Cama de polvo Fusion
Índice
Visión general
La fusión de lechos de polvo es un proceso de fabricación aditiva que utiliza energía térmica para fusionar selectivamente regiones de un lecho de polvo capa por capa para construir piezas. Es una de las tecnologías de impresión 3D de metales más utilizadas en la actualidad para aplicaciones de producción.
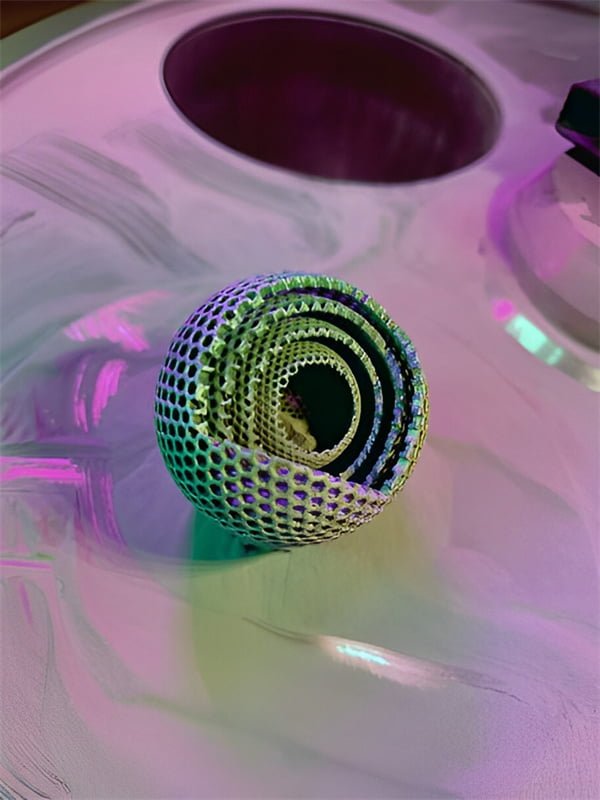
Algunos detalles clave sobre la fusión de lechos de polvo:
- Pertenece a la familia de la fotopolimerización en cuba de la fabricación aditiva.
- Se utiliza una fuente de energía térmica, como un láser o un haz de electrones, para fundir y fusionar el polvo de material.
- Los polvos utilizados suelen ser metales como acero inoxidable, titanio, aluminio, aleaciones de níquel y cromo-cobalto. En algunos procesos también pueden utilizarse polímeros y cerámicas.
- La fusión en lecho de polvo puede crear piezas metálicas totalmente densas con propiedades mecánicas comparables a las de la fabricación tradicional.
- Permite geometrías complejas que no son posibles con las técnicas sustractivas convencionales.
- Las aplicaciones abarcan los sectores aeroespacial, médico, dental, automovilístico e industrial en general.
- Entre las tecnologías de lecho de polvo más populares se encuentran la fusión selectiva por láser (SLM), el sinterizado directo de metales por láser (DMLS), la fusión por haz de electrones (EBM) y la inyección de aglutinante.
Procesos de fusión en lecho de polvo
Se han desarrollado varias tecnologías de fusión en lecho de polvo. Las principales son:
Proceso | Descripción |
---|---|
Fusión selectiva por láser (SLM) | Utiliza un láser de alta potencia para fundir y fusionar completamente el polvo metálico en el lecho. |
Sinterización directa de metales por láser (DMLS) | Similar a la SLM pero orientada a la sinterización de polvos frente a la fusión completa. |
Fusión por haz de electrones (EBM) | Utiliza un haz de electrones como fuente de energía para fundir el polvo. Se realiza en vacío. |
Fusión multichorro (MJF) | Impresión por chorro de tinta de un agente de fusión sobre un lecho de polvo polimérico antes de la sinterización con una fuente de energía. |
Chorro aglomerante | Agente aglutinante líquido depositado selectivamente para aglutinar material en polvo seguido de sinterización. |
Fusión selectiva por láser (SLM) es la tecnología de fusión de lecho de polvo más utilizada en la actualidad. Un láser de alta potencia (por ejemplo, fibra, CO2, YAG) se enfoca sobre un lecho de polvo para crear charcos de fusión y fundir el material. El lecho de polvo desciende después de cada capa y se esparce nuevo polvo sobre él. La SLM utiliza la fusión total, lo que permite fabricar piezas totalmente densas. Se suelen utilizar materiales como acero inoxidable, titanio, aluminio e Inconel.
Sinterizado directo de metales por láser (DMLS) funciona de forma similar, pero su objetivo es fundir sólo parcialmente el polvo para formar cuellos entre las partículas y producir una pieza sólida. El DMLS requiere menos potencia láser que el SLM.
Fusión por haz de electrones (EBM) utiliza un haz de electrones como fuente de energía enfocada al vacío para fundir los polvos metálicos capa por capa. La EBM permite mayores velocidades de fabricación que los procesos basados en láser, ya que el haz puede escanear más rápido. La EBM se utiliza sobre todo con aleaciones de titanio en aplicaciones aeroespaciales.
Fusión multichorro (MJF) utiliza cabezales de impresión de chorro de tinta para depositar selectivamente el agente de fusión en un lecho de polvo de polímero que, a continuación, se sinteriza mediante una fuente de energía. La MJF permite sinterizar termoplásticos a alta velocidad.
Chorro aglomerante deposita primero un agente aglutinante líquido en zonas seleccionadas para aglutinar el material en polvo, seguido de la sinterización para densificar la pieza. Puede utilizarse con metales, cerámicas y polímeros.
Materiales de fusión del lecho de polvo
En la fabricación aditiva por fusión en lecho de polvo pueden utilizarse diversos materiales. Los más comunes son:
Material | Procesos | Aplicaciones |
---|---|---|
Acero inoxidable | SLM, DMLS, Chorro aglomerante | Implantes médicos, utillaje, ingeniería general |
Aleaciones de titanio | SLM, EBM | Implantes médicos y aeroespaciales |
Aleaciones de aluminio | SLM, EBM | Aligeramiento en la industria aeroespacial y del automóvil |
Superaleaciones de níquel | SLM, EBM | Álabes de turbina, toberas de cohete para entornos extremos |
cromo cobalto | SLM, DMLS | Implantes dentales y prótesis |
Polímeros | MJF, Chorro de ligante | Prototipos y piezas de plástico de uso final |
Cerámica | Chorro aglomerante | Implantes médicos, aeroespacial |
Los más utilizados son aceros inoxidablesque ofrecen una buena resistencia a la corrosión y buenas propiedades mecánicas. Aleaciones de titanio como el Ti6Al4V son populares en la industria aeroespacial por su menor peso en comparación con el acero y las aleaciones de níquel. Aleaciones de aluminio permiten fabricar piezas ligeras para los sectores automovilístico y aeroespacial.
Superaleaciones de níquel como el Inconel se utilizan para álabes de turbinas de alta temperatura y toberas de cohetes. Aleaciones de cobalto-cromo son biocompatibles y se utilizan ampliamente en restauraciones dentales. Polímeros como el nylon, el PEEK y las poliamidas pueden sinterizarse para fabricar piezas de plástico. Cerámica como la zirconia y la alúmina tienen aplicaciones en implantes médicos.
La distribución del tamaño de las partículas, la fluidez, la densidad de empaquetado y el punto de fusión son propiedades clave del material en polvo que determinan la procesabilidad y las propiedades finales de la pieza.
Aplicaciones de fusión en lecho de polvo
La fabricación aditiva por fusión en lecho de polvo se utiliza en las industrias aeroespacial, médica, dental, de automoción y de ingeniería en general. Entre las aplicaciones típicas se incluyen:
Industria | Aplicaciones |
---|---|
Aeroespacial | Álabes de turbinas, toberas de cohetes, perfiles aerodinámicos, satélites, drones |
Médico | Implantes ortopédicos y dentales, prótesis, instrumental quirúrgico |
Automoción | Prototipos aligerados, utillaje a medida |
Industrial | Herramientas metálicas, equipos de minería, manipulación de líquidos |
Arquitectura | Elementos decorativos, fachadas, iluminación, mobiliario |
En aeroespacialLa fusión en lecho de polvo es ideal para componentes únicos, como satélites y vehículos aéreos no tripulados. Se utiliza para piezas ligeras de titanio y aleaciones de níquel, como turbinas, toberas y fuselajes.
Para médicoLos implantes y prótesis personalizados de titanio y cromo-cobalto son una de las principales áreas de aplicación. También permite personalizar las herramientas quirúrgicas.
En automociónEl lecho de polvo se utiliza para prototipos ligeros y utillaje personalizado, como plantillas. Para industrial permite fabricar herramientas especializadas, plantillas y piezas metálicas de uso final.
En arquitecturaLa fusión en lecho de polvo facilita geometrías únicas para elementos decorativos y funcionales en edificios y muebles.
Ventajas de la fusión de lechos de polvo
Algunas de las principales ventajas de las tecnologías de fusión en lecho de polvo son:
- Geometrías complejas - Son posibles intrincados rasgos internos y entramados.
- Personalización - Las piezas pueden adaptarse a aplicaciones concretas.
- Aligeramiento - reducir el peso de los componentes optimizando los diseños.
- Consolidación - combinar conjuntos en piezas individuales.
- Alta resistencia - metales totalmente densos comparables a la resistencia del material forjado.
- Plazos de entrega más cortos - entrega rápida del archivo digital a la pieza.
- Personalización masiva - combinando economías de escala con personalización de piezas.
- Sostenibilidad - menos residuos en comparación con los procesos sustractivos.
La capacidad de producir piezas metálicas densas con geometrías complejas personalizadas hace que la fusión en lecho de polvo sea ideal para componentes ligeros y de alto rendimiento en todos los sectores. La tecnología permite consolidar conjuntos en piezas únicas, lo que reduce los costes de fabricación e inventario. El uso de la fabricación aditiva también reduce significativamente el desperdicio de material en comparación con los métodos sustractivos tradicionales, como el mecanizado CNC.
Limitaciones de la fusión del lecho de polvo
Algunas de las limitaciones actuales son:
- Limitaciones de tamaño - Los volúmenes de construcción suelen ser inferiores a 1 metro cúbico.
- Acabado superficial - efecto escalonado que requiere un tratamiento posterior.
- Velocidad de construcción - más lentos que los métodos de fabricación de gran volumen.
- Propiedades anisotrópicas - variaciones direccionales de las propiedades de los materiales.
- Normas - falta de códigos y especificaciones para las piezas calificadas.
- Software - normas de diseño y complejidades en la preparación de archivos.
- Costes - los costes de equipamiento y material siguen siendo relativamente elevados.
El tamaño máximo de los componentes está restringido por el volumen de construcción de las máquinas, que está mejorando pero sigue siendo inferior a 1 metro cúbico. El proceso capa por capa puede dar lugar a un acabado superficial deficiente que requiere alisado y pulido.
En general, las velocidades de fabricación son más lentas en comparación con las tecnologías de producción de gran volumen, como el moldeo por inyección. Las piezas también pueden presentar propiedades anisótropas en función de la orientación de la fabricación. La falta de normas y especificaciones para calificar las piezas impresas también es una limitación en sectores muy regulados como el aeroespacial y el médico. Diseñar piezas óptimas y preprocesar archivos requiere conocimientos avanzados de software.
Los costes del sistema y de los materiales siguen siendo relativamente altos en comparación con la fabricación tradicional. Sin embargo, los costes se están reduciendo con el aumento de la adopción y muchas aplicaciones pueden justificar los costes debido al rendimiento de las piezas, la personalización y la flexibilidad del diseño.
Tratamiento posterior
El postprocesamiento hace referencia a los pasos necesarios tras el proceso de fabricación para obtener una pieza acabada:
- Eliminación de polvo - Las piezas se separan del polvo no fundido mediante cepillos.
- Soportes de eliminación - Se cortan las estructuras de soporte y se limpia la superficie.
- Acabado de superficies - Lijado, esmerilado, granallado para mejorar
Parámetros del proceso
Hay varios parámetros clave del proceso que pueden ajustarse para optimizar las propiedades, el rendimiento y la productividad con la fusión de lecho de polvo:
Parámetro | Alcance típico | Efecto |
---|---|---|
Potencia del láser | 50-500W | Velocidad de fusión, tamaño del baño de fusión, profundidad de penetración |
Velocidad de exploración | 100-10.000 mm/s | Velocidad de solidificación, velocidad de enfriamiento, microestructura |
Distancia entre escotillas | 50-200 μm | Pistas superpuestas, densidad, fuerza de adherencia |
Grosor de la capa | 20-100 μm | Resolución, rugosidad de la superficie, tiempo de construcción |
Estrategia de exploración | Islas, rayas, tablero de ajedrez | Tensiones residuales, distorsión, anisotropía |
Atmósfera de proceso | Vacío, gas inerte | Oxidación, contaminación, porosidad |
Potencia del láser afecta al aporte de energía, la velocidad de fusión, las dimensiones del baño de fusión y la profundidad de penetración. Velocidad de exploración controla la velocidad de solidificación y la velocidad de enfriamiento, que influyen en la morfología del grano y la formación de defectos.
Distancia entre escotillas establece el espaciado entre las pistas de escaneado y afecta a la superposición, densificación y unión entre capas. Grosor de la capa determina la resolución, la rugosidad de la superficie y el tiempo total de fabricación.
Estrategia de exploración (patrones de escaneado) afecta a las tensiones residuales, la distorsión y las propiedades anisotrópicas en función de la dirección de impresión. Atmósfera de proceso determina los niveles de oxidación y contaminación.
Reciclaje de polvo
- El polvo sin fundir puede recogerse y tamizarse para eliminar las partículas grandes
- Reutilización típica de hasta 20 ciclos
- Reduce significativamente los costes de polvo
- Polvo fresco añadido para reponer y mantener la química
- Propiedades controladas por umbrales de reutilización
Los procesos de fusión en lecho de polvo reutilizan el polvo no fundido para construcciones adicionales. Tras el despolvoreado, el polvo suelto se recoge, se tamiza para eliminar las partículas grandes y se mezcla con polvo fresco antes de reutilizarlo.
Los índices típicos de reutilización son de hasta 20 ciclos en función del material, los cambios de tamaño de las partículas y los niveles de contaminación. Este reciclaje mejora enormemente la eficiencia del material y reduce los costes totales de las piezas. La proporción de polvo reutilizado y sus propiedades se supervisan para determinar las tasas de reutilización.
Control de calidad
Algunas de las principales medidas de control de calidad utilizadas en la fusión de lecho pulvígeno son:
- Análisis químico de polvos
- Análisis de la distribución granulométrica
- Seguimiento de la reutilización del polvo
- Control del baño de fusión
- Inspección de la geometría de la pieza
- Pruebas de propiedades mecánicas
- Pruebas no destructivas (por ejemplo, rayos X)
- Tomografía computarizada para defectos internos
- Medición de la rugosidad superficial
La composición química del polvo de entrada y la distribución del tamaño de las partículas se analizan para garantizar una alta calidad. Se realiza un seguimiento de las tasas de renovación del polvo. Los sistemas de control durante el proceso, como el control del baño de fusión, detectan defectos durante la fabricación.
Se miden las tolerancias geométricas de las piezas impresas. Los ensayos mecánicos evalúan las propiedades en función de los parámetros del proceso y la orientación de la fabricación. El escaneado no destructivo y por TC identifica los defectos internos. Se evalúa el acabado superficial. Todos los datos se analizan para calibrar y optimizar los procesos.
Análisis de costes
Los costes típicos de las piezas de fusión en lecho de polvo dependen de:
- Amortización de máquinas
- Costes de material
- Mano de obra para preprocesamiento y postprocesamiento
- Tiempo de construcción y consumo de energía
- Cantidad de polvo reutilizable
- Ratio de compra por vuelo
Los costes de maquinaria se amortizan a lo largo de la vida útil prevista en función del uso. Los costes de material se calculan en función del volumen de piezas y del ratio de compra de material. La mano de obra incluye la preparación de las limas, la configuración, el despolvoreado y los pasos de acabado.
El consumo de energía depende del tiempo de construcción y de los niveles de potencia. El polvo reutilizable reduce los costes totales de material. Los ratios de compra de 3:1 a 20:1 son habituales para piezas de gran valor.
Proveedores
Algunos de los principales proveedores de sistemas de fusión de lecho pulvígeno son:
Proveedor | Tecnología clave |
---|---|
EOS | DMLS (Sinterización directa de metales por láser) |
Sistemas 3D | DMP (impresión directa sobre metal) |
Aditivos GE | DMLM (fusión directa de metales por láser) |
trompeta | Impresoras 3D de metal TruPrint |
Sisma | Sistemas de fusión de metales por láser |
AddUp | Impresoras 3D de metal FormUp |
EOS y Sistemas 3D fueron pioneros en la fusión de lechos de polvo y siguen siendo líderes en la actualidad. Aditivos GE adquirió Concept Laser y Arcam EBM para ofrecer tecnologías láser y de haz de electrones. trompeta y Sisma también ofrecen sistemas SLM industriales. AddUp es una empresa conjunta de Michelin y Fives centrada en la fabricación aditiva de metales.
También hay muchos proveedores de materiales para la fusión en lecho de polvo, como Carpenter, Sandvik, Praxair, LPW Technology y AP&C.
Comparación de costes
Proceso | Coste del equipo | Costo material | Velocidad |
---|---|---|---|
Fusión del lecho de polvo | $100K - $1M+ | $100-500/kg | 5-100 cm3/h |
Mecanizado CNC | $50K - $500K | $5-50/kg | 50-500 cm3/h |
Moldeo por inyección | $100K - $1M+ | $2-5/kg | 100-1000 cm3/h |
Los sistemas de lecho de polvo tienen unos costes de equipamiento elevados, desde $100.000 para impresoras industriales hasta más de $1 millón para sistemas de gran producción. Los materiales oscilan entre $100-500/kg. Las velocidades de producción varían de 5 a 100 cm3/h dependiendo de la tecnología.
El mecanizado CNC tiene unos costes de equipo más bajos, a partir de $50.000. Los costes de los materiales metálicos son más baratos: $5-50/kg. Las velocidades oscilan entre 50 y 500 cm3/h.
Los sistemas de moldeo por inyección también cuestan más de $100.000. Pero el material plástico es muy barato, a $2-5/kg. Las velocidades son de 100-1000 cm3/h.
Así pues, la fusión en lecho de polvo sólo es rentable para piezas metálicas de bajo volumen y alto valor cuyo rendimiento justifique los costes más elevados.
Fusión de lecho de polvo frente a inyección de ligante
Cama de polvo Fusion | Chorro aglomerante | |
---|---|---|
Materiales | Metales, polímeros, cerámica | Metales, polímeros, cerámica |
Densidad | Piezas totalmente densas | Partes porosas, infiltración necesaria |
Precisión | Media, ±0,1% con postprocesado | Medio, ±0,2% |
Acabado superficial | Moderado, requiere acabado | Queda una textura justa y estratificada |
Velocidad | Lento, depende de la fuente de energía | Rápido, independiente de la fuente de energía |
Aplicaciones | Piezas metálicas de uso final | Utillaje, patrones de fundición, prototipos |
- La fusión de lecho de polvo puede producir piezas totalmente densas, mientras que las piezas de inyección de aglutinante son porosas y requieren infiltración.
- La precisión del chorro de aglutinante es moderada, mientras que la fusión de lecho de polvo puede alcanzar mayores precisiones con el postprocesado.
- El acabado superficial por fusión en lecho de polvo requiere acabado, mientras que el chorreado con aglutinante tiene un acabado estratificado y texturizado.
- Las velocidades de fabricación de la inyección de ligante son mucho más rápidas que los procesos de lecho de polvo limitados por la fuente de energía.
- El lecho de polvo se utiliza más para piezas de uso final, mientras que la inyección de ligante es mejor para utillaje, fundición y modelos conceptuales.
Fusión en lecho de polvo frente a deposición de energía dirigida
Cama de polvo Fusion | DED | |
---|---|---|
Materiales | Principalmente metales | Metales, polímeros |
Geometría | Complejidad habilitada | Complejidad media |
Precisión | Media a alta | Medio |
Acabado superficial | Moderado, requiere acabado | En bruto, más acabado |
Escalabilidad | Piezas pequeñas y medianas | Piezas medianas y grandes |
Tasa de deposición | Baja, depende de la velocidad de exploración | Alta, aumenta con boquillas más grandes |
- La fusión en lecho de polvo se utiliza sobre todo con metales, mientras que la DED puede utilizar metales y polímeros.
- La fusión en lecho de polvo permite una mayor complejidad que la DED, que tiene algunas limitaciones geométricas.
- La precisión es mayor con la fusión en lecho de polvo. La precisión del DED es media.
- La DED crea superficies rugosas que requieren más acabado debido a las perlas aditivas.
- La fusión en lecho de polvo construye piezas más pequeñas, mientras que la DED hace formas medianas y grandes cercanas a la red.
- DED tiene tasas de deposición mucho más altas debido a su enfoque de polvo soplado.
Así pues, la fusión en lecho de polvo suele producir geometrías más pequeñas y complejas a velocidades moderadas. La DED produce formas sencillas más grandes mucho más rápido, pero con más trabajo de acabado.
El futuro de la fusión de lechos de polvo
Algunas áreas de desarrollo futuro de la fusión en lecho de polvo son:
- Grandes volúmenes de construcción de hasta varios metros cúbicos
- Métodos de escaneado más rápidos para aumentar la velocidad de fabricación
- Materiales en expansión como aleaciones de alta temperatura, MMC, polímeros
- Fabricación híbrida que integra fusión de lecho de polvo y CNC
- Depuración y postprocesamiento automatizados
- Supervisión y control avanzados en tiempo real
- Procedimientos de cualificación y certificación más rigurosos
Las plataformas de fabricación de mayor tamaño permitirán fabricar piezas más grandes o aumentar el rendimiento de la producción. Las nuevas tecnologías de escaneado más rápidas pueden aumentar drásticamente la velocidad de fabricación. Las opciones de materiales seguirán ampliándose, especialmente en aleaciones de alto rendimiento.
Compartir
MET3DP Technology Co., LTD es un proveedor líder de soluciones de fabricación aditiva con sede en Qingdao, China. Nuestra empresa está especializada en equipos de impresión 3D y polvos metálicos de alto rendimiento para aplicaciones industriales.
Solicite información para obtener el mejor precio y una solución personalizada para su empresa.
Artículos relacionados
Acerca de Met3DP
Actualización reciente
Nuestro producto
CONTACTO
¿Tiene alguna pregunta? ¡Envíenos un mensaje ahora! Atenderemos su solicitud con todo un equipo tras recibir su mensaje.
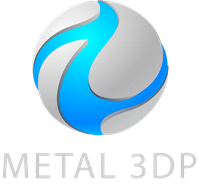
Polvos metálicos para impresión 3D y fabricación aditiva