sistemas de atomización:
- Atomización con gas: utiliza gas a alta presión para romper la corriente de metal fundido.
- Atomización con agua: utiliza agua a alta presión para romper el metal fundido.
La atomización con gas produce polvos más finos por término medio, mientras que la atomización con agua ofrece mayores índices de producción. Ambos métodos pueden alcanzar rendimientos razonablemente altos en función del diseño y los parámetros de funcionamiento.
sistemas de atomización de metales Composición
Componente | Descripción |
---|---|
Horno | Funde el metal en estado líquido mediante inducción, combustión, etc. Los tipos más comunes son los hornos de inducción y los hornos de arco eléctrico. |
Tundish | Actúa como depósito para retener el metal fundido una vez que sale del horno. Proporciona un flujo continuo de metal al sistema de suministro. |
Sistema de entrega | Transfiere metal fundido de la artesa de colada al atomizador. A menudo utiliza un embudo de vertido, una cuba calentada o una boquilla presurizada. |
Atomizador | Rompe el metal fundido en gotas mediante chorros de gas o agua. Varios diseños y número de chorros. |
Sección de refrigeración | Permite que el polvo se solidifique tras la atomización antes de su recogida. Aire o gas inerte utilizado como medio de refrigeración. |
Sistema de separación | Captura las partículas finas de polvo al tiempo que permite la recirculación de los medios de refrigeración. Utiliza ciclones, filtros de bolsa. |
Colección de polvo | Recoge el polvo atomizado para su recuperación. A menudo contenedores de tambor o caja, cajas de guantes o cintas transportadoras que conducen a contenedores. |
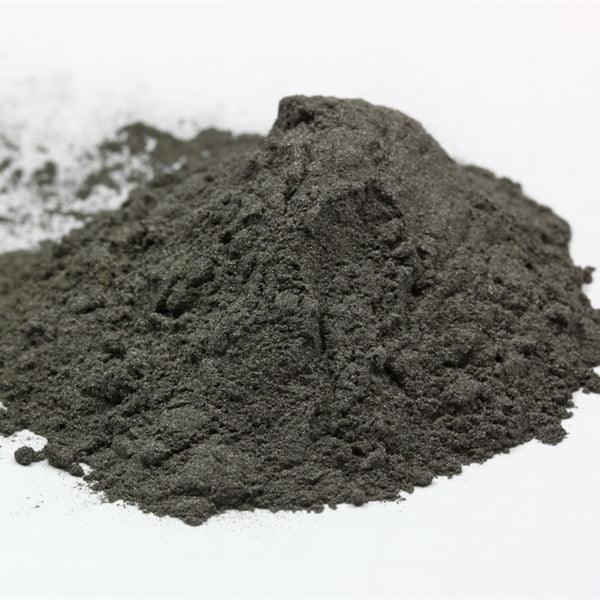
sistemas de atomización de metales Tipos
En la producción comercial de polvo metálico se utilizan varios diseños de atomizadores:
Atomizadores de gas
- Atomizador de gas supersónico - Las boquillas Laval aceleran el gas inerte hasta velocidades sónicas.
- Atomizador de gas de acoplamiento estrecho - Chorros de gas múltiples que inciden en el flujo de metal fundido.
- Atomizador de gas de caída libre - La corriente de metal fundido cae libremente a través de gas inerte a alta velocidad.
Atomizadores de agua
- Atomizador de agua a presión - Chorros de agua a alta presión golpean el chorro de metal fundido.
- Atomizador de agua giratorio: la corriente de metal fundido entra en contacto con chorros de agua giratorios.
- Atomizador de agua sumergida - Chorros de agua colocados bajo la superficie de la corriente de metal fundido.
Atributos del atomizador de metal
Atributo | Descripción |
---|---|
Tipo de gas | Los gases inertes como el nitrógeno y el argón se utilizan para evitar la oxidación. El nitrógeno es el más económico. |
Presión del agua | Presión de 30-150 MPa necesaria para atomizar correctamente los metales. |
Número de chorros | Más chorros aumentan la rotura del metal pero pueden reducir el rendimiento. Alrededor de 4-8 común. |
Disposición del chorro | Chorros redondos o rectangulares que cubren el chorro metálico. Polvo rectangular más uniforme. |
Velocidad del chorro | Las velocidades de gas inerte más rápidas producen polvos más finos. La velocidad óptima del gas varía para cada metal. |
Altura de caída | Altura a la que cae la corriente de metal fundido antes de chocar con las toberas. Afecta a la distribución del tamaño de las partículas. |
Diseño del flujo | Se prefiere un flujo metálico suave y laminar para evitar salpicaduras en gotas tempranas. |
Diseño de la boquilla | Las boquillas mecanizadas con precisión en los atomizadores de gas son cruciales para el rendimiento. |
Tasa de enfriamiento | Un enfriamiento más rápido produce polvos más finos. Depende de la temperatura del gas/agua y de la cámara. |
Eficacia de separación | Un mayor índice de separación aumenta el rendimiento. Los ciclones autoinyectables funcionan bien. |
Método de recogida | Los sistemas cerrados evitan la oxidación del polvo. Son habituales los transportadores de tambor automatizados. |
Características del polvo metálico
Las propiedades del polvo metálico producido dependen en gran medida de los parámetros y condiciones del proceso de atomización.
Atributos del polvo
Atributo | Alcance típico |
---|---|
Forma de las partículas | Estructuras irregulares, esféricas, satélites |
Tamaño de las partículas | 1 micra a 1000 micras |
Distribución granulométrica | Gaussiano, log-normal común |
Densidad aparente | Generalmente 30-80% de densidad verdadera |
Densidad del grifo | Alrededor de 60-95% de densidad verdadera |
Caudal | Varía mucho según la forma y la distribución del tamaño |
Pureza | 93-99,5% intervalo objetivo |
Contenido de oxígeno | Intervalo de 300-3000 ppm |
Contenido en nitrógeno | Rango 75-1500 ppm |
Efecto sobre las propiedades de la pieza
Atributo Polvo | Efecto en piezas sinterizadas/impresas |
---|---|
Tamaño de las partículas | Los polvos más finos aumentan la densidad y reducen los poros |
Distribución por tamaños | Una distribución más amplia mejora la densidad de empaquetado |
Forma de las partículas | Las partículas esféricas tienen mejor flujo y empaquetamiento |
Densidad aparente | La mayor densidad aumenta la resistencia en verde para la manipulación |
Densidad del grifo | La mayor densidad reduce los huecos de contracción tras la sinterización |
Pureza | Una mayor pureza reduce defectos como las inclusiones |
Contenido de oxígeno | Por encima de 3000 ppm puede causar problemas de porosidad |
sistemas de atomización de metales Aplicaciones
Los polvos metálicos finos obtenidos por atomización se utilizan en muchas industrias para fabricar piezas de alto rendimiento.
Industria | Ejemplos de aplicación |
---|---|
Automoción | Componentes del motor, engranajes, tornillería |
Aeroespacial | Álabes de turbina, componentes aerodinámicos |
Biomédica | Implantes ortopédicos, herramientas quirúrgicas |
Electrónica | Blindaje, conectores, contactos |
Energía | Piezas nucleares y de turbinas sometidas a entornos extremos |
Fabricación aditiva | Piezas finales impresas en 3D en todos los sectores |
Sistemas populares de atomización de metales Utilizados
Muchas aleaciones se atomizan en forma de polvo para la fabricación de piezas. Estos son algunos metales y aleaciones comunes atomizados:
Material | Propiedades clave |
---|---|
Aleaciones de titanio | Alta resistencia y bajo peso. Biocompatibilidad. |
Aleaciones de níquel | Mantiene sus propiedades a altas temperaturas. Resistencia a la corrosión. |
Aleaciones de cobalto | Biocompatibilidad. Propiedades de resistencia al desgaste. |
Aceros para herramientas | Altos niveles de dureza tras el tratamiento térmico. |
Aceros inoxidables | Excelente resistencia a la corrosión. |
Aleaciones de aluminio | Peso ligero. Buena conductividad térmica. |
Aleaciones de cobre | Alta conductividad térmica y eléctrica. |
Aleaciones magnéticas | Altas permeabilidades para aplicaciones magnéticas. |
Proveedores y precios de polvo metálico
Hay varios proveedores de renombre que fabrican y distribuyen polvos metálicos en todo el mundo. Los precios dependen de la aleación, el tamaño de las partículas y la cantidad solicitada.
Proveedor | Precios |
---|---|
AP&C | $50 - $1500 por kg |
Sandvik Osprey | $100 - $2000 por kg |
Productos en polvo Carpenter | $75 - $1800 por kg |
Tecnologías de superficie Praxair | $250 - $2500 por kg |
Höganäs | $45 - $1600 por kg |
ECKA Granulado | $80 - $1200 por kg |
Las aleaciones de mayor rendimiento o un control más fino de la distribución del tamaño del polvo exigen precios más elevados, mientras que los metales y aleaciones más comunes son más económicos en volúmenes de producción.
Atomización de metales frente a otros métodos
Método | Ventajas | Limitaciones |
---|---|---|
Atomización de metales | - Polvos más finos - Mayor pureza - Gama de aleaciones | - Elevados costes de capital - Requiere grandes conocimientos de procesamiento |
Proceso electrolítico | - Polvos muy finos y limpios | - Limitado a aleaciones conductoras - Caro |
Desgaste mecánico | - Sencillo y barato - Amplia gama de metales | - Menor finura alcanzable - Mayor oxidación |
Precipitación química | - Polvos elementales puros y aleados | - Problemas de aglomeración del polvo - Contaminación potencial |
Pulverización térmica | - Puede producir polvo esférico | - Inclusiones de óxido- Amplias distribuciones de tamaño |
La atomización ofrece polvos razonablemente finos y limpios en una amplia gama de aleaciones con buenos volúmenes de producción. Es necesario tomar precauciones de seguridad al manipular polvos metálicos finos.
Consideraciones clave para la selección
Entre los factores importantes que guían la selección del sistema de atomización de metales se incluyen:
Factor | Descripción |
---|---|
Índice de producción | Salida de polvo requerida en kg/hr. Define la capacidad. |
Tamaño de partícula objetivo | Necesita finura definida, distribución. Influye en el rendimiento y el coste. |
Composición de la aleación | La mayoría de los sistemas manejan una gama de aleaciones. Puede influir la elección del método de fusión, el atomizador y las presiones de gas/agua. |
Calidad del producto | Los niveles de pureza, los límites de captación de oxígeno y los requisitos de consistencia del tamaño dictan los parámetros. |
Consideraciones sobre la manipulación | Es preferible la manipulación cerrada del polvo. Algunos metales plantean riesgos para la salud. |
Uso final del polvo | Requisitos de las propiedades de las piezas: densidad/porosidad, fluidez, factores de forma. |
Costes de explotación | Insumos para fundición, gases, agua. Mano de obra, gastos de mantenimiento. |
Seguridad | Los recipientes a presión para líquidos/gases requieren el cumplimiento de una normativa específica. |
Impacto medioambiental | Se aplican consideraciones sobre emisiones de gases y uso/eliminación de agua. |
Es necesario determinar cuidadosamente los requisitos de rendimiento, los parámetros de calidad, las condiciones de funcionamiento, los parámetros de seguridad y los costes en función de los requisitos de la pieza final.
sistemas de atomización de metales Mantenimiento
Se requiere un mantenimiento adecuado para que el equipo de atomización funcione de forma óptima.
Componente | Actividades de mantenimiento | Frecuencia |
---|---|---|
Horno | Inspeccionar el refractario y los elementos calefactores. Sustituir si es necesario. | 6-12 meses |
Boquillas | Inspeccione las aberturas de los chorros de las boquillas en busca de desgaste/obstrucciones. | Mensualmente |
Filtros y conductos de agua | Lave los conductos y sustituya los filtros con regularidad. | 2-4 semanas |
Tuberías y válvulas de gas | Comprobar si hay fugas, obstrucciones. Confirmar presiones. | 2-4 semanas |
Separadores | Inspeccionar el estado del medio filtrante y las juntas. | 4-6 meses |
Controles y sensores | Compruebe la calibración. Probar enclavamientos y respuestas. | 6-12 meses |
Colector de polvo | Inspeccionar el estado y las juntas de los contenedores. Confirmar los niveles de gas inerte para sistemas cerrados. | Mensualmente |
Interiores del sistema | Polvo metálico acumulado y limpio por todas partes. Más frecuente cerca de los caminos de corrientes metálicas. | Mensualmente |
La supervisión detallada de los equipos y el mantenimiento preventivo y predictivo minimizan las interrupciones inesperadas de la producción.
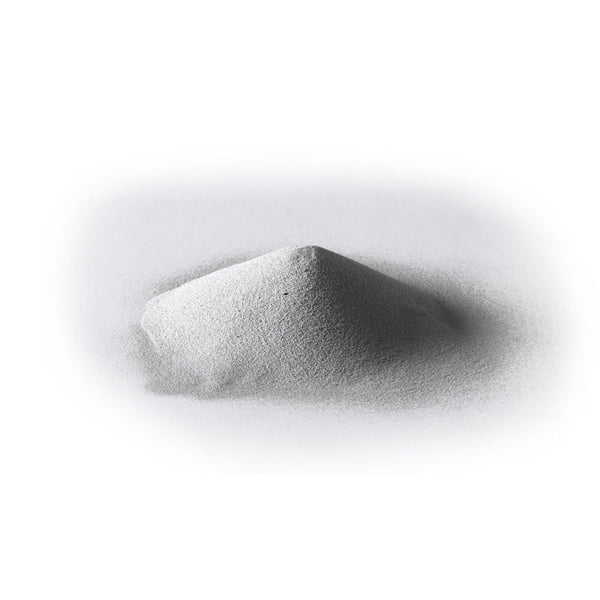
Preguntas frecuentes
P: ¿Cuál es el nivel adecuado de automatización y control para los sistemas de atomización de metales?
R: Se recomienda un alto grado de automatización en la alimentación de material, la supervisión y el control del proceso para obtener una producción de polvo constante y segura. Las variables clave del proceso, como temperaturas, presiones y flujos de gas, deben tener un control de retroalimentación automático. La supervisión del sistema, el ajuste de los parámetros y el modo de funcionamiento manual siguen siendo prudentes.
P: ¿Cómo determinar si para una aplicación es preferible la atomización con gas o con agua?
R: La atomización con agua ofrece un rendimiento de metal mucho mayor que la atomización con gas. Pero la atomización con gas puede lograr tamaños medios de polvo más finos, adecuados para piezas microestructuradas. Para polvos MIM típicos de más de 15 micras, se prefiere la atomización con agua por razones económicas.
P: ¿Qué medidas de seguridad se recomiendan para el funcionamiento de los sistemas de atomización?
R: Es obligatorio el uso de equipos de protección personal adecuados para la manipulación de sistemas de alta presión y polvos finos. Los sistemas de atomización de agua deben tener protectores contra salpicaduras. La manipulación cerrada del polvo con cajas de guantes de gas inerte y colectores de polvo automatizados mejora la seguridad. Los bloqueos, las restricciones de acceso y las paradas de emergencia son fundamentales.
P: ¿Cuáles son las causas de los problemas habituales de producción de polvo en la atomización?
R: Los tamaños irregulares del polvo y las partículas satélites suelen deberse a flujos incontrolados de corrientes metálicas. La contaminación puede deberse al desgaste de las boquillas, a medios filtrantes degradados o a fugas. El ensuciamiento de la cámara y el separador por desbordamientos reduce el rendimiento con el tiempo. La clave está en controlar y optimizar los parámetros de flujo.
P: ¿Qué conocimientos técnicos se necesitan para manejar con eficacia los sistemas de atomización?
R: Aunque la automatización de los controles reduce la carga manual, los ingenieros metalúrgicos o de ciencias de los materiales con formación y familiarizados con la producción de polvo son ideales para supervisar los equipos. Se necesitan ingenieros mecánicos y eléctricos para el mantenimiento y la resolución de problemas. Los operarios deben recibir una formación adecuada sobre manipulación de polvo metálico.
Compartir
MET3DP Technology Co., LTD es un proveedor líder de soluciones de fabricación aditiva con sede en Qingdao, China. Nuestra empresa está especializada en equipos de impresión 3D y polvos metálicos de alto rendimiento para aplicaciones industriales.
Solicite información para obtener el mejor precio y una solución personalizada para su empresa.
Artículos relacionados
Acerca de Met3DP
Actualización reciente
Nuestro producto
CONTACTO
¿Tiene alguna pregunta? ¡Envíenos un mensaje ahora! Atenderemos su solicitud con todo un equipo tras recibir su mensaje.
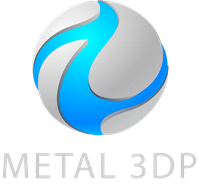
Polvos metálicos para impresión 3D y fabricación aditiva