El poder transformador de la tecnología MIM en los productos sanitarios
Índice
Imagine un mundo en el que puedan fabricarse en serie dispositivos médicos complejos y de alto rendimiento con una precisión y uniformidad sin precedentes. Esta es la realidad a la que da paso el moldeo por inyección de metal (MIM), un revolucionario proceso de fabricación que está a punto de redefinir el panorama de la tecnología médica.
¿Qué es la MIM y ¿Cómo funciona?
Piense en el MIM como una unión entre los mejores aspectos del moldeo por inyección de plástico y la metalurgia tradicional. He aquí un desglose de la magia que hay detrás del MIM:
- Poder de la pólvora: El proceso comienza con un polvo metálico meticulosamente formulado, meticulosamente elegido en función de las propiedades deseadas del producto final. Más adelante profundizaremos en las opciones específicas de polvo metálico.
- Binder Magic: A continuación, este polvo metálico se mezcla meticulosamente con un aglutinante, un polímero que actúa como pegamento, manteniendo unidas las partículas metálicas individuales. La mezcla resultante, denominada materia prima, tiene una consistencia similar a la plastilina, lo que permite darle una forma precisa.
- Moldeado Marvel: A continuación, la materia prima se inyecta a alta presión en una cavidad de molde diseñada con precisión, imitando el proceso utilizado para el moldeo por inyección de plástico. Esta increíble precisión permite crear geometrías complejas con detalles intrincados.
- Debinding Drama: Una vez finalizado el moldeo, el aglutinante se elimina meticulosamente mediante un proceso térmico de desligado. Esto implica calentar cuidadosamente la pieza moldeada en una atmósfera controlada, permitiendo que el aglutinante se volatilice (se convierta en gas) y escape, dejando tras de sí un frágil esqueleto metálico.
- Sinfonía de sinterización: El último paso es un proceso de sinterización a alta temperatura. En él, las partículas metálicas se calientan a una temperatura justo por debajo de su punto de fusión, lo que hace que se fusionen y adquieran fuerza. Esto transforma el frágil esqueleto metálico en un producto final robusto y con forma de red.
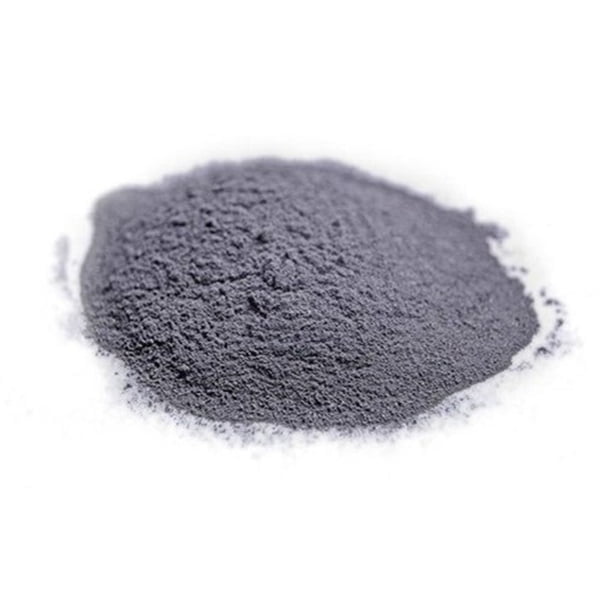
Elegir la herramienta adecuada para el trabajo
El corazón del MIM reside en la selección del polvo metálico. Los distintos polvos metálicos ofrecen una combinación única de propiedades, lo que los hace ideales para aplicaciones específicas en dispositivos médicos. A continuación presentamos algunos de los polvos metálicos más utilizados en MIM:
Polvos metálicos comunes utilizados en MIM para dispositivos médicos
Polvo metálico | Composición | Propiedades | Aplicaciones en productos sanitarios |
---|---|---|---|
Acero inoxidable 316L | Fe (Hierro), Cr (Cromo), Ni (Níquel), Mo (Molibdeno) | Excelente resistencia a la corrosión, biocompatible, alta resistencia | Tornillos óseos, implantes dentales, instrumental quirúrgico |
Acero inoxidable 17-4 PH | Fe (Hierro), Cr (Cromo), Ni (Níquel), Cu (Cobre) | Alta resistencia, buena ductilidad, buena resistencia a la corrosión | Muelles, clips, engranajes, carcasas para dispositivos implantables |
Aleación de CoCrMo | Co (cobalto), Cr (cromo), Mo (molibdeno) | Excepcional resistencia al desgaste, biocompatible | Componentes de implantes de cadera y rodilla |
Titanio (Ti) | Ti (titanio) | Ligero, alta relación resistencia-peso, excelente biocompatibilidad | Implantes dentales, tornillos óseos, dispositivos de fijación de fracturas |
MP35N (Nitronic 60) | Fe (Hierro), Cr (Cromo), Ni (Níquel), Mo (Molibdeno), N (Nitrógeno) | Alta resistencia, excelente resistencia al desgaste, buena resistencia a la corrosión | Instrumentos quirúrgicos, dispositivos de fijación ósea |
C40 (acero al carbono) | Fe (hierro), C (carbono) | Bajo coste, buena maquinabilidad | Componentes de dispositivos médicos no implantables, carcasas |
Acero inoxidable 304L | Fe (Hierro), Cr (Cromo), Ni (Níquel) | Buena resistencia a la corrosión, biocompatible | Carcasas, conectores para productos sanitarios |
Inconel 625 | Ni (Níquel), Cr (Cromo), Mo (Molibdeno), Fe (Hierro) | Excepcional rendimiento a altas temperaturas, buena resistencia a la corrosión | Componentes para dispositivos implantables expuestos a altas temperaturas |
Hastelloy C-276 | Ni (Níquel), Mo (Molibdeno), Cr (Cromo), W (Wolframio) | Excelente resistencia a la corrosión frente a una amplia gama de productos químicos | Componentes para productos sanitarios expuestos a entornos químicos agresivos |
Tungsteno (W) | W (Tungsteno) | Alta densidad, excepcional opacidad a los rayos X | Componentes de blindaje contra las radiaciones en equipos médicos de diagnóstico por imagen |
Las maravillosas ventajas del MIM
MIM ofrece una serie de ventajas que están revolucionando el sector de los dispositivos médicos:
- Precisión y complejidad inigualables: El MIM permite crear geometrías complejas con tolerancias muy ajustadas que resultarían increíblemente complicadas o prohibitivas desde el punto de vista económico si se utilizaran técnicas de mecanizado tradicionales. Imagine engranajes diminutos, delicadas estructuras reticulares e intrincados canales internos: todo ello es posible con el MIM.
- Proeza en la producción en masa: A diferencia de métodos tradicionales como el mecanizado, el MIM destaca en la producción de grandes volúmenes. Esto se traduce en una fabricación rentable de dispositivos médicos complejos, haciéndolos más accesibles a los pacientes.
- Material Magic: MIM ofrece una amplia selección de polvos metálicos que permiten crear dispositivos médicos con propiedades adaptadas con precisión. ¿Necesita un implante biocompatible? El acero inoxidable 316L o el titanio pueden ser sus héroes. ¿Una prótesis articular muy resistente al desgaste? El CoCrMo entra en escena. El MIM pone el poder de la selección de materiales al alcance de su mano.
- Libertad de diseño desatada: Atrás han quedado las limitaciones de la fabricación tradicional. La capacidad del MIM para producir formas complejas abre un mundo de posibilidades de diseño para los dispositivos médicos. Imagine instrumentos quirúrgicos más ligeros y ergonómicos o implantes que imiten las estructuras óseas naturales, todo ello gracias a la libertad de diseño que ofrece el MIM.
- La fuerza en envases pequeños: El MIM es excelente para fabricar componentes pequeños y muy resistentes. Por eso es ideal para dispositivos médicos delicados, como microfluidos para la administración de fármacos o componentes intrincados de marcapasos. Es como fabricar piezas robustas en miniatura, perfectas para el intrincado mundo de la tecnología médica.
- No desperdicies, no quieras: El MIM es un proceso extraordinariamente eficaz, que minimiza el desperdicio de material en comparación con las técnicas de mecanizado tradicionales. Esto se traduce en un ahorro de costes y en un proceso de fabricación más respetuoso con el medio ambiente, una situación en la que tanto los fabricantes como el medio ambiente salen ganando.
Consideraciones y limitaciones del MIM
Aunque el MIM presenta una notable serie de ventajas, es importante reconocer sus limitaciones:
- Limitaciones materiales: No todos los metales son adecuados para el MIM. Los metales con puntos de fusión altos o los que se oxidan con facilidad pueden ser difíciles de procesar mediante MIM.
- Rugosidad superficial: Las piezas producidas por MIM pueden tener un acabado superficial ligeramente más rugoso que las piezas mecanizadas. Esto puede no ser ideal para aplicaciones que requieren una superficie perfectamente lisa. Sin embargo, las técnicas de postprocesado, como el pulido, pueden ayudar a mitigar esta limitación.
- Restricciones del tamaño de las piezas: Existen limitaciones en cuanto al tamaño de las piezas que pueden fabricarse con MIM. Las piezas muy grandes o muy pequeñas pueden ser más adecuadas para otras técnicas de fabricación.
- ** Costes iniciales:** Los costes iniciales de configuración del MIM pueden ser más elevados que los de algunos métodos tradicionales. Sin embargo, estos costes suelen verse compensados por la eficiencia y la rentabilidad de la producción de grandes volúmenes mediante MIM.
MIM en acción: Un tour de force en dispositivos médicos
El impacto de MIM en la industria de los dispositivos médicos es nada menos que transformador. He aquí algunos ejemplos cautivadores de cómo MIM está marcando la diferencia:
- Los implantes echan raíces: Desde tornillos óseos biocompatibles e implantes dentales hasta componentes intrincados en prótesis de rodilla y cadera, el MIM permite crear implantes más duraderos y resistentes que se integran a la perfección en el cuerpo humano.
- Instrumentos quirúrgicos con delicadeza: Imagine instrumentos quirúrgicos delicados con características intrincadas, creados para una precisión y un control inigualables. MIM lo hace realidad, permitiendo a los cirujanos operar con una destreza inigualable y una invasión mínima.
- El quid de la cuestión: El MIM desempeña un papel vital en la producción de componentes para marcapasos, desfibriladores y otros dispositivos cardíacos. Su capacidad para crear piezas en miniatura de alta precisión es crucial para estas tecnologías que salvan vidas.
- Un futuro más brillante para el diagnóstico: La MIM está causando sensación en el mundo del diagnóstico médico. Los complejos componentes microfluídicos de los sistemas de administración de fármacos y los dispositivos lab-on-a-chip son sólo algunos ejemplos. MIM está impulsando la innovación en el diagnóstico.
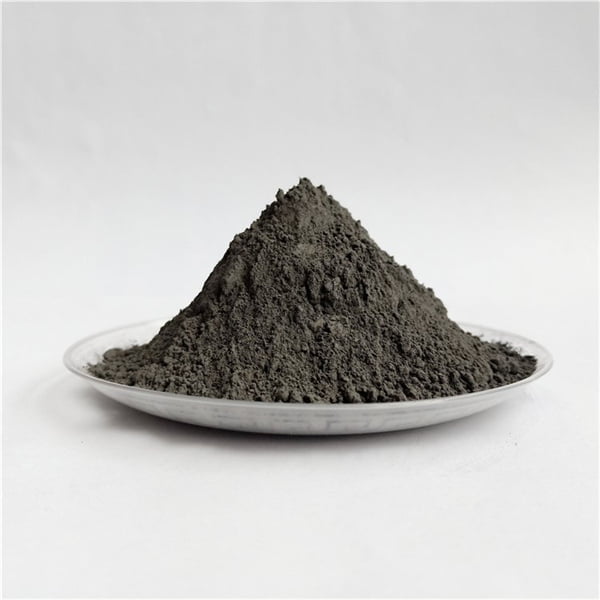
PREGUNTAS FRECUENTES
Estas son algunas de las preguntas más frecuentes sobre la tecnología MIM:
P: ¿Es seguro el MIM para dispositivos médicos?
R: Cuando se utiliza con polvos metálicos biocompatibles adecuados, el MIM es perfectamente seguro para dispositivos médicos. La selección del polvo metálico adecuado es crucial, y la realización de pruebas rigurosas garantiza la seguridad y biocompatibilidad de los productos sanitarios fabricados con MIM.
P: ¿Qué resistencia tienen las piezas MIM?
R: Las piezas MIM pueden ser increíblemente resistentes, dependiendo del polvo metálico elegido y del proceso de sinterización. El MIM puede alcanzar niveles de resistencia comparables a los de las piezas mecanizadas tradicionalmente.
P: ¿Cuáles son las implicaciones económicas del MIM?
R: Aunque los costes iniciales pueden ser más elevados, el MIM ofrece importantes ventajas económicas en la producción de grandes volúmenes. La eficiencia del proceso y el mínimo desperdicio de material contribuyen a su rentabilidad para los dispositivos médicos producidos en serie.
P: ¿Es el MIM adecuado para todos los productos sanitarios?
R: El MIM es más adecuado para dispositivos médicos complejos de tamaño pequeño o mediano que requieren alta precisión y geometrías intrincadas. Para piezas muy grandes o muy pequeñas, o que requieran un acabado superficial ultrasuave, podrían ser más apropiadas otras técnicas de fabricación.
El futuro de los productos sanitarios: Formado por la MIM
La tecnología MIM está llamada a desempeñar un papel aún más importante en el futuro de los dispositivos médicos. A medida que la tecnología siga evolucionando, podemos esperar ver dispositivos médicos aún más intrincados y sofisticados fabricados con MIM. Esto dará lugar a una mayor funcionalidad, mejores resultados para los pacientes y una nueva era de innovación en el sector de los dispositivos médicos.
Compartir
MET3DP Technology Co., LTD es un proveedor líder de soluciones de fabricación aditiva con sede en Qingdao, China. Nuestra empresa está especializada en equipos de impresión 3D y polvos metálicos de alto rendimiento para aplicaciones industriales.
Solicite información para obtener el mejor precio y una solución personalizada para su empresa.
Artículos relacionados
Acerca de Met3DP
Actualización reciente
Nuestro producto
CONTACTO
¿Tiene alguna pregunta? ¡Envíenos un mensaje ahora! Atenderemos su solicitud con todo un equipo tras recibir su mensaje.
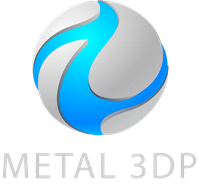
Polvos metálicos para impresión 3D y fabricación aditiva