Aplicación de la tecnología MIM en la industria aeroespacial
Índice
Imagine un mundo en el que la fabricación de piezas complejas y de alto rendimiento para aviones no fuera una carrera contra el peso y la complejidad. Un mundo en el que la fabricación de formas casi netas ofreciera la resistencia del metal con la precisión del plástico. El moldeo por inyección de metal (MIM), una maravilla tecnológica que está transformando silenciosamente la industria aeroespacial.
Tecnología MIM: A vista de pájaro
El MIM cambia las reglas del juego para los fabricantes aeroespaciales que buscan un equilibrio entre un diseño ligero y una resistencia inquebrantable. Es como hornear un complejo pastel de metal. Esto es lo esencial:
- Mezclar la masa: Los polvos metálicos, normalmente superaleaciones y aceros inoxidables, se mezclan meticulosamente con un aglutinante para crear una materia prima con propiedades moldeables.
- Dar forma a la masa: La materia prima se inyecta a alta presión en un molde diseñado con precisión, imitando los intrincados detalles de la pieza deseada.
- Horneado y fermentación: El aglutinante se elimina mediante un proceso térmico de desencolado, dejando tras de sí una frágil réplica metálica.
- Sinterización para mayor resistencia: La estructura metálica restante se somete a sinterización a alta temperatura, transformándola en una forma robusta y casi definitiva.
Polvos metálicos: Los componentes básicos del vuelo
El éxito del MIM depende del tipo de polvo metálico utilizado. He aquí un vistazo a algunos de los actores clave:
Polvos de acero inoxidable:
- 316L: El caballo de batalla de los aceros inoxidables, que ofrece una excelente resistencia a la corrosión y buena conformabilidad (perfecto para piezas intrincadas).
- 17-4 PH: Presenta una resistencia y dureza superiores a las de los aceros inoxidables estándar, ideal para piezas que soportan grandes esfuerzos.
Polvos de superaleación:
- Inconel 625: Conocida por su excepcional resistencia a las altas temperaturas y a los entornos agresivos, es la mejor opción para los componentes de los motores a reacción.
- Hastelloy X: Otro campeón en la lucha contra el calor y la corrosión, muy adecuado para piezas expuestas a condiciones extremas.
- Nimonic 90: Esta aleación de níquel-cromo brilla en aplicaciones de alta temperatura por su notable resistencia a la fluencia (capacidad de resistir la deformación bajo tensión).
Polvos de titanio:
- Grado 2: El polvo de titanio de referencia por su excelente relación resistencia-peso y su buena resistencia a la corrosión, ideal para componentes ligeros de fuselajes de aviones.
- Grado 6: Ofrece una atractiva combinación de resistencia, ductilidad (capacidad de deformarse sin romperse) y excelente resistencia a la corrosión, lo que lo hace versátil para diversas aplicaciones aeroespaciales.
Otros polvos notables:
- Aleaciones de aluminio: Estos ligeros contendientes aportan un importante ahorro de peso, especialmente beneficioso para los componentes no críticos.
- Aceros para herramientas: Conocidos por su excepcional resistencia al desgaste, estos polvos se utilizan para moldes y herramientas dentro del propio proceso MIM.
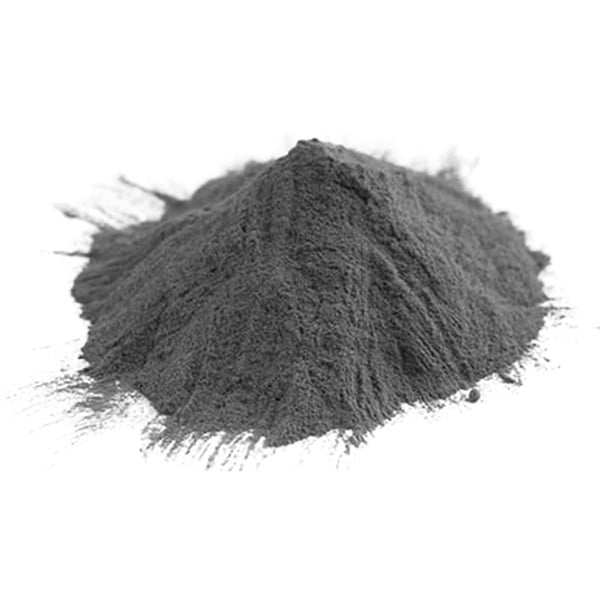
El Arsenal de MIM: Aplicaciones
La tecnología MIM no es sólo cuestión de materiales sofisticados, sino también de fabricar componentes cruciales para que los aviones sigan volando. Aquí te mostramos cómo se fabrican las piezas MIM:
Aplicación | Ventajas del MIM | Ejemplos |
---|---|---|
Componentes del motor | El MIM ofrece detalles intrincados y resistencia a altas temperaturas para piezas como: | * Álabes de turbina * Guías * Toberas * Camisas de cámara de combustión |
Sistemas de combustible | El MIM garantiza precisión y rendimiento a prueba de fugas en componentes como: | * Inyectores * Filtros * Válvulas |
Sistemas de tren de aterrizaje | El MIM ofrece soluciones ligeras y robustas para piezas como: | * Componentes del actuador * Rodamientos * Juntas |
Sistemas de control de vuelo | El MIM garantiza un funcionamiento preciso y fiable en piezas como: | * Palancas * Engranajes * Poleas |
Otras aplicaciones | La versatilidad del MIM se extiende a: | * Elementos de fijación (tornillos, tuercas, pernos) * Carcasas * Soportes |
MIM frente a la fabricación tradicional
La batalla por los campeones ligeros
Cuando se trata de fabricar piezas complejas y de alto rendimiento para aviones, tanto el moldeo por inyección de metal (MIM) como los métodos de fabricación tradicionales, como el mecanizado y la fundición, se disputan el dominio. Pero, ¿cuál es el mejor? He aquí un rápido desglose para ayudarle a decidir:
MIM: La estrella en alza
- Puntos fuertes:
- Rey de la Complejidad: El MIM destaca en la producción de formas intrincadas con un procesamiento posterior mínimo, ideal para componentes aeroespaciales ligeros y complejos.
- Material Marvel: Ofrece una amplia gama de polvos metálicos que permiten que las piezas resistan temperaturas extremas y entornos difíciles.
- Potencia de producción masiva: Eficiente para la producción de grandes volúmenes, garantizando un suministro constante de piezas vitales de aeronaves.
- Debilidades:
- Factor de coste: La creación de una línea de MIM requiere una elevada inversión inicial, lo que repercute en los costes de producción de bajo volumen.
- Material Matchmaker: No todos los metales pueden fabricarse por MIM. Las aleaciones exóticas pueden requerir métodos tradicionales.
- Restricciones de tamaño: Actualmente existen limitaciones en cuanto al tamaño de las piezas, aunque la tecnología evoluciona constantemente.
Fabricación tradicional: La flota establecida
- Puntos fuertes:
- Métodos de eficacia probada: Los métodos tradicionales, como el mecanizado y la fundición, tienen una larga historia de éxitos en diversas aplicaciones.
- Flexibilidad del material: Puede manipular una gama más amplia de materiales en comparación con el MIM.
- Económico para lotes pequeños: Suele ser la opción más rentable para la producción de piezas sencillas o de bajo volumen.
- Debilidades:
- Desafío de la complejidad: Los métodos tradicionales tienen dificultades con las formas complejas, que a menudo requieren un mecanizado exhaustivo, lo que aumenta el coste y el plazo de entrega.
- Residuos materiales: Una importante eliminación de material durante el mecanizado conlleva un aumento de los residuos y, potencialmente, de los costes.
- Velocidad de producción: Puede ser más lento para piezas complejas en comparación con la eficiencia de gran volumen del MIM.
El veredicto: depende de su ruta de vuelo
El MIM brilla por producción de grandes volúmenes de piezas complejas y ligeras donde las propiedades del material son cruciales. Los métodos tradicionales siguen siendo una buena opción para poco volumen o geometrías más sencillas y una gama más amplia de materiales. En última instancia, la mejor opción depende de sus necesidades específicas: complejidad de la pieza, volumen de producción y requisitos de material.
Ventajas y desventajas del MIM: la perspectiva de un piloto
El impacto del MIM en la industria aeroespacial se dispara, pero, como cualquier tecnología, tiene su propio patrón de vuelo. Profundicemos en sus convincentes ventajas y reconozcamos los posibles inconvenientes que hay que tener en cuenta:
Volar alto con el MIM: las ventajas
- Campeón de peso ligero: Las piezas MIM presentan una relación resistencia-peso excepcional, un factor crucial para la eficiencia del combustible y el rendimiento general del avión. Imagine un avión que pierde kilos sin sacrificar un ápice de resistencia: ésa es la magia del MIM.
- Proezas de forma casi neta: El MIM produce piezas cercanas a su forma final, minimizando la necesidad de un mecanizado exhaustivo. Esto se traduce en tiempos de producción más rápidos, menos desperdicio de material y costes generales más bajos, lo que beneficia tanto a los fabricantes como al medio ambiente.
- Libertad de diseño: La capacidad del MIM para manejar geometrías complejas abre nuevas posibilidades de diseño. Piense en intrincados canales de refrigeración en componentes del motor o en soportes ligeros de alta resistencia: el MIM permite a los ingenieros ampliar los límites del diseño sin comprometer la funcionalidad.
- Potencia de producción masiva: Para componentes de gran volumen, el MIM brilla con luz propia. El proceso racionalizado permite una producción rápida y constante, garantizando un suministro constante de piezas vitales para el ensamblaje de aeronaves.
- Material Marvel: La gran variedad de polvos metálicos disponibles con el MIM satisface una amplia gama de aplicaciones aeroespaciales. ¿Necesita una pieza que resista temperaturas abrasadoras? Los polvos de superaleación son la solución. ¿Busca una pieza ligera? Las aleaciones de aluminio vienen al rescate. El MIM ofrece el material perfecto para cada componente crucial.
Se avecinan turbulencias: Consideraciones para el MIM
- Limitaciones materiales: Aunque el MIM ofrece una amplia selección de polvos metálicos, no puede utilizarse con todos los materiales. Algunas aleaciones exóticas o con puntos de fusión extremadamente altos pueden no ser adecuadas para el proceso MIM.
- Inversión inicial: La creación de una línea de producción de MIM requiere una importante inversión inicial. Sin embargo, para la producción de grandes volúmenes, el ahorro de costes a largo plazo suele compensar el coste inicial.
- Restricciones del tamaño de las piezas: Existen limitaciones en cuanto al tamaño de las piezas que pueden fabricarse con MIM. Aunque la tecnología está en constante evolución, las piezas muy grandes o muy pequeñas podrían ser más adecuadas para los métodos de fabricación tradicionales.
- Acabado superficial: Las piezas MIM pueden requerir procesos de acabado adicionales para conseguir la calidad superficial deseada. Esto puede aumentar el tiempo y el coste totales de producción.
Elegir el camino correcto: ¿Cuándo es el MIM la opción ideal?
El MIM no es una solución válida para todos los casos, pero para situaciones concretas, levanta el vuelo de maravilla. Estos son algunos factores clave que debe tener en cuenta para decidir si el MIM es la opción adecuada para su aplicación aeroespacial:
- Parte Complejidad: Si su componente presenta formas o características internas complejas, el MIM puede ser un salvavidas.
- Volumen de producción: Para grandes volúmenes de producción, el MIM destaca por su eficacia y rentabilidad.
- Necesidades materiales: Si existe un polvo metálico adecuado para su aplicación, el MIM ofrece unas propiedades de material excepcionales.
- Restricciones de peso: Cuando el diseño ligero es primordial, la relación resistencia-peso del MIM cambia las reglas del juego.
El futuro del vuelo: El cielo es el límite para MIM
A medida que la industria aeroespacial continúa su incesante búsqueda de eficiencia y rendimiento, el MIM está preparado para desempeñar un papel aún más importante. He aquí un vistazo a las apasionantes posibilidades que se vislumbran en el horizonte:
- Polvos avanzados: El desarrollo de nuevos polvos metálicos con propiedades aún más extraordinarias ampliará los límites de lo que se puede conseguir con el MIM.
- Producción a mayor escala: Los avances tecnológicos prometen superar las actuales limitaciones de tamaño, permitiendo que el MIM aborde componentes aeroespaciales aún mayores.
- Fabricación híbrida: La integración del MIM con otros procesos de fabricación, como la impresión 3D, podría abrir posibilidades de diseño y eficiencias de producción totalmente nuevas.
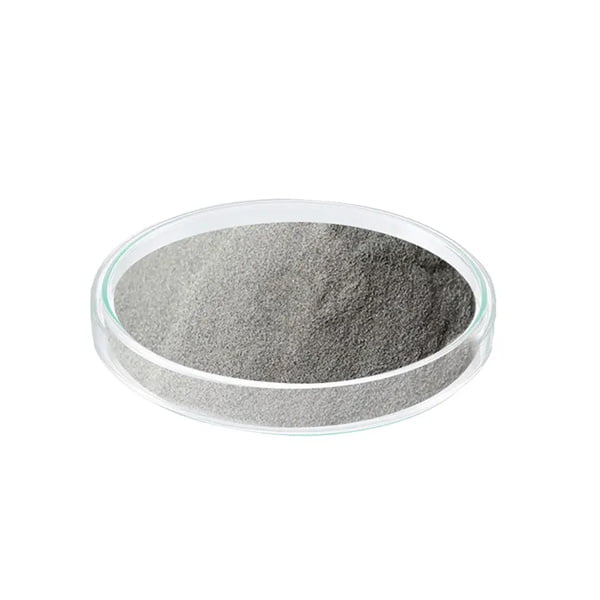
MIM en la cabina: Reflexiones finales de un piloto
El moldeo por inyección de metal no es sólo una tecnología elegante; es una revolución que se está produciendo silenciosamente en el corazón de la industria aeroespacial. Al ofrecer una combinación única de libertad de diseño, ahorro de peso y materiales de alto rendimiento, el MIM está ayudando a construir la próxima generación de aviones más ligeros, resistentes y eficientes en el consumo de combustible. A medida que seguimos explorando el potencial del MIM, el futuro del vuelo parece más brillante, más ligero y más innovador que nunca.
PREGUNTAS FRECUENTES
Pregunta | Respuesta |
---|---|
¿Cuáles son las limitaciones de tamaño de las piezas MIM? | Las limitaciones actuales suelen restringir las piezas MIM a unos pocos centímetros en cada dimensión. Sin embargo, los avances superan constantemente estos límites. |
¿Se puede utilizar el MIM para todos los metales? | No, el MIM se limita actualmente a polvos metálicos específicos con propiedades adecuadas para el proceso de moldeo. |
¿Cuál es el coste del MIM en comparación con la fabricación tradicional? | El coste del MIM depende del volumen de producción y de la complejidad de la pieza. Para piezas complejas de gran volumen, el MIM suele ser más rentable que los métodos tradicionales, debido a su eficacia y al mínimo desperdicio. Para piezas sencillas de bajo volumen, los métodos tradicionales pueden ser más baratos. |
Compartir
MET3DP Technology Co., LTD es un proveedor líder de soluciones de fabricación aditiva con sede en Qingdao, China. Nuestra empresa está especializada en equipos de impresión 3D y polvos metálicos de alto rendimiento para aplicaciones industriales.
Solicite información para obtener el mejor precio y una solución personalizada para su empresa.
Artículos relacionados
Acerca de Met3DP
Actualización reciente
Nuestro producto
CONTACTO
¿Tiene alguna pregunta? ¡Envíenos un mensaje ahora! Atenderemos su solicitud con todo un equipo tras recibir su mensaje.
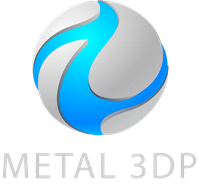
Polvos metálicos para impresión 3D y fabricación aditiva