Moldeo por inyección de metal (MIM)
Índice
Imagínese un proceso de fabricación que fusiona el detalle intrincado y la libertad de diseño del moldeo por inyección de plástico con la resistencia y durabilidad sin igual del metal. Esa es la magia de Moldeo por inyección de metales (MIM), un cambio de juego en el mundo de la metalurgia.
¿Qué es el moldeo por inyección de metales (MIM)?
El MIM es una técnica de fabricación que utiliza una mezcla única de polvo metálico y un aglutinante polimérico. Esta combinación, conocida como materia prima, se comporta como una pasta moldeable. El proceso MIM inyecta estratégicamente esta materia prima en una cavidad de molde a alta presión, replicando la intrincada geometría deseada. A continuación se desglosa el proceso MIM en sus etapas clave:
- Preparación de la materia prima: El metal finamente pulverizado, normalmente acero inoxidable, aleaciones de acero o incluso materiales exóticos como el carburo de tungsteno, se mezcla meticulosamente con un sistema aglutinante. Este aglutinante garantiza la fluidez de la mezcla durante el moldeo por inyección.
- Moldeado: La materia prima preparada se inyecta a alta presión en una cavidad de molde diseñada con precisión. De este modo se reproduce la intrincada forma casi neta del componente metálico deseado.
- Debinding: Tras el moldeo, es necesario eliminar el aglutinante de la pieza moldeada. Este delicado proceso, a menudo denominado desencolado, puede implicar técnicas térmicas (calentamiento) o desencolado con disolvente, en función del sistema de aglutinante elegido.
- Sinterización: La pieza desbastada, ahora una frágil estructura de polvo metálico, se somete a un proceso de sinterización a alta temperatura en una atmósfera controlada. Este paso crucial fusiona las partículas metálicas, consiguiendo la resistencia y densidad deseadas para el componente final.
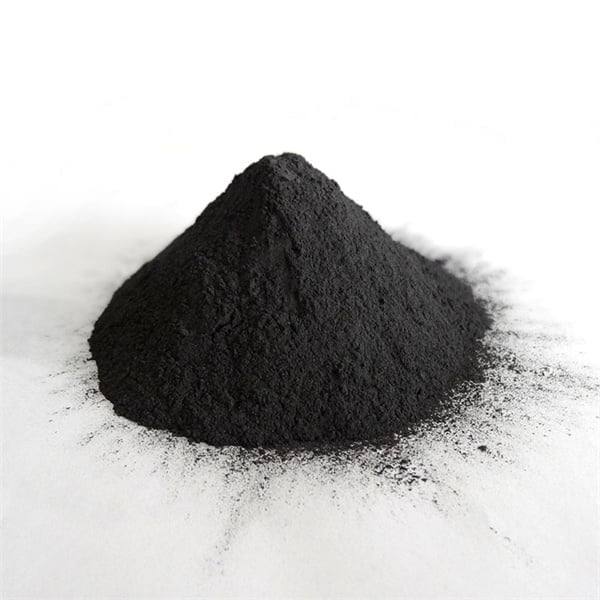
Las ventajas de Moldeo por inyección de metales (MIM)
El MIM ofrece un convincente conjunto de ventajas que lo convierten en un proceso muy solicitado por diversas industrias:
- Geometrías complejas: A diferencia de las técnicas de mecanizado tradicionales, que pueden tener dificultades con las formas complejas, el MIM destaca en la producción de componentes con características complejas, tolerancias estrechas y paredes finas. Esto abre las puertas a diseños innovadores que antes eran difíciles o imposibles de conseguir con los métodos convencionales.
- Alta precisión y repetibilidad: El MIM aprovecha la precisión del moldeo por inyección, lo que da como resultado piezas muy uniformes con variaciones dimensionales mínimas. Esto se traduce en un rendimiento fiable y una reducción de las necesidades de postprocesado.
- Producción en serie: El MIM es un proceso muy adecuado para grandes volúmenes de producción. Una vez configurado el molde, el MIM puede producir un gran número de piezas idénticas de forma eficiente, por lo que es ideal para aplicaciones que requieren una calidad constante y grandes cantidades.
- Versatilidad de materiales: El MIM cuenta con una amplia gama de materiales compatibles, desde los aceros inoxidables y aceros para herramientas más comunes hasta opciones exóticas como el titanio y el inconel. Esto permite seleccionar el material óptimo en función de la resistencia específica, la resistencia a la corrosión u otros requisitos de rendimiento de la aplicación.
- Rentabilidad: En comparación con las técnicas de mecanizado tradicionales, especialmente para geometrías complejas, el MIM puede ofrecer importantes ahorros de costes. La capacidad de forma casi neta minimiza el desperdicio de material y reduce la necesidad de extensas operaciones de mecanizado.
Aplicaciones del moldeo por inyección de metales (MIM)
Las diversas ventajas del MIM lo han convertido en una opción popular en un amplio espectro de industrias. He aquí algunos ejemplos destacados:
- Automóvil: El MIM brilla en el sector de la automoción, donde produce componentes intrincados como engranajes, piñones, componentes de válvulas y piezas del sistema de combustible, conocidos por su durabilidad y precisión dimensional.
- Productos sanitarios: La naturaleza biocompatible de ciertos materiales MIM los hace perfectos para aplicaciones médicas. El MIM se utiliza para crear intrincados instrumentos quirúrgicos, implantes y componentes de diversos dispositivos médicos.
- Electrónica de consumo: La capacidad de producir piezas pequeñas y complejas con gran precisión hace que el MIM sea ideal para la industria de la electrónica de consumo. El MIM se utiliza en conectores, carcasas y componentes internos de diversos dispositivos electrónicos.
- Aeroespacial y defensa: Los exigentes requisitos de los sectores aeroespacial y de defensa se adaptan bien al MIM. El MIM produce componentes ligeros y de alta resistencia para aviones, naves espaciales y sistemas de armamento.
Más allá de los beneficios: Consideraciones sobre el MIM
Aunque el MIM ofrece un sinfín de ventajas, es esencial tener en cuenta algunos factores antes de elegirlo para su aplicación específica:
- Limitaciones del tamaño de las piezas: Actualmente, el MIM tiene limitaciones en cuanto al tamaño máximo de las piezas que puede producir. Las piezas que superan un determinado volumen podrían ser más adecuadas para las técnicas tradicionales de trabajo del metal.
- Limitaciones materiales: Aunque el MIM ofrece una amplia gama de materiales, es posible que algunas aleaciones exóticas o especiales no estén disponibles fácilmente o no sean rentables a través del MIM.
- Costes de desarrollo: Establecer el proceso MIM para un nuevo componente requiere una inversión inicial en el desarrollo del molde y la optimización del proceso. Este factor de coste debe sopesarse con el volumen de producción potencial y los beneficios a largo plazo.
Entender el MIM: una inmersión técnica profunda
Para los interesados en los entresijos técnicos del MIM, he aquí algunos aspectos clave:
Selección de materias primas: La selección de la materia prima adecuada es crucial para el éxito del MIM. He aquí algunos aspectos clave a tener en cuenta:
- Polvo metálico:
- Tamaño y distribución de partículas: El tamaño y la distribución del polvo metálico influyen considerablemente en las propiedades finales de la pieza. Los polvos más finos suelen permitir tolerancias más estrictas y acabados más suaves, pero también pueden ser más difíciles de procesar debido a problemas de fluidez. A menudo se prefiere una distribución granulométrica equilibrada.
- Morfología del polvo: La forma de las partículas metálicas también influye. Los polvos esféricos tienden a fluir mejor y a compactarse más, lo que mejora la resistencia y la precisión dimensional.
- Sistema de encuadernación: El sistema aglutinante actúa como un pegamento temporal que mantiene unido el polvo metálico durante el moldeo y el desencolado. Los distintos sistemas aglutinantes ofrecen características variables, como la estabilidad térmica, el comportamiento de desaglomerado y la compatibilidad con el proceso de desaglomerado elegido.
Diseño de moldes para MIM:
Los moldes MIM comparten similitudes con los moldes de inyección de plástico, pero requieren consideraciones específicas para el comportamiento del polvo metálico:
- Diseño de la puerta: El diseño de las compuertas, que son los puntos de entrada de la materia prima en la cavidad del molde, debe garantizar un flujo adecuado y minimizar las turbulencias que pueden provocar defectos.
- Ventilación: Los canales de ventilación son cruciales para permitir la salida del aire atrapado durante la inyección, evitando la formación de huecos y garantizando el llenado completo de la pieza.
- Ángulos de tiro: Los ángulos de desmoldeo en las paredes del molde son esenciales para facilitar la extracción de la pieza moldeada tras el enfriamiento.
Técnicas de desbobinado en MIM:
Como se ha mencionado anteriormente, el descortezado es el paso crítico para eliminar el aglutinante de la pieza moldeada. He aquí un desglose de las dos principales técnicas de desbobinado:
- Desbobinado térmico: Este método consiste en calentar gradualmente la pieza moldeada en una atmósfera controlada. A medida que aumenta la temperatura, el aglutinante se degrada y descompone, dejando atrás la estructura de polvo metálico. El perfil de calentamiento debe diseñarse cuidadosamente para garantizar la eliminación completa del aglutinante sin dañar la delicada estructura metálica.
- Desencolado con disolvente: Esta técnica utiliza un disolvente que disuelve selectivamente el sistema aglutinante. La pieza moldeada se sumerge en el disolvente, lo que permite la lixiviación del aglutinante mientras el polvo metálico permanece intacto. El desbastado con disolvente puede ser más rápido que el desbastado térmico, pero puede requerir consideraciones especiales de manipulación y eliminación del disolvente utilizado.
Sinterización en MIM:
La sinterización es la etapa final del proceso MIM, en la que el polvo metálico desbastado se transforma en un componente sólido y funcional. Durante la sinterización, la pieza se expone a altas temperaturas (normalmente entre 1/2 y 2/3 del punto de fusión del metal) en una atmósfera controlada. Esta alta temperatura favorece la unión por difusión entre las partículas metálicas, lo que produce una densificación y una mejora significativa de la resistencia y otras propiedades mecánicas.
Control de calidad en MIM:
Mantener una calidad constante es primordial en la producción de MIM. He aquí algunas medidas esenciales de control de calidad:
- Caracterización de las materias primas: Las pruebas periódicas de las propiedades de la materia prima, como la distribución del tamaño del polvo metálico y el contenido de aglutinante, garantizan un comportamiento uniforme del material durante el procesamiento.
- Inspección dimensional: Las dimensiones de las piezas moldeadas se inspeccionan meticulosamente para garantizar que cumplen las especificaciones de diseño y mantienen tolerancias estrictas.
- Medición de la densidad: La densidad de las piezas sinterizadas es un indicador crítico de su resistencia y rendimiento. Para medir la densidad pueden utilizarse diversas técnicas, como el principio de Arquímedes o la picnometría.
- Análisis de microestructuras: El examen microscópico de la microestructura de la pieza sinterizada revela información sobre el tamaño del grano, la porosidad y los posibles defectos.
El futuro de Moldeo por inyección de metales
La MIM es una tecnología en continua evolución, con esfuerzos continuos de investigación y desarrollo centrados en:
- Ampliación de la gama de materiales: La exploración de nuevos materiales y sistemas aglutinantes compatibles con el MIM amplía las posibilidades de aplicación de este versátil proceso.
- Mejora de la eficiencia de los procesos: El objetivo de la investigación es optimizar las fases de desaglomerado y sinterización para reducir la duración de los ciclos y mejorar la eficacia global de la producción.
- Complejidad avanzada de las piezas: Los avances en el diseño de moldes y la ciencia de los materiales están ampliando los límites de la complejidad de las piezas que se pueden conseguir mediante el MIM.
Moldeo por inyección de metales ofrece una combinación única de libertad de diseño, versatilidad de materiales y rentabilidad para una amplia gama de sectores. A medida que la tecnología siga madurando, podemos esperar aplicaciones aún más innovadoras y avances en el apasionante mundo del MIM.
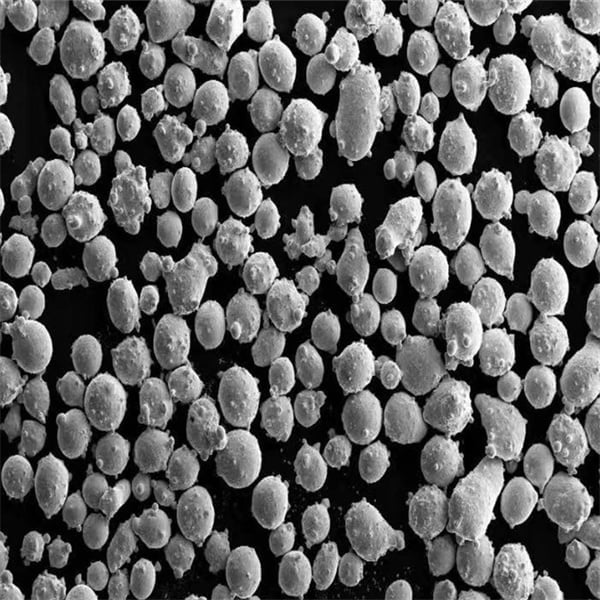
PREGUNTAS FRECUENTES
Tabla 1: Preguntas frecuentes sobre el moldeo por inyección de metales (MIM)
Pregunta | Respuesta |
---|---|
¿Cuáles son las limitaciones de tamaño típicas de las piezas MIM? | El tamaño máximo de las piezas MIM suele limitarse a unas pocas pulgadas cúbicas. Esta limitación se debe a los problemas de flujo de la materia prima y a la necesidad de garantizar un desbobinado uniforme en las piezas de mayor tamaño. |
¿Se puede utilizar el MIM para crear prototipos? | Sí, el MIM puede ser una opción viable para crear prototipos de piezas metálicas complejas, sobre todo cuando se requiere un alto grado de precisión y fidelidad al diseño final. Sin embargo, hay que tener en cuenta el coste inicial del desarrollo del molde. |
¿Cuáles son las ventajas del MIM frente al mecanizado tradicional? | El MIM ofrece varias ventajas con respecto al mecanizado tradicional, entre ellas: Capacidad para producir geometrías complejas con tolerancias estrictas Mayor libertad de diseño para elementos complejos Alta precisión y repetibilidad para piezas uniformes Eficacia de producción en serie para grandes cantidades Reducción del desperdicio de material en comparación con las técnicas sustractivas |
¿Cuáles son las desventajas del MIM frente al mecanizado tradicional? | También hay que tener en cuenta algunas limitaciones del MIM: Limitaciones del tamaño de las piezas en comparación con técnicas como la fundición o la forja Limitaciones de materiales para determinadas aleaciones exóticas o especiales Mayores costes iniciales debido al desarrollo del molde Es posible que el acabado de la superficie no se corresponda con los acabados excepcionalmente lisos que se consiguen mediante pulido o esmerilado. |
¿Qué factores hay que tener en cuenta a la hora de elegir entre el MIM y la metalurgia tradicional? | La elección ideal depende de su aplicación específica. He aquí algunos factores clave que hay que sopesar: Complejidad de la geometría de la pieza Requisitos de volumen de producción Necesidades de selección de materiales Consideraciones sobre los costes, incluida la inversión inicial y el ahorro potencial Requisitos de acabado superficial |
¿Cuáles son las tendencias futuras de la tecnología MIM? | Los esfuerzos de investigación y desarrollo del MIM se centran en ampliar la gama de materiales, mejorar la eficacia de los procesos para acelerar los tiempos de ciclo y ampliar los límites de complejidad de las piezas. |
¿Cuáles son las aplicaciones típicas del MIM? | El MIM tiene aplicaciones en una amplia gama de industrias, entre ellas: Automoción (engranajes, piñones, componentes de válvulas) Productos sanitarios (instrumentos quirúrgicos, implantes) Electrónica de consumo (conectores, carcasas) Aeroespacial y defensa (componentes ligeros de alta resistencia) |
¿Qué tipos de materias primas se utilizan en el MIM? | La materia prima del MIM suele consistir en un polvo metálico (por ejemplo, acero inoxidable, aleaciones de acero, titanio) mezclado con un sistema aglutinante polimérico. El tipo específico de polvo metálico y aglutinante dependerá de las propiedades finales deseadas de la pieza. |
¿Cuáles son las diferentes técnicas de desbobinado utilizadas en MIM? | Existen dos técnicas principales de desbobinado: Desencolado térmico: Calentamiento gradual para eliminar el aglutinante. Desaglomerante disolvente: Utilización de un disolvente para disolver selectivamente el aglutinante. |
Elegir el proceso adecuado: MIM vs. Metalurgia tradicional
La decisión entre el MIM y las técnicas metalúrgicas tradicionales depende de varios factores específicos de su aplicación. He aquí algunas consideraciones clave para orientar su elección:
- Geometría de la pieza: Si su componente tiene características complejas, tolerancias ajustadas y detalles intrincados, el MIM ofrece una ventaja significativa.
- Volumen de producción: Para series de producción de gran volumen, la eficiencia y repetibilidad del MIM lo convierten en una opción convincente.
- Selección de materiales: Asegúrate de que el material que necesitas es compatible con el MIM. Si necesita una aleación exótica no disponible en MIM, la metalurgia tradicional puede ser el camino a seguir.
- Consideraciones de costos: Hay que tener en cuenta los costes iniciales del desarrollo de moldes para MIM frente a los posibles desperdicios de material y los plazos de producción más largos de las técnicas tradicionales para piezas complejas.
- Requisitos de acabado de la superficie: Si lo primordial es un acabado superficial impecable, puede ser necesario recurrir a técnicas tradicionales como el pulido.
Conclusión
El moldeo por inyección de metal (MIM) es un proceso de fabricación potente y versátil que ofrece una combinación única de libertad de diseño, opciones de materiales y rentabilidad para una amplia gama de aplicaciones. Si conoce sus ventajas, limitaciones y comparaciones con las técnicas tradicionales de metalurgia, podrá tomar decisiones con conocimiento de causa para aprovechar el MIM para sus necesidades específicas y liberar el potencial de componentes metálicos innovadores y de alto rendimiento.
Compartir
MET3DP Technology Co., LTD es un proveedor líder de soluciones de fabricación aditiva con sede en Qingdao, China. Nuestra empresa está especializada en equipos de impresión 3D y polvos metálicos de alto rendimiento para aplicaciones industriales.
Solicite información para obtener el mejor precio y una solución personalizada para su empresa.
Artículos relacionados
Acerca de Met3DP
Actualización reciente
Nuestro producto
CONTACTO
¿Tiene alguna pregunta? ¡Envíenos un mensaje ahora! Atenderemos su solicitud con todo un equipo tras recibir su mensaje.
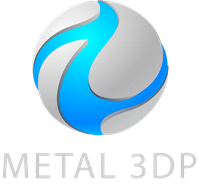
Polvos metálicos para impresión 3D y fabricación aditiva