Soportes de carga útil para satélites y aviones mediante impresión 3D
Índice
Introducción: Revolucionando los componentes aeroespaciales con soportes de carga útil impresos en 3D
La industria aeroespacial opera en el cenit de los logros de la ingeniería, exigiendo componentes que muestren un rendimiento extraordinario en condiciones extremas. Desde el vacío del espacio hasta las tensiones dinámicas del vuelo atmosférico, cada pieza debe funcionar a la perfección, a menudo superando los límites de la eficiencia del peso y la integridad estructural. Entre la miríada de componentes críticos a bordo de satélites, aeronaves y vehículos aéreos no tripulados (UAV), soportes de carga útil aeroespacial desempeñan un papel indispensable, aunque a menudo pasado por alto. Estas estructuras son la interfaz vital entre la estructura primaria del vehículo y las cargas útiles sensibles y de gran valor que transportan: instrumentos como cámaras de alta resolución, sensores sofisticados, antenas de comunicación, paquetes de experimentos científicos y mucho más. La función principal de un soporte de carga útil es aparentemente sencilla: mantener la carga útil en la posición designada, garantizando la estabilidad y la alineación precisa durante todo el ciclo de vida de la misión, que incluye el lanzamiento, el despliegue y el funcionamiento. Sin embargo, para lograrlo es necesario superar una compleja red de retos de ingeniería, como la gestión de las vibraciones, la resistencia a fuerzas G significativas durante las maniobras o el lanzamiento, la adaptación a la expansión y contracción térmicas y, sobre todo, la minimización de la masa para optimizar la eficiencia del combustible o maximizar la capacidad de la carga útil.
Tradicionalmente, para fabricar estos componentes complejos y sometidos a grandes esfuerzos se utilizaban métodos sustractivos, principalmente el mecanizado CNC a partir de materiales como el aluminio o las aleaciones de titanio, o a veces la fundición a la cera perdida para formas más complejas. Aunque fiables, estos métodos suelen imponer importantes limitaciones. El mecanizado puede dar lugar a un gran desperdicio de material (alta relación entre compra y vuelo), restringir la complejidad geométrica (dificultando o imposibilitando la producción de diseños óptimamente ligeros) y conllevar largos plazos de entrega, especialmente para piezas de bajo volumen y altamente personalizadas, típicas del sector aeroespacial. La consolidación de piezas, una estrategia clave para reducir el peso y los posibles puntos de fallo, a menudo se ve obstaculizada por las limitaciones de accesibilidad al mecanizado y al utillaje.
Entre en fabricación aditiva (AM) de metalesmás conocido como impresión 3D en metal. Esta tecnología transformadora está cambiando rápidamente el paradigma del diseño y la producción de componentes aeroespaciales de alto rendimiento, incluidos los soportes de carga útil. A diferencia de los procesos sustractivos que eliminan material, la AM construye piezas capa por capa directamente a partir de modelos digitales, utilizando normalmente fuentes de alta energía como láseres o haces de electrones para fusionar polvos metálicos finos. Esta diferencia fundamental desbloquea una libertad de diseño sin precedentes, permitiendo la creación de geometrías de gran complejidad y topología optimizada que antes no se podían fabricar. Ahora, los ingenieros pueden diseñar soportes de carga útil que sigan con precisión las trayectorias de tensión, incorporando intrincadas estructuras internas enrejadas o formas orgánicas suaves para reducir drásticamente el peso, manteniendo o incluso mejorando el rendimiento estructural (rigidez y resistencia). Además, la AM facilita la consolidación de múltiples subcomponentes en una sola pieza monolítica, eliminando fijaciones, reduciendo el tiempo de montaje, minimizando posibles vías de fuga o puntos de fallo y contribuyendo aún más al ahorro de peso. La capacidad de iterar rápidamente los diseños y producir prototipos funcionales o piezas finales directamente a partir de datos CAD también acorta considerablemente los ciclos de desarrollo, una ventaja crucial en el vertiginoso sector aeroespacial.
Empresas a la vanguardia de este cambio tecnológico, como Met3dpestán desempeñando un papel fundamental en la adopción de la AM para aplicaciones críticas. Con sede en Qingdao (China), Met3dp se especializa en el suministro de soluciones integrales de fabricación aditiva, que abarcan tanto las tecnologías más avanzadas como las más avanzadas. Impresión 3D (utilizando la fusión selectiva por haz de electrones - SEBM y otras tecnologías de fusión de lecho de polvo) y el desarrollo y producción de polvos metálicos de alto rendimiento optimizados específicamente para los procesos de AM. Con capacidades líderes en el sector en cuanto a volumen de impresión, precisión y fiabilidad, Met3dp permite a los ingenieros aeroespaciales y a los responsables de compras aprovechar todo el potencial de la AM metálica para componentes como los soportes de carga útil. Su experiencia va más allá de los equipos y materiales, ofreciendo servicios de desarrollo de aplicaciones y aprovechando décadas de experiencia colectiva para ayudar a las organizaciones a integrar la AM de forma eficaz y acelerar sus transformaciones de fabricación digital. A medida que profundicemos en las particularidades de los soportes de carga útil impresos en 3D, las ventajas que ofrece esta tecnología, impulsada por proveedores expertos como Met3dp, serán cada vez más evidentes. El viaje implica comprender las aplicaciones, los materiales, los principios de diseño y todo el ecosistema necesario para producir componentes de alto rendimiento y aptos para el vuelo que redefinan las posibilidades de la ingeniería aeroespacial.
Aplicaciones críticas: ¿Dónde se utilizan los soportes de carga útil impresos en 3D?
La adopción de la fabricación aditiva de metales para los soportes de carga útil no es un ejercicio teórico, sino una solución práctica que se está aplicando en una amplia gama de exigentes plataformas aeroespaciales. Las ventajas exclusivas de la AM (ligereza, geometrías complejas, consolidación de piezas y rapidez de producción) la hacen especialmente adecuada para aplicaciones en las que cada gramo ahorrado y cada optimización del diseño se traducen en importantes mejoras de rendimiento o ahorros de costes. Los entornos de uso de estos componentes son de los más exigentes que se puedan imaginar, ya que llevan los materiales y las estructuras al límite.
1. Plataformas de satélites (LEO, MEO, GEO, CubeSats): Los satélites representan un ámbito de aplicación primordial para los soportes de carga útil impresos en 3D. Los costes de lanzamiento son directamente proporcionales a la masa, por lo que la reducción de peso es primordial.
- Montaje de instrumentación: El montaje seguro de instrumentos ópticos sensibles, espectrómetros, radiómetros y sensores de observación de la Tierra requiere una estabilidad extrema y una alineación precisa y constante, a menudo en condiciones de ciclos térmicos a medida que el satélite entra y sale de la luz solar. La AM permite fabricar soportes con una relación rigidez-peso optimizada y características de gestión térmica potencialmente integradas (por ejemplo, complejas vías de conducción) diseñadas directamente en la estructura. La optimización de la topología garantiza que el material se coloque sólo donde sea estructuralmente necesario, lo que reduce considerablemente la masa en comparación con los soportes mecanizados tradicionales.
- Soportes de antena: Las antenas de comunicaciones, desde las pequeñas antenas de telemetría/mando hasta los grandes reflectores desplegables, necesitan estructuras de montaje robustas que puedan soportar las vibraciones del lanzamiento y mantener la precisión de apuntamiento. Las curvaturas complejas y los puntos de integración que suelen requerir los alimentadores y reflectores de antena pueden realizarse más fácilmente con AM, a veces consolidando varios soportes en una sola pieza impresa. Materiales como el Ti-6Al-4V ofrecen una excelente resistencia y rigidez específicas, ideales para estas aplicaciones.
- Integración de carcasas electrónicas: Los soportes de carga útil pueden diseñarse para integrarse directamente con las carcasas de los componentes electrónicos de carga útil, proporcionando soporte estructural, vías térmicas e interfaces de montaje en un único componente. Esta consolidación simplifica el montaje y reduce el número total de piezas.
- CubeSats y pequeños satélites: Para plataformas más pequeñas, como los CubeSats, en las que el volumen y la masa son muy limitados, la AM permite crear estructuras muy compactas y multifuncionales. Un único componente impreso puede servir como soporte de la carga útil, formar parte de la estructura del bus del satélite e incorporar elementos para el tendido de cables o correas térmicas, maximizando la utilidad dentro del diminuto factor de forma. Scalmalloy®, con su alta resistencia comparable a la del titanio pero menor densidad, resulta especialmente atractivo en este caso.
2. Aviones comerciales y militares: Aunque quizás menos limitada por la masa que los satélites, la reducción de peso en las aeronaves sigue traduciéndose directamente en ahorro de combustible o mayor capacidad de carga útil/alcance. La fiabilidad y la resistencia a la fatiga son aspectos críticos.
- Soportes para sensores y vainas: El montaje de sensores externos, módulos de reconocimiento, sistemas de puntería o equipos de comunicación en el fuselaje requiere estructuras que puedan soportar cargas aerodinámicas, vibraciones de los motores y del flujo de aire, y fuerzas G potencialmente elevadas durante las maniobras. La AM permite crear montajes conformados y aerodinámicamente eficientes que minimizan la resistencia al tiempo que proporcionan la integridad estructural necesaria. La capacidad de utilizar materiales de alta resistencia, como el Ti-6Al-4V, garantiza la durabilidad y la resistencia a la fatiga.
- Bastidores y soportes de aviónica: En el interior del avión, el montaje de las cajas y equipos de aviónica en los compartimentos designados suele requerir complejos soportes diseñados para encajar en espacios reducidos. La AM permite fabricar soportes muy personalizados y ligeros que se ajustan con precisión al espacio disponible, lo que puede consolidar varios soportes sencillos en una única estructura más eficiente.
- Soportes de cámara (internos/externos): El montaje de cámaras de vigilancia, reconocimiento o grabación en vuelo exige estabilidad para garantizar imágenes nítidas. AM puede fabricar soportes con características de amortiguación optimizadas o geometrías específicas para aislar la cámara de las vibraciones del fuselaje.
3. Vehículos aéreos no tripulados (UAV): Los vehículos aéreos no tripulados, desde los pequeños drones tácticos hasta las grandes plataformas de gran altitud y larga resistencia (HALE), son muy sensibles al peso y a menudo transportan cargas útiles sofisticadas y miniaturizadas.
- Integración del sistema de cardán: El montaje de sistemas cardán multieje con cámaras o sensores requiere estructuras ligeras pero rígidas para garantizar la estabilidad y la capacidad de apuntar con rapidez. Los soportes AM de topología optimizada son ideales para minimizar la inercia del sistema de cardán y proporcionar al mismo tiempo un soporte robusto.
- Integración de cargas útiles personalizadas: Los UAV se adaptan a menudo para misiones específicas con configuraciones de carga útil únicas. La AM permite diseñar y fabricar rápidamente montajes personalizados adaptados a sensores, antenas o paquetes de equipos específicos, lo que facilita una adaptación más rápida de la plataforma y la preparación de la misión. Scalmalloy® se considera con frecuencia debido a su excelente relación resistencia-peso, que permite tiempos de vuelo más largos o una mayor capacidad de carga útil.
- Integración estructural: En los UAV más pequeños, los soportes de carga útil pueden diseñarse como partes integrantes del propio fuselaje, lo que reduce aún más el peso y la complejidad. La capacidad de la AM para crear estructuras complejas y portantes lo hace factible.
Afrontar los retos medioambientales: En todas estas aplicaciones, los soportes de carga útil impresos en 3D deben resistir:
- Vibración: Desde la acústica de los lanzamientos y el estruendo de los motores de los cohetes hasta las sacudidas aerodinámicas y las vibraciones de los motores de los aviones. Los soportes deben diseñarse para evitar la resonancia e incorporar características de amortiguación.
- Cargas de choque: Los eventos de separación pirotécnica, los impactos de aterrizaje o las maniobras bruscas generan importantes cargas de choque.
- Extremos térmicos: Los satélites experimentan grandes oscilaciones de temperatura en órbita, mientras que los componentes de los aviones pueden estar sometidos a altas temperaturas cerca de los motores o al calentamiento por fricción a altas velocidades, así como a temperaturas criogénicas en altitud o para sistemas de propulsión específicos. La selección de materiales (como la excelente estabilidad térmica del Ti-6Al-4V) y las características de diseño que tienen en cuenta la dilatación térmica son cruciales.
- Fuerzas G: Las aceleraciones de lanzamiento, las maniobras de alta gravedad en aviones de combate y la reentrada en la atmósfera imponen cargas inerciales sustanciales.
La capacidad de la AM metálica, que utiliza materiales y técnicas de diseño avanzados, para crear soportes de carga útil capaces de satisfacer estos requisitos tan diversos y exigentes explica su creciente adopción en el sector aeroespacial. Asociarse con proveedores experimentados como Met3dp, que conocen tanto el proceso de fabricación como los matices de materiales como Scalmalloy® y Ti-6Al-4V, es clave para implementar con éxito estos componentes críticos.
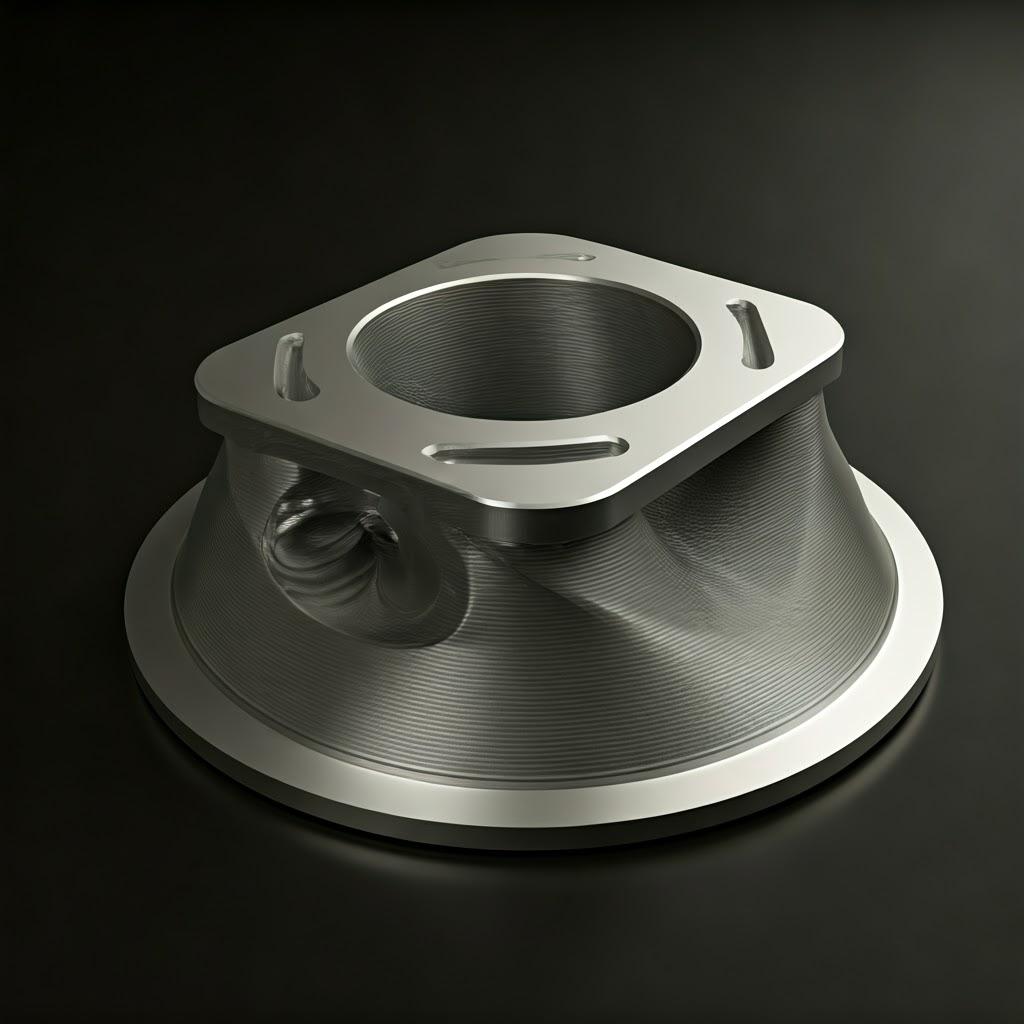
La ventaja aditiva: ¿Por qué elegir la impresión metálica 3D para los soportes de carga útil?
Aunque los métodos de fabricación tradicionales, como el mecanizado CNC y la fundición, han sido muy útiles para la industria aeroespacial durante décadas, la fabricación aditiva de metales presenta una serie de ventajas convincentes, sobre todo para componentes como los soportes de carga útil, en los que el rendimiento, el peso y la complejidad son factores clave. Optar por la AM no consiste sólo en adoptar una nueva tecnología; se trata de abrir posibilidades fundamentalmente nuevas en el diseño y la producción, lo que se traduce en beneficios tangibles en rendimiento, coste y plazo de entrega para los gestores de compras e ingenieros del sector aeroespacial.
1. Aligeramiento sin precedentes gracias a la libertad de diseño: Podría decirse que ésta es la ventaja más significativa de la AM para el sector aeroespacial. Los métodos tradicionales se ven limitados por el acceso a las herramientas y los costes de eliminación del material. La AM, que construye capa por capa, libera a los diseñadores de estas limitaciones.
- Optimización de la topología: Los algoritmos de software pueden optimizar la geometría de un soporte de carga útil en función de las cargas aplicadas, las condiciones de contorno y los objetivos de rendimiento (por ejemplo, rigidez máxima, masa mínima). Las estructuras orgánicas resultantes, similares a los huesos, colocan el material sólo donde es necesario para soportar la tensión, lo que a menudo supone un ahorro de peso de 30-60% o incluso más en comparación con las piezas diseñadas y mecanizadas de forma convencional, sin comprometer la integridad estructural. Producir estas formas complejas suele ser poco práctico o imposible con el mecanizado CNC.
- Estructuras reticulares: La AM permite integrar estructuras reticulares internas (por ejemplo, panales, giroscopios, espumas estocásticas) dentro de la geometría sólida del soporte. Estas celosías ofrecen una excepcional relación rigidez-peso, propiedades de amortiguación de vibraciones y pueden facilitar la disipación del calor si se diseñan correctamente.
- Eficiencia del material: A diferencia de la fabricación sustractiva, que puede desperdiciar hasta 80-90% del bloque de material inicial (elevado ratio de compra por vuelo), la AM es intrínsecamente más eficiente en cuanto al material. Aunque se necesitan algunas estructuras de soporte y la reutilización del polvo requiere gestión, el consumo total de material es significativamente menor, sobre todo en piezas complejas y materiales caros como las aleaciones de titanio o Scalmalloy®.
2. Consolidación de piezas: Los sistemas de montaje de cargas útiles suelen constar de varios soportes, elementos de fijación y placas de interfaz que deben ensamblarse. Cada pieza añade peso, requiere una gestión de fabricación e inventario e introduce posibles puntos de fallo (por ejemplo, aflojamiento de elementos de fijación, concentraciones de tensión en las juntas).
- Reducción del tiempo y los costes de montaje: La AM permite a los diseñadores consolidar múltiples componentes en una única pieza impresa monolítica. Un montaje complejo que antes requería 5, 10 o incluso 20 piezas distintas puede rediseñarse e imprimirse como una sola estructura integrada. Esto reduce drásticamente la mano de obra de montaje, simplifica las cadenas de suministro y minimiza la necesidad de herramientas y accesorios.
- Fiabilidad mejorada: La eliminación de fijaciones y uniones elimina posibles fuentes de fallos debidos a vibraciones, fatiga o montaje incorrecto, lo que se traduce en un componente final más robusto y fiable.
- Rendimiento mejorado: Los diseños integrados pueden ofrecer trayectorias de carga más suaves y una mayor eficiencia estructural en comparación con los conjuntos atornillados. También pueden incorporarse directamente elementos como canales de fluidos o disipadores de calor integrados.
3. Complejidad de fabricación sin penalización: En la fabricación tradicional, la complejidad aumenta directamente el coste y el plazo de entrega debido a las intrincadas configuraciones de mecanizado, el utillaje especializado o los complejos moldes de fundición. En AM, la complejidad es en gran medida "gratuita" una vez finalizado el diseño.
- Geometrías intrincadas: Características como los canales de refrigeración internos, los huecos ocultos para reducir el peso, las formas conformadas que encajan perfectamente con las superficies de acoplamiento, las paredes finas y las curvaturas complejas pueden producirse con relativa facilidad mediante procesos de AM como la fusión selectiva por láser (SLM) o la fusión selectiva por haz de electrones (SEBM), tecnologías utilizadas con pericia por proveedores como Met3dp.
- Personalización: La AM es ideal para producir montajes de carga útil altamente personalizados o exclusivos, habituales en la fabricación de satélites o para modificaciones especializadas de aeronaves, sin los prohibitivos costes de utillaje asociados a los métodos tradicionales para la producción de bajo volumen.
4. Desarrollo acelerado y creación de prototipos: La industria aeroespacial exige pruebas y validaciones rigurosas. La AM acelera considerablemente el ciclo de diseño, construcción y pruebas.
- Creación rápida de prototipos: Los prototipos funcionales con el material metálico final previsto pueden producirse directamente a partir de datos CAD en cuestión de días, en lugar de semanas o meses. Esto permite a los ingenieros probar y validar rápidamente los diseños, realizar comprobaciones de ajuste e iterar mejoras mucho más rápido que con las rutas de prototipado tradicionales.
- Tiempo de vuelo más rápido: Al comprimir las fases de diseño y fabricación, la AM puede acortar el plazo total de entrega de hardware apto para el vuelo, lo que permite un despliegue más rápido de nuevas capacidades de satélites o actualizaciones de aeronaves.
5. Metal AM vs. CNC Machining/Casting for Payload Mounts:
Característica | Metal AM (por ejemplo, SLM/EBM) | Mecanizado CNC | Fundición a la cera perdida |
---|---|---|---|
Libertad de diseño | Muy alto (geometrías complejas, celosías) | Moderado (limitado por el acceso a las herramientas) | Alta (pero requiere utillaje) |
Aligeramiento | Excelente (optimización topológica factible) | Limitado (optimización compleja difícil) | Moderada (posible forma casi neta) |
Consolidación de piezas | Excelente | Pobre | Moderado |
Residuos materiales | Baja (reciclabilidad del polvo) | Alta (alta relación compra-vuelo) | Moderado (puertas, elevadores) |
Plazo de entrega (Proto) | Ayuno (días/semanas) | Moderado (semanas) | Lento (semanas/meses para el utillaje) |
Plazo de entrega (Prod) | Moderado (depende del tamaño/cantidad de la construcción) | Rápido (para piezas sencillas) / Lento (complejas) | Moderado (una vez fabricado el utillaje) |
Coste de utillaje | Ninguno | Bajo (accesorios) / Alto (plantillas complejas) | Alta (creación de moldes/patrones) |
Volumen ideal | Baja a media, alta complejidad/personalización | Media a alta, complejidad moderada | Medio a alto, diseños estables |
Acabado superficial | Moderado (requiere tratamiento posterior) | Excelente | Bueno (requiere acabado) |
Opciones de material | Crecimiento (aleaciones específicas optimizadas para AM) | Muy ancho | Ancho |
Exportar a hojas
Mientras que el mecanizado CNC sigue siendo excelente para lograr una precisión y unos acabados superficiales muy elevados en superficies accesibles, y la fundición puede resultar económica para la producción de grandes volúmenes de diseños estables, La AM metálica ofrece una combinación superior de libertad de diseño, potencial de aligeramiento, consolidación de piezas y velocidad para componentes complejos de volumen bajo a medio, como los soportes de carga útil aeroespaciales. Aprovechar las capacidades de los sistemas avanzados de AM y los materiales de alta calidad de proveedores experimentados es clave para conseguir estas ventajas.
Material Focus: Scalmalloy® y Ti-6Al-4V para soportes de alto rendimiento
La elección del material es primordial en el diseño aeroespacial, ya que influye directamente en el rendimiento, el peso, la durabilidad y el coste de un componente. Para los soportes de carga útil impresos en 3D que operan en entornos exigentes, hay dos materiales que destacan por sus excepcionales propiedades cuando se procesan mediante fabricación aditiva: Scalmalloy y Ti-6Al-4V (titanio de grado 5). Comprender sus características y por qué son adecuadas es crucial para los ingenieros y especialistas en compras que seleccionan materiales para aplicaciones de misión crítica. Además, la calidad de la materia prima -el polvo metálico- es fundamental para conseguir estas propiedades en la pieza impresa final.
1. Scalmalloy® (aleación Al-Mg-Sc): El aluminio de alto rendimiento Scalmalloy® es una aleación patentada de aluminio-magnesio-escandio desarrollada específicamente para la fabricación aditiva. Supera los límites de lo que se puede conseguir con aleaciones de aluminio, ofreciendo propiedades que rivalizan con algunos grados de titanio, pero con una densidad significativamente menor.
- Propiedades clave:
- Alta resistencia específica: Esta es la característica que define a Scalmalloy®. Presume de un límite elástico (( \sigma_y )) típicamente superior a 450 MPa y una resistencia última a la tracción (( \sigma_{UTS} )) superior a 500 MPa tras el tratamiento térmico adecuado, junto con una baja densidad de aproximadamente 2,67 g/cm³. Esto da como resultado una resistencia específica (Resistencia/Densidad) significativamente superior a la de las aleaciones de aluminio aeroespaciales tradicionales de alta resistencia (como 7075 o 2024) y comparable, o incluso superior, a la del Ti-6Al-4V en algunas condiciones.
- Excelente ductilidad y tenacidad: A diferencia de algunas aleaciones de aluminio de muy alta resistencia que pueden ser quebradizas, Scalmalloy® mantiene un buen alargamiento (normalmente >10%) y tenacidad a la fractura, lo que la hace resistente al agrietamiento bajo tensión.
- Buena soldabilidad (relevante para AM): Su composición la hace muy adecuada para el proceso de fusión capa a capa inherente a la SLM, lo que da lugar a piezas densas y con forma casi de red.
- Buena resistencia a la corrosión: Ofrece una buena resistencia a la corrosión atmosférica.
- Resistencia a la fatiga: Presenta una excelente resistencia a la fatiga, especialmente beneficiosa para los componentes sometidos a cargas cíclicas, como los soportes de carga útil que sufren vibraciones durante el lanzamiento y el funcionamiento.
- Control de microestructuras: La rápida solidificación durante la AM, combinada con la adición de escandio, da lugar a una microestructura de grano muy fino, clave para su alta resistencia y tenacidad.
- Por qué es importante para los soportes de carga útil:
- Ahorro máximo de peso: Su excepcional resistencia específica permite el diseño de soportes extremadamente ligeros, lo que se traduce directamente en una reducción de los costes de lanzamiento de satélites o en una mejora de la eficiencia del combustible y de la capacidad de carga de aeronaves y vehículos aéreos no tripulados. A menudo es la opción preferida cuando la reducción de peso es el factor principal.
- Rendimiento dinámico: La elevada relación rigidez-peso es ventajosa para los soportes que requieren frecuencias naturales elevadas para evitar la resonancia con las vibraciones del vehículo.
- Geometrías complejas: Su idoneidad para la AM permite los complejos diseños de topología optimizada necesarios para aprovechar al máximo su potencial de aligeramiento.
2. Ti-6Al-4V (titanio de grado 5): El caballo de batalla aeroespacial Ti-6Al-4V (aleación de titanio con aluminio 6% y vanadio 4%) es la aleación de titanio más utilizada en el sector aeroespacial, conocida por su excelente combinación de resistencia, baja densidad, resistencia a la corrosión y rendimiento a temperaturas moderadamente elevadas. Tiene un largo historial de éxito en aplicaciones exigentes.
- Propiedades clave:
- Alta relación resistencia-peso: Aunque su densidad (aprox. 4,43 g/cm³) es superior a la de Scalmalloy®, el Ti-6Al-4V ofrece una resistencia muy elevada (( \sigma_y ) típicamente > 830 MPa, ( \sigma_{UTS} ) > 900 MPa en estado recocido, mayor posible con tratamiento térmico). Esto se traduce en una excelente resistencia específica, lo que lo convierte en la mejor elección para aplicaciones sensibles al peso.
- Excelente resistencia a la corrosión: Las aleaciones de titanio forman una capa de óxido pasiva y estable que proporciona una resistencia excepcional a la corrosión en diversos entornos, como el agua de mar y los ácidos oxidantes, algo crucial para las misiones espaciales de larga duración o las aeronaves que operan en entornos marinos.
- Buen rendimiento a altas temperaturas: Conserva una resistencia significativa hasta temperaturas en torno a 300-400°C (aprox. 600-750°F), lo que lo hace adecuado para montajes situados cerca de motores o que experimenten calentamiento aerodinámico.
- Biocompatibilidad: Aunque no suele ser relevante para los montajes de cargas útiles, su biocompatibilidad pone de relieve su inercia.
- Resistencia a la fatiga: Ofrece una buena resistencia a la fatiga, esencial para los componentes sometidos a cargas vibratorias.
- Procesamiento AM establecido: Se ha llevado a cabo una amplia investigación y desarrollo de parámetros para el procesamiento de Ti-6Al-4V mediante SLM y EBM, lo que ha dado lugar a propiedades de material y controles de proceso bien comprendidos.
- Por qué es importante para los soportes de carga útil:
- Fiabilidad probada: Su larga trayectoria en el sector aeroespacial inspira confianza para aplicaciones críticas.
- Capacidad para temperaturas más altas: Preferible a aleaciones de aluminio como Scalmalloy® si el soporte funciona a temperaturas elevadas.
- Resistencia superior a la corrosión: Ideal para misiones de muy larga duración o exposición a entornos corrosivos.
- Saldo de propiedades: Ofrece una sólida combinación de fuerza, rigidez, tenacidad y resistencia medioambiental adecuada para una amplia gama de escenarios de montaje de cargas útiles.
Resumen comparativo de materiales:
Propiedad | Scalmalloy | Ti-6Al-4V (Grado 5) | Caso de uso típico Controlador |
---|---|---|---|
Densidad | ~2,67 g/cm³ | ~4,43 g/cm³ | Densidad inferior (Scalmalloy®) |
Límite elástico | > 450 MPa (tratado térmicamente) | > 830 MPa (Recocido) | Mayor resistencia absoluta (Ti-6Al-4V) |
Fuerza específica | Muy alta | Alta | Ahorro máximo de peso (Scalmalloy®) |
Capacidad de temperatura máxima | Inferior (generalmente < 150-200°C) | Superior (~300-400°C) | Necesidades de alta temperatura (Ti-6Al-4V) |
Resistencia a la corrosión | Bien | Excelente | Entornos agresivos (Ti-6Al-4V) |
Madurez AM | Alto (diseñado específicamente para AM) | Muy alto (ampliamente estudiado) | Ambos bien establecidos |
Coste | Alto (contenido de escandio) | Alta (base de titanio) | Compromiso específico de la aplicación |
Exportar a hojas
La importancia de los polvos metálicos de alta calidad: Alcanzar las propiedades teóricas de Scalmalloy® y Ti-6Al-4V en una pieza impresa en 3D depende fundamentalmente de la calidad del polvo metálico utilizado como materia prima. Factores como:
- Esfericidad: Las partículas de polvo altamente esféricas garantizan una buena fluidez dentro del sistema de recubrimiento de la máquina AM, lo que da lugar a capas de polvo uniformes y reduce el riesgo de huecos o defectos en la pieza final.
- Distribución del tamaño de las partículas (PSD): Una PSD controlada es crucial para lograr una alta densidad de empaquetamiento en el lecho de polvo, lo que contribuye a obtener piezas totalmente densas y un comportamiento de fusión predecible.
- Pureza y química: El control estricto de la composición de la aleación y la reducción al mínimo de las impurezas (como el oxígeno y el nitrógeno, especialmente críticos para el titanio) es esencial para obtener las propiedades mecánicas y la resistencia a la corrosión deseadas. Los niveles de satélites deben gestionarse con precisión.
- Ausencia de satélites: Las partículas pequeñas e irregulares adheridas a otras esféricas más grandes (satélites) pueden afectar negativamente a la fluidez y a la densidad de empaquetamiento.
Compromiso de Met3dp con la excelencia en polvo: Reconocer este vínculo crítico, Met3dp emplea tecnologías de producción de polvo líderes en la industria, incluidas avanzadas Atomización de gases y Proceso de electrodos rotativos de plasma (PREP) sistemas. Su equipo de atomización de gas utiliza diseños exclusivos de boquillas y flujo de gas optimizados para producir polvos metálicos con la alta esfericidad, la PSD controlada y la excelente fluidez que requieren las exigentes aplicaciones de AM. Este enfoque garantiza que los polvos de Scalmalloy®, Ti-6Al-4V y otras aleaciones innovadoras (como TiNi, TiTa, TiAl, TiNbZr, CoCrMo, aceros inoxidables y superaleaciones) que ofrece Met3dp proporcionen una base fiable para imprimir montajes de carga útil densos y de alta calidad con propiedades mecánicas superiores y consistentes. Su enfoque integral, que abarca desde polvos metálicos avanzados a impresoras SEBM de alto rendimiento y soporte de aplicaciones, los convierte en un socio valioso para las empresas aeroespaciales que buscan aprovechar todo el potencial de estos materiales avanzados. Elegir el material adecuado es solo la mitad de la batalla; asegurarse de que procede de un proveedor comprometido con la calidad del polvo, como Met3dp, es igualmente vital para el éxito de la misión.
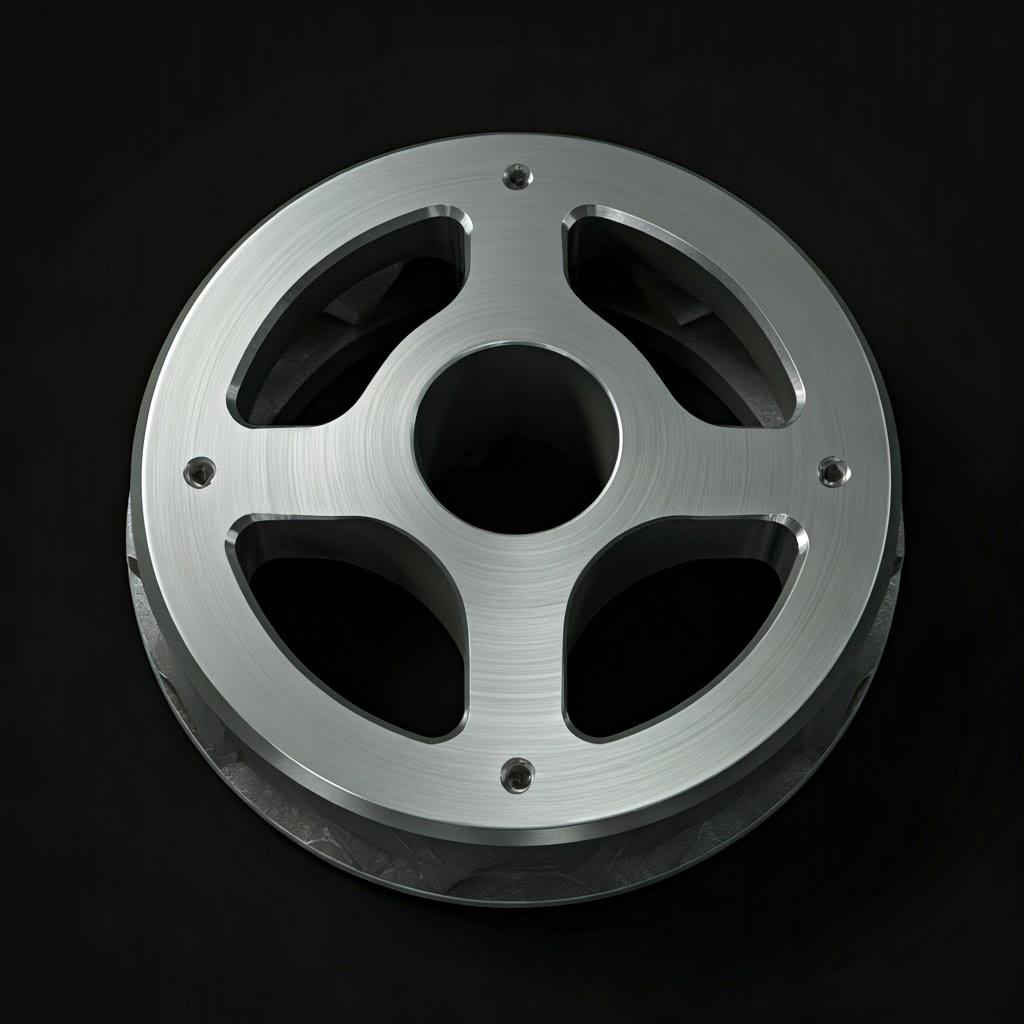
Diseño para la fabricación aditiva (DfAM): Optimización de la geometría del soporte de carga útil
Pasar de la por qué a la cómoEl diseño de un soporte de carga útil específico para la fabricación aditiva de metales requiere un cambio de mentalidad en comparación con los enfoques tradicionales de diseño para mecanizado o fundición. El diseño para la fabricación aditiva (DfAM) no consiste simplemente en hacer imprimibles los diseños existentes, sino en aprovechar las capacidades únicas de los procesos de AM, como la fusión selectiva por láser (SLM) o la fusión selectiva por haz de electrones (SEBM), para crear componentes fundamentalmente mejores: más ligeros, más resistentes, más funcionales y con la posibilidad de integrar múltiples funciones. Para los soportes de carga útil aeroespacial, donde el rendimiento y el peso son fundamentales, el dominio de los principios de DfAM es esencial para liberar todo el potencial de materiales como Scalmalloy® y Ti-6Al-4V. Esto implica un examen detallado de la optimización de la topología, las estructuras reticulares, la minimización del soporte, las limitaciones de las características y las restricciones específicas del proceso.
1. Optimización de la topología: Diseño por ruta de carga Quizá sea la herramienta DfAM más potente para aligerar componentes aeroespaciales. En lugar de empezar con un bloque de material y tallarlo, los algoritmos de optimización topológica parten de un espacio de diseño definido (el volumen máximo admisible para el soporte), aplican casos de carga realistas (por ejemplo, cargas estáticas, cargas vibratorias, cargas térmicas), definen restricciones (por ejemplo, puntos de montaje fijos, zonas de exclusión para interfaces de carga útil) y, a continuación, eliminan iterativamente material de las zonas que no contribuyen significativamente a la integridad estructural.
- Flujo de trabajo: Suele implicar el análisis de elementos finitos (FEA) integrado con software de optimización. El ingeniero define el problema, el software genera una disposición de materiales optimizada (a menudo orgánica y compleja) y el ingeniero interpreta el resultado, suavizando las geometrías y haciéndolas fabricables dentro de las limitaciones de la AM.
- Ventajas para los soportes de carga útil: Da lugar a estructuras muy eficientes que siguen las trayectorias naturales de las tensiones. El resultado es una reducción significativa del peso (a menudo 30-60%+) en comparación con los diseños convencionales, al tiempo que se cumplen o superan los requisitos de rigidez y resistencia. Las formas orgánicas resultantes son a menudo imposibles o prohibitivamente caras de producir mediante mecanizado.
- Consideraciones: Requiere una definición precisa del caso de carga. Los resultados brutos suelen requerir un perfeccionamiento para facilitar la fabricación (por ejemplo, garantizar espesores de pared mínimos, suavizar las esquinas afiladas para reducir las concentraciones de tensión). También debe realizarse un análisis de vibraciones (análisis modal) en el diseño optimizado para garantizar que las frecuencias naturales son aceptables.
2. Estructuras reticulares: Aligeramiento y multifuncionalidad La AM permite integrar estructuras reticulares (celdas unitarias repetitivas) en el volumen sólido de una pieza. No se trata de un simple adorno, sino que ofrece importantes ventajas técnicas para los soportes de carga útil.
- Tipos:
- Entramados basados en puntales: Simples, bien entendidos (por ejemplo, cúbicos, octeto-cercha). Buenos para la rigidez y la resistencia.
- Entramados basados en superficies (TPMS): Superficies mínimas triplemente periódicas (por ejemplo, Gyroid, Schwarz Diamond). Ofrecen transiciones suaves, una distribución potencialmente mejor de la tensión y buenas propiedades para el intercambio de calor o la amortiguación de vibraciones.
- Ventajas:
- Mayor reducción de peso: La sustitución de volúmenes internos sólidos por celosías reduce drásticamente la masa, al tiempo que mantiene un soporte y una rigidez estructurales significativos.
- Amortiguación de vibraciones: Determinados tipos y configuraciones de celosía pueden diseñarse para absorber o amortiguar las vibraciones, lo que podría proteger con mayor eficacia las cargas útiles sensibles.
- Rigidez a medida: La densidad y el tipo de entramado pueden variar en toda la pieza para conseguir características específicas de rigidez en distintas direcciones.
- Gestión del calor: Los entramados de celdas abiertas pueden facilitar el flujo de aire o permitir la integración de conductos/canales de calor para la gestión térmica de los componentes electrónicos de la carga útil.
- Consideraciones sobre el diseño: Requiere software especializado para la generación y simulación. Garantizar la fabricabilidad (diámetro mínimo del puntal, evitar el polvo atrapado en celdas cerradas) es crucial. El análisis de la resistencia a la fatiga de las estructuras reticulares es un campo de investigación activo que requiere un estudio minucioso.
3. Diseño de estructuras de soporte mínimas Los procesos de AM metálica suelen requerir estructuras de soporte para los elementos que sobresalen y para anclar la pieza a la placa de impresión, gestionando las tensiones térmicas. Estos soportes consumen material, aumentan el tiempo de impresión, deben retirarse en el postprocesado (lo que puede requerir mucho trabajo y afectar al acabado de la superficie) y pueden limitar la libertad de diseño si no se tienen en cuenta con cuidado.
- Ángulos autoportantes: Diseñe elementos con ángulos de voladizo superiores a un umbral crítico (normalmente 40-45° respecto a la horizontal, dependiendo del proceso) para minimizar la necesidad de soportes. Los ángulos poco pronunciados requieren soportes.
- Orientación de las características: Oriente la pieza en la plataforma de construcción estratégicamente para minimizar el área total que requiere soporte. Esto suele implicar compromisos con otros factores, como el acabado superficial de las caras críticas o el tiempo de fabricación.
- Apoyos al diseño:
- Utilice chaflanes o filetes en lugar de salientes horizontales afilados.
- Emplear formas de "lágrima" o diamante para los agujeros horizontales, haciéndolos autoportantes.
- Divida las piezas complejas en subcomponentes más fáciles de imprimir sin soportes internos extensos, aunque esto anula algunas ventajas de la consolidación de piezas.
- Acceso para la retirada: Si los soportes son inevitables (especialmente los internos), asegúrese de que haya una línea de visión clara o puertos de acceso diseñados en la pieza para facilitar su eliminación mediante herramientas manuales, mecanizado o grabado químico. El polvo atrapado en cavidades internas también necesita vías de escape.
4. Cumplimiento de las limitaciones de características específicas del proceso Todos los procesos y máquinas de AM tienen limitaciones en cuanto al tamaño mínimo de las características que pueden producir de forma fiable. Diseñar por debajo de estos umbrales puede provocar fallos de impresión o piezas que no cumplan las especificaciones dimensionales.
- Espesor mínimo de pared: Normalmente, entre 0,4 y 1,0 mm, en función del material, la altura de la pared y el proceso (la SLM suele ser más fina que la EBM). Las paredes finas son propensas al alabeo y pueden no resolverse con precisión.
- Diámetro mínimo del orificio: Los agujeros pequeños (normalmente < 0,5 - 1,0 mm) pueden sellarse durante la impresión o ser difíciles de limpiar de polvo. Considere la posibilidad de taladrar agujeros pequeños y críticos después de la impresión.
- Diámetro mínimo de pasador/puntal: Los pasadores finos o los puntales de celosía tienen diámetros mínimos imprimibles (rango similar al grosor de la pared).
- Extensión máxima no soportada: Los puentes o vanos horizontales requieren apoyo si superan cierta longitud (depende del proceso/material, a menudo unos pocos milímetros).
- Relación de aspecto: Los elementos muy altos y delgados pueden ser propensos a distorsiones o fallos durante la construcción.
- Comprender Métodos de impresión: Conocer las características específicas del proceso de AM elegido (por ejemplo, SLM frente a EBM utilizado por proveedores como Met3dp) es crucial, ya que los sistemas basados en láser (SLM) a menudo ofrecen una resolución de características más fina pero una tensión residual potencialmente más alta que los sistemas de haz de electrones (EBM), que funcionan a temperaturas más altas.
5. Gestión de la anisotropía Debido al proceso de fabricación capa por capa y al flujo de calor direccional, las piezas metálicas de AM suelen presentar propiedades mecánicas anisótropas, lo que significa que su resistencia, rigidez y vida útil a la fatiga pueden variar en función de la dirección relativa a las capas de fabricación (X, Y frente a Z).
- Implicaciones del diseño: Lo ideal es que las trayectorias de las cargas críticas estén alineadas con la dirección de las propiedades óptimas del material (a menudo paralelas a la placa de impresión, plano X-Y). Evite orientar las cargas de tracción primarias perpendicularmente a las capas (dirección Z) si es posible, ya que suele ser la orientación más débil.
- Simulación y pruebas: Lo ideal sería que los modelos de elementos finitos tuvieran en cuenta las propiedades anisótropas de los materiales si se requiere una alta fidelidad. Los ensayos con cupones en diferentes orientaciones (X, Y, Z) son esenciales durante la cualificación del proceso para caracterizar estas diferencias direccionales.
6. Diseño para el postprocesamiento Tenga en cuenta cómo se manipulará, acabará e inspeccionará la pieza tras la impresión.
- Tolerancias de mecanizado: Añada material de reserva adicional (por ejemplo, de 0,5 a 2,0 mm) a las superficies que requieran alta precisión o acabados específicos conseguidos mediante mecanizado posterior.
- Puntos de fijación: Incorporar elementos que ayuden a sujetar la pieza con seguridad durante el mecanizado posterior o la inspección (por ejemplo, orejetas temporales, superficies de referencia planas).
- Acceso de inspección: Garantizar que las características críticas sean accesibles para las herramientas de medición (sondas de MMC, escáneres) y los métodos END (por ejemplo, que las líneas de visión del escáner CT no estén bloqueadas).
El dominio de la DfAM para los montajes de carga útil requiere un enfoque de colaboración entre los ingenieros de diseño, los ingenieros de fabricación y los proveedores de servicios de AM como Met3dp, que poseen un profundo conocimiento de las capacidades de sus máquinas, los comportamientos de los materiales y los requisitos de postprocesamiento. Al adoptar estos principios, las empresas aeroespaciales pueden crear componentes realmente optimizados que superen los límites del rendimiento.
Alcanzar la precisión: Tolerancia, acabado superficial y exactitud dimensional en soportes AM
Aunque la fabricación aditiva de metales ofrece una increíble libertad de diseño, es fundamental que los ingenieros y los responsables de compras tengan expectativas realistas en cuanto a la precisión que se puede alcanzar directamente desde la impresora. Las aplicaciones aeroespaciales, especialmente los montajes de carga útil con interfaces críticas, exigen un control estricto de las dimensiones, las tolerancias y las características superficiales. Comprender la calidad típica de las piezas de AM fabricadas con Scalmalloy® o Ti-6Al-4V, los factores que influyen en ella y la necesidad habitual de postmecanizado es vital para el éxito de la aplicación.
1. Tolerancias as-built: La precisión dimensional que se puede conseguir directamente con los procesos de fusión de lecho de polvo metálico (SLM, EBM) depende de numerosos factores, como la calibración de la máquina, el tamaño del punto del haz láser/electrón, el grosor de la capa, las características del polvo, la gestión térmica y la geometría/tamaño de la pieza.
- Rangos generales: Las tolerancias típicas alcanzables en procesos bien controlados suelen situarse en el intervalo de ±0,1 mm a ±0,3 mm para dimensiones más pequeñas (por ejemplo, hasta 100 mm), o ±0,1% a ±0,2% de la dimensión nominal para piezas más grandes. Algunos sistemas de gama alta podrían lograr resultados ligeramente mejores en condiciones óptimas.
- Capacidades de Met3dp: Utilizando impresoras líderes del sector conocidas por su precisión y fiabilidad, Met3dp se esfuerza por suministrar piezas con tolerancias ajustadas, proporcionando un mejor punto de partida para cualquier operación de acabado necesaria. Sin embargo, la física inherente a la fusión y solidificación por capas impone límites.
- Factores que influyen en la tolerancia:
- Efectos térmicos: Las tensiones residuales acumuladas durante la impresión pueden provocar alabeos o distorsiones, sobre todo en piezas grandes o complejas.
- Encogimiento: Las aleaciones metálicas se contraen al solidificarse y enfriarse; predecirlo y compensarlo es complejo.
- Estructuras de apoyo: Cuando los soportes tocan la pieza, pueden dejar marcas de testigos o afectar a la precisión local después de retirarlos.
- Parte Orientación: La orientación en la placa de impresión puede afectar a la estabilidad dimensional y a la precisión debido a la variación de las condiciones térmicas y las necesidades de soporte.
2. Acabado superficial as-built (rugosidad): El acabado superficial de las piezas fabricadas por AM es intrínsecamente más rugoso que el obtenido por mecanizado o pulido. Esta rugosidad se debe a las partículas de polvo parcialmente fundidas que se adhieren a la superficie y a la construcción por capas (efecto escalonado).
- Valores típicos: La rugosidad superficial (Ra) de las piezas SLM/EBM suele oscilar entre 5 µm a 25 µm (micrómetros). Los procesos EBM, que suelen utilizar capas más gruesas y mayor energía, tienden a producir superficies más rugosas que los SLM. Scalmalloy® y Ti-6Al-4V suelen estar dentro de este rango.
- Efecto Escalera: Las superficies angulosas o curvas presentan una textura "escalonada" característica debida a las capas discretas. La gravedad depende del grosor de la capa y del ángulo de la superficie con respecto a la dirección de impresión (las superficies casi paralelas a la placa de impresión son más rugosas, mientras que las paredes verticales suelen ser más lisas).
- Factores que influyen en la rugosidad:
- Grosor de la capa: Las capas más finas suelen producir superficies más lisas, pero aumentan el tiempo de fabricación.
- Polvo Tamaño de las partículas: Los polvos más finos pueden dar lugar a acabados más suaves.
- Parámetros del proceso: La potencia del láser/rayo, la velocidad de exploración y la estrategia de eclosión influyen significativamente en la dinámica del baño de fusión y en la textura de la superficie.
- Orientación: Las paredes verticales tienden a ser más lisas que las superficies orientadas hacia arriba o en ángulo. Las superficies orientadas hacia abajo, donde se fijaron los soportes, suelen ser las más ásperas después de retirar los soportes.
3. La necesidad del mecanizado posterior: Para muchos elementos críticos de los montajes de cargas útiles aeroespaciales, las tolerancias y el acabado superficial de fábrica son insuficientes para cumplir los estrictos requisitos de ingeniería. Por ello, el mecanizado posterior suele ser un paso esencial y planificado.
- Interfaces críticas: Los puntos de montaje, las superficies de contacto con la carga útil o la estructura del vehículo, los orificios de los cojinetes o casquillos y los orificios de los elementos de fijación suelen requerir tolerancias mucho más estrictas que ±0,1 mm (a menudo en el rango de ±0,01 a ±0,05 mm) y acabados superficiales más lisos (Ra < 1,6 µm o incluso inferior) para garantizar una transferencia de carga, alineación, estanquidad o vida útil a la fatiga adecuadas.
- Alcanzar la precisión: El mecanizado CNC (fresado, torneado, rectificado) se utiliza para llevar estas características específicas a la tolerancia final y lograr el acabado superficial deseado. En el diseño de la pieza AM debe incluirse suficiente material de mecanizado en estas superficies críticas.
- Fabricación híbrida: Algunos enfoques consisten en imprimir piezas de forma casi neta y utilizar después máquinas CNC multieje para el acabado, combinando la libertad de diseño de la AM con la precisión de los métodos sustractivos.
- Coste/implicación temporal: La incorporación del mecanizado posterior añade costes y plazos al proceso global, pero a menudo no es negociable para lograr la calidad requerida en los componentes aeroespaciales.
4. Verificación dimensional y control de calidad: Garantizar que el montaje final de la carga útil cumple todas las especificaciones dimensionales y de superficie requiere una inspección rigurosa.
- Máquinas de medición por coordenadas (MMC): Se utiliza para la verificación dimensional de alta precisión de características críticas tras la impresión y el mecanizado posterior.
- Escaneado 3D: Los escáneres ópticos o láser capturan la geometría general de la pieza, lo que permite compararla con el modelo CAD original para evaluar la forma general e identificar desviaciones o alabeos.
- Perfilometría de superficie: Mide la rugosidad superficial (Ra, Rz, etc.) en superficies críticas para verificar el cumplimiento de las especificaciones.
En resumen, aunque la AM metálica proporciona la complejidad geométrica necesaria para optimizar los montajes de carga útil, alcanzar la precisión final que exigen las normas aeroespaciales suele requerir una combinación de un proceso de AM de alta calidad (utilizando máquinas precisas como las de Met3dp y polvos de calidad) y operaciones de postmecanizado específicas para las características críticas. Comprender estos requisitos en una fase temprana del diseño es crucial para una planificación y un cálculo de costes eficaces.
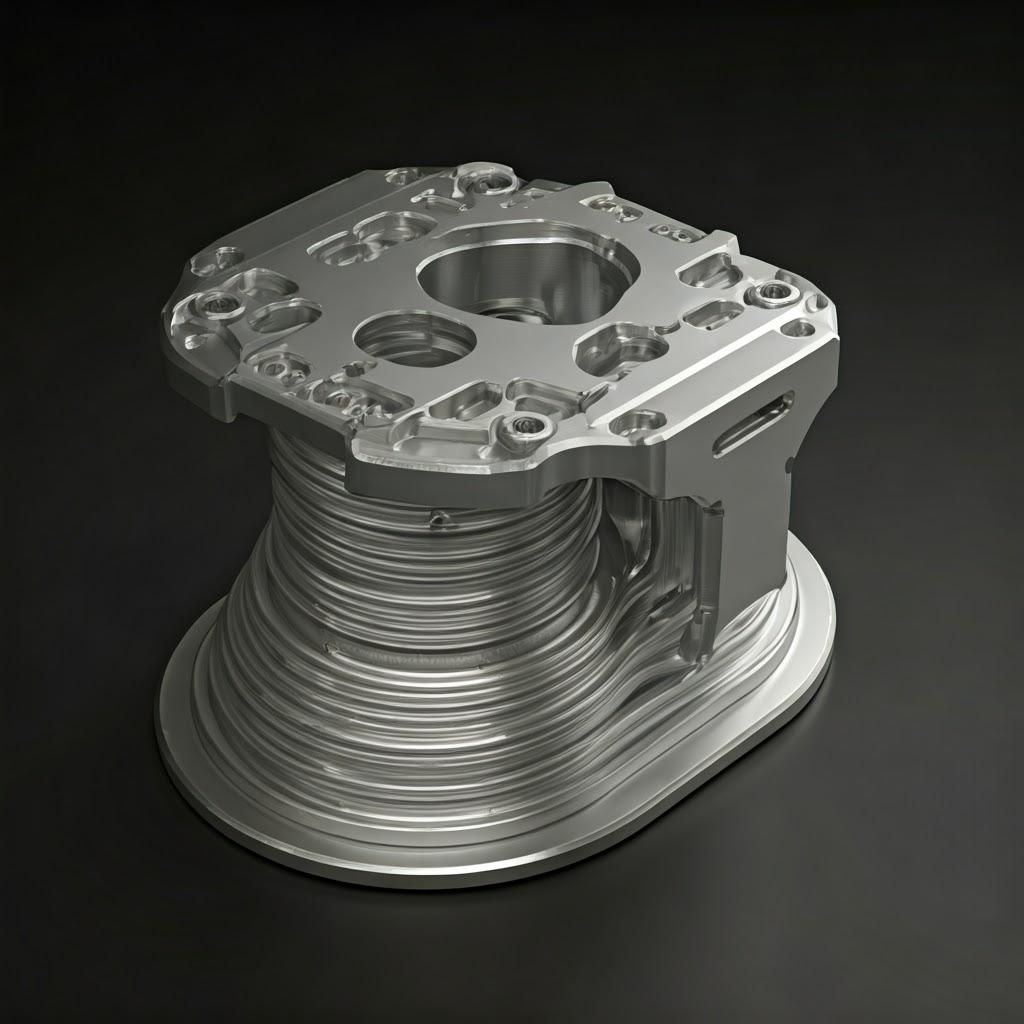
Más allá de la impresión: Postprocesado esencial para montajes de cargas útiles aeroespaciales
Producir un soporte de carga útil dimensionalmente preciso mediante fabricación aditiva metálica es sólo el primer paso importante. La pieza "tal cual", recién salida de la impresora, requiere una serie de pasos cruciales de postprocesado para transformarla en un componente apto para el vuelo que cumpla las estrictas exigencias de las aplicaciones aeroespaciales. Estos pasos son esenciales para aliviar las tensiones internas, conseguir las propiedades deseadas del material (resistencia, ductilidad, vida a la fatiga), eliminar las estructuras de soporte, lograr el acabado superficial y las tolerancias requeridas en las interfaces críticas y garantizar la calidad interna. Para materiales como Scalmalloy® y Ti-6Al-4V, los tratamientos térmicos específicos son especialmente vitales.
1. Alivio del estrés: Los rápidos ciclos de calentamiento y enfriamiento inherentes a la fusión de capas de polvo crean importantes tensiones residuales en la pieza impresa. Estas tensiones pueden provocar alabeos o distorsiones al retirar la pieza de la placa de impresión y pueden afectar negativamente al rendimiento mecánico y a la vida útil a fatiga de la pieza.
- Proceso: Suele ser el primer paso tras la impresión y a menudo se realiza cuando la pieza aún está fijada a la placa de impresión. Consiste en calentar la pieza en un horno con atmósfera controlada (vacío o gas inerte como el argón) a una temperatura específica inferior a la temperatura de transformación o envejecimiento del material, mantenerla durante un periodo definido y, a continuación, enfriarla lentamente.
- Parámetros (Ejemplos):
- Ti-6Al-4V: Los ciclos habituales incluyen el calentamiento a 595 °C - 800 °C (1100 °F - 1470 °F) durante 1-4 horas, seguido de un enfriamiento en horno o por aire, dependiendo del objetivo específico (alivio de tensiones frente a recocido).
- Scalmalloy®: Los parámetros de alivio de tensiones son específicos de la aleación, a menudo a temperaturas inferiores a las del titanio, normalmente en torno a 300-325°C.
- Importancia: Crítico para la estabilidad dimensional durante los pasos posteriores (como la retirada de la placa de impresión y el mecanizado) y para mejorar el rendimiento a la fatiga.
2. Tratamiento térmico (solubilización, envejecimiento): Más allá del alivio de tensiones, a menudo se requieren tratamientos térmicos específicos para conseguir la microestructura y las propiedades mecánicas (resistencia, ductilidad, dureza) óptimas para la aleación elegida.
- Ti-6Al-4V:
- Recocido: A menudo se realiza simultáneamente con el alivio de tensiones, refinando la microestructura para mejorar la ductilidad y la tenacidad.
- Tratamiento de soluciones y envejecimiento (STA): Proceso en varias etapas para aumentar significativamente la resistencia. Consiste en calentar a alta temperatura (disolución, por ejemplo, 900-950°C), enfriar rápidamente (temple) y recalentar a baja temperatura (envejecimiento, por ejemplo, 500-600°C) durante varias horas. Los parámetros STA se seleccionan cuidadosamente para alcanzar objetivos específicos de resistencia/ductilidad (una mayor resistencia suele implicar una menor ductilidad).
- Scalmalloy®: Requiere un tratamiento específico de envejecimiento (endurecimiento por precipitación) tras la impresión y el alivio de tensiones para desarrollar su característica resistencia ultra alta. Este tratamiento suele consistir en un calentamiento a 325-375°C durante varias horas. El ciclo exacto es crucial para conseguir las mejores propiedades.
- Proporciona un acabado mate, limpio y uniforme. Eficaz para eliminar el polvo suelto y mezclar imperfecciones menores de la superficie. Puede inducir tensiones residuales de compresión beneficiosas. Varios medios (perlas de vidrio, óxido de aluminio) ofrecen diferentes acabados. Estos tratamientos deben realizarse en vacío o en atmósferas inertes para evitar la oxidación, especialmente crítica para el titanio a altas temperaturas.
3. Prensado isostático en caliente (HIP): El HIP es un proceso que somete las piezas simultáneamente a alta temperatura y alta presión isostática (utilizando un gas inerte como el argón).
- Propósito: Se utiliza principalmente para cerrar huecos internos o porosidad (como porosidad de gas o defectos de falta de fusión) que pueden estar presentes después de la impresión. Esto aumenta la densidad de la pieza hasta acercarla a la densidad teórica 100%.
- Ventajas: Mejora significativamente la vida a la fatiga, la ductilidad y la resistencia a la fractura, que son fundamentales para los componentes aeroespaciales sometidos a cargas cíclicas y posibles impactos. Reduce la variabilidad de las propiedades mecánicas.
- Proceso: Las temperaturas y presiones son específicas de la aleación (por ejemplo, para Ti-6Al-4V, a menudo en torno a 900-950°C y 100-150 MPa). En ocasiones, los ciclos HIP pueden combinarse con etapas de tratamiento térmico.
- Cuando se usa: A menudo se especifica para piezas o componentes giratorios críticos en los que la fatiga es un factor principal de diseño. Cada vez más común para piezas aeroespaciales AM críticas para el vuelo, incluidos los soportes de carga útil.
4. Extracción de piezas y retirada de la estructura de soporte: Una vez finalizados los tratamientos térmicos (o a veces antes, según el flujo de trabajo), hay que separar la pieza de la placa de impresión y retirar las estructuras de soporte.
- Extracción de la placa de construcción: Normalmente se realiza mediante electroerosión por hilo (EDM), aserrado o mecanizado.
- Retirada del soporte: Puede ser un reto, especialmente para geometrías internas complejas. Los métodos incluyen:
- Eliminación manual: Romper o cortar los soportes accesibles con herramientas manuales (alicates, amoladoras). Requiere mucha mano de obra y puede dañar la superficie de la pieza si no se hace con cuidado.
- Mecanizado: Fresado o esmerilado de las estructuras de soporte.
- Electroerosión por hilo: Eliminación precisa, útil para soportes intrincados o zonas de difícil acceso.
- Grabado químico: Menos común para soportes estructurales, pero a veces se utiliza para materiales específicos o acabados superficiales.
- Impacto superficial: Los puntos de contacto de los soportes dejan marcas de testigos o zonas más rugosas que suelen requerir un acabado posterior.
5. Acabado de superficies: Las superficies de AM fabricadas suelen ser demasiado rugosas para muchas aplicaciones aeroespaciales, especialmente las superficies de contacto o las zonas propensas a la fatiga.
- Acabado básico: El chorreado abrasivo (granallado, arenado) proporciona un acabado mate uniforme y elimina el polvo suelto, pero no mejora significativamente la tolerancia dimensional.
- Acabados mejorados:
- Tumbling/Acabado en masa: El acabado por vibración o el volteo con medios pueden alisar superficies y desbarbar bordes, lo que resulta eficaz para lotes de piezas más pequeñas.
- Pulido: Pulido manual o automatizado para conseguir acabados muy lisos, tipo espejo, en zonas específicas.
- Fresado/grabado químico: Eliminación controlada de material mediante baños químicos para mejorar el acabado superficial o conseguir paredes finas.
- Electropulido: Proceso electroquímico que elimina preferentemente los picos, dando como resultado una superficie muy lisa y limpia, a menudo utilizado para mejorar la resistencia a la corrosión o la vida a fatiga.
6. Mecanizado final: Como se ha comentado anteriormente, el mecanizado CNC es a menudo necesario para lograr las tolerancias finales y las especificaciones de acabado superficial en las características críticas (orificios de montaje, planos de interfaz, etc.).
7. Inspección y garantía de calidad: A lo largo de toda la cadena de postprocesado, la inspección es fundamental.
- Ensayos no destructivos (END):
- Tomografía computarizada (TC): Esencial para detectar defectos internos como porosidad o inclusiones en piezas complejas de AM.
- Inspección por líquidos penetrantes fluorescentes (FPI): Se utiliza para detectar grietas que rompen la superficie.
- Pruebas ultrasónicas (UT): Puede detectar defectos internos, aunque las geometrías complejas pueden suponer un reto.
- Inspección dimensional: La MMC y el escaneado 3D verifican las dimensiones finales después de todos los pasos de procesamiento.
- Pruebas de materiales: Los ensayos destructivos de muestras representativas o cupones testigo procesados junto con la pieza principal verifican las propiedades mecánicas (resistencia a la tracción, límite elástico, alargamiento, vida a fatiga).
Navegar con éxito por esta compleja secuencia de pasos de posprocesamiento requiere una gran experiencia, equipos especializados (hornos de vacío, unidades HIP, máquinas CNC multieje, sistemas NDT) y un sólido control del proceso. Las empresas como Met3dp, que ofrecen soluciones integrales que tienen en cuenta todo el flujo de trabajo, desde el polvo hasta la pieza acabada, incluidas las asociaciones o capacidades de posprocesamiento necesarias, son vitales para garantizar que los montajes de carga útil impresos en 3D cumplan los exigentes estándares de la industria aeroespacial. Comprender estos pasos ayuda a los responsables de compras y a los ingenieros a evaluar con precisión el tiempo, el coste y los requisitos técnicos necesarios.
Afrontar los retos: Superar los obstáculos en la impresión 3D de soportes de carga útil
Aunque las ventajas de la fabricación aditiva de metales para los montajes de cargas útiles aeroespaciales son convincentes, la tecnología no está exenta de desafíos. Para implantar con éxito la AM en el hardware de vuelo crítico es necesario reconocer los posibles obstáculos y emplear estrategias proactivas para mitigarlos. Los ingenieros y los responsables de compras deben ser conscientes de los problemas comunes relacionados con la tensión residual, las estructuras de soporte, la porosidad, la anisotropía y el reto global de la cualificación de las piezas. Superarlos requiere un diseño cuidadoso, un control riguroso del proceso, una inspección minuciosa y la colaboración con proveedores de AM experimentados.
1. Gestión del estrés residual: El calentamiento intenso y localizado y el enfriamiento rápido inherentes a los procesos de fusión de lecho de polvo generan gradientes térmicos significativos, lo que provoca la acumulación de tensiones residuales internas en la pieza y en la interfaz con la placa de impresión.
- Consecuencias:
- Deformación/Distorsión: Las tensiones pueden hacer que la pieza se deforme durante la construcción, después de retirarla de la placa de impresión o durante el procesamiento posterior (especialmente el mecanizado).
- Rompiendo: Las tensiones de tracción elevadas pueden provocar grietas durante la fabricación o más adelante en el ciclo de vida de la pieza.
- Rendimiento reducido: Las tensiones residuales pueden afectar negativamente a la vida a fatiga y a la precisión dimensional.
- Estrategias de mitigación:
- Estrategias de exploración optimizadas: El uso de técnicas como el escaneado en isla, la sectorización o los patrones vectoriales optimizados ayuda a distribuir el calor de forma más uniforme y a reducir los picos de tensión.
- Construir calefacción de placas: El precalentamiento de la placa de impresión (habitual en EBM, también utilizado en algunos sistemas SLM) reduce los gradientes térmicos.
- Estructuras de apoyo: Unos soportes bien diseñados ayudan a anclar la pieza y a gestionar la acumulación de tensiones durante la construcción.
- Simulación térmica: La simulación del proceso basada en el análisis de elementos finitos puede predecir la distribución de tensiones e identificar posibles áreas problemáticas, lo que permite realizar ajustes en el diseño o el proceso antes de la impresión.
- Alivio del estrés posterior a la impresión: Realizar un ciclo adecuado de tratamiento térmico de alivio de tensiones inmediatamente después de la impresión es crucial para reducir las tensiones internas antes del procesamiento posterior.
2. Desafíos de la estructura de apoyo: Los soportes suelen ser un mal necesario en la AM metálica, pero conllevan sus propias dificultades.
- Dificultad de eliminación: La retirada de soportes, especialmente los densos o internos dentro de geometrías complejas (habituales en montajes optimizados de cargas útiles), puede resultar extremadamente difícil, lenta y costosa. Una retirada incompleta puede comprometer la funcionalidad o provocar concentraciones de tensiones.
- Mitigación: Dar prioridad a los principios DfAM para minimizar los soportes (ángulos autoportantes, orientación optimizada). Diseñar para el acceso: incluir puertos o canales específicos para herramientas de retirada de soportes o lavado. Considerar materiales de soporte disolubles o químicamente extraíbles cuando estén disponibles (menos común para metales estructurales).
- Acabado superficial Impacto: Los puntos de contacto de los soportes dejan superficies rugosas ("marcas testigo") que requieren un importante trabajo de acabado si se necesitan propiedades estéticas o superficiales específicas en esas zonas.
- Mitigación: Utilice tipos de soporte y ajustes de parámetros que minimicen el área de contacto y sean más fáciles de retirar limpiamente. Planifique el postprocesado (mecanizado, esmerilado, pulido) en las zonas apoyadas si el acabado es crítico.
- Polvo atrapado: Los canales o cavidades internas complejas, aunque sean autoportantes, pueden atrapar polvo sin fundir que es difícil o imposible eliminar por completo.
- Mitigación: Diseñar orificios de drenaje o puertos de acceso para la eliminación del polvo. Utilizar la simulación del proceso para predecir el atrapamiento del polvo. Es esencial realizar una limpieza e inspección minuciosas tras la impresión (por ejemplo, escaneado CT).
3. Control de la porosidad: Alcanzar la densidad total (>99,9%) es fundamental para la integridad mecánica, especialmente la vida a fatiga, de los componentes aeroespaciales. La porosidad (vacíos internos) puede tener varias causas.
- Tipos y causas:
- Porosidad por falta de fusión: Un aporte de energía insuficiente o un solapamiento inadecuado entre las pistas de exploración deja partículas de polvo sin fundir entre las capas o las pistas. Su forma suele ser irregular.
- Porosidad del ojo de la cerradura: La excesiva densidad de energía crea inestabilidad en el baño de fusión, vaporizando el metal y atrapando burbujas de gas al solidificarse. Suelen ser esféricas.
- Porosidad del gas: El gas disuelto en el polvo (por ejemplo, el argón utilizado en la atomización o el procesamiento) sale de la solución durante la fusión y queda atrapado. Suele ser esférico.
- Consecuencias: Actúan como concentradores de tensiones, reduciendo significativamente la ductilidad, la tenacidad a la fractura y, especialmente, la vida a fatiga.
- Mitigación:
- Parámetros de proceso optimizados: Es fundamental desarrollar conjuntos de parámetros sólidos (potencia del láser/rayo, velocidad de escaneado, grosor de la capa, espaciado de la trama) específicos para el material y la máquina.
- Polvo de alta calidad: El uso de polvo con química controlada, bajo contenido de gas atrapado, buena esfericidad y PSD adecuado minimiza los defectos relacionados con el polvo. Abastecimiento fiable polvos metálicos de proveedores cualificados como Met3dp es esencial.
- Supervisión de procesos: Los sistemas de control in situ pueden ayudar a detectar anomalías durante la construcción.
- Prensado isostático en caliente (HIP): Muy eficaz para cerrar los poros internos y lograr una densidad casi total. A menudo se exige para piezas aeroespaciales críticas.
4. Gestión de la anisotropía: Como se menciona en DfAM, la naturaleza direccional del proceso de construcción conduce a propiedades anisotrópicas del material.
- Desafío: Las propiedades mecánicas (resistencia, rigidez, fatiga) pueden variar significativamente en función de la dirección de la carga con respecto a las capas de construcción. Esto debe tenerse en cuenta en el diseño y el análisis.
- Mitigación:
- Orientación estratégica: Oriente la pieza en la placa de impresión de modo que las tensiones críticas se alineen con la dirección más fuerte del material (normalmente paralela al plano de impresión).
- Caracterización: Para cuantificar la anisotropía para el material, la máquina y el conjunto de parámetros específicos, es esencial realizar ensayos exhaustivos del material (tracción, fatiga) en cupones fabricados en diferentes orientaciones (X, Y, Z).
- Diseño admisible: Utilizar valores admisibles de diseño que tengan en cuenta las propiedades en la orientación más débil prevista en función de las condiciones de carga.
- Tratamiento térmico: Los tratamientos térmicos adecuados pueden ayudar a homogeneizar la microestructura hasta cierto punto, reduciendo (pero normalmente no eliminando) la anisotropía.
5. Calificación y certificación de piezas: Este suele ser el obstáculo más importante para la adopción de piezas de AM en aplicaciones aeroespaciales críticas para el vuelo. Demostrar que una pieza de AM es equivalente o superior a su homóloga fabricada tradicionalmente requiere un proceso riguroso y bien documentado.
- Desafíos: Establecer la coherencia de los procesos, garantizar la trazabilidad de los materiales, desarrollar protocolos de ensayo normalizados, realizar evaluaciones no destructivas de geometrías internas complejas y obtener la aceptación de las autoridades de certificación (FAA, EASA, NASA, etc.).
- Enfoque: Requiere un sólido Sistema de Gestión de Calidad (SGC), a menudo certificado conforme a normas aeroespaciales como AS9100. Implica:
- Bloqueo de procesos: Definir y controlar estrictamente todos los parámetros del proceso (ajustes de la máquina, especificaciones del polvo, etapas de postprocesamiento).
- Control de materiales: Pruebas rigurosas y trazabilidad de los lotes de polvo entrantes.
- Pruebas exhaustivas: Pruebas a nivel de cupón (tracción, fatiga, resistencia a la fractura) y pruebas a nivel de pieza completa (estáticas, dinámicas, medioambientales) para validar el rendimiento.
- Inspección no destructiva (NDI): Utilización de NDI avanzados, como la tomografía computarizada, para garantizar la integridad interna.
- Documentación: Registros exhaustivos de cada paso, desde el diseño hasta la inspección final.
- Asociarse para el éxito: Trabajar con un proveedor de servicios de AM con experiencia como Met3dp, que comprende las complejidades de la cualificación aeroespacial, cuenta con sólidos sistemas de calidad y ofrece soluciones integrales que incluyen experiencia en materiales y control de procesos, es muy valioso para navegar por este complejo panorama.
Al comprender estos retos y aplicar proactivamente estrategias de mitigación a lo largo de las fases de diseño, fabricación y posprocesamiento, la industria aeroespacial puede aprovechar con confianza el potencial transformador de la AM metálica para montajes de cargas útiles de alto rendimiento y otros componentes críticos.
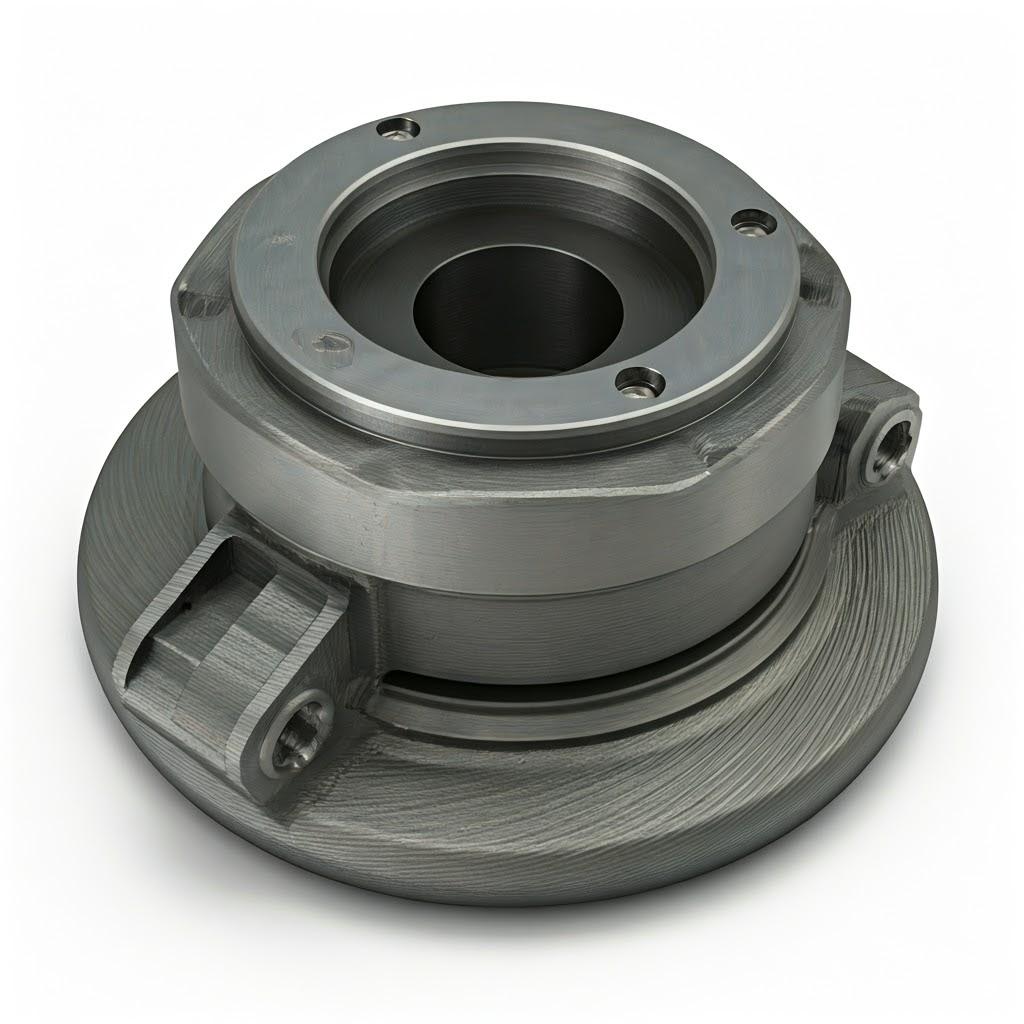
Selección de proveedores: Elección del socio de AM metálica adecuado para componentes aeroespaciales
La decisión de utilizar la fabricación aditiva de metales para componentes críticos como los soportes de carga útil aeroespacial es sólo el principio. La selección del derecha es primordial para garantizar la calidad, fiabilidad y rendimiento necesarios para el hardware de vuelo. En el sector aeroespacial hay mucho en juego, y no todos los proveedores de servicios de AM poseen la experiencia, los equipos, los controles de procesos y los sistemas de calidad necesarios para satisfacer estas demandas. Los responsables de compras, los ingenieros y los profesionales de la cadena de suministro deben actuar con la diligencia debida, evaluando a los posibles proveedores en función de un estricto conjunto de criterios adaptados específicamente a las aplicaciones aeroespaciales. Elegir a un proveedor inadecuado puede provocar retrasos en los proyectos, sobrecostes, componentes de calidad inferior y fallos potencialmente catastróficos.
Criterios clave para la evaluación de proveedores de AM metálica para el sector aeroespacial:
- Certificaciones y conformidad aeroespacial: Suele ser un punto de partida no negociable.
- Certificación AS9100: Esta norma especifica los requisitos del Sistema de Gestión de Calidad (SGC) para las organizaciones que diseñan, desarrollan o fabrican productos aeronáuticos, espaciales y de defensa. La certificación AS9100 indica el compromiso de un proveedor con el control riguroso de procesos, la trazabilidad, la gestión de riesgos y la mejora continua en línea con las expectativas de la industria aeroespacial. La falta de AS9100 es a menudo un descalificador para el hardware de vuelo crítico.
- Acreditación NADCAP: El Programa Nacional de Acreditación de Contratistas Aeroespaciales y de Defensa ofrece acreditaciones especializadas para procesos específicos. Aunque la propia AM aún está evolucionando dentro del NADCAP, las acreditaciones para etapas de posprocesamiento cruciales relacionadas como el tratamiento térmico, los ensayos no destructivos (END) y la soldadura (que comparte algunos principios metalúrgicos con la fusión AM) demuestran un alto nivel de control de procesos y una competencia reconocida en todo el sector.
- Conformidad ITAR/EAR: En el caso de proyectos o componentes relacionados con la defensa sujetos a controles de exportación en Estados Unidos, los proveedores deben demostrar que cumplen la normativa sobre tráfico internacional de armas (ITAR) o la normativa sobre administración de exportaciones (EAR) para manejar datos técnicos y hardware sensibles.
- Experiencia y conocimientos demostrados: Los conocimientos teóricos no bastan; la experiencia práctica es vital.
- Especificidad del material: Experiencia demostrada en la impresión y el tratamiento posterior de los materiales específicos requeridos, en este caso, Scalmalloy® y Ti-6Al-4V. Pida pruebas de proyectos con éxito, datos sobre las propiedades de los materiales generados por sus procesos y conocimiento de los matices de cada aleación en AM.
- Relevancia de la aplicación: Se valorará muy positivamente la experiencia en la fabricación de componentes de complejidad, tamaño y criticidad similares a los montajes de cargas útiles aeroespaciales. ¿Han fabricado anteriormente hardware apto para el vuelo? ¿Pueden compartir estudios de casos o ejemplos (no patentados)?
- Asistencia técnica (DfAM): Evalúe la capacidad de su equipo de ingeniería para ofrecer asistencia en el diseño para la fabricación aditiva (DfAM). Pueden ayudar con la optimización de la topología, la integración de estructuras reticulares, el desarrollo de estrategias de apoyo y la garantía de que el diseño es fabricable y cumple los objetivos de rendimiento?
- Resolución de problemas: Evaluar su capacidad para solucionar posibles problemas relacionados con la impresión, el tratamiento posterior o el control de calidad basándose en experiencias anteriores.
- Equipamiento, tecnología y capacidad: Las herramientas importan mucho en AM.
- Tipo de máquina y calidad: ¿Disponen de máquinas de SLM o EBM industriales en buen estado de mantenimiento, adecuadas para Scalmalloy® y Ti-6Al-4V? ¿Se calibran las máquinas con regularidad? ¿Cuál es el fabricante y el modelo? Proveedores como Met3dp utilizan impresoras líderes del sector conocidas por su precisión y fiabilidad, lo que es un indicador positivo.
- Construir volumen: ¿Pueden sus máquinas adaptarse al tamaño de los soportes de carga útil necesarios? Tenga en cuenta tanto las necesidades actuales como los posibles requisitos futuros.
- Redundancia y capacidad: ¿Disponen de varias máquinas capaces de procesar el material necesario para garantizar la redundancia y hacer frente a las fluctuaciones de la demanda o a los pedidos urgentes? ¿Cuál es su tasa de utilización típica y su capacidad disponible?
- Supervisión de procesos: ¿Incorporan sus máquinas capacidades de supervisión del proceso in situ (por ejemplo, supervisión del baño de fusión, imágenes térmicas) para ayudar a garantizar la calidad y la coherencia de la fabricación?
- Abastecimiento, manipulación y trazabilidad de materiales: La calidad del polvo es fundamental.
- Abastecimiento de polvo: ¿De dónde proceden los polvos Scalmalloy® y Ti-6Al-4V? ¿Están los proveedores cualificados y gozan de buena reputación? ¿Realizan inspecciones y pruebas del polvo entrante (química, PSD, morfología, fluidez)? Empresas como Met3dpque fabrican sus propios polvos esféricos de alta calidad utilizando tecnologías avanzadas de atomización con gas y PREP, ofrecen una clara ventaja en el control de esta variable de entrada crítica.
- Manipulación de polvos: ¿Cuáles son sus procedimientos de almacenamiento, manipulación, tamizado y reutilización de polvos metálicos para evitar la contaminación (especialmente la contaminación cruzada entre aleaciones) y la degradación (por ejemplo, la captación de oxígeno en el titanio)?
- Trazabilidad de lotes: ¿Pueden garantizar la trazabilidad completa de los lotes de polvo desde el origen de la materia prima hasta la pieza impresa final? Esto es esencial para el control de calidad aeroespacial y la investigación de no conformidades.
- Capacidades de postprocesamiento (internas o en red): Una pieza acabada requiere algo más que la impresión.
- Evaluación de las capacidades: Evalúe sus capacidades (o su red de socios cualificados) para todos los pasos de postprocesado necesarios: alivio de tensiones, tratamientos térmicos específicos para Scalmalloy®/Ti-6Al-4V, HIP, mecanizado de precisión (CNC multieje), eliminación de soportes, acabado de superficies y END exhaustivos (especialmente escaneado CT).
- Integración y gestión: Si se recurre a socios externos, ¿cómo gestionan la calidad y la logística y garantizan una integración perfecta de estas etapas? ¿Tienen los socios la certificación AS9100/NADCAP?
- Sólido sistema de gestión de la calidad (SGC): Más allá de la certificación, evaluar la aplicación práctica.
- Documentación: Revisar sus procedimientos de control de procesos, gestión de documentación, control de revisiones, notificación de no conformidades y acciones correctivas.
- Capacidad de inspección: ¿Cuáles son sus capacidades metrológicas internas (MMC, escaneado)? ¿Cómo verifican la conformidad de las piezas?
- Control de procesos: ¿Cómo garantizan una ejecución coherente de los procesos bloqueados para obtener piezas cualificadas? ¿Datos de control estadístico de procesos (CEP)?
- Comunicación, gestión de proyectos y costes:
- Capacidad de respuesta: ¿Con qué rapidez y eficacia responden a las consultas y preguntas técnicas?
- Transparencia: ¿Hablan abiertamente de sus procesos, capacidades y posibles retos?
- Gestión de proyectos: ¿Disponen de procesos claros para gestionar los proyectos, proporcionar actualizaciones y cumplir los plazos?
- Estructura de costes: ¿Sus precios son transparentes y competitivos? Asegúrese de que todos los costes (impresión, material, posprocesamiento, END, apoyo a la cualificación) se entienden claramente.
Elegir un proveedor como Met3dpcon sus profundas raíces tanto en equipos de fabricación aditiva como en la producción de polvo metálico de alto rendimiento, junto con décadas de experiencia colectiva en AM metálica, ofrece una base sólida. Su enfoque en soluciones integrales, que abarcan impresoras, materiales avanzados y desarrollo de aplicaciones, les convierte en un socio comprometido con el éxito de sus clientes. Para conocer mejor sus capacidades, visite su sitio web y, en particular, la sección "Quiénes somos"puede aportar información valiosa sobre su filosofía y experiencia. En última instancia, una auditoría exhaustiva y una comunicación abierta son necesarias para confirmar que cualquier proveedor cumple los exigentes requisitos para producir soportes de carga útil de calidad aeroespacial.
Comprender la inversión: Factores de coste y plazos de entrega de los soportes de carga útil AM
La fabricación aditiva ofrece ventajas técnicas convincentes para los montajes de cargas útiles aeroespaciales, pero comprender los costes y plazos asociados es crucial para la planificación del proyecto, la presupuestación y la evaluación del caso empresarial global. Aunque en ocasiones la AM puede suponer un ahorro de costes con respecto a los métodos tradicionales para piezas muy complejas y de bajo volumen (sobre todo si se tienen en cuenta los costes totales del ciclo de vida, como el montaje), es esencial reconocer los diversos factores que influyen en el precio final y el calendario de entrega. Los responsables de compras y los ingenieros necesitan tener una idea clara de estos elementos para tomar decisiones con conocimiento de causa.
Principales factores de coste de los soportes de carga útil impresos en 3D:
- Coste del material: Las aleaciones aeroespaciales de alto rendimiento son caras.
- Elección de aleación: El polvo de Ti-6Al-4V suele ser costoso debido a la base de titanio y a los requisitos de procesamiento. Scalmalloy®, con su contenido en escandio, también es un material de precio elevado. El coste del material suele cobrarse por kilogramo de polvo consumido (incluidos los soportes).
- Volumen y densidad de la pieza: Las piezas más grandes y densas consumen naturalmente más material, lo que repercute directamente en el coste. La optimización topológica y las estructuras reticulares, aunque pueden aumentar el tiempo de diseño/simulación, reducen considerablemente el consumo de material.
- Volumen de la estructura de soporte: El material utilizado para los soportes aumenta el coste y es esencialmente un residuo (aunque a veces se puede recuperar el polvo de los soportes). Minimizar los soportes mediante DfAM reduce este coste.
- Hora de la máquina AM: Las máquinas industriales de AM metálica representan una importante inversión de capital, y su tiempo de funcionamiento es un factor de coste importante.
- Altura de construcción: Este suele ser el principal del tiempo de impresión. Las piezas más altas tardan más, independientemente de la superficie que ocupen en la placa de impresión. Orientar las piezas para minimizar la altura a veces puede reducir el tiempo y el coste de impresión, pero debe equilibrarse con las necesidades de soporte y las propiedades anisotrópicas.
- Volumen de piezas y complejidad: Aunque menos impactante que la altura, el volumen total a escanear y la complejidad de las rutas de escaneado (por ejemplo, celosías intrincadas) influyen en el tiempo por capa.
- Anidamiento y utilización de placas de construcción: La impresión simultánea de varias piezas en una sola placa de impresión (anidamiento) permite amortizar el tiempo de preparación/refrigeración y mejorar potencialmente la utilización de la máquina, reduciendo el coste por pieza en la producción por lotes.
- Máquina Tarifa por hora: Los proveedores tienen en cuenta la depreciación de la máquina, el mantenimiento, el consumo de energía, el uso de gas inerte y el tiempo del operario en una tarifa horaria por tiempo de construcción.
- Costes laborales: Se requiere mano de obra cualificada en todo el flujo de trabajo AM.
- Preprocesamiento: Preparación de archivos, simulación de configuración de construcción, generación de soporte.
- Funcionamiento de la máquina: Configurar la construcción, supervisar el proceso.
- Tratamiento posterior a la impresión: Retirada de piezas de la placa de impresión, limpieza básica.
- Retirada del soporte: A menudo, un importante componente de trabajo manual, especialmente para piezas complejas.
- Acabado básico: Granallado, limpieza inicial de la superficie.
- Costes de postprocesamiento: Estos pasos añaden un coste significativo más allá de la impresión inicial.
- Alivio del estrés y tratamiento térmico: Requiere hornos especializados de vacío/atmósfera inerte y energía; los costes dependen de la duración del ciclo y de la capacidad del horno.
- Prensado isostático en caliente (HIP): Requiere grandes equipos de capital de alta presión; normalmente se subcontrata y se cobra por ciclo, con un coste que depende del tamaño/cantidad de las piezas que encajan en la unidad HIP. Puede suponer una parte sustancial del coste total.
- Mecanizado CNC: Se factura en función del tiempo de máquina y la complejidad; es necesario para conseguir tolerancias estrechas y acabados finos en características críticas.
- Acabado superficial: Los costes varían mucho en función del método (volteo, pulido, grabado) y del nivel de acabado requerido.
- END e inspección: Tiempo de inspección en MMC, servicios de escaneado por TC (pueden ser costosos, sobre todo para piezas de alta resolución o de gran tamaño), FPI, etc.
- Costes de diseño e ingeniería:
- DfAM y Optimización: Si se requiere un rediseño significativo o una optimización de la topología, hay que tener en cuenta esta inversión inicial en ingeniería.
- Apoyo a la cualificación: Tiempo de ingeniería dedicado a desarrollar planes de pruebas, analizar resultados y preparar documentación para la cualificación de piezas.
- Cantidad:
- Prototipos/One-Offs: Mayor coste por pieza debido al tiempo de preparación y a la falta de amortización.
- Producción por lotes: Menor coste por pieza, ya que la configuración, el tiempo de máquina (si se anida de forma eficaz) y, potencialmente, el posprocesamiento pueden optimizarse para el volumen.
Cuadro sinóptico de los factores de coste:
Categoría del generador de costes | Factores específicos | Nivel de impacto | Notas |
---|---|---|---|
Material | Tipo de aleación (Scalmalloy®/Ti-6Al-4V), Volumen de la pieza, Volumen del soporte | Alta | Aleaciones de primera calidad; DfAM crítico para minimizar el volumen. |
Hora de la máquina AM | Altura de construcción, volumen de construcción/complejidad, eficiencia de anidamiento, velocidad de la máquina | Alta | La altura es clave; el anidado reduce el tiempo por pieza para los lotes. |
Trabajo | Preparación de la construcción, funcionamiento, retirada de piezas/soportes, acabado básico | Medio | La retirada de soportes puede requerir mucho trabajo. |
Tratamiento posterior | Alivio de tensiones, tratamiento térmico, HIP, mecanizado CNC, acabado superficial, END | Alta | HIP y CNC/NDT extensivos pueden aumentar significativamente el coste. |
Diseño e ingeniería | Esfuerzo DfAM, simulación, apoyo a la cualificación | Medio | Inversión inicial, especialmente para piezas altamente optimizadas/cualificadas. |
Cantidad | Producción única frente a producción por lotes | Medio | Los costes de instalación se amortizan en cantidades mayores. |
Exportar a hojas
Plazos de entrega de los soportes de carga útil AM:
El plazo de entrega es la duración desde la realización del pedido (o la congelación del diseño) hasta la entrega final de la pieza. Puede variar significativamente en función de la complejidad, la cantidad, el procesamiento posterior necesario y el retraso del proveedor. Un desglose típico podría ser el siguiente:
- Procesamiento de pedidos y preparación de archivos: 1-3 días laborables. Revisión del diseño, generación de archivos de construcción, programación del tiempo de máquina.
- Imprimiendo: De 2 días a 1,5 semanas o más. Depende en gran medida de la altura de la pieza y de la utilización del volumen de construcción. Un montaje alto y complejo puede requerir varios días de impresión continua.
- Post-procesamiento: De 1 a más de 4 semanas. Esta fase suele dominar el plazo de entrega.
- Alivio del estrés/Tratamiento térmico: 1-3 días (incluyendo tiempo de horno y enfriamiento).
- HIP: La programación puede llevar tiempo; el ciclo en sí tarda aproximadamente un día, pero la logística hacia/desde un proveedor de HIP añade días/semanas.
- Eliminación de soportes y acabado básico: 1-5 días, dependiendo de la complejidad.
- Mecanizado CNC: de 2 días a más de 2 semanas, en función de la complejidad, las características y la carga de trabajo del taller de mecanizado.
- END e inspección: 1-5 días.
- Envío: De 1 día a más de 1 semana, según el lugar y el método.
Tiempo total estimado de entrega: Normalmente oscila entre De 3 a 8 semanas o más para un montaje de carga útil aeroespacial complejo, totalmente postprocesado e inspeccionado. Esto puede ser mucho más rápido que los meses que puede requerir la fabricación tradicional con herramientas complejas (fundición) o amplias configuraciones de mecanizado para una pieza comparable de bajo volumen y alta complejidad.
Comprender estos factores de coste y los componentes del plazo de entrega permite una mejor planificación del proyecto, un presupuesto realista y una comunicación eficaz con los proveedores de servicios de AM, como Met3dp, para optimizar el proceso de fabricación en función de las necesidades específicas del proyecto.
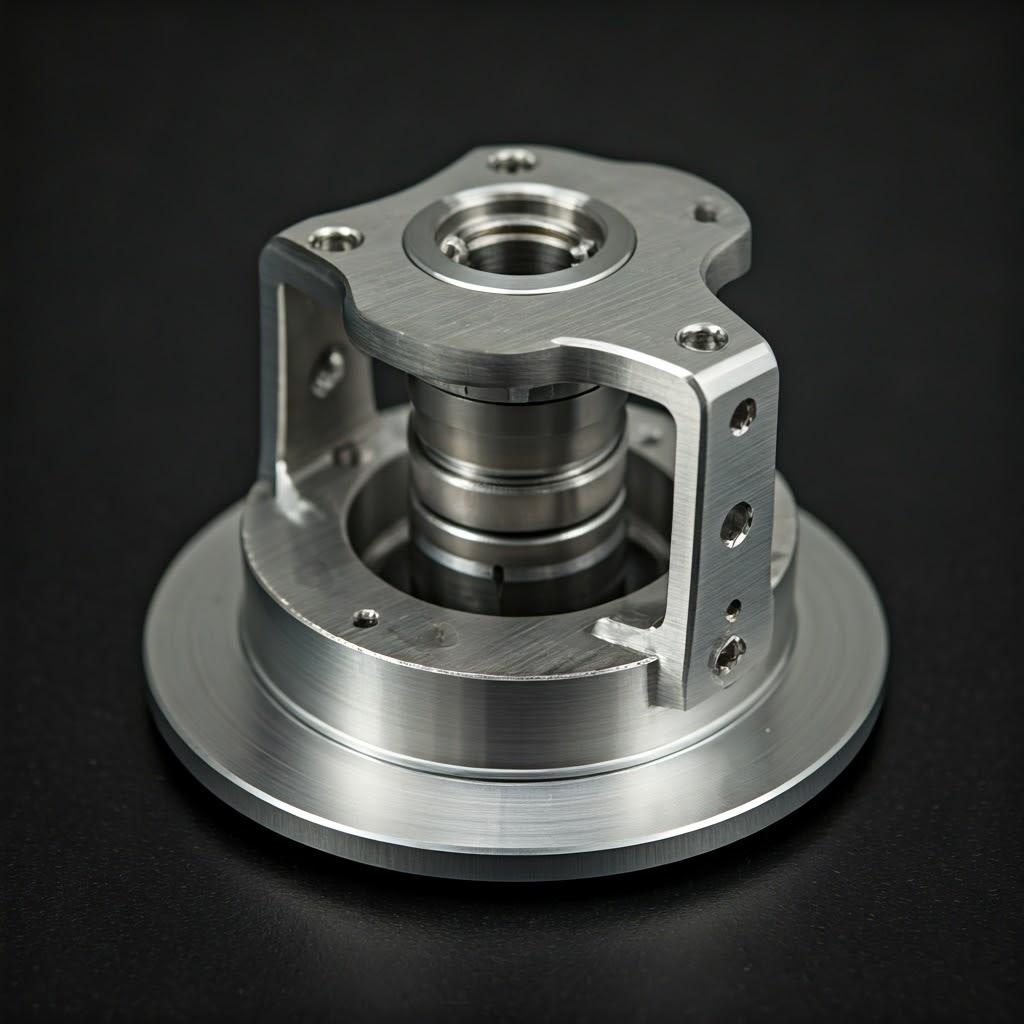
Preguntas frecuentes sobre los soportes de carga útil aeroespacial impresos en 3D
Cuando los ingenieros y los responsables de compras se plantean adoptar la fabricación aditiva de metales para componentes críticos como los soportes de carga útil utilizando materiales avanzados como Scalmalloy® y Ti-6Al-4V, surgen varias preguntas comunes. He aquí las respuestas a algunas de las preguntas más frecuentes:
1. ¿Cómo es la vida a fatiga de los soportes de carga útil AM en comparación con los mecanizados tradicionalmente?
- La vida a fatiga de las piezas de AM depende en gran medida de varios factores: la elección del material, los parámetros del proceso, la densidad alcanzada, el acabado superficial y el postprocesado (especialmente el tratamiento térmico y el HIP).
- Estado As-Built: Sin un postprocesado como el HIP, las piezas de AM (especialmente las de SLM) pueden presentar a veces una vida útil a la fatiga inferior a la de sus equivalentes forjadas o mecanizadas, debido a la posible microporosidad que actúa como lugar de iniciación y a un acabado superficial más rugoso.
- Con HIP y acabado: Cuando se somete a prensado isostático en caliente (HIP) para cerrar la porosidad interna y a un acabado superficial adecuado (por ejemplo, pulido o mecanizado de las zonas críticas), el comportamiento a fatiga de los materiales AM Ti-6Al-4V y Scalmalloy® puede igualar o incluso superar el de los materiales fundidos o, en ocasiones, forjados, especialmente cuando el DfAM permite optimizar las trayectorias de carga que reducen los picos de tensión.
- Lo más importante: Conseguir una vida a la fatiga excelente, comparable o superior a la de los métodos tradicionales, es posible, pero requiere un control meticuloso del proceso, polvo de alta calidad, un postprocesado adecuado (el HIP suele ser crucial) y pruebas exhaustivas para su validación.
2. ¿Qué normas de cualificación (por ejemplo, NASA, ESA, FAA) deben cumplir las piezas aeroespaciales AM?
- Las vías de cualificación de los componentes aeroespaciales de AM siguen evolucionando, pero cada vez están más normalizadas. No existe una única norma universal, pero las piezas suelen tener que cumplir los requisitos establecidos por la autoridad de certificación pertinente (FAA para aviones comerciales, NASA/ESA para misiones espaciales, DoD para militares) y las normas específicas del contratista principal.
- Proceso: La cualificación suele implicar un riguroso enfoque de "cualificación del diseño por puntos":
- Bloqueo de procesos: Definición y congelación de todos los parámetros: tipo de máquina, versiones de software, especificación del material (química del polvo, PSD, proveedor), parámetros de fabricación, ciclos térmicos de postprocesado, estrategias de soporte, métodos de acabado, procedimientos END.
- Desarrollo de materiales admisibles: Pruebas exhaustivas de cupones de material construidos con el proceso bloqueado en varias orientaciones para establecer propiedades de diseño fiables desde el punto de vista estadístico (por ejemplo, admisibles en base A o B), a menudo siguiendo directrices similares a las del MMPDS (Metallic Materials Properties Development and Standardization) o el CMH-17 (Composite Materials Handbook).
- Pruebas de componentes: Construcción y ensayo de componentes completos en condiciones estáticas, dinámicas (vibración, choque), de fatiga y ambientales representativas.
- Documentación: Documentación exhaustiva que abarca todo el proceso, los resultados de las pruebas y las medidas de control de calidad.
- Normas: Entre los documentos pertinentes figuran NASA-STD-6016, NASA-STD-6030, las normas elaboradas por el comité AMS-AM de SAE International y los requisitos específicos de empresas primarias como Boeing, Airbus, Lockheed Martin, etc.
3. ¿Pueden integrarse canales de refrigeración internos complejos o rutas de cableado en los soportes de carga útil impresos en 3D?
- Sí, ésta es una de las ventajas significativas de la fabricación aditiva. La AM permite crear canales, conductos o cavidades internas de gran complejidad directamente dentro de la estructura de montaje de la carga útil durante el proceso de impresión.
- Aplicaciones: Puede utilizarse para:
- Gestión térmica: Integración de canales para refrigeración líquida o vías pasivas de disipación de calor para componentes electrónicos sensibles dentro de la carga útil.
- Reducción de peso: Creación de vacíos internos o estructuras reticulares.
- Cableado integrado/fibra óptica: Diseño de conductos para proteger y enrutar cables o fibras ópticas, reduciendo el desorden y los posibles riesgos de enganche.
- Desafíos: Es fundamental diseñar estos canales para que sean autoportantes o garantizar que los soportes y el polvo atrapado puedan retirarse completamente después de la impresión. Es necesario realizar una limpieza y una inspección minuciosas (por ejemplo, un escáner CT) para verificar la integridad y la holgura de los canales.
4. ¿Cuál es la consistencia típica entre lotes para las propiedades críticas en AM?
- Conseguir propiedades uniformes de una fabricación a otra y de una máquina a otra es uno de los principales objetivos de la maduración de la tecnología AM para la producción. La uniformidad depende en gran medida del rigor del sistema de gestión de calidad (SGC) del proveedor y de los controles del proceso.
- Factores clave para la coherencia:
- Estricto control y ensayo de los lotes de polvo entrantes.
- Calibrado y mantenimiento periódicos de las máquinas.
- Parámetros de proceso bloqueados y validados.
- Ejecución coherente del postprocesado (por ejemplo, hornos calibrados, ciclos validados).
- Utilización de herramientas de supervisión de procesos y control estadístico de procesos (CEP).
- ~1600-1900 MPa Con un sólido control del proceso, los proveedores experimentados pueden alcanzar altos niveles de consistencia entre lotes en cuanto a propiedades mecánicas (tracción, fluencia, alargamiento) y densidad. Sin embargo, la demostración de esta uniformidad mediante controles y ensayos continuos forma parte del proceso de cualificación y producción.
5. ¿Cómo garantiza Met3dp la calidad y trazabilidad de sus polvos metálicos y piezas impresas?
- Met3dp hace especial hincapié en la calidad a lo largo de toda la cadena de valor de la fabricación aditiva.
- Calidad del polvo: Mediante el empleo de avanzadas tecnologías internas de atomización con gas y PREP, Met3dp mantiene un estricto control sobre la producción de polvo, centrándose en lograr una alta esfericidad, una distribución controlada del tamaño de las partículas (PSD), una alta pureza y una buena fluidez, factores críticos para una impresión consistente. Cada lote se somete a rigurosas pruebas y certificaciones.
- Control de procesos: Utilizando impresoras SEBM y otras impresoras PBF líderes del sector, conocidas por su precisión y fiabilidad, Met3dp se centra en el desarrollo y la aplicación de parámetros de proceso sólidos y optimizados para las aleaciones que ofrecen.
- Trazabilidad: La implantación de sistemas de trazabilidad exhaustivos permite realizar un seguimiento de los materiales y los datos del proceso desde el lote de polvo en bruto, pasando por la impresión y el postprocesado, hasta el componente final certificado, lo que resulta esencial para los requisitos aeroespaciales.
- Asociación: Met3dp colabora con los clientes para comprender los requisitos de calidad específicos y apoya el desarrollo de los planes de ensayo y cualificación necesarios para aplicaciones críticas, aprovechando su experiencia tanto en materiales como en procesos de AM.
6. ¿Existen cantidades mínimas de pedido (MOQ) para los soportes de carga útil impresos en 3D?
- Las cantidades mínimas de producción pueden variar considerablemente de un proveedor a otro. La AM es idónea para producir piezas únicas o lotes muy pequeños (por ejemplo, para prototipos, satélites o modificaciones personalizadas), lo que constituye una de sus ventajas frente a los métodos tradicionales basados en herramientas.
- Estructura de precios: Aunque las MOQ no siempre son estrictas, el coste por pieza suele ser mucho más elevado en el caso de piezas únicas o cantidades muy pequeñas, en comparación con lotes más grandes, debido a la amortización de los costes fijos y de preparación. Los proveedores pueden ofrecer descuentos en función de la cantidad. Lo mejor es discutir los volúmenes específicos del proyecto directamente con el proveedor.
7. ¿Cómo se protege la propiedad intelectual (PI) cuando se envían diseños aeroespaciales sensibles a un proveedor de AM?
- Proteger los datos de diseño confidenciales es crucial. Los proveedores de AM reputados del sector aeroespacial deben contar con medidas sólidas:
- Acuerdos de confidencialidad: Práctica habitual para proteger legalmente la información confidencial.
- Transferencia segura de datos: Utilización de métodos cifrados para transferir archivos CAD y datos técnicos.
- Controles de acceso: Limitar el acceso a datos sensibles dentro de su organización en función de la necesidad de conocerlos.
- Conformidad ITAR/EAR: Para los datos controlados, los proveedores deben disponer de procedimientos de conformidad demostrados.
- Es esencial discutir los protocolos de protección de la propiedad intelectual y firmar los acuerdos de confidencialidad apropiados antes de compartir cualquier información de diseño patentada.
Conclusiones: La fabricación aditiva avanzada al servicio de las misiones aeroespaciales
El viaje a través de los entresijos del diseño, la fabricación y la cualificación de soportes de carga útil aeroespacial mediante fabricación aditiva de metales revela una tecnología preparada para redefinir la creación de componentes para satélites, aeronaves y vehículos aéreos no tripulados. Aprovechando materiales avanzados como el Scalmalloy y el caballo de batalla aeroespacial Ti-6Al-4VLa AM permite a los ingenieros liberarse de las limitaciones de la fabricación tradicional. La capacidad de producir geometrías muy complejas y de topología optimizada se traduce en importantes beneficios. reducción de peso - un objetivo primordial en el sector aeroespacial: reducir los costes de lanzamiento, aumentar la capacidad de carga útil o mejorar la eficiencia del combustible.
Más allá del aligeramiento, la AM metálica permite libertad de diseñoEsto permite la creación de montajes funcionalmente superiores con características integradas como canales internos, estructuras reticulares para mejorar la rigidez o la amortiguación de vibraciones, y ensamblajes consolidados que reducen el número de piezas, la complejidad y los posibles puntos de fallo. Esto acelera los ciclos de desarrollo mediante prototipado rápido y facilita la producción de componentes altamente personalizados esenciales para los requisitos de misiones específicas.
Sin embargo, para aprovechar estas ventajas es necesario un planteamiento riguroso. El éxito depende de Diseño para fabricación aditiva (DfAM) principios, planificando y ejecutando meticulosamente los post-procesamiento de las tensiones, el tratamiento térmico, el HIP y el mecanizado de precisión, y superar posibles retos como la tensión residual, la eliminación de soportes y el control de la porosidad. Por encima de todo, garantizar la aptitud para el vuelo exige un compromiso inquebrantable con control de calidad, validación de procesos e inspección minuciosaque culmina en una rigurosa cualificación de las piezas que cumple las estrictas normas aeroespaciales.
Elegir al socio de fabricación adecuado es, sin duda, el paso más crítico en este viaje. Las empresas aeroespaciales necesitan proveedores que posean no solo equipos de última generación, sino también profundos conocimientos en ciencia de materiales, experiencia demostrada en aplicaciones aeroespaciales, sólidos sistemas de gestión de la calidad (con certificación AS9100) y un conocimiento exhaustivo de toda la cadena de procesos, desde el polvo hasta la pieza cualificada.
Met3dp encarna estas cualidades, situándose como proveedor líder de soluciones integrales de fabricación aditiva. Con capacidades líderes en el sector en impresión SEBM de alta precisión, producción propia de polvos metálicos esféricos de alto rendimiento mediante técnicas avanzadas de atomización y décadas de experiencia colectiva, Met3dp se encuentra en una posición única para satisfacer los exigentes requisitos del sector aeroespacial. Su compromiso abarca desde el suministro de materiales y equipos de calidad superior hasta la prestación de servicios de desarrollo de aplicaciones y la colaboración con organizaciones para superar las complejidades de la adopción y cualificación de la AM.
Al adoptar la fabricación aditiva de metales y colaborar con socios expertos como Met3dp, la industria aeroespacial puede seguir superando los límites del rendimiento, la eficiencia y la capacidad de misión. El futuro de los componentes aeroespaciales se está construyendo capa a capa, permitiendo que vehículos más ligeros, más fuertes y más capaces exploren los cielos y el espacio más allá.
¿Está listo para explorar cómo la impresión 3D en metal puede revolucionar sus componentes aeroespaciales? Visita https://met3dp.com/ o póngase en contacto con el equipo de Met3dp hoy mismo para hablar de su aplicación específica y saber cómo sus soluciones avanzadas de AM pueden elevar su próxima misión.
Compartir
MET3DP Technology Co., LTD es un proveedor líder de soluciones de fabricación aditiva con sede en Qingdao, China. Nuestra empresa está especializada en equipos de impresión 3D y polvos metálicos de alto rendimiento para aplicaciones industriales.
Solicite información para obtener el mejor precio y una solución personalizada para su empresa.
Artículos relacionados
Acerca de Met3DP
Actualización reciente
Nuestro producto
CONTACTO
¿Tiene alguna pregunta? ¡Envíenos un mensaje ahora! Atenderemos su solicitud con todo un equipo tras recibir su mensaje.
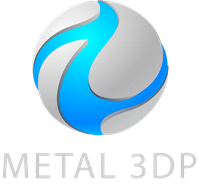
Polvos metálicos para impresión 3D y fabricación aditiva