Las fases del proceso de la tecnología MIM
Índice
¿Alguna vez ha sostenido un pequeño engranaje o un complejo componente de reloj y se ha maravillado ante sus intrincados detalles? Lo más probable es que esa intrincada pieza de metal haya nacido de un fascinante proceso llamado Moldeo por Inyección de Metal (MIM). El MIM no se limita a crear maravillas en miniatura, sino que es una poderosa técnica para fabricar piezas metálicas complejas, casi en forma de red, con una precisión y repetibilidad excepcionales.
Pero, ¿cómo transforma exactamente el MIM el fino polvo metálico en intrincados componentes metálicos? Abróchese el cinturón, porque estamos a punto de embarcarnos en un viaje al cautivador mundo de la tecnología MIM, diseccionando sus cuatro pasos principales y explorando el mundo de los polvos metálicos que alimentan este proceso.
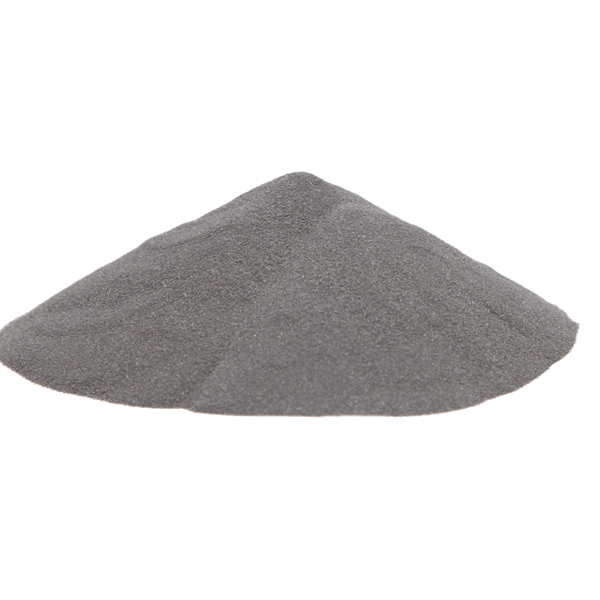
Los cuatro pasos principales de MIM Tecnología
MIM, como una obra de teatro bien ensayada, se desarrolla en cuatro actos distintos:
- Compuesto: Imagine a un experto panadero mezclando meticulosamente harina, azúcar y otros ingredientes para crear una masa perfecta. Del mismo modo, el compounding en MIM implica mezclar polvo metálico con un sistema aglutinante especial. Estos aglutinantes, que suelen consistir en termoplásticos y ceras, actúan como el pegamento que mantiene unidas las partículas metálicas durante el proceso de moldeo.
Metal Powder Mania:
El corazón del MIM reside en la diversa gama de polvos metálicos utilizados. A continuación presentamos algunos de los polvos metálicos más populares y sus propiedades únicas:
Polvo metálico | Composición | Propiedades | Aplicaciones |
---|---|---|---|
Acero inoxidable 316L | Fe (Hierro), Cr (Cromo), Ni (Níquel), Mo (Molibdeno) | Excelente resistencia a la corrosión, buena resistencia y ductilidad | Dispositivos médicos, componentes aeroespaciales, piezas de automóvil |
Acero inoxidable 17-4 PH | Fe (Hierro), Cr (Cromo), Ni (Níquel), Cu (Cobre) | Alta resistencia, buena ductilidad, endurecible por envejecimiento | Engranajes, cierres, válvulas, componentes de bombas |
Acero al carbono | Fe (hierro) con una cantidad controlada de carbono (C) | Alta resistencia, bajo coste, buena mecanizabilidad | Rodamientos, engranajes, palancas, componentes estructurales |
Níquel | Ni (níquel) | Excelente resistencia a la corrosión, alta conductividad térmica y eléctrica | Componentes electrónicos, intercambiadores de calor, equipos de procesamiento químico |
Cobre | Cu (Cobre) | Alta conductividad eléctrica y térmica, buena ductilidad | Conectores eléctricos, disipadores térmicos, materiales de soldadura fuerte |
Titanio | Ti (titanio) | Elevada relación resistencia/peso, excelente resistencia a la corrosión | Componentes aeroespaciales, implantes médicos, artículos deportivos |
Inconel 625 | Ni (Níquel), Cr (Cromo), Mo (Molibdeno) | Excepcional resistencia a altas temperaturas y a la oxidación | Componentes de turbinas de gas, piezas de motores de cohetes, intercambiadores de calor |
Kovar | Fe (Hierro), Ni (Níquel), Co (Cobalto) | Excelente adaptación a la dilatación térmica del vidrio y la cerámica | Envases electrónicos, dispositivos optoelectrónicos, juntas de vacío |
Tungsteno | W (Tungsteno) | Punto de fusión muy alto, excelente resistencia al desgaste | Herramientas de corte, electrodos, escudos térmicos |
Molibdeno | Mo (molibdeno) | Alto punto de fusión, buena conductividad térmica | Componentes del horno, contactos eléctricos, elementos calefactores |
La selección del polvo metálico adecuado depende de las propiedades deseadas de la pieza final, como la solidez, la resistencia a la corrosión y la conductividad térmica.
- Moldeado: Ahora, imagine al panadero vertiendo la masa preparada en un molde para crear la forma deseada. En el MIM, la materia prima compuesta (mezcla de polvo metálico y aglutinante) se inyecta a alta presión en un molde de acero diseñado con precisión. Este proceso de moldeo por inyección reproduce los intrincados detalles de la cavidad del molde en la pieza verde, que es el término técnico para el componente recién formado antes de su posterior procesamiento.
- Debinding: Imagínese al pastelero sacando con cuidado la tarta del molde, dejando tras de sí una hermosa creación. El desmoldeo en MIM es un proceso controlado en el que el aglutinante se elimina gradualmente de la pieza verde. Esto puede lograrse mediante técnicas térmicas o basadas en disolventes. La eliminación del aglutinante es crucial, ya que permite que las partículas metálicas se acerquen entre sí, allanando el camino para la etapa final.
- Sinterización: El acto final de la obra MIM es como hornear el pastel. La sinterización consiste en calentar la pieza desbastada en una atmósfera controlada a una temperatura cercana, pero inferior, al punto de fusión del polvo metálico. Esta alta temperatura favorece el crecimiento del grano y la unión entre las partículas metálicas, lo que da como resultado un componente metálico de alta densidad con forma casi de red y excelentes propiedades mecánicas.
Las ventajas de MIM Tecnología
El MIM ofrece una serie de ventajas convincentes que lo convierten en una técnica de fabricación muy solicitada:
- Geometrías complejas: A diferencia del mecanizado tradicional, el MIM destaca en la producción de formas complejas con tolerancias estrechas.
- Fabricación en forma próxima a la red: En comparación con el mecanizado tradicional, el MIM reduce al mínimo la necesidad de extensos pasos de postprocesado. Las piezas salen del proceso de sinterización muy próximas a sus dimensiones finales, lo que reduce el desperdicio de material y el tiempo de producción.
- Alta precisión y repetibilidad: El MIM ofrece un control excepcional de la precisión dimensional y la uniformidad entre piezas. Esto es especialmente beneficioso para aplicaciones que requieren componentes idénticos en grandes cantidades.
- Versatilidad de materiales: Como ya hemos explicado, el MIM es compatible con una amplia gama de polvos metálicos, lo que permite crear piezas con propiedades diversas que se adaptan a necesidades específicas.
- Rentabilidad: Para series de producción complejas y de gran volumen, el MIM puede ser una alternativa rentable al mecanizado tradicional. El reducido desperdicio de material y el mínimo postprocesado contribuyen a su viabilidad económica.
- Libertad de diseño: El MIM abre las puertas a diseños innovadores que podrían resultar difíciles o imposibles de conseguir mediante técnicas convencionales. Esta libertad de diseño permite a los ingenieros ampliar los límites de la funcionalidad del producto.
Desventajas de la tecnología MIM
Aunque el MIM es una tecnología potente, no está exenta de limitaciones:
- Inversión inicial elevada: La creación de una línea de producción de MIM requiere importantes costes iniciales en equipos y herramientas. Esto puede suponer un obstáculo para las empresas más pequeñas o con volúmenes de producción limitados.
- Limitaciones del tamaño de las piezas: El tamaño de las piezas MIM suele estar restringido debido a las limitaciones del proceso de moldeo por inyección y a los posibles problemas durante el desbobinado y la sinterización.
- Acabado superficial: Es posible que las piezas MIM no alcancen el mismo nivel de acabado superficial que las producidas mediante mecanizado u otras técnicas. Sin embargo, las técnicas de postprocesado, como el pulido o el volteo, pueden mejorar la estética de la superficie.
- Consideraciones sobre el diseño: El diseño de piezas MIM debe tener en cuenta factores como las propiedades del material, los ángulos de desmoldeo y los posibles problemas de desbobinado. Es fundamental consultar a ingenieros expertos en MIM durante la fase de diseño.
Aplicaciones de la tecnología MIM
El MIM se aplica en una amplia gama de sectores gracias a su capacidad para producir piezas metálicas complejas y de alta precisión. He aquí algunos ejemplos destacados:
- Productos sanitarios: El MIM se utiliza mucho en la fabricación de componentes médicos complejos, como endoprótesis, implantes e instrumentos quirúrgicos. La biocompatibilidad de ciertos polvos metálicos y la alta precisión del MIM lo hacen ideal para estas aplicaciones críticas.
- Aeroespacial y defensa: Las industrias aeroespacial y de defensa utilizan el MIM para componentes que requieren una elevada relación resistencia-peso, una excelente resistencia al calor y tolerancias estrictas. Algunos ejemplos son los componentes de motores a reacción, misiles y armas de fuego.
- Automóvil: El MIM se utiliza cada vez más en la industria del automóvil para la producción de engranajes complejos, piezas de transmisión y componentes del sistema de combustible. La capacidad de producción de formas casi netas y la versatilidad de los materiales del MIM contribuyen a su creciente adopción en este sector.
- Electrónica: El MIM interviene en la creación de componentes electrónicos en miniatura con características complejas, como conectores, carcasas y disipadores de calor. La alta conductividad y la precisión dimensional del MIM lo hacen idóneo para estas aplicaciones.
- Bienes de consumo: Desde componentes de relojes hasta artículos deportivos, el MIM se está abriendo camino en una gran variedad de productos de consumo. La capacidad de producir formas complejas con una buena estética lo convierte en una opción atractiva para determinadas aplicaciones de bienes de consumo.
Consideraciones para la elección MIM
El MIM es una tecnología potente, pero no es una solución universal. Estos son algunos factores clave que debe tener en cuenta para decidir si el MIM es la opción adecuada para su aplicación:
- Parte Complejidad: Si su diseño implica formas complejas, paredes finas o características internas, el MIM puede ser la solución perfecta.
- Volumen de producción: El MIM destaca en series de producción de gran volumen, donde brilla su rentabilidad.
- Requisitos materiales: A la hora de seleccionar un polvo metálico compatible con el MIM, hay que tener en cuenta las propiedades deseadas, como la solidez, la resistencia a la corrosión y la conductividad térmica.
- Tamaño de la pieza: Asegúrese de que el diseño de su pieza se ajusta a las limitaciones de tamaño de la tecnología MIM.
- Presupuesto: Los costes de inversión iniciales asociados a MIM La configuración debe tenerse en cuenta a la hora de tomar una decisión.
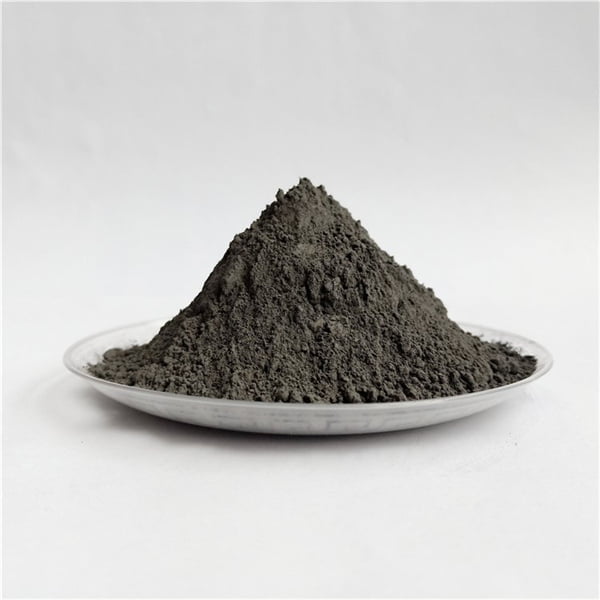
PREGUNTAS FRECUENTES
P: ¿Cuál es la diferencia entre el MIM y el mecanizado tradicional?
R: El mecanizado tradicional consiste en retirar material de un bloque sólido para crear la forma deseada. El MIM, en cambio, construye la pieza capa a capa utilizando polvo metálico y un sistema aglutinante. El MIM ofrece ventajas para geometrías complejas, fabricación de formas casi netas y producción de grandes volúmenes.
P: ¿Qué tipos de polvos metálicos se utilizan en el MIM?
R: Una amplia gama de polvos metálicos son compatibles con el MIM, incluidos aceros inoxidables, aceros al carbono, níquel, cobre, titanio y diversas aleaciones. La elección del polvo metálico depende de las propiedades deseadas de la pieza final.
P: ¿Cuáles son las limitaciones de acabado superficial de las piezas MIM?
R: Las piezas MIM pueden tener un acabado superficial ligeramente más rugoso que los componentes mecanizados. Sin embargo, las técnicas de postprocesado como el pulido, el volteo o el vibroacabado pueden mejorar significativamente la estética de la superficie.
P: ¿Se puede utilizar el MIM para piezas multimaterial?
R: El MIM suele limitarse a piezas de un solo material. Sin embargo, pueden emplearse técnicas como el moldeo por inserción de metal para crear componentes híbridos con elementos de metal y plástico.
P: ¿Cuáles son las consideraciones medioambientales del MIM?
R: El proceso de desbobinado en MIM puede implicar disolventes que requieren una manipulación y eliminación adecuadas para minimizar el impacto medioambiental. Los fabricantes adoptan cada vez más técnicas de desbobinado respetuosas con el medio ambiente para hacer frente a este problema.
P: ¿Cuál es el futuro de la tecnología MIM?
R: La tecnología MIM evoluciona constantemente. Los avances en el desarrollo del polvo metálico, las técnicas de desbobinado y los procesos de sinterización están ampliando los límites de las capacidades del MIM. Es de esperar que en el futuro se creen piezas aún más complejas y de alto rendimiento mediante MIM.
Conclusión
La tecnología MIM ofrece una combinación única de libertad de diseño, alta precisión y rentabilidad para la producción de componentes metálicos complejos con forma casi de red. Con su creciente versatilidad y sus continuos avances, el MIM está llamado a desempeñar un papel aún más importante en diversos sectores en los próximos años. Si usted es diseñador, ingeniero o simplemente siente curiosidad por las técnicas de fabricación innovadoras, comprender el potencial del MIM puede abrirle las puertas a interesantes posibilidades en el mundo de la creación de piezas metálicas.
Compartir
MET3DP Technology Co., LTD es un proveedor líder de soluciones de fabricación aditiva con sede en Qingdao, China. Nuestra empresa está especializada en equipos de impresión 3D y polvos metálicos de alto rendimiento para aplicaciones industriales.
Solicite información para obtener el mejor precio y una solución personalizada para su empresa.
Artículos relacionados
Acerca de Met3DP
Actualización reciente
Nuestro producto
CONTACTO
¿Tiene alguna pregunta? ¡Envíenos un mensaje ahora! Atenderemos su solicitud con todo un equipo tras recibir su mensaje.
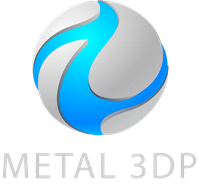
Polvos metálicos para impresión 3D y fabricación aditiva