Polvo para el tratamiento posterior a la atomización
Índice
Imagine a un escultor elaborando meticulosamente una obra maestra a partir de un bloque de mármol. Pero en el mundo de la fabricación aditiva (AM), también conocida como impresión 3D, la materia prima no es tan monolítica. En cambio, la AM metálica se basa en una sinfonía de diminutas partículas metálicas -polvos- para construir objetos capa a capa.
Sin embargo, la historia no termina con la creación de estos polvos metálicos. polvo para tratamiento posterior a la atomización desempeña un papel crucial para garantizar que estas maravillas metálicas cumplan las exigentes normas de la industria AM.
Este artículo se adentra en el fascinante mundo de los polvos para el tratamiento posterior a la atomización, explorando sus características, aplicaciones y los factores que los diferencian.
Visión general del polvo para el tratamiento posterior a la atomización
¿Qué es la atomización? Se trata de transformar el metal fundido en una fina niebla de partículas. Diversas técnicas, como la atomización con gas o agua, lo consiguen descomponiendo la corriente de metal líquido en un mar de gotitas diminutas que se solidifican en el aire.
Pero el viaje no termina ahí. El polvo metálico resultante, aunque aparentemente listo para la AM, puede albergar algunas imperfecciones. Aquí es donde entra en juego el tratamiento posterior a la atomización. Estos procesos especializados refinan las características del polvo, optimizándolo para las exigencias específicas de técnicas de AM como la fusión selectiva por láser (SLM) o la fusión por haz de electrones (EBM).
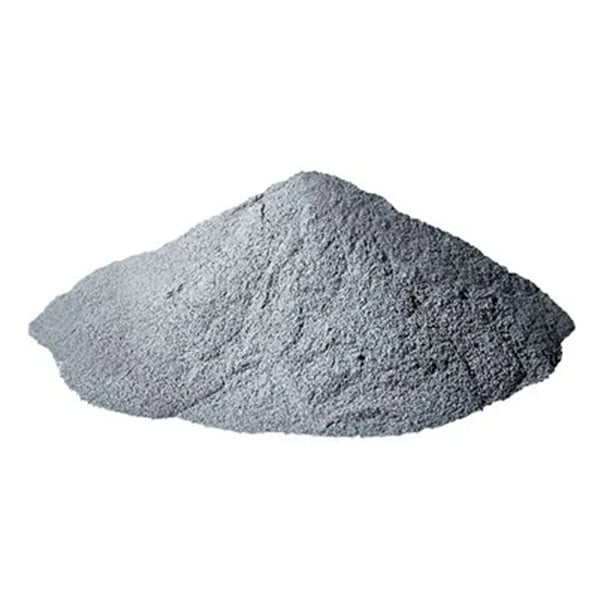
Características de los polvos para el tratamiento posterior a la atomización
Imagínese a un panadero tamizando meticulosamente la harina para garantizar la consistencia del tamaño de las partículas y conseguir un pastel perfecto. Del mismo modo, los polvos para el tratamiento posterior a la atomización se someten a un análisis crítico de diversas características:
- Tamaño y distribución de partículas: Los polvos para AM requieren un rango de tamaños de partícula muy controlado. Las partículas demasiado grandes pueden dificultar la fluidez y provocar una deposición desigual de las capas durante la impresión. Por el contrario, las partículas demasiado finas pueden dificultar la manipulación e incluso impedir la penetración del láser durante el proceso de AM.
- Morfología de partículas: La forma de las partículas de polvo también desempeña un papel fundamental. Idealmente, las partículas esféricas con superficies lisas ofrecen la mejor fluidez y densidad de empaquetamiento, lo que conduce a un proceso de construcción más uniforme y predecible.
- Composición química: Incluso las más mínimas variaciones en la composición química del polvo pueden afectar significativamente a las propiedades finales de la pieza impresa. Los tratamientos posteriores a la atomización pueden ayudar a resolver problemas como la formación de óxido o la presencia de elementos no deseados.
- Fluidez: La fluidez eficaz del polvo es esencial para el buen funcionamiento de la AM. Los polvos poco fluidos dificultan los mecanismos de alimentación y pueden provocar incoherencias en la densidad de las capas.
Los tratamientos posteriores a la atomización se centran en optimizar estas características, garantizando que el polvo resultante lo sea:
- Tamaño y distribución precisos: Piense en ello como si tuviera un lote uniforme de harina, perfecto para obtener resultados de horneado uniformes.
- Forma esférica: Imagínese canicas redondas y lisas, ideales para empaquetar herméticamente y permitir un flujo continuo.
- Químicamente puro: Al igual que para seguir una receta al pie de la letra, el polvo necesita los ingredientes adecuados para que la impresión sea un éxito.
- Muy fluido: Imagínese que la arena fluye sin esfuerzo por un reloj de arena: ésa es la característica de flujo deseada para un rendimiento AM óptimo.
Aplicaciones de los polvos para el tratamiento posterior a la atomización
Los polvos para el tratamiento posterior a la atomización cubren una amplia gama de aplicaciones en el ámbito de la AM. He aquí algunas áreas clave:
- Aeroespacial: La industria AM está revolucionando el sector aeroespacial con la creación de componentes ligeros y de alta resistencia. Los polvos con características precisas son cruciales para construir piezas fiables para aeronaves y naves espaciales, donde la seguridad y el rendimiento son primordiales.
- Implantes médicos: Los implantes médicos personalizados y adaptados a cada paciente se están haciendo realidad gracias a la AM. Aquí, los polvos biocompatibles con una pureza excepcional son esenciales para crear implantes que se integren a la perfección en el cuerpo humano.
- Automóvil: La industria del automóvil recurre cada vez más a la AM para componentes ligeros y geometrías complejas. Los polvos con una fluidez optimizada garantizan resultados de impresión uniformes, vitales para la producción en serie en el sector de la automoción.
- Bienes de consumo: Desde piezas de bicicleta personalizadas hasta joyas complejas, la AM se está haciendo un hueco en el sector de los bienes de consumo. Los polvos con un equilibrio entre estética y funcionalidad son necesarios para crear productos de consumo visualmente atractivos y duraderos.
Procesos clave del tratamiento posterior a la atomización
Varios tratamientos posteriores a la atomización desempeñan un papel vital en el perfeccionamiento de las características de los polvos metálicos para la AM:
- Tamizado y clasificación: De forma similar al tamizado de la harina, el tamizado separa las partículas de polvo en diferentes rangos de tamaño. Esto ayuda a conseguir la distribución granulométrica deseada para aplicaciones AM específicas.
- Desgasificación: Los polvos metálicos pueden contener gases atrapados en el proceso de atomización. Las técnicas de desgasificación, como el secado al vacío, eliminan estos gases y evitan que causen huecos o porosidades en la pieza impresa final.
- Esferoidización: Algunos tratamientos posteriores a la atomización, como la atomización por plasma, pueden producir de forma inherente polvos con una morfología más esférica. Sin embargo, en el caso de polvos generados mediante otras técnicas, procesos adicionales como la atomización rotatoria o el fresado químico pueden ayudar a mejorar su esfericidad.
- Modificación de la superficie: Adaptar la química superficial de las partículas de polvo puede mejorar su rendimiento en el proceso de AM. Técnicas como la carbonitruración o el recubrimiento con lubricantes pueden mejorar la fluidez y la interacción con el láser durante la impresión.
Elegir bien Tratamiento posterior a la atomización:
La selección del tratamiento post-atomización más adecuado depende de varios factores:
- Las características deseadas del polvo final: ¿Es prioritaria una distribución granulométrica estrecha o una mayor fluidez?
- El tipo de polvo metálico: Diferentes metales podrían responder mejor a técnicas específicas de post-atomización.
- La aplicación AM prevista: Los requisitos de los polvos utilizados en componentes aeroespaciales pueden diferir significativamente de los de los bienes de consumo.
He aquí una tabla que resume las ventajas e inconvenientes de algunos tratamientos habituales tras la atomización:
Tratamiento | Ventajas | Desventajas |
---|---|---|
Tamizado y clasificación | Consigue una distribución precisa del tamaño de las partículas | Puede llevar mucho tiempo y provocar pérdidas de material |
Desgasificación | Reduce la porosidad y mejora las propiedades mecánicas | Puede requerir equipos especializados y consumir mucha energía |
Esferoidización | Mejora la fluidez y la densidad de empaquetado | Puede ser un proceso caro, y algunas técnicas pueden introducir impurezas en la superficie |
Modificación de la superficie | Mejora la fluidez y la interacción con el láser | Puede alterar la composición química del polvo y requerir un control estricto |
Es importante señalar que estos tratamientos suelen combinarse para conseguir las características óptimas del polvo. Por ejemplo, el tamizado puede combinarse con la desgasificación para obtener un polvo de tamaño preciso y sin gas.
Comparación de polvos para Tratamiento posterior a la atomización
Los polvos metálicos pueden clasificarse en dos tipos en función de su origen:
- Polvos vírgenes: Estos polvos se producen directamente a partir de fuentes primarias de metal y se someten a un tratamiento posterior a la atomización para aplicaciones de AM.
- Polvos reciclados: Cada vez se presta más atención a la sostenibilidad, por lo que los polvos metálicos reciclados están ganando adeptos. Estos polvos proceden de chatarra y pueden someterse a tratamientos posteriores a la atomización para cumplir las normas de calidad de la AM.
He aquí una comparación de los polvos vírgenes y reciclados para el tratamiento posterior a la atomización:
Parámetro | Polvos vírgenes | Polvos reciclados |
---|---|---|
Composición química | Generalmente mayor pureza y consistencia | Puede contener oligoelementos o impurezas del material de origen |
Fluidez | Buena fluidez típica debido a una manipulación mínima | Puede requerir un tratamiento adicional posterior a la atomización para mejorar la fluidez |
Coste | Generalmente más caro debido a la fuente de material virgen | Puede ser una opción más rentable |
Impacto medioambiental | Mayor huella medioambiental debido a la extracción de metales vírgenes | Menor impacto medioambiental gracias a la reutilización de materiales |
La elección entre polvos vírgenes y reciclados depende de la aplicación específica y del equilibrio deseado entre coste, rendimiento y sostenibilidad.
El futuro de los polvos para Tratamiento posterior a la atomización
El ámbito de los polvos para tratamientos posteriores a la atomización evoluciona constantemente. Estas son algunas de las tendencias más interesantes:
- Desarrollo de técnicas avanzadas de post-atomización: Los investigadores están explorando nuevos métodos, como el tratamiento con microondas o ultrasonidos, para refinar aún más las características del polvo.
- Centrarse en prácticas sostenibles: El uso de polvos reciclados y el desarrollo de procesos de post-atomización respetuosos con el medio ambiente están ganando importancia.
- Diseño de polvo a medida: En el futuro podríamos ver polvos diseñados específicamente con propiedades personalizadas para aplicaciones únicas de AM.
En conclusión, los polvos para el tratamiento posterior a la atomización desempeñan un papel fundamental, aunque a menudo desapercibido, en el éxito de la fabricación aditiva. Conocer sus características, aplicaciones y los distintos procesos de tratamiento nos permite apreciar mejor el intrincado mundo que construye el futuro, partícula a partícula.
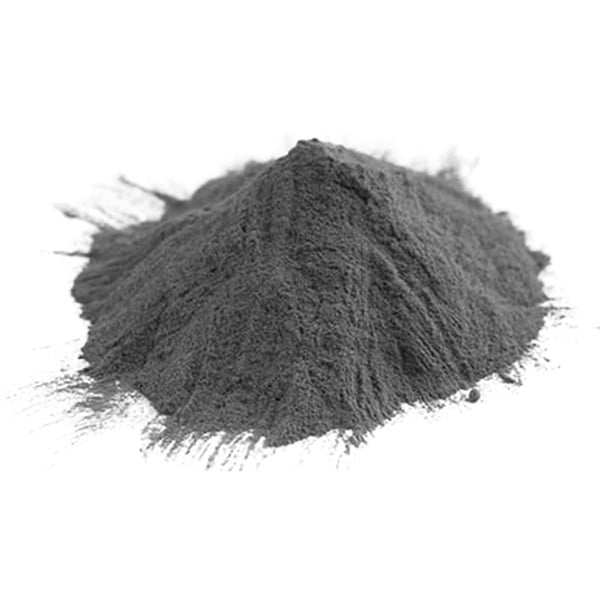
PREGUNTAS FRECUENTES
¿Cuáles son los tamaños típicos de los polvos utilizados en AM?
El tamaño de las partículas de los polvos utilizados en AM puede variar en función de la aplicación específica. Normalmente, los polvos tienen entre 10 y 150 micrómetros de diámetro.
Aplicación | Gama típica de tamaños de partículas (micrómetros) |
---|---|
Aeroespacial | 20-60 |
Implantes médicos | 40-100 |
Automoción | 50-120 |
Bienes de consumo | 70-150 |
¿Cómo influye la calidad del polvo en la pieza impresa final?
La calidad del polvo influye significativamente en las propiedades de la pieza impresa final. Las características del polvo, como el tamaño, la forma y la composición química, pueden afectar a factores como:
- Resistencia mecánica: Las inclusiones, huecos o impurezas en el polvo pueden comprometer la resistencia mecánica de la pieza impresa.
- Acabado superficial: La rugosidad superficial de las partículas de polvo puede traducirse en un acabado más rugoso de la superficie de la pieza impresa.
- Precisión dimensional: Una distribución incoherente del tamaño de las partículas puede provocar imprecisiones dimensionales en la pieza impresa.
¿Cuáles son algunos de los retos asociados al uso de polvos reciclados para la AM?
Aunque los polvos reciclados ofrecen una alternativa sostenible, presentan algunos retos:
- Composición química: Los polvos reciclados pueden contener trazas de elementos o impurezas del material de origen. Estos elementos deben supervisarse y controlarse cuidadosamente para garantizar que la pieza final cumple las especificaciones de rendimiento.
- Fluidez: Los polvos reciclados pueden haber sido sometidos a múltiples etapas de procesamiento, lo que puede afectar a su fluidez. Podría ser necesario un tratamiento adicional posterior a la atomización para conseguir unas características de fluidez óptimas.
- Clasificación y segregación: Los polvos reciclados pueden requerir procesos de selección y clasificación más rigurosos para garantizar una distribución homogénea del tamaño de las partículas.
¿Cuáles son las ventajas de utilizar polvos esféricos en AM?
Los polvos esféricos ofrecen varias ventajas en AM:
- Mejora de la fluidez: Las partículas esféricas con superficies lisas fluyen más fácilmente, lo que permite una formación de capas más lisas durante la impresión.
- Densidad de empaquetado mejorada: Las partículas esféricas se empaquetan de forma más compacta, minimizando los huecos y mejorando la densidad general de la pieza impresa.
- Porosidad reducida: La minimización de los huecos se traduce en una reducción de la porosidad, lo que se traduce en unas propiedades mecánicas más resistentes y consistentes.
¿Cómo pueden asegurarse los usuarios de que están seleccionando el polvo adecuado para su aplicación de AM?
He aquí algunos consejos para seleccionar el polvo adecuado para su aplicación AM:
- Consulte con un proveedor de materiales: Los proveedores de materiales pueden ofrecerle asesoramiento experto sobre la selección del polvo en función de sus necesidades específicas y de la aplicación prevista.
- Considere las propiedades deseadas de la pieza final: Factores como la resistencia mecánica, el acabado superficial y la precisión dimensional deben guiar su selección de polvo.
- Evalúe la relación coste-rendimiento: Los polvos vírgenes pueden ofrecer un rendimiento superior, pero los polvos reciclados pueden ser una opción más rentable.
Al comprender los entresijos de los polvos para el tratamiento posterior a la atomización, los usuarios pueden tomar decisiones informadas que contribuyen al éxito y la alta calidad de los proyectos de fabricación aditiva.
Compartir
MET3DP Technology Co., LTD es un proveedor líder de soluciones de fabricación aditiva con sede en Qingdao, China. Nuestra empresa está especializada en equipos de impresión 3D y polvos metálicos de alto rendimiento para aplicaciones industriales.
Solicite información para obtener el mejor precio y una solución personalizada para su empresa.
Artículos relacionados
Acerca de Met3DP
Actualización reciente
Nuestro producto
CONTACTO
¿Tiene alguna pregunta? ¡Envíenos un mensaje ahora! Atenderemos su solicitud con todo un equipo tras recibir su mensaje.
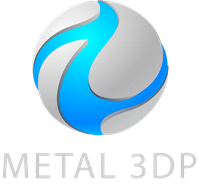
Polvos metálicos para impresión 3D y fabricación aditiva